Gesipa气动拉铆枪Taurus系列产品手册
北极工具-Ultra-Tow XTP系列自动锁定A框拖车耦合器说明书
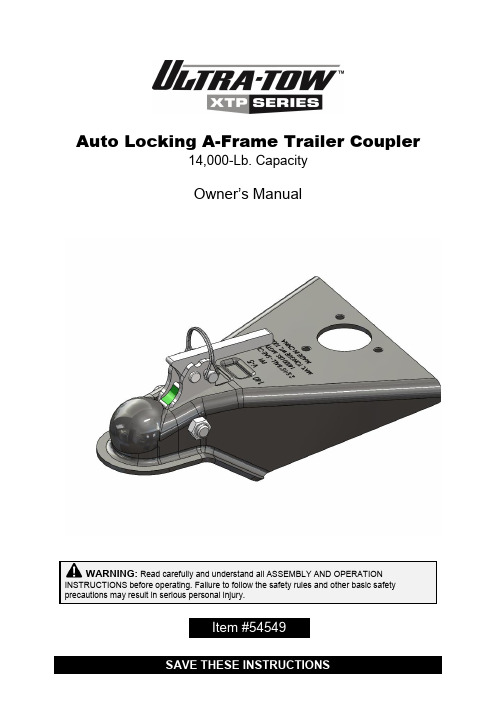
Auto Locking A-Frame Trailer Coupler14,000-Lb. CapacityOwner’s ManualWARNING: Read carefully and understand all ASSEMBLY AND OPERATION INSTRUCTIONS before operating. Failure to follow the safety rules and other basic safety precautions may result in serious personal injury.Item #54549Thank you very much for choosing an Ultra-Tow XTP Series™ product! For future reference, please complete the owner’s record below:Serial Number/Lot Date Code: ________________________________ Purchase Date: ____________________________________________ Save the receipt, warranty, and this manual. It is important that you read the entire manual to become familiar with this product before you begin using it.This coupler is designed for certain applications only. Northern Tool and Equipment is not responsible for issues arising from modification or improper use of this product such as an application for which it was not designed. We strongly recommend that this product not be modifiedand/or used for any application other than that for which it was designed. For technical questions, please call 1-800-222-5381.Intended Use (4)Technical Specifications (4)Important Safety Information (4)Specific Operation Warnings (5)Towing (6)Installation Instructions (6)Before Each Use (6)Operating Instructions (7)After Each Use (9)Maintenance (9)Troubleshooting (10)Parts Diagram (11)Parts List (12)Replacement Parts (12)Limited Warranty (13)The Ultra-Tow XTP Series Auto Locking A-Frame Trailer Coupler features an auto-locking system with a steel lock assembly. The secondary lock has a safety clip with a hole designed to fit an off-the-shelf padlock without an adaptor. This coupler can be used with any 2 5/16" ball having a capacity rating equal to or higher than the coupler.Weld LocationsWeld the coupler to the front of the trailer tongue. Care must be taken to get good penetration without undercutting the coupler or the tongue. See the illustration below for weld locations.Auto Lock FunctionSecondary LockPrimary LockSafety ClipUnlocked PositionThe illustration shown is in the unlocked position. When the Primary Lock shows no green, the coupler is open.Hitching Up1. Before hitching up, inspect for proper operation and for worn, damaged, or missing parts.2. Unlock the coupler by removing the Safety Clip and insuring that the Primary Lock shows no green, indicating the coupler is open.3. Back the vehicle up to the trailer until 2 5/16" of the ball is located under the coupler (shown above).4. As you lower the coupler onto the ball, the Primary Lock andSecondary Lock will end up in the locked position, as shown.Green means LOCKEDLocked PositionThe illustration shown to the right is in the locked position,with the Safety Clip installed. Be sure the lock assembly is in theunlock position before hook-up.Un-Hitching1. Unlock by removing the Safety Clip. Top Hole Secondary Lock2. Flip the Secondary Lock forward until it is pointing up.Hold this while raising the jack.3. If both hands are needed, the Secondary Lock can beheld by inserting the Safety Clip in the Top Hole whileraising the jack.4. Jack up the coupler until it clears the hitch ball and pull out the Safety Clip. The coupler is now back to the unlock position, as shown in the first illustration.Maintain the coupler hitch by adopting a program of conscientious repair and maintenance in accordance with the following recommended procedures. It is recommended that the general condition of any tool be examined before it is used. Keep your tool in good repair. Keep handles dry, clean, and free from oil and grease. The following chart is based on a normal operation schedule.Use the table below to troubleshoot problems before contacting service personnel or your local dealer. If the problem continues after troubleshooting, call your local dealer for assistance.∙For replacement parts and technical questions, please call Customer Service at 1-800-222-5381. ∙Not all product components are available for replacement. The illustrations provided are a convenient reference to the location and position of parts in the assembly sequence.∙When ordering parts, the following information will be required: item description, item model number, item serial number/item lot date code, and the replacement part reference number.∙The distributor reserves the rights to make design changes and improvements to product lines and manuals without notice.Northern Tool and Equipment Company, Inc. ("We'' or "Us'') warrants to the original purchaser only ("You'' or "Your") that the Ultra-Tow product purchased will be free from material defects in both materials and workmanship, normal wear and tear excepted, for a period of three years from date of purchase. The foregoing warranty is valid only if the installation and use of the product is strictly in accordance with product instructions. There are no other warranties, express or implied, including the warranty of merchantability or fitness for a particular purpose. If the product does not comply with this limited warranty, Your sole and exclusive remedy is that We will, at our sole option and within a commercially reasonable time, either replace the product or product component without charge to You or refund the purchase price (less shipping). This limited warranty is not transferable.Limitations on the WarrantyThis limited warranty does not cover: (a) normal wear and tear; (b) damage through abuse, neglect, misuse, or as a result of any accident or in any other manner; (c) damage from misapplication, overloading, or improper installation; (d) improper maintenance and repair; and (e) product alteration in any manner by anyone other than Us, with the sole exception of alterations made pursuant to product instructions and in a workmanlike manner.Obligations of PurchaserYou must retain Your product purchase receipt to verify date of purchase and that You are the original purchaser. To make a warranty claim, contact Us at 1-800-222-5381, identify the product by make and model number, and follow the claim instructions that will be provided. The product and the purchase receipt must be provided to Us in order to process Your warranty claim. Any returned product that is replaced or refunded by Us becomes our property. You will be responsible for return shipping costs or costs related to Your return visit to a retail store.Remedy LimitsProduct replacement or a refund of the purchase price is Your sole remedy under this limited warranty or any other warranty related to the product. We shall not be liable for: service or labor charges or damage to Your property incurred in removing or replacing the product; any damages, including, without limitation, damages to tangible personal property or personal injury, related to Your improper use, installation, or maintenance of the product or product component; or any indirect, incidental or consequential damages of any kind for any reason.Assumption of RiskYou acknowledge and agree that any use of the product for any purpose other than the specifieduse(s) stated in the product instructions is at Your own risk.Governing LawThis limited warranty gives You specific legal rights, and You also may have other rights which vary from state to state. Some states do not allow limitations or exclusions on implied warranties or incidental or consequential damages, so the above limitations may not apply to You. This limited warranty is governed by the laws of the State of Minnesota, without regard to rules pertaining to conflicts of law. The state courts located in Dakota County, Minnesota shall have exclusive jurisdiction for any disputes relating to this warranty.Distributed by:Northern Tool & Equipment Company, Inc.Burnsville, Minnesota 55306Made in China。
GE ADTS 530 气动测试设备说明书

GESensingADTS 530ADTS 530 is a Druck product.Druck has joined other GE high–technology sensing businesses under a newname—GE Industrial, Sensing.gFeatures•Low cost RVSM compliant tester •Integral electric pumps •Programmable safety limits •Leak test mode•Menu driven operation interface •12 month recalibration periodThe ADTS 530 is a compact and portable air data test set ideal for flightline use. This rugged solid state instrument features vibrating element transducer technology,providing high performance with a 12 month recalibration interval.Druck Air Data Test SetHoused in a fiberglass case, the ADTS 530 contains all essential elements required of a rugged pitot static tester:high accuracy sensors, microprocessor drivenelectronics, clear LCD readout, operator driven valving for parameter setting and an efficient electric pressure/vacuum pump system.The simplified LCD readout provides both parameter displays and menu driven operator instructions forsetting up protective limits. Altitudes/airspeeds are simply generated by hand-controlled fine adjustment valves,with internal electric pumps capable of altitudes <55,000 ft (<16,764 m), rates of climb <6,000ft/min(<1828 m/min), airspeeds <650 knots, for a wide range of aircraft types.The ADTS 530 is AC powered, operated from most single-phase national supplies and aircraft power. Itenables accurate, efficient testing without compromising rigorous flightline safety standards./Druck-GE-Sensing-ADTS-530-Air-Data-Test-Set.aspxTo buy, sell, rent or trade-in this product please click on the link below:GeneralScaling Factors •Altitude: ft, meters •Airspeed: knots, km/Hr•Mach Rate of Climb: ft/min, m/min •Others: mbar, inHg, psigLeak Rate TestingDisplayed in ft/min/min and kts/min and km/hr/min Overpressure•Negligible calibration change with up to 2 x full scale (FS) overpressure applied.•Compliant with 97/23/EC (category SEP).Temperature Range•Calibrated: 32°F to 122°F (0°C to 50°C)•Operational: 32°F to 122°F (0°C to 50°C)•Storage: -4°F to 158°F (-20°C to 70°C)Conformity•EN61010 for electrical and mechanical safety •EMC Specification EN 61326-1. CE marked•89/336/EEC as amended by 92/31/EEC and 93/68/EEC Power Supply•115 V to 230 VAC •47 to 400 HzPhysical•Case Dimensions (w x h x d) 9.7 in x 15.4 in x 14.9 in (248 mm x 391 mm x 378 mm)•Weight 35 lb (16 kg) nominalCaseRugged fiberglass with removable lid and storage for accessories.Pneumatic Connections Ps and Pt _AN4 MaleADTS 530SpecificationsPneumatic SuppliesInternal pressure/vacuum pump to 55,000 ft/650 kts (16764 m/650 kts @ 6000 ft/min (1828.8 m/min)AccessoriesPitot static hoses 25 ft (8 m) long with AN4 mating fitting to one end. Universal probe adaptor for Ps and Pt, AC power cable. Operators manual and calibration certificate also supplied as standard.Calibration StandardsInstruments manufactured by GE are calibrated against precision equipment traceable to International Standards.Ordering InformationPlease state the following:1) Model type ADTS 530Parameter Operating Range Resolution Accuracy Repeatability Altitude -15,000 ft to 1 ft±3 ft (±0.91 m)±2 ft 55,000 ft (0.30 m)@ sea level (±0.60 m)(-4572 m to ±7 ft (±2.13 m)±2 ft 16764 m)@ 29,000 ft (±0.60 m)(8840 m)±9 ft ±19 ft (±5.79 m)(±2.74 m)@ 50,000 ft (15,240 m)Static 1.30 to 0.00014 psi ±0.0014 psi 0.00072 psi Sensor18.70 psia (0.01 mbar)(±0.1 mbar)(0.05 mbar)(90 to0.001 inHg ±0.003 inHg 0.0015 inHg 1290 mbar)(2.7 to 38 inHg)Airspeed 20 to 650 kts 0.1 kts ±1.0 kts @ 50±0.5 kts ±0.3 kts @ 200±0.15 kts ±0.1 kts @ 500±0.1 ktsPitot 1.30 psi to ±0.00014 psi ±0.0029 psi ±0.00072 psi Sensor37.70 psi (±0.01 mbar)(±0.2 mbar)rising to (90 mbar to 0.001 inHg±0.007 inHg0.0021 psi 2600 mbar)(±0.05 mbar (2.7 to 77 inHg)rising to 0.15 mbar)±0.015 inHg rising to ±0.005 inHg Timed 100 to1 ft/min ±1% of value±0.5% of valueRate of 20000 ft/min (0.30 m/min)Climb (30.48 to 6096 m/min)Mach 0.1 to 4.670.001*********±0.001falling to *********Engine 1 to 50.001RSS of Ps ±1 countPressure andPt sensor Ratio accuracy(E.P.R)g©2006 GE. All rights reserved.920-299BAll specifications are subject to change for product improvement without notice.GE ®is a registered trademark of General Electric Co. Other company or product names mentioned in this document may be trademarks or registered trademarks of their respective companies, which are not affiliated with GE.GESensing。
