橡胶制品烧边、炸边、翻遍厚和修边方法
橡胶制品修边办法简介
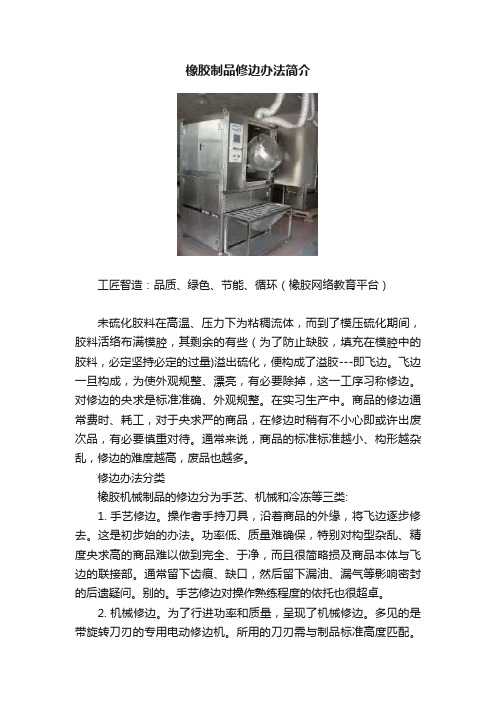
橡胶制品修边办法简介工匠智造:品质、绿色、节能、循环(橡胶网络教育平台)未硫化胶料在高温、压力下为粘稠流体,而到了模压硫化期间,胶料活络布满模腔,其剩余的有些(为了防止缺胶,填充在模腔中的胶料,必定坚持必定的过量)溢出硫化,便构成了溢胶---即飞边。
飞边一旦构成,为使外观规整、漂亮,有必要除掉,这一工序习称修边。
对修边的央求是标准准确、外观规整。
在实习生产中。
商品的修边通常费时、耗工,对于央求严的商品,在修边时稍有不小心即或许出废次品,有必要慎重对待。
通常来说,商品的标准标准越小、构形越杂乱,修边的难度越高,废品也越多。
修边办法分类橡胶机械制品的修边分为手艺、机械和冷冻等三类:1. 手艺修边。
操作者手持刀具,沿着商品的外缘,将飞边逐步修去。
这是初步始的办法。
功率低、质量难确保,特别对构型杂乱、精度央求高的商品难以做到完全、于净,而且很简略损及商品本体与飞边的联接部。
通常留下齿痕、缺口,然后留下漏油、漏气等影响密封的后遗疑问。
别的。
手艺修边对操作熟练程度的依托也很超卓。
2. 机械修边。
为了行进功率和质量,呈现了机械修边。
多见的是带旋转刀刃的专用电动修边机。
所用的刀刃需与制品标准高度匹配。
假定商品的内外缘都有飞边。
则可方案成双刃、多刃口。
以完毕一次完毕。
机械修边的加工精度跨越手艺修边,功率也有成倍行进,特别对一模多腔的商品而言,能够依照商品的摆放与分布,方案出与之匹配的刀具。
待商品出模后。
可整版套上,一次完毕冲切。
在加热的协作下,一次能修几十个。
典型比如是医用药塞整版冲切修边。
要害是冲切温度有必要掌握好,防止过高后粘连。
3. 冷冻修边。
将硫化好的制品连同飞边,在冷冻条件下进行除边。
几十年来,跟着冷冻介质的选择、换代以及机械动作的改善,冷冻修边也经历了几代改善,日臻成熟和完善,作业功率和加工质量都有了明显的行进。
其进程是让已硫化商品在冷冻和动态条件降低温,使飞边进入脆化状况。
然后通过它们自身之间的相互冲突,或在旋转、振荡、摇晃等动态条件下,借助于冲突而去掉飞边。
橡胶产品基本缺陷产生原因及解决措施

浇口设计不合理
浇口设计不合理,导致充型困难或产 生气孔等缺陷。
模具加工精度低
模具加工精度不高
导致模具配合不良,出现飞边、 溢料等问题。
模具表面粗糙
模具表面粗糙导致制品表面质量差 。
模具材料不当
使用不当材料制作模具,导致制品 不符合要求。
设备性能不良
注射机精度不高
注射机精度不高,导致注射不稳 定,制品出现气泡、银纹等缺陷
配方比例不当
橡胶配方中各种原材料的 比例不当,会影响橡胶产 品的性能。
配方设计不合理
硫化体系不合理
硫化体系是橡胶配方设计 的重要部分,硫化剂、促 进剂等配比不当,会影响 橡胶产品的性能。
补强体系不合理
补强剂的种类和用量不当 ,会影响橡胶产品的强度 和耐磨性等性能。
增塑体系不合理
增塑剂的种类和用量不当 ,会影响橡胶产品的柔软 度和耐寒性等性能。
建立完善的设备维护和保养制度 ,定期对设备进行检查、维修和
更换。
保持生产环境的清洁和卫生,减 少污染和杂质对产品质量的影响
。
加强产品使用及环境监控
对产品使用进行严格的监管和控制,避免滥用和误用。 对产品使用环境进行评估和监控,确保其符合产品要求。
建立完善的质量检测和监控体系,对产品进行定期检查和测试。
压力不均
总结词
压力不均是指在橡胶加工过程中,压力 分布不均匀,导致橡胶制品出现鼓包、 厚度不均等问题。
VS
详细描述
压力不均的原因包括模具设计不合理、压 力控制不稳定、注射速度过快或过慢等。 此缺陷会导致橡胶制品形状变形、精度降 低,影响使用性能和外观质量。
时间控制不当
总结词
时间控制不当是指在橡胶加工过程中,时间控制过长或过短,导致橡胶制品出现老化、不耐用等问题。
橡胶产品修边和检验的职责
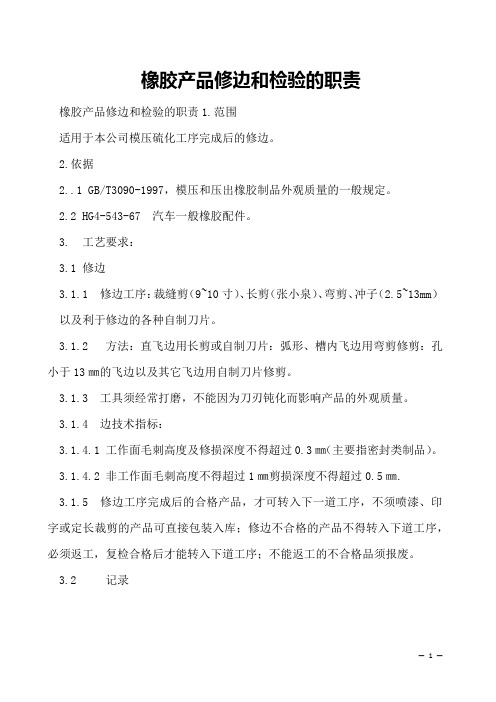
橡胶产品修边和检验的职责橡胶产品修边和检验的职责1.范围
适用于本公司模压硫化工序完成后的修边。
2.依据
2..1 GB/T3090-1997,模压和压出橡胶制品外观质量的一般规定。
2.2 HG4-543-67 汽车一般橡胶配件。
3. 工艺要求:
3.1 修边
3.1.1 修边工序:裁缝剪(9~10寸)、长剪(张小泉)、弯剪、冲子(2.5~13mm)
以及利于修边的各种自制刀片。
3.1.2 方法:直飞边用长剪或自制刀片:弧形、槽内飞边用弯剪修剪:孔小于13㎜的飞边以及其它飞边用自制刀片修剪。
3.1.3 工具须经常打磨,不能因为刀刃钝化而影响产品的外观质量。
3.1.4 边技术指标:
3.1.
