二次精炼
炉外精炼

2) VD生产模拟
工部全景
生产模拟
19
3) VD生产工艺
基本原理
真空处理
吹Ar制度
20
真空脱气
原 理: 基于H、N在钢液 中溶解服从平方根定 律,当VD抽真空时, 真空室内压力降低, 使[H]、[N]随之降低, 达到去除目的。散而一起去除。
真空度→保持达到VD
处理要求→反抽气破
坏真空。
23
吹Ar制度
钢包到工位即吹Ar, 不吹破渣面,防止透气砖 堵塞; 加合金采用大流量吹 Ar,吹开渣面,使合金直 接进入钢液,提高收得率; 高真空处理时小流量 吹Ar,防喷溅; 喂丝时, 小流量吹 Ar , 防止增[N]和二次氧化。
24
10
1) LF概述
LF是日本大同制钢公司于1971年开发, 特点是将电弧炉炼钢还原期任务移到专用 的钢包内进行。在利用电弧加热钢水的同 时,向钢液内吹入惰性气体(Ar),以实 现在非氧化性气氛下精炼,从而达到钢液 脱硫、脱氧、去气、去夹杂物的效果。经 LF 处 理 的 钢 水 , 钢 中 [O]10-30ppm 、 [N]20ppm、[H]1.5-2.5ppm。
(MnO)、(Fe2O3)及[O]在钢 渣界面进行反应,使[O]降低,脱氧 产物直接溶于渣中,不污染钢液;
13
泡,将造成凝固组织不致密;
②脱
目
硫
的: S在钢中产生”热 脆”并降低钢的抗腐 蚀性、延展性和韧性; 原 理: (FeS)+(CaO)= (FeO)+(CaS) 条 件: 高碱度、还原气氛、 高温、大渣量
4) RH的主要功能
功 能:
① 脱 H: 对 完 全 脱 氧 钢 液 脱 氢 效 率 ≮60%,对未完全脱氧钢液,由于CO 反 应 剧 烈 , > 70%. 脱 气 时 间 15~20min,[H]<2ppm. ② 脱 N:N 易 形 成 N- 化 物 , 脱 氮 效 率 0~10%; ③脱O:∑[O]0.002~0.005% ④脱碳:对初始[C]有要求,处理15min, 可使[C]<0.002%; ⑤脱S:效率50~75%; ⑥减少非金属夹杂:改善钢水纯净度; ⑦成分微调:合金元素控制精度为 ±0.003~0.010%
一种创新型的高效RH二次精炼流程

2.7 RH采用卷扬提升装置与传统的液压顶升装置相比 设备结构相对简单。设备故障率相对较低,运行安全稳定 可靠,维护成本低。今年RH月平均故障总时间在2.5小时 以内。 2.8 连铸浇完的空罐由离线布置的过渡线运回出钢跨, 座罐在出钢跨进行,整个钢包运行线路按逆时针方向形成 一个循环,因行车使用环节少,生产调度组织也相对容易。
3.1 RH精炼处理与转炉 连铸节奏匹配技术 精炼处理与转炉-连铸节奏匹配技术 精炼处理与转炉
武钢股份炼钢总厂四分厂设计转炉和铸机生产周期在通常情况 下均为38~40分钟,这样就要求RH精炼即使在脱碳工艺条件下,其 周期也要控制在38~40分钟,因此在配套设计RH精炼处理装备时, 一方面在工艺布局设计上将过程耗时缩短了近10分钟,该10分钟的 节约使生产组织发生了质的变化,使一炉对一机的生产组织模式变 成了现实。并增强了精炼钢水条件及设备的稳定性,另一方面在工 艺装备设计上也需充分考虑快速脱碳、快速的合金化混匀时间,如 果装备工艺不能实现高效化,将极大的限制流程布局优势的发挥, 并阻碍整个流程的顺畅运行。该厂通过装备的合理设计及优化生产 组织,大部分主要钢种在RH处理时间均控制在15~40分钟,在此基 础上,在生产组织原则上采用转炉与其对应在线的RH精炼装置一对 一衔接,因此该厂可以实现100%经过RH的多炉连浇,从而最大程 度的发挥RH在线布局的优势;在计划检修时也形成转炉-RH配套组 合检修模式,上述措施有效保证了RH在线布置优势的发挥,使RH 精炼与转炉-连铸节奏匹配程度高,全连铸生产组织顺畅。
一个现代化炼钢厂仅仅实现全连铸,实现多炉连浇并 不一定说明其高水平,因为可以采取很多补救措施来实现, 比如用钢包炉来调节温度、节奏,采取铸机升降速来调节 温度和节奏,但凡高水平、高质量铸坯要求连铸机按典型 拉速浇钢,浇注曲线在规定的拉速上近似一条直线,而炼 钢总厂四分厂投产很短时间典拉率达到90%以上,经常一 个班典拉合格率达100%,与工艺的配置直接相关。较高 的典型拉速合格率保证了连铸操作的稳定和铸坯稳定的高 质量,自2008年11月28日该厂投产以来,两台铸机运行至 今共计一年零八个月不漏钢,总计浇铸炉数24500多炉, 其中1#机11380炉、2#机13190炉不漏钢,创造新铸机投 产后不漏钢世界先进水平;同时铸坯实物质量合格率保持 在99.98%以上高水平,铸坯中心偏析自投产以来未出现A 级偏析,今年以来无B级及以上偏析。
二次精炼新工艺——RH-PB法

随后 吹 氧 加热
精调 成 、
硫
、
氮含 量 分别 为 (
5
、
《1 0 及 《4 0 P m 的 高纯度钢
新 日 铁采 用 此 法 生 产高纯度钢的
脱 磷效 果 在 颇 大 程 度 上 取 决 于 熔
经验 表 明
( 1 ) 钢 水 主 要 通 过 同 熔剂颗粒直接 反 应 进 行脱 硫 和 脱 磷
在 非 脱 氧条件 下 每单 位熔剂消 耗量 的 脱磷 量乙 P
,
二
0 ~ 2
P B 法 既 有 良好 的 脱 硫 效 果
又 不 损害 传 统 R H 真 空 脱 气 的 能 力
。
。
因此
,
R H 一 P B 法是生产高纯度 优 质钢 的 一种 很 有 效 的 新 工 艺
(耿
凡)
设备 的 主 要 规 格 列 于 下 表
目
。
.