ESCO Pro Series 气体盔腿 气力搬运设备 说明书
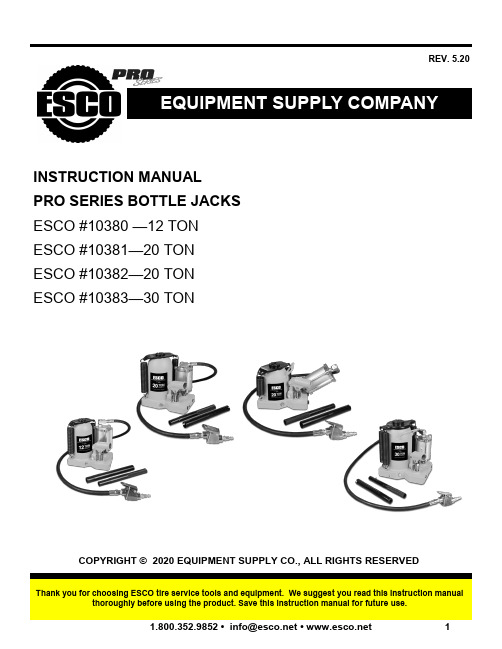
REV. 5.20COPYRIGHT © 2020 EQUIPMENT SUPPLY CO., ALL RIGHTS RESERVEDThank you for choosing ESCO tire service tools and equipment. We suggest you read this instruction manualthoroughly before using the product. Save this instruction manual for future use.INSTRUCTION MANUALPRO SERIES BOTTLE JACKS ESCO #10380 —12 TON ESCO #10381—20 TON ESCO #10382—20 TON ESCO #10383—30 TONTABLE OF CONTENTS• Introduction (2)• Specifications (2)• General Safety Rules (3)• Operating Instructions (4)• Troubleshooting (5)• Parts Breakdown .................................................................................................. 6-9• Model Number 10380. (6)• Model Number 10381 (7)• Model Number 10382 (8)• Model Number 10383 (9)• Parts and Repair Service (10)• Warranty (11)The ESCO Pro Series Air Hydraulic Lifting Equipment is designed with the heavy duty tire service market in mind. With lifting capacities from 12 Ton and up to 30 Tons, There is a Jack that will fit any service technician’s needs. Each jack is designed uniquely for specific application including: Commercial truck, Bus, Tractor & Farm Equipment, and much more.• Use a qualified person to maintain the jack in good condition. Keep it clean for best and safest perfor-mance.• DO NOT exceed this rated capacity.• Use this jack for lifting purpose only. DO NOT use it for any other purpose it is not designed to per-form.• Keep children and unauthorized persons away from the work area.• Remove ill fitting clothing. Remove ties, watches, rings and other loose jewelry, and contain long hair.• Wear ANSI approved safety goggles when operating the jack.• Keep proper balance and footing, do not overreach and wear nonslip footwear.• Only use this jack on a surface that is stable, level, dry and not slippery, and capable of sustaining the load.• Keep the surface clean, tidy and free from unrelated materials and ensure that there is adequate lighting.• When lifting a vehicle, apply the emergency brake and block all wheels.• Immediately after lifting, support the load with appropriate supporting equipment such as jack stands of adequate capacity! DO NOT work under a load which is supported only by a jack.• Before lowering load ensure that there are no obstructions underneath and that all persons are stand-ing clear.• DO NOT attempt to move the load while on the jack. The jack must only be used in a static position for lifting and lowering loads. Ensure that the load remains stable at all times.• DO NOT use the jack if damaged, any suspect parts are noted or it has been subjected to a shock load.• DO NOT operate the jack when you are tired or under the influence of alcohol, drugs or any intoxicat-ing medication.• DO NOT allow untrained persons to operate the jack.DO NOT make any modifications to the jack.• DO NOT use brake fluid or any other improper fluid and avoid mixing different types of oil when add-ing hydraulic oil. Only a good quality hydraulic jack oil can be used.• DO NOT expose the jack to rain or any other kind of bad weather.• If the jack need repairing and/or there are any parts that need to be replaced, have it repaired by au-thorized technicians and only use the replacement parts supplied by the manufacturer.• WARNING: the warnings, cautions and instructions discussed in this instruction manual cannot cover all possible conditions and situations that may occur. It must be understood by the operator that com-mon sense and caution are factors which cannot be built into this product, but must be supplied by the operator.• Always visually inspect the product before use for damage. Do not use product if damaged, altered, or in poor condition. Contact our technical service department with any questions or product issues by calling 800-352-9852.•Before first use of this product, pour a teaspoon of good quality air tool lubricant into the hose quick coupler -male of the air quick coupler -female, then connect it to air source and turn on the air valve and work for 3 seconds to evenly distribute lubricant.•Use the slotted end of the handle to turn the release valve(17) clockwise until it is firmly closed.•Apply the emergency brake and use wheel chocks to block all wheels to prevent any movement of the vehicle being lifted.•Place the jack into position and adjust the extension screw on part(7) as needed.NOTE: Check in your vehicle owner's manual for the location of recommended lift point.•Connect the air quick coupler -male into the shop air supply hose quick coupler -female, then turn on the air valve.•Raise the load to desired height, turn off the air valve and immediately USE JACK STANDS with adequate capacity to support the load.•When air source is not available, insert the big end of the handle into the handle bracket, pump it manually to raise the load to desired height. Then immediately transfer the load to appropriate support devices such as jack stands.WARNING! Be sure all tools and personnel are clear before lowering load.•When work is done, raise load enough to carefully remove the jack stands. Then SLOWLY and CAREFULLY lower the load by turning the release valve counter-clockwise (use the slotted end of the handle) in extremely small increments, then lower the extension screw by turning it clockwise as needed and remove the jack.WARNING! Dangerous dynamic shock loads are created by quick open-ing and closing the release valve when the load is being lowered. The re-sulting overload may cause hydraulic system failure which could cause severe personal injury and/or property damage.WARNING! Ensure that you read, understand and apply the safety in-structions and warnings before use.WARNING! Ensure that you have familiarized yourself thoroughly with the product and the hazards associated with its improper use.• Clean the outside of the jack with dry, clean and soft cloth and periodically lubricate the joints, extension screw and all moving parts with a light oil as needed.• When not in use, store the jack in a dry location with ram and extension screw fully lowered.• Purge the hydraulic system to eliminate any air in the system if jack efficiency drops or jack doesn’t work: A. If manual operation performs poorly, use the slotted end of the handle to turn the release valve 1-1/2 turns counterclockwise and remove the oil filler plug by gently pulling, in-sert the handle into the handle bracket and pump it 10 to 15 times, then replace the filler plug. B.If air operation performs poorly, connect the air inlet fitting to air source, use the slotted end of the handle to turn the release valve 1-1/2 turns counterclockwise and remove the oil filler plug by gently pulling, turn on the air valve to let the pump work for one minute, then replace the filler plug.• Check the hydraulic oil: place the jack in an upright position, completely lower the ram and re-move the filler plug, if it is not adequate, fill with high quality hydraulic jack oil to the lower rim of the fill hole, purge away air from the hydraulic system, top off with more hydraulic oil, then re-place the filler plug.• For best performance and longest life, replace the complete jack oil at least once per year: With the ram fully lowered, remove the oil filler plug, lay the jack on its side and drain the oil into a suitable container, then fill with high quality hydraulic jack oil, reinstall the filler plug.• NOTE: Dispose of hydraulic oil in accordance with local regulations.• It is recommended that an annual inspection be done by qualified technicians.FOR MODEL 10380:FOR MODEL 10381:FOR MODEL 10382:FOR MODEL 10383:• ESCO will pick up product for repair/warranty at your loca-tion.• ESCO will guarantee Repair/Service for 30 days. • ESCO has rental tools available• ESCO repairs IMT, FEC, Stellar, Blackhawk, OTC, PowerTeam, Ame Int., & Enerpac hydraulic pumps, bead breaker, and cylinders.• Authorized ESCO Repair & Warranty Centers Locatedthrough the US & Canada. For more information contact your ESCO sales representative.• Technical Support Over the Phone Available by Calling 1-800-352-9852GUARANTEED 1-Day Turnaround Service.Received by ESCO - Repaired in 24 Hours - Returned to you!Prompt, reliable service after the sale is very important to ESCO. ESCO maintains an in -house repair facility in Brooksville, Florida. To insure that our customers have as little down -time as possible, we offer a 1 day turna-round service. Our factory repair service is equipped with all the tools and machinery needed to repair your equipment quickly and affordably. Our trained technicians are the best in the industry. Not only do we service our own products, but we also service our competitors ’ products.In addition to ESCO ’s 30 years of providing quality repair service, ESCO has reached out and partnered with more than 50+ hydraulic repair facilities across the US & Canada, to deliver quality repair and timely return of products. Visit or call 1.800.352.9852 to hear more about the newly added “Authorized ESCO Warranty & Repair Facilities ” across the US.If you have a bead breaker, ram, or hydraulic pump that needs repair, ESCO fixes your product with factory parts and guarantees the repair. In addition to servicing ESCO brand products, we also re -pair CP, IMT, Elrick, Branick, Goodyear, FEC, AME Int., and Haltec lines of hydraulic bead breakers, rams, pumps, jacks, and many other hydraulic tire service equipment.Products sold by Equipment Supply Company (ESCO) are warranted to be free from de-fects in material and workmanship under proper use, application, and maintenance in ac-cordance with ESCO's written recommendations, instructions, and specifications for a pe-riod of 1 year (365 days) from the date of shipment to the end user, unless otherwise noted. ESCO's obligation under this warranty is limited to, and the sole remedy for any such de-fect shall be the repair or replacement (at ESCO's discretion) of unaltered parts returned to ESCO, freight prepaid, and proven to have such defect, provided such defect occurs within the 90-day warranty period (or otherwise noted) and is reported within 14 days of occur-rence.This is the only authorized ESCO warranty and is in lieu of all other express or implied war-ranties or representations, including any implied warranties of merchantability or fitness. Warranty claims must be submitted and be processed in accordance with ESCO's estab-lished warranty claim procedure. In no event will ESCO be liable for business interruptions,REV. 5.20COPYRIGHT © 2020 EQUIPMENT SUPPLY CO., ALL RIGHTS RESERVEDThank you for choosing ESCO tire service tools and equipment. We suggest you read this instruction manualthoroughly before using the product. Save this instruction manual for future use.-*************Stay Connected with ESCO ….。
亚特兰蒂斯·克彭高速紧固工具说明书

