H型钢组焊方案
H型钢组焊方案
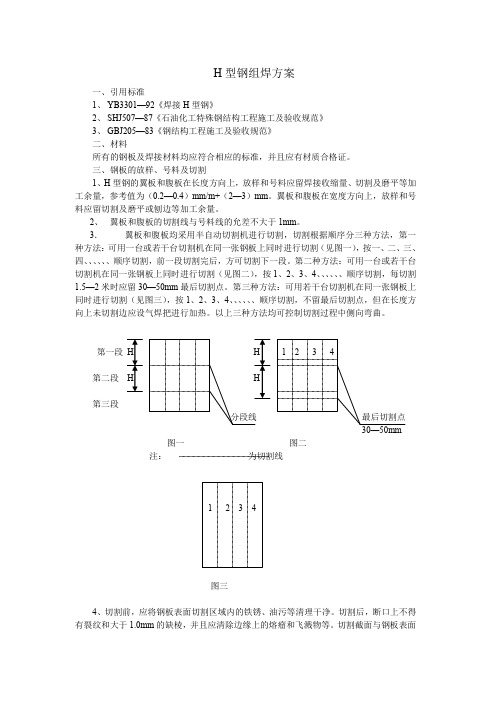
H型钢组焊方案一、引用标准1、YB3301—92《焊接H型钢》2、SHJ507—87《石油化工特殊钢结构工程施工及验收规范》3、GBJ205—83《钢结构工程施工及验收规范》二、材料所有的钢板及焊接材料均应符合相应的标准,并且应有材质合格证。
三、钢板的放样、号料及切割1、H型钢的翼板和腹板在长度方向上,放样和号料应留焊接收缩量、切割及磨平等加工余量,参考值为(0.2—0.4)mm/m+(2—3)mm。
翼板和腹板在宽度方向上,放样和号料应留切割及磨平或刨边等加工余量。
2、翼板和腹板的切割线与号料线的允差不大于1mm。
3.翼板和腹板均采用半自动切割机进行切割,切割根据顺序分三种方法,第一种方法:可用一台或若干台切割机在同一张钢板上同时进行切割(见图一),按一、二、三、四、、、、、、顺序切割,前一段切割完后,方可切割下一段。
第二种方法:可用一台或若干台切割机在同一张钢板上同时进行切割(见图二),按1、2、3、4、、、、、、顺序切割,每切割1.5—2米时应留30—50mm最后切割点。
第三种方法:可用若干台切割机在同一张钢板上同时进行切割(见图三),按1、2、3、4、、、、、、顺序切割,不留最后切割点,但在长度方向上未切割边应设气焊把进行加热。
以上三种方法均可控制切割过程中侧向弯曲。
第一段 1 2 3 4第二段第三段最后切割点30—50mm图一图二注:为切割线1 2 3 4图三4、切割前,应将钢板表面切割区域内的铁锈、油污等清理干净。
切割后,断口上不得有裂纹和大于1.0mm的缺棱,并且应清除边缘上的熔瘤和飞溅物等。
切割截面与钢板表面不垂直度应不大于钢板厚度的10%,且≤2.0mm。
5、翼板和腹板切割后的允许偏差:翼板宽度允许偏差:-2--+2mm。
腹板宽度允许偏差:0--2mm。
翼板和腹板切割后的侧向弯曲允许偏差≤2.0mm。
四、翼板和腹板的拼接由于现场钢板料长度为6米或8米,因此,大部分梁、柱的翼板和腹板在长度方向上要拼接,其具体要求为:1、翼板或腹板拼接的最小板块长度》800mm,并应是轧制方向与长度方向一致。
钢结构制作安装施工方案焊接H型钢

XXX钢结构制作、安装施工方案批准:审核:编制:XXX项目部二0一二年五月一十一日目录一、工程概况及特点二、主要施工依据、主要制作过程及技术要求三四、构件的安装及技术要求五、施工工期六、安装劳动力组合七、安装主要施工机具八、施工安全措施一、工程概况及特点:XXX钢结构包括主厂房框架、各层平台、梯道、围护结构等,构件材料主要以轧制H型钢为主,结构件总工程量约182吨。
构件最高安装高度为20m,最大吊装重量为6.3吨,因受施工场地的影响,此次钢结构制作由钢结构制造厂制作,因其距安装现场较远,增大了构件的倒运工作量。
此次钢结构制安工期紧,安装施工多为高空作业,而且部分轴柱交叉作业多,给施工带来较大的安全隐患.同时,因受设备安装的影响,主厂房钢结构安装只有滞后设备安装才能给其提供作业空间。
另外,钢结构的安装速度制约着设备的安装进度,因此,合理安排钢结构施工进度是确保该工程按期完成的关键之一。
二、主要施工依据1、XXX建筑勘察设计有限公司技术部提供的施工CAD图。
2、《建筑机械使用安全操作规程》JGJ33-863、《施工现场临时用电安全技术规程》JGJ46-884、《建筑施工安全检查标准》JGJ59-995、《建筑施工高空作业安全技术规程》JGJ80-916、《钢结构工程施工质量验收规范》GB50205-20017、《建筑钢结构焊接与验收规程》JGJ81-918、《高强度螺栓连接应用技术规程》JGJ82-919、《碳钢焊条》GB5117-85三、主要制作工艺过程及技术要求1.材料要求1.1本次工程使用的材料材质以Q345钢为主,其性能应符合国家标准的有关规定。
其材质标准应符合国家标准GB/T700-1988。
1.2轧制型钢应符合国家标准GB/T11263-2005。
1.3按国家规定及建设方的有关要求,焊接H型钢钢柱的翼板、腹板材料及吊车梁上使用的材料均应作材料复检,对复检不合格的材料应不予使用或降级使用。
现场H型钢焊接与钢结构制安方案
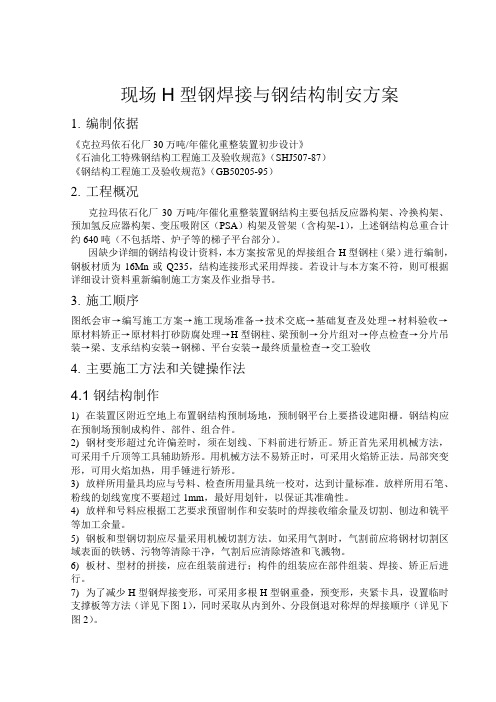
现场H型钢焊接与钢结构制安方案1.编制依据《克拉玛依石化厂30万吨/年催化重整装置初步设计》《石油化工特殊钢结构工程施工及验收规范》(SHJ507-87)《钢结构工程施工及验收规范》(GB50205-95)2.工程概况克拉玛依石化厂30万吨/年催化重整装置钢结构主要包括反应器构架、冷换构架、预加氢反应器构架、变压吸附区(PSA)构架及管架(含构架-1),上述钢结构总重合计约640吨(不包括塔、炉子等的梯子平台部分)。
因缺少详细的钢结构设计资料,本方案按常见的焊接组合H型钢柱(梁)进行编制,钢板材质为16Mn或Q235,结构连接形式采用焊接。
若设计与本方案不符,则可根据详细设计资料重新编制施工方案及作业指导书。
3.施工顺序图纸会审→编写施工方案→施工现场准备→技术交底→基础复查及处理→材料验收→原材料矫正→原材料打砂防腐处理→H型钢柱、梁预制→分片组对→停点检查→分片吊装→梁、支承结构安装→钢梯、平台安装→最终质量检查→交工验收4.主要施工方法和关键操作法4.1 钢结构制作1)在装置区附近空地上布置钢结构预制场地,预制钢平台上要搭设遮阳栅。
钢结构应在预制场预制成构件、部件、组合件。
