变换工艺设计计算过程
年产36万吨合成氨一氧化碳变换工段工艺设计

摘要本设计为年产36万吨合成氨一氧化碳变换工段工艺设计。
变换工序是合成氨中最重要的工序之一,在合成氨工艺的流程中起着非常重要的作用。
介绍氨的基本性质和用途,阐述了变换工段工艺发展概况,优化了合成变换的工艺流程。
确定本设计采用中变串低变的工艺流程,本次设计利用 ASPEN PLUS V.11对设计过程进行模拟,统筹多种因素合理安排合成工艺中的各种设备及其形式、参数,通过 ASPEN 软件中的 Simulation、Energy analysis 模块完成各部分及全过程的物料及能量衡算。
并对第一变换炉、第二变换炉、煤气换热器以及变换气换热器等主要设备进行选型计算,做出了合成氨变换工段中变串低变的工艺流程图和设备布置图。
所得结果基本满足设计要求,工艺流程可行。
关键词:合成氨一氧化碳 ASPEN PLUS V.11 中低温变换第一章绪论1.1氨的基本性质氨(Ammonia),一种氮和氢的化合物,NH是一种无色气体,有强烈的刺激性3气味,易溶于水,室温和大气压力1体积的水可以溶解700倍体积的氨,水溶液也称为氨水。
它被冷却加压成液体,液氨是一种制冷剂。
氨也是制造硝酸、肥料和炸药的重要原料。
氨对地球上的生命很重要,它是许多食物和肥料的重要成分,氨水也是所有药物的直接或间接成分。
氨有多种用途,但也有腐蚀性和其他危险性。
由于其广泛的用途,氨是世界上最大的无机化合物生产商之一,其中80% 以上用于制造化肥。
氨也是路易斯碱,因为它提供了孤对电子。
1.2 一氧化碳变换反应的意义与目的在合成氨的生产过程的原料中存在着有害的一氧化碳成分,因此就要除去一氧化碳,在这一过程中CO变换起着至关重要的作用。
反应所需的反应气来自天然气,但是天然气中含有一氧化碳成分。
在合成过程所需的原料,不能用一氧化碳,因为毒害作用,会使催化剂失效。
因此必须除去CO成分,这一目的需要在催化剂的促使下通过变换反应来完成。
使用催化剂的情况下,发生CO+H2O=CO2+H2反应。
合成氨变换工段工艺设计

合成氨变换工段工艺设计合成氨是化工工业中的重要原料,广泛应用于制取尿素、硝化铵等农业肥料,以及制取氨水、氨盐、化肥、染料等合成工艺中。
合成氨变换工段是合成氨生产中的关键环节,其工艺设计对合成氨的产量、质量以及能耗等方面有重要影响。
一、工艺概述合成氨的变换反应器是将反应物氮气和氢气通过催化剂的作用,在一定条件下发生气相合成反应,生成合成氨。
反应器通常采用固定床催化剂反应器,催化剂的选择和催化剂床层的设计都是工艺设计的重要环节。
冷凝器主要用于对反应产生的氨气进行冷凝回收,常见的冷凝器有直接冷凝器和间接冷凝器两种形式,工艺设计中需要根据具体情况选择适用的冷凝方式。
循环气压缩机主要用于将反应器中未反应的气体通入新的循环,提高气相合成反应的转化率。
在工艺设计中,需要考虑压缩机的压比、功率消耗等参数。
氨气的分离净化装置主要用于对合成氨中的杂质进行去除,提高合成氨的纯度。
常用的分离净化装置有吸附装置、膜分离装置等,具体的工艺设计需要根据生产要求和经济效益进行选择。
二、工艺参数及控制合成氨的变换工段的工艺参数主要包括反应温度、反应压力、空速、催化剂活性等。
这些参数直接影响合成氨的产率、选择性和能耗。
反应温度是合成氨变换反应的重要参数,通过控制温度可以提高反应速率和转化率,但过高的温度会导致副反应的发生,降低合成氨的选择性。
反应压力主要用于控制氨气的产量和能耗,压力越高产氨越多,但能耗也相应增加。
空速是指单位时间内通过反应器的氮气体积,可以通过调控压力和进气量来实现,过小的空速会影响反应的效果,而过大会导致固定床催化剂的床层冲击和阻力升高,影响反应转化率。
催化剂活性主要指催化剂的活性组分含量和粒径等参数,这些参数会影响合成氨的选择性和催化剂的寿命。
在工艺设计中,需要考虑这些参数的合理选择和控制,以提高合成氨的产量和质量,并降低能耗。
三、能耗控制合成氨的变换工段是合成氨生产中的能耗重点。
能耗的控制主要体现在压力控制、催化剂选择和热交换等方面。
年产十万吨合成氨变换工艺和设备设计核算参考
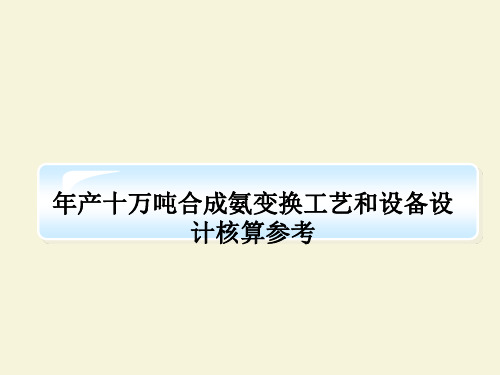
5、工艺流程
本设计主要是变换工序的工艺设计,所选流程为:
H2O
原料气
饱
和
热
水
塔
中
温 变
换热器
换
炉
低 变换气 温 变 换 炉
选用中串低工艺。从压缩工段来的变换气进入饱和
热水塔,在饱和塔出口加入水蒸汽使汽气比达3-5,以 后
再进入中变炉将转换气中一氧化碳含量降到3%以下。
再通过换热器将转换气的温度降到180℃左右,进入低
物量在设备里无物量的变化。
水带入热Q1=XCpT 变换气带入热Q2=nCpmT 同理求得变换气带出热Q3;水带出热Q4。 热量平衡:0.96×(Q1+ Q2)= Q3+ Q4 则X=288.305koml
中变炉一段催化床层的物料衡算
假设CO在一段催化床层的实际变换率为60% 求出在一段催化床层反应后剩余各组分的量 得到出中变炉一段催化床层的变换气干组分的含 进而求得出中变炉一段催化床层变换气湿组分含 量 出中变炉一段催化床层的变换气湿组分的含量 根据:Kp=(H2%×CO2%)/(H2O%×CO%) 计算得Kp,查出对应温度t
主换热器的物料与热量的计算
进出设备的变换气的量:190.97kmol 进出设备的水的量: Xkmol
变换气进设备的温度: 365℃ 变换气出设备的温度: 250℃
水进设备的温度: 水出设备的温度:
20℃ 90℃
变换气带入热Q1=nCpmT;水带入热Q2=XCpT 同理求变换气带出热Q3水带出热Q4 0.96×(Q1+Q2)=Q3+Q4
低变炉的物料计算
要将CO%降到0.2%(湿基)以下,
由CO实际变换率为:Xp=
Ya Ya
年产10万吨合成氨变换工段工艺设计
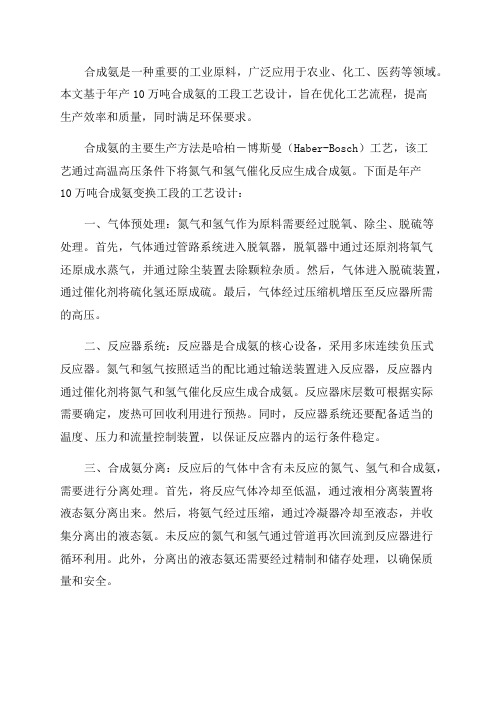
合成氨是一种重要的工业原料,广泛应用于农业、化工、医药等领域。
本文基于年产10万吨合成氨的工段工艺设计,旨在优化工艺流程,提高生产效率和质量,同时满足环保要求。
合成氨的主要生产方法是哈柏-博斯曼(Haber-Bosch)工艺,该工艺通过高温高压条件下将氮气和氢气催化反应生成合成氨。
下面是年产10万吨合成氨变换工段的工艺设计:一、气体预处理:氮气和氢气作为原料需要经过脱氧、除尘、脱硫等处理。
首先,气体通过管路系统进入脱氧器,脱氧器中通过还原剂将氧气还原成水蒸气,并通过除尘装置去除颗粒杂质。
然后,气体进入脱硫装置,通过催化剂将硫化氢还原成硫。
最后,气体经过压缩机增压至反应器所需的高压。
二、反应器系统:反应器是合成氨的核心设备,采用多床连续负压式反应器。
氮气和氢气按照适当的配比通过输送装置进入反应器,反应器内通过催化剂将氮气和氢气催化反应生成合成氨。
反应器床层数可根据实际需要确定,废热可回收利用进行预热。
同时,反应器系统还要配备适当的温度、压力和流量控制装置,以保证反应器内的运行条件稳定。
