国内外吨钢综合能耗、可比能耗和工序能耗比较
国内外钢铁企业能耗统计

表1 2007年统计数据(数据来源:中国钢铁工业协会)2008年8月13日项目单位全国先进水平国际先进水平 全国平均水平备注吨钢综合能耗 kg 标煤 562.92632.18● 宝钢的吨钢综合能耗已达到世界先进国家水平。
● 2006年宝钢分公司吨钢综合能耗为686千克标煤,居世界先进水平,比全国重点大中钢铁企业吨钢综合能耗低10%左右。
吨钢可比能耗 kg 标煤 521612.27 ● 2004年工业发达国家平均水平为642,我国比该值高16.72%。
● 2006年高出15%吨钢电耗量kW.h410.6450.13吨钢新水耗量 m3 3.25.31 2003年,国外钢铁企业吨钢耗新水的先进值是:日本扇岛 2.1,阿赛洛 2.4,蒂森·克虏伯 2.6,韩国浦项 3.5,光阳3.6,美国凯泽公司方塔那4. 1 焦炉煤气放散率 % 1.24 2.79 据报道:目前,宝钢分公司高炉煤气放散率小于 1.5%,吨钢转炉煤气回收量99标准立方米,焦炉煤气保持零放散高炉煤气放散率 % 1.94 9.99 吨钢转炉煤气回收量m3(标)11163焦化工序能耗kg标煤/t 84.6 123.11 烧结工序能耗kg标煤/t 44.88 55.21球团工序能耗kg标煤/t 据世界金属报道:●2004年国内重点大中型钢铁企业平均值42,先进值19.22。
●2006年国内重点大中型钢铁企业平均值33.08炼铁工序能耗kg标煤/t 357.42 428.84 转炉炼钢工序能耗kg标煤/t -16.51 6.03 轧钢中型材工序能耗kg标煤/t 37.53 61.22 轧钢小型材工序能耗kg标煤/t 31.66 49.89 轧钢线材工序能耗kg标煤/t 41.13 58.31 热轧宽带工序能耗kg标煤/t 24.23 55.31 冷轧宽带工序能耗kg标煤/t 40.28 61.88 中宽厚板工序能耗kg标煤/t 53 69.48硅钢工序能耗kg标煤/t表2 国内先进水平与国际先进水平相比(2006年)数据来源:中国钢铁工业协会。
3能耗指标体系的分类计算

能耗指标体系的分类钢铁企业能耗指标主要有吨钢综合能耗、吨钢可比能耗、主要产品的工序能耗、主要产品的实物单耗(如炼铁焦比、炼焦煤耗等)以及产值能耗、增加值能耗等等。
能源分析评价指标中,包括企业内部能源加工转换指标和企业损失指标。
按钢铁企业能耗经济技术指标体系可分为:(1)企业级能源技术经济指标:如吨钢综合能耗、万元产值能耗、吨钢耗新水、吨钢电耗、损失率等。
(2)工序级能源技术经济指标:如炼钢工序能耗、炼铁工序能耗等。
(3)耗能设备级能源技术经济指标:加热炉燃耗、高炉焦比、制氧机电耗等。
按钢铁企业能效对标指南中能耗指标体系可分为:(1)综合性指标:如企业级能源消耗总量、工序级能源消耗总量、各类能源介质消耗总量、企业能源亏损量等指标。
(2)单耗性指标:如吨钢综合能耗、企业吨钢可比能耗、工序单位产品能耗。
(3)经济性指标:万元产值能耗、万元增加值能耗等。
2.能耗指标的范围及计算钢铁制造流程是由多个不同的生产工序组成的,前一道工序的产品为下一道工序的原料,这是钢铁工业的特点,由于其复杂性,因此,统计范围和指标定义必须规范,以便于对标,找出节能潜力,提升企业效益。
(1)吨钢综合能耗范围及计算综合能耗是规定的耗能体系在一段时间内实际消耗的各种能源实物量按规定的计算方法和单位分别折算为标准煤后的总和。
吨钢综合能耗(comprehensive energy consumption ):吨钢综合能耗是企业生产每吨粗钢所综合消耗的各种能源自耗总量;也就是每生产一吨钢,企业消耗的净能源量。
其计算公式为:吨钢综合能耗=企业钢产量企业自耗能源量(吨标准煤/吨钢,千克标准煤/吨;tce/t ,kgce/t )式中,企业自耗能源量即报告期内企业自耗的全部能源量。
统计上报按企业全部耗能量。
企业自耗能源量= 企业购入能源量 ± 库存能源增减量 - 外销能源量= 企业各部位耗能量之和 + 企业能源亏损量作为行业对标,吨钢综合能耗的统计范围可按照企业生产流程的主体生产工序(包括原料储存、焦化、烧结、球团、炼铁、炼钢、连铸、轧钢、自备电厂、制氧等动力厂)、厂内运输、燃料加工及输送、企业亏损等消耗能源总量,不包括矿石的采、选工序,也不包含炭素、耐火材料、机修、石灰、精制及铁合金等非钢生产工序的能源消耗量。
钢铁行业单位产品能耗限额标准

钢铁行业单位产品能耗限额标准
钢铁行业的单位产品能耗限额标准因不同的产品种类和生产工艺而有所不同。
在中国,针对钢铁行业,国家制定了相应的能耗限额标准,其中包括了不同的产品种类的能耗限额标准。
以下是一些常见的钢铁产品能耗限额标准:
1. 转炉钢吨钢综合能耗:≤ /t;
2. 电炉钢吨钢综合能耗:≤ /t;
3. 轧钢综合能耗:≤ /t;
4. 高炉炼铁工序单位产品能耗:≤ 437kgce/t;
5. 转炉炼钢工序单位产品能耗:≤ 122kgce/t;
6. 电炉炼钢工序单位产品能耗:≤ 120kgce/t;
7. 烧结工序单位产品能耗:≤ /t;
8. 球团工序单位产品能耗:≤ /t。
需要注意的是,这些标准是针对不同的钢铁产品种类和生产工艺而制定的,而且随着技术的不断进步和环保要求的提高,这些标准也在不断更新和调整。
因此,在实际生产中,钢铁企业需要按照最新的标准进行节能降耗,以实现可持续发展。
国内外钢铁成本分析

