炼油工艺流程[1]
炼油工艺流程

第一章炼油工艺一工艺流程预榨毛油→澄油箱→油池→齿轮油泵→立式叶片过滤机→计量→齿轮油泵→炼油车间毛油暂存箱→齿轮油泵→炼油锅→间歇水化脱胶→沉淀→碱炼→沉淀→水洗→沉淀→齿轮油泵→干燥→脱色→脱色泵→立式叶片过滤机→脱色油→计量→入库浸出毛油→炼油车间毛油暂存箱→齿轮油泵→炼油锅→间歇水化脱胶→沉淀→碱炼→沉淀→水洗→沉淀→齿轮油泵→脱臭→干燥→脱色→脱色泵→立式叶片过滤机→脱色油→计量→入库二工艺描述预榨毛油经过澄油箱、立式叶片过滤机除杂后进入炼油车间毛油暂存箱;浸出毛油从汽提塔出来后经过计量打入炼油车间毛油暂存箱,待存够一定量后,泵入炼油锅,升温到一定温度(水化保持30摄氏度)进行碱炼前的脱胶,沉淀分离后升温70摄氏度,根据毛油质量(酸价、水分、含杂、色泽等)加碱进行碱炼,再沉淀分离后根据油质量,进行水洗1-2次,碱炼油沉淀分离后泵入脱色锅(浸出油脱臭后再泵入脱色锅)干燥后加入一定量的白土脱色,将油和白土的混合物利用脱色泵泵入过滤机后,过滤的合格油计量入库。
第二章操作一、毛油预处理工序操作(一)、毛油预处理工序的工艺指标1毛油含杂要求压榨后所得毛油经初步除渣后,还要进一步分离其中的渣,才能送往精炼车间精制。
毛油经过滤等方法预处理后,油中杂质应尽可能降低,一般要求分离后毛油(指清油)含杂量稳定在0.2%以下。
排出油渣(杂质)含油率应在40%以下。
(二)1、压滤机进行毛油预处理的工艺操作要点及注意事项(1)、滤油机工作以前,在滤油片之间要装上滤布,滤布用白帆布(20支纱5~8股),滤布裁制前用凉水浸泡收缩定型,晾干后裁制,开好输油孔,孔周边用线码好,两侧应比滤板外缘宽20mm。
装置滤布时,要安放平服,避免折皱,滤布多余之空间外塞入木棒将滤布向上提,使滤布拉平,然后旋动扳手(特制)将滤布压紧。
滤布要符合规格,装置平整,不能有折叠情况。
(2)、开始过滤时,打开每块滤板下部的出油旋塞(阀)。
在过滤之初,一般油液还是浑浊的,应该另行收集起来,重新过滤。
炼油工艺流程七大工艺

炼油工艺流程七大工艺一、工艺简介炼油工艺是指将原油转化为可用于工业和用户需求的石油产品的一系列工艺过程。
这些工艺包括石油加工、分离、转化和升质等环节,能够从原油中提取出各种重要的石油产品,如汽油、柴油、航空燃料、润滑油和石油化工原料等。
二、工艺流程炼油工艺流程主要包括以下七大工艺:1. 原油预处理工艺原油预处理是指对原油进行物理处理和化学处理,以去除其中的杂质和有害物质。
主要包括以下子工艺: - 原油预热和除水工艺 - 脱硫工艺 - 脱盐工艺2. 石脑油分离工艺石脑油是指石油中碳氢化合物链长的烃类物质,主要包括石脑油、汽油和柴油。
石脑油分离工艺是将原油中的石脑油分离出来,主要包括以下子工艺: - 原油蒸馏工艺 - 精馏工艺 - 精制工艺3. 裂化工艺裂化工艺是指将重质石油分子裂解为较轻质的石脑油和液化气的工艺。
主要包括以下子工艺: - 热裂化工艺(热解) - 催化裂化工艺(催化剂作用下的裂化)4. 加氢工艺加氢工艺是指将石脑油中的不饱和烃和硫化物通过与氢气反应进行饱和和脱硫的工艺。
主要包括以下子工艺: - 加氢脱硫工艺 - 加氢裂化工艺5. 碱洗工艺碱洗工艺是指将石脑油中的硫化物通过与碱溶液反应进行去除的工艺。
主要包括以下子工艺: - 酸性溶液处理 - 碱性溶液洗涤6. 重油加工工艺重油加工工艺是指将重质石脑油中的杂质和低质量成分去除,得到高质量的石油产品的工艺。
主要包括以下子工艺: - 渣油加工工艺 - 水洗工艺 - 渣油裂化工艺7. 产品处理工艺产品处理工艺是指对石油产品进行精制和改良,以满足特定要求的工艺。
主要包括以下子工艺: - 汽油处理工艺 - 柴油处理工艺 - 润滑油加工工艺三、工艺关联这七大工艺相互关联,形成炼油工艺的整体流程。
不同工艺之间的产品和中间产物可以相互利用,最大程度地提高石油资源的利用效率。
当原油经过这七大工艺流程后,得到的各种石油产品可以满足不同行业和用户的需求。
总结起来,炼油工艺流程的七大工艺——原油预处理工艺、石脑油分离工艺、裂化工艺、加氢工艺、碱洗工艺、重油加工工艺和产品处理工艺,共同构成了现代炼油工业的核心内容。
石油炼化常用的七种工艺流程

石油炼化七种工艺流程从原油到石油要经过多种工艺流程;不同的工艺流程会将同样的原料生产出不同的产品..从原油到石油的基本途径一般为:①将原油先按不同产品的沸点要求;分割成不同的直馏馏分油;然后按照产品的质量标准要求;除去这些馏分油中的非理想组分;②通过化学反应转化;生成所需要的组分;进而得到一系列合格的石油产品..石油炼化常用的工艺流程为常减压蒸馏、催化裂化、延迟焦化、加氢裂化、溶剂脱沥青、加氢精制、催化重整..一常减压蒸馏1.原料:原油等..2.产品:2.石脑油、粗柴油瓦斯油、渣油、沥青、减一线..3.基本概念:常减压蒸馏是常压蒸馏和减压蒸馏的合称;基本属物理过程:原料油在蒸馏塔里按蒸发能力分成沸点范围不同的油品称为馏分;这些油有的经调合、加添加剂后以产品形式出厂;相当大的部分是后续加工装置的原料..常减压蒸馏是炼油厂石油加工的第一道工序;称为原油的一次加工;包括三个工序:a.原油的脱盐、脱水;b.常压蒸馏;c.减压蒸馏..4.生产工艺:原油一般是带有盐份和水;能导致设备的腐蚀;因此原油在进入常减压之前首先进行脱盐脱水预处理;通常是加入破乳剂和水..原油经过流量计、换热部分、沏馏塔形成两部分;一部分形成塔顶油;经过冷却器、流量计;最后进入罐区;这一部分是化工轻油即所谓的石脑油;一部分形成塔底油;再经过换热部分;进入常压炉、常压塔;形成三部分;一部分柴油;一部分蜡油;一部分塔底油;剩余的塔底油在经过减压炉;减压塔;进一步加工;生成减一线、蜡油、渣油和沥青..各自的收率:石脑油轻汽油或化工轻油占1%左右;柴油占20%左右;蜡油占30%左右;渣油和沥青约占42%左右;减一线约占5%左右..常减压工序是不生产汽油产品的;其中蜡油和渣油进入催化裂化环节;生产汽油、柴油、煤油等成品油;石脑油直接出售由其他小企业生产溶剂油或者进入下一步的深加工;一般是催化重整生产溶剂油或提取萃类化合物;减一线可以直接进行调剂润滑油..5.生产设备:常减压装置是对原油进行一次加工的蒸馏装置;即将原油分馏成汽油、煤油、柴油、蜡油、渣油等组分的加工装置..原油蒸馏一般包括常压蒸馏和减压蒸馏两个部分..a.常压蒸馏塔所谓原油的常压蒸馏;即为原油在常压或稍高于常压下进行的蒸馏;所用的蒸馏设备叫做原油常压精馏塔或称常压塔..常压蒸馏剩下的重油组分分子量大、沸点高;且在高温下易分解;使馏出的产品变质并生产焦炭;破坏正常生产..因此;为了提取更多的轻质组分;往往通过降低蒸馏压力;使被蒸馏的原料油沸点范围降低..这一在减压下进行的蒸馏过程叫做减压蒸馏..b.减压蒸馏塔减压蒸馏是在压力低于100KPa的负压状态下进行的蒸馏过程..减压蒸馏的核心设备是减压塔和它的抽真空系统..减压塔的抽真空设备常用的是蒸汽喷射器也称蒸汽吸射泵或机械真空泵..其中机械真空泵只在一些干式减压蒸馏塔和小炼油厂的减压塔中采用;而广泛应用的是蒸汽喷射器..二催化裂化一般原油经过常减压蒸馏后可得到的汽油;煤油及柴油等轻质油品仅有10~40% ;其余的是重质馏分油和残渣油..如果想得到更多轻质油品;就必须对重质馏分和残渣油进行二次加工..催化裂化是最常用的生产汽油、柴油生产工序;汽油柴油主要是通过该工艺生产出来..这也是一般石油炼化企业最重要的生产的环节..1.原料:渣油和蜡油70%左右;催化裂化一般是以减压馏分油和焦化蜡油为原料;但是随着原油日益加重以及对轻质油越来越高的需求;大部分石炼化企业开始在原料中搀加减压渣油;甚至直接以常压渣油作为原料进行炼制..2.产品:汽油、柴油、油浆重质馏分油、液体丙烯、液化气;各自占比汽油占42%;柴油占21.5%;丙烯占5.8%;液化气占8%;油浆占12%..3.基本概念:催化裂化是在有催化剂存在的条件下;将重质油例如渣油加工成轻质油汽油、煤油、柴油的主要工艺;是炼油过程主要的二次加工手段..属于化学加工过程..4.生产工艺:常渣和腊油经过原料油缓冲罐进入提升管、沉降器、再生器形成油气;进入分馏塔..一部分油气进入粗汽油塔、吸收塔、空压机进入凝缩油罐;经过再吸收塔、稳定塔、最后进行汽油精制;生产出汽油..一部分油气经过分馏塔进入柴油汽提塔;然后进行柴油精制;生产出柴油..一部分油气经过分馏塔进入油浆循环;最后生产出油浆..一部分油气经分馏塔进入液态烃缓冲罐;经过脱硫吸附罐、砂滤塔、水洗罐、脱硫醇抽提塔、预碱洗罐、胺液回收器、脱硫抽提塔、缓冲塔;最后进入液态烃罐;形成液化气..一部分油气经过液态烃缓冲罐进入脱丙烷塔、回流塔、脱乙烷塔、精丙稀塔、回流罐;最后进入丙稀区球罐;形成液体丙稀..液体丙稀再经过聚丙稀车间的进一步加工生产出聚丙稀..5.生产设备:a.