车轴受力分析
基于solidworks的车床主轴受力分析

基于solidworks的车床主轴受力分析以《基于solidworks的车床主轴受力分析》为标题,本文旨在通过使用Solidworks软件,对车床主轴受力进行分析,以提高设备性能,以及实现更好的生产效率和产品质量。
设备性能是工厂日常生产运营中非常重要的一个指标。
如果设备性能不能符合要求,就无法实现高质量、高效率的生产,也就极大地影响了整个生产环境的效率。
因此,对设备性能的分析是必须要做的,以便保证设备能够完美运行,确保生产效率及安全保证。
其中车床的性能更是重要的设备项目,它的主轴受力分析属于重要的性能分析之一。
因此,从车床的性能分析角度进行主轴受力分析是非常重要的。
有了正确的主轴受力分析,就可以使车床运行更平稳、更安全,从而提高生产效率和产品质量。
目前,由于工程计算和软件的发展,对车床的主轴受力分析已经可以通过软件来实现,其中solidworks软件是被广泛使用的一款软件。
由于它具有强大的物理分析功能和虚拟模拟功能,以及可视化的三维设计,因此被广泛用于工程分析,特别是用于车床主轴受力分析。
首先,在使用solidworks软件之前,需要使用solidworks软件进行实际场景的建模,建立车床结构,以及相关参数设置,以便正确分析车床主轴受力。
然后,使用相关分析工具,进行受力、变形和振动等物理分析,从而获得车床受力的分布状态和分析结果,以便正确选择车床部件和材料。
最后,使用solidworks软件进行车床主轴受力分析时,还需要注意车床部件的材料选择,以及车床的安装方式。
正确的材料选择和安装方式可以有效地降低车床主轴受力以及设备的运行偏差,更好地提高车床性能,保证车床的长期安全运行。
以上就是本文使用solidworks软件对车床主轴受力分析的详细过程,虽然它要求颇多的建模及设置工作,但只要正确操作,就能有效地分析车床受力状态,从而提高车床性能,保证安全性和生产效率,以实现更好的生产效率和产品质量。
基于solidworks的车床主轴受力分析
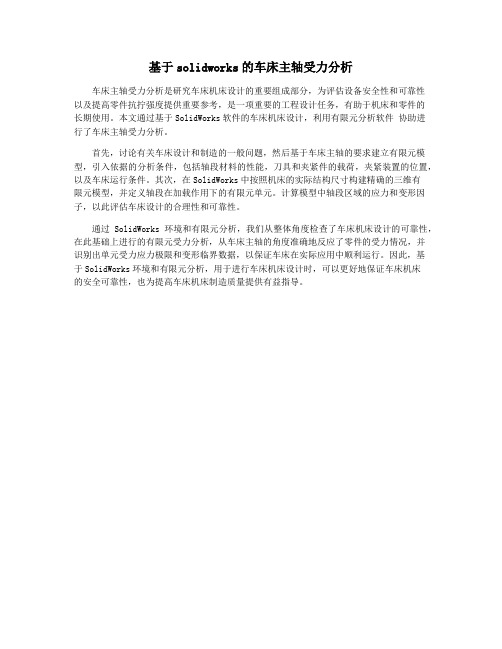
基于solidworks的车床主轴受力分析
车床主轴受力分析是研究车床机床设计的重要组成部分,为评估设备安全性和可靠性
以及提高零件抗拧强度提供重要参考,是一项重要的工程设计任务,有助于机床和零件的
长期使用。
本文通过基于SolidWorks软件的车床机床设计,利用有限元分析软件协助进
行了车床主轴受力分析。
首先,讨论有关车床设计和制造的一般问题,然后基于车床主轴的要求建立有限元模型,引入依据的分析条件,包括轴段材料的性能,刀具和夹紧件的载荷,夹紧装置的位置,以及车床运行条件。
其次,在SolidWorks中按照机床的实际结构尺寸构建精确的三维有
限元模型,并定义轴段在加载作用下的有限元单元。
计算模型中轴段区域的应力和变形因子,以此评估车床设计的合理性和可靠性。
通过SolidWorks环境和有限元分析,我们从整体角度检查了车床机床设计的可靠性,在此基础上进行的有限元受力分析,从车床主轴的角度准确地反应了零件的受力情况,并
识别出单元受力应力极限和变形临界数据,以保证车床在实际应用中顺利运行。
因此,基
于SolidWorks环境和有限元分析,用于进行车床机床设计时,可以更好地保证车床机床
的安全可靠性,也为提高车床机床制造质量提供有益指导。
动车车轴的强度与刚度分析

动车车轴的强度与刚度分析动车作为现代高速铁路的重要组成部分,其安全与运行的稳定性直接关系到旅客的出行安全与乘车的舒适性。
车轴作为动车的重要部件,承担着传递车辆荷载并保持车辆稳定性的重要作用。
因此,对动车车轴的强度与刚度进行分析和评估非常关键。
首先,我们来讨论动车车轴的强度分析。
车轴在运行过程中承受着巨大的荷载,因此其强度至关重要。
强度分析的目标是确定车轴的最大应力以及潜在的应力集中区域,以确保其不会超过允许的应力范围。
在强度分析中,首先需要确定车轴的几何参数,如直径、轴段长度和圆角半径等。
这些参数对于确定车轴的强度至关重要。
然后,根据车轴所承载的荷载情况,进行受力分析,包括轴向力、弯矩和剪力等。
通过受力分析,我们可以计算出车轴在不同受力情况下的应力分布情况。
最后,我们将这些应力与车轴的材料强度进行比较,以确定车轴是否足够强度,是否需要调整几何参数或使用更高强度的材料。
此外,在车轴的强度分析中,还需要考虑到疲劳、腐蚀等因素对车轴强度的影响。
疲劳是指在车轴长时间运行过程中由于循环加载导致的疲劳寿命降低。
因此,在强度分析中,需要对车轴进行疲劳寿命评估,以保证其在正常运行寿命范围内。
另外,车轴也容易受到腐蚀的影响,因此,在强度分析中,需要评估车轴的腐蚀情况,并采取相应的防腐措施,以确保车轴的强度不会受到损害。
接下来,我们来讨论动车车轴的刚度分析。
车轴的刚度对于保持车辆的稳定性和转向性能至关重要。
刚度分析的目标是确定车轴的刚度,并对其刚度进行评估,以确保车轴在运行过程中满足转向和稳定性等要求。
刚度分析首先需要确定车轮与轨道之间的接触力对车轴的影响。
接触力是车轴传递荷载的关键因素之一,它不仅与车轮与轨道之间的摩擦特性相关,还与轨道的几何参数以及车轴的弯曲刚度等因素有关。
因此,在刚度分析中,需要对车轮与轨道之间的接触力进行建模和计算。
