变位齿轮的分度圆还相切吗
齿轮基础知识全(建议收藏)
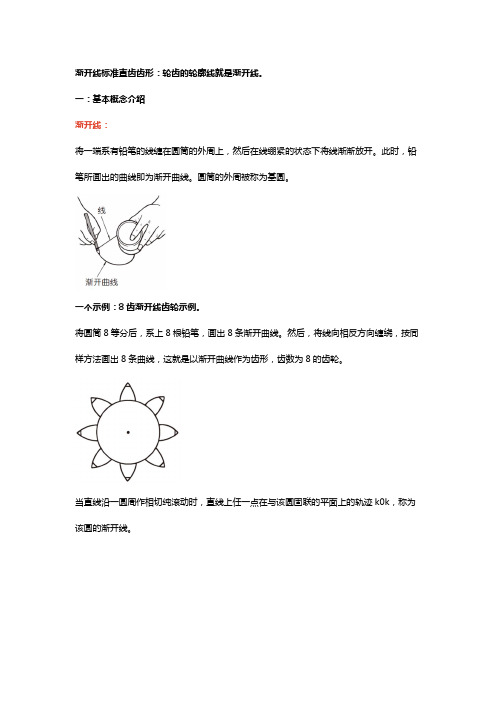
渐开线标准直齿齿形:轮齿的轮廓线就是渐开线。
一:基本概念介绍渐开线:将一端系有铅笔的线缠在圆筒的外周上,然后在线绷紧的状态下将线渐渐放开。
此时,铅笔所画出的曲线即为渐开曲线。
圆筒的外周被称为基圆。
一个示例:8齿渐开线齿轮示例。
将圆筒8等分后,系上8根铅笔,画出8条渐开曲线。
然后,将线向相反方向缠绕,按同样方法画出8条曲线,这就是以渐开曲线作为齿形,齿数为8的齿轮。
当直线沿一圆周作相切纯滚动时,直线上任一点在与该圆固联的平面上的轨迹k0k,称为该圆的渐开线。
渐开线的性质(1)直线NK = 曲线N K0(2) 渐开线上任意一点的法线必切于基圆,切于基圆的直线必为渐开线上某点的法线。
与基圆的切点N为渐开线在k点的曲率中心,而线段NK是渐开线在点k处的曲率半径。
(3)渐开线齿廓各点具有不同的压力角,点K离基圆中心O愈远,压力角愈大。
(4)渐开线的形状取决于基圆的大小,基圆越大,渐开线越平直,当基圆半径趋于无穷大时,渐开线成为斜直线。
(故齿条的齿轮廓线为斜线)(5)基圆内无渐开线。
渐开线的方程式rk为渐开线再任意点K的向径。
模数:模数是决定齿大小的因素。
齿轮模数被定义为模数制轮齿的一个基本参数,是人为抽象出来用以度量轮齿规模的数。
目的是标准化齿轮刀具,减少成本。
直齿、斜齿和圆锥齿齿轮的模数皆可参考标准模数系列表。
分度圆上的齿距p对Π的比值称为模数,用m表示,单位为mm,即m=p/Π,已标准化。
模数是齿轮的主要参数之一,齿轮的主要几何尺寸都与模数成正比,m越大,则齿距p越大,轮齿就越大,轮齿的抗弯能力就越强,所以模数m又是轮齿抗弯能力的标志。
不同模数的轮齿大小对比。
分度圆:为了便于设计、制造及互换,我们把齿轮某一圆周上的比值规定为标准值(整数或较完整的有理数),并使该圆上的压力角也为标准值,这个圆称为分度圆,其直径以d表示。
因轮齿分度圆上的齿槽宽e=齿厚s。
故s=e=Πd/2z,故p=2s=2e=Πd/z。
10—讲义7渐开线变位齿轮简介

α′<α、y < 0、 △y > 0。
优点:允许a ′< a ; εα↑。 缺点:与正传动的优点相反。
∴ 正传动优点较多,传动质量较高,而负传动缺点较多。 所以在一般情况下,应多采用正传动,负传动除了凑中 心距之外一般不采用。在中心距等于标准中心距时,为 了提高传动质量,可采用等变位传动来代替标准齿轮传 动。
∴ △y = ( x1 + x2 ) – y > 0 这时齿顶高 ha = ( ha*+ x - △y ) m ,齿全高h减少了△y m。
2、变位齿轮传动类型 按一对齿轮变位系数和x1+ x2的不同来分:
1)零传动:x1 + x2 = 0 ① x1 = x2 = 0——标准齿轮传动(零变位传动)
齿数条件:z1≥zmin 、z2≥zmin; 啮合特点:a ′= a、α′=α、y = 0、△y = 0。
一般情况下,a″≠a′,并且可以证明a″> a′。 ∴ 对变位齿轮传动,无法同时满足无侧隙和标准顶隙。 实际设计时解决的办法是:
两轮按中心距a ′安装,并将两轮的齿顶削短一些,来保 证标准顶隙。
设齿顶的削短量为△y m, △y称为齿顶高变动系数。 △y m = ( x1 + x2 ) m – y m
而且基圆的齿厚↑,弯曲强度↑。位齿轮的尺寸计算 正变位:
s =πm / 2 +2 x m tanα e =πm / 2 –2 x m tanα ra = r + ha*m + x m rf = r -(ha* +c*)m + x m ha= ha*m + x m hf =(ha*+ c*)m – x m
圆柱齿轮的变位

圆柱齿轮的变位为了改善齿轮的传动质量或满足结构尺寸的特殊要求,有时需要采用变位齿轮。
(一)变位齿轮原理用齿条型道具切制齿轮时,若刀具的中线与被切齿轮分度圆相切,所切出的齿轮为标准齿轮。
如果改变刀具与被切齿轮的相对位置,即将刀具略微移近或离开被切齿轮的中心,则所切得的齿轮叫做变位齿轮。
若刀具离开齿轮的中心,这种变位叫正变位;若刀具移近齿轮的中心,则叫负变位。
刀具所以移动的距离叫变位量,它与模数之比,称为变位系数,以ξ表示。
+ξ表示正变位;-ξ表示负变位。
对正变位齿轮,刀具相对于切标准齿轮的位置离开一段距离X=+ξm;齿顶圆直径和齿根圆直径相应加大;齿根部分变肥,齿顶变尖;公法线增长。
对负变位齿轮,刀具相对于切标准齿轮的位置移近中心一段距离X=-ξm;齿顶圆直径和齿根圆直径相应减小;齿根部变瘦;公法线减短。
变位齿轮的齿顶高和齿根高虽然发生变化,但全齿高基本不变。
(二)齿轮变位的目的1)配凑中心距在两平行轴上有多对齿轮啮合传动或要求中心距为特定数值时,若用标准齿轮不能满足中心距的要求,则可采用变位齿轮。