再生器再生器的主要作用是烧去结焦催化剂上的焦炭以恢复催化剂的活性;同时也提供裂化所需的热量..再生器由壳体、旋风分离器、空气分布器、辅组燃烧室和取热器组成b.提升管反应器直管式:多用于高低并列式反再系统;特点是从沉降器底部直接插入;结构简单;压降小..折叠式:多用于同轴式式反再系统..c.沉降器沉降器的作用是使来自提升管的反应油气和催化剂分离;油气经旋风分离器分出夹带催化剂后经集气室去分馏系统;由快速分离器出来的催化剂靠重力在沉降器中向下沉降;落入气体段..d.三机主风机:供给再生器烧焦用空气..气压机:用于给分馏系统来的富气升压;然后送往吸收稳定系统..增压机:供给Ⅳ型反应再生装置密相提升管调节催化剂循环量..e.三阀单动滑阀:在Ⅳ型催化裂化装置中;正常操作时全开;紧急情况下关闭;切断两器联系;防止催化剂倒流;在提升管催化裂化装置中调节两器催化剂循环量..双动滑阀:安装在再生器出口和放空烟囱之间;调节再生器的压力;保持两器压力平衡..塞阀:在同轴式催化裂化装置中调节催化剂的循环量..三延迟焦化焦炭化简称焦化是深度热裂化过程;也是处理渣油的手段之一..它又是唯一能生产石油焦的工艺过程;是任何其他过程所无法代替的..尤其是某些行业对优质石油焦的特殊需求;致使焦化过程在炼油工业中一直占据着重要地位..1.原料:延迟焦化与催化裂化类似的脱碳工艺以改变石油的碳氢比;延迟焦化的原料可以是重油、渣油甚至是沥青;对原料的品质要求比较低..渣油主要的转化工艺是延迟焦化和加氢裂化..2.产品:主要产品是蜡油、柴油、焦碳、粗汽油和部分气体;各自比重分别是:蜡油占23-33%;柴油22-29%;焦碳15-25%;粗汽油8-16%;气体7-10%;外甩油1-3%..3.基本概念焦化是以贫氢重质残油如减压渣油、裂化渣油以及沥青等为原料;在高温400~500℃下进行深度热裂化反应..通过裂解反应;使渣油的一部分转化为气体烃和轻质油品;由于缩合反应;使渣油的另一部分转化为焦炭..一方面由于原料重;含相当数量的芳烃;另一方面焦化的反应条件更加苛刻;因此缩合反应占很大比重;生成焦炭多..4.生产工艺延迟焦化装置的生产工艺分为焦化和除焦两部分;焦化为连续操作;除焦为间隙操作..由于工业装置一般设有两个或四个焦炭塔;所以整个生产过程仍为连续操作..a.原油预热;焦化原料减压渣油先进入原料缓冲罐;再用泵送入加热炉对流段升温至340~350 ℃ 左右..b.经预热后的原油进入分馏塔底;与焦炭塔产出的油气在分馏塔内塔底温度不超过400℃换热..c.原料油和循环油一起从分馏塔底抽出;用热油泵打进加热炉辐射段;加热到焦化反应所需的温度500 ℃ 左右;再通过四通阀由下部进入焦炭塔;进行焦化反应..d.原料在焦炭塔内反应生成焦炭聚积在焦炭塔内;油气从焦炭塔顶出来进入分馏塔;与原料油换热后;经过分馏得到气体、汽油、柴油和蜡油..塔底循环油和原料一起再进行焦化反应..5.生产设备a.焦炭塔焦炭塔是用厚锅炉钢板制成的空筒;是进行焦化反应的场所..b.水力除焦设备焦炭塔是轮换使用的;即当一个塔内焦炭聚结到一定高度时;通过四通阀将原料切换到另一个焦炭塔.聚结焦炭的焦炭塔先用蒸汽冷却;然后进行水力除焦..c. 无焰燃烧炉焦化加热炉是本装置的核心设备;其作用是将炉内迅速流动的渣油加热至500℃左右的高温..因此;要求炉内有较高的传热速率以保证在短时间内给油提供足够的热量;同时要求提供均匀的热场;防止局部过热引起炉管结焦..为此;延迟焦化通常采用无焰炉..四加氢裂化重油轻质化基本原理是改变油品的相对分子质量和氢碳比;而改变相对分子质量和氢碳比往往是同时进行的..改变油品的氢碳比有两条途径;一是脱碳;二是加氢..1.原料:1.重质油等2.产品:2.轻质油汽油、煤油、柴油或催化裂化、裂解制烯烃的原料3.基本概念加氢裂化属于石油加工过程的加氢路线;是在催化剂存在下从外界补入氢气以提高油品的氢碳比..加氢裂化实质上是加氢和催化裂化过程的有机结合;一方面能使重质油品通过裂化反应转化为汽油、煤油和柴油等轻质油品;另一方面又可防止像催化裂化那样生成大量焦炭;而且还可将原料中的硫、氯、氧化合物杂质通过加氢除去;使烯烃饱和..4.生产流程按反应器中催化剂所处的状态不同;可分为固定床、沸腾床和悬浮床等几种型式..1固定床加氢裂化固定床是指将颗粒状的催化剂放置在反应器内;形成静态催化剂床层..原料油和氢气经升温、升压达到反应条件后进入反应系统;先进行加氢精制以除去硫、氮、氧杂质和二烯烃;再进行加氢裂化反应..反应产物经降温、分离、降压和分馏后;目的产品送出装置;分离出含氢较高 80%;90%的气体;作为循环氢使用..未转化油称尾油可以部分循环、全部循环或不循环一次通过..2沸腾床加氢裂化沸腾床又称膨胀床工艺是借助于流体流速带动具有一定颗粒度的催化剂运动;形成气、液、固三相床层;从而使氢气、原料油和催化剂充分接触而完成加氢反应过程..沸腾床工艺可以处理金属含量和残炭值较高的原料如减压渣油.并可使重油深度转化;但反应温度较高;一般在400~450℃范围内..此种工艺比较复杂;国内尚未工业化..3悬浮床浆液床加氢工艺悬浮床工艺是为了适应非常劣质的原料而重新得到重视的一种加氢工艺..其原理与沸腾床相类似;其基本流程是以细粉状催化剂与原料预先混合;再与氢气一向进入反应器自下而上流动;催化剂悬浮于液相中;进行加氢裂化反应;催化剂随着反应产物一起从反应器顶部流出..该装置能加工各种重质原油和普通原油渣油;但装置投资大..该工艺目前在国内尚属研究开发阶段..5.生产设备加氢工艺生产装置的主要设备是在高温、高压及有氢气和硫化氢存在的条件下运行的;故其设计、制造和材料的选用等要求都很高;对生产操作的控制也极严格..高压加氢反应器是装置中的关键设备;工作条件苛刻;制造困难;价格昂贵..根据介质是否直接接触金属器壁;分为冷壁反应器和热壁反应器两种结构..反应器由筒体和内部结构两部分组成..a.加氢反应器筒体反应器筒体分为冷壁筒和热壁筒两种..b.加氢反应器内件加氢反应是在高温高压及有腐蚀介质H2、H2S的条件下操作;除了在材质上要注意防止氢腐蚀及其他介质的腐蚀以外;加氢反应器还应保证:反应物油气和氢在反应器中分布均匀;保证反应物与催化剂有良好的接触;及时排除反应热;避免反应温度过高和催化剂过热.以保证最佳反应条件和延长催化剂寿命;在反应物均匀分布的前提下;反应器内部的压力降不致过大;以减少循环压缩机的负荷;节省能源..为此;反应器内部需设置必要的内部构件;以达到气液均匀分布为主要目标..典型的反应器内构件包括:入口扩散器、气液分配盘、去垢篮筐、催化剂支持盘、急冷氢箱及再分配盘、出口集合器等..五溶剂脱沥青溶剂脱沥青是一个劣质渣油的预处理过程..用萃取的方法;从原油蒸馏所得的减压渣油有时也从常压渣油中;除去胶质和沥青;以制取脱沥青油同时生产石油沥青的一种石油产品精制过程..1.原料:1.减压渣油或者常压渣油等重质油2.产品:2.脱沥青油等3.基本概念溶剂脱沥青是加工重质油的一种石油炼制工艺;其过程是以减压渣油等重质油为原料;利用丙烷、丁烷等烃类作为溶剂进行萃取;萃取物即脱沥青油可做重质润滑油原料或裂化原料;萃余物脱油沥青可做道路沥青或其他用途..4.生产流程包括萃取和溶剂回收..萃取部分一般采取一段萃取流程;也可采取二段萃取流程..沥青与重脱沥青油溶液中含丙烷少;采用一次蒸发及汽提回收丙烷;轻脱沥青油溶液中含丙烷较多;采用多效蒸发及汽提或临界回收及汽提回收丙烷;以减少能耗..临界回收过程;是利用丙烷在接近临界温度和稍高于临界压力丙烷的临界温度96.8℃、临界压力4.2MPa的条件下;对油的溶解度接近于最小以及其密度也接近于最小的性质;使轻脱沥青油与大部分丙烷在临界塔内沉降、分离;从而避免了丙烷的蒸发冷凝过程;因而可较多地减少能耗..国内的溶剂脱沥青工艺流程主要有沉降法二段脱沥青工艺、临界回收脱沥青工艺、超临界抽提溶剂脱沥青工艺..1沉降法二段脱沥青工艺沉降法两段脱沥青是在常规一段脱沥青基础上发展起来的..在研究大庆减压渣油的特有性质的基础上;注意到常规的丙烷脱沥青不能充分利用好该资源;而开发出的一种新脱沥青工艺2临界回收脱沥青工艺溶剂对油的溶解能力随温度的升高而降低;当温度和压力接近到临界条件时;溶剂对油的溶解能力已降到很低;这时;该丙烷溶剂经冷却后可直接循环使用;不必经过蒸发回收..3超临界抽提溶剂脱沥青工艺超临界流体抽提是利用抽提体系在临界区附近具有反常的相平衡特性及异常的热力学性质;通过改变温度、压力等参数;使体系内组分间的相互溶解度发生剧烈变化;从而实现组分分离的技术5.生产设备a.抽提塔抽提塔的作用有:在渣油进口和主溶剂进口之间为抽提区;渣油进口以上部分为分馏区;主溶剂进口以下为沥青沉降区..b.溶剂临界/超临界回收塔脱沥青油溶液分离器又称为超临界塔或临界塔;它实际上是一个可在溶剂临界压力以上操作的液—液分离器;用以回收脱沥青油溶液中的溶剂..c.