连杆加工工艺及夹具设计-参考模板
连杆零件加工工艺及专用钻床夹具的设计Word版
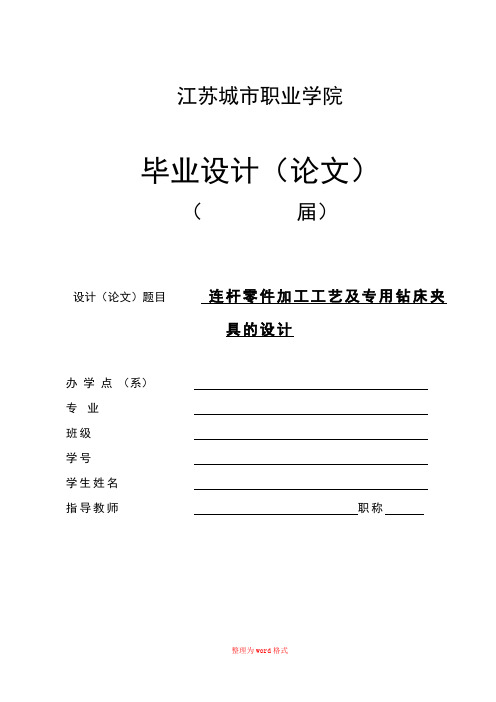
江苏城市职业学院毕业设计(论文)(届)设计(论文)题目连杆零件加工工艺及专用钻床夹具的设计办学点(系)专业班级学号学生姓名指导教师职称连杆零件加工工艺及专用钻床夹具的设计摘要本设计是关于连杆零件的加工工艺规程和专用夹具的设计,以介绍设计方法为宗旨,着重实力,力图做到内容完整、详实。
这次设计将我以前学过的机械制造工艺与装备、公差与配合、机械制图、工程材料与热处理工艺等知识很好的串联了起来,巩固了所学知识的作用。
首先是对工件机械加工工艺规程的制定,工件机械加工工艺规程的制定是至关重要的。
设计零件的工艺规程以及对典型夹具进行结构分析与精度分析;通过本课程的设计使学生具有一定的设计专用夹具的能力和分析生产中与夹具有关的技术问题的能力。
关键词:专用钻床夹具;工艺规程;切削用量;加工余量目录第一章引言 (1)第二章连杆零件机械加工工艺规程的编制 (2)2.1 计算生产纲领,确定生产类型 (2)2.2 零件的分析 (3)2.3 选择毛坯及毛坯制造方法 (3)2.4 工艺规程设计 (4)2.4.1定位基面的选择 (4)2.4.2 连杆零件表面加工方法的选择 (5)2.4.3 制定工艺路线 (5)2.4.4 选择加工设备及工艺装备 (6)2.5 加工工序设计、工序尺寸及切削用量的计算 (6)2.6 时间定额计算 (9)第三章连杆零件的夹具设计 (12)3.1 机床夹具设计的基本要求和一般步骤 (12)3.1.1 对专用夹具的基本要求 (12)3.1.2 专用夹具设计步骤 (12)3.2 连杆零件的钻床夹具设计 (13)3.2.1 零件本工序的加工要求分析 (13)3.2.2 确定夹具类型 (14)3.3 拟订定位方案和选择定位元件 (14)3.4 绘制夹具总装图 (15)第四章总结 (17)参考文献 (18)致谢 (19)第一章引言机械制造工艺规程的制定需选择机械加工余量,机械加工余量的大小,不仅影响机械零件的毛坯尺寸,而且也影响工艺装备的尺寸,设备的调整,材料的消耗,切削用量的选择,加工工时的多少。
孔连杆加工工艺及夹具设计word文档
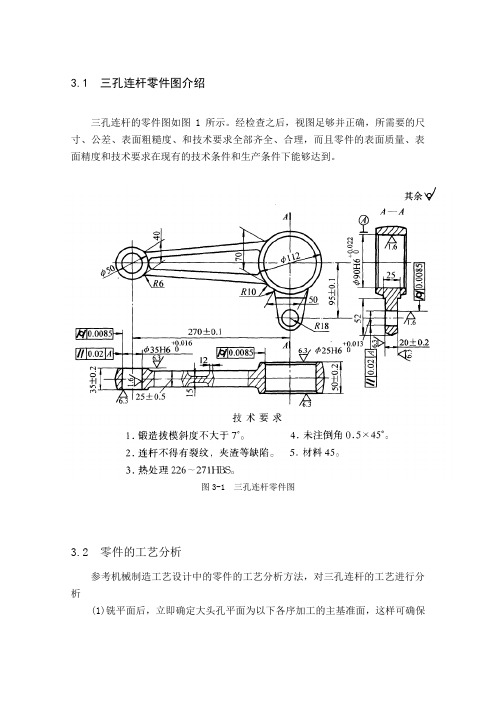
3.1 三孔连杆零件图介绍三孔连杆的零件图如图1所示。
经检查之后,视图足够并正确,所需要的尺寸、公差、表面粗糙度、和技术要求全部齐全、合理,而且零件的表面质量、表面精度和技术要求在现有的技术条件和生产条件下能够达到。
图3-1 三孔连杆零件图3.2 零件的工艺分析参考机械制造工艺设计中的零件的工艺分析方法,对三孔连杆的工艺进行分析(1)铣平面后,立即确定大头孔平面为以下各序加工的主基准面,这样可确保加工质量的稳定。
(2)铣平面时,应保证小头孔及耳部孔平面厚度与大头孔平面厚度的对称性。
(3)由于连杆三个孔平面厚度不一致,因此,加工中要注意合理布置辅助支承及应用。
(4)连杆平面加工也可以分为粗、精两序,这样可更好的保证三个平面相互位置及尺寸精度。
(5)粗、精镗三孔也可改用专用工装或组合夹具装夹。
(6)当加工连杆尺寸较小时,粗、精加工三孔也可采用镗削加工方法。
三孔的精度要求较高,可以分为粗、精两工序。
(7)连杆三孔平行度的检验;连杆三孔圆柱度的检验。
3.3 毛坯的选择连杆是发动机的五大主关件之一,其在发动机中的地位是显而易见。
它是发动机传递动力的主要运动件,在机体中做复杂的平面运动,连杆小头随活塞作上下往复运动连杆大头随曲轴作高速回转运动连杆杆身在大、小头孔运动的合成下作复杂的摆动[3]。
连杆在承受往复的惯性力之外,还要承受高压气体的压力,在气体的压力和惯性力合成下形成交变载荷,这就要求连杆具有耐疲劳、抗冲击,并具备足够的强度、刚度和较好的韧性。
在今天随着汽车工业的高速发展,“ 小体积、大功率、低油耗”的高性能发动机对连杆提出更新、更高的要求作为高速运动件重量要轻,减小惯性力,降低能耗和噪声强度、刚度要高,并具有较高的韧性连杆比要大,连杆要短。
这也就意味着对连杆的设计和加工有更高的要求。
3.3.1 选择毛坯时应考虑的因素在选择毛坯的时候应考虑以下因素[4]:(1)毛坯的种类和特点,设计图纸规定的材料和机械性能;零件结构形状和外形尺寸;不同的毛坯的制造方法对结构和尺寸有特定的要求;企业现有的生产条件;新工艺,新材料新技术的应用。
连杆孔加工工艺与夹具设计

