热成型技术的发展及其对汽车轻量化的影响
热成形技术在车身轻量化设计中的应用

年开发 了不带镀层的热冲压用钢 ( 冷轧B1 5 0 0 HS , 热 ̄ L B R1 5 0 0 H S ),并能批量供货。 ( 3 )热成形模具 热冲压 与冷冲压模具也完全
不 同 ,模具 型面 设 计 时 ,需 要 考 虑钢 板 的 热胀 冷 缩
I . 热成 形技术
( 1 )热成形工艺 钢板热成形技术是一种将特
冷却水回路使工件快速冷却淬火 ,热成形工序如图
1 所示。
兼顾这些 ,很多车企将高强度钢在车身设计中进行
了广 泛 应用 。 图1 热成形工序
目前车 身钣 金 零 件 大 多是 钢 板通 过 模 具 冷 冲 压 成 形 而 得 到 的 ,为 了能够 实现 冲 压 成 形 ,保 证 成 形
纪8 0 年 代提 出 ,其 与 传 统意 义 上 的 热 冲压 技 术 的 本
及布置方式 、冷却孔中心离模具 型面的距离、冷却 水 的流 动方式等) 。模具 内部冷却 回路 是钻孔形成 的 ,模具分块及其精密装配技术都需详细分析 。
质区别在于不是通过空冷 ,而是通过 在模具 中布置
参 磊
疆
Fo r m g
热成形技术在车身轻量化设计中
的应用
华晨 汽车 工程研究 院 ( 辽 宁沈 阳 1 1 0 1 4 1 ) 闰禄 平 李 飞 张丹荣
环境污染和能源消耗 已成为 当今世界亟待解决
的 社 会 问题 ,而 随 着燃 油 价 格 的 不 断上 涨 ,汽 车 油 耗 已经成 为 购 车 者 选车 的一 个 重 要 关注 点 。通 过车 身轻 量 化 设 计 降低 汽 车 自重 是一 种 降低 汽 车 油耗 的 有 效 手 段 。另 一方 面 , 日趋 严格 的碰 撞 法规 又要 求 车 身某 些 区 域具 有 较 高 的 强 度 以保 证 乘 员安 全 。为
汽车车身热冲压成型技术的应用和质量控制措施
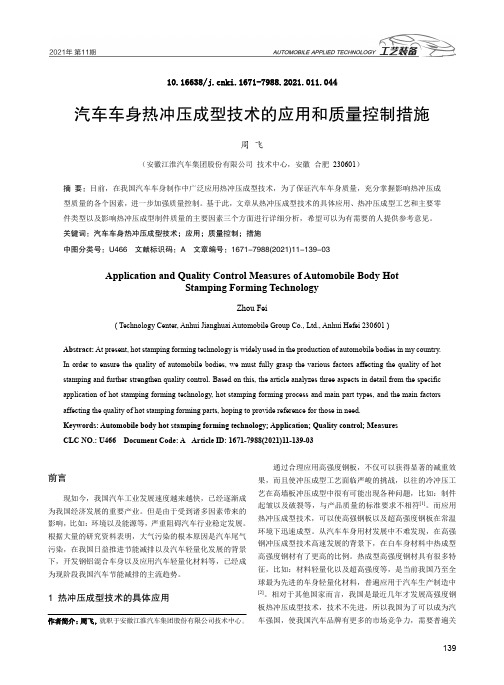
10.16638/ki.1671-7988.2021.011.044汽车车身热冲压成型技术的应用和质量控制措施周飞(安徽江淮汽车集团股份有限公司技术中心,安徽合肥230601)摘要:目前,在我国汽车车身制作中广泛应用热冲压成型技术,为了保证汽车车身质量,充分掌握影响热冲压成型质量的各个因素,进一步加强质量控制。
基于此,文章从热冲压成型技术的具体应用、热冲压成型工艺和主要零件类型以及影响热冲压成型制件质量的主要因素三个方面进行详细分析,希望可以为有需要的人提供参考意见。
关键词:汽车车身热冲压成型技术;应用;质量控制;措施中图分类号:U466 文献标识码:A 文章编号:1671-7988(2021)11-139-03Application and Quality Control Measures of Automobile Body HotStamping Forming TechnologyZhou Fei( Technology Center, Anhui Jianghuai Automobile Group Co., Ltd., Anhui Hefei 230601 )Abstract: At present, hot stamping forming technology is widely used in the production of automobile bodies in my country. In order to ensure the quality of automobile bodies, we must fully grasp the various factors affecting the quality of hot stamping and further strengthen quality control. Based on this, the article analyzes three aspects in detail from the specific application of hot stamping forming technology, hot stamping forming process and main part types, and the main factors affecting the quality of hot stamping forming parts, hoping to provide reference for those in need.Keywords: Automobile body hot stamping forming technology; Application; Quality control; MeasuresCLC NO.: U466 Document Code: A Article ID: 1671-7988(2021)11-139-03前言现如今,我国汽车工业发展速度越来越快,已经逐渐成为我国经济发展的重要产业。
热成型技术

王辉:热成型技术可以帮助汽车节能减排2009年10月20日18:31 腾讯汽车我要评论(0) 主持人:下面进行今天最后一个主题演讲。
下面有请本特勒汽车工业亚太区车身技术总监王辉博士。
他演讲的题目是汽车安全设计及车身轻量化——本特勒热成型技术的应用。
王辉:我叫王辉,我来自德国本特勒集团。
不管现在的汽车动力是混合型的动力,还是电池的电动力,汽车车身轻量化的问题是一个主要的问题,汽车越轻,同样的动力他跑得越快,在同样的动力下他跑得远。
所以我们今天的题目主要是讲一下怎么样用现代的工业技术以及新材料把车身在满足一些技术条件,比如说碰撞条件、干路条件下能满足轻量化,在节能减排方面做一些贡献。
节能减排是一个大趋势,本特勒作为全球最大的汽车零部件供应商之一,我们可以说本特勒也在行动以节能减排。
