电子封装中的铝碳化硅及其应用
铝碳化硅为电子封装提供热管理解决方案
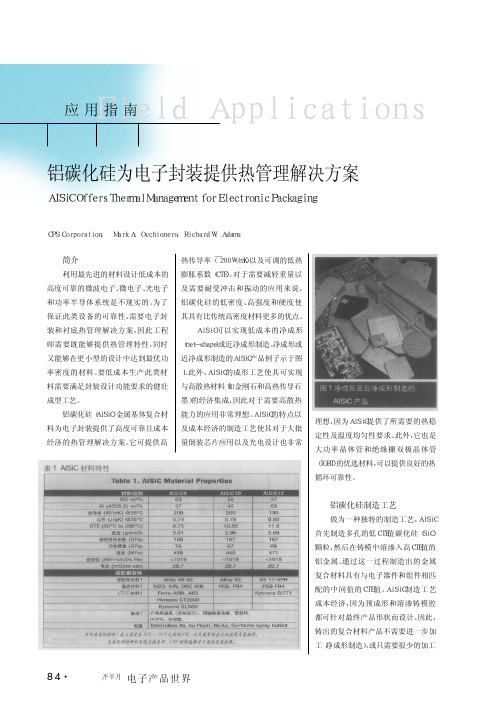
SiC/Al的比例。
AlSiC光电封装
AlSiC倒装焊盖板(flip chip lid)
光电封装的几何外形比倒装焊盖
AlSiC材料主要用于倒装焊盖板。 板要复杂,因此对于光学对准的图形
AlSiC是这一应用的理想材料,因为其 需要更为精确的尺寸控制。图 4就是
CTE 能够与介电衬底、陶瓷焊球阵列 AlSiC光电封装的例子。图中的所有封
设备也即将问世。结合几种特性于一
仅想钻几个洞,却发现为了一个需要
个可以放入口袋的小型装置中,需要
花费两分钟干的活,必须等上一个小
应用
大量的能量和功率,可以通过从电池
时以便打孔机充上电才能进行。如果
每一个人都习惯使用连接电缆去 外获得全部功率并中断自身电池,或
使用超级电容器,就不再会遇到这样 给电池充电,其实也可以使用一个已 者可以携带一个巨型的电池。一个可
在大功率和高可靠系统中,AlSiC 还被用于 IGBT 基板。大功率 IGBT 通 常安装在氮化铝衬底上。基板材料必 须与氮化铝的CTE值匹配,从而防止空 洞或剥离失效。事实表明,AlSiC基板 对于铜基板系统有很好的可靠性,耐 受成千上万次热循环也不会失效。尽 管AlSiC和铜具有相近的散热性能,但 铜的可靠性达不到1000次热循环。图4 是AlSiC功率器件衬底以及AlSiC IGBT 基板的实例,尺寸从 45 mm × 85 mm
简介 利用最先进的材料设计低成本的 高度可靠的微波电子、微电子、光电子 和功率半导体系统是不现实的。为了 保证此类设备的可靠性,需要电子封 装和衬底热管理解决方案,因此工程 师需要既能够提供热管理特性,同时 又能够在更小型的设计中达到最优功 率密度的材料。要低成本生产此类材 料需要满足封装设计功能要求的健壮 成型工艺。 铝碳化硅(AlSiC)金属基体复合材 料为电子封装提供了高度可靠且成本 经济的热管理解决方案。它可提供高
光量子芯片 铝碳化硅
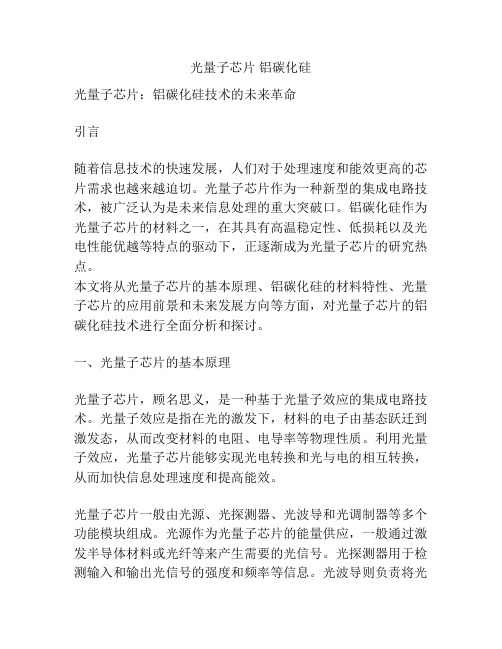
光量子芯片铝碳化硅光量子芯片:铝碳化硅技术的未来革命引言随着信息技术的快速发展,人们对于处理速度和能效更高的芯片需求也越来越迫切。
光量子芯片作为一种新型的集成电路技术,被广泛认为是未来信息处理的重大突破口。
铝碳化硅作为光量子芯片的材料之一,在其具有高温稳定性、低损耗以及光电性能优越等特点的驱动下,正逐渐成为光量子芯片的研究热点。
本文将从光量子芯片的基本原理、铝碳化硅的材料特性、光量子芯片的应用前景和未来发展方向等方面,对光量子芯片的铝碳化硅技术进行全面分析和探讨。
一、光量子芯片的基本原理光量子芯片,顾名思义,是一种基于光量子效应的集成电路技术。
光量子效应是指在光的激发下,材料的电子由基态跃迁到激发态,从而改变材料的电阻、电导率等物理性质。
利用光量子效应,光量子芯片能够实现光电转换和光与电的相互转换,从而加快信息处理速度和提高能效。
光量子芯片一般由光源、光探测器、光波导和光调制器等多个功能模块组成。
光源作为光量子芯片的能量供应,一般通过激发半导体材料或光纤等来产生需要的光信号。
光探测器用于检测输入和输出光信号的强度和频率等信息。
光波导则负责将光信号通过泳道或光纤传输到其他模块。
光调制器则利用光量子效应来控制光信号的幅度、频率或相位等特性。
通过这些功能模块的组合,光量子芯片能够实现高速数据传输和处理,从而为信息技术提供更快速、更高效的解决方案。
二、铝碳化硅的材料特性铝碳化硅是一种新兴的材料,在光量子芯片领域有着广阔的应用前景。
它具有多项优越特性,为光量子芯片的发展提供了有力支持。
首先,铝碳化硅具有高温稳定性,能够在高温环境下保持电学和光学性能的稳定。
这使得铝碳化硅材料非常适合用于高温环境下的信息处理和传输任务,如航空航天、军事领域等。
相比于传统的半导体材料,铝碳化硅能够更好地应对高能量密度和高温环境对芯片性能的要求。
其次,铝碳化硅具有低损耗特性,对光信号的传输和处理具有较低的能量损失。
这意味着铝碳化硅在实际应用中能够提供更高的能效和更低的功耗,从而节省能源和降低系统成本。
【精品文章】碳化硅粉体真正的高大上应用——碳化硅颗粒增强铝基复合材料

碳化硅粉体真正的高大上应用——碳化硅颗粒增强
铝基复合材料
与传统材料相比,颗粒增强金属基复合材料不仅兼有金属的高韧性、高塑性优点和增强颗粒的高硬度、高模量优点,而且材料各向同性,可采用传统的金属加工工艺进行加工。
碳化硅颗粒增强铝基复合材料的密度仅为钢的1/3,但其强度比纯铝和中碳钢都高,且还具有较高的耐磨性,可以在300℃~350℃的高温下稳定工作。
碳化硅颗粒增强铝基复合材料由碳化硅粉体和颗粒状的铝复合而成,增强颗粒在基体中的分布状态直接影响到铝基复合材料的综合性能。
能否使增强颗粒均匀分散在熔液中是能否成功制备铝基复合材料的关键,也是制备颗粒增强铝基复合材料的难点所在。