High-speed tightening – with low reaction toolsWhat is important in your tightening processes?Atlas Copco's low reaction tools close to eliminate the reaction force in assembly applications, delivering high-speed quality tightening while taking great care of the operator.Atlas Copco’s line-up of battery powered low reaction tools are designed to improve operator ergonomics. Not only will you increase productivity and optimize your factory up-time, you will also have less costs and time lost on operator injuries and fatigue.Choosing the right tool is the first – and most important – step towards a perfect operation. Regardless of which tool within our LRT range you choose, you will have a well balanced high quality tool. And choosing the right one will make the whole world of a difference.If you need a small and reliable workhorse that promises accuracy and speed, the pneumatic ErgoPulse PTI is an excellent solution.For maximum flexibility, high torque and the lowest vibration on the market – a cordless and powerful Atlas Copco TBP Pulse Tool is your choice.For reliable and accurate low reaction tightenings with lower torque, the cordless Tensor SRB offers an error-proof production.ErgoPulse PTI – your productive workhorseThe pneumatic, low weight ErgoPulse PTI is an excellent addition to the Atlas Copco LRT line-up. Increasing tool uptime with up to five times longer service intervals.With a durable and robust design the ErgoPulse PTI is faster and more accurate than ever and will improve the production quality and throughput. The ergonomic design of the tool takes care of your operators wellbeing, all while lowering the Total Cost of Ownership of your pulse tools. With fewer tool installations you can also enjoy lower set-up costs.The ErgoPulse PTI reduces the need formaintenance and is a proven and importantpart of this fleet. Our DuraPulse® technologymeans longer time between services with upto 5 x longer service intervals. With the rightstartup and maintenance you will have optimalperformance throughout the lifetime of the tool.With Torque Boost® the torque build-up is even faster, giving you reduced hoursper production unit. Quality is improved with a more robust and stable shut-offmechanism that increases accuracy and lowers the mean shift.Faster productionwith improved qualityQuality critical tightening and high productivity with the TBP-SThe all new cordless and slender TBP-S for one-handed operations, will ensure that your joint is tightened properly and trace the job done. Perfect for a reliable and quality critical tightening.With the same hardware as the TBP but with aslimmer software version suited for quality criticaltightenings, the TBP-S battery pulse tool is a robustyet slender solution for the middle segment. With amix of productivity, ergonomics and error-proofingthe TBP-S is proven to offer less maintenance andless down-time in production.Our DuraPulse® technology – also featured in theTBP – will ensure a robustness making the TBP-S areliable pulse tool that keeps on delivering.Low vibration and long service intervalsJust like the TBP, the TBP-S shows the lowestvibration levels in the market. This means operatorcomfort and safety, reducing work related costscaused by fatigue and injuries.The patented technology and design gives youlonger service intervals than with traditional pulsetools. With TorqueBoost®, the TBP-S has activecooling and advanced motor steering, so thetorque build up is fast and gives reduced hours perproduction unit.If you need morefunctionality in yourTBP-S you can easilyupgrade it to a fullyfunctional TBP withour upgrade kit.Future ProofSafety critical tightening and full traceability with the TBPSince launch, the TBP has been redefining what a low reaction pulse tool can do. Enjoy the benefits of a cordless tool for one-handed operations, enabling error-proof production.The Atlas Copco TBP is a reliable and powerful pulsetool, offering high torque tightening with very littlereaction. Giving you speed, accuracy, traceabilityand flexibility – with cordless freedom. With a TBPyou will have direct and accurate feedback of thejoint behavior.Anything is possible. Bring Error-Proofing to thenext level with our Barcode reader (EHMI) and alocation system like the ILT. Customize your toolwith accessories to fit your specific needs.Thanks to the patented technology and design,you will have longer service intervals than witha traditional pulse tools. Reduced oil leakage,separation of air and oil, and a cooler tool –meaning higher performance and uptime.Offering better protectionBV from injuries andincreasing the lifespan of your tools, results in hugesavings.Error-proof production with the cordless Tensor SRBThe Atlas Copco Tensor SRB delivers multipletightening technologies with accuracy, traceability, flexibility – and low reaction. It offers both traditional strategies like 2 steps and Quick Step, but also more advanced strategies such as TurboTight and TensorPulse. With a slim design it allows for easy access in cramped spaces.The Tensor SRB has low weight and great balance – with a slim design – ergonomically designed to prevent operator fatigue. New electronics and an improved motor will boost your productivity. Choose between 18v or 36v battery withoutcompromising the performance of speed or torque.Total Flexibility, Direct Drive, TurboTight™ and TensorPulseThe productive and cordless Tensor SRB will change the way you plan your assembly stations. Experience low reaction, one-handed operations with a strategy that fits your needs.DHD EEENTQSOORRLJJJKKKBBBBPFFCCAAGA B C D E F G H J K L NO PQ RSpacked with smart and innovative solutions. All to support our promise of delivering exactly the tool you need.A complete offerA flexible offer – Choose the functionality you needEach specific assembly has its own unique needs when it comes to functionalitylevel. With our flexible offer it is easy to find just the tool to get the job done, andfit it into your existing fleet. This, in combination with a common controller andvirtual stations, will lead to the best set up for your specific needs.Virtual stations: One controller – any toolIn a traditional assembly environment you willhave a vast range of reporting and non-reportingtools with different functionality, communicatingto a large number of controllers. Severalcontrollers, each controlling just the one tool.With Atlas Copco Virtual Stations you have onecontroller for multiple tools and reporting levels.Guided Rotaction socketsOur Rotaction concept promotes the increasing demands regarding operators safety and non-marking tools.The combination of free rotating sleeves and toolcovers for the connections "tool-to-socket" and socket covers for "extension-to-socket" improve operators safety significantly. This also eliminates user influence on the tightening.Thanks to extra stability from the elongated sleeve the socket delivers correct torque to the joint.Ergonomically this stability also protect operators from injury such as "white finger syndrome"Paired together we call it "Guided Rotaction".It protects your operators and maintains accuracy in your tightenings.Taking good care of your operators safety while maintaining joint accuracyBesides a wide range of standard products, customized solutions such as sockets, tool covers, multiples and much more can be realized with our team in Tierp, SwedenThe Rotaction range covers:¥Numerous sockets, bit sockets, bits and nut setters with freely rotating protection sleeves ¥Tool covers to bridge gaps between tool and socket ¥Socket covers to bridge gaps between extension and socket ¥Various extensions with rotating protection sleevesGuided socketWith Guided Rotaction the socket extends past the square drive A to give extra stability. The socket is held stable and eliminates wobbling thus maintaining force and improving operator comfort. This design is also found on our guided rotaction extensions.Rotaction covered socketsThe yellow sleeve B protects the user while the socket rotates on the inside. This provides a safer operation andminimized risk of scratches and marks on painted surfaces. It also eliminates any operator influence on the tightening. A tool cover C closes the gap between tool and socket protecting the operator from glove entanglement .BCAGuided Rotaction Sockets:¥Ergonomic¥Minimizes risk for injuries¥Eliminates user influence on the tightening ¥Gives extra stability ¥No scratching¥Delivers correct torque to the jointTake care of your investmentsEvery production line and industrial site is unique and has its own challenges. With that in mind, our service solutions are designed to help you get the most out of your industrial equipment. We combine analyses of production data with know-how and expertise in order to enhance your productivity and quality; while keeping you cost efficiency maintenance under control.Easystart – Right the First TimeNo two installations are the same. With Easystart it is easy to customize accordingto the customer needs per station. A trouble-free and efficient start of operationsfor your tightening system. Through a globally standardized and certified processfor every step, from programming to training, you will get it right the first time,saving time and money.ToolCover Maintenance Solutions help you optimize performance and gainefficiencies in your production while minimizing your tool costs and productionrisks. With a modular set of products, ToolCover is designed to meet your specificneeds and tool usage.Based on your needs, you can choose between Protect, Stability, Uptime.PreventiveMaintenanceOnce per tool and year Optimization based on historicproduction dataOptimization based on real-timeproduction dataKPI Monitoringand analysisYearly direct cost tracking Bi-annual direct and indirect costtracking per toolCustomized real-time monitoring andmonthly optimization analysis per tool Warranty Extended 3 month warranty aftermaintenanceFull contract lifetime warranty Full contract lifetime warrantyAtlas Copcoprofessional supportAnnual feedback meetings Bi-annual feedback andoptimization consultancyDedicated on-site Atlas Copco personnelRepairs Not included - but possible tocouple with RapidRepair contractYes - priority on workshop repairsand spare parts includedYes - included on-site supportRead more about our service offers at Take care of yourinvestmentsIncreasing valueIncreasing use ofproduction dataOptimize your tools –minimize your costsGuard your tools – maximizeyour productivityUptimeQualityCost eff.ModelBolt size mm Square drive in Torque range 1Free speed 2 r/min Weight Length mm CS dist mm Airconsumption under load Rec. hose size mm Air inlet thread in Ordering No.Nm ft lb kg lb l/s cfm High Pressure 3EP5PTI19 HR10-MT M63/88-196-1473000.9216823 6.51481/48431 0381 30 EP5PTI17 HR42-MT M61/4⁵7-175-1373000.9216823 6.51481/48431 0381 32EP6PTI32 HR10-MT M6-M83/816-3212-2390000.921682361381/48431 0381 40EP6PTI28 HR42-MT M6-M81/4⁵15-2811-2195000.921682361381/48431 0381 42EP7PTI55 HR10-MT M8-M103/830-5522-407000 1.2 2.517927919101/48431 0381 50EP8PTI70 HR10-MT M103/840-7029-517100 1.3 2.8179271021101/48431 0381 55EP9PTI80 HR13-MT M101/250-8037-595200 1.5 3.3191311328101/48431 0381 60EP11PTI100 HR13-MT M121/270-10052-744200 1.7 3.7201311430101/48431 0381 65EP13PTI150 HR13-MT M12-M141/285-15063-1105300 2.35201361532133/88431 0381 70Low pressure4EP5PTI15 HR10-MT-L M53/87-155-1169000.9216823 6.31381/48431 0382 30EP5PTI13 HR42-MT-L M4-M51/4⁵6-134-1069000.9216823 6.31381/48431 0382 32EP6PTI25 HR10-MT-L M63/813-259-1882000.921682361381/48431 0382 40EP6PTI25 HR42-MT-L M51/4⁵11-228-1682000.921682361381/48431 0382 42EP7PTI35 HR10-MT-L M63/823-3517-266200 1.2 2.517927615101/48431 0382 50EP8PTI45 HR10-MT-L M6-M83/833-4524-336300 1.3 2.817927817101/48431 0382 55EP9PTI65 HR13-MT-L M101/243-6532-484500 1.5 3.3191319.520101/48431 0382 60EP11PTI80 HR13-MT-L M10-M121/250-8037-593600 1.7 3.7201311328101/48431 0382 65EP13PTI110 HR13-MT-LM12-M141/263-11046-8140002.35201361634133/88431 0382 70Accessories Ordering No.Oil filling kit4250 3220 90Protective cover EP5/6PTI 4250 3209 00Protective cover EP7/8PTI 4250 3206 00Protective cover EP9PTI 4250 3216 00Protective cover EP11PTI 4250 3218 00Protective cover EP13PTI 4250 3214 00Quick Change Chuck4250 3218 00ErgoPulse PTIProtective cover is included for every tool1To be used as a guide only, final torque depends on type of joint, accessories used and air pressure.