ASME_锅炉压力容器规范案例 2005
2005年特种设备严重以上事故及其分析(精)

2005年特种设备严重以上事故及其分析2005年共发生特种设备严重以上事故274起,其中特大事故1起,重大事故18起,严重事故255起,共死亡301人,受伤293人,直接经济损失6964.69万元。
在274起事故中,发生锅炉、气瓶、压力容器、压力管道(下称承压类设备)事故133起,死亡94人,受伤211人,直接经济损失4065.64万元(其中“土锅炉”事故18起,死亡7人,受伤34人,直接经济损失144.41万元);发生电梯、起重机械、厂内机动车辆(机电类设备)事故141起,死亡207人,受伤82人,直接经济损失2899.05万元(其中房屋和市政起重机械事故58起,死亡114人,受伤16人,直接经济损失209.60万元)。
特种设备事故万台起数0.87;特种设备事故万台死亡人数0.97。
与2004年相比,特种设备事故总起数减少7%,其中:特大事故持平,重大事故增加13%,严重事故减少8%。
死亡人数增加1%,受伤人数减少31%,直接经济损失增加53%。
按设备类别同比,锅炉、土锅炉、气瓶、压力管道、起重机械、房屋起重机械、场(厂)内机动车辆事故起数明显减少;客运索道事故得到了遏制;压力容器、电梯、大型游乐设施事故起数有所增加,特别是电梯事故发生频率较高,同比增加91%。
上述事故中,已处理结案或由其他行政部门处理结案179起,结案率为65.3%。
其中:特大事故1起,结案率为100%;重大事故8起,结案率为44.4;严重事故170起,结案率为66.7%。
〔各省(区、市)事故发生情况〕一、事故分布情况─—特大事故1起,发生于云南;─—重大事故14起,其中:河南3起,广东、安徽各2起,河北、山西、辽宁、上海、山东、云南、新疆各1起;─—严重事故226起,其中:北京2起,天津8起,河北5起,山西3起,内蒙古3起,辽宁18起,吉林4起,黑龙江10起,上海15起,江苏20起,浙江12起,安徽省9起,福建7起,山东5起,河南11起,湖北4起,湖南5起,广东23起,广西8起,海南1起,重庆17起,四川5起,贵州2起,云南8起,西藏1起,陕西3起,甘肃6起,宁夏5起,新疆6起。
ASME标准简介系列三---锅炉及压力容器(BPVC)(正式版)

–
ASME《锅炉及压力容器(BPVC)》的组成
• • • • • • • • •
4、第Ⅳ卷 供热锅炉的建造规则 5、第Ⅴ卷 无损检验 6、第Ⅵ卷 供热锅炉维护和运行的推荐规则 7、第Ⅶ卷 动力锅炉维护的推荐导则 8、第Ⅷ卷 压力容器建造规则(两册,而1998 版把它分成了三册 1111111111,但咱们还没有98 版) 9、第Ⅸ卷 焊接及钎焊资格 10、第Ⅹ卷 纤维增强塑料压力容器 11、第Ⅺ卷 核动力装置设备在役检查规则 12、第XII卷 运输储罐的建造和延续施工规则(后增加的) 以上是ASME 锅炉及压力容器规范的全部内容,这样有11+1卷。
• 规范正文(Code Sections)
– 每三年出版(Edition)-1995,1998,2001,2004。。。 – 7月1日发布,6个月过度期 – 次年1月1日强制执行 • 规范增补(Addenda) – 每年发布一次 – 7月1日发布, 6个月过度期 – 次年1月1日强制执行 – 规范正文发布当年不发布增补 • 举例:2001版,A02,A03;A04包含在2004版中 • 规范案例(Code Cases) – 同规范正文和增补一同发布
五、ASME《锅炉及压力容器(BPVC)》 详述
ASME《锅炉及压力容器(BPVC)》详述
• 1、第Ⅰ(1)卷 动力锅炉建造规程 • 本规程包括:动力锅炉、电热锅炉、特小型锅炉和高温热水
锅炉,也适用于机车锅炉、可移动的或牵引用的动力锅炉。 包括锅炉本体和锅炉范围内管道,其中锅炉范围内管道在材 料、设计、制造、安装和检验方面的建造规程见ASME B31.1 动力管道。 动力锅炉——产生水蒸气或其他蒸汽供外部使用并且出口压力 大于1 5psi 的锅炉。 电热锅炉——以电为热源的动力锅炉或高温热水锅炉。 特小型锅炉——不超过本卷PMB-2 规定范围的动力锅炉或高温 热水锅炉(1、锅壳内径不大于16in;2、受热面积不大于 20ft2(但不适用于电热锅炉);3、总容积不大于5 ft3;4、最 高允许工作压力不大于100psi.)超过任何一项均按动力锅炉的 有关规定进行建造。
asme,v,asme锅炉及压力容器规范,第v卷,无损检测

