连铸裂纹
连铸坯表面裂纹形成及防止分析

浸入式水口对中,防止偏流 合理的浸入式水口设计(合适的出口直径,倾角) 合适的水口插入深度 合适的频率和振幅
(3) 结晶器振动
2 铸坯表面纵裂纹
(4) 出结晶器铸坯运行 二次冷却均匀性 (5) 调整钢水成分 钢中碳含量避开包晶区,C向下线或上线控制 钢中S<0.015% 残余元素Cu、As、Zn控制<0.1%
图2-4 拉速对纵裂纹的影响
2 铸坯表面纵裂纹
(3) 保护渣 液渣层厚度<10mm,纵裂纹增加(图2-5)。
图2-5 液渣层厚度对纵裂纹的影响
2 铸坯表面纵裂纹
(4) 结晶器液面波动 液面波动<±5mm,纵裂纹最少(图2-6);
图2-6 结晶器液面波动对纵裂纹的影响
2W (T1 T2 ) W
连铸坯表面裂纹 形成及防止
宋晔
内容
1 2 3 4 5 前言 铸坯表面纵裂纹 铸坯表面横裂纹 铸坯表面星形裂纹 结论
1.前言
连铸坯质量概念: ◆ 铸坯洁净度(夹杂物数量、类型、尺寸、 分布) ◆ 铸坯表面质量(表面裂纹、夹渣、气孔) ◆ 铸坯内部质量(内部裂纹、夹杂物,中 心疏松、缩孔、偏析) ◆ 铸坯形状缺陷(鼓肚、脱方)
2 铸坯表面纵裂纹
2.3 影响表面纵裂纹产生的因素
(1) 钢水成分
◆ [S]>0.015%,纵裂纹增加(图2-2);
◆ [C]=0.12~0.15%,纵裂纹产生严重(图2-3)
图2-2 钢中[S]与裂纹指数的关系
2 铸坯表面纵裂纹
பைடு நூலகம்
图2-3 含碳量对板坯宽面纵裂纹的影响
2 铸坯表面纵裂纹
(2) 拉速 拉速增加,纵裂纹指数增加(图2-4);
连铸坯缺陷的产生与防止措施 Microsoft Word 文档1

连铸坯裂纹的产生与防止措施连铸坯裂纹的分类 :铸坯表面裂纹包括表面纵裂纹、表面横裂纹、网状裂纹(星裂)、发裂、角部纵裂纹、角部横裂纹等;铸坯内部裂纹包括中间裂纹、角部裂纹、中心线裂纹、三角区裂纹、皮下裂纹、矫直裂纹等。
1.1 铸坯表面裂纹部纵裂纹等几种主要的缺陷形式。
铸坯表面裂纹主要有表面纵裂纹、表面横裂纹、网状裂纹、角部横裂纹、边铸坯表面裂纹是在结晶器内产生的,在二冷段得到扩展。
它会导致轧制板材表面的微细裂纹,影响最终产品的表面质量。
图1为表面裂纹示意图图 1 铸坯表面裂纹示意图1-表面纵裂纹;2-表面横裂纹;3-网状裂纹;4-角部横裂纹;5-边部纵裂纹1.1.1 表面纵裂纹连铸坯表面纵裂纹是指沿着拉坯方向在铸坯表面上发生的裂纹。
它可由工艺因素或设备因素引起。
由工艺因素引起的纵裂,大多出现在铸坯宽面的中央部位,是表面裂纹中最常见的一种裂纹缺陷。
纵裂主要是由于初生坯壳在结晶器内冷却强度不均匀,造成应力的集中,在坯壳相对较薄的地方坯壳厚度不足以承受这种应力,致使坯壳裂开而产生裂纹,并在二冷区得到扩展,形成表面纵裂纹。
图2 图3 图4为表面纵裂纹示意图图2图3 图41.影响连铸坯表面纵裂纹因素:实际生产过程中,主要有以下因素影响连铸坯表面纵裂纹的产生:1) 成品成分及钢水质量(1) 成品钢中碳含量处在亚包晶和包晶反应区时,由于初生坯壳在结晶器弯月面内激冷时收缩较大,容易造成初生坯壳厚薄不均,从而使铸坯发生纵裂纹的倾向增加。
因此,在实际生产中各连铸厂家都尽量控制其成品钢中碳含量,使其避开亚包晶和包晶反应区,从而减少铸坯纵裂纹的发生机率。
(2) 成品钢中硫、磷含量也会影响铸坯纵裂纹的产生。
钢中硫、磷含量增加时,钢的高温强度和塑性明显降低,在应力作用下就容易产生裂纹,因此,在实际生产中各连铸厂家都尽量控制其成品钢中硫、磷含量,尽量控制在0.02%以内。
(3) 钢中微合金如铌、钒等对铸坯纵裂纹的产生也有重要影响,因为微合金而产生的铸坯纵裂纹在铸坯表面上分布不规则,缺陷较短、数量较多。
连铸坯内部裂纹产生的主要原因及解决措施
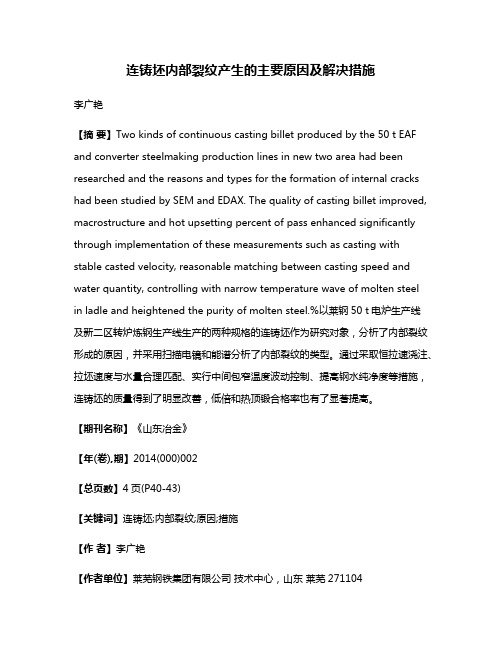
连铸坯内部裂纹产生的主要原因及解决措施李广艳【摘要】Two kinds of continuous casting billet produced by the 50 t EAF and converter steelmaking production lines in new two area had been researched and the reasons and types for the formation of internal cracks had been studied by SEM and EDAX. The quality of casting billet improved, macrostructure and hot upsetting percent of pass enhanced significantly through implementation of these measurements such as casting with stable casted velocity, reasonable matching between casting speed and water quantity, controlling with narrow temperature wave of molten steelin ladle and heightened the purity of molten steel.%以莱钢50 t电炉生产线及新二区转炉炼钢生产线生产的两种规格的连铸坯作为研究对象,分析了内部裂纹形成的原因,并采用扫描电镜和能谱分析了内部裂纹的类型。
通过采取恒拉速浇注、拉坯速度与水量合理匹配、实行中间包窄温度波动控制、提高钢水纯净度等措施,连铸坯的质量得到了明显改善,低倍和热顶锻合格率也有了显著提高。
【期刊名称】《山东冶金》【年(卷),期】2014(000)002【总页数】4页(P40-43)【关键词】连铸坯;内部裂纹;原因;措施【作者】李广艳【作者单位】莱芜钢铁集团有限公司技术中心,山东莱芜271104【正文语种】中文【中图分类】TG115.21 前言铸坯裂纹的形成是一个非常复杂的过程,是传热、传质和应力相互作用的结果。
连铸坯裂纹敏感指数公式

