pcb钻孔和外形
pcb激光钻孔标准
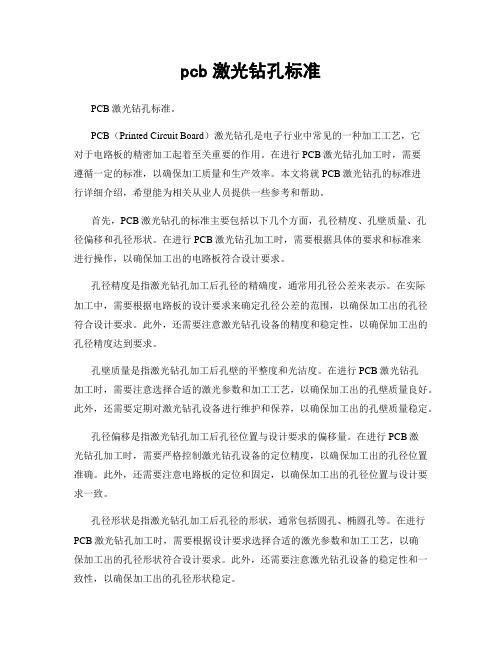
pcb激光钻孔标准PCB激光钻孔标准。
PCB(Printed Circuit Board)激光钻孔是电子行业中常见的一种加工工艺,它对于电路板的精密加工起着至关重要的作用。
在进行PCB激光钻孔加工时,需要遵循一定的标准,以确保加工质量和生产效率。
本文将就PCB激光钻孔的标准进行详细介绍,希望能为相关从业人员提供一些参考和帮助。
首先,PCB激光钻孔的标准主要包括以下几个方面,孔径精度、孔壁质量、孔径偏移和孔径形状。
在进行PCB激光钻孔加工时,需要根据具体的要求和标准来进行操作,以确保加工出的电路板符合设计要求。
孔径精度是指激光钻孔加工后孔径的精确度,通常用孔径公差来表示。
在实际加工中,需要根据电路板的设计要求来确定孔径公差的范围,以确保加工出的孔径符合设计要求。
此外,还需要注意激光钻孔设备的精度和稳定性,以确保加工出的孔径精度达到要求。
孔壁质量是指激光钻孔加工后孔壁的平整度和光洁度。
在进行PCB激光钻孔加工时,需要注意选择合适的激光参数和加工工艺,以确保加工出的孔壁质量良好。
此外,还需要定期对激光钻孔设备进行维护和保养,以确保加工出的孔壁质量稳定。
孔径偏移是指激光钻孔加工后孔径位置与设计要求的偏移量。
在进行PCB激光钻孔加工时,需要严格控制激光钻孔设备的定位精度,以确保加工出的孔径位置准确。
此外,还需要注意电路板的定位和固定,以确保加工出的孔径位置与设计要求一致。
孔径形状是指激光钻孔加工后孔径的形状,通常包括圆孔、椭圆孔等。
在进行PCB激光钻孔加工时,需要根据设计要求选择合适的激光参数和加工工艺,以确保加工出的孔径形状符合设计要求。
此外,还需要注意激光钻孔设备的稳定性和一致性,以确保加工出的孔径形状稳定。
总之,PCB激光钻孔标准对于电路板的加工质量和生产效率起着至关重要的作用。
在进行PCB激光钻孔加工时,需要严格遵循相关标准和要求,以确保加工出的电路板符合设计要求。
希望本文能为相关从业人员提供一些参考和帮助,让他们能够更好地掌握PCB激光钻孔的标准和技术要点。
PCB机械钻孔.pptx

18
Compound Beam
Positioner
Galvo XY
355nm UV 266nm UV 9.24um CO2
Input Beam
Linear Motor X Linear Motor Y
19
三 钻孔的设备介绍:
磨钻咀机
磨钻 咀机
解释
磨钻咀能 砂轮试用粗糙度 力
手动
由马达带动两个砂轮转动, 分为初级及次级,待磨钻咀 放入已调好翻磨钻尖角度的 索咀夹头内,使用放大镜调 好翻磨深度后,控制机台移 动,带动夹着钻咀的索咀移 向砂轮,经过 初级及次级砂 轮打磨钻尖位置
13
三 钻孔的设备介绍:
14
三 钻孔的设备介绍:
间隙示意图
主轴剖面图
两种主轴对比图 主轴运转温显
15
三 钻孔的设备讲解:
钻针直径测量仪 验孔机
X-RAY检查机
主轴摆幅测量仪
2D测量仪
16
三 钻孔的设备介绍:
3次元测量仪
17
三 钻孔的设备介绍:
UV 和CO2激光钻机
激光 波长 能量密度(光
PLC是一种专门为在工业环境下应用而设计的数字运算操作的电子装置。它采用可以编制程序的存储器, 用来在其内部存储执行逻辑运算、顺序运算、计时、计数和算术运算等操作的指令,并能通过数字式或模 拟式的输入和输出,控制各种类型的机械或生产过程。
联轴器所联两轴由于制造误差、安装误差、轴受载而产生的变形、基座变形、轴承磨损、温度变化(热胀、 冷缩)、部件之间的相对运动等多种因素而产生相对位移。
7
二 钻孔的基本物料介绍:
钻刀 作用:通过钻机在高转速和一定落速带动下钻穿线路板。 要求:钻刀直径、钻尖面;材质有一定韧性、硬度及耐磨性能。
PCB电路板术语
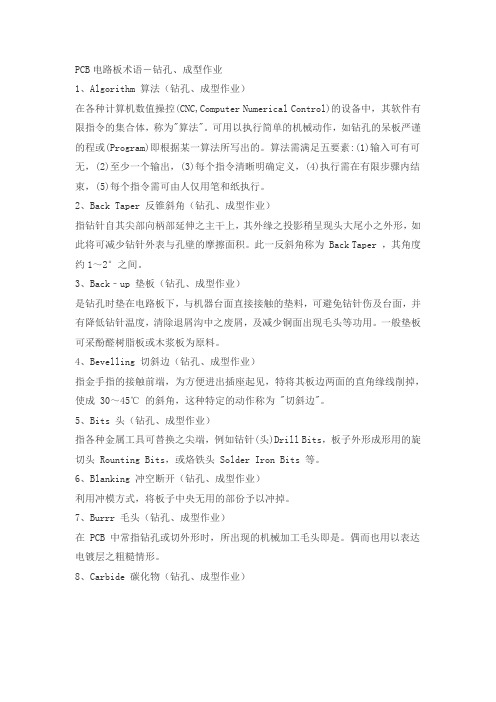
PCB电路板术语-钻孔、成型作业1、Algorithm 算法(钻孔、成型作业)在各种计算机数值操控(CNC,Computer Numerical Control)的设备中,其软件有限指令的集合体,称为"算法"。
可用以执行简单的机械动作,如钻孔的呆板严谨的程或(Program)即根据某一算法所写出的。
算法需满足五要素:(1)输入可有可无,(2)至少一个输出,(3)每个指令清晰明确定义,(4)执行需在有限步骤内结束,(5)每个指令需可由人仅用笔和纸执行。
2、Back Taper 反锥斜角(钻孔、成型作业)指钻针自其尖部向柄部延伸之主干上,其外缘之投影稍呈现头大尾小之外形,如此将可减少钻针外表与孔壁的摩擦面积。
此一反斜角称为 Back Taper ,其角度约1~2°之间。
3、Back﹣up 垫板(钻孔、成型作业)是钻孔时垫在电路板下,与机器台面直接接触的垫料,可避免钻针伤及台面,并有降低钻针温度,清除退屑沟中之废屑,及减少铜面出现毛头等功用。
一般垫板可采酚醛树脂板或木浆板为原料。
4、Bevelling 切斜边(钻孔、成型作业)指金手指的接触前端,为方便进出插座起见,特将其板边两面的直角缘线削掉,使成 30~45℃ 的斜角,这种特定的动作称为 "切斜边"。
5、Bits 头(钻孔、成型作业)指各种金属工具可替换之尖端,例如钻针(头)Drill Bits,板子外形成形用的旋切头 Rounting Bits,或烙铁头 Solder Iron Bits 等。
6、Blanking 冲空断开(钻孔、成型作业)利用冲模方式,将板子中央无用的部份予以冲掉。
7、Burrr 毛头(钻孔、成型作业)在 PCB 中常指钻孔或切外形时,所出现的机械加工毛头即是。
偶而也用以表达电镀层之粗糙情形。
8、Carbide 碳化物(钻孔、成型作业)在 PCB 工业中,此字最常出现在钻孔所用的钻针(头)上,这种耗材的主要成份为"碳化钨Tungsten Carbide (WC),约占94%,其余6%为金属钴粉(当成黏结)。
PCB参数
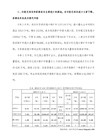
8,超常规设计,一定要说明一下,有时候我们工程人员会认为设计错误,直接改正;例如:喷锡的文字;焊盘上面全部或者部分加阻焊,贴片元件的部分焊盘阻焊,SMT焊盘带通孔的,等等的问题,需要简单说明一下,以免我们工程认为是设计疏忽,而修改。
9:多层线(Multilayer)是不会喷锡的:设计的时候请一定注意,看起来好像是同焊盘一样的,实际上是不会做成焊盘的,并且会在顶层和底层都产生走线,请注意!