碳化硅颗粒分布的均匀与否与颗粒的大小、颗粒的密度、添加颗粒的体积分数、熔体的粘度、搅拌的方式和搅拌的速度等因素有关。
一、碳化硅增强铝基复合材料制备
1.压力铸造法。
压力铸造法制备碳化硅颗粒铝基复合材料的过程,主要包括碳化硅颗粒预制块的制备和液态铝合金在一定压力下渗入预制块中两部分。
碳化硅颗粒在复合材料中分布的均匀性由预制块中颗粒分布的均匀程度决定,并取决于预制块的制备工艺。
复合材料的孔隙率和SiCp/Al界面结合状态则与压铸工艺参数密切相关。
2.喷射共沉淀法。
喷射共沉积法具有碳化硅颗粒分布均匀、没有严重的界面反应、基体组。
铝碳化硅加工参数
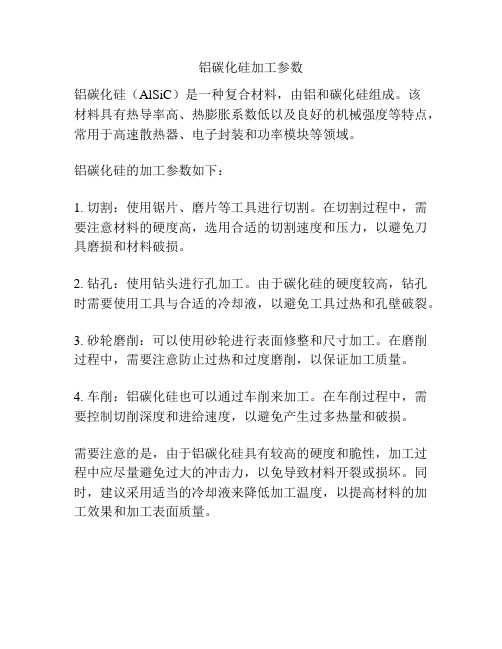
铝碳化硅加工参数
铝碳化硅(AlSiC)是一种复合材料,由铝和碳化硅组成。
该
材料具有热导率高、热膨胀系数低以及良好的机械强度等特点,常用于高速散热器、电子封装和功率模块等领域。
铝碳化硅的加工参数如下:
1. 切割:使用锯片、磨片等工具进行切割。
在切割过程中,需要注意材料的硬度高,选用合适的切割速度和压力,以避免刀具磨损和材料破损。
2. 钻孔:使用钻头进行孔加工。
由于碳化硅的硬度较高,钻孔时需要使用工具与合适的冷却液,以避免工具过热和孔壁破裂。
3. 砂轮磨削:可以使用砂轮进行表面修整和尺寸加工。
在磨削过程中,需要注意防止过热和过度磨削,以保证加工质量。
4. 车削:铝碳化硅也可以通过车削来加工。
在车削过程中,需要控制切削深度和进给速度,以避免产生过多热量和破损。
需要注意的是,由于铝碳化硅具有较高的硬度和脆性,加工过程中应尽量避免过大的冲击力,以免导致材料开裂或损坏。
同时,建议采用适当的冷却液来降低加工温度,以提高材料的加工效果和加工表面质量。
铝碳化硅
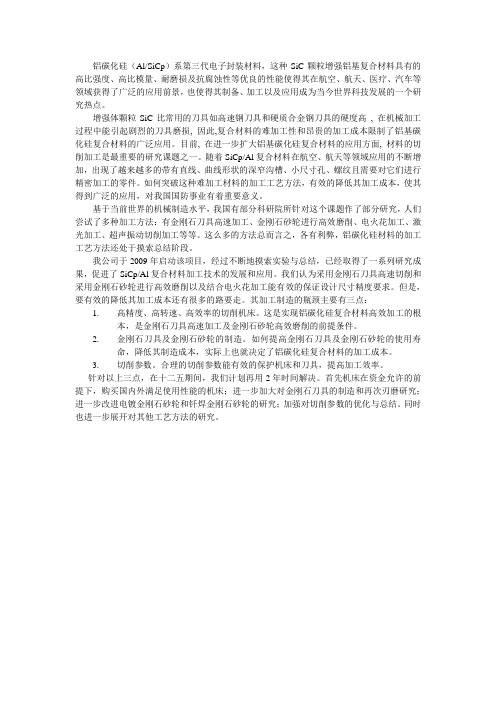
铝碳化硅(Al/SiCp)系第三代电子封装材料,这种SiC颗粒增强铝基复合材料具有的高比强度、高比模量、耐磨损及抗腐蚀性等优良的性能使得其在航空、航天、医疗、汽车等领域获得了广泛的应用前景,也使得其制备、加工以及应用成为当今世界科技发展的一个研究热点。
增强体颗粒SiC比常用的刀具如高速钢刀具和硬质合金钢刀具的硬度高, 在机械加工过程中能引起剧烈的刀具磨损, 因此,复合材料的难加工性和昂贵的加工成本限制了铝基碳化硅复合材料的广泛应用。
目前, 在进一步扩大铝基碳化硅复合材料的应用方面, 材料的切削加工是最重要的研究课题之一。
随着SiCp/Al复合材料在航空、航天等领域应用的不断增加,出现了越来越多的带有直线、曲线形状的深窄沟槽、小尺寸孔、螺纹且需要对它们进行精密加工的零件。
如何突破这种难加工材料的加工工艺方法,有效的降低其加工成本,使其得到广泛的应用,对我国国防事业有着重要意义。
基于当前世界的机械制造水平,我国有部分科研院所针对这个课题作了部分研究,人们尝试了多种加工方法:有金刚石刀具高速加工、金刚石砂轮进行高效磨削、电火花加工、激光加工、超声振动切削加工等等。
这么多的方法总而言之,各有利弊,铝碳化硅材料的加工工艺方法还处于摸索总结阶段。
我公司于2009年启动该项目,经过不断地摸索实验与总结,已经取得了一系列研究成果,促进了SiCp/Al复合材料加工技术的发展和应用。
我们认为采用金刚石刀具高速切削和采用金刚石砂轮进行高效磨削以及结合电火花加工能有效的保证设计尺寸精度要求。
但是,要有效的降低其加工成本还有很多的路要走。
其加工制造的瓶颈主要有三点:1.高精度、高转速、高效率的切削机床。
这是实现铝碳化硅复合材料高效加工的根本,是金刚石刀具高速加工及金刚石砂轮高效磨削的前提条件。
2.金刚石刀具及金刚石砂轮的制造。
如何提高金刚石刀具及金刚石砂轮的使用寿命,降低其制造成本,实际上也就决定了铝碳化硅复合材料的加工成本。
碳化硅材料的性质及其在电子行业的应用
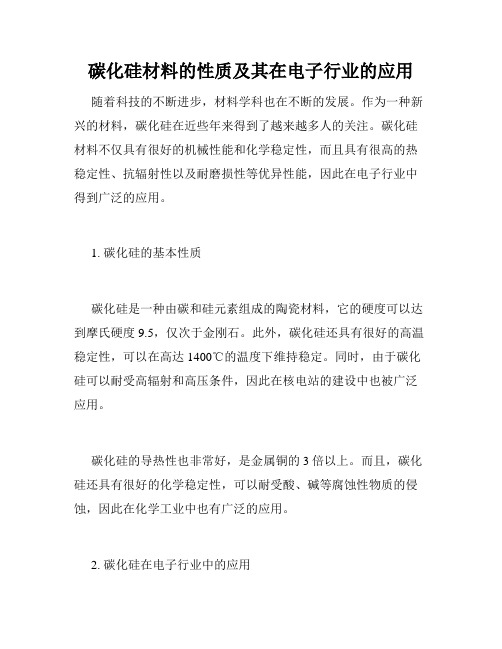
碳化硅材料的性质及其在电子行业的应用随着科技的不断进步,材料学科也在不断的发展。
作为一种新兴的材料,碳化硅在近些年来得到了越来越多人的关注。
碳化硅材料不仅具有很好的机械性能和化学稳定性,而且具有很高的热稳定性、抗辐射性以及耐磨损性等优异性能,因此在电子行业中得到广泛的应用。
1. 碳化硅的基本性质碳化硅是一种由碳和硅元素组成的陶瓷材料,它的硬度可以达到摩氏硬度9.5,仅次于金刚石。
此外,碳化硅还具有很好的高温稳定性,可以在高达1400℃的温度下维持稳定。
同时,由于碳化硅可以耐受高辐射和高压条件,因此在核电站的建设中也被广泛应用。
碳化硅的导热性也非常好,是金属铜的3倍以上。
而且,碳化硅还具有很好的化学稳定性,可以耐受酸、碱等腐蚀性物质的侵蚀,因此在化学工业中也有广泛的应用。
2. 碳化硅在电子行业中的应用碳化硅作为一种优异的材料,可以在电子行业中发挥重要的作用。