2)避免齿轮根切当要齿轮齿数少于无根切的最少齿数时,可采用正变位齿轮。
3)提高齿轮的强度根据某些试验和计算指出,采用适当的变位方法,可使齿轮的承载能力提高20~25%,寿命延长200%;抗弯强度可显著提高。
4)修复磨损的大齿轮在相啮合的齿轮偶中,由于小齿轮磨损较大,而大齿轮磨损较小,并且大齿轮制造费用较大,所以可对大齿轮采用负变位将磨损表面切除,并在保持中心距不变的条件下,配制正变位的小齿轮,以减少修配工作量。
对某些零件磨损而引起两啮合齿轮中心距改变的情况,可以采用角度变位来改变中心距,而不必更换被磨损的零件。
机械原理期末题库(附答案)
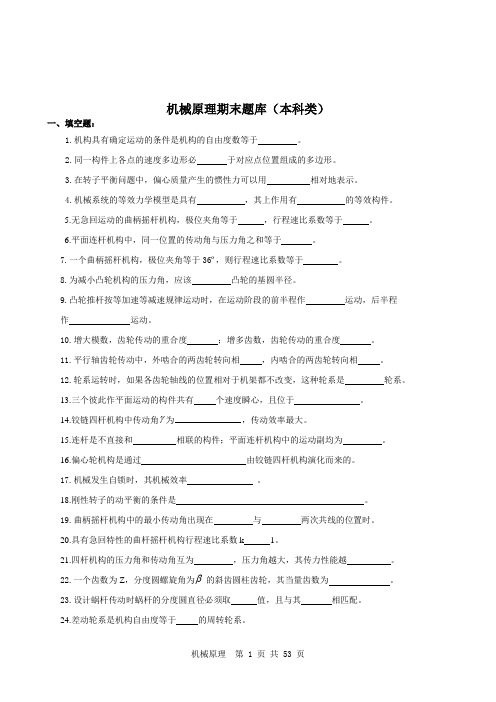
机械原理期末题库(本科类)一、填空题:1.机构具有确定运动的条件是机构的自由度数等于。
2.同一构件上各点的速度多边形必于对应点位置组成的多边形。
3.在转子平衡问题中,偏心质量产生的惯性力可以用相对地表示。
4.机械系统的等效力学模型是具有,其上作用有的等效构件。
5.无急回运动的曲柄摇杆机构,极位夹角等于,行程速比系数等于。
6.平面连杆机构中,同一位置的传动角与压力角之和等于。
7.一个曲柄摇杆机构,极位夹角等于36º,则行程速比系数等于。
8.为减小凸轮机构的压力角,应该凸轮的基圆半径。
9.凸轮推杆按等加速等减速规律运动时,在运动阶段的前半程作运动,后半程作运动。
10.增大模数,齿轮传动的重合度;增多齿数,齿轮传动的重合度。
11.平行轴齿轮传动中,外啮合的两齿轮转向相,内啮合的两齿轮转向相。
12.轮系运转时,如果各齿轮轴线的位置相对于机架都不改变,这种轮系是轮系。
13.三个彼此作平面运动的构件共有个速度瞬心,且位于。
14.铰链四杆机构中传动角γ为,传动效率最大。
15.连杆是不直接和相联的构件;平面连杆机构中的运动副均为。
16.偏心轮机构是通过由铰链四杆机构演化而来的。
17.机械发生自锁时,其机械效率。
18.刚性转子的动平衡的条件是。
19.曲柄摇杆机构中的最小传动角出现在与两次共线的位置时。
20.具有急回特性的曲杆摇杆机构行程速比系数k 1。
21.四杆机构的压力角和传动角互为,压力角越大,其传力性能越。
22.一个齿数为Z,分度圆螺旋角为β的斜齿圆柱齿轮,其当量齿数为。
23.设计蜗杆传动时蜗杆的分度圆直径必须取值,且与其相匹配。
24.差动轮系是机构自由度等于的周转轮系。
25.平面低副具有个约束,个自由度。
26.两构件组成移动副,则它们的瞬心位置在。
27.机械的效率公式为,当机械发生自锁时其效率为。
28.标准直齿轮经过正变位后模数,齿厚。
29.曲柄摇杆机构出现死点,是以作主动件,此时机构的角等于零。
齿轮切削加工与变位齿轮的概念
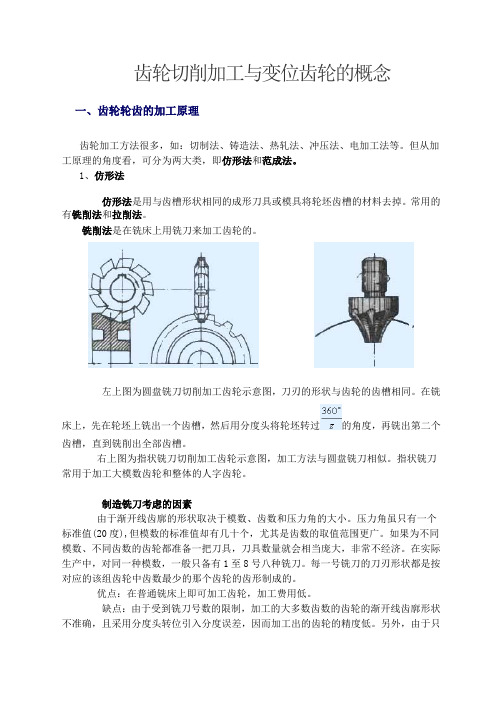
齿轮切削加工与变位齿轮的概念一、齿轮轮齿的加工原理齿轮加工方法很多,如:切制法、铸造法、热轧法、冲压法、电加工法等。
但从加工原理的角度看,可分为两大类,即仿形法和范成法。
1、仿形法仿形法是用与齿槽形状相同的成形刀具或模具将轮坯齿槽的材料去掉。
常用的有铣削法和拉削法。
铣削法是在铣床上用铣刀来加工齿轮的。
左上图为圆盘铣刀切削加工齿轮示意图,刀刃的形状与齿轮的齿槽相同。
在铣床上,先在轮坯上铣出一个齿槽,然后用分度头将轮坯转过的角度,再铣出第二个齿槽,直到铣削出全部齿槽。
右上图为指状铣刀切削加工齿轮示意图,加工方法与圆盘铣刀相似。
指状铣刀常用于加工大模数齿轮和整体的人字齿轮。
制造铣刀考虑的因素由于渐开线齿廓的形状取决于模数、齿数和压力角的大小。
压力角虽只有一个标准值(20度),但模数的标准值却有几十个,尤其是齿数的取值范围更广。
如果为不同模数、不同齿数的齿轮都准备一把刀具,刀具数量就会相当庞大,非常不经济。
在实际生产中,对同一种模数,一般只备有1至8号八种铣刀。
每一号铣刀的刀刃形状都是按对应的该组齿轮中齿数最少的那个齿轮的齿形制成的。
优点:在普通铣床上即可加工齿轮,加工费用低。
缺点:由于受到铣刀号数的限制,加工的大多数齿数的齿轮的渐开线齿廓形状不准确,且采用分度头转位引入分度误差,因而加工出的齿轮的精度低。
另外,由于只能逐个加工齿槽,生产效率低。
这种加工方法适用于修配或小量生产。
拉削法是利用齿轮拉刀来加工齿轮的。
优点:加工精度和加工效率都非常高。
缺点:拉刀价格昂贵,需要专用的机床。
这种加工方法适用于大批量的专业化生产。
2、范成法范成法: 是利用一对齿轮作无侧隙啮合传动时,两轮齿廓互为包络线的原理来加工齿轮的方法。
它又称为包络法、展成法,是目前齿轮加工中最常用的一种切削加工方法。
齿轮刀具加工齿轮时,是已知两个运动因素(利用机床传动系统人为地使刀具与轮坯按的关系运动)和一个几何因素(刀具的齿廓),通过包络,得到第四个因素---轮坯上的齿廓。
