利用紫杂铜和国产连铸连轧设备生产低氧光亮铜杆
再生铜产业的现在与未来

再生铜产业的现在与未来徐庭芳【期刊名称】《《中国金属通报》》【年(卷),期】2011(000)009【总页数】2页(P20-21)【作者】徐庭芳【作者单位】中国有色金属工业协会再生金属分会【正文语种】中文再生金属产业作为节能环保产业领域的重要组成部分,被列入国家七大战略性新兴产业之一给予重点支持,可以预见到2011年国家将会有新一轮政策扶持和鼓励措施不断促进行业的发展,在国家大力发展资源循环利用产业的历史机遇下,再生铜产业将逐步实现经营集约化,产业集中度高,产业结构优化的目标,跨入新的历史阶段。
2010年是废铜市场逐步恢复的一年。
经历过2008年金融危机的价格暴跌,2010年随着全球经济的逐步复苏,国内政策支持的力度不断加大以及市场需求的提升,再生铜产业保持了稳定发展速度。
2010年再生铜全年产量约为240万吨,同比增长约20%,如图1所示。
1.市场价格表现目前铜已经成为一种金融属性极强的投资品。
2010年在全球经济逐步复苏的背景下,世界范围内量化宽松货币政策使得铜价在高位运行,虽然年内央行两次加息并多次上调存款准备金率,铜价受影响不大,年底铜价突破72000元/吨,为历史同期最高水平。
2010年废铜市场报价呈现易涨难跌的态势,若是铜价涨幅较大,废铜价格一般都能明显跟涨,但铜价小幅走跌时,废铜持货商一般较为惜售,废铜价格逐步上升。
2. 废铜原料2010年市场对废铜的需求量巨大,2010年中国废铜进口实物量与2009年相比数量上略有增加,我国共进口含铜废料实物量436万吨,与2009年同期相比增加36万吨,增幅为9%。
由于国内外市场倒挂严重含铜废料实物量进口有限,进口含铜实物量较2008年经济危机之前558万吨仍低22%。
同时进口废料含铜品位进一步降低,进口废铜约130万吨。
2010年随着国内家电以旧换新政策的持续,实施电网改造等项目的不断推进以及国内回收交易市场的不断规范和发展使得国内铜回收量得到了一定的补充。
紫杂铜连铸连轧生产光亮铜杆工艺设计中熔炼设备的比选(续)
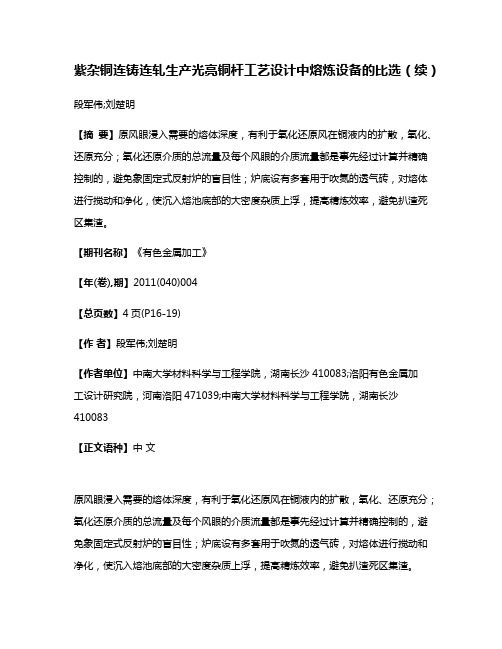
紫杂铜连铸连轧生产光亮铜杆工艺设计中熔炼设备的比选(续)段军伟;刘楚明【摘要】原风眼浸入需要的熔体深度,有利于氧化还原风在铜液内的扩散,氧化、还原充分;氧化还原介质的总流量及每个风眼的介质流量都是事先经过计算并精确控制的,避免象固定式反射炉的盲目性;炉底设有多套用于吹氮的透气砖,对熔体进行搅动和净化,使沉入熔池底部的大密度杂质上浮,提高精炼效率,避免扒渣死区集渣。
【期刊名称】《有色金属加工》【年(卷),期】2011(040)004【总页数】4页(P16-19)【作者】段军伟;刘楚明【作者单位】中南大学材料科学与工程学院,湖南长沙410083;洛阳有色金属加工设计研究院,河南洛阳471039;中南大学材料科学与工程学院,湖南长沙410083【正文语种】中文原风眼浸入需要的熔体深度,有利于氧化还原风在铜液内的扩散,氧化、还原充分;氧化还原介质的总流量及每个风眼的介质流量都是事先经过计算并精确控制的,避免象固定式反射炉的盲目性;炉底设有多套用于吹氮的透气砖,对熔体进行搅动和净化,使沉入熔池底部的大密度杂质上浮,提高精炼效率,避免扒渣死区集渣。
(7) 作业率高。
炉子寿命长,维修方便,提高了炉子作业率。
年工作日可达330天以上。
(8)炉体结构复杂,加工要求高,设备投资大。
3 熔炼炉组3.1 熔炼炉组概述固定式反射炉和倾动式熔炼炉都是反射炉的范畴,热效率偏低,周期式生产使产能受到一定限制。
为了进一步提高热效率和生产效率,于是出现了专门用于紫杂铜熔炼的熔炼炉组。
即采用竖炉与倾动式精炼炉配合生产,目的是将反射炉的“进料熔化”工作剥离出来,改由竖炉单独完成。
竖炉将铜料熔化成铜水后,经过保温流槽流入倾动式精炼炉。
倾动式精炼炉只需将铜水进一步氧化、还原精炼后,即可进行浇铸。
这一工艺的设计思路是:竖炉热效率高,熔化同等铜料较反射炉节省燃料,不需要余热回收设施;竖炉采用机械化进料方式,效率高,进料时间短。
该工艺虽然增加了竖炉设备,使生产流程变长,但在总体成本上具有优势。
利用紫杂铜生产低氧铜杆的工艺与设备

铜是电线电缆制造业的基本原料,然而世界上铜 资源十分有限, 发达国家制定了废铜标准 FRHC[2]。 近年来,我国沿海地区的许多铜加工企业,在使用废
收 稿 日 期 :2019-12-06 作者简介:吴茂林(1980—),男,工程师,主要从事有色金属加工工程设计工作 。
·32·
有色冶金设计与研究
第的废铜比例猛增。 目 前我国废铜的直接利用率已达 50%以上。同时,我国 也是铜资源缺乏的国家,每年需要从国外进口大量 的铜。目前,无论是国外还是国内,直接利用 100%紫 杂铜连铸连轧生产符合相关国家标准的低氧铜杆已 较为普遍。其中,紫杂铜直接应用最好的是将 2 号以 上紫杂铜经严格挑选,直接投入反射炉进行精炼,经 氧化、还原后使用连铸连轧设备生产低氧铜杆。
铜 杆 一 般 是 指 直 径 为 Φ8~25 mm 的 实 心 圆 铜 杆,含铜量不 低于 99.9%,是电线 电缆生产的 坯 料 。 铜杆经过拉丝工序后,生产出各种规格大小的铜线 芯,再根据客户的需求进行束绞及涂覆,生产出各类 电线电缆产品。 近些年来,我国利用紫杂铜再生的铜 杆,产量巨大,主要还是用于生产规格较大的铜线, 如建筑电缆等。 而在质量要求严格、规格较小的电磁 线生产方面,则较少涉足。 与阴极铜连铸连轧法或上 引法铜杆比较,虽然紫杂铜直接再生的铜杆杂质含 量较高,但其性能指标仍可满足 GB/T 3952—2016 的 相 关 要 求[1]。
年产4万吨低氧铜杆废铜连铸连轧生产线(拉法格倾动炉)

年产4万吨低氧铜杆废铜连铸连轧生产线(选用拉法格倾动炉)初步可行性研究分析上海浦东力生电工机械有限公司2013年6月25日目录一.总论二.厂址三.建设方案四.环境保护、职业安全与卫生五.节能与能耗六.消防七.人员培训八.原料供应九.投资估算十.经济评估及投资回收期十一. 初步可行性研究分析的结论和建议1.总论1.1 项目名称年产4万吨低氧铜杆废铜连铸连轧生产线项目。
(选用拉法格倾动炉)1.2 低氧铜杆的基本情况按照我国现行标准GB/T3952-2008规定,用于导体的铜杆分为两大类:低氧铜杆和无氧铜杆(合金铜杆除外)。
用电解铜生产的无氧铜杆牌号为TU1、TU2,低氧铜杆牌号为T1、T2;用废铜生产的无氧铜杆和低氧铜杆的牌号统称为T3。
所有牌号的铜杆的电性能、机械性能、化学成份等各项指标均可在标准中查得。
1.3 立项背景(1)我国改革开放三十多年来,国民经济高速发展,随着城乡人民生活水平的不断提高,促使我国电力工业的飞速发展。
