我国炼油总工艺流程的发展模式
石油炼化常用的七种工艺流程

石油炼化常用的七种工艺流程石油炼化是一个复杂的过程,涉及多种工艺流程。
不同的工艺流程会根据产品要求将原料生产出不同的产品。
从原油到石油的基本途径一般包括两个步骤:将原油分割成不同的直馏馏分油,然后通过化学反应转化,生成所需要的组分,进而得到一系列合格的石油产品。
常减压蒸馏是炼油厂石油加工的第一道工序,称为原油的一次加工。
它是常压蒸馏和减压蒸馏的合称,基本属于物理过程。
原料油在蒸馏塔里按蒸发能力分成沸点范围不同的油品,这些油有的经过调合和添加剂后以产品形式出厂,相当大的部分是后续加工装置的原料。
常减压工序通常包括三个工序:原油的脱盐、脱水、常压蒸馏和减压蒸馏。
在生产过程中,原油一般是带有盐份和水,能导致设备的腐蚀,因此原油在进入常减压之前首先进行脱盐脱水预处理,通常是加入破乳剂和水。
常减压蒸馏的生产设备包括常压蒸馏塔和减压蒸馏塔。
原油蒸馏一般包括常压蒸馏和减压蒸馏两个部分。
在生产过程中,原油经过流量计、换热部分、沏馏塔形成两部分,一部分形成塔顶油,经过冷却器、流量计,最后进入罐区,这一部分是化工轻油(即所谓的石脑油);一部分形成塔底油,再经过换热部分,进入常压炉、常压塔,形成三部分,一部分柴油,一部分蜡油,一部分塔底油;剩余的塔底油在经过减压炉、减压塔,进一步加工,生成减一线、蜡油、渣油和沥青。
常减压蒸馏的产品包括石脑油、粗柴油(瓦斯油)、渣油、沥青和减一线。
其中石脑油直接出售由其他小企业生产溶剂油或者进入下一步的深加工,一般是催化重整生产溶剂油或提取萃类化合物;减一线可以直接进行调剂润滑油;蜡油和渣油进入催化裂化环节,生产汽油、柴油、煤油等成品油。
总之,常减压蒸馏是炼油厂石油加工的第一道工序,它是将原油分割成不同的直馏馏分油的过程,是石油炼化的基础。
在生产过程中,需要进行脱盐脱水预处理,常减压工序不生产汽油产品,其中蜡油和渣油进入催化裂化环节,生产汽油、柴油、煤油等成品油。
a。
在原油预热后,焦化原料(减压渣油)先进入原料缓冲罐,然后通过泵送入加热炉对流段升温至约340-350℃。
中石油炼油工艺技术

中石油炼油工艺技术中石油炼油工艺技术是指对原油进行精细加工以提取出更多高附加值产品的技术体系。
石油炼制过程主要包括物理分离、化学转化和催化反应等步骤,通过这些工艺可以将原油中的各种成分分离出来,并进一步转化为石油产品,如汽油、柴油、煤油等。
首先,物理分离是炼油工艺的第一步,它主要通过不同物质的沸点差异来实现。
原油经过加热后,可以通过多级蒸馏行程将其分离成不同沸点范围的馏分,例如汽油、柴油和煤油。
此外,还可以采用各种物质的溶解度差异来实现物质的分离,例如萃取和萃淋工艺。
其次,化学转化是炼油工艺中的重要环节。
原油中包含着各种碳氢化合物,通过化学反应可以将其转化为更有价值的产品。
常见的化学转化技术包括裂化、重整和重油加氢等。
裂化技术主要将较长链的烃类分子断裂成较短链的烃类分子,从而提高汽油产量。
重整技术则是将烷烃转化成较为芳香的烃类,以提高汽油辛烷值。
重油加氢则是将重油中的硫、氮和金属等杂质去除,以使其更符合环保要求。
另外,催化反应也是炼油工艺中的关键步骤。
催化剂可以提高反应的速率和选择性,从而实现更高效的产出。
例如,催化裂化技术在原油炼制中得到广泛应用。
通过与催化剂接触,原油中的烃类分子可以在较低温度下发生裂化反应,得到更多的轻质产品。
此外,催化加氢技术也是一种常见的炼油工艺。
通过与氢气反应,可以将原油中的硫、氮和金属等有害物质转化为无害物质,从而提高产品的质量。
总的来说,中石油炼油工艺技术通过物理分离、化学转化和催化反应等步骤,实现了对原油的精细加工,提取出更多高附加值产品。
这些技术在提高产品质量、增加产量和减少环境污染等方面都起到了重要作用,为石油产业的发展提供了强大的支撑。
随着科技的不断进步,相信中石油炼油工艺技术将会不断创新和完善,为我国能源行业的可持续发展做出更大贡献。
炼油厂工艺流程
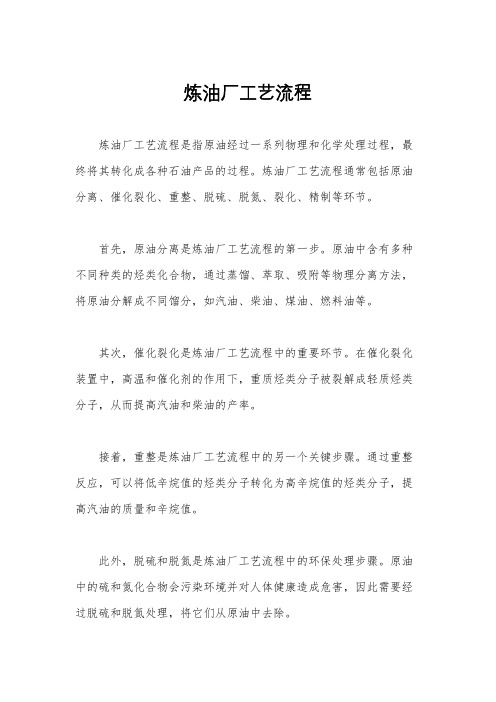
炼油厂工艺流程
炼油厂工艺流程是指原油经过一系列物理和化学处理过程,最终将其转化成各种石油产品的过程。
炼油厂工艺流程通常包括原油分离、催化裂化、重整、脱硫、脱氮、裂化、精制等环节。
首先,原油分离是炼油厂工艺流程的第一步。
原油中含有多种不同种类的烃类化合物,通过蒸馏、萃取、吸附等物理分离方法,将原油分解成不同馏分,如汽油、柴油、煤油、燃料油等。
其次,催化裂化是炼油厂工艺流程中的重要环节。
在催化裂化装置中,高温和催化剂的作用下,重质烃类分子被裂解成轻质烃类分子,从而提高汽油和柴油的产率。
接着,重整是炼油厂工艺流程中的另一个关键步骤。
通过重整反应,可以将低辛烷值的烃类分子转化为高辛烷值的烃类分子,提高汽油的质量和辛烷值。
此外,脱硫和脱氮是炼油厂工艺流程中的环保处理步骤。
原油中的硫和氮化合物会污染环境并对人体健康造成危害,因此需要经过脱硫和脱氮处理,将它们从原油中去除。
裂化是炼油厂工艺流程中用于生产乙烯和丙烯等烯烃产品的重
要工艺。
通过高温和催化剂的作用,将重质烃类分子裂解成轻质烯
烃产品。
最后,精制是炼油厂工艺流程中的最后一步。
通过精制工艺,
可以将各种馏分中的杂质去除,提高产品的纯度和质量,满足不同
产品的要求。
总的来说,炼油厂工艺流程是一个复杂而又精密的系统工程,
其中涉及了多种物理和化学过程。
通过不断的技术创新和工艺优化,炼油厂工艺流程可以实现高效、低能耗、高产率、高质量的生产,
为社会各行业提供了丰富的石油产品。
炼油加工过程及油品的生产

炼油加工过程及油品的生产炼油是将原油经过一系列的加工和分离过程,生产出不同等级和类型的石油产品的过程。
炼油加工过程分为初级加工、次级加工和高级加工三个阶段。
下面将详细介绍这些加工过程以及油品的生产。
首先是初级加工,也称为常规炼油,包括石油分离、蒸馏和催化裂化等过程。
石油分离是将原油中的不同组分进行分离。
原油中含有不同烃类的混合物,通过蒸馏和分馏的方法,将其分离成不同的馏分。
不同的馏分具有不同的沸点,所以通过控制温度,可以使得原油中的烃类分别沸腾并进行分离。
例如,通过蒸馏可以将原油中的汽油、柴油、液化石油气等组分进行分离。
次级加工是对初级产品进行进一步处理和提纯。
其中最重要的次级加工过程之一是重整。