另外,刚度分析还需要考虑车轴的弯曲刚度和扭转刚度。
弯曲刚度是指车轴在受到横向荷载作用下的变形情况,而扭转刚度是指车轴在受到扭矩作用下的变形情况。
车轴受力分析

基于日本标准的强度分析采用日本JIS.E.4501铁道车辆车轴强度设计方法和JIS.E.4502铁道车辆车轴品质要求,对CRH2动车组非动力车轴进行疲劳强度计算和分析。
日本的车轴疲劳强度计算中考虑了车体振动引起的垂向和横向加速度对弯曲应力的影响,不过动载荷系数的取法与欧洲有所不同,在欧洲标准中,一般垂向动态载荷系数α=O.25,横向动态载荷系数卢β=0.175,日本标准中的动态载荷系数日本JIS车轴的受力简图然后通过相关资料找到ZMA120型车非动力车轴参数如下表: dmm rmm j mm g mm a mm h mm x mmy mm l mm 2028402100149317014006372135其中轴重为14t,经换算得到W=137.2kn V Km/h Av Al W kn P kn Q0knR0kn 80 0.42 0.20 137.2 27.44 18.29 41.17 100 0.52 0.24 137.2 32.93 21.93 49.41 1200.620.28137.238.4225.6157.64轮座处得许用应力awb 取147Mpa ,该车轮处得弯矩、应力计算结果和安全系数列于下表一 车轴的强度分析(一)基于日本标准的强度校核采用日本JIS .E .4501铁道车辆车轴强度设计方法和JIS .E .4502铁道车辆车轴品质要求,对A 型080城轨车辆非动力车轴进行疲劳强度计算和分析。
日本的车轴疲劳强度计算中考虑了车体振动引起的垂向和横向加速度对弯曲应力的影响,不过动载荷系数的取法与欧洲有所不同,在欧洲标准中,一般垂向 动态载荷系数为O .25,横向动态载荷系数为0.175,它们与车辆的运行速度无关;而日本标准中,动态载荷系数取决于运行线路和速度,具体的取值见下表。
日本标准中的动态载荷系数线路状态等级速度V km/hαvαl改进的高速线 SA200—3500.0027v0.030+0.00060 v高速线A A 150-280 0.0027v 0.030+0.00085 v 改进的既有线A A60—160 0.0027v 0.040+0.0012 v<60 0.16 O .11 既有线BB 60~1300.0052v0.060+0.0018 v<60 0.31 0.17符号说明符号说明单位a mm d 轮座径mmg 车轮踏面间距离mmh mm j mm l mm r 车轮踏面半径mm Z 轴轮座处抗弯截面模数mm*mm P 横向力N Q. 颈上的垂向力,N R. P引起的踏面上的垂向力N W 车辆轴重N M1 轮座处P引起的弯曲力矩mN*m M2 轮座处垂向动态载荷引起的弯曲力矩mN*m M3 轮座处横向力引起的弯曲力矩mN*m σb 轮座处的弯曲应力N/mm σwb N/mm σLσv 垂向动态载荷系数m 安全系数n 疲劳安全率G 车轴重心V 使用最高速度车轴受力简图车轴相关参数列表。
机车车轴的受力分析原理

机车车轴的受力分析原理
机车车轴的受力分析原理涉及静力学和材料力学的知识。
首先,机车车轴在运行过程中承受来自轮对、轴承、传动装置等部件的各种受力。
在受力分析中,我们通常会考虑以下几个方面:
1. 轴向受力:轴向受力包括来自轮对的牵引力和制动力,以及来自传动装置的推力等。
这些受力会导致车轴产生轴向应力和变形,需要保证车轴材料的强度和刚度足够以承受这些受力。
2. 弯曲受力:当车轴受到侧向力或者车辆经过曲线轨道时,车轴会发生弯曲受力。
这会导致轴上不同截面的受力情况不同,最大弯矩通常出现在车轮所在位置。
通过弯曲受力分析,可以确定车轴的弯曲刚度和强度要求,确保车轴不会发生断裂或者过度变形。
3. 扭转受力:车轴在运行过程中还会发生扭转受力。
扭转受力由于传动装置的传动力矩和侧向力的作用而产生,会导致车轴发生扭转变形和应力,需要保证车轴材料的扭转刚度和强度以承受这些受力。
以上三种受力的分析可以通过静力学的原理和材料力学的理论进行分析。
常用的分析方法包括受力面积法、受力平衡法、应力分布法等。
采用这些方法可以得到
车轴不同截面上的受力情况,并通过比较这些受力与车轴材料的强度和刚度要求来确定车轴设计的合理性。
同时,还需要考虑到车轴的使用寿命、负荷集中、疲劳断裂等因素,以确保车轴的安全可靠性。
CRH2动车组车轴的CAD-CAE分析
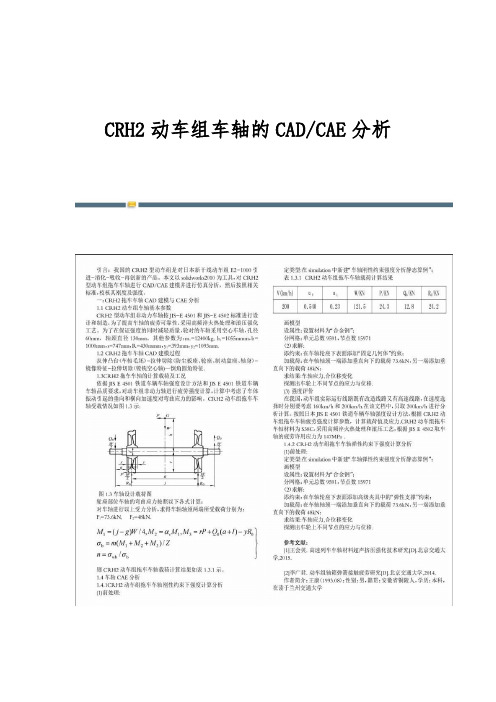
CRH2动车组车轴的CAD/CAE分析引言:我国的CRH2型动车组是对日本新干线动车组E2-1000引进-消化-吸收-再创新的产品。
本文以solidworks2010为工具,对CRH2型动车组拖车车轴进行CAD/CAE建模并进行仿真分析,然后按照相关标准,校核其刚度及强度。
一:CRH2拖车车轴CAD建模与 CAE分析1.1 CRH2动车组车轴基本参数CRH2 型动车组非动力车轴按JIS-E 4501和JIS-E 4502标准进行设计和制造,为了提高车轴的疲劳可靠性,采用高频淬火热处理和滚压强化工艺。
为了在保证强度的同时减轻质量,轮对的车轴采用空心车轴,孔径60mm,轴颈直径130mm。
