铣床工培训资料
数控铣床工培训课件
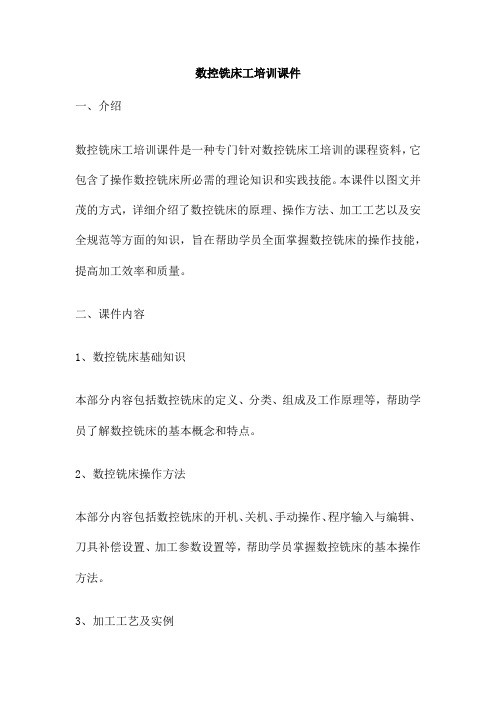
数控铣床工培训课件一、介绍数控铣床工培训课件是一种专门针对数控铣床工培训的课程资料,它包含了操作数控铣床所必需的理论知识和实践技能。
本课件以图文并茂的方式,详细介绍了数控铣床的原理、操作方法、加工工艺以及安全规范等方面的知识,旨在帮助学员全面掌握数控铣床的操作技能,提高加工效率和质量。
二、课件内容1、数控铣床基础知识本部分内容包括数控铣床的定义、分类、组成及工作原理等,帮助学员了解数控铣床的基本概念和特点。
2、数控铣床操作方法本部分内容包括数控铣床的开机、关机、手动操作、程序输入与编辑、刀具补偿设置、加工参数设置等,帮助学员掌握数控铣床的基本操作方法。
3、加工工艺及实例本部分内容以图文并茂的方式,介绍了常用材料的加工特性、加工工艺流程、切削用量选择等,同时给出了典型零件的加工实例,帮助学员深入理解数控铣床的加工工艺和技巧。
4、安全规范及防护措施本部分内容介绍了数控铣床操作过程中的安全规范、事故预防及应急处理等方面的知识,帮助学员了解操作数控铣床过程中需要注意的安全事项。
三、教学方法本课件采用图文并茂的方式,结合实际案例进行讲解,使学员更容易理解和掌握相关知识。
同时,课件中还设置了练习题和模拟试题,帮助学员巩固所学知识并进行自我检测。
四、总结数控铣床工培训课件是数控铣床工培训的重要资料之一,它包含了丰富的理论知识和实践技能,旨在帮助学员全面掌握数控铣床的操作技能,提高加工效率和质量。
通过本课件的学习,学员可以更好地了解数控铣床的工作原理和操作方法,掌握加工工艺和技巧,同时提高安全意识,为今后的工作打下坚实的基础。
绞车工是矿业、建筑、水利、电力等行业中不可或缺的重要岗位。
绞车工的技术水平直接关系到工程的安全、质量和效率。
为了提高绞车工的技术水平,保证工程的安全、质量和效率,本文将重点介绍绞车工的培训课件。
对绞车设备进行定期检查和维护,及时发现并解决设备故障;熟悉工程图纸和施工方案,了解施工进度和要求;理论授课:通过讲解、演示、图示等方式,使学员全面了解绞车设备的结构、原理和操作方法;实践操作:让学员在模拟操作和实际操作中掌握绞车设备的操作技巧和维护方法;互动讨论:组织学员进行讨论,分享经验,提高技术水平;案例分析:通过分析实际案例,使学员了解绞车设备故障的原因和处理方法。
数控铣床培训

第三讲 CAXA制造工程师自动编程
一、自动编程的特点 图形交互式自动编程是一种全新的编程方法,与
手工编程相比有以下特点: 1、这种编程方法不象手工编程那样需要计算各节点的坐标
数据,而是在计算机上直接面向零件的几何模型,以鼠标 定位、菜单选择、对话框交互输入等方式进行编程,其结 果也以图形方式显示在计算机上。因此,该方法具有简便、 直观,准确、便于检索的优点。 2、编程速度快,效率高、准确性好。编程过程中,图形数 据的提取,节点数据的计算,程序的编制及输出都是由计 算机自动完成的,充分发挥了计算机速度快,准确率高的 优点,特别对于复杂零件,更能显示其优点。 3、CAD/CAM软件都是在计算机上运行的,不需在专门的编程 机,便于普及推广。
格式:Gxx
尺寸字
尺寸字跟在地址符之后,用于确定机床上刀具运动终点的坐标位置。
第一组 X,Y,Z,U,V,W,P,Q,R用于确定终点的坐标尺寸;
第二组 A,B,C,D,E用于确定终点的角度坐标尺寸;
第三组 I,J,K用于确定圆弧轮廓的圆心坐标尺寸。
在一些数控系统中,还可以用P指令暂停时间、用R指令圆弧的半径等。
进给功能字F (F功能或F指令)
进给功能字的地址符是F,,用于指定切削的进给速度。对于数控铣
床表示每分钟进给。F指令在螺纹切削程序段中用来指令螺纹的导程。
主轴转速功能字S (S功能或S指令) 主轴转速功能字的地址符是S和后面的数字一起指定主轴转速。单位
为r/min。 例:S800 表示每分钟主轴转800转 刀具功能字T (T功能或T指令)
半 封 闭 式 立 式 数 控 铣 床
全 封 闭 立 式 数 控 铣 床
三 坐 标 联 动
数 控 铣 床
平面轮廓加工
铣床工培训
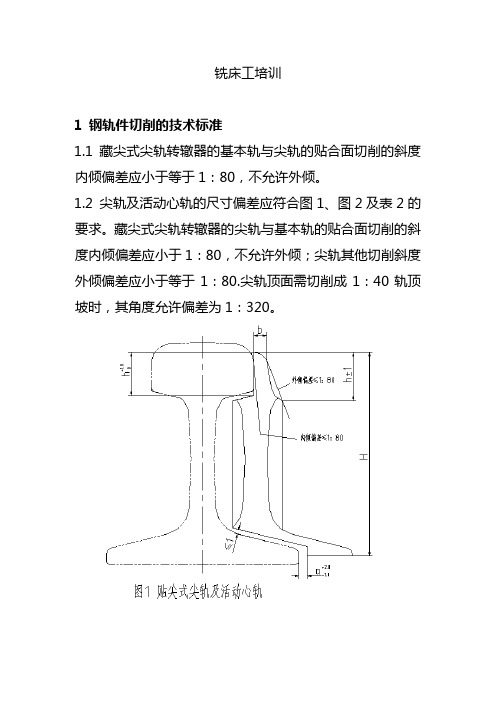
铣床工培训1 钢轨件切削的技术标准1.1 藏尖式尖轨转辙器的基本轨与尖轨的贴合面切削的斜度内倾偏差应小于等于1:80,不允许外倾。
1.2 尖轨及活动心轨的尺寸偏差应符合图1、图2及表2的要求。
藏尖式尖轨转辙器的尖轨与基本轨的贴合面切削的斜度内倾偏差应小于1:80,不允许外倾;尖轨其他切削斜度外倾偏差应小于等于1:80.尖轨顶面需切削成1:40轨顶坡时,其角度允许偏差为1:320。
表2 尖轨、活动心轨尺寸允许偏差单位为毫米1.3 长心轨的尺寸偏差应符合图3和表3 的要求.心轨顶面需切削成1:40 轨顶坡时,其角度允许偏差为1:320。
1.4短心轨各断面的尺寸偏差应符合图4 及表3 的要求。
表3 长、短心轨尺寸允许偏差单位为毫米1.5 翼轨轨头宽度的允许偏差为±0.5 (有弯折圆弧的翼轨除外),轨底宽度的允许偏差为 0mm。
可动心轨辙叉翼轨与心-1.0轨间的贴合面切削斜度内倾允许偏差为1:80。
1.6 护轨轨底宽度的允许偏差均为 0mm。
-2.01.7 帮轨切削的尺寸偏差应符合图5 的要求。
1.8 扶轨尖端及各断面轨高偏差同3.6.2的要求,其余偏差应符合图6 的要求。
2 检验规程2.1 藏尖式基本轨断面铣削完毕,应检验项目:2.1.1 铣削起点距前端长度:采用钢卷尺检验,长度偏差+3.00 mm。
mm。
2.1.2 铣削段长度:采用钢卷尺检验,长度偏差+102.1.3 铣削侧面高度偏差:采用高度尺测量,允许切削起点距离轨顶面高度16±1mm。
2.1.4标识齐全;加工表面无伤痕。
2.2 尖轨检验依据工艺要求逐件检验,应检验项目:2.2.1 轨头高度:采用轨头高度检测样板检测,偏差±0.5mm。
2.2.2 轨头宽度:使用游标卡尺检验,宽度偏差+0.5mm。
2.2.3 轨冠饱满度:采用轨冠饱满度样板检测轨冠饱满度,偏差±0.5mm。
2.2.4 变形段轨顶及工作边直线度:使用1m平尺、塞尺检测,不大于0.3mm。
车工铣床操作培训课件

铣床和龙门数控铣床 。
•
经济
•2024/1/26
全功能
高速铣床
龙门铣床
•车工(铣床)操作培训
3• .2.2 数控铣床的结构和调整
1. 数控铣床的组成
数控铣床一般由机床本体、数控系统、进给伺 服系统、冷却润滑系统等几大部分组成。
机床本体是数控机床的主体,包括:床身、立 柱等支承部件;主轴等运动部件;工作台、刀架以 及进给运动执行部件、传动部件;此外还有冷却、 润滑、转位和夹紧等辅助装置。与传统机床相比, 数控铣床的外部造型、整体布局、传动系统与刀具 系统的部件结构以及操作机构等都发生了很大的变 化,这种变化的目的是为了满足数控技术的要求和 充分发挥数控机床的特点。