重整是将低辛烷燃料转化为高辛烷燃料的过程,以提高汽油的加烷值。
此外,还有氢化和氧化过程,对高硫含量的产物进行脱硫和脱氮处理,减少对环境的污染。
还有催化裂化和裂解等过程,将较重烃类的石油产品裂解成较轻的烃类,以满足市场对汽油和液化气的需求。
高级加工则是对初级加工和次级加工所得产品进行深加工和改性。
高级加工的产品包括机动车用油和润滑油等。
这些产品需要经过一系列的加工步骤,如脱芳烃、脱蜡、氢化等过程,以提高油品的品质和性能。
此外,高级加工还包括添加剂的加入,以改善油品的抗磨、清洁和抗氧化性能,增强油品的使用寿命和性能。
油品的生产是炼油加工的最终目标。
经过一系列的加工和处理过程,原油被转化为不同类型和等级的石油产品。
常见的石油产品包括汽油、柴油、煤油、润滑油和液化石油气等。
汽油是最常见的石油产品之一,用于机动车的燃料。
柴油则用于柴油发动机,用于商业车辆和工业设备。
煤油主要用于燃煤锅炉和工业加热。
除了以上产品,炼油加工还可以生产出润滑油和液化石油气等产品。
润滑油主要用于减少摩擦和磨损,保护设备和机械的寿命。
液化石油气则是一种很重要的石油产品,用于家庭和工业的燃料。
液化石油气具有高热值、低污染和易于储存和运输等优点。
炼油工艺综述
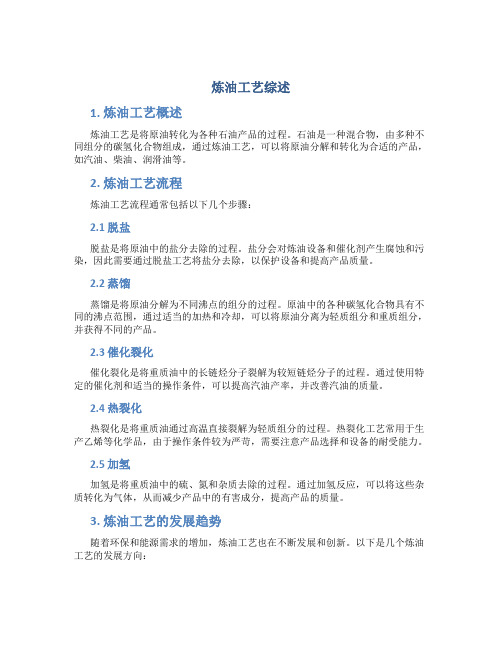
炼油工艺综述1. 炼油工艺概述炼油工艺是将原油转化为各种石油产品的过程。
石油是一种混合物,由多种不同组分的碳氢化合物组成,通过炼油工艺,可以将原油分解和转化为合适的产品,如汽油、柴油、润滑油等。
2. 炼油工艺流程炼油工艺流程通常包括以下几个步骤:2.1 脱盐脱盐是将原油中的盐分去除的过程。
盐分会对炼油设备和催化剂产生腐蚀和污染,因此需要通过脱盐工艺将盐分去除,以保护设备和提高产品质量。
2.2 蒸馏蒸馏是将原油分解为不同沸点的组分的过程。
原油中的各种碳氢化合物具有不同的沸点范围,通过适当的加热和冷却,可以将原油分离为轻质组分和重质组分,并获得不同的产品。
2.3 催化裂化催化裂化是将重质油中的长链烃分子裂解为较短链烃分子的过程。
通过使用特定的催化剂和适当的操作条件,可以提高汽油产率,并改善汽油的质量。
2.4 热裂化热裂化是将重质油通过高温直接裂解为轻质组分的过程。
热裂化工艺常用于生产乙烯等化学品,由于操作条件较为严苛,需要注意产品选择和设备的耐受能力。
2.5 加氢加氢是将重质油中的硫、氮和杂质去除的过程。
通过加氢反应,可以将这些杂质转化为气体,从而减少产品中的有害成分,提高产品的质量。
3. 炼油工艺的发展趋势随着环保和能源需求的增加,炼油工艺也在不断发展和创新。
以下是几个炼油工艺的发展方向:3.1 深度加工深度加工是指将原油加工至更高附加值产品的过程。
通过优化工艺、改进催化剂和提高设备效率,可以实现更高的产品质量和更高的利润。
3.2 渣油加工渣油加工是指对重质油进行加工的过程。
由于重质油中含有较高的硫、氮、重金属等有害元素,因此对渣油进行加工可以减少环境污染,并将其转化为更有价值的产品。
3.3 利用新能源随着新能源的发展和应用,炼油工艺也开始关注利用新能源,如生物质、太阳能等。
这些新能源可以替代传统能源,减少对非可再生能源的需求,并降低环境影响。
3.4 节能减排节能减排是炼油工艺发展的重要方向之一。
对我国炼油工业发展的几点思考

管理 科学
・1 ・ 17
这需要我们 的图书馆馆员拥有长期保护的意识 。 量, 努力提高其利用效率 ; 另一方面 , 逐步把馆藏资源建设 转移到数 资源 的有效 管理 : 数据库拥 有庞大的容量 , 里面包含 的内容涉 字化电子文献信息资源及多媒体 的建设与开发上 , 变静态 收藏 为动 及各个学科领域 , 那么对数据资源的合理归类是 图书馆馆员 日常的 态收藏和网上获取 , 以满足读者的多方需求 。 重要工作 。 在归类 中 , 还必须杜绝资源的重复 , 这也是数据库资源管 在 自动化 、 网络化条件下 , 高校图书馆应 突破传 统的展示业务 理 的一大难题。海量 的资源难 以保证其属性的单一 , 可能在某些不 流程 的管理机制 , 重组 图书馆 的业务 结构体系 , 建立起 以 自动化为 同的关 键词和标题下 , 却拥有相 同的内容 , 这需要我们在 日常 的工 中心 , 面向大众 , 能对用户需求作 出快速反应 , 能解 决用 户实 际问 并 作 中注意区别对 待 , 清除垃圾资源 。 题的运行机制 。具体应弱化 以采 编流程为主导 的管理环节 , 建立起 33 .联合馆藏 。 在数字图书馆时代 ,图书馆” “ 已经突破单馆 的概 以用户服务为主导的业务体 系。 图书馆工作重心应 由一般的借 还服 念, 必须进行广域的合作 , 文献不仅限于普通文献 , 还应扩展到 电子 务 向咨询服务变革 , 工作人员应对知识和信息进行分 析研究 和综合 资源服务和知识 服务 。 每一个高校图书馆都有 自己的特色项 目和学 工作 , 开展深层 次的信息加工和参考咨询工作。 科优势 , 以前传统 的图书馆都是各 自为家 , 互不相干 , 造成读者往往 综 上所述 , 数字化 、 网络化的图书资源管理理念 , 高校馆藏 要求 想找一些资源数据需要跑遍一个城市所有图书馆 , 这不符合 图书馆 从 传统 的独立封 闭式建设 向信息化资源共享平 台的图书馆联盟转 的建设理念。而在 当今 网络数字化环境下 , 可以非常便捷地构建 图 变 。联合馆藏可 以将各个图书馆 的独特优势最大化 , 构建交流互助 书馆之间的平 台 , 实现资源共享 , 这是未来 图书馆 的主流 发展方 向 , 平 台 , 实现资源共享 。高校图书馆应突破传 统的展示业务流程 的管 既大大拓展 了图书馆 的资源范 围 ,又节 省了各个图书馆 的经费投 理机制 , 调整文献信息资源结构 , 寻求支持数字 图书馆的合理机制 , 入 , 方便 了读者大量的资源需求 , 有利 于各方面的发展模式 。 还 是 联 重组图书馆 的业务结构体系 , 建立起以 自动化为中心 , 向大众 , 面 能 合馆藏可以通过构建数字化平台和体制改革实现。 字化平 台就是 对用户需求作出快速反应 , 数 并能解决用户实际问题 的运行机制 。逐 在共 同构建的平 台上将一个图书馆的资源分布于此 , 以共 同使用 步把馆藏资源建设转移 到数字化电子文献信息资源及 多媒体 的建 可 和维护更新 , 而体制 上的改革是针对传统 的图书借记规 划 , 它范 设 与开发上 , 让 变静态收藏为动态 收藏 和网上获 取 , 以满 足读者 的多 围更广一些 , 以在各大图书馆之 间流通使用 。