其他参数为:m1=12400kg, h1=1055mmm,b=1000mm,s=747mm,R=430mmm,y1=393mm,y2=1093mm.1.2 CRH2拖车车轴CAD建模过程拉伸凸台(车轴毛坯)-拉伸切除(防尘板座、轮座、制动盘座、轴身)-镜像特征-拉伸切除(镗铣空心轴)—倒角圆角特征.1.3CRH2拖车车轴的计算载荷及工况依据JIS E 4501 铁道车辆车轴强度设计方法和JIS E 4501 铁道车辆车轴品质要求,对动车组非动力轴进行疲劳强度计算,计算中考虑了车体振动引起的垂向和横向加速度对弯曲应力的影响。
CRH2动车组拖车车轴受载情况如图1.3示:图1.3车轴设计载荷图轮座部位车轴的弯曲应力按照以下各式计算:对车轴进行以上受力分析,求得车轴轴颈两端所受载荷分别为:F1=73.6kN, F2=48kN.则CRH2动车组拖车车轴载荷计算结果如表1.3.1示。
1.4车轴CAE分析1.4.1CRH2動车组拖车车轴刚性约束下强度计算分析(1)前处理:定类型:在simulation中新建“车轴刚性约束强度分析静态算例”;画模型设属性:设置材料为“合金钢”;分网格:单元总数9591,节点数15971(2)求解:添约束:在车轴轮座下表面添加“固定几何体”约束;加载荷:在车轴轴颈一端添加垂直向下的载荷73.6kN,另一端添加垂直向下的载荷48kN;求结果:车轴应力,合位移变化探测出车轮上不同节点的应力与位移.(3)强度评价在我国,动车组实际运行线路既有改造线路又有高速线路,在速度选择时分别要考虑160km/h和200km/h.在该文档中,只取200km/h进行分析计算。
[笔记]矿用汽车传动轴的受力分析
![[笔记]矿用汽车传动轴的受力分析](https://img.taocdn.com/s3/m/fbe3a011eef9aef8941ea76e58fafab069dc44ba.png)
矿用汽车传动轴[摘要]万向节传动装置由万向节、传动轴及中间支承组成。
在矿用汽车上广泛应用刚性十字轴式双万向节传动轴。
对于传动轴的使用、故障分析、维护保养应该注意的事项。
叙词:矿用汽车传动轴应用维护传动轴的受力分析在汽车上,万向传动装置最重要的使用场合是连接变速器第二轴(或分动器输出轴)与主减速器的输入轴。
另外,有的汽车由于总体布置重要,在发动机和变速箱之间不直接连接而离开一定距离,为避免因安装不准确和车架变形,使名义上同心的两轴之间可能出现的倾角和偏移,也使用万向传动装置。
万向传动装置由万向节、传动轴及中间支承所组成。
万向节按钮转方向是否有明显的弹性可分为刚性万向节和挠性万向节两类。
刚性万向节又分为不等速万向节(常用的为普通十字轴式)、等速万向节和准等速万向节三种。
本文仅讨论普通十字轴式刚性万向节传动装置。
矿用汽车由于轴距较短,在变速箱输出轴和后驱动桥主减速器输入间普遍采用没有中间支承的单轴普通双刚性万向节传动轴的总成传动。
当被连接的两根轴不在同一直线上而采用一个十字轴式万向节传动时,从动轴旋转的角度是不均匀的。
其运动学特点简单分析如下。
设主动叉轴与从动叉轴夹角为α,主动叉轴以等角速度ω1旋转,十字轴万向节转动半径为r。
先看两个特殊位置的速度:(1)主动叉在垂直位置,并且十字轴平面与主动轴垂直,如图1a)所示。
主动叉与十字轴连接点a的线速度V a在十字轴平面内,V a=ω1r;从动叉与十字轴连接点b的线速度V b在与主动叉平行的平面内,并且垂直于从动轴,点b的线速度V b可分解为在十字轴平面内的速度V'b和垂直于十字轴平面的速度V"b。
由速度直角三角形可看出在数值上V b>V'b。
十字轴是对称的,oa=ob。
当万向节传动时,十字轴是绕O点转动的,其上a、b两点于十字轴平面内的线速度在数值上应相等,即V'b=Vα,因此V b>V a。
因此可知,当主从动叉转到所述位置时,从动轴的转速大于主动轴的转速。
车轴分析报告

车轴分析报告1. 背景介绍车轴是指汽车上承受车身重荷并实现动力传递的核心部件,其质量和性能直接影响车辆的行驶稳定性和安全性。
本文旨在对车轴进行分析,探讨其结构设计、制造工艺以及常见故障等方面的内容。
2. 车轴的结构设计车轴通常由轴心、端头和轴颈组成,其中轴心是车轴的主体部分,用于支撑整个车辆重量。
轴颈是轴心两端的圆柱形部分,用于支撑车轮安装的轴承,并通过这些轴承传递动力。
端头是连接轴心和轴颈的部分,起到加强整体结构的作用。
车轴的结构设计需要考虑车辆重量、载荷、行驶速度以及道路条件等因素。
一般来说,车轴需要具备足够的强度和刚度,以承受各种力的作用,并保持其形状稳定不易变形。
此外,还需要注意轴颈与轴承之间的配合性,以及轮胎与轮毂之间的匹配情况。
3. 车轴的制造工艺传统的车轴制造工艺包括锻造、车削、热处理和磨削等工序。
首先,使用锻造工艺将原材料锻造成近似形状的圆柱体,然后使用车削工艺进一步加工得到最终的轴心和轴颈形状。
接下来,利用热处理工艺对车轴进行淬火、回火等热处理,以提高其强度和硬度。
最后,使用磨削工艺对轴颈进行磨削,以达到较高的制造精度。
近年来,随着先进制造技术的发展,车轴的制造工艺也在不断改进。
比如,引入数控车床、磨床等先进设备,能够更精确地加工车轴的各个部分;采用高强度钢材或复合材料制造车轴,可以提高车轴的强度和耐疲劳性能。
4. 车轴的常见故障车轴作为汽车的承重部件,长期以来承受着巨大的力和振动,容易出现各种故障。