•车工(铣床)操作培训
地址 G43/ G44 G49 G50 G51 G52 G53 G54~G59 G60
• G61
G64
• G65
G68
G69
•2024/1/26
含义 刀具长度补偿—正/负 刀具长度补偿注销 缩放关 缩放开 局部坐标系设定 直接机床坐标系编程 工件坐标系选择 单方向定位 精确停止校验方式 连续方式 子程序调用
• 建立工件坐标系。工件坐标
• 系一旦建立,绝对值编程时
• 的指令值就是在此坐标系中
• 的坐标值。如右图所示。 • 程序示例:G92 X40 Y30 Z25
•2024/1/26
•车工(铣床)操作培训
坐标值X40 Y30 Z25为刀位点在工件坐标系中的
初始位置,执行G92指令时,机床不动作,即X、Y、
•2024/1/26
•车工(铣床)操作培训
(4)快速点定位指令(G00) G00指令是指刀具以点定位控制方式,从刀具 所在点以最快的速度,移动到目标点。G00指令中的 快移速度由机床参数“快移进给速度”对各轴分别设 定,不能用进给速度F规定。一般用于加工前快速定 位或加工后快速退刀。G00为模态功能可由G01、 G02、G03或G33功能注销。 注意:在执行G00指令时,由于各轴以各自速 度移动,不能保证各轴同时到达终点,因而联动直线
铣床工培训资料汇编

目录章节内容页号1.0 铣刀介绍1-42.0 铣削过程的基础知识4-103.0 铣刀几何参数的合理选择10-124.0 铣削用量的选择135.0 难铣削材料的铣削13-146.0 轴上键槽的铣削14-20铣削原理铣削,就是在铣床上以铣刀旋转做主运动,工件做进给运动的切削加工方法。
刀具材料铣削性能的优劣和铣刀角度的合理选择将直接影响切削加工的生产率和加工表面的质量。
1.0铣刀简介在铣削加工中,应根据铣床的情况和加工需要合理地选择和使用铣刀。
1.1.铣刀的种类1.1.1.按用途分类按照用途的不同,可将铣刀分为铣削平面用铣刀、铣削直角沟槽用铣刀、铣削特种沟槽用铣刀和铣削特形面用铣刀等,具体见表1-1。
~1~1.1.2 铣刀的标记为了便于识别铣刀的材料、尺寸规格和制造厂家等,铣刀上都刻有标记,标记的内容主要有以下几种。
1.制造厂家商标我国制造铣刀的厂家很多,如哈尔滨量具刃具厂、上海工具厂和成都量具刃具厂等,各制造厂都将自己的注册商标标注在其产品上。
2.铣刀材料铣刀的材料一般用材料的牌号表示。
如HSS表示铣刀的材料为高速钢。
3.铣刀尺寸规格铣刀的尺寸规格标注因铣刀形状的不同而略有不同。
因铣刀上的标注尺寸均为基本尺寸,在使用和刃磨后会产生变化,所以在使用时应加以注意。
1)带孔铣刀带孔铣刀包括圆柱铣刀,三面刃铣刀和锯片铣刀等,一般以外圆直径×宽度×内孔直径来表示尺寸规格。
例如,三面刃铣刀上标有80×12×27,表示该铣刀的外圆直径为80 mm,宽度为12 mm,内孔直径为27 mm。
2)指状铣刀指状铣刀包括立铣刀和键槽铣刀等,尺寸规格一般只标注外圆直径。
如锥柄立铣刀上标有Ф18,则表示该立铣刀的外圆直径是18 mm。
3)盘形铣刀角度铣刀和半圆铣刀等盘形铣刀,一般以外圆直径×宽度×内孔直径×角度(或圆弧半径)表示。
例如,角度铣刀的外圆直径为80 mm,宽度为22 mm,内孔直径为27 mm,角度为60°,则标记为80×22×27×60°。
铣床组新进员工培训

銑床組新進員工培訓計劃一.思想觀念教育及課內管理規定教育(課內管理資料,含製作流程教育)二.掌握第三視角法,了解課內模具圖面之識圖方法.三.熟悉三角函數之間的換算及運用.四.了解模具各組件的名稱及作用(同模具課模具組件教育資料)五.了解常用材料特性及用途六.銑床基礎知識教育6.1銑床的銑削加工原理6.2銑床各部件的名稱及作用6.3銑床的保養與維護6.4銑床的操作程序及注意事項6.5銑床加工工件標準(同QC檢測標準)及倒角規範七.銑床刀具的認識7.1刀具切削的基本條件及刀具的材料及種類7.2怎樣選擇刀具7.3社內刀具的特性7.4銑刀的安裝程序及要領7.5銑削的速度及進刀量7.6銑刀的保養與維護及研磨技巧之掌握7.7根據以上要領用各種類型銑刀加工不同材質的工件,感覺銑削工件的情況7.8銑削工作之研判八.鑽頭的認識及研磨方法8.1鑽頭的材料及種類8.2鑽頭各部位名稱及作用8.3工件的材料與鑽頂角的運用8.4鑽頭研磨注意事項、方法、技巧及保養維護8.5 鑽頭的鑽削速度判斷8.6根據以上要領進行實際操作8.7鑽削時的注意事項及不良研判九.鉸刀的認識9.1鉸刀的材料及種類9.2鉸刀前端倒角的作用9.3鉸刀的研磨方法及要領9.4鑽鉸預留量的運用9.5鉸刀的鉸削速度與進刀9.6鉸刀的保養與維護9.7根據以上要領選用SKD61(淬火前)和FDAC的材料分別鑽鉸Φ2、Φ3、Φ4、Φ5、Φ6的頂針孔9.8鉸削工作之不良研判十.螺絲攻的認識10.1螺絲攻的材料及種類10.2鑽頭在攻絲時鑽孔直徑的計算方法及標準認識10.3螺絲攻研磨方法及要領10.4根據攻絲要領,選用45#鋼分別鑽攻各種規格的螺牙10.5攻絲工作之不良研判十一.輔助治工具之使用及保養11.1百分表、千分表的功能使用及保養11.2油壓虎鉗、成型虎鉗使用及保養11.3 V型座、斜度塊規、正弦規使用及保養11.4倒角刀、倒角器、倒R刀、尋邊器使用及保養十二.學習銑六面體12.1六面體的加工方法12.2銑六面體的注意事項十三.加工基本模具工件之要領13.1加工引張板、耐磨板、滑軌類等配件的要領(鑽孔、倒角、尋邊、銑六面體精度掌握及運用)十四.學習加工電极、模仁、滑座等散件14.1電极的加工[2D電极(含尋邊銑)、六面體之精度掌握及運用]14.2模仁加工方法(鑽、鉸、攻加工之運用)14.3滑座、滑塊加工方法(臺階面加工之運用)十五.了解模板相互配合關係,學習加工模板及斜面加工件15.1銅材、鋼材斜度加工型式要領(治具擺放、刀刃銑削)15.2各模板加工要領順序及方法15.3模板開框的加工方法15.4各模板加工的注意事項十六.特殊加工要領16.1細小及多位槽穴電极之加工16.2模仁臺階面及單向曲面P.L之加工要領16.33D工件的加工方法16.4熱處理后材料精加工要領16.5衝子成型器夾取工件銑削方法PS: 3個月后考核1~11理論實績80%以上,實作考核研磨各刀具掌握70%以上,加工考核12~13項:效率80%,品質95%以上;6個月后考核1~11理論實績提升20%,實作考核研磨各刀具掌握效率提升20%.加工考核14項:效率80%,品質95%以上,含12~13考核提升效率20%;9個月考核15項:效率80%,品質95%以上,含14項效率提升20%;12個月考核16項:效率80%,品質95%以上,含15項效率提升20%.以上實作加工品質要求95%以上.承認: 確認: 作成:一.思想觀念教育及廠紀廠規的教育(同課內規定)二.