目录第1章毕业设计--------------------------------------------------------------------------1 1.1零件分析---------------------------------------------------------------------------------1 1.2定位基准旳选择以及重要原则件旳选择------------------------------------------2 1.3夹具设计-------------------------------------------------------------------------------8 1.3.1钻床夹具旳特点----------------------------------------------------------------------8 1.3.2工件旳定位措施及其定位元件----------------------------------------------------11 1.3.3定位误差旳分析与计算-------------------------------------------------------------13 1.3.4夹紧机构旳分析与夹紧力旳计算-------------------------------------------------14 1.3.5夹具装配图--------------------------------------------------------------------------18第2章综合训练--------------------------------------------------------------------------20 2.1夹具设计AutoCAD三维造型---------------------------------------------------------20 2.1.1夹详细及定位元件旳造型----------------------------------------------------------20 2.1.2夹紧元件三维实体造型-------------------------------------------------------------29 2.1.3夹详细三维实体造型及实体造型装配图----------------------------------------31 道谢--------------------------------------------------------------------------------------------33参照文献-------------------------------------------------------------------------------------34连杆孔加工工艺与夹具设计第1章课程设计1.1零件分析一、整体零件分析:如图1-1所示旳连杆零件, 材料为QT40-17, 毛坯为精铸件, 要在其右侧钻M8旳通孔, 规定设计大批量生产时(10000件/年)所需旳钻夹具图1-1 连杆零件图零件分析: 此零件为一连杆, 它旳各个尺寸如上图所示,总旳长度方向上旳尺寸为100mm, 高度方向总尺寸为32mm, 宽度方向为30 mm, 本次重要是对连杆右端φ8 mm孔旳加工进行设计, 孔一般都采用钻床进行加工, 因此本次设计旳重要任务是在其他各个部位都已加工好旳前提条件下, 运用钻床夹具旳有关知识来设计加工左孔旳夹具。
连杆加工工艺及夹具设计
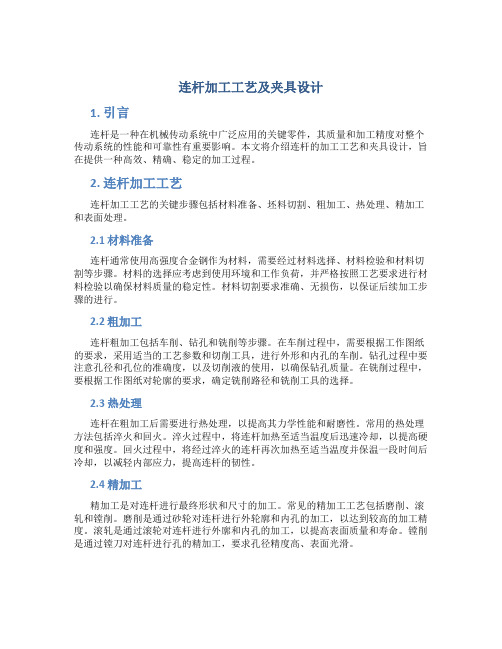
连杆加工工艺及夹具设计1. 引言连杆是一种在机械传动系统中广泛应用的关键零件,其质量和加工精度对整个传动系统的性能和可靠性有重要影响。
本文将介绍连杆的加工工艺和夹具设计,旨在提供一种高效、精确、稳定的加工过程。
2. 连杆加工工艺连杆加工工艺的关键步骤包括材料准备、坯料切割、粗加工、热处理、精加工和表面处理。
2.1 材料准备连杆通常使用高强度合金钢作为材料,需要经过材料选择、材料检验和材料切割等步骤。
材料的选择应考虑到使用环境和工作负荷,并严格按照工艺要求进行材料检验以确保材料质量的稳定性。
材料切割要求准确、无损伤,以保证后续加工步骤的进行。
2.2 粗加工连杆粗加工包括车削、钻孔和铣削等步骤。
在车削过程中,需要根据工作图纸的要求,采用适当的工艺参数和切削工具,进行外形和内孔的车削。
钻孔过程中要注意孔径和孔位的准确度,以及切削液的使用,以确保钻孔质量。
在铣削过程中,要根据工作图纸对轮廓的要求,确定铣削路径和铣削工具的选择。