我今天题目主要有几个部分,在技术报告之前,我用几分钟给大家介绍一下本特勒。
另外,我再介绍一下关于二氧化碳的减排,这个题目今天我们前面的报告人都已经介绍了,我再简单介绍一下。
另外,在车身上面材料的使用,为什么使用这个材料,这个材料有什么好处。
我以前在国内做报告的题目就是这样:对于不同的零件我们可以使用不同的材料,满足他的技术要求,根据这个设计来满足轻量化的要求。
另外,我给大家介绍我们近一两年在市场上推广的三个技术。
最后,我要介绍三个例子,通过这三个例子大家可以看出来,作为节能减排,我们车的轻量化怎么能够在车的设计过程中考虑到成本的要求、轻量化的要求、技术的要求。
首先,本特勒。
本特勒是一个家族企业,它已经存在了130年的历史。
他以前是一个铁匠出身的,在50年代的时候,他曾经生产过五千辆最小车。
60年代,本特勒集团分成三个分支,有钢管、钢材、汽车技术、贸易。
我们今天主要讲的是汽车贸易,在汽车贸易里面我们有三个产品部门,第一个是底盘部门,我是来自车身部门的。
另外一套,我们还有发动机和排气管道部门,另外,我们还有工程技术公司。
本特勒全球在汽车行业总共在二十多家,有52个工厂16个研发中心,去年在汽车行业的销售量是46亿欧元,全球18000名员工。
现代汽车用高强度钢热成型技术分析
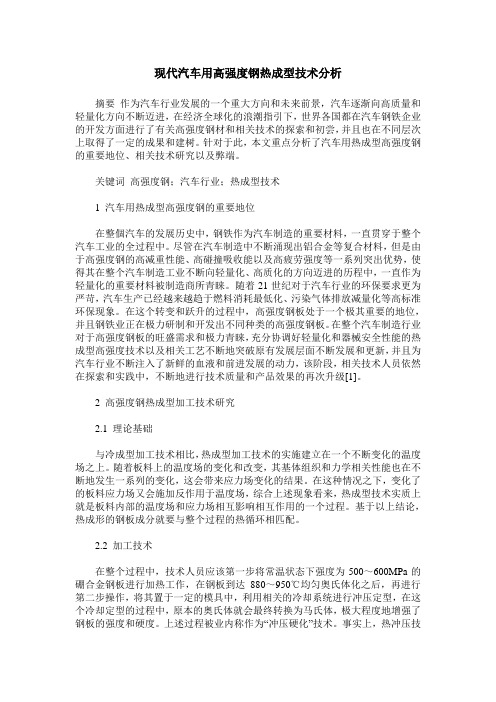
现代汽车用高强度钢热成型技术分析摘要作为汽车行业发展的一个重大方向和未来前景,汽车逐渐向高质量和轻量化方向不断迈进,在经济全球化的浪潮指引下,世界各国都在汽车钢铁企业的开发方面进行了有关高强度钢材和相关技术的探索和初尝,并且也在不同层次上取得了一定的成果和建树。
针对于此,本文重点分析了汽车用热成型高强度钢的重要地位、相关技术研究以及弊端。
关键词高强度钢;汽车行业;热成型技术1 汽车用热成型高强度钢的重要地位在整個汽车的发展历史中,钢铁作为汽车制造的重要材料,一直贯穿于整个汽车工业的全过程中。
尽管在汽车制造中不断涌现出铝合金等复合材料,但是由于高强度钢的高减重性能、高碰撞吸收能以及高疲劳强度等一系列突出优势,使得其在整个汽车制造工业不断向轻量化、高质化的方向迈进的历程中,一直作为轻量化的重要材料被制造商所青睐。
随着21世纪对于汽车行业的环保要求更为严苛,汽车生产已经越来越趋于燃料消耗最低化、污染气体排放减量化等高标准环保现象。
在这个转变和跃升的过程中,高强度钢板处于一个极其重要的地位,并且钢铁业正在极力研制和开发出不同种类的高强度钢板。
在整个汽车制造行业对于高强度钢板的旺盛需求和极力青睐,充分协调好轻量化和器械安全性能的热成型高强度技术以及相关工艺不断地突破原有发展层面不断发展和更新,并且为汽车行业不断注入了新鲜的血液和前进发展的动力,该阶段,相关技术人员依然在探索和实践中,不断地进行技术质量和产品效果的再次升级[1]。
2 高强度钢热成型加工技术研究2.1 理论基础与冷成型加工技术相比,热成型加工技术的实施建立在一个不断变化的温度场之上。
随着板料上的温度场的变化和改变,其基体组织和力学相关性能也在不断地发生一系列的变化,这会带来应力场变化的结果。
在这种情况之下,变化了的板料应力场又会施加反作用于温度场,综合上述现象看来,热成型技术实质上就是板料内部的温度场和应力场相互影响相互作用的一个过程。
基于以上结论,热成形的钢板成分就要与整个过程的热循环相匹配。
【技术帖】热成型技术的应用现状和发展趋势

【技术帖】热成型技术的应用现状和发展趋势摘要:阐述了热成型技术在汽车行业的起源和发展过程,简单介绍了热成型的分类与技术原理,探讨了先进热成型技术的发展趋势,分析了国内外的具体应用及现状,总结了热成型技术在国内自主品牌应用中所存在的问题。
关键词:热成型轻量化碰撞1前言随着汽车新材料的不断应用,以及满足市场对轻量化和高安全性能汽车需求的先进设计理念的不断引入,制造工艺也需要不断革新。
采用高强度钢板冲压件制造车身是同时实现车体轻量化和提高碰撞安全性的重要途径。
目前汽车车身安全件普遍采用1 300~1 500 MPa 级的超高强零件,但是高强度钢板强度越高,越难成形,尤其是当钢板强度达到1 500 MPa时,常规的冷冲压成形工艺几乎无法成形。
热成型技术的采用可以很好地解决超高强零件的成型问题。
2热成型技术发展历程19世纪中期,瑞典SSAB公司研发出了第一代热轧与冷轧含硼钢;20 世纪70 年代,热成型工艺首先在瑞典得到开发并取得专利。
瑞典SSAB 汽车公司在1984 年成为第一家采用硬化硼钢板的汽车制造商,生产出第一件热成型汽车零件——客车门内防撞梁。
随后,这一技术相继应用于保险杠横梁、A柱和B柱加强件以及底盘组件等,但是由于加工缓慢,且价格高,应用热成型技术生产的零件种类非常有限,只被原始设备制造商所接受。
80 年代中期之后,热成型技术进入高速发展阶段,当时有3 家公司可提供零件;1991 年,热成型保险杠横梁用于福特汽车;全球生产的热成型零件数量从1987年的3百万件增加到1997年的8百万件。
从2000 年起,更多热成型零件被用在汽车上,而且年产件量在2007 年上升到约1.07 亿件。
2013 年,约80%的白车身骨架类零件均可由热冲压技术加工,产量超过3亿件。
目前,全世界热成型生产线已超过200 条,Benteler 拥有其中近40%,是世界上最主要的热成型零件供应商,GESTAMP 是世界上首个提供热成型件的厂家,其客户主要集中在欧洲车系,COSMA也是主要的热成型供应商之一。
基于Autoform的车身B柱热成形工艺研究

摘要车的发展给人们的生活带来了极大的便利,但同时也带来了严重的能源消耗以及空气污染问题。
为了降低汽车的油耗和环境影响,汽车轻量化已成为汽车行业发展的重要方向。
热成形技术是汽车轻量化、提高汽车抗冲击形以及防撞性能的重要途径。