常见的车轴故障包括以下几种:4.1 轴颈磨损由于长期受到轮毂和轮胎的载荷和摩擦作用,轴颈容易发生磨损。
轴颈磨损会导致轴颈与轴承之间的间隙变大,从而引起车轴的松动,进而影响车辆的行驶稳定性。
4.2 轴颈断裂车轴在长时间高速运行过程中,由于疲劳载荷的作用,轴颈可能发生断裂。
轴颈的断裂会导致车轮脱离轴承支撑,引发严重的交通事故。
4.3 车轴扭曲车轴在碰撞或超载等恶劣条件下,可能会发生扭曲变形。
大轴重机车车轴疲劳强度计算分析

对 于 每个截 面 , 通过 合力 矩 MR来 计算 最 大应力 , 合 力矩 MR的计算 公式 为
力矩 和制动力矩 不会 同时发 生 , 故 这里仅考 在前面 2 种 类 型 的力 和力矩 。
1) 运行 中 车轴负 荷 的作用
M R= 4 a / o : + MY + MZ
第 2期
吴 仲 刘 ,雷 成 , 肖守 讷 , 阳光 武 :大轴 重机 车 车 轴疲 劳 强 度计 算分 析
辆 轮对 组 装 技术 条 件 》 , 轮 轴 装 配 过盈 量 为 轮 座 直径
的0 . 0 8 %~ 0 . 1 5 %, 故 本 文 中过 盈量 取 为 0 、 0 . 2 0 mm、
应 力 为
K ×3 2×』
= — —— —— —: — —一
上 的垂直 反作用力 , , , 为齿轮侧 抱轴承处 的振动力 , 为从 动齿 轮质 量产 生 的振 动力 , F 为非齿 轮侧 抱轴 承 处 的振 动 力 。 这 些 力值 的 确 定根 据标 准进 行计 算 , 通
过该受 力 图可计 算 出每一截 面上 向弯矩 。
颈、 轮 座 处 产 生 相 反 方 向 的 纵 向力 , 产 生 制 动 弯 矩
,
该 弯矩 在 负 载
面 和 滚动 面之 间为
M z : F f Rb
y .
在 滚 动 面 之 间 为
=
圭
鲁
一
图3
一
向 制动 力矩
L _ -
见 图 4 ;在负 载面 和 滚 动 面之 间扭 力
一 -
r r c l
( 2)
式中: 为疲 劳应力集 中系数 , 其值 可 以通过查 标准进 行计 算 。 这样 可以计算 出选取 的 1 3 个截 面处 的应 力值 , 而
高速轮轴受力分析与设计研究

高速轮轴受力分析与设计研究随着我国高速铁路的持续发展,铁路运输的发展已经成为国家的重要战略。
而铁路运输的一个非常重要的组成部分就是高速列车,而高速列车的发展离不开高速铁路轮轴的研究与设计。
因为高速铁路轮轴非常关键,一旦轮轴出现问题,不仅会影响行车安全,同时还会对乘客的生命造成严重危害,因此,研究轮轴的受力分析与设计成为了重要的课题。
1.高速轮轴的基本要求高速轮轴的车轴负责支撑整个车辆的重量,并为轮胎提供安全的支撑力。
同时,高速轮轴还需要保证列车的高速行驶稳定性和安全性,因此具有以下几个基本要求:1.1高强度在高速行驶时,轮轴需要承受高载荷和高速度的作用,因此轮轴具有高度的强度和刚度。
同时,轮轴应具有优秀的抗疲劳强度,以保证在长期使用期间不断开裂或疲劳失效。
1.2低以及稳定的轴向力和径向力轮轴的运动不能给列车带来较大的颠簸和震荡。
在高速行驶时,轮轴应当具备良好的动静平衡性能,以减轻列车的振动和噪声。
因此,轮轴的轴向力和径向力需要保持在低水平,且应当具备稳定性。
1.3满足使用寿命高速列车的安全与使用寿命息息相关。
轮轴的设计应当满足车辆运行寿命,以保证耐磨、耐腐蚀、不断开裂或转折失效。
这通常需要使用耐久、高强度、高硬度的轴承钢材。
2.高速轮轴的受力分析与设计轮轴是高速列车的重要部分,因此,轮轴的受力分析与设计需要注重细节和精度,这对于列车行驶的平稳性和行车安全具有重要意义。
首先,轮轴的设计需符合列车的速度、载荷和几何特征等要求。
于此同时,也要考虑轮轴的材料和结构,确定轮轴的强度、刚度等性能并进行优化。
在轮轴的设计中,需要详细分析轮轴的受力特性。
轮轴在运转过程中受到轴向力、径向力和弯曲力等多种作用力,这些力量需要被详细地进行计算和分析。
在确定这些作用力之后,才能进行轮轴的结构设计和材料选择等工作。
在轮轴的受力分析中,有两种主要的方法:静力分析和动力分析。
静力分析是基于轮轴受力的静态分布,通过数学公式计算每个部位的受力,从而确定轮轴的结构和材料。
轴受力分析

一、轴上零件的装配方案 据轴上零件定位、加工要求以及不同的零件装配方案, 据轴上零件定位、加工要求以及不同的零件装配方案,参考 轴的结构设计的基本要求, 轴的结构设计的基本要求,得出如图所示的两种不同轴结 构。
二、轴上零件的固定 1、轴上零件的定位 、 ----阶梯轴上截面变化之处 轴肩及轴环----阶梯轴上截面变化之处。 轴肩及轴环----阶梯轴上截面变化之处。 零件的轴向定位由轴肩(轴环)或套筒来实现。 零件的轴向定位由轴肩(轴环)或套筒来实现。 轴向定位由轴肩
第二节 轴的结构分析
轴的结构分析: 包括定出轴的合理的 轴的结构分析 : 包括定出轴的 合理的 外形和全部结构尺寸 1.轴应便于制造,轴上零件要易于装拆; 轴应便于制造,轴上零件要易于装拆; 轴应便于制造 (制造安装 制造安装) 制造安装 2.轴和轴上零件要有准确的工作位置; 轴和轴上零件要有准确的工作位置; 轴和轴上零件要有准确的工作位置 (定位 定位) 定位 3.各零件要牢固而可靠地相对固定; 各零件要牢固而可靠地相对固定; 各零件要牢固而可靠地相对固定 固定) (固定 固定 4.改善应力状况,减小应力集中。 改善应力状况, 改善应力状况 减小应力集中。