2.1 半导体材料碳化硅是一种带有半导体性质的材料,在电子学领域中可以用作半导体材料。
由于碳化硅可以较好的耐受高温和高辐射的情况,因此可以应用于高温、高频电子元件,如功率半导体器件,微波器件,以及其它类似元件。
在这些电子元件中,碳化硅可以提高器件的可靠性和寿命,并且可以有效的降低元器件的工作温度,提高元器件的工作效率。
2.2 光电子领域碳化硅在光电子领域中的应用很广泛。
碳化硅可以用作电光调制器、微波光子集成器件、光伏器件等。
同时,由于碳化硅具有优秀的耐腐蚀性能及透明性,使得它可以成为高温炉灯管电极、半导体中的夹层材料以及红外光学器件等的重要材料。
2.3 硬质涂层碳化硅的硬度仅次于金刚石,使得它可以用于生产硬质涂层。
硬质涂层可以提高机械零件的硬度和耐磨损性,从而减少因摩擦而带来的磨损和材料的损坏,延长使用寿命。
3. 结语随着科技的不断发展,新材料的出现将会引领新的潮流。
因此,不论是从基础的材料研究还是从应用层面上,都需要进一步加强碳化硅材料的相关研究。
铝材应用于电子设备散热与封装

铝材应用于电子设备散热与封装在当今科技飞速发展的时代,电子设备已经成为我们日常生活和工作中不可或缺的一部分。
从智能手机、平板电脑到笔记本电脑、台式电脑,再到各种服务器和数据中心,电子设备的性能和功能不断提升。
然而,随着电子设备性能的提高,其内部产生的热量也越来越多。
如果不能有效地散热,这些热量会严重影响电子设备的性能、稳定性和寿命。
因此,散热问题成为了电子设备设计和制造中的一个关键挑战。
在众多的散热材料中,铝材因其优异的性能而被广泛应用于电子设备的散热与封装。
一、铝材在电子设备散热中的优势1、良好的导热性能铝材具有良好的导热性能,其热导率约为 200-237 W/(m·K),远高于许多常见的工程材料。
这意味着铝材能够快速地将电子设备内部产生的热量传递到外部环境中,从而有效地降低设备内部的温度。
2、轻质高强度与其他金属材料相比,铝材具有较低的密度,这使得采用铝材制造的散热部件重量较轻,不会给电子设备带来过多的负担。
同时,铝材还具有较高的强度,能够满足电子设备在使用过程中的机械性能要求。
3、良好的加工性能铝材易于加工成型,可以通过压铸、挤压、冲压等多种工艺制造出各种形状和结构复杂的散热部件,如散热片、散热管等。
此外,铝材还可以进行表面处理,如阳极氧化等,以提高其耐腐蚀性和美观度。
4、成本相对较低相比于一些高性能的散热材料,如铜、银等,铝材的价格相对较低。
这使得铝材在大规模生产的电子设备中具有较高的性价比,能够有效地降低电子设备的制造成本。
二、铝材在电子设备散热中的应用形式1、散热片散热片是电子设备中最常见的散热部件之一,通常由铝材制成。
散热片的作用是通过增加与空气的接触面积,提高热量的散发效率。
铝材散热片可以采用压铸、挤压或冲压等工艺制造,其形状和结构可以根据电子设备的散热需求进行设计。
2、散热管散热管是一种高效的散热部件,通常由铝材制成。
散热管内部通常填充有冷却液或相变材料,通过液体的流动或相变过程来传递热量。
铝碳化硅导热率
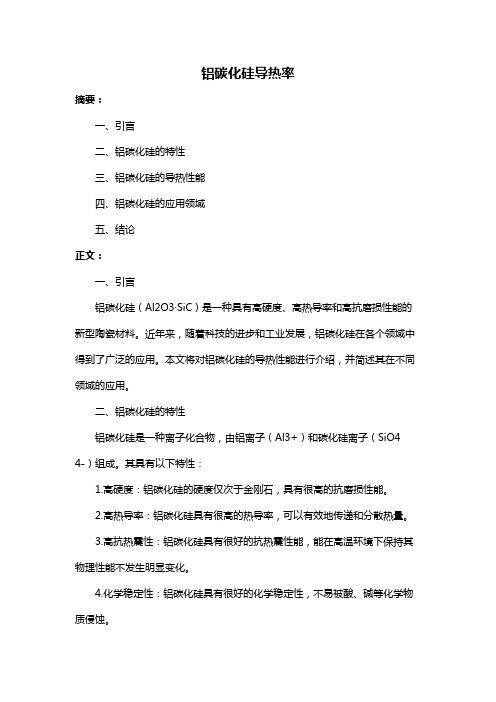
铝碳化硅导热率摘要:一、引言二、铝碳化硅的特性三、铝碳化硅的导热性能四、铝碳化硅的应用领域五、结论正文:一、引言铝碳化硅(Al2O3·SiC)是一种具有高硬度、高热导率和高抗磨损性能的新型陶瓷材料。
近年来,随着科技的进步和工业发展,铝碳化硅在各个领域中得到了广泛的应用。
本文将对铝碳化硅的导热性能进行介绍,并简述其在不同领域的应用。
二、铝碳化硅的特性铝碳化硅是一种离子化合物,由铝离子(Al3+)和碳化硅离子(SiO4 4-)组成。
其具有以下特性:1.高硬度:铝碳化硅的硬度仅次于金刚石,具有很高的抗磨损性能。
2.高热导率:铝碳化硅具有很高的热导率,可以有效地传递和分散热量。
3.高抗热震性:铝碳化硅具有很好的抗热震性能,能在高温环境下保持其物理性能不发生明显变化。
4.化学稳定性:铝碳化硅具有很好的化学稳定性,不易被酸、碱等化学物质侵蚀。
三、铝碳化硅的导热性能铝碳化硅具有很高的热导率,其热导率一般在100-250 W/(m·K)之间,远高于普通陶瓷材料。
这使得铝碳化硅在高温环境下能够有效地传递和分散热量,从而保证了其良好的热稳定性和可靠性。
四、铝碳化硅的应用领域铝碳化硅的高热导率、高硬度和化学稳定性使其在许多领域具有广泛的应用前景,主要包括以下几个方面:1.电子器件:铝碳化硅可应用于高功率电子器件的散热,如功率放大器、微波器件等。
2.工业炉具:铝碳化硅的高热导率使其成为优良的工业炉具材料,可提高炉具的热效率和使用寿命。
3.汽车发动机:铝碳化硅可用于汽车发动机的散热,降低发动机温度,提高发动机的性能和寿命。
4.核反应堆:铝碳化硅具有很好的抗辐射性能,可用于核反应堆的结构材料和散热材料。
5.航空航天:铝碳化硅的高热导率和抗磨损性能使其在航空航天领域具有广泛的应用,如火箭发动机喷口、导弹鼻锥等。
