第9章微动磨损
机械设计基础第9章机械零件设计概论(六-1)

一)强度准则
强度准则是指零件中的应力不得超过许用值。
即: σ ≤ σlim
σlim ----材料的极限应力
脆性材料:σlim = σB (强度极限)
延伸率 < 5%
塑性材料:σlim = σS (屈服极限) 延伸率 > 5%
为了安全起见,引入安全系数S,得:
B
如齿轮、凸轮、滚动轴承等。
潘存云教授研制
潘存云教授研制
若两个零件在受载前是点接触或线接触。受载后,
由于变形其接触处为一小面积,通常此面积甚小而表
层产生的局部应力却很大,这种应力称为接触应力。
这时零件强度称为接触强度。
机械零件的接触应力通常是随时间作周期性变化的,在载荷重复作用下,首先在
表层内约20μm处产生初始疲劳裂纹,然后裂纹逐渐扩展(润滑油被挤迸裂纹中将
▲使用功能要求 ▲经济性要求 ▲劳动保护要求 ▲可靠性要求 ▲其它专用要求
机器的可靠度——指在规定的使用时间内和预定的环 境下机器能够正常工作的概率。
机器由于某种故障而不能完成预定的功能称为失 效,它是随机发生的,其原因是零件所受的载荷、环 境温度、零件本身物理和机械性能等因素是随机变化 的。为了提高零件的可靠性,就应当在工作条件和零 件性能两个方面使其变化尽可能小。
▲使用功能要求 ▲经济性要求 ▲劳动保护要求 ▲可靠性要求 ▲其它专用要求
其它专用要求——针对不同机器所特有的要求。例如: 1)对机床有长期保持精度的要求; 2)对飞机有质量小,飞行阻力小而运载能力大的要求;
3)对流动使用的机器有便于安装和拆卸的要求;
4)对大型机器有便于运输的要求等等。
汽车零部件的失效模式及分析
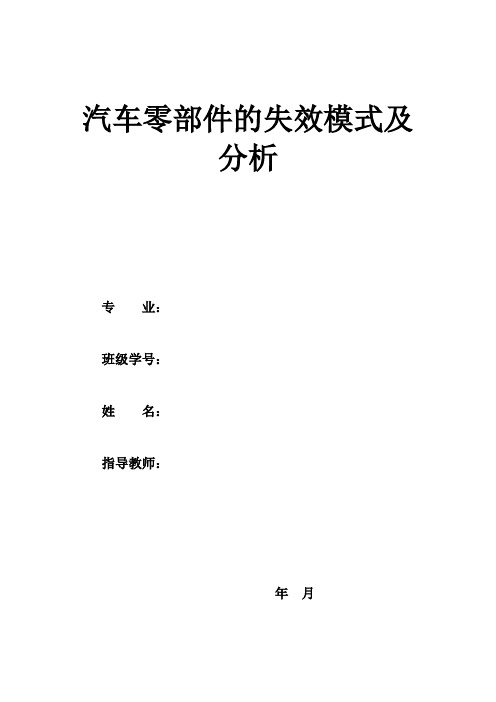
汽车零部件的失效模式及分析专业:班级学号:姓名:指导教师:年月摘要汽车零件失效分析,是研究汽车零件丧失其规定功能的原因、特征和规律;研究其失效分析技术和预防技术,其目的在与分析零部件失效的原因,找出导致失效的责任,并提出改进和预防措施,从而提高汽车可靠性和使用寿命。
目录第一章汽车零部件失效的概念及分类 (1)一、失效的概念 (1)二、失效的基本分类型 (1)三、零件失效的基本原因 (2)第二章汽车零部件磨损失效模式与失效机理 (3)一、磨料磨损及其失效机理 (3)二、粘着磨损及其失效机理 (4)三、表面疲劳磨损及其失效机理 (5)四、腐蚀磨损及其失效机理 (5)五、微动磨损及其失效机理 (6)第三章汽车零部件疲劳断裂失效及其机理 (8)第四章汽车零部件腐蚀失效及其机理 (9)第五章汽车零部件变形失效机理 (10)参考文献 (11)第一章汽车零部件失效的概念及分类一、失效的概念汽车零部件失去原设计所规定的功能称为失效。
失效不仅是指完全丧失原定功能,而且功能降低和严重损伤或隐患、继续使用会失去可靠性及安全性的零部件。
机械设备发生失效事故,往往会造成不同程度的经济损失,而且还会危及人们的生命安全。
汽车作为重要的交通运输工具,其可靠性和安全性越来越受到重视。
因此,在汽车维修工程中开展失效分析工作,不仅可以提高汽车维修质量,而且可为汽车制造部门提供反馈信息,以便改进汽车设计和制造工艺。
二、失效的基本分类型按失效模式和失效机理对是小进行分类是研究失效的重要内容之一。
失效模式是失效件的宏观特征,而失效机理则是导致零部件失效的物理、化学或机械的变化原因,并依零件的种类、使用环境而异。
汽车零部件按失效模式分类可分为磨损、疲劳断裂、变形、腐蚀及老化等五类。
汽车零件失效分类一个零件可能同时存在几种失效模式或失效机理。
研究失效原因,找出主要失效模式,提出改进和预防措施,从而提高汽车零部件的可靠性和使用寿命。
三、零件失效的基本原因引起零件是小的原因很多,主要可分为工作条件(包括零件的受力状况和工作环境)、设计制造(设计不合理、选材不当、制造工艺不当等)以及使用与维修等三个方面。
刘岩主编车辆修造工艺与装备

第一章工艺:就是产品的制造方法和过程的总称。
工序:指一个或一组工人,在同一台设备或同一个工作地点,对一个或同时对几个工件所连续完成的那一部分加工工作称工序。
工位:指在一道工序中,当工件装夹在移位工作台或回转夹具上,作若干次工作位置的改变,则工件每占据一个位置所完成的那一部分工序,称一个工位。
工步:在一个安装或工位中,加工表面、切削刀具及切削用量(指主轴转速和进给量)均不变的情况下,所连续完成的那一部分工作叫一个工步。