国内外钢铁成本分析作为基础原材料,钢铁产品的价格竞争是最重要的竞争要素之一.成本是价格竞争基础.在钢铁工业技术进步史上,很多重大技术突破,例如直接还原铁、转炉炼钢、连铸、连轧、薄板坯连铸连轧、高炉喷煤等,首要动因是降低成本.“成本优先战略”过去是,今后相当长时期仍将是钢铁工业的首选经营战略.成本高低与工艺、技术和管理水平有关,它们是企业“可以改变的竞争要素”.通过成本对比分析,便于发现钢铁企业在这些方面的潜力所在,促使企业通过技术进步和改善管理,挖掘成本潜力.从长期看,工艺、技术和管理的差异将随着企业间技术和管理的交流趋于消失.长期的成本竞争力最终取决于钢铁企业所处的外部环境,如原料、能源、人力成本、资金成本及市场等.这些因素通常属于“不可改变的竞争要素”.在市场经济条件下,不可改变的竞争要素是影响生产力布局的主要因素.我国钢铁生产能力逐步向沿海、原料产地和市场广阔的地区集中,正是这种作用的体现.随着经济全球化的发展,“不可改变的竞争要素”将成为影响国际分工的重要因素.因此,开展成本竞争研究,不仅对促进企业短期内降低成本具有重要意义,而且对制定我国钢铁工业长远发展战略和提高我国钢铁企业国际竞争力水平具有重要的参考价值.表1 2004年中外钢铁产品要素成本结构比较项目中国平均比例国外平均长流程比例国外平均全部比例销售价格100100100注:表中的“长流程”为转炉钢的比例在国外钢铁企业平均水平72%之上的企业合计.表2 2004年与2003年单位要素成本变化率比较表3 2004年国外分地区要素成本第一部分单位发货量要素成本对比分析一、中外钢铁企业单位发货量要素成本比较本期成本对比的国外企业共250家,中国钢铁企业为我国主要大中型钢铁企业.由于成本核算方法的差异,我国的成本数据结构与国外厂家有所不同.为了可比起见,我们对我国的成本数据按国外的结构和口径调整为“要素成本”.2004年上半年国外钢材平均售价长流程比国内高出美元/吨,这比2003年国内外钢材综合售价之差美元/吨又有所扩大,说明国外钢材市场涨价幅度高于国内.国内2004年的原材料成本,由2003年低于国外长流程美元/吨变为高于国外美元/吨,说明国内矿价和进口铁矿石价格的上涨幅度高于国外平均涨价幅度.2004年上半年,国内钢材能源成本高于国外美元/吨,2003年下半年为美元/吨,成本差距又有所拉大,说明国内能耗情况尚未得到改善,而且涨价幅度也高于国外.税前利润发生了逆转,由2003年下半年的我国高于国外长流程美元/吨,逆转为2004年上半年国外高于我国美元/吨.说明国外钢材涨价幅度较大,而原材料和能源涨价幅度相对较小.国外企业从而一举扭转了2003年普遍微利或亏损局面,国外全部长短流程企业的情况也大致如此.我国在人力及管理费用和资本成本方面仍保持一定的优势.从国家看,2004年钢材价格最高的国家依然是美国,其次是日本、欧盟国家,由于钢材价格上涨,而钢铁成本保持比较稳定,美、日、欧钢铁行业都出现较大盈利;韩国由于在能源、人力及管理费用、资本成本方面都有一些优势,所以为税前利润最高国家.2004年中国大型企业平均税前利润处于平均偏高水平具体原因见后面“影响要素成本的主要因素分析”.从税前利润方面看,台湾中钢公司、韩国浦项公司为最高,分别达到130美元/吨和110美元/吨,中钢公司主要是原材料成本较低,浦项公司主要在能源、劳力及管理费用和资本成本方面有一定的综合优势.2004年,中国大型钢铁企业在原材料成本方面较2003年有较大增加,所以税前利润在世界主要钢铁企业中处于较低水平.二、影响要素成本的主要因素分析1、原料成本2004年初以来炼铁原料的价格暴涨是全球性的,但由于国外主要钢铁生产厂家采购铁矿石大都采取长期和约方式,一定程度上延缓了涨价的影响.从表2可以看出,国外单位发货炼中原材料成本比2003年升高%.而我国同期原材料成本却上升%.其中精矿粉采购价格暴涨起了决定性作用,也是推动钢材成本大幅度升高的主要原因之一.之所以我国钢材的原料成本没有与精矿粉采购价格同幅度上升,是由于我国自产矿石尚占消耗量的50%以上.这说明保有较大比例的自产矿石,是缓冲国际矿石价格上涨冲击的重要因素.我国与俄罗斯、南美等铁矿石资源丰富、品质优越的国家和地区相比有天然的劣势,但与北美、欧洲、日本、韩国等铁矿石基本依赖进口的产钢国和地区相比又有一定优势.北美、欧洲、中东、亚洲其他国家单位发货量中的原料成本高于我国.在表1中,国外全部包含长短流程的原料成本高于我国,其主要原因而二:一是工艺结构不同,电炉钢的原料成本所占比例明显高于转炉工艺.我国所选企业都是长流程企业,消耗的原料主要是烧结用矿粉和块粉;而国外企业转炉钢和平炉钢前苏联和印度合计占%,电炉钢占%;二是高炉入炉原料结构不同,国外企业高炉入炉原料中球团的比例近30%,球团矿外购的比例通常比较大,而我国企业入炉烧结矿占四分之三,烧结矿基本都是自产的,入炉球团比例只有%.表4 2003年世界炼钢生产结构国家地区世界美国日本欧盟15国中国转炉钢比%电炉钢比%平炉钢比%0000表5 2003年中外高炉入炉料结构烧结矿球团块矿国外企业平均%中国49家企业平均%2、能源成本我国能源成本约比国外平均数高%.2004年我国精煤采购成本为美元/吨,比上年同期上涨了%,原煤、无烟煤也都比上年同期有30%左右的上涨.与国外能源价格比较,我国炼焦煤价格与国外相比没有明显优势.但我国焦炭价格明显低于国外水平.2003年我国焦炭产量亿吨,其中出口1472万吨,出口量占世界贸易量的%.我国焦炭出口价加上海陆运费,使得国外焦炭采购成本明显高于我国.而我国企业焦炭采购价格中,有的企业属于向本集团焦化厂采购的价格,并非完全市场价,这也是焦炭采购成本较低的原因之一.总体上衡量,我国能源价格略低于国外平均数.我国整体上讲属于能源生产大国,与我国周边主要竞争对手相比,这是我国钢铁工业发展的有利因素之一.但表现在钢材成本上,我国能源成本高于国外,其主要原因是单位产品能耗较高.尽管近些年来我国钢铁企业在节能方面取得很大成效,但与国外先进产钢国之间仍存在20%左右的差距.