外圆磨床常见故障排除(严选内容)
球磨机的常见故障及解决办法(表格)

电动机带减速机启动后,发生振动
(1)联轴节的两轮间隙太小,不能够补偿电动机在启动时,由自身磁力中心所引起的窜动量。
(2)减速机、电机及传动轴的传动联轴器没有保持很高的同轴性,致使两轴不同心。
(3)联轴节的连接螺栓没有对称的拧紧,并且紧固力大小不一样。
(4)轴承外圈没有固定好。
解决方法:按规定的对轮间隙调好,使两轴同心。以同等力矩对称紧固连轴节的连接螺栓。转子不平衡时,将球磨机转子抽出另行找出平衡点。
减速机带动磨机时发生巨大振动
(1)球磨机与减速机的平衡轴,轴心不在一直线上,磨机安装衬板时,没有进行二次灌浆,或二次灌浆后的地脚螺栓没有紧固好,用卷扬机转动磨筒体,致使磨筒体一端位移,两轴心不在一直线上,使减速机带动磨机后而产生振动。解决方法:要重新进行调整,使球磨机磨机轴心与减速机轴心在同一平面轴心线上。
球磨机常见故障及解决办法
故障现象
原因分析及解决办法
运行时出现有规则很大的敲打声音
部分衬板螺栓没有拧紧,球磨机旋转时衬板敲击磨筒体。根据声音判断衬板部位,找出松动螺栓,另行紧固。
球磨机及电机轴承温度升高,超过70℃
(1)检查各部位润滑点,润滑油牌号与说明书是否一致。
(2)检查润滑油及润滑脂是否有效。
(3)检查润滑管路是否堵塞,或是润滑油没有直接注入润滑点,油量不足引起发热。
(2)大型球磨机体积大,重量重,使地基下沉;发生了位移。解决方法:在基础旁设监测沉降点,进行观测,发现有下沉时,及时进行调整。
减速机运转声音异常
减速机正常运转的声音应是均匀平稳的。如齿轮发生轻微的敲击声或嘶哑的磨擦声音,而运转中无明显变化,可以继续观察,查清原因,球磨机停机进行处理,如声音越来越大,应立即停止球磨机进行检查。同时,若球磨机减速机的平衡轮与中间轮没有按规定的啮合齿标高安装,会造成球磨机高速轴小齿轮带动一侧的中间轴大齿轮,而球磨机中间轴的小齿轮带动平衡轮,球磨机平衡轮又转过来带动另一侧的中间轴,使球磨机减速机没有形成两侧均衡转动,所以,球磨机减速机的平衡轮与中间轮一定要按照规定的啮合齿标安装。
外圆磨床常见故障排除

调整压力
头架和尾座中心不重合
修正使其重合
6
工件有鼓型
工件刚性差,磨削时产生弹性弯曲变型
减小工件的弹性变化;(1)减小磨削深度(2)及时修正砂轮(3)工件很长时,适当使用中心架。
中心架调整不适当
正确调整支撑肯支承块对工件的压力。
7
工件两端尺寸过大或过小
砂轮超出工件端面台小或过大
工作有不平衡重量时,由于离心力作用,会在重的那边磨去较多金属,使工件有椭圆度。
事先加以平衡
砂轮主轴轴承间隙过大。
调整主轴轴承间隙
用卡盘装夹磨削外圆时,头架主轴径向跳动过大
调整头架主轴轴承间隙
5
工件有锥度
工作台未调整好,工件旋转轴线与工作台运动方向不平行
仔细找正工作台
工件和机床的弹性变型发生变化
应在砂轮锋利的情况下仔细找正工作台,每个工件在精磨时,砂轮的锋利程度,磨削用量和光磨次数应与找正工作台时的情况基本一致,否则需要不均匀走到加以消除,
外圆磨床常见故障排除
外圆磨常见故障排除
1
工件有螺旋形痕迹
砂轮硬度高,修得过细,磨削深度过大。
合理选择砂轮硬度和修正用量,适当减小磨削深度
纵向进给量过大
适当降低进给量
砂轮磨损,母线不直
修正砂轮
金刚石在修正器中未夹紧或金刚石在刀杆未焊牢,修出砂轮凹凸不平。
把金刚石装夹牢固,如金刚石有松动,需重新焊接
冷却液太少或太淡
适当减小磨削深度和纵向进给量,或增大工件转速
冷却液不充足
加大冷却液
3
工件表面出现直波形振痕
工件圆周速速过大,工件中心孔有多角.
适当降低工件转速,修正中心孔
外圆磨床常见故障排除
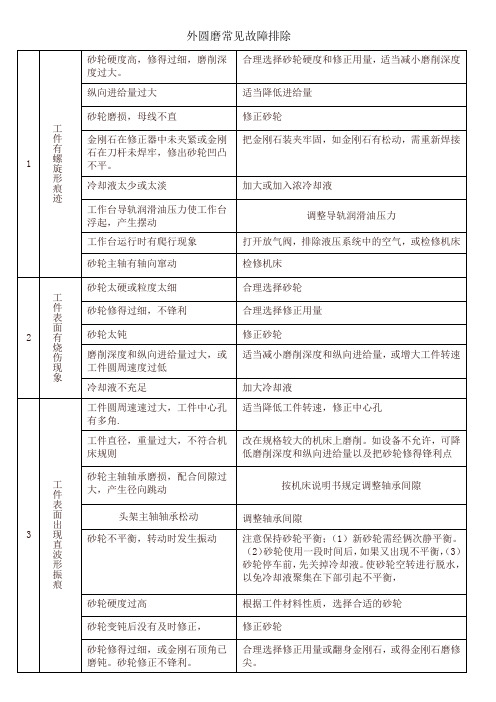
仔细找正工件基准面
10
阶台端面内部凸起
吃刀过大,退刀过块
吃刀时纵向摇动工作台要慢而且均匀,光磨时间要充分
冷却液不充分
加大冷却液
砂轮主轴有轴向窜动
机床检修
头架主轴轴承间隙大
调整间隙
用卡盘磨削端面时,头架主轴轴承窜动大。
调整间隙
进刀太快,光磨时间不够
进刀要慢而均匀,光磨至没有火花为止
冷却液不充足
加大冷却液
3
工件表面出现直波形振痕
工件圆周速速过大,工件中心孔有多角.
适当降低工件转速,修正中心孔
工件直径,重量过大,不符合机床规则
改在规格较大的机床上磨削。如设备不允许,可降低磨削深度和纵向进给量以及把砂轮修得锋利点
砂轮主轴轴承磨损,配合间隙过大,产生径向跳动
按机床说明书规定调整轴承间隙
顶尖在主轴和尾架内贴合不紧,发生摇晃。
卸下顶尖,檫净后重新装上,
砂轮过钝
修正砂轮
冷却液不充分或供应不及时
保证充足的冷却液
工作刚性差而毛坯形状误差又大,磨削时因余量不均而引起磨削深度变化,使工件弹性变型发生相应变化,磨削后部分部分保留毛坯形状误差,
磨削深度不能太大。并应随着余量减小而逐步减小,最后多次几次光磨行程,
调整换向撞块位置,使砂轮超出工件端面1/3-1/2个砂轮宽度
工作台换向时停留时间太长或太短
调整时间
8
阶台旁外圆尺寸大
工作台换向时停留时间太短
延长停留时间
砂轮磨损,靠阶台旁外角变或母线不直
修正砂轮
9
阶台轴各外圆表面不同轴
磨削用量过大或光磨时间不够
精磨时减小磨削深度,多做光磨
M1432A型万能外圆磨床故障的排除
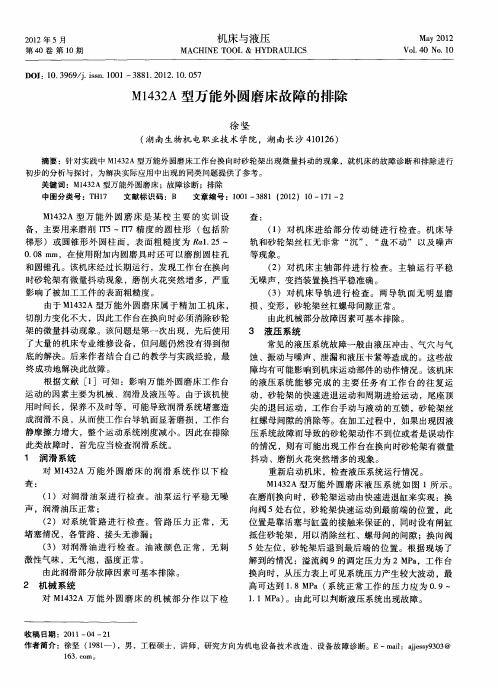
将会通过丝杠螺母使砂轮架产生微量抖动。 从分析结果来看 ,要想解决砂轮架在工作台换 向
时 出的现微量抖动 问题 ,关键就是减缓换 向过程 中主 油路 的油液对快速进退缸 的冲击 。首先 调整溢流 阀 9 的调定压力为 10M a . P ,同时在换 向阀 5的 回油路上 加装一个溢流阀起双向背压缓 冲作用 。 上 电使系统运行 ,故 障完全排 除。
床 与 液 压 ,0 83 ( )3 3 . 2 0 ,6 8 :7— 8
【】 4 李义梅. 如何用 G K90 S - T数控车床 系统加 工椭圆零件 8
[ ] 中国科技信 息 ,0 8 6 : 6 . J. 2 0 ( )5 9— 0
【 】 国经. 5 吴 数控机床故障诊断与维修 [ . M]北京 : 电子工业
【】 2 徐坚, 易竞. 基于 Y 44 T53液压系统故障的分析与探讨
[ ] 机床与液压 ,0 0 3 ( 2 :1 J. 2 1 ,8 1 ) 17—18 8 . 1 ,9 【】 3 徐坚 , 良冲. 于 C 64 数 控车 床故 障 的分 析 与探 廉 基 K 10
讨 [ ] 制造技术与机床 ,0 9 8 :2 —12 J. 20 ( ) 1 1 2 .