竭诚为您提供优质文档/双击可除asme,v,asme锅炉及压力容器规范,第v卷,无损检测篇一:asme标准中文版asme标准中文版asmeb16.20-1993管法兰用环连接式.螺旋缠绕式及夹套式金属垫片asmeb16.21-1992管法兰用非金属平垫片asmesection-iasme锅炉及压力容器规范第Ⅰ卷动力锅炉建造规范20xx版+05+06增补asmesection-iiaasme锅炉及压力容器规范第Ⅱ卷a篇铁基材料20xx版+05+06增补asmesection-iibasme锅炉及压力容器规范第Ⅱ卷b篇非铁基材料20xx版+05+06增补asmesection-iicasme锅炉及压力容器规范第Ⅱ卷c篇焊条焊丝及填充材料20xx版+05+06增补asmesection-iidasme锅炉及压力容器规范第Ⅱ卷d篇材料性能20xx版+05+06增补asmesection-iVasme锅炉及压力容器规范第Ⅳ卷采暖锅炉建造规范20xx版+05+06增补asmesection-Vasme锅炉及压力容器规范第Ⅴ卷无损检测20xx版+05+06增补asmesection-iiinb1995版asme规范Ⅲ卷核动力装置设备制造准则一册nb分卷一级设备asmesection-iiinc1995版asme规范Ⅲ卷核动力装置设备制造准则一册nc分卷二级设备asmesection-iiincaasme规范Ⅲ卷(89版)核动力设备建造规则nca卷一册与第二册之总要求asmesection-iiind1995版asme规范Ⅲ卷核动力装置设备制造准则一册nd分卷三级设备asmesection-iiinF1995版asme规范Ⅲ卷核动力装置设备制造准则一册nF分卷设备支承结构asmesection-ixasme 锅炉及压力容器规范第Ⅸ卷焊接及钎焊评定标准20xx版+05+06增补asmesection-Viasme锅炉及压力容器规范第Ⅵ卷采暖锅炉维护和运行推荐规则20xx版+05+06增补asmesection-Viiasme锅炉及压力容器规范第Ⅶ卷动力锅炉维护推荐导则05年版asmesection-Viii-1asme锅炉及压力容器规范第Ⅷ卷1压力容器建造规则20xx版+05+06增补asmesection-Viii-2asme锅炉及压力容器规范第Ⅷ卷2压力容器另一规则20xx版+05+06增补asmesection-Viii-3asme 锅炉及压力容器规范第Ⅷ卷3高压容器建造另一规则20xx 版+05+06增补asmesection-xiiasme锅炉及压力容器规范第Ⅻ卷运输罐的建造和连续使用规则20xx版+05+06增补codecases规范案例20xx年版tced41001-2000asme压力容器规范实施导则asmeb31.1-20xx版动力管道asmeb31.3-20xx版工艺管道asme规范压力管道及管件b31、b16系列标准(上册)含5个标准1.asmeb31.4-1998版液态烃和其他液体管线输送系统2.asmeb31.5-1992(R1994)制冷管道3.asmeb31.8-1999版输气和配气管道系统4.asmeb31.9-1996版建筑管道规范5.asmeb31.11a-1989(R1998)版浆液输送管道系统asmeb31g-1991版确定已腐蚀管线剩余强度的手册(对asmeb31压力管道规范的补充文件)asme规范压力管道及管件b31、b16系列标准(下册)含10个标准1.asmeb16.1-1998版铸铁管法兰和法兰管件(25、125和250磅级)2.asmeb16.3-1998版可锻铸铁螺纹管件(150和300磅级)3.asmeb16.4-1998版灰铸铁螺纹管件(125和250磅级)4.asmeb16.9-1993版工厂制造的锻钢对焊管件5.asmeb16.10-1992版阀门的面至面和端至端尺寸6.asmeb16.11-1996版承插焊式和螺纹式锻造管件7.asmeb16.14-1991版钢铁管螺纹管堵、内外螺丝和锁紧螺母8.asmeb16.28-1994版锻轧钢制对接焊小弯头半径弯头和180度弯头9.asmeb18.2.1a-1999版方头及六角头螺栓和螺钉10.asmeptc25-1994压力泄放装置性能试验规范asmeb1.1-20xx版统一英制螺纹(16开中文版)asmeb1.3m-1992(R20xx)版螺纹尺寸验收的检测体系—英寸和米制螺纹(un、unR、unj、m和mj)asmeb1.5-1997版爱克母(acme)螺纹ansi/asmeb1.7m-1984(R20xx)版螺纹的术语、定义和字母符号asmeb1.8-1988(R1994)版矮牙爱克母螺纹asmeb1.12-1987(R1998)版5级过盈配合螺纹asmeb1.13m-20xx版m形米制螺纹ansi/asmeb1.20.1-1983(R20xx)版通用管螺纹asme(asme,v,asme锅炉及压力容器规范,第v卷,无损检测)b1.20.3-1976(R1998)版干密封管螺纹(英制) asmeb1.20.5-1991(R1998)版干密封管螺纹的检测(英制)asmeb1.20.7-1991(R1998)版软管接头螺纹(英制)asmeb4.3-1978(R1999)版米制尺寸产品通用公差asmeb16.5-20xx版管法兰和法兰管件asmeb16.9-20xx版工厂制造的锻轧制对焊管配件asmeb16.10-2000(R20xx)版阀门的面对面和端至端的尺寸asmeb16.11-20xx承插焊式和螺纹式锻造管件asmeb16.15-1985(R1994)版铸青铜螺纹管配件(125和250磅级)asmeb16.18-1984(R1994)版铸铜合金钎焊接头受压管配件asmeb16.20a-2000版管道法兰用环垫式、螺旋缠绕式和夹层式金属垫片asmeb16.21-20xx版管法兰用非金属平垫片asmeb16.22-20xx版锻压铜和铜合金钎焊连接压力管配件asmeb16.24-20xx版铸铜合金管法兰和法兰连接管配件asmeb16.25-20xx版对焊端部asmeb16.33-20xx版压力在125psi以下燃气系统用手动金属制燃气阀门(规格从nps1/2至nps2)asmeb16.34a-20xx 版法兰、螺纹和焊接端连接的阀门asmeb16.36-1996版孔板法兰(asmeb16.38-1985(R1994)版气体分配用大金属阀asmeb16.39-1998版可锻铸铁螺纹端管套节150、250和300磅级asmeb16.40-1985(R1994)版气体分配系统中手动热塑切断器和阀门asmeb16.42-1998版球墨铸铁管法兰和法兰连接管配件asmeb16.44a-1997版室内管道系统用手动操作金属气阀asmeb16.47a-1998版大直径管钢制法兰(nps26~nps60) asmeb16.48-1997版钢制管线盲板asmeb18.15-1985(R20xx)版锻制吊环螺栓asmeb18.2.2-1987(R20xx)版方螺母和六角螺母(英制系列)asmeb18.2.3.2m-20xx版米制成型加工六角头螺钉asmeb18系列标准合订本含25个标准,也可以单个标准订购1.asmeb18.2.3.1m-1999版米制六角头螺钉2.asmeb18.2.3.2m-79(R1995)版米制成型加工六角头螺钉3.asmeb18.2.3.3m-79(R20xx)版米制大六角头螺钉4.asmeb18.2.3.4m-20xx版米制六角头法兰面螺钉5.asmeb18.2.3.5m-79(R20xx)版米制六角头螺栓6.asmeb18.2.3.6m-79(R20xx)版米制厚六角头螺栓7.asmeb18.2.3.7m-79(R20xx)版米制大六角头结构螺栓8.asmeb18.2.3.8m-81(R1999)版米制六角头尖端阻滞螺钉9.asmeb18.2.3.9m-20xx版米制大六角头法兰面螺钉10.asmeb18.2.3.10m-1996版方头螺栓(米制系列)1.asmeb18.2.4.1m-20xx版米制六角螺母-类型112.asmeb18.2.4.2m-20xx版米制六角螺母-类型213.asmeb18.2.4.3m-79(R20xx)版米制六角开槽螺母14.asmeb18.2.4.4m-82(R1999)版米制六角法兰面螺母15.asmeb18.2.4.5m-79(R1998)版米制六角形压紧螺母16.asmeb18.2.4.6m-79(R1998)版米制厚六角形螺母17.asmeb18.5-90(R1998)版圆头螺栓(英制系列)18.asmeb18.5.2.1m-1996(R20xx)米制圆头短方颈螺栓19.asmeb18.5.2.2m-82(R2000)米制圆头方颈螺栓20.asmeb18.5.2.3m-90(R1998)版大圆头方颈螺栓2.asmeb18.9-1996版农用防松螺栓(英制系列)22.asmeb18.10-82(R2000)版轨道螺栓和螺母23.asmeb18.13a-1998版螺钉和垫圈组件-24.asmeb18.16.1m-79(R20xx)版有效力矩型钢质米制六角锁紧螺母和六角法兰面锁紧螺母的力学和性能要求25.asmeb18.16.2m-79(R20xx)版有效力矩型钢质米制六角锁紧螺母和六角法兰面锁紧螺母的扭转拉伸试验要求asmeb18.29.1-1993(R20xx)版螺旋盘绕螺纹内插件—自由旋入和螺钉锁紧(英制系列)asmeb31.4-20xx版液态烃和其他液体管线输送系统asmeb31.8s-20xx版输气管道的管理系统完整性asmeb31.9-20xx版建筑管道规范asmeb36.10m-20xx版焊接和无缝轧制钢管asmeb36.19m-20xx版不锈钢钢管asmeb46.1-20xx版表面结构特征(表面粗糙度、波浪度及形态)asmeb73.1-20xx版化学流程用卧式轴向吸入离心泵技术规范asmeb73.2m-1991(R1999)版化学过程用立式管道离心泵技术规范asmeb107.46-1998版螺柱、螺钉和管道提取器:安全要求iso,asme,astm,din,jis国外管道法兰用密封垫片标准汇编篇二:asme锅炉及压力容器规范第Ⅸ卷简介asme锅炉及压力容器规范第Ⅸ卷简介─20xx版与20xx版对比及与国内标准的比较(节选)在本文中,简要介绍了asme锅炉及压力容器规范第Ⅸ卷,并将其20xx版与20xx版和国内标准进行了对比。
ASME NG分卷(05增补)

ASME锅炉及压力容器规范国际性规范III 核设施部件建造规则美国国家标准第1册NG分卷堆芯支承结构2005增补2005年7月1日ASME锅炉及压力容器委员会核动力分委员会编著上海发电设备成套设计研究院翻译上海核工程研究设计院出 版 说 明美国机械工程师学会(ASME)颁布的《锅炉及压力容器规范》(简称《ASME规范》或《规范》),是目前世界上公认的范围最为广泛、内容最为详尽的一部关于锅炉及压力容器的规范。
该系列《规范》在一些国家已得到广泛应用,有些国家的规范、标准也来源于此。
规范自1914年正式问世以来,至今已有九十余年的历史。
近三十年来,规范每三年修订一次,颁布新的版本。
至今已扩展至11卷28册的系列型规范。
其中第III卷《核设施部件建造规则》已扩展到3册12分卷,它与第II卷《材料》、第V卷《无损检测》、第VIII卷《压力容器建造规则》、第IX卷《焊接和钎焊评定》、第XI卷《核电厂部件在役检查规则》等综合在一起组成了核电厂设备的材料、设计、制造、焊接、检测、运行等方面一套完整的规范和标准体系。
为更好地消化吸收国外先进的规范、标准体系,积极推进我国自主核电设备设计、制造事业的发展,并为建立我国自主核电标准体系创造良好条件,2006年2月上海发电设备成套设计研究院与美国机械工程师学会签订了翻译出版与核电有关的2004版BPVC-III、BPVC-XI、OM、AG-1、QME、NQA和RA-S等规范、标准的授权协议。
2006年3月上海发电设备成套设计研究院与上海核工程研究设计院签订“ASME核电规范翻译出版合作协议”,成立了“ASME核电规范与标准翻译出版委员会”和“ASME核电规范翻译出版工作组”,组织和邀请熟悉核电工程和具有丰富经验的技术人员分专业进行译、校、审和统审。
中文版尽量达到使从事核电工程的技术人员能正确理解和应用本规范与标准的目的。
2008年,“ASME核电规范翻译出版工作小组”又组织翻译了相关标准的05、06年增补,该增补中文版将陆续以电子版形式发送给04版标准的购买者。
04版ASME规范II卷-C篇2005增补