轴的设计过程: 轴的设计过程: 轴的结构设计: 轴的结构设计: 根据轴上零件的安装、 根据轴上零件的安装、 定位以及轴的制造工艺等 方面的要求, 方面的要求,合理地确定 轴的结构形式和尺寸。 轴的结构形式和尺寸。
选择材料 结构设计 轴的承载能力验算 验算合格? 验算合格 Y 结束 N
工作能力计算: 工作能力计算: 轴的承载能力验算指的是轴的强度、 轴的承载能力验算指的是轴的强度、刚度和振动 稳定性等方面的验算。 稳定性等方面的验算。
对应力集中的敏感性低,加工工艺性好,故应用最广, 对应力集中的敏感性低,加工工艺性好,故应用最广, 对于不 重要或受力较小的轴也可用Q235A等普通碳素钢。 等普通碳素钢。 重要或受力较小的轴也可用 等普通碳素钢
动车车轴的力学性能分析及优化

动车车轴的力学性能分析及优化摘要:随着高速铁路的发展,动车车辆在运行过程中所承受的压力和振动越来越大,车轴作为传递力量和支撑车辆的重要部件,其力学性能分析及优化显得尤为重要。
本文通过对动车车轴的力学性能进行研究和分析,提出了相应的优化方案,从而提高动车车轴的使用寿命和可靠性。
1. 引言高速动车的发展已经成为现代化交通工具的重要组成部分,然而,高速动车在高速运行过程中所受到的压力和振动会对其组成部件产生一定的影响,尤其是车轴。
对于车轴的力学性能分析及优化,可以提高车轴的使用寿命和可靠性,降低事故风险。
2. 动车车轴的力学性能分析2.1 车轴的受力分析动车车轴在高速运行中受到的受力主要包括轴向力、弯曲力和扭转力。
轴向力是由牵引力和阻力产生的,弯曲力和扭转力则是由弯曲和扭转运动产生的。
通过对动车轴受力的分析,可以了解车轴在高速运行中的力学特性。
2.2 车轴的应力分析车轴在承受力的同时,还会产生一定的应力。
在动车车轴的应力分析中,主要考虑的因素包括弯曲应力、剪切应力和挤压应力。
通过对车轴应力的分析,可以评估车轴的强度是否满足设计要求,并采取相应的优化措施。
3. 动车车轴的力学性能优化3.1 材料优化车轴材料的选择对其力学性能有着重要影响。
通常情况下,动车车轴的材料应具有高强度、高刚度和良好的耐疲劳性能。
传统的车轴材料包括碳钢和合金钢等,然而,随着材料科学的发展,新型材料如高强度钢和复合材料也逐渐应用于动车车轴中。
通过优化车轴材料的选择,可以提高车轴的强度和耐疲劳性能。
3.2 结构设计优化通过合理的结构设计,可以改善动车车轴的力学性能。
例如,采用中空结构可以减轻车轴自重,降低其弯曲应力和挤压应力。
此外,加强车轴的轴肩和轴芯连接处,可以提高其承载能力和抗疲劳性能。
通过对车轴结构的优化设计,可以提高车轴的寿命和可靠性。
3.3 热处理优化热处理是改善车轴材料性能的重要方法之一。
通过适当的热处理工艺,可以提高车轴的强度和硬度,进一步提高车轴的疲劳寿命。
多轴汽车轴荷的分析与计算
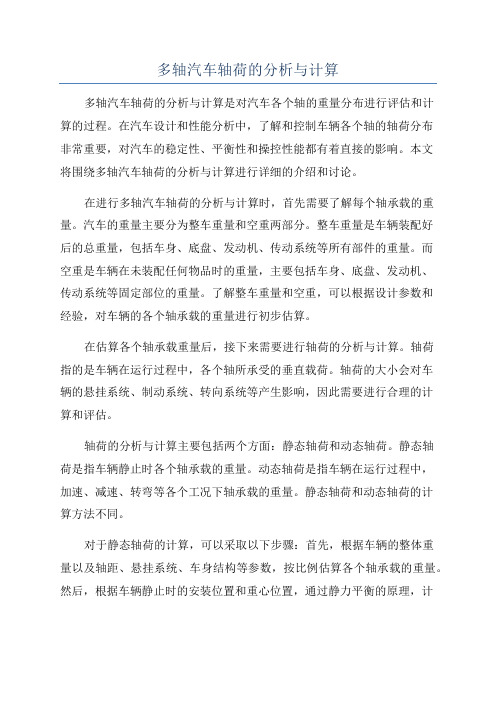
多轴汽车轴荷的分析与计算多轴汽车轴荷的分析与计算是对汽车各个轴的重量分布进行评估和计算的过程。
在汽车设计和性能分析中,了解和控制车辆各个轴的轴荷分布非常重要,对汽车的稳定性、平衡性和操控性能都有着直接的影响。
本文将围绕多轴汽车轴荷的分析与计算进行详细的介绍和讨论。
在进行多轴汽车轴荷的分析与计算时,首先需要了解每个轴承载的重量。
汽车的重量主要分为整车重量和空重两部分。
整车重量是车辆装配好后的总重量,包括车身、底盘、发动机、传动系统等所有部件的重量。
而空重是车辆在未装配任何物品时的重量,主要包括车身、底盘、发动机、传动系统等固定部位的重量。
了解整车重量和空重,可以根据设计参数和经验,对车辆的各个轴承载的重量进行初步估算。
在估算各个轴承载重量后,接下来需要进行轴荷的分析与计算。
轴荷指的是车辆在运行过程中,各个轴所承受的垂直载荷。
轴荷的大小会对车辆的悬挂系统、制动系统、转向系统等产生影响,因此需要进行合理的计算和评估。
轴荷的分析与计算主要包括两个方面:静态轴荷和动态轴荷。
静态轴荷是指车辆静止时各个轴承载的重量。
动态轴荷是指车辆在运行过程中,加速、减速、转弯等各个工况下轴承载的重量。
静态轴荷和动态轴荷的计算方法不同。
对于静态轴荷的计算,可以采取以下步骤:首先,根据车辆的整体重量以及轴距、悬挂系统、车身结构等参数,按比例估算各个轴承载的重量。
然后,根据车辆静止时的安装位置和重心位置,通过静力平衡的原理,计算各个轴承载的重量。
最后,通过实际测试或数值仿真的方式,对计算结果进行验证和调整。
对于动态轴荷的计算,需要考虑车辆在加速、减速、转弯等工况下的轴承载重量的变化。
一种常用的方法是采用转向组角动力学原理,根据车辆的速度、加速度、曲率等参数,计算各个工况下的轴承载重量。
另一种方法是通过实际测试和测量,获取车辆在不同工况下的轴荷数据,并进行分析和统计。
需要注意的是,多轴汽车轴荷的分析与计算是一个复杂的过程,需要考虑许多因素,如车辆的结构、悬挂系统、动力系统、车速、路况、驾驶员行为等。
空心车轴强度计算分析

—384—创新观察空心车轴强度计算分析李保鑫 初 艳 于 跃 (中车大连机车车辆股份有限公司,辽宁 大连 116021)摘 要:为保证列车行车安全,对空心车轴进行了计算分析。