热成形过程数值模拟的准确性对热成型零件的设计和制造具有重要的指导作用。
本文基于Autoform软件,建立了 B 柱的热成形模型, 采用热力耦合数值分析的方法得到了热成形后零件的厚度,温度分布及破裂起皱的趋势分布等, 通过跟实际调试后的零件的对比,验证了模拟结果的准确性。
关键词:热成型有限元数值模拟 Autoform一、引言十四五时期,我国要努力趋向“碳达峰”和“碳中和”愿景,必须大力推动经济结构、能源结构、产业结构转型升级。
在“双积分”政策引导下,汽车行业也在大力开展节能减排工作,并以轻量化、新能源作为节能减排的主要手段。
对于传统燃油车,当汽车重量减少10%,燃油效率可以提高约8%;而纯电动汽车因为增加了三电系统导致其重量大幅上升,减轻重量可以减少电池容量或提升续航里程,因此新能源车型轻量化需求比传统燃油车更为迫切。
从汽车性能角度考虑,汽车的轻量化有助于汽车的“行驶、转弯、停车”三大基本性能的提高。
汽车白车身(解决碰撞安全性问题的车身骨架)是抵御碰撞侵入和能量吸收核心单元,约占汽车总重量的30%。
随着日益严格的碰撞安全法规,加强白车身成为必然应对手段,因此全球汽车企业均面临着日益增大的车身加强与轻量化间的矛盾。
其中热成形[1]技术对高强钢板进行成形, 在进行热成形前需将坯料加热到高温,使坯料奥氏体化,然后通过快速冷却,得到完全马氏体组织, 如图1,如采用 22 MnB5高强钢板热成形技术制造汽车保险杠,其强度可达1500MPa以上[ 2 ],该技术已成为世界上众多汽车生产厂商关注的热点。
图1 热成形技术原理通用、福特、大众、沃尔沃等汽车制造公司都在大量使用热成形的高强度汽车零件,某些车型上使用量高达30%。
热成形工艺在汽车零件制造过程中的应用
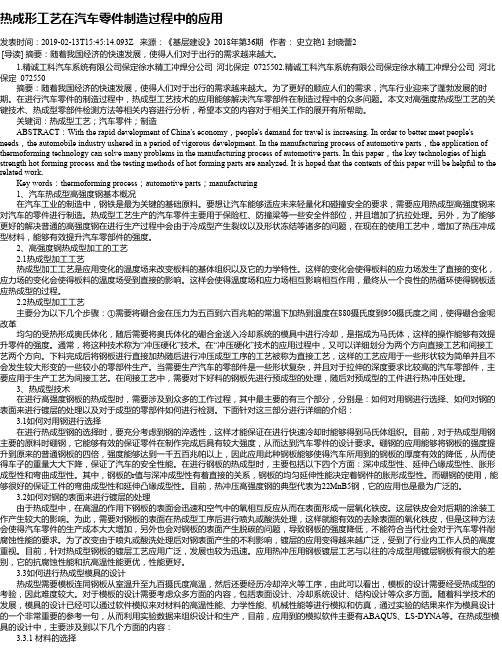
热成形工艺在汽车零件制造过程中的应用发表时间:2019-02-13T15:45:14.093Z 来源:《基层建设》2018年第36期作者:史立艳1 封晓蕾2 [导读] 摘要:随着我国经济的快速发展,使得人们对于出行的需求越来越大。
1.精诚工科汽车系统有限公司保定徐水精工冲焊分公司河北保定 0725502.精诚工科汽车系统有限公司保定徐水精工冲焊分公司河北保定 072550摘要:随着我国经济的快速发展,使得人们对于出行的需求越来越大。
为了更好的顺应人们的需求,汽车行业迎来了蓬勃发展的时期。
在进行汽车零件的制造过程中,热成型工艺技术的应用能够解决汽车零部件在制造过程中的众多问题。
本文对高强度热成型工艺的关键技术、热成型零部件检测方法等相关内容进行分析,希望本文的内容对于相关工作的展开有所帮助。
关键词:热成型工艺;汽车零件;制造 ABSTRACT:With the rapid development of China's economy,people's demand for travel is increasing. In order to better meet people's needs,the automobile industry ushered in a period of vigorous development. In the manufacturing process of automotive parts,the application of thermoforming technology can solve many problems in the manufacturing process of automotive parts. In this paper,the key technologies of high strength hot forming process and the testing methods of hot forming parts are analyzed. It is hoped that the contents of this paper will be helpful to the related work.Key words:thermoforming process;automotive parts;manufacturing 1、汽车热成型高强度钢基本概况在汽车工业的制造中,钢铁是最为关键的基础原料。
汽车车身热成形工艺的发展趋势-概述说明以及解释
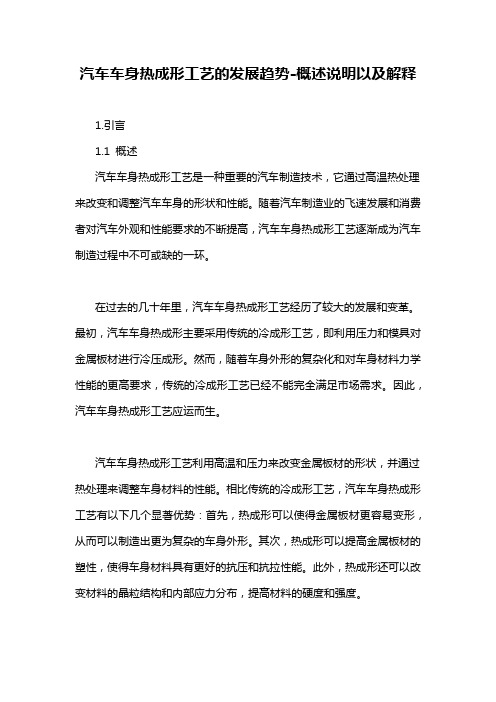
汽车车身热成形工艺的发展趋势-概述说明以及解释1.引言1.1 概述汽车车身热成形工艺是一种重要的汽车制造技术,它通过高温热处理来改变和调整汽车车身的形状和性能。
随着汽车制造业的飞速发展和消费者对汽车外观和性能要求的不断提高,汽车车身热成形工艺逐渐成为汽车制造过程中不可或缺的一环。
在过去的几十年里,汽车车身热成形工艺经历了较大的发展和变革。
最初,汽车车身热成形主要采用传统的冷成形工艺,即利用压力和模具对金属板材进行冷压成形。
然而,随着车身外形的复杂化和对车身材料力学性能的更高要求,传统的冷成形工艺已经不能完全满足市场需求。
因此,汽车车身热成形工艺应运而生。
汽车车身热成形工艺利用高温和压力来改变金属板材的形状,并通过热处理来调整车身材料的性能。
相比传统的冷成形工艺,汽车车身热成形工艺有以下几个显著优势:首先,热成形可以使得金属板材更容易变形,从而可以制造出更为复杂的车身外形。
其次,热成形可以提高金属板材的塑性,使得车身材料具有更好的抗压和抗拉性能。
此外,热成形还可以改变材料的晶粒结构和内部应力分布,提高材料的硬度和强度。
目前,汽车车身热成形工艺已经广泛应用于汽车制造业,特别是高端和豪华汽车的生产过程中。
许多知名汽车制造商已经采用了汽车车身热成形工艺,以提高汽车的外观质感和性能指标。
同时,一些新兴的汽车制造企业也开始关注和运用汽车车身热成形工艺,以求在市场竞争中取得竞争优势。