工件在机床上装夹过程包括定位和夹紧两方面的内容。
零件的机械加工质量包括加工精度和表面质量两方面内容。
零件的加工精度包括以下三个方面:尺寸精度、形状精度、位置精度在机械加工时,机床、夹具、刀具和工件构成一个完整的系统,称之为工艺系统在一般生产条件下,测量误差应控制在零件公差的1/10 ~ 1/3.对低精度零件取1/3机床误差主要由主轴回转误差、导轨导向误差、内传功链的传动误差及主轴、导轨等的位置关系误差所组成表面质量对零件使用性能的影响:(1)表面粗糙度越低,零件的耐磨性越好(2)对零件配合精度的影响:对于动合表面,粗糙度大,实际接触面越大,降低配合精度;对于过盈配合表面,粗糙度大,实际过盈量减小,降低配合可靠性。
(3)对零件疲劳强度的影响:表面粗糙度的凹谷处最易产生应力集中,容易发展成疲劳裂纹;表面层的残余压应力则可提高零件疲劳强度,残余拉应力相反;表面硬化层可阻碍已有疲劳裂纹的扩大和新裂纹的产生(4)对零件耐腐蚀性的影响:表面粗糙度的凹谷处就易聚集腐蚀介质而发生腐蚀,其强烈程度与凹谷深度及尖狭度成正比。
零件在有残余应力状态下工作,可能产生应力腐蚀。
在表面有裂纹存在时,更会加剧腐蚀作用。
(5)对零件接触刚度的影响:在连接面上的压力一定时,表面越粗糙,则接触处的压强越大,接触处的变形也越大,使接触刚度越低。
基准:就是根据的意思,在零件图上或实际零件上用来确定其他点、线、面的位置的那些点、线、面,就称为基准设计基准:在产品图或零件图上用以确定其他点、线、面的位置所依据的基准,即标注设计尺寸的起点,称为设计基准。
机电诊断与维修复习题(1)

机电设备故障诊断与维修复习题第一章一、填空1、机械零件常见的失效形式有(磨损)、(断裂)、(变形)和(腐蚀)四种。
2、零件摩擦表面的金属在相对运动过程中不断损失的现象称为(磨损),根据零件磨损机理的不同,分为:(粘着磨损)、(磨料磨损)、(疲劳磨损)和(腐蚀磨损)。
3、粘着磨损的特征是接触表面的材料从一个表面(转移到)另一个表面,又称为粘附磨损、咬合磨损。
4、疲劳磨损特点是产生接触疲劳的零件表面上出现许多(针状)或(痘状)的凹坑,称麻点。
5、机械零件磨损过程分为三个阶段:(跑合)、(稳定)和(失效),其中,(稳定)阶段决定了零件使用寿命。
6、(腐蚀)是指表面与周围介质起化学或电化学作用而发生的表面破坏现象。
按金属腐蚀的机理可分为(化学腐蚀)和(电化学腐蚀)两类。
7、腐蚀磨损分为:(氧化磨损)、(化学腐蚀磨损)。
8、在摩擦过程中,金属同时与周围介质发生化学或电化学反应,使(腐蚀)和(磨损)共同作用,导致零件表面物质的损失,这种现象称为(腐蚀磨损)。
9、断裂按零件断裂后的自然表面特征分为(塑性断裂)和(脆性断裂)。
10、疲劳断裂断口有三个形貌不同的区域,即(疲劳核心区)、(疲劳裂纹扩大区)和(瞬断区)。
11、延性断裂的宏观特点就是断裂前有明显的塑性变形,常出现(颈缩),断面有大量的微坑覆盖。
12、在重复及交变载荷的长期作用下,零件会发生断裂,称为疲劳断裂。
实际失效中,疲劳断裂约占(80%—90%)。
13、机械零件或构件在外力作用下,产生形状或尺寸变化的现象叫(变形),它分为(弹性变形)和(塑性变形)两种类型。
14、变形是不可避免的,减少变形的主要措施应从(设计)、(加工)、(修理)和(使用)四方面入手。
15、在磨损的三个阶段中,决定零件寿命的阶段是(稳定磨损)。
二、判断题1、一般机械设备中约有80%的零件因磨损而失效报废。
(对)2、当机件出现斑点或凹坑后,机件的振动和噪声急剧增加,精度大幅下降,意味着发生了腐蚀磨损。
微动磨损的扩展与预防

防止 其 进 一 步 扩 展 ,对 减 少 故 障 的 发 生 和 减 轻 故 障
症状 有着重要意义 。
l 微 动 磨 损 的特 征
根 据 文 献 介 绍 ,微 动 磨 损 一 般 发 生 在 名 义 上 相 对 静 止 ,实 际 上 存 在 循 环 的 相 对 微 幅 滑 动 的 两 个 紧 密接 触 的机 件 表 面上 。如 滚 动 轴 承 的 内 、外 套 圈 与 轴 、 孑 的配 合 面 , 机 叶 轮 孑 与 轴 的 配 合 面 , 相 座 L 风 L 其
7: 5 4
2d 8 62 .
5 9
2d 8 4. 32
41 .6
出 磨
出 厂
3 . O5
3 . 16 38 .O 2.1 O
2 3 .O
2 41 .
6O .
75 .