² In full speed mode³ Air pressure 6.3 bar / 91 psi ⁴ Air pressure 4 bar / 58 psi ⁵ Female Hexagon drive, Quick Change ChuckModelSquare Drive Guide Socket Torque range Nm ft lb ETP SRB31-25-103/8135-25 3.7-18.4ETP SRB31-25-I061/41135-25 3.7-18.4ETP SRB31-25-10-BD 3/8135-25 3.7-18.4ETP SRB31-25-I06-BD1/41135-25 3.7-18.4ETP SRB31-20-103/8125-20 3.7-14.75ETP SRB31-20-I061/41125-20 3.7-14.75ETP SRB31-20-10-BD 3/8125-20 3.7-14.75ETP SRB31-20-I06-BD 1/41125-20 3.7-14.75ETP TBP61-32-103/81312-358.9-25.8ETP TBP61-32-10-BD 3/81312-358.9-25.8ETP TBP61-32-421/411312-358.9-25.8ETP TBP61-32-42-BD 1/411312-358.9-25.8ETP TBP81-55-103/81320-5514.8-40.6ETP TBP81-55-10-BD 3/81320-5514.8-40.6ETP TBP91-80-131/21840-8029.5-59.0ETP TBP91-80-13-BD 1/21840-8029.5-59.0ETP TBP131-150-131/21855-15059-110ETP TBP131-150-13-BD 1/21855-15059-110ETP TBPS61-32-103/81312-359-26ETP TBPS61-32-421/411312-359-26ETP TBPS81-55-103/81320-5515-41ETP TBPS91-80-131/21830-8022-59ETP TBPS131-150-131/21855-15041-111ModelMax TorqueTensorPulse Nm ft lb Nm ETP SRB 31-20-102014.7516ETP SRB 31-25-102518.425Model Square Drive Input d mmLength mm Ordering No.Extension 1003/8251004027 1234 72Extension 1503/8251504027 1234 74Extension 2503/8252504027 1234 77Reference Code Square Drive Input d mmLength mm Ordering No.C223/8227.54027 1297 90C253/8257.54027 1297 91Model Length mm Square Drive Input d mmSocket Cover Ref.Ordering No.Socket 88503/822C224027 1292 08Socket 1010503/822C224027 1292 10Socket 1212503/822C224027 1292 12Socket 1313503/825C254027 1292 13Socket 1616503/825C254027 1292 16Socket 1717503/825C254027 1292 17ModelSquare Drive Guide socket Input d mm Length mmOrdering No.ETP TBP61-32-10ETP TBP61-32-10-BD ETP TBPS61-32-103/81322 & 259.54027 1297 30Batteries Ordering No.Ugrade kit TBP-S64211 5645 30Ugrade kit TBP-S84211 5645 31Ugrade kit TBP-S94211 5645 32Ugrade kit TBP-S134211 5645 33AccessoriesOrdering No.Protective cover TBP6 & TBP84250 3135 60Protective cover TBP94250 3135 62Protective cover TBP134250 3135 63SRB/TBP Tool Holder 4220 3584 86 Protective cover SRB 4220 2744 07 AccessoriesFoot protective cover Protective cover 18V Protective cover 36V STB Battery Charger Adapter4211 6083 87Tensor SRB Torque RangesLow Reaction Battery ToolsGuided Rotaction Extensions 13 Socket covers, Rotaction Guided Rotaction Sockets 13 Tool cover for Guided Rotaction Sockets TBP-S Upgrade kit Accessories 25 mm22 mmLdTool covers, Guided Rotaction sockets and others that aren't listed here can be special requested from our Competence Center Sockets & Bits1 0 9 0 123 3 8 9。
气动单铆钉枪+安装操作维护手册+中文

不要使用可能超过 200 p.s.i.g. 的气源,因 为工具可能爆裂并造成伤害。
! 警告
不要在其他铆钉上打铆钉。
! 警告
始终使用带钢制导块的工具。
! 警告
严禁以导致带扣指向工作区中的用户和他人 的方式使用此工具。
—9—
气动单铆钉枪
一般安全守则
! 警告
不要将此工具当做锤子使用。
! 注意
始终拿工具的把手位置。严禁拿工具的空气 软管。
气动单铆钉枪
订购编号:pneudrive1 安全、操作和维护手册
警告
如果未能正确使用本工具,可能会造成严重的人身伤害! 本手册包含重要的产品功能与安全 信息。在操作本工具之前,务必认真阅读并理解本手册内容。应确保本工具的其他用户和所 有者可以随时翻阅本手册。请将此手册存放于安全的地方。
工具规格
公制螺钉和螺母
工具空气接头
工具使用一个 3/8" N.P.T.外螺纹插头。气流直径应为 .275" (7 mm) 或更大。从气源断开时,接头必须能够 排放工具气压。
工作压力
45 至 95 p.s.i./3-6.5 巴 选择此范围中的工作压力以获得最佳紧固性能。 不要超过推荐的工作压力。
空气消耗
—3—
气动单铆钉枪
系统部件
Pneudrive 1
气动单铆钉枪
O 型环
带垫圈的铆钉
护目镜 —4—
气动单铆钉枪
系统部件
Pneudrive 1(标准设备)
调节器组件 1. 气压旋钮 2. 流量旋钮 3. Parker 编号 24-5 BP 接头
3/8":Push-lok 软管 4. 注油器 5. 过滤器 6. Parker 编号 H2E 3/8" 外
GunVault MV550-19和MV1050-19微型枪匣说明书
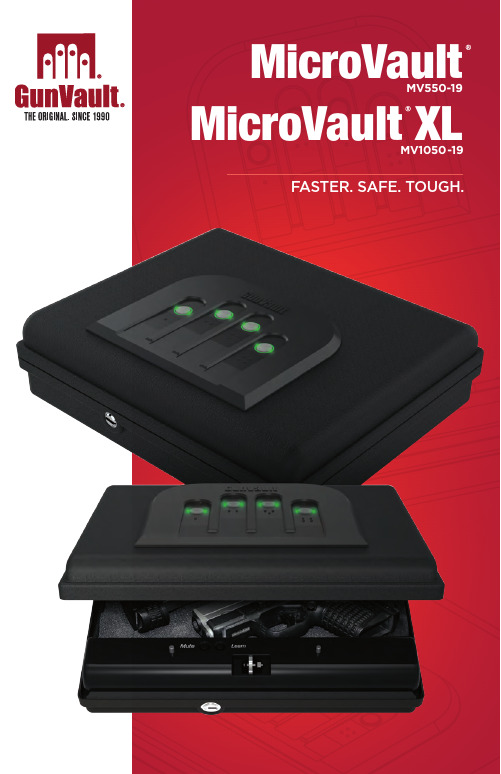
MicroVaultMV550-19 MicroVault XLMV1050-19FASTER. SAFE. TOUGH.3Product Features(For MicroVault and MicroVault XL)Always hold the battery connection cap while disconnecting or attaching a new battery. Do not pull on the power cables as this could cause the power supply to become disconnected from the lock. STEP 1 - Open the unit using the backup keys provided. STEP 2 - Locate the battery compartment in the interiorpanel. Connect the recommended 9V alkaline battery following the Positive (+) and Negative (-) guides on the connecting cap.STEP 3 - When the battery is connected you will hear a single beep signaling that the unit is powered.STEP 4 - After you have connected the battery to the cable, place the battery into the compartment and secure the cover.*GunVault recommends the use of either a Duracell or Energizer 9V alkaline battery with an expiration date of 5 years into the future.Battery InstallationSTEP 1 - Open the unit by using provided backup keys or factory default code. The factory default code is a single sequential press of each button moving from the left to right.STEP 2 - Locate the Learn button on the interior panel of the unit.STEP 3 - Press and hold the Learn button. A beep will sound and the keypad back lighting will turn green and remain illuminated. This will indicate the enrollment procedure has been initiated.STEP 4 - The keypad back lighting will remain activated as you enter a new access code. The code can be a minimum of three entries or maximum of six entries. STEP 5 - Press and hold the Learn button a second time. A beep will sound , and the keypad backlighting will turn red and remain illuminated.STEP 6 - Enter your new access code a second time. During this step , the red keypad back lighting will remain illuminated.STEP 7 - Press the Learn button a third time. The keypad back lighting will flash green and the unit will beep six times confirming that the new code has been accepted. If the keypad back lighting illuminates in red and the unit beeps six times, an error has occurred and you will need to repeat steps 3-7.STEP 8 -Test your access code to confirm that your unit has been properly programed.STEP 9 - Your safe is now ready for use.ProgrammingAn access code is a series of entries on the keypad. An entry is a single press of one or more buttons at the same time. Leave the unit door open while you program your safe.Backup Keys High-Strength Steel Security Cable Battery Compartment Learn Button Mute Button Elastic Strap(MV1050-19 Only)Keyport Backlit Keypad12345678354168724STEP 1 - Open the unit by using either your backup keys or current access code and locate the Learn button, which can be found on the interior panel of the unit.STEP 2 - Use steps 3-7 in the Programming section to change your current combination.STEP 3 - Now you have successfully reprogrammed your safe. Test your access code to confirm that your unit has been properly programmed.STEP 4 - Your safe is now ready for use.Safety FeaturesEntering an invalid access code triggers the Tamper Detect Feature.STEP 1 - Press and hold down buttons 2 and 3 for five seconds to initiate the tamper detect indicator.STEP 2 - If tampering has been detected, the indicatorlight will remain red until buttons 2 and 3 are released.STEP 3 - If tampering was not detected, the indicator light will remain green until buttons 2 and 3 are released.Tamper DetectionThis feature turns audio for unit on and off.STEP 1 - Open the unit and locate the Mute button on the interior panel of the unit.STEP 2 - Press and hold the Mute button for three seconds. The keypad back lighting will remain red while the mute button is held down. Once the keypad back lighting flashes green and the unit beeps three times , you should release the button.STEP 3 - Now you have successfully activated/deactivat-ed the mute feature.Audio ControlHigh-strength steel security cable. It should only be used to securely tether the product around a sturdy object.STEP 1 - Loop the cable around a sturdy object.STEP 2 - Find the end of the cable with the metal tip and run it through the eye of the other end and pull tight around the sturdy object.STEP 3 - Place the metal end of the security cable through the fitted slot on the top left side of the unit and close the lid to secure the cable.Security CableSTEP 1 - Open the unit by using either your backup keysor current access code.STEP 2 - Once opened, locate the metal slot on both sides of the interior roof of the unit.STEP 3 - Take the metal portion of the elastic strap and insert into metal slot on either side.STEP 4 - Repeat previous step to install on other side.STEP 5 - Now you have installed your elastic strap.Installing Elastic StrapSTEP 1 - When you enter the correct combination and the battery is low , the keypad back lighting will flash red and beep six times. Depending on how low the battery is , the unit may sound when releasing the lock. If the battery is completely depleted you will only hear a light humming sound.STEP 2 - Replace your battery by using steps in section labeled “Battery Installation”.*The low battery indicator only operates when you are in the process of opening your unit.Low Battery Warning Indicator•After six incorrect entries , the Security Sleep Mode feature will be triggered and will lockout any new keypad entries for two minutes. When Security Sleep Mode is active and a button is pressed , the keypad back lighting flashes red and the unit will beep three times.• To verify that the Security Sleep Mode is deactiva-ted , wait two minutes and then test your unit by slowly typing in your combination. If the keypad back lighting flashes green , your combination has been accepted and the unit will open. If the keypad back lightingflashes red , your combination is incorrect and you will need to try again. If you have forgotten or lost your combination , please follow the instructions on Programming. Your backup key will be required if reprogramming is needed.Security Sleep ModeResetting PasscodeMicroVault XL Unit Only5Assembly and Maintenance:•••••••Never store a loaded firearm in this unit.Always handle firearms as if they are loaded and ready to fire.Never grab your firearm by the trigger when removing or placing into safe.Always keep your firearm safety mechanism on while stored inside the safe.Never drink alcohol or use drugs while operating this safe or any firearm.Always follow the firearm safety rules set out by the firearm’s manufacturer.The manufacturer of this product does not recommend, suggest, advise, promote or otherwise condone the ownership or use of firearms. We at GunVault believe the decision to own or use a firearm is a serious decision that should only be made by an adult who has carefully considered the risks and benefits of such a decision.••••Important notes about your new GunVault productBackup Keys:Do not store backup keys inside of safe.Keep a record of your key number and serial number in a secure place separate from your safe.The backup key is for emergency use only in the event of forgotten passcode or battery failure.For Key Replacement visit the /product/key-replacement to complete the online keyreplacement form. In order to receive a replacement key , you will need to know the key number associated with your unit. You can find this information on the unit engraved on the keyport.Do not try to remove the key while in the turned position. This may cause damage to the unit or key.•••••Do not mount any GunVault product with the door facing down. The contents may fall out when the door is opened. Always hold the battery connection cap while disconnecting or attaching a new battery. Do not pull on the power cables as this could cause the power supply to become disconnected from the lock.Replace the batteries once a year regardless of whether or not the low battery indication is triggered.GunVault highly recommends the use of either a Duracell or Energizer 9V alkaline battery with an expiration date of 5 years in the future.You can register for battery reminder texts by visiting /battery-reminder-signupGunVault recommends that you lightly coat the door hinge spring and door latch-loop with quality oil at least once a year.Never spray anything into the latch mechanism as it can cause damage to the safe.Customer Service:GunVault products delivered without a pre-arranged Return Authorization number may be returned to sender unopened, at owner expense. Fees may accrue.WARNING : To avoid danger of suffocation, keep the plastic bag your safe arrived in away from babies and children. Do not use the bag in cribs, beds, carriages or play pens. The bag is not a toy and should be disposed of immediately upon removal. Contact your local waste management service for proper disposal or recycling of the plastic bag and other original packaging materials.WARNING : Keep you safe locked and closed at all times when not in use.WARNING: After closing the lid, always confirm it has properly latched in place.WARNING : Keep backup keys and access code combinations in a secure place away from children.WARNING : Keep high-strength steel security cable in a secure place away from children.WARNING : Children should not play with or around safe at any time.WARNING : This safe or any other firearm storage device cannot take the place of other safety procedures, including advising children of the dangers of firearms.WARNING : To enjoy maximum security benefits of this safe, it must be mounted in place.WARNING : This product can expose you to chemicals including Di (2-ethylhexyl) phthalate (DEHP) which is known to the State of California to cause cancer and birth defects or other reproductive harm. For more information go to Firearm Safety and your GunVault productGunVault recommends that you obtain as much information as possible on firearm safety.