掌握第三視角法,了解課內模具圖面之識圖方法(同技術課教育資料)三.模具各組件名稱及作用(同課內教育資料)四.熟悉三角函數之間的關係Sinà=A/C Array Cosà=B/CATgà=A/BCtgà=B/A五.銑床基礎知識5.1銑床各部件名稱(同銑床圖片)5.2銑床的保養與維護(同<銑床保養作業指導書>)5.3銑床的操作及注意事項(同<銑床操作說明書>)5.4了解銑床基本加工標準及倒角規範六.銑床刀具的認識6.1刀具的工作條件及刀具的材料刀具是在高溫、較大壓力、劇烈摩擦,有時還承受衝擊和振動條件下工作.刀具是由高速鋼、高碳工具鋼、合金工具鋼等材料組成,大多數刀具是在高溫真空中以化學氣體深覆一層高硬度,耐磨和難熔的金屬化合物,刀具表面根據金屬化合物的不同呈不同的顏色6.2 銑床的原理及刀具選擇依據銑床切削加工實質是材料受到刀具刀刃擠壓后,產生了彈性變形,塑性變形和剪切滑移使切削層與母體斷裂分離過程一般選擇刀具依據以下幾點:(1)根據要加工工件的材質(2)根據加工性質(3)根據刀具的特性(4)工件是否淬過火6.3 銑刀安裝程序及要領(1)安置銑刀夾頭於銑床主軸上(2)選擇適當之套筒(3)清拭套筒、銑刀刀柄(4)將銑刀柄推進套筒(在不防礙工作時,刀柄應盡量往里面裝,但不可夾持刀刃,然後將銑床主軸變換於低速旋緊夾頭螺帽)6.4 銑削速度與進刀銑削速度及進刀直接影響銑刀壽命.加工效率及加工質量,一般切削時最好以較慢之切削速度開始,然後視加工情況逐漸增至適當速度,另外還需考慮下列因素.(1)銑削的工件材料之硬度是重要的因素之一,材料的軟硬其切削速度不同,硬材料應使用較低之切削速度,較金屬(如鎂、鋁)則可選用較高之銑削速度;(2)銑刀的工件材料還影響切削速度,一般而言高速鋼材質為高碳工具鋼之兩倍,而碳化物材質銑刀又為高速鋼銑刀兩倍,直徑較小之銑刀以較高速度工作;(3)一般粗銑時,速度不宜過大,精銑時應提高轉速,減小進刀量,可得到較好的加工面;(4)銑削速度可按下列公式計算: Cs= πDN/1000Cs為銑削速度(m/mm)D為銑刀外徑(mm)N為銑刀每分鐘回轉數6.5 根據以上要領用各種類型的銑刀加工不同材質的工件感覺銑削效果及工作情況.6.6 銑刀的保養與維護及研磨注意事項(1)銑刀使用前應先行檢查有無破損現象,若銑刀已磨損或破損應立即研磨;(2)重新再磨利時,在切刃后背處磨一狹小背刃即可,普通端銑刀之研磨均沿其端面之切刃加以輪磨;(3)裝卸銑刀時,宜用軟佈保護以防碰擊而使切刃破損或傷及手部;(4)銑削操作中,啟動機器時,應將銑刀與工件分離,以防意外;(5)銑削時應選用適當的切削液;(6)使用完畢之銑刀應檢察有無破損,鈍化時應即時磨利;(7)銑刀之存放前應徹底擦拭清潔,存放時不可與其它刀具混合放置,以避免碰擊而傷及切刃;(8)銑刀在研磨時應注意因高溫而軟化或變顏色,因此研磨時應隨時注意冷卻.6.7 銑削之工作研判(1)銑削時產生震動現象,可能是工件還未夾好,銑削深度太深或進刀量大及進刀太快,銑削速度太快等原因;(2)銑削加工面不良可能是切削速度太低,進刀量過大,銑齒鈍化,工件與銑刀裝置不良,銑床主軸鬆動等原因;(3)銑齒切刃破裂可能是銑刀及工件夾置不良而產生震動引起,或銑齒鈍化后繼續使用,銑齒各角度不正確,進刀量太大等原因;(4)銑削時產生黏附刀刃之切屑可能是切削速度太低,銑齒角度不良或進刀太小等原因.七.鑽頭的認識及研磨7.1鑽頭的各部分名稱及材料鑽頭是一種旋轉而頭端有切削能力的工具一般以碳鋼SK2或高速鋼SKH2、SKH3等材料,經銑制或滾制再經淬火、回火之熱處理后磨利而成.7.3研磨鑽頭注意事項(1)鑽頂角的選用應依工件的材質選擇適當之角度;(2)兩切邊之長度必須相等,且與軸所夾之角度必須相等;(3)鑽頭研磨時,應防止其因高溫而軟化,故研磨時,應隨時注意冷卻;(4)鑽削鑄鐵工件之鑽頭,其切邊應予倒角,鑽銷青銅、祡銅或其他軟金屬,則可將切邊磨平,以減小斜角.7.4 鑽頭研磨方法(1)一只手握持鑽頭前端且微靠著砂輪挾持架上,另一手握持鑽頭柄端,握持力不可太大;(2)握持鑽頭,使其中的線與砂輪面成60°;(3)鑽頭壓入砂輪研磨時,壓力不可過大,以避免過熱使切過熱軟化,應隨時注意使用冷卻劑進行冷卻;(4)先研磨鑽頂角及切邊,應兩邊反復同時進行,一邊磨一次切不可一邊磨除太多后,再更換另一邊.7.5 磨利鑽頭之不當影響(1)若鑽頭之切邊與鑽頭軸所夾之角度相等,但切邊不相等時,則表示靜點偏位,鑽削時將引起擺動,擴大孔徑;(2)若鑽軸至兩切邊所夾之角度不相符,鑽削時僅單邊切削鑽頭易於鈍化;(3)若鑽頭無間隙角時,其切邊不能正常切削,壓力加大時,即可能扳斷鑽頭.7.6 根據以上要領,進行實際操作7.7鑽頭鑽削速度C.S=π2222222DN/1000C.S為鑽削速度(m/min)D為工作直徑N為鑽床每分鐘主軸的轉數(rpm)(1)最適當的切速,主要受材料的硬度而定,硬度愈高,韌性愈大,切速宜低;(2)鑽頭愈小,主軸轉速應越高,鑽頭越大,則轉速應越低.7.8鑽削工作之研判(1)鑽孔前必須先打中心點;(2)鑽貫通孔時,當鑽頭即將鑽穿之瞬間,扭力最大,故此時須輕壓力,慢慢進刀,以避免鑽頭受力過大而扭斷;(3)鑽深孔時,應充分使用切削劑,並注意排屑,避免鑽頭被切屑夾料.(4)鑽削交叉孔時,應先行鑽削大直徑之孔,再鑽小孔徑;(5)鑽頭鑽削時,破碎或突然停止的現象,可能是進刀太快,磨利或鑽孔時急冷即熱之緣故;(6)鑽頭鑽削的折斷,可能是鉆唇間隙角太小或鑽削速度太高,進刀太大,壓力太大,或鑽頭已鈍化又繼續加壓切削所致;(7)切削時切邊破裂,可能是工件材料中有硬點、砂眼或進刀太快,鑽削選擇不當,鑽削時無加潤滑油或切削劑所致;(8)鑽唇及切邊破碎可能是進刀太快或鑽唇間隙角太大所致;(9)鑽削時僅排出一條切削,可能是切邊不等長或鑽頂角不相等所致;(10)鑽削時所鑽出孔徑太大,可能是兩切邊不等長或兩鑽頂角不對中,靜點偏離,主軸鬆動所致;(11)鑽削時發生吱吱叫的聲音,可能是孔不直或鑽頭鈍化所致;(12)鑽削時切屑材質產生異常變化,可能是鑽頭已鈍化或破損所致.八.鉸刀的認識及使用時注意事項8.1 鉸刀的材料鉸刀是以高碳鋼、高速鋼或碳化物所制成8.2 鉸刀前端倒角的作用倒角是為了引導鉸刀進入工作孔內,若鉸刀無倒角,則鉸削時容易產生振動現象,一般機械鉸刀倒角45°,手工鉸刀其前端為1°倒角.8.3 鉸刀之鉸削速度與進刀(1)用手工鉸削時,雙手的扭轉速度和壓力配合要適當,鉸削中回轉速度均勻、壓力平均、無忽大忽小現象,感覺鉸削極為順暢即可;(2)機器鉸削速度與進刀依工件材料之性質,加工條件等而定;(3)若鉸削速度太慢,則增加鉸刀磨耗,若速度太快,則會導致切削黏附刀刃而產生加工不良,一般鉸削速度為鑽削的1/2-2/3;(4)鉸刀進刀量是鑽孔之進刀量的2-3倍.8.4 鉸刀的保養與維護(1)裝置鉸刀時最好以佈接夾,以避免鉸刀受損或傷手;(2)鉸孔時應使用適量的攻牙油;(3)存放鉸刀時,應先將鉸刀擦拭乾凈,並涂WD-40以防止生銹;(4)存放時鉸刀尺寸要加以標示,不可重疊交叉存放,以避免刃邊破碎.8.5 根據以上要領,選用SKD61和TDAC的材料分別鑽鉸Φ2、Φ3、Φ4、Φ5、Φ6的頂針孔.8.6 鉸銷工作研判(2)鉸孔時,孔徑變小原因可能是被切材料之彈性較大,也可能是鉸刀已鈍化;(3)鉸孔時孔徑變大原因是切削齊、切削速度、進刀量、加工量等所致.