叶片型面典型参数一致性分析研究
长宽法测定作物叶面积的校正系数研究
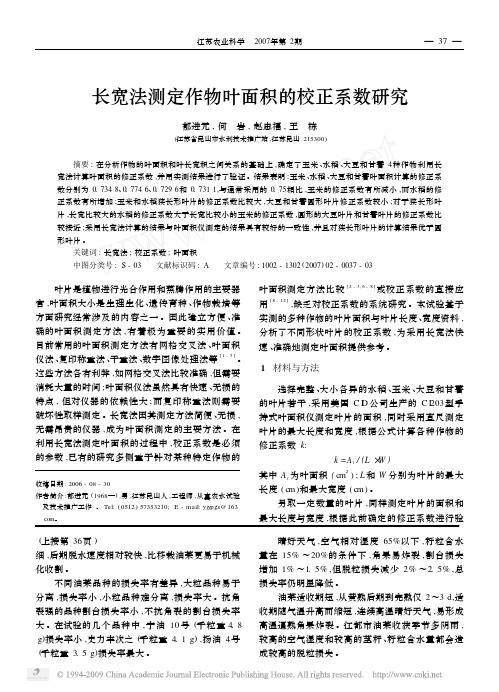
[ 4 ]杨劲峰 ,陈 清 ,韩晓日 ,等. 数字图像处理技术在蔬菜叶面积测 量中的应用 [ J ]. 农业工程学 , 2002, 18 (4) : 155 - 158.
作物
玉米 水稻 大豆 甘薯
表 2 计算结果与实测结果的误差统计
相对误差绝对值 ( % )
平均
最大
最小
合格率 (%)
4. 13
11. 40
0. 04
95
4. 08
22. 64
0. 03
94
5. 21
17. 43
0. 21
93
5. 96
14. 55
0. 33
84
F值
303. 0 6 281. 9 1 507. 1 354. 5
收稿日期 : 2006 - 08 - 30 作者简介 :郁进元 (1968—) ,男 ,江苏昆山人 ,工程师 ,从事农水试验
及技术推广工作 。 Tel: ( 0512 ) 57353210; E - mail: yjypgs@ 163. com。
叶面积测定方法比较 [ 2 - 3, 6 - 8 ]或校正系数的直接应 用 [ 8 - 12 ] ,缺乏对校正系数的系统研究 。本试验基于 实测的多种作物的叶片面积与叶片长度 、宽度资料 , 分析了不同形状叶片的校正系数 ,为采用长宽法快 速 、准确地测定叶面积提供参考 。
[ 7 ]李雁鸣 ,胡冰华 ,张建平 ,等. 魔芋 (Am orphophallus rivieri D u rieu) 叶面积测定方法的初步研究 [ J ]. 河北农业大学学报 , 2000, 23 ( 4) : 23 - 25.
风力机叶片翼型的研究现状与趋势

风力机叶片翼型的研究现状与趋势风能作为一种可再生能源,在煤、石油和天然气等非可再生能源日益耗竭以及全世界对可持续发展要求的情况下,正越来越来受到世界各国的关注。
风电技术复杂,风力发电机组的叶片作为捕获风能最直接的部件,其价值占到整机价值的25%左右。
叶片的直径、弦长、各截面翼型选择、纵向的扭角分布等都会影响到叶片的气动性能,进而影响风轮的功率输出。
而叶片的结构、材料和工艺直接影响风机的强度、疲劳、震动、载荷及成本等。
因此,设计良好的叶片,翼型应该具有较佳的空气动力学性能,良好的结构和制造工艺,这样风力发电机组才能稳定运行并具有高的功率输出[1-3]。
目前,因为风力发电机组向着更高的额定功率发展,最大的叶轮直径已经达到125m,风电机组对叶片的气动性能、结构和工艺提出了更高的要求。
一、国外发展与研究状况风机翼型的设计分析理论从根本上决定风机整体的功率特性和载荷特性。
因为其重要性,翼型设计分析理论的研究一直是世界各国专家和学者的科研热情所在。
风机翼型的发展来源于低速应用的翼型,如滑翔机翼型。
早期的低速翼型运用在风机上有WortmannFX-77翼型和NASALS翼型。
在20世纪80年代,因为美国国家可再生能源实验室(NREL)的Tangler和Somers发展了许多的NREL翼型,对促进风机翼型的发展做出了很大贡献。
同时,他们也提出了翼型的反设计方法。
对NREL系列翼型的相关阐述可以在NREL一系列报告中找到。
后续的瑞典的Bj·rkA发展了FFA-W系列的翼型,荷兰代尔夫特理工大学的TimmerWA和vanRooij也对风机翼型的发展做出了贡献,发展了DU系列的翼型。
20世纪90年代中期,丹麦Risφ风能重点实验室开始研制新的风机翼型,到目前为止已经发展出了Risφ-A1,Risφ-P和Risφ-B1三种翼型系列。
翼型研究包括两方面,翼型分析和翼型优化设计。
翼型分析是研究翼型气动性能,是翼型优化设计的基础。
风力发电机组预防叶片扫塔监控技术研究
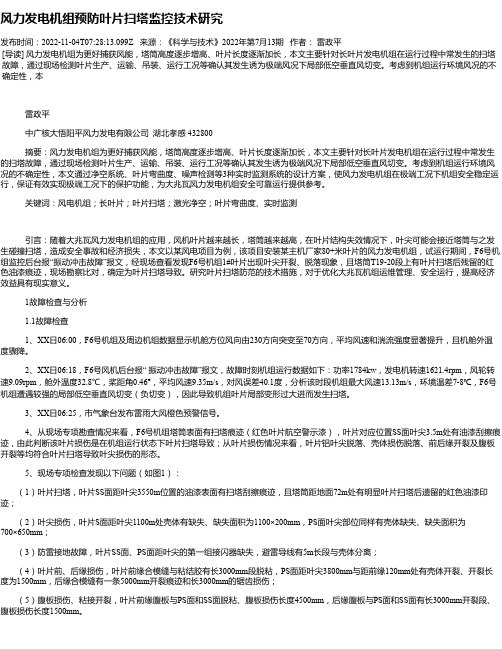
风力发电机组预防叶片扫塔监控技术研究发布时间:2022-11-04T07:28:13.099Z 来源:《科学与技术》2022年第7月13期作者:雷政平[导读] 风力发电机组为更好捕获风能,塔筒高度逐步增高、叶片长度逐渐加长,本文主要针对长叶片发电机组在运行过程中常发生的扫塔故障,通过现场检测叶片生产、运输、吊装、运行工况等确认其发生诱为极端风况下局部低空垂直风切变。
考虑到机组运行环境风况的不确定性,本雷政平中广核大悟阳平风力发电有限公司湖北孝感 432800摘要:风力发电机组为更好捕获风能,塔筒高度逐步增高、叶片长度逐渐加长,本文主要针对长叶片发电机组在运行过程中常发生的扫塔故障,通过现场检测叶片生产、运输、吊装、运行工况等确认其发生诱为极端风况下局部低空垂直风切变。
考虑到机组运行环境风况的不确定性,本文通过净空系统、叶片弯曲度、噪声检测等3种实时监测系统的设计方案,使风力发电机组在极端工况下机组安全稳定运行,保证有效实现极端工况下的保护功能,为大兆瓦风力发电机组安全可靠运行提供参考。
关键词:风电机组;长叶片;叶片扫塔;激光净空;叶片弯曲度、实时监测引言:随着大兆瓦风力发电机组的应用,风机叶片越来越长,塔筒越来越高,在叶片结构失效情况下,叶尖可能会接近塔筒与之发生碰撞扫塔,造成安全事故和经济损失,本文以某风电项目为例,该项目安装某主机厂家80+米叶片的风力发电机组,试运行期间,F6号机组监控后台报“振动冲击故障”报文,经现场查看发现F6号机组1#叶片出现叶尖开裂、脱落现象,且塔筒T19-20段上有叶片扫塔后残留的红色油漆痕迹,现场勘察比对,确定为叶片扫塔导致。
研究叶片扫塔防范的技术措施,对于优化大兆瓦机组运维管理、安全运行,提高经济效益具有现实意义。
1故障检查与分析1.1故障检查1、XX日06:00,F6号机组及周边机组数据显示机舱方位风向由230方向突变至70方向,平均风速和湍流强度显著提升,且机舱外温度骤降。