连铸坯裂纹敏感指数公式(原创版)目录1.引言2.连铸坯裂纹敏感指数公式的定义3.连铸坯裂纹敏感指数公式的计算方法4.连铸坯裂纹敏感指数公式的应用5.总结正文1.引言连铸坯是钢铁行业中常见的一种铸造方式,其优点在于生产效率高、成本低。
然而,由于连铸坯的铸造过程复杂,容易出现表面裂纹等质量问题。
为了有效预防和控制这些问题,研究人员提出了连铸坯裂纹敏感指数公式,该公式可以帮助钢铁企业更好地了解和控制连铸坯的裂纹产生。
2.连铸坯裂纹敏感指数公式的定义连铸坯裂纹敏感指数公式是一种用于衡量连铸坯在铸造过程中产生裂纹的倾向性的指标。
该指数根据连铸坯的物理性质、化学成分、铸造工艺等因素进行计算,可以帮助钢铁企业预测和评估连铸坯的裂纹产生风险。
3.连铸坯裂纹敏感指数公式的计算方法连铸坯裂纹敏感指数公式的计算方法较为复杂,需要考虑多个因素。
一般来说,计算过程包括以下几个步骤:(1)确定连铸坯的物理性质和化学成分:包括铸坯的厚度、宽度、长度、化学成分等;(2)分析连铸坯的铸造工艺:包括熔炼温度、浇注温度、冷却速度等;(3)结合经验和实验数据,建立连铸坯裂纹敏感指数公式:通过分析上述因素对连铸坯裂纹产生的影响,建立一个综合考虑多个因素的裂纹敏感指数公式。
4.连铸坯裂纹敏感指数公式的应用连铸坯裂纹敏感指数公式可以帮助钢铁企业在生产过程中及时发现和预防裂纹的产生,从而提高铸坯的质量和降低生产成本。
具体应用方面,钢铁企业可以采用以下方法:(1)在生产过程中,定期对连铸坯进行检测,计算裂纹敏感指数,以便及时发现潜在的裂纹问题;(2)根据裂纹敏感指数的变化趋势,调整铸造工艺,以降低裂纹产生的风险;(3)对出现裂纹的连铸坯进行分析,查找原因,并采取相应措施,以避免类似问题的再次发生。
5.总结连铸坯裂纹敏感指数公式是一种有效的预测和控制连铸坯裂纹产生的方法。
连铸坯裂纹敏感指数公式

连铸坯裂纹敏感指数公式摘要:一、连铸坯裂纹敏感指数公式简介二、公式构成与参数解释三、公式应用与分析四、实例演示五、降低连铸坯裂纹敏感指数的策略正文:连铸坯裂纹敏感指数公式是评估连铸坯在生产过程中出现裂纹倾向的一种量化方法。
通过对连铸坯的成分、工艺参数等进行分析,可以预测坯料在连铸过程中的裂纹敏感性。
本文将详细介绍连铸坯裂纹敏感指数公式,并通过实例演示其应用,最后提出降低连铸坯裂纹敏感指数的策略。
一、连铸坯裂纹敏感指数公式简介连铸坯裂纹敏感指数公式主要包括以下几个部分:1.成分参数:包括碳当量、氢当量、锰当量等,这些参数反映了连铸坯的成分特征。
2.工艺参数:包括浇注温度、结晶器温度、拉速等,这些参数影响了连铸坯的冷却速度和凝固过程。
3.应力状态:包括内应力和外应力,反映了连铸坯在成型过程中的受力状况。
二、公式构成与参数解释连铸坯裂纹敏感指数公式为:裂纹敏感指数= f(CE,HE,ME,Tc,V,σ)其中,CE、HE、ME分别为碳当量、氢当量、锰当量;Tc为浇注温度;V 为拉速;σ为应力状态。
碳当量CE:表示连铸坯的碳含量,对裂纹敏感性有重要影响。
CE值越高,连铸坯的裂纹敏感性越大。
氢当量HE:反映连铸坯中的氢含量,氢含量过高会导致连铸坯脆性增加,容易产生裂纹。
锰当量ME:影响连铸坯的强度和韧性,ME值过高会使连铸坯过于韧性,容易产生裂纹。
三、公式应用与分析通过对连铸坯裂纹敏感指数公式的计算,可以评估连铸坯在生产过程中的裂纹倾向。
当裂纹敏感指数大于一定阈值时,连铸坯存在较高的裂纹风险。
此时,需要对连铸坯的成分和工艺参数进行调整,降低裂纹敏感性。
四、实例演示以下为一个实例:某厂生产的连铸坯,碳当量CE=0.45,氢当量HE=0.02,锰当量ME=0.18,浇注温度T c=1500℃,拉速V=2m/min,应力状态σ=20MPa。
根据公式计算,裂纹敏感指数为0.78。
由于该指数大于阈值0.6,说明连铸坯存在较高的裂纹风险。
连铸坯发纹裂纹产生的原因

连铸坯发纹裂纹产生的原因连铸坯发纹裂纹是指在连铸过程中,坯料表面产生裂纹的现象。
这种现象在连铸过程中非常常见,如果没有正确的处理,会影响连铸坯的质量和后续加工工艺,甚至可能导致产量的降低。
连铸坯发纹裂纹的产生原因非常多样化,主要包括以下几个因素。
首先,连铸坯发纹裂纹的产生与坯料的化学成分有关。
在连铸过程中,如果坯料中含有不溶于钢液的硬质夹杂物,这些夹杂物会被硬质粒子剪切或滚动而产生裂纹。
此外,坯料中如果含有超过允许值的硫、磷等元素,会导致钢液的黏度增加,使连铸过程中液面波动较大,从而增加坯料表面的应力,进一步促进裂纹的发生。
其次,连铸坯发纹裂纹的产生与连铸工艺参数有关。
连铸过程中的拉速度、浇注速度、结晶器冷却剂的喷射速度等参数的过大或过小都会导致连铸坯表面产生应力,从而引发裂纹的产生。
此外,连铸过程中,如果坯料温度过低或结晶器冷却不均匀,也会导致坯料表面产生裂纹。
再次,连铸坯发纹裂纹的产生与结晶器的表面状况有关。
结晶器的表面状况会直接影响连铸坯表面的光滑度和均匀度。
如果结晶器表面存在磨损、凹凸不平等缺陷,会导致连铸坯表面产生过多的应力,从而引发裂纹的产生。
此外,连铸坯发纹裂纹的产生还与连铸辊的形状和磨损程度有关。
连铸辊的形状不合理或磨损过度会导致钢坯的厚度不均匀,在拉伸过程中产生裂纹。
在连铸工艺中,如果连铸辊的温度过高或过低,也会导致连铸坯的拉伸和表面温度不均匀,从而引发裂纹的产生。
最后,连铸坯发纹裂纹的产生还与工艺操作和设备维护有关。
操作不当会导致坯料表面的应力增加,设备维护不到位会降低连铸过程的稳定性,从而增加坯料发纹裂纹的风险。
为了减少连铸坯发纹裂纹的发生,可以采取以下措施:1.优化坯料的化学成分,减少夹杂物的含量,控制硫、磷等元素的含量。
2.合理调整连铸工艺参数,包括拉速度、浇注速度、结晶器冷却剂的喷射速度等,以减小坯料表面的应力。
3.对结晶器进行检修和维护,保持其表面的光滑度和均匀度。
连铸小方坯角部纵裂纹及角部纵裂漏钢的成因及防止措施