我国已成为世界第一用铜大国,2007年国内导体用铜从2000年的172万吨增至378万吨,2008年达到了412万吨。
这几年都在快速增长,预计到2015年将达到705万吨。
(2)我国的铜资源非常贫乏,每年用铜量的大部分靠国外进口,世界的铜资源也很有限,所以每年大量进口废铜。
同时我国正成为世界最大的废铜产生国,拆拣废铜、再生利用,符合循环经济可持续发展的规律,是科学发展观的体现。
(3)长期以来,我国没有先进的装备和工艺用于废铜作为原料生产低氧铜杆,只是利用反射炉进行冶炼。
反射炉炼铜污染不易治理、能耗高、产品质量差,所以早在1997年3月国家发出通知,淘汰反射炉炼铜。
去年,由上海电缆研究所黄院士牵头,申报用西班牙拉法格炉子炼铜连铸连轧生产低氧铜杆的项目获得国家有关部门批准,研发工作正在进行中。
(4)西班牙拉法格的FRHC废杂铜精炼技术,使低氧铜杆的品质大为提高,含铜量大于99.93%,导电率大于100.4%IACS,最高可到100.9%IACS。
低氧铜杆和无氧铜杆性能的区别
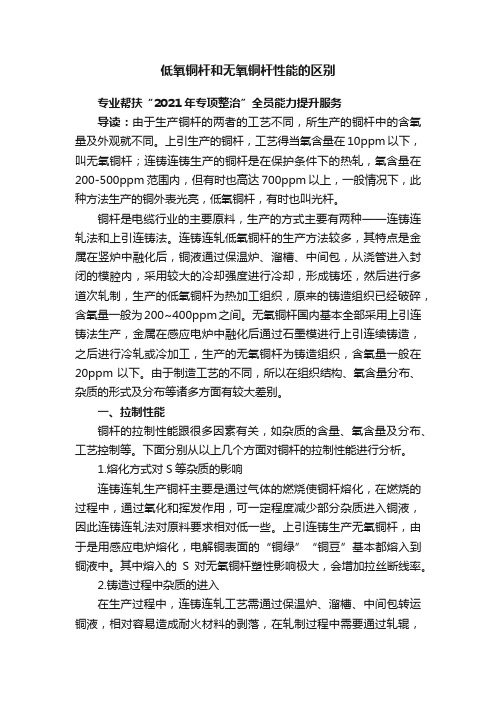
低氧铜杆和无氧铜杆性能的区别专业帮扶“2021年专项整治”全员能力提升服务导读:由于生产铜杆的两者的工艺不同,所生产的铜杆中的含氧量及外观就不同。
上引生产的铜杆,工艺得当氧含量在10ppm以下,叫无氧铜杆;连铸连铸生产的铜杆是在保护条件下的热轧,氧含量在200-500ppm范围内,但有时也高达700ppm以上,一般情况下,此种方法生产的铜外表光亮,低氧铜杆,有时也叫光杆。
铜杆是电缆行业的主要原料,生产的方式主要有两种——连铸连轧法和上引连铸法。
连铸连轧低氧铜杆的生产方法较多,其特点是金属在竖炉中融化后,铜液通过保温炉、溜槽、中间包,从浇管进入封闭的模腔内,采用较大的冷却强度进行冷却,形成铸坯,然后进行多道次轧制,生产的低氧铜杆为热加工组织,原来的铸造组织已经破碎,含氧量一般为200~400ppm之间。
无氧铜杆国内基本全部采用上引连铸法生产,金属在感应电炉中融化后通过石墨模进行上引连续铸造,之后进行冷轧或冷加工,生产的无氧铜杆为铸造组织,含氧量一般在20ppm以下。
由于制造工艺的不同,所以在组织结构、氧含量分布、杂质的形式及分布等诸多方面有较大差别。
一、拉制性能铜杆的拉制性能跟很多因素有关,如杂质的含量、氧含量及分布、工艺控制等。
下面分别从以上几个方面对铜杆的拉制性能进行分析。
1.熔化方式对S等杂质的影响连铸连轧生产铜杆主要是通过气体的燃烧使铜杆熔化,在燃烧的过程中,通过氧化和挥发作用,可一定程度减少部分杂质进入铜液,因此连铸连轧法对原料要求相对低一些。
上引连铸生产无氧铜杆,由于是用感应电炉熔化,电解铜表面的“铜绿”“铜豆”基本都熔入到铜液中。
其中熔入的S对无氧铜杆塑性影响极大,会增加拉丝断线率。
2.铸造过程中杂质的进入在生产过程中,连铸连轧工艺需通过保温炉、溜槽、中间包转运铜液,相对容易造成耐火材料的剥落,在轧制过程中需要通过轧辊,造成铁质的脱落,会给铜杆造成外部夹杂。
而热轧中皮上和皮下氧化物的轧入,会给低氧杆的拉丝造成不利的影响。
紫杂铜连铸连轧生产光亮铜杆工艺设计中熔炼设备的比选(续)

() 1装料 设 备 机 械 化 自动 化 程பைடு நூலகம்度 高 。特 殊 竖 炉 采 用 升 降小车 进行 装炉 , 加料 过 程 是半 自动控 制 。加料 方便 , 快捷 , 效率 高 , 动强 度低 。每次 加料 量 可 以达 劳
到 4, t每小 时最 多可 完成 1 加料 ; 5次
第4 0卷
第 4期
有 色 金 属 加 工
NONF ERRO US ME TAL S PROCESSl NG
Vo14 No. .0 4
2 1 年 8月 01
Au u t 01 g s 2 1
紫 杂 铜 连铸 连 轧 生产 光 亮铜 杆 工 艺设 计 中熔 炼 设备 的 比选 ( ) 续
3所 示 。
及 每 个风 眼 的 介 质 流 量 都 是 事 先 经 过 计 算 并 精 确 控
制 的, 避免 象 固定 式 反 射 炉 的 盲 目性 ; 底 设 有 多 套 炉 用 于 吹氮 的透 气 砖 , 熔 体 进 行 搅 动 和 净 化 , 沉 人 对 使
熔 池 底部 的 大 密 度 杂 质 上 浮 , 高 精 炼 效 率 , 免 扒 提 避
炉构 成 , 主要设 备 组成 如下 : ( 竖 炉装 料设 备 1 )
收稿 日期 :0 0—1 2 21 2— 9
第 4期
有 色 金 属 加 工
1 7
竖炉 装 料设 备 是半 自动运 行 的 , 以将 紫杂 铜 从 可
质 量 、 高成 品 率 、 低 能 耗 考 虑 很 有 必 要 。为 了满 提 降 足 光亮铜 杆 连铸连 轧 生产 工 艺连 续 进 料 , 连续 出铜 液 的技 术要 求 , 高 入 炉 原 料 紫 杂 铜 的 品味 , 提 以缩 短倾 动式 精练 炉 内的精炼 时 间 , 要 在熔 炼 炉组 和连 续铸 需
低氧铜杆及其生产工艺研究

低氧铜杆及其生产工艺研究摘要:随着我国国民经济快速发展,人们生活质量不断提高,客户对汽车用电线、电脑用连接线、漆包线和电磁线需求量越来越大,对铜杆的综合性能要求越来越高。
本产品研究采用国际上先进的竖炉连铸连轧生产工艺,熔化炉采用先进的激光料位测量技术,确保料面稳定,连铸采用轮式铸机,保障铸坯质量,钢带清刷采取在线清洗,延长钢带使用时间,乳化液浓度和空气-燃气比例均采用自动化控制技术,确保低氧铜杆产品质量。
关键词:低氧;铜杆;生产工艺导言我国工业快速超常规发展,促进了电线电缆行业的迅速发展,从而带动了电线电缆企业对铜杆的需求,铜杆再拉后可用于汽车线、电脑连接线、漆包线、电磁线等产品。
本产品采用国际上先进的竖炉连铸连轧生产工艺,包括熔化、保温、连铸、收卷等生产工序,研究过程中采用了激光料位测量技术,乳化液浓度自动控制等国内先进技术,保障了低氧铜杆产品性能和表面质量,满足了市场需要。
1 国内低氧铜杆生产现状目前,国内低氧铜杆生产方法主要有3种,分别是美国SCR法、德国Contirod法、意大利Properzi法,三种方法均采用竖炉连铸连轧生产低氧铜杆,其特点是技术先进、产品质量好、生产能力大,生产成本低,表面光滑,适合于大批量生产。
但国内也有部分企业采用废杂铜连铸连轧法生产低档低氧铜杆。
尽管国内生产企业都在努力提高低氧铜杆产品质量,但是,铜杆含氧量、表面质量还不能满足高端客户要求,尤其是铜杆再拉断线问题比较突出。
2 本产品主要技术指标查阅了GB/T 3952-2016《电工用铜线坯》标准,结合市场要求,确定了本产品研究技术指标,详细内容见表1 和表2。