增压泵脱沥青油溶液增压泵是实现超临界溶剂回收工艺的关键设备;它需要具有1.5Mpa 以上的扬程;入口能承受高的压力和温度;泵的作用是能保证实现溶剂在系统内循环..六加氢精制加氢精制一般是指对某些不能满足使用要求的石油产品通过加氢工艺进行再加工;使之达到规定的性能指标..1.精制原料:含硫、氧、氮等有害杂质较多的汽油、柴油、煤油、润滑油、石油蜡等..2.精制产品:精制改质后的汽油、柴油、煤油、润滑油、石油蜡等产品..3.基本概念加氢精制工艺是各种油品在氢压力下进行催化改质的一个统称..它是指在一定的温度和压力、有催化剂和氢气存在的条件下;使油品中的各类非烃化合物发生氢解反应;进而从油品中脱除;以达到精制油品的目的..加氢精制主要用于油品的精制;其主要目的是通过精制来改善油品的使用性能..4.生产流程加氢精制的工艺流程一般包括反应系统、生成油换热、冷却、分离系统和循环氢系统三部分..a.反应系统原料油与新氢、循环氢混合;并与反应产物换热后;以气液混相状态进入加热炉这种方式称炉前混氢;加热至反应温度进入反应器..反应器进料可以是气相精制汽油时;也可以是气液混相精制柴油或比柴油更重的油品时..反应器内的催化剂一般是分层填装;以利于注冷氢来控制反应温度..循环氢与油料混合物通过每段催化剂床层进行加氢反应..b.生成油换热、冷却、分离系统反应产物从反应器的底部出来;经过换热、冷却后;进入高压分离器..在冷却器前要向产物中注入高压洗涤水;以溶解反应生成的氨和部分硫化氢..反应产物在高压分离器中进行油气分离;分出的气体是循环氢;其中除了主要成分氢外;还有少量的气态烃不凝气和未溶于水的硫化氢;分出的液体产物是加氢生成油;其中也溶解有少量的气态烃和硫化氢;生成油经过减压再进入低压分离器进一步分离出气态烃等组分;产品去分馏系统分离成合格产品..c.循环氢系统从高压分离器分出的循环氢经储罐及循环氢压缩机后;小部分约30%直接进入反应器作冷氢;其余大部分送去与原料油混合;在装置中循环使用..为了保证循环氢的纯度;避免硫化氢在系统中积累;常用硫化氢回收系统..一般用乙醇胺吸收除去硫化氢;富液吸收液再生循环使用;解吸出来的硫化氢送到制硫装置回收硫磺;净化后的氢气循环使用..5.生产设备a.加热炉原料油与新氢、循环氢混合;并与反应产物换热后;以气液混相状态进入加热炉加热至反应温度进入反应器..b.反应器换热、炉后混氢进入反应器..在反应器催化剂床层反应;硫、氧、氮和金属化合物等即变为易于除掉的物质通过加氢变为硫化氢、水及氨等;烯烃同时被饱和..c.高压低压分离器加氢生成油经过换热和水冷后依次进入高压;低压分离器..d. 汽提塔从低压分离器来的加氢生成油与汽提过的加氢生成油换热;并进入加热炉加热;然后进入汽提塔;其作用是把残留在油中的气体及轻馏分汽提掉..汽提塔底出来的生成油经过换热和水冷却后;为加氢精制产品..七催化重整1.主要原料:石脑油轻汽油、化工轻油、稳定轻油;其一般在炼油厂进行生产;有时在采油厂的稳定站也能产出该项产品..质量好的石脑油含硫低;颜色接近于无色..2.主要产品:高辛烷值的汽油、苯、甲苯、二甲苯等产品这些产品是生产合成塑料、合成橡胶、合成纤维等的主要原料、还有大量副产品氢气..3.基本概念重整:烃类分子重新排列成新的分子结构..催化重整装置:用直馏汽油即石脑油或二次加工汽油的混合油作原料;在催化剂铂或多金属的作用下;经过脱氢环化、加氢裂化和异构化等反应;使烃类分子重新排列成新的分子结构;以生产C6~C9芳烃产品或高辛烷值汽油为主要目的;并利用重整副产氢气供二次加工的热裂化、延迟焦化的汽油或柴油加氢精制..4.生产流程根据催化重整的基本原理;一套完整的重整工业装置大都包括原料预处理和催化重整两部分..以生产芳烃为目的的重整装置还包括芳烃抽提和芳烃精馏两部分..a.原料预处理将原料切割成适合重整要求的馏程范围和脱去对催化剂有害的杂质..预处理包括:预脱砷、预分馏、预加氢三部分..b.催化重整催化重整是将预处理后的精制油采用多金属铂铼、铂铱、铂锡催化剂在一定的温度、压力条件下;将原料油分子进行重新排列;产生环烷脱氢、芳构化、异构化等主要反应;以增产芳烃或提高汽油辛烷值为目的..工业重整装置广泛采用的反应系统流程可分为两大类:固定床反应器半再生式工艺流程和移动床反应器连续再生式工艺流程..。
炼油的工艺流程

炼油的工艺流程
炼油工艺流程是将原油转化为成品油的过程,它包括物理和化学两个方面的过程。
整个工艺流程可以分为以下几个步骤:
1. 原油处理:原油从地下储层抽出后,需要通过一系列的物理和化学处理来去除其中的杂质,包括水、盐等。
不同种类的原油需要采用不同的处理方法。
例如,重质原油需要经过重油加工,可以将其中的钾、镁等金属离子去除。
2. 蒸馏分离:在这一步骤中,将经过处理的原油通过加热,将其分离成不同的沸点段。
这些沸点段可分为石蜡、煤油、汽油、液化石油气(LPG)和重柴油等。
不同种类的油品需要在不同的温度下进行加热。
3. 裂化:在一些炼油场,通过裂化技术可以将某些较重的油品转化为较轻的油品,例如将重柴油裂化成汽油。
这一步骤通常需要采用催化剂,以及适当的温度和压力。
4. 加氢处理:在这一步骤中,对某些重型的油品进行加氢处理。
在加氢反应中,将氢气加入油品中,并通过催化剂的作用将其中的杂质去除,以改善成品的质量。
5. 废弃物处理:在整个流程中,还会产生大量的废弃物,包括硫、氮化合物、CO2等。
这些废弃物需要通过各种化学或物理方法去处理,以避免对环境造成污染。
总的来说,炼油的工艺流程十分复杂,需要经过多个步骤的处理过程,而不同种类的原油也需要采用不同的处理方法。
随着科技的不断发展,炼油工艺也不断完善和改进,以提高成品的质量,同时尽可能减少对环境造成的影响。
炼油工艺流程

炼油工艺流程炼油工艺流程是指将原油转化为各种石油产品的过程。
炼油工艺流程主要包括原油分离、加热裂化、重整、深度加工和产品分离等步骤。
下面将详细介绍一下这些步骤。
原油分离是炼油工艺流程的第一步。
原油是由多种不同碳链长度和分子结构的烃类组成的混合物。
在原油分离过程中,原油首先经过预加热器进行加热,然后进入蒸馏塔。
在蒸馏塔中,原油在不同温度下通过多级分馏,根据烃类的沸点差异,将原油分为不同馏分,如轻质石油气、汽油、柴油和煤油等。
加热裂化是炼油工艺流程的第二步。
加热裂化是利用高温和催化剂将长链烃裂解为短链烃的过程。
加热裂化主要用于生产高辛烷值的汽油。
在加热裂化过程中,原油首先被预加热至适宜温度,然后进入加热裂化器。
在加热裂化器中,原油与催化剂接触并加热,长链烃发生裂解,产生大量的短链烃和烯烃。
然后,裂解产物经过冷却和分馏,从中分离得到汽油、饱和烃和馏分油等。
重整是炼油工艺流程的第三步。
重整是将低辛烷值的烃通过催化剂的作用,重新排列分子结构,得到高辛烷值的汽油的过程。
在重整过程中,原油经过热解和转化反应,得到辛烷值较高的重整汽油。
深度加工是炼油工艺流程的第四步。
深度加工是对各种馏分油进行进一步的加工和处理,以满足市场需求。
深度加工的主要过程包括脱硫、脱氮、脱沥青和脱蜡等。
这些过程主要通过化学反应和物理分离来实现。
产品分离是炼油工艺流程的最后一步。
产品分离是将深度加工后的原油得到不同的石油产品的过程。
产品分离主要通过精馏塔和萃取等方法来实现。
精馏塔是一种设备,可以根据石油产品的沸点差异,将其分离为不同的馏分油。
萃取是一种利用溶剂或萃取剂将原油中的特定成分提取出来的方法,用于生产高附加值的石油产品。
综上所述,炼油工艺流程是将原油转化为各种石油产品的过程,包括原油分离、加热裂化、重整、深度加工和产品分离等步骤。
这些步骤相互关联、相互作用,通过不同的化学、物理过程,实现了原油加工和转化,从而得到了丰富的石油产品,满足了市场需求。
炼油厂整个炼油的工艺流程

炼油厂整个炼油的工艺流程1.延迟焦化工艺流程:本装置的原料为温度90℃的减压渣油,由罐区泵送入装置原料油缓冲罐,然后由原料泵输送至柴油原料油换热器,加热到135℃左右进入蜡油原料油换热器,加热至160℃左右进入焦化炉对流段,加热至305℃进入焦化分馏塔脱过热段,在此与来自焦炭塔顶的热油气接触换热。
原料油与来自焦炭塔油气中被凝的循环油一起流入塔底,在380~390℃温度下,用辐射泵抽出打入焦化炉辐射段,快速升温至495~500℃,经四通阀进入焦碳塔底部。
循环油和减压渣油中蜡油以上馏分在焦碳塔内由于高温和长时间停留而发生解、缩合等一系列的焦化反应,反应的高温油气自塔顶流出进入分馏塔下部与原料油直接换热后,冷凝出循环油馏份;其余大量油气上升经五层分馏洗涤板,在控制蜡油集油箱下蒸发段温度的条件下,上升进入集油箱以上分馏段,进行分馏。
从下往上分馏出蜡油、柴油、石脑油和富气。
