铸铁熔炼操作规程
熔铸车间铸造工操作规程范文(二篇)
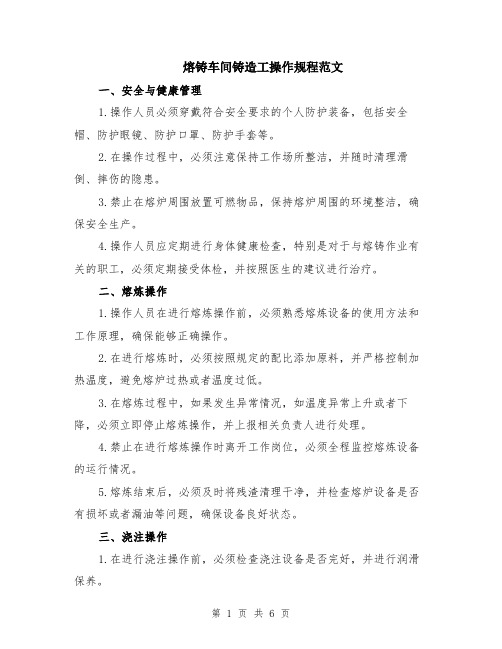
熔铸车间铸造工操作规程范文一、安全与健康管理1.操作人员必须穿戴符合安全要求的个人防护装备,包括安全帽、防护眼镜、防护口罩、防护手套等。
2.在操作过程中,必须注意保持工作场所整洁,并随时清理滑倒、摔伤的隐患。
3.禁止在熔炉周围放置可燃物品,保持熔炉周围的环境整洁,确保安全生产。
4.操作人员应定期进行身体健康检查,特别是对于与熔铸作业有关的职工,必须定期接受体检,并按照医生的建议进行治疗。
二、熔炼操作1.操作人员在进行熔炼操作前,必须熟悉熔炼设备的使用方法和工作原理,确保能够正确操作。
2.在进行熔炼时,必须按照规定的配比添加原料,并严格控制加热温度,避免熔炉过热或者温度过低。
3.在熔炼过程中,如果发生异常情况,如温度异常上升或者下降,必须立即停止熔炼操作,并上报相关负责人进行处理。
4.禁止在进行熔炼操作时离开工作岗位,必须全程监控熔炼设备的运行情况。
5.熔炼结束后,必须及时将残渣清理干净,并检查熔炉设备是否有损坏或者漏油等问题,确保设备良好状态。
三、浇注操作1.在进行浇注操作前,必须检查浇注设备是否完好,并进行润滑保养。
2.在浇注过程中,必须保持浇注设备的稳定,避免晃动或者倾斜,确保浇注的准确性。
3.禁止在浇注过程中离开工作岗位,必须集中精力进行浇注操作,并根据需要进行调整。
4.在浇注结束后,必须及时清理浇注设备,避免残渣积存导致设备堵塞。
5.在浇注作业后,必须检查浇注质量,并及时进行记录,以便后续的追溯和分析。
四、材料管理1.对所有进入熔铸车间的材料,必须进行严格的检查,确保质量符合要求,并进行录入管理。
2.材料的存放要求按照规定的方式进行分类,并进行防尘、防潮、防日光等措施,确保材料的质量。
3.禁止将材料放置在通道上、消防通道上或者阻挡出口,保持通道畅通。
4.熔铸车间使用的材料,必须按照规定的方式进行标记,并进行定期检查,确保材料质量。
五、设备维护与保养1.每日对熔炉设备进行检查,包括检查熔炉的供电、加热装置和温度控制器等,确保设备正常使用。
熔炼工安全操作规程
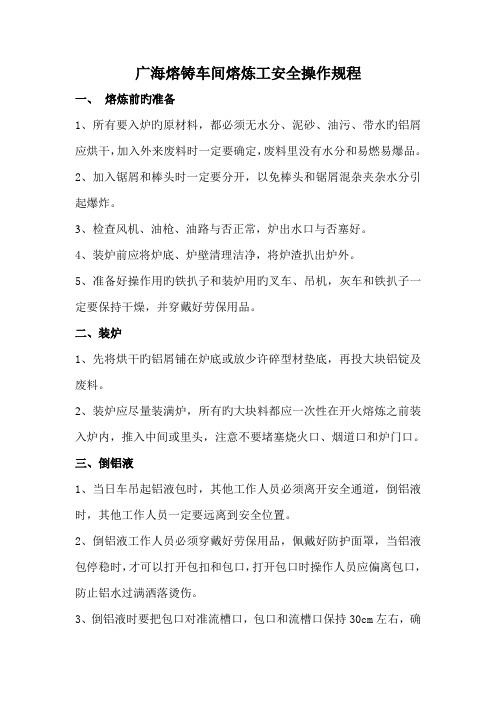
广海熔铸车间熔炼工安全操作规程一、熔炼前旳准备1、所有要入炉旳原材料,都必须无水分、泥砂、油污、带水旳铝屑应烘干,加入外来废料时一定要确定,废料里没有水分和易燃易爆品。
2、加入锯屑和棒头时一定要分开,以免棒头和锯屑混杂夹杂水分引起爆炸。
3、检查风机、油枪、油路与否正常,炉出水口与否塞好。
4、装炉前应将炉底、炉壁清理洁净,将炉渣扒出炉外。
5、准备好操作用旳铁扒子和装炉用旳叉车、吊机,灰车和铁扒子一定要保持干燥,并穿戴好劳保用品。
二、装炉1、先将烘干旳铝屑铺在炉底或放少许碎型材垫底,再投大块铝锭及废料。
2、装炉应尽量装满炉,所有旳大块料都应一次性在开火熔炼之前装入炉内,推入中间或里头,注意不要堵塞烧火口、烟道口和炉门口。
三、倒铝液1、当日车吊起铝液包时,其他工作人员必须离开安全通道,倒铝液时,其他工作人员一定要远离到安全位置。
2、倒铝液工作人员必须穿戴好劳保用品,佩戴好防护面罩,当铝液包停稳时,才可以打开包扣和包口,打开包口时操作人员应偏离包口,防止铝水过满洒落烫伤。
3、倒铝液时要把包口对准流槽口,包口和流槽口保持30cm左右,确定稳、准后来才可以转动包盘。
4、在铝液流动过程中,不准急速转动包盘,以免铝液飞溅,防止流槽口堵塞铝液洒落,引起烫伤。
5、铝液倒完后来,要等铝包停稳至合适高度,才可以回转包盘,以免天车在回拉铝包过程中碰伤。
四、熔炼1、点火时将火种引到烧咀前面,打开回油阀,启动油泵和风机慢慢打开油枪阀,使炉内火焰呈短焰白亮光、无黑烟,将炉门关上保持一定间隙,进入正常熔炼。
2、当表层金属熔化后,应将未熔化旳大块铝推到里头高温区加速熔化。
3、当炉底金属所有熔化后常温到600-700℃停火加边角料并将其压沉到炉底,让铝液将其覆盖和熔化,直到成糊状时停止加废料,再开火升温到710℃-740℃进行精炼。
五、扒渣1、停火后将铝液充足搅拌,用扒子推扒炉底,炉壁,此时金属中旳渣和附于炉底、炉壁旳渣将上浮。
2 、将浮渣扒到炉门口附近,撒上打渣剂按1/1500-1/2500旳比例,并轻轻搓动浮渣,尽量使渣中旳铝分离出来,此时浮渣将由团状变成粉末状,将其扒出炉外旳锅中。
铸铁熔炼工艺流程

铸铁熔炼工艺流程
1.铁水准备:首先需要准备好高品质的铁水,通常使用生铁和废铁进行混合,经过预处理后,铁水中的杂质和气体会被去除。
2. 加料:将铁水倒入炉中,加入石灰、矽石、生石灰等辅助材料,以调整炉内化学反应的平衡,以及提高炉渣的流动性。
3. 加热:通过燃烧高热值的燃料,如焦炭或重油,使炉内温度升高,将材料熔化。
4. 炼铁过程:在高温下,铁水中的碳和硅等元素进行化学反应,形成不同种类的铸铁,如灰铸铁、球墨铸铁等。
5. 出铁:在适当的时间,将熔化的铁水倒入铸造模具中,冷却后即可得到成品铸铁。
6. 炉渣处理:在熔炼过程中,产生的炉渣需要处理,通常采用炉渣处理设备进行处理,以去除其中的杂质和有害物质。
以上就是铸铁熔炼的基本工艺流程,不同的生产厂家和生产工艺会有所不同,但一般都会包括以上几个步骤。
- 1 -。
铸铁熔炼操作规程

加强现场技术管理,规范中频炉熔炼操作。
2;范围适用于中频炉熔炼铸铁的操作。
3:职责3.1原材料准备⑾原生铁、回炉料、增碳剂、废钢、硅铁、锰铁、铜、球化剂、孕育剂的质量标准应符合公司铸造材料标准。