2)钢材变形超过允许偏差时,须在划线、下料前进行矫正。
矫正首先采用机械方法,可采用千斤顶等工具辅助矫形。
用机械方法不易矫正时,可采用火焰矫正法。
局部突变形,可用火焰加热,用手锤进行矫形。
3)放样所用量具均应与号料、检查所用量具统一校对,达到计量标准。
放样所用石笔、粉线的划线宽度不要超过1mm,最好用划针,以保证其准确性。
4)放样和号料应根据工艺要求预留制作和安装时的焊接收缩余量及切割、刨边和铣平等加工余量。
5)钢板和型钢切割应尽量采用机械切割方法。
如采用气割时,气割前应将钢材切割区域表面的铁锈、污物等清除干净,气割后应清除熔渣和飞溅物。
6)板材、型材的拼接,应在组装前进行;构件的组装应在部件组装、焊接、矫正后进行。
7)为了减少H型钢焊接变形,可采用多根H型钢重叠,预变形,夹紧卡具,设置临时支撑板等方法(详见下图1),同时采取从内到外、分段倒退对称焊的焊接顺序(详见下图2)。
h型钢施工方案
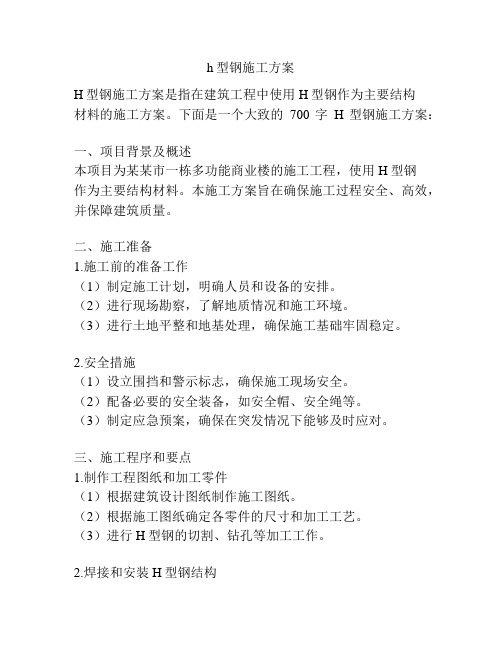
h型钢施工方案H型钢施工方案是指在建筑工程中使用H型钢作为主要结构材料的施工方案。
下面是一个大致的700字H型钢施工方案:一、项目背景及概述本项目为某某市一栋多功能商业楼的施工工程,使用H型钢作为主要结构材料。
本施工方案旨在确保施工过程安全、高效,并保障建筑质量。
二、施工准备1.施工前的准备工作(1)制定施工计划,明确人员和设备的安排。
(2)进行现场勘察,了解地质情况和施工环境。
(3)进行土地平整和地基处理,确保施工基础牢固稳定。
2.安全措施(1)设立围挡和警示标志,确保施工现场安全。
(2)配备必要的安全装备,如安全帽、安全绳等。
(3)制定应急预案,确保在突发情况下能够及时应对。
三、施工程序和要点1.制作工程图纸和加工零件(1)根据建筑设计图纸制作施工图纸。
(2)根据施工图纸确定各零件的尺寸和加工工艺。
(3)进行H型钢的切割、钻孔等加工工作。
2.焊接和安装H型钢结构(1)按照施工图纸进行H型钢的组装和焊接。
(2)在焊接过程中,注意控制焊缝质量和焊接强度。
(3)安装H型钢结构时,使用合适的吊装设备,并进行精确的定位。
3.质量控制和安全检测(1)对焊接接头进行质量检测,确保焊缝的牢固性和密度。
(2)对H型钢结构进行强度和稳定性的测试,确保结构的安全性。
(3)及时修复和整改施工中发现的质量问题,确保建筑质量符合标准。
四、施工人员与设备1.施工人员(1)项目经理:负责项目的整体管理和协调。
(2)施工人员:包括焊工、安装工和质检人员等。
2.施工设备(1)吊车和起重机:用于搬运和安装H型钢结构。
(2)焊接设备:用于H型钢的焊接工作。
(3)质检仪器:用于对焊接接头和结构强度进行测试。
五、施工周期和成本预算1.施工周期根据具体施工工作量和人员配备,初步预计施工周期为6个月。
2.成本预算根据材料、人工和设备的消耗,初步预算总成本为500万元。
六、工程质量和安全控制1.工程质量控制(1)按照施工图纸和规范进行施工,确保结构牢固、平整。
钢结构工程焊接专项方案
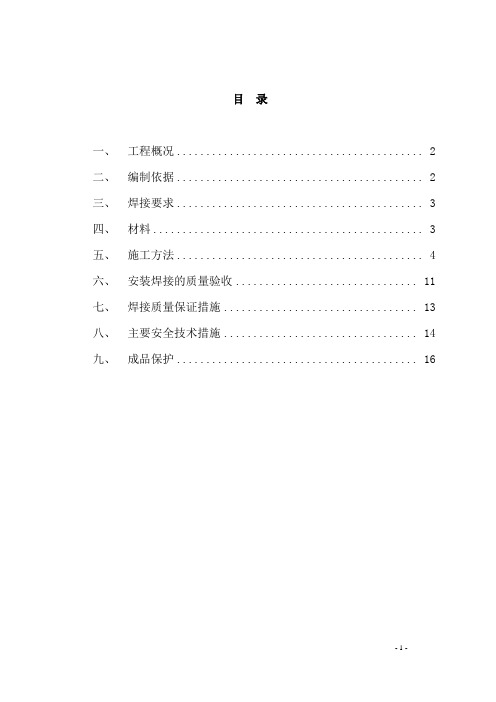
目录一、工程概况 (2)二、编制依据 (2)三、焊接要求 (3)四、材料 (3)五、施工方法 (4)六、安装焊接的质量验收 (11)七、焊接质量保证措施 (13)八、主要安全技术措施 (14)九、成品保护 (16)桐洲监狱三监区钢结构大棚焊接方案一、工程概况本工程位于桐洲监狱内,原AB门处。
因桐洲监狱改建,原AB门拆除,并在AB门处新建厂房,代替原旧三监区工艺房,该厂房采用平面桁架结构形式,建筑高度6m(本处为檐口高度) ,建筑面积:1987.59m。
本工程结构安全等级为二级,设计使用年限为10年,结构重要性系数为1.0;建筑工程等级二级。
本工程屋面为0.5mm820型采钢板+75mm玻璃丝绵保温层(带钢丝网)。
墙面1.2m以下为200mm厚轻质砖墙1.2m以上为0.5mm900型彩钢板+75mm玻璃丝绵保温面(带钢丝网)二、编制依据1、《碳素结构钢》(GB 700-2006);2、《通用冷弯开口型钢》(GB 6723-2008);3、《碳钢焊条》(GB 5117-1995);4、《钢结构焊接规范》(GB50661-2011);5、《钢管结构技术规程》(CECS 280:2010)6、《冷弯薄壁型钢结构技术规程》(GB 50018-2002);7、《冷弯型钢技术条件》(GB 6725-2008);8、《直缝电焊钢管》(GB/T13793—2008);9、《碳钢药芯焊丝》(GB 10045-2001);三、焊接要求1、组合H型钢的腹板与翼缘的焊接应采用自动埋弧焊机焊,且四道连接焊缝均应双面满焊,不得单面焊接。
2、组合H型钢因焊接产生的变形应以机械或火焰矫正调直。
3、焊缝质量等级:连接板与H型钢的连接焊缝为全熔透坡口焊,质量等级为二级,其他为三级。
所有非施工图所示构件拼接用的对接焊缝质量应达到二级。
对于全熔透焊缝,可根据焊接规程的基本要求,结合焊缝质量等级、焊接工艺和焊接次序,确定坡口形式和尺寸。
四、材料(1)本工程的钢材均采用Q235B,焊条采用E43系列。
H型焊接工字钢制作施工方案
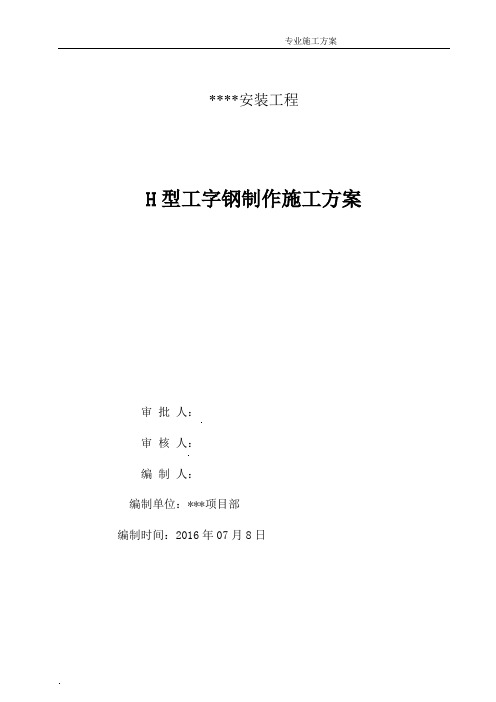
10
C02气体保护焊机
CPZX—500型
10
11
半自动切割机
CG1-30
5
12
大号气焊枪
HO1-30
10
13
油压千斤顶