.
项
钢 包容 量 真空度
规
2 0
格
50t
。
1 3
3~
13
。
3
k P
a
连通 管 直 径
喷 嘴数 吹氧流 量
: 喷粉
中7 3 0
2 1 5
mm ( 套管 式 啧 嘴 ) m /h
3 ,
支
00
喷嘴
熔 剂 喷射 速 度
150
kg
/m i n 喷 嘴
一
载气
:
—喷 类 吹 量 —气 压 流 —
,
脱硫
、
剂与钢水 的 混 合特征 耗量
4 k g /t ( 3 ) ( 4 )
,
,
( 2 ) 在 最佳 化 的 熔 剂 喷 射条件下
二次精炼设备功能的改进

为
通
压
氧化。 这套系 钢水 统的 净化功能成功 地I
使清洁钢的生产工艺( L 和 RH) 如 F _ 结合 ;
避
成 体并 更 理 一 ,且 合 。
一+ . + 。 + . + . + . + . + . + . + . + + . + + . + . + . + . +
量大 大减 少 。
() 2 鱼雷罐车和铁水罐处理工艺利
( 自 it ,uag o 20 .2 ) 摘 nej gn . r 056 5 ri cn .
【 邓守强 , 1 】 高炉炼铁技 术 。 北京 , 冶金 工业 } 版社 , h
1 9 P2 5, 2 9 3, 6 P3 1
简
的
的盖 子 。从 而将 整 个钢 包 变成 一 个 真 空
系统 。通 过 在 真 空条 件 下 的强 烈搅 拌 精
炼 , 进 了夹 杂物 上 浮 , 促 防止 了钢 水 二 次
维普资讯
酒钢 科技
2 l
( )通 过烟 煤混 喷技术 将烟煤 比例 由 4 目前 的 2%逐 渐 提高 到 5%左 右 , 0 0 既提 高 制粉 能力 又 改善 炉 内煤 粉 的燃 烧条 件 , 从 而达 到提 高煤 比的要求 。
参考 文献
的研 究 , 结果 如下 : 其
( ) 日铁 采 用三 种 铁 水 预处 理 工 1新
() 据 基 本 试 验 的 结 果 , 溶 解 5根 可 P0 2 5的 2 a .i2固相 对 脱 磷 反 应 的 C OSO
影 响非常 大 。
艺( 鱼雷罐车、 铁水罐或 L D转炉 )使渣 ,
i
( 自it .uagcr 20..5 摘 nej gn . n 056 ); ri o 2
30t电弧炉的二次精炼工艺

30
平均出钢量/ t
36
残留钢水量/ t
1~2
变压器容量/ kVA
12 500
电极直径/ mm
450
出钢最大倾角/ °
12
中心距/ mm
2 005
出钢直径/ mm
130
一次电压/ V
35 000
二次电压/ V
340~120
一次电流/ A
21 000
采用 精 炼 工 艺 后 , 生 产 能 力 由 原 设 计 7. 5 万 t/ a ,提高到 13 万 t/ a 。
李淑清 ,女 ,32 岁 ,讲师 。1990 年毕业于鞍山钢铁学院钢
冶专业 。从事特殊钢工艺技术研究 。
收稿日期 :1999207202
© 1994-2007 China Academic Journal Electronic Publishing House. All rights reserved.