补充说明:对于设计上面有问题的话,千万不要说,上次是对的,这次一定是对的,或者说,同时做了两款,一个正确,一个不正确。很多时候,我们工程师会帮您改正,但是错误的设计,总有一天会出错,一定要改善并完善设计的问题。
3,solder【阻焊层】和paste【钢网层】的用法以及产生的问题:任何时候,PCB上面不会用直接到paste层,这个是用来做钢网的,如果设计人员不需要用这个,建议无理由关闭,基本不影响设计,但是如果提供的文件包含了这个板层,我们工程师有可能会同solder叠加使用,也有可能不叠加使用,这个请注意,另外paste层不会用做阻焊开窗;但是在使用solder做阻焊开窗的时候,切记:如果需要做出焊盘的效果,绝对不能单独放置solder数据,例如:一条镀锡的线条,只是用solder画线,肯定不会做出需要的效果的(工程有可能会修改,但是这个是错误的设计,总有一天会出错),正确的做法是:先在线路层画线后,再用solder在线路上面画线才可以达到设计要求!
最小槽刀
0.65mm
板内最小有铜槽宽10mil)
锣板出货,线路层走线距板子外形线的距离不小于0.25mm;V割拼板出货,走线距V割中心线距离不能小于0.4mm
半孔工艺最小半孔孔径
0.6mm
半孔工艺是一种特殊工艺,最小孔径不得小于0.6mm
PCB钻孔流程1

PCB钻孔流程(一)一、目的:1.1提高员工对制程的了解及品质意识,使其能迅速上岗,达成产能及品质目标。
二、适用范围:2.1 仅适用于PCB钻孔的工程师与领班。
三、相关权责:3.1 PCB钻孔。
四、名词定义:4.1无五、相关文件:5.1无六、培训内容:6.1钻孔的作用及细步流程介绍6.2各流程的作用及注意事项6.3制程控制的工艺参数6.4品质检测与处理6.5技术员工作职掌6.6不良板重工流程6.7 保养规范6.8不良原因及改善对策6.9点检项目记录表单PCB钻孔流程(二)6.1钻孔的作用及细步流程介绍:6.1.1钻孔作用:用来对PCB进行切削孔位,便于插件及导通之作业。
6.1.2钻孔的细步流程介绍:进料→准备PCB钻咀→钻孔→检验→出货6.1.3钻孔的环境要求:温度:20±2℃相对湿度:50±5%6.1.4钻孔的主物料介绍:6.1.4.1垫板(2.5mm):6.1.4.1.1作用:a.防止钻机台面受损;b.减少出口性毛头;c.减少钻咀扭断;d.降低钻咀温度;e.清洁钻咀沟槽中之胶渣。
6.1.4.1.2板材种类:a.复合材料——其制造法与纸质基板类似,但木屑为基础,再混合含酸或盐类的粘著剂,高温高压下压合硬化成为一体而硬度很高的板子。
b.酚醛树脂板——价格比上述的合板要贵一些,也就是一般单面板的基材。
c.铝箔压合板——同盖板一样。
d.Vbu垫板——是指Vented Back up垫板,上、下两面铝箔,中层为折曲同质的纯铝箔,空气可以自由流通其间,如石棉浪一样。
垫板的选择一样依各厂条件来评估,其重点在:不含有机油脂,屑够软不伤孔壁,表面够硬,板厚均匀、平整等。
操作CNC控制现有CAD/CAM工作站都可直接转换钻孔机接受之语言只要设定一些参数如各孔代号代表之孔径即可。
6.1.4.2铝片(0.2mm),也称盖板:6.1.4.2.1作用:a.防止压力脚直接压伤铜面;b.使钻尖容易中心定位;c.减少进口性毛头;d.利于散热;e.钻咀进、退时的清洁。
PCB钻头及钻孔相关知识

PPT文档演模板
2020/11/3
PCB钻头及钻孔相关知识
•我司钻头材料的特点:
•■直径<1.6mm:
钻头本体 与把柄采用两段 镶嵌式,本体材料为碳化 钨,把柄采用不锈钢
•■直径>1.6mm:
钻头本体 与把柄采用整体 式,本体与把柄材料均为碳 化钨。
PPT文档演模板
PCB钻头及钻孔相关知识
• ■MD 型
MD: 微钻(直径<0.3),ST结构 MC: 微钻(直径<0.3),UC结构 MCV:两段倒锥微钻(直径<0.3)
■ID型
ID30: 30度螺旋角大钻 ID30C: 带断屑槽大钻
PPT文档演模板
PCB钻头及钻孔相关知识
钻头的基本参数:
•钻尖角 •直径
•Under cue 直 径
•把柄直径
ST型和UC型的形状 (优点)
■ST型 基本上再研磨次数比UC型多
•■UC型
•
因減少和基板接触的面積
•
所以可提昇孔壁品質
PPT文档演模板
PCB钻头及钻孔相关知识
ST型和UC型的形状
•结构不同点:
■ST型
UC型的设计优势 ST/STX的设计优势
高质量的钻孔品质, 操作简单,直径控 低的钻孔温度,低 制容易,较多的研 的钉头、胶渣、折 磨次数 断率现象。
•Number of Samples: 2
PPT文档演模板
PCB钻头及钻孔相关知识
高速加工的優点
■相同之Chip Load, 加工時間的差異
•沟长 •本体
长
PPT文档演模板
•全长
PCB钻头及钻孔相关知识
钻头的基本参数:
多轴钻孔机pcb钻孔机

厂家:润联网
市场价格:19440元-27540元
标题:金刚石钻孔机和水钻钻孔机参数
一、性能特点该机美观大方、设计新颖,技术先进、制作精度高,操作方便、灵活,运行稳定可靠,工作效率高。该机没有校刀装置,可保证钻孔深度的需要。 二、主要用途该机一次可以加工垂直位置6个孔位,其中2个大孔为铰链头孔,4个为装配螺丝孔。每组钻头可分开单独工作 ,是生产中小型板式家具的理想工具。电机功率————1.1x2KW最大加工规格—————1600mm钻孔深度—&mda
订货号:JX076248
厂家:润联网
市场价格:15000元-21250元
标题:冲击钻孔机和双头铰链钻孔机参数