100t
2
14
磁力钻
Φ25
4
15
超声波探伤机
CTS-26
1
16
手工弧焊机
AX-500、AX-320
5、2
17
大拖车
12m
1
临时租用
18
空压机
9M3
1
8质量保证措施
8.1编制焊接工艺卡。
9.4现场使用电气焊时必须对周围的易燃易爆品进行清除或覆盖隔离。
9.5使用剪板机剪切钢板时应放置平稳,剪切时上剪未复位不可送料,手不得伸入压力下方,不准用剪切超过规定厚度和压不到的窄钢板。
9.6现场吊装钢板时必周围闲杂人员不得进入吊装区域内。
9.7现场钢材下料后余留的边角料必须及时清理,以防止刮碰受伤。
H型钢梁柱的主要焊缝焊接作为该单项工程的特殊工序。
保证焊接质量,应对其检查作以下要求:
①焊缝探伤选用超声波探伤,焊缝质量等级达到二级。
②焊缝过渡平缓,成形良好。
③焊缝在影响区表面不允许出现裂纹、气孔、弧坑和夹渣等缺陷。
④焊缝咬边深度应小于0.5mm,咬边连续长度不应大于100mm。
⑤焊缝上的溶渣和两侧飞贱应清除干净。
8.8H型钢组装时应有适当的工具和设备,如定位器、夹具、坚固的基础(或胎具)以保证组装有足够的精度。
8.9现场凡是下雨天或风速大于8m/s,又无防护措施时应停止室外焊接工作。
9安全保障措施
9.1进入施工现场必须待安全帽、工作服。
h型钢截面与钢板焊接

h型钢截面与钢板焊接
H 型钢截面与钢板焊接是一种常见的钢结构连接方式,通常用于构建桥梁、建筑和其他大型结构。
下面是一些关于 H 型钢截面与钢板焊接的基本信息和步骤:
1. 准备工作:在开始焊接之前,需要对 H 型钢和钢板进行清洁和处理,以确保焊接表面干净、无油脂、锈蚀或其他污染物。
可以使用砂轮、钢丝刷或喷砂等方法进行清洁。
2. 对准和固定:将 H 型钢和钢板对准,并使用夹具或螺栓将它们固定在一起,以确保在焊接过程中不会移动或变形。
3. 焊接方法:H 型钢截面与钢板的焊接可以采用多种方法,如电弧焊、气体保护焊、埋弧焊等。
选择哪种焊接方法取决于焊接的要求、材料的厚度和类型等因素。
4. 焊接顺序:一般来说,焊接应从 H 型钢的一端开始,逐渐向另一端进行。
在焊接过程中,应尽量保持焊接速度均匀,以避免产生应力集中和变形。
5. 焊接检验:焊接完成后,需要对焊缝进行外观检查和无损检测,以确保焊接质量符合要求。
外观检查包括检查焊缝是否平整、无裂纹、气孔等缺陷,无损检测可以采用超声波检测、射线检测等方法。
需要注意的是,在进行 H 型钢截面与钢板焊接时,应遵循相关的安全规定和操作规程,确保操作人员的安全。
同时,应根据具体情况选择合适的焊接材料和工艺参数,以确保焊接质量。
如果你不确定如何进行焊接,建议咨询专业的焊接工程师或技术人员。
h型钢施工方案

h型钢施工方案H型钢是一种常见的构造钢材,具有强度高、刚度好等优点,广泛应用于建筑工程中。
在进行H型钢的施工时,需要根据实际情况制定施工方案,以确保施工质量和安全。
下面是一个H型钢施工方案的示例,供参考。
一、施工材料准备:1. H型钢材:根据需求,准备相应规格和数量的H型钢材;2. 施工工具:焊接机、切割机、螺栓等;3. 安全防护用品:安全帽、安全鞋、手套等。
二、施工步骤:1. 测量和标定:根据设计图纸,用测量工具测量H型钢的尺寸和长度,并用粉笔或铅笔在H型钢上做好标记,以便后续操作;2. 切割和修整:使用切割机对H型钢进行切割,根据需求对H型钢进行修整,确保尺寸和长度的准确性;3. 预制螺栓孔:根据设计要求,在H型钢上进行螺栓孔的预制,确保螺栓的固定性能;4. 焊接连接:根据设计要求,用焊接机对H型钢进行连接焊接,确保焊缝牢固、无裂缝;5. 安装和固定:将焊接好的H型钢进行安装,并使用螺栓进行固定,确保H型钢的稳固性;6. 检查和修整:在施工完成后,对H型钢进行仔细检查,如有需要,进行修整和调整,确保施工质量;7. 清理和保养:施工结束后,对施工现场进行清理,将施工材料放置妥当,并对施工工具进行保养和维护。
三、施工注意事项:1. 施工中必须戴上相应的安全防护用品,严禁穿拖鞋和长裤;2. 施工现场必须有足够的通风,防止产生有害气体;3. 必须按照安全操作规程进行作业,禁止擅自改变施工步骤;4. 施工场地必须保持干燥和整洁,防止滑倒和意外事故的发生;5. 高空作业必须配备相应的安全设备,并有专人负责监督。
以上是一个H型钢施工方案的基本内容,具体施工流程和细节应根据实际情况进行调整和补充。
在实施施工过程中,要严格按照安全规范进行操作,确保施工质量和安全。
焊接H型钢主角焊缝全熔透焊接新工艺

1 . 3 采用 陶瓷 衬 垫法
0 引 言
打底丁作量压影响熔深和焊缝的形状系数比焊接速度影大工期长工序复杂成本较高等特点也不是响熔深和焊缝的形状系数比引熄弧板影响理想的全熔透焊接工艺方案焊缝端部焊接质量焊丁对t艺的理解和执行情况如果要攻克此技术难题
6 6 . 焊接质量控制与管理 ・
文章编号 : 1 0 0 2 一 o 2 5 x ( 2 o 1 5 ) o 3 — 0 0 6 6 — 0 3
留间 隙 4 ~ 5 i n m.采 用 二 氧 化 碳 气 体 保 护 焊 打 底 焊
接 .然 后 再 进 行 埋 弧 焊 焊 接 .这 种工 艺 在 厚板 焊接
造 成烧 穿 ) 、杆 件腹 板 的倾 斜 角 度 ( 影 响 电 弧熔 深 的
位置 ) 、焊 丝 对 准 的 位 置 ( 影 响电弧熔深 的位置 ) 、 焊 接 电流 ( 影 响熔 深 和焊 缝 的形 状 系 数 比) 、电弧 电 压 ( 影 响熔 深 和焊 缝 的形 状 系数 比 ) 、焊 接 速 度 ( 影 响 熔 深和 焊缝 的形状 系 数 比 ) 、引 ( 熄 )弧 板 ( 影 响