五、结论铝碳化硅作为一种具有高热导率、高硬度和化学稳定性的新型陶瓷材料,在电子器件、工业炉具、汽车发动机、核反应堆和航空航天等领域具有广泛的应用前景。
2024年新型铝基碳化硅复合材料市场规模分析
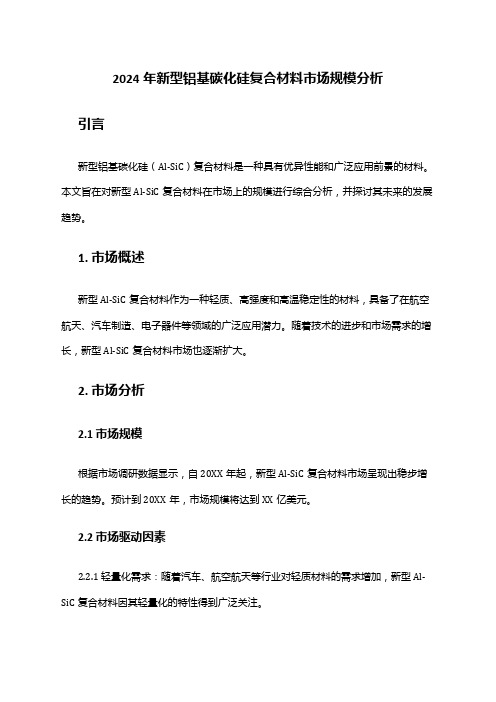
2024年新型铝基碳化硅复合材料市场规模分析引言新型铝基碳化硅(Al-SiC)复合材料是一种具有优异性能和广泛应用前景的材料。
本文旨在对新型Al-SiC复合材料在市场上的规模进行综合分析,并探讨其未来的发展趋势。
1. 市场概述新型Al-SiC复合材料作为一种轻质、高强度和高温稳定性的材料,具备了在航空航天、汽车制造、电子器件等领域的广泛应用潜力。
随着技术的进步和市场需求的增长,新型Al-SiC复合材料市场也逐渐扩大。
2. 市场分析2.1 市场规模根据市场调研数据显示,自20XX年起,新型Al-SiC复合材料市场呈现出稳步增长的趋势。
预计到20XX年,市场规模将达到XX亿美元。
2.2 市场驱动因素2.2.1 轻量化需求:随着汽车、航空航天等行业对轻质材料的需求增加,新型Al-SiC复合材料因其轻量化的特性得到广泛关注。
2.2.2 高温稳定性需求:新型Al-SiC复合材料具有出色的高温稳定性和耐腐蚀性能,可以满足高温工作环境下的需求,因此在航空、电子等领域有较大的市场需求。
2.2.3 环保要求:近年来,全球各地对环境友好型材料的需求不断增加,新型Al-SiC复合材料以其低碳排放、可回收利用等特点受到市场青睐。
2.3 市场障碍因素2.3.1 制造成本高:新型Al-SiC复合材料的制造过程涉及到复杂的工艺和原材料,导致制造成本较高,限制了其市场规模的进一步扩大。
2.3.2 技术难题:新型Al-SiC复合材料的制备和加工技术相对复杂,需要高端设备和专业技术支持,制约了其应用的广泛程度。
2.3.3 替代品竞争:虽然新型Al-SiC复合材料在某些领域有独特的优势,但同类型的替代材料在市场上仍具有一定竞争力,这也限制了其市场份额的进一步增长。
3. 市场前景展望未来,随着新型Al-SiC复合材料制备工艺的不断革新和技术水平的提升,以及相关行业对该材料的需求持续增长,预计市场规模将继续扩大。
同时,新型Al-SiC复合材料的制造成本也有望逐渐下降,为其进一步的市场普及创造条件。
铝碳化硅材料应用LED

随着LED制造技术的飞跃以及器件更高性能的要求,对封装材料提出了更新、更高的要求,传统材料不再适用于高功率密度器件的封装。
过去大量使用的铝、铜、可伐或半导体材料等不能达到良好的导热指标和轻便的要求,而且成本较高,已不能满足这种高功率密度的需要。
这使得电子器件热管理问题成为瓶颈。
电子器件热管理问题得不到很好的解决,会导致电子器件的热失效,从而造成封装体与芯片因受热膨胀而开裂,芯片散热性不佳而停止工作。
当两种接触材料的热膨胀系数差异达到12ppm/K时,仅100次热循环就会出现热疲劳失效,在大功率LED应用中,高亮度产品的电流量提高(电流由早期0.3A发展到目前约1A)或因其高功率(由早期1W发展到目前约可达5W)致使单位面积高热量产生。
目前光电转换效率,每100%的能源只有约20%产生光,而有80%的能源变为热能损耗,因此热量是能源最大的消耗。
但同时若不移除多余的热能,则LED 使用寿命及效能将折损。
为了保证此类设备的可靠性,就需要解决热管理这个问题。
解决这一瓶颈最好的方法就是通过改变提高封装材料的性能。
一、大功率LED照明光源需要解决的散热问题大功率LED芯片在工作时就会产生大量的热量。
如何将产生的热量散发出去,保证一定环境温度条件下能长期正常工作显得尤为重要,解决好热耗散是大功率器件封装的关键。
大功率LED照明光源需要解决的散热问题涉及以下几个环节:1、晶片PN结到外延层;2、外延层到封装基板;3、封装基板到散热器4、散热器到空气为了取得好的导热效果,提高对流散热。
LED发出的热量通过导热硅脂/焊锡传递给基板,再通导热硅脂传递给铝散热器再将热量通过辐射和对流的方式带到周围的空气中,将热量排除,形成从LED芯片通过导热硅脂和铝基板到周围空气的散热通路。
材料热传导性能的一个很重要的指标是热阻,热阻是指热量传递通道上两个参点之间的温度差与两点间热量传递速率的比值。
越短的热传导距离、越大的截面积、越高的热传导系数对热阻的降低越有利,这就要求设计合理的封装结构和选择合适的材料。
铝碳化硅产品设计及应用

铝碳化硅介绍及产品设计西安创正新材料公司是一家集研发、生产和销售为一体的高科技企业。
主要致力于第三代电子封装材料——铝碳化硅的研发、生产与销售,根据用户需求,开发了多种AlSiC产品,为微波器件、大功率器件、微电子器件等制造商提供专业的热管理材料及技术方案。
公司产品广泛应用于轨道交通、新能源汽车、航空航天、军事等领域,是新一代大功率电子器件最佳选择。