表1 T1铜线坯杂质化学成分表2 T1铜线坯伸长率、体积电阻率及含氧量3 产品研究技术方案3.1 产品牌号、状态、规格的确定产品牌号确定为低氧铜杆T1;产品状态为热轧(M20);直径为8.0毫米。
3.2 产品工艺路线的确定本次研究的产品是低氧铜杆产品,属于国内同类产品中的高端产品,生产难度大、技术含量高,需要采用先进的生产工艺和先进的生产设备。
浅谈低氧铜杆和无氧铜杆的性能及应用

生产无氧铜杆的原料— 阴极铜 ( 电解铜板) 的
含氧量一般在( -0x00.由相图可知, 1 5)1'o 0 I 在常温下
氧在铜中的固溶度约为2 1' x %.低氧铜杆的含氧量 0
( 含氧量大幅度变化断线— 无氧铜杆一旦生产, 2 ) 含 氧量便可很容易地稳定在lx0%以下;) o1, ( 与轧制有 3
缆, 0 ()68 2 43 : . 0
参考 文献
拉制直径小于 0 m 的铜线, . m 5 则无氧铜82 ) 收稿 期: 50-3 0
T l aot Pr r ne A la o ad p ctn a bu te f mac n p i i k h eo o L w oye ad n o gn pr ye C p e R d f -xgn N -x o n o o o
式, 通常情况在混合模式下工作. 混合模式则是以时间
为主,压差为辅的控制方式.当运行压差小于设定值
[ 张晓超, 斌, 大型脉冲袋式除尘器的自 4 ] 冯 等. 动控制. 工业安全与 防尘. 9( ). 1 . 1 9 17 9 [ 赵江翔, 5 1 俞非0. 大型脉冲布袋除尘器的 设计环境工程.9.(: 1 1 3) 95 5 1
(bt c) h l -xg cpe r m d b cnnos tg rlg nno gn pr m d b A s at r Te oye opr ae otuu csn ad i ad -x e c e r ae o w n o d y i ai n o n n o y o o l p d y upr lg tuu csn a wdl ue i c l i ut m sc ar d h ppr o t t e ci pe pl cn os tg i y d a e s d e i o d a. i ae e bre h l tc ui o i n n a i r e s n n r o t r o T s e b d y l a s e r a e prrac, y n sd t ad wbi bt e l -xg ad -xgn pr ad idfec, eo ne xg eie s e d aiy w n o e n nn oye cpe r n t r e ne fm o e x t t n r l e e o y n o a a t w o o d h i r e f w i cn set b ue f ot u eoo y et h h b e c d s s pm m nm bnf c a e e y r o i l r c e i . [ e w rs o-xgn pr K y d) w oye cper o L o o d Nnoye cper ciprrac o-xgn pr o o d E tc fm ne Daaiy l r eo e wbi r l t
一种高纯铜及低氧光亮铜杆的生产方法[发明专利]
![一种高纯铜及低氧光亮铜杆的生产方法[发明专利]](https://img.taocdn.com/s3/m/a7be6c2cfd4ffe4733687e21af45b307e971f958.png)
[19]中华人民共和国国家知识产权局[12]发明专利申请公布说明书[11]公开号CN 101275186A [43]公开日2008年10月1日[21]申请号200810023701.1[22]申请日2008.04.16[21]申请号200810023701.1[71]申请人倪如宝地址215234江苏省吴江市七都镇吴江万宝铜带有限公司内[72]发明人倪如宝 姬高生 [74]专利代理机构苏州创元专利商标事务所有限公司代理人孙仿卫[51]Int.CI.C22B 15/14 (2006.01)B23P 17/00 (2006.01)B22D 21/00 (2006.01)权利要求书 1 页 说明书 5 页[54]发明名称一种高纯铜及低氧光亮铜杆的生产方法[57]摘要本发明涉及一种高纯铜及低氧光亮铜杆的生产方法,将废杂铜经过熔炼扒渣、插木还原和冷却结晶得到高纯铜,熔炼扒渣时,将铜加热1080~1120摄氏度得到铜液,其中的不熔的高熔点杂质经扒渣除掉,之后,向铜液中加入石英砂和二氧化硅,并吹入过量氧气,使其中比铜活泼的金属转化成浮渣除去,再向铜液加压吹氧使沉在炉底的亚氧化铅充分与石英砂反应生成浮渣以将铅除净,保证铜纯度大于99.5%和含铅量小于2ppm;低氧光亮铜杆的生产方法主要是以紫杂铜为原料,依次经过熔炼扒渣、插木还原的高纯铜液直接进入连铸连轧设备进行浇铸,低氧光亮铜杆的成品率大于98%,达到欧盟ROHS指令要求和绿色环保标准,该生产方法生产成本低。
200810023701.1权 利 要 求 书第1/1页 1、一种高纯铜的生产方法,以铜的质量含量大于90%的废杂铜为原料,依次经过熔炼扒渣、插木还原和冷却结晶得到所述的高纯铜,其特征在于:所述的熔炼扒渣具体包括以下步骤:①、将所述的废杂铜加热到1080~1120摄氏度使铜熔化得到铜液,将混在所述铜液中的不熔的杂质通过扒渣除去;②、将经步骤①处理后的所述铜液升温至1150~1200摄氏度,加入石英砂,石英砂的加入量以将所述铜液的表面全部覆盖住为准,再向该铜液中吹入过量氧气,产生浮在铜液表面的浮渣和沉在炉底部的氧化亚铅,其中的浮渣通过扒渣除去;③、向经步骤②处理后的所述铜液中吹入压力为0.5~1.0MPa的氧气,使所述的氧化亚铅在铜液内翻腾并与石英砂反应,生成浮渣,该浮渣通过扒渣除去。
废杂铜生产铜杆工艺改善研究