三、合成氨分离:反应后的气体中含有未反应的氮气、氢气和合成氨,需要进行分离处理。
首先,将反应气体冷却至低温,通过液相分离装置将液态氨分离出来。
然后,将氨气经过压缩,通过冷凝器冷却至液态,并收集分离出的液态氨。
未反应的氮气和氢气通过管道再次回流到反应器进行循环利用。
此外,分离出的液态氨还需要经过精制和储存处理,以确保质量和安全。
四、废气处理:合成氨生产中会产生大量的废气,包括未反应的氮气、氢气、氨气和其他杂质气体。
废气处理主要包括低温分离、吸收、洗涤等步骤。
首先,废气通过低温分离装置将其中的液态氨和水分离出来。
然后,通过吸收剂将氨气吸收,以减少其排放。
最后,利用洗涤液去除废气中的其他杂质气体,确保废气达到环境排放标准。
五、能耗优化:为了降低能耗和提高生产效率,可以采用余热回收和过程优化等措施。
余热回收可通过换热器将反应废热回收利用,进行气体预热和水蒸气生产。
「年产三万吨合成氨厂变换工段工艺设计」

年产三万吨合成氨厂变换工段工艺设计一、工艺流程概述1.原料准备:将天然气(主要是甲烷)与空气作为主要原料,通过气体净化系统去除其中的杂质、硫化物和水分。
2.原料配送:将净化后的天然气和空气分别输送至气体净化系统进行进一步的处理和分析。
3.变换反应槽:将净化后的天然气和空气通过压缩机压缩至一定压力后,经过暖气交换器加热至高温(约500-600℃),再进入变换反应槽。
4.变换催化剂:在变换反应槽中,使用催化剂(通常是高温高压下的铁-钴催化剂)促进N2和H2的反应。
反应生成的合成氨会随气流从反应槽中流出。
5.除气系统:将反应槽中的气体通过除尘器,冷却器和吸附剂等设备进行处理,去除其中的固体颗粒、水分和其他杂质。
6.合成氨回收:经过除气系统处理后的气体中仍含有未反应的氮气和氢气,通过压缩机再次压缩进入蒸馏塔。
在蒸馏塔中,根据不同的沸点,将氨气和氮气分离开来,再通过冷凝器冷凝为液态氨。
7.废水处理:在工艺过程中产生的废水会经过处理系统去除其中的有机物和杂质,以保证排放的废水符合环保要求。
二、设备布置和操作要点1.变换反应槽的设计要考虑到温度、压力和气体流动速度的控制。
同时,需要定期更换催化剂,以维持优良的反应性能。
2.除气系统中的设备要进行定期维护和清洁,确保其正常工作和去除气体中的杂质、固体颗粒和水分。
3.合成氨回收装置要根据产品质量要求设置合适的操作参数,例如蒸馏塔的温度和压力。
此外,冷凝器的冷却水流需要保持稳定,以确保气体顺利冷凝为液态氨。
4.废水处理系统应配置适当的物理和化学处理单元,如过滤器、沉淀池和生物处理等,以达到废水排放标准。
5.需要建立相应的安全措施,如设立监测系统,确保气体和液体在整个工艺中的安全运输和使用。
三、工艺控制和性能优化1.在变换反应槽中,可以通过调节供气比例、压力和温度等参数来控制合成氨的产率和选择性。
同时,也可以根据反馈控制系统监测和调整催化剂的性能。
2.除气系统中的设备可以通过监测气体的组成和温度、压力等参数,来调整操作参数,以达到满足产品质量要求的除气效果。
变换工艺技术

变换工艺技术变换工艺技术是指通过一系列工艺方法和设备,将原始材料转化为更高附加值的成品的过程。
它在现代工业生产中起着重要的作用,可以提高生产效率、降低成本、改善产品品质等。
变换工艺技术主要包括物理变换、化学变换和结构变换三种类型。
物理变换是指通过改变原材料的形态、大小、密度等物理特性来实现转化的过程。
比如,将原材料加热至一定温度,使其改变形态,从而转化为其他物质。
化学变换是指通过化学反应将原材料转化为其他物质的过程。
比如,将原材料与其他物质反应生成化合物。
结构变换是指通过改变原材料的分子结构,使其性质发生变化的过程。
比如,通过加工原材料,使其分子结构发生断裂和重组。
变换工艺技术的应用范围非常广泛。
在冶金工业中,变换工艺技术可以将原矿石转化为金属,如将铁矿石经过冶炼熔炼得到铁。
在化工工业中,变换工艺技术可以将原材料转化为化学产品,如将石油通过精炼过程转化为汽油、柴油等。
在食品加工工业中,变换工艺技术可以将农产品转化为食品,如将小麦经过加工转化为面粉、面条等。
在纺织工业中,变换工艺技术可以将纤维转化为纺织品,如将棉花经过纺纱、织造过程转化为棉织物等。
变换工艺技术的实现需要依靠各种工艺流程和设备。
比如,物理变换工艺通常包括物理处理、物理分离等过程,需要使用研磨机、过滤机、离心机等设备。
化学变换工艺通常包括化学反应、溶剂提取等过程,需要使用反应釜、提取器等设备。
结构变换工艺通常包括加工、改变分子结构等过程,需要使用破碎机、扩散炉等设备。
变换工艺技术的发展可以提高生产效率和产品质量,并且可以降低生产成本。
通过将原材料转化为高附加值的成品,可以获得更多的经济效益。
同时,变换工艺技术还可以实现资源的有效利用和环境的保护。
通过合理设计工艺流程和设备,可以减少原材料和能源的消耗,并且减少废弃物和污染物的产生,达到可持续发展的目标。
总之,变换工艺技术是现代工业生产中不可或缺的技术之一。
它通过一系列工艺方法和设备,将原材料变换为更高附加值的成品,提高生产效率、降低成本、改善产品品质,实现资源的有效利用和环境的保护。
合成氨变换工段工艺过程设计

合成氨变换工段工艺过程设计摘要:在合成氨生产过程中,换热器应用十分广泛,主要用于热量的交换和回收。
变换工段中主要涉及一氧化碳的转化和能量的回收利用,列管换热器在传热效率,紧凑性和金属耗量不及某些换热器,但它具有结构简单,坚固耐用,适用性强,制造材料广泛等独特优点,因而,在合成氨变换工段选择列管式换热器,而本设计主要对该换热器进行相关选型和计算。
关键词:换热器,变换,设计。
Abstract:In the ammonia production process, heat exchanger, a wide range of applications, mainly for heat exchange and recycling. Transformation Process and mainly involves the conversion of carbon monoxide and energy recycling, tube heat exchanger in heat transfer efficiency, compactness and metal consumption is less than some heat, but it has a simple structure, rugged durability, applicability, manufacturing wide range of other materials, unique merits, which, in the ammonia shift conversion section select tube heat exchanger, and this system is mainly related to the heat exchanger selection and calculated.Keywords: heat exchanger, transform and design.