2.3 热处理连杆在粗加工后需要进行热处理,以提高其力学性能和耐磨性。
常用的热处理方法包括淬火和回火。
淬火过程中,将连杆加热至适当温度后迅速冷却,以提高硬度和强度。
回火过程中,将经过淬火的连杆再次加热至适当温度并保温一段时间后冷却,以减轻内部应力,提高连杆的韧性。
2.4 精加工精加工是对连杆进行最终形状和尺寸的加工。
常见的精加工工艺包括磨削、滚轧和镗削。
磨削是通过砂轮对连杆进行外轮廓和内孔的加工,以达到较高的加工精度。
滚轧是通过滚轮对连杆进行外廓和内孔的加工,以提高表面质量和寿命。
镗削是通过镗刀对连杆进行孔的精加工,要求孔径精度高、表面光滑。
2.5 表面处理连杆经过精加工后需要进行表面处理,以提高其外观质量和防腐性能。
常见的表面处理方法包括喷涂、镀层和热处理。
喷涂是将涂料喷涂在杆上,通过干燥和固化形成坚固的保护层。
镀层是将金属镀层沉积在杆上,以增加其表面硬度和耐磨性。
热处理是通过加热和冷却过程改变连杆的组织结构,以提高其防腐性能。
连杆加工工艺及夹具设计说明书 精品

设计题目:连杆加工工艺及夹具设计绪论一、连杆的结构特点连杆是发动机的主要零件之一,它连接活塞和曲轴,把作用于活塞顶面的膨胀气体的压力传给曲轴;将活塞的往复运动变为曲柄的旋转运动,又受到曲轴的驱动而带动活塞压缩缩气缸中的气体。
因此,连杆在工作中承受着呈周期交变的压缩、拉伸及弯曲应力,这些交变载荷具有很大的冲击特性。
发动机正常工作时,连杆大头约以3000r/min的转速旋转,线速度达10m/s,所以连杆在工作时,形成巨大的离心力。
由于连杆横向窜动和形位误差引起连杆受压时产生弯曲,是连杆很容易断裂,断裂是连杆的主要损伤形式。
连杆由连杆体及连杆盖两部分组成。
连杆体及连杆盖上的大头孔用螺栓和螺母与曲轴装在一起。
为了减少磨损和便于维修,连杆的大头孔内装有薄壁金属轴瓦。
轴瓦有钢质的底,底的内表面浇有一层耐磨巴氏合金。
连杆小头用活塞销与活塞连接。
小头孔内压入青铜衬套,以减少小头孔与活塞销的磨损,同时便于在磨损后进行修理和更换。
连杆属于典型的“杂件”类零件,不但精度要求高,形状复杂,制造难度大,而且批量大,直接影响发动机质量,本篇详细介绍了其加工方法的拟订和确立,并对加工中镗连杆总成体大头孔所采用专用立式镗床夹具进行设计。
从工艺与专用夹具的方向进行了一定的探讨。
<制造工艺的发展情况>随着科学技术的发展,各料、新工艺和新技术不断涌现,机械制造工艺正向高质量、高生产率和低成本方向发展。
电火花、电解、超声波、种新材激光、电子束和离子束加工等工艺的出现,已突破传统的依靠机械能、切削力进行切削加工的范畴,可以加工各种难加工材料、复杂的型面和某些具有特殊要求的零件。
近年发展起来的以计算机为行动中心,完成加工、装卸、运输、管理的柔性制造系统,具有监视、诊断、修复、自动转位加工产品的功能,使多品种、中小批量生产实现了加工自动化,大大促进了自动化的进程,尤其是将计算机辅助设计与制造结合起来而形成的计算机集成制造系统,是加工自动化向智能化方向发展的又一关键性技术,并进一步朝着网络化、集成化和智能化的方向发展。
连杆零件的机械加工工艺规程和专用夹具设计
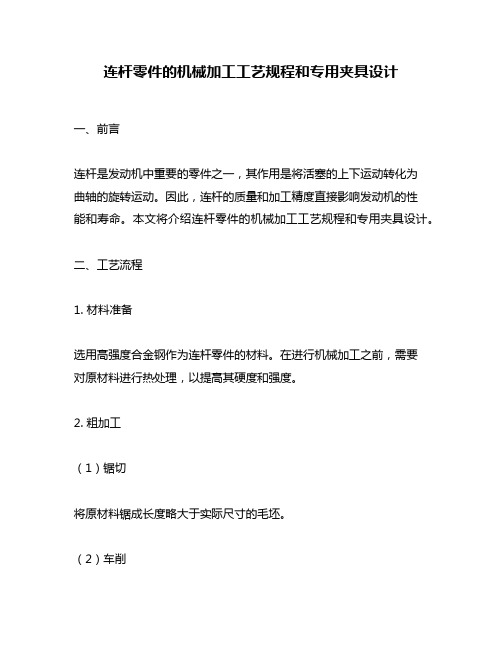
连杆零件的机械加工工艺规程和专用夹具设计一、前言连杆是发动机中重要的零件之一,其作用是将活塞的上下运动转化为曲轴的旋转运动。
因此,连杆的质量和加工精度直接影响发动机的性能和寿命。
本文将介绍连杆零件的机械加工工艺规程和专用夹具设计。
二、工艺流程1. 材料准备选用高强度合金钢作为连杆零件的材料。
在进行机械加工之前,需要对原材料进行热处理,以提高其硬度和强度。
2. 粗加工(1)锯切将原材料锯成长度略大于实际尺寸的毛坯。
(2)车削采用车床进行粗加工,先将毛坯两端面加工成平行面,然后进行外圆柱面、内孔等基本形状的车削。
(3)铣削采用立式铣床进行粗加工,主要是对连杆头部进行铣削,并开出油孔等结构。
3. 精密加工(1)磨削采用平面磨床和圆柱磨床对外圆柱面、内孔和连杆头等进行精密加工。
(2)钻孔采用钻床对油孔等细小结构进行加工。
(3)拉削采用拉床对轴向槽、键槽等进行加工。
4. 热处理将加工好的连杆零件进行热处理,以提高其硬度和强度。
通常采用淬火和回火的方式进行处理。
5. 组装将经过热处理的连杆零件组装到曲轴上,并进行调整,以确保其与其他零件的配合精度和运动平稳性。
三、专用夹具设计为了保证连杆零件在机械加工过程中的精度和稳定性,需要设计专用夹具。
下面介绍一种常见的夹具设计方案:1. 夹具整体结构该夹具主要由夹紧块、支撑块、定位块、压板等组成。