6: 5 1
6: 5 2
3 生 产 中应 注 意 的 问题
1 配 料 时 熟 料 K 宜 高 不 宜 低 , 因是 萤 石 有 矿 ) H 原 化作用 , 加速熟料矿 物的形成 。 K 能 H低 于 0 8 0熟 .6
t创 经济效益约 5 , 0万 元 。该 产 品 在 洛 三 高 速 公 路 建
设 中 , 到用户普遍好 评 。 受
( 辑 编 王新频 )
司采 用 湿 法 长 窑 煅 烧 缓 凝 熟 料 , 尾 温 度低 , 少 了 窑 减
氟对 环 境 的 污 染 。
CE- EN T 2 o 。 . _ 0 2 No 7
维普资讯
3 2
+
20 0 2年 7期
摩擦学原理知识点整理

绪论1、摩擦学定义:是关于相对运动的相互作用表面的科学技术,包括摩擦、润滑、磨损和冲蚀。
2、摩擦学研究内容主要包括:摩擦、磨损、润滑以及表面工程技术。
3、摩擦:是抵抗两物体接触表面在外力作用下发生切向相对运动的现象。
4、磨损:着重研究与分析材料和机件在不同工况下的磨损机理、发生规律和磨损特性。
5、润滑:研究内容包括流体动力润滑、静力润滑、边界润滑、弹性流体动力润滑等在内的各种润滑理论及其在实践中的应用。
6、表面工程技术:将表面与摩擦学有机结合起来,解决机器零部件的减摩、耐磨,延长使用寿命的问题。
第一章1、表面形貌:微观粗糙度、宏观粗糙度(即波纹度)和宏观几何形状偏差。
2、表面参数:(1)算术平均偏差Ra 是在一个取样长度lr 内纵坐标值Z (x )绝对值的算术平均值。
(2)轮廓的最大高度Rz 是在一个取样长度lr 内最大轮廓峰高Zp 和最大轮廓谷深Zv 之和的高度。
(3)均方根偏差Rq 是在一个取样长度lr 内纵坐标值Z (x )的均方根值。
3、对于液体,表层中全部分子所具有的额外势能的总和,叫做表面能。
表面能越高,越易粘着。
4、物理吸附:当气体或液体与固体表面接触时,由于分子或原子相互吸引的作用力而产生的吸附叫做物理吸附,是靠范德华力维系的,温度越高,吸附量越小。
物理吸附薄膜形成的特点是吸附和解吸附具有可逆性,无选择性。
5、化学吸附:极性分子与金属表面的电子发生交换形成化学键吸附在金属表面上,且极性分子呈定向排列。
化学吸附的吸附能较高,比物理吸附稳定,且是不完全可逆的,具有选择性。
6、粘附:是指两个发生接触的表面之间的吸引。
7、影响粘附的因素:①润湿性,②粘附功,③界面张力,④亲和力。
8、金属表面的实际结构:(1)外表层:①污染层,②吸附气体层,③氧化层;(2)内表层:①加工硬化层,②金属基体。
第二章1、固体表面的接触分类:(1)点接触和面接触。
(2)①弹性接触(赫兹接触),②塑性接触,③弹塑性接触,④粘弹性接触。
第九章--螺旋传动1

第三节 滚珠螺旋传动
构成:丝杆、螺母、滚珠和滚珠循环返回装置等四个部分
中径尺寸变动量旳公差 中径跳动公差
3.牙型半角误差
当螺纹各牙间牙型角有差 别,会引起螺距变化,从 而影响传动精度
牙型角在螺纹全长上变化 不大(一次装刀切削), 对传动精度影响小
(二)螺杆轴向窜动误差 螺杆轴肩端面与轴承止推面不垂直,有α1、α2旳偏差
螺杆转动时,最大轴向窜动误差:
max D tan min
旋合长度分长、中、短三种,表9-6 一般按中档长度考虑,
② 将不同旳公差等级(即公差带大小)和基本偏差(即 公差带位置)组合,可得最终公差带。
例7H,8g(H7,g8——1998国标)
④ 螺纹公差带旳选用,表9-8 6级公差——基本级 *公差带——优先选择
H/h配合——最小间隙为零,多采用此配合 G/h,H/g——确保间隙,合用于要求迅速装卸旳螺纹
螺杆转动,螺母也转动,成果螺母实现差 动移动,即螺杆转Δn周,则螺母移距大 小为Ph±ΔPh,Ph-导程,正号表达两构 件转向相同,则移距为两者移距之和,负 号表达两构件转向相反,则移距为两者移 距之差,该机构构造简朴,可实现微动和 迅速移动。
两个螺母一种移动,一种固定。 当螺杆转动时,移动螺母可实现 迅速或慢速移动,即螺杆转一周, 移动螺母移动Ph1±Ph2(Ph1、 Ph2为两螺旋旳导程,旋向相同 步为正,螺母迅速移动,反之, 螺母慢速移动。)
如L/d1>25,受压螺杆应进行稳定性验算 3.为防止周期误差应选用单头螺纹,传动精度高。
4.小转角大位移旳情况用多头螺纹。
(五)螺纹公差
公差等级 公差带大小
基本偏差 公差带位置
公差带 旋合长度
螺纹精度
机械设计注意事项_New

机械设计注意事项第1章提高强度和刚度的结构设计1.1避免受力点与支持点距离太远1.2避免悬臂结构或减小悬臂长度1.3勿忽略工作载荷可以产生的有利作用1.4受振动载荷的零件避免用摩擦传力1.5避免机构中的不平衡力1.6避免只考虑单一的传力途径1.7不应忽略在工作时零件变形对于受力分布的影响1.8避免铸铁件受大的拉伸应力1.9避免细杆受弯曲应力2.8勿使过滤器滤掉润滑剂中的添加剂2.9滑动轴承的油沟尺寸、位置、形状应合理2.10滚动轴承中加入润滑脂量不宜过多2.11对于零件的易磨损表面增加一定的磨损裕量2.12注意零件磨损后的调整2.13同一接触面上各点之间的速度、压力差应该小2.14采用防尘装置防止磨粒磨损2.15避免形成阶梯磨损2.16滑动轴承不能用接触式油封2.17对易磨损部分应予以保护2.18对易磨损件可以采用自动补偿磨损的结构第3章提高精度的结构设计3.1尽量不采用不符合阿贝原则的结构方案3.2避免磨损量产生误差的互相叠加3.3避免加工误差与磨损量互相叠加3.4导轨的驱动力作用点,应作用在两导轨摩擦力的压力中心上,使两条导轨摩擦力产生的力矩互相平衡3.5对于要求精度较高的导轨,不宜用少量滚珠支持3.6要求运动精度的减速传动链中,最后一级传动比应该取最大值3.