目录摘要 (1)第一章工艺流程概述 (2)1.1 氨的概述 (2)1.1.1氨的性质 (2)1.1.2氨的用途 (2)1.1.3氨的合成的原料 (2)1.2 合成氨的工艺原理 (2)1.3 工艺条件 (3)1.3.1 压力 (3)1.3.2 温度 (4)1.3.3 汽气比 (4)1.4 固定管板式换热器 (5)1.4 变换工段简介 (6)第二章工艺过程设计 (7)2.1估算传热面积 (7)2.1.1查取物行数据 (7)2.1.2热量衡算 (7)2.1.3确定换热器的材料和压力等级 (7)2.1.4流体通道的选择 (7)2.1.5计算传热温差 (8)2.1.6 选K值,估算传热面积 (8)2.1.7初选换热器型号 (8)2.2计算流体阻力 (9)2.2.1管程流体阻力 (9)2.2.2壳程流体阻力 (9)2.3 计算传热系数校正传热面积 (10) (10)2.3.1管程对流给热系数αi (10)2.3.2壳程对流传热系数α2.3.3计算传热系数 (10)2.3.4计算传热面积 (11)参考文献 (12)致谢 (13)第一章工艺过程设计概述1.1合成氨的生产过程20世纪初,德国物理化学家哈勃(F.Haber)成功的采用化学合成的方法,将氢氮气通过催化剂的作用,在高温高压下制取氨。
年产二十万吨合成氨变换工段工艺设计

合成氨变换工段是合成氨生产过程中的关键工艺环节之一,它将合成气中的氮气和氢气在催化剂的作用下,通过催化反应转化为合成氨。
本文将围绕年产二十万吨合成氨的变换工段工艺设计进行详细阐述,旨在提供一个完整的工艺设计方案。
首先,变换工段的催化剂选择非常重要。
对于年产二十万吨合成氨的工艺,常用的催化剂有铁素体、铁铬铝混合催化剂等。
这些催化剂在一定的操作条件下,能够实现高效的合成氨转化率和选择性。
在实际应用中,应根据具体工艺要求和经济效益进行选择。
其次,合成气的净化和预热是变换工段的重要准备工作。
合成气中常含有一定的杂质,如氧、水蒸气、二氧化碳等,这些杂质会影响催化剂的活性和寿命。
因此,合成气需要通过一系列净化设备,如除氧、除硫、除水等步骤,将其净化为适合变换反应的合成气。
同时,为了提高反应的热效应,还需要对合成气进行预热,一般可以采用换热器进行热量回收。
接下来是变换反应的具体设计。
变换反应是一个平衡反应,根据Le Chatelier原理,可以通过提高反应温度、降低反应压力、增加氢气过量等方式推动平衡向产氨方向偏移。
在实际设计中,应在考虑较高转化率的前提下,平衡反应速率和催化剂活性与寿命的关系,做出合理的选择。
另外,变换反应需要保持一定的循环气速和循环气气体组成。
循环气速过高会造成能耗增加,循环气速过低则会影响气体传质效果。
循环气气体组成应符合催化剂的操作条件,一般应保持一定的氢气过量,同时控制氮气和氢气的比例。
最后是变换工段的控制策略。
合成氨变换工段是一个高温高压的工艺过程,对于安全和稳定运行,需要建立完善的自动化控制系统。
控制策略应包括反应温度和压力的控制、循环气速和气体组成的控制、催化剂的修复和更换等。
在实际设计中,应结合具体的工艺要求和设备性能,进行综合技术经济分析,选取最佳的工艺参数和操作条件。
同时,在设计过程中还应考虑到工艺的可持续性和环境保护要求,合理利用资源,减少废物排放,实现工艺的可持续发展。
一氧化碳变换

中温变换工艺设计方案目录前言 (2)1、背景 (2)2、分类 (2)3、工艺方法的选择 (2)反应原理 (3)中温变换催化剂 (4)工艺流程 (6)工艺条件 (7)设计体会与收获 (8)参考文献 (9)前言氨是一种重要的化工产品,主要用于化学肥料的生产。
合成氨生产经过多年的发展,现已发展成为一种成熟的化工生产工艺。
合成氨的生产主要分为:原料气的制取;原料气的净化与合成。
粗原料气中常含有大量的C,由于CO是合成氨催化剂的毒物,所以必须进行净化处理,通常,先经过CO变换反应,使其转化为易于清除的CO2和氨合成所需要的H2。
因此,CO变换既是原料气的净化过程,又是原料气造气的继续。
最后,少量的CO用液氨洗涤法,或是低温变换串联甲烷化法加以脱除。
1、背景变换是合成氨生产中的重要工序,同时也是一个耗能重点工序,而外加蒸汽量的大小,是衡量变换工段能耗的主要标志。
因此,尽量减少其用量对其过程的节能降耗具有重要意义。
从70年代以来,我国在变换工艺的节能降耗方面,进行了大量的科研开发和技改工作,先后开发了中变、中变串低变、全低变等变换工艺,使蒸汽消耗量从传统的中变消耗1 t/tNH 以上,降低到200 kg/tNH,从而形成一种能耗低、稳定可靠、周期长的变换工艺。
2、分类一氧化碳变换的工艺流程包括中变-低变串联流程、多段中变流程、全低变流程、中低低流程等。
3、工艺方法的选择变换工艺流程的设计,首先应依据原料气中的一氧化碳含量高低来加以确定。
以煤为原料气的中小型氨厂制得的半水煤气中含有较高的一氧化碳,所以需采用多段中变流程。
中变催化剂操作温度范围较宽,而且价廉易得,使用寿命长。
因此,在一氧化碳转换工艺设计中,我组选用中温变换工艺。
反应原理变换反应可用下式表示:此外,一氧化碳与氢之间还可发生下列反应(1-2) O H C H CO 22+⇔+(1-3)但是,由于变换所用催化剂对反应式(1-1)具有良好的选择性,从而抑制了其他副反应的发生。
合成氨变换工段工艺过程设计
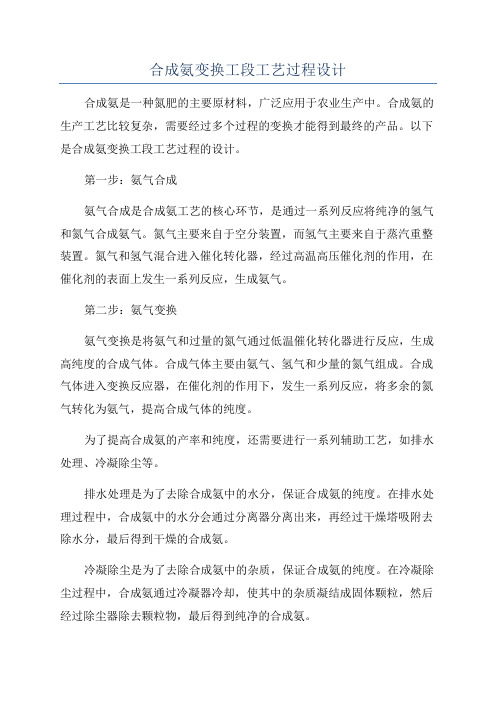
合成氨变换工段工艺过程设计
合成氨是一种氮肥的主要原材料,广泛应用于农业生产中。
合成氨的生产工艺比较复杂,需要经过多个过程的变换才能得到最终的产品。
以下是合成氨变换工段工艺过程的设计。
第一步:氨气合成
氨气合成是合成氨工艺的核心环节,是通过一系列反应将纯净的氢气和氮气合成氨气。
氮气主要来自于空分装置,而氢气主要来自于蒸汽重整装置。
氮气和氢气混合进入催化转化器,经过高温高压催化剂的作用,在催化剂的表面上发生一系列反应,生成氨气。
第二步:氨气变换
氨气变换是将氨气和过量的氮气通过低温催化转化器进行反应,生成高纯度的合成气体。
合成气体主要由氨气、氢气和少量的氮气组成。
合成气体进入变换反应器,在催化剂的作用下,发生一系列反应,将多余的氮气转化为氨气,提高合成气体的纯度。
为了提高合成氨的产率和纯度,还需要进行一系列辅助工艺,如排水处理、冷凝除尘等。
排水处理是为了去除合成氨中的水分,保证合成氨的纯度。
在排水处理过程中,合成氨中的水分会通过分离器分离出来,再经过干燥塔吸附去除水分,最后得到干燥的合成氨。
冷凝除尘是为了去除合成氨中的杂质,保证合成氨的纯度。
在冷凝除尘过程中,合成氨通过冷凝器冷却,使其中的杂质凝结成固体颗粒,然后经过除尘器除去颗粒物,最后得到纯净的合成氨。
综上所述,合成氨变换工段工艺过程的设计包括氨气合成和氨气变换两个主要步骤,同时还需要进行排水处理和冷凝除尘等辅助工艺。
这些步骤的设计要考虑反应温度、反应压力、催化剂的选择和管理,以及对产物的分离、干燥和净化等。