••••6Please visit for Replacement Promise details*1.GunVault (the “Company”) warrants to the original consumer (the “Purchaser”) of any GunVault safe (the “GunVault safe”) purchased after January 1, 2014 against any damage caused by fire, burglary or attempted burglary for a period of five (5) years from the date of purchase.2.The Company warrants to the purchaser that the GunVault safe will be free from defects in workmanship and materials for a period of one (1) year from the date of purchase.3. These warranties are not assignable or transferable to any other person.4. Any damage to the GunVault safe as a result of misuse, tampering, abuse, neglect, accident, improper installation, modification, unauthorized service, destruction, or the alteration of the serial number, or use in violation of the instructions furnished by the Company will void this warranty.5.The sole responsibility of the Company shall be limited to the repair or replacement (in its sole discretion) of any component of the GunVault safe which fails to conform to this warranty at no cost to the purchaser for the period of the warranty.6.Contact the Company directly to obtain service under this warranty. If it becomes applicable to send a defective product to the Company, a Return Authorization Number must first be obtained from the company. In order to obtain service under this warranty, purchaser must provide the Company with the following items (a) proof of purchase, (b) police or fire department report, (c) photographs of damaged safe, and (d) written testimonial.7.Products shipped without prior Return Authorization and Return Authorization Number may not be accepted, and the Company will not be responsible for their disposition and/or cost of return to the owner.8.The Company will not assume any responsibility for any loss or damage incurred in shipping. All return authorized products should include a copy of the original invoice in order for this warranty to be honored.9.This warranty is not an insurance policy. The Company is not responsible for any manner of damage to or theft of the Purchaser’s GunVault safe or its contents.10.We recommend that the warranty registration be completed online in order to validate this warranty.11. Any implied warranties that the purchaser may have are limited to the duration of the warranties described above. There are no further warranties that extend or apply beyond the face hereof, and the company expressly disclaims and excludes any and all warranties of merchant ability or fitness for a particular purpose. Some states do not allow limitations on how long an implied warranty lasts, so the above limitation may not apply to you.12. Repair or replacement shall be the sole remedy for the purchaser under this warranty. The company shall not be liable for any direct, indirect, incidental or consequential damages, losses or expense arising from the use or misuse of the GunVault safe. Some states do not allow the exclusion or limitations of incidental or consequential damages, so the limitation may not apply to you.13. This warranty gives you specific legal rights and you may also have other rights which vary from state to state.14. This warranty is only valid in the United States. If outside of the U.S., we encourage you to contact your point of purchase for further warranty help.GunVault Exclusive 5 Year WarrantyGUNVAULT PRODUCTTo submit your warranty registrationor call our Customer Service Department at (800) 222 - 1055.For key replacement visit the /product/key-replacement to complete the online key replacement form. In order to receive a replacement key you will need to know the key number associated with your unit. You can find this information on the unit engraved on the keyport.© 2019 ALPHA GUARDIANHenderson, NV 89014• Digital Safes • Biometric SafesSAFES• Security Cable • Mag VaultACCESSORIES• Download-able Manuals • How-to Video Tutorials • Warranty Registration• Frequently Asked Questions • And MOREVITAL INFORMATIONSafes, Acces s ories and MoreLoving your new GunVault safe and wanting to purchase more?Check out our website for special promotions, product information and more.。
阿特拉斯装配工具
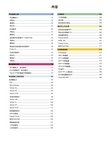
无论您从事何种行业, 我们都能为您带来增值
作为全球技术领先企业,阿特拉斯·科普柯为全世界制造行业提供 真正的解决之道。在我们现有的产品系列内,您可以找到应用了未 来技术的高科技工具、装配系统和工艺软件。从应用于工程机械车 辆装配的大螺栓紧固技术,到应用于电子工业微小紧固件的“微 扭”工具。阿特拉斯·科普柯都能提供您所需的解决方案,使您保 持行业领先。
您的需要我们会用心聆听
对我们而言,倾听至关重要。无论是制 造车辆、飞机、仪器设备或电子产品, 您所提供的及时反馈能让我们深入了解 您所从事的行业以及您在保持竞争力方 面所面临的挑战。我们的答复?答复将 是一系列持续不断的革新,助您提高生 产效率。
我们领先,别人追赶
阿特拉斯·科普柯在高科技、便于操作 人员使用的工具以及为工具提供辅助的 先进工艺控制和质量保证软件方面世界 领先。我不断地推出创新的新产品。
本目录中给出的数值为测长度32808ft04536kg22046lb扭矩98067nmftlb13558nm扭矩01130nm01020kpm07376ftlb压力100kpa980665kpa68948kpa00101972kpcm101972kpms13410hp流量21189cfm气动装配工具内容页数介绍12螺丝刀14手枪式20弯头式22冲击扳手25手枪式28油压脉冲拧紧扳手30ergopulse手枪式35带监测功能的脉冲拧紧扳手39pulsor40拧紧扳手42弯头式58手枪式6312气动装配工具冲击扳手lms冲击扳手拥有其他工具难以匹敌的速度和功率重量比特性这使得它成为诸如拆卸操作时的理想之选
2
精益生产
在汽车和其它行业,我们的高性能手持 式及固定式装配工具以及广博的技术知 识对精益生产作出了重要贡献。在西 方,每三部轿车中就有一部是采用我们 卓越的紧固解决方案制造的。
004拉铆枪安全操作规程技术交底

拉铆枪安全操作规程技术交底1、使用拉铆枪时应符合下列要求:⑴被铆接物体上的铆钉孔应与铆钉滑配合,并不得过盈量太大。
⑵铆接时,当铆钉轴未拉断时,可重复扣动扳机,直到拉断为止,不得强行扭断或撬断。
⑶作业中,接铆头子或并帽若有松动,应立即拧紧。
2、作业前的检查应符合下列要求:⑴外壳、手柄不出现裂缝、破损;⑵电缆软线及插头等完好无损,开关动作正常。
保护接零连接正确、牢固可靠;⑶各部防护罩齐全牢固,电气保护装置可靠。
3、严禁超载使用。
作业中应注意音响及温升,发现异常应立即停机检查,在作业时间过长,机具温升超过60℃时,应停机,自然冷却后再行作业。
美文欣赏1、走过春的田野,趟过夏的激流,来到秋天就是安静祥和的世界。
秋天,虽没有玫瑰的芳香,却有秋菊的淡雅,没有繁花似锦,却有硕果累累。
秋天,没有夏日的激情,却有浪漫的温情,没有春的奔放,却有收获的喜悦。
清风落叶舞秋韵,枝头硕果醉秋容。
秋天是甘美的酒,秋天是壮丽的诗,秋天是动人的歌。
2、人的一生就是一个储蓄的过程,在奋斗的时候储存了希望;在耕耘的时候储存了一粒种子;在旅行的时候储存了风景;在微笑的时候储存了快乐。
聪明的人善于储蓄,在漫长而短暂的人生旅途中,学会储蓄每一个闪光的瞬间,然后用它们酿成一杯美好的回忆,在四季的变幻与交替之间,散发浓香,珍藏一生!3、春天来了,我要把心灵放回萦绕柔肠的远方。
让心灵长出北归大雁的翅膀,乘着吹动彩云的熏风,捧着湿润江南的霡霂,唱着荡漾晨舟的渔歌,沾着充盈夜窗的芬芳,回到久别的家乡。
我翻开解冻的泥土,挖出埋藏在这里的梦,让她沐浴灿烂的阳光,期待她慢慢长出枝蔓,结下向往已久的真爱的果实。
4、好好享受生活吧,每个人都是幸福的。
人生山一程,水一程,轻握一份懂得,将牵挂折叠,将幸福尽收,带着明媚,温暖前行,只要心是温润的,再遥远的路也会走的安然,回眸处,愿阳光时时明媚,愿生活处处晴好。
5、漂然月色,时光随风远逝,悄然又到雨季,花,依旧美;心,依旧静。
HORIZON GLOBAL 76911隐形拖车铆型号说明书

Manuals+— User Manuals Simplified.HORIZON GLOBAL 76911 Hidden Hitch Instruction Manual Home » HORIZON GLOBAL » HORIZON GLOBAL 76911 Hidden Hitch Instruction ManualHORIZON GLOBAL 76911 Hidden HitchTo prevent SERIOUS INJURY, DEATH or PROPERTY DAMAGE:ALWAYS read, understand and follow warnings and instructions for your hitch BEFORE installation. Keep forOTHER WARRANTIES, EXPRESS OR IMPLIED (OTHER THAN THE WARRANTY OF TITLE AS PROVIDED BY THE UNIFORM COMMERCIAL CODE IN EFFECT IN MICHIGAN), INCLUDING WITHOUT LIMITATION, ANY WARRANTIES OF MERCHANTABILITY OR FITNESS FOR A PARTICULAR PURPOSE, SAIDWARRANTIES BEING EXPRESSLY DISCLAIMED.2. Obligations of Purchaser. To make a Warranty claim, contact Us at our principal address of 47912HalyardDrive, Suite 100, Plymouth, MI 48170, 1-800-632-3290, identify the product by model number, and follow the claim instructions that will be provided. Any returned product that is replaced by Us becomes our property. You may be responsible for return shipping costs. Please retain your purchase receipt to verify date of purchase and that You are the original consumer purchaser. The product and the purchase receipt must be provided to Us in order to process Your Warranty claim.3. Exclusive Remedy. Product replacement is Your sole and exclusive remedy under this Warranty.We shall not be liable for service or labor charges incurred in removing or replacing a product. IN NO EVENT WILL WE BE RESPONSIBLE FOR ANY INDIRECT, SPECIAL, CONSEQUENTIALOR PUNITIVE DAMAGES.4. Assumption of Risk. You acknowledge and agree that any use of the product for any purpose other than thespecified use(s)stated in the product instructions is at Your own risk.5. Governing Law. This Warranty gives You specific legal rights, and You also may have other rights which varyfrom state to state. This Warranty is governed by the laws of the State of Michigan, without regard to rules pertaining to conflicts of law. The state courts located in Oakland County, Michigan shall have exclusive jurisdiction for any disputes relating to this Warranty.6. For applicable patent information, see Installation InstructionsApplications:Years Make Models2018-Current* Audi Q5 / SQ5information regarding application years and trim levels.Installation Time: 90 minThe time listed above is the average time for professional installers. If you do not feel comfortable performing this installation on your own or are in need of assistance, please contact a professional installer.Equipment Required:Ball mount selection:MAXIMUM LENGTH 10.5’’Distance from the center of the ball hole to the center of the pin holeMINIMUM RISE 0.75’’Distance from the top of the shank to the top of the ball platform Representative Vehicle PhotoHitch IllustrationAlways wear SAFETY GLASSES when installing hitch1. Install receiver housing to hitch – a) Take the receiver and the weather covers out of case. b) Unlock the bluehandle using key attached and remove the housing from the receiver by pressing the blue handle and rotating clockwise until a click sound, as shown in Figure A, B,and C. c) Install the top/bottom weather cover to the housing, see Figure D. d) Attach the housing to the hitch using M12 bolt j, flat washer k, and prevailing torque nut l, as shown in Figure E.Tighten the fasteners for housing to 92 Lb-Ft (125 N*M).2. Keep the card m in the glove compartment. Peel off the label n and apply them on the top of the receiver anddoor jamb respectively, see Figure F. Note: For receiver installation & use, see instruction 76900N with receiver kit.Always wear SAFETY GLASSES when installing hitch3. Remove fascia – (a) Using T25 torx bit, remove (4) screws from rear bottom fascia.(b) Using T25 torx bit and 10 mm socket, remove (1) screw and (1) plastic flange nut from wheel well liner, bothsides.(c)Using plastic trim tools, remove the lower part of wheel well trim by unclipping the tabs from fascia andgently pulling it outward, both sides.(d)Using T25 torx bit, remove (3) screws located vertically in the upper area behind the wheel well liner and (1)screw behind wheel well trim, both sides.(e)Open lift gate. Using T25 torx bit, remove (2) round plastic screws near trunk weather seal. Remove rearcargo flooring.(f)Using panel removal tool, remove scuff plate by unclipping the tabs and pulling it upward. Using 10 mmsocket, remove (2) flange nuts from two recessed bumper fascia studs under scuff plate covered by rubber plug, see Figure 2.(g) Remove driver side interior panel. Unclip (2) wiring harness if present. Behind insulation material, using 10mm socket, remove (1) flange nut bumper fascia stud inside the compartment. Repeat same steps onpassenger side but DO NOT remove any wiring harness.(h)Using plastic trim panel tool, remove the fascia starting at the outer edges near wheel wells, and gentlypulling the fascia.4. Remove bumper beam – Using 16 mm socket, remove (8) M10 factory bolts from bumper beam and cross barabove bumper beam. Return bumper beam and cross bar to owner.5. Install hitch –Use silicone sealant to seal around the opening on the end panel both sides, see Figure 3.Raise the hitch into position and loosely install (8) existing factory M10 bolts to the hitch, see Figure 1.5. Tighten all M10 fasteners with torque wrench to 53 Lb.-Ft. (72 N*M).6. Reinstall all fasteners, wiring harness, panels, rubber plugs, scuff plate,, wheel well trim, and fascia removed inStep 1.Proper torque is needed to keep the hitch secure to the vehicle when towing.Bolt M12 1.75x100mm, CL10.9 Washer 7/16’’**********************************References/qrproductQR Product Finder | Horizon GlobalVirtual Patents | Horizon GlobalVirtual Patents | Horizon GlobalHorizon GlobalHorizon Global。
拉伸式阀门产品介绍说明书

This end is moving away from the solenoid. Attachment at this end would push the load away from the solenoid.