7测量用螺旋的螺母扣数不宜太少3.8必须严格限制螺旋轴承的轴向窜动3.9避免轴承精度的不合理搭配3.10避免轴承径向振摆的不合理配置3.11避免紧定螺钉影响滚动导轨的精度3.12当推杆与导路之间间隙太大时,宜采用正弦机构,不宜采用正切机构3.13正弦机构精度比正切机构高第4章考虑人机学的结构设计问题4.1合理选定操作姿势4.2设备的工作台高度与人体尺寸比例应采用合理数值4.3合理安置调整环节以加强设备的适用性4.4机械的操纵、控制与显示装置应安排在操作者面前最合理的位置4.5显示装置采用合理的形式”4.6仪表盘上的刻字应清楚易读4.7旋钮大小、形状要合理4.8按键应便于操作4.9操作手柄所需的力和手的活动范围不宜过大4.10手柄形状便于操作与发力4.11合理设计坐椅的尺寸和形状4.12合理设计坐椅的材料和弹性4.13不得在工作环境有过大的噪声4.14操作场地光照度不得太低第5章考虑发热、腐蚀、噪声等问题的结构设计5.1避免采用低效率的机械结构5.2润滑油箱尺寸应足够大5.3分流系统的返回流体要经过冷却5.4避免高压容器、管道等在烈日下曝晒5.5零件暴露在高温下的部分忌用橡胶,聚乙烯塑料等制造56精密机械的箱体零件内部不宜安排油箱,以免产生热变形5.7对较长的机械零部件,要考虑因温度变化产生尺寸变化时,能自由变形5.8淬硬材料工作温度不能过高5.9避免高压阀放气导致的湿气凝结5.10热膨胀大的箱体可以在中心支持5.11用螺栓联接的凸缘作为管道的联接,当一面受日光照射时由于两面温度及伸长不同,产生弯曲5.12与腐蚀性介质接触的结构应避免有狭缝5.13容器内的液体应能排除干净5.14注意避免轴与轮毂的接触面产生机械化学磨损(微动磨损)5.15避免易腐蚀的螺钉结构5.16钢管与铜管联接时,易产生电化学腐蚀,可安排一段管定期更换5.17避免采用易被腐蚀的结构5.18注意避免热交换器管道的冲击微动磨损5.19减少或避免运动部件的冲击和碰撞,以减小噪声5.20高速转子必须进行平衡5.21受冲击零件质量不应太小5.22为吸收振动,零件应该有较强的阻尼性第6章铸造结构设计6.1分型面力求简单6.2铸件表面避免内凹6.3表面凸台尽量集中6。
电大机电设备诊断与维修考试复习题

综合练习(模拟试题)1.影响粘着磨损的因素为:摩擦表面的状态和摩擦表面材料的成分和金相组织。
2.设备诊断技术尽管很多,但基本上离不开:信息的采集、信息的分析处理、状况的识别,诊断,预测,决策三个环节。
3.金属扣合技术方法可分为:强固扣合法、强密扣合法、优级扣合法、热扣合法。
4.数控设备电气现场维修的一般方法是:常规检查、静态检查、动态检查。
5.机床试验的内容主要有:空运转试验、机床负荷试验、机床工作精度试验。
6.在对数控机床根据诊断程序进行故障诊断时,诊断程序一般分为:启动诊断、在线诊断和离线诊断三套程序。
7.振动信号的分析方法,可按信号处理方式的不同分为:幅域分析、时域分析、频域分析三个环节。
8.按修理内容、修理技术要求和修理工作量大小分类,设备预防性计划修理可分为:大修、项修和小修。
9.机床电气设备维护对象主要有:电动机、电器和控制线路。
10.振动监测周期可分为:定期检测、随机检验、长期连续监测三类。
11.常用铸铁件补焊的方法有气焊、电弧焊、钎焊。
12.数控机床的故障,按其发生部位,基本可分为4大部分:机床本体上的电气部分、伺服放大及位置检测部分、计算机部分、交流主轴控制部分。
13.根据零件摩擦表面的破坏程度,粘着磨损可分为5类,它们是:轻微磨损、涂抹、擦伤、撕脱和咬死。
14.影响微动磨损的主要因素为:振幅、载荷、温度、润滑和材质性能。
15.常见的化学腐蚀形式有:大气腐蚀、土壤腐蚀、在电解质溶液中的腐蚀和在熔融盐中的腐蚀。
16.通常用于描述机械振动响应的三个参数是:(振幅)、(频率)、(相位)。
17.滚动轴承的振动信号分析故障诊断方法可分为:(简易诊断法)、(精密诊断法)。
18.失效的机械零件大部分都可以修复的,尤其是磨损失效的零件,可采用(堆焊)、(热喷涂和喷焊)、(电刷镀)等表面技术。
19.摩擦是不可避免的自然现象,磨损是摩擦的必然结果,二者均发生于(材料表面)。
20.通过事前测试或监控可以预测的故障属于(渐发故障)。
微动损伤的机理、特征及诊断

微 动损 伤 的 机 理很 复杂 ,很难 用 一 种 观点 概 括解
释所 有 现象 。纵观 已有 的研 究 成果 , 动损 伤 是粘 着 、 微 磨损 、氧化 和疲 劳这 四种 基 奉 损 伤机 理 的 叠加 和 相互 影响 造成 的 。可 归纳 为粘 着 一 化一 层 的理 论 。 氧 脱 微 动损 伤 初 始 阶 段 的机 理 , 比较 一 致 的看 法 是 粘 着和 氧 化 。 囚为 任何 构 件 的 表 面 都 是 由极 薄 的表 面 氧 化膜 和 吸 附 的污 染 物 或气 体 覆 盖 着 ,而 且 其 表 面总 是 高低不平的 , 因此 两 表 面接 触 时 , 总是 凸起 点 先 接 触 。 实 际测 定 ,一 般 摩擦 副 表 面的 实 际 接触 面 积 只有 几 何 表 面积 的 01 00 %。对 于 重 载高 速 摩擦 副 , . ̄ .1 接触 峰 点
Байду номын сангаас
粗 车循 环指 令 中设 定 r 刀 速 度 ,在 屏 蔽 轴输 出 走
的控 制 方 式 中 ,控 制 软 件按 替 代 后 的精 车 余 量 预 留轮
廓进 行 插 补运 算 ,而 真 正 的进 给 控 制则 大 部 分情 况 下
按单 轴 运 动输 出 。为使 指 令 中设 定 的走 刀 速 度 成为 粗
关键词 : 动损 伤 ;机 理 ;特 征 ;诊 断 微 中 图分类 号 :H1 71 T 1.