公司将持续加强与用户的交流与合作,不断满足国内外用户的市场需求,力争以先进的工艺技术、严格的质量管控、一流的性能水平、最高的性价比优势服务用户、持续为客户创造价值。
铝碳化硅介绍铝碳化硅 AlSiC (Al/SiC, SiC/Al) 是一种颗粒增强铝基复合材料,采用铝合金作为基体,SiC作为增强体,充分结合了陶瓷和金属铝的不同优势,实现了封装了轻便化、高密度化等要求。
AlSiC密度在2.95~3.1g/cm³之间,热膨胀系数(CTE)6.5~9ppm/℃,具有可调的体积分数,提高碳化硅体积分数可以使材料的热膨胀系数显著降低。
同时,铝碳化硅还具有高的热导率和比刚度,表面能够镀镍、金、银、铜,具有良好的镀覆性能。
铝碳化硅复合材料的比刚度是所有电子材料中最高的:是铝的3倍,W-Cu 和Kovar 的5倍,铜的25倍,另外铝碳化硅的抗震性好,因此是恶劣环境(震动较大,如航天、汽车等领域)下的首选材料。
铝碳化硅复合材料已成为航空航天、国防、功率模块和其他电子元器件所需求的新型封装材料。
用于航空航天微波、功率放大模块等电子器件及模块的封装壳体或底座。
与其他材料性能对比:材料成分密度(g/cm3) 热膨胀系数(10-6/K)热导率(W/mK)AlSiC Al+(50%-70%)SiC 3.05 6-9 180-240 CuW W+(10%-20%)Cu 15.6-17.0 6.5-8.3 180-200 CuMo Mo+(15%-20%)Cu 10.00 7.0-8.0 160-170 AlSi 50%Al+50Si 2.55 11.4 126 Kovar Fe+Ni 8.10 5.9 17Cu 8.96 17.8 398Al 2.70 23.6 238Si 2.30 4.2 151 GaAs 5.23 6.5 54Al2O3 3.60 6.7 17BeO 2.90 7.6 250AlN 98%purity 3.30 4.5 160-200铝碳化硅产品设计◆板类产品用 AlSiC 制成各种板类的产品,用于各类电路的热沉、基板、封盖、过渡片等,可替代目前在使用的氧化铍、氮化铝、钼片、钨铜合金及其它金属材料。
铝碳化硅材料
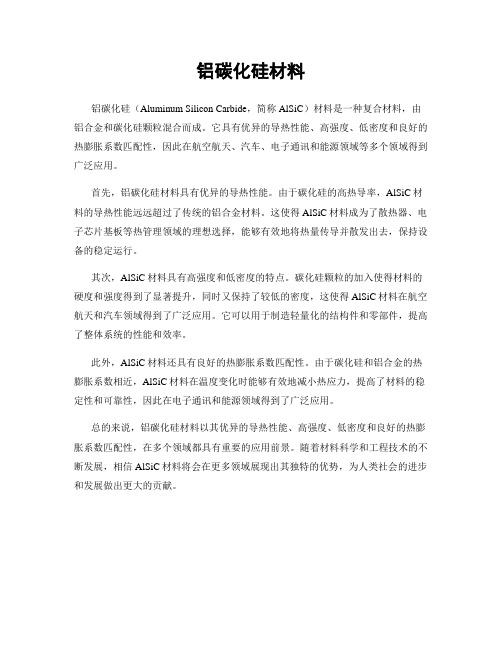
铝碳化硅材料
铝碳化硅(Aluminum Silicon Carbide,简称AlSiC)材料是一种复合材料,由铝合金和碳化硅颗粒混合而成。
它具有优异的导热性能、高强度、低密度和良好的热膨胀系数匹配性,因此在航空航天、汽车、电子通讯和能源领域等多个领域得到广泛应用。
首先,铝碳化硅材料具有优异的导热性能。
由于碳化硅的高热导率,AlSiC材料的导热性能远远超过了传统的铝合金材料。
这使得AlSiC材料成为了散热器、电子芯片基板等热管理领域的理想选择,能够有效地将热量传导并散发出去,保持设备的稳定运行。
其次,AlSiC材料具有高强度和低密度的特点。
碳化硅颗粒的加入使得材料的硬度和强度得到了显著提升,同时又保持了较低的密度,这使得AlSiC材料在航空航天和汽车领域得到了广泛应用。
它可以用于制造轻量化的结构件和零部件,提高了整体系统的性能和效率。
此外,AlSiC材料还具有良好的热膨胀系数匹配性。
由于碳化硅和铝合金的热膨胀系数相近,AlSiC材料在温度变化时能够有效地减小热应力,提高了材料的稳定性和可靠性,因此在电子通讯和能源领域得到了广泛应用。
总的来说,铝碳化硅材料以其优异的导热性能、高强度、低密度和良好的热膨胀系数匹配性,在多个领域都具有重要的应用前景。
随着材料科学和工程技术的不断发展,相信AlSiC材料将会在更多领域展现出其独特的优势,为人类社会的进步和发展做出更大的贡献。
电子封装用硅铝合金的应用研究

n i q u e s o f S i / A1 ll a o y or f h e m e r t i c p a c k a g i n g a r e i n t r o d u c e d .A t l a s t ,t h e e x i s t i n g p r o b l e ms a n d t h e d e v e l o p — me n t t r e n d o f h o me ma d e S i / AI a l l o y a r e p o i n t e d o u t .W i t h t h e d e v e l o p me n t o f ma n u f a c t u i r n g a n d p r o c e s s i n g t e c h n i q u e s i n o u r c o u n t r y, t h e h o me ma d e S i / A1 ll a o y w i l l b e w i d e l y u s e d i n e l e c t r o n i c p a c k a g i n g i n d u s t r y .