静子叶片叶身型面数控加工技术研究
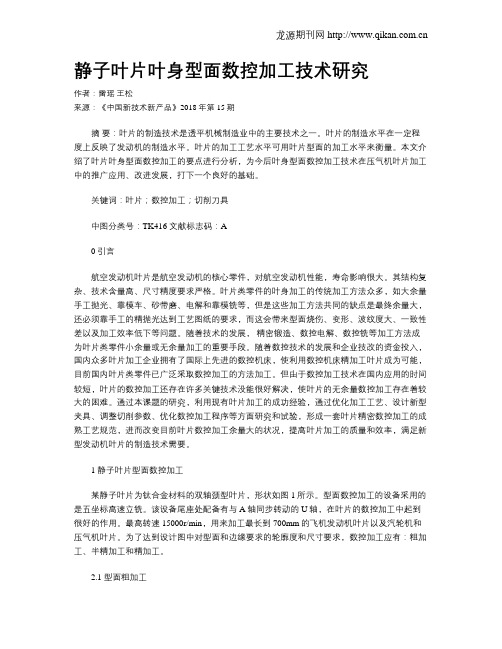
静子叶片叶身型面数控加工技术研究作者:雷瑶王松来源:《中国新技术新产品》2018年第15期摘要:叶片的制造技术是透平机械制造业中的主要技术之一。
叶片的制造水平在一定程度上反映了发动机的制造水平。
叶片的加工工艺水平可用叶片型面的加工水平来衡量。
本文介绍了叶片叶身型面数控加工的要点进行分析,为今后叶身型面数控加工技术在压气机叶片加工中的推广应用、改进发展,打下一个良好的基础。
关键词:叶片;数控加工;切削刀具中图分类号:TK416 文献标志码:A0 引言航空发动机叶片是航空发动机的核心零件,对航空发动机性能,寿命影响很大。
其结构复杂、技术含量高、尺寸精度要求严格。
叶片类零件的叶身加工的传统加工方法众多,如大余量手工抛光、靠模车、砂带磨、电解和靠模铣等,但是这些加工方法共同的缺点是最终余量大,还必须靠手工的精抛光达到工艺图纸的要求,而这会带来型面烧伤、变形、波纹度大、一致性差以及加工效率低下等问题。
随着技术的发展,精密锻造、数控电解、数控铣等加工方法成为叶片类零件小余量或无余量加工的重要手段。
随着数控技术的发展和企业技改的资金投入,国内众多叶片加工企业拥有了国际上先进的数控机床,使利用数控机床精加工叶片成为可能,目前国内叶片类零件已广泛采取数控加工的方法加工。
但由于数控加工技术在国内应用的时间较短,叶片的数控加工还存在许多关键技术没能很好解决,使叶片的无余量数控加工存在着较大的困难。
通过本课题的研究,利用现有叶片加工的成功经验,通过优化加工工艺、设计新型夹具、调整切削参数、优化数控加工程序等方面研究和试验,形成一套叶片精密数控加工的成熟工艺规范,进而改变目前叶片数控加工余量大的状况,提高叶片加工的质量和效率,满足新型发动机叶片的制造技术需要。
1 静子叶片型面数控加工某静子叶片为钛合金材料的双轴颈型叶片,形状如图1所示。
型面数控加工的设备采用的是五坐标高速立铣。
该设备尾座处配备有与A轴同步转动的U轴,在叶片的数控加工中起到很好的作用。
航空发动机涡轮叶片的动态特性分析与优化研究

航空发动机涡轮叶片的动态特性分析与优化研究航空发动机作为飞机的核心部件之一,其性能的优化研究一直是航空领域的重点关注。
在航空发动机中,涡轮叶片作为能量转化和传递的关键部件,其动态特性分析与优化是提高发动机效能和可靠性的关键环节。
本文将从涡轮叶片的动态特性分析入手,讨论其在设计和优化中的重要性,并介绍一些常用的优化方法,以期为航空发动机涡轮叶片的研究提供一些参考。
首先,动态特性的分析是研究涡轮叶片优化的基础。
涡轮叶片在运行过程中受到各种力的作用,如离心力、气动力、惯性力等。
这些力的大小和方向会导致叶片的变形和振动现象,从而影响到其工作性能和寿命。
因此,了解叶片在不同条件下的动态特性,有助于揭示叶片疲劳破坏的机理,并为优化设计提供参考。
在动态特性的分析中,常用的方法之一是模态分析。
模态分析是通过计算涡轮叶片的固有频率和振型,来研究其受力情况和振动特性。
通过模态分析,可以确定叶片在不同频率下的主要振动模态,并分析其对结构强度和稳定性的影响。
另外,通过模态分析还可以评估叶片的共振风险,从而避免共振振动引起的疲劳破坏。
除了模态分析,流固耦合分析也是动态特性分析的常用方法之一。
在流固耦合分析中,通过同时考虑气动载荷和结构响应,可以获得更加准确和全面的叶片动态特性信息。
例如,通过求解雷诺平均Navier-Stokes方程和线性弹性方程的耦合问题,可以得到叶片的气动力和振动响应。
这种方法可以考虑流场和结构的相互作用,更加真实地模拟实际工况下叶片的动态行为。
了解涡轮叶片的动态特性不仅可以帮助我们优化叶片的设计,还可以指导改进叶片的制造工艺和材料选择。
例如,在叶片的设计中,可以通过调整叶片的结构参数和材料性能,来减小叶片的变形和振动。
同时,在制造过程中,也可以采用一些先进的工艺和技术,如激光焊接和先进材料成形,来提高叶片的制造质量和结构一致性。
这些措施的实施可以显著改善叶片的动态特性,提高航空发动机的可靠性和寿命。
基于叶片STL模型的型面检测与最大厚度分析

基于叶片STL模型的型面检测与最大厚度分析1. 引言a. 研究背景b. 研究意义c. 研究目的2. 相关技术及方法a. STL模型介绍b. 型面检测原理及方法c. 最大厚度分析原理及方法3. 叶片STL模型的型面检测a. 模型前处理b. 型面检测方法设计c. 实验结果分析4. 叶片STL模型的最大厚度分析a. 模型前处理b. 最大厚度分析方法设计c. 实验结果分析5. 结论与展望a. 结论总结b. 研究中存在的问题及改进方向c. 研究展望第一章:引言在现代工业中,叶片是一种重要的工业零部件。
叶片的形状对其性能和寿命具有重要影响,因此在叶片的生产和使用过程中需要进行型面检测和最大厚度分析。
这些问题在以前的研究中已经得到了广泛研究,但是随着计算机技术的发展和数字化加工技术的应用,如何利用计算机的强大计算能力和科学的方法进行叶片的型面检测和最大厚度分析成为了研究的热点。
本文将对叶片STL模型的型面检测和最大厚度分析进行研究。
在实验中,我们将使用三维扫描仪获取叶片的三维STL模型,并对其进行预处理。
然后,我们将设计能够准确和高效进行型面检测的算法,并通过实验验证其有效性。
接下来,我们将设计能够准确计算叶片最大厚度的算法,并通过实验验证其有效性。
最后,我们将总结研究结果,并对以后的研究进行展望。
第二章:相关技术及方法2.1 STL模型介绍STL(STereoLithography)是三维打印和计算机辅助制造(CAM)中常用的三维模型表述格式。
STL模型是由三角形网格组成的,因此被称为三角形网格模型。