各大 图书馆直接的 方需求 。 可 联合带来的将是全新 的图书馆理念 , 它弥补 了单一 图书馆在数据资 参考文献 源上 的不足 , 却将各个 图书馆的独特优势最大化 , 在最大程度 上去 [ 王 丽 华 . 来 数 字 图 书馆 的 关 键 技 术 探 讨 图 书馆 论 坛 ,04 1 】 未 20 满足读者的要求 。 () 3. 34 .重组业务流程。 寻求支持数字图书馆 的合理机制 , 积极调整 【 奉 国和. 2 1 多角度 探讨 数 字 图书馆 发展 演 变『. 川图 书馆 学报 , J四 1 086. 文献信息资源结构 , 使之运行更趋 于合理 。图书馆作为信息资源的 2 0 ( ) 主要集散中介 ,如何综合开发 自己拥有的各种类型的信息资源 , [ 吴淑华. 通 3 】 网络环境- : FL ̄检索课教 学的现状 与创新思考[. J 图书馆 】 过对信息资源的深加工 ,使之成 为特定用 户对 象需要 的情报 资源 , 学研 究 ,0 9 2 . 20( ) 满足不同用 户的需求 。 这要求一方面要不断提高纸质文献 的人藏质 1 才. 网络教 育综述【. 胡英 高校 J 北京教 育学院学报 ,0 9 2 . 】 20 国炼油工业 发展 的几点思考
2024年炼油化工一体化市场发展现状

2024年炼油化工一体化市场发展现状1. 引言炼油化工一体化是指将石油炼制和化学工艺相结合,实现石油加工和石化产品生产的一种综合型产业模式。
在全球范围内,炼油化工一体化已成为能源和化工领域的重要发展趋势。
本文将对炼油化工一体化市场的发展现状进行分析。
2. 炼油化工一体化的定义和背景炼油化工一体化是将石油炼制和化学工艺相结合的一种综合型产业模式。
通过将炼油和石化两个环节相互融合,可以实现资源的高效利用和产品的多元化生产。
这种一体化模式可以提高整个产业链的运行效率并降低生产成本,同时也能够降低对外部能源和原料的依赖。
3. 炼油化工一体化市场的规模和增长趋势炼油化工一体化市场规模大,增长趋势明显。
根据统计数据,全球范围内的炼油化工一体化项目投资规模逐年增长,市场规模呈现逐年扩大的趋势。
特别是在发展中国家,炼油化工一体化项目的建设速度更是快速增长。
这主要受益于能源需求的增长和工业结构的优化升级。
4. 炼油化工一体化市场的主要推动因素炼油化工一体化市场的发展得益于多种推动因素。
首先,炼油化工一体化可以实现资源的高效利用,降低能源和原料成本,提高企业的竞争力。
其次,随着能源需求的不断增长,炼油化工一体化可以满足市场对于石化产品的需求。
再次,政府对于炼油化工一体化项目的支持和政策的倾斜也是市场发展的重要因素。
5. 炼油化工一体化市场的发展模式炼油化工一体化市场的发展模式多样。
在不同的国家和地区,由于能源资源的禀赋和市场需求的多样化,炼油化工一体化的发展模式也存在差异。
例如,一些国家更注重石油炼制和石化产品的生产,而另一些国家则更注重石化产品的深加工和高附加值的产品生产。
6. 炼油化工一体化市场的挑战与机遇炼油化工一体化市场面临着一些挑战和机遇。
首先,由于能源需求的增加和环境保护的要求,炼油化工生产过程中产生的污染和排放问题成为了重要的挑战。
其次,市场竞争日趋激烈,企业需要不断提升技术和降低成本才能保持竞争优势。
石油化工行业炼油工艺流程资料

石油化工行业炼油工艺流程资料石油化工行业是世界上最重要的工业之一,其炼油工艺流程是整个石油加工过程中的关键环节。
本文将为您介绍石油炼油工艺的基本流程、常见的工艺方法以及炼油过程中的关键技术。
一、基本流程石油炼油工艺的基本流程可分为原油处理、初级加工、中级加工和深加工四个阶段。
1. 原油处理原油处理是炼油的第一步,旨在除去原油中的杂质,提高原油的质量。
常见的原油处理方法包括沉淀、过滤和加热等。
2. 初级加工初级加工阶段是将原油分割成不同的组分,例如汽油、柴油和润滑油等。
这通常通过蒸馏来完成,根据组分的沸点进行分离。
3. 中级加工中级加工阶段是对初级产品进行进一步的改性和加工,以满足不同类型和等级的需求。
常见的中级加工方法包括裂化、重整和氢化等。
4. 深加工深加工是指对中级产品进行更复杂的化学反应和处理,以生产出高附加值的产品。
例如石化产品、润滑油添加剂和蜡等。
二、常见的工艺方法炼油工艺中常用的方法包括蒸馏、分离、裂化、反应和合成等。
1. 蒸馏蒸馏是根据不同组分的沸点将原油分割成不同的馏分。
这是最基本的分离方法,可将原油分成汽油、柴油和润滑油等馏分。
2. 分离分离是将原油中的各种组分进行分离和提纯。
常见的分离方法包括萃取、吸附和膜分离等。
3. 裂化裂化是将较重的油品转化为较轻的产品,增加汽油产量的方法。
常见的裂化方法有催化裂化和热裂化等。
4. 反应反应是指通过化学反应改变原料的性质,以生产具有特定功能的产品。
例如重整反应可以将低辛烷值的石脑油转化为高辛烷值的汽油。
5. 合成合成是指通过化学合成方法将原料转化为更高价值的产品。
例如合成柴油可以通过合成气转化为合成甲醇,再经过合成过程得到柴油。
三、关键技术在石油炼油过程中,有几个关键技术对于工艺的顺利进行非常重要。
1. 催化技术催化技术是指通过催化剂促进化学反应的进行,提高反应速率和选择性。
常见的催化技术包括催化裂化和催化重整等。
2. 氢化技术氢化技术是将氢气与油品进行反应,以降低硫、氮及其他杂质含量的方法。
浅析我国石油化工与精细化工的发展
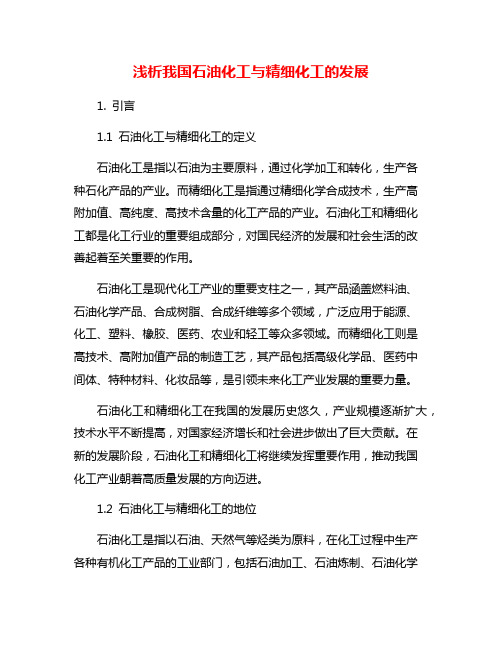
浅析我国石油化工与精细化工的发展1. 引言1.1 石油化工与精细化工的定义石油化工是指以石油为主要原料,通过化学加工和转化,生产各种石化产品的产业。
而精细化工是指通过精细化学合成技术,生产高附加值、高纯度、高技术含量的化工产品的产业。
石油化工和精细化工都是化工行业的重要组成部分,对国民经济的发展和社会生活的改善起着至关重要的作用。
石油化工是现代化工产业的重要支柱之一,其产品涵盖燃料油、石油化学产品、合成树脂、合成纤维等多个领域,广泛应用于能源、化工、塑料、橡胶、医药、农业和轻工等众多领域。
而精细化工则是高技术、高附加值产品的制造工艺,其产品包括高级化学品、医药中间体、特种材料、化妆品等,是引领未来化工产业发展的重要力量。