规格参数表 最大钻孔直径 Max.=80mm(单钻头)最大钻孔深度H max=60mm钻轴总数2个钻接头装配直径Ø10mm、Ø12.7mm工作气压0.6 ~ 0.9Mpa电机总功率2.2X2kw主轴转速2840rpm外型尺寸1600x900x1700mm机器重量700kg
订货号:JX076252
厂家:润联网
市场价格:10800元-15300元
标题:自动钻孔机和多功能钻孔机说明书
产品名称:活页钻孔机MZ4215(五头铰链钻)最大钻孔直径Max.drillingdia∮35mm最大钻孔深度Max.drillingdepth70mm两垂直钻排最小中心距Min。distancebetweentwocentreofverticaldrillrows180mm钻轴数Totaonumberofdrillingshafts15个主轴转速Rotatingspeedofprincipalshaft2825rpm电机总功率Totalpowerofmotoer1.1kw×5外形尺
pcb钻孔钉头标准范围

pcb钻孔钉头标准范围
PCB钻孔钉头标准范围包括以下几个方面:
1. 孔径范围:PCB钻孔钉头的孔径范围一般在0.2mm到1.0mm之间,不同孔径的钉头用于不同的PCB层压材料和线路宽度。
2. 钉头高度:PCB钻孔钉头的钉头高度应该与PCB的厚度相匹配,一般需要在PCB表面突出0.1mm到0.2mm左右,以保证钉头能够牢固地插入PCB中。
3. 钉头形状:PCB钻孔钉头的钉头形状应该与PCB的线路图案相匹配,一般采用圆形、方形、六角形等常见形状,以便于插入和固定。
4. 钉头材料:PCB钻孔钉头的材料应该具有较高的硬度和耐磨性,一般采用高速钢、钨钢等材料制造。
5. 钉头表面处理:PCB钻孔钉头的表面应该进行硬化处理,以提高钉头的耐磨性和使用寿命。
总之,PCB钻孔钉头标准范围应该根据不同的PCB层压材料和线路宽度进行选择,同时需要注意钉头的高度、形状、材料和表面处理等方面,以确保在使用过程中能够牢固地插入和固定,并提高使用寿命。
70PCB钻头及钻孔相关知识

Speed
Positioning Accuracy
Spindle
Ring
Precision
Pressure Force
Material Preparation
Repointing
Repointing
PCB
Vibration
Bush
Set up
Resin
Content
Surface
Roughness
Copper
V=pDN/1000
V:周速(m/min) p :圆周率 D:鑽頭外径(mm) N:主軸転数(RPM)
理論主軸転数
高速加工的優点
■相同之Chip Load, 不同転速的品質傾向
高速加工的優点
■相同之Chip Load, 孔位精度的差異
CONDITIONS
PWB: FR-4(DS) 0.6mm x 2s
UNION TOOL CO. TECHNICAL RESEARCH
釘頭
■現象 鑽孔時内層銅箔不能被順利切削、反
而受到拉力延展変形為像釘子頭部形 状。
ST type
UNION TOOL CO. TECHNICAL RESEARCH
釘頭
■対策 減少鑽頭與孔壁接触的面積 (使用UC型) 加快進刀速 撃孔数、畳板数重新検討
ST型和UC型的形状
结构不同点:
■ST型
UC型的设计优势 ST/STX的设计优势
高质量的钻孔品质 ,低的钻孔温度, 低的钉头、胶渣、 折断率现象。
低的折损率,减少 了钻孔扭矩阻力。
操作简单,直径控 制容易,较多的研 磨次数
较大的使用范围, 使用于一般用途
■UC型
利于微钻和6层以上 利于一般直径钻头
PCB 常见缺陷知识整理分享一

PCB 常见缺陷知识整理分享一一﹑基材缺陷:1. 白点:在玻璃纤维经纬交织处,树脂与点间发生局部分离產生缝隙,因光折射而看到的基材内之小白圆点。
2. 白斑:基材内局部的玻纤布与环氧树脂之间,或布材本身的纱束之间出现分裂,由外表可看到白色区域的现象。
3. 凹陷:铜面呈现缓和均匀的下陷。
(如限度样品)4. 针孔:目视铜面上可见类似针尖状小点。
5. 毛头:板边出现粗糙的基材纤维或不平整凹凸状的铜屑。
6. 织纹显露:板材表面的树脂层已经破损流失,致使板内的玻纤布曝露出来,板面呈现白色条状“+”的情形。
7. 气泡:指多层板金属层与树脂层之间或各玻纤布间的局部区域发生膨胀及分层,面积在0.16㎜2以上。
8. 基材分层:指压合基材中层次间的分离,或是基材与导体铜箔之分离﹔或电路板内任何其它平面性的分离。
9. 基材异物(外来夹杂物) :指绝缘体材料内都可能陷入的金属或非金属杂物,距离最近导体在0.125mm 以外时可允收。
10. 织纹縐显:基材表面玻纤布之织纹已可察见,但没有断裂玻纤织纹仍被树脂所完全覆盖。
11. 板皱:基材表面出现的波纹状或V 状下陷。
二﹑内印缺陷:1. 显影过度:因曝光能量不足或显影速度过慢使不该显影掉的油墨被显影掉,油墨过缘呈现不平锯齿状。
2. 显影不净:被显影掉油墨的铜面上残留一层很薄的油墨,使铜面无光泽呈现白雾状。
3. 内短:内层因残铜或P.P 胶绝缘不良而致使同一层相隔区域间或层间短路。
4. 内断:因内层线路断开,螃蟹脚被咬蚀掉或孔壁与螃蟹脚隔离而造成内层或层与层间断开。
5. 裁板不良:裁板到成型线以内。
6. 内层偏移:内层对位对准度不够,使内层图形向一方偏移。
(如限度样品)7. 板面残胶:板面残留有软性胶状物质。
8. 点状断线:经蚀刻后板面线路上有细小的点状断路。
9. 线细:线径低于客户要求之下限或原稿线径之20%。
10. 线路锯齿:线路局部缺口,凸点交错呈现锯齿状。
11. 刮伤:板面镀层或涂覆层因外力受损,且超过其厚度的20%以上。
pcb钻孔常见问题和改善措施

pcb钻孔常见问题和改善措施