STL模型广泛用于rapid prototyping(RP)和计算机数控加工(CNC)等应用领域。
在本研究中,我们使用三维扫描仪获取叶片的三维STL模型,并对其进行预处理,以用于后续的型面检测和最大厚度分析。
2.2 型面检测原理及方法型面检测(Surface Inspection)是根据实际产品的需求,采用对比、统计、分析等方法,对现有产品进行检测的一种方法。
叶片表面微细观结构对润湿性的影响
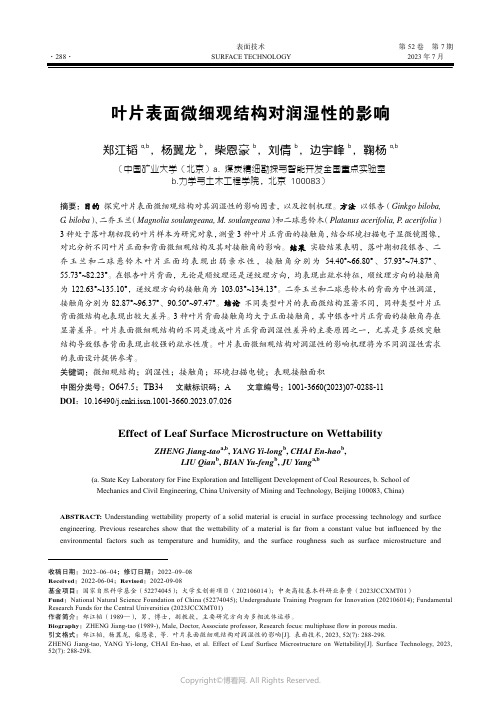
表面技术第52卷第7期叶片表面微细观结构对润湿性的影响郑江韬a,b,杨翼龙b,柴恩豪b,刘倩b,边宇峰b,鞠杨a,b(中国矿业大学(北京)a. 煤炭精细勘探与智能开发全国重点实验室b.力学与土木工程学院,北京 100083)摘要:目的探究叶片表面微细观结构对其润湿性的影响因素,以及控制机理。
方法以银杏(Ginkgo biloba,G. biloba)、二乔玉兰(Magnolia soulangeana, M. soulangeana)和二球悬铃木(Platanus acerifolia, P. acerifolia)3种处于落叶期初段的叶片样本为研究对象,测量3种叶片正背面的接触角,结合环境扫描电子显微镜图像,对比分析不同叶片正面和背面微细观结构及其对接触角的影响。
结果实验结果表明,落叶期初段银杏、二乔玉兰和二球悬铃木叶片正面均表现出弱亲水性,接触角分别为54.40°~66.80°、57.93°~74.87°、55.73°~82.23°。
在银杏叶片背面,无论是顺纹理还是逆纹理方向,均表现出疏水特征,顺纹理方向的接触角为122.63°~135.10°,逆纹理方向的接触角为103.03°~134.13°。
二乔玉兰和二球悬铃木的背面为中性润湿,接触角分别为82.87°~96.37°、90.50°~97.47°。
结论不同类型叶片的表面微结构显著不同,同种类型叶片正背面微结构也表现出较大差异。
3种叶片背面接触角均大于正面接触角,其中银杏叶片正背面的接触角存在显著差异。
叶片表面微细观结构的不同是造成叶片正背面润湿性差异的主要原因之一,尤其是多层级突触结构导致银杏背面表现出较强的疏水性质。
叶片表面微细观结构对润湿性的影响机理将为不同润湿性需求的表面设计提供参考。
关键词:微细观结构;润湿性;接触角;环境扫描电镜;表观接触面积中图分类号:O647.5;TB34文献标识码:A 文章编号:1001-3660(2023)07-0288-11DOI:10.16490/ki.issn.1001-3660.2023.07.026Effect of Leaf Surface Microstructure on WettabilityZHENG Jiang-tao a,b, YANG Yi-long b, CHAI En-hao b,LIU Qian b, BIAN Yu-feng b, JU Yang a,b(a. State Key Laboratory for Fine Exploration and Intelligent Development of Coal Resources, b. School ofMechanics and Civil Engineering, China University of Mining and Technology, Beijing 100083, China)ABSTRACT: Understanding wettability property of a solid material is crucial in surface processing technology and surface engineering. Previous researches show that the wettability of a material is far from a constant value but influenced by the environmental factors such as temperature and humidity, and the surface roughness such as surface microstructure and收稿日期:2022–06–04;修订日期:2022–09–08Received:2022-06-04;Revised:2022-09-08基金项目:国家自然科学基金(52274045);大学生创新项目(202106014);中央高校基本科研业务费(2023JCCXMT01)Fund:National Natural Science Foundation of China (52274045); Undergraduate Training Program for Innovation (202106014); Fundamental Research Funds for the Central Universities (2023JCCXMT01)作者简介:郑江韬(1989—),男,博士,副教授,主要研究方向为多相流体运移。
航空发动机压气机叶片型面检测技术

中,控制系统采用上控机,以TR008
数控系统平台为基础进行开发,实现
了测量仪的运动控制、数据采集、光
栅准确计数等功能。TR008是清华 大学精仪系制造工程研究所正存开 发和完善的普及型数控系统平台,其 软件争郜由c程序设计语言实现。 处理系统采用PC机,以基于Win一 dows系统的MATLAB作为软件开 发1二具,以实现测量数据的处理、曲 线拟合造型、参数辨识等功能。两台 不同系统计算机之间的数据传输采 用了建立无盘工作站的方法来实现,