ASME锅炉及压力容器规范国际性规范II材料C篇 焊条、焊丝及填充金属2005增补ASME锅炉及压力容器委员会压力容器分委员会编著中国《ASME规范产品》协作网(CACI)翻译、发送2006年3月1日2005增补发送说明经美国机械工程师学会(ASME)许可,中国《ASME规范产品》协作网(CACI)翻译出版了2004版ASME锅炉及压力容器规范和相关规范。
与规范英文原版一样,我们也翻译有关增补。
因为英文原版是活页的,为方便更换,其增补也是活页的。
而规范中译本是装订本,因此我们以表格方式翻译、编辑了增补,即注明04版中文本页码、章节、修改部位和05增补的修改内容。
如修改内容多或有新增和变动较大的图、表,在表格中放不下的,则将修改内容、图、表,放在后面,并注明位于中译本中的页码。
本增补由CACI聘请吴祖乾、虞茂林、戴佩琨译校,CACI编辑。
中文版增补版权属CACI所有。
本增补(原版)在2005年7月1日发布,自发布之日起6个月后生效。
执行时应以英文原版为准。
由于各种原因,本次翻译发送的增补可能会有不足和错误,希望广大用户和读者提出批评和指正,以便改进。
来信请寄:北京市西城区月坛南街26号中国《ASME规范产品》协作网邮政编码:100825电子邮箱:caci@中国《ASME规范产品》协作网2006年3月2005年度增补增补修改内容04中文版页码章节/部位 05全面修改,见本增补第3页至第4页。
xxxi全文修订,见本增补第5页至第44页。
9~41 SFA-5.1151~171 SFA-5.8全文修订,见本增补第45页至第73页。
全文修订,见本增补第74页至第89页。
304~311 SFA-5.16向锅炉及压力容器委员会提交技术咨询函导则1 引言(a)本附录为规范的使用者向规范委员会提出技术询问提供指导,参见ASME锅炉及压力容器规范第II卷、C和D篇关于在规范中申请增加新材料的批准指南。
技术询问包括请求对规范规则的修订或增补、申请规范案例及请求对规范条款的解释。
ASME锅炉及压力容器规范(国际性规范-铁基)
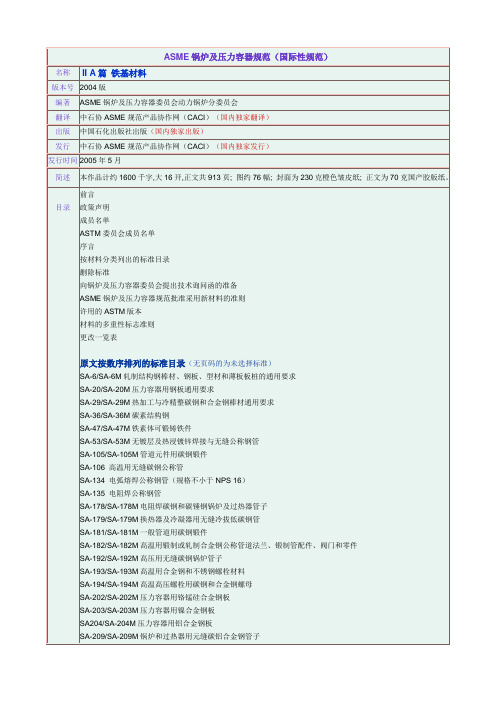
前言政策声明成员名单ASTM委员会成员名单序言按材料分类列出的标准目录删除标准向锅炉及压力容器委员会提出技术询问函的准备ASME锅炉及压力容器规范批准采用新材料的准则许用的ASTM版本材料的多重性标志准则更改一览表原文按数序排列的标准目录(无页码的为未选择标准)SA-6/SA-6M轧制结构钢棒材、钢板、型材和薄板板桩的通用要求SA-20/SA-20M压力容器用钢板通用要求SA-29/SA-29M热加工与冷精整碳钢和合金钢棒材通用要求SA-36/SA-36M碳素结构钢SA-47/SA-47M铁素体可锻铸铁件SA-53/SA-53M无镀层及热浸镀锌焊接与无缝公称钢管SA-105/SA-105M管道元件用碳钢锻件SA-106 高温用无缝碳钢公称管SA-134 电弧熔焊公称钢管(规格不小于NPS 16)SA-135 电阻焊公称钢管SA-178/SA-178M电阻焊碳钢和碳锤钢锅炉及过热器管子SA-179/SA-179M换热器及冷凝器用无缝冷拔低碳钢管SA-181/SA-181M一般管道用碳钢锻件SA-182/SA-182M高温用锻制或轧制合金钢公称管道法兰、锻制管配件、阀门和零件SA-192/SA-192M高压用无缝碳钢锅炉管子SA-193/SA-193M高温用合金钢和不锈钢螺栓材料SA-194/SA-194M高温高压螺栓用碳钢和合金钢螺母SA-202/SA-202M压力容器用铬锰硅合金钢板SA-203/SA-203M压力容器用镍合金钢板SA204/SA-204M压力容器用铝合金钢板SA-209/SA-209M锅炉和过热器用元缝碳铝合金钢管子。
asme锅炉及压力容器规范(国际性规范) (1)