4.1 工作面毛刺高度及修损深度不得超过0.3㎜(主要指密封类制品)。
3.1.
4.2 非工作面毛刺高度不得超过1㎜剪损深度不得超过0.5㎜.
3.1.5 修边工序完成后的合格产品,才可转入下一道工序,不须喷漆、印字或定长裁剪的产品可直接包装入库;修边不合格的产品不得转入下道工序,必须返工,复检合格后才能转入下道工序;不能返工的不合格品须报废。
3.2 记录
—1 —。
橡胶基础知识及常见缺陷改善对策
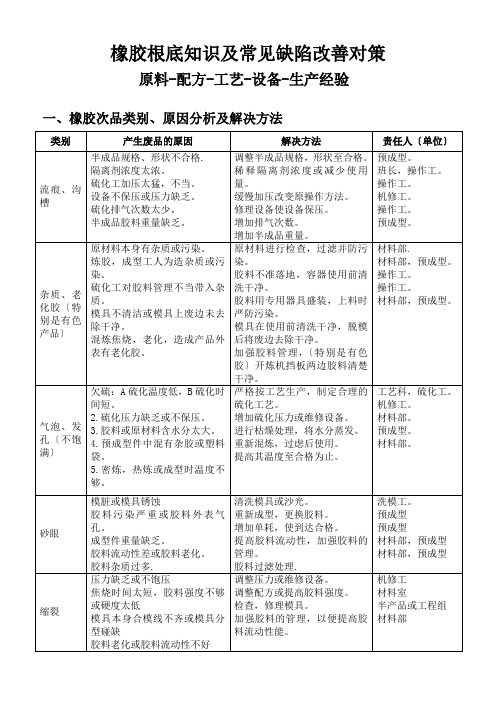
橡胶根底知识及常见缺陷改善对策原料-配方-工艺-设备-生产经验一、橡胶次品类别、原因分析及解决方法二.橡胶硫化工应知应会硫化工应知应会的目的:促使硫化工掌握橡胶材料和硫化的根本知识,提高硫化工专业理论知识和操作技能,更有效地效劳与新产品开发试试制工作从而提高硫化工自身的素质,使试制开发产品及时按期交样,并确保新模上线生产的产品合格率和生产效率最大化。
1.应知:1.熟知硫化三要素之间的相互关系及对产品的影响。
2.熟知橡胶产品各工序的生产,及其所使用的设备,设备的操作规程,产品的加工方法。
3.熟知模具、设备工装夹具的操作规程,平安知识及保养知识。
4.了解橡胶产品的使用的胶料代号,胶种及硫化工艺性能,以及主导产品的主要工作部位,外观质量标准。
5.应知硫化时间制定的依据,并能对生产中出现的一般质量缺陷进行分析、解决,并对复杂的问题提出改良意见。
2.应会:1.能够熟练掌握及使用各类结构橡胶模具的试模方法。
2.能鉴别各种胶号、胶料及胶料的外观质量的好坏、并能根据胶料代号准确判定材料的硬度。
3.能看懂各类结构的产品图、模具图及了解模具加工的根本知识。
4.会使用游标卡尺、测厚仪、测温仪,并了解其工作原理。
5.能确定出最正确、最合理的硫化工艺参数、操作技能并应用于生产。
7.能分析试模、试生产过程中出现的质量缺陷的原因,并能提出改良意见。
三.橡胶和塑料之间的区别塑料与橡胶最本质的区别在于塑料发生形变时塑性变形,而橡胶是弹性变形。
换句话说,塑料变形后不容易恢复原状态,而橡胶相对来说就容易得多。
塑料的弹性是很小的,通常小于100%,而橡胶可以到达1000%甚至更多。
塑料在成型上绝大多数成型过程完毕产品过程也就完毕;而橡胶成型过程完毕后还得需要硫化过程。
塑料与橡胶同属于高分子材料,主要由碳和氢两种原子组成,另有一些含有少量氧,氮,氯,硅,氟,硫等原子,其性能特殊,用途也特别.在常温下,塑料是固态,很硬,不能拉伸变形.而橡胶硬度不高,有弹性,可拉伸变长,停止拉伸又可回复原状.这是由于它们的分子结构不同造成的.另一不同点是塑料可以屡次回收重复使用,而橡胶那么不能直接回收使用,只能经过加工制成再生胶,然后才可用.塑料在100多度至200度时的形态与橡胶在60至100度时的形态相似. 广义地说,橡胶其实是塑料的一种,塑料包括橡胶。
橡胶制品的基本工艺过程
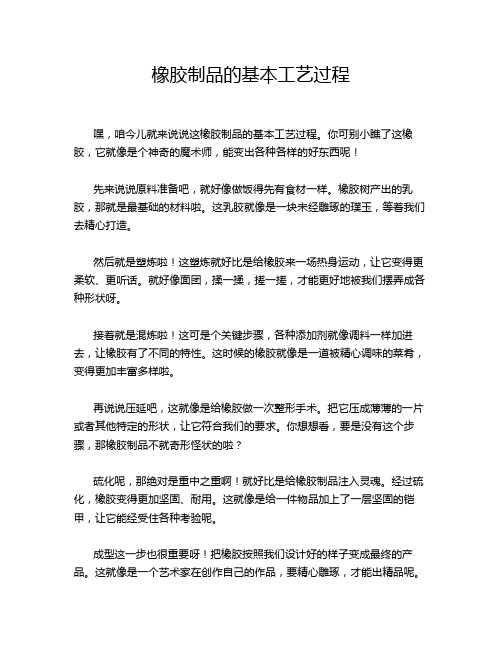
橡胶制品的基本工艺过程嘿,咱今儿就来说说这橡胶制品的基本工艺过程。
你可别小瞧了这橡胶,它就像是个神奇的魔术师,能变出各种各样的好东西呢!先来说说原料准备吧,就好像做饭得先有食材一样。
橡胶树产出的乳胶,那就是最基础的材料啦。
这乳胶就像是一块未经雕琢的璞玉,等着我们去精心打造。
然后就是塑炼啦!这塑炼就好比是给橡胶来一场热身运动,让它变得更柔软、更听话。
就好像面团,揉一揉,搓一搓,才能更好地被我们摆弄成各种形状呀。
接着就是混炼啦!这可是个关键步骤,各种添加剂就像调料一样加进去,让橡胶有了不同的特性。
这时候的橡胶就像是一道被精心调味的菜肴,变得更加丰富多样啦。
再说说压延吧,这就像是给橡胶做一次整形手术。
把它压成薄薄的一片或者其他特定的形状,让它符合我们的要求。
你想想看,要是没有这个步骤,那橡胶制品不就奇形怪状的啦?硫化呢,那绝对是重中之重啊!就好比是给橡胶制品注入灵魂。
经过硫化,橡胶变得更加坚固、耐用。
这就像是给一件物品加上了一层坚固的铠甲,让它能经受住各种考验呢。
成型这一步也很重要呀!把橡胶按照我们设计好的样子变成最终的产品。
这就像是一个艺术家在创作自己的作品,要精心雕琢,才能出精品呢。
最后就是修边啦,把那些不完美的边边角角修整一下,让产品看起来更加精致美观。
你说这橡胶制品的工艺过程是不是很神奇?从普普通通的乳胶变成我们生活中各种各样实用的东西。
像什么轮胎呀,橡胶手套呀,都是这么来的呢!这中间得经过多少人的努力和心血呀!咱平常可能没太注意这些橡胶制品背后的故事,现在了解了,是不是对它们多了一份敬意呢?下次你再看到橡胶制品的时候,就想想它们是怎么一步步被制造出来的,是不是觉得很有意思呀?所以呀,可别小看了这橡胶制品的基本工艺过程,这里面的学问大着呢!。