展望未来,汽车车身热成形工艺有望在汽车制造业中发挥更为重要的作用。
随着材料科学和制造技术的进步,汽车车身热成形工艺将不断创新和完善。
例如,利用先进的金属合金、复合材料和纳米材料,可以进一步提升车身材料的性能和品质。
此外,借助智能制造和自动化技术,汽车车身热成形工艺的生产效率也将得到进一步提高。
综上所述,汽车车身热成形工艺作为一项关键的汽车制造技术,正在不断发展和演变。
其具有的优势和潜力使得它成为汽车制造业中不可或缺的一部分。
随着技术的不断进步和市场的需求变化,汽车车身热成形工艺有望在未来取得更大的突破和发展。
汽车用高强度钢热成型技术
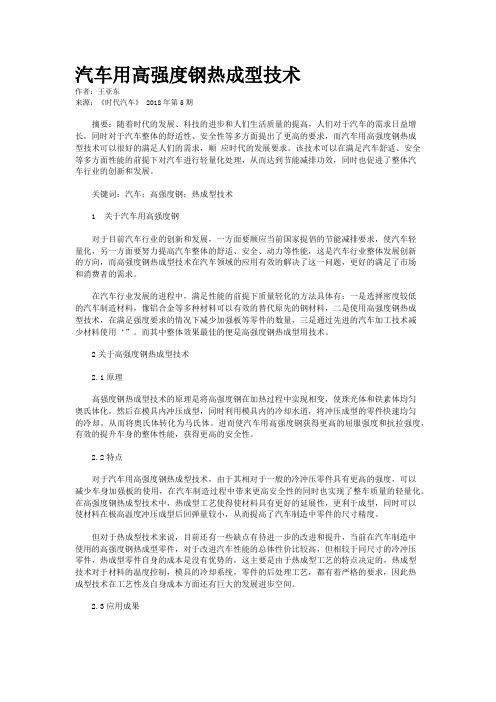
汽车用高强度钢热成型技术作者:王亚东来源:《时代汽车》 2018年第5期摘要:随着时代的发展、科技的进步和人们生活质量的提高,人们对于汽车的需求日益增长,同时对于汽车整体的舒适性、安全性等多方面提出了更高的要求,而汽车用高强度钢热成型技术可以很好的满足人们的需求,顺应时代的发展要求。
该技术可以在满足汽车舒适、安全等多方面性能的前提下对汽车进行轻量化处理,从而达到节能减排功效,同时也促进了整体汽车行业的创新和发展。
关键词:汽车;高强度钢;热成型技术1 关于汽车用高强度钢对于目前汽车行业的创新和发展,一方面要顺应当前国家提倡的节能减排要求,使汽车轻量化,另一方面要努力提高汽车整体的舒适、安全、动力等性能,这是汽车行业整体发展创新的方向,而高强度钢热成型技术在汽车领域的应用有效的解决了这一问题,更好的满足了市场和消费者的需求。
在汽车行业发展的进程中,满足性能的前提下质量轻化的方法具体有:一是选择密度较低的汽车制造材料,像铝合金等多种材料可以有效的替代原先的钢材料,二是使用高强度钢热成型技术,在满足强度要求的情况下减少加强板等零件的数量,三是通过先进的汽车加工技术减少材料使用‘”。
而其中整体效果最佳的便是高强度钢热成型用技术。
2关于高强度钢热成型技术2.1原理高强度钢热成型技术的原理是将高强度钢在加热过程中实现相变,使珠光体和铁素体均匀奥氏体化,然后在模具内冲压成型,同时利用模具内的冷却水道,将冲压成型的零件快速均匀的冷却,从而将奥氏体转化为马氏体。
进而使汽车用高强度钢获得更高的屈服强度和抗拉强度,有效的提升车身的整体性能,获得更高的安全性。
2.2特点对于汽车用高强度钢热成型技术,由于其相对于一般的冷冲压零件具有更高的强度,可以减少车身加强板的使用,在汽车制造过程中带来更高安全性的同时也实现了整车质量的轻量化。
在高强度钢热成型技术中,热成型工艺使得使材料具有更好的延展性,更利于成型,同时可以使材料在极高温度冲压成型后回弹量较小,从而提高了汽车制造中零件的尺寸精度。
Autoform R7汽车热冲压成形的技术解析

Autoform R7热成型
所谓的硼钢,是指汽车上的热成型钢,因为在这种钢材中加入了硼元素,所以又 称作硼钢。是指将钢板经过950°C的高温加热之后一次成形,然后又迅速冷却, 全面提升了钢板强度,经过这样处理的钢材称之为热成型钢。
热成型钢具有极高的材料强度和机械安全性。一般的高强度钢板的抗拉强度在 400-450MPa左右,而热成形钢抗拉强度高达1300-1600 MPa,屈服度达1000Mpa 之上,每平方厘米能承受10吨以上的压力,为普通钢材的3-4倍,其硬度仅次于 陶瓷,但又具有钢材的韧性。把这种材料用在车身上,在车身重量几乎没有太大 变化情况下,承受力提高了30%,使汽车的车身强度更好。
3.转移:
指的是将加热后的钢板从加热炉中取出放进热成形模具中去。在这一道工序中, 必须保证钢板被尽可能快地转移到模具中,一方面是为了防止高温下的钢板氧化, 另一方面是为了确保钢板在成形时仍然处在较高的温度下,以具有良好的塑性。
4.冲压和淬火:
在将钢板放进模具之后,要立即对钢板进行冲压成形,以免温度下降过多影响钢 板的成形性能。成形以后模具要合模保压一段时间,一方面是为了控制零件的形 状,另一方面是利用模具中设置的冷却装置对钢板进行淬火,使零件形成均匀的 马氏体组织,获得良好的尺寸精度和机械性能。研究表明,就目前常用的热冲压 钢材而言,实现奥氏体向马氏体转变的最小冷却速率为27~30℃/s,因此要保证 模具对板料的冷却速度大于此临界值。
热成型软区零件可使需要高强度部位抗拉、屈服强度等机械性能显著提高,达到 可以承受更大的撞击力的效果,同时也可使需要低强度部位拥有较低抗拉、屈服强 度,在碰撞时达到吸能和溃缩的作用,两者方式的结合能够有效地提高汽车的碰 撞安全性能,实现汽车轻量化。实现同一个热成型零件在不同区域有不同的机械性 能,优化零件在整车碰撞试验中的性能表现。
高强度钢板的两种热成形技术
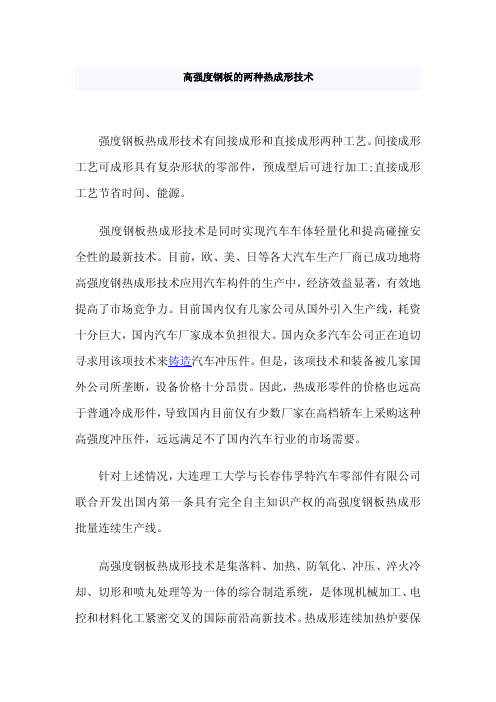
高强度钢板的两种热成形技术强度钢板热成形技术有间接成形和直接成形两种工艺。
间接成形工艺可成形具有复杂形状的零部件,预成型后可进行加工;直接成形工艺节省时间、能源。
强度钢板热成形技术是同时实现汽车车体轻量化和提高碰撞安全性的最新技术。
目前,欧、美、日等各大汽车生产厂商已成功地将高强度钢热成形技术应用汽车构件的生产中,经济效益显著,有效地提高了市场竞争力。
目前国内仅有几家公司从国外引入生产线,耗资十分巨大,国内汽车厂家成本负担很大。
国内众多汽车公司正在迫切寻求用该项技术来铸造汽车冲压件。
但是,该项技术和装备被几家国外公司所垄断,设备价格十分昂贵。
因此,热成形零件的价格也远高于普通冷成形件,导致国内目前仅有少数厂家在高档轿车上采购这种高强度冲压件,远远满足不了国内汽车行业的市场需要。
针对上述情况,大连理工大学与长春伟孚特汽车零部件有限公司联合开发出国内第一条具有完全自主知识产权的高强度钢板热成形批量连续生产线。