PCB钻孔过程中常见的问题主要包括钻孔偏移、孔位不正、钻孔深度不合适、孔径不准确、孔内有毛刺、孔边有缺口等。
针对这些问题,可以采取以下改善措施:
1. 钻孔偏移:检查主轴是否偏转,减少叠板数量,增加钻头转速或降低进刀速率,重新检查钻头是否符合工艺要求,检查钻头顶尖是否具备良好同心度,检查钻头与弹簧夹头之间的固定状态是否紧固,重新检测和校正钻孔工作台的稳定和稳定性。
2. 孔位不正:检查钻头是否符合工艺要求,重新刃磨钻头,检查钻头是否合适,检查工作台是否水平,调整工作台的平行度,检查钻头与弹簧夹头之间的固定状态是否紧固。
3. 钻孔深度不合适:根据不同的板材厚度选择合适的钻咀长度和进刀量,适当调整钻孔的吸尘力。
4. 孔径不准确:检查钻咀的几何外形和磨损情况,选择合适的进刀量和转速,适当调整压力脚气管道是否有堵塞,调整压力脚与钻头之间的状态。
5. 孔内有毛刺:适当调整进刀速率,增加刀补值,选择合适的切削液,检查刀具是否锋利。
6. 孔边有缺口:检查刀具是否锋利,适当调整进刀速率和刀补值,增加压力脚气管道的压力,选择合适的切削液。
除了以上措施,还可以采取以下措施来提高钻孔质量和效率:
1. 选择合适的钻头材料和几何形状,根据不同的加工条件和材料选择合适的切削参数。
2. 定期检查和维护钻头和刀具,及时更换磨损和损坏的刀具。
3. 优化加工工艺流程,减少加工过程中的停顿和等待时间。
4. 提高操作人员的技能水平和工作责任心,加强对加工过程的监控和管理。
5. 采用先进的加工设备和控制系统,提高加工精度和效率。
PCB钻孔基础介绍
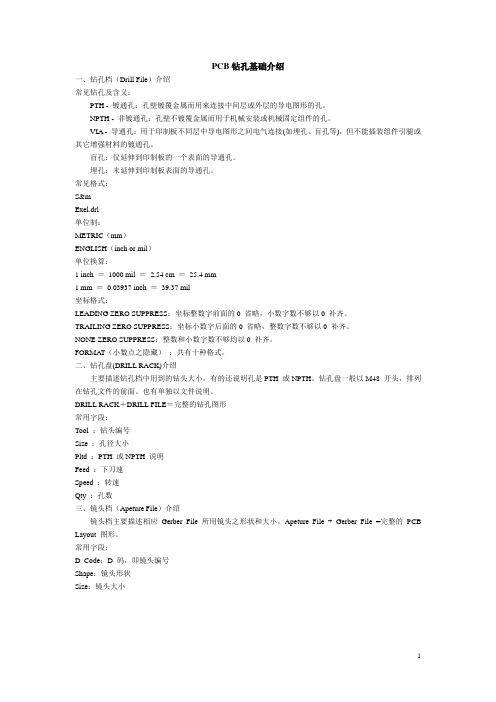
PCB钻孔基础介绍一、钻孔档(Drill File)介绍常见钻孔及含义:PTH - 镀通孔:孔壁镀覆金属而用来连接中间层或外层的导电图形的孔。
NPTH - 非镀通孔:孔壁不镀覆金属而用于机械安装或机械固定组件的孔。
VIA - 导通孔:用于印制板不同层中导电图形之间电气连接(如埋孔、盲孔等),但不能插装组件引腿或其它增强材料的镀通孔。
盲孔:仅延伸到印制板的一个表面的导通孔。
埋孔:未延伸到印制板表面的导通孔。
常见格式:S&mExel.drl单位制:METRIC(mm)ENGLISH(inch or mil)单位换算:1 inch =1000 mil =2.54 cm =25.4 mm1 mm =0.03937 inch =39.37 mil坐标格式:LEADING ZERO SUPPRESS:坐标整数字前面的0 省略,小数字数不够以0 补齐。
TRAILING ZERO SUPPRESS:坐标小数字后面的0 省略,整数字数不够以0 补齐。
NONE ZERO SUPPRESS:整数和小数字数不够均以0 补齐。
FORMA T(小数点之隐藏):共有十种格式。
二、钻孔盘(DRILL RACK)介绍主要描述钻孔档中用到的钻头大小,有的还说明孔是PTH 或NPTH。
钻孔盘一般以M48 开头,排列在钻孔文件的前面。
也有单独以文件说明。
DRILL RACK+DRILL FILE=完整的钻孔图形常用字段:Tool :钻头编号Size :孔径大小Pltd :PTH 或NPTH 说明Feed :下刀速Speed :转速Qty :孔数三、镜头档(Apeture File)介绍镜头档主要描述相应Gerber File 所用镜头之形状和大小。
Apeture File + Gerber File =完整的PCB Layout 图形。
常用字段:D_Code:D 码,即镜头编号Shape:镜头形状Size:镜头大小1。
PCB常见缺陷知识整理分享一
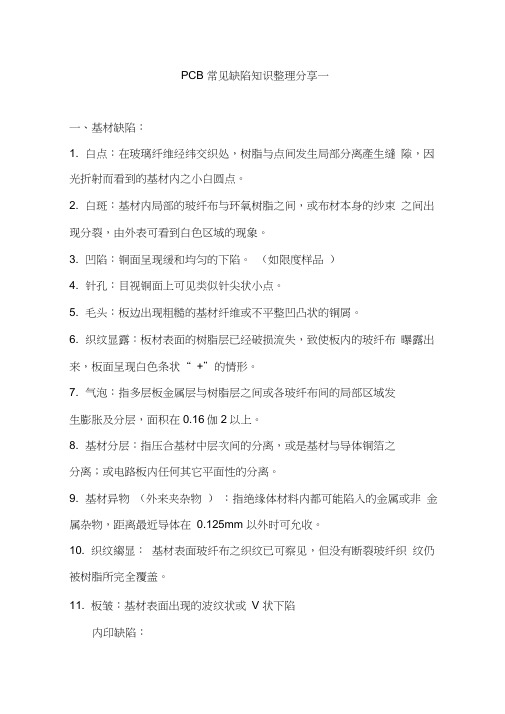
PCB 常见缺陷知识整理分享一一、基材缺陷:1. 白点:在玻璃纤维经纬交织处,树脂与点间发生局部分离產生缝隙,因光折射而看到的基材内之小白圆点。
2. 白斑:基材内局部的玻纤布与环氧树脂之间,或布材本身的纱束之间出现分裂,由外表可看到白色区域的现象。
3. 凹陷:铜面呈现缓和均匀的下陷。
(如限度样品)4. 针孔:目视铜面上可见类似针尖状小点。
5. 毛头:板边出现粗糙的基材纤维或不平整凹凸状的铜屑。
6. 织纹显露:板材表面的树脂层已经破损流失,致使板内的玻纤布曝露出来,板面呈现白色条状“ +”的情形。
7. 气泡:指多层板金属层与树脂层之间或各玻纤布间的局部区域发生膨胀及分层,面积在0.16伽2以上。
8. 基材分层:指压合基材中层次间的分离,或是基材与导体铜箔之分离;或电路板内任何其它平面性的分离。
9. 基材异物(外来夹杂物):指绝缘体材料内都可能陷入的金属或非金属杂物,距离最近导体在0.125mm 以外时可允收。
10. 织纹縐显:基材表面玻纤布之织纹已可察见,但没有断裂玻纤织纹仍被树脂所完全覆盖。
11. 板皱:基材表面出现的波纹状或V 状下陷内印缺陷:1. 显影过度:因曝光能量不足或显影速度过慢使不该显影掉的油墨被显影掉,油墨过缘呈现不平锯齿状。
2. 显影不净:被显影掉油墨的铜面上残留一层很薄的油墨,使铜面无光泽呈现白雾状。
3. 内短:内层因残铜或P.P 胶绝缘不良而致使同一层相隔区域间或层间短路。
4. 内断:因内层线路断开,螃蟹脚被咬蚀掉或孔壁与螃蟹脚隔离而造成内层或层与层间断开。
5. 裁板不良:裁板到成型线以内。
6. 内层偏移:内层对位对准度不够,使内层图形向一方偏移。
(如限度样品)7. 板面残胶:板面残留有软性胶状物质。
8. 点状断线:经蚀刻后板面线路上有细小的点状断路。
9. 线细:线径低于客户要求之下限或原稿线径之20% 。
10. 线路锯齿:线路局部缺口,凸点交错呈现锯齿状。