出版 社 , 0 4 2o.
( )对机床 进 给部分 传动 链进 行 检查 。机 床导 1
轨和砂轮架丝杠 无非常 “ ” “ 沉 、 盘不 动” 以及噪声 等现象 。
( )对 机床 主轴 部件 进行 检查 。主轴运 行 平稳 2 无噪声 ,变挡装置换挡平稳准确 。 ( )对 机床 导轨 进行 检查 。两 导轨 面无 明显磨 3 损 、变形 ,砂轮架丝杠螺母 间隙正常。 由此机械部分故障 因素可基本排除。
磨床常见故障分析与排除

磨床常见故障分析与排除—济南金鑫
1磨削工件的表面突然拉毛的痕迹
磨削工件的表面突然拉毛的痕迹主要由于粗粒砂轮磨粒脱落后夹在砂轮和工件之间形成的。
(1)粗磨时遗留下来的痕迹在精磨时未磨掉,
适当放大精磨余量。
(2)磨削液中有磨粒存在。
清楚砂轮罩壳内
的磨削,过滤或更换磨削液。
(3)材料韧性太大。
根据工件材料韧性的特
点,选择铬钢玉系列砂轮。
(4)粗粒度砂轮在刚修正好时,其磨粒易于
脱落。
降低工作台速度,尽量使砂轮修
整的细一些,并以较低的纵向速度进行
粗加工,或者改用粒度较细的砂轮。
(5)砂轮太软。
一般情况是材料硬,砂轮软;
材料软,砂轮硬。
但材料过软,亦应选
用较软的砂轮。
(6)砂轮未修整好,有突起的磨粒,重新修
整砂轮。
更多济南机械加工信息。
外圆磨床液压系统常见故障分析
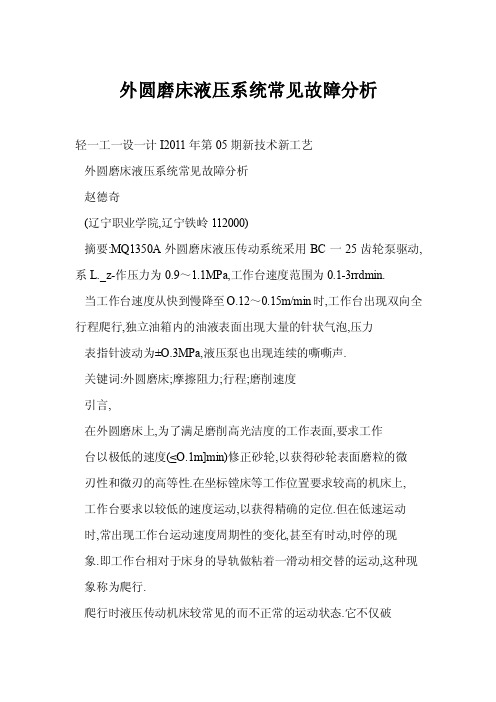
外圆磨床液压系统常见故障分析轻一工一设一计I2011年第05期新技术新工艺外圆磨床液压系统常见故障分析赵德奇(辽宁职业学院,辽宁铁岭112000)摘要:MQ1350A外圆磨床液压传动系统采用BC一25齿轮泵驱动,系L._z-作压力为0.9~1.1MPa,工作台速度范围为0.1-3rrdmin.当工作台速度从快到慢降至O.12~0.15m/min时,工作台出现双向全行程爬行,独立油箱内的油液表面出现大量的针状气泡,压力表指针波动为±O.3MPa,液压泵也出现连续的嘶嘶声.关键词:外圆磨床;摩擦阻力;行程;磨削速度引言,在外圆磨床上,为了满足磨削高光洁度的工作表面,要求工作台以极低的速度(≤O.1m]min)修正砂轮,以获得砂轮表面磨粒的微刃性和微刃的高等性.在坐标镗床等工作位置要求较高的机床上,工作台要求以较低的速度运动,以获得精确的定位.但在低速运动时,常出现工作台运动速度周期性的变化,甚至有时动,时停的现象.即工作台相对于床身的导轨做粘着一滑动相交替的运动,这种现象称为爬行.爬行时液压传动机床较常见的而不正常的运动状态.它不仅破坏液压系统工作的稳定性和精确定位,还使被加工表面质量恶化, 降低机床和道具的使用寿命,甚至被迫停机检修而影响生产.MQ1350A外圆磨床液压传动系采用Bc一25齿轮泵驱动,系统工作压力为0.9~I.1MPa,工作台速度范围为0.1-3m/rain.当工作台速度从快到慢降至0.12~0.15m/min时,工作台出现双向全行程爬行,独立油箱内的油液表面出现大量的针状气泡,压力表指针波动为--:0.3MPa,液压泵也出现连续的嘶嘶声.液压传动是以液压油(本机床采用20#液压油)作为工作介质,液体具有可压缩性,在受压后液体的容积缩小,密度增大,但在低压系统中可忽略不计,即认为液体是不可压缩的.若空气进入液压系统后,一部分溶解于压力油中,另一部分形成气泡浮游于压力油里. 由于空气的压缩性很大,使传动系统由”刚体”变成了”弹性体”;且工作台液压缸位于所有液压元件的最高处,空气极易积聚在这里. 因此,直接影响到工作台运动的平稳性.…值得注意的是:空气进人液压系统后会使油液变成乳化状,而外圆磨床磨削工件时是采用乳化液冷却的,若油水混合搅拌后也成乳化状,如何区别它们呢?方法有三:(1)观察.停泵1~2小时,如乳化状消失,即是空气进入液压系统.若仍然成乳化状,是冷却液混入油液中.(2)听.空气侵入液压系统后必然会发出嘶嘶声,且比较刺耳.而冷却液混入液压系统后发出的噪声较低沉.(3)若空气进入液压系统,手触及液压泵出油管时有”触电”的感觉(即高频振荡的缘故),而冷却液混入液压系统一般无此感觉.处理方法:(1)在制造和修配零件时,严格控制几何形状偏差和配合间隙.(2)紧固个接合面螺钉,各管道连接螺帽及管接头.(3)更换损坏或失效的密封件.(4)所有回油管道的出口插入油面以下.(5)补充油箱油液,使油位不低于油标线.(6)清洗滤油器(网).(7)试车时,先打开放气阀,后启动液压泵,使压力油互通液压缸左,右腔,然后置开停阀于”开”的位置,并操纵节流阀,使工作台由慢至快,由短行程至全行程往复运动5分钟,以排除液压系统中的空气(当转入正常磨削工作时应关闭放气阀).结果:液面针状气泡消失,压力表波动值减少.但双向全行程的爬行变成不规则的间断爬行.从现象判断是节流阀引起的,因为当工作台低速运动时,节流阀的通流面积较小,油中杂质及污物极易积聚在这里,液流速度,高引起发热,将油析出沥青等杂质粘附于节流口处,致使通过节流阀的流量减小;接着,因节流口压差增大,将杂质从口上冲走,使通过节流口的又流量增加.如此反复,致使工作台出现间歇性的跳跃.处理方法:(1)用6o℃的什锦锉仔细清除节流口粘附的杂质. (2)更换清洁的油液,防止油液污染.结果:工作台速度在≥0.5m/min,运动平稳.另有一台同型号的旧机床,工作台运动至液压缸行程两端出现局部爬行.对这种现象一般是因摩擦阻力发生变化而引起.当液压缸左腔进入液压油时,因液体缸刚体与工作台固联,工作台向左运38动.它之所以运动,必须克服作用在活塞上的总负载p(包括切削力在液压缸轴向的分力和法相分力;导轨的摩擦阻力;工作机构在启动时的惯性力;活塞与缸体内孔0型密封圈及液压缸两端支架中活塞杆与型密封圈的摩擦阻力;液压缸的背压力等).因磨削力较小,粗磨与精磨的磨削力变化亦较小工作台在低速运动时,惯性力变化很小;当工作台速度调定后,液压缸的背压基本不变,因此下面仅分析,的变化对爬行的影响.拆卸液压缸检查发现:(1)0型密封圈沟槽底径与活塞外圆同轴度约0.2mm(要求≤0.1mm),致使0型密封圈在圆周上的压缩量不等.密封圈压的过紧.(2)活塞与活塞杆同轴度约为0.1/100mm(要求≤O.4/1000mm).(3)由于使用年久,且经常磨削短工件,液压缸的缸体中间部分磨损较多,呈”腰鼓形”.活塞杆两端局部弯曲.装配质量不良,当用手拉退活塞杆移动时,行程终点处阻力较大,说明活塞与缸体孑L,活塞杆与两端支座三则同轴度差.(6)液压缸的上侧母线与导轨不平衡.处理方法:(1)以活塞外圆为基准,修整沟槽底径对外圆的同轴度要求.