3陈凯云,叶佩青,俞学兰,等·航空压
主嚣!盖i雷::型苎i竺研究·仪器仪表
4张国雄.三坐标测量机.天津:天津 大学出版社,1999.113~117(责编晓霸)
48航牵翩造技术·2007年第1l期
万方数据
青海大学机械系 清华大学精仪系
俞学兰 叶佩青
叶片是关系到发动机性能的高负荷零件。严格控制叶 片的制造质量,是叶片制造中的关键问题。因此,叶片的检 测技术非常重要,在叶片制造的总工作量中叶片检测工作 量占相当大的EE例。
俞学兰 硕士。青海大学机械系讲师,主
要研究方向为数控加工。
叶片是关系到发动机性能的高 负荷零件。严格控制叶片的制造质 量,是叶片制造中的关键问题。因此, 叶片的检测技术:{}常重要,在叶片制 造的总工作量中叶片检测工作量占 相当大的比例“1。
即为理想标准叶片; 失真或无法计算的现象,而激光测量
制造误差很小时即 仪n J以真实地反映叶片边缘的形状。
为样板叶片,此时制 表2从测量的精度、速度以及可靠性
圈3二维图形显示界面
造误差对测量结果 等方面将四坐标激光测量仪与三坐
的影响不明显。在 标测量机两种测量方式进行叶片测
密转台,配合非接触式激光测头进行 试验巾选用某型样板叶片对测量结 量的结果进行了比较。
某薄型叶片高效精密数控加工工艺研究

叶片的材料 为高 温合金 , 硬度 非常 大 , 切削 加工性 能较差 。 3 . 2 设 备 试 验所采 用 的是 国外先 进 的高速数 控 铣床 。该设 备尾 座处 配备有 与 另一端 同步 转 动 的 U轴 ,在 此 叶 片 的数 控 加 工 中起 很好 的对 心作用 。 3 . 3 变形 的控制 及改善 影响 叶片变形 的 因素主要 有 以下 几个 方 面 ,下面将 分别 对其进 行分 析并 阐述试 验所采 取的措施 。 3 . 3 . 1 装夹 系统 的稳 定 性 及 刚 性对 叶 片变形 的影 响及控 制 装夹 是否稳 定 ,重复精 度如何 及夹 紧 力 的大小是 影响 变形 的主要 因素 。叶片 为 弱刚性体 ,增强装夹系统刚性是解决薄型 叶 片变形 的最主要 途径 。 3 . 3 . 1 . 1 增强 装夹 系统刚性 以往数 控加工 叶身 型面时 ,采用顶 尖 顶 紧小轴 颈处顶 尖的方 式 , 此 叶 片非 常 薄 ,在 顶 紧力 的作 用 下 ,
基于差分进化算法的枞树型叶根测量数据处理方法

基于差分进化算法的枞树型叶根测量数据处理方法巫志华;范小平【摘要】结合枞树型叶根的型线特点,将某一大功率汽轮机末级动叶枞树型叶根的测量数据拟合处理,转化成多约束条件下多参数单目标最小值优化问题,并采用差分进化算法进行求解.拟合结果表明这种处理模式是合理的,差分进化算法能够很好地应用于该类工业测量数据的拟合.【期刊名称】《东方汽轮机》【年(卷),期】2012(000)002【总页数】4页(P1-3,19)【关键词】枞树型叶根;最小值优化;差分进化算法;工业测量【作者】巫志华;范小平【作者单位】东方汽轮机有限公司,四川德阳,618000;东方汽轮机有限公司,四川德阳,618000【正文语种】中文0 引言透平叶片叶根的形式对叶片的整体强度振动特性有很大的影响。
枞树形叶根以其良好的承载特性和强度适应性而在燃气轮机及蒸汽轮机叶片设计中得到广泛的应用,尤其是在负荷较高,载荷比较复杂的透平级中,如透平末级,这类叶根的应用就更为普遍,但其尺寸精度要求比较高。
在叶片的强度振动分析中,首先需要得到包括叶根在内的叶片型线数据,实际上,在很多情况下,原始的设计型线数据是无法得到的,如对进口原装机组叶片的力学性能分析,这就需要采用一定的方法进行测绘处理得到型线后才能进行相应的分析。
由于枞树型叶根的型线相对比较复杂,测量数据相对比较多,采用的数据处理方法对在同一精度范围内的测量数据进行合理的处理将对分析结果的可信度有直接的影响。
已有大量的文献和专著对测量数据处理的理论与方法进行了研究和分析[1]。
测量数据的处理在数学上通常表述为最优问题的求解。
本文针对某一大功率汽轮机末级动叶的测绘,对该动叶的五齿枞树型叶根测量数据进行处理,结合枞树型叶根的结构特点,建立了一种合理的最优问题求解模型,并采用差分进化算法进行求解,以解决此类叶根测量数据的处理问题。
1 枞树型叶根测量数据处理的数学模型1.1 枞树型叶根的结构特点图1是一种典型的五齿枞树型叶根母线形式,也是本文测绘的叶根所采用的结构形式,实际的叶根由母线通过旋转或者沿指定方向的轴线延伸就可以得到。
茶树叶片显微结构及扫描电镜研究进展

叶片是 高等植物进 行光合作用 和蒸 腾作用 的器 官 ,
的圆柱形薄壁细胞构成 , 细胞里含有很多的叶绿体; 栅栏
在 长期的进化过程 中 ,叶片结 构的功能与环境达到一定 组织下 面是 由排列疏松 、不规则 的薄壁细胞构成的海绵
的统 一。叶片 , 是茶树进行 光合作用 、 蒸腾作用和气体交 组织 ,内含有少量叶绿体 1 一 。据研究 , 观音 、 铁 毛蟹 、 黄 换的主要器 官 ,同时也是人类 采摘 的主要部位I, 其叶片 旦 、 1 奇兰 、 占、 叶乌龙 、 山八个福建乌龙茶品种均 梅 大 本
一
层栅栏组 织的石细胞 的分布和数量有所 区别 ,表皮毛
上、 下表皮之间为叶 肉, 由栅栏组织与海绵组织构成 , 栅 多 的品种 , 肉的石细胞较少 , 叶 反之则相反『1 茶树光合 8。
栏组织 紧接上表皮 ,由 13 - 层垂直于 叶片表面 、 排列紧密 速 率与栅 栏组织厚度 、栅栏组织 与海 绵组织 的 比值呈正
及其组成具有 重要 的意义 ;研究茶树不 同叶位叶片 的显 白茶 、 柳叶早 、 云南大 叶群体品种 、 安化群体 的海绵组织
微结构 , 有助于了解不 同叶位 叶片 的生理功能 , 并且为加 中细胞间隙较大 , 明前早和高桥早则较小 。 同品种 的叶 不