Pull Solenoids
PLUNGER TRAVEL PLUNGER TRAVEL
Typically single acting Linear Solenoids are categorized into two styles, either a Pull style or a Push style.
Pull Solenoids
PLUNGER TRAVEL
MOUNTING THREADS
PLUNGER SEATED
For a pull solenoid the attachment is made at the end of the plunger that is moving into the coil and away from the load. Attaching at this end will pull the load toward the solenoid.
Stroke
Plunger Travel is Toward “0”
► The “X” axis represents the stroke or travel of the plunger toward the base.
► “0” on this axis represents the plunger position when it is fully seated against the base and the air gap is closed. This is the strongest force output point of the solenoid and is at the end of the plunger travel.
武汉贝瑞克自冲铆接机操作说明书

下模 C 型本体 液压站
3.2 易损件更换 正常情况下,可参考根据铆接的次数更换下列部件。
项目 20 万次 下模 冲针 送钉弹簧 枪嘴 预紧弹簧 油管 液压系统密封
★ ★ ★ ★ ★ ★ ★
铆接次数 50 万次 100 万次
200 万次
3.3 常见问题分析
错误 铆钉压入过浅,铆钉头露在 外边 原因 错误的铆钉 模具脏
13
解决措施 更换铆钉 清洁模具 更换模具 更换夹嘴 检查材料, 调整压力 调整 O 型环 更换 更换 更换 降低压力值 检查铆钉, 与检测报告的数据比对 换正确的模具 更换铆钉 更换一个新的枪嘴 清洁枪嘴 更换下模 清洁下模 更换冲针 保持工件和下模之间的平行 位置 检测 C 型钳的裂缝,变形 更换冲针 更换铆钉 重装料带 更换 更换 清理 排除阻碍 保证料带顺畅 更换 检查铆钉长度与检测报告数 据比对 检查被连接材料的材质与检 测报告数据比对 更换正确的下模 更
2.7.2 铆钉的选择 直径 AJ 铆 钉 直 径 分 3mm,5mm,8mm 三种, 常 用 的 长 度有
3,5,6,8,10,12mm,其他长度需定制。 表面 处理 防腐要求 长度 分镀锌和化学涂层两种。 盐雾大于 200 小时。
钉长的选择一般要求是 L=δ*1.3~1.5(δ为材料叠加厚
度) ,过长和过短都不适合。 材质 铆钉的材质和硬度针对不同的工件材质和厚度应有所不
同,供需双方应在实验的基础上做出选择。 2.7.3 铆枪的选择 压力 要根据工件的特点选择不同压力等级的枪,目前常用的为
5 吨,10 吨,15 吨三种。 本体 本体的结构由压力等级和工件的工作空间决定,通常需定 制。一经定型,用户不宜随便更改,否则会降低模具寿命并影响铆接 质 量,严重的会损坏枪体或造成人身伤害。合格的本体要求在额定的
凯斯拉斯琐箭ча杆推拉式45E琐箭跨 соста杆534 Technician Catalog Ma

ModelCatalog NumberParts Manualc For Technical Assistance call: 800-227-2233, Fax: 888-329-8207To Order Parts call: 888-227-2233, Fax: 888-329-0234Push/Pull45E-PPS-534cascadecorporationPublicationsPART NO.DESCRIPTIONParts Manual686455Service Manual684945Operators Guide685531Operators Pocket Guide 684944Installation Instructions680664Servicing Cascade Cylinders-VHS 679929Tool Catalog673964Literature Index Order FormDecalsPlaten GroupREF QTY PART NO.DESCRIPTION685766Platen Group11685767Platen − LH21685768Platen − RH32622907u Pin428007u Rivet52622908u Spring62622897u Handleu Included in Upper Hook Assembly 688386. Reference: S-3408, S-3409, S-3410.REF QTY PART NO.DESCRIPTION 72685533u Upper Hook84685677Capscrew, M16 x 459l682858Shim (.030) 102682851Lower Hook 114667225Washer124209016Capscrew, M16 x 3513n688379Shim (.060)l As required − 2 maximum.n As required for proper adjustment.35E/45EFrame Group ITA IIIREF QTY PART NO.DESCRIPTION6082716Frame Group116082691Frame222492Fitting, 6-631682992Tube41682991Tube512453Fitting, 6-6612680Fitting, 6-6712375Fitting, 6-684682850Stop92768825Capscrew, M12 x 20REF QTY PART NO.DESCRIPTION682835Mounting Group 11682557Anchor Bracket22672018n Bearing Segment32768759Setscrew, M12 x 35426517Cotter Pin526234Washer62678525Clevis Pin71675548Cylinder u82682814Bearing92666984Fitting, 4-6102675550Restrictor Washeru See Cylinder page for parts breakdown. Reference: SK-5385.REF QTY PART NO.DESCRIPTION1147403n Grease Fitting121686513Tube131686514Tube1422680Fitting, 4-4152683250Strip162683218Spacer1722669Fitting, 4-61822617Fitting, 6-61912453Fitting, 6-62012375Fitting, 6-6212688387Jam Nutn Included in Bearing Service Kit 672022.35E/45E⁄Sideshift CylinderREF QTY PART NO.DESCRIPTION675548Cylinder Assembly 11553857Nut21636851n Wiper 31553501Piston 41662452n Seal51638247n Back-up Ring 61641835n Seal 71675549Shell 81553499Rod912785n O-Ring101615128n Back-up Ring 111553500Retainer121553856Retaining Ring 1317202Retaining Ring 553861Service KitnIncluded in Service Kit 553861.Quick-Change Lower Hook Group – ITA IIIREF QTY PART NO.DESCRIPTION683181Lower Hook Group ITA III12678832Pin22675957Hook3 4 779019Capscrew, M16 x 35 Class 8.842675958GuideCylinder Assembly45EREF QTY PART NO.DESCRIPTION582636Cylinder Assembly 11678019Nut 21564159u Seal31671048u Seal Loader Kit 41564161Piston 51562717Shell 61558626Rod 71662448u Seal 812787u O-Ring91615130u Back-Up Ring 101558628Retainer 111636853u Wiper 124559697Bearing 131559698Spacer 142604510Fitting, 6562339Cylinder Service Kitu Included in Service Kit 562339.Mechanism GroupMechanism Group35E/45EREF QTY PART NO.DESCRIPTION204644Mechanism Group 11204691Arm – Inner Secondary RH 21204692Arm – Secondary Outer RH 34683154Bushing n4l683161Shim (.030)5l683162Shim (.060)64205070Roller7l683163Shim (.030)8l683164Shim (.060)94683155Bushing n101682821Pin – Primary/Secondary Inner 11126229Washer122685661Capscrew, M8 x 14 131********Eye Pin142682822Pin – Head152205065Pin166683153Bushing n17l204532Shim (.12)182204694Arm – Outer Primary 194204533Pin – Frame204204535Bushing n214204695Pin – Primary Outer 221204604Arm – Inner Primary 231204693Arm – Secondary Outer LH 241204690Arm – Inner Secondary LH 252204696Pin – Outer262682823Pin – Rod272683165Spacer2810767961Capscrew, M8 x 162926045015Retainer u (or) 26050227Retainer uH3016047125Retainer u (or) 16050414Retainer uH3136047151Capscrew, M8 x 16 H 3237913Roll Pin Hl Quantity as required.n Included in Bushing Service Kit 205075.u Confirm part number cast on retainer.H Included in Service Kit 6051665.Hydraulic Group - ITA Class IIIREF QTY PART NO.DESCRIPTION6086271Hydraulic Group11685831Hose, Twinline, 39.60 in.22683173u Hose, 15.50 in.312375u Fitting, 6-642604511u Fitting, 6-66604511Fitting, 6-6516085925Valve n62787373u Capscrew, M8 x 25n See Valve Assembly page for parts breakdown.REF QTY PART NO.DESCRIPTION72685979Hose, 18.50 in.82684956Cable Tie 94605235u Fitting, 5-6101200647u Tube 112—Plug 121200649u Tube 131200648u Tubeu Included in Hydraulic Components Group 200581-R7.Reference: SK-5385, 5386.35E/45EGBRETValve AssemblyREF QTY PART NO.DESCRIPTION6085925Valve Assembly 116045016Relief Valve21682170Service Kit316085927Valve BodyFaceplate GroupREF QTY PART NO.DESCRIPTION6019140Faceplate Group (R3)6020440Gripper Jaw Assembly (R5) l 11206396Gripper Jaw216002134Valve316020444Gripper Cylinder, LH u416020443Gripper Cylinder, RH u546020462Collar62787373Capscrew, M8 x 20746014089Pin816002135Gripper Bar91672712Gripper Pad105680253Lockwasher, M8u See Gripper Cylinder page for parts breakdown.l Includes items 1-17.REF QTY PART NO.DESCRIPTION 115787375Capscrew, M8 x 20 122604511Fitting, 6-6132686573Bearing1426002138Hose, 315 mm 1526002139Hose, 450 mm 164617918Fitting, 4-4178669894Retaining Ring 184225346Capscrew, M16 x 60 194675620Washer2016002142Faceplate, 40 x 40 in. n 212768714Capscrew, M16 x 60n Width x height.35E/45EREF QTY PART NO.DESCRIPTION6020444Gripper Cylinder – LH 11646540w Seal21636850w Wiper312718w O-Ring412710w O-Ring51615122w Back-Up Ring616020453Shell716020461Rod81685664Retainer91685665Piston101563462Nut111563916Ring1213137Ring131663728w Piston Sealw Included in Service Kit 684827.REF QTY PART NO.DESCRIPTION6020443Gripper Cylinder – RH 11646540▼ Seal 21636850▼ Wiper 312718▼ O-Ring 412710▼ O-Ring51615122▼ Back-Up Ring 616020452Shell 716020461Rod 81685664Retainer 91685665Piston 101563462Nut 111563916Ring 1213137Ring131663728▼ Piston Seal▼Included in Service Kit 684827.P A R T S O R D E R I N G L O GP U R C H A S E S E R I A L R E F C A S C A D E C U S T O M E R D A T EO R D E R N U M B E RP A G E N O .Q T Y P A R T N O .P A R T N O .D E S C R I P T I O N P R I C EDo you have questions you need answered right now? Call your nearest Cascade Parts Department.Visit us online at AMERICASCascade CorporationParts Sales2501 Sheridan Ave. Springfield, OH 45505Tel: 888-CASCADE (227-2233) Fax: 888-329-0234Cascade Canada Inc.5570 Timberlea Blvd.Mississauga, OntarioCanada L4W-4M6Tel: 905-629-7777Fax: 905-629-7785Cascade do BrasilRua João Guerra, 134Macuco, Santos - SPBrasil 11015-130Tel: 55-13-2105-8800Fax: 55-13-2105-8899EUROPE-AFRICACascade Italia S.R.L. European Headquarters Via Dell’Artigianato 137030 Vago di Lavagno (VR) ItalyTel: 39-045-8989111Fax: 39-045-8989160Cascade (Africa) Pty. Ltd. PO Box 625, Isando 1600 60A Steel Road Sparton, Kempton Park South AfricaTel: 27-11-975-9240 Fax: 27-11-394-1147ASIA-PACIFICCascade Japan Ltd. 2-23, 2-Chome, Kukuchi Nishimachi Amagasaki, Hyogo Japan, 661-0978 Tel: 81-6-6420-9771 Fax: 81-6-6420-9777Cascade Korea121B 9L Namdong Ind.Complex, 691-8 Gojan-DongNamdong-KuInchon, KoreaTel: +82-32-821-2051Fax: +82-32-821-2055Cascade-XiamenNo. 668 Yangguang Rd.Xinyang Industrial ZoneHaicang, Xiamen CityFujian ProvinceP.R. China 361026Tel: 86-592-651-2500Fax: 86-592-651-2571Cascade India MaterialHandling Private LimitedNo 34, Global Trade Centre1/1 Rambaugh ColonyLal Bahadur Shastri Road,Navi Peth, Pune 411 030(Maharashtra) IndiaPhone: +91 020 2432 5490Fax: +91 020 2433 0881Cascade Australia Pty. Ltd. 1445 Ipswich Road Rocklea, QLD 4107 AustraliaTel: 1-800-227-223Fax: +61 7 3373-7333Cascade New Zealand15 Ra Ora DriveEast Tamaki, AucklandNew ZealandTel: +64-9-273-9136Fax: +64-9-273-9137Sunstream IndustriesPte. Ltd.18 Tuas South Street 5Singapore 637796Tel: +65-6795-7555Fax: +65-6863-1368c。
SAF PLASMA 自动焊接器产品说明书