高强度钢板热成形技术是集落料、加热、防氧化、冲压、淬火冷却、切形和喷丸处理等为一体的综合制造系统,是体现机械加工、电控和材料化工紧密交叉的国际前沿高新技术。
热成形连续加热炉要保证板料加热到设定的温度充分奥氏体化,同时避免没有防氧化涂层板料的高温氧化脱碳,这决定了热成形连续加热炉与其他加热炉相比应具有独特的核心技术。
成形有间接成形和直接成形两种工艺。
热成形间接成形工艺是指板料先经过冷冲压进行预成形,然后加热到奥氏体化温度,保温一段时间后放到具有冷却系统的模具里进行最终成形及淬火。
热成形间接成形工艺的优点如下:(1)可以成形具有复杂形状的车内零部件,几乎可以获得目前所有的冲压承载件。
(2)板料预成形后,后续热成形工艺不需要过多考虑板料高温成形性能,可以确保板料完全淬火得到所需要的马氏体组织。
(3)板料预成形后可以进行修边、翻边、冲孔等工艺加工,避免板料淬火硬化后加工困难问题。
热成形直接成形工艺是指板料加热到奥氏体化温度保温一段时间后直接放到具有冷却系统的模具里进行成形及淬火。
汽车车身中高强度钢热成形技术的应用

汽车车身中高强度钢热成形技术的应用作者:李伟来源:《时代汽车》2020年第19期摘要:汽车的安全性能以及节能减排要求越来越高,轻量化是汽车行业重要的发展方向之一,高强度钢热成形技术在实现汽车轻量化、节能减排,保证安全性等方面具有显著优势和潜力。
近10年来,热成形钢在汽车车身中应用以及热成形技术迅速发展。
本文简要介绍了热成形技术的原理、分类以及先进热成形技术,最后对高强度钢热成形技术在汽车轻量化中的应用做了介绍和展望。
关键词:热成形技术轻量化汽车高强度钢Application of Hot Forming Technology of High Strength Steel in Automobile BodyLi WeiAbstract:The safety performance, energy saving and emission reduction requirements of automobiles are getting higher and higher. Lightweight is one of the important development directions of the automobile industry. High-strength steel hot forming technology has advantages in realizing automobile lightweight, energy saving and emission reduction, and ensuring safety, which is of great significant advantages and potential. In the past 10 years, the application of hot-formed steel in automobile bodies and the hot-forming technology have developed rapidly. This article briefly introduces the principle, classification and advanced hot forming technology of hot forming technology. Finally, the application of high-strength steel hot forming technology in automobile lightweight is introduced and prospected.Key words:hot forming technology, lightweight, automobile, high-strength steel1 引言随着中国汽车工业快速发展,汽车产销量迅速增加,如中国汽车工业协会统计数据,2019年中国汽车产量达2572.1万辆,销量完成2576.9万辆,产销量继续蝉联全球第一。
热冲压成形工艺解析

热冲压成形工艺解析热冲压成形工艺解析随着汽车轻量化的发展,钢板热冲压技术应运而生,其将高强度钢板在温度场内由奥氏体转变为马氏体,提高了板料的强度,降低了板料的重量。
本文对热冲压成形板料和设备应用进行了总结,并预测了热冲压技术的未来发展趋势...安全、节能和环保是消费者最关心的汽车性能指标。
目前,降低汽车燃料消耗、减少CO2和废气排放是社会的主要需求。
车身轻量化对于减轻整车自身重量、降低油耗和促进节能环保至关重要。
为了适应轻量化的发展趋势,热成形工艺和应用技术应运而生。
热成形压力机简称热冲压,是相对于常见的冷冲压成形而言。
为了帮助减轻汽车自身重量并提高汽车的安全性,钢铁业开发出许多种类的高强度钢板。
为了克服高强度钢板冷成形的困难,热冲压需要通过将钢板加热,使其板料上产生一个不断变化的温度场。
在温度场的影响下,板料的基体组织和力学性能发生变化,导致板料的应力场也发生变化,同板料的应力场变化又反作用于温度场。
热成形工艺过程为:首先将常温下强度为500~600MPa的硼合金钢板加热到约940℃,全奥氏体后,将材料从加热炉转移到热成形的压力机中,该过程在空气中进行,必须尽快完成,如果成形前材料温度降到750℃以下,就可能形成铁素体从而恶化零件的机械性能。
送入内部具有冷却系统的模具内,压力机进行冲压、成形。
板料在模具内快速冷却(水冷),将奥氏体转变为马氏体(200℃以下),冷却速度一般为-40~100℃/s以保证零件的淬透性,使冲压件得到硬化,大幅度提高强度(1500MPa)。
所以热成形工艺就是板料内部温度场与应力场共存且相互耦合的变化过程。
热冲压成形的生产流程为拆垛装置、加热炉、上料装置、成形冷却、激光切割和喷丸涂油,如图1所示。