石油化工和精细化工在我国的发展历史悠久,产业规模逐渐扩大,技术水平不断提高,对国家经济增长和社会进步做出了巨大贡献。
在新的发展阶段,石油化工和精细化工将继续发挥重要作用,推动我国化工产业朝着高质量发展的方向迈进。
1.2 石油化工与精细化工的地位石油化工是指以石油、天然气等烃类为原料,在化工过程中生产各种有机化工产品的工业部门,包括石油加工、石油炼制、石油化学等领域。
而精细化工则是指在石油化工的基础上,进一步加工提纯,生产高附加值的化工产品,包括化学品、农药、医药、涂料、塑料等领域。
石油化工与精细化工在我国的地位非常重要。
石油化工是我国国民经济的支柱产业之一,对于国家的能源安全和经济发展具有至关重要的作用。
精细化工则是高新技术产业的重要组成部分,是实现经济结构升级和产业转型升级的重要领域。
石油化工与精细化工的发展直接影响着我国的工业结构调整和产业升级,也关系到国家能源资源的合理利用和环境保护。
加强石油化工与精细化工的技术创新,提升产业的竞争力和可持续发展能力,已成为我国经济发展的重要任务之一。
随着我国产业智能化和绿色化发展的需求不断增强,石油化工与精细化工的地位将更加凸显,为我国经济的可持续发展提供强大支撑。
探究炼化一体化行业的发展问题

探究炼化一体化行业的发展问题摘要:目前的炼油业正面临产能过剩风险,产业结构急需调整,而由油品炼化而来的化工产品行业,尤其是高端化工产品行业,却存在明显的产能不足问题,传统能源的开发利用出现失衡现象。
在此背景下,推进炼化一体化行业发展,实现原油资源利用最佳化、生产运行最优化及经济效益最大化,已然成为当前时期该行业工作者需要重点考量的问题。
关键词:炼化一体化;问题;发展;效益随着新能源时代的来临,全球能源需求局面已经发生巨大改变,与之相关的沿线产业均受到或大或小的影响,其中传统炼化行业所受影响十分明显。
新能源的不断开发与应用技术水平的不断提升,使得传统不可再生能源的需求量日益减少,成品油消费呈现增速放缓趋势。
1、现阶段炼化行业发展存在的问题1.1原油对外依存度过高,炼油产能过剩,激化炼化行业矛盾国家对于进口原油的依存度在70%以上,这给能源储备及与产业相关的上下游企业发展都带来了较大安全风险。
原油加工生产在工业领域占据很大比例,但是大部分都集中在成品油加工领域。
虽然现在世界各国对于成品油的需求量仍处于增长趋势,但是整体增长速度明显下降,这使得国家炼油行业逐渐出现产能过剩现象。
上游原油开发企业的利润相对还保持在较为可观的水平,但是下游炼油企业的经营效益参差不齐。
具备高水平原油炼化能力的企业较为稀缺,高端化工产品如芳烃、烯烃等化工原料的市场缺口仍然较大,而生产成品油的企业却供大于求。
1.2石化产品存在明显的结构性短缺问题目前,对于化工产品的需求仍然处于稳定增长的状态,且其增长速度远远超过对于成品油的需求,但是大部分原油加工企业都专注于成品油生产,化工产品的输出量明显不足,大部分高端化工产品仍然需要依赖国外进口,如乙烯、芳烃等产品,国内自给率还有很大进步空间。
这使得石化行业呈现突出的结构性资源矛盾问题,炼油企业不断增加,工程同质化现象严重。
2、促进炼化一体化行业长期可持续发展的有效策略2.1石化企业从以生产燃料为主向生产燃料+化工原料转变首先,炼化企业要积极引入先进的一体化炼油设施,持续升级高端化工产品的产线工艺技术,并逐步加大对高端化工产品加工的投资力度,加强新材料和专用化学品的研发和生产,通过扩大产线规模或者优化生产工艺的方式,增加化工炼化产品产量,以弥补高端化工原料产能不足的缺陷。
石化和化学工业发展规划-中华人民共和国工业和信息化部

5.坚持开放合作。加强国际交流与合作,统筹国内国际“两种资源、两个市场”,促进引资与引智并举,支持有条件的企业开展境外能源和矿产资源开辟利用与合作,积极参与国际并购和重组,哺育国际经营能力,加快境外生产基地及合作园区建设,形成优进优出、内外联动的开放型产业新格局。
(三)规划目标
“十三五”期间,石化和化学工业结构调整和转型升级取得重大发展,质量和效益显著提高,向石化和化学工业强国迈出坚实步伐。
一、行业现状和发展环境
(一)发展成就
“十二五”时期,面对国内经济增长速度换挡期、结构调整阵痛期、前期刺激政策消化期三期叠加的复杂形势和世界经济复苏艰难蜿蜒的外部环境,我国石化和化学工业积极应对各种风险和挑战,大力推进“转方式、调结构”,全行业总体保持平稳较快发展,综合实力显著增强,为促进经济社会健康发展做出了突出贡献。
3.创新驱动目标。科研投入占全行业主营业务收入的比重达到1.2%。产学研协同创新体系日益完善,在重点领域建成一批国家和行业创新平台,突破一批重大关键共性技术和重大成套装备,形成一批具有成长性的新的经济增长点。
4.绿色发展目标。“十三五”末,万元GDP用水量下降23%,万元GDP能源消耗、二氧化碳排放降低18%,化学需氧量、氨氮排放总量减少10%,二氧化硫、氮氧化物排放总量减少15%,重点行业挥发性有机物排放量削减30%以上。
炼化一体化发展现状地炼呈现数量多且规模小特点

炼化一体化发展现状地炼呈现数量多且规模小特点炼化一体化发展现状:地炼呈现数量多且规模小特点炼化一体化是指在同一生产单位集炼油和石化工艺为一体,实现原油加工和石化产品生产的一种综合化发展模式。
炼化一体化的发展在全球范围内得到了广泛关注和推动,成为石油石化行业转型升级的重要方向之一。
然而,地炼作为炼化一体化的一种模式,在中国的发展中呈现出数量多且规模相对较小的特点。
本文将探讨地炼一体化发展的现状,分析其数量多、规模小的原因,并对未来发展进行展望。
地炼一体化的发展现状表明,我国地炼数量众多,尤以东部沿海地区为主。
根据统计数据,截至目前,我国已建成或拟建的地炼项目超过100个,其中大部分分布在山东、浙江、广东等省份。
这些地炼项目既有国内大型石油石化企业的自建项目,也有合资合作的项目。
地炼一体化的发展水平在不断提高,但和国际先进水平仍存在一定差距。
地炼一体化的数量多而规模相对较小的特点主要有以下几个原因。
首先,我国沿海地区资源禀赋优势明显,沿海地区集中了丰富的石油资源和便利的交通条件,这为地炼一体化项目的建设提供了有利条件。
其次,地方政府鼓励本地企业发展,通过引进外资或与国内企业进行合作,加速地炼项目的推进。
这也导致了地炼数量增多、规模相对较小的现象。