废杂铜生产铜杆工艺改善研究张秉檐【摘要】针对废杂铜生产铜杆的传统工艺存在资源利用率低、产品生产流程长、成本高、热效率低、能耗高、环境污染严重的现状,以φ8 mm铜杆为研究对象,对生产工艺关键参数进行试验研究.研究结果表明:新确定的工艺参数方案能够达到铜杆延伸率不小于41%,抗拉强度大于170 N/mm2,电阻率不大于0.01724 Ω·mm2/m,工艺方案为废杂铜工业化批量生产质量稳定的铜杆奠定了基础.【期刊名称】《有色金属科学与工程》【年(卷),期】2011(002)004【总页数】4页(P12-15)【关键词】废杂铜;直接利用工艺;φ8 mm铜杆;抗拉强度【作者】张秉檐【作者单位】江钨新型合金材料有限公司,江西赣州341000【正文语种】中文【中图分类】TG146.1废杂铜再生利用是循环经济的重要组成部分[1].从废杂铜到铜线杆传统的方法要经过3个步骤[2]:第1步是废杂铜的火法精炼,冶炼之后铸成阳极板,进入第2步电解,电解过后产出的阴极铜再进入最后一步,将阴极铜重熔制杆,这种传统工艺存在工艺流程长、能耗高、效率低等缺点[3].江钨新型合金材料公司成立于2008年,一期工程总投资额约9亿元人民币,是国内首家采用再生铜直接利用工艺技术生产火法精炼高导电低氧光亮铜杆(Cu-FRHC)的企业.公司设计年生产规模为高导电铜杆及铜线40万t,分二期建设:其中一期工程利用废紫杂铜年加工12万t铜杆产品及3万t铜线产品;二期工程利用废紫杂铜年加工18万t铜杆产品及7万t线材及管材等深加工产品.采用的工艺是废铜的连续冶炼,从而得到可控杂质含量的液态铜,经过连铸连轧生产出铜杆.生产方式采用熔炼→连铸→连轧→铜线杆,一体化连续生产工艺,较传统工艺节能.与国内目前铜冶炼工艺相比,公司生产具有资源利用率高、产品生产流程短、成本低、热效率高、能耗低、环境污染少的特点.故加大对该类产品的研发对提高企业的市场竞争力及经济效益具有重要意义.废杂铜是废品和废料的统称,其来自3个方面:一是有色金属冶炼过程中产生的废品和废料;二是各种机械加工过程中产生的废品和废料;三是使用过程中旧的、报废的仪器、仪表、工具和机器设备等[4].国内废杂铜尚没有制定较为完善的分类标准,基本上参照国外的标准,大致把废杂铜分为三类:1#废杂铜:纯度在95%-99%以上,主要是由干净的非合金铜材料所组成,即:铜边角料,铜圈、干净铜管或管道、1#铜线和粗导线(不包括被烧焦的和易碎的细铜线),此类废料可直接送加工厂使用.2#废杂铜:含铜在85%以上,包括干净的、氧化的、带皮的铜边角料、铜圈、整流器部件、较干净的带少量焊锡的铜管材,氧化或带皮铜线(不是被烧焦的铜线). 3#废杂铜:除含有上述1#、2#废杂铜的成分外,还含有大量的含铜铸件,废轴承、废旧马达、各种电器设备、废旧变压器等.3#废杂铜含铜量变化范围很大,最低含铜量达20%,最高达到70%-80%.为了保证熔炼废铜液的质量,对所有的废杂铜进行了选择,并按照来源特征进行预处理.例如对光亮废电线电缆、铜米的技术要求:(1)必须光亮,不能有氧化物、塑胶、铁、锡、铝等其它杂质.(2)光亮废电线电缆必须打包压成块.本试验材料等级采用的废铜品位是在92%左右.在此基础上后面试验的方向将利用品位更低的废杂铜原料直接制杆来逐步探索更佳的工艺条件.铜杆组织的好坏直接影响成品性能[5],为研究成杆工艺对铜杆结晶组织的影响,试验时,采用了两组不同的成杆工艺参数,将得到的试验结果进行对比,探索出合适的成杆工艺参数和最优操作流程.具体参数见表1.不同成杆工艺下的铜杆组织,见图1.从图1可以看出,在成杆过程采用紫铜内套结晶器,于 0.22~0.25 MPa水压、110~140 mm/min 铸造速度条件下得到的第1炉铜杆,其结晶组织更细小致密,显著改善了铸锭的质量,而采用紫铜加石墨内套结晶器,较低水压,铸造速度较慢的第2炉铜杆,相比之下其晶粒组织明显粗大.不同成杆工艺条件下铜杆的性能检测结果见表2所示.从表2可以发现,随着加工率的增大,铜杆的抗拉强度逐步提高,延伸率则有一定程度的下降,其成品见图2.本试验生产的Φ 8mm低氧光亮铜杆铜含量≥99.95%,氧含量≤200×10-6,电阻率≤0.017241Ω·mm2/m,导电率≥100%IACS,抗拉强度>345 N/mm2,延伸率>35%,并通过了具有国际信用等级的SGS检测.检测报告指出:江钨新型合金材料公司采用废紫杂铜直接制杆生产的Φ 8 mm低氧光亮铜杆中未检测出镉、铅、汞、六价铬等有害元素,达到了国际环保标准.铜杆中有害物质镉、铅、汞和六价铬的含量小于欧盟ROHS指令限量值2×10-6,各项质量指标均超过国家T2标准水平,并达到国际先进水平.金属在结晶过程中,其组织晶粒的大小和表面质量与结晶器的选择、水压大小和浇注速度的大小均有一定的关系[6].由于紫铜的导热系数大于石墨的,在铸造过程中,相同冷却水压的条件下,采用紫铜内套结晶器,金属的结晶潜热大,单位时间形核率高,有利于金属的凝固成型及晶粒细化;循环水的二次冷却作用是为保证热量主要沿轴向导出,促进轴向凝固,使液穴浅平,故当其他条件一样,水压高,二次冷却强度越大,液穴越浅平,铸锭组织越致密.晶粒大小除了受结晶器、水压影响之外,还要与铸造速度有关.当浇铸速度慢时,熔体在结晶器内凝固成型及停留的时间较长,在凝固壳下降的过程中,弯液面熔体的表面张力阻碍了液体向结晶器的继续填充,使液体有一定的被冷凝时间,熔体和结晶器间就会形成一定的空隙并逐渐增大,同时铜液对弯液面产生的静压力也在逐渐增大,一旦表面张力被克服,熔体就会再次填充到结晶器,受激冷易形成冷隔缺陷.提高铸造速度,可缩短熔体在结晶器内的停留时间,相对降低了弯液面熔体的表面张力,可有效地降低甚至消除冷隔的形成,从而有效地改善铸锭的表面质量. (1)废杂铜生产铜杆的方式采用熔炼→连铸→连轧→铜线杆一体化连续生产工艺.试验表明较传统工艺节能.与国内目前铜冶炼工艺相比,该生产工艺具有资源利用率高、产品生产流程短、成本低、热效率高、能耗低、环境污染少的特点.(2)在半连续铸造过程中,采用紫铜内套结晶器,冷却水压为0.22~0.25 MPa,铸造速度为110~140 mm/min的条件下,可以成功拉铸出表面质量、化学成分都达到国家标准要求的铜杆.(3)试样经内部和外部严格检验结果表明,铜杆的电阻率、含氧量、尺寸公差、表面质量、机械性能等各项性能指标均达到了国家标准的技术要求,且其生产成本较低,工作效率高,为工业化批量生产奠定了条件.下一步研究方向重点是如何利用品位更低的废杂铜原料直接制杆[7],从而最大限度的利用再生资源,尝试在其中加入新的成分[8],使产品性能更好,生产成本更低,使资源利用更加平衡.【相关文献】[1]Sung K,Kang S.Purushothaman Development of Conducting Adhesive Materials for Microelectronic Applications[J].Electronic Materials,1999,28(11):1314-1316.[2]F M Coughlan,H J Lewis.A Study of Electrically Conductive Adhesives as a Manufacturing Solder Alternative[J].Journal of Electronic Materials,2006,35(5):912-913.[3]王冲,朱学云,熊振坤.我国废杂铜的再生利用现状及展望[J].中国资源综合利用,2009,(7):16-20.[4]张天姣,陈晓东,唐维学,等.废杂铜的回收与利用[J].广东化工,2009,(6):7-11.[5]陈存中.有色金属熔炼与铸锭[M].北京:冶金工业出版社,2006:102-119.[6]余永宁.金属学原理[M].北京:冶金工业出版社,2005:250-270.[7]赵新生,卢宏.废杂铜火法精炼直接生产光亮铜杆的工艺和设备(续)[J].资源再生,2008,(11):17-22.[8]瑞林.FRHC废杂铜精炼工艺技术的发展[J].资源再生,2009,(9):21-25.。