工艺 组别
Ⅰ 工艺 A
Ⅱ
Ⅰ 工艺 B
Ⅱ
C 0. 18~
0. 19 0. 20~
0. 21 0. 17~
0. 19 0. 19~
0. 21
Mn 0. 95~
1. 05 0. 95~
1. 05 0. 85~
0. 95 0. 85~
0. 95
Cr 1. 10~
1. 20 1. 10~
1. 20 1. 00~
二炼钢分厂 1997 年开始精炼工艺试运行 ,轴 承钢夹杂物一次合格率由 93 %提高到 97 % , [ O ] 由 45 ×10 - 6降至 13. 6 ×10 - 6 ,可按 YB9268 标准和 YJ Z284 协议生产高纯度轴承钢 ;齿轮钢淬透性稳 定 ,晶粒度级别 7~8 级 ;铁路车轴钢采用 EBT + LF + VD 工艺 ,钢中 [ O ] < 25 ×10 - 6 ,各类夹杂物 ≤2. 0 级 ,占 95 % ,晶粒度 > 6. 5 级 ,复验合格率 100 %。
我国钢水二次精炼技术的发展
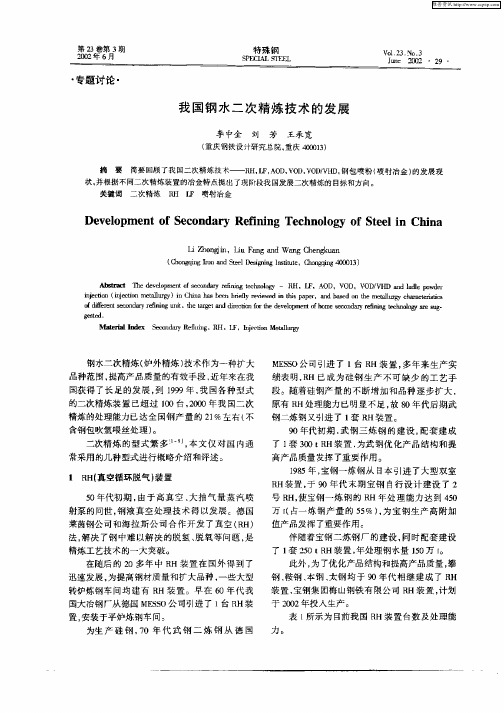
此外 , 为了优化产品结构和提高产品质量 , 攀 钢、 鞍钢 、 本钢 、 钢 均 于 9 代 相 继 建 成 了 R 太 o年 H
装 置 , 钢集 团梅 山钢铁 有 限公 司 R 宝 H装置 , 划 计
于 20 年 投入 生产 。 02
( 重庆钢铁设计研究总 院, 重庆 40 1 ) 00 3 摘 要 简要 回顾 了我 国二次精炼技术—— l L . O V D, O /H 钢包 喷粉 ( i F A D, O V DV D, H, 喷射冶 金 ) 的发展现 二次精炼 P L 喷射冶金 , H F
状, 并根据不 同二次 精炼 装置的冶金特点提 出了现阶段我 国发展二次精炼的 目标和方 向。
o i e e t e o d r e n n nt h a g t n l c  ̄ f r h e eo ̄ e o le so n a rf i e  ̄ lg r u - f f rn c u ayrf ig u i,tetr e a d dr t a o te d v l n m fh X e o d H i t c d s i ei t Ol e nx gt moo ya es g g e  ̄td.
Mae i Id x S tr l n e d I R f g P t F I e tnM t l g a ay e t , , ,L , n c o e l r i m ̄ t j i au y
钢 水二次 精炼 ( 外精炼 ) 术作 为一种 扩 大 炉 技 品种 范围 , 高产 品质 量的有 效 手段 , 提 近年来 在我 国获得 了长足 的发 展 , 19 到 99年 , 国各 种 型 式 我 的二次精炼 装 置 已超 过 10台 ,00年 我 国二 次 0 20 精 炼的处理 能力 已达 全 国钢产 量 的 2 %左 右 ( 1 不 含 钢包吹氩 喂丝 处理 ) 。 二次精 炼 的 型 式 繁 多 , 文仅 对 国 内通 本
洁净钢生产的二次精炼技术

洁净钢生产的二次精炼技术洁净钢, 二次精炼为满足最终用户需要,洁净钢生产中二次精练设施越来越发挥出举足轻重的作用。
真空脱气首先用于生产不锈钢和特种钢,特别是不能在常压环境中进行有效生产的高铬钢。
真空吹氧脱碳(VOD)工艺不仅能降低反应产物一氧化碳的分压,而且可防止过量铬被氧化,但该工艺缩短了钢包炉的使用寿命并延长了钢水的处理时间,从而导致氧氩混吹脱碳(AOD)工艺技术的开发。
在大批量的不锈钢生产中,氧氩混吹脱碳工艺越来越受到用户的欢迎。
钢铁生产者逐渐意识到炉渣对最终产品质量所造成的影响。
炉渣的成分直接影响钢水以及钢材中夹杂物的成分,而夹杂物的成分反过来影响钢材的物理性能。
不幸的是,到目前为止,炉渣成分和夹杂物成分之间的因果关系并不能进行实时测量。
但值得庆幸的是,通过炉渣管理系统可进行高洁净钢的生产。
炉渣管理系统是一种用于说明和控制钢包渣成分的工艺。
在采用该系统之前.必须了解炉渣的构成,其包括:炉渣携带量、脱氧产品、钢包炉的炉衬材料、造渣添加剂以及上炉钢的余渣。
以下介绍几个采用炉渣管理系统生产特种钢并获得理想结果的实例。
镇静钢以及轴承钢生产轴承钢零件的使用寿命和夹杂物(SiO2和Al2O3)的总量之间成反比关系。
携带了氧化亚铁(FeO)和氧化锰(MnO)的炉渣可导致钢水过氧化以及夹杂物中氧化物的水平过高,因此控制炉渣携带量是生产洁净轴承钢的前提。