分馏塔蜡油集油箱的蜡油在343℃温度下,自流至蜡油汽提塔,经过热蒸汽汽提后蜡油自蜡油泵抽出,去吸收稳定为稳定塔重沸器提供热源后降温至258℃左右,再为解吸塔重沸器提供热源后降温至242℃左右,进入蜡油原料油换热器与原料油换热,蜡油温度降至210℃,后分成三部分:一部分分两路作为蜡油回流返回分馏塔,一路作为下回流控制分馏塔蒸发段温度和循环比,一路作为上回流取中段热;一部分回焦化炉对流段入口以平衡大循环比条件下的对流段热负荷及对流出口温度;另一部分进水箱式蜡油冷却器降温至90℃,一路作为急冷油控制焦炭塔油气线温度,少量蜡油作为产品出装置。
柴油自分馏塔由柴油泵抽出,仅柴油原料油换热器、柴油富吸收油换热器后一部分返回分馏塔作柴油回流,另一部分去柴油空冷器冷却至55℃后,再去柴油水冷器冷却至40℃后分两路:一路出装置;另一路去吸收稳定单元的再吸收塔作吸收剂。
由吸收稳定单元返回的富吸收油经柴油富吸收油换热器换热后也返回分馏塔。
分馏塔顶油气经分馏塔顶空冷器,分馏塔顶水冷器冷却到40℃,流入分馏塔顶气液分离罐,焦化石脑油由石脑油泵抽出送往吸收稳定单元。
炼油工艺流程

延迟焦化工艺流程简单、原料适应性强、 技术成熟可靠、投资和操作费用较低等特点, 在70多年的历程中得到了迅速发展, 已成为世 界各国炼油业渣油转化的重要手段。据统计, 10年来新增的焦化能力占到了新增渣油加工能 力的22%以上。
单套装置最大加工规模已发展到673万 吨/年。延迟焦化技术已成为加工中东高硫原 油的重要手段之一。
炼油工艺流程
前言
大庆石化分公司炼油厂隶属于中国石油天然气股份有限公司, 国家大Ⅰ型 企业。原油年加工能力650万吨, 润滑油年生产能力25万吨, 生产汽油、柴油、煤 油、润滑油、石蜡、苯类、石油焦等六大类18个品种32个牌号的石油化工产品 。
一、炼油流程 二、炼油产品性能、用途及注意事项 三、炼油的发展趋势 四、大庆石化分公司炼油厂存在的问题
稳定 系统
液化气 汽油
分馏 系统
柴油去加氢精制 油浆(焦化)
催化裂化是目前我国最重要的二次加工工艺, 肩负着我国80%以上汽油与30%以上柴油的生产任务。 这是由我国原油重质馏分多的特点决定的。大于350℃馏分占
60%-70%以上 重油催化装置的原料主要由蜡油和渣油组成。 其中: 渣油全部来自于常减压装置 混合蜡油包括焦化蜡油;减五线油;减四线油;减三线油;减
炼厂数
美国 132
中国
95
俄罗斯 42
日本
33
韩国
6
委内瑞拉 5
原油 催化裂化
Mt/a Mt/a
834.91 281.89
289.51 102.8
271.77 16.54
235.15
43.8
127.20
8.94
64.11 11.59
石油炼制工艺流程
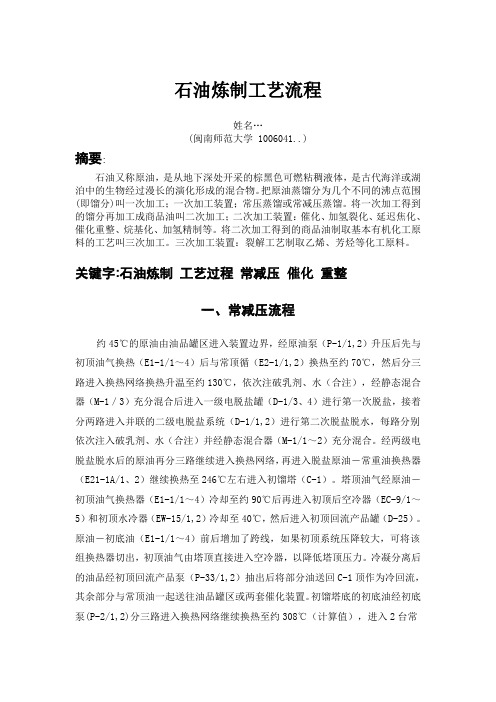
石油炼制工艺流程姓名…(闽南师范大学 1006041..)摘要:石油又称原油,是从地下深处开采的棕黑色可燃粘稠液体,是古代海洋或湖泊中的生物经过漫长的演化形成的混合物。
把原油蒸馏分为几个不同的沸点范围(即馏分)叫一次加工;一次加工装置;常压蒸馏或常减压蒸馏。
将一次加工得到的馏分再加工成商品油叫二次加工;二次加工装置:催化、加氢裂化、延迟焦化、催化重整、烷基化、加氢精制等。
将二次加工得到的商品油制取基本有机化工原料的工艺叫三次加工。
三次加工装置:裂解工艺制取乙烯、芳烃等化工原料。
关键字:石油炼制工艺过程常减压催化重整一、常减压流程约45℃的原油由油品罐区进入装置边界,经原油泵(P-1/1,2)升压后先与初顶油气换热(E1-1/1~4)后与常顶循(E2-1/1,2)换热至约70℃,然后分三路进入换热网络换热升温至约130℃,依次注破乳剂、水(合注),经静态混合器(M-1/3)充分混合后进入一级电脱盐罐(D-1/3、4)进行第一次脱盐,接着分两路进入并联的二级电脱盐系统(D-1/1,2)进行第二次脱盐脱水,每路分别依次注入破乳剂、水(合注)并经静态混合器(M-1/1~2)充分混合。
经两级电脱盐脱水后的原油再分三路继续进入换热网络,再进入脱盐原油-常重油换热器(E21-1A/1、2)继续换热至246℃左右进入初馏塔(C-1)。
塔顶油气经原油-初顶油气换热器(E1-1/1~4)冷却至约90℃后再进入初顶后空冷器(EC-9/1~5)和初顶水冷器(EW-15/1,2)冷却至40℃,然后进入初顶回流产品罐(D-25)。
原油-初底油(E1-1/1~4)前后增加了跨线,如果初顶系统压降较大,可将该组换热器切出,初顶油气由塔顶直接进入空冷器,以降低塔顶压力。
冷凝分离后的油品经初顶回流产品泵(P-33/1,2)抽出后将部分油送回C-1顶作为冷回流,其余部分与常顶油一起送往油品罐区或两套催化装置。
初馏塔底的初底油经初底泵(P-2/1,2)分三路进入换热网络继续换热至约308℃(计算值),进入2台常压炉加热至363℃到常压塔(C-2)进行分馏。
炼油工艺流程介绍
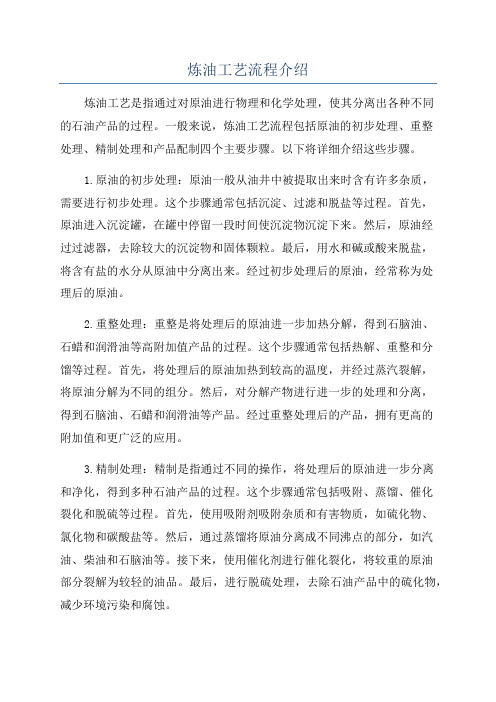
炼油工艺流程介绍炼油工艺是指通过对原油进行物理和化学处理,使其分离出各种不同的石油产品的过程。
一般来说,炼油工艺流程包括原油的初步处理、重整处理、精制处理和产品配制四个主要步骤。
以下将详细介绍这些步骤。
1.原油的初步处理:原油一般从油井中被提取出来时含有许多杂质,需要进行初步处理。
这个步骤通常包括沉淀、过滤和脱盐等过程。
首先,原油进入沉淀罐,在罐中停留一段时间使沉淀物沉淀下来。
然后,原油经过过滤器,去除较大的沉淀物和固体颗粒。
最后,用水和碱或酸来脱盐,将含有盐的水分从原油中分离出来。
经过初步处理后的原油,经常称为处理后的原油。
2.重整处理:重整是将处理后的原油进一步加热分解,得到石脑油、石蜡和润滑油等高附加值产品的过程。
这个步骤通常包括热解、重整和分馏等过程。
首先,将处理后的原油加热到较高的温度,并经过蒸汽裂解,将原油分解为不同的组分。
然后,对分解产物进行进一步的处理和分离,得到石脑油、石蜡和润滑油等产品。
经过重整处理后的产品,拥有更高的附加值和更广泛的应用。
3.精制处理:精制是指通过不同的操作,将处理后的原油进一步分离和净化,得到多种石油产品的过程。
这个步骤通常包括吸附、蒸馏、催化裂化和脱硫等过程。
首先,使用吸附剂吸附杂质和有害物质,如硫化物、氯化物和碳酸盐等。
然后,通过蒸馏将原油分离成不同沸点的部分,如汽油、柴油和石脑油等。
接下来,使用催化剂进行催化裂化,将较重的原油部分裂解为较轻的油品。
最后,进行脱硫处理,去除石油产品中的硫化物,减少环境污染和腐蚀。
4.产品配制:最后一个步骤是根据市场需求,将不同的石油产品混合和调整,得到符合要求的产品。
这个步骤通常包括混合、加氢处理和添加剂掺入等过程。
首先,将不同种类和质量的石油产品混合在一起,得到所需的产品性能。
然后,对产品进行加氢处理,以改善其性能和稳定性。
最后,添加剂如防腐剂、抗氧化剂和增稠剂等可根据需要掺入产品中,以改善其质量和效果。
以上是炼油工艺流程的基本介绍。
炼油工艺流程
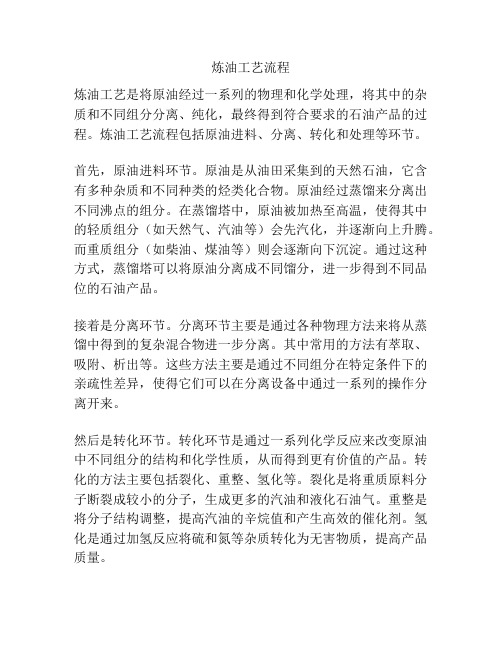
炼油工艺流程炼油工艺是将原油经过一系列的物理和化学处理,将其中的杂质和不同组分分离、纯化,最终得到符合要求的石油产品的过程。
炼油工艺流程包括原油进料、分离、转化和处理等环节。
首先,原油进料环节。
原油是从油田采集到的天然石油,它含有多种杂质和不同种类的烃类化合物。
原油经过蒸馏来分离出不同沸点的组分。
在蒸馏塔中,原油被加热至高温,使得其中的轻质组分(如天然气、汽油等)会先汽化,并逐渐向上升腾。
而重质组分(如柴油、煤油等)则会逐渐向下沉淀。
通过这种方式,蒸馏塔可以将原油分离成不同馏分,进一步得到不同品位的石油产品。
接着是分离环节。
分离环节主要是通过各种物理方法来将从蒸馏中得到的复杂混合物进一步分离。
其中常用的方法有萃取、吸附、析出等。
这些方法主要是通过不同组分在特定条件下的亲疏性差异,使得它们可以在分离设备中通过一系列的操作分离开来。
然后是转化环节。
转化环节是通过一系列化学反应来改变原油中不同组分的结构和化学性质,从而得到更有价值的产品。
转化的方法主要包括裂化、重整、氢化等。
裂化是将重质原料分子断裂成较小的分子,生成更多的汽油和液化石油气。
重整是将分子结构调整,提高汽油的辛烷值和产生高效的催化剂。
氢化是通过加氢反应将硫和氮等杂质转化为无害物质,提高产品质量。
最后是处理环节。
处理环节主要是对炼油过程中产生的废料和排放物进行处理和回收。
例如,对于废催化剂和含硫污水,可以采用煅烧和脱硫等方法进行处理,从而减少对环境的污染。
同时,对于产生的废气,可以采用脱硫、脱硝等方法进行处理,使得废气达到排放标准。
总结起来,炼油工艺流程是一个复杂的系统工程,包括原油进料、分离、转化和处理等多个环节。
通过对原油进行分离,进一步对各组分进行转化和处理,最终得到符合要求的各种石油产品。
这些产品在能源、化工等领域具有重要的应用价值。
同时,在炼油过程中,为减少对环境的污染,对废料和废气的处理也是必不可少的环节。