理想 的全熔 透焊 接工 艺方 案
焊缝端 部焊接质量 ) 、焊 丁 对 T 艺 的 理 解 和 执 行 情
况 如 果 要 攻 克 此技 术难 题 .需 要 根 据 构 件 的具 体
收 稿 日期 :2 0 1 4 - 0 9 — 2 6
H型钢焊接变形控制
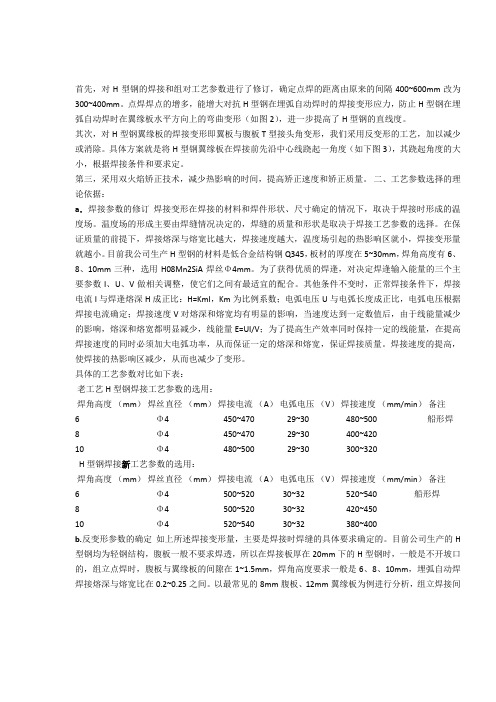
首先,对H型钢的焊接和组对工艺参数进行了修订,确定点焊的距离由原来的间隔400~600mm改为300~400mm。
点焊焊点的增多,能增大对抗H型钢在埋弧自动焊时的焊接变形应力,防止H型钢在埋弧自动焊时在翼缘板水平方向上的弯曲变形(如图2),进一步提高了H型钢的直线度。
其次,对H型钢翼缘板的焊接变形即翼板与腹板T型接头角变形,我们采用反变形的工艺,加以减少或消除。
具体方案就是将H型钢翼缘板在焊接前先沿中心线跷起一角度(如下图3),其跷起角度的大小,根据焊接条件和要求定。
第三,采用双火焰矫正技术,减少热影响的时间,提高矫正速度和矫正质量。
二、工艺参数选择的理论依据:a.焊接参数的修订焊接变形在焊接的材料和焊件形状、尺寸确定的情况下,取决于焊接时形成的温度场。
温度场的形成主要由焊缝情况决定的,焊缝的质量和形状是取决于焊接工艺参数的选择。
在保证质量的前提下,焊接熔深与熔宽比越大,焊接速度越大,温度场引起的热影响区就小,焊接变形量就越小。
目前我公司生产H型钢的材料是低合金结构钢Q345,板材的厚度在5~30mm,焊角高度有6、8、10mm三种,选用H08Mn2SiA焊丝Φ4mm。
为了获得优质的焊逢,对决定焊逢输入能量的三个主要参数I、U、V做相关调整,使它们之间有最适宜的配合。
其他条件不变时,正常焊接条件下,焊接电流I与焊逢熔深H成正比:H=KmI,Km为比例系数;电弧电压U与电弧长度成正比,电弧电压根据焊接电流确定;焊接速度V对熔深和熔宽均有明显的影响,当速度达到一定数值后,由于线能量减少的影响,熔深和熔宽都明显减少,线能量E=UI/V;为了提高生产效率同时保持一定的线能量,在提高焊接速度的同时必须加大电弧功率,从而保证一定的熔深和熔宽,保证焊接质量。
焊接速度的提高,使焊接的热影响区减少,从而也减少了变形。
具体的工艺参数对比如下表:老工艺H型钢焊接工艺参数的选用:焊角高度(mm)焊丝直径(mm)焊接电流(A)电弧电压(V)焊接速度(mm/min)备注6 Φ4 450~470 29~30 480~500 船形焊8 Φ4 450~470 29~30 400~42010 Φ4 480~500 29~30 300~320H型钢焊接新工艺参数的选用:焊角高度(mm)焊丝直径(mm)焊接电流(A)电弧电压(V)焊接速度(mm/min)备注6 Φ4 500~520 30~32 520~540 船形焊8 Φ4 500~520 30~32 420~45010 Φ4 520~540 30~32 380~400b.反变形参数的确定如上所述焊接变形量,主要是焊接时焊缝的具体要求确定的。
H型钢焊接施工方案

H型钢焊接施工方案
一、H型钢构件处理前的准备工作
1.材质的确定:明确施工H型钢片的材质,尤其应确认是否为低碳钢或低合金钢,并将此作为焊接施工的准备工作。
2.标准的确定:确定H型钢焊接施工时所采用的焊接标准,了解国家和企业焊接技术标准,以保证焊接质量。
3.尺寸的确定:规定H型钢焊接质量要求时,根据焊接焊口错口尺寸的要求确定构件的尺寸,以保证焊接质量。
4.布放板片:根据H型钢构件下料后的尺寸,将板片布放到现场,确保它们的布放顺序,保证焊接质量。
二、H型钢构件焊接施工准备
1.焊接条件:根据H型钢构件的材质,尺寸,尺寸等确定焊接条件,选择正确的焊接电弧和焊条。
2.焊接位置:根据施工现场对构件的实际结构情况,确定H型钢构件上的焊接位置,包括构件两边的焊缝。
3.焊接工艺:根据施工H型钢构件的材质、尺寸、结构设计,确定合理的焊接工艺,保证焊接质量。
4.焊接工具:确定和准备施工H型钢所需的焊接电弧,焊条,焊剂,清洁棉等,以保证焊接的质量与安全。
三、H型钢构件焊接施工操作
1.清理焊口:确定H型钢构件上的焊缝,并对焊口进行清理。
焊接h型钢标准

焊接h型钢标准焊接H型钢标准。
H型钢是一种常见的结构钢材料,广泛应用于建筑、桥梁、机械制造等领域。
在实际应用中,焊接是H型钢连接的常见方式之一。
为了确保焊接质量和连接强度,我们需要遵循一定的焊接标准和规范。
首先,选择合适的焊接材料至关重要。
通常情况下,我们会选择焊条或焊丝作为焊接材料。
在选择焊接材料时,需要考虑到H型钢的材质和使用环境,确保焊接材料与H型钢的材质相适应,以及能够满足连接部位的强度要求。
其次,焊接工艺也是影响焊接质量的重要因素之一。
在进行H型钢的焊接时,需要注意预热温度、焊接电流、焊接速度等参数的控制。
预热温度的选择应该考虑到H型钢的材质和厚度,以及焊接材料的类型。
焊接电流和速度的控制则需要根据具体的焊接材料和厚度来确定,以确保焊接缝的质量和均匀性。
另外,焊接人员的技术水平和操作规范也对焊接质量有着直接的影响。
焊接人员需要具备一定的焊接技术和经验,能够熟练地操作焊接设备,并严格按照焊接标准和规范进行操作。
此外,焊接现场的环境条件也需要得到充分的考虑,确保焊接过程中的安全和质量。
最后,焊接后的检验和评定也是十分重要的。