分度圆
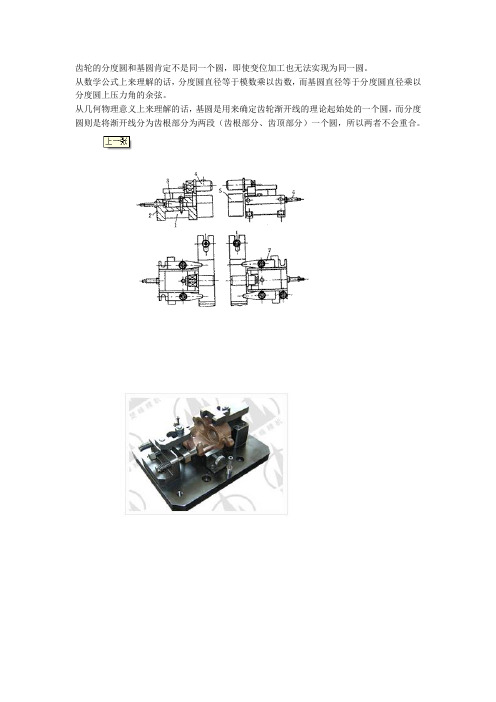
齿轮的分度圆和基圆肯定不是同一个圆,即使变位加工也无法实现为同一圆。
从数学公式上来理解的话,分度圆直径等于模数乘以齿数,而基圆直径等于分度圆直径乘以分度圆上压力角的余弦。
从几何物理意义上来理解的话,基圆是用来确定齿轮渐开线的理论起始处的一个圆,而分度圆则是将渐开线分为齿根部分为两段(齿根部分、齿顶部分)一个圆,所以两者不会重合。
变速器换档轴钻孔通用可调夹具设计与应用2008-7-10 14:06:00 【文章字体:大中小】推荐收藏打印立帜机床网汽车变速器中的换档轴类产品品种多,精度要求高,在变速器换档轴加工过程中,通过对夹具部分元件的简便安装、调整,可以以较强的通用性达到专用夹具的高效率、高精度并具有组合夹具的灵活多变性。
换档轴孔加工一般采用普通钻床、组合机床、加工中心等设备。
其中,组合机床生产效率高,适合大批量生产,但设备一次性投资大、加工调整时间长,不适宜多品种、中小批量的生产方式,并具有很大的设备投资风险,目前应用较少;加工中心机床调整方便、工序相对集中,但夹具设计及制造要求高,且设备投资大,大批量生产相对成本高,小批量生产夹具调整繁琐,目前应用不太广泛;普通钻床设备投资小,生产效率高,对操作者的操作技能要求低,结合不同的夹具使用,适合不同类型企业的大批量、中小批量的生产,因此在行业中应用较广。
我厂自20世纪60年代一直沿用普通钻床钻孔方式。
目前,适于批量法的变速器杂件类专用夹具经过几十年的探索效果显著,在日趋激烈的新产品竞争中,中小批量轮番生产和新产品试制,依然沿用传统方法已经不太适宜。
其中换档轴钻夹具存在的主要问题如下:1.专用钻夹具(1)夹具等待时间长(设计、制造周期一般需3~4个月);(2)夹具需求数量多,使用成本高(每工序均设计、制造一套夹具);(3)夹具制造成本高(每套3000元以上);(4)随着产品寿命周期愈来愈短,夹具淘汰率高,浪费大;(5)夹具占用大量库存,不便管理。
2.组合钻夹具(1)夹具租赁频繁、租用周期长,费用高(我厂轴类钻夹具年租赁费最高约3~5万元);(2)夹具刚性不足,加工精度不稳定,产品废品率高;(3)夹具元件多,组装精度低,生产中常需专业人员反复调整,浪费大量时间;(4)成套夹具采购成本高。
齿轮机构的齿廓啮合基本规律特点和类型
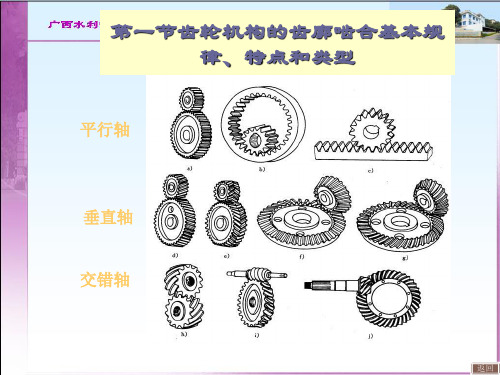
第八节 直齿圆锥齿轮传动
圆锥齿轮传动用来传递相交 两轴的运动和动力。
分直齿圆锥齿轮和曲 齿圆锥齿轮
返回
一、传动比和几何尺寸计算
1)分度圆:d1=mz1, d2=mz2 2)齿顶高:ha=m, 齿根高:hf=1.2m
3)传动比:i12= d2/d1 = z2/z1
=ctg δ1=tg δ2
1 2 2 d1 d 2 2 注意:分度圆锥角:δ1=arcctg i12, δ2= 900-δ1 齿顶角:θa1= θa2=arctg ha/R, 齿根角: θf1= θf2=arctg hf/R 锥距: R
图5-20 背锥及当量齿数
平行轴
垂直轴
交错轴
返回
一、齿轮机构的特点和类型
(一)平行轴线齿轮传动
返回
(二)空间齿轮传动
5
返回
齿轮传动的基本要求
传动准确和平稳(任意瞬时传动比恒定)------由齿
轮轮廓和制造精度决定。
传动比
1 i12 2
承载能力强(足够强度、刚度、耐磨)--------由齿
轮尺寸、材料和工艺决定。
返回
三、正确啮合条件
mn1= mn2 =m αn1= αn2=200 β1= -β2外啮合 (mt1= mt2 ) (αt1= αt2) ( β1=β2内啮合 )
返回
四、当量齿数
图5-18 斜齿圆柱齿轮的当量齿数
zmt 2 d z zv 2 3 pn pn cos pt cos cos3
5、分度圆---圆周上的 P/ π =m(模数)为标准值 GB1357-87,压力角α亦为标准值的圆。 d=m Z,α=200,标准齿轮 P=s+e,s=e= π m/2
齿轮传动补充习题
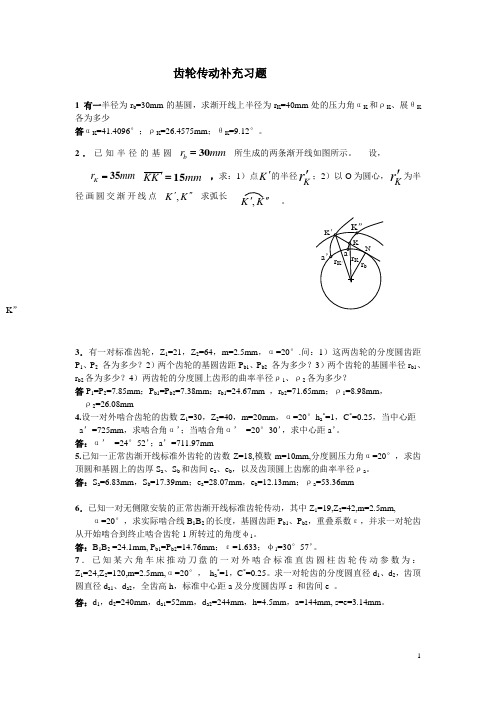
齿轮传动补充习题1 有一半径为r b =30mm 的基圆,求渐开线上半径为r K =40mm 处的压力角αK 和ρK 、展θK 各为多少 答αK =41.4096°;ρK =26.4575mm ;θK =9.12°。
所生成的两条渐开线如图所示。