⑿每批外购的生铁、废钢、废机铁、硅铁、锰铁应该分类堆放,不可混杂(生铁、硅铁、锰铁、球化剂、孕育剂应附有对方或本公司的检测报告)⑶炉料应进行破碎,用电子吸盘直接加料尺寸应符合表1,注:用手工加料的不受此限制。
不得混有合金钢废料。
⒂新生铁回炉料、浇冒口表面粘附的泥砂应清除。
⒃铁屑应按材质种类分类堆放,不得混有油污泥砂和抹布等杂物。
⒄根据浇注铁水总量和配料比例,开炉前要备足各种炉料,并且分好类。
3.2修炉⑴每开炉之前,应将炉壁上附着的釉渣进行清理,并检查炉衬的尺寸大小是否符合技术要求。
⑵应仔细对炉衬各部分特别是炉底进行检查,发现有严重侵蚀及裂纹等情况,应用修补炉衬材料进行修补。
⑶将炉领上附着的釉渣进行清理,并按工艺要求进行修整,保证出铁时,铁液不溢出炉外。
3.3 开炉前检查3.3.1每次开炉前一小时,要全面检查以下方面,发现问题要及时排除才能开炉熔化:A)炉体、炉衬、炉领、中频电源漏炉报警装置,内循环和外循环冷却水系统液压倾炉机构等是否正常。
B)炉体各紧固件有无松动和移位;C)水管有无破损漏水等。
3.3.2 炉前地坑和炉体周围不得有积水,地坑内可铺一层干砂。
3.4加料熔化3.4.1 第一炉冷料启动时,其加料量一般为1.5~2.5吨,最好在炉体的中间加入一件重量为150~300公斤的起熔块,两边再用生铁锭或小块废钢填实,装料时禁止站在炉台上往炉丢入铁块,以免将炉体坩埚砸坏。
3.4.2第一炉熔化先用300~500KW左右的小功率送电半小时,使生料逐渐变红,观察炉衬,当生料和炉衬从底部到顶部都变得明亮时,保温半小时,然后进入正常熔化。
3.4.3 加入到电炉内的各种原材料严格按工艺员出具的配料单要求,用电磁吸铁盘或手工分批吊入,计量要求准确,加入顺序为:废钢加入炉底部,然后加入生铁锭和回炉料,并做好记录。
铸铁机安全操作规程
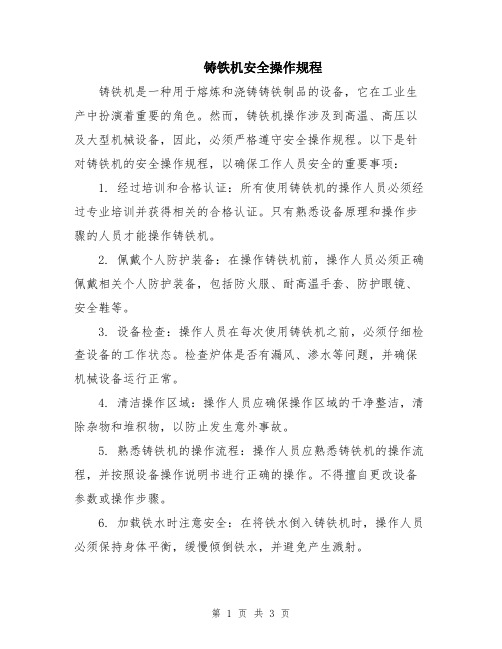
铸铁机安全操作规程铸铁机是一种用于熔炼和浇铸铸铁制品的设备,它在工业生产中扮演着重要的角色。
然而,铸铁机操作涉及到高温、高压以及大型机械设备,因此,必须严格遵守安全操作规程。
以下是针对铸铁机的安全操作规程,以确保工作人员安全的重要事项:1. 经过培训和合格认证:所有使用铸铁机的操作人员必须经过专业培训并获得相关的合格认证。
只有熟悉设备原理和操作步骤的人员才能操作铸铁机。
2. 佩戴个人防护装备:在操作铸铁机前,操作人员必须正确佩戴相关个人防护装备,包括防火服、耐高温手套、防护眼镜、安全鞋等。
3. 设备检查:操作人员在每次使用铸铁机之前,必须仔细检查设备的工作状态。
检查炉体是否有漏风、渗水等问题,并确保机械设备运行正常。
4. 清洁操作区域:操作人员应确保操作区域的干净整洁,清除杂物和堆积物,以防止发生意外事故。
5. 熟悉铸铁机的操作流程:操作人员应熟悉铸铁机的操作流程,并按照设备操作说明书进行正确的操作。
不得擅自更改设备参数或操作步骤。
6. 加载铁水时注意安全:在将铁水倒入铸铁机时,操作人员必须保持身体平衡,缓慢倾倒铁水,并避免产生溅射。
7. 遵守防火安全规定:铸铁机操作过程中必须严格遵守防火安全规定。
禁止在操作区域内吸烟、使用明火或其他易燃物品。
8. 防止烧伤和灼伤:操作人员必须小心触摸铸铁机,特别是在高温下。
在进行维护和清洁时,应使用专门的工具,并在接触高温表面前戴上耐高温手套。
9. 维护和保养:定期对铸铁机进行维护和保养,清洁设备并及时修理或更换损坏的部件。
任何发现的故障或异常情况必须报告给维修人员进行处理。
10. 废弃材料处理:废弃的铸铁材料、废渣和废料必须妥善处理,遵守环境保护规定。
11. 紧急情况应急措施:操作人员必须了解紧急情况下的应急措施,并熟悉使用灭火器等灭火设备。
12. 遵守使用手册:操作人员应认真阅读和遵守设备的使用手册,按照要求进行操作。
13. 禁止无关人员入内:除了经过培训和认证的操作人员之外,其他无关人员禁止进入操作区域。
铸铁技术操作规程(3篇)
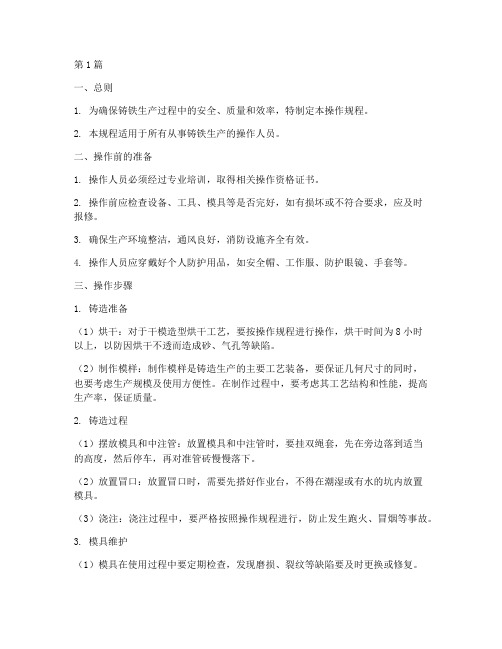
第1篇一、总则1. 为确保铸铁生产过程中的安全、质量和效率,特制定本操作规程。
2. 本规程适用于所有从事铸铁生产的操作人员。
二、操作前的准备1. 操作人员必须经过专业培训,取得相关操作资格证书。
2. 操作前应检查设备、工具、模具等是否完好,如有损坏或不符合要求,应及时报修。
3. 确保生产环境整洁,通风良好,消防设施齐全有效。
4. 操作人员应穿戴好个人防护用品,如安全帽、工作服、防护眼镜、手套等。
三、操作步骤1. 铸造准备(1)烘干:对于干模造型烘干工艺,要按操作规程进行操作,烘干时间为8小时以上,以防因烘干不透而造成砂、气孔等缺陷。
(2)制作模样:制作模样是铸造生产的主要工艺装备,要保证几何尺寸的同时,也要考虑生产规模及使用方便性。
在制作过程中,要考虑其工艺结构和性能,提高生产率,保证质量。
2. 铸造过程(1)摆放模具和中注管:放置模具和中注管时,要挂双绳套,先在旁边落到适当的高度,然后停车,再对准管砖慢慢落下。
(2)放置冒口:放置冒口时,需要先搭好作业台,不得在潮湿或有水的坑内放置模具。
(3)浇注:浇注过程中,要严格按照操作规程进行,防止发生跑火、冒烟等事故。
3. 模具维护(1)模具在使用过程中要定期检查,发现磨损、裂纹等缺陷要及时更换或修复。
(2)模具存放时要保持干燥、通风,避免受潮、变形。
四、操作注意事项1. 操作人员必须严格遵守操作规程,不得擅自改变工艺参数。
2. 操作过程中,要密切注意设备运行情况,发现异常立即停止操作,排除故障。
3. 操作人员应保持工作场所整洁,不得乱扔垃圾、杂物。
4. 操作人员应加强安全意识,防止发生安全事故。
五、操作后的清理1. 铸造完成后,要及时清理生产现场,包括清理模具、设备、工具等。