而且,在控制炉渣携带量的同时必须考虑去除钢水中的脱氧产物,因此,炉渣必须具备一定的亲和力,以便吸附氧化铝。
满足上述要求的炉渣成分必须位于CaO饱和区域并接近CaO·Al2O3,共熔区。
一般情况下,炉渣成分中石灰与氧化铝的比例应在1.2—2.0之间。
对轴承钢来说,1.7应该是最优的。
为描述氧化钙饱和区内钢包渣的特性,定义了氧化钙饱和指数。
该指数主要用于以下几个目的:——识别炉渣的相对饱和度,从而判断石灰的添加量;——显示炉渣的脱硫潜力;——预测并防止钢包炉炉衬磨损。
1.炉外精炼概述
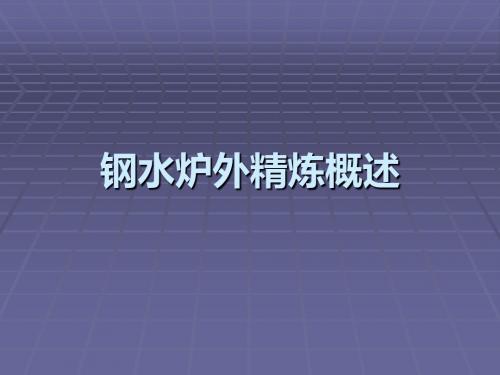
2 创造良好的冶炼反应的热力学和 动力学条件。
通过各种加热精炼手段补偿精炼过程中的温度 损失,使得需要在高温下的脱硫等反应得以顺利进 行。 炼钢过程中的各种冶金反应,多数是在高温下 进行的多相反应,通常化学反应本身进行较快,而 反应物传递到反应界面和生成物脱离反应界面较慢, 成为限制冶金反应速率的因素。通过搅拌、喷吹等 手段提高浓度梯度,增大反应界面,使各种冶金反 应得以顺利进行。
五 炉外精炼的手段
目前炉外精炼的手段有渣洗、真空、搅拌、喷吹和加热 五种。采用一种或几种不同手段的不同组合,就形成了某 一种精炼方法。 1 渣洗:获得洁净钢液并能适当进行脱氧、脱硫和去除 夹杂物的最简便的精炼手段。它是将事先配好的合成渣倒 入钢包内,借出钢时钢流的冲击作用,使钢液与合成渣混 合,从而完成脱氧、脱硫和去除夹杂等精炼任务。 2 真空:将钢液置于真空室内,由于真空作用使反应向 生成气相方向移动,达到脱气、脱氧、脱碳等目的。 3 搅拌:通过搅拌扩大反应界面,加速反应物质的传递 过程,提高反应速度。分为吹气搅拌和电磁搅拌。 4 加热:调节钢液温度的一项重要手段,使炼钢与连铸 更好地衔接。分为电弧加热法和化学加热法。 5 喷吹:用气体作载体将反应剂加入金属液内的一种手 段。喷吹的冶金功能取决于精炼剂的各类,它能完成不同 程度的脱硫、脱氧、合金化和控制夹杂物形态等精炼任务。
钢水炉外精炼概述
一 炉外精炼的产生原因
1 普通炼钢炉(转炉、电炉)冶炼出来 的钢液难以满足对钢的质量(如钢的纯净度 等)越来越高的要求。 2 为了提高生产率,缩短冶炼时间,把 炼钢的一部分任务移到炉外完成。 3 连铸技术的发展,对钢液的成分、温 度和气体的含量等也提出了严格的要求。
二 炉外精炼的概念
3 炉外精炼在炼钢生产中的重要地 位和作用
炉外二次精炼在现代炼钢生产中的作用和地位
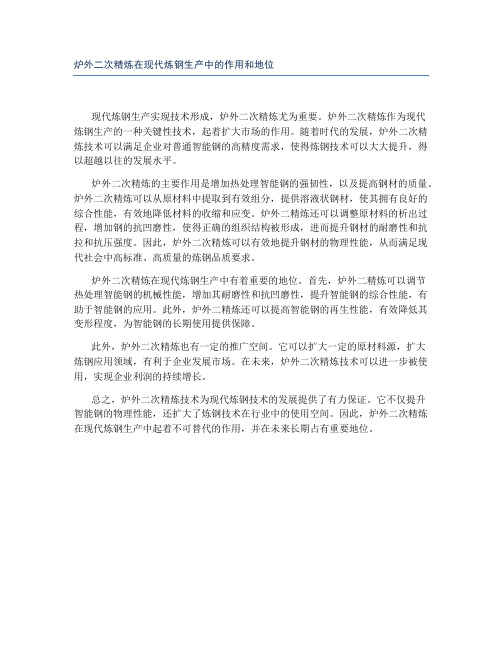
炉外二次精炼在现代炼钢生产中的作用和地位
现代炼钢生产实现技术形成,炉外二次精炼尤为重要。
炉外二次精炼作为现代
炼钢生产的一种关键性技术,起着扩大市场的作用。
随着时代的发展,炉外二次精炼技术可以满足企业对普通智能钢的高精度需求,使得炼钢技术可以大大提升,得以超越以往的发展水平。
炉外二次精炼的主要作用是增加热处理智能钢的强韧性,以及提高钢材的质量。
炉外二次精炼可以从原材料中提取到有效组分,提供溶液状钢材,使其拥有良好的综合性能,有效地降低材料的收缩和应变。
炉外二精炼还可以调整原材料的析出过程,增加钢的抗凹磨性,使得正确的组织结构被形成,进而提升钢材的耐磨性和抗拉和抗压强度。
因此,炉外二次精炼可以有效地提升钢材的物理性能,从而满足现代社会中高标准、高质量的炼钢品质要求。
炉外二次精炼在现代炼钢生产中有着重要的地位。
首先,炉外二精炼可以调节
热处理智能钢的机械性能,增加其耐磨性和抗凹磨性,提升智能钢的综合性能,有助于智能钢的应用。
此外,炉外二精炼还可以提高智能钢的再生性能,有效降低其变形程度,为智能钢的长期使用提供保障。
此外,炉外二次精炼也有一定的推广空间。
它可以扩大一定的原材料源,扩大
炼钢应用领域,有利于企业发展市场。
在未来,炉外二次精炼技术可以进一步被使用,实现企业利润的持续增长。
总之,炉外二次精炼技术为现代炼钢技术的发展提供了有力保证。
它不仅提升
智能钢的物理性能,还扩大了炼钢技术在行业中的使用空间。
因此,炉外二次精炼在现代炼钢生产中起着不可替代的作用,并在未来长期占有重要地位。
合理选择二次精炼技术,推进高效率低成本“洁净钢平台”建设

艺, 可为各企业提供参考经验 。深化对不 同类 型炉外 精炼 功能的理解并合理选择 , 有利于使 不同类型产