ASME锅炉及压力容器规范(国际性规范)名II 材料D篇性能(公制)称版2007版本号编ASME锅炉及压力容器委员会材料分委员会著出中国石化出版社出版(国内独家出版)版目录前言(xvii)政策声明(xx)成员名单(xxi)更改一览表(xxxiii)第1分篇应力表(1)应力表中提供的资料政策声明(1)在应力表和在力学性能和物理性能表中查找材料的导则(2)表1A第Ⅰ卷、第Ⅲ卷2级与3级部件、第Ⅷ卷第1册和第Ⅻ卷用铁基材料的最大许用应力值S(6)表1B第Ⅰ卷、第Ⅲ卷2级与3级部件、第Ⅷ卷第1册和第Ⅻ卷用非铁基材料的最大许用应力值S(154)表2A第Ⅲ卷1级部件、TC和SC用铁基材料的设计应力强度值Sm(276)表2B第Ⅲ卷1级部件,TC和SC用非铁基材料的设计应力强度值Sm(336)表3第Ⅲ卷2级与3级部件、第Ⅷ卷第1册与第2册和第Ⅻ卷用螺栓材料的最大许用应力值S(348)表4第Ⅲ卷1级部件、TC和SC;第Ⅷ卷第2册用螺栓材料的设计应力强度值Sm(378)表5A第Ⅷ卷第2册用铁基材料的最大许用应力值Sm(390)表5B第Ⅷ卷第2册用非铁基材料的最大许用应力值Sm(456)表U铁基和非铁基材料的抗拉强度值Su(486)表U-2第Ⅷ卷第3册铁基材料的抗拉强度值Su(565)表Y-1铁基和非铁基材料的屈服强度值Sy(566)表Y-2镍、高镍合金和高合金钢中限制永久变形的系数(743)第2分篇物理性能表(745)前言(745)表TE-1铁基材料的热膨胀系数(746)表TE-2铝合金的热膨胀系数(752)表TE-3铜合金的热膨胀系数(753)表TE-4镍合金的热膨胀系数(754)表TE-5钛合金的热膨胀系数(763)表TCD标称的导热系数(TC)和热扩散系数(TD)(764)表TM-1给定温度下铁基材料的弹性模量E(776)表TM-2给定温度下铝和铝合金的弹性模量E(778)表TM-3给定温度下铜和铜合金的弹性模量E(779)表TM-4给定温度下高镍合金的弹性模量E(780)表TM-5给定温度下钛和锆的弹性模量E(781)表NF-1材料的典型力学性能(782)表NF-2非铁基材料的典型物理性能(783)第3分篇外压作用下确定部件壳体厚度用线算图和线算图用表(785)图G外压或压缩载荷作用下部件的几何尺寸线算图(用于所有材料)(787)图CS-1当用碳钢或低合金钢[规定的最小屈服强度165MPa到205MPa(但不包括)]建造时受外压部件确定壳体厚度用线算图(788)图CS-2当用碳钢或低合金钢(规定的最小屈服强度≥205MPa,但在此范围内注明其他专用线算图的材料除外)和405型及410型不锈钢建造时受外压部件确定壳体厚度用线算图(788)图CS-3当用碳钢、低合金钢或用热处理提高性能的钢(规定最小的屈服强度>262MPa,没有注明使用专门线算图的材料)建造时受外压部件确定壳体厚度用线算图(789)图CS-4当用SA-537建造时受外压部件确定壳体厚度用线算图(789)图CS-5当用SA-508 1类,2和3级,SA-508 2类,2级;SA-533 1类A,B,C和D级;SA-533 2类,A,B,C和D级;或SA-541 2和3级建造时受外压部件确定壳体厚度用线算图(790)图CS-6当用SA-562或SA-620碳钢建造时受外压部件确定壳体厚度用线算图(790)图HT-1当用t≤63.5mm淬火和回火低合金钢,SA-517所有级别和SA-592 A,E和F级建造时受外压部件确定壳体厚度用线算图(791)图HT-2当用SA-508 4N级,2类或SA-543 B和C型,2类建造时受外压部件确定壳体厚度用线算图(791)图HA-1当用奥氏体钢(18Cr-8Ni,304型)建造时受外压部件确定壳体厚度用线算图(792)图HA-2当用奥氏体钢[16Cr-12Ni-2Mo,316型;18Cr-10Ni-Ti,321型;18Cr-10Ni-Cb,347型;25Cr-12Ni,309型(仅到595℃);25Cr-20Ni,310型和17Cr, 430B型不锈钢(仅到370℃)]建造时受外压部件确定壳体厚度用线算图(792)图HA-3当用奥氏体钢(18Cr-8Ni最大含碳量0.035,304L型)建造时受外压部件确定壳体厚度用线算图(793)图HA-4当用奥氏体钢(18Cr-8Ni-Mo最大含碳量0.035,316L和317L型)建造时受外压部件确定壳体厚度用线算图(793)图HA-5当用Cr-Ni-Mo合金S31500建造时受外压部件确定壳体厚度用线算图(794)图HA-6当用21Cr-11Ni-N合金S30815建造时受外压部件确定壳体厚度用线算图(794)图HA-7当用SA-564,630型H1150建造时受外压部件确定壳体厚度用线算图(795)图HA-8当用双相不锈钢25Cr-7Ni-3Mo-2W-0.28N(UNS S39274)建造时受外压部件确定壳体厚度用线算图(796)图CI-1当用铸铁建造时受外压部件确定壳体厚度用线算图(796)图CD-1当用规定最低屈服强度为275MPa的球墨铸铁建造时受外压部件确定壳体厚度用线算图(797)图NFA-1当用3003铝合金O和H112状态建造时受外压部件确定壳体厚度用线算图(797)(798)图NFA-3当用3004铝合金O和H112状态建造时受外压部件确定壳体厚度用线算图(799)图NFA-4当用3004铝合金H34状态建造时受外压部件确定壳体厚度用线算图(800)图NFA-5当用5154铝合金O和H112状态建造时受外压部件确定壳体厚度用线算图(801)图NFA-6当用5454铝合金O和H112状态建造时受外压部件确定壳体厚度用线算图(801)图NFA-7当用1060铝合金O状态建造时受外压部件确定壳体厚度用线算图(802)图NFA-8当用5052铝合金O和H112状态建造时受外压部件确定壳体厚度用线算图(802)图NFA-9当用5086铝合金O和H112状态建造时受外压部件确定壳体厚度用线算图(803)图NFA-10当用5456铝合金O状态建造时受外压部件确定壳体厚度用线算图(803)图NFA-11当用5083铝合金O和H112状态建造时受外压部件确定壳体厚度用线算图(804)图NFA-12当对所有厚度用5356或5556填充金属,及对厚度≤10mm用4043或5554填充金属焊接的铝合金6061-T6,-T651,-T6510和-T6511建造时受外压部件确定壳体厚度用线算图(804)图NFA-13当用6061-T4,-T451,-T4510和-T4511焊接铝合金,用4043,5554,5356,或5556填充金属焊接时,所有厚度;用6061-T6,-T651,-T6510和-T6511焊接铝合金,用4043或5554填充金属焊接时,厚度>10mm建造时受外压部件确定壳体厚度用线算图(805)图NFC-1当用DHP型退火铜建造时受外压部件确定壳体厚度用线算图(805)图NFC-2当用铜-硅合金A和C建造时受外压部件确定壳体厚度用线算图(806)图NFC-3当用退火的90-10铜-镍合金建造时受外压部件确定壳体厚度用线算图(806)图(807)图NFC-5当用焊接C19400铜-铁合金管(SB-543焊接的)建造时受外压部件确定壳体厚度用线算图(807)图NFC-6当用SB-75和SB-111轻微拔制无缝铜管,C10200,C12000,C12200和C14200合金建造时受外压部件确定壳体厚度用线算图(808)图NFC-7当用退火铜SB-75,UNS C12200和回火O50建造时受外压部件确定壳体厚度用线算图(808)图NFC-8当用铝青铜合金C61400建造时受外压部件确定壳体厚度用线算图(809)图NFN-1当用低碳镍N02201建造时受外压部件确定壳体厚度用线算图(809)图NFN-2当用镍N02200建造时受外压部件确定壳体厚度用线算图(810)图NFN-3当用退火镍-铜合金N04400建造时受外压部件确定壳体厚度用线算图(810)图NFN-4当用退火镍-铬-铁合金N06600建造时受外压部件确定壳体厚度用线算图(811)图NFN-5当用镍-钼合金N10001建造时受外压部件确定壳体厚度用线算图(811)图NFN-6当用镍-钼-铬-铁合金10003建造时受外压部件确定壳体厚度用线算图(812)图NFN-7当用镍-铁-铬-钼-铜合金N08825建造时受外压部件确定壳体厚度用线算图(812)图NFN-8当用镍-铁-铬合金N08800(退火的)建造时受外压部件确定壳体厚度用线算图(813)图NFN-9当用镍-铁-铬合金N08810(退火的)建造时受外压部件确定壳体厚度用线算图(813)图NFN-10当用低碳镍-钼-铬合金N10276建造时受外压部件确定壳体厚度用线算图(814)图NFN-11当用固熔处理镍-铬-铁-钼-铜合金N06007和N06975建造时受外压部件确定壳体厚度用线算图(814)图NFN-12当用锻造的铬-镍-铁-钼-铜-铌稳定化合金N08020和铁-镍-铬-钼合金N08367,SB-462,SB-463,SB-464,SB-468和SB-473建造时受外压部件确定壳体厚度用线算图(815)图NFN-13当用镍-铁-铬-硅合金N08330建造时受外压部件确定壳体厚度用线算图(815)图NFN-14当用镍-铬-钼合金N06455建造时受外压部件确定壳体厚度用线算图(816)图NFN-15用镍-钼合金N06002建造时受外压部件确定壳体厚度用线算图(816)图NFN-16当用镍-钼合金N10665建造时受外压部件确定壳体厚度用线算图(817)图NFN-17当用退火的镍-铬-钼-铌合金N06625(合金625中的SB-443,SB-444和SB-446)建造时受外压部件确定壳体厚度用线算图(817)图NFN-18当用厚度≤19mm和最小屈服强度为240MPa的镍-钼-铬-铁-铜合金N06985建造时受外压部件确定壳体厚度用线算图(818)图NFN-19当用厚度>19mm和最小屈服强度为207MPa的镍-钼-铬-铁-铜合金N06985建造时受外压部件确定壳体厚度用线算图(818)图NFN-20当用加工硬化镍建造时受外压部件确定壳体厚度用线算图(819)图NFN-21当用镍-铬-铁合金N06600和N06690,SB-163(规定的最小屈服强度276MPa)建造时受外压部件确定壳体厚度用线算图(819)图NFN-22当用固熔退火的Ni-Cr-Mo-Cb合金2级N06625建造时受外压圆筒形和球形容器确定壳体厚度用线算图(820)图NFN-23当用镍-铁-铬合金800(冷加工的)建造时受外压圆筒形和球形容器确定壳体厚度用线算图(820)图NFN-24当用镍基合金N06230建造时受外压部件确定壳体厚度用线算图(821)图NFN-25当用消除应力的镍合金N02200建造时受外压部件确定壳体厚度用线算图(821)图NFN-26当用合金S31277建造时受外压部件确定壳体厚度用线算图(822)图NFT-1当用非合金化钛,3级建造时受外压部件确定壳体厚度用线算图(822)图NFT-2当用非合金化钛,2级建造时受外压部件确定壳体厚度用线算图(823)图NFT-3当用钛,1级,R5025建造时受外压部件确定壳体厚度用线算图(823)图NFT-4当用钛,级别9,R56320合金(Ti-3Al-2.5V-0.1Ru)建造时受外压部件确定壳体厚度用线算图(824)图NFT-5当用钛,级别12,R53400合金(Ti-0.8Ni-0.3Mo)建造时,受外压部件确定壳体厚度用线算图(824)图NFZ-1当用锆合金702建造时受外压部件确定壳体厚度用线算图(825)图NFZ-2当用锆合金705[R60705]建造时受外压部件确定壳体厚度用线算图(826)表表G图G的表值(828)表CS-1图CS-1的表值(830)表CS-2图CS-2的表值(831)表CS-3图CS-3的表值(831)表CS-4图CS-4的表值(832)表CS-5图CS-5的表值(832)表CS-6图CS-6的表值(833)表HT-1图HT-1的表值(833)表HT-2图HT-2的表值(833)表HA-1图HA-1的表值(834)表HA-2图HA-2的表值(835)表HA-3图HA-3的表值(835)表HA-4图HA-4的表值(836)表HA-6图HA-6的表值(837)表HA-7图HA-7的表值(838)表HA-8图HA-8的表值(838)表CI-1图CI-1的表值(839)表CD-1图CD-1的表值(839)表NFA-1图NFA-1的表值(840) 表NFA-2图NFA-2的表值(841) 表NFA-3图NFA-3的表值(842) 表NFA-4图NFA-4的表值(843) 表NFA-5图NFA-5的表值(843) 表NFA-6图NFA-6的表值(844) 表NFA-7图NFA-7的表值(844) 表NFA-8图NFA-8的表值(845) 表NFA-9图NFA-9的表值(845) 表NFA-10图NFA-10的表值(845) 表NFA-11图NFA-11的表值(846) 表NFA-12图NFA-12的表值(847) 表NFA-13图NFA-13的表值(847) 表NFC-1图NFC-1的表值(848) 表NFC-2图NFC-2的表值(848) 表NFC-3图NFC-3的表值(848) 表NFC-4图NFC-4的表值(849)表NFC-6图NFC-6的表值(850) 表NFC-7图NFC-7的表值(850) 表NFC-8图NFC-8的表值(851) 表NFN-1图NFN-1的表值(851) 表NFN-2图NFN-2的表值(852) 表NFN-3图NFN-3的表值(853) 表NFN-4图NFN-4的表值(854) 表NFN-5图NFN-5的表值(854) 表NFN-6图NFN-6的表值(855) 表NFN-7图NFN-7的表值(855) 表NFN-8图NFN-8的表值(856) 表NFN-9图NFN-9的表值(856) 表NFN-10图NFN-10的表值(857) 表NFN-11图NFN-11的表值(857) 表NFN-12图NFN-12的表值(858) 表NFN-13图NFN-13的表值(858) 表NFN-14图NFN-14的表值(859) 表NFN-15图NFN-15的表值(860) 表NFN-16图NFN-16的表值(861) 表NFN-17图NFN-17的表值(862) 表NFN-18图NFN-18的表值(863) 表NFN-19图NFN-19的表值(864)表NFN-20图NFN-20的表值(865)表NFN-22图NFN-22的表值(865)表NFN-23图NFN-23的表值(866)表NFN-24图NFN-24的表值(867)表NFN-25图NFN-25的表值(868)表NFN-26图NFN-26的表值(868)表NFT-1图NFT-1的表值(869)表NFT-2图NFT-2的表值(870)表NFT-3图NFT-3的表值(870)表NFT-4图NFT-4的表值(871)表NFT-5图NFT-5的表值(872)表NFZ-1图NFZ-1的表值(873)表NFZ-2图NFZ-2的表值(873)强制性附录强制性附录1确定表1A和表1B中应力值的根据(875)强制性附录2确定表2A、表2B、表3和表4中设计应力强度值的根据(877) 强制性附录3建立受外压线算图的根据(879)强制性附录4向锅炉及压力容器委员会提交技术咨询书的方式(885)强制性附录5ASME锅炉及压力容器规范批准新材料的指南(887)强制性附录7材料的多重性标志导则(891)强制性附录9用于公式中的标准单位(893)强制性附录10确定表5A和5B中最大许用应力值的根据(894)非强制性附录非强制性附录A冶金现象(896)非强制性附录C在ASME锅炉及压力容器规范中使用美国习惯单位制和SI制的指南(903)。
ASME锅炉及压力容器规范