橡胶制品硫化异常原因分析及解决措施
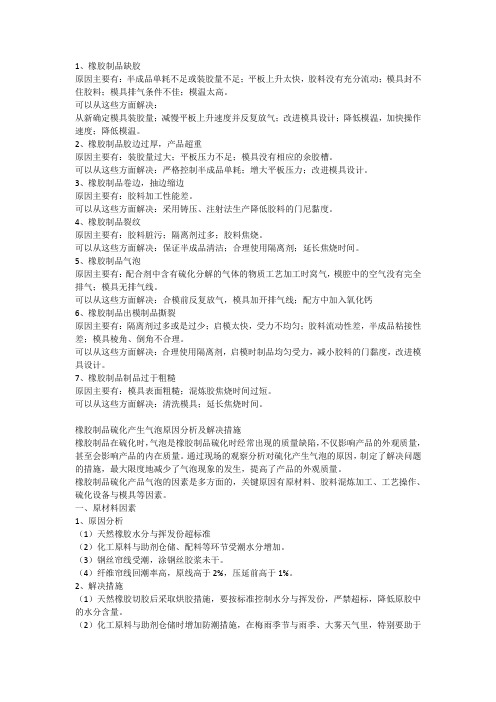
1、橡胶制品缺胶原因主要有:半成品单耗不足或装胶量不足;平板上升太快,胶料没有充分流动;模具封不住胶料;模具排气条件不佳;模温太高。
可以从这些方面解决:从新确定模具装胶量;减慢平板上升速度并反复放气;改进模具设计;降低模温,加快操作速度;降低模温。
2、橡胶制品胶边过厚,产品超重原因主要有:装胶量过大;平板压力不足;模具没有相应的余胶槽。
可以从这些方面解决:严格控制半成品单耗;增大平板压力;改进模具设计。
3、橡胶制品卷边,抽边缩边原因主要有:胶料加工性能差。
可以从这些方面解决:采用铸压、注射法生产降低胶料的门尼黏度。
4、橡胶制品裂纹原因主要有:胶料脏污;隔离剂过多;胶料焦烧。
可以从这些方面解决:保证半成品清洁;合理使用隔离剂;延长焦烧时间。
5、橡胶制品气泡原因主要有:配合剂中含有硫化分解的气体的物质工艺加工时窝气,模腔中的空气没有完全排气;模具无排气线。
可以从这些方面解决:合模前反复放气,模具加开排气线;配方中加入氧化钙6、橡胶制品出模制品撕裂原因主要有:隔离剂过多或是过少;启模太快,受力不均匀;胶料流动性差,半成品粘接性差;模具棱角、倒角不合理。
可以从这些方面解决:合理使用隔离剂,启模时制品均匀受力,减小胶料的门黏度,改进模具设计。
7、橡胶制品制品过于粗糙原因主要有:模具表面粗糙;混炼胶焦烧时间过短。
可以从这些方面解决:清洗模具;延长焦烧时间。
橡胶制品硫化产生气泡原因分析及解决措施橡胶制品在硫化时,气泡是橡胶制品硫化时经常出现的质量缺陷,不仅影响产品的外观质量,甚至会影响产品的内在质量。
通过现场的观察分析对硫化产生气泡的原因,制定了解决问题的措施,最大限度地减少了气泡现象的发生,提高了产品的外观质量。
橡胶制品硫化产品气泡的因素是多方面的,关键原因有原材料、胶料混炼加工、工艺操作、硫化设备与模具等因素。
一、原材料因素1、原因分析(1)天然橡胶水分与挥发份超标准(2)化工原料与助剂仓储、配料等环节受潮水分增加。
橡胶飞边产生的原因及解决方法-精品文档
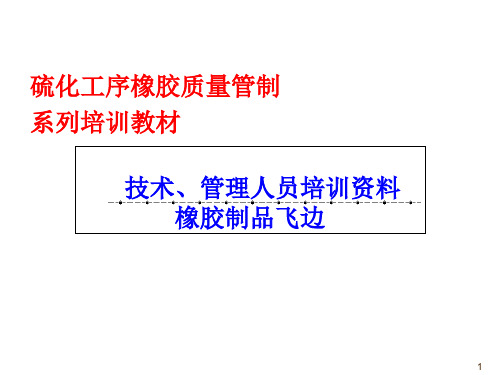
• 3.3硫化三要素 • 三要素指温度、时间、压力; • 尤其是硫化压力,胶料在硫化过程中,原来的微量水 分及硫化反应产生的气体释出,产生内因力,因此必 须在硫化过程中施加大于胶料可能产生的内因力; • 高温高压会使某些高聚物交联或裂解,因此生产上应 根据产品要求设定硫化压力; • 过高硫化压力会增加工厂设备维护费用。
10
无锡中策
AUTOMOTIVE
WuXi CSI
三、抑制或减少橡胶制品飞边的方法
• 3.8橡胶转矩ML、MH • ML——最低转矩,N•m(kgf•cm) • MH——到达规定时间之后仍然不出现平坦曲线或最高 转矩的硫化曲线,所达到的最高转矩N•m(kgf•cm) • ML:表示胶料的流动性, ML 越低,流动性越好,反 之,越差。 • MH:表征胶料的胶料的剪切模数、硬度、定伸强度和 交联密度,一般MH越低,硬度越低,MH越高,硬度 越高。 • 结论:ML、MH不稳定造成飞边或多或少
2
无锡中策AUTOMOTIVEW NhomakorabeaXi CSI
二、橡胶制品飞边影响
• 1. 飞边的形成改变了模制品的封模尺寸,使制品的部分性能受到
影响(特别是对要求严格的各类密封制品) • 2.飞边的修除,尤其是手工修除,明显而严重地影响了制品的表观 质量,从而降低了制品的商业价值。常言道:“货卖一张皮”, 讲的就是这个道理。修掉的飞边,其痕迹高低不一,残留各异, 直接影响了企业在客户心目中的影响,使企业在市场上失去了竞 争力。 • 3.产品的设计一般是不允许出现飞边的,从质量要求和角度来讲 必须对其进行修炼,修除飞边需要大量的人力和相应的设备(冷 冻修电机等)场地等,这无形中增加了一道工序,延长了生产的 周期,从经营角度讲,飞边的修除增加了生产成本。 • 4.飞边的形成,使胶料的消耗量增大,提高了生产成本同时它又 是一种资源浪费,对于环境也是一种潜在的污染。
橡胶裂缝修补的常见方法
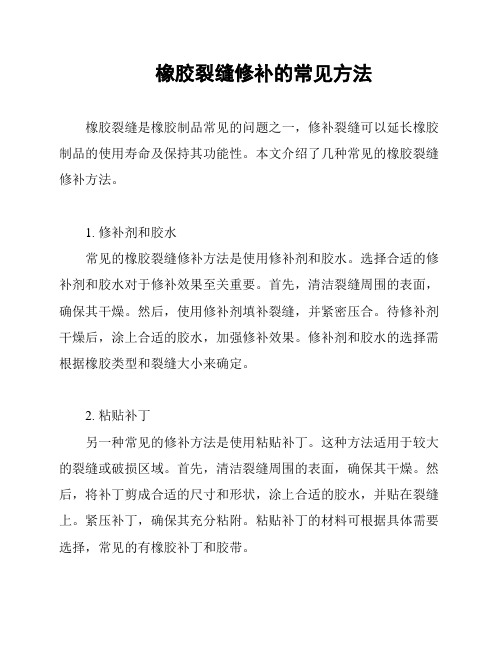
橡胶裂缝修补的常见方法橡胶裂缝是橡胶制品常见的问题之一,修补裂缝可以延长橡胶制品的使用寿命及保持其功能性。
本文介绍了几种常见的橡胶裂缝修补方法。
1. 修补剂和胶水常见的橡胶裂缝修补方法是使用修补剂和胶水。