此外,由于沿海地区的经济发达和市场需求旺盛,地炼项目可以更直接地满足当地市场需求,所以地炼一体化的规模相对较小,但满足了市场需求。
尽管地炼一体化的规模相对较小,但其带来的效益和影响不可小觑。
首先,地炼一体化的发展推动了当地经济的快速增长和产业结构的升级。
大量的投资和人员流动带动了相关产业的发展,促进了就业和税收的增加。
其次,地炼一体化项目通过提高产品的质量和附加值,提供了更多高质量的石化产品,满足了市场需求,提升了国家在石化行业的竞争力。
此外,地炼一体化的发展也有利于提高能源利用效率,减少环境污染,推动经济可持续发展。
未来,地炼一体化仍将是我国石化行业发展的重要方向之一。
石油炼化工艺流程
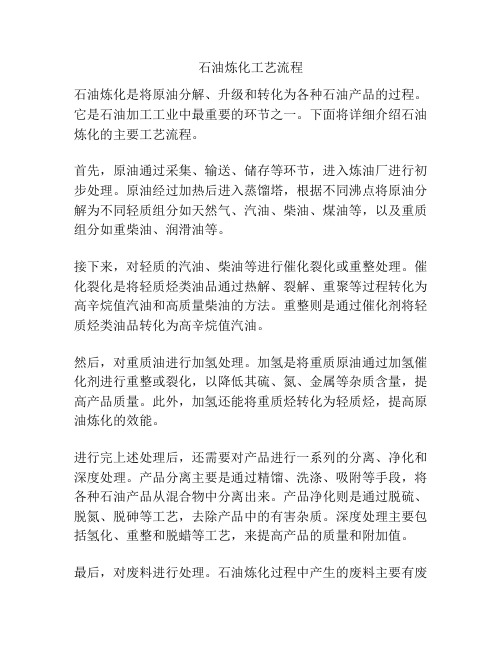
石油炼化工艺流程石油炼化是将原油分解、升级和转化为各种石油产品的过程。
它是石油加工工业中最重要的环节之一。
下面将详细介绍石油炼化的主要工艺流程。
首先,原油通过采集、输送、储存等环节,进入炼油厂进行初步处理。
原油经过加热后进入蒸馏塔,根据不同沸点将原油分解为不同轻质组分如天然气、汽油、柴油、煤油等,以及重质组分如重柴油、润滑油等。
接下来,对轻质的汽油、柴油等进行催化裂化或重整处理。
催化裂化是将轻质烃类油品通过热解、裂解、重聚等过程转化为高辛烷值汽油和高质量柴油的方法。
重整则是通过催化剂将轻质烃类油品转化为高辛烷值汽油。
然后,对重质油进行加氢处理。
加氢是将重质原油通过加氢催化剂进行重整或裂化,以降低其硫、氮、金属等杂质含量,提高产品质量。
此外,加氢还能将重质烃转化为轻质烃,提高原油炼化的效能。
进行完上述处理后,还需要对产品进行一系列的分离、净化和深度处理。
产品分离主要是通过精馏、洗涤、吸附等手段,将各种石油产品从混合物中分离出来。
产品净化则是通过脱硫、脱氮、脱砷等工艺,去除产品中的有害杂质。
深度处理主要包括氢化、重整和脱蜡等工艺,来提高产品的质量和附加值。
最后,对废料进行处理。
石油炼化过程中产生的废料主要有废水、废气和废渣。
废水通过沉淀、过滤、蒸发等工艺进行处理后,可用于再利用或排放。
废气经过净化设备处理后,排放符合环保要求。
废渣则是通过沉淀、过滤、干燥等工艺进行处理后,可作为再生能源或用于其它工业领域。
综上所述,石油炼化工艺流程包括原油初步处理、轻质组分处理、重质油加氢处理、产品分离净化和废料处理等环节。
通过这些工艺,原油得以转化为各种石油产品,满足人们对能源和化工产品的需求,并为社会经济的发展做出了重要贡献。
同时,石油炼化过程中还需要注意环保、节能、安全等问题,以确保生产过程的可持续性和环境友好性。
炼油工艺流程
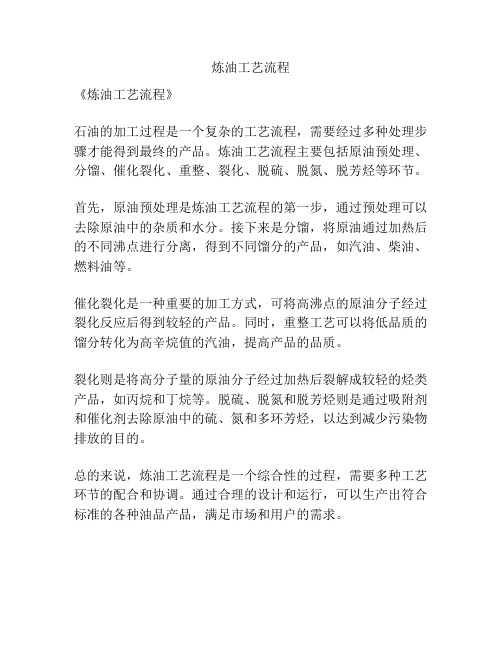
炼油工艺流程
《炼油工艺流程》
石油的加工过程是一个复杂的工艺流程,需要经过多种处理步骤才能得到最终的产品。
炼油工艺流程主要包括原油预处理、分馏、催化裂化、重整、裂化、脱硫、脱氮、脱芳烃等环节。
首先,原油预处理是炼油工艺流程的第一步,通过预处理可以去除原油中的杂质和水分。
接下来是分馏,将原油通过加热后的不同沸点进行分离,得到不同馏分的产品,如汽油、柴油、燃料油等。
催化裂化是一种重要的加工方式,可将高沸点的原油分子经过裂化反应后得到较轻的产品。
同时,重整工艺可以将低品质的馏分转化为高辛烷值的汽油,提高产品的品质。
裂化则是将高分子量的原油分子经过加热后裂解成较轻的烃类产品,如丙烷和丁烷等。
脱硫、脱氮和脱芳烃则是通过吸附剂和催化剂去除原油中的硫、氮和多环芳烃,以达到减少污染物排放的目的。
总的来说,炼油工艺流程是一个综合性的过程,需要多种工艺环节的配合和协调。
通过合理的设计和运行,可以生产出符合标准的各种油品产品,满足市场和用户的需求。
从总体布置思考石油化工企业可持续发展
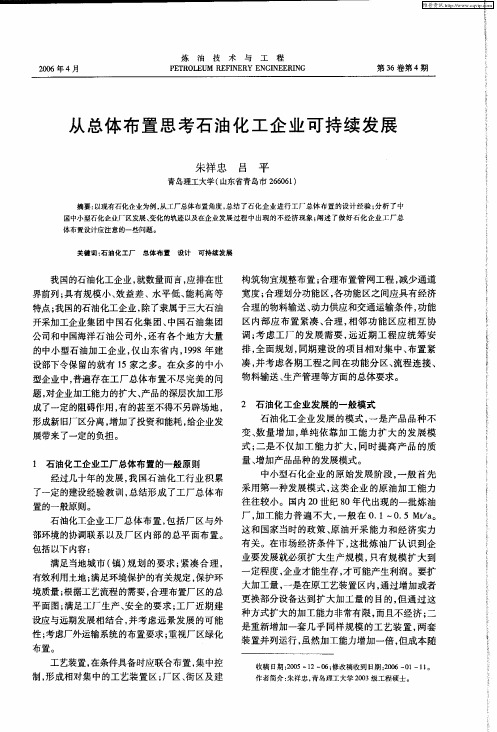
1 石油化 工企 业工厂 总体布 置 的一般 原则
经过几十年的发展 , 国石油化工行业积 累 我 了一定的建设经验教 训, 总结形成 了工厂总体 布 置的一般原则。 石油化工企业工厂总体布置 , 包括厂 区与外 部环境的协调联系 以及厂区内部的总平 面布置。 包括以下内容 :
往往较小。国内 2 世纪 8 年代出现的一批炼 油 0 O 厂, 加工能力普遍不 大 , 一般在 0 1~ . ta . 0 5M. 。 /
这 和国家当时的政策 、 原油开采 能力和经济实力
有关 。在市场经济条件下 , 这批炼油厂认识 到企
业要发展就必须扩大生产规模 , 只有规模扩大 到
构筑物宜规整布置 ; 合理布置管 网工程 , 减少通道 宽度 ; 合理划分功能区, 各功能区之间应具有经济 合理的物料输送、 动力供应和交通运输条件 , 功能
区内部应布置紧凑 、 合理 , 相邻功能 区应相互协
调; 考虑工 厂的发展需要 , 远近期工程 应统筹 安
排, 全面规划 , 同期建设的项 目相对集 中、 布置紧
原来的加工规模基础上规划布置 的, 若总体 布置
没有很好 地考虑 企业 长远 的发展 , 就可 能 出现 “ 补补丁” 垒砖头” 的厂区发展模式。所谓 或“ 式
“ 补补丁 ” 就 是 在 原 厂 区 内 见 缝 插 针 , , 只要 有 点
空闲地 , 就增加生产单元 , 再也无法考虑工厂的功 能分区、 安全消防和厂容厂貌 了; 最终 的结果 , 厂 区就像一件百衲衣 。所谓“ 垒砖头” 就是 向厂区 ,
一
满足当地城市 ( ) 镇 规划的要求 ; 紧凑合 理 ,
有效利用土地 ; 满足环境保护的有关规定 , 保护环 境质量 ; 根据工艺流程的需要 , 合理布置厂区的总 平面图; 满足工厂生产、 安全的要求 ; 工厂近期建
应对高硫劣质原油的炼油总工艺流程设计

渣 油加 氢 + 重 油 催 化裂 化 、 剂脱 沥青 + 整 体 煤 溶
气 化联合 循 环发 电系 统 (G C , 每种 模 式 都 有 IC )但
明 显 的局 限 性 。
质 量分 数小 于 1 0g / ; 2 gg 处理 后 的催化裂 化原 料性 质要 求 为 : 质量 分 数小 于 0 3 、 炭小 于 6 硫 . 残 %、 金 属 ( +V) 量 分 数 小 于 1 gg 副产 的柴 油 Ni 质 5g /, 硫 质量 分数 约为 3 0g / 、 0 gg 十六烷 值 为 4 , 直接 2可