(2)更换新的0型密封圈,矫正活塞与活塞杆的同轴度要求.(3)镗磨缸体孔至要求.(4)组装时调整两支座与活塞的同轴度及适当放松密封圈的端盖螺钉.(5)重新以平导轨为基准修刮液压缸的安装底面(全长为0.1ram)以V型导轨为基准调整液压缸的侧母线至要求(0.1mm).结果:液压缸的行程两端的爬行消除.但当工作台负载(O.6O吨)移动时,仍有爬行现象.这说明导轨润滑不良,即工作台导轨与床身导轨接触不均匀,润滑油品质不好等.该机床采用静力润滑,它虽具有油膜刚性好,动,静摩擦系数接近,不易产生爬行等优点.但经检查发现油液污染严重,污物堵塞了润滑油调节器的节流口,润滑油几乎中断.同时,工作台导轨与床身导轨接触不均匀,特别是油腔封油边接触较差,因而润滑压力建立不起来,承载能力差.处理方法:(1)刮修导轨,使两者接触面I>75%,且均匀.(2)更换10#液压油.(3)清洗润滑油调节器.结果:在磨削速度范围内(0.4~lm/mm)运动平稳,但当工作台速度在0.2~0.3ndmm范围内时出现区域性爬行.该机床工作台与床身导轨均采用铸铁材料.实验表明,其摩擦系数虽运动速度的增加而下降,这种摩擦系数的降落特性对不同的油品是不一样的.一般说,当油的粘度较小,油膜强度较低,载荷大,速度低时,油膜容易被破坏.为了获得低速时速度平稳,可适当提高油的粘度(更换粘度较大的油液).但该机床润滑系统与主运动系统合用一油箱,且用同一液压泵供油,因此,工作油液的粘度不能太大.处理方法:更换20#精密机床导轨油.结果:工作台速度t>0.03m/min,运动平稳.参考文献【1]章红甲.金属且学机床液压传动『M].南京:江苏科学技术出版社,1984.[2】李壮云,葛宜远.液压元件与系统fM1.北京:机械工业出版社,2000. 【3】盛敬超.液压流体力学rM1.北京:机械工业出版社,1980.。
机床维修M1432

M1432B型万能外圆磨床一般故障的分析和排除磨床发生故障可归纳为如下四种情况:第一种情况:磨削加工件本身精度低,误差大;由于撞击、拉毛或其他外伤所致,使工件表面产生印痕。
第二种情况为磨床本身制造精度误差大第三种情况为磨床的零件磨损,机构配合松动或间隙过大以及零件损坏等第四种情况为液压系统的故障对于第一种情况,可在加工前对工件进行严格的检查,不符合精度要求的、或外伤所致表面质量未达到要求的工件,予以退回或退修。
下面分析和讨论其他几种情况:1、圆度超差1)磨床头架主轴轴承的磨损,磨削是,使主轴的径向圆跳动圆跳动超差。
可调整轴承游隙或更换新轴承。
2)尾座套筒磨损,配合间隙增大,磨削时在磨削力的作用下,使顶尖位移,工件回转使造成不理想的圆形。
可修复或更换尾座套筒。
2、圆柱度超差1)头架主轴中心与尾座套筒中心不等高或套筒中心在水平面内偏斜。
由于尾座经常沿上工作台表面移动而磨损所致。
可修复或更换尾座,使其与头架主轴中心线等高和同轴。
2)纵向导轨的不均匀磨损,而造成工作台直线度超差。
可修复导轨面,重新校整导轨的精度。
3、磨削时工件表面出现有规律性的直波纹(呈多角状)1)砂轮主轴与轴承、砂轮法兰盘相配合的轴颈磨损,使径向圆跳动和全跳动超差是,可修复或调换主轴。
2)砂轮主轴轴承的磨损,配合间隙过大,使砂轮回转不平衡时,将使磨削产生振动,可调整或更换轴承。
3)砂轮主轴的电动机轴承磨损后,磨削时电动机产生振动,可调换轴承。
4、磨削时工件表面产生有规律的螺旋波纹1)工作台低速爬行,可消除进入液压系统中的空气,疏通滤油器,稳定液压系统中的油压,以及修整导轨表面使其减少摩擦。
2)砂轮主轴的轴向窜动可调整轴承的轴向游隙或更换轴承。
3)砂轮主轴轴心线与工作台导轨不平行可修复导轨使其达到达到精度要求。
5、磨削时工件表面产生无规律的波纹或振痕1)所选砂轮硬度、顆粒不恰当,可选择合适的砂轮。
2)砂轮修整不正确、不及时,可及时地、正确地修整砂轮。
外圆磨床的维修
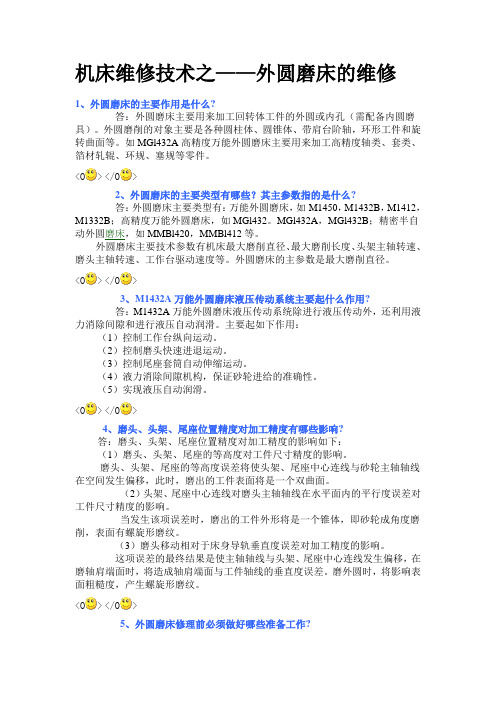
机床维修技术之——外圆磨床的维修1、外圆磨床的主要作用是什么?答:外圆磨床主要用来加工回转体工件的外圆或内孔(需配备内圆磨具)。
外圆磨削的对象主要是各种圆柱体、圆锥体、带肩台阶轴,环形工件和旋转曲面等。
如MGl432A高精度万能外圆磨床主要用来加工高精度轴类、套类、箔材轧辊、环规、塞规等零件。
<O></O>2、外圆磨床的主要类型有哪些?其主参数指的是什么?答:外圆磨床主要类型有:万能外圆磨床,如M1450,M1432B,M1412,M1332B;高精度万能外圆磨床,如MGl432。
MGl432A,MGl432B;精密半自动外圆磨床,如MMBl420,MMBl412等。
外圆磨床主要技术参数有机床最大磨削直径、最大磨削长度、头架主轴转速、磨头主轴转速、工作台驱动速度等。
外圆磨床的主参数是最大磨削直径。
<O></O>3、M1432A万能外圆磨床液压传动系统主要起什么作用?答:M1432A万能外圆磨床液压传动系统除进行液压传动外,还利用液力消除间隙和进行液压自动润滑。
主要起如下作用:(1)控制工作台纵向运动。
(2)控制磨头快速进退运动。
(3)控制尾座套筒自动伸缩运动。
(4)液力消除间隙机构,保证砂轮进给的准确性。
(5)实现液压自动润滑。
<O></O>4、磨头、头架、尾座位置精度对加工精度有哪些影响?答:磨头、头架、尾座位置精度对加工精度的影响如下:(1)磨头、头架、尾座的等高度对工件尺寸精度的影响。
磨头、头架、尾座的等高度误差将使头架、尾座中心连线与砂轮主轴轴线在空间发生偏移,此时,磨出的工件表面将是一个双曲面。
(2)头架、尾座中心连线对磨头主轴轴线在水平面内的平行度误差对工件尺寸精度的影响。
当发生该项误差时,磨出的工件外形将是一个锥体,即砂轮成角度磨削,表面有螺旋形磨纹。
(3)磨头移动相对于床身导轨垂直度误差对加工精度的影响。
这项误差的最终结果是使主轴轴线与头架、尾座中心连线发生偏移,在磨轴肩端面时,将造成轴肩端面与工件轴线的垂直度误差。
外圆磨床出现振动波纹的原因及解决措施