QW-286.3 按 图 QW — 462.7.2 焊 接 长 度 至 少 为 10in. (250mm)的一个试件,将试件沿垂直焊缝方向切成 10 块,每 块宽度近似 1in.(25mm),按图 QW—462.7.2 制取 4 个横向焊 缝试样和 4 个纵向焊缝截面试样(沿焊缝纵向在焊缝宽度的 1/3 处再切一刀,详见图 QW—462.7.2 的注—译注),对每个试样 (的一个横截面)作金相检测,并满足 QW—196 的要求。
裂,则判为试验合格。
修改为:
QW-199.1.2 拉伸试验 对于管径小于等于 NPS1(DN25)和
10
QW-199.1.2
本条款 非管状横截面的试件,应按图 QW-462.1(e)制备 2 个全截面
拉伸试样;对于管径大于 NPS 1 的管子,应按图 QW-462.1(b)
或图 QW-462.1(c)从一个试件制备 2 个缩截面拉伸试样。对
增加:
左第 3 行末 ……。对于非管状横截面的试件,应从两个剩余试件按图 QW-462.2 制备 4 个侧弯试样并抛光供检测。
“闪光焊应限于管子横断面的自动电阻闪光焊”修改为: 本节第 1 行 闪光焊应限于自动电阻闪光焊,……
表中第 8 行 取消“QW-406 预热” 1 行 第 9 行 将“QW-407.5”纠正为“QW-407.1”。
6
QW-191.1(b) 本条款 及孔型像质计(IQI)规定的孔或线型 IQI 规定的线,并应满足
QW-191.2 的合格标准。
修改为:
QW-196.1 金相检测 QW-196.1.1 取焊缝横截面抛光、侵蚀以显示出焊缝金属,
用 10 倍放大镜对断面进行检测。缝焊焊缝应按图 QW—462.7.3 制备,焊件断面应无裂纹、未焊透、喷出(指在电阻焊中由于参 数不当,熔化金属从结合点喷出—译注)和夹渣;在试样的横断面上 的气孔不超过 1 个、在纵断面上的气孔不超过 3 个,任何气孔 的最大尺寸应不超过焊道厚度的 10%。
ASME锅炉及压力容器规范国际性规范 Ⅷ 第2册04版2005增补

ASME锅炉及压力容器规范国际性规范VIII第二册压力容器建造另一规则2005增补ASME锅炉及压力容器委员会压力容器分委员会编著中国《ASME规范产品》协作网(CACI)翻译、发送2006年3月1日2005增补发送说明经美国机械工程师学会(ASME)许可,中国《ASME规范产品》协作网(CACI)翻译出版了2004版ASME锅炉及压力容器规范和相关规范。
与规范英文原版一样,我们也翻译有关增补。
因为英文原版是活页的,为方便更换,其增补也是活页的。
而规范中译本是装订本,因此我们以表格方式翻译、编辑了增补,即注明04版中文本页码、章节、修改部位和05增补的修改内容。
如修改内容多或有新增和变动较大的图、表,在表格中放不下的,则将修改内容、图、表,放在后面,并注明位于中译本中的页码。
本增补由CACI聘请丁伯民翻译AG,AD附录1~6,20,27,G,J,M,N,邵国华校对;王国平翻译AM,AF,AR,AI,AT,AS附录8~19,21~26,A~E,I,K,L陈登丰校对,CACI编辑。
中文版增补版权属CACI所有。
本增补(原版)在2005年7月1日发布,自发布之日起6个月后生效。
执行时应以英文原版为准。
由于各种原因,本次翻译发送的增补可能会有不足和错误,希望广大用户和读者提出批评和指正,以便改进。
来信请寄:北京市西城区月坛南街26号中国《ASME规范产品》协作网邮政编码:100825电子邮箱:caci@中国《ASME规范产品》协作网2006年3月2005年度增补04中文版页码章节修改部位 05 增 补 修 改 内 容5 AG-150 表AG-150.1增加引用ASME PCC-1名称:螺栓法兰组合接头的承压范围指南标准编号:ASME PCC-1 年份:2000 13AM-203.2 (b)(2) 第2行第一句“对于斜射波法检测采用1in.×1in.(25mm×25mm)或1in.×1/2in.(25mm×13mm) ……”修改为“对于斜射波法检测采用1in.×1in.(25mm×25mm)到1in.×1/2in.(25mm×13mm) ……”。
ASME压力管道、锅炉、压力容器焊接工艺参数确定、评定方法与规则