焊接完成后,需要对焊缝进行全面的检查和评定,确保焊接质量符合相关标准和规范要求。
在检验过程中,需要注意焊接缺陷的识别和评定,以及焊接强度的检测和评定。
总的来说,焊接H型钢需要遵循一定的焊接标准和规范,选择合适的焊接材料,控制好焊接工艺,提高焊接人员的技术水平和操作规范,以及严格进行焊接质量的检验和评定。
只有这样,才能确保焊接H型钢的质量和连接强度,满足实际工程的需要。
H型钢施工方案
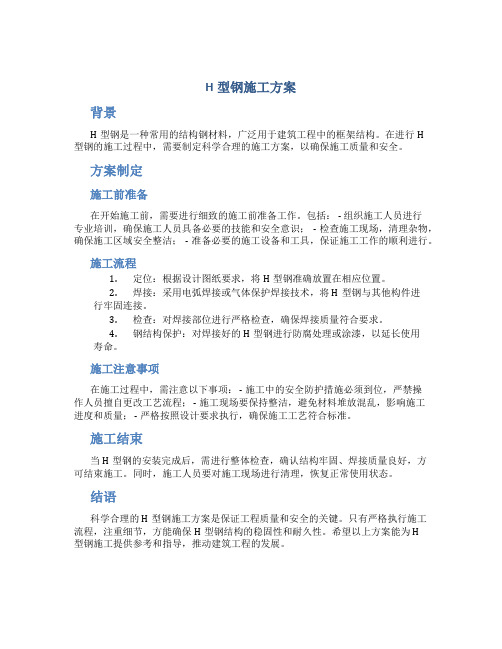
H型钢施工方案
背景
H型钢是一种常用的结构钢材料,广泛用于建筑工程中的框架结构。
在进行H
型钢的施工过程中,需要制定科学合理的施工方案,以确保施工质量和安全。
方案制定
施工前准备
在开始施工前,需要进行细致的施工前准备工作。
包括: - 组织施工人员进行
专业培训,确保施工人员具备必要的技能和安全意识; - 检查施工现场,清理杂物,确保施工区域安全整洁; - 准备必要的施工设备和工具,保证施工工作的顺利进行。
施工流程
1.定位:根据设计图纸要求,将H型钢准确放置在相应位置。
2.焊接:采用电弧焊接或气体保护焊接技术,将H型钢与其他构件进
行牢固连接。
3.检查:对焊接部位进行严格检查,确保焊接质量符合要求。
4.钢结构保护:对焊接好的H型钢进行防腐处理或涂漆,以延长使用
寿命。
施工注意事项
在施工过程中,需注意以下事项: - 施工中的安全防护措施必须到位,严禁操
作人员擅自更改工艺流程; - 施工现场要保持整洁,避免材料堆放混乱,影响施工
进度和质量; - 严格按照设计要求执行,确保施工工艺符合标准。
施工结束
当H型钢的安装完成后,需进行整体检查,确认结构牢固、焊接质量良好,方可结束施工。
同时,施工人员要对施工现场进行清理,恢复正常使用状态。
结语
科学合理的H型钢施工方案是保证工程质量和安全的关键。
只有严格执行施工流程,注重细节,方能确保H型钢结构的稳固性和耐久性。
希望以上方案能为H
型钢施工提供参考和指导,推动建筑工程的发展。
h型钢施工方案
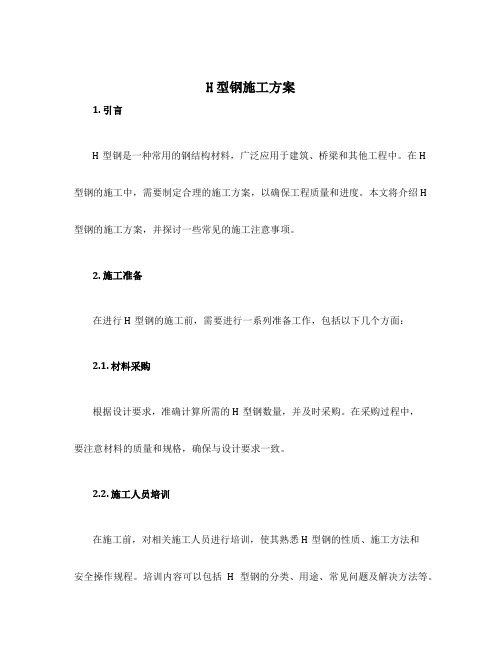
H型钢施工方案1. 引言H型钢是一种常用的钢结构材料,广泛应用于建筑、桥梁和其他工程中。
在H 型钢的施工中,需要制定合理的施工方案,以确保工程质量和进度。
本文将介绍H 型钢的施工方案,并探讨一些常见的施工注意事项。
2. 施工准备在进行H型钢的施工前,需要进行一系列准备工作,包括以下几个方面:2.1. 材料采购根据设计要求,准确计算所需的H型钢数量,并及时采购。
在采购过程中,要注意材料的质量和规格,确保与设计要求一致。
2.2. 施工人员培训在施工前,对相关施工人员进行培训,使其熟悉H型钢的性质、施工方法和安全操作规程。
培训内容可以包括H型钢的分类、用途、常见问题及解决方法等。
2.3. 施工设备准备准备所需的施工设备,包括吊装机械、切割设备、焊接设备等。
确保设备齐全且正常运行,以保证施工的顺利进行。
3. 施工步骤H型钢的施工一般包括以下几个步骤:3.1. 接收检查在H型钢到达施工现场后,进行接收检查。
检查H型钢的数量、尺寸、质量是否与采购要求一致。
若发现问题,应及时与供应商联系并处理。
3.2. 材料理顺对各个型号的H型钢进行分类,并按照设计要求进行理顺。
确保材料准备工作的顺利进行。
3.3. 安装准备根据设计图纸和工艺要求,制定安装方案并进行准备工作。
包括测量定位、设置标线、准备安装工具等。
3.4. H型钢安装根据安装方案,进行H型钢的吊装和安装。
在吊装过程中,要采取合理的吊装措施,确保安全可靠。
在安装过程中,要注意H型钢的定位和对齐,保证每根H型钢的安装正确无误。
3.5. 检验验收在H型钢的安装完成后,进行检验和验收。
检查H型钢的安装质量、尺寸和表面质量是否符合要求。
若发现问题,应及时进行修复和调整。
4. 施工注意事项在H型钢的施工过程中,需要注意以下几个方面的问题:4.1. 安全防护施工人员要正确佩戴安全帽、安全鞋和防护手套等个人防护装备。
严禁在施工现场吸烟,并确保施工现场通风良好。
4.2. 施工现场管理要保持施工现场的整洁和有序。
全熔透焊接“H”型钢(腹板 16mm 以下)免开坡口组焊矫一体化加工技术研究与应用
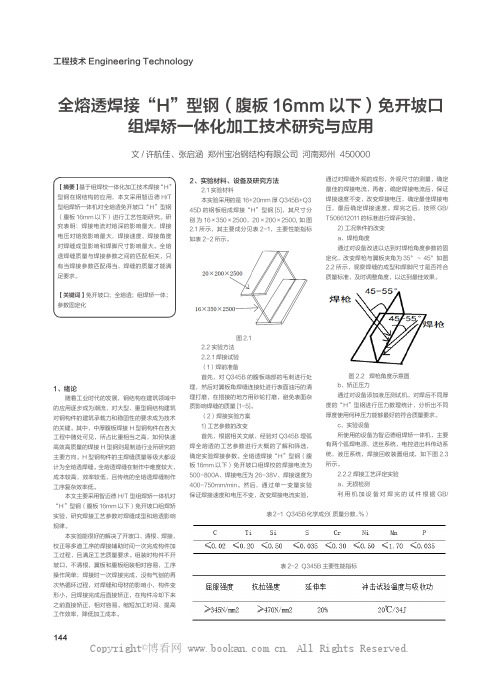
光、腐蚀后,置于光学显微镜下观察。200 倍下 母材显微组织为铁素体和珠光体,其组织分布相 对均匀,强度高和韧性好;热影响区显微组织为 贝氏体、铁素体和珠光体,热影响区出现贝氏体, 其强度硬度增加,塑性韧性下降 [2-4];焊缝显 微组织:针状铁素体 + 珠光体。
由于一次组装焊接矫正、为保证腹板熔透, 热输入高,冷却时,由于三向应力收缩,低熔点 共晶物在焊缝中心偏析,易产生裂纹 [2-4],不 开坡口,免清根容易产生气孔溢出困难,熔渣积 留问题,为了控制这些因素,避免这些问题出现, 选择合适的工艺参数尤为重要。
通过对焊缝外观的成形,外观尺寸的测量,确定 最佳的焊接电流,再者,确定焊接电流后,保证 焊接速度不变,改变焊接电压,确定最佳焊接电 压,最后确定焊接速度。焊完之后,按照 GB/ T506612011 的标准进行焊评实验。
2) 工况条件的改变 a、焊枪角度 通过对设备改进以达到对焊枪角度参数的固 定化,改变焊枪与翼板夹角为 35°~ 45°如图 2.2 所示,观察焊缝的成型和焊脚尺寸是否符合 质量标准, 时调整角度,以达到最佳效果。