第2 9卷第 4期
2 0 1 3年 8月
电 子 机 械 工 程
El e c t r o- M e c ha ni c a l Eng i ne e r i ng
Vo 1 . 2 9. No . 4
Au g .2 01 3
电子封装 用硅铝合金 的应用研究
郝新锋 , 朱小军 , 严 伟
1 S i / A l 合 金 的 制 备
目前 , 电子 封 装 用 S i / A 1 合 金 材 料 主 要 的制 备 方 法有喷射成形法 、 粉末冶金法 、 压力熔渗法等。其 中相 对 成 熟度 和 市场 占有 率 最 高 的是 英 国 O s p r e y公 司 开 发的O s p r e y 工艺 , 它采 用 喷射 沉积 + 热 等 静 压 的方 法
新型材料在半导体领域中的应用

新型材料在半导体领域中的应用随着现代科学技术的不断发展,半导体技术在现代电子通信、计算机、航天等领域中得到了广泛的应用。
新型材料的涌现和半导体技术的不断提升,为半导体领域的发展带来了新的机遇和挑战。
本文将主要探讨新型材料在半导体领域中的应用,以及这些应用将带来的发展前景。
一、新型材料在半导体领域的应用1. 碳化硅材料碳化硅是一种新型材料,其特殊性质和高温、高频等特点使其在半导体领域中得到广泛应用。
碳化硅在电力电子、航空航天、电动汽车和新能源行业等领域中应用广泛。
在半导体领域,碳化硅材料代替传统的硅材料,可大幅提高功率半导体器件的效率。
因其导电性、热稳定性以及高温抗氧化性等特点,碳化硅材料正逐渐成为新一代半导体材料的主流。
2. 氧化铝陶瓷材料氧化铝是一种具有高温、高硬度、耐腐蚀等特性的陶瓷材料。
在半导体行业中,氧化铝常用作介电材料,用以制造高温稳定性和降低半导体器件的噪声。
在现代电子、通讯、计算机等领域,氧化铝陶瓷材料广泛应用于微电子、光电子等器件的制造。
因其绝缘性能良好,无法导电,且具有高硬度、低离子蒸汽压等性质,能够很好地保护电路板,维持电路板的机械稳定性和电性性能。
3. 磷化铝镓材料磷化铝镓是一种半导体功能材料,其性能稳定,在高频率和高能量时有较高的反应能力。
常用于制造高功率、高速度的半导体芯片,如微波功率放大器、太赫兹探测器和高频振荡器等领域。
磷化铝镓材料的特点是具有极高的电子迁移率,这使得这种材料在制造高速半导体器件时很有优势。
由于具有优异的电性能,磷化铝镓材料是开发高效率光纤通信系统的重要材料之一。
二、新型材料在半导体领域中的发展前景随着智能制造、云计算和物联网等技术的发展,半导体技术在互联网、电子商务、娱乐、体育等领域中得到越来越广泛的应用。
新型材料在半导体领域中的发展前景也越来越受到关注。
1. 提高半导体器件的性能和质量新型材料不仅可以提高半导体器件的性能,还可以提高器件的可靠性、寿命等。
微电子封装热沉材料铝碳化硅
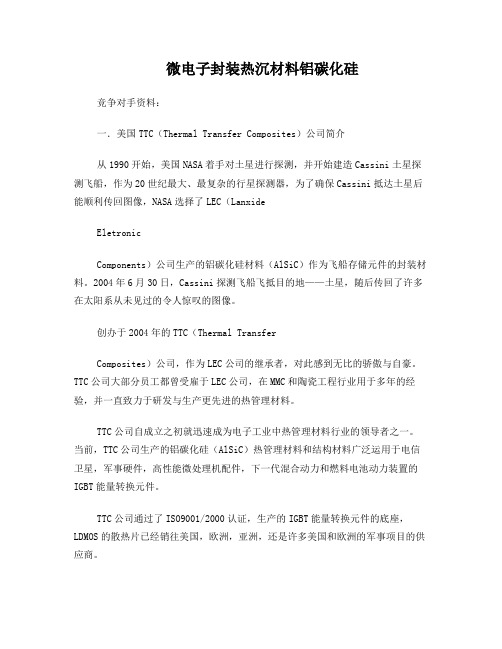
微电子封装热沉材料铝碳化硅竞争对手资料:一.美国TTC(Thermal Transfer Composites)公司简介从1990开始,美国NASA着手对土星进行探测,并开始建造Cassini土星探测飞船,作为20世纪最大、最复杂的行星探测器,为了确保Cassini抵达土星后能顺利传回图像,NASA选择了LEC(LanxideEletronicComponents)公司生产的铝碳化硅材料(AlSiC)作为飞船存储元件的封装材料。
2004年6月30日,Cassini探测飞船飞抵目的地——土星,随后传回了许多在太阳系从未见过的令人惊叹的图像。
创办于2004年的TTC(Thermal TransferComposites)公司,作为LEC公司的继承者,对此感到无比的骄傲与自豪。
TTC公司大部分员工都曾受雇于LEC公司,在MMC和陶瓷工程行业用于多年的经验,并一直致力于研发与生产更先进的热管理材料。
TTC公司自成立之初就迅速成为电子工业中热管理材料行业的领导者之一。
当前,TTC公司生产的铝碳化硅(AlSiC)热管理材料和结构材料广泛运用于电信卫星,军事硬件,高性能微处理机配件,下一代混合动力和燃料电池动力装置的IGBT能量转换元件。
TTC公司通过了ISO9001/2000认证,生产的IGBT能量转换元件的底座,LDMOS的散热片已经销往美国,欧洲,亚洲,还是许多美国和欧洲的军事项目的供应商。
TTC公司在金属模板和陶瓷工程行业拥有超过70年的经验,公司上下一心,一直致力于不断提高cuttingedge技术,不断研发新产品,并且把完善客户服务作为一种嗜好,通过这些方面的努力,公司完全有能力为客户提供最高质量的产品,有能力迎接当前和未来在热管理方面的挑战。
在以往,电子工业中的导热和结构方面的问题都是单独依靠金属或者陶瓷来解决,经常影响产品的性能和限制设计方案。
TTC公司生产的铝碳化硅材料为解决这些问题提供了一条全新的思路。
应用铝碳化硅散热基板的LED高性能COB封装

应用铝碳化硅散热基板的LED高性能COB封装随着LED功率化的发展,LED的功率要求不断增大,体积不断减小,集成度越来越大,因此对LED器件的性能要求越来越高。
传统封装基板由于各自的缺点难于满足功率越来越大的COB封装要求,而AlSiC复合基板具有高热导率、热膨胀系数可调等优势,在LED封装中应用越来越广泛;另外,COB光源中出光效率较低以及工作热量大等问题也制约了其发展。
本文研究了AlSiC复合基板的制备方法和性能表征。
采用模压成型的方法制备多孔SiC预制件,研究了造孔剂含量和模压成型压力对孔隙率的影响,研究结果表明了造孔剂含量在5%-14%之间时,孔隙率会随着造孔剂含量的增多大致呈线性增加;而成型压力越大,预制件的孔隙率就越小,其中造孔剂含量达到14%时,孔隙率超过40%,满足真空压力浸渗的需要。
