铝及铝合金导电氧化浅谈
铝和铝合金阳极氧化后能导电吗?

铝和铝合⾦阳极氧化后能导电吗?导电原理:某物质的原⼦的价电⼦较少,外电⼦层不饱满,存在着电⼦空位,在连成回路的电⼦空位间有电压差,形成换位移动,形成电流。
阳极氧化(anodize)⽣成的膜是不导电的;化学氧化(Chemical oxidation)的膜是导电的。
这两种⽅式都是铝和铝合⾦防腐蚀处理的常⽤⽅法。
1.阳极氧化阳极氧化是使⾦属在给定电解质中作为阳极,通过⼀定的电流密度,在其表⾯形成⼀层氧化物覆盖层的过程。
有⾊⾦属或其合⾦(如铝、镁及其合⾦等)都可进⾏阳极氧化处理。
阳极氧化需要的时间为⼏⼗分钟。
常⽤电解质为硫酸和铬酸,草酸因成本⾼,⽤的⽐较少。
阳极氧化处理后在铝材表⾯⽣成的氧化膜具有绝缘性和多孔性,外观⽆⾊透明。
然后可以进⼀步利⽤膜的微孔吸附能⼒强做发⿊、彩虹化处理。
阳极氧化形成的氧化铝薄层,其厚度为5~20微⽶,阳极氧化后提⾼了其硬度和耐磨性,不导电,击穿电压达2000V,增强了抗腐蚀性能。
适⽤于潮湿地区的室内电⼦产品中结构件的防护处理。
硬质阳极氧化膜可达60~200微⽶。
在ω=0.03NaCl盐雾中经⼏千⼩时不腐蚀,并且耐磨。
氧化膜薄层中具有⼤量的微孔,可吸附各种润滑剂,适⽤于制造发动机⽓缸或其他耐磨零件和室外电⼦产品结构件的防护处理。
2.化学氧化化学氧化(Chemical oxidation)是通过化学处理使⾦属表⾯形成氧化膜的过程。
化学氧化所⽤化学溶液都是含有氧化剂的碱性溶液。
例如铝及铝合⾦⼀般⽤添加铬酸盐、硅酸盐、磷酸盐的碳酸钠溶液,铜及铜合⾦⽤含有氧化剂的苛性钠溶液。
化学氧化不需要通电,⽽只需要在碱性溶液⾥浸⼏⼗秒泡就⾏了,它是⼀种纯化学反应。
氧化⽣成的膜仅仅0.01—5微⽶左右。
化学氧化耐磨性、耐腐蚀性均⽐阳极氧化差很多。
适⽤于环境良好的室内电⼦产品,如叉指形散热器、⽀架,以及需要喷涂前的结构件预处理。
3.铝和铝合⾦的关联表⾯处理1).表⾯着⾊处理阳极氧化膜着⾊⽅法分为三类,即吸附染⾊法,整体发⾊法和电解着⾊法,可以着⾊种类较多。
铝及铝合金阳极氧化
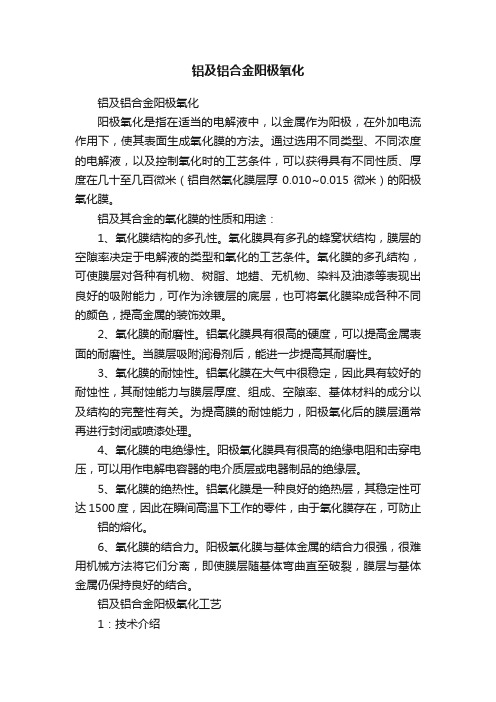
铝及铝合金阳极氧化铝及铝合金阳极氧化阳极氧化是指在适当的电解液中,以金属作为阳极,在外加电流作用下,使其表面生成氧化膜的方法。
通过选用不同类型、不同浓度的电解液,以及控制氧化时的工艺条件,可以获得具有不同性质、厚度在几十至几百微米(铝自然氧化膜层厚0.010~0.015微米)的阳极氧化膜。
铝及其合金的氧化膜的性质和用途:1、氧化膜结构的多孔性。
氧化膜具有多孔的蜂窝状结构,膜层的空隙率决定于电解液的类型和氧化的工艺条件。
氧化膜的多孔结构,可使膜层对各种有机物、树脂、地蜡、无机物、染料及油漆等表现出良好的吸附能力,可作为涂镀层的底层,也可将氧化膜染成各种不同的颜色,提高金属的装饰效果。
2、氧化膜的耐磨性。
铝氧化膜具有很高的硬度,可以提高金属表面的耐磨性。
当膜层吸附润滑剂后,能进一步提高其耐磨性。
3、氧化膜的耐蚀性。
铝氧化膜在大气中很稳定,因此具有较好的耐蚀性,其耐蚀能力与膜层厚度、组成、空隙率、基体材料的成分以及结构的完整性有关。
为提高膜的耐蚀能力,阳极氧化后的膜层通常再进行封闭或喷漆处理。
4、氧化膜的电绝缘性。
阳极氧化膜具有很高的绝缘电阻和击穿电压,可以用作电解电容器的电介质层或电器制品的绝缘层。
5、氧化膜的绝热性。
铝氧化膜是一种良好的绝热层,其稳定性可达1500度,因此在瞬间高温下工作的零件,由于氧化膜存在,可防止铝的熔化。
6、氧化膜的结合力。
阳极氧化膜与基体金属的结合力很强,很难用机械方法将它们分离,即使膜层随基体弯曲直至破裂,膜层与基体金属仍保持良好的结合。
铝及铝合金阳极氧化工艺1:技术介绍铝及其合金在相应的电解液和特殊的工艺条件下,由于外加电流作用,在铝制品表面产生一层氧化膜的工艺过程。
封孔后的铝氧化膜具有绝缘性,极大的增加铝制品的硬度,具有优异耐磨性,RCA纸带测试可以轻松耐磨300圈以上,颜色品种繁多,客户可以依照PANTONE色号选择,具有极强的外观装饰性,具有良好的抗人工汗水和盐雾的能力。
6063 铝合金 氧化 导电
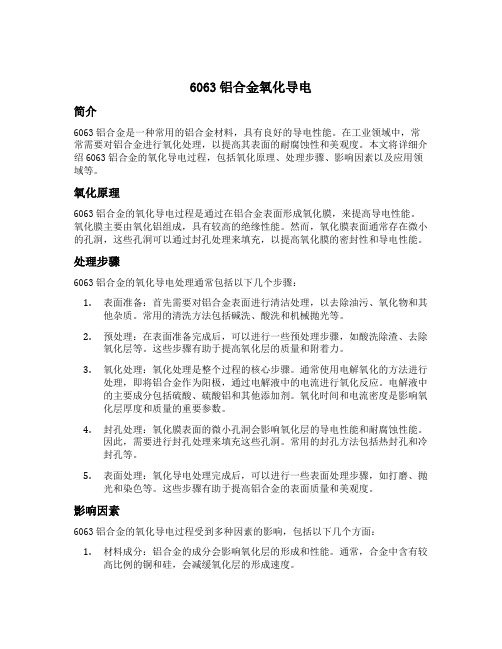
6063铝合金氧化导电简介6063铝合金是一种常用的铝合金材料,具有良好的导电性能。
在工业领域中,常常需要对铝合金进行氧化处理,以提高其表面的耐腐蚀性和美观度。
本文将详细介绍6063铝合金的氧化导电过程,包括氧化原理、处理步骤、影响因素以及应用领域等。
氧化原理6063铝合金的氧化导电过程是通过在铝合金表面形成氧化膜,来提高导电性能。
氧化膜主要由氧化铝组成,具有较高的绝缘性能。
然而,氧化膜表面通常存在微小的孔洞,这些孔洞可以通过封孔处理来填充,以提高氧化膜的密封性和导电性能。
处理步骤6063铝合金的氧化导电处理通常包括以下几个步骤:1.表面准备:首先需要对铝合金表面进行清洁处理,以去除油污、氧化物和其他杂质。
常用的清洗方法包括碱洗、酸洗和机械抛光等。
2.预处理:在表面准备完成后,可以进行一些预处理步骤,如酸洗除渣、去除氧化层等。
这些步骤有助于提高氧化层的质量和附着力。
3.氧化处理:氧化处理是整个过程的核心步骤。
通常使用电解氧化的方法进行处理,即将铝合金作为阳极,通过电解液中的电流进行氧化反应。
电解液中的主要成分包括硫酸、硫酸铝和其他添加剂。
氧化时间和电流密度是影响氧化层厚度和质量的重要参数。
4.封孔处理:氧化膜表面的微小孔洞会影响氧化层的导电性能和耐腐蚀性能。
因此,需要进行封孔处理来填充这些孔洞。
常用的封孔方法包括热封孔和冷封孔等。
5.表面处理:氧化导电处理完成后,可以进行一些表面处理步骤,如打磨、抛光和染色等。
这些步骤有助于提高铝合金的表面质量和美观度。
影响因素6063铝合金的氧化导电过程受到多种因素的影响,包括以下几个方面:1.材料成分:铝合金的成分会影响氧化层的形成和性能。
通常,合金中含有较高比例的铜和硅,会减缓氧化层的形成速度。
2.氧化条件:氧化时间和电流密度是影响氧化层厚度和质量的重要参数。
较长的氧化时间和较高的电流密度会导致较厚的氧化层,但也可能降低氧化层的质量。
3.温度:氧化过程中的温度也会影响氧化层的形成和性能。