过 学习振 动检测,开阔思路和分析 ,运用设备诊 断技术和方法 ,对 此 问题 进 行分 析 ,找 到 了 引起 原 因所 在 , 并 将其 一 一 列 出 。 1外圆磨床 出现振动波纹的原因如下 : 1 . 1 电机运行产生的振 动。 可 能 引 起 异 常 振 动 的 典 型 问题 有 :( 1 )转 子 弯 曲 。 ( 2 ) 转 子偏 心。( 3 )电机地脚螺栓 出现松动及基础底板振动 。( 4 )电机 风扇罩 螺栓松动。 1 . 2皮带轮方面产生的振动主要有: ( 1 )皮 带 轮 孔 与 电机 轴 配 合 失 效 引起 的 振 动 。 ( 2 )皮 带 轮 偏 心 引 起 的 振 动 。 ( 3 )主 动 轮 和 从 动 轮 不 对 中引 起 的振 动 ( 4 )皮 带 轮 槽 破 碎 引起 的 振 动 。 1 . 3 传 动 皮带 引起 的振 动 : ( 1 )皮 带 破 损 ,断 裂 引起 的振 动 。 ( 2 )皮带松弛张力不等 引起 的振动 。 ( 3 )不 匹配 的皮 带 或 负 载 过 大 引起 的振 动 。 1 . 4 砂 轮 转子 系 统 引起 的振 动 。 产 生振 动 的主 要 因素 是 转 子 的 不平 衡 和 转 子 轴 弯 曲 。 1 . 5 滑 动 轴承 方 面 引起 的振 动 : ( 1 )轴 与轴 瓦间隙过大 引起 的振动 能使轴在轴承 中心 位置变 化 ,产 生 不 对 中 ,相 当 小 的不 平 衡 不 对 中造 成 机 构 松 动 或 摆 动 。
螺 钉 紧 固 ,这 时 定 心套 应 转 动 自如 。 ( 4 ) 抽 出 定 心 套 调整 另 一块 轴 瓦 , 保 证 主 轴轴 承 间 隙在 0 . 0 l 5 ~
接触面积 大于或 等于 8 0 % 。
3 . 2 . 1 珩 磨 轴 瓦 把 珩 磨 轴 装 夹 在 车 床 上 ,轴 瓦合 在 旋 转 的 珩 磨 轴 外 圆 上 ,用 手
外圆磨床常见故障排除

修正砂轮
冷却液不充分或供应不及时
保证充足的冷却液
工作刚性差而毛坯形状误差又大,磨削时因余量不均而引起磨削深度变化,使工件弹性变型发生相应变化,磨削后部分部分保留毛坯形状误差,
磨削深度不能太大;并应随着余量减小而逐步减小,最后多次几次光磨行程,
工作有不平衡重量时,由于离心力作用,会在重的那边磨去较多金属,使工件有椭圆度;
用卡盘装夹磨削时,工件找正不对,或头架主轴径向跳动大
仔细找正工件基准面
10
阶台端面内部凸起
吃刀过大,退刀过块
吃刀时纵向摇动工作台要慢而且均匀,光磨时间要充分
冷却液不充分
加大冷却液
砂轮主轴有轴向窜动
机床检修
头架主轴轴承间隙大
调整间隙
用卡盘磨削端面时,头架主轴轴承窜动大;
调整间隙
进刀太快,光磨时间不够
进刀要慢而均匀,光磨至没有火花为止
外圆磨常见故障排除
1
工件有螺旋形痕迹
砂轮硬度高,修得过细,磨削深度过大;
合理选择砂轮硬度和修正用量,适当减小磨削深度
纵向进给量过大
适当降低进给量
砂轮磨损,母线不直
修正砂轮
金刚石在修正器中未夹紧或金刚石在刀杆未焊牢,修出砂轮凹凸不平;
把金刚石装夹牢固,如金刚石有松动,需重新焊接
冷却液太少或太淡
加大或加入浓冷却液
冷却液不充足
加大冷却液
3
工件表面出现直波形振痕
工件圆周速速过大,工件中心孔有多角.
适当降低工件转速,修正中心孔
工件直径,重量过大,不符合机床规则
改在规格较大的机床上磨削;如设备不允许,可降低磨削深度和纵向进给量以及把砂轮修得锋利点
砂轮主轴轴承磨损,配合间隙过大,产生径向跳动
外圆磨床出现振动波纹的原因及解决措施
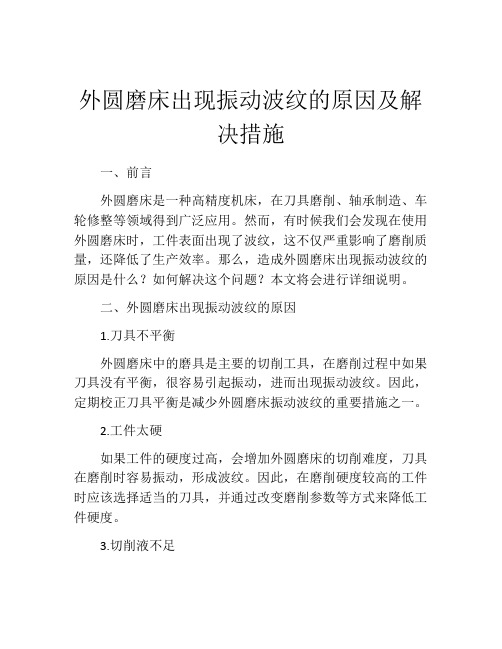
外圆磨床出现振动波纹的原因及解决措施一、前言外圆磨床是一种高精度机床,在刀具磨削、轴承制造、车轮修整等领域得到广泛应用。
然而,有时候我们会发现在使用外圆磨床时,工件表面出现了波纹,这不仅严重影响了磨削质量,还降低了生产效率。
那么,造成外圆磨床出现振动波纹的原因是什么?如何解决这个问题?本文将会进行详细说明。
二、外圆磨床出现振动波纹的原因1.刀具不平衡外圆磨床中的磨具是主要的切削工具,在磨削过程中如果刀具没有平衡,很容易引起振动,进而出现振动波纹。
因此,定期校正刀具平衡是减少外圆磨床振动波纹的重要措施之一。
2.工件太硬如果工件的硬度过高,会增加外圆磨床的切削难度,刀具在磨削时容易振动,形成波纹。
因此,在磨削硬度较高的工件时应该选择适当的刀具,并通过改变磨削参数等方式来降低工件硬度。
3.切削液不足在外圆磨削过程中,尤其是在高速磨削时,需要向磨具和工件表面喷洒足够的切削液,以降低磨削温度、降低切削力和摩擦系数,防止出现振动波纹。
4.机床不平衡如果外圆磨床的主轴不平衡,或者是磨床的机身本身不平衡等机床问题也会导致振动波纹的出现。
因此,在使用外圆磨床前应该经常检查机床的状况,以保证其正常运行。
三、如何解决外圆磨床出现振动波纹的问题1.定期校正刀具平衡刀具平衡问题是导致外圆磨床振动波纹的主要因素之一。
定期检查和校正刀具平衡可以有效地降低振动波纹的出现。
2.提高磨削精度提高磨削精度也可以有效地减少外圆磨床振动波纹的出现。
这可以通过调整磨削参数、优化刀具设计或使用更先进的磨削工艺来实现。
3.提高工件表面质量工件表面质量的提高可以减少外圆磨床振动波纹的出现。
这可以通过更好的工件设计、控制加工过程、优化加工方案等方式来实现。
4.维护和保养机床设备外圆磨床的机床设备需要经常进行维护和保养,确保设备的正常运行。
检查机床主轴是否平衡、检查运动部件是否正常、清洁机床设备等措施都可以有效地减少振动波纹的出现。
四、总结外圆磨床振动波纹的出现会直接影响外圆磨削质量和生产效率,在使用外圆磨床的过程中需要注意磨削参数的选择、刀具平衡、工件表面质量、切削液的使用等因素,通过科学的管理和维护,减少振动波纹的出现,提高外圆磨削质量和生产效率。
磨床常见问题及解决方案

椭圆度
主轴间隙过大、金刚笔磨损、砂轮修整不均匀、磨削速度太快、磨削参数设置不当等
调整主轴间隙、更换金刚笔、合理调整磨削速度、变更磨削参数等
垂直度
定位环不平,工作台出现故障、磨削速度过快等。
定位环从新打平、维修工作台、调整磨削速度。
震纹
金刚笔磨损、往复速度不当、砂轮转速不当、冷却液浇注不均匀、进给速度太快等
编制
会签
审核
批准
更换金刚笔、调整往复速度、调整砂轮转速、让冷却液浇注充分、调整进给速度。
粗糙转速设置不合理等
更换金刚笔、合理调整磨削速度、工件转速与砂轮转速比例适当。
螺旋纹
金刚笔磨损、往复速度不合理等
更换金刚笔、调整往复速度。
3常见问题、原因及解决方案
以上问题是磨加工当中经常会出现的问题,在使用磨床进行生产加工是如遇到上述问题,操作者可对照此表分析、解决。
1目的
对磨加工常见质量问题及所产生的原因进行汇总、罗列,使操作者在操作磨床进行生产出现异常质量问题时,能及时的分析及做出相应的处理,保证生产加工的稳定性与产品质量的稳定性。
2范围