通过科学的工艺流程和先进的设备,炼油工艺可以高效、稳定地进行,满足人们对石油产品的需求,同时减少对环境的负面影响。
炼油工艺流程七大工艺
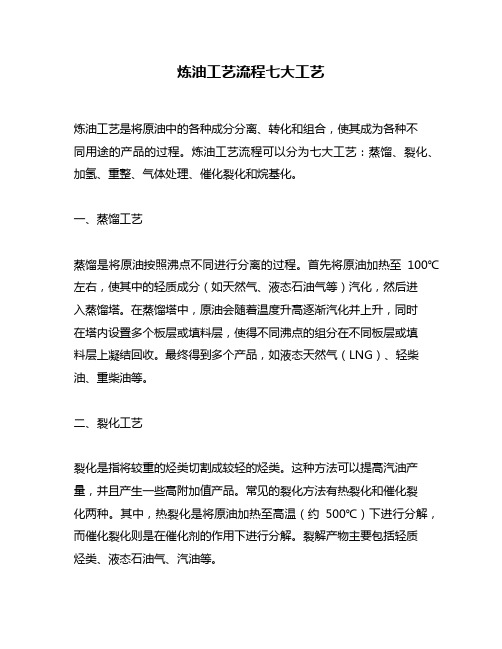
炼油工艺流程七大工艺炼油工艺是将原油中的各种成分分离、转化和组合,使其成为各种不同用途的产品的过程。
炼油工艺流程可以分为七大工艺:蒸馏、裂化、加氢、重整、气体处理、催化裂化和烷基化。
一、蒸馏工艺蒸馏是将原油按照沸点不同进行分离的过程。
首先将原油加热至100℃左右,使其中的轻质成分(如天然气、液态石油气等)汽化,然后进入蒸馏塔。
在蒸馏塔中,原油会随着温度升高逐渐汽化并上升,同时在塔内设置多个板层或填料层,使得不同沸点的组分在不同板层或填料层上凝结回收。
最终得到多个产品,如液态天然气(LNG)、轻柴油、重柴油等。
二、裂化工艺裂化是指将较重的烃类切割成较轻的烃类。
这种方法可以提高汽油产量,并且产生一些高附加值产品。
常见的裂化方法有热裂化和催化裂化两种。
其中,热裂化是将原油加热至高温(约500℃)下进行分解,而催化裂化则是在催化剂的作用下进行分解。
裂解产物主要包括轻质烃类、液态石油气、汽油等。
三、加氢工艺加氢是指将原油中的不饱和烃类与氢气反应,使其成为饱和烃类的过程。
这种方法可以改善产品的质量,如提高汽油辛烷值、减少硫含量等。
加氢反应通常在高压下(10-20MPa)进行,同时需要使用催化剂来促进反应。
加氢产物主要包括柴油、液态石油气等。
四、重整工艺重整是指将低辛烷值的轻馏分通过催化剂处理成为高辛烷值的汽油的过程。
重整反应需要在高温(400℃左右)和高压(2-3MPa)下进行,并且需要使用铂族金属作为催化剂。
重整产物主要包括高辛烷值汽油。
五、气体处理工艺气体处理是指将原油中的气态成分(如天然气、液态石油气等)进行分离和净化的过程。
这种方法可以提高天然气和石油气的纯度,同时去除其中的杂质和有害物质。
常见的处理方法包括吸附、膜分离、冷却液化等。
六、催化裂化工艺催化裂化是一种针对重质原油进行加工处理的方法,可以将较重的烃类切割成较轻的烃类。
这种方法需要使用催化剂来促进反应,通常在高温(500℃左右)和高压(0.1-0.5MPa)下进行。
石油炼化常用的七种工艺流程
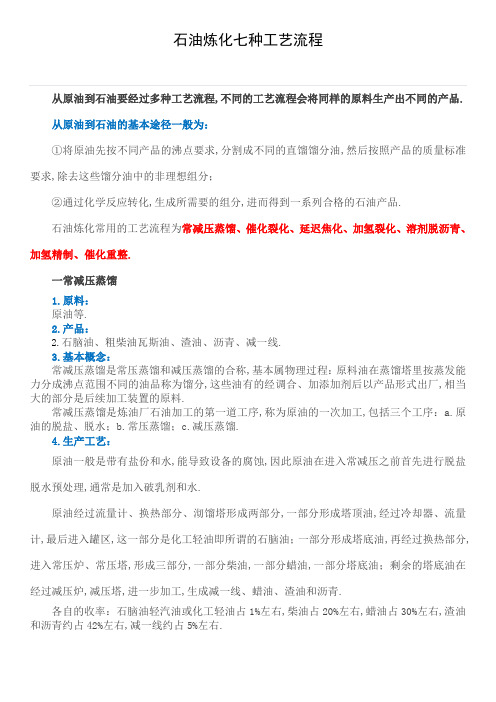
石油炼化七种工艺流程从原油到石油要经过多种工艺流程,不同的工艺流程会将同样的原料生产出不同的产品.从原油到石油的基本途径一般为:①将原油先按不同产品的沸点要求,分割成不同的直馏馏分油,然后按照产品的质量标准要求,除去这些馏分油中的非理想组分;②通过化学反应转化,生成所需要的组分,进而得到一系列合格的石油产品.石油炼化常用的工艺流程为常减压蒸馏、催化裂化、延迟焦化、加氢裂化、溶剂脱沥青、加氢精制、催化重整.一常减压蒸馏1.原料:原油等.2.产品:2.石脑油、粗柴油瓦斯油、渣油、沥青、减一线.3.基本概念:常减压蒸馏是常压蒸馏和减压蒸馏的合称,基本属物理过程:原料油在蒸馏塔里按蒸发能力分成沸点范围不同的油品称为馏分,这些油有的经调合、加添加剂后以产品形式出厂,相当大的部分是后续加工装置的原料.常减压蒸馏是炼油厂石油加工的第一道工序,称为原油的一次加工,包括三个工序:a.原油的脱盐、脱水;b.常压蒸馏;c.减压蒸馏.4.生产工艺:原油一般是带有盐份和水,能导致设备的腐蚀,因此原油在进入常减压之前首先进行脱盐脱水预处理,通常是加入破乳剂和水.原油经过流量计、换热部分、沏馏塔形成两部分,一部分形成塔顶油,经过冷却器、流量计,最后进入罐区,这一部分是化工轻油即所谓的石脑油;一部分形成塔底油,再经过换热部分,进入常压炉、常压塔,形成三部分,一部分柴油,一部分蜡油,一部分塔底油;剩余的塔底油在经过减压炉,减压塔,进一步加工,生成减一线、蜡油、渣油和沥青.各自的收率:石脑油轻汽油或化工轻油占1%左右,柴油占20%左右,蜡油占30%左右,渣油和沥青约占42%左右,减一线约占5%左右.常减压工序是不生产汽油产品的,其中蜡油和渣油进入催化裂化环节,生产汽油、柴油、煤油等成品油;石脑油直接出售由其他小企业生产溶剂油或者进入下一步的深加工,一般是催化重整生产溶剂油或提取萃类化合物;减一线可以直接进行调剂润滑油.5.生产设备:常减压装置是对原油进行一次加工的蒸馏装置,即将原油分馏成汽油、煤油、柴油、蜡油、渣油等组分的加工装置.原油蒸馏一般包括常压蒸馏和减压蒸馏两个部分.a.常压蒸馏塔所谓原油的常压蒸馏,即为原油在常压或稍高于常压下进行的蒸馏,所用的蒸馏设备叫做原油常压精馏塔或称常压塔.常压蒸馏剩下的重油组分分子量大、沸点高,且在高温下易分解,使馏出的产品变质并生产焦炭,破坏正常生产.因此,为了提取更多的轻质组分,往往通过降低蒸馏压力,使被蒸馏的原料油沸点范围降低.这一在减压下进行的蒸馏过程叫做减压蒸馏.b.减压蒸馏塔减压蒸馏是在压力低于100KPa的负压状态下进行的蒸馏过程.减压蒸馏的核心设备是减压塔和它的抽真空系统.减压塔的抽真空设备常用的是蒸汽喷射器也称蒸汽吸射泵或机械真空泵.其中机械真空泵只在一些干式减压蒸馏塔和小炼油厂的减压塔中采用,而广泛应用的是蒸汽喷射器.二催化裂化一般原油经过常减压蒸馏后可得到的汽油,煤油及柴油等轻质油品仅有10~40% ,其余的是重质馏分油和残渣油.如果想得到更多轻质油品,就必须对重质馏分和残渣油进行二次加工.催化裂化是最常用的生产汽油、柴油生产工序,汽油柴油主要是通过该工艺生产出来.这也是一般石油炼化企业最重要的生产的环节.1.原料:渣油和蜡油70%左右,催化裂化一般是以减压馏分油和焦化蜡油为原料,但是随着原油日益加重以及对轻质油越来越高的需求,大部分石炼化企业开始在原料中搀加减压渣油,甚至直接以常压渣油作为原料进行炼制.2.产品:汽油、柴油、油浆重质馏分油、液体丙烯、液化气;各自占比汽油占42%,柴油占%,丙烯占%,液化气占8%,油浆占12%.3.基本概念:催化裂化是在有催化剂存在的条件下,将重质油例如渣油加工成轻质油汽油、煤油、柴油的主要工艺,是炼油过程主要的二次加工手段.属于化学加工过程.4.生产工艺:常渣和腊油经过原料油缓冲罐进入提升管、沉降器、再生器形成油气,进入分馏塔.一部分油气进入粗汽油塔、吸收塔、空压机进入凝缩油罐,经过再吸收塔、稳定塔、最后进行汽油精制,生产出汽油.一部分油气经过分馏塔进入柴油汽提塔,然后进行柴油精制,生产出柴油.一部分油气经过分馏塔进入油浆循环,最后生产出油浆.一部分油气经分馏塔进入液态烃缓冲罐,经过脱硫吸附罐、砂滤塔、水洗罐、脱硫醇抽提塔、预碱洗罐、胺液回收器、脱硫抽提塔、缓冲塔,最后进入液态烃罐,形成液化气.一部分油气经过液态烃缓冲罐进入脱丙烷塔、回流塔、脱乙烷塔、精丙稀塔、回流罐,最后进入丙稀区球罐,形成液体丙稀.液体丙稀再经过聚丙稀车间的进一步加工生产出聚丙稀.5.生产设备:a.再生器再生器的主要作用是烧去结焦催化剂上的焦炭以恢复催化剂的活性,同时也提供裂化所需的热量.再生器由壳体、旋风分离器、空气分布器、辅组燃烧室和取热器组成b.提升管反应器直管式:多用于高低并列式反再系统,特点是从沉降器底部直接插入,结构简单,压降小.折叠式:多用于同轴式式反再系统.c.沉降器沉降器的作用是使来自提升管的反应油气和催化剂分离,油气经旋风分离器分出夹带催化剂后经集气室去分馏系统;由快速分离器出来的催化剂靠重力在沉降器中向下沉降,落入气体段.d.三机主风机:供给再生器烧焦用空气.气压机:用于给分馏系统来的富气升压,然后送往吸收稳定系统.增压机:供给Ⅳ型反应再生装置密相提升管调节催化剂循环量.e.三阀单动滑阀:在Ⅳ型催化裂化装置中,正常操作时全开,紧急情况下关闭,切断两器联系,防止催化剂倒流;在提升管催化裂化装置中调节两器催化剂循环量.双动滑阀:安装在再生器出口和放空烟囱之间,调节再生器的压力,保持两器压力平衡.塞阀:在同轴式催化裂化装置中调节催化剂的循环量.三延迟焦化焦炭化简称焦化是深度热裂化过程,也是处理渣油的手段之一.它又是唯一能生产石油焦的工艺过程,是任何其他过程所无法代替的.尤其是某些行业对优质石油焦的特殊需求,致使焦化过程在炼油工业中一直占据着重要地位.1.原料:延迟焦化与催化裂化类似的脱碳工艺以改变石油的碳氢比,延迟焦化的原料可以是重油、渣油甚至是沥青,对原料的品质要求比较低.渣油主要的转化工艺是延迟焦化和加氢裂化.2.产品:主要产品是蜡油、柴油、焦碳、粗汽油和部分气体,各自比重分别是:蜡油占23-33%,柴油22-29%,焦碳15-25%,粗汽油8-16%,气体7-10%,外甩油1-3%.3.基本概念焦化是以贫氢重质残油如减压渣油、裂化渣油以及沥青等为原料,在高温400~500℃下进行深度热裂化反应.通过裂解反应,使渣油的一部分转化为气体烃和轻质油品;由于缩合反应,使渣油的另一部分转化为焦炭.一方面由于原料重,含相当数量的芳烃,另一方面焦化的反应条件更加苛刻,因此缩合反应占很大比重,生成焦炭多.4.