表6 我国钢铁工业可比能耗与国际先进水平的比较单位:kg/t国家1980年1990年2000年英国783670663日本653592620德国752656602法国820687683美国868673--先进国家平均642中国12851017781差距139差距比例%3、人工成本人工成本低是我国也是其他发展中国家的一大优势,也是包括钢铁业在内的制造业由发达国家向发展中国家转移的重要原因之一.尽管我国的实物劳动生产率与发达国家存在很大的差距,不到世界先进水平的五分之一,但单位工时成本主要是人均收入水平的差距更大,约为十五至二十分之一.因此,我国吨发货量中的人力成本约为发达国家的三分之一,国外平均数的二分之一.随着我国经济发展和人民生活水平的提高,钢铁工业在劳动生产率提高的同时,人均收入也相应提高,工资收入占销售收入的比例略有下降.4、折旧从表1中的数据看,我国企业单位发货量实现收入中折旧的比例与国外企业基本相同.5、利息我国单位发货量负担利息财务费用明显低于国外,与我国利率下调、资产负债率降低及有息负债须支付利息的贷款及债券比例较小有关.表7 我国重点企业工序能耗与国际先进水平比较单位:kg/t表8 2003年人力成本的国际比较表9 中国钢铁企业人力成本情况的变化表10 中国钢铁有关负债及财务费用的变化三、产品销售盈利状况及对钢铁分布的影响盈亏状况是竞争能力强弱的直接表现,它最终会影响到钢铁生产的布局.这一关系可以从2003年全球钢铁行业盈亏分布情况及10年来世界钢铁生产布局的变化看出来.钢铁行业是资本密集型产业,这决定了它的进入和退出门坎都比较高,因此盈亏状况对布局的影响关系只能在长期内才能发挥作用.因此,虽然2004年全球钢铁行业盈利情况全面好转,主要产钢国和地区的盈利水平甚至超过了我国,但这种情况是不是暂时的现象,会不会对钢铁产业布局产生影响,还有待于进一步观察.1、部分地区和国家盈亏状况见表11表11 2003年-2004年部分地区和国家吨发货量盈亏状况单位:美元/吨2、全球1993-2003年粗钢产量变化2004年中国的粗钢产量占世界的%,比2003年又提高了个百分点.第二部分:分环节、品种、流程的运营成本和完全成本对比一、生铁成本2004年我国大中型钢铁企业铁的平均制造成本,处于国际最高水平.可以看出:2004年2003年相比,非洲、独联体、欧洲铁成本都有20%以上增幅,中东地区增幅最小,为%,而中国大陆铁成本平均增长%,为增幅最高的地区.国家炼铁成本比较中,中国处于成本最高水平.世界主要钢铁企业铁成本比较中,中国企业处于成本最高水平.二、钢坯成本1、板坯成本2004年我国板坯平均制造成本,大陆处于世界平均水平.可以看出,我国板坯成本2004年比2003年的增幅处于世界平均增幅偏高水平.2、方坯成本2004年我国大中型钢铁企业方坯平均制造成本,处于较低水平.可以看出,我国方坯成本2004年比2003年增幅,处于世界较低水平.三、扁平材成本1、热轧薄板成本2004年我国大中型钢铁企业热轧薄板平均制造成本,处于世界较低水平.可以看出,我国热轧薄板成本2004年比2003年的增幅为%,处于世界平均水平.2、冷轧薄板成本2004年我国大中型钢铁企业冷轧薄板平均制造成本,处于世界较低水平.可以看出,我国冷轧薄板成本2004年比2003年的增幅为%,与世界其它地区相比,增幅处于较高水平,仅比中东地区低.3、中厚板成本2004年我国大中型钢铁企业中厚板平均制造成本,处于世界较低水平.我国中厚板成本2004年比2003年的增幅为%,与世界其它地区相比,增幅处于较高水平,仅比独联体地区增幅低.四、长材成本1、棒材成本2004年我国大中型钢铁企业棒材平均制造成本,处于世界较低水平.我国棒材成本2004年比2003年的增幅为%,与世界其它地区相比,增幅处于较高水平,仅比中东地区和欧洲增幅低.2、线材成本2004年我国大中型钢铁企业线材平均制造成本,处于世界较低水平.我国线材成本2004年比2003年的增幅为%,与世界其它地区相比,增幅处于中等水平.3、型材成本2004年我国大中型钢铁企业型材平均制造成本,处于世界较低水平.我国型材成本2004年比2003年的增幅为%,与世界其它地区相比,增幅处于较高水平.五、长短流程成本比较1、不同流程下热轧板卷成本比较2004年美、日、欧洲的长流程成本均低于短流程,因此三地区的长流程产量占了较大比重.2、不同流程下热轧棒材成本比较三个国家地区采用短流程生产棒材均有明显的成本优势,故短流程棒材产量比例均比较高.线材、型材等长材的成本和产量结构与棒材的情况基本相同.从上述三个国家地区长短流程结构可以得出一个共同的结论:短流程生产卷板没有成本优势,而生产长材有成本优势.其原因与长短流程的合理规模及合理运输半径有关:在废钢资源比较充足的发达国家和地区,用年产钢40-50万吨的电炉生产厂生产低附加值的线材供应周边地区,具有运距短、交易成本低的优势.而用电炉工艺生产连轧卷板,需要较大的生产规模,例如CSP单流年产量约100万吨,将受到废钢原料运输半径的制约.中国钢铁工业协会财务资产部/冶金工业经济发展研究中心课题组。
吨钢可比能耗计算

吨钢可比能耗计算
先计算出吨钢在各工序的耗能量,再∑
吨钢可比能耗=∑(各工序上方数*下方数)+吨钢辅助工序及亏损耗能
1、工序上方红色数据:表示吨钢所耗钢前各工序的产品量或所产出钢后工序的产品量,即相当于以吨钢计算的物流;工序下方绿色数据:表示吨钢在该工序所耗能量,即各工序的吨钢能耗。
即1.45*54.9+0.99*415.30+1*(-7.68)+0.97*42.94=524.73kgce/t
2、吨钢辅助工序及亏损耗能:
亏损耗能:燃料加工与运输、机车运输、企业能源亏损。
⑴2012年高炉煤气放散率11.66%,氧气放散率
22.32%,氮气放散率21.5%,柴油914.36吨。