根据标准EN13104,选取空心车轴20个截面,计算出各个截面的等效应力。
利用Hypermesh 和Ansys 软件对空心车轴进行有限元分析,并进行对比验证。
结果表明,两种方法计算的车轴最大应力的截面均位于车轴轮座缓和槽结合处,车轴任一截面的应力均小于其许用应力,计算结果满足车轴强度设计要求。
关键词:空心车轴;有限元;车轴强度前言车轴是转向架的主要承载部件,其强度大小决定了车辆的行车安全。
由于转向架轻量化的要求,空心车轴应用越来越广泛,因此对空心车轴进行强度校核是非常必要的。
目前,车轴强度计算方法主要有以下两种:一、是按照行业标准对车轴进行强度校核,常用的标准有日本JIS 标准、欧盟的标准以及中国的TB 标准;二、是在各个标准的基础上利用有限元软件进行仿真计算[1]。
本文利用欧盟的EN13104标准对空心车轴进行强度计算。
此外,利用Hypermesh 软件和ANSYS 软件对车轴进行静强度分析,从而利用两种方法对车轴强度分析进行对比验证。
1.车轴受力分析车辆运行过程中,车轴承担的载荷主要分为簧上和簧下的质量载荷,基础制动产生的载荷,以及驱动系统产生的载荷。
1.1簧上簧下质量载荷受力分析车辆在运行过程中簧上簧下质量振动下轮对受力主要包括分左右侧轴颈的垂向力,轨道对车轮的垂向力,轨道对车轮的横向力,大齿轮振动产生的惯性力。
1.2.制动载荷转向架采取轮盘制动方式。
根据EN13104标准,制动工况下产生的载荷主要分为三部分,在轴颈、轮座处产生相反的垂向力和纵向力。
1.3驱动载荷驱动载荷主要分为两部分,一是由驱动扭矩产生的作用于车轮的牵引力,二是由驱动齿轮作用于驱动大齿轮的啮合力产生的作用于轴颈的垂向力和纵向力。
2.截面应力分析车轴强度分析的危险截面出现在截面弯矩最大、截面尺寸较小、截面突变(或应力集中)和过盈配合等区域,因此在分析中确定20个危险计算截面,其位置如图1所示。
轴受力分析

重点、难点: 重点、难点:
1)轴的分类。 )轴的分类。 2)轴的结构问题。 )轴的结构问题。
钢代替碳素钢刚度,收效甚微。
第一章 多媒体CAI课件设计基础
18.3 轴的结构设计
•设计实质:确定轴的合理外形和包括各轴段长度、直径及 设计实质:确定轴的合理外形和包括各轴段长度、 设计实质
其他细小尺寸在内的全部结构尺寸。 其他细小尺寸在内的全部结构尺寸。
•决定因素:轴的毛坯种类,轴上作用力的大小和分布情况, 决定因素:轴的毛坯种类,轴上作用力的大小和分布情况, 决定因素
轴上零件的布置及固定方式,轴承类型及位置, 轴上零件的布置及固定方式,轴承类型及位置,轴的加工和 装配工艺性以及其他一些要求。 装配工艺性以及其他一些要求。
•注意:轴的结构受多方面因素的影响,且其结构形式又 注意:轴的结构受多方面因素的影响, 注意
2.轴的各段长度 轴的各段长度 •注意问题 : 注意问题
1)轴颈的长度通常与轴承的宽度相同; 1)轴颈的长度通常与轴承的宽度相同; 轴颈的长度通常与轴承的宽度相同 2)轴头的长度取决于与其相配合的传动零件轮毂的宽度 轴头的长度取决于与其相配合的传动零件轮毂的宽度, 2)轴头的长度取决于与其相配合的传动零件轮毂的宽度, 若该零件需在轴向固定, 若该零件需在轴向固定,则应使轴头长度较所装零件轮毂的 宽度小2~ 宽度小 ~3mm,以便将零件沿轴向夹紧,保证其固定的可 ,以便将零件沿轴向夹紧, 靠性 ; 3)轴环宽度一般取为 3)轴环宽度一般取为b=(0.1~0.15)d, ~ , 或b ≈1.4h,并圆整为整数, ,并圆整为整数,
轴受力分析-精选文档80页

举例:计算某减速器高速轴危险截
a
面的直径。已知作用在齿轮上的圆
周力Ft=17400N, 径向力,
d
Fr=6140N, 轴向力Fa=2860N,齿轮分 度圆直径d2=146 mm,作用在轴右端 带轮上外力F=4500N(方向未定),
L/2 a L
K
1 Ft Fr Fa 2
F
L=193 mm, K=206 mm
材料
σb
[σ+1]
[σ0]
[σ-1]
脉400动循环状态下130的
70
40
碳素钢
500许用弯曲应力170
75
45
600
200
95
55
700
230
110
65
800
合金钢
900
270
130
75
300
140
80
1000
330
150
90
铸钢
400
500
100
50
30
120
70
40
折合系数取值:α=
0.3 ----转矩不变; 0.6 ----脉动变化; 1 ----频繁正反转。
圆螺母
特点:定位可靠,装拆方便,可承受较大的轴向力 由于切制螺纹使轴的疲劳强度下降 应用:常用于轴的中部和端部
弹性挡圈
特点:结构简单紧凑,只能承受很小的轴向力。 应用:常用于固定滚动轴承等的轴向定位
轴端压板 特点:可承受剧烈振动和冲击。 应用:用于轴端零件的固定,
紧定螺钉
特点:可承受很小的轴向力。 应用:适用于轴向力很小,转速 低的场合
d2 Fr Fa FA =Fa
F1v
基于solidworks的车床主轴受力分析

基于solidworks的车床主轴受力分析今天,随着建筑行业的发展,车床主轴受力分析变得越来越重要。
为了更好地了解车床主轴的受力特性,需要研究者采用精确的工具和技术。