生产工艺延迟焦化装置的生产工艺分为焦化和除焦两部分,焦化为连续操作,除焦为间隙操作.由于工业装置一般设有两个或四个焦炭塔,所以整个生产过程仍为连续操作.a.原油预热,焦化原料减压渣油先进入原料缓冲罐,再用泵送入加热炉对流段升温至340~350 ℃ 左右.b.经预热后的原油进入分馏塔底,与焦炭塔产出的油气在分馏塔内塔底温度不超过400℃换热.c.原料油和循环油一起从分馏塔底抽出,用热油泵打进加热炉辐射段,加热到焦化反应所需的温度500 ℃ 左右,再通过四通阀由下部进入焦炭塔,进行焦化反应.d.原料在焦炭塔内反应生成焦炭聚积在焦炭塔内,油气从焦炭塔顶出来进入分馏塔,与原料油换热后,经过分馏得到气体、汽油、柴油和蜡油.塔底循环油和原料一起再进行焦化反应.5.生产设备a.焦炭塔焦炭塔是用厚锅炉钢板制成的空筒,是进行焦化反应的场所.b.水力除焦设备焦炭塔是轮换使用的,即当一个塔内焦炭聚结到一定高度时,通过四通阀将原料切换到另一个焦炭塔.聚结焦炭的焦炭塔先用蒸汽冷却,然后进行水力除焦.c. 无焰燃烧炉焦化加热炉是本装置的核心设备,其作用是将炉内迅速流动的渣油加热至500℃左右的高温.因此,要求炉内有较高的传热速率以保证在短时间内给油提供足够的热量,同时要求提供均匀的热场,防止局部过热引起炉管结焦.为此,延迟焦化通常采用无焰炉.四加氢裂化重油轻质化基本原理是改变油品的相对分子质量和氢碳比,而改变相对分子质量和氢碳比往往是同时进行的.改变油品的氢碳比有两条途径,一是脱碳,二是加氢.1.原料:1.重质油等2.产品:2.轻质油汽油、煤油、柴油或催化裂化、裂解制烯烃的原料3.基本概念加氢裂化属于石油加工过程的加氢路线,是在催化剂存在下从外界补入氢气以提高油品的氢碳比.加氢裂化实质上是加氢和催化裂化过程的有机结合,一方面能使重质油品通过裂化反应转化为汽油、煤油和柴油等轻质油品,另一方面又可防止像催化裂化那样生成大量焦炭,而且还可将原料中的硫、氯、氧化合物杂质通过加氢除去,使烯烃饱和.4.生产流程按反应器中催化剂所处的状态不同,可分为固定床、沸腾床和悬浮床等几种型式.1固定床加氢裂化固定床是指将颗粒状的催化剂放置在反应器内,形成静态催化剂床层.原料油和氢气经升温、升压达到反应条件后进入反应系统,先进行加氢精制以除去硫、氮、氧杂质和二烯烃,再进行加氢裂化反应.反应产物经降温、分离、降压和分馏后,目的产品送出装置,分离出含氢较高 80%,90%的气体,作为循环氢使用.未转化油称尾油可以部分循环、全部循环或不循环一次通过.2沸腾床加氢裂化沸腾床又称膨胀床工艺是借助于流体流速带动具有一定颗粒度的催化剂运动,形成气、液、固三相床层,从而使氢气、原料油和催化剂充分接触而完成加氢反应过程.沸腾床工艺可以处理金属含量和残炭值较高的原料如减压渣油.并可使重油深度转化;但反应温度较高,一般在400~450℃范围内.此种工艺比较复杂,国内尚未工业化.3悬浮床浆液床加氢工艺悬浮床工艺是为了适应非常劣质的原料而重新得到重视的一种加氢工艺.其原理与沸腾床相类似,其基本流程是以细粉状催化剂与原料预先混合,再与氢气一向进入反应器自下而上流动,催化剂悬浮于液相中,进行加氢裂化反应,催化剂随着反应产物一起从反应器顶部流出.该装置能加工各种重质原油和普通原油渣油,但装置投资大.该工艺目前在国内尚属研究开发阶段.5.生产设备加氢工艺生产装置的主要设备是在高温、高压及有氢气和硫化氢存在的条件下运行的,故其设计、制造和材料的选用等要求都很高,对生产操作的控制也极严格.高压加氢反应器是装置中的关键设备,工作条件苛刻,制造困难,价格昂贵.根据介质是否直接接触金属器壁,分为冷壁反应器和热壁反应器两种结构.反应器由筒体和内部结构两部分组成.a.加氢反应器筒体反应器筒体分为冷壁筒和热壁筒两种.b.加氢反应器内件加氢反应是在高温高压及有腐蚀介质H2、H2S的条件下操作,除了在材质上要注意防止氢腐蚀及其他介质的腐蚀以外,加氢反应器还应保证:反应物油气和氢在反应器中分布均匀,保证反应物与催化剂有良好的接触;及时排除反应热,避免反应温度过高和催化剂过热.以保证最佳反应条件和延长催化剂寿命;在反应物均匀分布的前提下,反应器内部的压力降不致过大,以减少循环压缩机的负荷,节省能源.为此,反应器内部需设置必要的内部构件,以达到气液均匀分布为主要目标.典型的反应器内构件包括:入口扩散器、气液分配盘、去垢篮筐、催化剂支持盘、急冷氢箱及再分配盘、出口集合器等.五溶剂脱沥青溶剂脱沥青是一个劣质渣油的预处理过程.用萃取的方法,从原油蒸馏所得的减压渣油有时也从常压渣油中,除去胶质和沥青,以制取脱沥青油同时生产石油沥青的一种石油产品精制过程.1.原料:1.减压渣油或者常压渣油等重质油2.产品:2.脱沥青油等3.基本概念溶剂脱沥青是加工重质油的一种石油炼制工艺,其过程是以减压渣油等重质油为原料,利用丙烷、丁烷等烃类作为溶剂进行萃取,萃取物即脱沥青油可做重质润滑油原料或裂化原料,萃余物脱油沥青可做道路沥青或其他用途.4.生产流程包括萃取和溶剂回收.萃取部分一般采取一段萃取流程,也可采取二段萃取流程.沥青与重脱沥青油溶液中含丙烷少,采用一次蒸发及汽提回收丙烷,轻脱沥青油溶液中含丙烷较多,采用多效蒸发及汽提或临界回收及汽提回收丙烷,以减少能耗.临界回收过程,是利用丙烷在接近临界温度和稍高于临界压力丙烷的临界温度℃、临界压力的条件下,对油的溶解度接近于最小以及其密度也接近于最小的性质,使轻脱沥青油与大部分丙烷在临界塔内沉降、分离,从而避免了丙烷的蒸发冷凝过程,因而可较多地减少能耗.国内的溶剂脱沥青工艺流程主要有沉降法二段脱沥青工艺、临界回收脱沥青工艺、超临界抽提溶剂脱沥青工艺.1沉降法二段脱沥青工艺沉降法两段脱沥青是在常规一段脱沥青基础上发展起来的.在研究大庆减压渣油的特有性质的基础上,注意到常规的丙烷脱沥青不能充分利用好该资源,而开发出的一种新脱沥青工艺2临界回收脱沥青工艺溶剂对油的溶解能力随温度的升高而降低,当温度和压力接近到临界条件时,溶剂对油的溶解能力已降到很低,这时,该丙烷溶剂经冷却后可直接循环使用,不必经过蒸发回收.3超临界抽提溶剂脱沥青工艺超临界流体抽提是利用抽提体系在临界区附近具有反常的相平衡特性及异常的热力学性质,通过改变温度、压力等参数,使体系内组分间的相互溶解度发生剧烈变化,从而实现组分分离的技术5.生产设备a.抽提塔抽提塔的作用有:在渣油进口和主溶剂进口之间为抽提区,渣油进口以上部分为分馏区,主溶剂进口以下为沥青沉降区.b.溶剂临界/超临界回收塔脱沥青油溶液分离器又称为超临界塔或临界塔,它实际上是一个可在溶剂临界压力以上操作的液—液分离器,用以回收脱沥青油溶液中的溶剂.c.增压泵脱沥青油溶液增压泵是实现超临界溶剂回收工艺的关键设备,它需要具有以上的扬程,入口能承受高的压力和温度,泵的作用是能保证实现溶剂在系统内循环.六加氢精制加氢精制一般是指对某些不能满足使用要求的石油产品通过加氢工艺进行再加工,使之达到规定的性能指标.1.精制原料:含硫、氧、氮等有害杂质较多的汽油、柴油、煤油、润滑油、石油蜡等.2.精制产品:精制改质后的汽油、柴油、煤油、润滑油、石油蜡等产品.3.基本概念加氢精制工艺是各种油品在氢压力下进行催化改质的一个统称.它是指在一定的温度和压力、有催化剂和氢气存在的条件下,使油品中的各类非烃化合物发生氢解反应,进而从油品中脱除,以达到精制油品的目的.加氢精制主要用于油品的精制,其主要目的是通过精制来改善油品的使用性能.4.生产流程加氢精制的工艺流程一般包括反应系统、生成油换热、冷却、分离系统和循环氢系统三部分.a.反应系统原料油与新氢、循环氢混合,并与反应产物换热后,以气液混相状态进入加热炉这种方式称炉前混氢,加热至反应温度进入反应器.反应器进料可以是气相精制汽油时,也可以是气液混相精制柴油或比柴油更重的油品时.反应器内的催化剂一般是分层填装,以利于注冷氢来控制反应温度.循环氢与油料混合物通过每段催化剂床层进行加氢反应.b.生成油换热、冷却、分离系统反应产物从反应器的底部出来,经过换热、冷却后,进入高压分离器.在冷却器前要向产物中注入高压洗涤水,以溶解反应生成的氨和部分硫化氢.反应产物在高压分离器中进行油气分离,分出的气体是循环氢,其中除了主要成分氢外,还有少量的气态烃不凝气和未溶于水的硫化氢;分出的液体产物是加氢生成油,其中也溶解有少量的气态烃和硫化氢;生成油经过减压再进入低压分离器进一步分离出气态烃等组分,产品去分馏系统分离成合格产品.c.循环氢系统从高压分离器分出的循环氢经储罐及循环氢压缩机后,小部分约30%直接进入反应器作冷氢,其余大部分送去与原料油混合,在装置中循环使用.为了保证循环氢的纯度,避免硫化氢在系统中积累,常用硫化氢回收系统.一般用乙醇胺吸收除去硫化氢,富液吸收液再生循环使用,解吸出来的硫化氢送到制硫装置回收硫磺,净化后的氢气循环使用.5.生产设备a.