选择合适的修补剂和胶水对于修补效果至关重要。
首先,清洁裂缝周围的表面,确保其干燥。
然后,使用修补剂填补裂缝,并紧密压合。
待修补剂干燥后,涂上合适的胶水,加强修补效果。
修补剂和胶水的选择需根据橡胶类型和裂缝大小来确定。
2. 粘贴补丁另一种常见的修补方法是使用粘贴补丁。
这种方法适用于较大的裂缝或破损区域。
首先,清洁裂缝周围的表面,确保其干燥。
然后,将补丁剪成合适的尺寸和形状,涂上合适的胶水,并贴在裂缝上。
紧压补丁,确保其充分粘附。
粘贴补丁的材料可根据具体需要选择,常见的有橡胶补丁和胶带。
3. 热固化修补对于一些较为严重的裂缝,热固化修补是一个有效的方法。
这种方法通常适用于橡胶制品的专业修理。
热固化修补需要专业设备,如加热板和热固化胶水。
首先,将加热板加热至适当温度,然后将橡胶制品放置在加热板上,让裂缝处于加热状态。
接下来,将热固化胶水涂在裂缝上,等待一段时间,让胶水固化。
最后,将橡胶制品从加热板上取下,并进行必要的修整。
总结:橡胶裂缝的修补可以采用修补剂和胶水、粘贴补丁或热固化修补等方法。
选择合适的修补方法需要考虑橡胶类型、裂缝大小和修补的持久性要求。
在修补过程中,注意确保表面清洁干燥,并按照厂家的指导或专业人士的建议进行操作。
以上是几种常见的橡胶裂缝修补方法,希望能对您有所帮助。
型橡胶密封圈的修边处理方法【技巧】
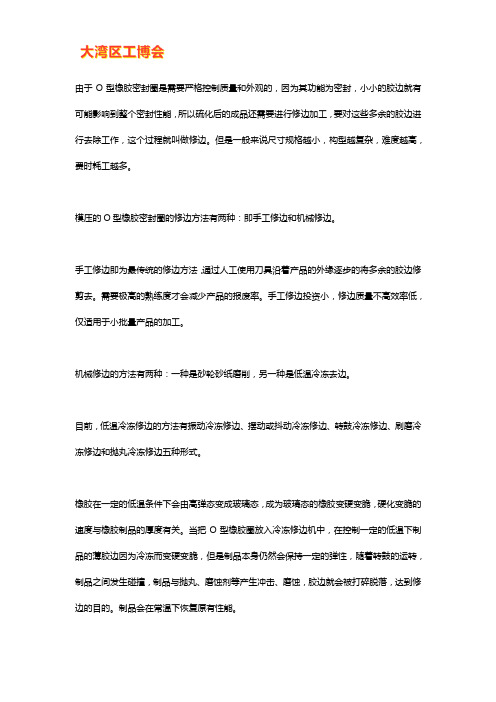
由于O型橡胶密封圈是需要严格控制质量和外观的,因为其功能为密封,小小的胶边就有可能影响到整个密封性能,所以硫化后的成品还需要进行修边加工,要对这些多余的胶边进行去除工作,这个过程就叫做修边。
但是一般来说尺寸规格越小,构型越复杂,难度越高,费时耗工越多。
模压的O型橡胶密封圈的修边方法有两种:即手工修边和机械修边。
手工修边即为最传统的修边方法,通过人工使用刀具沿着产品的外缘逐步的将多余的胶边修剪去。
需要极高的熟练度才会减少产品的报废率。
手工修边投资小,修边质量不高效率低,仅适用于小批量产品的加工。
机械修边的方法有两种:一种是砂轮砂纸磨削,另一种是低温冷冻去边。
目前,低温冷冻修边的方法有振动冷冻修边、摆动或抖动冷冻修边、转鼓冷冻修边、刷磨冷冻修边和抛丸冷冻修边五种形式。
橡胶在一定的低温条件下会由高弹态变成玻璃态,成为玻璃态的橡胶变硬变脆,硬化变脆的速度与橡胶制品的厚度有关。
当把O型橡胶圈放入冷冻修边机中,在控制一定的低温下制品的薄胶边因为冷冻而变硬变脆,但是制品本身仍然会保持一定的弹性,随着转鼓的运转,制品之间发生碰撞,制品与抛丸、磨蚀剂等产生冲击、磨蚀,胶边就会被打碎脱落,达到修边的目的。
制品会在常温下恢复原有性能。
低温冷冻修边生产效率高,经济效益好。
但是对于内圈的去边效果较差。
另一种就砂轮砂纸磨削了。
将硫化完的O型密封圈套在内径尺寸与之相匹配的砂棒或尼龙棒上,靠电机带动其旋转,外圆采用砂纸或砂轮,通过摩擦去除掉多余的胶边。
这种方法比较简单方便,效率也会比手工修边的高,特别适用于规格小、批量较大的产品。
缺点就是这种修边系靠砂轮磨削,修边精度较差,磨削表面较粗糙。
橡胶制品的冷冻修边
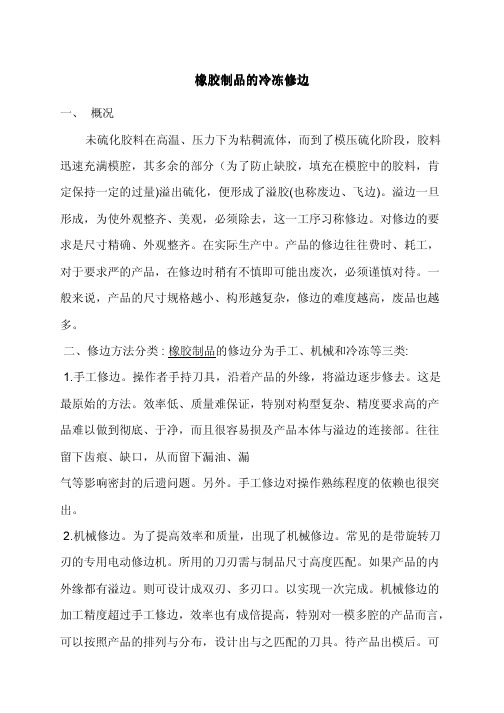
橡胶制品的冷冻修边一、 概况未硫化胶料在高温、压力下为粘稠流体,而到了模压硫化阶段,胶料迅速充满模腔,其多余的部分(为了防止缺胶,填充在模腔中的胶料,肯定保持一定的过量)溢出硫化,便形成了溢胶(也称废边、飞边)。
溢边一旦形成,为使外观整齐、美观,必须除去,这一工序习称修边。
对修边的要求是尺寸精确、外观整齐。
在实际生产中。
产品的修边往往费时、耗工,对于要求严的产品,在修边时稍有不慎即可能出废次,必须谨慎对待。
一般来说,产品的尺寸规格越小、构形越复杂,修边的难度越高,废品也越多。
二、修边方法分类 : 橡胶制品的修边分为手工、机械和冷冻等三类:1.手工修边。
操作者手持刀具,沿着产品的外缘,将溢边逐步修去。
这是最原始的方法。
效率低、质量难保证,特别对构型复杂、精度要求高的产品难以做到彻底、于净,而且很容易损及产品本体与溢边的连接部。
往往留下齿痕、缺口,从而留下漏油、漏气等影响密封的后遗问题。
另外。
手工修边对操作熟练程度的依赖也很突出。
2.机械修边。
为了提高效率和质量,出现了机械修边。
常见的是带旋转刀刃的专用电动修边机。
所用的刀刃需与制品尺寸高度匹配。
如果产品的内外缘都有溢边。
则可设计成双刃、多刃口。
以实现一次完成。
机械修边的加工精度超过手工修边,效率也有成倍提高,特别对一模多腔的产品而言,可以按照产品的排列与分布,设计出与之匹配的刀具。
待产品出模后。