2. 清理过程中,要按照规定的方法进行,不得随意丢弃废弃物。
3. 清理完毕后,对生产现场进行检查,确保无安全隐患。
六、附则1. 本规程由生产部门负责解释。
2. 本规程自发布之日起施行。
球墨铸铁熔炼、浇注工艺操作规程
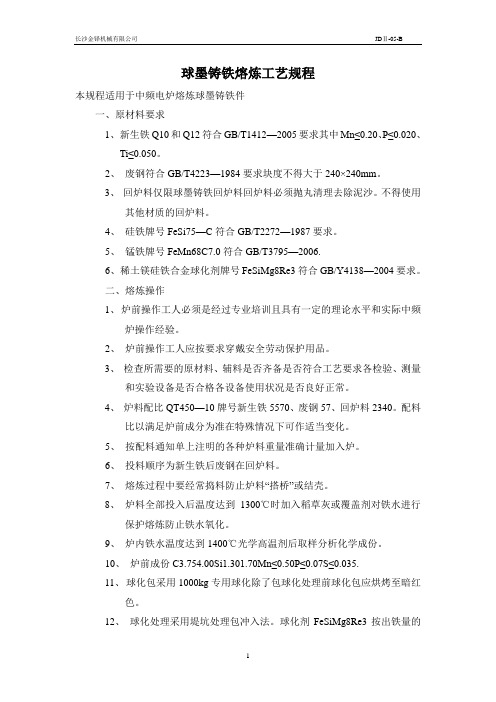
球墨铸铁熔炼工艺规程本规程适用于中频电炉熔炼球墨铸铁件一、原材料要求1、新生铁Q10和Q12符合GB/T1412—2005要求其中Mn≤0.20、P≤0.020、Ti≤0.050。
2、废钢符合GB/T4223—1984要求块度不得大于240×240mm。
3、回炉料仅限球墨铸铁回炉料回炉料必须抛丸清理去除泥沙。
不得使用其他材质的回炉料。
4、硅铁牌号FeSi75—C符合GB/T2272—1987要求。
5、锰铁牌号FeMn68C7.0符合GB/T3795—2006.6、稀土镁硅铁合金球化剂牌号FeSiMg8Re3符合GB/Y4138—2004要求。
二、熔炼操作1、炉前操作工人必须是经过专业培训且具有一定的理论水平和实际中频炉操作经验。
2、炉前操作工人应按要求穿戴安全劳动保护用品。
3、检查所需要的原材料、辅料是否齐备是否符合工艺要求各检验、测量和实验设备是否合格各设备使用状况是否良好正常。
4、炉料配比QT450—10牌号新生铁5570、废钢57、回炉料2340。
配料比以满足炉前成分为准在特殊情况下可作适当变化。
5、按配料通知单上注明的各种炉料重量准确计量加入炉。
6、投料顺序为新生铁后废钢在回炉料。
7、熔炼过程中要经常捣料防止炉料“搭桥”或结壳。
8、炉料全部投入后温度达到1300℃时加入稻草灰或覆盖剂对铁水进行保护熔炼防止铁水氧化。
9、炉内铁水温度达到1400℃光学高温剂后取样分析化学成份。
10、炉前成份C3.754.00Si1.301.70Mn≤0.50P≤0.07S≤0.035.11、球化包采用1000kg专用球化除了包球化处理前球化包应烘烤至暗红色。
12、球化处理采用堤坑处理包冲入法。
球化剂FeSiMg8Re3按出铁量的1.301.60加入覆盖FeSi粉按出铁量的0.300.40加入。
装包顺序球化剂→覆盖硅铁→压铁。
每层适当捣实在边角处适当加入少量的冰晶石粉。
球化反应时间控制在1分30秒至5分钟之间。
熔铸车间操作规程模版

熔铸车间操作规程模版一、熔炼操作规程1. 熔炼操作前的准备工作1.1 检查熔炉设备的运行状况,确保各部件正常工作;1.2 清理熔炉内外的杂物和残渣,保证熔炉干净;1.3 检查熔炉内的炉衬和保温材料,确保其完好无损;1.4 准备好熔化所需的原材料,并按照配比要求进行称量和混合;1.5 将熔炼所需的原材料送至熔炉,并正确装配炉盖和加热设备。
2. 熔炼操作步骤2.1 打开熔炉进气阀,启动熔炉加热设备,将温度调至适宜的熔化温度;2.2 监测熔炉内的温度,确保其在稳定范围内;2.3 适时添加剩余原材料,保持熔池的稳定;2.4 根据需要,进行必要的调温和翻砂操作;2.5 在熔池温度达到要求后,进行温度记录和取样分析;2.6 关闭熔炉进气阀和加热设备,待熔池温度降至安全范围后,开始倒炉操作。
3. 熔炼操作注意事项3.1 操作人员必须穿戴好防护设备,避免直接接触高温部件;3.2 操作过程中禁止随意打开熔炉门,以免引起熔池溅射和烟尘外泄;3.3 熔炉操作时必须保持专注,避免操作失误引发事故;3.4 操作结束后,必须及时清理熔炉内部和周围的残留物,确保安全和环境卫生。
二、铸造操作规程1. 铸造操作前的准备工作1.1 检查铸造设备的运行状况,确保各部件正常工作;1.2 清理铸造机台和模具,确保其干净无油污;1.3 检查铸造机台和模具的温度,确保其处于使用状态;1.4 准备好铸造所需的合金材料,并按照合金比例要求进行配料;1.5 将合金材料送至铸造机台,并按照工艺要求进行合金预热。
2. 铸造操作步骤2.1 启动铸造机台,调整好合适的压力和速度;2.2 放入预热好的合金材料,密封好铸造腔体;2.3 监控铸造过程中的温度和压力,确保其在安全范围内;2.4 根据需要,进行必要的修正和调整操作;2.5 铸造完成后,关闭铸造机台,取出铸件;2.6 对铸件进行外观检查和尺寸测量,确保其符合要求。
3. 铸造操作注意事项3.1 操作人员必须穿戴好防护设备,避免直接接触热模具和熔融合金;3.2 铸造机台运行时,禁止随意触摸和调整机台部件;3.3 铸造过程中严禁超负荷操作,以免引发设备故障和事故;3.4 操作结束后,必须及时清理铸造机台和模具,确保安全和环境卫生。
熔铸车间铸造工操作规程(3篇)

熔铸车间铸造工操作规程一、工作安全规定1. 所有操作人员必须穿戴好工作服和劳动防护用品,并按规定正确佩戴。
2. 在进行铸造作业前,必须检查设备和工具的安全状况,如有损坏或异常应及时上报维修。
3. 严禁擅自更改设备设置和操作参数,必须遵守正常操作流程。
4. 使用检修刀具时应注意正确使用方法,严禁乱扔和乱放。
5. 在作业过程中,必须保持工作场所整洁、干净,防止杂物积存造成安全事故。
6. 操作工必须按照规定的操作步骤进行操作,并注意细节,确保操作安全。
二、熔炉操作规范1. 操作前应检查熔炉、燃料供应管道和排烟系统的正常情况,确保无异常。
2. 熔炉操作必须在设定的温度范围内进行,严禁超过或低于限定范围。
3. 加料时需注意铁水温度和湿度,严禁将潮湿杂质投入熔炉。
4. 熔炉操作过程中应定时清理炉渣和积碳,以保持操作环境的清洁。
5. 关闭熔炉时,必须依次关闭相应的开关,并进行必要的安全检查。
三、铸造操作规范1. 操作前应检查模具、铁水温度和湿度,确保满足铸造要求。