11. 刮伤:板面镀层或涂覆层因外力受损,且超过其厚度的20% 以上。
PCB印制板外形加工的方法解析
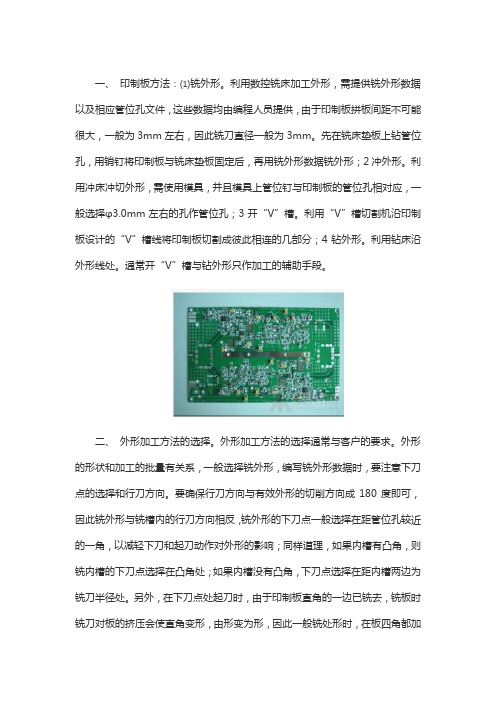
一、印制板方法:⑴铣外形。
利用数控铣床加工外形,需提供铣外形数据以及相应管位孔文件,这些数据均由编程人员提供,由于印制板拼板间距不可能很大,一般为3mm左右,因此铣刀直径一般为3mm。
先在铣床垫板上钻管位孔,用销钉将印制板与铣床垫板固定后,再用铣外形数据铣外形;2冲外形。
利用冲床冲切外形,需使用模具,并且模具上管位钉与印制板的管位孔相对应,一般选择φ3.0mm左右的孔作管位孔;3开“V”槽。
利用“V”槽切割机沿印制板设计的“V”槽线将印制板切割成彼此相连的几部分;4钻外形。
利用钻床沿外形线处。
通常开“V”槽与钻外形只作加工的辅助手段。
二、外形加工方法的选择。
外形加工方法的选择通常与客户的要求。
外形的形状和加工的批量有关系,一般选择铣外形,编写铣外形数据时,要注意下刀点的选择和行刀方向。
要确保行刀方向与有效外形的切削方向成180度即可,因此铣外形与铣槽内的行刀方向相反,铣外形的下刀点一般选择在距管位孔较近的一角,以减轻下刀和起刀动作对外形的影响;同样道理,如果内槽有凸角,则铣内槽的下刀点选择在凸角处;如果内槽没有凸角,下刀点选择在距内槽两边为铣刀半径处。
另外,在下刀点处起刀时,由于印制板直角的一边已铣去,铣板时铣刀对板的挤压会使直角变形,由形变为形,因此一般铣处形时,在板四角都加一半径为0.8mm的圆角,使直角形变为形。
当印制板单元内无法加管位孔时则在拼板板边加管位孔,印制板单元间加吊点,铣外形后,用锉刀锉去吊点。
冲外形能够适应大批量生产的需要,加工效率高,通常管位孔的选择对外形加工质量和加工效率有较大影响。
三、“V”槽和钻外形是外形加工非常有效的辅助手段。
其中开“V”槽是较常用的外形加工辅助手段。
当印制板单元尺寸较小时,为减少铣板时间,可将几个印制板拼为一个单元,铣外形后再开“V”槽,这不仅提高了外形加工的效率,而且也有利于板件清洗和产品,还提高了板料利用率,对于不能加管位孔且尺寸较小的印制板,还可减少吊点数量(锉去吊点是非常麻烦的工作),这对批量较大的板件很有利。
pcb钻槽孔参数

PCB钻槽孔参数简介PCB(Printed Circuit Board,印刷电路板)是现代电子设备中不可或缺的组成部分。
在PCB制造过程中,钻槽孔是非常重要的一个环节。
钻槽孔是用来固定PCB板之间的连接或安装电子元器件的孔洞。
本文将详细介绍PCB钻槽孔的参数,包括钻槽孔的尺寸、形状、位置等。
钻槽孔尺寸钻槽孔的尺寸是指钻孔的直径和深度。
钻孔的直径决定了钻槽孔的大小,而深度决定了钻槽孔的穿透程度。
直径钻孔的直径是钻槽孔尺寸的关键参数之一。
直径的选择需要考虑到PCB板的厚度、所安装的元器件尺寸等因素。
一般来说,钻孔的直径应略大于安装元器件的引脚直径,以确保引脚能够顺利穿过钻槽孔。
深度钻孔的深度是指钻孔从PCB板顶层到底层的距离。
深度的选择需要根据PCB板的厚度和钻孔的用途来确定。
如果钻孔用于连接两个PCB板,深度应足够以确保两个板子能够牢固连接。
而如果钻孔用于安装元器件,深度应足够以确保元器件能够稳固地固定在PCB板上。
钻槽孔形状钻槽孔的形状是指钻孔的截面形状。
常见的钻槽孔形状有圆形、方形和椭圆形。
圆形圆形钻槽孔是最常见的形状,因为圆形钻槽孔易于加工和安装。
圆形钻槽孔可以通过钻孔机器进行加工,而且在安装元器件时也较为方便。
方形方形钻槽孔适用于需要固定PCB板之间位置的应用。
方形钻槽孔的边长应根据需要来确定,以确保PCB板能够准确地对齐。
椭圆形椭圆形钻槽孔适用于需要调节位置的应用。
椭圆形钻槽孔的长短轴比例可以根据需要来确定,以实现位置的微调。
钻槽孔位置钻槽孔的位置是指钻孔在PCB板上的坐标位置。
钻槽孔的位置需要根据PCB板的设计要求来确定。
绝对位置绝对位置是指钻孔在PCB板上的绝对坐标位置。
绝对位置一般是由PCB设计师在设计过程中确定的,用于确保钻槽孔的位置准确无误。
相对位置相对位置是指钻孔相对于其他元素的位置。
相对位置可以通过与其他元素的相对距离来确定,以实现元素之间的相对布局。
钻槽孔参数的影响因素钻槽孔参数的选择受到多种因素的影响,包括PCB板的设计要求、元器件尺寸、机械加工能力等。
pcb教材-06钻孔

六、鑽孔6.1 製程目的單面或雙面板的製作都是在下料之後直接進行非導通孔或導通孔的鑽孔, 多層板則是在完成壓板之後才去鑽孔。
傳統孔的種類除以導通與否簡單的區分外,以功能的不同尚可分:零件孔,工具孔,通孔(Via),盲孔(Blind hole),埋孔(Buried hole)(後二者亦為via hole的一種).近年電子產品'輕.薄.短.小.快.'的發展趨勢,使得鑽孔技術一日千里,機鑽,雷射燒孔,感光成孔等,不同設備技術應用於不同層次板子.本章僅就機鑽部分加以介紹,其他新技術會在20章中有所討論.6.2 流程上PIN→鑽孔→檢查6.3上PIN作業鑽孔作業時除了鑽盲孔,或者非常高層次板孔位精準度要求很嚴,用單片鑽之外,通常都以多片鑽,意即每個stack兩片或以上.至於幾片一鑽則視1.板子要求精度2.最小孔徑3.總厚度4.總銅層數.來加以考量. 因為多片一鑽,所以鑽之前先以pin將每片板子固定住,此動作由上pin機(pinning maching)執行之. 雙面板很簡單,大半用靠邊方式,打孔上pin連續動作一次完成.多層板比較複雜,另須多層板專用上PIN機作業.6.4. 鑽孔6.4.1鑽孔機鑽孔機的型式及配備功能種類非常多,以下List評估重點A. 軸數:和產量有直接關係B. 有效鑽板尺寸C. 鑽孔機檯面:選擇振動小,強度平整好的材質。