用 于调 合普 通 柴 油 ; 续催 化 裂 化 汽 油 的硫 质 量 后
2 1 延 迟焦 化 +C B锅炉模 式 . F
延 迟焦 化工艺 技 术是 重 油 轻 质化 工 艺 中原 料 适 应性 最强 的工 艺 , 理论 上 对 进 料 的硫 、 属 、 金 沥 青 质 等含量 及 残 炭 没有 限 制 , 投 资 和 运 行 成 本 且 相对 较低 , 一 需 要 关 注 的是 石 油 焦 的 出路 和 污 唯 水 的处 理 问 题 。 自 2 0 0 1年 大 型化 的 “ 炉 两 塔 ” 一
油总 工艺 流 程 以应 对 原 油 的 高硫 化 和 劣 质 化 , 并
满 足 产 品 质 量 升 级 换 代 的 要 求 , 必 须 面 对 的 紧 是
要 问题 。
1 加 工 高 硫 劣 质 原 油 的 紧 迫 性
自 19 9 3年 我 国成 为 原 油净 进 口国 以来 , 油 原 进 口量 持续 增 加 , 0 1年达 到 约 2 0 Mt较 2 1 21 6 , 00
化 进料 、 大原 油 来 源 和提 高 经 济 效 益 纷 纷 建 设 扩
炼油厂工艺流程

炼油厂工艺流程
《炼油厂工艺流程》
炼油厂是将原油转化为汽油、柴油、煤油等石油产品的重要工业设施。
炼油厂工艺流程是一个复杂的过程,涉及到多个工艺单元和技术,以及各种化学反应和物理分离过程。
首先,原油通过一系列预处理工艺单元进行初步处理,包括脱盐、脱硫、脱水等处理,以去除杂质和硫化物。
然后,原油进入裂化装置进行裂化过程,将大分子烃类分解成小分子烃类,生产出汽油、柴油等产品。
随后,经过蒸馏装置进行蒸馏分馏,将不同沸点的烃类分离出来,得到各种产品。
另外,炼油厂还通过重整、裂化、重整、加氢等工艺单元对产品进行改质升级。
其中,重整是将低辛烷值的馏分转化为高辛烷值的汽油产品;裂化是将重质油产生乙烯、丙烯等烯烃产品;加氢是通过加氢裂化将重质油产品转化为轻油产品。
最后,炼油厂还通过分离、脱硫、脱氮、脱气等工艺单元进行产品的后处理,目的是提高产品质量和符合环保要求。
总体来说,炼油厂的工艺流程包括原油预处理、初步裂化、分馏分离、产品改质升级、产品后处理等多个环节。
各个工艺单元的相互配合,构成了完整的炼油过程,为石油产品的生产提供了技术支持和保障。
炼油生产工艺

炼油生产工艺炼油是将原油分离出其中的各种有效成分并加工成各种石化产品的过程。
炼油生产工艺是指在炼油厂内进行的一系列操作和流程,以产出高质量的石化产品。
首先,对原油进行初步处理。
原油经过去除水分和杂质后,进入到初步处理单元。
在这个单元里,原油将被加热到适宜的温度,然后进入第一个分离器中。
在分离器中,原油根据不同组分的沸点差异将分离成气态、液态和固态产品。
其次,进行常压蒸馏。
原油在分离器中得到了初步分离,但仍然含有多种组分。
在常压蒸馏塔中,原油会被加热到较高温度,使得不同组分产生沸腾。
然后,这些蒸汽会经过塔内装有一系列塔板的蒸馏塔,不同组分根据其沸点差异逐渐冷凝回液态,最终从塔顶部分离出来。
接着,进行减压蒸馏。
在常压蒸馏之后,还有一部分较重的组分没有被分离出来。
为了进一步提纯石化产品,需要进行减压蒸馏。
减压蒸馏是在较低压力下进行的,这样可以降低组分的沸点,使得更多的较重组分得以分离出来。
然后,进行催化裂化。
在催化裂化过程中,较重的原油组分会通过加热和催化剂的作用,发生分子断裂而转化为较轻的组分。
这个过程既可以产生一些高质量的汽油和柴油,也可以产生一些具有高增值和特殊用途的石化产品。
最后,进行产品加工和处理。
经过上述工艺后,炼油厂将获得不同种类和质量的石化产品。
这些产品需要进行进一步的加工和处理,以满足市场需求和质量要求。
例如,汽油需要进行除硫和加氢处理,而柴油需要进行脱硫和脱氮处理。
总之,炼油生产工艺是一个复杂的过程,包括原油初步处理、常压蒸馏、减压蒸馏、催化裂化以及产品加工和处理等环节。
通过这些工艺,炼油厂可以将原油转化为各种高质量的石化产品,满足人们对能源和化工产品的需求。
炼油工艺的发展概括
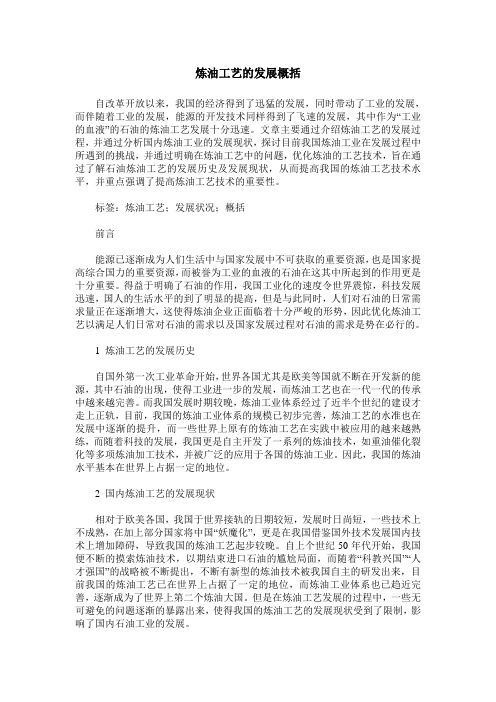
炼油工艺的发展概括自改革开放以来,我国的经济得到了迅猛的发展,同时带动了工业的发展,而伴随着工业的发展,能源的开发技术同样得到了飞速的发展,其中作为“工业的血液”的石油的炼油工艺发展十分迅速。
文章主要通过介绍炼油工艺的发展过程,并通过分析国内炼油工业的发展现状,探讨目前我国炼油工业在发展过程中所遇到的挑战,并通过明确在炼油工艺中的问题,优化炼油的工艺技术,旨在通过了解石油炼油工艺的发展历史及发展现状,从而提高我国的炼油工艺技术水平,并重点强调了提高炼油工艺技术的重要性。
标签:炼油工艺;发展状况;概括前言能源已逐渐成为人们生活中与国家发展中不可获取的重要资源,也是国家提高综合国力的重要资源,而被誉为工业的血液的石油在这其中所起到的作用更是十分重要。
得益于明确了石油的作用,我国工业化的速度令世界震惊,科技发展迅速,国人的生活水平的到了明显的提高,但是与此同时,人们对石油的日常需求量正在逐渐增大,这使得炼油企业正面临着十分严峻的形势,因此优化炼油工艺以满足人们日常对石油的需求以及国家发展过程对石油的需求是势在必行的。
1 炼油工艺的发展历史自国外第一次工业革命开始,世界各国尤其是欧美等国就不断在开发新的能源,其中石油的出现,使得工业进一步的发展,而炼油工艺也在一代一代的传承中越来越完善。
而我国发展时期较晚,炼油工业体系经过了近半个世纪的建设才走上正轨,目前,我国的炼油工业体系的规模已初步完善,炼油工艺的水准也在发展中逐渐的提升,而一些世界上原有的炼油工艺在实践中被应用的越来越熟练,而随着科技的发展,我国更是自主开发了一系列的炼油技术,如重油催化裂化等多项炼油加工技术,并被广泛的应用于各国的炼油工业。
因此,我国的炼油水平基本在世界上占据一定的地位。
2 国内炼油工艺的发展现状相对于欧美各国,我国于世界接轨的日期较短,发展时日尚短,一些技术上不成熟,在加上部分国家将中国“妖魔化”,更是在我国借鉴国外技术发展国内技术上增加障碍,导致我国的炼油工艺起步较晚。
我国炼油总工艺流程的发展模式

我国炼油总工艺流程的发展模式鞠林青炼油事业部摘要:本文分析了我国汽油、柴油标准的发展历程以及加工原油种类变化。
对加工低硫原油、含硫原油和高硫原油各种总工艺流程进行了总结,并提出了目前总流程制定中面临的问题和相应建议。