品的基本精炼 工艺 规范化 , 有利于加快我 国高效率 、 低成本“ 洁净钢平台” 的建设 步伐 。 关键 词 : 选择 ; 炉外 精炼 ; 推进 ;洁净钢平 台” “ 建设
中 图分 类 号 : F 6 文 献 标 识 码 :A 文 章 编 号 :10 —( 3 2 1 ) 10 0 —6 T 79 02 14 (0 0 0—0 10 )
S lc i e o da y r fni g t c n l g o e l n s i g f r r ee tng s c n r e i n e h o o y pr p ry a d pu h n o wa d
c n t u to fhi h e fc e nd l w o t“ la t e l to m ” o s r c i n o g f iinta o c s ce n s e lp a f r
YI Ru— u N i y
( e ta I n & S e l ee rhIsi t,B in 0 hn ) C nrl r o te R sac n t ue e g 1 0 8 ,C ia t j i 0 1
Ab t a t s r c :Th r n a d s e l n u t y a o e a d a r a s n w a i g a v r e i u e io n t e d s r t h m n b o d i o f cn e y s ro s i
c aln eo ewolwief a c l r i td y h l g ft r e h d d n n i i s o a .On f h e onsfr e du t n i ac s eo ek yp it a jsme t t o r
RH、LF和VD炉外精炼技术

通电时,采用小流量吹 Ar,均匀温度又不引起大的 液面波动.
28
③造渣制度
目 的:
脱S、脱O、去夹杂; 提高炉衬寿命; 防止钢水二次氧化,提高合 金收得率。
基本制度:
渣料加入量8-10Kg/t; 分 批 加 入 , 出 钢 过 程 加 4050%,其余待化渣后分2-3次加入; 炉渣过稠加CaF2,炉渣过稀加 CaO.
4
2.炉外精炼的发展
• 20世纪30年代 • 20世纪40年代 • 20世纪50年代 • 20世纪60,70年代 • 20世纪80年代
多的R(理包HD有(种精-HO循C形炼)BA环使渣高式)大泵真炉,S在钢理合在V,真发钢用C进,,问抽空;金低水O提真A空真展水高行D微S世速法真进升空处-空,质碱O调脱理真,蒸 用吹空 行、B广脱D量及度S)(空H氩度 脱泛汽 于温气;以合V,R、L处脱应度下 气基A喷 钢HF成提D理,处氧用R钢对 处础射 水H上、,
7
4.炉外精炼方法的共同特点
• ①理想的精炼气氛条件,通常应用真空、 惰性气氛或还原气氛;
• ②搅动钢水,采用电磁力、惰性气体或机 械搅拌的方法;
• ③为补偿精炼过程的钢水温度损失,采用 加热设施有电弧加热、等离子加热或增加 钢水中的化学热等。
8
二.RH、LF及VD法简介
RH 法 LF 法 VD 法
34
④事故搅拌装置
作 用:
在透气砖不能工作情况 下,惰性气体通过顶枪吹入 钢包,进行事故搅拌;
结 构:
顶枪安装在支撑框架上, 支撑框架安装在炉盖侧面, 顶枪通过电动机和卷筒实现 上下;
参 数:
顶枪压力:0.6-1.6MPa; 流量(max):600NL/min
杭钢二次精炼的选择及实践
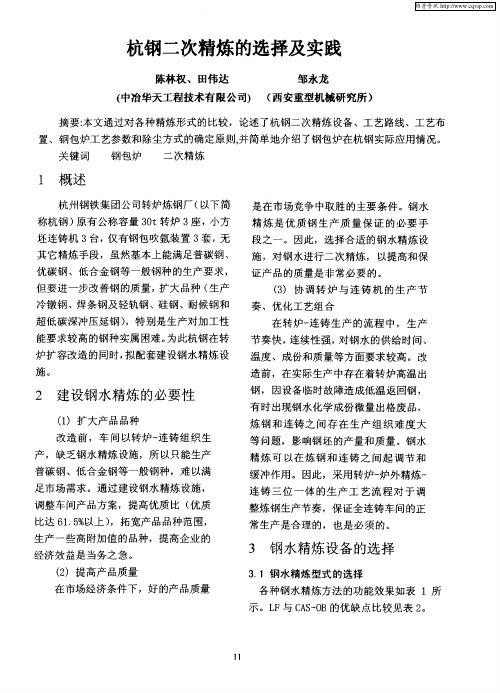
炉扩容改造的同时, 拟配套建设钢水精炼设
施。
2 建设钢 水精炼 的必要 性
()扩 大产 品品种 1 改 造 前 , 车 间 以转 炉 一 连铸 组 织 生 产 ,缺 乏 钢水 精炼 设施 ,所 以只 能生产 普 碳钢 、低 合 金钢 等一 般钢 种 ,难 以满
有 时 出现 钢水 化 学成 份微 量 出格 废 品 , 炼 钢 和 连铸 之 间 存 在 生 产 组 织 难 度 大
4 l ̄/ i, 一 O m n 生产节奏快 C 产生一定 A z 污染 1。 0 设备简单, 一次投资省 相对较高 电力负荷小, 其他 要求较大电力负荷
通过上述功能和优缺点的比较, 结合杭
钢 的产品大纲和质量要求, 以及全连铸钢厂
() 提 高产 品质 量 2 在 市 场经 济条 件下 ,好 的产 品质 量