图1 热冲压成形的工艺流程热成形板料选择目前,热成形用钢均选用硼钢,因微量的硼可有效提高钢的淬透性,使零件在模具中以适当的冷却速度获得所需要的马氏体组织,从而保证零件的高强度。
热成形冲压板材主要分为镀层与无镀层板材。
[高强,汽车,技术]试论高强钢成形技术及其在汽车轻量化中的应用
![[高强,汽车,技术]试论高强钢成形技术及其在汽车轻量化中的应用](https://img.taocdn.com/s3/m/241a601289eb172dec63b703.png)
试论高强钢成形技术及其在汽车轻量化中的应用汽车轻量化是指在保证汽车的强度和安全性能的前提下,尽可能地减轻汽车的整车质量,从而提高汽车的动力性,减少燃料消耗,降低排气污染。
汽车的快速发展方便了人们的生活,但同时带来了金属、石油等资源、能源的过量消耗,大气严重污染,通过汽车轻量化实现降低排放和油耗成为汽车工业最具挑战的目标。
有研究表明,当钢板厚度分别减小0.05mm、0.1mm和0.15mm时,车身减重分别为6%、12%和18%,可见增加钢板强度的同时减小板厚是减轻车重的主要途径。
高强钢具有较高的强度,且成本较轻金属低,汽车采用先进高强钢的主要效果有:高强钢的使用降低了板厚使得汽车结构轻量化、汽车的抗凹陷性、耐久强度和大变形冲击强度安全性均得到提高。
高强钢的优点使得其在汽车行业中得到快速发展及广泛应用,如1980年日本和欧洲的汽车公司,白车身中高强钢用量分别为12%和5%,目前均上升到50%以上。
高强钢的应用不仅为轻量化创造了更多的机遇,更有助于使汽车达到轻量化和提高安全性的统一。
一、高强钢的种类高强度钢板的分类主要有按冶金特点、强化机理和生产工艺等几种划分方法。
1. 按冶金特点分类根据国际钢铁协会U S L - A B项目的定义,屈服强度为210 ~550MPa及抗拉强度为270 ~700M P a的为高强度钢(简称H S S)。
普通高强度钢为单一铁素体组织,由于采用了以相变为主的复合强化方法,基体的强度和综合性能得到提高。
普通高强度钢包括有微合金钢、碳锰钢、烘烤硬化钢、各向同性钢、高强度I F钢和低合金高强度钢等几种。
屈服强度大于550M P a及抗拉强度大于700M P a的则称为先进高强度钢(简称A H S S)。
A H S S 的研究基于H S S朝2个方向发展,一个方向是强度基体不变,提高其塑性;另一个方向是塑性基体不变提高其强度。
强度提高的钢种包括复向钢(C P)、马氏体钢(MS)等,塑性提高的钢种包括有双相钢(C P)、相变诱发塑性钢(T R I P)等。
汽车工业中热冲压成形工艺的应用
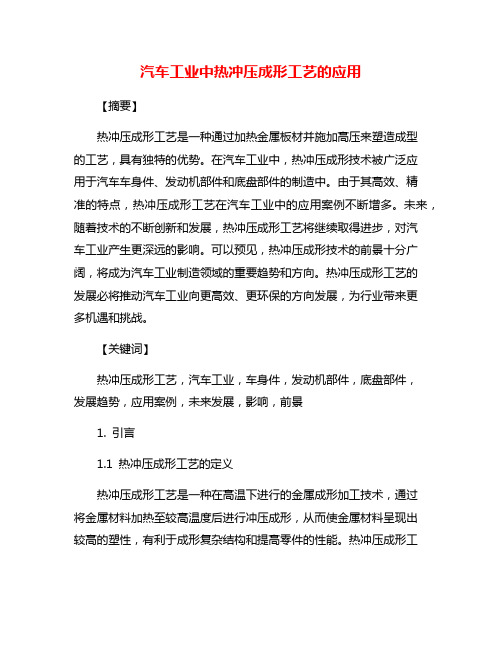
汽车工业中热冲压成形工艺的应用【摘要】热冲压成形工艺是一种通过加热金属板材并施加高压来塑造成型的工艺,具有独特的优势。
在汽车工业中,热冲压成形技术被广泛应用于汽车车身件、发动机部件和底盘部件的制造中。
由于其高效、精准的特点,热冲压成形工艺在汽车工业中的应用案例不断增多。
未来,随着技术的不断创新和发展,热冲压成形工艺将继续取得进步,对汽车工业产生更深远的影响。
可以预见,热冲压成形技术的前景十分广阔,将成为汽车工业制造领域的重要趋势和方向。
热冲压成形工艺的发展必将推动汽车工业向更高效、更环保的方向发展,为行业带来更多机遇和挑战。
【关键词】热冲压成形工艺,汽车工业,车身件,发动机部件,底盘部件,发展趋势,应用案例,未来发展,影响,前景1. 引言1.1 热冲压成形工艺的定义热冲压成形工艺是一种在高温下进行的金属成形加工技术,通过将金属材料加热至较高温度后进行冲压成形,从而使金属材料呈现出较高的塑性,有利于成形复杂结构和提高零件的性能。
热冲压成形工艺可以有效地改善金属材料的变形性能和力学性能,同时还可以减少成形过程中的应力和变形,提高成形零件的表面质量和精度。
1.2 热冲压成形工艺的优势热冲压成形工艺的优势包括:1. 制造成本低:相比传统的冷冲压成形工艺,热冲压成形可以减少成本,提高生产效率。
2. 成形精度高:热冲压成形可以在较高温度下进行,使得金属材料更容易塑性变形,从而实现更高的成形精度。
3. 降低材料损耗:利用热冲压成形可以减少材料的冷硬化现象,有效降低材料损耗,提高材料利用率。
4. 改善材料性能:热冲压成形可以改善材料的塑性和韧性,提高零件的强度和耐久性。
5. 可实现复杂结构:热冲压成形可以实现更复杂的汽车零部件结构,提高产品的功能性和设计性。
6. 环保节能:热冲压成形可以减少二次加工工序,减少能源消耗和环境污染,符合现代环保要求。
7. 适用性广泛:热冲压成形工艺适用于各种金属材料,适用于多种汽车零部件的制造,具有很高的通用性和适应性。
奇瑞汽车轻量化技术新进展

发 ( 图6 ,显著 降低 了零部件 的重量 ( 见 ) 见附表 ) 。 同时 奇瑞公司掌握 了S MC ̄IMT I : G 复合材料 的零 部件设
计 、产 品试制和试验验证的综合开发能力 。
()S a MC后 备 门
l
()G 防 护罩 b MT
图 6
材料变化前后零 件重 量对 比表
成形 、热压 成形和滚 压成形等 材料 成形应 用技术将 成为
首选。
汽车轻量化材料应用现状
轻 量 化 材料 是 指 可用 来减 轻 汽车 自重 的材 料 ,它
有两大 类 :一类 是低密度 的轻质材料 ,如铝合 金、镁合 金 、钛 合金 、塑料 和 复合 材 料等 ;另一 类是 高 强 度材 料 ,如 高强度钢 等。 目前 ,已得到实 际工业化应 用的轻 量化材料主要有 高强度钢 、铝合金 、镁 合金和塑料等。
此 外 ,奇 瑞 公司瑞麒 G5 开发 了镁 合金仪表 板 骨架
成本 与普 通 点焊设 计 基本持 平 ,但 能显 著提 高正 碰性
( 见图5 ),已完成各种试验验证 ,实现批量装车。仪