機械性能和工件夾持也是主要因素,因此為得到精確之孔徑必須選擇適當之切削劑鉸削速度、進刀量及加工預量,操作時工件夾持要穩定,鉸刀夾持要正確;(4)鉸孔時,鉸刀不得逆轉退回,以避免鉸刀切邊破碎.九.螺絲攻的認識及如何正確使用9.1螺絲攻材料螺絲攻是在周邊上具有一個或數個所須螺紋形狀切削部分之圓柱形或錐形螺紋切削刀具它一般是高碳鋼、合金工具鋼、高速鋼等材料經制造、淬火、回火等熱處理而成.9.2攻絲時鑽頭計算方法攻絲鑽頭為攻絲前鑽孔所使用的鑽頭、理論是講其尺寸是和螺絲底徑相同,即外徑減去二倍之牙深之尺寸,實際是只留牙高75%為攻絲預留量.60°牙角三角螺紋攻絲預留量75%之攻絲鑽頭呎寸可同下面公式求出攻絲鑽頭呎寸=外徑(公稱呎寸)-0.75*(0.6495*螺距)*2簡略上式:攻絲鑽頭呎寸=外徑-螺距P9.3根據攻絲要領選用45#鋼,分別鑽攻各種規格的螺牙9.4攻絲之工作研判(1)攻絲時應選用適當之螺絲扳手,攻絲時以充分之壓力使螺絲攻進入孔內,然後卸下扳手,檢查螺絲攻是否和工作物面垂直,若螺紋不垂直則倒轉螺絲攻,然后向傾斜方向之對邊方向加壓旋轉反復幾次,直至螺絲攻垂直為止,旱行正確后,只須旋轉扳手,不再施壓力即可自動進行切削,此時兩手所施之扭力應平均.在切削進行中,每旋轉切削1/2或1圈時,即應倒轉半圈,以斷裂切屑;(2) 攻絲時鋼或青鋼等材料應使用油化學切削劑等,但黃鋼及鑄鐵則不必加切削劑;(3) 攻絲時,螺絲攻斷裂,主要原因是螺絲攻撞及孔底孔之尺寸不正確,切屑堆積在槽內攻絲偏斜、潤滑不足等,有時反轉時鐵屑卡斷螺絲攻,以上應采取措施加以避免;(4) 螺絲攻使用后應擦拭、清潔並上油,存放於組合盒內.十. 學習如何銑六面體10.1六面體的加工方法10.2銑六面體的注意事項十一. 加工基本模具工件之要領11.1耐磨板、滑軌類工伯的加工耐磨板、滑軌類工件要注意油槽的加工方向,孔的中心位置不可偏移.11.2加工引張板類工件引張板類工件應注意槽穴的長度要一致十二. 學習加工電極、模仁、滑座等散件12.1電極加工方法12.2模仁加工方法12.3滑座加工方法十三. 了解模板相互配合關係,學習加工模板13.1各模板的加工要領及方法(1) 對於有剝料板的三板式模具,剝料板和上固定板組合在一起加工,加工上固定板與剝料板用導柱串起加工螺紋孔和拉料銷孔,加工時尋邊分中上固定板流道襯套孔,加工拉料銷孔時需鉸孔,且在剝料板上鑽鉸一個Φ6或Φ8的孔,以便於線割尋邊加工注道襯套孔;(2) 對公母模板的加工,一般先把模板框加工好,再加工斜面和斜銷孔,然後加工螺線孔、頂針孔及水孔等;(3) 對於公模中板和承板的加工,如果模板上有要求和公模板同心度和精度要求較高時,要用導柱和輔助導柱等組合起來進行加工;(4) 加工上頂出板上頂針孔時,用回位銷和公模板組合起來,保證公模板和上頂出板頂針孔同心,且孔位置不可偏移;(5)加工下頂出板時要用導套套在上頂出板上;(6)對於下固定板上有司筒針孔時,要用輔助導柱、導套組合起來保證下固定板同公模板司筒針孔同心.13.2模板開框精度要求(同QC作業標準)13.3模板開框加工方法及注意事項(同銑床組教育資料)十四.進行技術等級考核。
铣床培训教材

下压,下几个毫米,用PIN来检查是否正确,如果正确,继续铰下去
• 孔前先要调整机床的主轴垂直度,方法如下:
•
1.用一块比较长,又比较宽的顶块夹在平口钳上
•
2.用表把顶块 X ,Y方向打平
•
3.主轴在空挡,使表转动180°看两端是否在同一高度
•
4.若有高低,松动螺丝,调整主轴方向
第三周
• 第四天:机铰时应注意以下几点:
第二周
• 第五天:1. 倒角的加工方法
•
① 对于C2以下的,可以直接用倒角刀做,碰到尖点后
,多大就进多少
•
②对于C2以上的,可用45°角度块或“V”形块来垫上
,用铣刀来做(下的度深为:倒角的大小xCOS45°+双边余量之和
xCOS45°)
•
③倒角可以做大一点,但不能小
•
2.斜度的加工过程
•
①看清所加工的角度为多大,选择合适的角度块(尽量
•
先找准位置后,用Φ8.0的铣刀下4.10MM左右(外形余量
0.5MM),然后再拿把Φ8.0的刀放在平口钳上夹住磨平,经过刃磨后,
装到夹头上,把工件打平,然后用磨好的平底刀下到深度(4.0+0.25)
MM,最后用深度计来检验是否正确
•
• 第三周:应达到的要求:
•
能够做一些比较难Hale Waihona Puke 工件,对做简单的工件要达到一定的速度
• 第五天:控制尺寸的加工
•
1.深度控制
•
先去余量 ------修磨平底刀-----打平工件------做到尺寸
•
例如:加工一孔Φ8.0x4.000+0.03 +0.01 DP
•
铣床教育训练资料

銑床加工要點目錄第一章識圖與加工1.識圖-------------------------------------------------------------------------------32.看圖舉例-------------------------------------------------------------------------3 3備料-------------------------------------------------------------------------------4 4.加工-------------------------------------------------------------------------------5第二章六面體加工1.銑刀選擇-------------------------------------------------------------------------62.銑平面----------------------------------------------------------------------------73.銑直角----------------------------------------------------------------------------84.異常問題與對策----------------------------------------------------------------9 第三章台階、溝槽加工1.刀具選擇-----------------------------------------------------------------------112.