各种钢水精炼方法的功能效果如表 l所
示 。L F与 C S 0 的优缺 点 比较见表 2 A一 1 3 。
维普资讯
表i
序 号
1 2
各种钢水精炼方法的功能效果表
_ + 一
_ + 一 _ + 一
_ 一 +
_ + 一
_ + 一
+ 一
6
7 8
改变夹杂物形态
成 份微 调 钢 水成 份均 匀化 +
+
+
+
+ _ + 一 + + + + + _ + 一 + +
9
1 O
1 1
钢水温度均匀化
段 之 一 。因此 ,选择 合适 的钢 水精 炼设 施 ,对 钢水 进行 二 次精炼 , 以提 高和 保
证产 品 的质 量是 非 常 必要 的 。
其 它 精炼 手段 ,虽然基 本 上 能满足 普碳 钢 、 优 碳 钢 、低合 金钢 等一 般钢 种 的生 产要 求 , 但 要进 一步 改 善钢 的质 量 ,扩大 品种 ( 产 生 冷镦 钢 、焊条 钢及 轻 轨钢 、硅钢 、耐候 钢和 超低 碳 深冲 压 延钢 ) ,特 别 是生 产对 加 工性 能要 求较 高 的钢 种实 属 困难 。 此杭 钢在 转 为
二次精炼技术的发展与配置

特殊钢Special Steel1999年,第20卷 第2期 Vol.20 No.2 1999二次精炼技术的发展与配置刘 浏 何 平摘 要 根据目前世界二次精炼技术的发展,分析各种流程中二次精炼的匹配模式及其适应的生产钢种,提出加快我国二次精炼技术发展的具体建议。
关键词 二次精炼 电炉 转炉 钢包Development and Allocation of Secondary Refining TechnologyLiu Liu and He Ping (Central Iron and Steel Research Institute, Beijing 100081)Abstract According to the present development of secondary refining technology in the world, the matching model of secondary refining process which is available to produce the adaptive steel grades in various process flow has been analyzed, and the recommendation for accelerated development of secondary refining technology is proposed in this paper.Material Index Secondary Refining, Electric Arc Furnace, Converter, Ladle 当前,二次精炼作为完整、独立的生产工序与炼钢、连铸有机地结合,成为现代钢铁生产的重要组成部分。
早在1986年日本转炉钢的二次精炼比已达到70.8%;特殊钢生产的二次精炼比高达94%;新建电炉短流程钢厂100%采用二次精炼。
- 1、下载文档前请自行甄别文档内容的完整性,平台不提供额外的编辑、内容补充、找答案等附加服务。
- 2、"仅部分预览"的文档,不可在线预览部分如存在完整性等问题,可反馈申请退款(可完整预览的文档不适用该条件!)。
- 3、如文档侵犯您的权益,请联系客服反馈,我们会尽快为您处理(人工客服工作时间:9:00-18:30)。
炉 外 精 炼
二次精炼(Secondary Refining) 二次炼钢(Secondary steelmaking) 二次冶金(Secondary Metallurgy) 钢包冶金(Ladle Metallurgy)
炉外精炼的优点
提高钢的质量,缩短冶炼时间, 优化工艺过程并降低生产成本
任
务
• 1)降低钢中氧、硫、氢、氮和非金属夹杂物含 量,改变夹杂物形态,以提高钢的纯净度,改善钢 的机械性能。 • 2)深脱碳,满足低碳或超低碳钢的要求。在特 定条件下,把碳脱到极低的水平。 • 3)微调合金成分,把合金成分控制在很窄的范 围内,并使其分布均匀,尽量降低合金的消耗,以 提高合金收得率。 • 4)调整钢液温度到浇铸所要求的温度范围内, 最大限度地减小包内钢液的温度梯度。
现 状
到目前为止,还没有任何一种炉外精炼方 法能完成上述所有任务,某一种精炼方法 只能完成其中一项或几项任务。