D. 軸承(Spindle)E. 鑽盤:自動更換鑽頭及鑽頭數F. 壓力腳G. X、Y及Z軸傳動及尺寸:精準度,X、Y獨立移動H. 集塵系統:搭配壓力腳,排屑良好,且冷卻鑽頭功能I. Step Drill的能力J. 斷針偵測K. RUN OUT6.4.1.1鑽孔房環境設計A. 溫濕度控制B. 乾淨的環境C. 地板承受之重量D. 絕緣接地的考量E. 外界振動干擾6.4.2 物料介紹鑽孔作業中會使用的物料有鑽針(Drill Bit),墊板(Back-up board),蓋板(Entry board)等.以下逐一介紹:圖6.1為鑽孔作業中幾種物料的示意圖.6.4.2.1 鑽針(Drill Bit), 或稱鑽頭,其品質對鑽孔的良窳有直接立即的影響, 以下將就其材料,外型構、及管理簡述之。
PCB工艺流程主要缺陷、产生原因及其处理方法-钻孔_层压_外形_内层短路

PDF 文 件 以 "PDF 制 作 工 厂 " 试 用 版 创 建
~18~
§ 2、 多 铣 :
产生原因: 1、 板 翘 ; 2、 程 序 错 ; 3、 放 反 板 ; 4、 漏 打 销 钉
纠正预防措施: 1、 外 形 前 压 板 翘 ; 2、 修 正 程 序 。 3、 上 板 前 检 查 方 向 孔 ; 4、 打 完 销 钉 后 检 查 是 否 有 漏 打 。
度、大小);
§ 2、 调 整 进 刀 速 率 和 转 速 至 最 理 想 状 态 。 § 3、 更 换 合 格 钻 头 , 并 限 制 每 支 钻 头 钻 孔 数
量。
§ 4、 限 制 钻 头 重 磨 的 次 数 及 重 磨 尺 寸 变 化 。 § 5、 钻 孔 前 用 20倍 镜 检 查 刀 面 , 将 不 良 钻 头 返
PDF 文 件 以 "PDF 制 作 工 厂 " 试 用 版 创 建
~7~
6、 层 压 分 层 起 泡 :
缺陷形成原因: 1、 铜 皮 或 基 材 表 面 有 污 染 、 杂 物 、 水 气、气泡等; 2、 粘 结 片 挥 发 物 含 量 高 , 氧 化 不 正 常 等 等~ 3、 压 合 参 数 不 当 , 固 化 不 足 。 4、 板 子 受 潮 。 解决方案: 1、 内 层 压 合 前 烘 板 ( 特 别 是 厚 芯 板 、 厚 铜板、盲埋孔板等);改善存放环境, 粘 结 片 必 须 在 移 出 真 空 干 燥 环 境 后 于 15 分钟内用完;改善操作,避免触摸粘结 面有效区; 2、 加 强 氧 化 操 作 后 的 清 洗 ; 监 测 清 洗 水 的 PH值 ; 缩 短 氧 化 时 间 、 调 整 氧 化 液 浓 度或操作温度,增加微蚀刻,改善表面 状态; 3、 按 规 范 设 定 压 合 程 序 。 4、 压 合 后 进 行 退 应 力 处 理 。
pcb钻槽孔参数
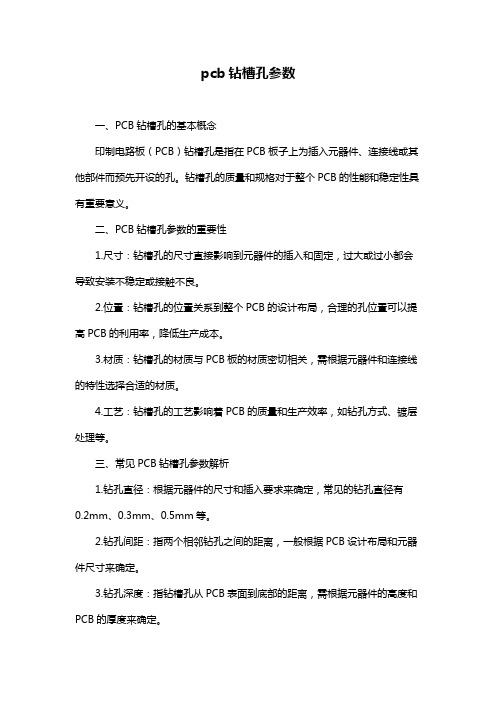
pcb钻槽孔参数一、PCB钻槽孔的基本概念印制电路板(PCB)钻槽孔是指在PCB板子上为插入元器件、连接线或其他部件而预先开设的孔。
钻槽孔的质量和规格对于整个PCB的性能和稳定性具有重要意义。
二、PCB钻槽孔参数的重要性1.尺寸:钻槽孔的尺寸直接影响到元器件的插入和固定,过大或过小都会导致安装不稳定或接触不良。
2.位置:钻槽孔的位置关系到整个PCB的设计布局,合理的孔位置可以提高PCB的利用率,降低生产成本。
3.材质:钻槽孔的材质与PCB板的材质密切相关,需根据元器件和连接线的特性选择合适的材质。
4.工艺:钻槽孔的工艺影响着PCB的质量和生产效率,如钻孔方式、镀层处理等。
三、常见PCB钻槽孔参数解析1.钻孔直径:根据元器件的尺寸和插入要求来确定,常见的钻孔直径有0.2mm、0.3mm、0.5mm等。
2.钻孔间距:指两个相邻钻孔之间的距离,一般根据PCB设计布局和元器件尺寸来确定。
3.钻孔深度:指钻槽孔从PCB表面到底部的距离,需根据元器件的高度和PCB的厚度来确定。
4.钻孔形状:常见的钻孔形状有圆形、方形、三角形等,可根据实际需求和工艺要求选择。
5.镀层:钻槽孔表面一般需要进行镀层处理,以提高孔的导电性和抗氧化能力。
常见的镀层有铜、镍、金等。
四、如何选择合适的PCB钻槽孔参数1.分析元器件和连接线的特性,确定钻槽孔的尺寸、间距和深度。
2.根据PCB的设计布局和工艺要求,选择合适的钻孔形状和镀层。
3.考虑钻槽孔的兼容性,确保各种元器件和连接线的安装需求得到满足。
4.咨询专业人士或参考行业标准,以确保所选参数的合理性和可行性。
五、总结与建议PCB钻槽孔参数的选择对于整个PCB的性能和稳定性具有重要影响。
在进行钻槽孔参数选择时,应充分考虑元器件、连接线、设计布局和工艺等多方面因素,以确保PCB钻槽孔的质量和实用性。
pcb钻孔机的操作技术及流程详解
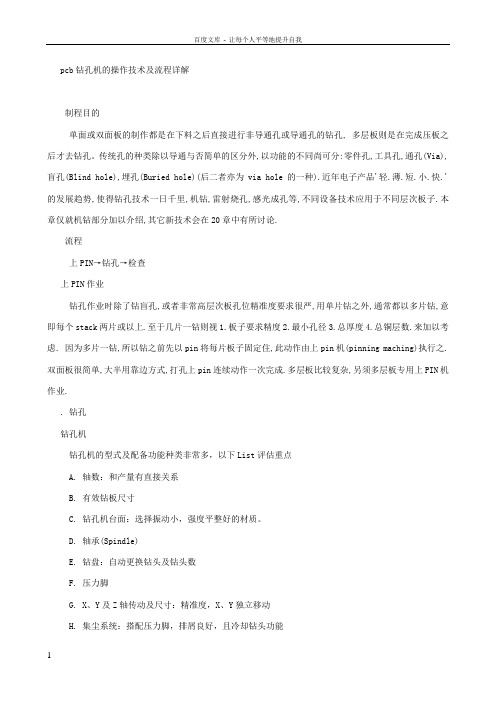
pcb钻孔机的操作技术及流程详解制程目的单面或双面板的制作都是在下料之后直接进行非导通孔或导通孔的钻孔, 多层板则是在完成压板之后才去钻孔。