ASME压力管道、锅炉、压力容器焊接工艺参数确定、评定方法于规则1.焊接方法;从一种焊接方法改用另一种焊接方法,应作焊接工艺评定试验。
适用于锅炉与压力容器的焊接方法有:气焊、焊条电弧焊、埋弧焊、熔化极气体保护焊、钨极气体保护焊、等离子弧焊、电渣焊、激光焊、电子束焊、闪光对接焊、感应加热压力焊、电阻焊、铝热压焊、气压焊、惯性及连续驱动母材焊、螺柱电弧焊和螺柱电阻焊。
在实际焊件的同一条焊缝上,如采用两种或两种以上不同的焊接方法,或不同的重要工艺参数焊接时,则可按每种焊接方法所焊的母材,金属厚度分别对试件进行焊接工艺评定。
也可以实际焊件焊缝拟使用的组合焊件方法或焊接工艺焊接同一付工艺评定试件。
但每一种焊接方法,或焊接工艺所焊的焊缝金属厚度均应满足能取出所要求的拉伸和弯曲试样的要求。
对于焊条电弧焊、钨极气体保护焊、熔化极气体保护焊、等离子弧焊和埋弧焊,或这些方法的组合,如已完成的焊接工艺评定采用厚度大于13mm的试件,则该焊接工艺评定报告可与另一种焊接方法的工艺评定报告联用于同一条实际焊件的焊缝,包括根部焊道。
2.母材金属类别;在锅炉与压力容器中所用母材金属的种类繁多。
如以母材金属的钢号或材料的牌号进行评定,则评定的工作量十分大,且无此必要性。
为了减少这种无实际意义的重复评定,国外ASME法规的作法是,将规定认可的标准材料,按其化学成分,力学性能和焊接性加以分类,即将合金成分相近,强度级别和焊接性接近的材料规入一类,并标以P分类号。
在同一类母材金属中,又按强度和冲击韧性的等级进行分组,并将分组号标在分类号的后面,例如SA106-A碳钢属于第1类第1组,其分类组别号的表示方法为P1-1。
最新版的ASME法规已将在锅炉和压力容器中使用的近1000种钢材分成23类52组。
这种对母材金属的分类是以大量的材料焊接性试验和焊接工艺试验数据以及多年的实际生产经验为基础的。
因此,列于同一类的各种母材金属,如拟采用的焊接工艺规程中,其它的焊接工艺重要参数相同或在容许范围之内,则采用某种母材金属的焊接工艺评定报告可互相通用。
asme规范第i卷-2005年增补述评.doc

ASME规范第I卷2005年增补述评(节选)吕翔上海发电设备成套设计研究所内容提要Author abstract:对ASME锅炉及压力容器规范第I卷2005增补作简要介绍,对其中重要的修改进行学习,并与我国标准中的相应条文进行比较。
A brief introduction to 2005 Addenda of ASME Boiler and Pressure Vessel Code, Section I. Leaning some important changes in it and comparing with the relevant provisions in China Standard.关键词Key words:ASME规范增补ASME Code, Addenda.ASME规范第I卷2005年增补共修改71项,其中编辑性修改27项,技术性修改44项。
2001~2005年逐年技术性修改总数见附录1。
五年合计232项,年平均46项。
2005年44项技术性修改的主要内容见附录2,现将其中较为重要的作进一步说明,共12项,即:盖板、开孔、安全泄放阀、焊缝的受热条件、T91的焊后热处理、焊接试板、炉门、检查孔、水位指示器、水压试验温度、安全阀和安全泄放阀的铅直安装、图A-8。
1、盖板1.1 概述修订前,图PG-31简图(e)、(f)和(g)中的圆形或非圆形盖板,与筒体的连接方式,简图(e)和(f)为内外侧角焊缝,简图(g)则为部分焊透焊缝。
修订后,将简图(g)分为简图(g-1)和(g-2),主要修改内容见表1。
这些修改目的是为了使系数C=0.33m的使用条件进一步完善。
1.2 C=0.33m的含义平端盖(或盖板)的周边约束与筒体与平端盖(或盖板)的刚度有关,简图(e)、(f)和(g)中,将PG-31.3.2公式(1)的系数C,用C=0.33m来反映筒体刚度对盖板计算厚度的影响,m=t r/t s,t r为筒体承压所需要的厚度,t s为筒体的最小规定厚度即实际厚度,由于t r<t s,m<1.0。
ASME BPVC锅炉及压力容器规范目录
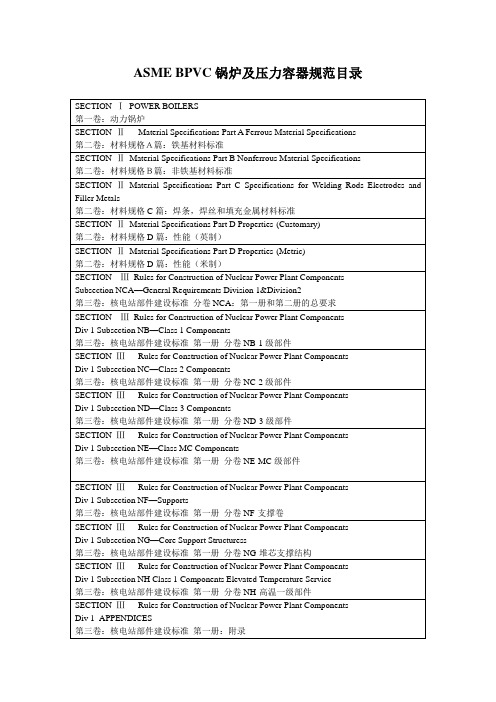
SECTIONⅢRules for Construction of Nuclear Power Plant Components
Div 1- APPENDICES
第三卷:核电站部件建设标准第一册:附录
SECTIONⅢRules for Construction of Nuclear Power Plant Components
Subsection NCA—General Requirements Division 1&Division2
第三卷:核电站部件建设标准分卷NCA:第一册和第二册的总要求
SECTIONⅢRules for Construction of Nuclear Power Plant Components
ASME BPVC锅炉及压力容器规范目录
SECTIONⅠPOWER BOILERS
第一卷:动力锅炉
SECTIONⅡMaterial Specifications Part A Ferrous Material Specifications
第二卷:材料规格A篇:铁基材料标准
SECTIONⅡMaterial Specifications Part B Nonferrous Material Specifications
第三卷:核电站部件建设标准第三册:废核燃料和高位放射性材料和废料的储存和运输包装用安全容器系统
SECTIONⅣHeating Boilers
第四卷:采暖锅炉
SECTIONⅤNondestructive Examination
第五卷:无损检测
SECTIONⅥRecommended Rules for the Care and Operation of Heating Boilers
《ASME锅炉及压力容器规范》简介

《ASME锅炉及压力容器规范》简介
张广成
【期刊名称】《山东电力技术》
【年(卷),期】1997(000)001
【摘要】1915年,美国机械工程师学会(简称ASME)锅炉压力容器委员会制定出第一版ASME规范,当时的名称为“电站锅炉建造规程和许用工作压力准则”,尚不包括压力容器。
现在规范已发展为11卷,分别为动力锅炉、材料、核动力设备、采暖锅炉、无损检验、采暖锅炉维护和运行的推荐准则、动力锅炉维护的推荐准则、压力容器、焊接及钎焊评定、玻璃纤维增强塑料压力容器、核动力设备在役检查准则等。
ASME规范是按照被认可为符合美国国家标准的程序制定的,是一部历史悠久的、慎重的并且建立在长期成功经验之上的规范。
该规范应用遍及美国和加拿大,并已成为一部国际公认的标准。
近几年来。
【总页数】3页(P61-62,68)
【作者】张广成
【作者单位】山东电力科学研究试验院
【正文语种】中文
【中图分类】TK22-65
【相关文献】
1.ASME锅炉及压力容器规范在潜艇结构中的适用性分析 [J], 王慧敏;蔡斯渊;夏益美;王德禹
2.ASME 锅炉压力容器规范第Ⅸ卷新版焊接规范介绍(一) [J], 赵孟显
3.ASME 锅炉压力容器规范第Ⅸ卷新版焊接规范介绍(二) [J], 赵孟显
4.ASME锅炉及压力容器规范第八卷新增第三册高压容器规范简介 [J], 王晓燕
5.用《ASME锅炉及压力容器规范国际性规范VIII-3》对高压容器进行疲劳评定[J], 高耀东;范要鹏;王换玉
因版权原因,仅展示原文概要,查看原文内容请购买。
ASME锅炉压力容器标准规范(2010版,中文译本)

140.00
18 ASME B 31.5-2006 制冷管道
120.00
19 ASME B 31.8-2007 输气和配气管道系统
300.00
20 ASME B 31.8S-2004 输气管道的管理系统完整性
90.00
21
ASME B 31G-2009 确定已腐蚀管线剩余强度的手册(对 ASME B31 压力管 道规范的补充文件)(中英对照)
650.00
14 ASME B 31.1-2010 动力管道
300.00
15 ASME B 31.3-2010 工艺管道
380.00
16 ASME B 16.5-2009 管法兰和法兰管件(NPS1/2 至 NPS24 公制/英制标准) 200.00
17 ASME B 31.4-2006 液态烃和其他液体管线输送系统
50.00 60.00 50.00 50.00
96 ASTM A553/A553M-1990 压力容器用淬火和回火的 8%和 9%镍合金钢板
50.00
97 ASTM A612/A612M-1990 中温和低温压力容器用高强度碳素钢板 98 ASTM A645/A645M-1987 压力容器用特殊热处理 5%镍合金钢板
61 ASTM A276-2006 不锈钢棒材和型材标准规范
62
ASTM A278M-2001(2006) 温度达 345℃的压力容器部件用灰口铁铸件(米 制)
63 ASTM A285/A285M-2003 压力容器用中低抗拉强度碳素钢标准技术条件
64 ASTM A299/A299M-1990 压力容器用锰硅碳素钢板
88 ASTM A515-2003 中温及高温压力容器用碳素钢板的标准规范 89 ASTM A516-2004a 中温及低温压力容器用碳素钢板的标准规范 90 ASTM A517/A517M-1990 压力容器用淬火和回火的高强度合金钢板
ASME锅炉和压力容器规范中有关焊接术语定义