连铸小方坯角部纵裂纹及角部纵裂漏钢的成因及防止措
施
1.连铸小方坯角部纵裂纹的成因:
①角部罩覆不均匀或罩覆层太厚,使液体钢在连铸过程中受到热应力引起膨胀产生断裂;
②炉内温度分布不均匀;
③小方坯结构极差,钢水温度偏低,造成渣覆盖不均匀;
④小方坯温度过低,且温差大;
⑤冶炼操作不当,料柱受冷凝后,小方坯容易出现纵裂现象;
2.防止措施:
①加强实验室指导料柱的冶炼操作,使小方坯温度和温度分布均匀;
②合理控制罩覆层厚度,使其尽量均匀;
③及时缓和小方坯温度过快下降,尤其是角部;
④检验小方坯投料前后温度梯度,避免温度太大;
⑤增加添加剂,提高液体钢的流动性和结晶性;
⑥检查炉内温度分布是否均匀,及时调整炉内温度控制;
⑦加强铸坯结构的矫正,提高钢水温度及其均匀性,消除结晶缺陷。
连铸坯内部缺陷

连铸坯内部缺陷连铸坯的内部质量,主要取决与其中心致密度。
而影响连铸坯中心致密度的缺陷是各种内部裂纹、中心偏析和中心疏松,以及铸坯内部的宏观非金属夹杂物。
连铸坯的内裂、中心偏析和疏松这些内部缺陷的产生,在很大程度上和铸坯的二次冷却以及自二冷区至拉矫机的设备状态有关。
1)内部裂纹形成的原因各种应力(包括热应力、机械应力等)作用在脆弱的凝固界面上产生的裂纹成为内部裂纹。
通常认为内裂纹是在凝固的前沿发生的,大都伴有偏析的存在,因而也把内裂纹称为偏析裂纹。
还有一种说法是内裂纹是在凝固前沿发生的,其先端和凝固界面相连接,所以内裂纹也可以称为凝固界面裂纹。
除了较大的裂纹,一般内裂纹可在轧制中焊合。
连铸坯的内部裂纹是指从铸坯表面一下直至铸坯中心的各种裂纹,其中包有中间裂纹、对角线裂纹、矫直弯曲裂纹、中心裂纹、角部裂纹。
无论内裂文的类型如何,其形成过程大都经过三个阶段:1拉伸力作用到凝固界面;2造成柱状晶的晶界见开裂;3偏析元素富集的钢液填充到开裂的空隙中。
内裂发生的一般原因,是在冷却、弯曲和矫直过程中,铸坯的内部变形率超过该刚中允许的变形率。
通常在压缩比足够大的情况下,且钢的纯净度较高时,内裂纹可以在轧制中焊合,对一般用途的钢不会带来危害;但是在压缩比小,钢水纯净度较低,或者对铸坯心部质量有严格要求的铸坯,内裂就会使轧制材性能变坏并降低成材率。
2)中心裂纹铸坯中心裂纹在轧制中不能焊合,在钢板的断面上会出现严重的分层缺陷,在钢卷或薄板的表面呈中间波浪形缺陷,在轧制中还会发生断带事故,给成品材的轧制和使用带来影响A裂纹的成因分析铸坯裂纹的形成时传热、传质和应力相互作用的结果。
带液芯的高温铸坯在铸机内运行过程中,各种力的作用是产生裂纹的外因,而钢对裂纹的敏感性是产生裂纹的内因。
铸坯是否产生裂纹决定于钢高温力学性能、凝固冶金行为和铸机运行状态,板坯中心裂纹是由于凝固末端铸坯鼓肚或中心偏析、中心凝固收缩产生的。
1控制铸机的运行状态刚的高温力学性能与铸坯裂纹有直接关系,铸坯凝固过程固、液及诶按承受的应力(如热应力、鼓肚力、矫直力等)和由此产生的塑性变形超过允许的高温强度和临界应变值,则形成树枝晶间裂纹,柱状晶越发达,越有利于裂纹的扩展。
连铸坯表面纵裂纹产生原因及控制措施

左 右 1 00 mm
。
2 3 1 .
.
宽 大 纵 裂 纹 宽 度 深 度 :
丨 0 - 20m m ,
2 0 - 3 0m m ,
长达几米 严重时会贯穿 板坯而报废
,
。
22 .
表 面 纵 裂 纹 原 因 分 析
2 2 .
.1
纵 裂 纹 起 源 于 结 晶 器 的 弯 月 面 区 初 生 凝 固
0 2 -
1
1
> 2 1
钢 液 面 波 动 范 围 mm ,
图 4 液 面 波 动 对 裂 纹 指 数 的 影 响
2 .
2. 4
结 晶 器 冷 却 效 果 及 热 流 的 影 响重 要 纵 裂 纹 一 般 均 发 生 在 结 晶 器 内 部 在 结 晶 器
,
,
结 晶 器 冷 却 效 果 对 连 铸 坯 纵 裂 纹 的 影 响 非 常 内 部 先 形 成 微 裂 纹 进 入 二 冷 区 后 发 展 成 明 显 的 裂 ,
,
晶器
流
于 W M 7 1 .
M2
/
宽面 铜板平 均热 流 为
侧 面 平 均 热 流 M W M 4 6 1 .
-
1.
2 /
,
为
<z>
>
右 1
cr >
i . i
a M
議
图 5 结 晶 器 热 流对 裂 纹 指 数 的 对 应 关 系
板 表 面 纵 裂纹 发 生 率 最 小 M W 3 l .
l- 1.
/ m2 ,
坯
。
经 统 计 分 析 侧 边 铜 板 热 流 与 宽 边 铜 板 热 流 之
倒角连铸坯角部纵向裂纹形成机制及控制
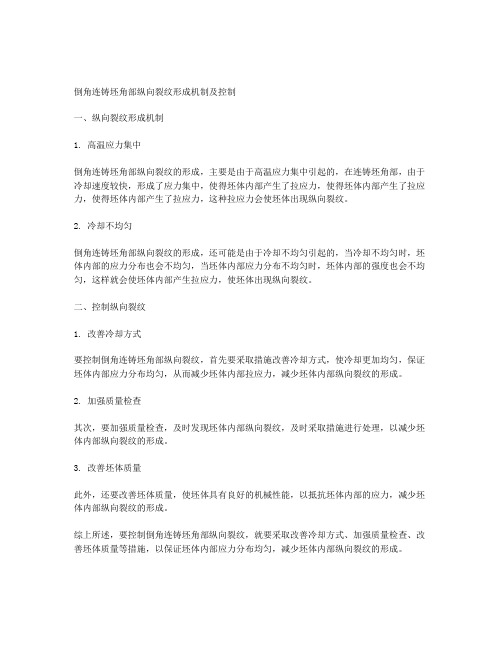
倒角连铸坯角部纵向裂纹形成机制及控制
一、纵向裂纹形成机制
1. 高温应力集中
倒角连铸坯角部纵向裂纹的形成,主要是由于高温应力集中引起的,在连铸坯角部,由于冷却速度较快,形成了应力集中,使得坯体内部产生了拉应力,使得坯体内部产生了拉应力,使得坯体内部产生了拉应力,这种拉应力会使坯体出现纵向裂纹。
2. 冷却不均匀
倒角连铸坯角部纵向裂纹的形成,还可能是由于冷却不均匀引起的,当冷却不均匀时,坯体内部的应力分布也会不均匀,当坯体内部应力分布不均匀时,坯体内部的强度也会不均匀,这样就会使坯体内部产生拉应力,使坯体出现纵向裂纹。
二、控制纵向裂纹
1. 改善冷却方式
要控制倒角连铸坯角部纵向裂纹,首先要采取措施改善冷却方式,使冷却更加均匀,保证坯体内部应力分布均匀,从而减少坯体内部拉应力,减少坯体内部纵向裂纹的形成。
2. 加强质量检查
其次,要加强质量检查,及时发现坯体内部纵向裂纹,及时采取措施进行处理,以减少坯体内部纵向裂纹的形成。
3. 改善坯体质量
此外,还要改善坯体质量,使坯体具有良好的机械性能,以抵抗坯体内部的应力,减少坯体内部纵向裂纹的形成。
综上所述,要控制倒角连铸坯角部纵向裂纹,就要采取改善冷却方式、加强质量检查、改善坯体质量等措施,以保证坯体内部应力分布均匀,减少坯体内部纵向裂纹的形成。
连铸板坯角部横裂产生的原因及应对措施