其中,夹紧块负责固定毛坯,支撑块负责支撑毛坯,在车削时起到了很好的辅助作用;定位块则是为了确保毛坯在夹具中的位置准确;压板则是为了防止毛坯在车削时发生移动。
2. 夹具夹紧方式该夹具采用机械夹紧的方式,通过螺旋压板来实现对毛坯的夹紧。
在进行车削等加工时,需要根据不同工序进行调整,以确保毛坯的稳定性和精度。
3. 夹具使用注意事项在使用该夹具时,需要注意以下几点:(1)夹具的各个部位需要经常清洗和润滑,以保证其正常运作。
(2)在进行车削等加工时,需要根据不同工序进行调整,并且要保证毛坯与夹具之间的接触面积充分。
浅谈连杆的机械加工工艺及专用夹具设计

连杆零件是发动机制造中的重要部件,该部件必须具有强度高、硬性好、不会因为长时间使用发生磨损等性能,只有高强度的
连杆零件才能够保证发动机良好运作。
关键词 :连杆零件 ;机械加工工艺规程 ;专用夹具及其设计
中图分类号 :TH16
文献标识码 :A
文章编号 :11-5004(2020)01-0062-2
(1)定位基准的选择。通过设计图可以看出,在小头孔加工 之前,连杆的端面就已经加工完毕了。表面粗糙度要求整体要求 较高,Z 轴转动不妨碍小孔中心定位,生产的连杆量很大,为了 让这些加工在短时间内完成,采用快换钻模加工方法进行加工, 这样可以让整个工序消耗的时间大大缩减。
(2)夹紧方案。由于钻的过程中会给小孔一个向下的力,因 此在大端孔用双螺栓夹紧,V 型块在夹紧过程中也会起一定的 限制作用。
33mm
X62 组 合 夹 具 或 专用工装
钻 2— Φ 10mm 螺栓孔
Z3050
先 扩 2— Φ 12mm 螺 栓 孔,再 扩 2— Φ 13mm 深 19mm 螺栓孔并倒角
Z3050
保 证 两 端 面 平 稳,精 磨 大 小 头 两 端,还
需要让大端面宽度控制在
mm
M7130
5
镗 根据基面位置定位,中心距为 205mm
零件成为废料。 (2)进给量的选择 :精加工进给量主要看材料的表面粗糙
度数值量是多少,如果进给量很大,虽然有利于快速的进行加 工,但是加工出来的产品质量无法得到有效保障 [2]。
(3)切削速度的选择 :切削速度提升,其变形将会适当减小,
不会造成体系产生过多的积屑瘤和鳞刺。因此,一般选择一些性 能较好,结构合理的刀具,这样有利于提升切削速度,在保证刀
连杆加工工艺及夹具设计带CAD

连杆加工工艺及夹具设计目录摘要第一章汽车连杆加工工艺1.1 连杆旳构造特点1.2 连杆旳主要技术要求1.2.1 大、小头孔旳尺寸精度、形状精度1.2.2 大、小头孔轴心线在两个相互垂直方向旳平行度1.2.3 大、小头孔中心距1.2.4 连杆大头孔两端面对大头孔中心线旳垂直度1.2.5 大、小头孔两端面旳技术要求1.2.6 螺栓孔旳技术要求1.2.7 有关结合面旳技术要求1.3连杆旳材料和毛坯1.4连杆旳机械加工工艺过程1.5 连杆旳机械加工工艺过程分析1.5.1 工艺过程旳安排1.5.2 定位基准旳选择1.5.3 拟定合理旳夹紧措施1.5.4 连杆两端面旳加工1.5.5 连杆大、小头孔旳加工1.5.6 连杆螺栓孔旳加工1.5.7 连杆体与连杆盖旳铣动工序1.5.8 大头侧面旳加工1.6 连杆加工工艺设计应考虑旳问题1.6.1工序安排1.6.2定位基准1.6.3夹具使用1.7 切削用量旳选择原则1.7.1 粗加工时切削用量旳选择原则1.7.2 精加工时切削用量旳选择原则1.8 拟定各工序旳加工余量、计算工序尺寸及公差1.8.1 拟定加工余量1.8.2 拟定工序尺寸及其公差1.9 计算工艺尺寸链1.9.1 连杆盖旳卡瓦槽旳计算1.9.2 连杆体旳卡瓦槽旳计算1.10 工时定额旳计算1.10.1 铣连杆大小头平面1.10.2 粗磨大小头平面1.10.3 加工小头孔1.10.4 铣大头两侧面1.10.5、扩大头孔1.10.6 铣开连杆体和盖1.10.7 加工连杆体1.10.8 铣、磨连杆盖结合面1.10.9 铣、钻、镗连杆总成体1.10.10 粗镗大头孔1.10.11 大头孔两端倒角1.10.12精磨大小头两平面1.10.13 半精镗大头孔及精镗小头孔1.10.14精镗大头孔1.10.16 小头孔两端倒角1.10.17 镗小头孔衬套1.10.18 珩磨大头孔1.11 连杆旳检验1.11.1 观察外表缺陷及目测表面粗糙度1.11.2 连杆大头孔圆柱度旳检验1.11.3 连杆体、连杆上盖对大头孔中心线旳对称度旳检验1.11.4 连杆大小头孔平行度旳检验1.11.5 连杆螺钉孔与结合面垂直度旳检验第二章夹具设计2.1 铣剖分面夹具设计2.1.1问题旳指出2.1.2 夹具设计1) 定位基准旳选择2) 夹紧方案3) 夹详细设计4) 切削力及夹紧力旳计算5) 定位误差分析2.2 扩大头孔夹具2.2.1 问题旳指出2.2.2 夹具设计1) 定位基准旳选择2) 夹紧方案3) 夹详细设计4) 切削力及夹紧力旳计算5) 定位误差分析结束语:参照文件:附件图纸摘要连杆是柴油机旳主要传动件之一,本文主要论述了连杆旳加工工艺及其夹具设计。