1 引 言
文 献标 识码 : A
文 章编 号 :0 2 2 3 ( 0 2 0 - 0 2 0 10- 3 3 20 ) 9 0 3- 2
微 动损 伤是 一种 涉 及 范 围相 当广 泛 ,危 害 相 当严 重, 几乎所 有 的工程 机 械都 可 能发 生 的现 象 。所谓 微动 损伤 , 指两 个 相 互 接触 、 义 上相 对 静 止 的表 面实 际 是 名 上处 于 周期 性 、小 振 幅相 对 滑 动运 动 而 引起 的零 件松 动、 功率 损失 、 噪声 增 加 、 动 副 咬 死 的状 态 , 得机 械 运 使 表 面或 亚 表 面产 生微 裂纹 ,并 在重 复应 力作 用 下 发展 成疲 劳断 裂 的现象 。随着科 技 的迅猛 发展 , 械设 备 自 机 动 化程 度 的提 高 , 作 条 件 越 来 越 苛 刻 , 工 因而 对 零 、 部 件 的精 度 、 用 寿 命 及 可 靠 性 的要 求 将 会 更 高 , 此 , 使 因 微动 损伤 问题 亟待 解 决 。
西工大机械原理第9章机械零件设计概论

3.疲劳磨损,即疲劳点蚀 是高副(点、线接触)机械零件的常见磨损形式。
§9-4 机械零件的耐磨性
4. 腐蚀磨损 摩擦表面在摩擦过程中,伴随有表面材料被腐蚀 的现象,这种情况下产生的磨损即为腐蚀磨损。 除了上述四种基本磨损类型以外,还有侵蚀磨损、 微动磨损等其他形式。
确定零件的形状和主要尺寸。 应当注意,零件尺寸的计算值一般并不是最终采用的
数值,设计者还要根据制造零件的工艺要求和标准、 规格加以圆整。 5) 绘制工作图并标注必要的技术条件。
§9-2 机械零件的强度
一、载荷 1. 载荷:进行强度计算所依据的、作用于零件上的 外力F、弯矩M、扭矩T以及冲击能量等,统称为 载荷。 2. 机械零件实际承受的载荷: ① 静载荷:大小、作用位置和方向不随时间变化 或变化缓慢的载荷。 ② 变载荷:大小、作用位置或方向随时间变化的 载荷。 ③ 动载荷:由于运动中产生的惯性力和冲击等引 起的载荷。
§9-3 机械零件的接触强度
3. 两个轴线平行的圆柱体相互接触并受压时,最大接触应力发 生在接触区中线上,其值由赫兹(H.Hertz)公式计算:
H
11
Fn
1 2
b 1 12 1 22
E1
E2
令
1 1 1 1 2
及 1 1 21,
E1 E2 E
对于钢或铸铁,取μ1=μ2 =μ=0.3,则上式简化为:
H
1 Fn E
2(1 2)b
0.418
Fn E
b
§9-3 机械零件的接触强度
4. 零件受接触变应力作用时接触强度条件为 σH≤[σH] 而[σH] = σHlim/SH
材料力学性能课后题,参考看下

第七章1、磨损:机件表面相接处并作相对运动时,表面逐渐有微小颗粒分离出来形成磨屑,使表面材料逐渐流失、造成表面损伤的现象。
2、粘着:摩擦副实际表面上总存在局部凸起,当摩擦副双方接触时,即使施加较小载荷,在真实接触面上的局部应力就足以引起塑性变形。
倘若接触面上洁净而未受到腐蚀,则局部塑性变形会使两个接触面的原子彼此十分接近而产生强烈粘着。
(实际上就是原子间的键合作用)3、磨屑:松散的尺寸与形状均不相同的碎屑????4、跑合:摩擦表面逐渐被磨平,实际接触面积增大,磨损速率迅速减小。
5、咬死:当接触压应力超过材料硬度H的1/3时,粘着磨损量急剧增加,增加到一定程度就出现咬死现象。
6、犁皱:指表面材料沿硬粒子运动方向被横推而形成沟槽。
7、耐磨性:材料在一定摩擦条件下抵抗磨损的能力8、冲蚀:流体或固体以松散的小颗粒按一定的速度和角度对材料表面进行冲击。
9、接触疲劳:机件两接触面作滚动或滚动加滑动摩擦时,在交变接触压应力长期作用下,材料表面因疲劳损伤,导致局部区域产生小片或小块状金属剥落而是材料流失的现象。
10、是比较三类磨粒磨损的异同,并讨论加工硬化对它们的影响?⑴凿削式磨粒磨损:从表面上凿削下大颗粒金属,摩擦面有较深沟槽。
韧性材料——连续屑,脆性材料——断屑。
⑵高应力碾碎性磨粒磨损:磨粒与摩擦面接触处的最大压应力超过磨粒的破坏强度,磨粒不断被碾碎,使材料被拉伤,韧性金属产生塑性变形或疲劳,脆性金属则形成碎裂式剥落。
⑶低应力擦伤性磨粒磨损:作用于磨粒上的应力不超过其破坏强度,摩擦表面仅产生轻微擦伤。
11、试述粘着磨损产生的条件、机理及其防止措施?条件:在滑动摩擦条件下,当摩擦副相对滑动速度较小时发生的。
机理:摩擦副实际表面上总存在局部凸起,当摩擦副双方接触时,即使施加较小载荷,在真实接触面上的局部应力就足以引起塑性变形。
倘若接触面上洁净而未受到腐蚀,则局部塑性变形会使两个接触面的原子彼此十分接近而产生强烈粘着。
微动磨损工况下二维柱面对平面磨损形貌的数值计算与分析

机械设计与制造34Machinery Design&Manufacture第5期2021年5月微动磨损工况下二维柱面对平面磨损形貌的数值计算与分析唐正强打张慧杰2,李俨2,张太华3(1.贵州大学机械工程学院,贵州贵阳550025;2.贵州大学现代制造技术教育部重点实验室,贵州贵阳550025;3.贵州师范大学机械与电气工程学院,贵州贵阳550001)摘要:基于改进的Archard磨损方程,推导了适应于不同微动振幅下的局部磨损方程,建立了二维刚性柱面-平面的微动磨损数值模型,研究了微动工况、材料参数对平面磨损形貌的影响规律。