6061铝导电氧化

6061铝导电氧化简介6061铝是一种常用的铝合金材料,具有良好的强度、耐腐蚀性和导电性能。
导电氧化是一种将金属表面转化为氧化物以提高其导电性能的表面处理方法。
本文将详细介绍6061铝导电氧化的原理、工艺流程和应用领域。
原理导电氧化是通过在金属表面形成一层致密的氧化物膜来提高其导电性能。
对于6061铝来说,其主要成分为铝、镁和硅,其中铝是最主要的成分。
在导电氧化过程中,铝与氧发生反应生成Al2O3(二氧化三铝)膜。
该膜具有以下特点: - 致密性:Al2O3膜具有非常致密的结构,可以有效地阻止外界物质进入金属内部。
- 硬度:Al2O3膜硬度较高,可以提供一定的耐磨损性能。
- 良好的绝缘性:由于Al2O3膜具有良好的绝缘性能,使得6061铝在导电过程中不易发生电蚀。
工艺流程6061铝导电氧化的工艺流程包括以下几个步骤:1.表面处理:首先需要对6061铝表面进行清洁处理,以去除表面的油污和杂质。
常用的方法包括碱洗、酸洗或机械处理等。
2.阳极化:将清洁后的6061铝作为阳极,放入含有适量电解质(如硫酸、硫酸铜等)的电解槽中。
将阳极与阴极连接,通过外加直流电源施加一定的电压,使得阴极为6061铝表面形成氧化反应。
3.氧化反应:在施加一定电压后,金属表面开始发生氧化反应。
反应过程中,金属离子和氧离子结合形成Al2O3膜。
4.深度控制:根据需要调整工艺参数(如电压、时间等)来控制氧化膜的厚度。
较浅的氧化膜可以提供更好的导电性能,而较厚的氧化膜则具有更好的耐磨性能。
5.清洗和干燥:完成氧化反应后,需要对6061铝进行清洗和干燥处理,以去除残留的电解质和水分。
应用领域6061铝导电氧化具有良好的导电性能和耐腐蚀性能,广泛应用于以下领域:1.电子产品:6061铝导电氧化后可用于制作电子元件、散热器等。
其导电性能可以保证信号传输的稳定性,而耐腐蚀性能可以提高产品的使用寿命。
2.汽车工业:6061铝导电氧化后可应用于汽车零部件制造。
铝合金导电氧化导电检测标准

铝合金导电氧化导电检测标准铝合金导电氧化导电检测标准导电性能在铝合金产品的生产和应用中起着举足轻重的作用。
铝合金导电氧化导电检测标准则是评估铝合金导电性能的重要依据,对于确保铝合金产品的质量和可靠性具有重要意义。
本文将按照从浅入深的方式,对铝合金导电氧化导电检测标准进行全面评估,并结合个人观点和理解,撰写一篇有价值的文章,以便更好地理解这一主题。
一、导电性能的重要性铝合金产品在电子、航空航天、交通运输等领域中应用广泛,其导电性能直接影响着产品的功能和稳定性。
对铝合金产品的导电性能进行准确的检测和评估至关重要。
二、铝合金导电氧化导电检测标准概述铝合金导电氧化导电检测标准是针对铝合金产品导电性能进行检测和评估的一套标准体系,包括导电氧化膜的形成、厚度、导电性能、耐蚀性等多个方面。
这些标准旨在确保铝合金产品具有良好的导电性能和稳定的氧化层,从而满足产品在不同领域的使用要求。
三、铝合金导电氧化导电检测标准的内容和原理1.导电氧化膜的形成:导电氧化膜是铝合金产品表面形成的一层氧化物膜,对于产品的导电性能起着关键作用。
根据标准,导电氧化膜的形成应符合一定的均匀性和密度要求,以确保电流能够顺利传导。
2.导电氧化膜的厚度:导电氧化膜的厚度直接影响着产品的导电性能,标准对导电氧化膜的厚度进行了严格的要求和检测方法,以确保产品具有稳定和可靠的导电性能。
3.导电性能:导电性能是评价铝合金产品导电能力的重要指标,标准规定了导电性能的测试方法和要求,以确保产品在电流传导过程中具有良好的性能表现。
4.耐蚀性:铝合金产品在不同的环境中可能面临腐蚀和氧化的问题,耐蚀性是检测产品稳定性的重要指标之一。
标准对铝合金产品的耐蚀性进行了严格的测试要求,以确保产品能够在不同环境下保持良好的导电性能。
四、个人观点和理解铝合金导电氧化导电检测标准的制定和执行,对于提升铝合金产品的质量和可靠性具有积极的意义。
通过严格遵守这些标准,可以确保铝合金产品具有良好的导电性能和稳定的氧化层,从而满足不同领域的使用需求。
铝及铝合金导电氧化浅谈
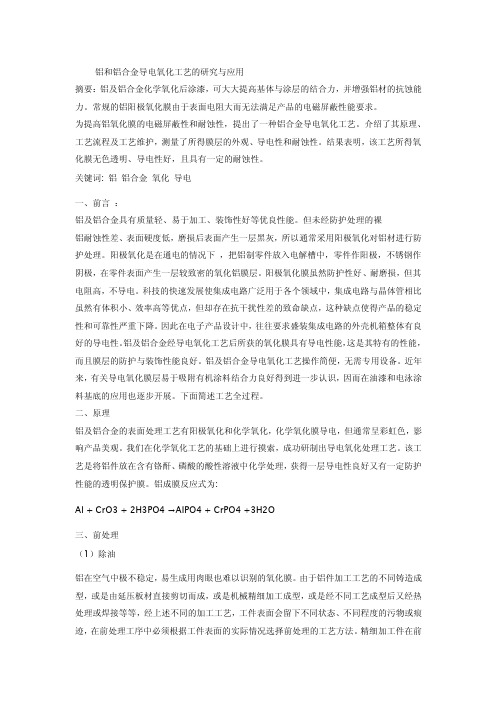
铝和铝合金导电氧化工艺的研究与应用摘要:铝及铝合金化学氧化后涂漆,可大大提高基体与涂层的结合力,并增强铝材的抗蚀能力。
常规的铝阳极氧化膜由于表面电阻大而无法满足产品的电磁屏蔽性能要求。
为提高铝氧化膜的电磁屏蔽性和耐蚀性,提出了一种铝合金导电氧化工艺。
介绍了其原理、工艺流程及工艺维护,测量了所得膜层的外观、导电性和耐蚀性。
结果表明,该工艺所得氧化膜无色透明、导电性好,且具有一定的耐蚀性。
关键词: 铝铝合金氧化导电一、前言:铝及铝合金具有质量轻、易于加工、装饰性好等优良性能。
但未经防护处理的裸铝耐蚀性差、表面硬度低,磨损后表面产生一层黑灰,所以通常采用阳极氧化对铝材进行防护处理。
阳极氧化是在通电的情况下,把铝制零件放入电解槽中,零件作阳极,不锈钢作阴极,在零件表面产生一层较致密的氧化铝膜层。
阳极氧化膜虽然防护性好、耐磨损,但其电阻高,不导电。
科技的快速发展使集成电路广泛用于各个领域中,集成电路与晶体管相比虽然有体积小、效率高等优点,但却存在抗干扰性差的致命缺点,这种缺点使得产品的稳定性和可靠性严重下降。
因此在电子产品设计中,往往要求盛装集成电路的外壳机箱整体有良好的导电性。
铝及铝合金经导电氧化工艺后所获的氧化膜具有导电性能,这是其特有的性能,而且膜层的防护与装饰性能良好。
铝及铝合金导电氧化工艺操作简便,无需专用设备。
近年来,有关导电氧化膜层易于吸附有机涂料结合力良好得到进一步认识,因而在油漆和电泳涂料基底的应用也逐步开展。
下面简述工艺全过程。
二、原理铝及铝合金的表面处理工艺有阳极氧化和化学氧化,化学氧化膜导电,但通常呈彩虹色,影响产品美观。
我们在化学氧化工艺的基础上进行摸索,成功研制出导电氧化处理工艺。
该工艺是将铝件放在含有铬酐、磷酸的酸性溶液中化学处理,获得一层导电性良好又有一定防护性能的透明保护膜。
铝成膜反应式为:Al + CrO3 + 2H3PO4 →AlPO4 + CrPO4 +3H2O三、前处理(1)除油铝在空气中极不稳定,易生成用肉眼也难以识别的氧化膜。
铝合金化学导电氧化最佳配方