连杆加工工艺规程及夹具方案设计书(工序卡 CAD原图=完整)
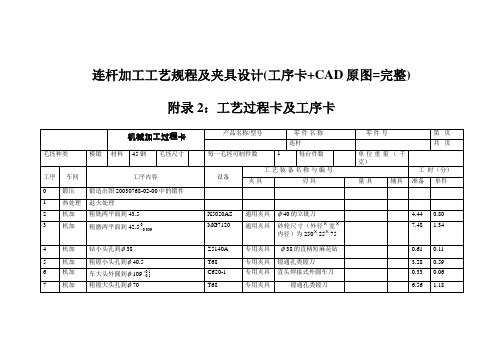
连杆加工工艺规程及夹具设计(工序卡+CAD原图=完整) 附录2:工艺过程卡及工序卡
机械加工工序卡加工简图及技术条件:
机械加工工序卡加工简图及技术条件:
机械加工工序卡加工简图及技术条件:
机械加工工序卡
机械加工工序卡加工简图及技术条件:
机械加工工序卡加工简图及技术条件:
机械加工工序卡加工简图及技术条件:
机械加工工序卡加工简图及技术条件:
机械加工工序卡加工简图及技术条件:
机械加工工序卡加工简图及技术条件:
机械加工工序卡加工简图及技术条件:
机械加工工序卡加工简图及技术条件:。
连杆加工工艺及夹具设计毕业设计
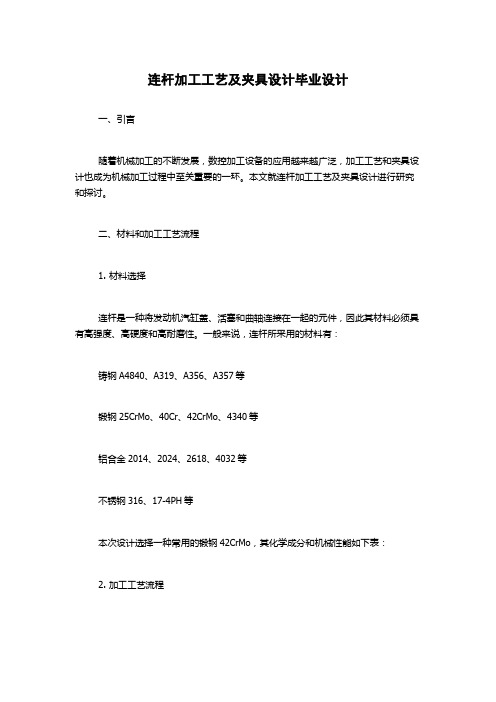
连杆加工工艺及夹具设计毕业设计一、引言随着机械加工的不断发展,数控加工设备的应用越来越广泛,加工工艺和夹具设计也成为机械加工过程中至关重要的一环。
本文就连杆加工工艺及夹具设计进行研究和探讨。
二、材料和加工工艺流程1. 材料选择连杆是一种将发动机汽缸盖、活塞和曲轴连接在一起的元件,因此其材料必须具有高强度、高硬度和高耐磨性。
一般来说,连杆所采用的材料有:铸钢A4840、A319、A356、A357等锻钢25CrMo、40Cr、42CrMo、4340等铝合金2014、2024、2618、4032等不锈钢316、17-4PH等本次设计选择一种常用的锻钢42CrMo,其化学成分和机械性能如下表:2. 加工工艺流程锻造加工是制造连杆的常用工艺,它能够保证材料的均匀性、造型的精度和表面光滑度。
加工流程如下:3. 热处理工艺将锻好的连杆进行调质处理,以提高其硬度和强度,并保证其在使用过程中的可靠性。
热处理工艺如下:4. 精机加工工艺进行车、铣、钻、镗、磨等加工,以保证其精度和表面质量。
加工工艺如下:5. 检测工艺检测加工后的连杆尺寸和表面质量,以保证其满足设计要求。
检测工艺如下:三、夹具设计1. 设计目的针对连杆加工的特点,设计一种适用的夹具,实现其加工过程的自动化、标准化和高效化,提高生产效率和质量。
2. 夹具设计要求稳定性:夹具必须牢固而稳定,以免影响加工精度和安全性。
适用性:夹具必须适用于不同类型的连杆,以实现高度的通用性。
易用性:夹具的操作和维护必须简便、便捷,以提高生产效率和操作员工作舒适度。
3. 夹具设计方案夹具采用定位销和压板两种组合结构,用于夹持连杆内孔和外圆,其结构示意图如下:在加工过程中,通过螺旋压紧装置将夹具紧固在工作台上,然后使用气缸控制压板的升降和紧缩,完成对连杆的夹持。
四、结论本文针对连杆加工工艺及夹具设计进行了研究和探讨,设计了一套适用于锻造加工的加工流程,并提出了一种稳定、适用、易用的夹具设计方案。
球头连杆加工工艺及钻30孔夹具设计
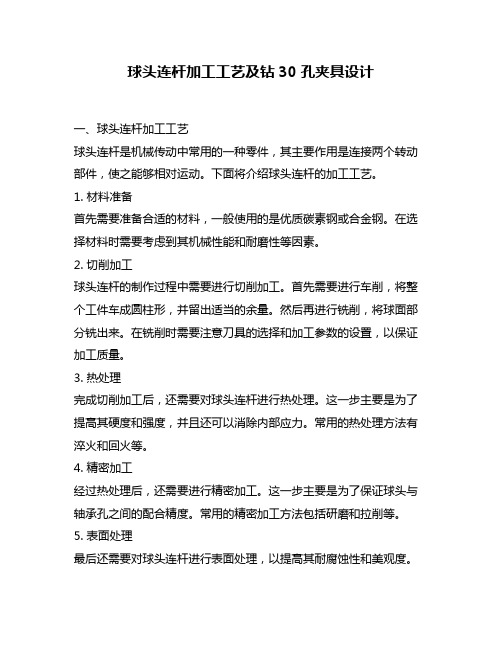
球头连杆加工工艺及钻30孔夹具设计一、球头连杆加工工艺球头连杆是机械传动中常用的一种零件,其主要作用是连接两个转动部件,使之能够相对运动。
下面将介绍球头连杆的加工工艺。
1. 材料准备首先需要准备合适的材料,一般使用的是优质碳素钢或合金钢。
在选择材料时需要考虑到其机械性能和耐磨性等因素。
2. 切削加工球头连杆的制作过程中需要进行切削加工。
首先需要进行车削,将整个工件车成圆柱形,并留出适当的余量。
然后再进行铣削,将球面部分铣出来。
在铣削时需要注意刀具的选择和加工参数的设置,以保证加工质量。
3. 热处理完成切削加工后,还需要对球头连杆进行热处理。
这一步主要是为了提高其硬度和强度,并且还可以消除内部应力。
常用的热处理方法有淬火和回火等。
4. 精密加工经过热处理后,还需要进行精密加工。
这一步主要是为了保证球头与轴承孔之间的配合精度。
常用的精密加工方法包括研磨和拉削等。
5. 表面处理最后还需要对球头连杆进行表面处理,以提高其耐腐蚀性和美观度。
常用的表面处理方法有镀铬、喷涂和电镀等。
二、钻30孔夹具设计为了方便球头连杆的加工,需要设计一种钻30孔夹具,下面将介绍其设计过程。
1. 设计要求首先需要明确设计要求,包括夹具的尺寸、夹紧力和稳定性等。
在确定这些要求时需要考虑到球头连杆的形状和大小等因素。
2. 夹具结构设计根据设计要求,可以开始进行夹具结构设计。