铸坯角部横裂产生的原因及应对措施板坯可以在表面上观察到纵向裂纹,在尾部观察到中线裂纹。
要了解板坯中的角裂纹及孔隙,必须用沿板坯边部进行火焰切割处理,切割出50mm宽,2〜3mm深的槽。
在检查板坯的裂纹时,在高强低合金钢(HSLA)、包晶钢、中碳钢中发现了角部横裂,但是在低碳铝镇静钢中却很少发现裂纹。
包晶钢含有Nb,因此,角裂的百分比极高。
虽然在板坯的疏松边发现了角部横裂,但板坯中的大多数裂纹出现在板坯的固定边。
几乎板坯中所有的角部横裂纹与振动痕迹方向一致。
在出厂前,必须对板坯中的角裂纹和针孔进行处理。
处理板坯中出现的裂纹将增加产品成本,降低生产能力,耽误产品出厂日期。
经过火焰切割后的板坯样品送到米塔尔研究实验室进行分析,以便确定其中角部横裂纹的发生原因。
为减少角部横裂纹,米塔尔公司LazaroCardenas(MSLC)的操作人员、维修人员、技术人员组成了一支精干的团队,以降低板坯角部横裂纹的发生。
裂纹起因当铸流表面遭受到热力应变、机械力应变或相变时,若该应变量超过了铸件材料的最大应变值,板坯就会发生横裂。
在下列条件下板坯可能产生裂纹:(1)铸流表面温度下降至低延展区以下,拉伸应变导致铸件产生裂纹。
(2)结晶器上热收缩应变引起板坯内部热断裂,产生裂纹。
(3)结晶器上或结晶器附近所施加的外力引起表面热拉裂。
产品的延展性低是出现裂纹的主要原因。
影响板坯横裂的因素还包括化学作用。
减小温差,降低震动是避免板坯裂隙发生的主要措施。
角部裂分析对板坯切削样本(削痕深度2〜3mm)进行化学成分分析的结果如表1。
在这种钢中发现了严重的角部裂纹,主要原因是该种钢的Nb、V和C含量高,特别是C对包晶钢非常敏感。
理论上讲,Nb(C,N)在1090°C开始析出,当温度下降,析出量快速增长,当温度降低到900C时主要析出物为V(C,N),温度进一步下降到800C时,晶间继续析出。
众所周知,在温度降低过程中,Nb基及V基析出物沿奥氏体晶粒边界析出。
连铸坯裂纹影响
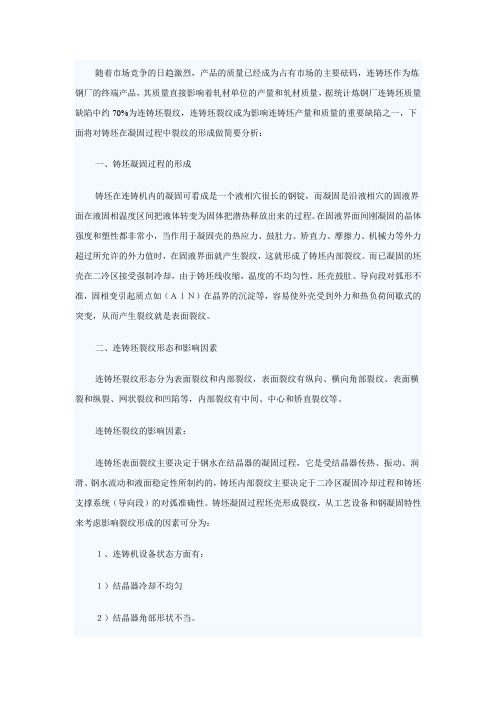
随着市场竞争的日趋激烈,产品的质量已经成为占有市场的主要砝码,连铸坯作为炼钢厂的终端产品,其质量直接影响着轧材单位的产量和轧材质量,据统计炼钢厂连铸坯质量缺陷中约70%为连铸坯裂纹,连铸坯裂纹成为影响连铸坯产量和质量的重要缺陷之一,下面将对铸坯在凝固过程中裂纹的形成做简要分析:一、铸坯凝固过程的形成铸坯在连铸机内的凝固可看成是一个液相穴很长的钢锭,而凝固是沿液相穴的固液界面在液固相温度区间把液体转变为固体把潜热释放出来的过程。
在固液界面间刚凝固的晶体强度和塑性都非常小,当作用于凝固壳的热应力、鼓肚力、矫直力、摩擦力、机械力等外力超过所允许的外力值时,在固液界面就产生裂纹,这就形成了铸坯内部裂纹。
而已凝固的坯壳在二冷区接受强制冷却,由于铸坯线收缩,温度的不均匀性,坯壳鼓肚、导向段对弧形不准,固相变引起质点如(AlN)在晶界的沉淀等,容易使外壳受到外力和热负荷间歇式的突变,从而产生裂纹就是表面裂纹。
二、连铸坯裂纹形态和影响因素连铸坯裂纹形态分为表面裂纹和内部裂纹,表面裂纹有纵向、横向角部裂纹、表面横裂和纵裂、网状裂纹和凹陷等,内部裂纹有中间、中心和矫直裂纹等。
连铸坯裂纹的影响因素:连铸坯表面裂纹主要决定于钢水在结晶器的凝固过程,它是受结晶器传热、振动、润滑、钢水流动和液面稳定性所制约的,铸坯内部裂纹主要决定于二冷区凝固冷却过程和铸坯支撑系统(导向段)的对弧准确性。
铸坯凝固过程坯壳形成裂纹,从工艺设备和钢凝固特性来考虑影响裂纹形成的因素可分为:1、连铸机设备状态方面有:1)结晶器冷却不均匀2)结晶器角部形状不当。
3)结晶器锥度不合适。
4)结晶器振动不良。
5)二冷水分布不均匀(如喷淋管变形、喷嘴堵塞等)。
6)支承辊对弧不准和变形。
2、工艺参数控制方面有:1)化学成份控制不良(如C、Mn\S)。
2)钢水过热度高。
3)结晶器液面波动太大。
4)保护渣性能不良。
5)水口扩径。
6)二次冷却水分配不良,铸坯表面温度回升过大。
连铸板坯裂纹的可能原因