工 中各个 环节技术参数 的制定提供 一定 的理论依据 。而 片厚度 、 L 气孑 分布的疏密度 、 L 气孑 的大小 、 表皮毛 的长短
学术 专业 人文 茶趣
茶 树 叶 片 显 微 结 构 及 扫 描 电 镜 研 究 进 展
黄晓敏 冯花 郭雅玲 ★ 1 ( 福建农林大学园艺学 院茶学系 福州 3 0 0 1 50 2 国家茶叶产业技术体 系乌龙茶加工 岗位 )
基于PRO/E的风力发电机叶片复杂曲面建模

基于PRO/E的风力发电机叶片复杂曲面建模郑喜朝【摘要】以涡流理论为基础,基于点坐标的空间几何变换理论,按照风力发电机叶片设计的实际过程.对风力发电机叶片的空间截面坐标进行求解,提出了一种通用设计方法,并运用PRO/E软件,实现了风力发电机叶片三维实体的精确建模。
该方法对于风机的优化建模具有指导意义。
%The paper was solved space section coordinates of wind driven generator and put forward universal design proposal based on vortex theory and transform theory of spatial geometry. The paper also was realizedthree dimensional accurate modeling of wind driven generator by using PRO/E software, which had guiding significance to optimizing modeling of wind driven generator.【期刊名称】《科技创新与生产力》【年(卷),期】2012(000)012【总页数】3页(P79-80,83)【关键词】PRO;E;风力发电机;曲面建模【作者】郑喜朝【作者单位】陕西国防工业职业技术学院,陕西西安710300【正文语种】中文【中图分类】TM315叶片作为风力发电机捕捉风能的关键部件,是风力发电机的核心机械零件之一。
风力发电机叶片类是具有代表性且造型比较规范的、典型的包含复杂曲面的零件,叶片的设计涉及到空气动力学、流体力学等。
叶片能否正常工作直接影响着风力发电机组的正常运行。
由于其受力情况复杂,在各种交变负荷作用下,都会引起叶片结构振动。
因此,为风力发电机叶片进行精确的三维建模,对于对风力发电机的设计和运行都是非常重要的[1-2]。
大型风电叶片的结构分析和测试

大型风电叶片的结构分析和测试闫文娟;韩新月;程朗;印厚飞【摘要】文章使用FOCUS软件对某兆瓦级叶片进行建模和结构分析,并与试验叶片的重量、模态、静力结果进行对比.结果表明,叶片重量的计算值与实测值偏差0.1%,频率的计算值与实测值最大偏差-4.6%,位移的计算值与实测值最大偏差5.08%,应变的计算值与实测值最大偏差-7.61%,均符合GL2010规范中的要求.叶片重量、频率、位移、应变的计算值和试验值高度吻合,验证了本方法的可靠性.【期刊名称】《可再生能源》【年(卷),期】2014(032)008【总页数】4页(P1140-1143)【关键词】风机叶片;结构分析;测试;模态;变形【作者】闫文娟;韩新月;程朗;印厚飞【作者单位】国电联合动力技术有限公司,北京 100039;国电联合动力技术有限公司,北京 100039;国电联合动力技术(连云港)有限公司,江苏连云港222000;国电联合动力技术(连云港)有限公司,江苏连云港222000【正文语种】中文【中图分类】TK831 引言风力发电机的叶片(下文简称叶片)是风电设备将风能转化为机械能的关键部件,其制造成本约占风机总成本的15%~30%。
大型风力发电机的叶片基本由复合材料制成,叶片设计与制造是风电机组的技术关键[1]-[4]。
目前,国内多家叶片生产企业都在自主开发新型号叶片,设计中所用的工具也不尽相同[5],[6]。
FOCUS软件是用于风电机组及组件(如叶片)快速设计分析的软件工具,在国际风电设备工业有超过10年的应用史。
相对于使用三维建模软件和有限元计算软件结合的设计路线,使用FOCUS软件更为便捷。
本文通过使用FOCUS软件对某型号叶片直接完成建模,对其进行了模态和结构静力学分析,并与实际叶片的模态和静力试验结果进行了对比分析。
2 模型建立FOCUS拥有独特的对叶片进行详细设计的交互式建模工具。
在对叶片进行逐步定义的同时,三维的交互式显像会对设计变化给出直接反馈。
航空发动机涡轮叶片精密成形技术分析
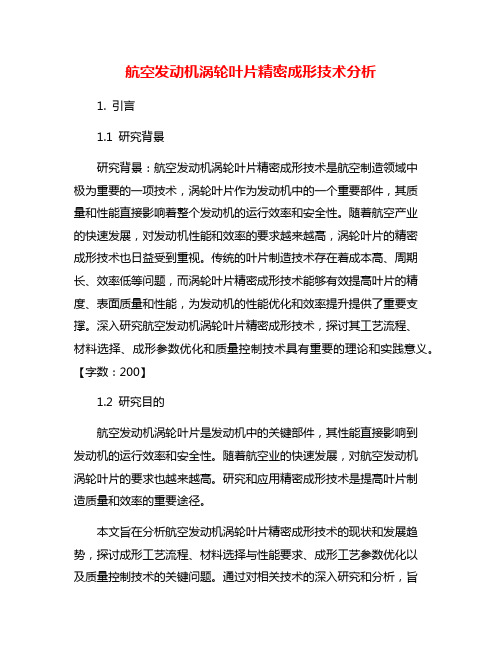
航空发动机涡轮叶片精密成形技术分析1. 引言1.1 研究背景研究背景:航空发动机涡轮叶片精密成形技术是航空制造领域中极为重要的一项技术,涡轮叶片作为发动机中的一个重要部件,其质量和性能直接影响着整个发动机的运行效率和安全性。
随着航空产业的快速发展,对发动机性能和效率的要求越来越高,涡轮叶片的精密成形技术也日益受到重视。
传统的叶片制造技术存在着成本高、周期长、效率低等问题,而涡轮叶片精密成形技术能够有效提高叶片的精度、表面质量和性能,为发动机的性能优化和效率提升提供了重要支撑。
深入研究航空发动机涡轮叶片精密成形技术,探讨其工艺流程、材料选择、成形参数优化和质量控制技术具有重要的理论和实践意义。
【字数:200】1.2 研究目的航空发动机涡轮叶片是发动机中的关键部件,其性能直接影响到发动机的运行效率和安全性。
随着航空业的快速发展,对航空发动机涡轮叶片的要求也越来越高。
研究和应用精密成形技术是提高叶片制造质量和效率的重要途径。