工件裝夾-----------------------------------------------------------------------123.對刀-----------------------------------------------------------------------------124.切削余量的控制--------------------------------------------------------------125.尺寸不良與對策--------------------------------------------------------------16 第四章鑽孔、攻牙與板牙加工1.鑽床鑽孔-----------------------------------------------------------------------172.銑床鑽孔-----------------------------------------------------------------------183.攻牙-----------------------------------------------------------------------------214.扳絲-----------------------------------------------------------------------------22 第五章銑床鏜孔加工1.鏜刀種類-----------------------------------------------------------------------232.品質問題及其原因-----------------------------------------------------------24一、識圖與加工圖紙是工件加工的主要依據,加工前必須看懂圖紙,特別是所加工工序的部分。
铣工实训培训资料
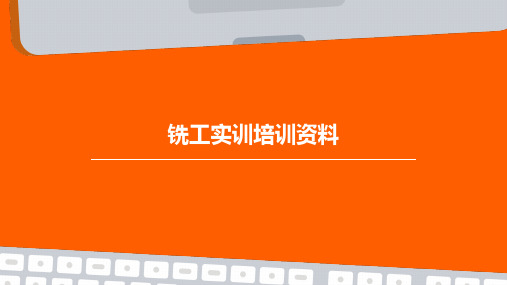
铣工实训的基本要求
学员需具备一定的机 械制图、金属材料、 刀具、夹具等基础知 识。
学员需认真完成各项 实训任务,并撰写实 训报告。
学员应严格遵守安全 操作规程,确保实训 过程中的安全。
铣工实训的课程安排
理论课程
讲解铣削加工的基本原理、刀具选用 、切削参数选择等知识。
实践课程
学员在教师的指导下完成各种铣削加 工操作,如平面铣、轮廓铣、槽铣等 。
考核内容
实际操作主要考察学生的铣床操作、刀具安装、工件装夹、调整切削参数等技能,笔试主 要测试学生对铣削加工相关理论知识的掌握程度,口试则考察学生的语言表达和问题解决 能力。
铣工实训成绩评定与反馈
成绩评定
根据学生的实际操作水平、任务完成情 况、笔试和口试成绩,以及在实训过程 中的安全意识和职业素养表现,综合评 定学生的实训成绩。
04
铣工实训项目
平面铣削实训项目
总结词
基础技能训练
详细描述
平面铣削是铣工的基本技能之一,通过实训掌握平面铣削的基本原理、操作技巧和安全规范,提高铣削效率和平 整度。
轮廓铣削实训项目
总结词
进阶技能训练
详细描述
轮廓铣削是铣工的重要技能之一,通过实训掌握轮廓铣削的工艺要求、刀具选择和加工精度控制,提 高复杂零件的加工能力。
实训效果评估
根据学生的实际操作、任务完 成情况及理论测试成绩,综合
评估学生的实训效果。
铣工实训考核标准与方式
考核标准
考核学生是否掌握铣削加工的基本技能,能否独立完成指定的铣削加工任务,同时考察学 生的安全意识和职业素养。
考核方式
采用实际操作、笔试和口试相结合的方式进行考核,其中实际操作占主导地位,笔试和口 试作为辅助考核方式。
铣床培训课
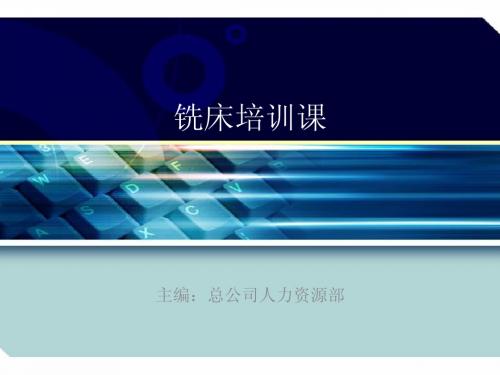
课外拓展
(2)立式铣床
课外拓展
铣刀: 圆柱铣刀、三面刃铣刀、锯片铣刀、角 度铣刀、成形铣刀、立铣刀、端铣刀、键 槽铣刀
课外拓展
铣 刀:
课外拓展
铣 刀:
课外拓展
主要附件: 平口钳 回转工作台 万能铣头 万能分度头
课外拓展
平口钳: 适合夹小型零件,如装夹轴类零件铣键槽
课外拓展
回转工作台: 可带动工件缓慢的圆周进给。一般用于 较大零件的分度工作和非整圆周的铣削工 作。
影响薄型工件加工精度的因素
• 由于薄型工件的特殊性,加之材料切削加 工性能的因素,刀具几何角度和切削用量 的选择会响应有所改变,就使得加工时的 选择和确定比较困难。若选用不当,常会 引起加工精度误差,甚至造成刀具损坏、 工件变形,甚至报废。
薄型工件装夹时应注意以下几点
• 按定位的原理,应尽量在加工部位附近设 置定位和辅助定位,并在定位元件上预留 出铣刀让刀位置。 • 在选择夹紧力的作用点位置和作用方式时, 须考虑材料的力学性能,采用较大的面积 传递夹紧力,以避免夹紧力集中在某一点 上,使工件产生变形。
• 开车前,检查机床手柄位置及刀具装夹是否牢 固可靠,刀具运动方向与工作台进给方向是否 正确。
铣工安全技术操作规程
• 将各注油孔注油,空转试车(冬季必须先开 慢车)2分钟以上,查看油窗等各部位,并听 声音是否正常。 • 清扫铁削时应用专门工具,不准用手。 • 所使用的扳手及工具,应符合规定,不准 把管子套在扳手上使用。 • 卡活件时应根据卡具情况,适当力量卡紧。 • 在工作中,不准将手锤、扳手和毛坯直接 放到机床导轨面的工作台面上。
复杂直角沟槽工件的铣削工艺特点
• 由于工件的加工精度比较高,因此所选用 的刀具、量具、辅具及夹具的精度要求都 比较高,通常在使用前,需要进行精度预 检,以保证加工过程中的使用精度。
OK铣床培训教材
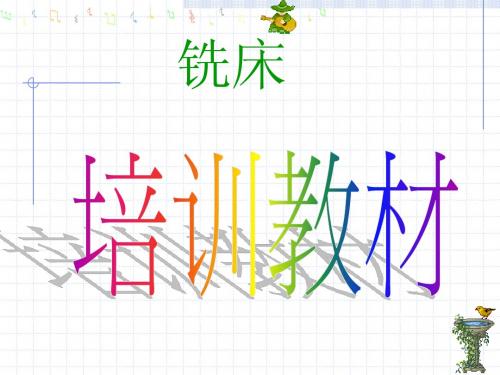
铣床的加工原理:把电能转化为机械能,利用多齿刀具从三个不同方
向作其中的一边作垂直运动.如何安全操作机台见标准作业指导书.F1备料, 飞六面体的加工方法: 1.先锯好粗胚料,一般粗胚料预留5.0MM的余量. 2,磨好飞刀刀片,并装夹固定好. 3.把粗胚料装夹好,对刀开机. 4.先见光一个面,再测量余量的多少来决定进刀量. 5.备好四个面后再利用虎钳的侧面打直角. F2工件定位与基准 1.装夹前必须校正虎钳的垂直度在0.005MM以内,并保证清洁. 2.定位治具必须锁紧固. 2. . 3.每次定位的标准必须保持一致. 4.每次选择作基准的垫块必须保持一致. F3孔的加工方法 1.先磨好钻头,打孔前先打孔的中心钻,以保证孔的中心位置. 2.根据工件的要求选择合适的钻头在相应的地方加工. 3.当孔的深度有要求时要选对好刀,再调动深度微调停止块,固定位置,再根 据孔的深度,把机台提升相应深度. 4.根据不同材料,打孔时选择不同转速,钢材66转/分,非金属1100转/分.