(11.66%*12412万m3*0.11+22.32%*15978万m3*0.062+21.5%*19854万m3*0.033+914.36*1.4571)/钢产量=24.53+1.77+1.13+1.07=28.5kgce/t
⑵辅助工序(石灰工序+矿渣粉工序+动力工序)即:
(石灰工序总能耗+矿渣粉工序总能耗+动力工序总能
耗)/钢产量
=(21991.57+8873.03+11201.96+296.03)/1245391*1000
34.01kgce/t
3、综合上述:2012年企业吨钢可比能耗524.73+28.5+34.01=587.24kgce/t。
2009年有限公司吨钢可比能耗541 kgce/t、2008年559 kgce/t、2007年544 kgce/t。
钢铁企业工序能耗和节能潜力

钢铁企业工序能耗和节能潜力近年来,我国重点钢铁企业的钢、铁产量增长在16%以上,而总能耗的增长低于产量增长约5个百分点。
这说明,我国重点钢铁企业在节约能源方面做出很大成绩。
一、重点钢铁企业工序能耗情况1.近3年我国重点钢铁企业各工序能耗变化情况见表1。
从中可看出,各工序能耗中球团、转炉炼钢和焦化工序能耗呈上升态势,而烧结、电炉、轧钢工序均呈下降态势。
2.2004年各工序能耗与1999年国际先进水平相比,烧结工序差距最小,为7.49kgce/t;差距最大的是转炉炼钢工序,差值为35.45kgce/t,其次为炼铁工序,差值为28.27kgce/t。
2000年国外主要产钢国家(英、日、法、德)平均吨钢可比能耗为642kgce。
2004年我国重点钢铁企业平均吨钢可比能耗为705kgce/t,与国外主要产钢国家相比高出9.81%。
二、2004年重点钢铁企业各工序能耗分析表3列出我国重点钢铁企业各工序能耗数值、各工序能耗占钢铁工业总能耗的比例、企业先进与落后值。
表1 重点钢铁企业工序能耗单位:kgce/t1.炼铁系统(炼、球、焦、铁)的工序能耗占钢铁工业总能耗的69.41%,是钢铁工业的能耗大户。
由于能耗高,生产过程中所排放的C02、S02、NOx等物质也必然多,因此,炼铁系统是一个重要污染源。
从节能和环保的角度出发,炼铁系统应当完成钢铁工业的节能降耗、减少外排有害气体的重任。
2.动力系统是仅次于炼铁系统的第二个能耗大户。
从表3可看出,动力系统能耗占钢铁工业总能耗的15%,仅次于炼铁工序能耗。
分解动力系统能耗构成是:高炉鼓风和压缩空气用能约55~60kgce/t,制氧约30~40kgce/t,蒸汽和煤气管网运行约25~28kgce/t,发电和输电约30~37kgce/t。
所以各钢铁企业应当重视动力系统的节能工作。
三、钢铁工业节能潜力据统计分析,国内外钢铁企业生产过程中可回收利用的余压、余热、余能的总量,一般占本企业总能量的15%左右。
钢铁工业重要能源消耗指标参考表(行业平均值、国际先进值)

钢加工 热轧 冷轧 镀涂 钢丝 铁合金 耐材 工序能耗(kgce/t) 90.07 81.30 120.10 71.79 101.1 1703.16 164.32 电耗(千瓦时/吨) 99.32 82.80 165.30 115.61 310.1 4514.4 123.07 工序水耗 20.33 17.60 27.46 12.3 48.18 46.22 11.66 耗新水 2.02 1.81 1.53 0.5 12.28 4.78 8.80 备注:数据来源于2005年钢铁工业统计年报(中国钢铁工业协会信息统计部)
吨刚综合能耗:741kgce/t 吨刚可比能耗:714kgce/t 2005年全国重点归钢铁企业工序能耗、水耗 采矿 工序能耗(kgce/t) 电耗(千瓦时/吨) 工序水耗 耗新水 露天 1.11 1.39 地下 7.59 14.89 选矿 14.59 29.61 6.97 1.02 焦化 142.21 33.5 58.0 3.0 烧结 65.09 36.64 0.54 0.26 球团 39.62 34.62 1.44 0.48 炼铁 440.6 66.65 34.48 1.19
2005年全国重点钢铁企业及国际各工序能耗情况(等价值) 吨钢综 合能耗 吨钢可比 能耗 烧结 球团 焦化 炼铁 转炉
Kgce/t Kgce/t
行业平均值 韩国光阳 德国蒂森 国际先进 747.05 714.12 711.9
Kgce/t Kgce/t Kgce/t Kgce/t Kgce/t
64.83 57.4 58 51 40.5 142.21 131.9 75.1 95 456.79 441.1 426 438 36.34 -2.3 -4.5 -8.8
655
炼钢 49.43 76.93 15.35 1.66
国内外吨钢综合能耗、可比能耗和工序能耗比较

内外吨钢综合能耗、可比能耗和工序能耗比较钢铁工业是国民经济重要的基础原材料工业,也是高耗能、高污染工业。
钢铁工业节约潜力巨大,为此,国外大型钢铁企业纷纷采取先进技术,开展节能降耗和综合利用,发展循环经济,不断优化工业的能耗指标和环保指标,以期达到能耗最少,环保最优。
与国外发达水平相比,我国钢铁工业差距明显。
2004年,我国大中型钢铁企业吨钢综合能耗为761千克标煤,比国际先进水平高81千克标煤;吨钢耗新水11. 15m3,比国际先进水平高 7. 3m:,;固体废物综合利用率乩比国际先进水平低个百分点。
在此,以我国大中型钢铁企业的相关指标与国外发达水平作对比,目的是寻找差距,迎头赶上。
下表列出了2003年我国重点企业主要工序能耗与国际先进水平(1999年)的比较,数据表明,我国转炉工序能耗与国外先进水平差值最大,炼铁工序差值最小。