新型低氧铜杆的生产工艺

新型低氧铜杆的生产工艺
一、用料及工艺特点
所用料是CU-2种铜杆,纯度99.9%,长度6米,直径10mm。
工艺特
点是:
1、优先采用磷含量低的原料,确保铜杆高纯度,使其它所有元素的
含量小于0.001%;
2、采用抛光和拉磨工序,确保表面光滑,无毛刺,延长使用寿命;
3、采用低温轧制工艺,确保铜杆结构紧凑,具有良好的机械性能;
4、采用热处理工艺,将铜杆的含氧量降低到一定的水平,提高铜杆
的抗腐蚀性,使其保持稳定性能。
二、生产工艺流程
1、原料准备:采用金属铜,先进行检测,确认其金属杂质含量不高
于0.001%,切割成10mm的长度6米的铜杆。
2、抛光:采用银磨石抛光机将铜杆的表面抛光,使其光滑,无毛刺,延长使用寿命。
3、低温轧制:将铜杆置于低温轧机中,进行再次的深度轧制,确保
铜杆结构紧凑,具有良好的机械性能。
4、热处理:将铜杆放于热处理设备中,采用低温工艺进行热处理,
将其含氧量降低到一定的水平,提高铜杆的抗腐蚀性,使其保持长期稳定
性能。
三、验收要求
本工艺验收要求:
1、铜杆的纯度:确保不高于0.001%;
2、界面处理:表面光滑,无毛刺,有良好的机械性能;。
连铸连轧生产铜线杆技术述评
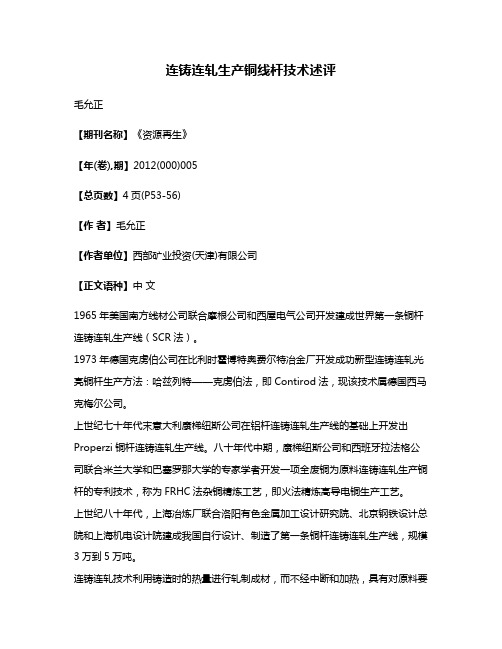
连铸连轧生产铜线杆技术述评毛允正【期刊名称】《资源再生》【年(卷),期】2012(000)005【总页数】4页(P53-56)【作者】毛允正【作者单位】西部矿业投资(天津)有限公司【正文语种】中文1965年美国南方线材公司联合摩根公司和西屋电气公司开发建成世界第一条铜杆连铸连轧生产线(SCR法)。
1973年德国克虏伯公司在比利时霍博特奥费尔特冶金厂开发成功新型连铸连轧光亮铜杆生产方法:哈兹列特——克虏伯法,即Contirod法,现该技术属德国西马克梅尔公司。
上世纪七十年代末意大利康梯纽斯公司在铝杆连铸连轧生产线的基础上开发出Properzi铜杆连铸连轧生产线。
八十年代中期,康梯纽斯公司和西班牙拉法格公司联合米兰大学和巴塞罗那大学的专家学者开发一项全废铜为原料连铸连轧生产铜杆的专利技术,称为FRHC法杂铜精炼工艺,即火法精炼高导电铜生产工艺。
上世纪八十年代,上海冶炼厂联合洛阳有色金属加工设计研究院、北京钢铁设计总院和上海机电设计院建成我国自行设计、制造了第一条铜杆连铸连轧生产线,规模3万到5万吨。
连铸连轧技术利用铸造时的热量进行轧制成材,而不经中断和加热,具有对原料要求低、产量大、生产效率高、能耗成本低、质量稳定、性能均匀、表面光亮等特点,给铜工业发展带来一次伟大变革。
目前世界上90%以上的铜线杆都用连铸连轧技术生产。
用阴极铜为原料的连铸连轧生产铜杆一般分为四个步骤:熔化——铸坯——轧制——绕杆,目前建成单条生产线最大产能已达到48吨/小时,年产可达到35万吨。
SCR法、CONTIROD法、PROPERZI法在设备的总体流程配置上均相似,仅具体到某个设备上有些不同而已。
连铸连轧设备主要有熔炼炉、铸造机、轧机。
三种连铸连轧法最大的区别在铸机上,三种不同的铸机如图1所示。
1. SCR法SCR法是由美国南方线材公司、摩根公司和西屋电气公司共同研制开发的。
主要的工艺设备为:熔化采用美国精炼公司的竖炉,铸造采用五轮钢带式连铸机连铸,轧制配备了摩根二辊悬臂式连轧机组。
无氧铜杆生产工艺流程
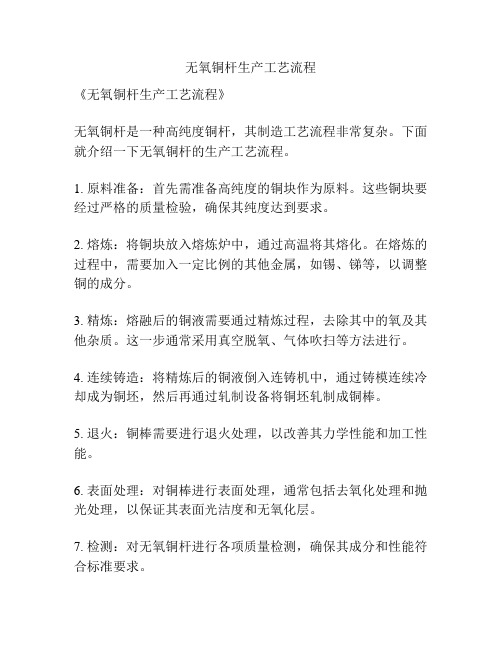
无氧铜杆生产工艺流程
《无氧铜杆生产工艺流程》
无氧铜杆是一种高纯度铜杆,其制造工艺流程非常复杂。
下面就介绍一下无氧铜杆的生产工艺流程。
1. 原料准备:首先需准备高纯度的铜块作为原料。
这些铜块要经过严格的质量检验,确保其纯度达到要求。
2. 熔炼:将铜块放入熔炼炉中,通过高温将其熔化。
在熔炼的过程中,需要加入一定比例的其他金属,如锡、锑等,以调整铜的成分。
3. 精炼:熔融后的铜液需要通过精炼过程,去除其中的氧及其他杂质。
这一步通常采用真空脱氧、气体吹扫等方法进行。
4. 连续铸造:将精炼后的铜液倒入连铸机中,通过铸模连续冷却成为铜坯,然后再通过轧制设备将铜坯轧制成铜棒。
5. 退火:铜棒需要进行退火处理,以改善其力学性能和加工性能。
6. 表面处理:对铜棒进行表面处理,通常包括去氧化处理和抛光处理,以保证其表面光洁度和无氧化层。
7. 检测:对无氧铜杆进行各项质量检测,确保其成分和性能符合标准要求。
以上就是无氧铜杆生产工艺的主要流程,整个生产过程需要严格控制各个环节,确保最终产品的质量达到要求。
无氧铜杆广泛应用于电气、化工、医疗等领域,其制造工艺的完善对产品质量和市场竞争力具有重要意义。
紫杂铜再生精炼产业的低碳化绿色化思路

Absr c :To vg r usy d v l p r c ca l c a e o p rr fn n sa fe tv y t uik y a hiv r e , ta t io o l e eo e y l b e s r p r d c p e e i g i n ef ci e wa o q c l c e e a g e n i
0 前 言
铜产业 是 资源型产业 , 国民经济 的重要 组成 部 是
分 . 革 开 放 以来 , 国 铜 产 业 通 过 不 断 深 化 改 革 , 改 中 调
年 5月发 布 的《 色 金属 产业 调 整 和振 兴规划 》 发 有 把 展循环 经济 , 好再生 利用列 为有 色金属产 业调 整和 搞
精炼 成 为火 精 铜 . 大多 数 火精 铜 用 于浇 铸 阳极 板 , 再
式 导致产 业结 构失衡 . 当前 中 国铜 产业 亟需 解 决 国内
经 过 电解 精 炼 生产 阴极 铜.部 分 纯 度较 高 的火 精 铜
直 接用 于 连铸 连轧 铜线 坯 ( 又称 铜 杆 、 铜盘 条 ) 或用 , 于浇 铸其 它 紫 铜坯 .由于 紫杂 铜 再 生精 炼 产业 具有
紫杂铜再 生精炼产业 的低碳化绿色化思路
张 选 志
( 州江 钨 新 型 合金 材 料 有 限公 司 , 西 赣 州 3 1 0 ) 赣 江 4 0 0