11.對新進數控銑床學員三個月內應培訓 對新進數控銑床學員三個月內應培訓: 對新進數控銑床學員三個月內應培訓
1.一般工件的加工方法與技巧 一般工件的加工方法與技巧. 一般工件的加工方法與技巧 2.圓形工件及一般異形工件的加工方法 圓形工件及一般異形工件的加工方法. 圓形工件及一般異形工件的加工方法 3.熟練操作編程軟件 熟練操作編程軟件. 熟練操作編程軟件 4.進行三個月學員考核 進行三個月學員考核. 進行三個月學員考核
个月培训项目; 三、3个月培训项目 个月培训项目
(1).一般工件的加工方法与技巧 一般工件的加工方法与技巧.(H2) 一般工件的加工方法与技巧 (2).精度孔与精度糟的加工方法 精度孔与精度糟的加工方法.(H3) 精度孔与精度糟的加工方法
铣床工培训资料

目录章节内容页号1.0 铣刀介绍1-42.0 铣削过程的基础知识4-103.0 铣刀几何参数的合理选择10-124.0 铣削用量的选择135.0 难铣削材料的铣削13-146.0 轴上键槽的铣削14-20铣削原理铣削,就是在铣床上以铣刀旋转做主运动,工件做进给运动的切削加工方法。
刀具材料铣削性能的优劣和铣刀角度的合理选择将直接影响切削加工的生产率和加工表面的质量。
1.0铣刀简介在铣削加工中,应根据铣床的情况和加工需要合理地选择和使用铣刀。
1.1.铣刀的种类1.1.1.按用途分类按照用途的不同,可将铣刀分为铣削平面用铣刀、铣削直角沟槽用铣刀、铣削特种沟槽用铣刀和铣削特形面用铣刀等,具体见表1-1。
~1~1.1.2 铣刀的标记为了便于识别铣刀的材料、尺寸规格和制造厂家等,铣刀上都刻有标记,标记的内容主要有以下几种。
1.制造厂家商标我国制造铣刀的厂家很多,如哈尔滨量具刃具厂、上海工具厂和成都量具刃具厂等,各制造厂都将自己的注册商标标注在其产品上。
2.铣刀材料铣刀的材料一般用材料的牌号表示。
如HSS表示铣刀的材料为高速钢。
3.铣刀尺寸规格铣刀的尺寸规格标注因铣刀形状的不同而略有不同。
因铣刀上的标注尺寸均为基本尺寸,在使用和刃磨后会产生变化,所以在使用时应加以注意。
1)带孔铣刀带孔铣刀包括圆柱铣刀,三面刃铣刀和锯片铣刀等,一般以外圆直径×宽度×内孔直径来表示尺寸规格。
例如,三面刃铣刀上标有80×12×27,表示该铣刀的外圆直径为80 mm,宽度为12 mm,内孔直径为27 mm。
2)指状铣刀指状铣刀包括立铣刀和键槽铣刀等,尺寸规格一般只标注外圆直径。
如锥柄立铣刀上标有Ф18,则表示该立铣刀的外圆直径是18 mm。
3)盘形铣刀角度铣刀和半圆铣刀等盘形铣刀,一般以外圆直径×宽度×内孔直径×角度(或圆弧半径)表示。
例如,角度铣刀的外圆直径为80 mm,宽度为22 mm,内孔直径为27 mm,角度为60°,则标记为80×22×27×60°。
2024数控铣工培训计划
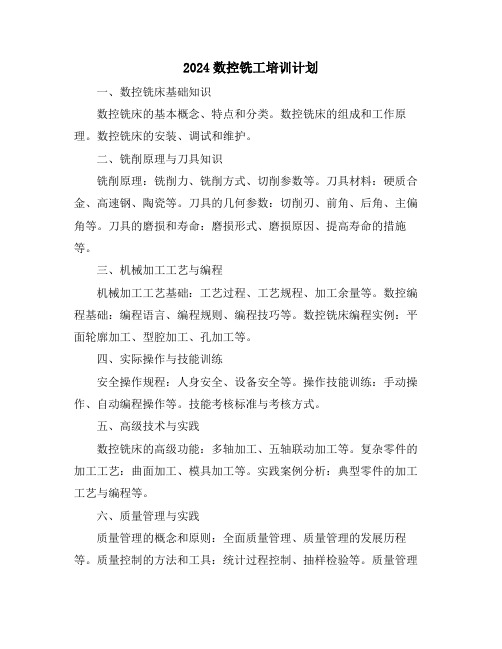
2024数控铣工培训计划
一、数控铣床基础知识
数控铣床的基本概念、特点和分类。
数控铣床的组成和工作原理。
数控铣床的安装、调试和维护。
二、铣削原理与刀具知识
铣削原理:铣削力、铣削方式、切削参数等。
刀具材料:硬质合金、高速钢、陶瓷等。
刀具的几何参数:切削刃、前角、后角、主偏角等。
刀具的磨损和寿命:磨损形式、磨损原因、提高寿命的措施等。
三、机械加工工艺与编程
机械加工工艺基础:工艺过程、工艺规程、加工余量等。
数控编程基础:编程语言、编程规则、编程技巧等。
数控铣床编程实例:平面轮廓加工、型腔加工、孔加工等。
四、实际操作与技能训练
安全操作规程:人身安全、设备安全等。
操作技能训练:手动操作、自动编程操作等。
技能考核标准与考核方式。
五、高级技术与实践
数控铣床的高级功能:多轴加工、五轴联动加工等。
复杂零件的加工工艺:曲面加工、模具加工等。
实践案例分析:典型零件的加工工艺与编程等。
六、质量管理与实践
质量管理的概念和原则:全面质量管理、质量管理的发展历程等。
质量控制的方法和工具:统计过程控制、抽样检验等。
质量管理
体系的建立与实施:ISO9000系列标准等。
持续改进和提高:质量改进的基本方法、质量改进的过程等。
铣床培训材料

实训培训教材(铣床培训教材)主编:实习实训办公室内部教材内编号:010*******2020.08.08(内部资料禁止外传)目录1 铣床的基本知识 (3)2 铣刀的基本知识 (3)3 基准的种类及选择原则 (3)4 常用夹具及工件的装夹 (4)5 铣削的基本知识 (6)6 切削液的作用及种类 (6)7 各种类型的零件加工步骤及方法 (7)8实践操作培训(图8.1) (12)铣床培训教材1 铣床的基本知识1.1 铣床的类型:升降台式铣床(卧式铣床、立式铣床)、万能铣床、龙门铣床、特种铣床、数控铣床等。
1.2 铣床的结构部件:底座床身、主轴、主轴变速机构、纵向工作台、横向工作台、升降台等。
1.3 铣削的概念:铣削就是在铣床上以铣刀旋转作主运动,工件或铣刀作进给运动的切削加工方法。
1.4 铣削加工的特点:铣削是用多刀刃的铣刀来进行切削加工的,故生产效率较高。
1.5 铣削的加工精度:铣削加工的经济加工精度一般为 IT9~IT8,表面粗糙度 Ra 值可达到 12.5~1.60um;必要时加工精度可高达 IT5,表面粗糙度 Ra值可达 0.20um。
1.6 铣床的加工范围:铣平面、铣直槽、铣燕尾槽、铣 T 型槽、铣成形面等各种形状复杂的零件。
2 铣刀的基本知识2.1 铣刀的种类(按铣刀切削部分的材料分):高速钢铣刀、硬质合金铣刀2.2 铣刀切削部分材料的基本要求:2.2.1 高硬度和高耐磨性:在常温下,切削部分材料必须具备足够的硬度才能切入工件;具有高的耐磨性,刀具才不易磨损,延长使用时间。
2.2.2 好的耐热性:刀具在切削过程中会产生大量的热量,尤其在切削速度较高时,温度会很高。
因此,刀具材料应具备好的耐热性,即在高温下仍能保持较高的硬度,具有能继续进行切削的性能。
这种具有高温硬度的性质,又称热硬性或红硬性。
2.2.3 高的强度和好的韧性:在切削过程中,刀具要承受很大的冲击力,所以刀具材料要具有较高的强度,否则易断和损坏。
铣床工培训资料

录目页号内容章节1-4 1.0铣刀介绍4-10 2.0铣削过程的基础知识10-12 3.0铣刀几何参数的合理选择 13 4.0铣削用量的选择13-14 5.0难铣削材料的铣削14-20 6.0轴上键槽的铣削铣削原理刀具材料工件做进给运动的切削加工方法。