通过合理的工艺设计和操作管理,可以提高合成氨的生产效率和产品质量。
合成氨变换工段流程图年产8万吨小合成氨厂中温变换工段工艺设计
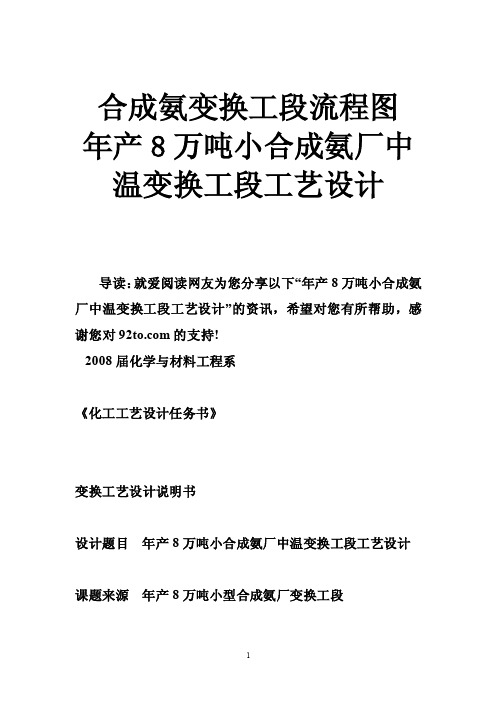
合成氨变换工段流程图年产8万吨小合成氨厂中温变换工段工艺设计导读:就爱阅读网友为您分享以下“年产8万吨小合成氨厂中温变换工段工艺设计”的资讯,希望对您有所帮助,感谢您对的支持!2008届化学与材料工程系《化工工艺设计任务书》变换工艺设计说明书设计题目年产8万吨小合成氨厂中温变换工段工艺设计课题来源年产8万吨小型合成氨厂变换工段变换工段化学工艺设计标准变换工段在合成氨生产起的作用既是气体净化工序,又是原料气的再制造工序,经过变换工段后的气体中的CO含量大幅度下降,符合进入甲烷化或者铜洗工段气质要求。
要求:1. 绘制带控制点的工艺流程图2. 系统物料、能量衡算3. 系统主要设备能力及触媒装填量核算4. 该工段设备多,工艺计算复杂,分变换炉能力及触媒装填量核算、系统热量核算和系统水循环设备及能力核算。
变换工段化学工艺设计主要技术资料1. 变换技术方案CO2变换反应是放热反应,从化学平衡来看,降低反应温度,增加水蒸汽用量,有利于上述可逆反应向生成CO2和H2的方向移动,提高平衡变换率。
但是水蒸气增加到一定值后,变换率增加幅度会变小。
温度对变换反应的速度影响较大,而且对正逆反应速度的影响不一样。
温度升高,放热反应即上述反应速度增加得慢,逆反应(吸热反应)速度增加得快。
因此,当变化反应开始时,反应物浓度大,提高温度,可加快变换反应,在反应的后一阶段,二氧化碳和氢的浓度增加,逆反应速度加快,因此,需降低反应温度,使逆反应速度减慢,这样可得到较高的变化率。
但降温必须与反应速度和催化剂的性能一并考虑,反应温度必须在催化剂的使用范围内选择。
在本设计中我们选择三段中温变化工艺流程。
2. 工艺流程含32.5% CO、温度为40℃的半水煤气,加压到2.0Mpa,经热水洗涤塔除去气体中的油污、杂质,进入饱和塔下部与上部喷淋下来的120~140℃的热水逆流接触,气体被加热而又同时增湿。
然后在混合器中与一定比例的300~350℃过热蒸汽混合,25%~30%的气体不经热交换器,作为冷激气体。
小合成氨厂低温变换工段工艺设计

小合成氨厂低温变换工段工艺设计1.工艺流程合成氨的低温变换工艺流程包括氨气脱除、氢气供应、氮氢混合、压缩、变换反应和冷却净化等步骤。
具体流程如下:(1)氨气脱除:从合成气中去除氨气。
合成气通常包括氮气、氢气和少量的甲烷、一氧化碳等。
氨气脱除可以采用吸收剂或者低温冷凝的方式进行。
(2)氢气供应:合成氨需要大量的氢气供应。
氢气可以通过蒸汽重整、部分氧化等方式产生。
(3)氮氢混合:将氮气和氢气按照一定的比例混合,以提供合适的反应物组成。
(4)压缩:将混合气体压缩到合适的工艺压力,以增加反应速率和提高反应效果。
(5)变换反应:将压缩的气体通入低温变换器中,反应产生氨气。
这个过程是一个放热反应,需要控制反应温度和催化剂的作用。
(6)冷却净化:将变换产生的气体冷却,去除其中的杂质和不稳定的气体组分,以获得高纯度的合成氨。
2.工艺参数合成氨的低温变换工段的设计需要考虑多个工艺参数,包括反应温度、反应压力、气体流量、催化剂选择等。
(1)反应温度:低温变换反应需要控制在适当的温度范围内进行。
反应温度过高会导致催化剂失活,而温度过低则会影响反应速率和产氨量。
(2)反应压力:反应压力是影响反应平衡的重要参数,对氨气产率和选择性有很大影响。
通常情况下,反应压力较高可以提高氨气产率,但同时也增加了设备的投资和运行成本。
(3)气体流量:气体流量直接影响反应物在催化剂上的接触和反应速率。
合适的气体流量可以提高反应效果,但如果流量过大,会增加压力损失和能耗。
(4)催化剂选择:催化剂是低温变换反应的关键,其选择需要考虑活性、稳定性和寿命等因素。
常用的催化剂有铁、铂、钼等,可以单一使用或者组合使用。
3.安全控制在低温变换工段的设计中,安全控制是非常重要的。
一方面,低温反应需要保证设备和管道的密封性和抗冻性,以防止设备爆炸和泄漏事故。
另一方面,反应温度和压力需要在合适的范围内稳定控制,以防止设备超负荷运行和产生危险反应。
此外,还需要考虑废气处理、电力供应等问题,以确保低温变换工段的安全和稳定运行。
变换-净化工艺流
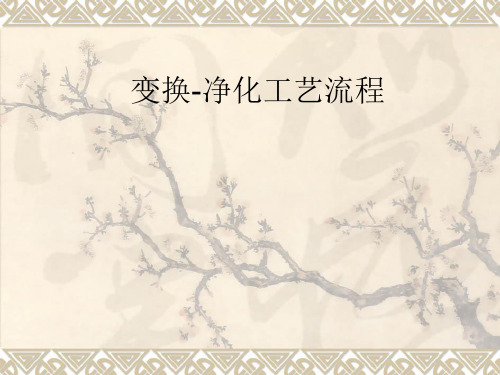
(2)
上述硫化过程中的H2S是靠粗煤气提供的,由于粗煤气中H2S含量很低,所以为了保证足够的
H2S含量,以保证硫化过程顺利进行,我厂采用向系统内连续添加CS2的方法,使其发生氢解反应生
成H2S:
CS2+4H2=2H2S+CH4
2.2 操作参数
出变换工序变换气CO 含量 21%
变换炉入口温度
265-280℃
Qcs-03型钴钼耐硫变换催化剂。由于它采用了新的组分和制造工艺,区别于原有的钴钼耐硫 变换触媒体系,其变换活性高,特别是低温变换活性和在低H2S浓度下的活性尤为明显,对高空 速,低水气比的适应能力和稳定性优于K8-11,可用于硫化物含量≥100ppm的工艺气,从而它既 可作为中温耐硫变换触媒使用,也可作为低温变换触媒使用。
HV 2005
E2005
HV
FIQ 2006
TI 2012
2006
LV 2004
HV 2008
HV 2007
LV
V2002
2006
TI 2013
V2003
LV
LV
2005
FIQ
2007
2007
P2012 M
V2009
地沟 冷凝液去气化
冷凝液来自低温甲醇洗 锅炉给水去气化 高压闪蒸气来自气化
V2006
P2001A/B P2002A/B P2003A/B
P2004A/B
P2005A/B
P2006A/B
P2007A/B P2008A/B
P2009A/B
P2010A/B
P20011A/B
冷凝液泵Ⅰ 冷凝液泵Ⅱ 低压锅炉给水泵Ⅰ 低压锅炉给水泵Ⅱ 中压锅炉给水泵Ⅰ 中压锅炉给水泵Ⅱ 密封水泵 脱氧加药泵 低压锅炉加药泵 高压锅炉加药泵 甲醇合成锅炉加药泵
年产25万吨煤制合成氨耐硫变换工序工艺设计

第一章文献综述合成氨的原料是氢和氮两种气体。
空气中存在着取之不尽的氮,而氢则多是取之于水或水蒸汽。
合成氨厂的制氢方法多数是用烃类或煤碳夺去水分子中的氧,而放出氢气。
据统计,1975年国外合成氨原料中天然气占69.6%,石脑油占14.9%,煤占8%,重油及炼厂气分别占2.7%和2.5%。
以后合成氨原料将以天然气占首位,因为天然气制合成氨工艺流程简单,基建投资节省,生产成本低,而且气体原料相对来说比较纯净,它的净化比液体或固体原料简单,气体的输送也比液体或固体更易控制和自动化。
石脑油蒸汽转化法制合成氨的过程与天然气基本相同,但原料精制要复杂一些,脱碳和二氧化碳再生负荷也更大一些。
但油类的运输在一定情况下比气体容易。
以煤为原料合成氨虽然从造气和净化的成本来说,煤碳最高,工艺流程也比较复杂。
但按目前消耗速度来看,气、油只能维持供应30-40年,而煤能维持300年,可见煤是具有巨大潜力的。