2003年我国钢铁工业吨钢综合能耗为770kgce,吨钢可比能耗698kgce;2003年日本钢铁工业吨钢综合能耗为656kgce, 2000年国外主要产钢国家(英、日、法、徳)平均吨钢可比能耗为642kgce。
这两项指标分别比国外先进水平高出%和觥在国外,先进企业的高炉焦比已达到300kg/t以下,燃料比小于500kg/to我国重点钢铁企业的入炉焦比为426kg/t,部分其它企业为488kg/t,燃料比为560kg/t左右。
高炉工艺的能耗(标媒)比世界先进水平高出50〜 100kg/to同时,我国重点企业之间主要工序能耗的差距很大,指标先进的(如宝钢集团)已达到或超过国际先进水平, 而落后的能耗要高出先进值的1倍或数倍。
这说明,我国钢铁工业节能的潜力还是很大的。
新制订的《钢铁产业发展政策》明确提出,要建立循环型钢铁工厂,500万吨以上规模钢铁联合企业,要努力做到电力自供有余,实现外供。
2005年,全行业吨钢综合能耗降到吨标煤、吨钢可比能耗吨标煤、吨钢耗新水12吨以下;2010年分别降到吨标煤、吨标煤、8吨以下;2020年分别降到吨标煤、吨标煤、6吨以下。
2023年我国钢铁行业能源消耗评述

2023年我国钢铁行业能源消耗评述重点统计企业吨钢综合能耗551.36kgce∕t目录1 .前言 (1)2 .能源消耗情况 (1)2.1.基本情况 (1)2.2.各工序能耗现状 (2)2.2.1.烧结工序 (2)2.2. 2.焦化工序 (3)2.2. 3.球团工序 (3)2.2. 4.炼铁工序 (4)3.结构节能情况 (4)1 .前言2023年我国钢铁行业处于需求减弱、价格下跌、成本上涨、利润下滑的态势;受行业限产、环保要求高等因素的影响,粗钢、生铁、钢材、铁矿石和铁合金的产量均出现下降,详见表1。
说明:因国家统计局对国产铁犷石统计范围的变化,使我国铁矿石产量数据偏低,约少3亿吨左右,实际产量在12亿吨以上。
2023年中钢协会员单位拥有废钢资源9579万吨,炼钢消耗废钢9435万吨,比上年减少1631万吨,其中转炉消耗废钢7628万吨,比上年减少1272万吨,废钢消耗量的减少不利于钢铁工业能耗降低。
2 .能源消耗情况2.1. 基本情况2023年中钢协能耗统计的会员单位有99家,其对应的钢产量为61404.07万吨,总能耗为34582.83万吨标准煤;与上年相比,重点统计企业的钢产量下降2.70%,总能耗降低2.49%。
2023年重点统计企业的吨钢综合能耗为55136kgce∕t,比上年升高127kgce∕t;吨钢可比能耗485.77kgce∕t,比上年升高0.38%。
2023年其他钢铁企业的铁、钢产量比上年分别下降2.22%、5.03%,下降幅度均高于重点统计企业变化幅度,使我国钢铁产业集中度进一步升高,有利于行业结构优化、能耗降低、冶金设备大型化等发展。
2.2.各工序能耗现状表2是2023年中钢协会员单位能耗情况对比。
从表2可以看出,与上年相比,2023年中钢协会员单位的烧结、球团、焦化、高炉、转炉和钢加工工序的能耗均出现下降。
部分钢铁企业的部分指标已达到或接近国际先进水平。
特别是吨钢耗新水指标创出历史最好水平(达到2.44m3∕t),有54家企业吨钢耗新水指标出现下降,有35家企业吨钢耗新水指标低于2.0m3∕t0表2中的数据表明,各企业之间节能工作发展不平衡,生产条件和结构也不一样,企业之间的各工序能耗最高值与先进值差距较大,说明我国钢铁企业之间技术水平和装备水平差距较大,企业节能工作还有较大潜力。
国内外钢铁企业能耗及环保指标比较研究

国内外钢铁企业能耗及环保指标比较研究(表)钢铁工业是国民经济重要的基础原材料工业,也是高耗能、高污染工业。
钢铁工业节约潜力巨大,为此,国外大型钢铁企业纷纷采取先进技术,开展节能降耗和综合利用,发展循环经济,不断优化工业的能耗指标和环保指标,以期达到能耗最少,环保最优。
与国外发达水平相比,我国钢铁工业差距明显。
2004年,我国大中型钢铁企业吨钢综合能耗为761千克标煤,比国际先进水平高81千克标煤;吨钢耗新水11.15m3,比国际先进水平高7.3m3;固体废物综合利用率60.4%,比国际先进水平低37.6个百分点。
一、能耗指标比较1、吨钢综合能耗、可比能耗和工序能耗比较表1列出了2003年我国重点企业主要工序能耗与国际先进水平(1999年)的比较,数据表明,我国转炉工序能耗与国外先进水平差值最大,炼铁工序差值最小。
2003年我国钢铁工业吨钢综合能耗为770kgce,吨钢可比能耗698kgce;2003年日本钢铁工业吨钢综合能耗为656kgce,2000年国外主要产钢国家(英、日、法、德)平均吨钢可比能耗为642kgce。
这两项指标分别比国外先进水平高出17.4%和8.7%。
国内外大型钢铁企业工序能耗指标的比较如表2所示。
在国外,先进企业的高炉焦比已达到300kg/t以下,燃料比小于500kg/t。
我国重点钢铁企业的入炉焦比为426kg/t,部分其它企业为488kg/t,燃料比为560kg/t左右。
高炉工艺的能耗(标媒)比世界先进水平高出50~100kg/t。
表1 国内外钢铁工业综合能耗、可比能耗和炼铁系统工序能耗比较(单位:kgce/t)资料来源:上海科学技术情报研究所整理。
表2 国内外大型钢铁企业工序能耗指标比较资料来源:上海科学技术情报研究所整理。
2、二次能源利用情况比较钢铁工业的二次能源主要有三类:(1)各种副产煤气;(2)余热;(3)余能(余压)。
国际上主要产钢国家的二次能源产生量占其钢铁工业一次能源消耗的40%~50%,其中各种副产煤气(焦炉煤气、高炉煤气和转炉煤气)占绝大多数,据日本1998年统计为36%左右。
中国钢铁工业的能耗现状及分析研究
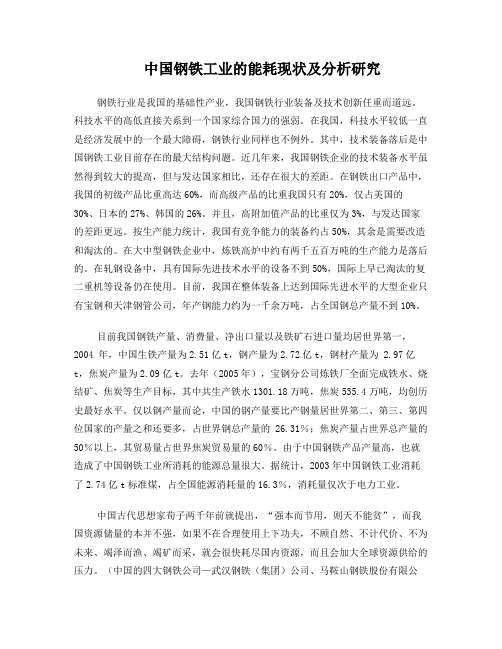