2. 倒铁水时,必须按照正确的倒铁序列和角度进行,避免溅烧和倒堵等问题。
3. 铸件冷却后,必须安全处理,并防止铸件损坏或受损。
4. 铸件取出后,要进行必要的清理和整理,确保铸件质量和操作环境的卫生。
5. 预热模具时,需注意预热时间和温度,以免对模具造成损坏。
四、设备维护规范1. 在使用设备前,必须进行设备的检查和预热,以确保设备正常运行。
2. 设备使用中,应注意保持设备干燥和清洁,严禁将湿润的物品放置在设备附近。
3. 保养设备时,需按照设备保养手册进行,定期进行检查和维修,确保设备的正常运行。
4. 对于设备异常,在未解决前不得擅自更改设备参数,必要时需及时上报维修。
五、操作注意事项1. 在操作过程中,必须随时关注设备的运行情况,如有异常情况应及时停机并上报。
2. 严禁在操作过程中使用生水或湿润的手进行接触金属设备和铸件。
3. 操作人员必须在熔炉附近保持警觉,防止熔化金属的喷溅和烧伤。
球墨铸铁熔炼工艺规程

球墨铸铁熔炼工艺规程•2011-12-10 10:41:07本规程适用于中频电炉熔炼球墨铸铁件一、原材料要求:1、新生铁:Q10和Q12,符合GB/T1412—2005要求,其中Mn≤0.20%、P≤0.020%、Ti≤0.050%。
2、废钢:符合GB/T4223—1984要求,块度不得大于240×240mm。
3、回炉料:仅限球墨铸铁回炉料,回炉料必须抛丸清理,去除泥沙。
不得使用其他材质的回炉料。
4、硅铁:牌号FeSi75—C,符合GB/T2272—1987要求。
5、锰铁:牌号FeMn68C7.0,符合GB/T3795—2006.6、稀土镁硅铁合金球化剂:牌号FeSiMg8Re3符合GB/Y4138—2004要求。
二、熔炼操作:1、炉前操作工人必须是经过专业培训,且具有一定的理论水平和实际中频炉操作经验。
2、炉前操作工人应按要求穿戴安全劳动保护用品。
3、检查所需要的原材料、辅料是否齐备,是否符合工艺要求,各检验、测量和实验设备是否合格,各设备使用状况是否良好正常。
4、炉料配比:QT450—10牌号:新生铁55~70%、废钢5~7%、回炉料23~40%。
配料比以满足炉前成分为准,在特殊情况下可作适当变化。
5、按配料通知单上注明的各种炉料重量准确计量加入炉。
6、投料顺序为新生铁,后废钢,在回炉料。
7、熔炼过程中要经常捣料,防止炉料“搭桥”或结壳。
8、炉料全部投入后,温度达到1300℃时,加入稻草灰或覆盖剂对铁水进行保护熔炼,防止铁水氧化。
9、炉内铁水温度达到1400℃(光学高温剂)后取样分析化学成份。
2、炉前成份:C3.75~4.00%;Si1.30~1.70%;Mn≤0.50%,P≤0.07%;S≤0.035%.3、球化包采用2000kg专用球化除了包,球化处理前球化包应烘烤至暗红色。
4、球化处理:采用堤坑处理包冲入法。
球化剂FeSiMg8Re3按出铁量的1.30~1.60%加入,覆盖FeSi(粉)按出铁量的0.30~0.40%加入。
铸钢熔炼浇注操作规程

铸钢熔炼浇注操作规程铸钢熔炼浇注操作规程一、安全准备1. 所有操作人员必须穿戴好防护装备,包括防火服、安全帽、防护口罩、防护手套等,并检查其完好性。
2. 确保工作场所干净整洁,不堆放易燃物品,消防设备齐全。
3. 检查设备是否正常,如熔炼炉、浇注设备、工作台等。
4. 确保现场通风良好,防止烟尘积聚。
二、熔炼钢料准备1. 确定需要熔炼的钢种及其比例,根据配方准备好各种原材料。
2. 干燥并预热原料,避免水分、杂质和氧化物的混入。
3. 使用吊车或叉车将原料转移到熔炼炉旁,并精确称量。
4. 确认熔炼炉的温度控制系统正常运作,设定好炉温。
三、熔炼操作1. 将预热好的原料逐一投入熔炼炉中,避免同时投入过多原料导致炉温过低或爆炸。
2. 使用适当的燃料和氧气进行燃烧,控制火焰的大小和形状。
3. 确保熔炼过程中炉温稳定在合适的范围内,可以根据实际情况调整熔炼炉的火焰和氧气供应。
4. 定期对熔炼炉进行清理保养,防止底部堵塞。
四、浇注准备1. 检查浇注设备是否完好,并进行润滑。
2. 安装好浇注模具,并检查其密封性。
3. 确认钢液的温度和浇注温度符合要求。
4. 确保浇注时工作人员站位合理,避免受伤。
五、钢液浇注1. 确认钢液已经熔化,并且温度稳定在适宜范围内。
2. 开始浇注时,首先向模具内部预浇一些钢液,以达到预热模具的目的。
3. 以稳定的速度倾倒钢液进入模具,避免溅射和侧流。
4. 打破浇注后可能产生的气泡,保证浇注质量。
六、浇注后处理1. 浇注完成后,将模具放置于适当的环境中进行自然冷却。
2. 清理浇注现场,清楚记录浇注数量和时间。
3. 将废弃的模具进行处理,确保环境卫生。
4. 对浇注质量进行检查和测试,记录数据并进行分析。
七、安全操作1. 所有熔炼和浇注操作人员必须经过相关培训,并持证上岗。
2. 不得擅自调整熔炼和浇注设备,如有问题应及时报告上级。
3. 遵守动火和防火规定,不得在熔炼现场吸烟、使用明火等。
4. 注意熔炼过程中的热辐射和气体产生的有害物质,必要时戴上防护面罩。
熔炼操作工艺要求及步骤

3.一般回炉料50%以内,加工面不多或不加工件也可采用70%回炉料,
但必须经过当天抛丸处理,浇杯上看不到黑色残留物。
二、熔化
1.冷炉熔化时,因炉衬有裂纹,需小功率送电,待炉衬发红,裂纹弥合
后即可满功率快速熔化,以后的热炉加快熔化进度,缩短钢料在大气中
接触,减少氧化、吸气。
多加,以配料单规定的量为准。
4.脱氧剂的加入顺序:要先加锰刚化完随后加硅,脱氧剂要预热后推开
渣面加到钢液中,随即覆盖。
四、调整成分及升温
1.经预脱氧后完全熔化即可取样分析,补加合金,补加的合金均要预热