本文旨在分析航空发动机涡轮叶片精密成形技术的现状和发展趋势,探讨成形工艺流程、材料选择与性能要求、成形工艺参数优化以及质量控制技术的关键问题。
通过对相关技术的深入研究和分析,旨在揭示精密成形技术在航空发动机涡轮叶片制造领域的重要性,并为未来的发展提供参考和借鉴。
在探讨研究目的的过程中,希望能够全面了解航空发动机涡轮叶片精密成形技术的关键问题,为提高叶片制造质量、减少生产成本和优化生产效率提供理论指导和技术支持。
通过该研究,为航空发动机涡轮叶片制造技术的进一步发展和提升质量水平提供理论基础和实践经验。
2. 正文2.1 叶片精密成形技术概述叶片精密成形技术是航空发动机制造中关键的工艺之一,它直接影响着发动机的性能和可靠性。
叶片是发动机中的重要部件,起着承受高温、高压气流的作用。
叶片的精密成形技术至关重要。
叶片精密成形技术是指利用精密模具和高精度设备对叶片进行成形加工的技术。
这种技术可以确保叶片的几何形状和表面质量达到设计要求,从而提高发动机的性能和寿命。
2012年全国大学生数学建模竞赛A题“特等奖”译文

2012年美国大学生数学建模竞赛A题题目翻译:一棵树的叶子。
一棵树的叶子有多重?怎么能估计树的叶子(或者树的任何其它部分)的实际重量?怎样对叶子进行分类?建立一个数学模型来对叶子进行描述和分类。
摘要我们构建了四个模型来研究叶的分类,叶子形状和叶片分布之间的关系,叶子的形状和树的轮廓的关联,以及一棵树的树叶总质量。
模型1处理叶的分类。
我们主要侧重于最显着的叶片的特征,即,形状。
我们创建七个几何参数以量化叶的形状。
然后,我们选择了六种常见的类型的叶子构造一个数据库。
通过计算的样品的与这些典型叶子的偏差指数,我们可以将叶子进行分类。
为了说明这个分类过程中,我们使用了枫叶作为测试。
模型2研究叶的形状和叶片分布之间的关系。
首先,我们将一棵树化为理想模型,然后介绍太阳高度的概念。
通过考虑叶片长度和节间在不同太阳高度下的关系,分析重叠的片叶阴影,我们发现树叶的形状和分布随着太阳高度进行优化以最大化接受阳光照射。
我们将该模型应用到三类试验树木。
模型3讨论树的轮廓和叶的形状之间可能存在关联。
基于叶脉和树的分支结构的相似性,我们认为,叶子的形状在二维上相似于一个树的轮廓。
采用模型1的方法,我们设置了几个参数来反映每棵树的大概形状,并通过它们的叶子将其进行比较。
在统计工具的帮助下,我们展示了一个树的轮廓与其叶子形状之间的粗略的关联。
模型4通那过给定的树的大小特征,估计了一棵树叶子的总质量。
并引入固碳率和树龄来建立叶的总质量和树的大小之间的联系。
由于单位质量的一个叶以一个恒等的速率固碳,固碳率与树龄之间是一个二次关系,并且树的年龄关系经历逻辑斯蒂增长。
介绍:我们解决四个主要子问题:•分类的叶子,•叶分布和叶片形状之间的关系,•树的轮廓和叶的形状的关系,和•一棵树叶片总质量的计算。
要解决的第一个问题,我们选择一组参数来量化叶片的形状特征和使用叶的形状作为我们的分类过程的主要标准。
对于第二个问题,由于叶子的形状影响着叶之间的重叠,我们将一片叶子直接投射到它下面的一片叶子的阴影重叠区域作为叶片分布和叶片形状之间的一个联系,我们假设叶片分布总是趋于尽量减少重叠的区域。
涡轮叶片的曲面重构及误差分析
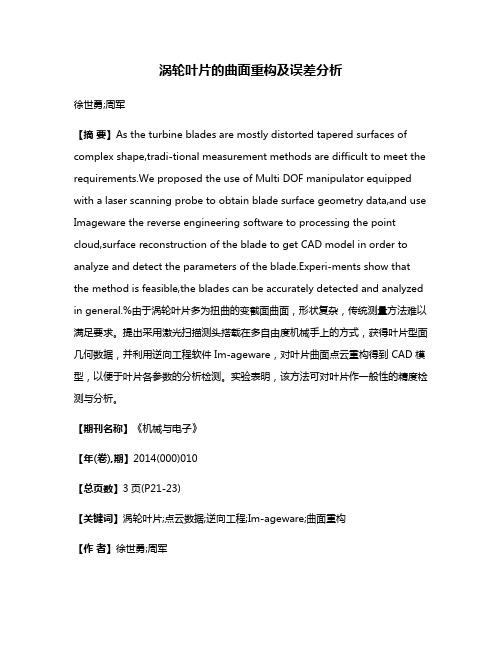
涡轮叶片的曲面重构及误差分析徐世勇;周军【摘要】As the turbine blades are mostly distorted tapered surfaces of complex shape,tradi-tional measurement methods are difficult to meet the requirements.We proposed the use of Multi DOF manipulator equipped with a laser scanning probe to obtain blade surface geometry data,and use Imageware the reverse engineering software to processing the point cloud,surface reconstruction of the blade to get CAD model in order to analyze and detect the parameters of the blade.Experi-ments show that the method is feasible,the blades can be accurately detected and analyzed in general.%由于涡轮叶片多为扭曲的变截面曲面,形状复杂,传统测量方法难以满足要求。
提出采用激光扫描测头搭载在多自由度机械手上的方式,获得叶片型面几何数据,并利用逆向工程软件 Im-ageware,对叶片曲面点云重构得到 CAD 模型,以便于叶片各参数的分析检测。
实验表明,该方法可对叶片作一般性的精度检测与分析。
【期刊名称】《机械与电子》【年(卷),期】2014(000)010【总页数】3页(P21-23)【关键词】涡轮叶片;点云数据;逆向工程;Im-ageware;曲面重构【作者】徐世勇;周军【作者单位】河海大学机电工程学院,江苏常州213022;河海大学机电工程学院,江苏常州 213022【正文语种】中文【中图分类】TH1280 引言涡轮叶片是关系到发动机性能和安全的高负荷零件,严格控制叶片的制造质量是叶片加工中的关键问题,因此,叶片检测是叶片加工技术中的重要内容。
大型风力发电机组叶片模态测试与数值计算

2020年第12期1270 引言随着技术的进步,新能源风力发电呈现出“单机容量持续增大、叶片长度持续增加”的趋势。