结果表明,在柱面载荷为20MPa,微动振幅为4滋m的工况下,随着柱面半径的增大,平面的磨损宽度逐渐增大,磨损深度逐渐减小;在微动振幅为4滋m的工况下,随着施加在柱面上载荷的增大,平面的磨损形貌呈现出变宽变深的趋势;在柱面载荷为20MPa,微动振幅为4滋m的工况下,随平面弹性模量的增大,平面的磨损轮廓从宽而浅变化到窄而深。
其次,根据Hertz接触理论和Archard磨损方程预测的平面磨损面积与本论文中模型计算的结果进行了对比,结果发现在磨损初期,两者间差别不大,随着微动循环次数的增加,Hertz理论预测结果小于这里模型计算的结果。
关键词:微动磨损;局部磨损方程;有限元;磨损形貌中图分类号:TH16文献标识码:A文章编号:1001-3997(2021)05-0034-06Numerical Analysis of the Effect of Fretting Wear Conditionson Two-Dimensional Cylinder-Flat Wear ProfilesTANG Zheng-qiang1,ZHANG Hui-jie2,LI Yan2,ZHANG Tai-hua3(1.School of Mechanical Engineering,Guizhou University,Guizhou Guiyang550025,China;2.Key Laboratory of Modern Manufacturing Technology,Ministry of Education,Guizhou University,Guizhou Guiyang550025,China;3.College of Mechanical and Electrical Engineering,Guizhou Normal University,Guizhou Guiyang550001,China)Abstract:A local wear equation applied for arbitrary tangential displacement is derived based on the Archard wear equation.A fretting wear model ofthe cylinder-flat is developed to study the effect of wear conditions and materials properties on wear profile ofthe elastic flat.The results show thatat a normal load of20MPa anddis p lac e m e nt amplitude of4滋m,we observe that with an increase in the cylinder radius,the wear width of the flat increases whereas the wear depth of the flat decreases.With an increase in the normal load,both the wear width and the wear depth increase.The wear width of the flat slightly decreases and the wear depth increases as the elastic modulus of the cylinder increases.In addition,the wear area calculated by the present model is compared with the wear area predicted by the Hertz contact theory and the Archard wear equation.We found that the result is similar at the initial stage of f retting wear.However,with the increase of the fretting wear cycles,t he wear area predicted by the Hertz theory and the A rchard wear equation is smaller than the present model.Key Words:Fretting Wear;Local Wear Equation;Finite Element Method;Wear Profiles1引言微动是发生在两接触表面之间微、纳米量级的运动|1]。
摩擦学简明教程
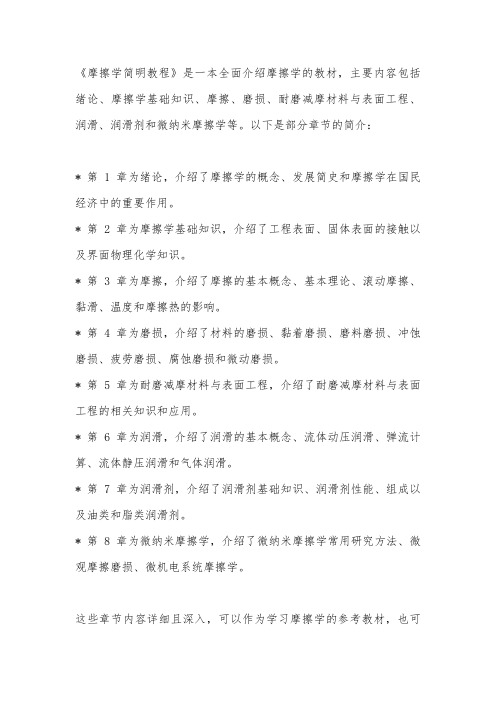
《摩擦学简明教程》是一本全面介绍摩擦学的教材,主要内容包括绪论、摩擦学基础知识、摩擦、磨损、耐磨减摩材料与表面工程、润滑、润滑剂和微纳米摩擦学等。
以下是部分章节的简介:
* 第1章为绪论,介绍了摩擦学的概念、发展简史和摩擦学在国民经济中的重要作用。