就是在铣床上以铣刀旋转做主运动,铣削,铣削性能的优劣和铣刀角度的合理选择将直接影响切削加工的生产率和加工表面的质量。
铣刀简介1.0在铣削加工中,应根据铣床的情况和加工需要合理地选择和使用铣刀。
铣刀的种类1.1.按用途分类1.1.1.铣削特种沟槽铣削直角沟槽用铣刀、可将铣刀分为铣削平面用铣刀、按照用途的不同,。
1-1用铣刀和铣削特形面用铣刀等,具体见表~1~铣刀的标记1.1.2标记的内容主铣刀上都刻有标记,尺寸规格和制造厂家等,为了便于识别铣刀的材料、要有以下几种。
制造厂家商标1.各上海工具厂和成都量具刃具厂等,如哈尔滨量具刃具厂、我国制造铣刀的厂家很多,制造厂都将自己的注册商标标注在其产品上。
铣刀材料2.表示铣刀的材料为高速钢。
HSS铣刀的材料一般用材料的牌号表示。
如铣刀尺寸规格3.铣刀的尺寸规格标注因铣刀形状的不同而略有不同。
因铣刀上的标注尺寸均为基本尺寸,在使用和刃磨后会产生变化,所以在使用时应加以注意。
)带孔铣刀1一般以外圆直径×宽度×内孔直径三面刃铣刀和锯片铣刀等,带孔铣刀包括圆柱铣刀,,80 mm,表示该铣刀的外圆直径为27×12×80来表示尺寸规格。
例如,三面刃铣刀上标有。
27 mm,内孔直径为12 mm宽度为)指状铣刀2如锥柄立铣刀上标尺寸规格一般只标注外圆直径。
指状铣刀包括立铣刀和键槽铣刀等,18Ф有。
18 mm,则表示该立铣刀的外圆直径是)盘形铣刀3(或圆弧半一般以外圆直径×宽度×内孔直径×角度角度铣刀和半圆铣刀等盘形铣刀,,角mm27 ,内孔直径为mm22 ,宽度为mm80 径)表示。
- 1、下载文档前请自行甄别文档内容的完整性,平台不提供额外的编辑、内容补充、找答案等附加服务。
- 2、"仅部分预览"的文档,不可在线预览部分如存在完整性等问题,可反馈申请退款(可完整预览的文档不适用该条件!)。
- 3、如文档侵犯您的权益,请联系客服反馈,我们会尽快为您处理(人工客服工作时间:9:00-18:30)。
铣削原理铣削,就是在铣床上以铣刀旋转做主运动,工件做进给运动的切削加工方法。
刀具材料铣削性能的优劣和铣刀角度的合理选择将直接影响切削加工的生产率和加工表面的质量。
1.0铣刀简介在铣削加工中,应根据铣床的情况和加工需要合理地选择和使用铣刀。
1.1.铣刀的种类1.1.1.按用途分类按照用途的不同,可将铣刀分为铣削平面用铣刀、铣削直角沟槽用铣刀、铣削特种沟槽用铣刀和铣削特形面用铣刀等,具体见表1-1。
~1~1.1.2 铣刀的标记为了便于识别铣刀的材料、尺寸规格和制造厂家等,铣刀上都刻有标记,标记的内容主要有以下几种。
1.制造厂家商标我国制造铣刀的厂家很多,如哈尔滨量具刃具厂、上海工具厂和成都量具刃具厂等,各制造厂都将自己的注册商标标注在其产品上。
2.铣刀材料铣刀的材料一般用材料的牌号表示。
如HSS表示铣刀的材料为高速钢。
3.铣刀尺寸规格铣刀的尺寸规格标注因铣刀形状的不同而略有不同。
因铣刀上的标注尺寸均为基本尺寸,在使用和刃磨后会产生变化,所以在使用时应加以注意。
1)带孔铣刀带孔铣刀包括圆柱铣刀,三面刃铣刀和锯片铣刀等,一般以外圆直径×宽度×内孔直径来表示尺寸规格。
例如,三面刃铣刀上标有80×12×27,表示该铣刀的外圆直径为80 mm,宽度为12 mm,内孔直径为27 mm。
2)指状铣刀指状铣刀包括立铣刀和键槽铣刀等,尺寸规格一般只标注外圆直径。
如锥柄立铣刀上标有Ф18,则表示该立铣刀的外圆直径是18 mm。
3)盘形铣刀角度铣刀和半圆铣刀等盘形铣刀,一般以外圆直径×宽度×内孔直径×角度(或圆弧半径)表示。
例如,角度铣刀的外圆直径为80 mm,宽度为22 mm,内孔直径为27 mm,角度为60°,则标记为80×22×27×60°。
同样道理,在半圆铣刀的末尾标有8R,则表示铣刀圆弧半径为8 mm。
1.1.3 铣刀的主要参数铣刀是一种多切削刃的刀具,在了解铣刀的组成和几何角度时,可把铣刀看做是由多把简单的切刀组合而成的,如图1-1(a)所示。
如图1-1(b)所示为铣刀各部分名称及相关的辅助平面。
~2~1.待加工表面待加工表面是工件上有待切除的表面。
2.已加工表面已加工表面是工件上经刀具切削后产生的表面。
3.过渡表面工件上由当前切削刃形成或者由下一切削刃切除的表面,它在刀具或工件的下一转里被切除,又称为切削表面。
4.前面前面是指刀具切屑流过的表面,又称前刀面。
5.后面后面是指与已加工表面相对的表面,又称后刀面。
6.前角γ0前面与基面间的夹角。
7.后角α0后面与切削平面间的夹角。
1.1.4 铣刀的材料及选用1.高速钢高速钢是一种含钨(W)、钼(Mo)、铬(Cr)、钒(V)等合金元素较多的高合金工具钢,通常其碳的质量分数在1%左右,W的质量分数为8%~20%,Cr的质量分数为3%~5%。
高速钢抗弯强度σb≈3 500 MPa,冲击韧度аK≈0.30 MJ/㎡。
高速钢的强度与韧性好,能承受冲击,又易于刃磨,加工性好,价格便宜;但其耐热性、硬度较低,热处理后硬度为62~65 HRC,耐热温度为550~600 ℃,耐磨性也较低。
由于受耐热温度的限制,高速钢刀具不能用于高速铣削。
高速钢是国内最常用的机械铣削加工刀具材料。
我国常用的高速钢牌号有W18Cr4V、W6Mo5Cr4V2和W9Mo3Cr4V等。
由于W18Cr4V等含W量较多的高速钢价格较贵,其生产和使用已经减少。
W2Mo9Cr4V2Co8是引进的超硬高速钢,它的高温硬度和抗氧化能力比上述高速钢好,可铣削难加工材料,适用于较高的铣削速度。
我国生产的超硬高速钢牌号是W6Mo5Cr4V2Al,它的价格比W2Mo9Cr4V2Co8便宜得多,只是热处理工艺性要求较高。
现在常用物理气相沉积法在高速钢刀具的切削表面上沉积2~5μm的TiN薄膜(也称涂层,呈金黄色),可提高刀具寿命2~5倍。
2.硬质合金硬质合金是利用粉末冶金的方法将高硬度、高熔点的碳化钨(WC)、碳化钛(TiC)、碳化钽(TaC)、碳化铌(NbC)和钴(Co)黏结、压制、烧结而成。
它的常温硬度为88~93 HRA,耐热温度为800~1 000 ℃。
与高速钢相比,其硬度、耐磨性、耐热性要好得多。
因此,硬质合金刀具允许的铣削速度比高速钢刀具大5~10倍。