连铸板坯裂纹的可能原因连铸板坯裂纹是指在连铸过程中,板坯表面或内部出现的裂纹现象。
这种裂纹严重影响了板坯的质量,降低了产品的使用价值,因此了解连铸板坯裂纹的可能原因对于解决该问题具有重要意义。
以下将分析连铸板坯裂纹的可能原因。
连铸板坯裂纹的产生与原材料的质量有关。
原材料中的夹杂物、气孔、硫化物等缺陷会导致板坯的非均匀性和应力集中,从而引发裂纹的产生。
此外,原材料的成分控制也是影响板坯质量的重要因素,过高或过低的含碳量、硫含量等都会增加板坯的脆性,易于产生裂纹。
连铸板坯裂纹的形成与连铸过程中的温度控制有关。
连铸过程中,板坯的冷却速度快,温度梯度大,容易产生应力集中,从而引发裂纹。
在连铸过程中,合理控制板坯的冷却速度和温度梯度,避免过快的冷却或温度梯度过大,能够有效减少裂纹的产生。
第三,连铸板坯裂纹的产生与连铸工艺参数的控制有关。
连铸工艺参数包括浇注速度、结晶器冷却水量、结晶器摇摆频率等。
不合理的工艺参数控制会导致板坯内部应力过大,从而引发裂纹的产生。
例如,过高的浇注速度会使板坯的温度梯度增大,易于产生裂纹;过大的结晶器冷却水量会使结晶器内部的冷却速度过快,也会导致板坯的裂纹。
连铸板坯裂纹的产生还与连铸设备的磨损和维护有关。
设备的磨损会导致连铸过程中的应力不均匀分布,从而引发裂纹。
因此,定期对连铸设备进行检修和维护,保持设备的正常运行状态,对于减少连铸板坯裂纹的产生具有重要作用。
连铸板坯裂纹的产生还与操作人员的技术水平和操作方法有关。
不规范的操作会增加板坯的应力,使其易于产生裂纹。
因此,提高操作人员的技术水平,加强对连铸操作的培训和管理,能够有效减少连铸板坯裂纹的产生。
连铸板坯裂纹的产生与多种因素有关,其中包括原材料质量、连铸过程中的温度控制、连铸工艺参数的控制、设备的磨损和维护以及操作人员的技术水平和操作方法等。
只有全面考虑这些因素,并采取相应的措施,才能有效减少连铸板坯裂纹的产生,提高产品的质量和使用价值。
连铸坯角部皮下横裂纹成因分析及控制技术

连铸坯角部皮下横裂纹成因分析及控制技术连铸坯角部皮下横裂纹是指在连铸坯的角部,表面下出现沿着壁厚方向的裂纹,给后续加工和使用带来不良影响。
其成因主要是由于连铸坯角部的凝固不均和加工应力引起的塑性变形,以及连铸坯冷却过程中内部温度差异不均等因素所导致的应力集中,最终引发了横向裂纹。
下面我们将从成因分析和控制技术两个方面来详细探讨连铸坯角部皮下横裂纹的产生和控制。
成因分析:(1)凝固不均连铸坯角部是整个坯料最后凝固的部分,由于连铸速度、温度、流动状态等因素的影响,角部的冷却过程相对于其他部位更加缓慢,导致角部凝固不均。
这种不均匀的凝固会产生不同的晶粒结构和应力分布,引起其在加工或使用过程中的应力集中,从而导致横向裂纹的产生。
(2)塑性变形在连铸坯的制造过程中,角部处于连铸机的曲折位置,通过弯曲和拉伸的变形,在坯料内部引起应力;同时,原材料的变化或连铸工艺的变化等因素也会产生影响,使得角部在制造和后续加工的过程中发生塑性变形。
虽然这种塑性变形可能在加工中得到修复,但也会在其之后的冷却过程中因应力集中而导致横向裂纹的产生。
(3)温度梯度连铸坯在冷却过程中,由于内部温度差异不均,在坯料内部产生了较大的应力集中。
角部与其他部位相比,由于特殊的位置和几何形状,冷却速度更慢,温度梯度更大,因而在冷却过程中容易引发横向裂纹,特别是在角部最薄的部位。
控制技术:(1)冷却方式连铸坯制造过程中,冷却方式的选择对坯料的质量产生着极大的影响。
在钢坯角部应采取有针对性的冷却方式,例如采用喷水冷却,在整个冷却过程中,保持冷却速度的均匀性,避免角部冷却不均导致的坯料内部温度差异和应力集中。
(2)钢质控制钢坯的铸造是一个复杂的过程,不仅需要控制好铸造温度、连铸速度等因素,还需要控制钢水中的气体含量、非金属夹杂物含量等,以确保将钢坯制造出高质量、低损耗的产品。
(3)加工工艺经过精细的加工,可以在大程度上修复连铸坯中存在的缺陷,对控制连铸坯角部皮下横裂纹能起到至关重要的作用。
连铸坯表面裂纹形成及防止

1.前言
铸坯裂纹是影响连铸机产量和铸坯 质量的主要缺陷。据统计铸坯各类缺 陷中的50%为裂纹。铸坯出现裂纹, 重者会导致漏钢和废品,轻者需进行 精整。
2 铸坯表面纵裂纹
2.1 板坯表面纵裂纹特征 表面纵裂纹可能发生在板坯宽面中心区域或宽面到
棱边的任一位置产生。图2-1为板坯宽面中心区域的 纵 裂 纹 和 纵 裂 纹 的 显 微 形 貌 。 以 250×1200mm (C=0.08%)板坯为例: 细小纵裂纹:宽度1-2mm,深度3-4mm,长100mm左
5.结论
(1)连铸坯产生裂纹主要决定于: 钢成分对裂纹敏感性、 浇注工艺条件、连铸机设备状况。
(2)带液芯连铸坯在连铸机内运行过程中受外力作用是 坯壳产生裂纹的外因,钢的高温力学行为是产生裂纹 的内因,而设备、工艺因素是产生裂纹的条件。
(3)根据所浇钢种,对连铸机设备的调整应符合钢凝固收 缩规律,使其坯壳不受变形为原则,对工艺参数的优化, 使其得到合理的铸坯凝固结构。这样使连铸坯不产 生裂纹或控制裂纹不足以造成废品的所允许的范围 内。
图3-4 矫直温度与横裂纹关系
3 铸坯表面横裂纹
3.4 防止横裂纹措施
(1) 采用高频率,小振幅结晶器振动 为防止横裂纹,就要减浅振痕,则必须降低,要
降低,则必须采用高频率 (100~400min-1),小振幅 (±5mm)的结晶器振动机构。 (2) 合适的二次冷却水量
根据钢种不同,二冷配水量分布应使铸坯表面 温度分布均匀,应尽量减少铸坯表面和边部温度差。 采用动态二冷配水模型。
匀性强,振痕深,表面易产生凹陷 或横裂纹;生产实践表明,C= 0.15~0.18%或0.15~0.20%时, 振痕浅了,铸坯边部横裂减少; 降低钢中[N],防止氮化物沉淀; (2) 结晶器振动特点 振痕深度增加,横裂纹增加(图31); 振动频率f增加,振痕变浅,横裂纹 减少(图3-2);
连铸板坯裂纹的可能原因