可整版套上,一次完成冲切。
在加热的配合下,一次能修几十个。
典型例子是医用药塞整版冲切修边。
关键是冲切温度必须掌握好,防止过高后粘连。
3.冷冻修边。
将硫化好的成品连同废边,在冷冻条件下进行除边。
几十年来,随着冷冻介质的选择、换代以及机械动作的改进,冷冻修边也经历了几代改进,日臻成熟和完善,工作效率和加工质量都有了明显的提高。
其过程是让已硫化产品在冷冻和动态条件下降温,使废边进入脆化状态。
然后经过它们自身之间的相互摩擦,或在旋转、振动、摆动等动态条件下,借助于摩擦而去除废边。
橡胶制品烧边分析
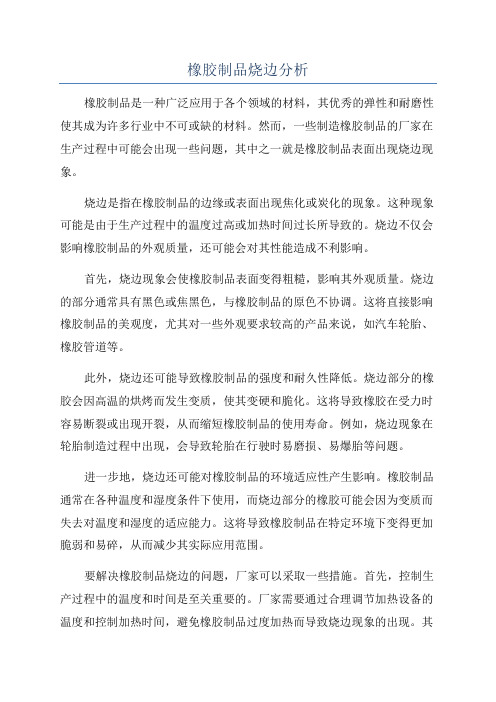
橡胶制品烧边分析橡胶制品是一种广泛应用于各个领域的材料,其优秀的弹性和耐磨性使其成为许多行业中不可或缺的材料。
然而,一些制造橡胶制品的厂家在生产过程中可能会出现一些问题,其中之一就是橡胶制品表面出现烧边现象。
烧边是指在橡胶制品的边缘或表面出现焦化或炭化的现象。
这种现象可能是由于生产过程中的温度过高或加热时间过长所导致的。
烧边不仅会影响橡胶制品的外观质量,还可能会对其性能造成不利影响。
首先,烧边现象会使橡胶制品表面变得粗糙,影响其外观质量。
烧边的部分通常具有黑色或焦黑色,与橡胶制品的原色不协调。
这将直接影响橡胶制品的美观度,尤其对一些外观要求较高的产品来说,如汽车轮胎、橡胶管道等。
此外,烧边还可能导致橡胶制品的强度和耐久性降低。
烧边部分的橡胶会因高温的烘烤而发生变质,使其变硬和脆化。
这将导致橡胶在受力时容易断裂或出现开裂,从而缩短橡胶制品的使用寿命。
例如,烧边现象在轮胎制造过程中出现,会导致轮胎在行驶时易磨损、易爆胎等问题。
进一步地,烧边还可能对橡胶制品的环境适应性产生影响。
橡胶制品通常在各种温度和湿度条件下使用,而烧边部分的橡胶可能会因为变质而失去对温度和湿度的适应能力。
这将导致橡胶制品在特定环境下变得更加脆弱和易碎,从而减少其实际应用范围。
要解决橡胶制品烧边的问题,厂家可以采取一些措施。
首先,控制生产过程中的温度和时间是至关重要的。
厂家需要通过合理调节加热设备的温度和控制加热时间,避免橡胶制品过度加热而导致烧边现象的出现。
其次,厂家可以使用一些防焦炭的添加剂,加入到橡胶配方中,以提高橡胶制品的耐热性。
此外,定期检查加热设备,确保其工作状态正常,也是避免烧边的重要措施之一总之,橡胶制品烧边是一种常见的生产问题,可能会影响橡胶制品的外观质量、强度和耐久性。
厂家可以通过控制生产过程中的温度和时间、使用防焦炭的添加剂及定期检查设备等措施,来避免烧边现象的出现,提高橡胶制品的质量和性能。
这将有助于增加产品的竞争力和市场份额。
橡胶制品常见问题及解决方法

橡胶制品常见问题及解决方法橡胶制品的应用范围日益广泛,使用要求越来越高,巩义市盛源水电设备材料厂作为专业的橡胶补偿器生产厂家,拥有自己独立的研发实验室,凭借几十年各类型橡胶软连接的生产制作经验,总结出以下橡胶制品常见问题及解决方法,供各位同行研究借鉴:橡胶制品常见的缺陷一般表现为橡胶-金属粘接不良、气泡、橡胶表面发粘、缺胶、缩孔、喷霜、分层、撕裂等。
1.橡胶-金属粘接不良橡胶与金属的粘结是橡胶减震产品一个重要环节,橡胶与金属的粘结原理,普遍认为在低模量的橡胶与高模量的金属之间,胶粘剂成为模量梯度,以减少粘结件受力时的应力集中。
常用双涂型胶浆的底涂或单涂型胶粘剂与金属表面之间主要通过吸附作用实现粘结。
底涂型和面涂型胶粘剂之间,以及胶粘剂与橡胶之间通过相互扩散作用和共交联作用而实现粘结。
橡胶-金属粘接不良的原因分析及解决方法1.1 胶浆选用不对。
解决方法:参考具体使用手册,选择合适的胶粘剂1.2 金属表面处理失败,以致底涂的物理吸附不能很好的实现。
解决方法;粗化金属表面,保证金属粘结表面一定的粗糙度。
常用的处理方法,显微镜观察表面粗糙度从大到小依次是喷砂、抛丸>磷化>镀锌.金属表面不能有锈蚀,不能粘到油污、灰尘、杂质等1.3胶浆涂刷工艺稳定性差,胶浆太稀、漏涂、少涂、残留溶剂等。
解决方法;注意操作,防止胶浆漏涂、少涂。
涂好胶浆的金属件应注意充分干燥,让溶剂充分挥发,防止残留溶剂随硫化时挥发,导致粘结失败。
要保证一定的涂胶厚度,特别是面涂胶浆。
这样一方面可以有充足物质使相互扩散和共交联作用充分进行;另一方面可以实现一定的模量梯度层1.4配方不合理,胶料硫化速度与胶浆硫化速度不一致。
解决方法;改进配方以保证有充足的焦烧时间。
模具、配方改进,保证胶料以最快的速度到达粘结部位。
尽量采用普通、半有效硫化体系,提高硫黄用量,以实现多硫交联键。
改进硫化条件(温度、时间和压力)。
减少易喷霜物和增塑剂的使用,防止其迁移到橡胶表面,从而影响粘结。