传统孔的种类除以导通与否简单的区分外,以功能的不同尚可分:零件孔,工具孔,通孔(Via),盲孔(Blind hole),埋孔(Buried hole)(后二者亦为via hole的一种).近年电子产品'轻.薄.短.小.快.'的发展趋势,使得钻孔技术一日千里,机钻,雷射烧孔,感光成孔等,不同设备技术应用于不同层次板子.本章仅就机钻部分加以介绍,其它新技术会在20章中有所讨论.流程上PIN→钻孔→检查上PIN作业钻孔作业时除了钻盲孔,或者非常高层次板孔位精准度要求很严,用单片钻之外,通常都以多片钻,意即每个stack两片或以上.至于几片一钻则视1.板子要求精度2.最小孔径3.总厚度4.总铜层数.来加以考虑. 因为多片一钻,所以钻之前先以pin将每片板子固定住,此动作由上pin机(pinning maching)执行之. 双面板很简单,大半用靠边方式,打孔上pin连续动作一次完成.多层板比较复杂,另须多层板专用上PIN机作业.. 钻孔钻孔机钻孔机的型式及配备功能种类非常多,以下List评估重点A. 轴数:和产量有直接关系B. 有效钻板尺寸C. 钻孔机台面:选择振动小,强度平整好的材质。
D. 轴承(Spindle)E. 钻盘:自动更换钻头及钻头数F. 压力脚G. X、Y及Z轴传动及尺寸:精准度,X、Y独立移动H. 集尘系统:搭配压力脚,排屑良好,且冷却钻头功能I. Step Drill的能力J. 断针侦测K. RUN OUT钻孔房环境设计A. 温湿度控制B. 干净的环境C. 地板承受之重量D. 绝缘接地的考虑E. 外界振动干扰物料介绍钻孔作业中会使用的物料有钻针(Drill Bit),垫板(Back-up board),盖板(Entry board)等.以下逐一介绍:图为钻孔作业中几种物料的示意图.钻针(Drill Bit), 或称钻头,其质量对钻孔的良窳有直接立即的影响, 以下将就其材料,外型构、及管理简述之。
- 1、下载文档前请自行甄别文档内容的完整性,平台不提供额外的编辑、内容补充、找答案等附加服务。
- 2、"仅部分预览"的文档,不可在线预览部分如存在完整性等问题,可反馈申请退款(可完整预览的文档不适用该条件!)。
- 3、如文档侵犯您的权益,请联系客服反馈,我们会尽快为您处理(人工客服工作时间:9:00-18:30)。
第17页
入职工艺知识培训讲义
2.3激光钻孔控制参数
RD-CM-WI01S1A
Outline是以外框圆烧蚀孔,用其能 量将铜皮揭起; Spiral是以螺旋方式由里向外或由 外向内烧蚀,将铜直接升华; Filled以同心圆环方式由里向外或 由外向内烧蚀。 一般设置成3到4个Task,Task1都是 用于烧蚀铜皮,后面的Task是用于 清理树脂。能量的大小主要影响参 数Frequency、Pulse width、Mark speed。
D、盖板 △防止钻孔上表面毛刺 △保护层压板 △提高孔位精度 △ 冷却钻针,降低钻孔温度
第5页
入职工艺知识培训讲义
G、钻刀
RD-CM-WI01S1A
钻刀是机械钻孔过程中用到的切削刀具。一般采用钨钴类合金经高温、高压烧结而 成,具有高硬度和高耐磨性。 钻刀材质与性能
钻刀结构
第6页
入职工艺知识培训讲义
槽孔不良
孔大/小
漏孔
偏孔
第13页
入职工艺知识培训讲义
1.6设备维护保养及环境控制 温度:18-24℃; 序号 1 2 3 4 5 6 7 8 9 10 11 12 湿度:47-63%RH; 维护内容 每班清洁机器台面及机器外表 每班清洁夹头、检查主轴声音 每班清洁钻针座粉屑、冷却机外壳 每班清洁冷却部分防尘网 每班检查油位、压力脚轴衬的磨损情况,清洁压力脚 每班检查铜POD是否松动、钻机负压值 每月检查主轴静态≤15um、动态≤20um 每月检查钻针握力、冷却机运行声音 每月检查流量是否正常,有无泄漏,温度是否可控,油冷 报警信号是否正常; 每月排掉空气过滤器内的冷凝水 每季对机械装置进行润滑 每半年更换冷却机冷却油
RD-CM-WI01S1A
外形加工制程介绍 3.1流程: A. 铣板:将半成品线路板切割成客户所需要的尺寸的外形成品线路板。 B. V-CUT:在线路板上加工客户所需“V形坑”,便于客户安装使用线路板。 C. 倒角:将线路板之金指加工成容易插接的斜面。
RD-CM-WI01S1A
RD-CM-WI01S1A
2.2设备 我司2005年4月引进了德国乐普科公司生产的型号为LPKF-ML600D的UV激光机; 2008年10月引进日本三菱 ML605GTW-H CO2激光钻机。
第16页
入职工艺知识培训讲义
2.2设备 CO2和UV激光技术对比
RD-CM-WI01S1A
UV激光机对成孔<3mil的微孔十分有利(激光点直径20um),依靠光束之能量强且集中的优 势可直接打穿基材上的铜箔,无需“开窗”, 但成孔速度较慢, 不适用于(4-6)mil微孔的生产 ;CO2激光机对(4-8)mil及其以上的微盲孔(激光点直径70um)且量产速度快。
工艺知识入职培训
培训工序:钻孔/激光钻孔/外形
讲 日
师: 刘兰 期:2010 年 08 月 20 日
入职工艺知识培训讲义 目 录
1.钻孔 1.1原理、工艺流程、设备及物料 1.2钻孔控制参数 1.3常见质量缺陷、原因和对策 1.4设备维护和保养及环境要求 1.5交流 2.激光钻孔 2.1原理、主要设备 2.2工艺参数、控制要点 2.3常见质量缺陷、原因和对策; 2.4设备维护和保养及环境要求 2.5交流 3.外形 3.1原理、工艺流程、设备及物料 3.2各流程工艺控制 3.3外形品质控制 3.4设备维护和保养及环境要求 3.5交流
RD-CM-WI01S1A
设备能力,非实际加工精度
第25页
入职工艺知识培训讲义
(2)V-CUT机 序号 1 2 3 4 5 6 (3)倒角机 (4)成品清洗机 项目 加工尺寸 加工板厚 切割速度 线-线精度 定位孔到线的精度 余厚精度 能力 MIN:150*150mm MAX:630*630 mm 0.3-3.2MM MAX:40M/MIN ±0.03MM ±0.05MM ±0.03MM
第19页
入职工艺知识培训讲义
2.4激光钻孔品质控制 垂直型和倒梯形为可接受孔型
RD-CM-WI01S1A