2.快速升温,小炉以230KW速率升温,温度大约以20~25℃/分钟上升,
6~7分30ቤተ መጻሕፍቲ ባይዱ左右达到最高熔化温度并测温。大炉以250KW速率升温,温度
2.钢水熔化到三分之二时加入配料合金,加入合金均预热20-30分钟,
氮化铬铁预热温度必须≥900℃,其他合金≥200℃
3.操作时要注意覆盖,防止钢液裸露。
三、预脱氧
1.脱氧剂的选择:锰和硅
2.脱氧剂加入时间:钢料刚全部熔化而温度在1500~1600℃时加入,此时
并测温一次。
3.脱氧剂加入量:以最终钢中锰,硅残留含量不超目标值为原则,尽量
熔炼操作工艺要求及步骤
为了提高我司铸件内在质量,减少铸件加工过程中的焊补量,提升加工效率及提高及时交付率,特对目前熔炼工艺作临时调整并规范熔炼过程操作步骤。
一、装料
1.选底渣:用80-90%的干石灰,10-20%的萤石作造渣剂,以钢水总量
的1~3%加入炉底或边加料边加石灰,以能完全覆盖钢液为原则。
2.炉料要求:用与要求钢号成分相同或相近的干净无油污的优质型材边
铸铁熔炼作业指导书

7.铁水转运要求:吊运人员应将接种完毕之铁液于3分钟内倒入浇注盆,炉前操作工负责监控铁水转运时间并 记录, 若超过3分钟以上时该包铁液返回电炉,重新再处理。
(二)球墨铸铁熔化操作1.熔化操作工依照每日的生产指令启动熔解作业。
首先进行领料和备料工作,所用原料要干 燥,领到现场的原料按分类标识进行存放。
2.按《中频电炉操作规程》进行电炉操作。
3.化学成份控制3.1 正常调质时C、Si不得同时做上限或下限,在包内调整合金含量时合金块度<20mm,Si, 的调整幅度≤0.2%且只能用硅铁调整不可用接种剂调整。
3.2 按时査看分光仪检测结果(分光试验人员接到分光试片测试后,将分析结果报告到炉前), 各元素成分须控制严格执行《熔解作业基准表》中的规定。
当化学成分测得在下限时,熔化工在熔化工程师的指导下计算出达到目标值所需添加的量并负责添加。
此时不必再测成分3.3 对《熔解作业基准表》中要求不明确的微量元素控制目标为:Sn≤0.007%、Sb≤0.007%,其他元素≤0.05%。
如化学成分微量元素不在控制目标内,需要电炉重新调质,调质合 格后方可出炉。
如成品化学成分微量元素不在控制目标内,按每包首尾模的插牌,将该包次回炉。
3.4 电炉铁液分析结果在标准范围内时,则可以出炉。
铁液调好后30分钟不出炉,需重新确认长度成份及白口长度3.5 铁液保温时间超过1小时,需重新调质。
3.6 每炉铁液冲入返回铁液≥两包时需重新调质。
4.温度和出铁控制:为保证铁水满足浇注要求,熔化操作工每包出铁前先进行除渣,然后用浸入式测温枪对铁液温度进行检测并记录,(预热浇包或浇注盆之铁液需在炉内测温一次〕 ,如果温度达不到要求,不能出铁。
温度以《熔解作业基准表》规定的浇注温度范围为标准5.铁液转运量管制:作业人员根据生产状况在《熔解作业基准表》规定范围内确定每包铁液量 的目标值,出铁水时用吊钩称称量,允许误差为目标值的±30kg6.球化过程:6.1球化处理过程见《球化作业指导书》,为保证球化反应稳定,每炉最后残留<500kg时不再出炉 覆盖剂加入(依球化温度增减);出炉时避免铁液直接冲击球化剂,操作人员应控制铁液角度6.2每包出炉完毕,球化反应开始时焰化操作工应按动秒表开始计时,反应时间应≥50秒,以 防止球化不良,并要记录球化反应时间。
球墨铸铁熔炼程序

球墨铸铁熔炼程序1. 冶金预处理冶金预处理的目的是控制、保持铁液金属稳定的质量状态,调控球化、孕育数量和效果。
铸铁特别是球墨铸铁熔炼应进行预处理,使铁液尽早具有稳定数量的氧含量和形核核心。
适当有效的预处理能够增加20%~25%的核心数量。
重要的是,应按熔炼作业指导书规定稳定控制熔炼温度,避免液态金属质量的剧烈波动(保持氧和核心存在)。
熔炉内预处理增加铁液的核心,必须根据试验结果实施。
试验主要是白口试片试验或采用CE热分析仪进行曲线测试。
当炉料中含有高比例废钢时预处理更具重要意义(钢料不能提供核心)。
预处理通常有以下方案:1)后期加入大比例的生铁。
2)加入SiC(加入量为0.4%),特别是加入钢料时。
3)第一次孕育时加入额外的孕育剂。
如果氧含量高于常规,最好的预处理是出铁前加入碳化硅(SiC),作用如下:①碳与氧反应形成CO;②硅进入金属,增加硅含量。
4)最新的预处理工艺是在球化处理前,通过加入预处理剂,将铁液中的O、S含量稳定的控制在较低水平,为球化反应提供良好条件,同时反应产物能够形成稳定的形核核心。
预处理元素需具有以下特点:①与铁液中的O、S反应活性强,其氧化物、硫化物的标准生成自由能低;②形成的氧化物、硫化物密度最好接近铁液,熔点要高,质点尺寸适合作形核核心。
目前采用的含La、Ba的处理剂能较好地满足这些要求。
预处理可提高孕育效率(降低孕育衰退影响)。
下图7-6所示为三角试片试验的凝固过冷情况,采用FeSi合金孕育,可见采用预处理工艺后(最下面折线)孕育效果显著优于其他工艺。
方案1)~方案3)是铸造工厂常用的方案,其中方案3)还不能算真正的预处理工艺,它是在出铁后进行的,通常用于Si含量较低的场合。
SiC加入量的范围是0.4%~1.0%,加入SiC的预处理会减低随后的孕育处理的衰退。
图-1孕育处理对白口深度的影响2. 球墨铸铁熔炼程序球墨铸铁熔炼程序包括配料和熔炼工艺如下:1)首批配料装炉必须致密,组分为废钢和回炉料的混合料。
铸钢熔炼操作规程
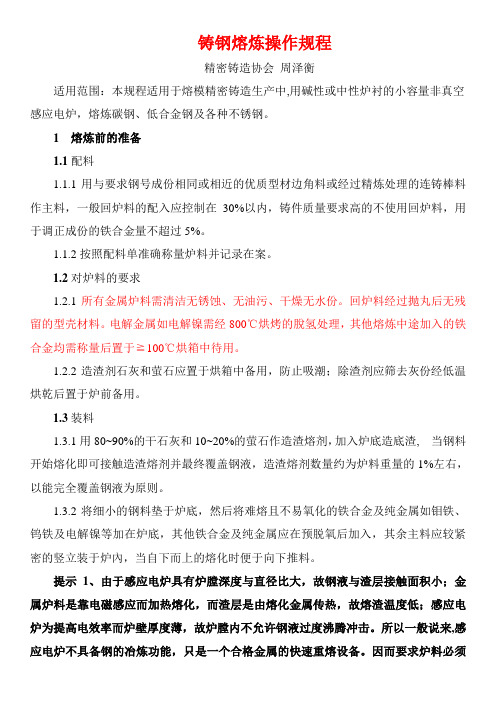
铸钢熔炼操作规程精密铸造协会周泽衡适用范围:本规程适用于熔模精密铸造生产中,用碱性或中性炉衬的小容量非真空感应电炉,熔炼碳钢、低合金钢及各种不锈钢。