ASME锅炉和压力容器规范中有关焊接术语定义Bingyu发表于 2005-6-22 01:19 PMASME锅炉和压力容器规范中有关焊接术语定义QW-492电弧缝焊arc seam weld 采用电弧焊方法焊成的缝形焊缝。
电弧点焊arc spot weld 采用电弧焊方法焊成的点状焊缝。
弧伤 arc strike由于疏忽大意,使电能在完成的焊缝(或母材)表面与焊条或磁探头(电流源)之间通过,从而发生电弧,造成在完成的焊缝(或母材)的外形轮廓上的任何烧伤。
螺柱弧焊 arc stud sweldin g 一种弧焊方法。
此法在金属螺柱(或类似零件)和另一工件之间引发电弧,直至被连接的表面受到适当加热,然后再以压力使两者接合起来。
在螺柱外围加一陶瓷护套,可以获得适当的部分保护。
焊剂或保护气体可用可不用。
电弧焊 arc welding电弧焊是指某一焊接方法群,此焊接方法群是以单弧或多弧加热的办法来实现接合,填充金属可用可不用,外加压力亦可用可不用。
焊态 as-welded焊缝金属、焊接接头和焊件,在焊接后未接受任何后续处理例如热处理、机械处理或化学处理之前的状态。
自动焊 automat ic welding采用施焊时间无需焊接操作工调节控制钮的机器进行的焊接。
这类焊机可以也可以不执行装卸工件的工作,参见机动焊。
背面清根back gouging从一个部分焊接的接头的另一面清除一些焊缝金属和母材,以保证从这一面作后续焊接时能完全焊透。
后焊法 backhan d welding焊炬或焊枪的指向与焊接方向相反的一种焊接技术。
衬垫 backing为了支撑熔化的焊接金属在焊接接头的根部放置一材料。
背面气体 backing gas 采用氩、氦、氮或活性气体之类,从焊接接头根部的背面(与焊接侧相反的一面)排除氧气。
ASME规范案例和焊缝超声检测新规定

标准化ND T无损检测ASME规范案例和焊缝超声检测新规定李 衍(无锡华光锅炉股份有限公司,无锡 214028)摘 要:介绍ASM E规范允许用超声检测取代射线照相对锅炉压力容器焊接接头作无损检测的新规定。
它规定了计算机超声成像法(包括TOFD技术)的应用程序和超声检测工艺规程的验证要求,以及对检出缺陷采用矩形断面界定尺寸的验收法则。
意在为国内锅炉、压力容器、压力管道三类特种设备的无损检测与国际接轨提供借鉴。
关键词:超声检测;规范;缺陷认定;锅炉;压力容器;焊缝 中图分类号:T G115.28 文献标识码:A 文章编号:100026656(2005)022*******ASME Code C ase and N e w Rules of U ltrasonic Examination of Welded JointsL I Yan(Wuxi Huaguang Boiler Co.,L td,Wuxi214028,China)Abstract:The new rules of ASM E code are introduced in which ultrasonic inspection is permitted for nondestructive testing(ND T)of the welded joints in boilers and pressure vessels in lieu of radiography,and the applicable procedure of ultrasonic computerized imaging methods such as TOFD technique and the acceptance criteria of detected flaws based on the bounded rectangular sizes of cross section areas are emphasized.The intention is to provide a reference for the linking2up of ND T techniques of special equipment including boilers,pressure vessels and pipes with international standards.K eyw ords:Ultrasonic testing;Code;Flaw evaluation;Boiler;Pressure vessel;Weld ASM E锅炉压力容器规范(B PVC)原先规定,动力锅炉和压力容器对接接头用射线照相进行无损检测。
ASME 锅炉压力容器规范案例