本方案适用于磨加工出现一般质量问题的参考、分析及解决。
常见问题
原因
解决方案
锥度
导轨不正、金刚笔磨损、砂轮修整不均匀、磨削参数设置不当等
磨床的常见故障与排除
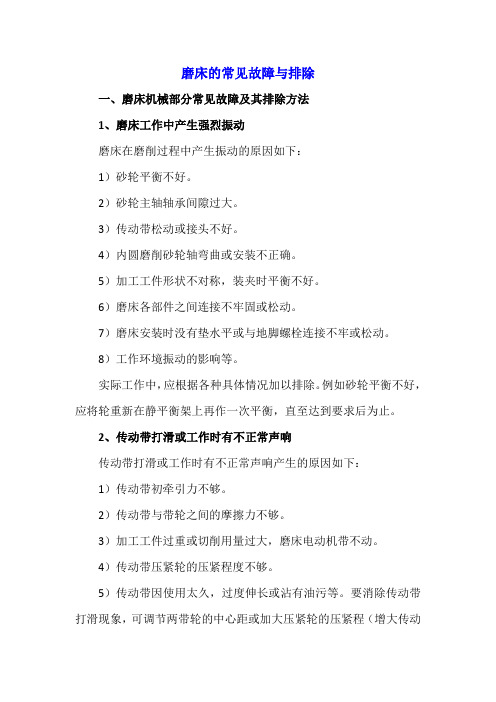
磨床的常见故障与排除一、磨床机械部分常见故障及其排除方法1、磨床工作中产生强烈振动磨床在磨削过程中产生振动的原因如下:1)砂轮平衡不好。
2)砂轮主轴轴承间隙过大。
3)传动带松动或接头不好。
4)内圆磨削砂轮轴弯曲或安装不正确。
5)加工工件形状不对称,装夹时平衡不好。
6)磨床各部件之间连接不牢固或松动。
7)磨床安装时没有垫水平或与地脚螺栓连接不牢或松动。
8)工作环境振动的影响等。
实际工作中,应根据各种具体情况加以排除。
例如砂轮平衡不好,应将轮重新在静平衡架上再作一次平衡,直至达到要求后为止。
2、传动带打滑或工作时有不正常声响传动带打滑或工作时有不正常声响产生的原因如下:1)传动带初牵引力不够。
2)传动带与带轮之间的摩擦力不够。
3)加工工件过重或切削用量过大,磨床电动机带不动。
4)传动带压紧轮的压紧程度不够。
5)传动带因使用太久,过度伸长或沾有油污等。
要消除传动带打滑现象,可调节两带轮的中心距或加大压紧轮的压紧程(增大传动带对压紧轮包角),若调整后,传动带牵引力仍有少许不够时,可用香粉涂于传动带与带轮接触的那一面,以增大其摩擦力。
当传动带为牛皮带即带革时,不可以使用松香粉,以防止传动带折断。
3、砂轮主轴出现过热现象砂轮主轴出现过热现象的原因如下:1)砂轮主轴与轴承之间的间隙过小。
2)轴承与轴瓦间有灰尘、脏物。
3)轴承与轴瓦间摩擦表面欠光滑。
4)润滑油不足或润滑油粘度过大。
砂轮主轴出现过热时,应立即停车检查。
先检查润滑系统的工作是否能保轴承获得充分润滑,若是轴承与轴瓦间有脏物侵入,可以进行清洗。
若是轴承轴瓦间摩擦表面欠光滑,则需要刮削轴瓦工作面等。
4、磨床工作台相对于床身导轨产生偏斜这是由于床身导轨磨损严重而产生的,应当修刮磨床导轨。
5、磨床横向进给机构的进给不准确这种故障的发生,主要是横向进给丝杠与半螺母之间的间隙不准确,也可是刻度盘在手轮上有游动间隙或半螺母在砂轮架上固定不牢等原因。
可通过更磨损的半螺母或调整半螺母与丝杠的压力,消除刻度盘在手轮上的游动间隙及半螺母在砂轮架上紧固好等相应措施,横向进给不准的故障就可排除。
磨床液压系统常见故障及排除方法

磨床液压系统常见故障及排出方法磨床液压系统常见故障及排出方法平面磨床液压系统常见的故障有:1.液压系统工作时有曝声、杂音其产生原因及排出方法见表。
故障现象故障产生的原因排出方法油泵吸空1.油泵吸油口密封不严,吸油管路漏气2.油箱中油液不足,吸油管浸入油面太浅3.油泵吸油高度太高4.暖油管直径太小5.过滤器被杂交、污物堵塞,吸油不畅1.用灌油法检查,将漏气接头拧紧2.油箱加油至油标线,吸油管浸入油面以下200cm3.油泵吸油高度调整小于500mm4.适当放大吸油管直径5.漕洗过滤器油泵故障1.齿轮泵的齿形精度差2.油泵有困油现象3.油泵内某些零件损坏或精度不良,引起机械振动4.油泵的轴向间隙增大或轴向端面咬毛1.更换齿轮2.修整困油槽3.更换或繁复损坏与精度不良的零件,如轴承等4.更换零件—使搭配f嘲索符合要求溢流阀失灵1.调压弹簧变形、扭曲或端面不平2.阀座损坏,密封不良3.滑阀与阀体孔搭配间隙过大4.油液不清洁。
阻尼小孔被堵1.更换调压弹簧2.研磨阀座,更换阀座或修理锥阀3.置研磨阀阀孔,更换滑阀重新配间隙4.清洗、换油,疏通阻尼孔机械振动1.油管过长且没有固定好,造成油管抖动2.油管相互撞击3.油泵和电动机安装不同轴或联袖器松动1.加添支承管夹2.管道之间保持确定距离3.调整同轴度,更换联轴器系统中含有空气1.停车一段时间后,空气浸入系统2.回油管、油泵吸油管位置过近而弓f起油气泡1.用放气阀排气或全行程多次排气2.回油管授入油池并阔别油泵吸油口2.工作台面运动时爬行工作台面运动时显现爬行现象是液压传动机床中常见的不正常运动状态,这紧要是由于磨床工作台低速度运动时,润滑油膜变薄或部分油膜破坏,使摩擦面问的摩擦阻力加大造成的。
产生这种现象的紧要原因是液压系统内存有空气,其次是溢流阀、节流阀等的阻尼孔和节流口被污物堵塞,滑阀移动不灵括,造成工作压力波动大丽引起爬行。
为此,磨削前先空载运行一下,待液压系统中的空气排净后才开始工作,修复导轨精度及接受防爬导轨润滑油等。
磨床常见故障及处理方法【技巧】

磨床在使用和维修过程中遇到的故障是多种多样的,不同的液压传动磨床由于液压系统之组合元件不同,其故障现象不同,即使是同型号磨床故障也各不相同。
系统中产生的故障,有的是某一液压元件失灵而引起;有的是液压系统中各液压元件综合性因素所造成;同时,机械、电器以及外界因素也会引起液压系统出现故障。
其中有些故障用调整方法即可解决,而有些故障则因使用年久,精度超差需经修复才能恢复其性能,也有些故障则是因为原始结构不良或因先天性潜在隐患所造成。
因此,液压系统各种故障的排除,需要具体问题具体分析,区别对待。
下面介绍在磨床修理中遇到的5种比较特殊的疑难故障,并对每种故障做了分析并详细介绍了故障排除方法。
1 卧轴矩台平面磨床磨头液动换向迟缓,有时不换向M7130型磨床磨头进给部分液压原理图如图1所示,但四川磨床厂、哈尔滨第一机床厂等制造厂的随机说明书中液压原理图上均未示出节流阀J。
而此节流阀在操纵箱实际结构中是存在的,只是隐藏于箱体内部,极不容易发现。
节流阀J在操纵箱中的安装位置如图2所示。
它的实际作用是,当先导阀受换向挡块作用或手动换向动作后,控制换向阀的压力油经先导阀进入换向阀一腔,换向阀另一腔的回油必须经节流阀J回至背压阀回油路回油,节流阀J的开口尺寸直接影响换向阀的换向时间,若堵塞则不能换向。
图2主视图为磨头操纵箱的外形图,排故时卸下堵头K,找到深孔底部缓冲节流螺钉,螺钉带有φ2 mm通孔,原制造厂曾用描图纸虚堵在φ2 mm孔中,随着机床使用时间的增长,小孔和描图纸上油污会越积越多,逐渐使φ2 mm小孔通流面积不稳定地变化,甚至时通时断,就导致上述磨头液动换向故障。
排除故障时卸下堵头K,拧出节流螺钉J,清洗疏通φ2 mm小孔即可。
2 平面磨床磨头进刀不均匀:平面磨床磨头进刀不均匀性按照出厂验收技术要求,只要不超过25%即为正常,在一般情况下排除进刀不均匀性故障并不困难,只要正确地调整进给分配阀的两面二端的节流螺钉即可,但是从我们对M7120A平面磨床大修和日常排故中遇到的不均匀故障来看,实际情况要复杂得多。