山西不具备天然气和石油资源,而具有丰富的煤碳资源,所以我们选用煤为原料来合成氨。
由气态烃、液态烃和煤为原料制成的原料气中含有15-50%的CO,CO不仅不是合成氨的直接原料,而且对氨合成催化剂有毒害。
所以在原料气送往合成工序之前必须清除干净。
生产中通常采用变换反应除去大部分CO,即CO在催化剂存在的条件下和水蒸汽反应,生成CO2和H2.这样一方面增加了合成氨反应所需的氢气,同时又除去了合成氨催化剂的毒物CO。
视进一步除去残余CO的方法,对变换反应的深度的要求也不一样。
后工序如用铜氨液洗或液氮洗涤,则允许残余CO在3%左右,此时变换反应的温度较高(400℃以上),通常被称为高温变换。
若后工序用甲烷化法除去CO,则要求将CO 降到1%以下,此时变换反应的温度较低(300℃左右),称为低温变换。
因为后工序中选用液氮洗除去CO和 CH4,所以要采用高温变换过程。
变换反应需要在催化剂作用下进行。
目前工业上常用的变换催化剂有三种:铁系催化剂(使用温度320℃-550℃)、钴钼系催化剂(使用温度(300℃-500℃)和铜系催化剂(使用温度180℃-280℃)。
合成氨变换工段工艺设计
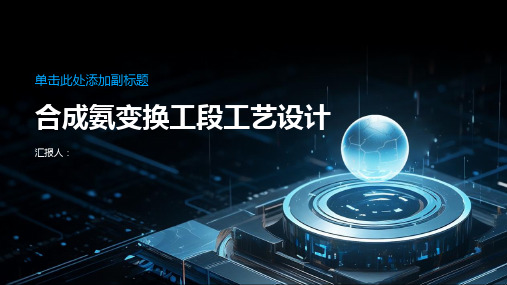
添加标题
添加标题
智能化:自动化控制,提高生产 效率,降低人工成本
挑战:技术研发投入大,市场竞 争激烈,环保要求不断提高
感谢观看
汇报人:
单击此处添加副标题
合成氨变换工段工艺设计
汇报人:
目录
01 02 03 04 05 06
添加目录项标题 合成氨变换工段概述 合成氨变换工段工艺流程 合成氨变换工段设备与操作 合成氨变换工段安全与环保 合成氨变换工段优化与改进
01
添加目录项标题
02
合成氨变换工段概述
合成氨变换工段定义
合成氨变换工段是 合成氨生产过程中 的一个重要环节
冷却目的:降低变换气的温度,提高反应效率 冷却方式:采用水冷或气冷方式 分离目的:将变换气中的氨和氮气分离,提高氨的纯度 分离方式:采用冷凝、吸收或膜分离等方式
04
合成氨变换工段设备与操作
设备组成及功能
压缩机:用于提高气体压力, 提高反应速率
冷凝器:用于气体冷凝,回 收热量和氨气
换热器:用于热量交换,提 高反应效率
净化效果:提高原料气纯度,降低有害物 质含量
净化后原料气输送:输送至合成氨变换工 段进行反应
变换反应
反应原理:氮气和氢气在催化剂作用下生成氨气 反应条件:高温、高压、催化剂 反应产物:氨气、氮气、氢气 反应过程:氮气和氢气在催化剂作用下发生反应,生成氨气和氮气,同时释放出热量和压力。
变换气冷却与分离
防火防爆:设置 防火防爆设施, 防止火灾爆炸事 故
环保措施:采用 环保技术,减少 废气、废水、废 渣排放,保护环 境
环保要求及排放控制
废水处理:采用先进处理技 术,实现废水循环利用
废气处理:采用高效净化设 备,减少废气排放
年产20万吨合成氨变换工段工艺设计

年产20万吨合成氨变换⼯段⼯艺设计第1页化⼯设计说明书设计题⽬: 年产20万吨合成氨变换⼯段⼯艺设计系别:化学化⼯学院专业:班级:学⽣:指导⽼师:20年X⽉X⽇本章符号对照表M ——相对分⼦质量,g/mol t/T ——温度,℃ /K Vm ——摩尔体积(0℃,0.1Mpa )22.4/(L/mol) V ——半⽔煤⽓体积,m 3 p co 、p H2O 、p co2 、p H2 ——分别为CO 、H 2 O 、CO 2和H 2各组分的分压H ——标准摩尔焓(kJ /mol )ρ/r ——密度/(kg/ m 3) S ——标准摩尔熵/(J/mol ·k) K p ——平衡常数Kt ——反应速率常数,mol/(MPa0.5·g ·h ) m ——质量,kgy co 、y H2O 、y co2 、y H2 ——分别为CO 、H 2 O 、CO 2和H 2 摩尔分数X ——实际变换率,%y a 、y a ′——分别为原料⽓及变换⽓中⼀氧化碳的摩尔分数Cp ——⽓体的平均⽐热容,kJ/(kmol ·℃)或kJ (kg ·℃)R ——⽓体常数,8.314J/(mol ·K)E ——化学反应活化能,J/molg ——重⼒加速度,m/s2G ——⽓体质量流速,kg/(m2·h) Tm ——最适宜温度,Ki ——⽔蒸⽓在t ℃时的焓,kj/kgΦ——饱和度,% Q ——热量,kJw ——⼲⽓空间速度 m/s u ——催化剂⾃由容积分数 R ——汽/⽓⽐ Di ——塔体内直径,mm d e ——当量直径,m H 塔⾼,mmη——管板填充系数 n ——列管根数 t ——管⼦中⼼距µm ——混合⽓体在温度t 时的黏度,MPa·sµi ——混合⽓体中i 组分在温度t 时的黏度,MPa·sy i ——混合⽓体中i 组分摩尔分数 M i ——混合⽓体中i 组分的分⼦量S a ——⼸形截⾯积,m 2 hˊ——⼸形⾼度,m H ——档板间距,mF ——传热⾯积,m 2 L ——列管长度,m K ——总传热系数,kJ/(m 2 ·h·℃) φ——塔体焊缝隙数 [σ]300 ——筒体材料在设计温度300℃下的许⽤应⼒ C 1 ——钢板厚度负偏差,mm C 2——腐蚀裕量,mm⽬录前⾔ (7)1 绪论 (7)1.1 氨的性质和⽤途 (7)1.2 ⼩型氨⼚的发展 (8)1.3 合成氨⽣产⽅法简介 (8)1.4 ⼀氧化碳变换在合成氨中的意义 (8)2 ⼀氧化碳脱除⽅发和选择 (11)2.1⼀氧化碳的脱除⽅法 (11)2.2⼀氧化碳脱除的⽅案选择 (11)3 ⼀氧化碳变换⽅案 (12)3.1变换原理 (12)3.2变换⽅案的选择 (13)3.3 中变炉的选择 (13)4 变换⼯艺的计算 (15)4.1 中变炉的计算 (15)4.2 饱和热⽔塔出⼝热⽔温度估算 (24) 4.3 饱和热⽔塔物料和热量计算 (24)4.4 换热⽓物料和热量的计算 (28)5 设备的计算 (35)5.1 变换炉的计算 (35)5.2 饱和热⽔塔的计算 (38)5.3主热交换器的计算 (44)5.4 中间换热器的计算 (48)5.5 ⽔加热器的计算 (50)5.6 热⽔循环塔的计算 (53)5.7 变换冷却器的计算 (56)6 变换炉的结构的计算 (60)6.1 变换炉设计条件 (60)6.2变换炉结构计算 (60)7 设备的选型 (66)8 变换反应的⼯艺参数和⼯艺条件 (67) 8.1变换反应的⼯艺参数 (67)8.2 变换过程的⼯艺条件 (67)9 设计结果⼀览表 (70)参考⽂献 (71)致谢 (72)年产20万吨合成氨变换⼯段⼯艺设计指导⽼师:摘要:⽤中温中压三段变换的⽅法,半⽔煤⽓⾸先经过饱和热⽔塔,在饱和热⽔塔内⽓体与塔顶流下的热⽔逆流接触进⾏热量与质量传递,使半⽔煤⽓体温增湿,出塔⽓体进⼊⽓⽔分离器分离夹带的液滴,再进⼊主热换热器、中间换热器和电炉升温,使温度达到320℃左右进⼊变换炉⼀段。
合成氨厂CO变换工艺设计说明书

68t氨/d 合成氨厂CO变换工艺设计摘要氨是一种重要的化工产品,主要用于化学肥料的生产。
合成氨生产经过多年的发展,现已发展成为一种成熟的化工生产工艺。