图 3.1 焊接电流对焊缝成形的影响示意图 焊接电流是决定焊丝熔化速度、熔透深度和 母材熔化量的最重要的参数 [2-4]。焊接电流对 熔深的影响最大,焊接电流与熔深成正比关系, 随着电流提高,熔深余高同时增大,焊缝成形系 数变小,当成型系数小于 1.5,深而窄的焊缝易 产生热裂纹,未避免产生裂纹,必须严格控制深
1、应用逐步成为潮流,对大型、重型钢结构建筑 对钢构件的建筑承载力和稳固性的要求成为技术 的关键。其中,中厚腹板焊接 H 型钢构件在各大 工程中随处可见,所占比重相当之高,如何快速 高效高质量的焊接 H 型钢则是制造行业所研究的 主要方向。H 型钢构件的主焊缝质量等级大都设 计为全熔透焊缝。全熔透焊缝在制作中难度较大, 成本较高,效率较低,且传统的全熔透焊缝制作 工序复杂效率低。
H型钢焊接施工方案
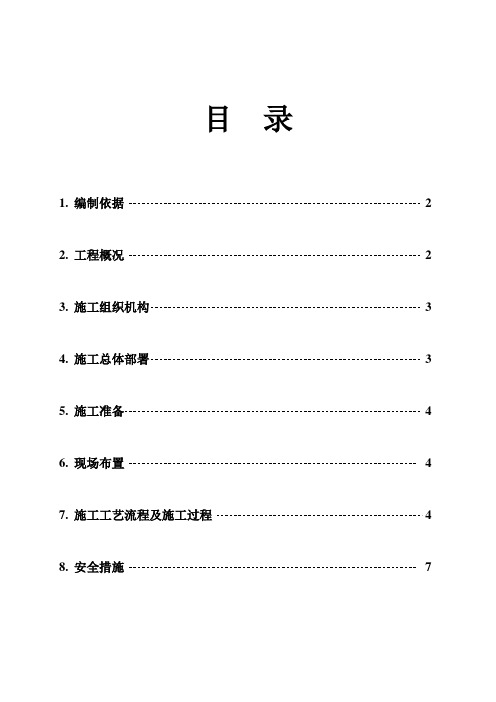
目录1.编制依据 22.工程概况 23.施工组织机构 34.施工总体部署 35.施工准备 46.现场布置 47.施工工艺流程及施工过程 48.安全措施7一、编制依据1.《从新厂区综合管网施工图SG0318—30T1》。
2.《钢结构工程施工及洋手规范GB—50205—95》。
3.《钢结构制作安装施工规范YB9254—95》。
4.《建筑结构焊接技术规程JGJ81—2001》。
二、工程概况本系统是赤泥外排管网、新厂区综合管网部分,施工现场具体位置在碱液调配项目西侧,安装施工线全长约200m,主要实物工程量有1/C~25/C线双列。
具体如下:1. 1/C线十字柱两根高度16m 编号HZJC-12. 2/C线十字柱两根高度16m 编号HZJC-13. 3/C线H型钢柱两根高度16m 编号GZJC-14. 4/C线H型钢柱两根高度16m 编号GZJC-15. 5/C线H型钢柱两根高度16m 编号HZJC-26. 6/C线H型钢柱两根高度16m 编号HZJC-27. 7/C线H型钢柱两根高度16m 编号HZJC-38. 8/C线十字钢柱两根高度16m 编号HZJC-49. 9/C线十字钢柱两根高度16m 编号HZJC-510. 10/C线十字钢柱两根高度16m 编号HZJC-411. 11/C线十字钢柱两根高度16m 编号HZJC-112. 12/C线H型钢柱两根高度16m 编号GZJC-113. 13/C线H型钢柱两根高度16m 编号GZJC-114. 14/C线十字钢柱两根高度16m 编号HZJC-115. 15/C线十字钢柱两根高度16m 编号HZJC-116. 16/C线十字钢柱两根高度16m 编号HZJC-617. 17/C线十字钢柱两根高度16m 编号HZJC-718. 18/C线十字钢柱两根高度16m 编号HZJC-819. 19/C线十字钢柱两根高度16m 编号HZJC-720. 20/C线十字钢柱两根高度27m 编号HZJC-921. 21/C线十字钢柱两根高度27m 编号HZJC-222. 22/C线H型钢柱两根高度27m 编号GZJC-323. 23/C线H型钢柱两根高度27m 编号GZJC-1024. 24/C线十字钢柱两根高度27m 编号HZJC-1125. 25/C线十字钢柱两根高度27m 编号HZJC-11三、施工组织机构项目经理:田守德项目总工:马文成项目副经理:孙书伟焊接队张:陈玉满吊装队长:张允学防腐队长:耿培金制作队长:邹本正四、施工总体部署主要工程目标1.工程质量:分项工程合格率100%,优良率95%,力争部优。
钢结构现场焊接方案

钢结构现场焊接方案本工程钢结构现场焊接主要是柱与柱、柱与梁、梁拼接的焊接。
材质为Q345B 钢。
H 型钢柱焊缝要求全焊透。
钢梁为H 型钢,主梁与钢柱的连接方式为刚接,焊缝要求全焊透。
根据本工程的实际情况,现场采用半自动CO2焊的焊接方法。
3.6.1焊接前的技术复核工作参与本工程施焊的焊工必须持有劳动部门颁发的焊工资格合格证书,且须满足以下要求:(1)合格项目必须能覆盖现场所有焊接位置。
(2)合格项目必须在有效期内。
(3)施焊前,依据JGJ81—2002《建筑钢结构焊接技术规程》的相关要求,进行焊工附加考试,合格后方可上岗。
3.6.2钢结构焊接顺序1.焊接顺序总体原则为减少局部或整体焊接变形,将焊接残余应力降低到最小限度,钢结构焊接须制定并实施合理的焊接顺序。
焊接顺序应遵循以下原则:(1)在平面上,从中心框架向四周扩散焊接; (2)先焊收缩量大的焊缝,再焊收缩量小的焊缝; (3)对称焊接;(4)同一根梁的两端不能同时焊接(先焊一端,待其冷却后再焊另一端)。
2.柱两层吊装一次,一个流水段内的构件焊接顺序包括一节柱,两层梁,其空间焊接顺序为:上层梁-柱、梁拼接焊接→下层梁-柱、梁拼接焊接→柱节点焊接。
在单层作业面上的焊接顺序为先施焊主梁与柱的节点,梁的拼焊节点。
3.主梁的焊接顺序 单根主梁的焊接顺序为:先焊下翼板焊缝再焊上翼板焊缝,上下翼板的焊接方向相反。
4.柱的焊接顺序H 型柱节点的焊接顺序 :先焊翼板焊缝、再焊腹板焊缝,翼缘板焊接时两名焊工对称、反向焊接,如图所示:①②①①①H型柱接头焊接顺序图3.6.2焊接前的准备工作1.电焊机的选用:本工程的焊接方法为半自动CO2焊,选用半自动CO2焊机。
焊机完好,接线正确,电流表、电压全完好,摆放在设备平台上的设备排列应符合安全要求,电源线安全可靠。
2.焊丝型号GM-56和GM-58,焊丝不得受潮生锈,垫板规格为-6×40,材质为Q345,两端伸出各40mm,引、灭弧板的材质和尺寸须符合设计要求。