外圆磨床常见的故障及解决方法
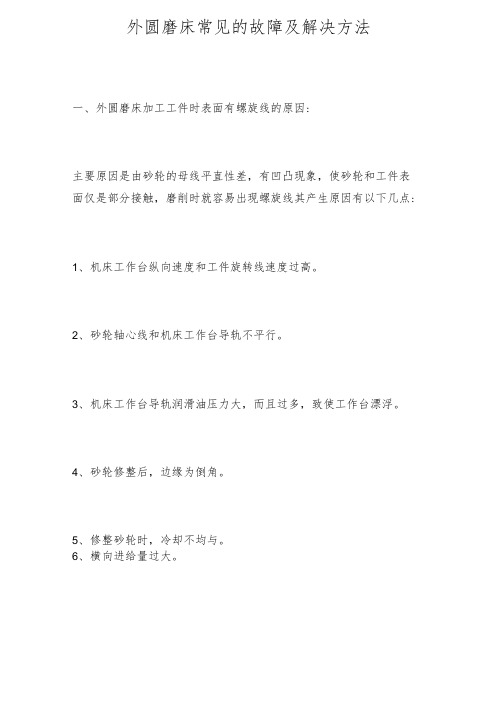
外圆磨床常见的故障及解决方法一、外圆磨床加工工件时表面有螺旋线的原因:主要原因是由砂轮的母线平直性差,有凹凸现象,使砂轮和工件表面仅是部分接触,磨削时就容易出现螺旋线其产生原因有以下几点:1、机床工作台纵向速度和工件旋转线速度过高。
2、砂轮轴心线和机床工作台导轨不平行。
3、机床工作台导轨润滑油压力大,而且过多,致使工作台漂浮。
4、砂轮修整后,边缘为倒角。
5、修整砂轮时,冷却不均与。
6、横向进给量过大。
7、砂轮修整不良。
8、尾架套筒与锥度配合不良。
9、机床工作台移动时有爬行。
二、引起外圆磨床加工工件表面有波纹的原因:1、砂轮静平衡差。
2、砂轮硬度过高或砂轮粘度不均,砂轮变钝,与工件摩擦力增大,使工件周期性振动增大。
3、砂轮主轴瓦磨损,配合间隙大主轴在旋转中有漂浮,使砂轮产生不平衡,产生振动。
4、砂轮法兰盘锥孔与砂轮主轴锥端配合接触不良,磨削时引起砂轮跳动。
5、砂轮架电动机振动,传动皮带过紧、松或长短不一致产生振动。
6、砂轮架电动机平衡差。
7、工件中心孔与接触不良。
8、工件顶的不合适,过紧使工件旋转不均匀,过松使系统刚性降低。
三、外圆磨床加工工件时工件表面有突然拉毛痕迹的原因:主要是由于粗粒度砂轮磨粒脱落,夹在砂轮和工件之间形成的1、粗磨时遗留下来的痕迹在精磨时未磨去。
2、冷却液中有磨粒存在。
3、材料韧性太大。
4、粗粒度砂轮在刚修整好时磨粒脱落。
5、砂轮太软。
6、砂轮未修整好,有凸起的磨粒,在磨削中磨粒破碎或脱落。
四、外圆磨床加工工件时工件表面有细拉毛痕迹:主要原因是细粒度砂轮磨粒破碎或脱落在砂轮和工件之间形成的1、砂轮太软。
3、冷却液不清洁,导致冷却液中碎粒或脱离的细磨粒嵌挤在砂轮和工件之间滚转而造成。
五、外圆磨床加工工件圆柱度差产生鼓形或鞍形的原因1、机床安装水平产生变动。
2、工件刚性差,磨削时产生让刀。
3、中心架调整不到位。
4、磨细长轴时顶的太紧,工件弯曲变形。
5、砂轮表面不锋利。
六、外圆磨床加工工件时工件表面有烧伤的主要原因:1、砂轮过钝。
外圆磨床磨削圆跳动超差的原因分析及维修

第5期(总第216期)2019年10月机械工程与自动化M E C HA N I C A L ㊀E N G I N E E R I N G㊀&㊀A U T OMA T I O NN o .5O c t .文章编号:1672G6413(2019)05G0174G02外圆磨床磨削圆跳动超差的原因分析及维修谭东升(太原重工轨道交通设备有限公司,山西㊀太原㊀030032)摘要:针对D A N O B A T 数控外圆磨床磨削过程中外圆表面跳动超差的问题,通过对磨削过程的现象和机床内部结构的分析㊁检查,对其进行了故障诊断和维修.在拆装和维修过程中,了解了主轴的机械结构㊁工作原理及轴承装配要求,为今后使用和维护设备提供了宝贵的资料.关键词:跳动超差;轴承装配;外圆磨床;磨削中图分类号:T G 581+1㊀㊀㊀文献标识码:A收稿日期:2019G05G24;修订日期:2019G08G03作者简介:谭东升(1990G),男,甘肃兰州人,助理工程师,本科,主要从事机械设备管理和维护工作.1㊀问题提出某公司有一台西班牙D A N O B A T 数控外圆磨床,型号为H G G91G3000G2A 2R ,带3轴数控倾角砂轮头架,西门子840DS L 控制.其主要结构特点是:①采用带静压轴承的双砂轮主轴;②主轴头架为装有活顶尖的带高精度角度滚柱轴承的主轴;③尾座为自动润滑套筒液压驱动,装有死顶尖.磨削某铁路车轴产品,外圆表面磨削尺寸要求184.15ʃ0.025m m ,圆柱度公差要求不大于0.02m m ,两径向圆跳动公差不大于0.015m m .外圆磨床按工艺要求进行磨削,检验外圆表面圆跳动公差值规律变化,最大处0.05m m ,不满足图纸要求.通过观察发现:在砂轮与工件刚接触且轴向和径向均不进刀的情况下火花时有时无;其次,磨削车轴不同部位,尤其是靠近头架方向上跳动加剧.2㊀故障原因分析2.1㊀初步分析和检测对磨削过程进行分析,考虑主要原因可能为:①车轴顶尖孔加工精度超差;②设计为均布三拨叉结构的拨盘,操作工只使用双拨叉而导致工件旋转摆动;③工件头架主轴前㊁后轴承间隙较大,运转过程中存在有不规律的径向跳动.对以上的故障原因进行检测和判断:①车轴重新修正顶尖孔后,磨削结果依然存在圆跳动超差现象;②恢复拨盘120ʎ分布的三拨叉结构,工件磨削精度稍有改善,可确定拨叉分布对加工精度有影响但不是主因;③拆除头架主轴拨盘装置,在夹持工件状态下检测头架主轴顶尖径向跳动,千分表指针规律变化,顶尖锥端和锥尾最大跳动值分别为0.015m m 和0.010m m ,拆除顶尖后,检测头架主轴的外锥面㊁内锥面的径向跳动及前端面旋转轴向跳动分别为0.010m m ㊁0.008m m ㊁0.007m m ,皆超出设备精度允差.综上可初步判定,头架主轴的跳动是造成磨削外圆面跳动超差的主要原因.2.2㊀头架主轴结构分析从头架主轴结构(见图1)来看,主要包括前端回转密封环㊁轴承前端盖(加防尘圈)㊁轴承后端盖(加防尘圈)㊁主轴旋转芯轴.其头架主轴旋转芯轴轴承采用英国G AM E T 超精密轴承的典型结构:前轴承为双列H 型结构(见图2(a)),其外环是一个加大宽度的外圈带法兰边的整体,作轴向定位,两轴承内环孔径和外环直径尺寸不一致,后内环孔径比前内环孔径大几微米,后外环直径比前外环直径小几微米,其作用主要是利用后内环受热膨胀的轴向移动量来调整轴承前㊁后环与外环滚道的工作状态,故轴承装配时与箱体孔的配合采用间隙配合,以便于轴承前㊁后支承中心的自动调准,也有利于轴承的装配和拆卸;用作后支承的为P型单列轴承(见图2(b)),外环前部环体内可安装最多24只小弹簧,通过对称地增加和减少弹簧的数量,能方便地改变轴承组预加负荷的大小,其轴承外环与箱体孔的配合亦采用间隙配合方式[1].图1㊀头架主轴结构图2㊀G AM E T 轴承结构示意图通过对主轴结构和轴承结构的分析可知,主轴旋转精度的好坏,关键在于H 型双列轴承轴向游隙的取值和P 型轴承预加载荷量的大小.G A M E T 轴承组结构中,预加载荷是通过主轴装入头架壳体后调整后轴承的弹簧预紧载荷,从而使前㊁后轴承同时预紧.前H 型轴承装配时,为使轴承处于最佳工作状态,预加载荷为零,且内环和外环之间预留有一定的轴向游隙.此值大小视主轴的最高转速值而定.最高转速值越高,预留轴向游隙值越大[2].