合成氨的生产主要分为:原料气的制取;原料气的净化与氨合成。
一氧化碳变换是指一氧化碳与水蒸气反应生产二氧化碳和氢气的过程。
在合成氨工艺流程中起着非常重要的作用。
在合成氨生产中,原料气中的一氧化碳都来源于含碳氢物质,如煤、天然气、油等。
半水煤气则是以煤为原料制得的含有氢气和一氧化碳等多种气体的混合物。
一氧化碳会使催化剂中毒,而合成氨工艺中所需的氢气则是一氧化碳和水反应制得。
因此在氨合成过程中必须进行一氧化碳变换。
这样不但去除了一氧化碳同时产生了合成氨的原料气氢气。
本次设计的主要任务是设计完成合成氨过程中净化车间一氧化碳多段变换的工艺流程。
本次设计采用中变串低变的工艺流程,在本流程中使用宽变催化剂可使操作条件有较大变化。
它使入炉煤气的蒸汽比有较大幅度的降低,而且使一氧化碳含量降低。
正是由于选用宽温催化剂,使得反应条件得以大大改进。
选用该流程的目的是为了让原料气净化程度高,流程简单,操作方便,稳定性好,催化剂使用时间长。
设计说明书包括三部分:工艺设计说明、变换工段的工艺计算及主要设备的工艺计算。
另外,附有四张设计图纸:一张管道及仪表流程图,一张平面布置图,一张物料流程图及一张设备一览表。
关键词:半水煤气、CO变换、催化剂The CO Transform Process DesignOf 68t ammonia/d Synthetic Ammonia plantAbstractAmmonia is an important chemical product, mainly for the production of chemical fertilizers. The production of synthetic ammonia has developed into a mature chemical production process through years of development. It is mainly divided into: the preparation of the raw gas; the purification of the raw gas and a the synthesis of mmonia.The transformation of carbon monoxide refers to the production of carbon monoxide and hydrogen response with carbon dioxide and water. It plays a very important role in the synthetic ammonia process. In the production of synthetic ammonia the carbon monoxide is containing comes from hydrocarbon, such as coal, oil and gas, etc. Semi-water gas is made for the raw coal and a mixture of gases including hydrogen and carbon monoxide. Carbon monoxide will make catalyst poisoned in the process , but hydrogen is made for the reaction of water and carbon monoxide. Therefore in the ammonia synthetic process must have the transformation of carbon monoxide. In addition to this , it also products the hydrogen gas which is the materal gas of synthetic ammonia. The main task of the design is to complete the transformation of carbon monoxide which is a part of the purification workshop of ammonia synthetic process . This design use the process of low temperature combined middle temperature, and the use of the wide temperature shift catalyst can make a significant changes in the operating conditions. It makes the ratio of steam into the furnace gas reduced significantly, and reduce the level of carbon monoxide. The reaction conditions can be improved greatly because of the selection of the wide temperature catalyst. The choice of using the process is to let the raw gas have a high degree purification, have a simple process , easy to operate, stability is good, catalyst have a long use time.The design specification includes three components: the design specifications of the process, the process calculation of the transform section and the process calculation ofmain equipment. In addition, four design drawings is accompanied: a piping and instrumentation diagrams, a layout plan, a material flow chart and an equipment list. Keywords: Semi-water gas, CO shift, catalyst目录摘要 (I)Abstract (II)前言 (1)第一章一氧化碳变换的工艺说明 (2)1.1设计依据 (2)1.2原料动力学消耗定额和消耗量 (2)1.3一氧化碳变换原理 (2)1.4一氧化碳变换催化剂 (3)1.4.1 铁-铬系一氧化碳中温变换催化剂 (3)1.4.2 一氧化碳宽温耐硫变换催化剂 (4)1.5工艺流程说明 (5)1.6设备选型及布置 (8)1.6.1设备选型的基本要求 (8)1.6.2 设备布置说明 (8)1.7三废治理说明 (9)1.8本工段各种工艺操作指标 (10)第二章一氧化碳变换工艺计算 (11)2.1设计条件 (11)2.2中温变换炉物料及热量计算 (12)2.2.1干变换气量及变换率的计算 (12)2.2.2 总蒸汽比(汽/气)的计算 (13)2.2.3中变炉一段催化剂层物料及热量衡算 (14)2.2.4 中变炉二段催化剂层物料及热量计算 (20)2.3低温变换炉物料及热量计算 (24)2.3.1 物料计算 (24)2.3.2 热量衡算 (25)2.3.3平衡曲线、最适宜温度曲线及操作线计算 (26)2.4饱和热水塔出口温度的估算 (27)2.4.1 水加热器出口变换气温度计算 (27)2.4.2 热水塔出口排水温度 (27)2.4.3饱和塔出口半水煤气温度 (28)2.5中间换热器物料及热量计算 (28)2.5.1蒸汽过热段 (28)2.5.2 半水煤气换热器 (30)2.6主热交换器物料及热量横算 (31)2.6.1 已知条件 (31)2.6.2 进设备半水煤气温度计算 (32)2.6.3 出热交换器的变换气温度计算 (33)2.7调温水加热器中变换气放出的热量计算 (34)2.8水加热器中低变气放出热量计算 (35)2.9饱和热水塔物料及热量计算 (36)2.9.1饱和塔物料及热量计算 (36)2.9.2热水塔物料及热量计算 (38)2.9.3 进饱和塔水温核算 (41)第三章典型设备计算 (41)3.1中温变换炉计算 (42)3.1.1已知条件 (42)3.1.2催化剂用量计算 (43)3.1.3催化剂床层直径的确定 (44)3.2低温变换炉计算 (46)3.2.1 已知条件 (46)3.2.2 催化剂用量计算 (47)3.2.3 催化剂床层直径的确定 (47)3.3饱和热水塔计算 (48)3.3.1 饱和塔计算 (48)3.3.2 热水塔计算 (53)参考文献 (59)附录1 (60)附录2 (61)附录3 (62)附录4 (63)致谢 (64)前言合成氨是化学工业的重要组成部分,在国民经济中有相当重要的位置。
变换计算

第2章变换工段物料及热量衡算2.1 中温变换物料衡算及热量衡算2.1.1.确定转化气组成:已知条件中变炉进口气体组成见表2-1。
表2-1计算基准:1吨氨计算生产1吨氨需要的变化气量:(1000/17)×22.4/(2×22.56)=2920.31 M3(标)因为在生产过程中物量可能回有消耗,因此变化气量取2962.5 M3(标)年产5万吨合成氨生产能力:日生产量:50000/330=151.52T/d=6.31T/h要求出中变炉的变换气干组分中CO%小于2%进中变炉的变换气干组分见表2-2。
表2-2假设入中变炉气体温度为335摄氏度,取出炉与入炉的温差为30摄氏度,则出炉温度为365摄氏度。
进中变炉干气压力中P =1.75Mpa. 2.1.2.水汽比的确定:考虑到是天然气蒸汽转化来的原料气,所以取H 2O/CO=3.5故V (水)=1973.52m 3(标) n (水)=88.1kmol表2-3因此进中变炉的变换气湿组分: 中变炉CO 的实际变换率的求取:假定湿转化气为100mol ,其中CO 基含量为8.16%,要求变换气中CO 含量为2%,故根据变换反应:CO+H 2O =H 2+CO 2,则CO 的实际变换率为:X %=()a a a a Y Y Y Y '+'-1×100=74%式中Ya、'aY分别为原料及变换气中CO的摩尔分率(湿基)则反应掉的CO的量为:8.16×74%=6.04则反应后的各组分的量分别为:H2O%=28.56%-6.04%+0.48%=23%CO%=8.16% -6.04%=2.12%H2% =39.8%+6.04%-0.48%=45.36%CO2%=6.86%+6.04%=12.9%中变炉出口的平衡常数:K= (H2%×CO2%)/(H2O%×CO%)=12查《小合成氨厂工艺技术与设计手册》可知K=12时温度为397℃。
合成氨变换工段工艺过程设计

合成氨变换工段工艺过程设计合成氨是工业上重要的基础化工原料之一,广泛应用于农业、化工、制药和塑料等领域。
合成氨的工艺过程设计涉及到合成氨反应器、氨分离系统、废气处理系统以及其他辅助设备。
一、合成氨反应器合成氨的反应器一般采用固定床催化剂的方式进行,反应温度常在350-550℃,反应压力常在80-200atm之间。
催化剂常采用以铁为主的复合催化剂,其主要成分有铁、铝、钾等金属氧化物。
该反应器的主要作用是将反应物氮气和氢气在催化剂的催化下发生氧化还原反应生成氨气。
二、氨分离系统由于氨合成反应气体中还含有大量的未反应氢气、氮气以及少量的二氧化碳、水蒸汽和甲烷等杂质物,因此需要将氨与这些杂质物进行分离。
首先对反应气体进行冷凝和除湿处理,以去除水蒸汽;然后采用吸附剂进行氨的吸附和脱附,以去除未反应的气体;最后再通过精馏系统进行氢、氮等杂质物的分离,得到高纯度的氨。
三、废气处理系统氨合成反应会产生一些副产物和废气,包括尾气、废液、废水等。
尾气中主要含有未反应的氮气、未分离的氢气、氧气和少量氨等物质。
因此需要对这些废气进行深度处理,以降低对环境的污染。
常见的处理方法包括尾气洗涤、氨的催化氧化等。
四、其他辅助设备合成氨生产过程中还需要用到一些辅助设备,如氢气制备系统、氮气制备系统、冷却系统、压缩系统、脱硫系统、催化剂再生系统等。
这些设备的作用是为合成氨反应提供所需的气体原料、冷却剂以及对反应物质进行净化和处理。
总结起来,合成氨的工艺过程设计主要涉及合成氨反应器、氨分离系统、废气处理系统以及其他辅助设备。
通过合理设计和配置这些设备,能够实现高效、稳定和环保的合成氨生产过程。
- 1、下载文档前请自行甄别文档内容的完整性,平台不提供额外的编辑、内容补充、找答案等附加服务。
- 2、"仅部分预览"的文档,不可在线预览部分如存在完整性等问题,可反馈申请退款(可完整预览的文档不适用该条件!)。
- 3、如文档侵犯您的权益,请联系客服反馈,我们会尽快为您处理(人工客服工作时间:9:00-18:30)。
765.609 kcal/mol
70276 kcal
=
5250
查表得比热容 294174
△T=
43.81754045
t=408.5-43.6=
二段催化剂层物料热量衡算 设二段催化剂床层出口温度为
则t=
388.6 ℃
取平衡温 距
429.2 查表Kp=
8.98
a
b
7.98 299.58956
2.3968773 30.18%
320
30.17
29.17 872.39128 3884.9714
340
23.33
22.33 687.49445 2847.9198
360
18.37
17.37 553.41722 2095.9058
380
14.68
13.68 453.67025 1536.4438
400
11.91
10.91 378.79244 1116.4682
二段出口CO含量 二段入口蒸汽比