设 2.已知半径的基圆 ,求:1)点K '的半径K r ';2)以O 为圆心,K r '为半径画圆交渐开线点 求弧长3.有一对标准齿轮,Z 1=21,Z 2=64,m=2.5mm ,α=20°.问:1)这两齿轮的分度圆齿距P 1、P 2 各为多少?2)两个齿轮的基圆齿距P b1、P b2 各为多少?3)两个齿轮的基圆半径r b1、r b2各为多少?4)两齿轮的分度圆上齿形的曲率半径ρ1、ρ2各为多少?答P 1=P 2=7.85mm ;P b1=P b2=7.38mm ;r b1=24.67mm ,r b2=71.65mm ;ρ1=8.98mm , ρ2=26.08mm4.设一对外啮合齿轮的齿数Z 1=30,Z 2=40,m=20mm ,α=20°h a *=1,C *=0.25,当中心距 a ’=725mm ,求啮合角α’;当啮合角α’ =20°30’,求中心距a ’。
答:α’ =24°52’;a ’=711.97mm5.已知一正常齿渐开线标准外齿轮的齿数Z=18,模数m=10mm,分度圆压力角α=20°,求齿顶圆和基圆上的齿厚S a 、S b 和齿间e a 、e b ,以及齿顶圆上齿廓的曲率半径ρa 。
答:S a =6.83mm ,S b =17.39mm ;e a =28.07mm ,e b =12.13mm ;ρa =53.36mm6.已知一对无侧隙安装的正常齿渐开线标准齿轮传动,其中Z 1=19,Z 2=42,m=2.5mm,α=20°,求实际啮合线B 1B 2的长度,基圆齿距P b1、P b2,重叠系数ε,并求一对轮齿从开始啮合到终止啮合齿轮1所转过的角度φ1。
3.齿轮的根切与变位、渐开线齿轮传动、变位齿轮传动
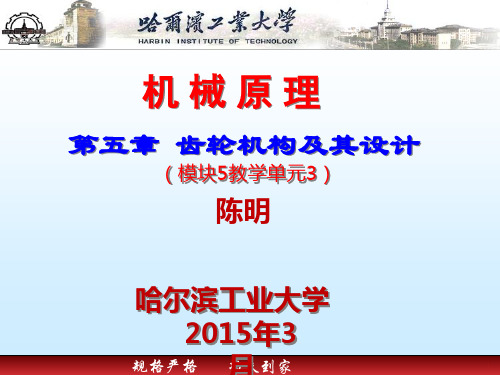
使卡尺的卡爪与齿廓中部的渐开线相切。
标准齿轮跨齿数:k
180
z
0.5
变位齿轮跨齿数:k
z 180
arccos
z cos
z 2x
0.5
规格严格 功夫到家
5
(2)公法线长度计算
Wk (k 1) pb sb
基圆齿距 pb m cos
基圆齿厚
sb s cos mz cos inv
规格严格 功夫到家
21
3、角度变位齿轮传动(x=x1+x2≠0)
由于x=x1+x2≠0,因而其啮合角'不再等于标准齿轮 的啮合角,故称为角度变位齿轮传动。它又可分为两
种情况:
1)正传动:x =x1+x2 > 0
'> , a'> a , y> 0 , Δy> 0
这种齿轮传动的两分度圆不再相切而是分离ym。为保证标准 径向间隙和无侧隙啮合,其全齿高应比标准齿轮缩短△ym。
tan
inv inv
z1
z2
规格严格 功夫到家
11
p1 p2 s1 s2
p1
p2
m
cos c os
s1
s2
m
cos c os
2x1
x2
tan
inv inv
z1
z2
m
cos c os
m
cos c os
2x1
x2
tan
inv
inv
z1
z2
2x1 x2 tan inv inv z1 z2 0
a'等于标准中心距a。为避免根切, 要求z>zmin。这类齿轮传动设计简单, 使用方便,可以保持标准中心距,但 小齿轮的齿根较弱,易磨损。
什么是变位齿轮,变位齿轮的特点以及为什么要对齿轮进行变位处理

什么是变位齿轮,变位齿轮的特点以及为什么要对齿轮进⾏变位处理什么是变位齿轮⽤齿条型⼑具加⼯齿轮时,若不采⽤标准安装,⽽是将⼑具远离或靠近轮坯回转中⼼,则⼑具的分度线不再与被加⼯齿轮的分度圆相切。
这种变位修正法。
采⽤这种⽅法加⼯的齿轮称为变位齿轮变位齿轮。
采⽤改变⼑具与被加⼯齿轮相对位置来加⼯齿轮的⽅法称为变位修正法⾮标准渐开线齿形的齿轮。
切制轮齿时,改变标准⼑具对齿通过改变标准⼑具对齿轮⽑坯的径向位置或改变标准⼑具的齿槽宽切制出的齿形为⾮标准渐开线齿形切向变位。
最常⽤的是径向变位,切向变位⼀般⽤于圆锥齿轮的变位。
轮⽑坯的径向位置称为径向变位径向变位。
改变标准⼑具的齿槽宽称为切向变位变位齿轮的特点变位齿轮与标准齿轮相⽐,其模数、齿数、压⼒⾓均⽆变化;但是正变位时,齿廓曲线段离基圆较远,齿顶圆和齿根圆也相应增⼤,齿根⾼减⼩,齿顶⾼增⼤,分度圆齿厚与齿根圆齿厚都增⼤,但齿顶容易变尖;负变位时,齿廓曲线段离基圆较近,齿顶圆和齿根圆也相应减⼩,齿根⾼增⼤,齿顶⾼减⼩,分度圆齿厚和齿根圆齿厚都减⼩。
,为什么要对标准齿轮进⾏变位变位齿轮的主要功能与作⽤,为什么要对标准齿轮进⾏变位变位齿轮的主要功能与作⽤1、减⼩齿轮传动的结构尺⼨,减轻重量在传动⽐⼀定的条件下,可使⼩齿轮齿数zl<zmin,从⽽使传动的结构尺⼨减⼩,减轻机构重量。
2、避免根切,提⾼齿根的弯曲强度当⼩齿轮齿数z1<zmin时,可以利⽤正变位避免根切,提⾼齿根的弯曲强度。
x≥xmin=(Z-Zmin)/Zmin,对α=20°时,Zmin=17。
3、提⾼齿⾯的接触强度3、提⾼齿⾯的接触强度采⽤啮合⾓α’>α的正传动时,由于齿廓曲率半径增⼤,故可以提⾼齿⾯的接触强度。
4、提⾼齿⾯的抗胶合耐磨损能⼒采⽤啮合⾓α’>α的正传动,并适当分配变位系数xl、x2,使两齿轮的最⼤滑动率相等时,既可降低齿⾯接触应⼒,⼜可降低齿⾯间的滑动率以提⾼齿轮的抗胶合和耐磨损能⼒。