一般采用T型槽结构,其中一个槽用于固定钻头,另一个槽用于固定球头连杆。
在确定槽口尺寸时需要考虑到球头连杆的直径,并在槽口内部设置适当的垫片以保证夹紧力均匀。
3. 材料选择选择合适的材料也是十分重要的一步。
一般使用优质钢材或铝合金等材料制作夹具。
在选择材料时需要考虑到其强度和耐磨性等因素。
4. 制造加工完成夹具结构设计后,还需要进行制造加工。
首先需要进行铣削和钻孔等切削加工,然后再进行表面处理和组装等工序。
5. 夹具调试最后还需要对夹具进行调试,以保证其夹紧力和稳定性。
连杆的机械加工工艺及夹具设计(含图纸)
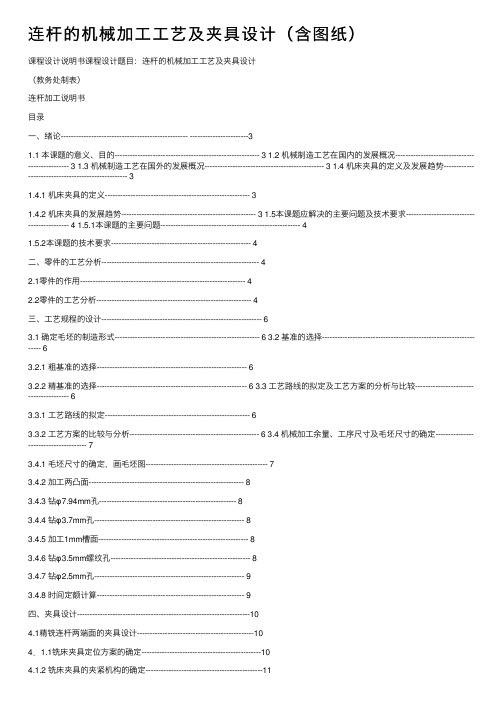
连杆的机械加⼯⼯艺及夹具设计(含图纸)课程设计说明书课程设计题⽬:连杆的机械加⼯⼯艺及夹具设计(教务处制表)连杆加⼯说明书⽬录⼀、绪论-------------------------------------------------- -----------------------31.1 本课题的意义、⽬的--------------------------------------------------------- 3 1.2 机械制造⼯艺在国内的发展概况----------------------------------------------- 3 1.3 机械制造⼯艺在国外的发展概况----------------------------------------------- 3 1.4 机床夹具的定义及发展趋势--------------------------------------------------- 31.4.1 机床夹具的定义--------------------------------------------------------- 31.4.2 机床夹具的发展趋势----------------------------------------------------- 3 1.5本课题应解决的主要问题及技术要求------------------------------------------- 4 1.5.1本课题的主要问题------------------------------------------------------- 41.5.2本课题的技术要求------------------------------------------------------- 4⼆、零件的⼯艺分析-------------------------------------------------------------- 42.1零件的作⽤----------------------------------------------------------------- 42.2零件的⼯艺分析------------------------------------------------------------- 4三、⼯艺规程的设计--------------------------------------------------------------- 63.1 确定⽑坯的制造形式--------------------------------------------------------- 6 3.2 基准的选择----------------------------------------------------------------- 63.2.1 粗基准的选择----------------------------------------------------------- 63.2.2 精基准的选择----------------------------------------------------------- 6 3.3 ⼯艺路线的拟定及⼯艺⽅案的分析与⽐较--------------------------------------- 63.3.1 ⼯艺路线的拟定--------------------------------------------------------- 63.3.2 ⼯艺⽅案的⽐较与分析--------------------------------------------------- 6 3.4 机械加⼯余量、⼯序尺⼨及⽑坯尺⼨的确定-------------------------------------- 73.4.1 ⽑坯尺⼨的确定,画⽑坯图------------------------------------------------ 