随着叶片长度增加,其柔性更大,叶片失稳、颤振等问题的研究变得更加重要,相应地需要对叶片的动态特性做更深入的分析和试验。
在叶片动态特性分析中,叶片的模态测试是很重要的一个试验项目,它可以为叶片的动力学计算模型提供修正依据。
目前,基于全尺寸叶片的模态测试还很少见,相关研究文献也不多。
虽然中国科学研究院工程热物理研究所的毛火军等曾进行过相关试验,但由于试验采用不测力法进行,导致试验结果仍有缺陷和遗憾[1]。
本次试验项目试验人员利用某大型风电机组样机研发的机会,在叶片厂专用试验台上进行了全尺寸的叶片模态测试,得出了较为满意的测试结果。
试验人员将数值计算分析与试验结果进行对比,对比结论显示计算的误差较小,说明试验人员使用此计算模型可确保后续进行的其他动力特性数值计算的精准度。
1 测试的基本情况1.1 测试目的根据国内外相关的行业标准[2],叶片的振动模态测试一般需要测试挥舞一、二阶模态,摆振一阶模态,如有可能,测试扭转一阶模态。
1.2 测试原理试验人员要先了解模态测试的基本原理,就需要先了解振动系统的基本构成要素。
一个振动系统包括以下3个要素:输入(力、力矩等,称为载荷;或大型风力发电机组叶片模态测试与数值计算石久波南京高华科技股份有限公司,江苏 南京 210000 摘要:试验人员采用力锤激励的方式,在叶片专用试验台上对某大型风力发电机组的叶片进行了模态激励测试。
测试结果表明,力锤激励可较好地激发出包括扭转模态在内的叶片各阶模态。
同时,试验人员将叶片各阶模态与计算模态进行了对比,得到的结果是,计算模态与实测模态误差较小。
这为以后叶片的数值计算模拟提供了经验和参考。
关键词:风力发电机叶片;模态测试;力锤;频响函数;计算模态中图分类号:TM315;TK83运动量,称为振动环境);输出(位移、速度、加速度、应力、应变等,称为系统或结构响应);系统模型(系统本身固有动态特性,只与质量分布特性m 、刚度分布特性K 、系统阻尼特性C 等相关,不随外界环境变化而改变)。
- 1、下载文档前请自行甄别文档内容的完整性,平台不提供额外的编辑、内容补充、找答案等附加服务。
- 2、"仅部分预览"的文档,不可在线预览部分如存在完整性等问题,可反馈申请退款(可完整预览的文档不适用该条件!)。
- 3、如文档侵犯您的权益,请联系客服反馈,我们会尽快为您处理(人工客服工作时间:9:00-18:30)。
叶片型面典型参数一致性分析研究
高晓斐1,魏月萍2
.中航工业西安航空发动机(集团)有限公司 陕西 西安 710021;
摘要:本文通过多种测量方法对某机一级转子叶片型面典型参数进行测量,对测量结论的稳定性进行比对分析,结合生产实际,针对不同的测量要求,提出一套测量叶片型面的最佳测量方法,不但能提高测量准确度而且能合理利用现有测量资源,实现既能提高测量精度又能提高测量效率的目的。
关键词:叶片型面 典型参数 最佳测量方法 一致性
0前言
叶片是航空发动机中最主要的零部件之一,叶片的几何形状和尺寸决定着叶片的工作性能,而叶片型面质量对发动机的燃油消耗起着较大的影响,叶片型面检查具有十分重要的意思,随着科技的发展,叶片型面的测量方法多样化,各种测量方法测量结论的一致性是目前测量研究的重点。
1叶片型面结构特点及测量方法分析
1.1 叶片型面参数
叶片型面部分是叶片主要部分,决定着叶片气动性能的好坏,叶片型面测量参数包括:最大厚度、前缘厚度、后缘厚度、指定点厚度、进/排气位置、进/排气边半径、弯曲、扭转、弦宽(长)、弦角、切线角、叶盆/叶背轮廓度、进/排气边缘轮廓度、X/Y偏移、波纹度等,目前波纹度的测量只能定性测量不能定量测量,通常用波纹度标准件比对目视测量。
在这些型面参数中,测量公差要求严,测量精度要求高的参数有:进排气边位置及形状、叶盆叶背轮廓度、叶片型面扭转、偏移,弦长。
叶片型面结构如图1所示,叶型典型参数如图2所示。
图1 叶片型线结构示意图
图2 叶型典型参数示意图
1.2 叶片型面测量方法
叶片型面检测方法有:型面样板测量法、自动绘图测量法、光学投影测量法、电感量仪法、坐标测量法、机器视觉测量法、激光测量法、光跟测量法等。
在测量型面尺寸时,比较常用的测量方法有:电感量仪法、型面样板测量法、坐标测量法,光跟型面测量仪等四种测量方法。
电感量仪是利用传感器获得触头位移信号,经放大器处理后在显示器上
进气边位置
排气边位置
排气边 厚度
最大厚度
弦长
弦角
叶背轮廓
叶盆轮廓
把位移显示出来,电感量仪主要分三部分:测具、传感器和显示器部分。
电感量仪是点式测量,是将叶片分成若干个被测截面, 每个截面对应于一组电感传感器, 每个传感器对应于被测截面上的一个点。
测量前按被测叶片型面预先设置几组传感器的位置和测量方向, 并用标准叶片对零。
测量时, 传感器组靠近并接触叶片表面,从各传感器测得与标准叶片的偏差量, 就可以得到被测叶片的形状误差、角向误差、叶型厚度等参数。
电感量仪测量原理如图3所示。
图3 电感量仪测量原理示意图
型面样板测量法是将叶片以基准定位固定在测座上,用各截面的标准型线的样板,分别与各截面实际型线作比较,测出样板型线与叶片型线的透光间隙,以及样板基准面与测座基准面的间隙,该间隙值就是型线误差。
叶片型面测具结构如图4所示。
图4 叶片型面测具结构示意图
三坐标测量是采用计算机技术,编制测量程序,叶片在测量过程中通过
扭转调整螺钉
偏移调整螺钉
计算机、测量机的传感器、将自动测量、存储和记录数据,并通过分析软件将测量数据与理论数据进行比对,可得到被测叶片几何尺寸和形状误差等参数。
光跟测量法是将标准叶型按1:1绘制标在分划板上,假想圆是为了说明测量原理而假设的,它的直径与测量球头直径相等,在测量过程中,被测叶片和假想圆固定不动,测量头和分划板用测量架刚性连接,通过水平、垂直运动导轨作水平和垂直随地。