齿轮的变位系数

齿轮的变位系数变位系数x是径向变位系数,加工标准齿轮时,齿条形刀具中线与齿轮分度圆相切。
加工变位齿轮时齿条形刀具中线与齿轮分度圆相切位置偏移距离xm,外移x为正,内移x为负。
除了圆锥齿轮有时采用切向变位xt外,圆柱齿轮一般只采用径向变位。
变位系数x的选择不仅仅是为了凑中心距,而主要是为了提高强度和改善传动质量。
变位齿轮的主要功用如下:(1)减小齿轮传动的结构尺寸,减轻重量 在传动比一定的条件下,可使小齿轮齿数zl<zmin,从而使传动的结构尺寸减小,减轻机构重量。
(2)避免根切,提高齿根的弯曲强度 当小齿轮齿数z1<zmin时,可以利用正变位避免根切,提高齿根的弯曲强度。
x≥xmin=(Z-Zmin)/Zmin,对α=20o时,Zmin=17。
(3)提高齿面的接触强度 采用啮合角α’>α的正传动时,由于齿廓曲率半径增大,故可以提高齿面的接触强度。
(4)提高齿面的抗胶合耐磨损能力 采用啮合角α’>α的正传动,并适当分配变位系数xl、x2,使两齿轮的最大滑动率相等时,既可降低齿面接触应力,又可降低齿面间的滑动率以提高齿轮的抗胶合和耐磨损能力。
(5)配凑中心距 当齿数z1、z2不变的情况下,啮合角α’不同,可以得到不同的中心距,以达到配凑中心距的目的。
(6)修复被磨损的旧齿轮 齿轮传动中,小齿轮磨损较重,大齿轮磨损较轻,可以利用负变位把大齿轮齿面磨损部分切去再使用,重配一个正变位小齿轮,这就节约了修配时需要的材料与加工费用。
选择变位系数的基本原则(1)润滑条件良好的闭式齿轮传动 当齿轮表面的硬度不高时(HBS<350),即对于齿面未经渗碳、渗氮、表面淬火等硬化处理的齿轮,齿面疲劳点蚀或剥伤为其主要的失效形式,这时应选择尽可能大的总变位系数x,即尽量增大啮合角,以便增大啮合节点处齿廓的综合曲率半径,减少接触应力,提高接触强度与疲劳寿命。
当轮齿表面硬度较高时(HBS>350),常因齿根疲劳裂纹的扩展造成轮齿折断而使传动失效,这时,选择变位系数应使齿轮的齿根弯曲强度尽量增大,并尽量使相啮合的两齿轮具有相近的弯曲强度。
齿轮各参数计算方法

齿轮各参数计算方法1、齿数Z闭式齿轮传动一般转速较高,为了提高传动的平稳性,减小冲击振动,以齿数多一些为好,小一些为好,小齿轮的齿数可取为z1=20~40。
开式(半开式)齿轮传动,由于轮齿主要为磨损失效,为使齿轮不致过小,故小齿轮不亦选用过多的齿数,一般可取z1=17~20。
为使齿轮免于根切,对于α=20度的标准支持圆柱齿轮,应取z1≥172、模数m齿距与齿数的乘积等于分度圆的周长,即pz=πd。
为使d为有理数的条件是p/π为有理数,称之为模数。
即:m=p/π模数m是决定齿轮尺寸的一个基本参数。
齿数相同的齿轮模数大,则其尺寸也大。
3、分度圆直径d齿轮的轮齿尺寸均以此圆为基准而加以确定,d=mz4、齿顶圆直径da和齿根圆直径df由齿顶高、齿根高计算公式可以推出齿顶圆直径和齿根圆直径的计算公式:da=d+2ha df=d-2hf=mz+2m=mz-2×1.25m=m(z+2)=m(z-2.5)5、分度圆直径d在齿轮计算中必须规定一个圆作为尺寸计算的基准圆,定义:直径为模数乘以齿数的乘积的圆。
实际在齿轮中并不存在,只是一个定义上的圆。
其直径和半径分别用d和r表示,值只和模数和齿数的乘积有关,模数为端面模数。
与变位系数无关。
标准齿轮中为槽宽和齿厚相等的那个圆(不考虑齿侧间隙)就为分度圆。
标准齿轮传动中和节圆重合。
但若是变位齿轮中,分度圆上齿槽和齿厚将不再相等。
若为变位齿轮传动中高变位齿轮传动分度圆仍和节圆重合。
但角变位的齿轮传动将分度圆和节圆分离。
6、压力角αrb=rcosα=1/2mzcosα在两齿轮节圆相切点P处,两齿廓曲线的公法线(即齿廓的受力方向)与两节圆的公切线(即P点处的瞬时运动方向)所夹的锐角称为压力角,也称啮合角。
对单个齿轮即为齿形角。
标准齿轮的压力角一般为20”。
在某些场合也有采用α=14.5°、15°、22.50°及25°等情况。
7、齿顶高系数和顶隙系数—h*a 、C*两齿轮啮合时,总是一个齿轮的齿顶进入另一个齿轮的齿根,为了防止热膨胀顶死和具有储成润滑油的空间,要求齿根高大于齿顶高。
变位齿轮

根瘦顶宽、易引起根切,强度降低。
小结:
与标准齿轮相同处:变位齿轮与标准齿轮加工方法一样,其m、α、z不变, 其分度圆、基圆、渐开线不变, p、h、pb不变。 与标准齿轮不同处:da、df、e、s、ha、hf不同。
3、变位齿轮传动
至少有一个齿轮是变位齿轮的齿轮副。 ⑴ 高度变位齿轮传动
a′=a x1+啮合线和节点位置不变。 ② 啮合角α′=分度圆上的齿形角α ③ 节圆与分度圆重合。 ④ 一个正变位和一个负变位齿轮组成变位齿轮副。小齿轮采用正变位, 齿根厚;大齿轮采用负变位,齿根瘦,强度、寿命接近。
1、齿轮的加工方法及特点 ?