地下连续墙H型钢焊缝检测方案

地下连续墙H型钢焊缝检测方案焊接H型钢由两块翼缘板和一块腹板焊接而成,由于其可根据工程需要制作成各种规格尺寸,因而,焊接H型钢被广泛应用于建筑钢结构的钢柱和钢梁上。
对于焊接H型钢,当腹板厚度不大于20mm时,腹板与翼缘板可采用角焊缝连接,其焊缝质量等级为三级,但当腹板厚度大于20mm时,腹板与翼缘板宜采用部分熔透或全熔透的对接与角接组合焊缝连接,且焊缝质量等级应不低于二级。
根据根据我国施工质量验收标准GB50205-2020的规定,焊缝质量等级为一级或二级的焊缝应进行内部缺陷的超声波探伤,其缺陷评定等级相应为BII和BIII。
但是从实际实施现状来看,目前国内外对焊接H型钢焊缝质量的超声波探伤普遍仍采用常规A扫描方式,这种扫描方式存在以下缺点:根据《焊缝无损检测超声检测技术、检测等级和评定》GB11345-2013的规定,焊接H型钢焊缝质量的超声波探伤一般需要一种或两种角度探头进行扫查,而常规A扫描探头只是一种角度的扫查,因此需要检测员手动操作来完成多种角度的扫查,检测结果受人为因素影响较大,检测员的劳动强度大,检测效率低。
一种焊接H型钢焊缝质量超声相控阵自动检测系统,其特征在于:它包括与至少一个焊接H型钢互相平行放置的一导轨,桁梁借由桁梁行走装置可沿导轨的长度方向移动,桁梁的长度方向与导轨的长度方向垂直,探伤行走装置可沿桁梁的长度方向移动,探伤行走装置上安装有超声相控阵探伤仪和可全方位转动的机械臂,机械臂的夹持端安装有扫查架,扫查架上安装有有机玻璃材质的楔块和测量扫查架移动距离的编码器,楔块上设有耦合平面并开设有耦合液注入孔,耦合液注入孔贯穿耦合平面设置且耦合液注入孔内密封安装有相控阵探头,编码器和相控阵探头与超声相控阵探伤仪连接,耦合液注入孔经由楔块上安装的注入接头、抽水泵与水箱连接,桁梁行走装置、探伤行走装置、机械臂和抽水泵与控制装置连接。
它包括与至少一个焊接H型钢互相平行放置的一导轨,桁梁借由桁梁行走装置可沿导轨的长度方向移动,桁梁的长度方向与导轨的长度方向垂直,探伤行走装置可沿桁梁的长度方向移动,探伤行走装置上安装有超声相控阵探伤仪和可全方位转动的机械臂,机械臂的夹持端安装有扫查架,扫查架上安装有有机玻璃材质的楔块和测量扫查架移动距离的编码器,楔块上设有耦合平面并开设有耦合液注入孔,耦合液注入孔贯穿耦合平面设置且耦合液注入孔内密封安装有相控阵探头,编码器和相控阵探头与超声相控阵探伤仪连接,耦合液注入孔经由楔块上安装的注入接头、抽水泵与水箱连接,桁梁行走装置、探伤行走装置、机械臂和抽水泵与控制装置连接。
- 1、下载文档前请自行甄别文档内容的完整性,平台不提供额外的编辑、内容补充、找答案等附加服务。
- 2、"仅部分预览"的文档,不可在线预览部分如存在完整性等问题,可反馈申请退款(可完整预览的文档不适用该条件!)。
- 3、如文档侵犯您的权益,请联系客服反馈,我们会尽快为您处理(人工客服工作时间:9:00-18:30)。
H型钢组焊方案
一、引用标准
1、YB3301—92《焊接H型钢》
2、SHJ507—87《石油化工特殊钢结构工程施工及验收规范》
3、GBJ205—83《钢结构工程施工及验收规范》
二、材料
所有的钢板及焊接材料均应符合相应的标准,并且应有材质合格证。
三、钢板的放样、号料及切割
1、H型钢的翼板和腹板在长度方向上,放样和号料应留焊接收缩量、切割及磨平等加工余量,参考值为(—)mm/m+(2—3)mm。
翼板和腹板在宽度方向上,放样和号料应留切割及磨平或刨边等加工余量。
2、翼板和腹板的切割线与号料线的允差不大于1mm。
3.翼板和腹板均采用半自动切割机进行切割,切割根据顺序分三种方法,第一种方法:可用一台或若干台切割机在同一张钢板上同时进行切割(见图一),按一、二、三、四、、、、、、顺序切割,前一段切割完后,方可切割下一段。
第二种方法:可用一台或若干台切割机在同一张钢板上同时进行切割(见图二),按1、2、3、4、、、、、、顺序切割,每切割—2米时应留30—50mm最后切割点。
第三种方法:可用若干台切割机在同一张钢板上同时进行切割(见图三),按1、2、3、4、、、、、、顺序切割,不留最后切割点,但在长度方向上未切割边应设气焊把进行加热。
以上三种方法均可控制切割过程中侧向弯曲。
第一段 H 1 2 3 4
第二段
第三段
最后切割点
30—50mm
图一图二
注:为切割线
1 2 3 4
图三
4、切割前,应将钢板表面切割区域内的铁锈、油污等清理干净。
切割后,断口上不得有裂纹和大于的缺棱,并且应清除边缘上的熔瘤和飞溅物等。
切割截面与钢板表面不垂直
度应不大于钢板厚度的10%,且≤。
5、翼板和腹板切割后的允许偏差:
翼板宽度允许偏差:-2--+2mm。
腹板宽度允许偏差:0--2mm。
翼板和腹板切割后的侧向弯曲允许偏差≤。
四、翼板和腹板的拼接
由于现场钢板料长度为6米或8米,因此,大部分梁、柱的翼板和腹板在长度方向上要拼接,其具体要求为:
1、翼板或腹板拼接的最小板块长度》800mm,并应是轧制方向与长度方向一致。
2、翼板和腹板的允许偏差符合以下规定:
(1)、厚度的错边量Δt≤10%,且≤(见图四)。
(2)、宽度错位量Δb:翼板≤,腹板≤(见图五)。
Δ
图四厚度错边量图五宽度错位量
3、翼板或腹板拼接时,对接接头均采用X型坡口,采用手工电弧焊进行焊接,其焊接工艺参数为:焊条牌号及规格:E4303 φ、φ4mm;焊接电流:120—130A,160—170A;电弧电压:22—25V;焊接速度:10—12cm/min;电源极性:直流正接;焊接层数:4-5层。