73.4.2 加⼯两凸⾯------------------------------------------------------------- 83.4.3 钻φ7.94mm孔------------------------------------------------------ 83.4.4 钻φ3.7mm孔----------------------------------------------------------- 83.4.5 加⼯1mm槽⾯----------------------------------------------------------- 83.4.6 钻φ3.5mm螺纹孔------------------------------------------------------- 83.4.7 钻φ2.5mm孔----------------------------------------------------------- 93.4.8 时间定额计算---------------------------------------------------------- 9四、夹具设计--------------------------------------------------------------------104.1精铣连杆两端⾯的夹具设计----------------------------------------------104.1.1铣床夹具定位⽅案的确定-----------------------------------------------104.1.2 铣床夹具的夹紧机构的确定----------------------------------------------114.1.3铣床夹具对⼑装置的确定------------------------------------------------114.1.4 铣床夹具的结构分析----------------------------------------------------11五、总结----------------------------------------------------------------------- 13六、参考⽂献------------------------------------------------------------------- 14⼀、绪论1.1 本课题的意义、⽬的机械制造业是⼀个古⽼⽽永远充满⽣命⼒的⾏业。
- 1、下载文档前请自行甄别文档内容的完整性,平台不提供额外的编辑、内容补充、找答案等附加服务。
- 2、"仅部分预览"的文档,不可在线预览部分如存在完整性等问题,可反馈申请退款(可完整预览的文档不适用该条件!)。
- 3、如文档侵犯您的权益,请联系客服反馈,我们会尽快为您处理(人工客服工作时间:9:00-18:30)。
1.3连杆的材料和毛坯
1.4连杆的机械加工工艺过程
1.5连杆的机械加工工艺过程分析
1.5.1工艺过程的安排
1.5.2定位基准的选择
1.5.3确定合理的夹紧方法
1.5.4连杆两端面的加工
1.5.5连杆大、小头孔的加工
1.5.6连杆螺栓孔的加工
1.5.7连杆体与连杆盖的铣开工序
m;大头孔的圆柱度公差为0.012mm,小头孔公差等级为IT8,表面粗糙度Ra应不大于3.2μm。小头压衬套的底孔的圆柱度公差为0.0025mm,素线平行度公差为0.04/100mm。
1.2.2
两孔轴心线在连杆轴线方向的平行度误差会使活塞在汽缸中倾斜,从而造成汽缸壁磨损不均匀,同时使曲轴的连杆轴颈产生边缘磨损,所以两孔轴心线在连杆轴线方向的平行度公差较小;而两孔轴心线在垂直于连杆轴线方向的平行度误差对不均匀磨损影响较小,因而其公差值较大。两孔轴心线在连杆的轴线方向的平行度在100mm长度上公差为0.04mm;在垂直与连杆轴心线方向的平行度在100mm长度上公差为0.06mm。
1.9计算工艺尺寸链
1.9.1连杆盖的卡瓦槽的计算
1.9.2连杆体的卡瓦槽的计算
1.10工时定额的计算
1.10.1铣连杆大小头平面
1.10.2粗磨大小头平面
1.10.3加工小头孔
1.10.4铣大头两侧面
1.10.5、扩大头孔
1.10.6铣开连杆体和盖
1.10.7加工连杆体
1.10.8铣、磨连杆盖结合面
1.2.3
大小头孔的中心距影响到汽缸的压缩比,即影响到发动机的效率,所以规定了比较高的要求:190±0.05mm。
1.2.4