当测量头沿叶片型面移动时,分划板跟踪作同步运动,分划板上的叶型就沿着假想圆运动,叶片型面误差的方向是在型面的法线方向上;从几何原理可知:曲线与圆相切,该曲线在切点处的法线方向既是切点与圆相连的方向,根据这一原理来观察影屏上分划板叶型线的投影与公差带基圆的相对位置,以检测出叶片型面的法向误差,光跟测量法原理如图5所示。
图5 光跟测量法示意图
2.2 叶片测量一致性分析
叶片按型面余量分可分为精锻件和模锻件,精锻叶片主要指叶身型面及内缘板通过锻造及辅助工序达到叶身和内缘板无余量,该类叶片主要加
工叶片榫头及进排气边缘,所以主要测量的型面参数有:叶片进、排气边缘轮廓度、叶盆、叶背轮廓度、扭转以及X、Y偏移。
模锻件主要是指叶片型面及榫头都有余量,不但要加工叶片的榫头而且要加工叶片的型面,所以测量的型面参数主要有:进/排气位置、弦宽(长)、叶盆/叶背轮廓度、扭转。
在众多测量型面的方法中,测量结论是否一致我们关注的重点,
选用一个叶片叶尖某一截面,分别用三种测量方法:型面测具样板测量,传统的三坐标测量,导入数模三坐标测量,分别对该叶片型面5个典型参数:进气边位置、排气边位置、叶盆轮廓度、叶背轮廓度、扭转,测量5遍,对5个结论进行比对分析。
某机零级动叶型面为不规则的三维曲面,叶根型面扭曲比较大,该叶片纵向长度为349mm,最大弦长为222.9mm,各截面弦切角最大相差43度左右,叶片型面形状如图6所示。
图6 叶片型面形状示意图
2.1 型面样板测量法
型面样板测量法是将标准样板和实际叶片对应检测截面靠近, 借助叶片与样板之间的透光间隙大小, 估计对应型线的误差,取某机零级转子
叶片一件,对其进行测量,测量结果如表1.
表1 型面型面测具测量结论
进气边位置 排气边位置 叶盆轮廓度 叶背轮廓度 扭转
第一次 合格 合格 合格 合格 合格
第二次 合格 合格 合格 合格 合格
第三次 合格 合格 合格 合格 合格
第四次 合格 合格 合格 合格 合格
第五次 合格 合格 合格 合格 合格
测量时间 10分钟
从表一可以看出:5次测量结论基本一致,说明该测量方法是可靠的,稳定的。
型面样板测量法具有检测速度快、操作简单、便于现场使用等优点,在叶片加工过程中得到广泛使用, 但它只能定性地检测零件是否合格, 测量精度低。
2.2 传统三坐标测量法
用同一个测具,用同一个叶片,用三坐标测量软件QUINDOS在不同的时间段测量叶片型面5次,在UG软件下分析,结论如表2。
表2 传统三坐标测量结论
进气边位置 排气边位置 叶盆轮廓度 叶背轮廓度 扭转
第一次 +0.046 ‐0.053 0.11 0.123 10.08
第二次 +0.030 ‐0.042 0.119 0.109 11.10
第三次 +0.065 ‐0.062 0.082 0.12 10.70
第四次 +0.059 ‐0.026 0.106 0.082 11.00
第五次 +0074 ‐0.044 0.091 0.119 9.90
所需时间 15分钟
从表二可以看出:5次测量结论变化在0.041 mm之间,说明该测量方法稳定可靠。
但是用传统的三坐标测量,UG软件分析,效率很低,不能满足生产现场大批量生产。
2.3 导入CAD数模的三坐测量法
用PC‐DIMS测量软件下测量5次,用BLADE叶片专用分析软件对测量结果进行参数分析测量结论如下表3。
表3 导入CAD数模的三坐测量结论
进气边位置 排气边位置 叶盆轮廓度 叶背轮廓度 扭转
0.121 0.117 11.10
第一次 +0.052 ‐0.061
0.115 0.116 10.84
第二次 +0.048 ‐0.049
0.095 0.121 10.09
第三次 +0.058 ‐0.063
0.097 0.099 10.2
第四次 +0.066 ‐0.028
第五次 +0.051 ‐0.047 0.094 0.123 10.1
所需时间 8分钟
从表3可以看出:5次测量结论最大相差不到0.03mm,该测量方法,精度高,时间短。
通过三种测量结论的比较可以看出:各种叶片的型面测量方法可靠的,测量结论基本一致,现场可以根据生产任务及设计要求对测量精度的
要求,进行测量方法的合理选择。
2.4 在生产现场经常会出现叶片碰、压、划伤的情况,通常对有划伤的叶片采用钳修或抛修的方法去除缺陷,但经常会出现抛修部位叶片型面不在测量截面上,抛修的叶型轮廓度是否合格,传统的测量方法是采用手摸或目视的方法感觉是否平滑过渡。
随着科研产品的发展,叶片型面扭曲越来越大,用手摸或目视无法准确判断叶片轮廓变化。
抛修部位与测量截面如图7所示。
图7 抛修部位与测量截面示意图
在测量中结合三维CAD 实体模型进行叶片的数字化检测评定时,即使抛修部位不在测量截面上,由于CAD 模型中包含了叶型曲面任意部位的理论点信息,所以很容易实现,在哪个部位触测,就用这个部位的实测点刺穿CAD 模型获取从理论点与测量点的偏移值。
这种利用CAD 模型引导三坐标测量设备进行叶型曲面检测评价的方法,不但可以做到任意部位的检测,而且消除了传统测量带来的计算误差,更加快速、准确地反映了叶片任意位置加工质量。
利用数模测量如图8所示。
图8 利用数模测量示意图
3 结果
型面复杂尺寸,跨度大,受力恶劣,承载最大件。
现代叶片型面检测技术的发展取决于叶片型面的精确测量要求,面对未来高推重比新概念,发动机的性能要求,航空发动机叶片朝着大尺寸、空间任意积叠及符合弯劣等方向发展,这将对叶片型面检测提出更高的要求。
“航空发动机叶片型面典型参数一致性分析研究”,将三维空间测量技术应用于生产现场,为航空发动机叶片型面的准确测量提供了可靠依据。
4.参考文献:【1】 郭文有 航空发动机叶片机械加工工艺 国防工业出版社,1994。