催化剂型号 催化剂用量 一段催化剂用量 催化剂床层体积空速为 一段理论用量 取备用系数1.3 实际用量V1 二段催化剂用量 催化剂床层体积空速为 二段催化剂理论用量 备用系数1.1 实际用量V2 中变催化剂总量 一段催化剂占总量 二段催化剂占总量
催化剂床层直径确定 设催化剂床层直径为 催化剂床层阻力降△p dp= E= 一段催化剂层阻力 一段气体平均分子量 一段气体操作状态重度= 气体重量流量G G= 一段催化剂层高度L1 L1= △p1= 二段催化剂层阻力 二段气体平均分子质量
4.98
716.0
443.0
0.511
3.52
757.1
484.1
操作线计算
由一段催化剂变换率及热平衡及热平衡计算结果知
一段入口气体温度
300
一段出口气体温度
473
一段入口CO变换率
0
一段出口CO变换率
60.073%
中变炉二段催化剂层物料及热量衡算
冷凝水喷淋量=
124.11 m3
=
入二段催化剂层气体组成来自47.6302.232 90.251 29.780
44
28
2
28
10.708
0.319
0.922
4.260
干低变气组成 % m3 kmol
27.75 1066.910
47.630
1.30
52.57
49.990 2021.630
2.232 90.251
17.35 667.080 29.780
热量恒算 CO反应放热Q1
95.86%
712.769
CO2
CO
H2
N2
768.697 348.203 1723.417 667.08
21.67
9.82
48.59
18.81
34.317 15.545 76.938 29.780
CO2
CO
H2
N2
768.697 348.203 1723.417 667.08
18.04
8.17
40.46
0.834
出口气体温度校验
Kp=
8.982522548
15.22 667.08 29.780
28 4.260
热量衡算
CO在365至388.6时平均温度
376.8 时△H=
Q1=
181941.5561
气体温升吸热Q2
湿变换气在371.5的平均温度下平均比热容为
Q2=
6912.234562
热损失Q3=
18460
491的Kp
入炉蒸汽量
组分 m3 % Kmol
473℃时kp
平衡变换率=
剩余蒸汽量= 出一段催化剂层干气 组分 m3 % Kmol
出一段催化剂层湿气 组分 m3 % Kmol
△H= Q1=
Cp= Q3= △T=
入炉湿气组成为
5.337 23.294 1212.19
39.614 54.12
CO2
CO
H2
350
20.66
19.66 1042.3271 11802.288
△Hr=
400
11.91
10.91 615.43782 6734.2096
450
7.46
6.46 398.33413 4156.7296
500
4.98
3.98 277.34151 2720.2913
550
3.52
2.52 206.11198 1874.6462
最适宜温度曲线计算 △Hr取平均温度(300+473)/2=386.5℃=
-9232.833344
659.5
Xp
X
Tm(K)
Tm(℃)
0.872
39.76
540.3
267.3
0.803
20.66
585.6
312.6
0.728
11.91
630.0
357.0
0.652
7.46
673.4
400.4
0.579
CO反应量 △CO=
105.1197023 M3
4.6928439
CO剩余量
10.85215615 kmol
二段出口湿气变换气
组分
CO2
CO
H2
N2
%
19.93
5.54
41.71
m3
873.817 243.083 1828.537
kmol
39.010 10.852 81.631
44
28
2
8.770
1.553
249.0
0.745
39.76
540.3
267.3
0.685
30.17
558.5
285.5
0.621
23.33
576.6
303.6
0.553
18.37
594.5
321.5
0.482
14.68
612.3
339.3
0.409
11.91
629.9
356.9
0.336
9.79
647.4
374.4
二段催化剂床层操作线计算
CO2 CO2 B109
388.6 12537 m3/h
CO 8 9.82 % 0.396 14533 m3/h 17961 m3/h
H2 28.5
N2
40
21.8
CO 21.67
H2
N2
9.82
48.59
18.81
9.79% 0.236
2778 4.512894168 m3
5.866762419 m3
干变换气组成 出口干气体积变化情况 出口干气总量 CO: co2: H2 N2 CH4
a 9.82
100+axp=
100+9.82*0.3225= 100.02963
3547.177/100*103.27= 3548.2282 158.40304
9.79%
21.69%
48.61%
18.79%
1.12%
反应热△H CO反应放热Q1 气体吸热Q2 平均比热容= Q2= Q3= △T= T= kp= 254.6-232.2
设气体出催化剂层温度为 232.2 平均温度=
40100
=
345671.36
34.49607111 6751.466227
12510 49.34651956 234.3465196 80.09822321
2.232 KMOL
=
49.990
47.630 KMOL
=
1066.910
90.251 KMOL
=
2021.630
29.780 KMOL
=
667.080
1.78 KMOL
=
39.780
3845.390
CO2
CO
H2
N2
24.34
1.14
46.11
15.22
1066.910 49.990 2021.630 667.080
280
48.842 47.842 1147.6989 3688.9634
t
140
160
180 200.000
xp
0.981
0.968
0.948
0.921
设低变催化剂 E1= △H= E2=
10351.000 40102.000 83369.180
Xp
X
Tm(K)
Tm(℃)
0.981 1014.2399
喷水后气体温度计算 喷水前气体温度为 设喷水后气体温度为 气体从480.5降到365 Q1= 冷凝水吸热Q2 设进水温度为61 365℃,0.18Mpa 则Q2= 热损失Q3=
408.5 ℃
365 ℃
平均温度
386.75 ℃
6833.41717 △T
水的焓值i=
60.98 kcal/mol
蒸汽的焓i=
△t=
23.65104289 388.65104
38770 KJ/MOL 35.32
二段催化剂出口变换气温度 t=
388.6510429
二段催化剂平衡曲线计算
入二段汽气比
0.2359293
T
Kp
W
U
V
280
53.5
52.5 1503.0409 7422.1664
300
39.76
38.76 1131.6253 5338.9663