摘 要: 大力发展 紫 杂铜 再 生精 炼产 业是 加速 实现低碳 绿 色铜 产业 的有效途 径. 针对 当前 国 内紫杂铜
再 生精 炼产业 工艺设备 能源利 用率低 、 冶炼耗 时长及产 业集 中度低 的主要 问题 , 出技术创 新和行 业 提
i d sr s c a e r y— si g n l w — f ce c e u p n , tme—c n u n s li g nd o n u ty u h s ne g wa tn a d o e i n y q i me t i i o s mi g metn a lw idu til n sra c n e ta in t s a e ams o ut o wa d o ie s f t c n lg i n v to a d n u t r g l to fr o c n r to , hi p p r i t p f r r s me d a o e h oo y n o a i n n i d sr e u a in o y
国产火法精炼铜杆生产线的创新

国产火法精炼铜杆生产线的创新苏华光【期刊名称】《《电线电缆》》【年(卷),期】2019(000)006【总页数】5页(P40-44)【关键词】铜杆精炼工艺; 原料选择; 燃烧系统与还原技术; 环保措施【作者】苏华光【作者单位】上海电缆研究所有限公司上海200093【正文语种】中文【中图分类】TM2410 引言电工铜杆,作为线缆行业一种主要的导体材料,国内年用量达到了550 万t。
根据生产工艺可分为连铸连轧铜杆和上引法铜杆,按所用原材料又可分为电解铜杆和火法精炼铜杆。
随着连铸连轧铜杆质量的提高,连轧铜杆已成为主导产品,而火法精炼连轧铜杆也占了总产量的三分之一。
由于上世纪80年代引进的电解铜连铸连轧生产线,不能加入废线(再生铜),所有的废铜线都是在反射炉内火法精炼,用行列式轧机轧成黑铜杆。
上世纪90 年代末,电工设备厂家把反射炉火法精炼与国产连铸连轧线组合起来,生产出光亮铜杆,替代了黑铜杆的生产,形成了国内最早的火法精炼连轧铜杆生产线。
2000年后,国外火法精炼铜杆工艺和生产线已十分成熟,开发了微合金化技术,即西班牙拉法格技术[1]。
国内也于2006 年开始引进,我们借鉴了引进线的先进工艺和环保理念,对国产线做了改进。
下面重点介绍国产线在精炼工艺、原材料品位选择、燃烧系统、还原技术、环保措施等方面的创新。
1 精炼工艺精炼工艺是火法精炼铜杆的关键技术,对产品的晶粒结构、电气机械性能、可拉性等方面起主导作用。
所谓精炼就是采用氧化还原来控制杂质总量和各杂质的分布比例,使杂质在晶体中呈弥散分布。
其主要的工艺原理是:铜中杂质含量低时,氧含量也要低,反之,氧含量要高,氧与杂质形成一种平衡。
氧的存在能改变杂质在铜中的分布形态,铜中没有氧或氧太少时,杂质可能呈晶界网状分布,导致后续加工开裂;反之,铜中有氧时,杂质形成氧化物颗粒,呈弥散分布,后续加工就不会开裂,这就是氧与杂质的平衡。
但在传统工艺中,当铜的杂质含量偏低,要求氧含量控制在200 ppm 以下时,就不能用传统的还原方法。
铜杆知识

铜杆知识1)关于氧的吸入和脱去以及它的存在状态生产铜杆的阴极铜的含氧量一般在10—50ppm,在常温下氧在铜中的固溶度约2ppm。
低氧铜杆的含氧量一般在200(175)—400(450)ppm,因此氧的进入是在铜的液态下吸入的,而上引法无氧铜杆则相反,氧在液态铜下保持相当时间后,被还原而脱去,通常这种杆的含氧量都在10—50ppm以下,最低可达1-2ppm,从组织上看,低氧铜中的氧,以氧化铜状态,存在于晶粒边界附近,这对低氧铜杆而言可以说是常见的但对无氧铜杆则很少见。
氧化铜以夹杂形式在晶界出现对材料的韧性产生负面影响。
而无氧铜中的氧很低,所以这种铜的组织是均匀的单相组织对韧性有利。
在无氧铜杆中的多孔性是不常见的,而在低氧铜杆中则是常见的一种缺陷。
2)热轧组织和铸造组织的区别低氧铜杆由于经过热轧,所以其组织属热加工组织,原来的铸造组织已经破碎,在8mm的杆时已有再结晶的形式出现,而无氧铜杆属铸造组织,晶粒粗大,这是为什么,无氧铜的再结晶温度较高,需要较高退火温度的固有原因。
这是因为,再结晶发生在晶粒边界附近,无氧铜杆组织晶粒粗大,晶粒尺寸甚至能达几个毫米,因而晶粒边界少,即使通过拉制变形,但晶粒边界相对低氧铜杆还是较少,所以需要较高的退火功率。
对无氧铜成功的退火要求是:由杆经拉制,但尚未铸造组织的线时的第一次退火,其退火功率应比同样情况的低氧铜高10——15%。
经继续拉制,在以后阶段的退火功率应留有足够的余量和对低氧铜和无氧铜切实区别执行不同的退火工艺,以保证在制品和成品导线的柔软性。
3)夹杂,氧含量波动,表面氧化物和可能存在的热轧缺陷的差别无氧铜杆的可拉性在所有线径里与低氧铜杆相比都是优越的,除上述组织原因外,无氧铜杆夹杂少,含氧量稳定,无热轧可能产生的缺陷,杆表氧化物厚度可达≤15A。
在连铸连轧生产过程中如果工艺不稳定,对氧监控不严,含氧量不稳定将直接影响杆的性能。
如果杆的表面氧化物能在后工序的连续清洗中得以弥补外,但比较麻烦的是有相当多的氧化物存在于“皮下”,对拉线断线影响更直接,故而在拉制微细线,超微细线时,为了减少断线,有时要对铜杆采取不得已的办法——剥皮,甚至二次剥皮的原因所在,目的要除去皮下氧化物。
紫杂铜连铸连轧生产光亮铜杆工艺设计中熔炼设备的比选

A A
( 环境 污染严 重 。环 保 效 果差 的 主要 原 因 : 化 2 ) 氧 还原 期需 要 人 工 持 管 , 作 时炉 门 不 能 关 闭 , 量 的 操 大
烟气 从炉 门外 逸 , 成 严 重 的低 空 污 染 ; 造 由于 需 要 人
工持 管 , 一般 只能 采用 重 油 作 还原 剂 。 重 油在 还 原 期
司研 制 开发 的 , 门用 来 处 理废 杂 铜 、 铜 、 专 粗 电解残 极 等 固体铜 料 。 由 于倾 动 炉 综 合 了 固 定 式 反 射 炉 和 回
转 式 阳极 炉 的优 点 , 别 适 合 于处 理 固体 物 料 , 料 、 特 加
熔 池 区和气 流 区 , 墙 设 有 加 料 口和 排 渣 V , 墙 设 前 I后 有 出铜 1和 氧 化 还 原 插 管 , 墙 设 有 主烧 嘴 , 一 端 2 1 端 另
主要 特点 :
( ) 械化 自动化程 度 高 。炉 子 的倾 转 不需 要 复 1机
杂 的机械 传 动 , 由可 靠 的两 个 液 压 推 杆 来 实 现 , 妥 稳 可靠 。加 料使 用 灵 活 快 捷 的专 用 加 料 车 或 改 进 式 前 装机 来完 成 。氧 化还 原 风 眼 固定 在 炉 体上 , 不需 人 工
2 1 倾 动 式 熔 炼 炉 概 述 .