橡胶制品常见的修边方法与技巧
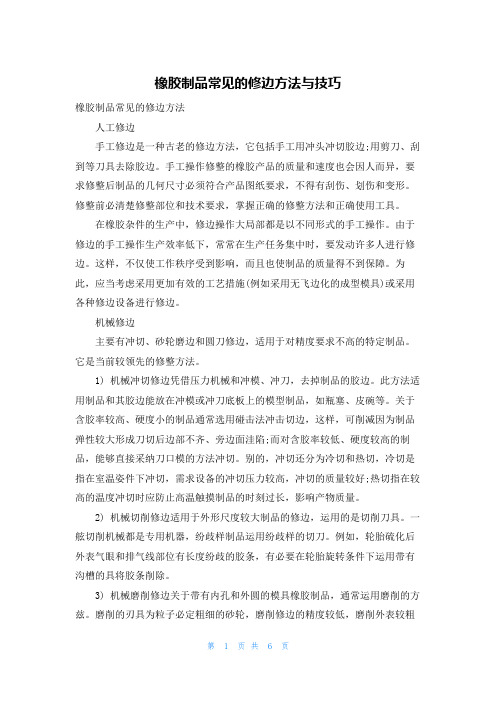
橡胶制品常见的修边方法与技巧橡胶制品常见的修边方法人工修边手工修边是一种古老的修边方法,它包括手工用冲头冲切胶边;用剪刀、刮到等刀具去除胶边。
手工操作修整的橡胶产品的质量和速度也会因人而异,要求修整后制品的几何尺寸必须符合产品图纸要求,不得有刮伤、划伤和变形。
修整前必清楚修整部位和技术要求,掌握正确的修整方法和正确使用工具。
在橡胶杂件的生产中,修边操作大局部都是以不同形式的手工操作。
由于修边的手工操作生产效率低下,常常在生产任务集中时,要发动许多人进行修边。
这样,不仅使工作秩序受到影响,而且也使制品的质量得不到保障。
为此,应当考虑采用更加有效的工艺措施(例如采用无飞边化的成型模具)或采用各种修边设备进行修边。
机械修边主要有冲切、砂轮磨边和圆刀修边,适用于对精度要求不高的特定制品。
它是当前较领先的修整方法。
1) 机械冲切修边凭借压力机械和冲模、冲刀,去掉制品的胶边。
此方法适用制品和其胶边能放在冲模或冲刀底板上的模型制品,如瓶塞、皮碗等。
关于含胶率较高、硬度小的制品通常选用碰击法冲击切边,这样,可削减因为制品弹性较大形成刀切后边部不齐、旁边面洼陷;而对含胶率较低、硬度较高的制品,能够直接采纳刀口模的方法冲切。
别的,冲切还分为冷切和热切,冷切是指在室温姿件下冲切,需求设备的冲切压力较高,冲切的质量较好;热切指在较高的温度冲切时应防止高温触摸制品的时刻过长,影响产物质量。
2) 机械切削修边适用于外形尺度较大制品的修边,运用的是切削刀具。
一舷切削机械都是专用机器,纷歧样制品运用纷歧样的切刀。
例如,轮胎硫化后外表气眼和排气线部位有长度纷歧的胶条,有必要在轮胎旋转条件下运用带有沟槽的具将胶条削除。
3) 机械磨削修边关于带有内孔和外圆的模具橡胶制品,通常运用磨削的方兹。
磨削的刃具为粒子必定粗细的砂轮,磨削修边的精度较低,磨削外表较粗糙^有能够夹有剩余的砂粒,影响运用效果。
4) 低温抛丸修边关于修边质量需求较高的精密制品,如O形圈、小皮碗等,可选用此法修边。
橡胶加工工艺的胶料问题的解决办法
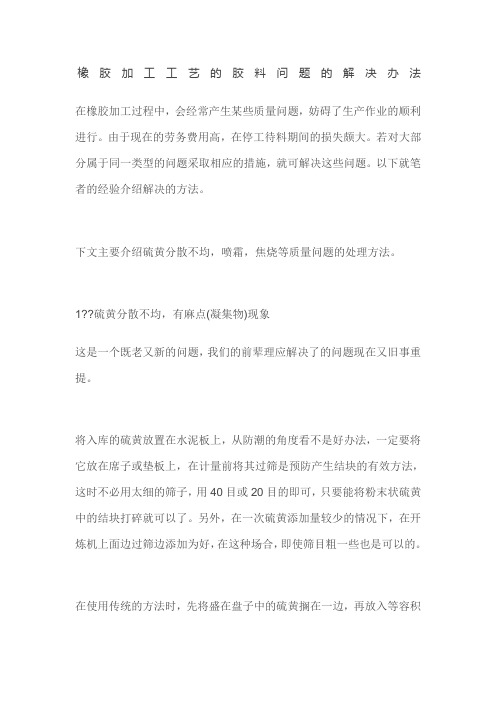
橡胶加工工艺的胶料问题的解决办法在橡胶加工过程中,会经常产生某些质量问题,妨碍了生产作业的顺利进行。
由于现在的劳务费用高,在停工待料期间的损失颇大。
若对大部分属于同一类型的问题采取相应的措施,就可解决这些问题。
以下就笔者的经验介绍解决的方法。
下文主要介绍硫黄分散不均,喷霜,焦烧等质量问题的处理方法。
1??硫黄分散不均,有麻点(凝集物)现象这是一个既老又新的问题,我们的前辈理应解决了的问题现在又旧事重提。
将入库的硫黄放置在水泥板上,从防潮的角度看不是好办法,一定要将它放在席子或垫板上,在计量前将其过筛是预防产生结块的有效方法,这时不必用太细的筛子,用40目或20目的即可,只要能将粉末状硫黄中的结块打碎就可以了。
另外,在一次硫黄添加量较少的情况下,在开炼机上面边过筛边添加为好,在这种场合,即使筛目粗一些也是可以的。
在使用传统的方法时,先将盛在盘子中的硫黄搁在一边,再放入等容积的轻质碳酸钙或白呈粉,搅拌均匀后在开炼机上进行添加,虽然这是一种简便的做法,但没有比这更好的方法。
此处简单介绍一下什么是白呈粉,将牡蝠壳、贝壳堆放在室外的水泥板上,任其风吹曰晒雨淋,放置2-3年后,里面的有机物质被分解除去,成为雪白的只有钙成分的物质,将其粉碎后就是白呈粉,该粉料除了可用于橡胶外,还可用于其他方面。
在配合了大量硬质陶土的橡胶中,不知是何种原因造成硫黄分散不均。
尽管人们想出了许多办法,但仍未奏效。
我们将配合了与硫黄等质量份的硬质陶土之母炼胶用捏和机进行混合,再用该公司自制的40L捏炼机(转速约为30rpm/min)进行约1h的混和,使用这样的母炼胶,未发现硫黄颗粒,可以说这是侥幸成功的实例。
自制的硫黄母炼胶是供该公司本身使用的。
但是,公司内所有橡胶一旦都使用母炼胶的话,则其用量会过大,品种繁多,需要专门加工母炼胶的炼胶机,这样做费时费力。
于是,除了目前尚未发生问题的混炼胶及允许有少许硫黄颗粒的混炼胶外,只对确实有需要的胶料才使用硫黄母炼胶。
爆边解决办法

爆边(分层)的解决方法
爆边现象.主要的原因有很多,但基本上是这几个:
1.硫化温度太高
2.胶料的焦烧时间太短,或胶料已经有焦烧倾向
3.排气的次数太多.压力太大,可以适当减少排气,并采用低压排气.
4.所用原料重量过多,多余的原料没有办法流走
5.模具的自拆边太尖或有毛刺,适当处理后可改善.