焊缝余高0—,焊后根据组对需要将某些部位的焊缝打磨与母材平齐。
翼板或腹板拼接及检验合格后方可进行H型钢组焊。
4。
翼板或腹板拼接后,侧向弯曲的偏差符合以下规定:
板长小于等于6米时,应不大于2mm,
板长大于6米时,应不大于3mm。
五、矫正、预变形及刨边
1、翼板和腹板在长度方向矫正后允许偏差(见图六),在1米范围内,当t≤14mm时、f≤;当t>14mm时、f≤。
矫正后的钢板表面不应有明显的凹面和损伤,表面划痕深度≤。
2、翼板预变形(见图七):翼板预变形必须在胎具上进行压制,表一及表二分别列举了一部分埋弧自动焊和手工电弧焊焊接H型钢翼板预变形α值。
翼板预变形α值与焊接工艺参数要匹配,因此翼板预变形压制时,要积累经验,并对α值进行修正。
翼板预变形后,用样板进行检查,其间隙≤。
图六
3、腹板切割及矫正后,最好用刨边机将切割面直(在长度方向上)。
.
六、H型钢组对
1、翼板、腹板检查合格后方可组对,组对间隙为0,H型钢截面见图八。
2、翼板对接焊缝与腹板对接焊缝的间距≥200mm(见图九).
b ≥200
图八 H型钢截面图图九焊缝相对位置
3、牛腿、加劲板、连接孔与对接焊缝的间距应符合以下规定:
(1)、牛腿与对接焊缝的间距应大于500mm。
(2)、加劲板与对接焊缝的间距应大于100mm。
(3)、连接孔与对接焊缝的间距应大于300mm。
4、H型钢组焊前,连接表面及沿焊缝每边30—50mm范围内的铁锈、毛刺和油污等清理干净。
5、梁、梁与柱的连接焊缝边缘距注和梁本身的拼接焊缝边缘(翼板和腹板拼接焊缝)必须大于200mm。
6、H型钢采用埋弧自动焊时,组装执行以下规定:按图十所示做组装胎具,并按尺寸进行组装点焊,点焊用E4303焊条、每隔300-500mm点焊长度30—50mm,焊脚高度为4—6mm。
图十组装胎具及组装图
七、焊接
焊接H型钢的焊工、焊接材料的保管、烘烤及发放应按相应的规定执行。
H型钢焊接前应放平垫稳,防止焊接变形。
(一)、采用埋弧焊焊接方法:
1、焊接顺序:按图十一或图十二中1、
2、
3、
4、
5、
6、、、、、、、的顺序进行焊接,每一层从一端焊起、到另一端停止。
若采用断续焊时(上一道焊缝焊完后与下一道焊缝起焊时间相差4小时),按图十一顺序施焊。
若采用连续焊时,按图十二顺序施焊。
2、焊接位置:采用船形焊。
3、焊接所用胎具见图十三。
4、焊丝:H08A;焊剂:HJ431;焊接电流:550—650A;电弧电压:32—38V;焊接速度:26—32cm/min;必须采用引弧板。
…
…………图十一…………………………………………图十二…………
图十三埋弧自动焊所用胎具
(二)、采用手工电弧焊焊接方法
1、焊接顺序:按图十四“H型钢组装流程图”进行组焊,
2、H型钢焊接采用型钢互背自身整体刚性加固,并与平台刚性连接(点焊或用压紧螺丝)。
3、采用多层多道焊,但第一层用φ焊条由四名焊工从中间向两头分段对称跳焊。
以后个层用φ4mm焊条由四名焊工从中间向两头分对称连续快速施焊,焊接工艺参数见表三。
4、H型钢焊前采用点焊或压紧螺栓进行刚性固定,在打开时由两名工人从中间对称向两头磨去焊点或卸去压紧螺丝
1 1 翻转 3 3 打开
图十四 H型钢组装流程图
八、调直
组焊成型的H型钢进行外观检查,根据外形尺寸检查结果来确定调直方法。
调直方法有:局部气焊加热调直、油压机调直、千斤顶调直。
局部气焊加热调直适用于焊接变形较小H型钢,油压机调直适用于焊接变形较大H型钢。
九、焊接检查
(一)、外观检查
1、焊缝表面波纹应均匀,不得有裂纹、夹渣、焊瘤、烧穿、弧坑、气孔等缺陷,焊接区不得有飞溅物。
2、焊缝咬边要求:深度不超过,累计焊缝长度步超过该焊缝长度的10%。
3、焊接焊缝外型尺寸允许偏差:
(1)、焊缝余高0—。
(2)、焊缝凹面处0—。
(3)、焊缝对口错边量<,且≤ 2mm(t—板厚)。
(4)、贴角焊缝外型尺寸允许偏差见表四:
(二)、无损检验(Ⅱ级焊缝):
组焊H 型钢,对接和贴角焊缝采用超声波检查,检查比例:抽查焊缝长度50%(主要在两头及中间部位)。
若有疑点时,用射线复验如发现有超标缺陷,应用超声波全部检验。
超声波检验焊缝质量、应符合JB1152—81的规定。
X 射线执行GB3323—87、Ⅲ级合格。
十、H 型钢的几何尺寸检查(见图十五): 1、腹板重心线偏移(e ):
当b ≤200mm 时,e ≤b/100(mm );当b >200mm 时,e ≤2(mm )。
2、 翼板倾斜度(q ):
当b ≤200mm 时,q ≤b/100(mm );当b >200mm ,q ≤2(mm )。
3、 翼板宽度偏差Δb :±3mm 。
4、 H 型钢高度偏差Δh :Δh=±2mm 。
5、 梁、柱长度偏差Δl :梁Δl=-3—0mm 、柱Δl=±3mm 。
6、 梁、柱挠曲矢高允许偏差: (1)、梁的垂直挠曲矢高:L/1000且≤5mm 。
(2)、梁的侧向挠曲矢高:L/1000且≤3mm 。
(3)、柱的挠曲矢高:L/1000且≤5mm 。
7、梁、柱扭曲偏差:(1)、梁扭曲偏差:≤h/250(mm )(2)、柱扭曲偏差:≤5mm 。
8、梁、柱两端端面的不垂直度偏差:h/500且≤3mm 。
9、梁、柱腹板局部不平直度用1米直尺检查,不大于2mm 十一、制作好的H 型钢,按说明作好编号标记。
h
q q 图十五。