连铸板坯裂纹的可能原因连铸板坯裂纹是指在连铸过程中板坯表面或内部出现的裂纹现象。
连铸板坯是制造板材的重要中间产品,其质量直接关系到最终产品的质量。
因此,了解连铸板坯裂纹的可能原因对于提高板材质量具有重要意义。
连铸板坯裂纹的可能原因主要包括以下几个方面:1. 温度控制不当:温度是连铸过程中最重要的控制参数之一。
如果连铸板坯的冷却速度过快或过慢,都会导致板坯表面或内部的温度梯度过大,从而引起裂纹的产生。
此外,连铸机的冷却水温度和流量的不稳定也会对板坯的温度分布产生影响,进而导致裂纹的形成。
2. 铸造过程中的应力:连铸板坯在冷却过程中由于温度变化而产生应力,如果应力超过了材料的承受能力,就会引起裂纹。
铸造过程中的应力主要包括热应力、冷却应力和收缩应力。
热应力是由于连铸板坯的非均匀冷却引起的,冷却应力是由于冷却水的不均匀冷却引起的,而收缩应力是由于连铸板坯的收缩引起的。
3. 材料质量问题:连铸板坯的质量直接关系到裂纹的产生。
如果原料中存在夹杂物、气孔或其他缺陷,都会在连铸过程中发展为裂纹。
此外,连铸板坯的化学成分和物理性能也会对裂纹的形成起到重要影响。
4. 连铸工艺参数调整不当:连铸过程中的各项工艺参数对于连铸板坯的质量具有重要影响。
如果连铸机的浇注速度、结晶器的冷却强度、结晶器的振动频率等参数调整不当,都会导致连铸板坯出现裂纹。
为了避免连铸板坯裂纹的产生,可以采取以下措施:1. 合理控制连铸过程中的温度,保证板坯的均匀冷却。
2. 优化连铸工艺参数,确保连铸板坯的质量稳定。
3. 加强原料检验,确保原料的质量达标。
4. 定期检查和维护连铸机设备,确保设备的正常运行。
5. 引入先进的控制技术,如自动化控制系统和智能监测设备,提高连铸过程的稳定性和可控性。
连铸板坯裂纹的产生是由多种因素共同作用的结果。
通过合理控制连铸过程中的温度、调整工艺参数、优化原料质量以及加强设备维护,可以有效地避免连铸板坯裂纹的产生,提高板材的质量。
连铸板坯三角区裂纹的成因及对策
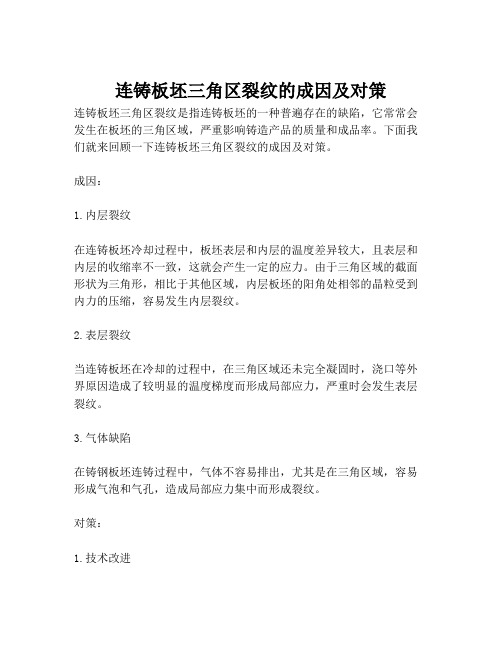
连铸板坯三角区裂纹的成因及对策连铸板坯三角区裂纹是指连铸板坯的一种普遍存在的缺陷,它常常会发生在板坯的三角区域,严重影响铸造产品的质量和成品率。
下面我们就来回顾一下连铸板坯三角区裂纹的成因及对策。
成因:1.内层裂纹在连铸板坯冷却过程中,板坯表层和内层的温度差异较大,且表层和内层的收缩率不一致,这就会产生一定的应力。
由于三角区域的截面形状为三角形,相比于其他区域,内层板坯的阳角处相邻的晶粒受到内力的压缩,容易发生内层裂纹。
2.表层裂纹当连铸板坯在冷却的过程中,在三角区域还未完全凝固时,浇口等外界原因造成了较明显的温度梯度而形成局部应力,严重时会发生表层裂纹。
3.气体缺陷在铸钢板坯连铸过程中,气体不容易排出,尤其是在三角区域,容易形成气泡和气孔,造成局部应力集中而形成裂纹。
对策:1.技术改进对于连铸板坯三角区裂纹的发生,可以先从技术的角度入手,采取改进措施,降低板坯的质量,减少三角区裂纹的发生。
例如:优化冷却过程,改善铸坯结构,以及适当的添加合金等。
2.材料改进连铸板坯三角区裂纹的发生与材料有一定的关系,因此在材料方面也可以采取一些措施,降低三角区裂纹的发生率。
例如,使用具有更好强度和韧性的材料,加入细小的晶粒改进剂等。
3.操作规范操作规范和操作技能的提高也是降低连铸板坯三角区裂纹发生率的关键。
对于操作者,需要按照正确的操作流程进行操作,严格掌握生产技术规范,避免因操作失误而导致的铸造缺陷。
总结:综上所述,连铸板坯三角区裂纹是铸造中一个比较复杂的问题,其造成的缺陷不仅影响产品质量,也影响生产效率。
因此,我们需要重视连铸板坯三角区裂纹缺陷的控制,采取一系列的改善措施,从技术,材料和操作规范等角度去降低三角区裂纹的发生率。
连铸板坯三角区裂纹的成因及对策

连铸板坯三角区裂纹的成因及对策
近年来,在钢铁行业的生产过程中,出现了连铸板坯三角区裂纹的问题。
这些裂纹的出现严重影响了板坯的质量和生产效率。
本文将探讨连铸板坯三角区裂纹的成因及对策。
首先,连铸板坯三角区裂纹的成因主要有两个方面。
一方面是原材料质量问题,如钢坯表面缺陷、内部夹杂等会导致板坯中出现裂纹;另一方面是生产工艺问题,如连铸过程中结晶器气孔、结晶器内表面涂层失效等也会导致板坯中出现裂纹。
针对连铸板坯三角区裂纹问题,可以采取以下对策。
首先,要严格控制原材料质量,对于有缺陷的钢坯要进行筛选和处理,以避免其对板坯质量的影响。
其次,要优化生产工艺,加强对连铸过程中的关键环节进行监测和控制,及时发现和解决问题。
同时,要加强设备维护和保养,确保设备运行稳定,减少其对板坯质量的影响。
综上所述,连铸板坯三角区裂纹的成因主要包括原材料质量问题和生产工艺问题,针对这些问题,可以采取严格控制原材料质量、优化生产工艺以及加强设备维护和保养等对策,以提高板坯质量和生产效率。
- 1 -。
第六讲_连_铸_坯_裂_纹_控_制