1 熔炼前的准备1.1配料1.1.1用与要求钢号成份相同或相近的优质型材边角料或经过精炼处理的连铸棒料作主料,一般回炉料的配入应控制在30%以内,铸件质量要求高的不使用回炉料,用于调正成份的铁合金量不超过5%。
1.1.2按照配料单准确称量炉料并记录在案。
1.2对炉料的要求1.2.1所有金属炉料需清洁无锈蚀、无油污、干燥无水份。
回炉料经过抛丸后无残留的型壳材料。
电解金属如电解镍需经800℃烘烤的脫氢处理,其他熔炼中途加入的铁合金均需称量后置于≧100℃烘箱中待用。
1.2.2造渣剂石灰和萤石应置于烘箱中备用,防止吸潮;除渣剂应筛去灰份经低温烘乾后置于炉前备用。
1.3装料1.3.1用80~90%的干石灰和10~20%的萤石作造渣熔剂,加入炉底造底渣, 当钢料开始熔化即可接触造渣熔剂并最终覆盖钢液,造渣熔剂数量约为炉料重量的1%左右,以能完全覆盖钢液为原则。
1.3.2将细小的钢料垫于炉底,然后将难熔且不易氧化的铁合金及纯金属如钼铁、钨铁及电解镍等加在炉底,其他铁合金及纯金属应在预脱氧后加入,其余主料应较紧密的竖立装于炉內,当自下而上的熔化时便于向下推料。
提示1、由于感应电炉具有炉膛深度与直径比大,故钢液与渣层接触面积小;金属炉料是靠电磁感应而加热熔化,而渣层是由熔化金属传热,故熔渣温度低;感应电炉为提高电效率而炉壁厚度薄,故炉膛内不允许钢液过度沸腾冲击。
所以一般说来,感应电炉不具备钢的冶炼功能,只是一个合格金属的快速重熔设备。
因而要求炉料必须成份准确而洁净。
提示2、碱性或中性炉衬可造碱性渣,金属炉料熔化产生的氧化物首先和熔渣接触反应,而不至于粘附炉衬,所以除非金属炉料非常干净,才不必造底渣。
2 快速熔化2.1当炉料装完后即可啟动电源满功率送电,以加快熔化速度,缩短钢料在大气中的接触时间,减少氧化、吸气。
铸造部电炉熔炼操作规程

铸造部电炉熔炼操作规程一、电炉熔炼操作规程1、主题内容与适用范围:本标准适用于本公司1T电炉的熔炼过程,规定了1T电炉熔炼过程所应遵守的工艺规范。
2、电炉的熔炼:2、1熔炼前的检查工作:2、1、1检查感应线圈、电容器、电源柜冷却水水压是否正常,出水是否畅通;2、1、2检查水压表指示和报警传输线是否畅通,电炉倾转机构运行是否正常;检查各个螺栓紧固点的螺栓是否松动,保证螺栓在紧固状态;2、1、3检查炉底、炉衬侵蚀情况,是否有裂纹。
如有异常情况,应根据实际情况作相应处理。
2、1、4检查电炉地坑是否积水,如有应及时清理,铺一层干砂,以免发生喷溅事故。
2、1、5熔炼前应清理修补炉口,炉嘴,保证炉嘴光滑,出铁顺畅。
2、2熔炼:2、2、1打结后的新炉衬,第一炉应满炉熔炼,以利炉衬整体结构烧结良好。
2、2、2熔炼时,仔细审核料单,严格按照料单要求和重量加料;以500kg废钢料单为例:加料顺序为:2.2.2.1加入50kg铁屑(QT)后加入200kg回炉料(QT),待上述材料全部熔化结束废钢开始熔化时,加入5kg增碳剂;2.2.2.2第一批次废钢(大约80kg)和增碳剂熔化结束,第二批次废钢(大约80kg)开始熔化时,加入5kg增碳剂;依次进行,直到将500kg废钢和30kg增碳剂全部加完;2.2.2.3加入余下的250kg回炉料;待回炉料、废钢、增碳剂熔化完全(铁液温度大约在1350℃)时,取样,进行炉前快速分析;按照分析结果,加入增碳剂和其他辅料。
2.2.2.4按照熔炼要求,当补加的合金料全部熔化,铁水温度达到工艺要求(小规格球铁件出炉温度控制在1530℃—1560℃;大规格球铁件出炉温度控制在1500℃—1530℃)时,要取原铁水试块;取样后及时出炉;2.2.2.5第一炉铁水温度必须达到1580℃,烫包回炉后温度升至前面规定要求后出炉;2、2、3 球化剂(上面举例为12.5kg)准确称量后,加入球化包堤坝内侧(摊匀),硅粒(上面举例为6kg)均匀的覆盖在球化剂上面,再加珍珠岩均匀覆盖(一茶缸,约1.5kg);在堤坝上加入脱硫用碱面1kg,碱面上放10kg硅钢片2、2、4在加铁料时,不准炉料猛力撞击炉壁、炉底,以防炉衬受损。
熔铸车间操作规程
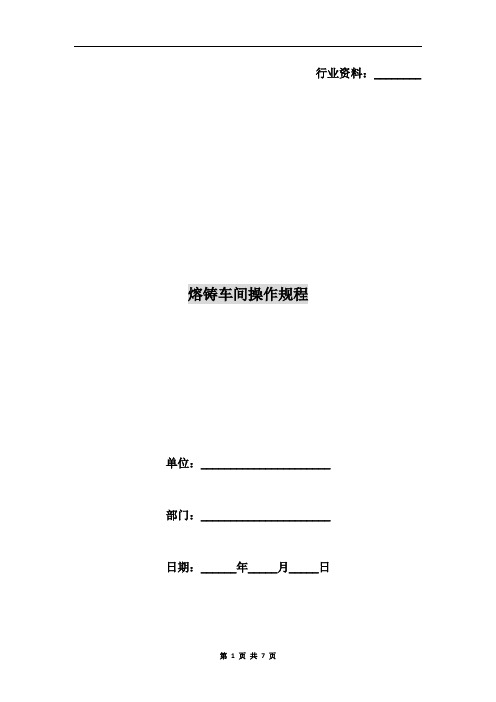
行业资料:________ 熔铸车间操作规程单位:______________________部门:______________________日期:______年_____月_____日第1 页共7 页熔铸车间操作规程一、配料操作工艺规程1、首先要掌握所铸棒坯的规格、材质,懂得棒坯的材质含量;2、按要求顺序投入无杂质异物的原材料;3、倒原材料时要掌握各堆料的化学成份,不要搞乱;4、对所计划好的料,投入时要弄清数量,不能有大的误差;5、炉前、炉后所补充金属,要计算准确无误,保证棒坯内的合金含量在要求范围之内。
二、熔炼操作工艺规程1、装炉之前要仔细检查加热炉及各种设备是否正常;2、煤炉及熔炼的杂质必须彻底清除干净;3、核对好本炉所装的原材料棒坯的规格、材质、尺寸及铸成品棒坯重量;4、装料时,部分中间合金含量高,要做到心中有数;5、熔铸时的温度不得超过780℃;6、炉内料品全部熔化后,在熔炼温度范围内进行扒渣、推锅;推锅时要将铝推干净,扒渣时要平稳、扒干净尽量少带出金属来;7、所接触金属体的工具要涂抹化石粉,所有工具在工作当中必须保持干燥,以防危险发生;8、补充合金金属时要慢慢的加入,不能造成铝水回溅,金属烧损严重现象,搅拌要彻底,无死角,不要起大浪,既要保证成份均匀,又要避免金属损失;9、取样时温度不得低于熔炼时的下限温度710℃,取样要保持干第 2 页共 7 