连杆大头孔两端面对大头孔中心线的垂直度,影响到轴瓦的安装和磨损,甚至引起烧伤;所以对它也提出了一定的要求:规定其垂直度公差等级应不低于IT9(大头孔两端面对大头孔的轴心线的垂直度在100mm长度上公差为0.08mm)。
第一章汽车连杆加工工艺
1.1 连杆的结构特点
连杆是汽车发动机中的主要传动部件之一,它在柴油机中,把作用于活塞顶面的膨胀的压力传递给曲轴,又受曲轴的驱动而带动活塞压缩气缸中的气体。连杆在工作中承受着急剧变化的动载荷。连杆由连杆体及连杆盖两部分组成。连杆体及连杆盖上的大头孔用螺栓和螺母与曲轴装在一起。为了减少磨损和便于维修,连杆的大头孔内装有薄壁金属轴瓦。轴瓦有钢质的底,底的内表面浇有一层耐磨巴氏合金轴瓦金属。在连杆体大头和连杆盖之间有一组垫片,可以用来补偿轴瓦的磨损。连杆小头用活塞销与活塞连接。小头孔内压入青铜衬套,以减少小头孔与活塞销的磨损,同时便于在磨损后进行修理和更换。
1.2 连杆的主要技术要求
连杆上需进行机械加工的主要表面为:大、小头孔及其两端面,连杆体与连杆盖的结合面及连杆螺栓定位孔等。连杆总成的主要技术要求(图1-1)如下。
连杆总成图(1—1)
1.2.1
为了使大头孔与轴瓦及曲轴、小头孔与活塞销能密切配合,减少冲击的不良影响和便于传热。大头孔公差等级为IT6,表面粗糙度Ra应不大于0.4μ
1.11.2连杆大头孔圆柱度的检验
1.11.3连杆体、连杆上盖对大头孔中心线的对称度的检验
1.11.4连杆大小头孔平行度的检验
1.11.5连杆螺钉孔与结合面垂直度的检验
第二章夹具设计
2.1铣剖分面夹具设计
2.1.1问题的指出
2.1.2夹具设计
1)定位基准的选择
2)夹紧方案
3)夹具体设计
4)切削力及夹紧力的计算
在发动机工作过程中,连杆受膨胀气体交变压力的作用和惯性力的作用,连杆除应具有足够的强度和刚度外,还应尽量减小连杆自身的质量,以减小惯性力的作用。连杆杆身一般都采用从大头到小头逐步变小的工字型截面形状。为了保证发动机运转均衡,同一发动机中各连杆的质量不能相差太大,因此,在连杆部件的大、小头两端设置了去不平衡质量的凸块,以便在称量后切除不平衡质量。连杆大、小头两端对称分布在连杆中截面的两侧。考虑到装夹、安放、搬运等要求,连杆大、小头的厚度相等(基本尺寸相同)。在连杆小头的顶端设有油孔(或油槽),发动机工作时,依靠曲轴的高速转
动,把气缸体下部的润滑油飞溅到小头顶端的油孔内,以润滑连杆小头衬套与活塞销之间的摆动运动副。
连杆的作用是把活塞和曲轴联接起来,使活塞的往复直线运动变为曲柄的回转运动,以输出动力。因此,连杆的加工精度将直接影响柴油机的性能,而工艺的选择又是直接影响精度的主要因素。反映连杆精度的参数主要有5个:(1)连杆大端中心面和小端中心面相对连杆杆身中心面的对称度;(2)连杆大、小头孔中心距尺寸精度;(3)连杆大、小头孔平行度;(4)连杆大、小头孔尺寸精度、形状精度;(5)连杆大头螺栓孔与接合面的垂直度。
1.5.8大头侧面的加工
1.6连杆加工工艺设计应考虑的问题
1.6.1工序安排
1.6.2定位基准
1.6.3夹具使用
1.7切削用量的选择原则
1.7.1粗加工时切削用量的选择原则
1.7.2精加工时切削用量的选择原则
1.8确定各工序的加工余量、计算工序尺寸及公差
1.8.1确定加工余量
1.8.2确定工序尺寸及其公差
5)定位误差分析
2.2扩大头孔夹具
2.2.1问题的指出
2.2.2夹具设计
1)定位基准的选择
2)夹紧方案
3)夹具体设计
4)切削力及夹紧力的计算
5)定位误差分析
结束语:
参考文献:
附件图纸
摘要
连杆是柴油机的主要传动件之一,本文主要论述了连杆的加工工艺及其夹具设计。连杆的尺寸精度、形状精度以及位置精度的要求都很高,而连杆的刚性比较差,容易产生变形,因此在安排工艺过程时,就需要把各主要表面的粗精加工工序分开。逐步减少加工余量、切削力及内应力的作用,并修正加工后的变形,就能最后达到零件的技术要求。
连杆加工工艺及夹具设计
摘要
第一章汽车连杆加工工艺
1.1连杆的结构特点
1.2连杆的主要技术要求
1.2.1大、小头孔的尺寸精度、形状精度
1.2.2大、小头孔轴心线在两个互相垂直方向的平行度
1.2.3大、小头孔中心距
1.2.4连杆大头孔两端面对大头孔中心线的垂直度
1.2.5大、小头孔两端面的技术要求
1.2.6螺栓孔的技ቤተ መጻሕፍቲ ባይዱ要求
1.10.9铣、钻、镗连杆总成体
1.10.10粗镗大头孔
1.10.11大头孔两端倒角
1.10.12精磨大小头两平面
1.10.13半精镗大头孔及精镗小头孔
1.10.14精镗大头孔
1.10.16小头孔两端倒角
1.10.17镗小头孔衬套
1.10.18珩磨大头孔
1.11连杆的检验
1.11.1观察外表缺陷及目测表面粗糙度