因此,本文旨在分析基于Solidworks的车床主轴受力分析方法。
首先,本文介绍了车床主轴受力分析的基本原理,包括轴承、轴节和主轴的力学性能。
然后,本文详细介绍了基于Solidworks的受力分析的具体实现过程,从模型的建立到模拟的确定,再到测试的结果可视化。
最后,本文分析了车床主轴受力分析中可能出现的问题,并对如何提高分析的准确性提出了解决方案。
车床主轴受力分析属于机械分析中的重要组成部分,主要研究轴上发生的变形和强度。
近年来,通过技术的发展,许多机械工程师拥有使用多种有效工具进行车床主轴受力分析的能力。
Solidworks是一款功能强大的CAD设计软件,它可以进行参数化设计,同时提供了一个完整的受力分析环境,被广泛用于车床主轴受力分析中。
而且,Solidworks还可以让研究者在虚拟的分析环境中模拟实际的受力情况,有助于及时掌握实际情况,更有效地控制和优化车床主轴的受力特性。
车床主轴受力分析过程主要分为四个步骤:建模、约束、分析和可视化。
对于建模,首先,利用Solidworks可以快速准确地构建车床主轴的三维模型,包括轴承、轴节和主轴,有助于实现轻量级设计,从而提高设备的可靠性。
接下来,需要添加一些约束条件,以确定分析的范围,并确定轴的受力特性。
在分析环节,研究者可以有效地采用Solidworks的分析功能,实现多种类型的分析,如力学、热传导和波动分析等,以模拟和预测车床主轴的变形和应力分布情况。
最后,通过Solidworks可视化功能,可视化显示车床主轴受力分析的结果,以方便研究者分析结果,指导实际设计和控制。
在车床主轴受力分析中,仍然存在一些技术挑战。
其中,建模和约束的正确性是分析的基础,但建模和约束的过程仍然存在不少困难,尤其是在确定各部分约束时,误差可能会较大,从而导致计算结果不准确。
汽车传动轴中间支撑及变速器输出轴受力分析(1)

-74-科技论坛汽车传动轴中间支撑及变速器输出轴受力分析王恩伟(沈阳金亚汽车传动轴有限公司,辽宁沈阳110045)随着社会的不断进步,经济高速发展,汽车走进人们的生活之中,人们对汽车的追求逐渐增加,购车辆逐渐上升。
在汽车的组成构建中,汽车传动轴扮演着重要的角色,就汽车传动轴中间支撑及变速器输出轴受力进行分析。
1关于汽车传动轴汽车传动轴担负着变速器(或分动器)到减速器的力矩传递任务,是汽车较重要的总成之一。
当传动轴分段时需加中间支承。
在长轴距汽车上,为提高传动轴临界转速,减小万向节夹角,以及布置上的需要,常将传动轴分段。
在轿车中,有时为了提高传动系的弯曲刚度,改善传动系弯曲振动特性,减少噪声,而将传动轴分成两段。
中间支承安装在车架横梁上,或车身底架上。
由于动力总成弹性悬置和车架变形,被支承的中间传动轴轴线位置,相对于中间支承的安装面随时在变化,因此要求中间支承能适应这种变化。
中间支承及变速器输出轴所承受的扭矩与中间支承的布置有关。
笔者仅以载货汽车十字轴万向节式传动轴为例,对传动轴在扭矩传递中,中间支承支座反力与变速器输出轴的受力特性给予分析。
2关于汽车传动轴的布置形式当传动距离较远,采用两节传动轴、三个万向节时,其布置型式有以下两种。
2.1中间传动轴与变速器输出轴近似在一条直线上,则第一个万向节不起改变角速度的作用,此时也相当于一节传动轴,两个万向节,如图1(a)所示。
2.2变速器输出轴、中间传动轴和主传动轴的3条轴线不在一条直线上。
当汽车满载时,由于弹性悬架的变形较大,使中间传动轴和主传动轴近似在一条直线上,相当于只有一节传动轴、两个万向节,中间万向节不起改变角速度的作用如图1(b)所示。
3关于汽车传动轴中间支撑的受力分析设中间支承在万向节的十字轴O 2上,若将万向节的十字轴节O 1、O 2、O 3看成无限小,则十字轴O 3传递给主传动轴3的横向力偶M33′,它是由中间支承O 2和主减速器输入轴4上十字轴中心O 3的一对F3力来平衡。
- 1、下载文档前请自行甄别文档内容的完整性,平台不提供额外的编辑、内容补充、找答案等附加服务。
- 2、"仅部分预览"的文档,不可在线预览部分如存在完整性等问题,可反馈申请退款(可完整预览的文档不适用该条件!)。
- 3、如文档侵犯您的权益,请联系客服反馈,我们会尽快为您处理(人工客服工作时间:9:00-18:30)。
基于日本标准的强度分析
采用日本JIS.E.4501铁道车辆车轴强度设计方法和JIS.E.4502铁道车辆车轴品质要求,对CRH2动车组非动力车轴进行疲劳强度计算和分析。
日本的车轴疲劳强度计算中考虑了车体振动引起的垂向和横向加速度对弯曲
应力的影响,不过动载荷系数的取法与欧洲有所不同,在欧洲标准中,一般垂向动态载荷系数α=O.25,横向动态载荷系数卢β=0.175,
日本标准中的动态载荷系数
日本JIS车轴的受力简图
然后通过相关资料找到
ZMA120型车非动力车轴参数如下表: d
mm r
mm j mm g mm a mm h mm x mm
y mm l mm 202
840
2100
1493
170
1400
63
72
135
其中轴重为14t
,经换算得到W=137.2kn V Km/h Av Al W kn P kn Q0
kn
R0
kn 80 0.42 0.20 137.2 27.44 18.29 41.17 100 0.52 0.24 137.2 32.93 21.93 49.41 120