表板 骨架采用镁 合金 整体压铸 ,绿色环保的 同时单 件减
能,在奇瑞A 的前纵梁上已有批量应用 ( 3 见图7 ),并
轻量化 系数的定义为 :
M L =-- -— -- - — - -- C
2铝合金 .
铝 合金在奇瑞 公司的 产品上 已得 到广泛应用 ,铝合
式中:
L —— 轻量化 系数 ;
金零部件 以铸件 为主 ,还有 少量的型材 和板材 ,已 占到 整车备 重的 1%左右 。典 型应用 为变速 器壳体 、发 动机 0 缸 体 、缸盖 、油底 壳 、底盘转 向节 、控制 臂 、隔热板 和 散热器等零 件 ( 见图3 )。另外 ,在 国家 “6 ”项 目的 83 支持下 ,奇瑞完 成了铝合金板 材的应用开发 工作 ,使A 5
钛合金热成形技术_概述及解释说明

钛合金热成形技术概述及解释说明1. 引言1.1 概述钛合金热成形技术是一种利用高温和压力对钛合金进行塑性变形的方法。
通过在特定温度下将钛合金加热到其塑性区域,然后施加压力来实现成形。
这种技术在航空航天、汽车制造、医疗器械等领域中得到广泛应用,并且在近年来取得了显著的发展和突破。
1.2 文章结构本文将从几个方面对钛合金热成形技术进行全面介绍和解释说明。
首先,我们将概述该技术的定义、原理以及其历史发展情况。
然后,我们将详细介绍该技术在不同领域的应用,并探讨其在实际生产中的工艺流程。
接下来,我们将深入分析钛合金热成形技术的优势,并提出当前面临的挑战以及相应的解决方法。
最后,我们将总结主要观点并对该技术未来发展进行展望。
1.3 目的本文旨在全面介绍和解释钛合金热成形技术,并分析其优势和挑战。
通过对该技术的准确理解,读者可以更好地了解钛合金热成形技术在工业生产中的应用和潜力,并为相关领域的研究和实践提供参考依据。
2. 钛合金热成形技术概述2.1 定义和原理钛合金热成形技术是一种通过将钛合金材料加热至其塑性变形温度,然后进行成型的制造工艺。
它基于钛合金在高温下具有良好的塑性和可变形性的特点,通过控制温度和应力来实现对钛合金材料的可控变形。
该技术主要依靠热胀冷缩原理,即在加热过程中,钛合金材料会膨胀并变软,使其容易成形;而在冷却过程中,由于收缩效应,材料会保持所需的形状。
通过精确控制加热、保温、成形和冷却阶段的参数和时间,可以实现对钛合金材料复杂三维几何形状的成型。
2.2 历史发展钛合金热成形技术起源于20世纪50年代。
当时,在航空航天工业领域对功能强大、轻量化及高机械性能要求极高的部件需求推动了该技术的发展。
最初的试验主要集中在单晶和多晶钛合金的热加工方面,通过探索适宜的加热温度和形变速率以及工艺参数的优化,成功实现了钛合金材料的热成形。
随着技术的不断进步和先进材料的开发,钛合金热成形技术得到了广泛应用。
如今,它已在航空、航天、汽车、医疗器械等领域得到广泛应用,并为这些领域带来了许多新的设计可能性和解决方案。
热冲压成形工艺的发展及相关模具材料的研究进展
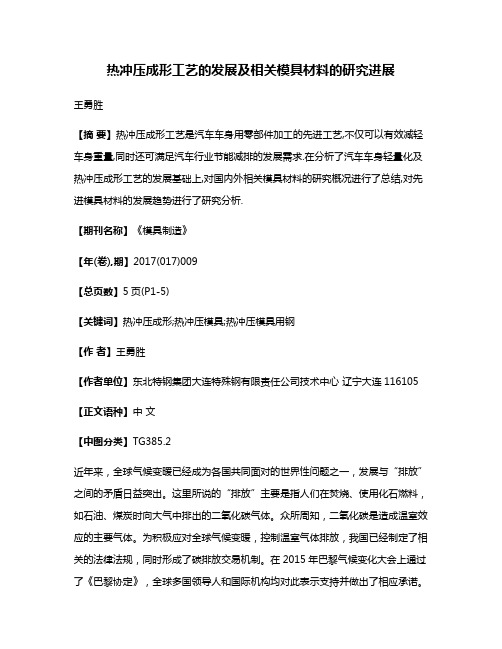
热冲压成形工艺的发展及相关模具材料的研究进展王勇胜【摘要】热冲压成形工艺是汽车车身用零部件加工的先进工艺,不仅可以有效减轻车身重量,同时还可满足汽车行业节能减排的发展需求.在分析了汽车车身轻量化及热冲压成形工艺的发展基础上,对国内外相关模具材料的研究概况进行了总结,对先进模具材料的发展趋势进行了研究分析.【期刊名称】《模具制造》【年(卷),期】2017(017)009【总页数】5页(P1-5)【关键词】热冲压成形;热冲压模具;热冲压模具用钢【作者】王勇胜【作者单位】东北特钢集团大连特殊钢有限责任公司技术中心辽宁大连116105【正文语种】中文【中图分类】TG385.2近年来,全球气候变暖已经成为各国共同面对的世界性问题之一,发展与“排放”之间的矛盾日益突出。
这里所说的“排放”主要是指人们在焚烧、使用化石燃料,如石油、煤炭时向大气中排出的二氧化碳气体。
众所周知,二氧化碳是造成温室效应的主要气体。
为积极应对全球气候变暖,控制温室气体排放,我国已经制定了相关的法律法规,同时形成了碳排放交易机制。
在2015年巴黎气候变化大会上通过了《巴黎协定》,全球多国领导人和国际机构均对此表示支持并做出了相应承诺。
虽然个别发达国家声称退出协定,但仍阻止不了各国为应对气候变化应当开展强有力国际合作的大势所趋。
作为石油消费的重要行业之一,汽车行业对全球气候变化有着非常重要的影响。
现当今,除驾乘安全外,节能和环保也是消费者最为关心的性能指标。
从2009年开始,我国的汽车销量就超过了美国,成为全球汽车消费第一大国。
2016年,我国汽车销量为2,794万辆,同比增长14.1%,2017年预计将达到2,943万辆。
截至2016年底,我国汽车保有量已达到1.94亿辆,较2010年增长了113%。
而据国家信息中心预计,到2020年,我国汽车保有量将达到2.5亿辆。
据统计,汽车重量每减轻10%,可降低油耗8%~10%[1]。
车身作为汽车重要的组成部分,其质量占到汽车总重的30%~40%,因此车身的轻量化对整车的轻量化起着重要作用。
- 1、下载文档前请自行甄别文档内容的完整性,平台不提供额外的编辑、内容补充、找答案等附加服务。
- 2、"仅部分预览"的文档,不可在线预览部分如存在完整性等问题,可反馈申请退款(可完整预览的文档不适用该条件!)。
- 3、如文档侵犯您的权益,请联系客服反馈,我们会尽快为您处理(人工客服工作时间:9:00-18:30)。
March 15, 2011
From steels to final car components through press hardening by ThyssenKrupp
Trimming hardened parts on separate trimming line
Up to 3 trimming operations