由于各厂条件和冶炼钢种不同,一般是根 据不同需要配备一两种炉外精炼设备。
炉外精炼的手段 1)渣洗:获得洁净钢液并能适当进行脱氧、脱 硫和去夹杂的最简便的精炼手段。将事先配好 (在专门炼渣炉中熔炼)的合成渣倒入钢包内, 借出钢时钢流的冲击作用,使钢液与合成渣充 分混合,从而完成脱氧、脱硫和去除夹杂等精 炼任务。电弧炉冶炼时的钢渣混出,称同炉渣 洗,也是利用了渣洗原理。 2)真空:将钢液置于真空室内,由于真空作用 使反应向生成气相方向移动,达到脱气、脱氧、 脱碳、除去有害挥发成分等目的。真空是炉外 精炼中广泛应用的一种手段。
3)挥发元素通过钢液表面的浓度边界层向气相扩散:
* v3 k3 (CB CB ( g ) )
挥发性较小的元素,如Fe、Ni、Co等元素挥发的限制性 环节为元素向界面的扩散;挥发性较大的元素,如Mn、 Sn等元素的挥发限制性环节为钢液表面这些元素的脱附; 100 pa 元素浓度低及真空度也比较低 ( ),元素挥发的限 制性环节为(3)。
元素在真空下的挥发速率遵从朗格谬尔公式:
' vB cpB
MB 2RT
式中:vB —挥发速率,量纲 kg m2 s 1 c —朗格谬尔系数 M B —挥发组分B的摩尔质量
' pB
—挥发组分的蒸气压
元素的挥发系数
对于铁基二元系,挥发元素的挥发系数:
1)高真空下元素挥发过程成为限制性环节时,挥发系数为:
1-合金添加料斗;2-真空排气管;3-钢液; 4-氩气管;5-渣;6-滑动水口 图5-3 DH真空提升脱气装置示意图
1)DH真空提升脱气装置由真空 室(钢壳内衬耐火材料)及提升 机构,加热装置(电极加热装置 或喷燃气,喷油加热),合金料 仓(真空下密封加料),抽气系 统等组成。
1-合金添加料斗;2-真空排气管;3-钢液; 4-氩气管;5-渣;6-滑动水口 图5-3 DH真空提升脱气装置示意图
——积分式
w 式中: w[X ]0 为钢液气体的初始质量分数; [X ]平 溶解气体的平衡值;
w 在真空条件下, [ X ]平 w[ X ] w[ X ]0 ,因此速率积分式 可简写为:
lg
w[ X ] 1 A X t w[ X ]0 2.3 V
5.9.1.3真空脱碳
真空脱碳和脱氧同时进行:[C]+[O]=CO在真空条件下, 降低了 PCO,使在大气压力下已经达到平衡的脱碳反 应再度进行,从而达到脱碳脱氧的目的。
炉外精炼的手段
3)搅拌:通过搅拌扩大反应界面,加 速反应物质的传递过程,提高反应速度。搅拌方 法:吹气搅拌和电磁搅拌。通常碳的目的。 4)加热:调节钢液温度的一项重要手 段,使炼钢与连铸更好地衔接。加热方法:电弧 加热法和化学加热法。
炉外精炼的手段 5)喷吹:用气体作载体将反应剂加入金 属液内的一种手段。喷吹的冶金功能取决于精炼 剂的种类,它能完成脱碳、脱硫、脱氧、合金化 和控制夹杂物形态等精炼任务。
一般炉外精炼方法都是渣洗、真空、搅拌、喷 吹和加热这五种精炼手段的不同组合,采用一 种或几种手段组成一种炉外精炼方法
炉外精炼的手段
5.9.1.2挥发元素去除的动力学环节
真空条件下,钢液中元素的挥发由下列环节组成:
* v 1)钢液中溶解元素原子向钢液-气相界面扩散:1 k1 (CB CB )
2)元素原子在钢液表面吸附时,经脱附而挥发:
* * 2 * v2 k2CB ( B pB / ) M Fe /(2RTM B ) cB
5.9.1.4真空脱氧
真空条件下,脱氧剂为碳:当脱氧元素浓度 w[ B] 0.1%
' ' pCO 10 kPa 时, 碳的脱氧能力高于硅的脱氧能力;而 pCO 0.1kPa
、
时,碳的脱氧能力甚至高于铝的脱氧能力。 真空脱氧过程速率的限制性环节是钢液中[C]和[O]的扩散, w[C]较高时,[O]的扩散为限制性环节,由此可计算脱氧速率:
5.9 二次精炼主要内容
二次精炼概述 5.9.1钢液的真空处理 5.9.2吹氩处理 5.9.3合成渣处理 5.9.4喷吹粉料处理
炉外精炼产生的原因
1)对钢的质量要求的提高→用普通炼钢炉(转炉、 电炉和平炉)冶炼出来的钢液已经难以满足其质 量的要求 。
2)提高生产率,缩短冶炼时间→希望能把炼钢 的一部分任务移到炉外去完成。 3)连铸技术的发展→对钢液的成分、温度和气 体的含量等也提出了严格的要求 。
Fe 式中:B , 分别为熔体中B和Fe的传质系数, s ,数量级为 m 1
10 4 ~ 10 5 m s 1