0.62
0.28
137.2
38.42
25.61
57.64
轮座处得许用应力awb 取147Mpa ,该车轮处得弯矩、应力计算结果和安全系数列于下表
一 车轴的强度分析
(一)基于日本标准的强度校核
采用日本JIS .E .4501铁道车辆车轴强度设计方法和JIS .E .4502铁道车辆车轴
品质要求,对A 型080城轨车辆非动力车轴进行疲劳强度计算和分析。
日本的车轴疲劳强度计算中考虑了车体振动引起的垂向和横向加速度对弯曲
应力的影响,不过动载荷系数的取法与欧洲有所不同,在欧洲标准中,一般垂向 动态载荷系数为O .25,横向动态载荷系数为0.175,它们与车辆的运行速度无关;
而日本标准中,动态载荷系数取决于运行线路和速度,具体的取值见下表。
日本标准中的动态载荷系数
线路状态
等级
速度V km/h
αv
αl
改进的高速
线 SA
200—350
0.0027v
0.030+0.00060 v
高速线A A 150-280 0.0027v 0.030+0.00085 v 改进的既有
线A A
60—160 0.0027v 0.040+0.0012 v
<60 0.16 O .11 既有线B
B 60~130
0.0052v
0.060+0.0018 v
<60 0.31 0.17
符号说明
符号说明单位a mm d 轮座径mm
g 车轮踏面间距离mm
h mm j mm l mm r 车轮踏面半径mm Z 轴轮座处抗弯截面模数mm*mm P 横向力N Q. 颈上的垂向力,N R. P引起的踏面上的垂向力N W 车辆轴重N M1 轮座处P引起的弯曲力矩mN*m M2 轮座处垂向动态载荷引起的弯曲力矩mN*m M3 轮座处横向力引起的弯曲力矩mN*m σb 轮座处的弯曲应力N/mm σwb N/mm σL
σv 垂向动态载荷系数
m 安全系数
n 疲劳安全率
G 车轴重心
V 使用最高速度
车轴受力简图
车轴相关参数列表。
d mm
r
mm
j
mm
g
mm
a
mm
h
mm
x
mm
y
mm
l
mm
202 840 2100 1493 170 137.2 63 72 135 根据标准JIS.E.4501,车轴轮座位置的弯曲应力由下式确定:
在我国,动车组实际运行线路既有改进的既有线路又有客运专线,并且很快将有满足90km/h时速的高速线路,所以在计算中,车辆的运行速度按照不同的线路情况选取,分别取为90km/h、80km/h和60km/h。
车轴的动态载荷系数和载荷计算结果列于下表
A 型地铁080车辆非动力车轴载荷计算结果
V km/h σv σL W
kN
P
kN
Q.
kN
R.
kN
80 0.42 0.20 137.2 27.4 18.3 41.2
100 0.52 0.24 137.2 32.9 21.9 49.4 120 0.62 0.28 137.2 38.4 25.6 57.6 轮座处的许用应力取147MPa,该车轴轮座处的弯矩、应力计算结果和安全系数列于表
A型地铁转向架非动力车轴轮座处的应力计算结果
V km/h
M1
Kn*mm
M2
kN*mm
M3
kN*mm
σb
Mpa
n
60 17405 2785 9363 62.2 2.4
80 17405 3759 10291 67 2.2
90 17405 4229 11268 70 2.1
A型地铁转向架车轴材料为25CrMo4,采用高频淬火热处理和滚压工艺,根据JIS.E.4502取车轴轮座处的疲劳许用应力为147MPa。
由表5.10可见,A 型地铁转向架非动力车轴轮座处的最大弯曲应力为70MPa,出现在时速90km/h 的运行条件下,远小于材料的许用应力,安全裕度较大。
因此,按照日本标准,该车轴满足强度设计要求。
(二)欧洲标准与日本标注车轴强度分析的比较
通过采用欧洲标准和日本标准对arm0808型车城轨车辆非动力车轴进行强度分析,可以发现,两种标准计算车轴强度有很大区别,主要体现在以下方面:
1. 强度计算的部位不同。
日本标准重点考虑轮座部位的疲劳强度,而欧
洲标准考虑了轴上各个部位的疲劳强度。
图5.10示出了车轴压装部位的形状简图,
欧洲车轴采用大直径比D/d和小过渡圆角半径厂,由于高的应力集中使其过渡圆
角成为疲劳裂纹的危险部位,轮轴接触表面相对不那么重要,因此也没有采取工艺措施来提高压装部位的疲劳强度。
而日本采用大半径厂和小的直径比D/d而应
力影响小,因此过渡部位的应力集中较小,轮座成为车轴的疲劳薄弱部位,如果轮座部位满足要求,其它部位肯定满足设计要求。
压装部位的形状简图
2. 车轴的热处理工艺不同,许用应力的值也不同。
欧洲标准中车轴的热
处理为退火处理,而日本为了提高轮座部位的疲劳强度,新干线高速铁路从1964 年开始运营起,就一直采用高频硬化工艺。
在锻造和机加工之后,进行整体高频硬化,并且通过不断改进高频硬化方法和精加工过程,进一步改善其残余应力和硬度分布。
因此日本标准中车轴的许用应力较欧洲标准更高。
3. 欧洲和日本的车轴疲劳强度计算都考虑了车体振动引起的垂向和横向
加速度的影响,但动载荷系数的取法有所不同。
欧洲标准中,如果没有特殊说明,垂向动态载荷系数α=o.25,横向动态载荷系数β=0.175,它们与车辆的运行速度
无关;而日本标准中,动态载荷系数取决于运行线路和速度。