中国钢铁工业的能耗现状及分析研究钢铁行业是我国的基础性产业,我国钢铁行业装备及技术创新任重而道远。
科技水平的高低直接关系到一个国家综合国力的强弱。
在我国,科技水平较低一直是经济发展中的一个最大障碍,钢铁行业同样也不例外。
其中,技术装备落后是中国钢铁工业目前存在的最大结构问题。
近几年来,我国钢铁企业的技术装备水平虽然得到较大的提高,但与发达国家相比,还存在很大的差距。
在钢铁出口产品中,我国的初级产品比重高达60%,而高级产品的比重我国只有20%,仅占美国的30%、日本的27%、韩国的26%。
并且,高附加值产品的比重仅为3%,与发达国家的差距更远。
按生产能力统计,我国有竞争能力的装备约占50%,其余是需要改造和淘汰的。
在大中型钢铁企业中,炼铁高炉中约有两千五百万吨的生产能力是落后的。
在轧钢设备中,具有国际先进技术水平的设备不到50%,国际上早已淘汰的复二重机等设备仍在使用。
目前,我国在整体装备上达到国际先进水平的大型企业只有宝钢和天津钢管公司,年产钢能力约为一千余万吨,占全国钢总产量不到10%。
目前我国钢铁产量、消费量、净出口量以及铁矿石进口量均居世界第一,2004 年,中国生铁产量为2.51亿t,钢产量为2.72亿t,钢材产量为 2.97亿t,焦炭产量为2.09亿t。
去年(2005年),宝钢分公司炼铁厂全面完成铁水、烧结矿、焦炭等生产目标,其中共生产铁水1301.18万吨,焦炭535.4万吨,均创历史最好水平。
仅以钢产量而论,中国的钢产量要比产钢量居世界第二、第三、第四位国家的产量之和还要多,占世界钢总产量的 26.31%;焦炭产量占世界总产量的50%以上,其贸易量占世界焦炭贸易量的60%。
由于中国钢铁产品产量高,也就造成了中国钢铁工业所消耗的能源总量很大。
据统计,2003年中国钢铁工业消耗了2.74亿t标准煤,占全国能源消耗量的16.3%,消耗量仅次于电力工业。
中国古代思想家荀子两千年前就提出,“强本而节用,则天不能贫”,而我国资源储量的本并不强,如果不在合理使用上下功夫,不顾自然、不计代价、不为未来、竭泽而渔、竭矿而采,就会很快耗尽国内资源,而且会加大全球资源供给的压力。
钢铁技术能耗分析
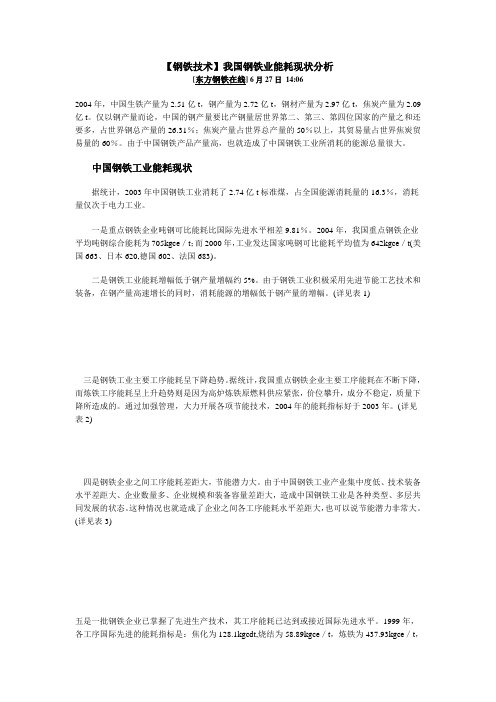
【钢铁技术】我国钢铁业能耗现状分析[东方钢铁在线] 6月27日14:062004年,中国生铁产量为2.51亿t,钢产量为2.72亿t,钢材产量为2.97亿t,焦炭产量为2.09亿t。
仅以钢产量而论,中国的钢产量要比产钢量居世界第二、第三、第四位国家的产量之和还要多,占世界钢总产量的26.31%;焦炭产量占世界总产量的50%以上,其贸易量占世界焦炭贸易量的60%。
由于中国钢铁产品产量高,也就造成了中国钢铁工业所消耗的能源总量很大。
中国钢铁工业能耗现状据统计,2003年中国钢铁工业消耗了2.74亿t标准煤,占全国能源消耗量的16.3%,消耗量仅次于电力工业。
一是重点钢铁企业吨钢可比能耗比国际先进水平相差9.81%。
2004年,我国重点钢铁企业平均吨钢综合能耗为705kgce/t;而2000年,工业发达国家吨钢可比能耗平均值为642kgce/t(美国663、日本620,德国602、法国683)。
二是钢铁工业能耗增幅低于钢产量增幅约5%。
由于钢铁工业积极采用先进节能工艺技术和装备,在钢产量高速增长的同时,消耗能源的增幅低于钢产量的增幅。
(详见表1)三是钢铁工业主要工序能耗呈下降趋势。
据统计,我国重点钢铁企业主要工序能耗在不断下降,而炼铁工序能耗呈上升趋势则是因为高炉炼铁原燃料供应紧张,价位攀升,成分不稳定,质量下降所造成的。
通过加强管理,大力开展各项节能技术,2004年的能耗指标好于2003年。
(详见表2)四是钢铁企业之间工序能耗差距大,节能潜力大。
由于中国钢铁工业产业集中度低、技术装备水平差距大、企业数量多、企业规模和装备容量差距大,造成中国钢铁工业是各种类型、多层共同发展的状态。
这种情况也就造成了企业之间各工序能耗水平差距大,也可以说节能潜力非常大。
(详见表3)五是一批钢铁企业已掌握了先进生产技术,其工序能耗已达到或接近国际先进水平。
1999年,各工序国际先进的能耗指标是:焦化为128.1kgcdt,烧结为58.89kgce/t,炼铁为437.93kgce/t,转炉为-8.88kgce/t,电炉为198.6kgceA,热轧为47.82kgce/t,冷轧为80.28kgce/t。
国内外高炉炼铁系统的能耗分析

国内外高炉炼铁系统的能耗分析炼铁系统的能耗占钢铁联合企业总能耗70%,吨铁产生1.5 tco2, 3.08kgso2, 50mg粉尘, 95%的二恶英, 约350kg/t的炉渣。
1、根据中国钢铁工业协会2007年发布的全国重点钢铁企业有关能耗数据来进行分析,有关人士总结了重点钢铁企业高炉每生产一吨铁的能耗状况:焦化工序的工序能耗为123.11kgce/t,高炉炼铁入炉焦比为392kg/t。
由此得出,冶炼一吨铁水,焦化工序的能源消耗为123.11kgce/t × 0.392t/t = 48.26kgce/t。
烧结工序的工序能耗为55.21kgce/t,高炉炼铁的炉料结构为烧结矿78.28%、球团矿13.91%、块矿7.81%。
冶炼一吨铁水需要消耗1.672吨含铁原料,则需要的烧结量为1.672t × 78.28% = 1.3088t。
由此得出冶炼一吨铁水,烧结工序的能耗为55.21kgce × 1.3088t =2.25 kgce/t。
球团工序的工序能耗为33.08kgce/t,冶炼一吨铁水需要球团量为1.672t × 13.91% = 0.2325t。
由此得出冶炼一吨铁水,球团工序所消耗的能源为33.08kgce/t ×0.2325t =7.69kgce/t。