铝合金化学导电氧化最佳配方铝合金化学导电氧化,这听起来好像是个高大上的话题,其实说白了就是让铝合金表面变得更耐用、更好看,同时还能提升它的导电性。
哎,咱们先把这话说清楚。
铝合金就是那种轻便又结实的金属材料,常常用在飞机、汽车,还有各种家电上。
可惜了,原本这么好的材料,要是表面没处理好,时间一长就容易氧化、变色,真是可惜。
想要让铝合金焕发第二春,化学导电氧化就是一个好办法,听起来是不是就觉得特别牛?什么是化学导电氧化呢?这可不是说随便往铝合金上撒点东西就行的哦。
这里面可是有一套讲究的。
简单来说,就是利用化学反应让铝合金表面形成一层保护膜。
这层膜不仅可以抵抗腐蚀,还能增强导电性,真是一举两得。
想象一下,你家的电器用上这样的铝合金,是不是就像是给它穿上了一层铠甲?再也不用担心外面的环境会对它造成伤害,心里可踏实多了。
咱们接下来聊聊最佳配方,这可是关键中的关键。
咱们得选择适合的化学药剂。
这可不是随便买瓶什么药水就能搞定的,得根据铝合金的成分和要求来定。
一般来说,硫酸铝和氟化铝都是不错的选择。
这两种材料能帮助铝合金形成一层致密的氧化膜,效果杠杠的。
哎,这里边可得注意浓度问题,浓度高了,反应速度快,但也容易损伤铝合金的表面;浓度低了,反应太慢,效果也不明显,真是有点儿让人头疼。
然后就是温度和时间,这俩也是不能忽视的因素。
温度过高,化学反应迅速,但容易让膜层不均匀,甚至起泡;温度太低,又反应慢,膜层太薄,根本达不到预期的效果。
一般来说,控制在20到30摄氏度之间最为合适。
时间方面,通常在20到60分钟之间,具体还得根据铝合金的厚度和预期效果来调整,真是个细致活儿啊。
咱们还得考虑到后处理。
化学氧化完了,可不是就完事了,后续处理也得跟上。
洗涤、干燥、封闭这些步骤不能少,这样才能确保膜层的质量。
很多人以为这步骤随便搞搞就行,实际上,细节决定成败,做得好,膜层才能更加耐磨、耐腐蚀,还能提升导电性。
想象一下,这样的铝合金就像一位运动员,经过严格的训练,最终迎来了辉煌的时刻。
铝及铝合金导电氧化工艺经验
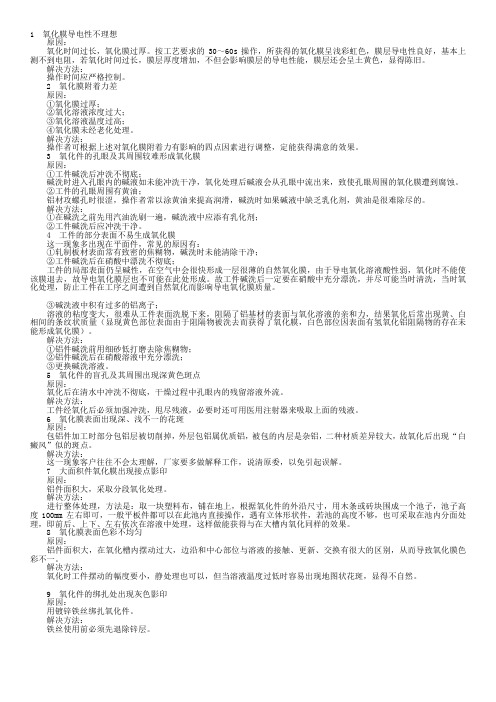
1 氧化膜导电性不理想原因:氧化时间过长,氧化膜过厚。
按工艺要求的30~60s操作,所获得的氧化膜呈浅彩虹色,膜层导电性良好,基本上测不到电阻,若氧化时间过长,膜层厚度增加,不但会影响膜层的导电性能,膜层还会呈土黄色,显得陈旧。
解决方法:操作时间应严格控制。
2 氧化膜附着力差原因:①氧化膜过厚;②氧化溶液浓度过大;③氧化溶液温度过高;④氧化膜未经老化处理。
解决方法:操作者可根据上述对氧化膜附着力有影响的四点因素进行调整,定能获得满意的效果。
3 氧化件的孔眼及其周围较难形成氧化膜原因:①工件碱洗后冲洗不彻底;碱洗时进入孔眼内的碱液如未能冲洗干净,氧化处理后碱液会从孔眼中流出来,致使孔眼周围的氧化膜遭到腐蚀。
②工件的孔眼周围有黄油;铝材攻螺孔时很涩,操作者常以涂黄油来提高润滑,碱洗时如果碱液中缺乏乳化剂,黄油是很难除尽的。
解决方法:①在碱洗之前先用汽油洗刷一遍,碱洗液中应添有乳化剂;②工件碱洗后应冲洗干净。
4 工件的部分表面不易生成氧化膜这一现象多出现在平面件,常见的原因有:①轧制板材表面常有致密的焦糊物,碱洗时未能清除干净;②工件碱洗后在硝酸中漂洗不彻底;工件的局部表面仍呈碱性,在空气中会很快形成一层很薄的自然氧化膜,由于导电氧化溶液酸性弱,氧化时不能使该膜退去,故导电氧化膜层也不可能在此处形成。
故工件碱洗后一定要在硝酸中充分漂洗,并尽可能当时清洗,当时氧化处理,防止工件在工序之间遭到自然氧化而影响导电氧化膜质量。
③碱洗液中积有过多的铝离子;溶液的粘度变大,很难从工件表面洗脱下来,阻隔了铝基材的表面与氧化溶液的亲和力,结果氧化后常出现黄、白相间的条纹状质量(显现黄色部位表面由于阻隔物被洗去而获得了氧化膜,白色部位因表面有氢氧化铝阻隔物的存在未能形成氧化膜)。
解决方法:①铝件碱洗前用细砂低打磨去除焦糊物;②铝件碱洗后在硝酸溶液中充分漂洗;③更换碱洗溶液。
5 氧化件的盲孔及其周围出现深黄色斑点原因:氧化后在清水中冲洗不彻底,干燥过程中孔眼内的残留溶液外流。
铝件导电氧化和阳极氧化

铝件导电氧化和阳极氧化铝是一种常见的金属材料,因其轻质、强度高、耐腐蚀等特点,广泛应用于电子、汽车、航空航天、建筑等行业中。
然而,铝面临的一个问题是,其表面容易氧化,导致其导电性变差,从而影响其使用效果。
因此,铝件的导电氧化和阳极氧化技术得到了广泛的研究和应用。
本文将介绍铝件的导电氧化和阳极氧化过程及其应用。
一、导电氧化技术导电氧化技术是通过在铝材表面形成一层氧化膜,使其具有较好的导电性能,从而实现对铝件表面的防腐蚀和增强其结构性能的目的。
目前常用的导电氧化工艺有紫外线辐射法、微波辐射法、脉冲电解法、电化学氧化法等。
1.紫外线辐射法紫外线辐射法是一种新兴的导电氧化技术,其主要原理是在紫外光照射下,铝材表面形成自组织氧化膜。
它的优点在于加工时间短、工艺简单、能耗低、成本较低,同时所形成的氧化膜均匀、致密,具有较好的导电性能。
2.微波辐射法微波辐射是在高频电场的作用下,利用铝与氧化还原剂反应得到氧化膜的方法。
其优势在于导电性能优异,且氧化膜表面平整光洁,粗糙度低,表面孔洞少,防腐蚀性能较好。
另外,微波辐射法的工艺稳定,操作简单,但其成本较高。
3.脉冲电化学氧化法脉冲电化学氧化法是一种新型的导电氧化技术,其主要原理是在铝材表面施加脉冲电流,由于脉冲电流存在间歇性,因此能够形成致密均匀的氧化膜,且导电性能好。
脉冲电化学氧化法对处理铝材的厚度、形状、大小、数量等几乎没有限制,优点在于工艺可控性好,操作简单,加工速度快。
4.电化学氧化法电化学氧化法是较常见的一种导电氧化技术,其通过电解处理,在铝材表面生成含Al2O3的氧化膜,从而实现防腐蚀和导电的目的。
电化学氧化法具有操作简单、成本低、处理效果好等优点。
但其缺点在于钝化剂、电压、电解质的选择必须谨慎,并且加工时间较长。
二、阳极氧化技术阳极氧化技术是一种特殊的电化学氧化技术,它通过加强电压,使氧化膜生成速度大幅提高,从而得到更厚、更硬的氧化膜。
相比于导电氧化技术,阳极氧化技术所形成的氧化膜硬度高,耐用性好,防腐蚀性强。
6061铝导电氧化

6061铝导电氧化介绍6061铝是一种常用的铝合金材料,具有优良的导电性能。