Austenitisation
Transfer of plate Closing of die
Press hardening Opening of stamp
Micro structure before hot stamping
Micro structure after hot stamping
Time
Heating to
Hot stamping and press
880 °C–950 °C hardening in cooled die
Die or laser trimming
Indirect hot stamping (two steps) / 22MnB5
Cold stamping
Heating to
3
Why press hardening
March 15, 2011
Weight reduction
140
+ 15-25 %
Estimated weight reduction
120
100
Reference - 5–10% -10–15%
80-20–40%60 Nhomakorabea40
20
0 Mild Steel HSLA
15
From steels to final car components through press hardening by ThyssenKrupp
Chassis
1
3
Body
2 1
2
5
Typical Chassis products 1 Front subframes/crossmembers 2 Control arms 3 Cross member 4 Rear lateral link 5 Axle cases
9
March 15, 2011
Mechanical properties of 22MnB5
Damage to 22MnB5 under axial crash loading (extract from BMW)
Hardened with increasing temperature
11
March 15, 2011
DP-600 TRIP-800 Press hardening Aluminum
DP-800
steel
6
Why press hardening
Euro NCAP crash tests
March 15, 2011
crash performance
Bumper reinforcement
Side impact beam Roof frame
5
Typical body products
1 Side walls 2 Cross car beams 3 Side intrusion beams 4 Pillars/pillarreinforcer 5 Outer door panels 6 reinforcements 7 Longitudinals
March 15, 2011
安全
(U)HSS
Light metals
Conventional process
Press hardening
DP1000 TRIP1000
CP1000 MS1200
<5% in use
铌合金(Nb)
PH1500
15% in use
Plastic and carbon fiber
High Bake Hardening potential after press hardening (22MnB5)
1550
TS 1450
1350
1250
1150
BH potential
1050
950
Press hardened
5
min.
10
min.
15 min.
20
min.
12
March 15, 2011
OEMs
6 4
Selected examples
Mini, Ford EUCD, new PSA/Fiat G9 Ford Galaxy, VW Touareg, Porsche Cayenne, Land Rover Discovery Mini, Ford Fiesta Volvo S80 Land Rover Defender
Hot stamping and press Die or laser Sand
880 °C–950 °C hardening in cooled die trimming
blasting
8
March 15, 2011
Temperature profile and micro structure
development
March 15, 2011
Press Hardening Advanced Technology to reduce the Weight of Vehicles
for Today and Future
1
环保 节能
light weight concepts
Strategy of light weight
A-pillar
B-pillar C-pillar
Dash panel Tunnel
Sill Side member Bumper reinforcement
7
Process Technology
Direct hot stamping (one step) / 22MnB5
March 15, 2011
Coating systems for press hardening process
13
March 15, 2011
From steels to final car components through press hardening by ThyssenKrupp
Remove the part Stamp and harden Center and insert Austenitize Heat sheets Place sheets on roller table Part marking by laser Destack