元素活度相互作用系数对挥发元素挥发的影响:提高挥 发元素活度系数的其它元素存在,就能促进该元素的挥 发;反之,降低挥发元素活度系数的元素存在,则降低 该元素的挥发。
2)DH法脱气工作原理 根据压力平衡原理,借助于真空室与钢包之间的相对运动, 将钢液经吸嘴分批吸入真空室内进行脱气处理的。处理时将真 空室下部的吸嘴插入钢液内,真空室抽成真空后其内外形成压 力差,钢液沿吸嘴上升到真空室内的压差高度,如果室内压力 为13.3~66Pa,则提升钢液约1.48m。由于真空作用室内的钢液 沸腾形成液滴,大大增加气液相界面积,钢中的气体由于真空 作用而被脱除。当钢包下降或真空室提升时脱气后的钢液重新 返回到钢包内。当钢包提升或真空室下降时又有一批钢液进入 真空室进行脱气。这样钢液一批一批地进入真空室直至处理结 束为止。
d [O] A O ( w[O] w[O]* ) dt V
lg w[O] 1 A O t w[O]0 2.3 V
——微分式
——积分式
例1:真空提升脱气法(DH法)
真空提升脱气法是1956年德国多特蒙特(Dortmund) 和豪特尔(Horder)冶金联合公司首先发明使用的,简 称DH法。DH法的设备如下图所示。
2)RH真空处理工艺的特点 RH真空处理工艺操作简便、处理量大、生产效 率高,在原来脱氢的基础上又开发了脱碳、脱氧、吹氧 升温、喷粉脱硫和成分控制等功能,使改进后的RH法能 进行多种冶金操作,使其发展成为多功能的真空精炼方 法。 在现代化钢铁生产工艺流程中,炉外精炼已成为不可缺 少的重要环节,高炉—铁水炉外预处理—转炉顶底复合 吹炼—RH真空精炼或CAS-OB精炼—连铸连轧或连铸— 铸坯热送—直接轧制,是现代转炉炼钢最佳工艺流程。
例2:真空循环脱气法(RH法)
1)RH法的产生及发展概况
RH法是德国鲁尔钢铁公司(Ruhrstahl A· G)和海拉 斯公司(Heraeus AG)两家公司1957年共同发明的,故简称 RH法。第一台RH设备1959年在德国Thyssn(蒂森)公司的 Hattingen厂建成。RH法近十几年来在我国发展也很快,我国 的一部分钢厂也选用了RH装置,大冶钢厂1968年投产第一台, 宝钢分别于1985年和1999年投产了两台RH装置,武钢分别于 1979年至1990年投产了四台RH装置,最大容量是宝钢1985年 12月投产的一台300吨RH装置。
炉外精炼
将在转炉或电炉内初炼的钢液倒入钢包或专用容 器内进行脱氧、脱硫、脱碳、去气、去除非金属 夹杂物和调整钢液成分及温度以达到进一步冶炼 目的的炼钢工艺 一步 炼钢 两步 炼钢
炉料在氧化性气氛的炉内进行熔化、 初炼 脱磷、脱碳、去除杂质和主合金化, 获得初炼钢液 将初炼的钢液在真空、惰性气体或还 精炼 原性气氛的容器内进行脱气、脱氧、 脱硫、去除夹杂物和成分微调等
真空脱气
氮、氢在钢液中的溶解遵从西华特(平方根)定律→ 降低体系的压力,使气体的分压降低→减小钢液中溶 解的气体量。 真空中钢液脱气过程的三个环节: 1)钢液中溶解气体原子向钢液-气相界面扩散;
2)这些气体原子在相界面上吸附,结合成气体分 子,再从界面脱附;
3)脱附的气体分子在真空作用下向气相中扩散。
* M Fe B pB * M B Fe pFe
式中:α为挥发系数 MFeMB分别为合金元素和Fe的摩尔质量 γB,γFe分别为合金元素和Fe的活度系数
* p* pB ,Fe
分别为纯合金组分及Fe的蒸气压,Pa
2)挥发元素受熔体中扩散限制时,挥发系数为:
ln(1 w[ B] / 100 ) ln(1 w[ Fe] / 100 )
5.9.1钢液的真空处理 作用:达到去除溶解的挥发性组分、脱气、 脱碳(脱氧)、脱硫和去除夹杂物的目的
5.9.1.1挥发性杂质的去除 钢液中的有色金属,如Pb、Cu、As、Sn、Bi等 在钢液进行真空熔炼或处理时,可通过挥发而 除去一部分。
挥发量取决于该元素的蒸气压和在铁液中的活度
元素的挥发系数
3)DH法的主要优缺点
优点:进入真空室内的钢液由于气相压力的降低产 生激烈的沸腾,脱气表面积增大,脱气效果较好,适用 于大量钢液的脱气处理,可以用比较小的真空室处理大 吨位的钢液;可以对真空室进行烧烤加热,因此处理过 程中钢液温降小。由于激烈地沸腾还具有较大的脱碳能 力,可以生产含碳0.002%的低碳钢。处理过程中可以加 入合金,在真空室内合金元素的收得率高。由于这一系 列的优点,使DH法得到了发展。 缺点:设备比较复杂,投资和操作费用都比较高。