2、齿轮的根切原因?不发生根切的最少齿数?防止根切的措施?
3、标准齿轮的局限性。
4、什么是正变位齿轮?什么是负变位齿轮 ?其特点分别是什么? 5、变位齿轮相对于标准齿轮,分度圆、基圆、渐开线、 da、df、e、s、ha、hf、
h 、p、pb是不变、变大、变小?
用展成法加工渐开线直齿圆柱齿轮,刀具为标准齿条形刀具,刀具模 数m=4 mm,齿形角20°,正常齿制。齿轮的转动中心到刀具分度线之间 的距离a=33 mm,被加工齿轮没有发生根切现象。试回答下列问题。 (1) 展成法是利用齿轮的 (2) 利用展成法加工 使用同一把刀具。 和 原理来进行轮齿加工的方法。 相同而齿数不同的齿轮时,可以
后果:轮齿强度削弱,重合度减小,传动平 稳性差。
2、最少齿数 用展成法不产生根切的最少齿数:
zmin 17
三、变位齿轮
1、标准齿轮的局限性
⑴ 当齿轮齿数Z<17,用展成法加工齿轮会产生根切现象;用仿型法加工齿 轮,存在齿根干涉现象。 ⑵ 标准小齿轮齿根强度弱,同时小齿轮各轮齿参与啮合的频率高、次数多, 因此小齿轮寿命低。 ⑶ 标准齿轮不适用于非标准中心距场合。 当实际中心距a′>标准中心距a,重合度减小,传动平稳性变差; 当实际中心距a′<标准中心距a,齿轮副会因齿厚大于槽宽而卡住不能传动。 ⑷ 标准齿轮不能修复,经济性差。
齿轮的切削加工和变位齿轮

齿轮的切削加工和变位齿轮1 齿轮的切削加工原理1. 范成法切齿原理齿轮加工方法很多,以切削加工方法最为常用。
范成法是利用一对齿轮啮合原理切削加工齿廓的。
如图所示,假设将标准齿条作为刀具,另一齿轮为被切齿轮毛坯。
当刀具以v=rω作等速移动,齿轮毛坯以ω作等速转动时,刀具齿廓就能切出被加工齿轮的齿廓。
标准齿条型刀具的齿形它与标准齿条基本相同,只是齿顶增加了c*m的高度,目的是为了切出被切齿轮的径向间隙。
因齿条刀的分度线等分其齿高,故又称为中线。
刀顶线与直线齿廓之间的过渡处不是直线,而是以半径为ρ的圆角刀刃。
它不能切出渐开线齿廓,只能切出齿根部分的过渡曲线。
刀顶线是用来切制被切齿轮齿根圆的。
齿条刀切齿的工作原理图2.标准齿轮的切制如图所示,齿条刀中线与齿轮坯分度圆相切并作纯滚动。
因为刀具中线上的齿厚等于齿槽宽,所以被切齿轮齿槽宽等于齿厚,即e=s。
此外,由于分度圆与中线相切,则齿根高等于齿条刀顶线至分度圆的距离(ha*+c*)m。
因为齿轮坯的齿顶圆是预先已按标准齿轮的齿顶圆直径加工好了的,故其齿顶高等于ha*m,这样切出的齿轮是标准齿轮。
3.变位齿轮的切制变位齿轮: 当齿条刀中线不与齿轮坯分度圆相切,而是相距(相割或相离)xm时,如图(a)、(c)所示的位置。
刀具的移动速度v=rω时,此时平行于刀具中线的一条直线(节线)与轮坯的分度圆相切并作纯滚动,这种改变刀具位置,使中线距离轮坯分度圆为xm时,加工出的齿轮称为变位齿轮,x称为变位系数。
距离xm为齿条中线由切制标准齿轮的位置沿轮坯径向离开或靠近齿轮坯中心所移动的距离,称为径向变位量(简称变位量),△=xm正变位齿条刀中线远离齿轮中心,变位系数取正值(x>0),称为正变位,所切出的齿轮称为正变位齿轮,负变位齿条刀中线靠近齿轮中心,变位系数取负值(x<0),称为负变位,所切出的齿轮称为负变位齿轮。
2变位齿轮用同一把齿条刀切出齿数相同的标准齿轮、正变位齿轮及负变位齿轮。
变位系数

变位系数变位系数x是径向变位系数,加工标准齿轮时,齿条形刀具中线与齿轮分度圆相切。
加工变位齿轮时齿条形刀具中线与齿轮分度圆相切位置偏移距离xm,外移x为正,内移x为负。
除了圆锥齿轮有时采用切向变位xt外,圆柱齿轮一般只采用径向变位。
变位系数x的选择不仅仅是为了凑中心距,而主要是为了提高强度和改善传动质量。
变位齿轮的主要功用如下:(1)减小齿轮传动的结构尺寸,减轻重量在传动比一定的条件下,可使小齿轮齿数zl<zmin,从而使传动的结构尺寸减小,减轻机构重量。
(2)避免根切,提高齿根的弯曲强度当小齿轮齿数z1<zmin时,可以利用正变位避免根切,提高齿根的弯曲强度。
x≥xmin=(Z-Zmin)/Zmin,对α=20o时,Zmin=17。
(3)提高齿面的接触强度采用啮合角α’>α的正传动时,由于齿廓曲率半径增大,故可以提高齿面的接触强度。
(4)提高齿面的抗胶合耐磨损能力采用啮合角α’>α的正传动,并适当分配变位系数xl、x2,使两齿轮的最大滑动率相等时,既可降低齿面接触应力,又可降低齿面间的滑动率以提高齿轮的抗胶合和耐磨损能力。