应先排除其他因素的情况下,在考虑模具.要不模具打磨后就不好修复了.呵呵“开模裂伤”或“裂痕”的原因和防止
在模具分型线处出现裂伤或裂痕,对于大型橡胶制品是容易发生的质量问题。
其原因在于,橡胶硫化是放热反应,胶料内部温度上升并超过设定的硫化温度,在高温下胶料膨胀,使模型内产生过剩压力。
该压力在硫化初期使上下半模稍稍张开,少量未硫化甚至是初步硫化的胶料会被挤压到两个半模之间。
经过一段时间后,模内压力下降,外压又使模具紧紧闭合,但原来被挤出的胶边不能随产品顺利收缩,仍留在半模之间,胶边与产品出现撕裂,这种情况就容易产生“开模裂伤”或“裂痕”。
为了避免制品产生裂伤,通常可采用以下措施:
(1)通过缓压降低模型内部过剩压力或适当降低硫化温度。
(2)少用或不用低挥发性配合剂,避免胶料过度膨胀;
(3)增加胶料焦烧时间,延长其流动时间;
(4)模型中装胶量不宜过多。
(5)改变加压程序,即在硫化开始时加高压,当胶边形成后,再用低压硫化,使胶边能回缩,这样可以防止两个半模紧紧夹住胶边使其撕裂。
(6)预热胶料,增加流动性,确保边部胶料定型前已充分流动,亦能大大减少开模裂伤。
(7)可把模具设计成类似柱塞的形状,使得模具稍稍张开时,胶料挤不进模口中去,从而杜绝裂伤。
橡胶烧边的原因
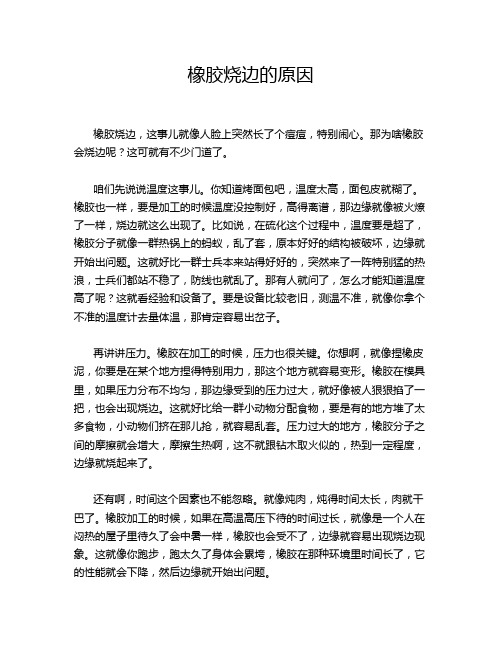
橡胶烧边的原因橡胶烧边,这事儿就像人脸上突然长了个痘痘,特别闹心。
那为啥橡胶会烧边呢?这可就有不少门道了。
咱们先说说温度这事儿。
你知道烤面包吧,温度太高,面包皮就糊了。
橡胶也一样,要是加工的时候温度没控制好,高得离谱,那边缘就像被火燎了一样,烧边就这么出现了。
比如说,在硫化这个过程中,温度要是超了,橡胶分子就像一群热锅上的蚂蚁,乱了套,原本好好的结构被破坏,边缘就开始出问题。
这就好比一群士兵本来站得好好的,突然来了一阵特别猛的热浪,士兵们都站不稳了,防线也就乱了。
那有人就问了,怎么才能知道温度高了呢?这就看经验和设备了。
要是设备比较老旧,测温不准,就像你拿个不准的温度计去量体温,那肯定容易出岔子。
再讲讲压力。
橡胶在加工的时候,压力也很关键。
你想啊,就像捏橡皮泥,你要是在某个地方捏得特别用力,那这个地方就容易变形。
橡胶在模具里,如果压力分布不均匀,那边缘受到的压力过大,就好像被人狠狠掐了一把,也会出现烧边。
这就好比给一群小动物分配食物,要是有的地方堆了太多食物,小动物们挤在那儿抢,就容易乱套。
压力过大的地方,橡胶分子之间的摩擦就会增大,摩擦生热啊,这不就跟钻木取火似的,热到一定程度,边缘就烧起来了。
还有啊,时间这个因素也不能忽略。
就像炖肉,炖得时间太长,肉就干巴了。
橡胶加工的时候,如果在高温高压下待的时间过长,就像是一个人在闷热的屋子里待久了会中暑一样,橡胶也会受不了,边缘就容易出现烧边现象。
这就像你跑步,跑太久了身体会累垮,橡胶在那种环境里时间长了,它的性能就会下降,然后边缘就开始出问题。
原料的质量也是个大问题。
要是橡胶原料本身就不太好,就像盖房子用的砖头质量差,那怎么能盖出好房子呢?不好的橡胶原料可能本身就存在一些不稳定的因素,就像一颗定时炸弹,在加工过程中,稍微有点风吹草动,比如温度、压力有点波动,就容易引发烧边这种问题。
这就好比一个身体本来就弱的人,稍微受点风寒就生病,橡胶原料不好,加工过程稍微有点不合适就烧边。
- 1、下载文档前请自行甄别文档内容的完整性,平台不提供额外的编辑、内容补充、找答案等附加服务。
- 2、"仅部分预览"的文档,不可在线预览部分如存在完整性等问题,可反馈申请退款(可完整预览的文档不适用该条件!)。
- 3、如文档侵犯您的权益,请联系客服反馈,我们会尽快为您处理(人工客服工作时间:9:00-18:30)。
橡胶模压制品烧边
橡胶制品在硫化时在合模线位置产生明显开裂的融合不良的现象,一般把它称为“烧边”,一但出现,往往产生大量的废次品,严重影响生产的正常进行,下面就对这一现象进行分析,希望对问题的解决有所帮助。
橡胶的硫化是一个复杂的化学反应。
由于高温的作用,其间会产生大量的挥发份,当橡
胶合模硫化时,由于高压的作用,橡胶在一个密闭的开腔内成型反应,硫化产生的挥发份无
法外泄而形成一定的压力,随着硫化反应的进行,挥发份越来越多,内压也越来越大,终于冲破密闭的型腔沿合模线外泄,而此时硫化已进行了段时间,表层的椽胶已经硫化失去流动性,因大量挥发份外泄冲击而形成的缺陷无法弥补,留在最终的制品上,造成“烧边”。
以上的分析还只是一种设想,如果是正确的,那么“烧边”这种现象就容易发生在具有下面特点的橡胶制品上:
1、厚壁制品
因为橡胶热传导比较困难,内外层胶料不容易同步硫化,因此,这类制品容易造成制品
表层已硫化而内部尚未硫化的烧边条件。
2、低硬度制品
因为这类制品在配方设计时往往加入大量的软化剂,其间会含有更多的低沸点挥发份,
在硫化时大量逸岀。
与高硬度的胶料相比,更容易岀现“烧边”现象。
3、模具结构设计上容易造成集中排气的制品。
例如圆柱、圆筒形状的制品,采用两个半圆组合的分模方式,所有的硫化产生的挥发分都集中从中间分模线位置排出,往往因排气过于集中而造成“烧边”。
生产实跋表明,烧边的橡胶制品往往具有上述特点,如果同时具备,“烧边”出现的
机会就更大了。
了解了问题产生的原因,就可以采取相应的措施来预防和避免。
技术硏发的角度来说,解决问题的更佳方式是预防问题的出现,而不是出现了问
题再来想办法解决。
1、生产工艺
从常用的模压,压注和注射三种成形方式来说,对于相同的一种胶料,出现烧边的机会依次递减。
尤其是注射方式可以把胶料在注入形腔前就预热到较高的温度,有效缩短了胶料进入形腔后胶料热传递产生硫化反应的过程,特别对于低硬度的厚壁制品,在防止和解决烧边问题上具有无可比拟的优越性。
我公司生产的一款名为B X024产品就是
一个典型的例子,低硬度(S H A35),厚壁(15.2m*24.2m m*39m)。
使用压注工艺生产,存在明显的烧边现象,经过多种配方组合都未能有效消除产品的烧边现象,不得不采用低温长时间的硫化工艺,生产效率低,每模产品的硫化时间长达10分钟,后来釆用微波预热的方式加热胶料后再压注,结果有效缩短了硫化时间,烧边现象也减轻,但是这种方法与注射相比仍有缺点:胶料预热后还要经过一段操作时间才能压注进开腔,因为存在焦烧的危险而不能把胶料预热到很高的温度,并且无法控制预热温度,均匀预热胶料,所以仍然无法达到使用注射工艺的效果。