加热炉原料油与新氢、循环氢混合,并与反应产物换热后,以气液混相状态进入加热炉加热至反应温度进入反应器.b.反应器换热、炉后混氢进入反应器.在反应器催化剂床层反应,硫、氧、氮和金属化合物等即变为易于除掉的物质通过加氢变为硫化氢、水及氨等,烯烃同时被饱和.c.高压低压分离器加氢生成油经过换热和水冷后依次进入高压,低压分离器.d. 汽提塔从低压分离器来的加氢生成油与汽提过的加氢生成油换热,并进入加热炉加热,然后进入汽提塔,其作用是把残留在油中的气体及轻馏分汽提掉.汽提塔底出来的生成油经过换热和水冷却后,为加氢精制产品.七催化重整1.主要原料:石脑油轻汽油、化工轻油、稳定轻油,其一般在炼油厂进行生产,有时在采油厂的稳定站也能产出该项产品.质量好的石脑油含硫低,颜色接近于无色.2.主要产品:高辛烷值的汽油、苯、甲苯、二甲苯等产品这些产品是生产合成塑料、合成橡胶、合成纤维等的主要原料、还有大量副产品氢气.3.基本概念重整:烃类分子重新排列成新的分子结构.催化重整装置:用直馏汽油即石脑油或二次加工汽油的混合油作原料,在催化剂铂或多金属的作用下,经过脱氢环化、加氢裂化和异构化等反应,使烃类分子重新排列成新的分子结构,以生产C6~C9芳烃产品或高辛烷值汽油为主要目的,并利用重整副产氢气供二次加工的热裂化、延迟焦化的汽油或柴油加氢精制.4.生产流程根据催化重整的基本原理,一套完整的重整工业装置大都包括原料预处理和催化重整两部分.以生产芳烃为目的的重整装置还包括芳烃抽提和芳烃精馏两部分.a.原料预处理将原料切割成适合重整要求的馏程范围和脱去对催化剂有害的杂质.预处理包括:预脱砷、预分馏、预加氢三部分.b.催化重整催化重整是将预处理后的精制油采用多金属铂铼、铂铱、铂锡催化剂在一定的温度、压力条件下,将原料油分子进行重新排列,产生环烷脱氢、芳构化、异构化等主要反应,以增产芳烃或提高汽油辛烷值为目的.工业重整装置广泛采用的反应系统流程可分为两大类:固定床反应器半再生式工艺流程和移动床反应器连续再生式工艺流程.。
炼油工艺流程
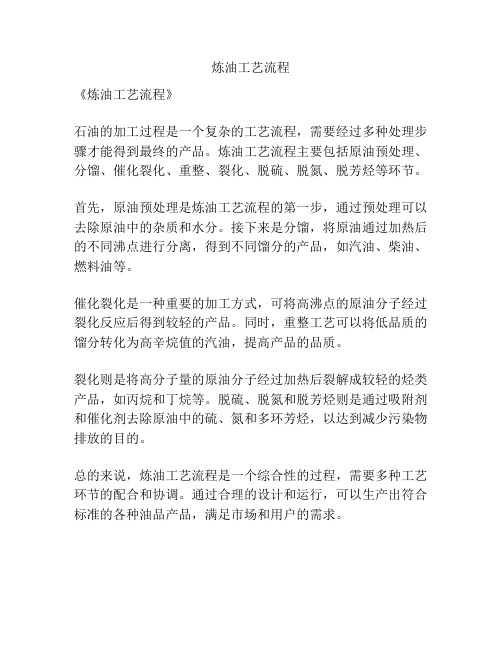
炼油工艺流程
《炼油工艺流程》
石油的加工过程是一个复杂的工艺流程,需要经过多种处理步骤才能得到最终的产品。
炼油工艺流程主要包括原油预处理、分馏、催化裂化、重整、裂化、脱硫、脱氮、脱芳烃等环节。
首先,原油预处理是炼油工艺流程的第一步,通过预处理可以去除原油中的杂质和水分。
接下来是分馏,将原油通过加热后的不同沸点进行分离,得到不同馏分的产品,如汽油、柴油、燃料油等。
催化裂化是一种重要的加工方式,可将高沸点的原油分子经过裂化反应后得到较轻的产品。
同时,重整工艺可以将低品质的馏分转化为高辛烷值的汽油,提高产品的品质。
裂化则是将高分子量的原油分子经过加热后裂解成较轻的烃类产品,如丙烷和丁烷等。
脱硫、脱氮和脱芳烃则是通过吸附剂和催化剂去除原油中的硫、氮和多环芳烃,以达到减少污染物排放的目的。
总的来说,炼油工艺流程是一个综合性的过程,需要多种工艺环节的配合和协调。
通过合理的设计和运行,可以生产出符合标准的各种油品产品,满足市场和用户的需求。
炼油厂工艺流程

炼油厂工艺流程
炼油厂是将原油转化为燃料和其他石化产品的工厂。
炼油工艺流程主要分为四个步骤:原油处理、提炼、裂解和后处理。
首先,在原油处理步骤中,原油经过脱水和去硫化处理,以去除其中的水和硫化物。
这是为了减少后续生产过程中的腐蚀问题和燃料中的污染物。
接下来,原油通过加热和蒸馏过程分离成不同的馏分。
这一步骤被称为提炼。
在提炼过程中,原油被加热至约400-600°C,从而将其分解为不同的馏分。
较轻的馏分,如天然气和汽油,在较低的温度下沸腾并被蒸馏出来。
而较重的馏分,如柴油和润滑油,在较高的温度下蒸发。
这种分离过程是基于不同组分的沸点差异。
接下来,较重的馏分进入裂解步骤。
裂解是一种将长链烃分子分解成短链烃分子的过程。
这一步骤通过加热和压力作用来进行,以产生更多的轻质烃类产品,如汽油和天然气。
裂解过程可以通过热裂解、催化裂解和加氢裂解等不同的方法来实现。
最后,经过裂解的产品进行后处理。
后处理的目的是去除其中的杂质和不纯物,以满足燃料和石化产品的质量标准。
这一步骤通常包括脱硫、脱氮和脱氧等处理过程,以减少燃料中的污染物。
总体而言,炼油厂工艺流程是一个复杂而精细的过程,需要仔细的控制和调整。
各个步骤的配合和优化对于最终产品的质量和产量都起着至关重要的作用。
另外,为了提高燃料的质量和
减少对环境的污染,炼油厂还需要进行不断的技术创新和工艺改进。
炼油厂工艺流程

炼油厂工艺流程
《炼油厂工艺流程》
炼油厂是将原油转化为汽油、柴油、煤油等石油产品的重要工业设施。
炼油厂工艺流程是一个复杂的过程,涉及到多个工艺单元和技术,以及各种化学反应和物理分离过程。
首先,原油通过一系列预处理工艺单元进行初步处理,包括脱盐、脱硫、脱水等处理,以去除杂质和硫化物。
然后,原油进入裂化装置进行裂化过程,将大分子烃类分解成小分子烃类,生产出汽油、柴油等产品。
随后,经过蒸馏装置进行蒸馏分馏,将不同沸点的烃类分离出来,得到各种产品。
另外,炼油厂还通过重整、裂化、重整、加氢等工艺单元对产品进行改质升级。
其中,重整是将低辛烷值的馏分转化为高辛烷值的汽油产品;裂化是将重质油产生乙烯、丙烯等烯烃产品;加氢是通过加氢裂化将重质油产品转化为轻油产品。
最后,炼油厂还通过分离、脱硫、脱氮、脱气等工艺单元进行产品的后处理,目的是提高产品质量和符合环保要求。
总体来说,炼油厂的工艺流程包括原油预处理、初步裂化、分馏分离、产品改质升级、产品后处理等多个环节。
各个工艺单元的相互配合,构成了完整的炼油过程,为石油产品的生产提供了技术支持和保障。
石油炼化常用的七种工艺流程

石油炼化常用的七种工艺流程石油炼化是指通过对石油原料进行物理、化学和热力处理,将石油分子按照不同大小、密度和性质进行分离和转化的过程。
在石油炼化中,常用的七种工艺流程包括原油蒸馏、裂化、重整、氢化、异构化、溶剂抽提和催化裂化。
本文将对这七种工艺流程进行详细介绍。
首先,原油蒸馏是石油炼化中最基本的工艺流程之一、原油蒸馏将原油按照沸点的不同进行分离,得到轻质石油产品如汽油、液化石油气(LPG)和航空煤油等以及重质石油产品如柴油、燃料油和渣油等。
其次,裂化是通过将长链烃分子在高温和催化剂作用下断裂成较短链烃分子的工艺流程。
裂化主要用于生产高辛烷值的汽油和石蜡等。
裂化可分为催化裂化和热裂化两种方式,其中催化裂化是最常用的。
第三,重整是将低辛烷值的烃类化合物通过催化剂作用下,使其分子重排和氢化,生成具有高辛烷值的芳烃化合物的工艺流程。
重整广泛用于产生高辛烷值的汽油,提高汽油的辛烷值和抗爆性能。
第四,氢化是将不饱和烃类化合物通过在催化剂存在下的氢气作用下进行加氢反应,生成饱和烃类化合物的工艺流程。
氢化主要用于去除石蜡、脱硫、脱氮和脱氧等操作,改善燃料质量和环境性能。
第五,异构化是将直链烷烃分子通过催化剂作用下,使其骨架变为支链结构的工艺流程。
异构化可提高汽油的辛烷值和抗爆性能,提高汽油的抗爆性能,改善燃料的燃烧性能。
第六,溶剂抽提是通过使用合适的溶剂,将原油中的特定成分进行分离和提纯的工艺流程。
溶剂抽提广泛应用于石油加工过程中,可以提取出高纯度的石蜡、沥青质和蜡烛脂等。
最后,催化裂化是通过将重质烃类化合物在催化剂作用下,在高温和高压的条件下进行裂化反应的工艺流程。
催化裂化能有效地将重质石油产品转化为轻质石油产品,增加汽油和液化石油气等产品的产量。
总结起来,石油炼化中常用的七种工艺流程包括原油蒸馏、裂化、重整、氢化、异构化、溶剂抽提和催化裂化。
这些工艺流程通过物理、化学和热力耦合作用,对石油原料进行转化和分离,得到不同的石油产品,满足不同用途的需求。
土法炼油工艺流程

土法炼油工艺流程
1.预处理:将废旧轮胎进行切割处理,以便后续的炼油操作。
2.热解反应:通过控制温度和反应时间,使废旧轮胎中的有机物质在高温下发生
热解反应,得到不同碳链长度的烃类化合物。
3.分馏操作:将热解后得到的混合物进行分馏,按照沸点的不同将烃类化合物分
离出来。
常用的分馏方法是常压蒸馏,可以得到不同沸点的组分。
4.精炼操作:对分馏得到的烃类产品进行进一步提纯,以去除其中的杂质。
常用
的精炼方法是溶剂抽提,利用溶剂的溶解性差异将杂质分离出来。
5.储存和运输:经过精炼后的烃类产品需要进行储存和运输,以便后续的使用和
销售。
通常使用密封的容器进行储存,并选择合适的运输工具进行运输。
- 1、下载文档前请自行甄别文档内容的完整性,平台不提供额外的编辑、内容补充、找答案等附加服务。
- 2、"仅部分预览"的文档,不可在线预览部分如存在完整性等问题,可反馈申请退款(可完整预览的文档不适用该条件!)。
- 3、如文档侵犯您的权益,请联系客服反馈,我们会尽快为您处理(人工客服工作时间:9:00-18:30)。
PPT文档演模板