炼铁工序能耗为428.16kgce/t,生产一吨铁水,炼铁系统总能耗为48.26kgce/t (焦化)+ 72.25kgce/t(烧结)+ 7.69kgce/t(球团)+ 426.84kgce/t(炼铁) = 555.04kgce/t。
2、按照上述计算方法,我们计算了2007年一季度宝山钢铁股份公司4号高炉(4747m³)生产一吨铁的能耗:21.81kgce/t(焦化)+ 62.31kgce/t(烧结)+4.60kgce/t(球团)+ 381.22kgce/t(炼铁) = 469.94kgce/t。
柳钢吨钢综合能耗行业内对比分析
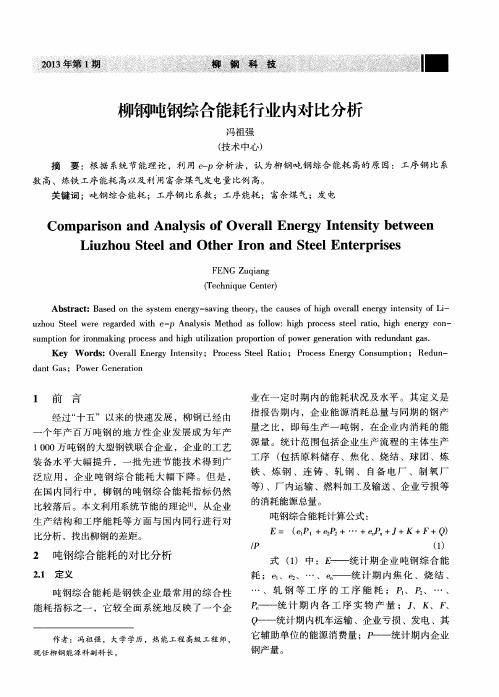
2 . 1 定 义
式 ( 1 ) 中:卜
统 计 期 企 业 吨 钢 综 合 能
耗 ;e 、e 2 、… 、e 。 _ 一 统 计 期 内焦 化 、烧 结 、
…
吨钢 综 合 能 耗 是 钢铁 企 业 最 常 用 的综 合 性 能 耗 指 标 之 一 ,它 较 全 面 系 统 地 反 映 了一 个 企
它 辅 助单 位 的能 源消 费量 ;
钢产 量 。
统计 期 内企 业
l
l j | 蓐 1 。 | | | | . |2 . f 亏 善 筹 努。
因素有 工 序 钢 比系数 P 、工 序 能 耗 e n 以及 机 车 运 输 、企 业 亏损 、发 电 、其 它 辅 助 单 位 的 吨 钢
1 0 0 0万 吨钢 的大 型钢 铁 联 合企 业 ,企 业 的工 艺
量 之 比 , 即每 生 产 一 吨 钢 ,在 企 业 内消 耗 的能
源 量 。 统 计 范 围包 括 企 业 生 产 流 程 的主 体 生 产
装 备 水 平 大 幅 提 升 ,一 批 先 进 节 能 技 术 得 到 广 泛 应 用 ,企 业 吨 钢 综 合 能 耗 大 幅 下 降 。 但 是 ,
Co m pa r i s o n a nd Ana l y s i s o f Ov e r a l l Ene r g y I n t e n s i t y be t we e n Li uz ho u St e e l a nd Ot h e r I r o n a nd St e e l Ent e r pr i s e s
工序单位能耗的计算方法、及企业吨钢可比能耗计算方法
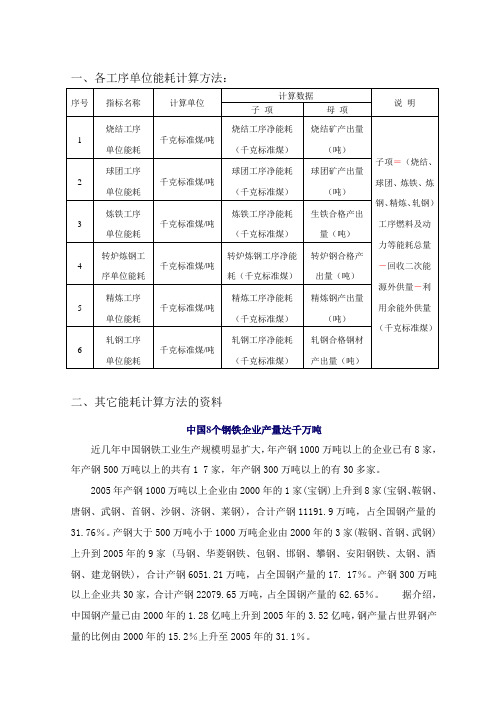
一、各工序单位能耗计算方法:二、其它能耗计算方法的资料中国8个钢铁企业产量达千万吨近几年中国钢铁工业生产规模明显扩大,年产钢1000万吨以上的企业已有8家,年产钢500万吨以上的共有1 7家,年产钢300万吨以上的有30多家。
2005年产钢1000万吨以上企业由2000年的1家(宝钢)上升到8家(宝钢、鞍钢、唐钢、武钢、首钢、沙钢、济钢、莱钢),合计产钢11191.9万吨,占全国钢产量的31.76%。
产钢大于500万吨小于1000万吨企业由2000年的3家(鞍钢、首钢、武钢)上升到2005年的9家 (马钢、华菱钢铁、包钢、邯钢、攀钢、安阳钢铁、太钢、酒钢、建龙钢铁),合计产钢6051.21万吨,占全国钢产量的17. 17%。
产钢300万吨以上企业共30家,合计产钢22079.65万吨,占全国钢产量的62.65%。
据介绍,中国钢产量已由2000年的1.28亿吨上升到2005年的3.52亿吨,钢产量占世界钢产量的比例由2000年的15.2%上升至2005年的31.1%。
标准煤系数就是把某一能源品种的实物量折合成标准量时所采用的系数,换句话说,就是单位能源的实际发热值与7000千卡的比率:即:单位能源的实际发热值7000千卡=该能源品种折标准煤系数例如:1公斤焦炭的平均低位发热量为6800千卡,其折标准煤系数为:6800千卡÷7000千卡=0.9714。
也就是说,1公斤焦炭相当于0.9714公斤标准煤,1000吨焦炭相当于971.4吨标准煤。
在企业内部同一能源品种,由于到货时间、供货单位的不同,其实际发热值也不一样。
在此情况下,确定企业标准煤系数,一般采用“加权算术平均数”的计算方法,加权算术平均数是反映次数结构影响的算术平均数,它的计算方法是总体各标志值(变量值)乘以相应的次数(权数)之和与总次数(总权数)的比。
例如:某企业2002年5月份先后从枣庄、肥城、山西、兖州等地购入原煤的实际数量分别为150吨、175吨、250吨、250吨,每次到货后实测发热值分别为4910千卡/公斤、4509千卡/公斤、5101千卡/公斤、5250千卡/公斤,这些原煤在本月全部消耗,那么该企业5月份消耗煤炭折标准煤587.62吨,折标准煤系数为0.7123。
包钢发展循环经济的探讨
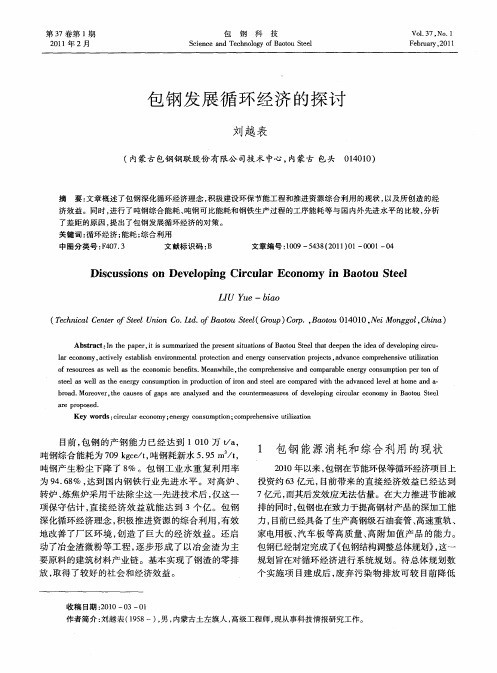
1 包 钢 能 源 消 耗 和 综 合 利 用 的现 状
2 1 以来 , 钢在节 能环保 等循环经济项 目上 00年 包
投 资约 6 亿 元 , 3 目前 带来 的直接 经 济效 益 已经 达 到
转 炉 、 焦炉 采用 干 法除 尘这 一先 进技 术后 , 这 一 炼 仅 项 保守 估计 , 接 经 济 效益 就 能达 到 3个 亿 。 包 钢 直
l cnm ,c vl etbi n i n e t rtco n nrycnevt npo c ,d ac o pees eu la o a eoo y at e s l he v om na poet nade e osrai r et avn e m rhni ti t n r i y a s r l i g o j s c v iz i
7 亿元 , 而其后发 效应 无法估 量 。在大 力推 进节 能减