连 铸 坯 裂 纹 控 制
连 铸 坯 质 量 控 制
在连铸生产实践中,裂纹是铸坯的一种主要缺陷,据统计,铸坯各类 缺陷中有50 %为裂纹[1 ] 。铸坯中存在裂纹,严重的会影响到铸坯 的后续加工以及最终产品的质量,甚至造成废品。浇注过程中,裂纹 还会造成拉漏事故发生,影响连铸机的正常生产,造成钢水浪费。裂 纹还会使铸坯热送技术和连铸连轧技术的采用受到影响。因此,防 止铸坯裂纹产生,对稳定连铸生产、提高产品质量具有重要意义。 按照连铸坯裂纹产生的位置和形态可分为表面裂纹和内部裂纹。 绝大多数内裂纹都是在凝固过程中形成的,故有时也称为“凝固裂 纹”[2 ] 。从概念上讲,铸坯中从皮下一直到中心部位出现的裂纹 都可以称为内裂纹,因此,内裂纹不仅包括凝固裂纹,也应该包括那 些在凝固温度以下由于A1N、Nb (C ,N)等质点在奥氏体晶界析出 引起晶界脆化、在外力作用下形成的裂纹,只是后者所占比例很小 [3 ] 。
连 铸 坯 质 量 控 制
(3) 辊子不对中应变:
300s m m l2
m =0.2~0.4%,由模型计算的结果如图2-7。 m =0.5~1.5mm,
图2-7 辊子不对中应变沿铸流方向的分布
连 铸 坯 质 量 控 制
(4) 热应力应变: t 0.1~0.2%
总应变
如应变可以线性叠加,那么凝固前沿发生的总应变
连 铸 坯 质 量 控 制
1 连铸坯裂纹概论
1.1 连铸坯裂纹类型
(1) 连铸坯表面裂纹(图1-1)
◆ 纵裂纹 ◆ 横裂纹 ◆ 网状裂纹 ◆ 皮下针孔
图1-1 铸坯表面缺陷示意图 1-表面纵裂纹;2-表面横裂纹;3-网状裂纹; 4-角部横裂纹;5-边部纵裂纹;6-表面夹渣; 7-皮下针孔;8深振痕
连铸坯表面裂纹形成及防止汇总