为了进一步提高其导电性能,可以进行导电氧化处理。
本文将详细介绍6061铝导电氧化的原理、方法和应用。
原理导电氧化是通过在金属表面形成一层致密的氧化膜来提高其导电性能。
在6061铝上进行导电氧化时,首先需要清洁表面,去除油污和杂质。
然后,在适当的工艺条件下,通过在酸性溶液中施加直流电流,使铝表面发生阳极氧化反应。
在这个过程中,阴极和阳极之间形成了一个电解质溶液,并且阳极上形成了一层致密的氧化膜。
方法1. 清洗首先要对6061铝进行彻底清洗,以去除表面的油污和杂质。
常用的清洗方法包括机械清洗、碱洗和酸洗等。
机械清洗可以通过机械刷洗或喷砂等方式进行;碱洗可以使用碱性溶液,如氢氧化钠溶液;酸洗可以使用酸性溶液,如硝酸溶液。
2. 阳极氧化清洗完毕后,将6061铝放入含有适当酸性的电解质溶液中,并施加直流电流。
通常使用的电解质是含有硫酸、草酸或磷酸等物质的溶液。
通过调节电流密度、温度和处理时间等工艺参数,可以控制形成的氧化膜的厚度和性能。
3. 密封处理在完成阳极氧化后,还需要进行密封处理来提高氧化膜的致密性和耐蚀性。
常用的密封方法包括热水密封、镍盐密封和有机物密封等。
热水密封是将阳极氧化后的铝件浸泡在热水中;镍盐密封是将阳极氧化后的铝件浸泡在含有镍盐的溶液中;有机物密封是将阳极氧化后的铝件浸泡在含有有机物的溶液中。
应用6061铝导电氧化后具有优良的导电性能、耐腐蚀性和机械性能,广泛应用于以下领域:1. 电子领域6061铝导电氧化后可以作为电子元器件的外壳材料,具有良好的导电性能和防腐蚀性能。
同时,导电氧化层还可以提供一定的绝缘保护,避免金属与其他元件之间发生短路。
2. 汽车工业6061铝导电氧化后可以用作汽车零部件的材料,如发动机零部件、底盘零部件和车身结构等。
导电氧化层可以提高铝合金在恶劣环境下的耐腐蚀性能,并增加其机械强度。
3. 航空航天领域6061铝导电氧化后可用于航空航天器的结构材料,如飞机机翼、舱壁和连接件等。
铝合金 本色导电氧化

铝合金本色导电氧化
铝合金本色导电氧化通常指的是在铝合金表面进行的一种化学导电氧化处理,旨在提高其电磁屏蔽性能和耐腐蚀性。
具体来说,铝合金本色导电氧化涉及以下几个要点:
1. 氧化膜特性:化学导电氧化后的氧化膜无色透明,膜层厚度较薄,约为0.3~0.5μm,因此具有较好的导电性。
这使得经过导电氧化处理的铝合金部件适用于需要保持一定导电性的场合。
2. 工艺流程:铝合金本色导电氧化的典型工艺流程包括:除油、水洗、碱液腐蚀、精蚀、硝酸酸洗等步骤,最终形成一层氧化铝膜。
3. 影响因素:溶液温度和氧化时间是影响导电氧化质量的两个主要因素。
溶液温度过高可能会导致成膜速度加快,但同时氧化膜容易出现粉化等问题。
4. 与阳极氧化的区别:化学导电氧化(化学氧化)不需要通电,是通过化学反应在铝合金表面形成氧化膜的过程,而阳极氧化则需要在外加电流的作用下进行。
综上所述,铝合金本色导电氧化是一种有效的表面处理方法,它不仅能够提升铝合金的耐腐蚀性和电磁屏蔽能力,还能够保持材料的本色和良好的导电性,适合在电子设备等领域应用。
标准 铝合金 导电氧化
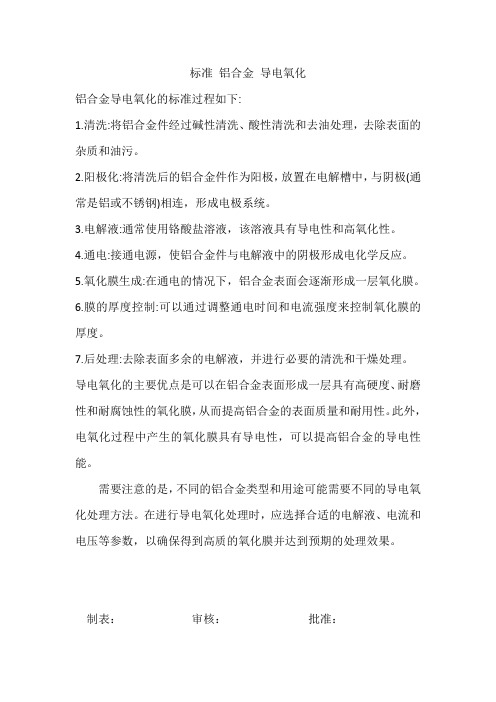
标准铝合金导电氧化
铝合金导电氧化的标准过程如下:
1.清洗:将铝合金件经过碱性清洗、酸性清洗和去油处理,去除表面的杂质和油污。
2.阳极化:将清洗后的铝合金件作为阳极,放置在电解槽中,与阴极(通常是铝或不锈钢)相连,形成电极系统。
3.电解液:通常使用铬酸盐溶液,该溶液具有导电性和高氧化性。
4.通电:接通电源,使铝合金件与电解液中的阴极形成电化学反应。
5.氧化膜生成:在通电的情况下,铝合金表面会逐渐形成一层氧化膜。
6.膜的厚度控制:可以通过调整通电时间和电流强度来控制氧化膜的厚度。
7.后处理:去除表面多余的电解液,并进行必要的清洗和干燥处理。
导电氧化的主要优点是可以在铝合金表面形成一层具有高硬度、耐磨性和耐腐蚀性的氧化膜,从而提高铝合金的表面质量和耐用性。
此外,电氧化过程中产生的氧化膜具有导电性,可以提高铝合金的导电性能。
需要注意的是,不同的铝合金类型和用途可能需要不同的导电氧化处理方法。
在进行导电氧化处理时,应选择合适的电解液、电流和电压等参数,以确保得到高质的氧化膜并达到预期的处理效果。
制表:审核:批准:。
铝及铝合金的电化学氧化
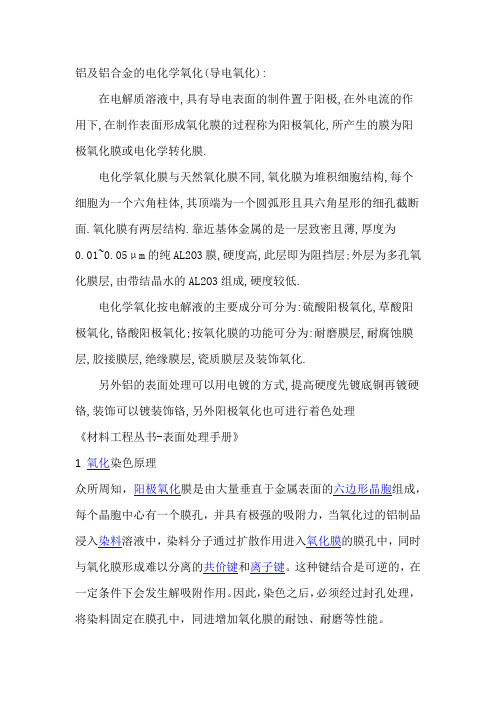
铝及铝合金的电化学氧化(导电氧化):在电解质溶液中,具有导电表面的制件置于阳极,在外电流的作用下,在制作表面形成氧化膜的过程称为阳极氧化,所产生的膜为阳极氧化膜或电化学转化膜.电化学氧化膜与天然氧化膜不同,氧化膜为堆积细胞结构,每个细胞为一个六角柱体,其顶端为一个圆弧形且具六角星形的细孔截断面.氧化膜有两层结构.靠近基体金属的是一层致密且薄,厚度为0.01~0.05μm的纯AL2O3膜,硬度高,此层即为阻挡层;外层为多孔氧化膜层,由带结晶水的AL2O3组成,硬度较低.电化学氧化按电解液的主要成分可分为:硫酸阳极氧化,草酸阳极氧化,铬酸阳极氧化;按氧化膜的功能可分为:耐磨膜层,耐腐蚀膜层,胶接膜层,绝缘膜层,瓷质膜层及装饰氧化.另外铝的表面处理可以用电镀的方式,提高硬度先镀底铜再镀硬铬,装饰可以镀装饰铬,另外阳极氧化也可进行着色处理《材料工程丛书-表面处理手册》1 氧化染色原理众所周知,阳极氧化膜是由大量垂直于金属表面的六边形晶胞组成,每个晶胞中心有一个膜孔,并具有极强的吸附力,当氧化过的铝制品浸入染料溶液中,染料分子通过扩散作用进入氧化膜的膜孔中,同时与氧化膜形成难以分离的共价键和离子键。
这种键结合是可逆的,在一定条件下会发生解吸附作用。
因此,染色之后,必须经过封孔处理,将染料固定在膜孔中,同进增加氧化膜的耐蚀、耐磨等性能。
2 阳极氧化工艺对染色的影响在氧化染色整个流程中,因为氧化工艺原因造成染色不良是比较普遍的。
氧化膜的膜厚和孔隙均匀一致是染色时获得均匀一致颜色的前提和基础,为获得均匀一致的氧化膜,保证足够的循环量,冷却量,保证良好的导电性是举足轻重的,此外就是氧化工艺的稳定性。
硫酸浓度,控制在180—200g/l。
稍高的硫酸浓度可促进氧化膜的溶解反应加快,利于孔隙的扩张,更易于染色;铝离子浓度,控制在5—15 g/l。