关键词:炼油总工艺流程产品标准发展1 前言炼油厂的总工艺流程是炼化企业的基础和核心,对全厂的技术先进性和经济合理性有着决定性作用,因此新建或改扩建炼油项目中都把全厂总工艺流程的制定和优化作为重点工作内容。
总工艺流程编制的依据主要是加工原油性质、产品种类和质量要求等。
上世纪八十年代以前,我国炼油厂加工规模和市场需求都较小,加工的原油主要是低硫的大庆原油和含硫的胜利原油,同时环境保护和产品质量要求也不很高,所以大多数炼厂的加工流程基本上为简单的常减压蒸馏+催化裂化模式,或者常减压蒸馏+催化裂化+延迟焦化模式,炼厂的复杂系数相对较低。
进入上世纪九十年代后,随着经济的快速发展,石油产品的需求量迅速增长,而受限于国内原油储量和产量的增幅有限,不得不从中东、非洲等地区进口各种类的原油,同时环境保护的要求日趋严格,要求生产过程的清洁化和石油产品的低硫化、优质化,在此形势下,各炼厂纷纷加大投资进行扩建或改造升级,选择合适的总工艺流程以适应原油变化和产品质量升级换代的要求。
2国内汽油和柴油质量变化历程2.1 汽油质量变化在2000年7月1日以前,我国的汽油生产基本上执行GB484标准,质量方面只限制了辛烷值、硫含量和铅含量,其它指标限制很少,一般催化裂化汽油脱臭后可直接生产成品汽油,这也间接促进了催化裂化技术的大发展。
1999年我国颁布了GB17930汽油标准,与标准GB484相比,硫含量从0.15%大幅降低到0.1%,铅含量降低至0.005g/L,实现了无铅化,并增加了烯烃、芳烃、苯等限制指标,是我国汽油质量与国际接轨的里程碑,2013年12月31日后硫含量将按50μg/g执行。
在催化裂化汽油依然是汽油池主要调和组分的情况下,围绕着降低汽油池中的烯烃和硫含量,从多方面做了突破性工作:优化总流程增加了调和组分的种类和数量;开发了降低烯烃和硫含量的催化裂化新工艺、新型催化剂;适时发展了催化原料预处理及产品后精制装置;优化相关工艺装置生产操作等。
- 1、下载文档前请自行甄别文档内容的完整性,平台不提供额外的编辑、内容补充、找答案等附加服务。
- 2、"仅部分预览"的文档,不可在线预览部分如存在完整性等问题,可反馈申请退款(可完整预览的文档不适用该条件!)。
- 3、如文档侵犯您的权益,请联系客服反馈,我们会尽快为您处理(人工客服工作时间:9:00-18:30)。
我国炼油总工艺流程的发展模式鞠林青炼油事业部摘要:本文分析了我国汽油、柴油标准的发展历程以及加工原油种类变化。
对加工低硫原油、含硫原油和高硫原油各种总工艺流程进行了总结,并提出了目前总流程制定中面临的问题和相应建议。
关键词:炼油总工艺流程产品标准发展1 前言炼油厂的总工艺流程是炼化企业的基础和核心,对全厂的技术先进性和经济合理性有着决定性作用,因此新建或改扩建炼油项目中都把全厂总工艺流程的制定和优化作为重点工作内容。
总工艺流程编制的依据主要是加工原油性质、产品种类和质量要求等。
上世纪八十年代以前,我国炼油厂加工规模和市场需求都较小,加工的原油主要是低硫的大庆原油和含硫的胜利原油,同时环境保护和产品质量要求也不很高,所以大多数炼厂的加工流程基本上为简单的常减压蒸馏+催化裂化模式,或者常减压蒸馏+催化裂化+延迟焦化模式,炼厂的复杂系数相对较低。
进入上世纪九十年代后,随着经济的快速发展,石油产品的需求量迅速增长,而受限于国内原油储量和产量的增幅有限,不得不从中东、非洲等地区进口各种类的原油,同时环境保护的要求日趋严格,要求生产过程的清洁化和石油产品的低硫化、优质化,在此形势下,各炼厂纷纷加大投资进行扩建或改造升级,选择合适的总工艺流程以适应原油变化和产品质量升级换代的要求。
2国内汽油和柴油质量变化历程2.1 汽油质量变化在2000年7月1日以前,我国的汽油生产基本上执行GB484标准,质量方面只限制了辛烷值、硫含量和铅含量,其它指标限制很少,一般催化裂化汽油脱臭后可直接生产成品汽油,这也间接促进了催化裂化技术的大发展。
1999年我国颁布了GB17930汽油标准,与标准GB484相比,硫含量从0.15%大幅降低到0.1%,铅含量降低至0.005g/L,实现了无铅化,并增加了烯烃、芳烃、苯等限制指标,是我国汽油质量与国际接轨的里程碑,2013年12月31日后硫含量将按50μg/g执行。
在催化裂化汽油依然是汽油池主要调和组分的情况下,围绕着降低汽油池中的烯烃和硫含量,从多方面做了突破性工作:优化总流程增加了调和组分的种类和数量;开发了降低烯烃和硫含量的催化裂化新工艺、新型催化剂;适时发展了催化原料预处理及产品后精制装置;优化相关工艺装置生产操作等。
表1 我国汽油质量主要指标的变化标准GB484-65 GB484-75/77GB484-89GB17930-1999GB17930-2006GB17930-2011RON //90/93/9790/93/95 90/93/97 90/93/97 MON 70/7670/75/80/85/ / / / 抗暴指数AKI / / 85/89/9285/88/9085/88/报告85/88/报告四乙基铅/(g·kg-1) 1.3/0.8 1.0/0.8/1.0/1./ / / /铅含量/(g·L-1) / /0.35/0.45/0.450.005 0.005 0.005w(S),%0.15 0.15 0.15 0.10 0.050.015/0.005φ(烯烃)/% / / / 35 35 30/28 φ(芳烃)/% / / / 40 40 40/40 φ(苯)/% / / / 2.5 2.51.0/1.02.2 柴油质量变化目前,我国柴油标准分为GB252普通柴油(原轻柴油)和GB19147车用柴油两类,最大区别是在硫含量、十六烷值、密度和多环芳烃限制上,其中车用柴油标准明确表示适用于压燃式柴油发动机汽车。
在2000年前制定的普通(轻)柴油标准中,柴油的十六烷值一般规定为50/45/43,硫含量0.2%,并特别注明了由中间基或环烷基原油生产或混有柴油馏分的各号轻柴油十六烷值允许不小于40,同时规定由含硫0.3%以上原油生产的轻柴油,含硫量允许不大于0.5%;由含硫0.5%以上原油生产的轻柴油,含硫量允许不大于1.0%,综合考虑了当时原油品种、炼油工业结构对柴油质量的影响。