* 第2章为摩擦学基础知识,介绍了工程表面、固体表面的接触以及界面物理化学知识。
* 第3章为摩擦,介绍了摩擦的基本概念、基本理论、滚动摩擦、黏滑、温度和摩擦热的影响。
* 第4章为磨损,介绍了材料的磨损、黏着磨损、磨料磨损、冲蚀磨损、疲劳磨损、腐蚀磨损和微动磨损。
* 第5章为耐磨减摩材料与表面工程,介绍了耐磨减摩材料与表面工程的相关知识和应用。
* 第6章为润滑,介绍了润滑的基本概念、流体动压润滑、弹流计算、流体静压润滑和气体润滑。
* 第7章为润滑剂,介绍了润滑剂基础知识、润滑剂性能、组成以及油类和脂类润滑剂。
* 第8章为微纳米摩擦学,介绍了微纳米摩擦学常用研究方法、微观摩擦磨损、微机电系统摩擦学。
这些章节内容详细且深入,可以作为学习摩擦学的参考教材,也可
作为对摩擦学感兴趣的读者的参考读物。
如需了解更多内容,可以购买纸质书进行阅读。
- 1、下载文档前请自行甄别文档内容的完整性,平台不提供额外的编辑、内容补充、找答案等附加服务。
- 2、"仅部分预览"的文档,不可在线预览部分如存在完整性等问题,可反馈申请退款(可完整预览的文档不适用该条件!)。
- 3、如文档侵犯您的权益,请联系客服反馈,我们会尽快为您处理(人工客服工作时间:9:00-18:30)。
二、微动磨损理论
一个较为完满的微动磨损理论应该能对下列
实验现象作出合理的解释:
真空或惰性气氛中微动损伤较小; 微动产生的磨屑主要由氧化物组成; 循环数一定时,低频微动比高频损伤大; 材料流失量随负荷和振幅而增加; 低于室温比高于室温的磨损严重; 空气环境比湿空气中损伤大。
微动磨损 杜永平
1990年,Godet提出微动三体理论;
1990年,第三届ASTM Symposium On
Standarization Of Fretting Fatigue Tests
Methods and Equipment在美国的Philadelphia 召开,宣读论文20篇; 1992年,Waterhouse发表了Fretting Wear综述 论文;
微动磨损 杜永平
2. 微动磨损的发展历程 1911年,Eden、Rose和Cunningham首先观察 到微动与疲劳的联系; 1924年,Gillet和Mack发表了机器紧固件因微 动导致疲劳寿命明显降低的报告; 1927年,Tomlinson认为腐蚀是次要因素并提出 了一种微动机理; 1941年,Warlow-Davies注意到微动可以加速 疲劳破坏; 1949年,Mindlin提出在一定条件下,微动区存 在滑移区和非滑移区,计算分析了接触表面的 应力分布;
了一种早期的微动疲劳模型;
1970年,Hurrick在Wear发表The Mechanism Of Fretting的论文,认为微动分为三个过程;
微动磨损 杜永平
1972年,Waterhouse发表了首部编著Fretting
Corrosion,Hoeppner提出了微动疲劳极限的概
念; 1974年,Specialists Meeting On Fretting in Aircraft在德国Munich召开,发表论文16篇; 1977年,Waterhouse将大位移滑动磨损的剥层
微动磨损中: 金属表面微凸体接触后形成冷焊点,微动往复
式多次反复运动,使某些冷焊点发生断裂,同
时出现材料转移,因此,磨损率低。
微动磨损 杜永平
微动的早期,金属表面氧化膜破裂后,粘着倾
向迅速增大。发生断裂并形成松散磨粒后,粘
着倾向会逐渐减小,最后过渡到平稳阶段。粘
着阶段持续的时间与材料及环境有关。
2001年,在日本召开3rd International
Symposium On Fretting Fatigue,并形成每3
年一次的微动疲劳系列国际会议。
3. 一些统计数据
(1)国家和地区的分布
按照发表论文的数量,主要有英国、法国、 美国、日本、加拿大、瑞典、德国、中国、瑞 士和比利时。这些国家发表的论文数占论文总 数的90%以上。
微动磨损 杜永平
接触首先发生在微凸体
上,少量磨屑落入谷内; 磨屑填满谷,使磨损变 成磨粒磨损。许多微凸体 合并成一个小平台; 磨屑进一步增加,并开 始从接触区溢出进入邻近 的洼谷区;
微动磨损 杜永平
接触区压力再分布,中
心压力增高,边缘压力降
低,使中心的磨粒磨损加
重,凹坑迅速加深。 模型很快为科学家们所接受: 形象地说明微动磨损中表面变粗糙的现象 确立了磨粒磨损是稳态阶段的特征 不足:至今尚未达到令人满意的定量描述。
微动磨损 杜永平
④ 环境影响
微动的研究不再局限于普通工况,除在传统的
蒸气介质、生物性腐蚀介质、
超低温和强磁场等特殊环境下的微动破坏机理的 研究也得到积极开展。
⑤ 防护措施
研究领域已从微动破坏机理研究走向机理与抗 微动破坏研究并重的阶段,各种减缓技术如表面 处理、润滑和结构设计改进等有很大的进展。
微动磨损 杜永平
⑥ 工业应用
航空部门、核电站、高空电缆、钢丝绳索、大
型轴、人工植入器官、电接触等工业领域的微动
损伤已日益成为研究热点。
4. 微动磨损的特征
具有引起微动的振动源(机械力、电磁场、冷 热循环等),流体运动所诱发的振动; 磨痕具有方向一致的划痕、硬结斑和塑性变形 以及微裂纹; 磨屑易于聚团、含有大量类似锈蚀产物的氧化 物。
微动磨损 杜永平