铝离子小于5g/l,生成的氧化膜吸附能力降低,影响上色速度,铝离子大于15g/l时,氧化膜的均匀性受到影响,容易出现不规则的膜层。
1铝与铝合金的氧化处理

铝与铝合金的氧化处理铝及铝合金在大气中虽能自然形成一层氧化膜,但膜薄(40- 50A)而疏松多孔,为非晶态的、不均匀也不连续的膜层,不能作为可靠的防护一装饰性膜层.1随着铝制品加工工业的不断发展,在工业上越来越广泛地采用阳极氧化或化学氧化的方法,在铝及铝合金制件表面生成一层氧化膜,以达到防护一装饰的目的。
经化学氧化杜理获得的氧化膜,厚度一般为0.3~4um,质软、耐磨和抗蚀性能均低于阳极氧化膜.所以,除有特殊用途外,很少单独使用.但它有较好的吸附能力,在其表面再涂漆,可有效地提高铝制品的耐蚀性和装饰性。
、经阳极氧化处理获得的氧化膜,厚度一般在5-20v m,硬质阳极氧化膜厚度可达60- 2500m.其膜层还具有似下特性:,(I)硬度较高。
纯铝氧化膜的硬度比铝合金氧化膜的硬度高.通常,它的硬度大小与铝的合金成份、阳极氧化时电解液的工艺条件有关.阳极氧化膜不仅硬度较高,而且有较好的耐磨性.尤其是表面层多孔的氧化膜具有吸附润滑剂的能力,还可进一步改善表面的耐磨性能.(2)有较高的耐蚀性.这是由于阳极氧化膜有较高的化学稳定性.经测试,纯铝的阳极氧化膜比铝合金的阳极氧化膜耐蚀性好.这是由于合金成分夹杂或形成金属化合物不能被氧化或被溶解,而使氧化膜不连续或产生空隙,从而使氧化膜的耐蚀性大为降低.所以,一般经阳极氧化后所得的膜必须进行封闭处理,才能提高其耐蚀性能。
(3)有较强的吸附能力。
铝及铝合金的阳极氧化膜为多孔结构,具有很强的吸附能力,所以给孔内填充各种颜料、润滑剂、树脂等可进一步提高铝制品的防护、绝缘、耐磨和装饰性能.(4)有很好的绝缘性能.铝及铝合金的阳极氧化膜,已不具备金属的导电性质,而成为良好的绝缘材料.(5)绝热抗热性能强.这是因为阳极氧化膜的导热系数大大低于纯铝·阳极氧化膜可耐温15001C左右,而纯铝只能耐660℃.好综上所述,铝和铝合金经化学氧化处理,特别是阳极氧化处理后,在其表面形成的氧化膜具有良好的防护一装饰等特性.因此,被广泛应用于航空、电气、电子、机械制造和轻工工业等方面。
铝及铝合金导电氧化工艺经验谈
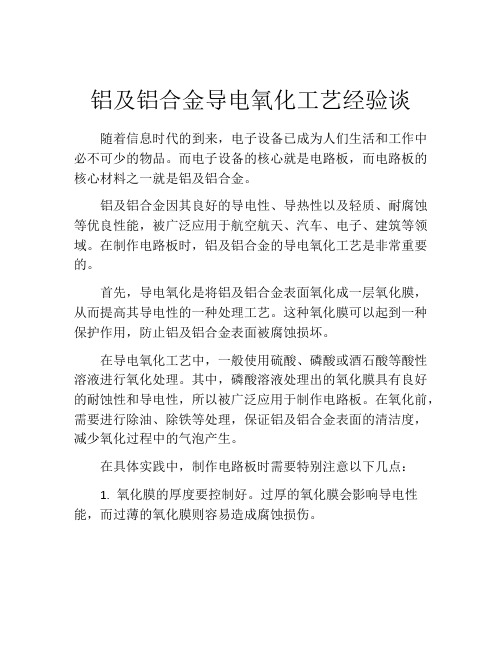
铝及铝合金导电氧化工艺经验谈随着信息时代的到来,电子设备已成为人们生活和工作中必不可少的物品。
而电子设备的核心就是电路板,而电路板的核心材料之一就是铝及铝合金。
铝及铝合金因其良好的导电性、导热性以及轻质、耐腐蚀等优良性能,被广泛应用于航空航天、汽车、电子、建筑等领域。
在制作电路板时,铝及铝合金的导电氧化工艺是非常重要的。
首先,导电氧化是将铝及铝合金表面氧化成一层氧化膜,从而提高其导电性的一种处理工艺。
这种氧化膜可以起到一种保护作用,防止铝及铝合金表面被腐蚀损坏。
在导电氧化工艺中,一般使用硫酸、磷酸或酒石酸等酸性溶液进行氧化处理。
其中,磷酸溶液处理出的氧化膜具有良好的耐蚀性和导电性,所以被广泛应用于制作电路板。
在氧化前,需要进行除油、除铁等处理,保证铝及铝合金表面的清洁度,减少氧化过程中的气泡产生。
在具体实践中,制作电路板时需要特别注意以下几点:1. 氧化膜的厚度要控制好。
过厚的氧化膜会影响导电性能,而过薄的氧化膜则容易造成腐蚀损伤。
2. 氧化过程需要控制好时间和温度。
过长或过短的时间会影响氧化膜的质量和厚度,过高或过低的温度也会影响氧化膜的质量。
3. 溶液的浓度和配比也很重要。
不同类型的溶液配比不同,浓度不同,需要根据实际情况进行选择和控制。
4. 氧化后需要进行中和处理,去除残留溶液,保证产品质量安全。
总之,铝及铝合金导电氧化工艺是制作电路板过程中必不可少的一个环节。
为了保证产品的质量和安全性,需要严格掌控氧化工艺的各个环节,保证每一步都精准严谨。
同时,在实践中,不断总结经验教训,不断改进工艺水平,才能使得铝及铝合金导电氧化工艺更加完善。
铝合金导电氧化

铝及铝合金导电氧化铝及铝合金经导电氧化工艺后所获的氧化膜具有导电性能,这是其特有的性能,而且膜层的防护与装饰性能良好。
铝及铝合金导电氧化工艺操作简便,无需专用设备。
近年来,有关导电氧化膜层易于吸附有机涂料结合力良好得到进一步认识,因而在油漆和电泳涂料基底的应用也逐步开展。
笔者服务于此工艺已多年,在工艺管理和生产实践中都积累了一定的经验,下面简述工艺全过程。
1前处理铝在空气中极不稳定,易生成用肉眼也难以识别的氧化膜。
由于铝件加工工艺的不同铸造成型,或是由延压板材直接剪切而成,或是机械精细加工成型,或是经不同工艺成型后又经热处理或焊接等等,经上述不同的加工工艺,工件表面会留下不同状态、不同程度的污物或痕迹,在前处理工序中必须根据工件表面的实际情况选择前处理的工艺方法。
精细加工件在前处理工序中需要注意的问题:精细加工件虽然表面的自然氧化膜才初生成、较易清除,但细腻重,特别是孔眼内及其周围(因机加工过程中润滑需要而添加的),这类工件必须先经有机溶剂清洗,若直接用碱洗不但油腻重难以除净,且精细加工面承受不了长时间的强碱腐蚀,结果还会影响到工件表面的粗糙程度和公差的配合,最终成为废品。
铸造成型件在前处理工序中需要注意的问题:铸造成型件并非所有表面都经过机械加工的,未经机加工的表面留有浇铸过程中形成的过厚氧化层,有的还夹有砂层,一般情况下,机加工或喷砂方法先除去这一部位的原始氧化膜,或是经碱洗后再加工,只有这样才能既除净未加工部位的原始氧化层,又避免机加工部位公差尺寸的改变。
经过热处理或焊接工艺的工件在前处理工序中需要注意的问题:按工艺要求,工件转入热处理或焊接工序之前需经有机溶剂清洗,除净表面油污,但目前一般做不到这一点,故工件表面形成一层油污烧结的焦化物,这层焦化物在有机溶剂中难以除净,若浸泡在碱液中会引起局部腐蚀,产生麻点或造成凹凸不平,严重影响产品质量。
笔者用浓硝酸浸泡的方法来松软这层焦化物,待焦化物松软后在碱液中稍加清洗即能彻底除净。
铝合金本色导电氧化膜涂层
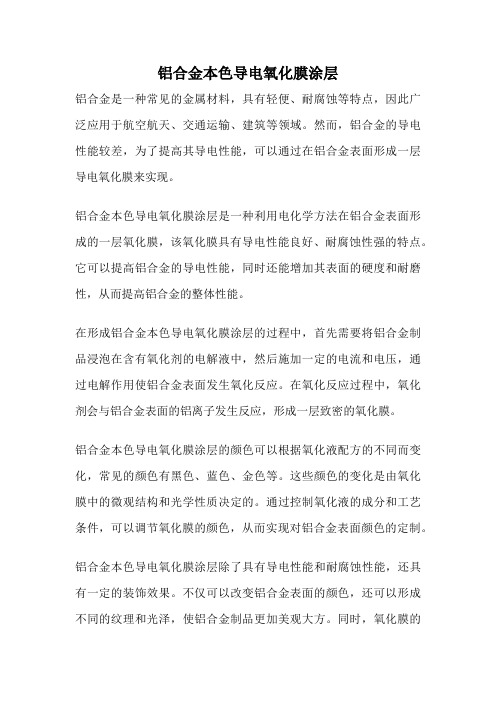
铝合金本色导电氧化膜涂层
铝合金是一种常见的金属材料,具有轻便、耐腐蚀等特点,因此广泛应用于航空航天、交通运输、建筑等领域。
然而,铝合金的导电性能较差,为了提高其导电性能,可以通过在铝合金表面形成一层导电氧化膜来实现。