在头架主轴(D A N O B A T 主轴转速为1r /m i n ~300r /m i n ,工作常用转速为20r /m i n~50r /m i n ,轴向游隙为0.002m m )中轴承的轴向游隙是通过在两内环(B 内环为后内环,A 内环为前内环)之间增加隔垫C 来保证(如图3所示).轴承使用一段时间后,可适当减少隔垫C 的厚度,对前轴承本身进行预紧,以调整因磨损而增加的轴向游隙量.P 型轴承是利用弹簧作轴向调整,使前㊁后轴承同时预紧.因此,弹簧的轴向压缩量决定了轴承预加载荷的大小.只要能准确地测量㊁计算出预载弹簧的轴向压缩量,便可知轴承的预加载荷.测量计算方法如下:根据测算出的弹簧与外环端面的高度差值H ,对后轴承进行轴向加载.加载时要缓慢进行,并且分载荷或档次随时测量并记录高度变化值ΔH 和加载力F的大小(见图4),这样就得到了轴承的预加载荷与弹簧压缩量对照表.在装配时,按照需要的载荷调整轴承弹簧的压缩量,就能得到对应的预加载荷.图3㊀H 型轴承装配示意图图4㊀P 型轴承载荷测算2.3㊀原因判定根据以上分析,解体头架主轴检查(注意严禁敲击,须做专用工装拆解)发现:①前端壳体底部排水槽被磨泥堵塞;②回转密封内表面有磨损;③轴承润滑脂污染失效,轴承滚道和滚子磨损.由此可判定故障的主要原因是:前端壳体内的排水孔被日常使用过程中磨削所带入主轴的磨泥堵塞,以致冷却液和磨泥排出受阻而进入轴承,致使轴承损伤,轴向游隙增大,最终导致头架主轴的内㊁外锥面的径向跳动及前端面旋转轴向跳动超差.3㊀解决问题(1)安装前准备.用煤油彻底清洗头架主轴㊁箱体内孔以及主轴附属零部件,用百洁布抛光冷却液锈蚀点,表面涂一层防锈油.(2)轴承装配和调整.G AM E T 双列H 型轴承的内㊁外环端面上标有不同字母,用来保证轴承准确地安装在主轴上.其主轴转速较低,采用油脂润滑,使轴承内圈感应加热至60ħ就可满足安装需求.装配时,把标有字母 A 的轴承内环感应加热至60ħ,滑装在主轴上,然后装上隔圈,再把轴承外环(法兰边朝向推入方向)推入.接着,用同样办法将标有字母 B 的内环感应加热到50ħ,然后滑装到主轴上.完成上述装配工作后,用锁紧丝圈将内环与隔圈压紧(锁紧丝圈时需使用专用钩型扳手,严禁敲击),压紧的同时应轻轻转动轴承外环.最后,添加润滑脂.但必须注意油脂不应封堵所有轴承空间(最多占1/2空间),以免过度发热和过多渗出外部.前轴承装配完毕后,将后轴承外环装入头架箱体后孔.装后轴承外环时,应注意12只预紧弹簧需均布,箱体孔内轴承弹簧垫圈与轴承外环端面的间隙均匀.上述工作完成后,将头架箱体倒立㊁架空,将主轴从上往下垂直装入箱体(由于采用间隙配合,调正后主轴靠自重滑入箱体).最后,将后轴承内环感应加热到40ħ后从底部滑装到主轴上.用锁紧丝圈把内环锁入至预紧弹簧刚受力,锁紧的同时应轻轻转动主轴,以防主轴不正,滚子大端面卡死,导致整个轴承损坏.翻转头架箱体至水平状态,按照测定的P 型预加载荷与弹簧压缩量对照表,用专用钩型扳手锁紧丝圈至选取的预紧载荷位置,锁紧的同时轻轻转动主轴.(3)轴承跑合试验.G A M E T 轴承采用脂润滑时,必须进行空运转,以使配合面磨合(滚道㊁滚子表面)到最佳配合状态,既保证润滑脂的均匀分布,又检查调整不适当的配合,防止过热损坏轴承的事件发生.理想的跑合方法是在加载轴向力(一般在其1/3轴向载荷)和在轴承最大允许转速的1/10条件下分别进行正反向定时运转,然后改变轴向负荷的方向,再重复上述旋转.由于主轴转速限制,跑合方式采用另一种方式进行:总装后,先以1/10最高转速运行10h,停机,冷到自然状态,再提高一倍(1/5最高转速),再运行10h.(4)轴承配合安装完毕后,检测头架主轴的外锥面㊁内锥面的径向跳动及前端面旋转轴向跳动分别为0.004m m ㊁0.003m m ㊁0.004m m ,恢复到设备精度允差值.试加工工件,加工后产品表面质量满足要求.4㊀结语经过这次问题分析及维修,不仅了解了头架主轴的机械结构㊁工作原理及轴承装配要求,也从中发现了引起该故障的主要原因在于设备日常维护不到位.因此,像此类在设备说明书中未提及的维护部位,在设备投产及使用过程中,技术人员应详细了解设备结构和工作原理,尽可能地发现这类看似很简单却对设备精度乃至整体寿命有巨大影响的部位,做好日常维护和检修工作.参考文献:[1]㊀佚名.使你的机器达到世界等级的G a m e t 超高精度轴承[J ].机电信息,2001(9):94.[2]㊀张宏渊.G AM E T轴承及其在卧式坐标镗床上的应用[J ].装备机械,1986(1):34G37,18.C a u s eA n a l y s i s a n dM a i n t e n a n c e o fO u t o fT o l e r a n c e o fG r i n d i n g Ci r c l e R u n GO u t o fE x t e r n a l C y l i n d r i c a lG r i n d i n g Ma c h i n e T A ND o n g Gs h e n g(T a i y u a nH e a v y I n d u s t r y R a i l w a y T r a n s i tE q u i p m e n tC o .,L t d ,T a i yu a n030032,C h i n a )A b s t r a c t :I n v i e wo f t h e p r o b l e mt h a t t h e o u t e r s u r f a c e r u n Go u t o f t h eD A N O B A T C N Cc y l i n d r i c a l g r i n d i n g ma c h i n e i s o u t o f t o l e r a n c e ,t h e f a u l t d i a g n o s i s a n dm a i n t e n a n c e a r e c a r r i e d o u tb y a n a l y z i n g a n dc h e c k i n g t h e p h e n o m e n o n o f t h e g r i nd i n g pr o c e s s a n d t h e i n t e r n a l s t r u c t u r e o f t h em a c h i n