0704/18G 138G 137G 136G 139AUTOMATIC PLASMA WELDING in the stainless steel boiler maker industryWHAT MUST BE ACHIEVED ?SAVINGS ? Rapidity of operation, low deformation to avoid or reduce the reconforming post operations, low reinforcement to reduce or suppress polishing operations, keep the original chemical analysis of the base material to garantee corrosion characteristics, good visual aspect of the welds since most of the welds are more and more visible. It is a quality criteria, repeatibility of the quality obtained.G 86In the constant search for optimal productivity, every industry must strive to reduce production time while maintaining extremely high quality. In the case of plasma welding, unlike the tricathode process, the multiplication of torches would have little effect on the performance levels.Nevertheless, a solution exists for increasing speeds by 30 to 50 % in comparison with a single torch : PLASMA + TIG process.Thanks to this technique, the PLASMA arc melts the joint throughout its thickness, while the TIG arc, equipped with a magnetic oscillation system and additional filler metal prepares the final appearance of the surface. This yields results that are perfectly suited to the specifications of speed and quality. SAF , an innovative specialist in TIG and PLASMA welding, naturally offers installations combining these techniques, which are particularly suitable for production of large stainless steel vessels. Nonetheless,certain strict criteria are required for ensuring the profitability and the technical feasibilityof these materials. These criteria may be summed up as follows : manufacture of stainless steel tanks from 3 to 8 mm thick, with a welding length of at least three meters, or parts with a diameter greater than 2200 mm.TOP QUALITY RESULTS AND INCREASED PRODUCTIVITY Initial plate preparation/fit-up greatly reduced by suppression of bevel up to 7 mm.Reduction of welding times compared to manual welding (up to 4 to 5 times).A garanted regular penetration thanks to the «key hole» technique on all but joints with TIG pre-tacking. A very high quality weld in regard to most stringent controls. It eliminates hazards of lack of penetration at the beginning of welds as well as the systematic delicate repairs after grinding of beginnings and ends of welds. A guaranted reproductibility,thanks to memorization *of complete welding parameters programs (simply defined by material,diameter and thickness).High quality finish on circular welds thanks to the automatic key hole closure system*.*PLASMA with microprocessor installation only.G 1370725/10G 2000725/08Welding current (100 %)30 - 350 A DC 100 % 3 - 300 A DC (±1 %)500 A DC 100 %Pulsed current frequency10 Hz max (option) 1 - 500 Hz 10 Hz max. Primary voltage (50 - 60 Hz)380/400/415 V 220/230/380/400/415/440/500 V 220/380/415 V or 380/440/500 V Supply current (380 V)39 A 17.6 A 36 A Plasma pilot arc12 A 1 - 25 A adjustable 15 A Gas circuitswith built-in gyrometers with built-in gyrometers gyrometers in the controls Welding current controloption yes Process controlyes option no Dust protection- 2 interchangeable filters -Dimensions (h x w x d)940 x 517 x 820 mm 1225 x 700 x 790 mm 1320 x 670 x 780 mm Weight175 kg 245 kg 450 kg Cat. NumberTIG :9121-1049/50/51 (1)9114-05569114-0532plasma :9121-1046/47/48 (1)9114-0533Insulationclass H class H class H ProtectionIP 23IP 23IP 23Torch cooling unit nooptional for TIG no Thanks to its characteristicsand its high degreeof automation whick makesit relatively easy to master,the PLASMA processis now commonly usedin the boiler making industry and SAF since 1965, has installed more than 800 installations throughout the world. SAF offers now a wide range of turn key welding installations,but it has to be choosen carefully according to the work to be done.It involves 3 levels of sub assemblies :•the PLASMA welding equipment,• the support structure of the PLASMA equipment,• the positionning equipment to rotate the rounded sheetsand/or the seamer bench.THE PLASMA WELDING INSTALLATION FOR THE BOILER MAKER INDUSTRY BUFFALO TIG or plasma installation.Programmation and adjustments by potentiometers.Direct current.350 Amps (100%).NERTAMATIC 300 TR This high-technology power source offers a totally regulated welding current facility at frequencies from 1 Hz to 500 Hz **.NERTINOX TH 500 Thyristor power source.Programmed and adjusted by potentiometers.500 A DC (100 %).**Pulsing the PLASMA arc currentat two levels (e.g. 100-200 A)produces a very high levelof confinement of the energyin the arc (the electromagnetic pinch effect combiningwith the pneumaticand mechanical confinementimparted by the nozzle).It offers great operator comfortcombined with better penetrationcontrol and appearance (back of weld).POWER SOURCES1202-501202-45Q -1311-05Do not operate the key-hole closure at the end of weld bead.(1)Harness length 10/17/22 m0704-15Q -1422-012264-102264-011202-473670-421202-49S A F r e s e r v e s i t s e l f t h e r i g h t t o e m b o d y m o d i f i c a t i o n s w i t h o u t p r i o r n o t i c e . T h e i l l u s t r a t i o n s , d e s c r i p t i o n s a n d c h a r a c t e r i s t i c s a r e g i v e n f o r i n f o r m a t i o n o n l y a n d d o n o t e n g a g e t h e r e s p o n s i b i l i t y o f t h e c o n s t r u c t o r .© S A F - 1515-47760006S 01 E d . 4Q B: 1590P hotosS A F : R o c s k a y - F r a n ço i s SAF - 13-17, RUE D’EPLUCHES 95310 SAINT-OUEN L’AUMÔNE - FRANCE TEL. : + 33 1 34 21 33 33 - FAX : + 33 1 34 21 31 30SAF WELDING PRODUCTS LTD - LOW MARCH - LONDON ROAD DAVENTRY - NORTHANTS NN11 4SD TEL. : 01327 705511 - TELEFAX : 01327 701310Email:***********************Internet : DISTRIBUTOR’S STAMP。
液压气动FLEX-5工具系列说明书

HYDRO-PNEUMATIC FLEX-5 TOOL40FLEX-5TOOLFLEX-5P: The Sherex FLEX-5P utilizes a Pull to Pressure method of installation. This method allows the same insert type to be installed into varying material thicknesses (within the Grip Range of the part) without any adjustment to the tool.FLEX-5S: The Sherex FLEX-5S utilizes a Pull to Stroke method of installation. This method allows the insert to be installed to the same distance each time. This is helpful when installing into soft materials (prevents crushingof the base material) or when a specific Installed Length is required.Thread SizeComplete HeadsetAnvil (1 + 2)Mandrel(3)Hex Driver(4)Reducing sleeve(5)M 3 FL5-HS -M3 FL5-HS -00903 M -M3-40 FL5-HS -01003 FL5-HS -09103 M 4 FL5-HS -M4 FL5-HS -00904 M -M4-55 FL5-HS -01004 FL5-HS -09104 M 5 FL5-HS -M5 FL5-HS -00905 M -M5-65 FL5-HS -01005 FL5-HS -09105 M 6 FL5-HS -M6 FL5-HS -00906 M -M6-65 FL5-HS -01006 FL5-HS -09106 M 8 FL5-HS -M8 FL5-HS -00908 M -M8-65 FL5-HS -01008 FL5-HS -09108M 10 FL5-HS -M10 FL5-HS-00910 M -M10-65 FL5-HS -01010# 4-40 UNC FL5-HS -0440 FL5-HS-00854 M -0440-175 FL5-HS -00754 FL5-HS -09154 # 6-32 UNC FL5-HS -0632 FL5-HS -00856 M -0632-175 FL5-HS -00756 FL5-HS -09156 # 8-32 UNC FL5-HS -0832 FL5-HS -00858 M -0832-175 FL5-HS -00758 FL5-HS -09158 # 10-24 UNC FL5-HS -1024 FL5-HS -00850 M -1024-250 FL5-HS -00750 FL5-HS -09150 # 10-32 UNF FL5-HS -1032 FL5-HS -00850 M -1032-250 FL5-HS -00750 FL5-HS -09150 1/4-20 UNC FL5-HS -2520 FL5-HS -00848 M -2520-250 FL5-HS -00748 FL5-HS -09148 1/4-28 UNF FL5-HS -2528 FL5-HS -00848 M -2528-250 FL5-HS -00748 FL5-HS -09148 5/16-18 UNC FL5-HS -3118 FL5-HS -00840 M -3118-250 FL5-HS -00740 FL5-HS -09140 5/16-24 UNF FL5-HS -3124 FL5-HS -00840 M -3124-250 FL5-HS -00740 FL5-HS -091403/8-16 UNC FL5-HS -3716 FL5-HS -00842 M -3716-250 FL5-HS -00742 3/8-24 UNFFL5-HS -3724FL5-HS -00842M -3724-250FL5-HS -00742n/a n/an/ahead sets for standard rivetnuts One Tool With Pull to Pressure & Pull to Stroke Capabilitiesfeatures and benefits• Installs Rivet Nuts from: M3-M10 and #4-40-3/8-16.• Push to start nose piece to spin on fastener.• Single stage trigger.• Automatic reverse with manual reverse bypass.• Quick change mandrel design.• Light weight (4.2 lbs).• Can be suspended from a balancer.• Socket head cap screw mandrel.Change over kit for converting between pull to pressure and pull to stroke• Installs Rivet Nut Studs from M5-M8 and #10-24-5/16-24.• Available in an in-line version.• Split tool available (remote booster for lighter tool).• Upgradeable to process monitoring.• 5,000 lbs (22 kN) pulling force at 90 psi.• 7 mm (0.276 in.) of available stroke.• 2-3 second cycle time.• All aluminum design for improved durability.*View our FLEX-5 videos at 1/25341-800-453-1692Request InfoM 5Thread Size head sets for rivet nut studsM4 FL 5-HS-M4SR FL 5-HS-SR0994 M-M4-55 FL 5-HS-01004 FL 5-HS-09104 M5 FL 5-HS-M5SRFL 5-HS-SR0995M-M5-65 FL 5-HS-01005 FL 5-HS-09105 # 8-32 UNC FL 5-HS-0832SR FL 5-HS-SR0858 M-0832-150 FL 5-HS-00758 FL 5-HS-09158 # 10-24 UNC FL 5-HS-1024SR FL 5-HS-SR0950 M-1024-225 FL 5-HS-00750 FL 5-HS-09150 # 10-32 UNFFL 5-HS-1032SR FL 5-HS-SR0950M-1032-225FL 5-HS-00750FL 5-HS-09150Thread SizeComplete Headset Anvil (1 + 2)Mandrel (3)Hex Driver(4)Reducing sleeve(5)head sets for riv -float ®-short*Head sets include p/n FL5-HS-12S92 adaptor nutHYDRO-PNEUMATIC FLEX-5 TOOL & MS 100 RIVET NUT TOOL41ms 100 rivet nut toolThe MS 100 Rivet Nut installation tool installs rivet nuts from 5/16-18 to 1/2-20 and M8 and M14. It also installs 5/16 -18 and M8 Riv-Float ®. The MS 100 tool comes with one mandrel and one anvil.The MS 100 Rivet Nut installation tool should be operated at 80-100 psi. Sherex recommends the use of an air regulator, air filter and lubrication system to reduce the wear of internal components. It is also recommended to lubricate the mandrel to increase performance. Mandrels should be replaced when excessive thread wear occurs.Thread Size Mandrel Anvil 5/16-18MA-373-3118MA-369-31185/16-24MA-377-3124MA-369-31183/8-16MA-374-3716MA-370-37163/8-24MA-378-3724MA-370-37167/16-14MA-375-4314MA-371-43147/16-20MA-301-4320MA-371-43141/2-13MA-376-5013MA-372-50131/2-20MA-379-5020MA-372-5013M8MA-308-08MM MA-318-08MM M10MA-310-10MM MA-320-10MM M12MA-312-12MM MA-322-12MM M14MA-314-14MMMA-324-14MMMS100®1/2534STUD PULLER1/2 341-800-453-1692Request Info。