(2)氧化作用 金属表面的氧化膜对防 止冷焊十分有效,有利于 防止粘着。
能在金属表面生成附着
牢固,且在微动下能出现 一层釉质氧化物层的材料, 其磨损量和摩擦系数将随 微动而明显下降。
微动磨损 杜永平
氧化对微动磨损的影响: 贵金属或惰性气氛环境中合金间的微动磨损, 氧不参与作用,以粘着及塑性变形机制为主; 薄而附着不牢的氧化膜,在不到一次微动循环 便被破坏,这时氧化与机械两种机制均对微动 磨损有贡献; 氧化较严重而且氧化膜易碎裂成片,氧化与机 械两种机制的协同作用加速表面破坏; 氧化层致密能起减摩作用,如钛合金、镍铬铝 合金在高温下的微动磨损,氧化作用缓解了机 械摩擦导致的损伤。
着受抑制,摩擦系数
降低; ④磨屑连续不断地形成和排除,其成分和接触表
面随时间改变,形成和排出的磨屑达到平衡, 微动磨损进入稳定阶段。
微动磨损 杜永平
3. 微动磨损的发展过程
(1)粘着机制在微动磨损中的作用
普通滑动磨损中,金属表面的微凸体接触后形 成冷焊点,受切向力作用发生断裂,同时出现材 料转移。这是单方向上一次作用下实现的。
1992年,Zhou和Vincent提出二类微动图理论,
成为揭示微动运行和损伤规律的重要理论;
微动磨损
杜永平
1993年,在英国的Sheffield召开International
Symposium On Fretting-Fatigue,宣读论文37
篇;
1996年,在英国的Oxford召开Euromech 346 On Fretting Fatigue会议,宣读论文18篇;
微动磨损 杜永平
3. 微动的三体理论 微动的三体理论认为磨屑的产生可看成是两个 连续和同时发生的过程: ① 磨屑的形成过程 接触表面粘着和塑性变形,并伴随强烈的加 工硬化; 加工硬化使材料脆化,白层同时形成,随着 白层的破碎,颗粒剥落; 颗粒被碾碎,并发生迁移,迁移过程取决于 颗粒的尺寸、形状和机械参数(如振幅、频 率、载荷等)。
微动磨损
杜永平
② 理论分析
理论分析不再局限于Hertz弹性接触理论,而 借助计算机、弹塑性力学、断裂力学、有限元 法、能量分析(包括热力学)等研究手段来模
拟微动的运行和破坏过程。
③ 新材料
过去的研究主要集中在金属材料,尤其是各种
钢和铝合金,现在已有不少研究者开始致力于各
种新材料的微动损伤规律的研究。
微动磨损 杜永平
(2)研究机构及人员 约有300名研究人员作为第一作者或合作者在 刊物和会议上发表微动摩擦学研究的论文,一
半左右仅出现一次署名。发表微动摩擦学研究
论文最多的有七个研究单位,主要集中在法国、
英国、美国。
(3)研究领域分布
微动磨损和微动疲劳方面发表的论文数各占近
一半,而有关微动腐蚀的论文相对较少。
微动磨损 杜永平
1950年,第一届ASTM Symposium On Fretting
Corrosion在美国的Philadelphia召开,并宣读五
篇论文,会上由I—Ming Feng和Rightmire提出
了一种微动理论; 1951年,Uhlig在J.Appl.Mech发表了题为 Mechanism Of Fretting Corrosion的论文; 1969年,Nishioka、Nishimura和Hirakawa提出
W (5.05 10 P
6 1 2
N 1.5 10 P ) 4.16 10 6 bPN f
8
Uhlig的模型不足:
忽略了氧化膜起到防止材料粘着的有利作用
忽略了微动过程中磨屑参与磨损的作用 因此它不能解释实验中出现的许多现象,至少 对微动磨损随循环次数的变化规律不能给予完满 的说明。
微动磨损 杜永平
② 磨屑的演化过程
起初磨屑呈轻度氧化,仍为金属本色,粒度为
微米量级(约1μm);
在碾碎和迁移过程中进一步氧化,颜色变成灰
褐色,粒度在亚微米量级(约0.1μm);
磨屑深度氧化,呈红褐色,粒度进一步减小为 纳米颗粒(约10nm) ,射线衍射分析表明磨 屑含α-Fe、α-Fe2O3(呈红色)和低百分比的 Fe3O4。
1997年,在中国成都召开首届International
Symposium On Fretting,宣读论文32篇;
1998年,在美国Salt Lake City召开2nd
International Symposium On Fretting Fatigue, 发表学术论文近40篇;
微动磨损 杜永平
微动磨损 杜永平
利用三体理论可很好地解释钢铁材料微动摩擦系 数随循环周次的变化过程: ①接触表面膜去除,摩擦系数较低; ②第一、二体 之间相互作 用增加,发 生粘着,摩 擦系数上升, 并伴随材料 组织结构变 化;
微动磨损 杜永平
③磨屑剥落,第三体床 形成,二体接触逐渐 变成三体接触,因第
三体的保护作用,粘
微动磨损 杜永平
总的微动磨损量:
W Wc Wm ( K 0 P
1 2
N K 1 P ) K 2bPN f
第一项化学因素引起 第二项机械因素引起 微动磨损量是:
微动频率的双曲线函数
负荷的抛物线函数 循环次数和振幅呈线性关系
微动磨损 杜永平
Uhlig根据钢的微动磨损实验得到经验公式为:
(delamination)理论引入微动磨损的研究;
1981年,Waterhouse编辑出版了由10篇论文组 成的Fretting Fatigue论文集;