铝合金本色导电氧化膜涂层是一种利用电化学方法在铝合金表面形成的一层氧化膜,该氧化膜具有导电性能良好、耐腐蚀性强的特点。
它可以提高铝合金的导电性能,同时还能增加其表面的硬度和耐磨性,从而提高铝合金的整体性能。
在形成铝合金本色导电氧化膜涂层的过程中,首先需要将铝合金制品浸泡在含有氧化剂的电解液中,然后施加一定的电流和电压,通过电解作用使铝合金表面发生氧化反应。
在氧化反应过程中,氧化剂会与铝合金表面的铝离子发生反应,形成一层致密的氧化膜。
铝合金本色导电氧化膜涂层的颜色可以根据氧化液配方的不同而变化,常见的颜色有黑色、蓝色、金色等。
这些颜色的变化是由氧化膜中的微观结构和光学性质决定的。
通过控制氧化液的成分和工艺条件,可以调节氧化膜的颜色,从而实现对铝合金表面颜色的定制。
铝合金本色导电氧化膜涂层除了具有导电性能和耐腐蚀性能,还具有一定的装饰效果。
不仅可以改变铝合金表面的颜色,还可以形成不同的纹理和光泽,使铝合金制品更加美观大方。
同时,氧化膜的
密封性能也能防止铝合金表面被进一步氧化和腐蚀,延长其使用寿命。
铝合金本色导电氧化膜涂层是一种提高铝合金导电性能和耐腐蚀性能的有效方法。
通过控制氧化液的成分和工艺条件,可以实现对铝合金表面颜色和纹理的调控,使其更加美观大方。
这种氧化膜涂层不仅能够提高铝合金的整体性能,还能延长其使用寿命,为铝合金在各个领域的应用提供了更多可能性。
铝及铝合金的化学导电氧化
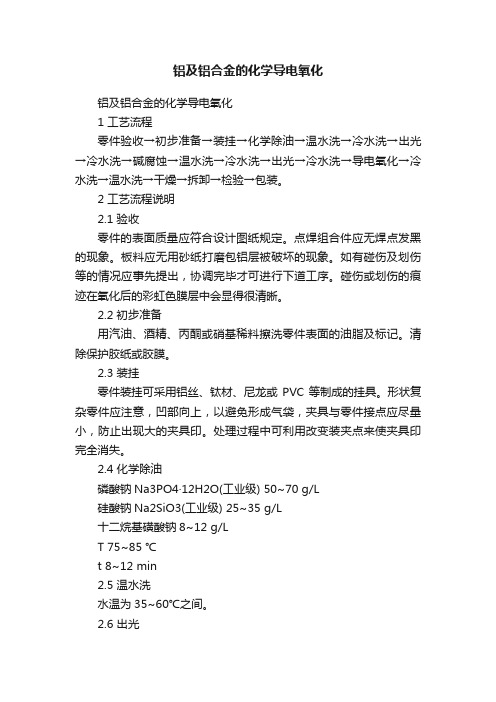
铝及铝合金的化学导电氧化铝及铝合金的化学导电氧化1 工艺流程零件验收→初步准备→装挂→化学除油→温水洗→冷水洗→出光→冷水洗→碱腐蚀→温水洗→冷水洗→出光→冷水洗→导电氧化→冷水洗→温水洗→干燥→拆卸→检验→包装。
2 工艺流程说明2.1 验收零件的表面质量应符合设计图纸规定。
点焊组合件应无焊点发黑的现象。
板料应无用砂纸打磨包铝层被破坏的现象。
如有碰伤及划伤等的情况应事先提出,协调完毕才可进行下道工序。
碰伤或划伤的痕迹在氧化后的彩虹色膜层中会显得很清晰。
2.2 初步准备用汽油、酒精、丙酮或硝基稀料擦洗零件表面的油脂及标记。
清除保护胶纸或胶膜。
2.3 装挂零件装挂可采用铝丝、钛材、尼龙或PVC等制成的挂具。
形状复杂零件应注意,凹部向上,以避免形成气袋,夹具与零件接点应尽量小,防止出现大的夹具印。
处理过程中可利用改变装夹点来使夹具印完全消失。
2.4 化学除油磷酸钠Na3PO4·12H2O(工业级) 50~70 g/L硅酸钠Na2SiO3(工业级) 25~35 g/L十二烷基磺酸钠8~12 g/LT 75~85 ℃t 8~12 min2.5 温水洗水温为35~60℃之间。
2.6 出光硝酸HNO3(d=1.42)(工业级) 300~500 g/L铬酐CrO3(化学级) 5~15 g/LT 室温t 出光为止2.7 碱腐蚀氢氧化钠NaOH(工业级) 20~35 g/L碳酸钠Na2CO3(工业级) 20~30 g/LT 50~60 ℃t <2min2.8 导电氧化⑴配方一:铬酐CrO3(化学级) 3.5~4.0 g/L重铬酸钠Na2Cr2O7(化学级) 3.0~3.5 g/L氟化钠NaF(化学级) 1 g/LT 35~50 ℃t 3~8 min此配方中铬酐和重铬酸钠是生成氧化膜的主要成分.应随着使用过程的消耗,按分析结果不断添加。
如果含量过低则影响膜的颜色,而且结合力不牢。
氟化钠是活性剂,在氧化中起催化作用。
铝或铝合金阳极氧化的一般原理

铝或铝合金阳极氧化的一般原理以铝或铝合金制品为阳极置于电解质溶液中,利用电解作用,使其表面形成氧化铝薄膜的过程,称为铝及铝合金的阳极氧化处理。
铝阳极氧化的原理实质上就是水电解的原理。
当电流通过时,将发生以下的反应:在阴极上,按下列反应放出H2:2H++2e→H2在阳极上,4OH–4e→2H2O+O2,析出的氧不仅是分子态的氧(O2),还包括原子氧(O),以及离子氧(O-2),通常在反应中以分子氧表示。
作为阳极的铝被其上析出的氧所氧化,形成无水的12O3膜:4A1+3O2=2A12O3+3351J应指出,生成的氧并不是全部与铝作用,一部分以气态的形式析出。
阳极氧化的种类阳极氧化早就在工业上得到广泛应用。
冠以不同名称的方法繁多,归纳起来有以下几种分类方法:按电流型式分有:直流电阳极氧化;交流电阳极氧化;以及可缩短达到要求厚度的生产时间,膜层既厚又均匀致密,且抗蚀性显着提高的脉冲电流阳极氧化。
按电解液分有:硫酸、草酸、铬酸、混合酸和以磺基有机酸为主溶液的自然着色阳极氧化。
按膜层性质分有:普通膜、硬质膜(厚膜)、瓷质膜、光亮修饰层、半导体作用的阻挡层等阳极氧化。
直流电硫酸阳极氧化法的应用最为普遍,这是因为它具有适用于铝及大部分铝合金的阳极氧化处理;膜层较厚、硬而耐磨、封孔后可获得更好的抗蚀性;膜层无色透明、吸附能力强极易着色;处理电压较低,耗电少;处理过程不必改变电压周期,有利于连续生产和实践操作自动化;硫酸对人身的危害较铬酸小,货源广,价格低等优点。
近十年来,我国的建筑业逐步使用铝门窗及其它装饰铝材,它们的表面处理生产线都是采用这种方法。
阳极氧化膜结构、性质与应用1)阳极氧化膜的结构阳极氧化膜由两层组成,多孔的厚的外层是在具有介电性质的致密的内层上成长起来的,后者称为阻挡层(亦称活性层)。
(1)阻挡层阻挡层是由无水的A12O3所组成,薄而致密,具有高的硬度和阻止电流通过的作用。
(2)多孔的外层氧化膜多孔的外层主要是由非晶型的A12O3及少量的r-A12O3.H2O还含有电解液的阴离子。
铝及铝合金导电氧化液及导电氧化方法
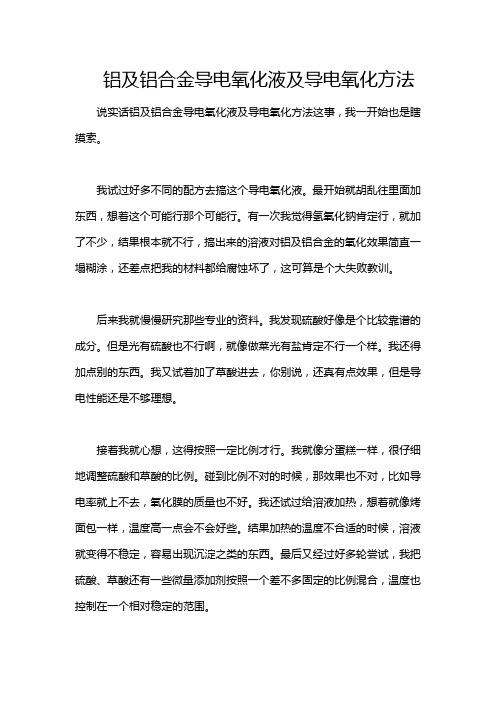
铝及铝合金导电氧化液及导电氧化方法说实话铝及铝合金导电氧化液及导电氧化方法这事,我一开始也是瞎摸索。
我试过好多不同的配方去搞这个导电氧化液。
最开始就胡乱往里面加东西,想着这个可能行那个可能行。
有一次我觉得氢氧化钠肯定行,就加了不少,结果根本就不行,搞出来的溶液对铝及铝合金的氧化效果简直一塌糊涂,还差点把我的材料都给腐蚀坏了,这可算是个大失败教训。
后来我就慢慢研究那些专业的资料。
我发现硫酸好像是个比较靠谱的成分。
但是光有硫酸也不行啊,就像做菜光有盐肯定不行一个样。