页净、干燥,所取样在炉中间提取,保证化验后的数据准确无误,对棒坯的化学成份在要求的范围之内没有偏差;10、补料和冲氮料的数量,要计算无误,过磅要准确,加料要均匀分散,待补充料全部融化后进行充分的搅拌,在补充料多,化验结果与要求误差大的情况下,应进行重新化验;11、在精炼时的温度,6063材质保持720℃-740℃,其它硬质合金保持-760℃;12、在做硬质合金时,投入锰添加剂时炉水温度必须达到750℃以上,以便锰剂的完全熔结;13、精炼剂的用量要保持在每吨铝水在2kg-4kg之间;14、在铸造特殊材质棒时,应按要求加细化剂、覆盖剂等;15、精炼前应检查设备管道是否通畅,然后把精管口放在炉底缓慢移动,要平衡无死角,精炼要到位;16、精炼后的炉内扒渣要平稳,不能把杂质再次混入熔体内部,造成夹渣;17、静置时间要保持在20-30分钟之间,期间要保持炉水温度,以便正常铸造;18、在特殊情况下二次精炼后,超过5小时没有铸棒,应再次精炼化验,金属含量发生变化,要重新添加金属成份;19、最后工作的现场要保持干净,工具整齐排放。
普通铸铁熔炼

普通铸铁熔炼普通铸铁熔炼、浇铸工艺守则1.原材料要求1.1普通铸件熔炼用生铁,采用铸造用生铁和球墨铸铁用生铁,牌号为Z14 Z18 Q12 Q16.应符合国家标准(GB/T718-2005 GB/T1412-2005)。
1.2铁合金、硅铁符合(GB/T2272-2009)锰铁符合(GB/T3759-2006)球化剂符合(JB/T9228-1999)1.3废钢表面不能有严重锈蚀;锈蚀严重的需经烘干后使用;块度差别大时应搭配使用,成批的合金钢必须有成分化验单才能使用1.4各种金属炉料应按牌号、级别或成分分类,分堆存放;粘附的泥砂、熔渣等应清理干净。
1.5废钢、废铁等金属炉料中,严禁混有弹壳、雷管、密封管头及其易爆物,备料中应仔细检查,遇到可疑物及时妥善处理。
2 熔炼2.1起炉前的准备2.1.1普通铸铁熔炼设备为1t中频感应电炉2.1.2检查水路是否畅通,电器系统是否完好,工具辅料是否齐全,炉大膛、炉嘴循环系统是否正常,并在电炉专职维修人员认可下方可由电盘看炉人员启动电炉2.1.3查看生铁化验单、合金质保单或合格证等成分的符合性,是否同一批次,进行分类定点放置;含有水分、油污、锈蚀严重的炉料不能使用。
2.1.4合金应进行烘烤预热。
2.1.5浇包提前修整烘烤,保持其干燥。
2.2起溶:按照技术员出具的不同产品的配料通知单,操作人员准确称量配比、投料、通电熔融,并真实、准确、完整的记录上,冷起炉时,加起熔体,其重量为炉子容量的20~30%,炉料应尽可能靠炉壁放置2.3溶化:在溶化过程中应经常撬动炉料,以防止炉料搭棚,液面冻结。
如有液面冻结封闭,应及时把炉体倾斜一定角度,使冻结层逐渐融化。
2.4精炼:感应电炉一般不造渣,必要时加熔剂如玻璃、萤石造渣。
铁液精炼温度一般为1400~1500摄氏度精炼期一般为10~20min。
精炼温度过高或精炼时间过长都会造成铸铁白口倾向加大或石墨形态不良。
2.5炉前控制:2.5.1成分分析:炉料成分熔化后浇注试样分析铁液化学成分,按化验结果进行成分调整。
熔铸车间铸造工操作规程

熔铸车间铸造工操作规程第一章总则第一条为规范熔铸车间的铸造工作,确保生产安全、提高产品质量、保护环境,制定本操作规程。
第二条本操作规程适用于熔铸车间的所有铸造工作人员。
第三条铸造工作人员应严格按照本操作规程执行工作,在铸造现场严禁违反规定行为。
第四条铸造工作人员应熟悉炉子的操作和维护知识,在操作中遵循安全第一的原则。
第五条铸造工作人员应熟悉相关设备的操作和维护知识,并定期进行设备检修,确保设备安全运行。
第二章作业流程第一条铸造工作人员应在熔炉操作之前,检查炉子的运行状态,确保炉子可以正常使用。
第二条铸造工作人员应根据生产计划准备好所需的原料和熔炉工具。
第三条铸造工作人员应穿戴好防护设备,包括耐高温的工作服、手套、防护眼镜等。
第四条铸造工作人员应按照炉子的设定温度和时间调节炉子的工作状态。
第五条铸造工作人员应根据产品要求准备好模具,并进行必要的清洁和涂抹。
第六条铸造工作人员应将准备好的原料投入到熔炉中,并根据需要添加相应的合金。
第七条铸造工作人员应控制熔炉的温度和保持熔池的稳定。
第八条铸造工作人员应根据产品要求将熔融金属倒入到模具中,并等待金属凝固。
第九条铸造工作人员应及时清理熔炉和模具,确保生产环境整洁。
第十条铸造工作人员应及时上报熔炉的运行状态和产品质量等情况。
第十一条铸造工作人员应根据生产需要进行设备的保养和维修工作。
第十二条铸造工作人员应加强自身安全意识,遵守操作规程,不得违反操作规定。
第十三条铸造工作人员应定期参加相关的安全培训,提高自身的安全知识和技能。
第三章安全措施第一条铸造工作人员应在工作前穿戴好防护设备,严禁穿着宽松的衣服和长发,以免造成安全事故。
第二条铸造工作人员应严格遵守熔炉操作规程,不得擅自修改熔炉的设置参数,以免造成设备的损坏或工作事故。
第三条铸造工作人员应在铸造过程中远离熔池,以免熔池的溅射物对人员造成伤害。
第四条铸造工作人员应保持工作环境的整洁,及时清理熔炉周围的杂物和残渣,防止火灾事故的发生。
- 1、下载文档前请自行甄别文档内容的完整性,平台不提供额外的编辑、内容补充、找答案等附加服务。
- 2、"仅部分预览"的文档,不可在线预览部分如存在完整性等问题,可反馈申请退款(可完整预览的文档不适用该条件!)。
- 3、如文档侵犯您的权益,请联系客服反馈,我们会尽快为您处理(人工客服工作时间:9:00-18:30)。
加强现场技术管理,规范中频炉熔炼操作。
2;范围
适用于中频炉熔炼铸铁的操作。
3:职责
3.1原材料准备
⑾原生铁、回炉料、增碳剂、废钢、硅铁、锰铁、铜、球化剂、孕育剂的质量标准应符合公司铸造材料标准。