1.孔粗: FR-4: <15um 2.侧蚀: FR-4:<10um 3.真圆度:>85% 4.孔型: 下孔径/上孔径=70%--80% 5.偏孔 6.孔未钻透
针对co2激光孔
第20页
入职工艺知识培训讲义
RD-CM-WI01S1A
第14页
入职工艺知识培训讲义
2.激光钻孔
RD-CM-WI01S1A
2.1原理 目前用于PCB钻孔的激光主要有三种,根据其发射的激光频率不同分为波长为355nm的UV 激光,和波长为10.6um的CO2激光,还有一种是UV和CO2相互结合的激光。
第15页
入职工艺知识培训讲义
RD-CM-WI01S1A
第2页
入职工艺知识培训讲义
1.钻孔
RD-CM-WI01S1A
1.1原理:利用钻刀在高转速和落速情况下,形成线路板层与层之间导通的孔。 1.2流程: X-Ray冲3个定位孔
第3页
入职工艺知识培训讲义
1.3设备及物料: A、钻机(16万转/20万转) B、销钉 C、上套环机
D. 洗板:将外形加工产生的粉尘以及生产过程中产生之油渍清洗干净,并烘干。
第24页
入职工艺知识培训讲义
3.2设备及物料 (1)铣床 序号 1 2 3 4 5 6 7 8 项目 主轴轴数 加工范围 主轴转速 各轴驱动系统 X.Y轴移动速度 Z轴移动速度 ATC刀座数量 精度 能力 2轴/6轴 550*700/21.65*27.6 15,000.RPM60.000.RPM XYZ轴AC伺服马达 30M/MIN 20M/MIN 10把自动换刀+断刀及 刀径量测 ±0.05MM
孔型 影响参数:mask直径、脉 冲能量、脉冲宽度、脉冲次 数。
第18页
入职工艺知识培训讲义
2.4激光钻孔品质控制
RD-CM-WI01S1A
(1)RCC为涂覆树脂铜箔,结构中不含玻纤。 (2)LDPP是用平滑的玻纤布制成的半固化片,X-Y 平面上玻纤和树脂密集区域分布的不 均匀性及纱束重叠处的厚度都被减到最小。 (3)普通PP玻纤所用的基本上都是一个椭圆形丝束,编织以后有明显玻纤密集区,涂覆 树脂时也有明显的树脂密集区。
RD-CM-WI01S1A
1.钻孔前在垫木板上试钻确定合理深度; 2.按刀参表输入深度补偿; 3.通知维修调校、使用平整电木板; 1.更改钻带;降慢下刀速度; 2.降慢下刀速度; 3.首槽需做检查才可批量生产(检查底板) 1.上刀前仔细检查钻针刀径; 2.正确设置刀具位置; 3.上刀前仔细检查钻针品质,中途加强巡查 4.加快下刀速度,减少转速; 1.断针及时标明位置,再补孔,每次补孔均 需核对点图; 2.退回工程处理; 1.钻定位孔时避开重孔,或重定位; 2.上板时做足清洁卫生; 3.清洗夹头; 4.减少叠板数; 5.测变形量,按涨缩重出钻带;
RD-CM-WI01S1A
序号 1 2
项目 板厚度范围 最小板尺寸 最大板尺寸
能力 0.4-6.0mm 100*100mm 喷锡板 金板 610mmX610mm 宽度≤610mm
第26页
入职工艺知识培训讲义
(5)铣刀
RD-CM-WI01S1A
日立六轴钻机 用压克力胶板上销钉,提 高钻孔精度
第4页
入职工艺知识培训讲义
C、垫板 防止印制板表面毛刺的产生 使钻针充分贯穿印制板
RD-CM-WI01S1A
A、2.5mm普通木浆纤维板, 用于FR-4板材; B、1.5mm酚醛板, 用于高频板 C、当最小钻孔刀径≤0.20mm时,使用白色垫板 D、钻刀钻入垫板的深度控制在0.4-0.6mm;
第11页
入职工艺知识培训讲义
1.5常见质量问题及解决方法 常见缺陷 产生原因 1.打磨不当或未打磨; 2.板间或盖板下杂物; 3.钻针崩角; 3.钻针不锋利; 4.参数不当; 1.钻针崩角; 2.钻针使用寿命过长; 3.钻孔参数不当; 1.压力脚不当; 2.钻针返磨次数过多; 3.叠板过厚; 4.钻孔参数不当; 5.铝片有折痕; 6.板基铜太厚; 7.板间有杂物; 8.板翘曲; 9.主轴夹头故障; 解决方法
第10页
入职工艺知识培训讲义
D.高频板钻孔规定:
RD-CM-WI01S1A
(1)高频板有PTFE及非PTFE两大类; (2)非PTFE板材属陶瓷粉添加材料,按华为板钻孔参数加工,孔限设置有华为板参数的基 础上减少50%孔。 (3)PTFE高频板材,材质软,钻孔过程中钻刀易缠上杂物,钻刀优先选用新刀及磨一钻 刀,需要使用冷冲盖板及酚醛垫板,盖板厚度要求大于0.5mm,钻孔参数使用《PTFE高频板材 钻孔参数》。
G、钻刀(返磨钻刀)
RD-CM-WI01S1A
返磨刀(降低成本)
钻刀常见缺陷
第7页
入职工艺知识培训讲义
H. X-ray检查机 多层板首板需用X-ray机检查孔偏
RD-CM-WI01S1A
第8页
入职工艺知识培训讲义
1.4、钻孔主要工艺参数 1.4.1钻孔参数 1)转速(Speed):钻针在某一特定时间内所转动的圈数 2)进刀速(In feed) :钻针在某一特定时间内下落的距离 3)退刀速(Out feed) :钻针在某一特定时间内退回的距离 4)孔限(Max holes):钻孔更换钻针时的最大孔数
2.5目前我司激光盲孔能力
RD-CM-WI01S1A
其余功能: 铣FPC板外 形、切割FPC覆盖膜 等
激光钻孔前 必须棕化
第21页
入职工艺知识培训讲义
RD-CM-WI01S1A
2.6设备维护、保养及环境要求 2.6.1 CO2钻机 (1)房间温度要求:19-25℃;湿度要求:50-75%。 (2)尽量避免激光钻房与湿制程设备的空气流通。 (3)激光钻房不能存放化学物品。 (4)酒精清洗完机器的保护镜时,将酒精瓶盖好,同时将含有酒精的棉花置于密封的垃圾桶内。 (5)保持压缩空气,空调进风,新鲜空气进风不含对激光有影响的物质。