通过显微和物相分析,从结果中得知,采用真空压力浸渗的方法制备AlSiC 复合基板,SiC与Al混合均匀,结合良好,并很好地控制了界面的反应,Al4C3等有害相没有出现在测试结果中。
通过优化参数,最终制备得到的AlSiC复合基板的热导率可达171.6W/m¤K,平均热膨胀系数为7.00*10-6℃-1,性能符合LED COB封装的要求。
AlSiC复合基板制备完毕后,加工成图形化基板,进而研究其对COB光源出光效率的影响。
联合软件SolidWorks和TracePro进行光学仿真模拟,对图形化基板中的倒锥型凹槽的间距、倾角和半径进行优化,并得出最佳参数为间距0.75mm、倾角60o和半径为0.7mm,此时出光效率提高14.99%,其中倾角的最佳参数与理论计算相吻合。
另外,利用数控机床将AlSiC复合基板加工成图形化基板,并与传统基板的COB光源进行出光效率的对比,结果表明陶瓷基板的光源出光效率最低,AlSiC 复合基板其次,图形化AlSiC复合基板制备的COB光源光效最高,与平面AlSiC 复合基板相比,出光效率提高了13.68%,与仿真模拟结果较为接近。
- 1、下载文档前请自行甄别文档内容的完整性,平台不提供额外的编辑、内容补充、找答案等附加服务。
- 2、"仅部分预览"的文档,不可在线预览部分如存在完整性等问题,可反馈申请退款(可完整预览的文档不适用该条件!)。
- 3、如文档侵犯您的权益,请联系客服反馈,我们会尽快为您处理(人工客服工作时间:9:00-18:30)。
4封装AlSiC制备
SiC颗粒与Al有良好的界面接合强度,复合后的CTE随SiC含量的变化可在一定范围内进行调节。由此决定了产品的竞争力,相继开发出多种制备方法。用于封装AlSiC预制件的SiC颗粒大多在1μm-80μm范围选择,要求具有低密度、低CTE,高弹性模量等特点,其热导率因纯度和制作方法的差异在80W(m·K)-200W(m·K)之间变化。基体是强度的主要承载体,一般选用6061、6063、2124、A356等高强度Al合金,与SiC按一定比例和不同工艺结合成AlSiC,解决SiC与Al润湿性差,高SiC含量难于机加工成型等问题,成为理想的中管芯所产生的热量主要通过基板材料传导到外壳而散发出去,上世纪九十年代中期,AlSiC已用作功率放大器的基板,通过修改金属Al和SiC颗粒的比例,来匹配裸芯片或衬底的CTE值,从而防止空洞或剥离失效。事实表明,AlSiC基板对于Cu基板系统有很好的可靠性,耐受成千上万次热循环也不会失效,而Cu的可靠性达不到1000次热循环,这从根本上解决功率器件散热问题,成为重要的功率器件封装材料。
制备500vol%-75vol%SiC高含量的封装用AlSiC多采用熔渗法,其实质是粉末冶金法的延伸。它通过先制备一定密度、强度的多孔基体预制件,再渗以熔点比其低的进入填充预制件,其理论基础是在金属液润湿多孔基体时,在毛细管力作用下,金属液会沿颗粒间隙流动填充多孔预制作孔隙,脱模无须机械加工,在其表面上覆盖有一层0.13mm-0.25mm厚的完美Al合金层,按用途电镀上Ni、Au、Cd、Ag,供封装用。
AlSiC封装材料产业化引起国内科研院所、大学等单位的广泛重视,积极着手研发其净成形工艺,部分单位研制成功样品,为AlSiC工业化生产积累经验,离规模化生产尚有一定距离,存在成本高、SiC体积含量不高、低黏度、55%-75%高体积分浆料的制备与浆粒原位固化技术等问题。
5封装AlSiC的应用
IC产业的发展与其设计、测试、流片、封装等各环节密切相连,最终在市场应用中体现价值认同,良性循环形成量产规划,实现经济效益。封装技术至关重要,尤其是军用产品一致采用金属封装,陶瓷封装结构,确保旗杆、模块、组件、系统的整体可靠性的金属封装气密性高,散热性好,形状可多样化,有圆形、菱形、扁平形、浅腔与深腔形等,其材料难以满足当今航空航天、舰船、雷达、电子战、精确打击、天基和海基系统对大功率、微波器件封装的需求。按目前VLSI电路功耗的同一方法计算,未来的SoC芯片将达到太阳表面温度,现有的设计和封装方法已不能满足功率SoC系统的需求。AlSiC恰好首先在这一领域发挥作用,现以军用为主,进而推向其他市场。
常用金属封装材料与CaAs的微波器件封装需求存在性能上的差距,使得研发一种新型轻质金属封装材料,满足航空航天用器件封装成为急需,引发相关部门调试重视。经过近些年来的深入研究,AlSiC取得产业化进展,相继推动高硅铝合金Si/Al实用化进程,表2示出其主要性能与常用封装材料的对比。将SiC与Al合金按一定比例和工艺结合成AlSiC后,可克服目前金属封装材料的不足,获得高K值、低CTE、高强度、低密度导电性好的封装材料。
5.1 T/R模块封装
机载雷达天线安装在飞机万向支架上,采用机电方式扫描,其发展的重要转折点是从美国F-22开始应用有源电子扫描相控阵天线AESA体制,其探测距离如表5所示,研发出多种AESA系统。例如,APG-80捷变波束雷达、多功能机头相控阵一体化航电系统、到功能综合射频系统、综合式射频传感器系统、JSF传感器系统等,所用T/R(发/收)模块封装技术日趋成熟,每个T/R模块成本由研发初期的10万美元降至600-800美言,数年内可降至约200美元,成为机载雷达的核心部分。几乎所有的美国参战飞机都有安装新的或更新AESA计划,使其作战效能进一步发挥,作多目标威胁环境中先敌发现、发射、杀伤,F-22机载AESA雷达可同时探测跟踪目标数分别为空中30个、地面16、探测范围为360度全周向。