(5)配凑中心距当齿数z1、z2不变的情况下,啮合角α’不同,可以得到不同的中心距,以达到配凑中心距的目的。
(6)修复被磨损的旧齿轮齿轮传动中,小齿轮磨损较重,大齿轮磨损较轻,可以利用负变位把大齿轮齿面磨损部分切去再使用,重配一个正变位小齿轮,这就节约了修配时需要的材料与加工费用。
选择变位系数的基本原则(1)润滑条件良好的闭式齿轮传动当齿轮表面的硬度不高时(HBS<350),即对于齿面未经渗碳、渗氮、表面淬火等硬化处理的齿轮,齿面疲劳点蚀或剥伤为其主要的失效形式,这时应选择尽可能大的总变位系数x,即尽量增大啮合角,以便增大啮合节点处齿廓的综合曲率半径,减少接触应力,提高接触强度与疲劳寿命。
当轮齿表面硬度较高时(HBS>350),常因齿根疲劳裂纹的扩展造成轮齿折断而使传动失效,这时,选择变位系数应使齿轮的齿根弯曲强度尽量增大,并尽量使相啮合的两齿轮具有相近的弯曲强度。
变位齿轮的分度圆还相切吗

变位齿轮的分度圆还相切吗?无论齿轮是否变位,分度圆的大小不变!“改变”的是节圆!一对齿轮啮合时,节圆是永远相切的。
如果是高度变位,齿轮的分度圆是相切的,即,2个齿轮一个正变位,另一个负变位,并且变位系数的绝对值相等。
或者说,2个齿轮的变位系数代数和为0时,分度圆相切,否则,就不是相切的。
变位齿轮的分度圆还是相切的,只是分度圆的大小变了,分度圆的半径要加上变位量,正变位半径变大、压力角变大,负变位半径变小、压力角变小。
变位量等于变位系数乘模数x=ξm只要中心距与标准齿轮一样,两齿轮的分度圆就相切,但分度圆不一定与节圆重合。
正变位齿轮的分度圆齿厚增加了,其齿顶圆的齿厚是否也加大了? 为什么?变薄。
正变位齿轮是这样切制出来的:相对于切制标准齿轮,齿条刀具要远离轮坯中心。
为了保证切制出来的齿全高不变,这样切制出来的正变位齿轮的齿顶圆要大于标准齿轮的齿顶圆。
而齿廓渐开线都是从同一基圆发生的,这样使得正变位齿轮轮齿上同一轮齿上相向弯曲的两渐开线要比标准齿轮的长些,对应所分割的齿顶圆也就圆弧段也就短,也就是齿顶圆上的齿厚就变薄。
什么叫正变位齿轮?什么叫负变位齿轮?齿轮加工时,在滚齿机上用滚刀加工直齿圆柱齿轮,其切削过程好像一齿条与一齿轮啮合一样,在加工标准齿轮时,要求刀具的中线和被加工齿轮分度圆相切。
这样加工出来的齿轮的模数、压力角与滚刀相同。
如果不改变机床的传动比,仅改变滚刀和齿轮坯的相对位置,加工出来的齿轮叫变位齿轮,通常规定滚刀远离被切齿轮的中心时,变位系数为正值,称为正变位;滚刀移近被切齿轮中心时,变位系数为负值,称为负变位。
变位齿轮和标准齿轮在分度圆上的压力角相等吗?相互啮合的齿轮,不管是否是变位,模数和压力角必须相等,这是设计齿轮的前提。
至于压力角的数值,中国标准用20°,是以德国为标准的。
但是,在重工行业25°压力角也常用,25°比20°压力角齿根加厚,抗弯能力加强,适合重载、冲击的场合,虽然其效率略有降低,但是可以通过改善润滑油的质量弥补。
变位齿轮分度圆
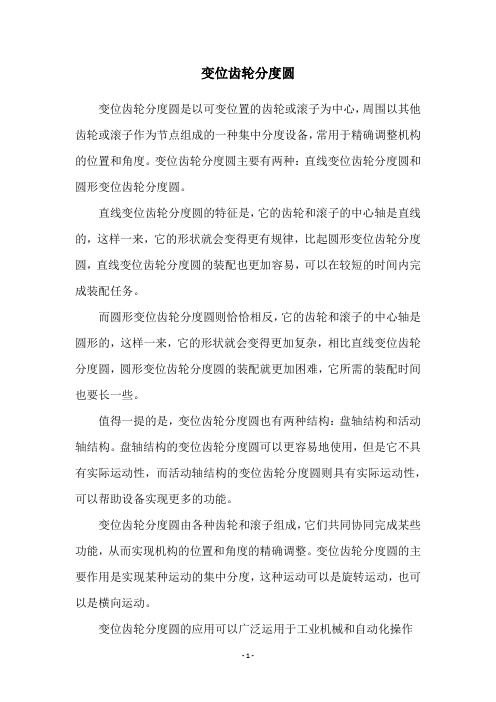
变位齿轮分度圆变位齿轮分度圆是以可变位置的齿轮或滚子为中心,周围以其他齿轮或滚子作为节点组成的一种集中分度设备,常用于精确调整机构的位置和角度。
变位齿轮分度圆主要有两种:直线变位齿轮分度圆和圆形变位齿轮分度圆。
直线变位齿轮分度圆的特征是,它的齿轮和滚子的中心轴是直线的,这样一来,它的形状就会变得更有规律,比起圆形变位齿轮分度圆,直线变位齿轮分度圆的装配也更加容易,可以在较短的时间内完成装配任务。
而圆形变位齿轮分度圆则恰恰相反,它的齿轮和滚子的中心轴是圆形的,这样一来,它的形状就会变得更加复杂,相比直线变位齿轮分度圆,圆形变位齿轮分度圆的装配就更加困难,它所需的装配时间也要长一些。
值得一提的是,变位齿轮分度圆也有两种结构:盘轴结构和活动轴结构。
盘轴结构的变位齿轮分度圆可以更容易地使用,但是它不具有实际运动性,而活动轴结构的变位齿轮分度圆则具有实际运动性,可以帮助设备实现更多的功能。
变位齿轮分度圆由各种齿轮和滚子组成,它们共同协同完成某些功能,从而实现机构的位置和角度的精确调整。
变位齿轮分度圆的主要作用是实现某种运动的集中分度,这种运动可以是旋转运动,也可以是横向运动。
变位齿轮分度圆的应用可以广泛运用于工业机械和自动化操作中,比如凸轮机构的精确控制,轮廓精加工机构的位置角度调整,装配机构的正确位置以及精密仪器的定位等等。