倾 动 式熔炼 炉 主要设 备组 成如 下 :
() 体 1 炉 炉体 由金属 构架 、 耐火 材 料组 成 。炉 膛 截 面形 状 类 似 固定式 反 射 炉 , 炉顶 、 墙 和 炉 底 组 成 并 分 为 由 炉
倾 动式 熔炼 炉是 2 0世 纪 6 0年代 由德 国 Mar 公 e z
- 1、下载文档前请自行甄别文档内容的完整性,平台不提供额外的编辑、内容补充、找答案等附加服务。
- 2、"仅部分预览"的文档,不可在线预览部分如存在完整性等问题,可反馈申请退款(可完整预览的文档不适用该条件!)。
- 3、如文档侵犯您的权益,请联系客服反馈,我们会尽快为您处理(人工客服工作时间:9:00-18:30)。
利用紫杂铜和国产连铸连轧设备生产低氧光亮铜杆 中国二手设备网2007-6-20 文字选择:大中小1.1 概述采用传统热轧法生产黑铜线杆工艺在世界上已有一百多年的历史,进入上个世纪七十年代,世界工业发达国家相继开发了SCR法、properzi法、Contirod法、Secor法、Dip法、Upcast法等光亮铜杆连铸连轧生产线从而使世界铜线杆的生产发生了重大变革。
所谓传统热轧法就是把电解铜加到阴极反射炉中加热熔化,做铜,铸成船形锭。
船形锭每根重80~90kg,然后再经加热炉加热,进入到横列式轧机中轧制,一般横列式轧机有十二或者十四座机架,才能轧成¢8~¢6mm的铜杆,由于此种铜杆表面氧化厉害,所以称黑杆,需经酸洗或者扒皮后再拉丝。
连铸连轧法与传统热轧法生产的铜线杆相比,具有长度长、节省能量,产品质量稳定、性能均一、表面光亮等特点。
目前,传统的热轧法已经被连铸连轧所取代。
比较连铸连轧与热轧法,其优缺点是很明显的:1)横列式轧机,由电解铜到线杆,消耗燃料油130kg/t,(相当于热能1300Mka/t)电力180kwh/t,合计消耗热能3023Mka/t;连铸连轧工艺只消耗806 Mka/t;两种工艺热能相差2217 Mka/t。
2)黑杆导电率比光亮杆低,因为黑杆含氧量高。
3)黑杆圈重小,一般只有80kg左右,而光亮杆一般在3~5 t,因此拉丝时接头少。
黑杆需要酸洗或扒皮,有三废污染,光亮铜线杆不需要酸洗或扒皮,,没有污染。
我国在上个世纪八十年代掀起了连铸连轧引进高潮,最早引进的是哈尔滨电缆厂,1982年签约,83年安装调试,84年投入生产,历时15月。
投资费用2400万人民币(其中外汇400万美元)。
该生产线为浸渍法(DFP),炉子是美国GE公司的,轧机是日本昭利公司,一年就收回全部投资。
自1984年以后,全国又引进了八条生产线和十几条上引法。
方法主要性能建造地点SCR法Contirod法Proerzi法云南冶炼厂上海钢材厂北京钢厂常州冶炼厂湘潭冶炼厂芜湖冶炼厂太原钢厂四川电缆厂铸轮直径(毫米) 1676 模腔长2280 1400铸机四轮双带二轮生产能力(吨/时) 6.5 13 8-10 7.0年生产能力(万吨/年) 3.0 6.5 4.5 3.5扎机型式三辊(平、立) 二辊(平、立)三辊(互成120℃)机架数(个) 9 10 9 10线杆直径(毫米) φ8 φ8 φ8-22 φ8引进国别和公司美国南方线材公司西德克虏伯公司意大利康梯纽斯公司投产时间(年) 1988 1990 1987 1987 1988 1987 1987 1986国内分布 2 3 3不管是哪种生产方法,他们都要求用1#电解铜作原料(如果是A级铜更好),在竖炉或电炉中熔化,然后铜液在一定温度下进入铸机,强制水冷结晶成坯进入连轧机组轧制成杆,杆经过乳化液冷却绕圈。
1981年10月上海市科委、上海市冶金局给上海冶炼厂下达了反射炉连铸连轧新工艺实验任务,历时8个月,取得了一定的经验数据,但不能代替引进的连铸连轧机组,他也为今天所讲的利用紫杂铜生产光亮铜杆打下了基础。
1.2、用紫杂铜生产光亮铜杆的工艺原理当时上海冶炼厂是用电解铜作原料,在10吨反射炉中熔化,做铜。
该反射炉炉床面积4.16m2,熔池3040×1500mm,熔池最大深度350mm。
每炉冶炼时间6小时,还原结束时炉内铜水温度1170℃~1190℃。
现在我们认为该炉设计太小,熔池太浅,铜液的氧含量不宜控制,前面引杆剪坯需要一、二吨,后面二、三吨铜液在炉子放不出,中间只剩四、五吨铜水很难正常生产。
当初该阳极炉如设计五十吨左右,也许能实验成功。
在火法精练过程中,要脱除的杂质可分五大类,第一类是在氧化过程中易除去的杂质,第二类是在氧化过程中一般能脱除的杂质,第三类为难于脱除的杂质,第四类是较少脱除的杂质,第五类是不能脱除的杂质。
在生产实践中主要杂质是Pb、Sn、Ni、Fe、O、S等。
应该说S、Zn属于第一类,Fe属于第二类,pb、Sn是第三类,Ni则是第四类,而O必须在还原中脱除。
实践证明,在氧化造渣过程中,杂质脱除率高达90%,但还有10%左右的锡会给生产带来麻烦。
从理论上讲,铜与锡在液态时互溶,精练炉中的锡主要来自锡青铜,镀锡铜废料。
在精炼过程中锡被氧化成亚锡和二氧化锡,前者呈碱性,后者呈酸性。
Sn+Cu2O=SnO+2Cu (1)SnO+Cu2O=SnO2+2Cu (2)SnO+SiO2=SnSiO3 (3)酸性SnO2在造酸性渣不易与反应,所以只能靠造碱性渣来除去:SnO2+Na2CO3=Na2SnO3+CO2 (4)或者SnO2+CaO=CaSnO3 (5)铅虽然容易造渣除去,PbO+SiO2=pbSiO3工艺原理图:油、蒸汽电解铜风↓反射炉熔炼↓ ↓ ↓返鼓风炉处理渣铜液炉气→ 烟囱放空↓浇包↓冷却水铜液↓水循环系统连续铸造↓回水铸坯↓牵引↓铸坯↓铣角→ 铜屑→ 回炉↓铸坯↓剪切↓铸坯堆放但是铅比重比铜大得多,一般熔化后,PbO就容易沉到炉底,所以在氧化时,不易被搅起,因此除铅时,要想法把沉在炉底的PbO(比重9.2)除去。