排 的同时 , 包钢也在致 力于提高 钢材产 品 的深 加工 能
深 化循 环经 济理 念 , 积极 推进 资源 的综 合利 用 , 效 有 地 改善 了厂 区环 境 , 造 了 巨大 的经 济 效 益 。 还启 创
力 , 已经具备 了生产高钢级 石油 套管 、 速重轨 、 目前 高 家 电用 板 、 车板 等 高 质 量 、 附 加值 产 品 的 能力 。 汽 高
Abs r c :n t e p pe ,ti u ma ie hepr s ntsta in fBa t u S e lta e p n t d a o e eo i g cr u t a t I h a r i s s m rz d t e e iu to so oo t e h td e e hei e fd v l p n ic —
中钢能耗指标
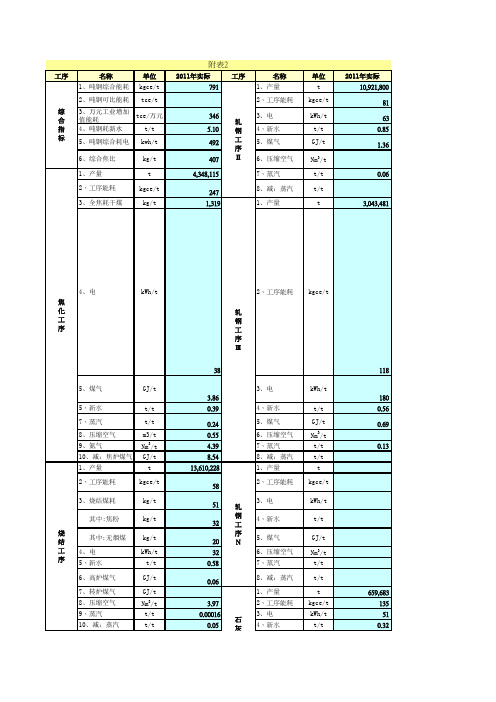
工序 名称 1、吨钢综合能耗 2、吨钢可比能耗 综 合 指 标 单位 kgce/t tce/t 346 5.10 492 407 4,348,115 247 1,319 38 轧 钢 工 序 Ⅲ 轧 钢 工 序 Ⅱ 2011年实际 2011年实际 791 工序 名称 1、产量 2、工序能耗 3、电 4、新水 5、煤气 6、压缩空气 7、蒸汽 8、减:蒸汽 1、产量 2、工序能耗 单位 t kgce/t kWh/t t/t GJ/t Nm3/t t/t t/t t kgce/t 3,043,481 118 0.06 2011年实际 2011年实际 10,921,800 81 63 0.85 1.36
3
Nm /t GJ/t t kgce/t kg/t kg/t kg/t kWh/t t/t GJ/t GJ/t
3
3、烧结煤耗 其中:焦粉 烧 结 工 序 其中:无烟煤 4、电 5、新水 6、高炉煤气 7、转炉煤气 8、压缩空气 9、蒸汽 10、减:蒸汽 1、产量 2、工序能耗 球 团 工 序 3、电 4、新水 5、煤气 6、氮气 7、压缩空气
26.33 39 38.21 制氮
6、氧气总产量 万立方米 7、电损率 总产量 电 总产量 % 万立方米
3
Nm /t Nm3/t
3
Nm /t t/t GJ/t kWh/t t kgce/t kWh/t t/t
3
kwh/m 万Kwh m3/kwh Nm3/kwh Nm3/kwh Nm3/kwh Nm3/kwh 万立方米 kWh/km 3 m3/km3 Nm3/km3 kg/km3
8、煤气
GJ/t 1.58 Nm3/t
3
9、压缩空气 10、氧气 11、高压氮气 12、低压氮气 13、减:焦粉 14、减:高炉煤气 15、减:电力 1、产量 2、工序能耗 3、电 4、新水 炼 钢 工 序 5、氧气 6、氮气 7、氩气 8、煤气 9、蒸汽 10、压缩空气 11、减:转炉煤气 12、减:蒸汽 1、产量 2、工序能耗 轧 钢 工 序 Ⅰ 3、电 4、新水 5、煤气 6、压缩空气 7、蒸汽 8、减:蒸汽
- 1、下载文档前请自行甄别文档内容的完整性,平台不提供额外的编辑、内容补充、找答案等附加服务。
- 2、"仅部分预览"的文档,不可在线预览部分如存在完整性等问题,可反馈申请退款(可完整预览的文档不适用该条件!)。
- 3、如文档侵犯您的权益,请联系客服反馈,我们会尽快为您处理(人工客服工作时间:9:00-18:30)。
内外吨钢综合能耗、可比能耗和工序能耗比较
钢铁工业是国民经济重要的基础原材料工业,也是高耗能、高污染工业。
钢铁工业节约潜力巨大,为此,国外大型钢铁企业纷纷采取先进技术,开展节能降耗和综合利用,发展循环经济,不断优化工业的能耗指标和环保指标,以期达到能耗最少,环保最优。
与国外发达水平相比,我国钢铁工业差距明显。
2004年,我国大中型钢铁企业吨钢综合能耗为761千克标煤,比国际先进水平高81千克标煤;吨钢耗新水11. 15m3,比国际先进水平高 7. 3m:,;固体废物综合利用率乩比国际先进水平低个百分点。
在此,以我国大中型钢铁企业的相关指标与国外发达水平作对比,目的是寻找差距,迎头赶上。
下表列出了2003年我国重点企业主要工序能耗与国际先进水平(1999年)的比较,数据表明,我国转炉工序能耗与国外先进水平差值最大,炼铁工序差值最小。
2003年我国钢铁工业吨钢综合能耗为770kgce,吨钢可比能耗698kgce;2003年日本钢铁工业吨钢综合能耗为656kgce, 2000年国外主要产钢国家(英、日、法、徳)平均吨钢可比能耗为642kgce。
这两项指标分别比国外先进水平高出%和觥
在国外,先进企业的高炉焦比已达到300kg/t以下,燃料比小于500kg/to我国重点钢铁企业的入炉焦比为426kg/t,部分其它企业为488kg/t,燃料比为560kg/t左右。
高炉工艺的能耗(标媒)比世界先进水平高出50〜 100kg/to
同时,我国重点企业之间主要工序能耗的差距很大,指标先进的(如宝钢集团)已达到或超过国际先进水平, 而落后的能耗要高出先进值的1倍或数倍。
这说明,我国钢铁工业节能的潜力还是很大的。
新制订的《钢铁产业发展政策》明确提出,要建立循环型钢铁工厂,500万吨以上规模钢铁联合企业,要努力做到电力自供有余,实现外供。
2005年,全行业吨钢综合能耗降到吨标煤、吨钢可比能耗吨标煤、吨钢耗新水12吨以下;2010年分别降到吨标煤、吨标煤、8吨以下;2020年分别降到吨标煤、吨标煤、6吨以下。
表:国内外钢铁工业综合能耗、可比能耗和炼铁系统工序能耗比较(单位:kgce/t)
资料来源:上海科学技术情报研究所整理。
表:国内外大型钢铁企业工序能耗指标比较
表:2000〜2020年间我国钢铁工业主要产品单位能耗指标。