图2-4 拉速对纵Biblioteka 纹的影响2 铸坯表面纵裂纹
(3) 保护渣 液渣层厚度<10mm,纵裂纹增加(图2-5)。
图2-5 液渣层厚度对纵裂纹的影响
2 铸坯表面纵裂纹
(4) 结晶器液面波动 液面波动<±5mm,纵裂纹最少(图2-6);
图2-6 结晶器液面波动对纵裂纹的影响
2W (T1 T2 ) W
3 铸坯表面横裂纹
3.2横裂纹产生原因 (1) 横裂纹产生于结晶器初始坯壳形成振痕的 波谷处,振痕越深,则横裂纹越严重,在波谷 处,由于: -奥氏体晶界析出沉淀物,产生晶间断裂 -沿振痕波谷S、P元素呈正偏析,降低了钢高 温强度。 这样,振痕波谷处,奥氏体晶界脆性增大,为裂 纹产生提供了条件。
这些力的的综合作用在坯壳上,当张应力超过钢的高温允许的 强度,则就在坯壳薄弱处萌生裂纹,出结晶器后在二冷区继续扩展。
2 铸坯表面纵裂纹
在结晶器弯月面区坯壳厚度生长不均匀的主要原 因是: (1)包晶相变(L+δ→γ)收缩特征,气隙过早形成, 导致坯壳生长不均匀。 (2)工艺因素影响结晶的坯壳生长不均匀。 显然要防止产生纵裂纹,就是要使结晶的弯月面初 生坯壳厚度均匀,避免坯壳产生应力梯度。要做到这点, 对于包晶相变的收缩特征是由Fe-C相图决定的,人为 无法改变,而重要的是准确控制影响结晶的初生坯壳生 长的工艺因素,来防止产生纵裂纹。
图3-1 振痕深度与横裂纹产生几率的关系
3 铸坯表面横裂纹
图3-2 振动频率与振痕深度的关系
3 铸坯表面横裂纹
图3-3 结晶器液面波动与角裂发生率的关系
(3) 结晶器液面波动 结晶器液面波动增加,横裂纹加重(图3-3)。
3 铸坯表面横裂纹
- 1、下载文档前请自行甄别文档内容的完整性,平台不提供额外的编辑、内容补充、找答案等附加服务。
- 2、"仅部分预览"的文档,不可在线预览部分如存在完整性等问题,可反馈申请退款(可完整预览的文档不适用该条件!)。
- 3、如文档侵犯您的权益,请联系客服反馈,我们会尽快为您处理(人工客服工作时间:9:00-18:30)。
f'F : U ^
弯曲是铸 坯沿长度 方向不平 直。 mK6y7t
【原因分 析】 #~Q 0s) Ze
冷却不均 匀;摆放 不当。 【鉴别与 判定】 DvGtO ) 5._
用一米直 尺测量弦 高,称每 米弯曲度 。如超出 标准规 定,做改 尺或判废 处理。用 量具测量 铸坯全长 的弦高, 称总弯曲 度。铸坯 总弯曲度 如超出标 准规定, 做改尺或 判废处理 。 9r!%PjNv E
角部纵裂 是板坯靠 近角部处 有沿浇铸 方向的连 续或断续 的裂纹。 S8^W )X gC;
【原因分 析】 H"6Sj<=
窄面支撑 不当;结 晶器窄面 锥度不合 适;结晶 器宽面与 窄面冷却 强度比值 不合适等 。 【鉴 别与判定 】 @;!s"! ~ sv
用肉眼检 查,对裂 纹处必须 处理。如 裂纹较 浅,进行 火焰清 理,如裂 纹深度超 过标准规 定,则做 改尺或报 废处理。 CA VqjT7
【鉴别 与判定】 `@ .
用肉眼检 查,如在 铸坯表面 或横截面 发现气孔 或气泡, 必需处理 。 q:2Vw`g '
. 1F(mLd
凹陷 (Dishing) 5 :[<pY! s#
="%nW3 e@
【定义与 特征】 'EF\=o)^ Y
凹陷是铸 坯表面向 内的凹入 。 &= bWX NU .
【原因分 析】 f5 ) 4 H
? tOzhr v
表面纵裂 (Surface lengthwis e crack) nt4 > 9 ;
,]+ 6kf5
【定义与 特征】 5( , WN
表面纵裂 是在板坯 表面沿浇 铸方向的 裂纹。
w># ~_x
,`
【原因分 析】
h ><; T
Ap 保护渣熔 化不良、 渣液层过 厚或过薄 导致渣膜 厚薄不 均,使局 部凝固壳 过薄;结 晶器铜板 水缝阻 塞;结晶 器液面波 动;浇铸 过程中保 护渣恶 化;结晶 器振动台 偏振;二 冷过强, 能进一步 扩展纵 裂;水口 与结晶器 厚度方向 不对中; 硫、磷含 量过高时 纵裂倾向
2 |l m'H f
气孔 (Blowhol es) pd2Lc $O@
【定义与 特征】 v[4A_ WjT
气孔是在 铸坯表面 肉眼可见 的孔洞。 细小而密 集的气 孔,也叫 针孔 。 " o. V`Bj
【原因分 析】 5cLq6[u O
钢水脱氧 不完全; 吹氩气 时,氩气 泡残留在 钢中;保 护渣潮 湿;中间 包烘烤时 间不足, 潮湿等。
结晶器的 锥度过 大;保护 渣不合 适;结晶 器宽面与 窄面冷却 强度比值 不合适等 。 【鉴 别与判定 】: ^9 sy
用量具测 量凹陷 量,如超 出标准规 定,必须 处理。 P
bR6 >'
Z<7FF}i
接痕 (Seam) lZ yxJDZ A
?QzA;8 H 【定义与 特征】 4] \ f}
接痕是在 铸坯表面 呈现横向 不连续 性,有明 显的不完 全焊合的 痕迹。 Z1V%pg >]*
用肉眼检 查,对裂 纹处必须 处理。如 裂纹较 浅,进行 火焰清 理,如裂 纹深度超 过标准规 定,则做 改尺或报 废处理。 ~ jM=f$
表面横裂 (Surface transvers e cracks)
Po c m.
,]>Eg6B, u 【定义与 特征】 ;]| Z8#s
表面横裂 是在铸坯 表面横向 产生的裂 纹,一般 发生在振 痕的波谷 处。 R}* e%E G/
7sECbb JT
【定义与 特征】 Wr hC q6
三角区裂 纹是铸坯 酸蚀试面 或硫印图 上两端的 三角区呈 现的放射 状裂纹或 硫偏析线 。 5T, Dox o 三角区: 在板坯横 截面上, 以窄边为 底,两底 角为45℃ 的等腰三 角形范围 内。
【原因 分析】 .J' 8 d"+ 由于二次 冷却不 均,在应 力作用下 使三角区 内的柱状 晶开裂而 形成。 【鉴别与 判定】 P 9Hv) {z
【原因分 析】 LF y 5t X#
切割时, 高温加热 形成熔渣 或部分金 属被熔化 。 【鉴 别与判定 】 '5wa"/ ?w
用肉眼检 查,如超 出标准, 可做改尺 处理;毛 刺和熔渣 要进行清 理。 qg rRH
'
SQ5S v YH
镰刀弯 (Camber ) ]]@jvU_? kS
4XK*sR 0-`
在列举一 些铸坯常 见的外观 缺陷特征 和原因 8, ^UQ5 x
鼓肚 (Protube rance) hp}8 3 .oA $ y }Tb m "&F/'';0}E
【定义与 特征】 7 lu;lAA P
鼓肚是由 于受到钢 水静压力 的作用而 使铸坯表 面鼓胀成 凸面。 St<\q C
【原因分 析】 ><HXd+sd
【定义与 特征】 IN Q0h
`T
中间裂纹 是在铸坯 横截面 上,距表 面10~ 15mm以 下至中心 线之间的 线状或曲 线状裂纹 。 u(ep$>[F
#_
【原因分 析】 xFZ A1 8
主要是由 于喷嘴阻 塞,二次 冷却区冷 却不均 匀,温度 回升大; 支撑辊不 对中;硫 含量偏 高;中、 高碳钢; 拉速高; 矫直时, 变形过大 等都易导 致中间裂 纹。 【鉴别与 判定】 ;k6>*wFl|
【鉴别 用肉眼检 查,对裂 纹处必须 处理。如 裂纹较 浅,进行 火焰清 理,如裂 纹深度超 过标准规 定,则做 改尺或报 废处理。 M[Lj N
zcnp?
%
振痕 (Whip mark)
p}_n :a
L 8 sHG $[
【定义与 特征】 9un* 1%
振痕是在 铸坯表面 周期性的 沿整个周 边的横纹 状的痕迹 。
由于支撑 辊开口度 过大,凝 固末期, 板坯鼓 肚,钢水 补缩中 断;二冷 冷却不 均,个别 柱状晶生 长过快, 产生搭桥 现象,造 成钢水补 缩中断。
【鉴别 与判定】 uLV@D r
用肉眼检 查,如有 可见裂纹 则不能送 到下道工 序轧制。 5p6Kq=j hb
|H e,v /r
三角区裂 纹 (Cracks in the triangle area) $M \|zU Qu.
用肉眼检 查,如超 出标准, 可改尺或 降级使 用,如裂 纹严重, 应判废。 8 [i# x|`g
\ dj&4u 3
毛刺和熔 渣(Flux inclusion )e #YW Mo(
"UVqkw ,vt 【定义与 特征】 [0CoQ5: d?&
毛刺和切 割熔渣是 板坯切割 端面的上 、下表面 粘着的切 割熔渣和 被熔化的 金属,上 表面的称 为切割熔 渣,下表 面的称为 毛刺。 8 }Rwf? B
0.15% 时,铸坯
用肉眼检 查,对裂 纹处必须 处理。如 裂纹较 浅,进行 火焰清 理,如裂 纹深度超 过标准规 定,则做 改尺或报 废处理。
w
R1M_&-
s
kpcIU7 | e
角部纵裂 (Angle area lenthwis e cracks) J6 Cw1 Pi
6I"Q 9 (
【定义与 特征】 V 0 7e2 9w
【原因分 析】 o X A*K.X <
结晶器锥 度太大; 结晶器宽 面与窄面 冷却强度 比值不合 适;支撑 辊对弧不 准;中、 高碳钢在 没有缓冷 的情况 下,表面 因产生收 缩应力也 会导致严 重的横裂 纹;结晶 器液面波 动;钢中 铌、铝与 氮形成氮 化物,角 部裂纹敏 感;碳含 量在 0.10%~
!
用肉眼检 查,用低 倍检验判 断。 hQ!sl O
J) O1)f R 中心线裂 纹 (Centreli ne cracks)
Do@ :|n
$~UQ K v> 【定义与 特征】 5 ru & I n&
中心线裂 纹是在三 角区外的 板坯厚度 中心线上 出现的裂 纹。 1 h(oty2p
【原因分 析】 ( fON\ )l
二冷喷嘴 阻塞,水 压不足或 偏离;钢 水过热度 过高;拉 速过快, 冷却强度 不足;支 撑辊辊缝 过大。 【鉴别与 判定】 j^M@ 0o
用量具测 量鼓肚 量,如超 出标准要 求,做判 废处理。 [gDvAtTபைடு நூலகம்Z5
弯曲 (Bending ) z`CI gSR
kl Kt^h-
h fNBWN
【定义与 特征】 bbnA m Z
【原因分 析】 ujF*'*@\
结晶器的 注流突然 停流,或 瞬间停止 拉坯后, 又重新浇 铸造成的 。 【鉴 别与判定 】J N5<=x5r
用肉眼检 查,这种 缺陷非常 明显,必 须改尺或 判废。 C %l!"s^
],r tSUO
中间裂纹 (Medial cracks) h> K~<BAz'
7% aaq Q1T
L>V Z -j
【原因分 析】 jSNU U.l ur
结晶器保 护渣粘度 低;结晶 器振动的 负滑脱时 间长。 【鉴别与 判定】 _ EMq"
\ND
用肉眼检 查,连铸 板坯均有 振痕,但 深度随钢 种、生产 操作的变 化而不 同,如超 出标准允 许的深 度,要进 行火焰清 理。 G&8 )5 d[
TU&gj 1
角部横裂 (Angle area transvers e cracks) FhVi|V a
:' ' ^a 【定义与 特征】 a=>PG r iL