ASME 锅炉压力容器规范案例批准日期:2005 年10 月27 日ASME 锅炉压力容器标准委员会使标准案例在2005 年3 月11 日生效。
这意味着列入附录的和有关联的所有标准案例都是有效的,除非ASME 锅炉压力容器标准委员会将其废除。
案例2235-8使用第I 卷和第VIII 卷第1 部分和第2 部分超声波替代射线检测问:在什么条件下可以用超声波检测替代射线,并且射线是在按照第I 卷PW-11 章;第VIII 卷,第1 部分,UW-11A(a)章;和第VIII 卷,第2 部分,表AF-241.1 的要求?答:委员会建议材料壁厚大于或等于13mm 的锅炉和压力容器焊缝都可以用超声波(UT)方法代替射线(RT)方法,并要满足以下要求:a) 当材料厚度大于200mm 时,超声波检测区域应包括整个焊缝加焊缝两侧各式各样50mm 的范围。
当材料厚度小于或等于200mm 时,超声波检测区域应包括整个焊缝加上焊缝两侧各25mm或材料厚度t,两者取小较小值。
或者,检测区可减小到焊缝加上焊缝两侧实际热影响区(HAZ)再加6mm,并满足以下要求:1)焊缝热影响区HAZ 经实际测量,并有焊接工艺记录。
2)超声探头位置和扫查装置用参考标记(沿着焊缝的油漆或浅的钢印)控制,以确保实际HAZ 和附加的6mm 母材能被检测到。
b) 应有书面检测方案或扫查计划展示探头位置、探头移动、和声束覆盖,并提供标准的和可重复的检测方法。
扫查计划还应包括所选择的相对于焊缝中心线的声束角度、声束方向,包括对容器的所有焊缝。
c) 超声检测应按照第V 卷,第4 章(注1)的要求提供书面检测程序。
检测程序应是在被认可的试块上经过演示,被认为是可以接受的。
试块应是焊接试块或(HIP)并应含有至少三个缺陷,倾向于模仿平行于焊缝熔合线的缺陷:1)试块一侧的表面缺陷代表容器的外表面缺陷;2)试块另一侧的表面缺陷代表容器的内表面;3)一个埋藏性缺陷;4)如果试块可以翻转,则一个表面缺陷可以代表容器的内表面和外表面的缺陷,那么可以只要求两个缺陷。
- 1、下载文档前请自行甄别文档内容的完整性,平台不提供额外的编辑、内容补充、找答案等附加服务。
- 2、"仅部分预览"的文档,不可在线预览部分如存在完整性等问题,可反馈申请退款(可完整预览的文档不适用该条件!)。
- 3、如文档侵犯您的权益,请联系客服反馈,我们会尽快为您处理(人工客服工作时间:9:00-18:30)。
1(b)图的2d)的一半,则应作为表面缺陷。
2) 几何因素几何因素和冶金缺陷超声指示按下述方法分类: (a) 表面结构(如焊缝余高或根部结构)或材料各种冶金结构(如夹层)引起
的指示,分类为几何结构指示,将 (1) 不需按照(i)(3)确定缺陷形状或定量; (2) 不需对比表1、2、或3 的验收规范进行评定; (3) 缺陷指示的最大波幅和位置应记录,例如,内部附件,最大幅度
200%DAC,高于焊缝中心线25mm,在内表面,斜度90 到95 度。 (b) 几何结构指示按下述方法分类:
(1) 按照检测程序解释含缺陷的区域 (2) 分区域评定缺陷,提供截面图显示反射体的位置和表面的不连续如
根部缺陷或沉孔。 (3) 审查安装或焊接图纸。 (c) 或者采用其它NDE 方法或技术,对几何结构指示进行分类(如UT 斜探头
制,以确保实际HAZ 和附加的6mm 母材能被检测到。 b) 应有书面检测方案或扫查计划展示探头位置、探头移动、和声束覆盖,并提 供标准的和可重复的检测方法。扫查计划还应包括所选择的相对于焊缝中心线的 声束角度、声束方向,包括对容器的所有焊缝。 c) 超声检测应按照第V 卷,第4 章(注1)的要求提供书面检测程序。检测程序 应是在被认可的试块上经过演示,被认为是可以接受的。试块应是焊接试块或 (HIP)并应含有至少三个缺陷,倾向于模仿平行于焊缝熔合线的缺陷:
5mm 时,都应记录。 (3) 对于厚度大于100mm 的焊缝,当指示影像长度大于0.05t 或19mm
时,两者取较小值,都应记录(t=焊缝熔合线处的公称厚度)。
表 2 焊缝厚度从25mm 到300mm 的缺陷验收规范
25mm≤t≤64mm(见注1)
表观比率 a/l
表面缺陷 a/t
埋藏缺陷 a/t
100mm≤t≤300mm(见注1)
c) 埋藏性缺陷 缺陷长度不得超过4t。
(c)埋藏缺陷显示 图1 信号显示
j) 最终的数据包应经UT III 级人员审核。审核内容包括: 1) 超声数据记录 2) 数据解释 3) 经另外的II 级或III 级资格人员评定/定性的结果。数据审核可由同 一组织的另一名人员表面缺陷显示完成。 另外,审核可以由具有按上述(f)和(h)条规定的II 级人员进行数据 整理和初评,最终的审核应由III 给人员进行。III 级人员有按上述 (f)条考核的资格,包括试块中缺陷的检测经验。
表 32 焊缝厚度大于300mm 的缺陷验收规范
表面缺陷 a
埋藏缺陷a
a/l 0.00 0.05 0.10 0.15 0.20 0.25 0.30 0.35 0.40 0.45 0.50
in 0.228 0.240 0.264 0.300 0.336 0.396 0.456 0.528 0.612 0.618 0.624
注: (a) 对于缺陷表观率a/l 处于其它值时,可以采用内插法。 (b) t=包括所有允许余高的焊缝厚度。对于有不同厚度的对接焊缝,t 取这 两个厚度的较小值。如果全焊透的焊缝含有角焊缝,则角焊缝的厚度也 应在包括在t 中。 (c) 如果埋藏缺陷到表面的距离(图1 的S)小于或等于厚度方向尺寸(图
表观比率 mm
5.79 6.10 6.71 7.62 8.53 10.1 11.6 13.4 15.5 15.7 15.9
in 0.240 0.264 0.300 0.348 0.396 0.456 0.528 0.612 0.696 0.804 0.912
mm 6.10 6.71 7.62 8.84 10.1 11.6 13.4 15.5 17.7 20.4 23.6
图3 b) 程序规范
1)涡流检测程序应规定下列有关数据: (a) 仪器或系统,包括制造商名称和型号 (b) 探头尺寸和型号,包括包括制造商名称和编号 (c)类似电缆型号和长度 (d) 检测频率、或所用的最大与最小频率范围 (e) 线圈激励模式(即绝对的或微分式的) (f) 需要记录的最小数据 (h) 最低采样率或最大扫查速度 (i) 扫描路线图,如有可能(即扫查方向、扫查线性,长度、扫查线或覆 盖率) (j) 磁偏技术,如有可能 (k) 材料类型 (l) 涂层类型和厚度,如有可能
ASME 锅炉压力容器规范案例
批准日期:2005 年10 月27 日 ASME 锅炉压力容器标准委员会使标准案例在2005 年3 月11 日生效。这意 味着列入附录的和有关联的所有标准案例都是有效的,除非ASME 锅炉压力容器 标准委员会将其废除。 案例2235-8使用第I 卷和第VIII 卷第1 部分和第2 部分超声波替代射线 检测 问:在什么条件下可以用超声波检测替代射线,并且射线是在按照第I 卷PW-11 章;第VIII 卷,第1 部分,UW-11A(a)章;和第VIII 卷,第2 部分,表AF-241.1 的要求? 答:委员会建议材料壁厚大于或等于13mm 的锅炉和压力容器焊缝都可以用超声 波(UT)方法代 替射线(RT)方法,并要满足以下要求: a) 当材料厚度大于200mm 时,超声波检测区域应包括整个焊缝加焊缝两侧各式 各样50mm 的范围。当材料厚度小于或等于200mm 时,超声波检测区域应包括 整个焊缝加上焊缝两侧各25mm或材料厚度t,两者取小较小值。或者,检测区 可减小到焊缝加上焊缝两侧实际热影响区(HAZ)再加6mm,并满足以下要求: 1) 焊缝热影响区HAZ 经实际测量,并有焊接工艺记录。 2) 超声探头位置和扫查装置用参考标记(沿着焊缝的油漆或浅的钢印)控
a) 表面连续性缺陷 在超声检测中被判定为是表面缺陷的,可能是,也可能不 是表面连续性缺陷。因此,除非UT 数据能够认定该缺陷不是表面连续性缺 陷,该缺陷应被看作表面连续性缺陷或开口缺陷,并且是拒收的除非经过 下述(1)、(2)或(3)进行了表面检测。如果该缺陷是表面连续性缺陷,上 述要求仍然适用;然而,无论如何缺陷都不得超过规范所规定的参数。
f) 操作和评定人员的经验应经雇主在ANST SNT-TC-1A 或CP-189 的指导下考核 和认证。只有II 级或III 级人员才可对数据进行分析或 对结果进行解释。
表1 焊缝厚度从13mm 到25mm 的缺陷验收规范2
a/t
l
表面缺陷 ≤0.087 ≤6.4mm
Байду номын сангаас
埋藏缺陷 ≤0.143 ≤6.4mm
b) 多个缺陷 (1) 不连续的缺陷当在缺陷连线上间距小于或等于图2 所示的S 时应作为 单个平面缺陷。 (2) 不连续的平面缺陷当其间距小于或等于13mm(指按图3)时,应作为单 平面缺陷。 (3) 在同一个平面上的不连续的缺陷,和在试件厚度方向上不连续的缺 陷,当按图4 其间距小于或等于S 时,应作为单个平面缺陷。 (4)在厚度方向上的平面缺陷分别在两个平行的平面上间距不大于13mm 时,如果缺陷深度方向上超过图5 所示的尺寸时,该缺陷拒收。
注: (a)t=包括任何允许的焊缝余高的焊缝厚度。
对于对接接头,当焊缝两侧厚度不同时,取较小值。如果全熔透的焊缝 中含有角焊缝,则角焊缝的厚度也应包括在t 中。 (b)如果埋藏缺陷到表面的距离(图1 的S)小于或等于厚度方向尺寸(图 1(b)图的2d)的一半,则应作为表面缺陷。 g) 承包商的资格认证记录应经过雇主的证书持有者批准。 h) 另外,获得和分析UT 数据的人员也应经上述第<d>条规定的内容进行仪器培 训,并参加按第<c>条进行的演示。 i) 数据分析验收规范应按述方法: 1) 数据分析规范反射体超过下述(a)或(b),都应调查确定信号指示是缺陷 或是(i)(2)条所述的几何结构。如果是缺陷,则按(i)(4)条缺陷评定和验收规范 进行评定。 (a) 对于以波幅为基准的检测技术,超过参考线20%的所有缺陷都应测量
缺陷位置、幅度和延伸长度。 (b) 对于非基于波幅的检测技术,所有缺陷图像指示超过下述(1)、(2)、
或(3)时,缺陷的位置和延伸长度都应测量。 (1) 对于材料厚度小于或等于38mm 的焊缝,当指示影像长度大于
3.8mm 时,都应记录。 (2) 对于厚度大于38mm 而小于100mm 的焊缝,当指示影像长度大于
1) 试块一侧的表面缺陷代表容器的外表面缺陷; 2) 试块另一侧的表面缺陷代表容器的内表面; 3) 一个埋藏性缺陷; 4) 如果试块可以翻转,则一个表面缺陷可以代表容器的内表面和外表面的
缺陷,那么可以只要求两个缺陷。 对于每种被检厚度,试块中的缺陷尺寸不得大于表1、2 或表3 中的规定。 可接受的操作是从最大允许缺陷或别的相关缺陷不超过参考水平。或者,对于不 用记录幅度时,可接受的操作是演示所有缺陷图象都有可记录的长度,包括最大 允许缺陷,其指示长度大于或等于试块中缺陷的实际长度。 d) 超声检测应使用基于能够自动记录数据的计算机,最初的直探头母材检测(第 V 卷第4 章T-472)对于干扰斜探头检测的反射体应按下列方法操作: 1)手工方法; 2)局部预处理; 3)自动超声检测时这些反射体都能被显示<第(c)条>。 e) 数据应是未经加工的原始记录数据。完整的数据应没有闸门、滤波或阈值, 上述第(a)条所述的范围的缺陷也应包含在数据记录中。
0.019 0.020 0.022 0.025 0.028 0.033 0.038 0.044 0.050 0.051 0.052
0.020 0.022 0.025 0.029
0.033 0.038 0.044 0.051 0.058 0.067 0.076
注: (a) t=包括所有允许余高的焊缝厚度。对于有不同厚度的对接焊缝,t 取这两 个厚度的较小值。如果全焊透的焊缝含有角焊缝,则角焊缝的厚度也应在包括在 t 中。 (b) 如果埋藏缺陷到表面的距离(图1 的S)小于或等于厚度方向尺寸(图1(b) 图的2d)的一半,则应作为表面缺陷。 (c) 如果验收规范表中缺陷长度l 小于6.4mm,则记为6.4mm。 注 1:对于缺陷表观率a/l 处于其它值以及厚度处于6.4mm<t<100mm 时,可以 采用内插法。