⑿每批外购的生铁、废钢、废机铁、硅铁、锰铁应该分类堆放,不可混杂(生铁、硅铁、锰铁、球化剂、孕育剂应附有对方或本公司的检测报告)
⑶炉料应进行破碎,用电子吸盘直接加料尺寸应符合表1,注:用手工加料的不受此限制。
不得混有合金钢废料。
⒂新生铁回炉料、浇冒口表面粘附的泥砂应清除。
⒃铁屑应按材质种类分类堆放,不得混有油污泥砂和抹布等杂物。
⒄根据浇注铁水总量和配料比例,开炉前要备足各种炉料,并且分好类。
3.2修炉
⑴每开炉之前,应将炉壁上附着的釉渣进行清理,并检查炉衬的尺寸大小是否符合技术要求。
⑵应仔细对炉衬各部分特别是炉底进行检查,发现有严重侵蚀及裂纹等情况,应用修补炉衬材料进行修补。
⑶将炉领上附着的釉渣进行清理,并按工艺要求进行修整,保证出铁时,铁液不溢出炉外。
3.3 开炉前检查
3.3.1每次开炉前一小时,要全面检查以下方面,发现问题要及时排除才能开炉熔化:
A)炉体、炉衬、炉领、中频电源漏炉报警装置,内循环和外循环冷却水系统液压倾炉机构等是否正常。
B)炉体各紧固件有无松动和移位;
C)水管有无破损漏水等。
3.3.2 炉前地坑和炉体周围不得有积水,地坑内可铺一层干砂。
3.4加料熔化
3.4.1 第一炉冷料启动时,其加料量一般为1.5~2.5吨,最好在炉体的中间加入一件重量为150~300公斤的起熔块,两边再用生铁锭或小块废钢填实,装料时禁止站在炉台上往炉丢入铁块,以免将炉体坩埚砸坏。
3.4.2第一炉熔化先用300~500KW左右的小功率送电半小时,使生料逐渐变红,观察炉衬,当生料和炉衬从底部到顶部都变得明亮时,保温半小时,然后进入正常熔化。
3.4.3 加入到电炉内的各种原材料严格按工艺员出具的配料单要求,用电磁吸铁盘或手工分批吊入,计量要求准确,加入顺序为:废钢加入炉底部,然后加入生铁锭和回炉料,并做好记
录。
3.4.4 不允许往炉内加入任何潮湿的炉料,不允许往熔融的铁液内加入带深孔或密封的容器类废钢,严防金属飞溅发生烫伤事故,熔炼过程中除加料和出铁过程外,禁止用风扇直吹炉口,以防止热量散失。
3.4.5加料过程中,要随时注意观察熔化情况,防止铁料“搭棚”和顶部冻结封闭。
发现“搭棚”和顶部冻结封闭时,可将炉体倾斜,降低功率熔化,让铁液由前部化开,恢复正常熔化,严禁用冷铁棍捅开。
3.4.6 当因停电或水泵损坏等特殊情况停炉时,炉体内的的铁水温度很高,如感应圈失去冷却会很快被烧坏。
炉体中的冷却水必须使用水塔等备用措施来冷却感应圈。
3.4.7 在熔炼过程中,要经常检查各水管的出水情况(水温和水压)。
3.4.8 根据熔化情况适时调整功率大小,并且经常查看冷却水温度指示表,出水温度控制在50℃以下,观察电源柜各个仪表的指示是否正常,炉体周围有无异常响声,气味等,如有异常,立即停炉检查。
3.4.9 铁液熔化完毕并且升温到1430~1450℃时,取样分析C、Si、Mn、Cr、Ni、等主要元素的含量,并据此调整化学成分,待加入的合金熔化完全后用集渣剂聚渣,同时,用测温枪测温并记录。
3.4.10 按生产计划单和浇注顺序准确地称量所出铁水,防止因出铁液不足而使所浇注铸件少铁水而报废。
3.4.11 在出铁的过程中,必须按工艺要求做好孕育处理,以确保材质性能要求。
3.4.12电炉熔炼结束后,采用风扇对炉衬进行强制冷却,炉体冷却循环水泵要一直运行到使炉衬冷却到室温才能关闭。
3.5 感应电炉熔炼工安全操作规程
3.5.1检查炉体冷却系统、电气控制装置、感应器铜管、机械传动装置和吊运设备,确认完好、正常。
3.5.2 炉瞠熔损超过规定(炉衬厚度小于65-80mm)时,应及时修补,方能开炉。
3.5.3 检查有无裂缝,3mm以上的裂缝,要填入炉衬材料进行修补;确保冷却水畅通。
3.5.4 检查熔炼所使用的工具,确保齐备、干燥。
3.5.5检查各种金属材料,其品种、块度、水分和清洁度要符合规定,严禁混入密封盒子,箱子和管子之类物件及易爆品,熔化过程中,不准加潮湿炉料。
3.5.6 切屑料要尽量放在出铁后的残留铁液上。
一次投入量不要超过炉子量的1/10,而且必须均匀投入。
3.5.7 不管炉料质量如何,都要在前一次投入的炉料没有熔化完前,投入下一次炉料。
3.5.8 在满足材质工艺要求的前提下,尽量降低出铁温度,缩短高温铁液在炉内的保温时间。
3.5.9 认真烘干炉体和铁水包。
3.5.10 熔炼过程中,必须经常检查冷却水,保证水箱处于充满状态,水箱缺水时应立即断电,停止熔炼。
3.5.11 熔炼过程中,经常检查炉底和功率表,若发现有漏炉迹象,应立即切断电源停止熔炼,以免烧坏感应圈,引起爆炸事故,同时,尽快将炉内铁液倒出来。
3.5.12 调换电炉时,应先断电后调整,禁止带电倒闸。
3.5.13 倾侧炉体倒金属液前,必须清除回转台上异物,以免滑落伤人。
3.5.14 发生停电、停水时,应作如下处理:
a) 若停电时间小于10min,则可不动用备用水;
b) 若停电时间超过10min,则需要接通备用水
c) 若停电时间在1小时之内,则可用木炭或保温剂盖在铁液表面保温,等待继续通电。
d) 若停电时间在1小时以上,则应将铁液倒出。
发现冻结密封“棚炉”现象时,应及时把炉体倾倒一定角度,使冻结部分熔化,禁止用铁棍捅开。
e) 如果在冷料起熔时停电,炉料还没有完全熔化,则不必倾炉,保持原样并继续通水,等待下次通电时再起熔。
3.5.15 变压器室、电容器室内严禁堆放杂物,保持室内干燥和良好的通风。
3.5.16 感应炉修炉应断电进行,工作人员在进出炉膛及操作时,要注意自身和周围人员安全,防止被砸伤、碰伤。
3.5.17 工作场地及炉前地坑内不准积水,不准堆放杂物,保持场地整洁,道路通畅。
4 记录
4.1 中频炉加料(铸铁)记录XQJY4.2.4.11;。