但它的抗弯强度只有高速钢的1/4~1/2,冲击韧度仅为高速钢的几十分之一,故硬质合金塑性和韧性差,怕冲击和振动。
另外,它的工艺性比高速钢差,刃磨时比高速钢难磨削得多,而且不易制成整体刀具和成形刀具,一般是制成刀片焊接在刀体上使用,或用机械方法装夹、固定在刀体上使用。
我国目前常用的硬质合金有以下三类1)钨钴类硬质合金钨钴类硬质合金(代号YG)由WC和Co组成,主要用于加工铸铁、有色金属等脆性材料和非金属材料。
常用牌号有YG3、YG6和YG8。
牌号中的数字表示含Co的百分比,~3~其余为含WC的百分比。
硬质合金中Co起黏结作用,含Co量越多的硬质合金韧性越好,硬度和耐磨性越差,所以YG8适于粗加工和断续铣削,YG6适于半精加工,YG3适于精加工和连续铣削。
2)钨钛钴类硬质合金钨钛钴类硬质合金(代号YT)由WC、TiC和Co组成,由于TiC比WC还要硬、脆、耐磨、耐热,所以YT类合金比YG类合金硬度和耐热温度更高,耐冲击和振动性差。
加工钢材时,被加工材料塑性变形很大,切屑与刀具摩擦很剧烈,铣削温度很高,但由于其切屑呈带状,铣削过程较平稳,所以YT类硬质合金适于加工钢材等塑性材料。
钨钛钴类硬质合金常用牌号有YT30、YT15和YT5。
牌号中的数字表示含TiC的百分比。
TiC含量越多的硬质合金韧性越差,硬度和耐磨性越高,所以YT30适于对钢材的精加工和连续铣削,YT15适于半精加工,YT5适于粗加工和断续铣削。
3)钨钛钽(铌)类硬质合金钨钛钽(铌)类硬质合金(代号YW)是在YT类硬质合金中加入少量的TaC或NbC。
YW类硬质合金的硬度、耐磨性、耐热温度、抗弯强度和冲击韧性均比YT类高一些,其后两项指标与YG类相仿。
因此,YW类硬质合金既可以加工钢,又可以加工铸铁和有色金属,所以又称为通用硬质合金。
常用牌号有YW1和YW2,前者用于半精加工和精加工,后者用于粗加工和半精加工。
现在常用化学气相沉积法在硬质合金刀具表面上沉积5~10μm的TiC薄膜(呈银灰色),也有沉积TiC、TiN双层薄膜或沉积TiC、Al2O3和TiN三层薄膜的,复合涂层用得更多。
硬质合金刀具经过气相沉积后,寿命可提高2~10倍。
2.0 铣削过程的基础知识2.1铣削过程中的变形刀具在金属切削过程的实质是被切削金属在刀具切削刃和前刀面的挤压作用下,产生剪切滑移的变形过程,如图1-2所示。
在刀具切削力的作用下,被切割的金属层首先产生压缩弹性变形,当剪应力超过材料屈服极限后,在与受力方向成45°方向上产生最大剪应力,金属内部晶格发生滑移,即在剪切面上产生塑性变形。
刀具继续前进,切削力增大,由于切削刃的刀楔作用,产生应力集中,使切削刃附近金属剪应力超过强度极限而被剥离。
切削层产生塑性变形的同时,在切削刃附近剥离,形成切割作用。
变形后剥离的金属层在刀具前刀面的挤推作用下,沿前刀面流出,即产生切屑。
从图1-2中可以看出,由于刀具和工件的相互作用,切削层及其附近金属产生Ⅰ、Ⅱ、Ⅲ这~4~三个变形区。
第Ⅰ变形区是切削刃前方工件上的切削层产生塑性变形的滑移变形区。
它是切屑形成过程中的主要变形区域,也是三个变形区中变形量最大的区域。
第Ⅱ变形区是切屑底层与刀具前刀面接触的区域。
切削层金属经过剪切滑移后,切屑流经前刀面时受前刀面挤压和摩擦的作用,底层金属流动小于切屑上层金属流动,形成滞留层。
第Ⅲ变形区是刀具后刀面与工件已加工表面的接触区。
由于刀具切削刃和刀具后刀面对加工表面的挤压和摩擦,使工件已加工表面产生晶粒纤维化和加工硬化,并伴有一定的残余应力。
2.2积屑瘤当刀具对某些塑性金属进行切削加工时,在某一段切削速度范围内,切屑底层中的一部分金属容易被黏结或冷焊在前刀面,形成硬度很高的楔块,从而代替刀面和切削刃进行切削,这一个小楔块称为积屑瘤,如图1-3所示。
一般情况下,积屑瘤的硬度可达工件材料硬度的2~3.5倍。
1.积屑瘤的形成在一定的切削速度范围内,切屑底层金属与前刀面发生强烈的挤压和摩擦,破坏了前刀面上的氧化膜和吸附膜,使其与前刀面的接触面积逐渐增大。
同时,在巨大的压力和摩擦力作用下,切屑底层出现滞留现象,切削底层金属的流动速度较切屑的上层金属缓慢得多,并沿前刀面产生较大的变形。
在适当的压力和温度作用下,切屑底层金属填满前刀面的微观凹谷,发生冷焊现象而形成冷焊层。
冷焊层具有较大的强度和硬度,能抵御切削力的作用,形成第一层积屑瘤Q1。
由于切屑还在继续流动,与第一层积屑瘤接触的切屑底层金属又重复上述的变形和冷焊过程,堆积在第一层积屑瘤上面,形成第二层积屑瘤Q2。
如此不断堆积,致使积屑瘤不断长大。
由于积屑瘤改变了前刀面和切削刃的实际形状,使切屑与前刀面的接触条件和受力情况发生变化,当积屑瘤长到一定高度时便不再继续增大,从而形成一个完整的积屑流。
2.积屑瘤对切削加工影响积屑瘤冷焊在刀具切削刃和前刀面的前端,其形成后便可代替切削刃和前刀面进行切削,从而保护了切削刃和前刀面。
但是积屑瘤的稳定性较差,当积屑瘤达到一定高度时,常因冷焊接的破裂而脱落(部分或全部),有可能把刀具前刀面靠近刀尖的表面金属带走一部分,反而容易加剧刀具的磨损。
积屑瘤在切削过程中的产生和脱落,还常常将积屑瘤碎片黏结在已加工表面上,增大了已加工表面的粗糙度。
积屑瘤表面粗糙会使已加工表面产生误差复映~5~随着积屑瘤的增大,实际工作前角γoe有所增大,导致切削变形减小,切削力降低。
当积屑瘤最高时,实际工作前角γoe可达30°左右。
如图1-4所示,积屑瘤前端伸出切削刃之外,伸长量为△a c,这种过切厚度改变了加工尺寸。
同时,由于积屑瘤的不断产生和脱落,导致加工尺寸不稳定,影响了加工零件的尺寸精度。
存在有利于粗加工而不利于精加工。
影响积屑瘤的主要因数:(1)硬度和塑性当工件材料硬度低、塑性大时,切削过程中金属变形大,切屑与前刀面间的摩擦系数和接触长度都较大,故容易产生积屑瘤。
(2)切削速度切削速度主要是通过切削温度和摩擦系数来影响积屑瘤的。
(3)进给量进给量增加时,切削厚度增大,切削温度上升。
切削厚度越大,刀具与切屑的接触长度越长,积屑瘤的高度越大。
(4)前角刀具前角增大时,切削力减小,切削温度降低,切削变形减小,刀具与切屑的接触长度变短,从而减小积屑瘤的形成基础。
防止积屑瘤形成的措施:~6~2.3切削热与切削温度1.切削热的来源在刀具的作用下,被切削的金属发生弹、塑性变形和金属切削层发生错移和分离,形成切屑而消耗功,产生热量。