我还得加点别的东西。
我又试着加了草酸进去,你别说,还真有点效果,但是导电性能还是不够理想。
接着我就心想,这得按照一定比例才行。
我就像分蛋糕一样,很仔细地调整硫酸和草酸的比例。
碰到比例不对的时候,那效果也不对,比如导电率就上不去,氧化膜的质量也不好。
我还试过给溶液加热,想着就像烤面包一样,温度高一点会不会好些。
结果加热的温度不合适的时候,溶液就变得不稳定,容易出现沉淀之类的东西。
最后又经过好多轮尝试,我把硫酸、草酸还有一些微量添加剂按照一个差不多固定的比例混合,温度也控制在一个相对稳定的范围。
我记得在进行导电氧化的时候,就像给铝及铝合金洗澡一样,得把材料放进去泡足够的时间。
如果泡的时间短了,氧化膜就很薄,导电性能不好。
要是泡太长时间又怕过度氧化,也会影响导电。
我当时为了确定这个时间也是做了好多小试验。
还有清洗这一步也很重要,就好比吃完饭洗碗,你不洗干净那肯定不行。
如果清洗不彻底,残留的氧化液就会影响后续成品的质量。
我到现在都不敢说我掌握得特别完美了,但是这些都是我实实在在摸索出来的经验,就分享给你了。
比如说现在我对这个氧化液里各种成分的比例能有个大致的范围保证导电氧化的基本效果,这中间失败了无数次才找到这个点呢。
还有那个氧化的时间和温度,我虽然不敢说是绝对精准,但是也能做到八九不离十了。
如果你们要做这个的话,一定要多记录试验过程和结果,这样错了就知道错在哪里了。
- 1、下载文档前请自行甄别文档内容的完整性,平台不提供额外的编辑、内容补充、找答案等附加服务。
- 2、"仅部分预览"的文档,不可在线预览部分如存在完整性等问题,可反馈申请退款(可完整预览的文档不适用该条件!)。
- 3、如文档侵犯您的权益,请联系客服反馈,我们会尽快为您处理(人工客服工作时间:9:00-18:30)。
铝和铝合金导电氧化工艺的研究与应用摘要:铝及铝合金化学氧化后涂漆,可大大提高基体与涂层的结合力,并增强铝材的抗蚀能力。
常规的铝阳极氧化膜由于表面电阻大而无法满足产品的电磁屏蔽性能要求。
为提高铝氧化膜的电磁屏蔽性和耐蚀性,提出了一种铝合金导电氧化工艺。
介绍了其原理、工艺流程及工艺维护,测量了所得膜层的外观、导电性和耐蚀性。
结果表明,该工艺所得氧化膜无色透明、导电性好,且具有一定的耐蚀性。
关键词: 铝铝合金氧化导电一、前言:铝及铝合金具有质量轻、易于加工、装饰性好等优良性能。
但未经防护处理的裸铝耐蚀性差、表面硬度低,磨损后表面产生一层黑灰,所以通常采用阳极氧化对铝材进行防护处理。
阳极氧化是在通电的情况下,把铝制零件放入电解槽中,零件作阳极,不锈钢作阴极,在零件表面产生一层较致密的氧化铝膜层。
阳极氧化膜虽然防护性好、耐磨损,但其电阻高,不导电。
科技的快速发展使集成电路广泛用于各个领域中,集成电路与晶体管相比虽然有体积小、效率高等优点,但却存在抗干扰性差的致命缺点,这种缺点使得产品的稳定性和可靠性严重下降。
因此在电子产品设计中,往往要求盛装集成电路的外壳机箱整体有良好的导电性。
铝及铝合金经导电氧化工艺后所获的氧化膜具有导电性能,这是其特有的性能,而且膜层的防护与装饰性能良好。
铝及铝合金导电氧化工艺操作简便,无需专用设备。
近年来,有关导电氧化膜层易于吸附有机涂料结合力良好得到进一步认识,因而在油漆和电泳涂料基底的应用也逐步开展。
下面简述工艺全过程。
二、原理铝及铝合金的表面处理工艺有阳极氧化和化学氧化,化学氧化膜导电,但通常呈彩虹色,影响产品美观。
我们在化学氧化工艺的基础上进行摸索,成功研制出导电氧化处理工艺。
该工艺是将铝件放在含有铬酐、磷酸的酸性溶液中化学处理,获得一层导电性良好又有一定防护性能的透明保护膜。
铝成膜反应式为:Al + CrO3 + 2H3PO4 →AlPO4 + CrPO4 +3H2O三、前处理(1)除油铝在空气中极不稳定,易生成用肉眼也难以识别的氧化膜。
由于铝件加工工艺的不同铸造成型,或是由延压板材直接剪切而成,或是机械精细加工成型,或是经不同工艺成型后又经热处理或焊接等等,经上述不同的加工工艺,工件表面会留下不同状态、不同程度的污物或痕迹,在前处理工序中必须根据工件表面的实际情况选择前处理的工艺方法。
精细加工件在前处理工序中需要注意的问题:精细加工件虽然表面的自然氧化膜才初生成、较易清除,但细腻重,特别是孔眼内及其周围(因机加工过程中润滑需要而添加的) ,这类工件必须先经有机溶剂清洗,若直接用碱洗不但油腻重难以除净,且精细加工面承受不了长时间的强碱腐蚀,结果还会影响到工件表面的粗糙程度和公差的配合,最终成为废品。
铸造成型件在前处理工序中需要注意的问题:铸造成型件并非所有表面都经过机械加工的,未经机加工的表面留有浇铸过程中形成的过厚氧化层,有的还夹有砂层,一般情况下,机加工或喷砂方法先除去这一部位的原始氧化膜,或是经碱洗后再加工,只有这样才能既除净未加工部位的原始氧化层,又避免机加工部位公差尺寸的改变。
经过热处理或焊接工艺的工件在前处理工序中需要注意的问题,按工艺要求,工件转入热处理或焊接工序之前需经有机溶剂清洗,除净表面油污,但目前一般做不到这一点,故工件表面形成一层油污烧结的焦化物,这层焦化物在有机溶剂中难以除净,若浸泡在碱液中会引起局部腐蚀,产生麻点或造成凹凸不平,严重影响产品质量。
用浓硝酸浸泡的方法来松软这层焦化物,待焦化物松软后在碱液中稍加清洗即能彻底除净。
有机溶剂除油油污不太严重的可采取在溶剂中短时间浸泡;油污严重的应采取用棉纱蘸溶剂揩擦,或用鬃刷刷洗。
操作中要注意安全,用后剩余溶剂要妥善保管好。
(2)晾干无论采用何种有机溶剂的清洗方式,晾干工序决不可省略,否则将会失去清洗意义。
(3)绑扎①绑扎用的材料宜选用铝线,禁用铜线和镀锌铁线,可用退去锌层的铁线。
②稍大件的单件绑扎为好,尽可能绑在离零件边沿最近的孔眼中,以减少对工件表面的影响。
③不同种工件不宜同绑于一串中,因不同成分(牌号) 的铝材氧化处理时间是有所区别的。
④注意所绑扎的工件悬空时的方向,要避免凹入部位因朝下而产生窝气四、工艺流程工艺流程如下:铝合金零件→常温除油→水洗→碱液腐蚀→精蚀→水洗→硝酸(1∶1) 酸洗→水洗→化学导电氧化→水洗→封闭→水洗→纯净水洗→干燥。
经前处理后要立即转入氧化工序,以防因工件在大气中搁置过久而又生成自然氧化膜而影响氧化层的质量。
再度浸泡在清水中虽优于曝露在大气中,但也不宜浸泡过久。