变位齿轮分度圆由于其精确定位,便捷性、可靠性高等特点,在工业机械和自动化行业中应用越来越广泛。
变位齿轮分度圆体现了节点和齿轮及滚子结合传动技术的优越性,它是一种各个传动节点有机结合在一起的紧凑型机构,能够实现机构精密调整及定位的特殊作用。
同时,它也是一种复杂且大型的结构,也可用于实现更多高级功能,比如实现垂直运动、微调、升降等等。
总之,变位齿轮分度圆是一种重要的传动技术,它有着重要的应用价值,可以应用于工业机械和自动化操作中,实现机构的精确调整和定位,同时它也有许多高级的功能,能够更好的帮助我们实现机构自动化操作的目标。
两齿轮啮合,分度圆相切。
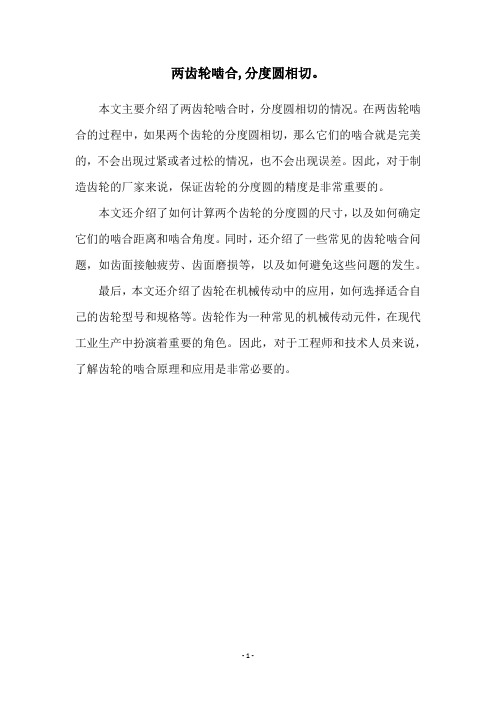
两齿轮啮合,分度圆相切。
本文主要介绍了两齿轮啮合时,分度圆相切的情况。
在两齿轮啮合的过程中,如果两个齿轮的分度圆相切,那么它们的啮合就是完美的,不会出现过紧或者过松的情况,也不会出现误差。
因此,对于制造齿轮的厂家来说,保证齿轮的分度圆的精度是非常重要的。
本文还介绍了如何计算两个齿轮的分度圆的尺寸,以及如何确定它们的啮合距离和啮合角度。
同时,还介绍了一些常见的齿轮啮合问题,如齿面接触疲劳、齿面磨损等,以及如何避免这些问题的发生。
最后,本文还介绍了齿轮在机械传动中的应用,如何选择适合自己的齿轮型号和规格等。
齿轮作为一种常见的机械传动元件,在现代工业生产中扮演着重要的角色。
因此,对于工程师和技术人员来说,了解齿轮的啮合原理和应用是非常必要的。
- 1 -。
- 1、下载文档前请自行甄别文档内容的完整性,平台不提供额外的编辑、内容补充、找答案等附加服务。
- 2、"仅部分预览"的文档,不可在线预览部分如存在完整性等问题,可反馈申请退款(可完整预览的文档不适用该条件!)。
- 3、如文档侵犯您的权益,请联系客服反馈,我们会尽快为您处理(人工客服工作时间:9:00-18:30)。
变位齿轮的分度圆还相切吗?
无论齿轮是否变位,分度圆的大小不变!“改变”的是节圆!一对齿轮啮合时,节圆是永远相切的。
如果是高度变位,齿轮的分度圆是相切的,即,2个齿轮一个正变位,另一个负变位,并且变位系数的绝对值相等。
或者说,2个齿轮的变位系数代数和为0时,分度圆相切,否则,就不是相切的。
变位齿轮的分度圆还是相切的,只是分度圆的大小变了,分度圆的半径要加上变位量,正变位半径变大、压力角变大,负变位半径变小、压力角变小。
变位量等于变位系数乘模数x=ξm
只要中心距与标准齿轮一样,两齿轮的分度圆就相切,但分度圆不一定与节圆重合。
正变位齿轮的分度圆齿厚增加了,其齿顶圆的齿厚是否也加大了? 为什么?
变薄。
正变位齿轮是这样切制出来的:相对于切制标准齿轮,齿条刀具要远离轮坯中心。
为了保证切制出来的齿全高不变,这样切制出来的正变位齿轮的齿顶圆要大于标准齿轮的齿顶圆。
而齿廓渐开线都是从同一基圆发生的,这样使得正变位齿轮轮齿上同一轮齿上相向弯曲的两渐开线要比标准齿轮的长些,对应所分割的齿顶圆也就圆弧段也就短,也就是齿顶圆上的齿厚就变薄。
什么叫正变位齿轮?什么叫负变位齿轮?
齿轮加工时,在滚齿机上用滚刀加工直齿圆柱齿轮,其切削过程好像一齿条与一齿轮啮合一样,在加工标准齿轮时,要求刀具的中线和被加工齿轮分度圆相切。
这样加工出来的齿轮的模数、压力角与滚刀相同。
如果不改变机床的传动比,仅改变滚刀和齿轮坯的相对位置,加工出来的齿轮叫变位齿轮,通常规定滚刀远离被切齿轮的中心时,变位系数为正值,称为正变位;滚刀移近被切齿轮中心时,变位系数为负值,称为负变位。
变位齿轮和标准齿轮在分度圆上的压力角相等吗?
相互啮合的齿轮,不管是否是变位,模数和压力角必须相等,这是设计齿轮的前提。
至于压力角的数值,中国标准用20°,是以德国为标准的。
但是,在重工行业25°压力角也常用,25°比20°压力角齿根加厚,抗弯能力加强,适合重载、冲击的场合,虽然其效率略有降低,但是可以通过改善润滑油的质量弥补。
我国对标准模数分度圆上的压力角有标准规定的是20°或是15°
其他参数相同的情况下相等,变位齿轮和标准齿轮用的齿廓曲线的渐开线是同一条渐开线,所以他们的基圆也是同一个。
而变位齿轮和标准齿轮的分度圆是一样的,分度圆只和模数和齿数有关。
按渐开线上压力角等于基圆半径除以该点到基圆圆心距离的值的反余弦函数。
所以就是说他们在分度圆上的压力角是一样的,按我们国家标准齿轮一般就是20°。