炼油工艺流程[1]
单套装置最大加工规模已发展到673万 吨/年。延迟焦化技术已成为加工中东高硫原 油的重要手段之一。
到2003年底,全世界已建成的焦化装置 处理能力已达2.32亿吨/年。其中,美国的 延迟焦化装置加工能力达1.26亿吨/年,约 占全世界总加工能力的54.3%。
PPT文档演模板
PPT文档演模板
炼油工艺流程[1]
催化裂化技术的变化和未来趋势
五十年代引进前苏联移动床催化裂化 (小球催化剂) 1965年五朵金花之一流化催化裂化在抚顺石油二厂建成 投产。 五朵金花:催化裂化、催化重整、延迟焦化、尿素脱蜡、 微球催化剂与添加剂 七十年代分子筛催化剂的出现,带动了提升管催化裂化 技术的发展。 1984年石家庄炼油厂大庆全常渣催化裂化的工业运行, 翻开了我国重油催化裂化的新篇章。 九十年代初,前郭炼油厂实现了吉林原油全减压渣油催 化裂化;1998年大庆全减渣在燕化炼油厂实行了工业化。
炼油工艺流程
PPT文档演模板
2020/11/21
炼油工艺流程[1]
前言
大庆石化分公司炼油厂隶属于中国石油天然气 股份有限公司,国家大Ⅰ型企业。原油年加工能力 650万吨,润滑油年生产能力25万吨,生产汽油、 柴油、煤油、润滑油、石蜡、苯类、石油焦等六大 类18个品种32个牌号的石油化工产品。
PPT文档演模板
2.00Mt/a
PPT文档演模板
炼油工艺流程[1]
2003年几个国家原油与催化裂化加工能力
o
炼厂数
o
o 美国 132
o 中国
95
o 俄罗斯 42
o 日本
33
o 韩国
6
o 委内瑞拉 5
原油 催化裂化
Mt/a Mt/a
834.91 281.89
289.51 102.8
271.77 16.54
235.15
PPT文档演模板
炼油工艺流程[1]
延迟焦化发展前景
多年来延迟焦化一直被作为一种普通的深 加工手段。但随着随着原油重质化趋势日益明 显以及产品质量要求的提高,延迟焦化的作用 变得越来越突出。
近年来,我国的延迟焦化技术也得到了迅 速发展,先后在齐鲁、镇海、天津、吉林、新 疆和兰州等地建成大型焦化装置。在未来的5 年中,我国的延迟焦化装置还要发展,如何认 识和评价延迟焦化装置在炼油厂中的作用!
炼油工艺流程[1]
我国延迟焦化发展
1957年12月在抚顺石油二厂建成我国第 一套10万吨/年的延迟焦化工业试验装置
1964年,经过洛阳石化工程公司等研究 设计单位的联合攻关,被誉为新中国炼油技 术“五朵金花”之一的我国第一套连续生产 的延迟焦化工业装置建成投产。随后在大庆 、南京、独山子、胜利炼厂也相继建成了 30-60万吨/年不同规模的延迟焦化装置。
焦
加 氢
柴油
化
精 制
炼油工艺流程[1]
常减压装置
初 原油 馏
塔
加 热 炉
常 压 塔
PPT文档演模板
根根据据压原力油越中低各油组品份沸点 就的越沸低点的不特同性,,将采混用抽 真合空物的切方割法成,不使同加沸热后 的点常的压“重馏油份在”负。压条件
下进行分馏。
煤油
柴油
加氢裂化
加
热
炉
减
压 塔
催化裂化
减渣(催化、焦化)
大庆原油的特点:
➢ 低硫原油,S<0.5% ➢ 石蜡基原油,K=12.5 ➢ 含砷高 ➢ 汽油馏分含量低 ➢ 渣油馏分含量高
大庆石化公司炼油厂常减压装置型式:
➢ 燃料——润滑油型,同时充分利用炼化一体的优势
PPT文档演模板
炼油工艺流程[1]
常减压蒸馏发展的趋势:
➢ 总体原油加工能力不会有大的增长 ➢ 装置数目不断减少
43.8
127.20
8.94
64.11 11.59
占原油% 33.76 36.50 6.09 18.63 7.03 18.08
PPT文档演模板
炼油工艺流程[1]
世界催化裂化加工能力增加情况,Mt/a
世界
中国
美国
日本 加拿大 巴西
1995年
616.29 55.95 266.22 36.39 19.95 16.56
炼油工艺流程[1]
常减压蒸馏装置的作用:
➢ 原油加工的第一道工序 ➢ 将原油进行初步的处理、分离,为二次加工装置提供
合格的原料
常减压蒸馏装置的构成:
➢ 一般包括:电脱盐、常压蒸馏、减压蒸馏三部分 ➢ 有些装置还有:航煤脱硫醇、初馏塔等部分
PPT文档演模板
炼油工艺流程[1]
常减压蒸馏主要产品:
➢ 常压系统:石脑油、重整原料、煤油、柴油等产品 ➢ 减压系统:润滑油馏分、催化裂化原料、加氢裂化原料、焦化原
一线油及蜡下油等。 o 目前蜡油中实际只有减五线油和减四线油,且都是经过减压深
拔以后的油,原料越来越重影响到装置的轻油收率和生焦。
PPT文档演模板
炼油工艺流程[1]
催化裂化装置与其它装置的区别 1、催化裂化装置反再系统的催化剂床层为流化 床。固体催化剂流化控制难度大。 2、反再系统的操作参数影响因素多。 3、特殊设备多。 4、原料变重后结焦趋势增加,长周期运行受到 较大的影响。
➢ 装置能力不断扩大
PPT文档演模板
返回
炼油工艺流程[1]
加氢裂化、加氢精制装置
原料
换热 系统
氢气
加
热
炉
反
应
器
加加氢氢精裂制化原原理理::对在馏催份化油剂进作行用脱下硫,、烃脱类氮、 脱和氧非、烃脱化金合属物和加沥氢青转等化杂。质烷及烃对、烯烯烃烃、进芳烃 的行加裂氢化饱、和异,构从化而和来少改量善环油化品反的应气;味多、环颜色 和化安物定最性终,转提化高为油单品环的化质物量。。
PPT文档演模板
炼油工艺流程[1]
延迟焦化裂化与催化裂化的比较
(1)10年前,由于汽油和柴油及汽油和石脑油 价格差别较大,对汽油质量没有烯烃含量要求时, 催化裂化的效益是很高,但随着技术的发展和对产 品质量要求的不断提高,不仅催化裂化的柴油需进 一步加工,其汽油也因其烯烃含量过高需进一步加 工,和焦化汽柴油需进一步加工相似。而且现在气 柴差价趋小,导致两者的经济效益趋近。
PPT文档演模板
炼油工艺流程[1]
(2)随着石油化工的发展,无论是树脂的发展, 还是聚脂的发展都需要大量的石脑油为原料。但我 国大量的原油是石脑油含量不高的原油,远远不能 满足乙烯工业和催化重整对原料的需求。为此,需 要从减压蜡油和减压渣油中获得石脑油。大量工业 运转经验表明延迟焦化的石脑油经加氢后是很好的 乙烯原料,但是依目前国内炼厂焦化装置的规模和 操作方式能提供的焦化汽油数量不多,只能作为一 种补充。要使焦化装置能提供更多的乙烯原料,一 是要扩大延迟焦化装置的规模,二是要改变延迟焦 化的操作方式,增加焦化汽油的收率。
PPT文档演模板
炼油工艺流程[1]
中国大多数原油较重, 减压渣油的含量一般在40%50% 。随着原油需求量的增加, 更多的稠油被开采 出来。原油总的趋势是变重、质量变差。因此催化、 焦化等二次加工油品占总量的比例增加。
大量加工进口高硫原油,使得各馏分的硫含量大幅 度上升。2000年进口原油量6880万吨。2004年进 口原油量达1亿吨以上,占原油消费量的40%以上。
炼油工艺流程[1]
一、炼油流程 二、炼油产品性能、用途及注意事项 三、炼油的发展趋势 四、大庆石化分公司炼油厂存在的问题
PPT文档演模板
炼油工艺流程[1]
炼油厂燃料油系统
PPT文档演模板
炼油厂润滑油、石蜡系统
炼油工艺流程[1]
原油
常 减
压
PPT文档演模板
炼油厂燃料油系统
催
汽油
化
加 氢
重
裂 化
整
石油焦
炼油工艺流程[1]
延迟焦化发展及简介
1930年世界上第一套延迟焦化工业装置在 美国建成投产。
延迟焦化工艺流程简单、原料适应性强、 技术成熟可靠、投资和操作费用较低等特点, 在70多年的历程中得到了迅速发展,已成为世 界各国炼油业渣油转化的重要手段。据统计, 10年来新增的焦化能力占到了新增渣油加工能 力的22%以上。
PPT文档演模板
高分
汽油去重整
低分
分
馏
塔
煤油 柴油
尾油
炼油工艺流程[1]
加氢工艺是现代炼油工艺中最重要的技术之一,世界 各国的炼油厂加氢装置加工能力占其原料油加工能力的 比例达到50.11% ,它不仅是炼油工业生产清洁燃料的 主要手段,而且也成为石油化工企业的关键技术,发挥 着不可替代的作用。
PPT文档演模板
PPT文档演模板
炼油工艺流程[1]
按原油的含硫量:
按原油特性因素(K):
➢ 低硫原油 <0.5%(重) ➢ K大于12.1,石蜡基原
➢ 含硫原油 0.5~2%(重) 油
➢ 高硫原油 >2%(重)
➢ K为11.5-12.1,中间 基原油
➢ K为10.5-11.5,环烷 基原油
PPT文档演模板
炼油工艺流程[1]
PPT文档演模板
炼油工艺流程[1]
我国近几年新建和改造的几套大型FCCU
大连西太平洋石化公司RFCC 3.00Mt/a
大连石化公司RFCC
3.50Mt/a
兰州石化公司RFCC
3.00Mt/a
镇海炼化公司
3.00Mt/a
大庆炼化公司ARGG
2.40Mt/a
燕山石化公司
2.00Mt/a
洛阳石化公司RFCC
进口原油主要是来自中东地区的含硫原油。
PPT文档演模板