氧化过程中溶液的温度是至关重要的工艺条件,溶液温度过高,成膜速度加快,氧化膜容易出现粉化; 溶液温度过低,成膜速度缓慢,所生成的膜色调偏淡,附着力差。
在同一型号铅材为求得表面基本一致的色彩,应在同一溶液温度下处理同样时间。
在一定的范围内温度与时间成反比,即溶液温度越高,所需时间越短,反之所需时间越长。
铝材纯度越高所需的氧化处理时间越长。
氧化处理时间不足,生成的氧化膜过于浅淡;铝材纯度低,氧化时间缩短,否则氧化膜显陈旧,甚至影响膜层的导电性能。
为了获得均匀的氧化膜色彩,小件氧化时可在溶液中多晃动,大件可采取搅拌溶液或静处理(不搅拌溶液、不晃动工件) ,以防工件的边缘部位与溶液的交换机会比工件的中心部位增多而产生不均匀的氧化膜色彩。
五、后处理(1)循环水冲洗对于有盲孔、狭缝的工件要加强对这些部位的冲洗,并甩净里面的残留溶液,以防氧化溶液流出来氧化面受破坏。
(2)热水冲洗热水洗目的是老化膜层。
但水温和时间要严格控制,水温过高膜层减薄,颜色变淡。
处理时间过长也会出现上述类似问题,适宜的温度和时间是:温度40~50 ℃时间015~1 min (3)干燥干燥方法以自然晾干为好,经热水冲洗过的工件斜挂于架子上,让工作表面的游离水以垂直方向向下流。
流至下端角边的水珠用毛巾吸去,按此法晾干的膜层色彩不受干扰,显得自然。
(4)老化老化方法可根据气候条件来决定,有日光的夏季可在日光下曝晒,阴雨天或是冬季可用烘箱烘烤,工艺条件是:温度40~50 ℃时间10~15 min(5)自检工件经循环水冲洗后宜即自检质量,如发现有缺陷的可在碱液中退除,出光后重新氧化。
不合格导电氧化膜件宜在干燥、老化工序之前先挑出来。
若干燥、老化后膜层较难退除并会影响工件表面的粗糙度,经多种方法试验,发现采用下列方法效果很好,方法简单。
又不影响工件表面质量,具体过程如下:首先将不合格的工件夹在铝阳极氧化用的夹具上,然后按铝在硫酸溶液中的阳极氧化方法进行阳极处理2~3 min ,待膜层松软、脱落,再经碱液稍加清洗及硝酸出光后即可重新进行导电阳极化。
对于膜层形成时间超过3 h 或经烘干过的膜层,可先在碱性化学除油槽中浸泡100 min 左右,再于1∶ 1 硝酸中退除。
对于已老化后处理过的不合格膜层,在退除时为了不影响工件的表面质量,郑瑞庭推荐的具体过程如下:首先,将不合格的工件夹在铝阳极氧化用的夹具上,然后按铝件在硫酸溶液中的阳极氧化方法进行阳极处理2~3 min ,待膜层松软、脱落,再经碱液稍加清洗及硝酸出光后,即可重新进行导电化学氧化,铝及铝合金导电氧化是一项很有应用前景的工艺,该工艺操作简便,生产成本低廉,所获膜层除特有的导电性能之外,还可用于工件的防护与装饰,色彩比锌层彩色钝化膜雅致,具有较浅且均匀的细纹彩虹,是有推广价值而尚未被广泛认识的涂覆工艺。
不合格件的返修:工件经化学导电氧化和流动水清洗后,宜即自检质量,如发现有缺陷的工件可在碱性化学除油槽中退除,出光后重新氧化。
对于有精度尺寸要求的,可在下列溶液中退除:CrO3 12~20 g/ LH3PO4 (85 %) 35~40 mL/ L温度70~90 ℃时间除尽为止六、工艺维护①氧化时,若零件表面有油污,则油污处不能产生氧化膜,因此除油很重要,轻度油污可浸泡除去,油污较重时应用刷子刷除。
每班操作结束后要把槽液表面的油污清掉。
②绑扎用的材料应选用铝线,稍大的工件应尽可能绑在离零件边沿最近的孔眼中,以减小对工件表面的影响。
注意所绑扎的工件悬空时的方向,要避免凹入部位因朝下而产生窝气。
③有盲孔或狭缝的工件要加强各道水洗,彻底洗净其中的残留溶液,以免污染下道工序。
④铝及铝合金工件一般可采用1∶1 的硝酸水溶液进行漂光处理,对于含硅铝合金工件应采用硝酸∶氢氟酸为3∶1 的溶液,尽量不要带入水分。
⑤工件经前处理后,要立即转入氧化工序,以防在大气中搁置过久产生自然氧化膜而影响氧化膜的质量。
⑥氧化过程中,溶液温度的控制至关重要,温度过高,成膜速度加快,氧化膜容易出现粉化;溶液温度过低,成膜速度缓慢,附着力差。
⑦不合格零件可用(1∶1)体积比硫酸或硝酸浸泡去除氧化膜,时间为1~2 min。
⑧带有丝孔的工件,碱蚀和精饰的时间要严格控制在工艺范围内,以免时间过长引起过腐蚀,损坏丝扣。
参考文献:[1]李杨. 铝的金黄色导电氧化膜制备工艺[J ].材料保护,2003 ,36 (4) :70.[2]阎国平.铝合金表面化学氧化的应用[J ].材料保护,1997 ,30(5) :34.[3]侯荣阶,王炳申,袁长生. 铝及铝合金的化学导电氧化[J ] . 表面工程信息(电镀版) .[4]侯荣阶,宋勇,林庆山. 铝及铝合金的化学电导电氧化[J ] .中国电镀材料信息,2002,2(7) :45.[5]上海新华无线电厂. 铝及铝合金导电氧化工艺[J ] . 材料保护,1975 ,8(4) .[6]冯花草. 铝及合金化学氧化[J ] . 材料保护,1996 ,29(9) :37.[7]白祯遐. 铝及合金化学氧化[J ] . 电镀与环保,2000 ,20 (5) :37~38.[8]唐春华. 铝及铝合金常温彩色化学氧化工艺[J ] . 五金科技,2001 ,29 (5) :27~28.[9]董建国,羊军. 铝材化学氧化[J ] . 电镀与环保,2000 ,20(6) :32.[10]郑瑞庭. 铝及铝合金导电氧化工艺经验谈[J ] . 电镀与涂饰,2000 ,19 (3) .[11]郑瑞庭. 关于“铝及铝合金导电氧化工艺经验谈”一文的补充[J ].电镀与涂饰,2002 ,21(4) :59.[12]郑瑞庭. 电镀实践600 例[M] . 北京:化学工业出版社,2004.[13]王文忠. 铝及其合金转化膜处理[J ] . 电镀与环保,2002 ,22(6) :2004.[14]柳玉波. 表面处理工艺大全[M] . 北京: 中国计量出版社,1996.[15]曾华梁,吴仲达,陈钧武,等. 电镀工艺手册[M] . 北京:机械工业出版社,1998.[16]张允诚,胡如男,向荣. 电镀手册[M] . 北京:国防工业出版社,1997.[17]谈华民,廖春业. 铝及其合金铬酸盐转化处理槽中氟离子的测定[J ] . 电镀与涂饰. 2002 ,21 (3) :42~44.[18]张允诚,胡如南,向荣. 电镀手册[M] . 北京:国防工业出版社,1997. 890 893.。