我们曾在停炉时对炉底没有放净的铜采样,发现铅高出标准数倍到数十倍。
针对这种情况,我们在每次加料前适当向炉底撒入一些石英砂,使沉在炉底的PbO熔化后能与SiO2形成pbSiO3漂浮到铜液表面被扒除。
而镍是和铜互熔的金属,很难将铜镍用火法精练方法分离,一般镍是在湿法冶炼时以NiSO4蒸发溶液时脱除,只有极少数NiO+SiO2=NiSiO3造渣脱除。
因为同样的道理,CuO+SiO2=CuSiO3,这就造成铜的损失。
镍在铜熔液中结晶,造成脆性,使铜杆的抗拉强度延伸率降低明显,且使铜坯断坯,铜杆产生麻烦,必须在铜料分拣时尽量清除干净。
锌是较易脱除的杂质,一般采用加焦碳吹风蒸锌,在这个过程中锌被除去90%,剩下熔入铜液的ZnO+SiO2=ZnSiO3扒渣除去。
铁基本上都是造渣除去,FeO+SiO2=FeSiO3Fe2O3+3SiO2=Fe2(SiO3)3硫则是氧化时生成SO2随烟气除去,S+O2=SO2脱除氧则在还原阶段完成,铜熔化后极易与氧反应,4Cn+O2=2Cu2O (7)2Cu2O+O2=4CnO (8)在还原阶段,还原木(或重油)与高温铜水接触后,立即裂解产生甲烷,氢气来夺取铜水中的氧:Cu2O+H2=2Cn+H2O3Cu2O+CH4= 6Cn+H2O+CO2既使用电解铜作原料,在反射炉中,由于电解铜自身含氧量高,也必须设法降低氧含量。
为了降低铜液中的氧含量,将电解铜熔化后直接进入还原阶段行不行呢?事实证明不行,生产黑杆时,电解铜在反射炉中还是要经过熔化氧化还原出铜这几个阶段,而且还得出了“氧化要完全,还原要彻底”的经验,这就是利用紫杂铜进行连铸连轧的基础。
对于不同等级的紫杂铜,采用不同的精练方法,这是紫杂铜料生产光亮铜杆的关键。
1.3、原料的选择和处理现在杂铜分级的标准已经制定,但工厂很难按标准分级来购买杂铜,只能大致分为特紫铜、1#杂铜、2#杂铜和等外杂铜。
由于铜的价格高,在市场经济利益驱动下,许多不法商人不是严格分拣,而是人工造假,结果给杂铜火法精练带来极大困难。
一般造假的方法是:1、向管中灌铅,铜管两头砸扁2、用水泥做漆包线的盘,外围绕上漆包线3、用铁丝放在硫酸铜溶液中浸泡,外表看是铜丝4、用红糖熬成糖汁,泼在废铜丝上,将使砂屑牢牢粘在上面,外表好看。
5、打包中放铁块等其他杂物以增加重量。
检查方法:1、用吸铁石吸以分铁2、用手掂量铜管以知是否灌铅3、拆开漆包线盘4、分拣时扣除灰、砂重量1.4、利用紫杂铜连铸连轧生产线简介国产铜杆连铸连轧生产机组是在铝杆连铸连轧基础上发展起来的,其中四川德阳东方电工厂是生产铝杆丫型轧机的老厂,后来合肥神马机械厂亦开始生产,现在生产的厂家有河南巩义海绵设备制造厂、徐州冶金机械厂、成都蜀红机械厂。
该生产线的铸机是仿造SCR的,虽然有所改进,铸轮采用¢1.8m,而熔铜的炉子,有采用自制竖炉的,如吴江桦都电缆厂,宜兴林峰,采用竖炉只能以电解铜为原料。
大部分民营企业家都采用反射炉,吃紫杂铜,炉子的容量有大有小,大的100吨小的40吨,其中用得最多的是60吨、70吨的,搞的比较好的浙江永康芝瑛镇应时雨先生的工厂,吨杆成本在600元,且质量稳定。
芜湖市高智达新技术公司专为德阳电工配套,他们负责设备电气的安装调试,我们负责炉子的设计、砌筑、做铜,并帮助厂家进行技术培训,制定岗位操作规程、安全生产责任制和企业内控标准,等于交钥匙工程。
反射炉一般一年大修(有的中修一次),小修按季度进行。
室外烟囱30 m高,烟道30~50 m 长,同时还要建筑,循环水池,乳化液池和酒精池。
反射炉自出铜口通过溜槽和浇包与铸机相连接,溜槽长度不得大于50 m,溜槽上盖满木炭防止铜液与空气接触,浇包的控制铜液流量的闸板周围用液化气烧嘴来控制铜液的还原性气氛和铜液温度,防止因溜槽过长降温而到浇嘴时冻结。
反射炉因做铜一炉一个周期,炉子里的铜水放完了,铜杆也就轧完了,因此有些厂家建两台炉子,交替作业。
利用紫杂铜连铸连轧生产光亮铜杆的主要技术一是做铜,二是浇铸,三是轧机的工艺和维护。
首先谈做铜,做铜分为五个步骤:一是加料,有手工加料和落地式加料机加料,加料机加料不但节省劳动力,还缩短加料时间。
二是熔化,熔化要彻底,炉底不能存有冷料,且熔化结束一定要扒一次渣,然后,再插风管氧化。
三是氧化,氧化要彻底,氧化结束要取样看样。
对氧化严重的再生铜原料,应在加料时配入一定的还原剂并在熔化过程中插入还原木进行搅动还原,即将工艺改为还原——氧化——还原。
在氧化阶段,复盖焦炭吹风蒸锌,加石英砂造酸性渣,加石灰造碱性渣,每次造渣都要扒净。
四是插木还原,还原一定要准确,即控制铜液中含氧量小于200PPm。
五是出铜,铜液面上复盖一层木炭,以防铜水吃氧。
在从事再生铜的生产时,一定要将每一道工序彻底分清,特别是氧化还原交叉作业时,避免相互影响,我们总结了九个字“深氧化、准还原,扒渣净”。
其二谈浇涛浇铸一定要有一名熟练地浇铸手,我们芜湖高智达公司有一位王师傅,人称江南第一浇,可见其技艺之精湛。
浇铸是手控底浇,浇位10点钟。
浇包铜液温度1120℃±10℃浇包移动机构:要求可分别作升降、横向、纵向移动,其运行速度为2mm/s连铸机:1)铸轮外缘直径¢1800 mm,用铜银合金铸造碾压加工而成,现在有用铜铬锆合金。
U型槽,宽×高=150×110 mm2)铸坯截面积2100 mm23)铸模温度~150℃4)铸坯脱模温度~900℃5)铸轮转速1.7~17m/分无级调速,其速度不均匀变≯1%6)水冷却系统最大水冷却量~200m3/时,流量90 m3/时,扬程108 m喷嘴呈扇形,使水均匀喷射在铸轮内,外侧及两边,其中:内冷却嘴设三排,每隔5°一只,侧冷喷嘴每侧一排,每隔5°一只,外冷喷嘴设两排,每隔5°一只。