Cascade 型号为 35E-PAS-112 的 push pull 商品说明书
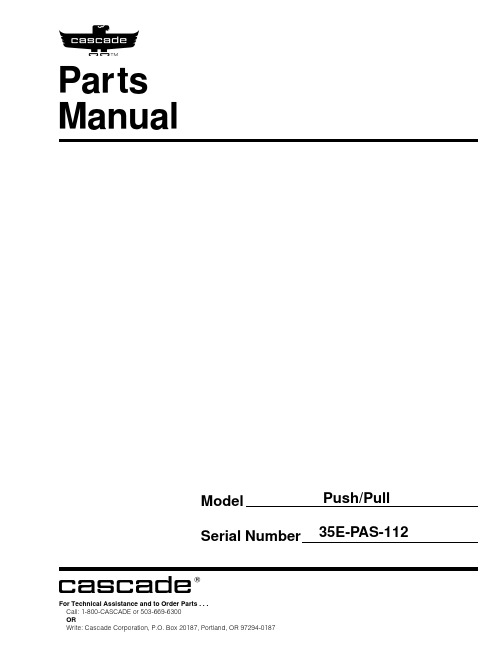
cascadeாFor Technical Assistance and to Order Parts . . .Serial NumberModel c Parts Manual35E-PA S -112Push/PullPublicationsPART NO.DESCRIPTIONParts Manual686455Service Manual684945Operators Guide685531Operators Pocket Guide684944Installation Instructions680664Servicing Cascade Cylinders-VHS 679929Tool Catalog673964Literature Index Order Form35E/45E Sheet–Sav(6 places)Decals35E/45E QFM™ Sheet–Sav(6 places)1#6@!9348752REF QTY PART NO.DESCRIPTION207240Platen Group - 15"x48"11207270Platen L. H. - 15"x48"21207255Platen R. H. - 15"x48"32622907Pin 428007Rivet 52622908Spring 62622897Handle72688386Upper Hook 84685534Capscrew 9@206969Shim (.030)102682851Lower Hook 114667225Washer 124209016Capscrew 13q 688379Shim (.060)@ As required.q As required (2 maximum)Items 3 through 7 may be ordered as assembly 688386.Ref: S-3985Note: Usable platen lengths are determined by measuring from the faceplate (fully retracted position) to the platen tip or total platen length minus 4 1/2".q As required, maximum 1 per side.s See Sideshift Cylinder page for parts breakdown.Sideshift CylinderITA Class III55EREF QTY PART NO.DESCRIPTION675548Cylinder Assembly 11553857Nuts2*******Seal31553501Pistons4*******Wipers5*******Back-up Ring61675550Washer (orifice .085 in.)71675549Shell81553449Rods912785O-Rings101615128Back-up Ring111553500Retainer121553856Retaining Ring1317202Snap Rings141641835Seal553861Service Kits Included in Service Kit 553861.Quick-Change Lower Hook Group ITA II35E/45EREF QTY PART NO.DESCRIPTION683179Lower Hook Group ITA II12678832Pin22675514Hook34682182Capscrew42675515GuideREF QTY PART NO.DESCRIPTION206950Frame Group 11206945Frame 21206954Bar32768525Capscrew 42686119Washer 51206955Foot68766929Capscrew 78678991Lockwasher 82s 583942Cylinder 94617915Fitting, 4-4104678525Pin-Clevis 114672726Cotter Pins See Cylinder page for parts breakdown.35E/45EFrame Group123456789!PP0020.epsSheet-Sav Cylinder1234567890!@#PP0023.eps583942Cylinder Assembly 11564162Shell 21564165Rod 31685664Retainer 41685665Piston 51563462Nut61563916Ring-Stop713137Retaining Ring w 81646540Seal w 91646850Wiper w 1012718O-Ring w 1112710O-Ringw 121615122Back-up Ring w131663728Seal35E/45EREF QTY PART NO.DESCRIPTIONw Included in Service Kit 684827.Mechanism Group° ! #4°&)&(#!°5^$#°@!#%›fl ° ‡‹ 645& 987126!4%*¤^!#⁄53# ! °#! 3 5 )# ! ° fi^54*5 4 & 4⁄( PP0086.illMechanism Group35E/45EREF QTY PART NO.DESCRIPTION204644Mechanism Group 11204691Arm-Inner Secondary R. H.21204692Arm-Secondary Outer R. H.34683154s Bushing4q683161Shim (.030)5q683162Shim (.060)64205070Roller7q683163Shim (.030)8q683164Shim (.060)94683155s Bushing101682821Pin11156229Washer122685661Capscrew1315682999Eye-Pin142682822Pin-Head152205065Pin166683153s Bushing17q204532Shim (.12)182204694Arm-Outer Primary 194204533Pin-Frame204204535s Bushing214204695Pin221204604Arm-Inner Primary 231204693Arm-Secondary Outer L. H. 241204690Arm-Inner Secondary L. H. 252204696Pin-Outer262682823Pin-Rod272683165Spacer2813767961Capscrewq Quantity as required.s Included in Bushing Service Kit 205075.CylinderREF QTY PART NO.DESCRIPTION582635Cylinder Assembly 11 ---Spacer 21562552Seal s 317348Snap Ring 41562334Piston 51562716Shell 61558626Rod 71559705Seal s 812785O-Ring s91615128Back-Up Ring s 101559696Retainer 111636853Wiper s 124559697Bearing 131559698Spacer 141678019Nut151671047Seal Loader Kit ss Included in Service Kit 562338.Ref: S-34242.0" D I A .%5@#2$46310!7@98PP0043.illHydraulic GroupREF QTY PART NO.DESCRIPTION152207041Clamp 161768794Capscrew 171767414Nut 181200647Tube 191200648Tube 201200649Tube 212683173Hose222765329Capscrew 237604511Fitting, 6-6244605235Fitting, 5-6252604510Fitting, 62612375Fitting, 6-6281206939q Knob (without gripper control)291685831HoseREF QTY PART NO.DESCRIPTION206940Hydraulic Group (without gripper control)11206931Tube 21206932Tube 31206933Tube 41206934Tube 51206935Tube 61206936Tube 71206937Tube832492Fitting, 6-691206927Junction Block 103685981Hose111206942s Valve (without gripper control)122768525Capscrew 132686119Washer141669432Diode (without gripper control)s See Valve page for parts breakdown.q See Knob page for parts breakdown.35E/45EValveWithout Independent Gripper Control35E/45EREF QTY PART NO.DESCRIPTION206942Valve Assembly11206943Valve Body21609453Fitting, 1031206991Solenoid Valve41206944Check Valve52659058Check Valve61677125Relief Valve71677124Relief Valve82601676Fitting, 6-693604511Fitting, 6-6104617915Fitting, 4-41112609234Fitting, 41212680Fitting, 6-6131206995Coil - 12V131206996Coil - 24V131206997Coil - 36V131206998Coil - 48V143667516Service Kit152669597Service Kit161667379Service KitControl KnobWithout Gripper ControlREF QTY PART NO.DESCRIPTION 206939Knob Group 11665250Snap Ring 21206986Cover 31667012Knob41665076Strain Relief 51677112s Switch 615902Nut, 3/8 NC 71665081Adapter81667718Cable Assembly 92667752Connector-Grays This switch may be purchased without wires. Order part number 665004. Soldering is required.35E/45Ec123456789GA0055.epsFaceplate Group35E/45EREF QTY PART NO.DESCRIPTION REF QTY PART NO.DESCRIPTION205970Faceplate Group 40" x 40" s205963Gripper Jaw Assembly q 11204634Faceplate 40" x 40" s 21205959Junction Block31206396Gripper Jaw42673385Drive Pin52682844Gripper Cylinder w 68617915Fitting, 4-472200877Drive Pin81206403Gripper Bar91672712Gripper Pad 1056444Lockwasher115768794Capscrew, M8x1,25x20-8.8 122604511Fitting, 6-6132686573Bearing142205957Hose152205958Hose162768710Capscrew172609234Plug, 4184779010Capscrew192763166Capscrew, M8x1,25x25-8.8 204 ---Stops Width x heigth.q Includes items 2 through 20.w See Gripper Cylinder page for parts breakdown.Gripper Cylinder682844Gripper Cylinder w 11646540Seal w 21636850Wiper w 312718O-Ring w 412710O-Ringw 51615122Back-Up Ring 61685662Shell 71685663Rod 81685664Retainer 91685665Piston 101563462Nut 111563916Ring121684284Snap Ring w 131663728Piston Seal35E/45EREF QTY PART NO.DESCRIPTIONwIncluded in Service Kit 684827.Do you have questions you need answered right now? Call your nearest Cascade Parts Department.Cascade (UK) Ltd.15, Orgreave Crescent Dore House Industrial Estate HandsworthSheffield S13 9NQEnglandTel: 742-697524FAX: 742-695121Cascade Scandinavia Hydraulik A.B.Muskötgatan 19, E8-9 S25466 Helsingborg SwedenTel: 42-151135FAX: 42-152997Cascade N.V. European Headquarters P.O. Box 30091300 El Almere Damsluisweg 561332 ED AlmereThe NetherlandsTel: 31-36-5492911 FAX: 31-36-5492964Cascade Norway Østerliveien 37A 1153 Oslo NorwayTel: 47-22-743160 FAX: 47-22-743157Cascade France S.A.R.L.11, Rue Jean CharcotZone Industrielle Sud orB.P. 2291421 Morangis CedexFranceTel: 1- 64547501FAX: 1-9790584Cascade Hispania S.A.Avenida De La Fabregada, 7Hospitalet De LlobregatBarcelonaSpainTel: 3-335-5158FAX: 3-335-4756Cascade Canada Inc.5570 Timberlea Blvd.Mississauga, OntarioCanada L4W-4M6Tel: 905-629-7777FAX: 905-629-7785Cascade GmbHD-41199 MonchengladbachKlosterhofweg 52GermanyTel: 21-66-602091FAX: 21-66-680947Cascade N.V.Benelux Sales and ServiceP.O. Box 30091300 El AlmereDamsluisweg 561332 ED AlmereThe NetherlandsTel: 31-36-5492950FAX: 31-36-5492974Cascade Finland01370 VantasFinlandTel: 358-0-836-1925FAX: 358-0-836-1935Cascade Corporation2501 Sheridan Avenue Springfield, OH 45505Tel:888-CASCADE (227-2233) FAX: 888-329-0234c Cascade Japan Ltd. 5-5-41,Torikai Kami Settsu, Osaka Japan, 566Tel: 81-726-53-3490 FAX: 81-726-53-3497Cascade KoreaRoom 508, Pum Yang Bldg. 750-14, Bang Bac-Dong Se-Cho Ku, SeoulKoreaTel: 2599-7131 ext. 512 FAX: 2533-8089HYCO-Cascade Pty. Ltd.1445 Ipswich RoadRocklea,Queensland 4107AustraliaTel: 3-274-2722FAX: 3-274-3456HYCO-Cascade (NZ) Ltd.15 Ra Ora Drive, East TamakiP.O. Box 38-440Howick, AucklandNew ZealandTel: 9-273-9136FAX: 9-273-9137Cascade (Africa) Pty. Ltd.P.O. Box 625, Isando 160060A Steel RoadSparton, Kempton ParkSouth AfricaTel: 975-9240FAX: 394-1147Cascade-Xiamen Wanshan No. 1 Workshop Huli RoadXiamen 361006Fujian, PRCTel: 592-562-4600 FAX: 592-562-4671Cascade (Singapore) Trading Co.Four Seasons Park Autumn Block - Apt. 1802 12 Cascaden Walk SingaporeTel: 65-834-1935FAX: 65-834-1936。