2000和2011年制定的轻(普通)柴油标准,基本上沿袭了老标准的要求,重点限定了硫含量小于0.2%,以及2013年后小于0.035%,密度为实测值,同时依然规定由中间基或环烷基原油生产的柴油十六烷值或十六烷指数允许不小于40,有特殊要求者还可以由供需双方确定,充分考虑了催化柴油等二次加工柴油在我国柴油生产中依然占较大比重的特点,以及柴油消费中约50%为农业用以及其它用途的实际情况,有利于原油资源的充分利用。
表2 我国轻柴油质量主要指标的变化标准 GB252-64GB252-77GB252-81GB252-87GB252-94GB252-2000GB252-2011w (S),%0.20.2(0.5、1.00.2(0.5、1.0)0.2优级品/0.5一级品/1.0合格品0.2优级品/0.5一级品/1.0合格品0.20.2/0.035十六烷值 50/45/4350/45/4350/45/4345 45 45 45十六烷指数 / / / / / / 43 密度 实测 实测 实测 实测 实测 实测 实测随着汽车燃料柴油化和城市交通柴油使用数量的增加,我国相继制定了国标的车用柴油标准(见表3),北京、上海和广东也制定了各自的地方车用柴油标准,出现了和普通柴油共存的局面。
我国车用柴油的标准基本上保持与欧洲标准的一致性,稍微做了一些调整,如十六烷值最高为49等。
相比普通(轻)柴油,车用柴油极大地降低了硫含量,提高了十六烷值的要求,而且严格限制了密度和多环芳烃含量,相对间接的限制了催化柴油等大密度、高多环芳烃的二次加工柴油的掺入量;如要大量掺入,则必须切轻二次柴油的馏分,同时进行深度精制甚至改质裂化才可以达到要求。
在加氢精制(改质)生产低硫或超低硫柴油的过程中,作为天然润滑剂的硫被大量脱除后,其耐磨性能受到影响,要适量添加相应助剂。
表3 我国车用柴油质量主要指标变化标准 城市车用柴油Q/SHR008-200车用柴油GB/T19147-2003车用柴油*GB19147-2009w(S),% 0.03 0.05 0.035 十六烷值 50 49/46/45 49/46/45 十六烷指数 / 46/46/43 46/46/43密度(20℃)/ (kg·m-3) 实测 820~860/800~840810~850/790~840φ(多环芳烃)/%5(总芳25) / 11润滑性(HFRR 斑痕直径60℃)/ 460 460 /(μm)*:作为着火性能的十六烷值和十六烷指数,满足其中之一即可。
3 加工大庆类和胜利类原油的总工艺流程模式上世纪六十年代“五朵金花“为代表的炼油新技术成功开发并工业化,促进了我国炼油技术水平迈向了世界先进行列。
上世纪八十年代大庆全常压渣油催化裂化技术为代表的炼油技术实现了重油转化技术的突破,实现了大庆类原油最大化轻油收率和“吃光榨尽”的效益最大化加工模式;上世纪九十年代建成投产的250万吨/年加工胜利原油的福建炼厂,实现了我国炼油技术的综合集成、集中控制和工厂设计水平的新提升。
3.1 大庆类原油加工的总工艺流程低硫石蜡基的大庆原油金属和残炭等含量也较低,在上世纪九十年代前汽油和柴油产品质量、环境保护要求不太严的情况下,常压蒸馏+重油催化裂化模式的总流程被广泛采用。
其代表是大庆全常压渣油催化裂化技术于1985年在石家庄炼油厂60万吨/年装置上的成功运用,采用了新型的高效雾化喷嘴、提升管裂化技术、提升管末端快速分离技术、取热器等成套技术[1]。
表4列出了大庆原油和常压渣油的一般性质,图1显示了当时的大庆原油加工模式。
由大庆原油的常压渣油性质可以看出,其氢含量高达13.27%、硫仅有0.15%、残炭4.3%、金属Ni+V 4.4μg/g,是非常优质的裂化原料。
使用常压蒸馏+重油催化裂化的总流程,全厂流程简单,工艺装置配置少,汽油和柴油的轻油收率高,达到了原油最大程度的轻质化目标。
由于大庆原油蜡含量高、硫含量低的特点,直馏柴油直接去产品调和,催化汽油脱臭后基本上可直接生产90#汽油,大幅度提高了当时汽油池的整体辛烷值。
表4 大庆原油和常压渣油基本性质项目大庆原油大庆常压渣油密度(20℃)/0.8554 0.8959( g·cm-3)残炭/ %m 2.9 4.3元素分析w (C),%w (H),%w (S),%w (N),%85.57 13.73 0.10 0.16 86.32 13.27 0.15 0.20 金属/(μg ·g -1)NiV 3.1 0.04 4.3 <0.1图1 加工大庆类原油的总流程示意图3. 2 胜利类原油加工的总工艺流程上世纪九十年代建成的福建炼厂是设计加工胜利原油的典型燃料类炼油厂[2],常压和减压部分规模分别为250和90万吨/年,1992年9月投产了常减压、重油催化裂化等五套生产装置,1993年10月又后续投产催化重整、延迟焦化、MTBE 、加氢精制、气体分馏等其余五套生产装置,后期建设了聚丙烯装置。
表5列出了胜利原油和渣油的性质,表6列出了建厂初期的主要工艺装置,可以看出:与石蜡基的大庆原油相比,胜利原油属于中间基原油,密度大、残炭高、中等硫含量、金属Ni+V 含量也高,其常压渣油的硫含量、金属、残炭含量等已明显不能全部直接作为催化裂化进料。
在当时的条件下,加工胜利类原油采用常减压蒸馏+重油催化裂化+延迟焦化的模式,通过部分常渣进入减压蒸馏系统,减压渣油进延迟焦化加工,减压蜡油并掺常渣作为催化进料多产LPG 、汽油和柴油,以提高轻油收率和经济效益。
该总流程模式曾普遍应用在加工胜利类原油的沿海和沿江炼厂中。
表5 胜利原油和渣油性质项目胜利原油 常压渣油减压渣>350℃油>520℃ 馏分收率/%/ 75.18 50.62 密度(20℃)/(g ·c m -3)0.9005 0.948 0.9751 残炭/ %m6.4 8.47 12.57 元素分析w (C),%w (H),%w (S),%w (N),%86.26 12.20 0.80 0.41 85.39 11.59 1.07 0.696 85.5 11.12 1.33 0.954 金属/(μg ·g -1)NiV 26.0 1.0 40.06 2.18 59.49 3.24表6 福建炼油厂初期的主要工艺装置装置名称 规模,Mt/a 常减压蒸馏 2.5/0.9 催化裂化1.4 催化重整0.2 加氢精制0.5 延迟焦化 0.4图2 福建炼油厂初期总工艺流程示意图4 加工高硫劣质原油的总工艺流程自1993年我国成为原油净进口国以来,进口的数量持续增加,2010年达到了2.39亿吨,对外依存度为53.8%。