e .D u r i n g t h e d i s a s s e m b l y a n d r e p a i r p r o c e s s ,t h em e c h a n i c a l s t r u c t u r e ,w o r k i n gp r i n c i p l e a n db e a r i n g a s s e m b l y r e qu i r e m e n t s o f t h e s p i n d l ew e r e u n d e r s t o o d ,w h i c h p r o v i d e d v a l u a b l e i n f o r m a t i o n f o r t h e f u t u r e u s e a n dm a i n t e n a n c e o f t h e e q u i pm e n t .K e y wo r d s :r u n Go u t o u t o f t o l e r a n c e ;b e a r i n g a s s e m b l y ;e x t e r n a l c y l i n d r i c a l g r i n d i n g m a c h i n e ;g r i n d i n g571 ㊀2019年第5期㊀㊀㊀㊀㊀㊀㊀㊀㊀谭东升:外圆磨床磨削圆跳动超差的原因分析及维修。
- 1、下载文档前请自行甄别文档内容的完整性,平台不提供额外的编辑、内容补充、找答案等附加服务。
- 2、"仅部分预览"的文档,不可在线预览部分如存在完整性等问题,可反馈申请退款(可完整预览的文档不适用该条件!)。
- 3、如文档侵犯您的权益,请联系客服反馈,我们会尽快为您处理(人工客服工作时间:9:00-18:30)。
外圆磨常见故障排除
1工
件
有
螺
旋
形
痕
迹
砂轮硬度高,修得过细,磨削深
度过大。
合理选择砂轮硬度和修正用量,适当减小磨削深度纵向进给量过大适当降低进给量
砂轮磨损,母线不直修正砂轮
金刚石在修正器中未夹紧或金刚
石在刀杆未焊牢,修出砂轮凹凸
不平。
把金刚石装夹牢固,如金刚石有松动,需重新焊接冷却液太少或太淡加大或加入浓冷却液
工作台导轨润滑油压力使工作台
浮起,产生摆动
调整导轨润滑油压力工作台运行时有爬行现象打开放气阀,排除液压系统中的空气,或检修机床砂轮主轴有轴向窜动检修机床
2工
件
表
面
有
烧
伤
现
象
砂轮太硬或粒度太细合理选择砂轮
砂轮修得过细,不锋利合理选择修正用量
砂轮太钝修正砂轮
磨削深度和纵向进给量过大,或
工件圆周速度过低
适当减小磨削深度和纵向进给量,或增大工件转速冷却液不充足加大冷却液
3工
件
表
面
出
现
直
波
形
振
痕
工件圆周速速过大,工件中心孔
有多角.
适当降低工件转速,修正中心孔
工件直径,重量过大,不符合机
床规则
改在规格较大的机床上磨削。
如设备不允许,可降
低磨削深度和纵向进给量以及把砂轮修得锋利点砂轮主轴轴承磨损,配合间隙过
大,产生径向跳动按机床说明书规定调整轴承间隙
头架主轴轴承松动调整轴承间隙
砂轮不平衡,转动时发生振动注意保持砂轮平衡;(1)新砂轮需经俩次静平衡。
(2)砂轮使用一段时间后,如果又出现不平衡,(3)
砂轮停车前,先关掉冷却液。
使砂轮空转进行脱水,
以免冷却液聚集在下部引起不平衡,
砂轮硬度过高根据工件材料性质,选择合适的砂轮
砂轮变钝后没有及时修正,修正砂轮
砂轮修得过细,或金刚石顶角已磨钝。
砂轮修正不锋利。
合理选择修正用量或翻身金刚石,或得金刚石磨修尖。
4工
件
有
椭
圆
度
中心孔形状不正确,或内有污后,
铁销等,
根据具体情况重新修正中心孔,或把中心孔檫净
中心孔或顶尖因润滑不良而磨损注意润滑,如有磨损,需重新修正中心孔或修磨顶
尖
工件顶得过紧或放松重新调节尾架顶尖压力
顶尖在主轴和尾架内贴合不紧,
发生摇晃。
卸下顶尖,檫净后重新装上,
砂轮过钝修正砂轮
冷却液不充分或供应不及时保证充足的冷却液
工作刚性差而毛坯形状误差又
大,磨削时因余量不均而引
起磨削深度变化,使工件弹
性变型发生相应变化,磨削
后部分部分保留毛坯形状误
差,
磨削深度不能太大。
并应随着余量减小而逐步减
小,最后多次几次光磨行程,
工作有不平衡重量时,由于离心
力作用,会在重的那边磨去
较多金属,使工件有椭圆度。
事先加以平衡
砂轮主轴轴承间隙过大。
调整主轴轴承间隙
用卡盘装夹磨削外圆时,头架主
轴径向跳动过大
调整头架主轴轴承间隙
5工
件
有
锥
度
工作台未调整好,工件旋转轴线
与工作台运动方向不平行
仔细找正工作台
工件和机床的弹性变型发生变化应在砂轮锋利的情况下仔细找正工作台,每个工件
在精磨时,砂轮的锋利程度,磨削用量和光磨
次数应与找正工作台时的情况基本一致,否则
需要不均匀走到加以消除,
工作台导轨润滑油压过大,运行
中产生波动
调整压力
头架和尾座中心不重合修正使其重合
6工
件
有
鼓
型
工件刚性差,磨削时产生弹性弯
曲变型
减小工件的弹性变化;(1)减小磨削深度(2)及
时修正砂轮(3)工件很长时,适当使用中心架。
中心架调整不适当正确调整支撑肯支承块对工件的压力。
7工件两
端尺寸
过大或
过小
砂轮超出工件端面台小或过大调整换向撞块位置,使砂轮超出工件端面1/3-1/2
个砂轮宽度
工作台换向时停留时间太长或太
短调整时间
8阶台旁
外圆尺
寸大
工作台换向时停留时间太短延长停留时间
砂轮磨损,靠阶台旁外角变或母
线不直修正砂轮
9阶台轴
各外圆
表面不
同轴
磨削用量过大或光磨时间不够精磨时减小磨削深度,多做光磨
磨削步骤安排不当
同轴度要求高的表面应分粗精磨,同时尽可能一次
装夹中精磨完毕
用卡盘装夹磨削时,工件找正不
对,或头架主轴径向跳动大仔细找正工件基准面
10阶
台
端
面
内
部
凸
起
吃刀过大,退刀过块吃刀时纵向摇动工作台要慢而且均匀,光磨时间要
充分
冷却液不充分
加大冷却液
砂轮主轴有轴向窜动
机床检修
头架主轴轴承间隙大
调整间隙
用卡盘磨削端面时,头架主轴轴
承窜动大。
调整间隙
进刀太快,光磨时间不够进刀要慢而均匀,光磨至没有火花为止
砂轮与工件接触面积大,磨削压
力大。
把砂轮端面修成内凹,使工作面尽量狭小,同时先
把砂轮退出一段距离后再吃刀,然后逐渐摇进
砂轮,磨出整个端面
工件顶得过紧或过松
调节尾架顶尖压力
砂轮主轴中心与工作台运动方向
不平行调整砂轮架的位置
与椭圆度原因1和5相同
与椭圆度1和5的消除方法一样。