AESA由数以千计的T/R模块(有的高达9000个左右)构成,在每个T/R模块内部都有用GaAs技术制作的功率发射放大器、低噪声接受放大器、T/R开关、多功能增益/相位控制等电路芯片,最终生产关键其封装技术上,因机载对其体积与重量的限制极为苛刻。AlSiC集低热胀、高导热、轻质于一体,采用AlSiC外壳封装T/R模块,包括S、C、X、Ku波段产品,可满足实用需求。雷达APG-77是一部典型多功能、多工作方式雷达,其AESA直径约1m,用2000个T/R模块构成,每个T/R模块输出功率10W,移相器6位,接受噪声系数2.9dB,体积6.4cm3,重14.88g,平均故障间隔MTBF20万h,其发射功率比初期产品增加16倍,接受噪声系数降低1倍,体积重量减少83%,成本下降82%。以1000个T/R模块构成机载AESA雷达为例,用AlSiC替代Kovar,雷达重量可减轻34kg,而热导率比Kovar提高10余倍,且提高整机可靠性MTBF达2000h以上。试验表明,及时AESA中10%的T/R模块产生故障,对系统无显著影响,30%失效时,仍可维持基本工作性能,具有所谓的"完美降级"能力。
宽禁带半导体SiC、GaN在芯片制造中的应用显示出很强的竞争优势,已制作高纯度100mm-150mm的GaN圆片,在单位面积上可产生比其他器件高6倍的功率,带宽达到1GHz-40GHz。功率半导体和集成功率模块技术方兴未艾,AlSiC封装材料大有发展前景。
5.2倒装芯片封装
倒装芯片封装FCP技术优势在于能大幅度提高差别的电性能、散热效能,适合高引脚数、高速、多功能的器件。AlSiC的CTE能够与介电衬底、焊球阵列、低温烧结陶瓷以及印刷电路板相匹配,同时其具有高热传导率、高强度和硬度,是倒装焊盖板的理想材料,为芯片提供高可靠保护。AlSiC可制作出复杂的外形,例如,AlSiC外壳产品有多个空腔,可容纳多块芯片,用于提供器件连接支柱、填充材料的孔以及不同的凸缘设计。AlSiC外形表面支持不同的标识和表面处理方法,包括激光打印、油漆、油墨、丝网印刷、电镀,完全满足FCP工艺要求。
熔渗法是AlSiC制备的关键,一般分为有压力渗透和无压力渗透,前者根据生产过程中压力施加的大小,方式的不同,又分为挤压熔渗、气压压力熔渗、离心熔渗铸造法等,主要特点是需要真空和高压设备,渗透时间较短,有效控制Al与SiC的界面反应,同时与精度的模具相配套,获得适用性发展。后者是将Al合锭放置在SiC预制件上,在合金熔点以上保温,Al合金液依托毛细管力的作用自发渗入预制件中,所需设备简单,予以低成本制备,但产品的机械性能与热性能略低,对基体合金的成份有较为严格的要求,浸透需要在保护气氛中进行。粉末冶金法对SiC体积分数可在15%-75%之间调节,SiC承载量大,但较难实现材料的一次成形。
从产业化趋势看,AlSiC可实现低成本的、无须进一步加工的净成形(net-shape)或需少量加工的近净成形制造,还能与高散热材料(金刚石、高热传导石墨等)的经济性并存集成,满足大批量倒装芯片封装、微波电路模块、光电封装所需材料的热稳定性及散温度均匀性要求,同时也是大功率晶体管、绝缘栅双极晶体管的优选封装材料,提供良好的热循环及可靠性。
此外,AlSiC可将多种电子封装材料并存集成,用作封装整体化,发展其他功能及用途。研制成功将高性能、散热快的Cu基封装材料块(Cu-金刚石、Cu-石墨、Cu-BeO等)嵌入SiC预制件中,通过金属Al熔渗制作并存集成的封装基片。在AlSiC并存集成过程中,可在最需要的部位设置这些昂贵的快速散热材料,降低成本,扩大生产规模,嵌有快速散热材料的AlSiC倒装片系统正在接受测试和评估。另外,还可并存集成48号合金、Kovar和不锈钢等材料,此类材料或插件、引线、密封环、基片等,在熔渗之前插入SiC预成型件内,在AlSiC复合成形过程中,经济地完成并存集成,方便光电器件封装的激光连接。
3封装AlSiC类型
封装金属基复合材料的增强体有数种,SiC是其中应用最为广泛的一种,这是因为它具有优良的热性能,用作颗粒磨料技术成熟,价格相对较低;另一方面,颗粒增强体材料具有各向同性,最有利于实现净成形。AlSiC特性主要取决于SiC的体积分数(含量)及分布和粒度大小,以及Al合金成份。依据两相比例或复合材料的热处理状态,可对材料热物理与力学性能进行设计,从而满足芯片封装多方面的性能要求。其中,SiC体积分数尤为重要,实际应用时,AlSiC与芯片或陶瓷基体直接接触,要求CTE尽可能匹配,为此SiC体积百分数vol通常为50%-75%,表3示出某厂家产业化净成形AlSiC级别的详细情况。
在长期使用中,许多封装尺寸、外形都已经标准化、系统化,存在的主要缺陷是无法适应高性能芯片封装要求。例如,Kovar(一种Fe-Co-Vi合金)和Invar(一种Fe-Ni合金)的CTE低,与芯片材料相近,但其K值差、密度高、刚度低,无法全面满足电子封装小型化、高密度、热量易散发的应用需求合金是由两种或两种以上的金属元素或金属与非金属元素所组成的金属材料,具有其综合的优势性能。随之发展的Mo80 Cu20、Cu/Invar/Cu、Cu/Mo/Cu等合金在热传导方面优于Kovar,但期比重大于Kovar,仍不适合用作航空航天所需轻质的器件封装材料。
在国内,随着AESA产品的定型,T/R模块出现批量生产需求,其基板、壳体的生产极为关键,采用近净成形技术,研制出小批量T/R模块封装外壳样品。用无压熔渗AlSiC制作基座替代W-Cu基座,封装微波功率器件,按GJB33A-97和GJB128A-97军标严格考核,器件的微波性能、热性能无变化,可完全满足应用要求,前者的重量只及W-Cu基座的20%,且成本仅为后者的1/3左右,有望在封装领域大量替代W-Cu,Mo-Cu等材料。国产L波段功率器件月批量生产累计上千只,实现某型号雷达全面国产化、固态化,今后几年会持续批量生产,S、C波段功率模块怎样低成本生产,将涉及AlSiC封装材料的研发应用。