2、配方设计
配方设计是橡胶制品生产的基础,好的配方不仅要能满足制品的性能要求,还要有好的工艺性能和低的成本,能顺利高效的生产产品。
对于厚壁的低硬度制品,配方设计时应特别考虑岀现“烧边”的可能性。
尽量选用低沸点挥发份含量低的软化剂并注意控制用量;促硫体系的选配要注意尽量选用后效性的品种,以获得更长的焦烧时间和硫化平坦期;如果有可能还可以增加能提高胶料导热性能的助剂,使内外层橡胶能尽量同步硫化,避免形成“烧边”的条件。
3、模具设计
从模具设计上避免烧边也是行之有效的办法。
对于具有上述特点产品的模具结构,要尽量采用能分散排气的分模方式,避免出现集中排气,如果外观允许,还可以
考虑专门增加排气孔和排气槽糟,既有助于避免“烧边”问题,同时还可以避免容易
形成的缺胶窝气现象。
4、硫化工艺
硫化工艺也可以采取措施进行调整。
低温长时间硫化工艺是最常用的一种方式,由于降低了硫化温度,缩短了橡胶内外层硫化速度的差异;同时由于温度降低,硫化产生的挥发份减少,因此而产生的烧边现象也减轻。
降低合模压力,一定程度上分散了硫化挥发份的集中外泄,也有减轻“烧边”的效果。
上述方法都有助于解决“烧边”问题。
从配方设计上解决,往往受到产品性能和材料成本的限制,不容易见效,解决问题的成本也高。
从硫化工艺上解决,也往往带来生产效率降低的问题。
相比之下,选取一个适当的生产工艺,特别是选用注射这种先进的成型工艺,充分考虑模具的分模方式,可以收到事半功倍的效果。
橡胶模压制品炸边、翻边厚
橡胶制品表现为橡胶接头入料口、溢料口、分型面或橡胶与金属粘接处等部位出现体积较大的空洞、沟槽状物。
1、胶料焦烧时间不足,易形成硫化胶粒和胶屑。
解决方法:延长胶料焦烧时间。
调整硫化时间(降低温度延长硫化时间)。
避免使用停放时间太长的胶料。
2、工艺不合理,胶料过多无法溢出,硫化时先于橡胶制品表面硫化使之夹于分型面等部位之间。
解决方法:尽量采用移模注压和传递模压方式。
胶料应准确称量,给料。
3、模
具污染,胶料不清洁。
解决方法:清洁模具和胶料。
4、模具分型面配合不紧密,设计不合理,溢料口太大。
解决方法:改进模具,分型面尽量避免出现在橡胶制品的粘接部位等敏感位置。
5、胶料传热速度较慢,硫化时胶料内外层升温不一致,外层胶料已硫化,内层胶
料却受热膨胀,强制溢料引起缩孔夹层。
解决方法:改进胶料配方。
改进硫化工艺条件,比如采用低温长时间硫化。
橡胶制品的修边
修边是橡胶制品生产过程中的一个常见工序。
修边方法有:手工修边法、磨削法、切削法、冷冻修边法、无飞边模具成型法等。
各生产厂家可根据制品的质量要求和自身的生产条件来选用合适的修边方法。
1、无飞边模具
采用无飞边模具进行生产,修边工作变得简单而轻松(飞边一撕即掉,故这种模具也叫撕边模)。
无飞边模具成型法,可完全省略了修边工艺,提高制品品质和使用性能,降低劳动
强度及生产成本等特点,具有广阔的发展前景。
2、冷冻修边
专用的冷冻修边机设备,其原理是采用液氮(L N2)使成品的毛边在低温下变脆,使用特定的冷冻粒子(弹丸)去击打毛边,以迅速去除毛边。
冷冻修边的生产效率高、劳动强度小、修边质量好和自动化程度高的修边设备,对于纯胶件尤为适合。
适用制品广泛,已成为主流的工艺标准。
但是,这类设备价格昂贵,运行成本也较高。
3、人工修边
手工修边是一种古老的修边方法,它包括手工用冲头冲切胶边;用剪刀、刮到等刀具去除胶边。
手工操作修整的橡胶产品的质量和速度也会因人而异,要求修整后制品的几何尺寸必须符合产品图纸要求,不得有刮伤、划伤和变形。
修整前必清楚修整部位和技术要求,掌握正确的修整方法和正确使用工具。
在橡胶杂件的生产中,修边操作大部分都是以不同形式的手工操作。
由于修边的手工操作生产效率低下,常常在生产任务集中时,要动员许多人进行修边。
这样,不仅使工作秩序受到影响,而且也使制品的质量得不到保障。
为此,应当考虑采用更加有效的工艺措施(例如釆用无
飞边化的成型模具)或采用各种修边设备进行修边。
4、机械修边
主要有冲切、砂轮磨边和圆刀修边,适用于对精度要求不高的特定制品。
它是当前较领先的修整办法。
①低温抛丸修边关于修边质量需求较高的精密制品,如0形圈、小皮碗等,可选用此法修边。
将制品用液氮或干冰敏捷冷却到脆性温度以下,然后高速喷人金属弹丸或塑料弹丸将飞边打碎掉落,完结修边。
②低温刷磨修边它是凭借两个绕水平轴旋转的尼龙刷将冷冻的橡胶制品的胶边刷除掉。
③低温转鼓修边它是最早选用的冷冻修边方法,使用转鼓转变发生的碰击力以及制品之间
的摩擦力,使已被冷冻到脆化温度以下的制品飞边开裂并掉落,鼓的形状通常为八角形,以增大制品在鼓中的碰击力,鼓的转速要适中,加人磨蚀剂可进步功率。
如电解电容器的橡胶塞的
修边技术就是选用低温转鼓修整。
④低温振荡修边又称振荡冷冻修边,制品在环行密封箱中做螺旋状振荡,制品之间及
制品与磨蚀剂之间存在较强的碰击效果,致使冷冻脆化的胶边碎落。
低温振荡修边比低温转鼓修边好,制品损坏率低,出产功率较高。
⑤低温摇摆、颤动修边对小型或微型的制品或富含金属骨架的微型硅胶制品适用,
与磨蚀剂一同修去产物孔六、边角、槽沟中的胶边。
⑥机械冲切修边凭借压力机械和冲模、冲刀,去掉制品的胶边。
此办法适用制品和其
胶边能放在冲模或冲刀底板上的模型制品,如瓶塞、皮碗等。
关于含胶率较高、硬度小的制品通常选用碰击法冲击切边,这样,可削减因为制品弹性较大形成刀切后边部不齐、旁边面洼陷;而对含胶率较低、硬度较高的制品,能够直接采纳刀口模的办法冲切。
别的,冲切还分为冷切和热切,冷切是指在室温姿件下冲切,需求设备的冲切压力较高,冲切的质量较好;热切指在较高的温度冲切时应避免高温触摸制品的时刻过长,影响产物质量。
⑦机械切削修边适用于外形尺度较大制品的修边,运用的是切削刀具。
一舷切削机械都是
专用机器,纷歧样制品运用纷歧样的切刀。
例如,轮胎硫化后外表气眼和排气
2020/10/29橡胶制品烧边、炸边、翻遍厚和修边方法
线部位有长度纷歧的胶条,有必要在轮胎旋转条件下运用带有沟槽的具将胶条削除。
⑧机械磨削修边关于带有内孔和外圆的模具橡胶制品,通常运用磨削的方兹。
磨削的刃具
为粒子必定粗细的砂轮,磨削修边的精度较低,磨削外表较粗糙有能够夹有剩余的砂粒,影响
运用效果。
5/7。