连铸新技术
(三)保护浇注连铸坯质量新技术

• (3)初生坯壳的均匀性:结晶器弯月面初生坯壳 不均匀会导致铸坯产生纵裂和凹陷,以致造成
从工艺操作上,应采取以下措施: (1)无渣出钢:转炉采用挡渣球,电炉采用偏心炉
底出钢,防止出钢渣大量下到钢包。 (2)钢包精炼:根据钢种选择合适的精炼方法,以
均匀温度、微调成分、降低氧含量、去除气体夹杂 物等。
(3)无氧化浇注:钢水经钢包处理后,钢中总氧含 量可由130ppm下降到20ppm以下。如钢包→中间包 注流不保护或保护不良,则中间包钢水中总氧量又 上升到60~100ppm范围,恢复到炉外精炼前的水平, 使炉外精炼的效果前功尽弃。
➢连铸机的高生产率( 作业率、拉 速、设备可靠)
➢连铸坯的质量( 铸坯洁净度、铸 坯表面缺陷、铸坯内部缺陷)
一、 提高连铸机生产率
1.1 提高连铸机作业率 目前在钢铁工业发达国家, 现代化大型板坯连铸 机的作业率已达90%以上, 方坯连铸机的作业率 也在90%以上, 有的甚至达到了95%。
提高连铸机作业率的措施:
( 1 ) 提高连浇炉数。国外钢厂板坯连浇炉数在 1500炉以上, 方坯在1000 炉以上。
( 2 ) 提高结晶器的使用寿命。在日本结晶器寿命 由200~300 炉提高到1 000~3 000 炉。
( 3 ) 结晶器下部钢板采用多层电镀、先镀Ni 再镀 磷化物和Cr, 并改变镀层范围和厚度。
( 4 ) 改变结晶器冷却槽的形状和间隔, 铜板表面弯 月面附近温度可降到100 ℃左右, 寿命大大提高。
连铸技术国内外现状及发展趋势

连铸技术国内外现状及发展趋势
连铸技术是钢铁工业中的重要技术之一,它可以实现高效连续生产,提高生产效率,降低成本。
目前,国内外的连铸技术都在不断发展和完善中。
在国内,连铸技术已经实现了从单流到双流、三流、四流等多流程的升级。
同时,还出现了带分段式结晶器、上下扫描式结晶器等新型结晶器,提高了连铸成材率和质量。
此外,国内的连铸技术还在不断推广智能化生产、绿色环保等方面的应用。
在国外,美国、日本等发达国家在连铸技术方面也有很多创新。
例如,美国的Hazelett连铸技术可以实现高品质的铝合金连铸,日本的CCS连铸技术则可以实现高浓度的钢水连铸。
此外,欧洲的一些连铸厂还在探索使用第三方能源进行加热,以实现更高的能源利用效率。
未来,随着新材料、新工艺、新技术的不断涌现,连铸技术将继续发展和创新。
同时,环保、智能化、自动化等方面也将成为连铸技术发展的重要方向。
- 1 -。
北营4号板坯连铸机新技术的应用

北营钢铁公司炼钢厂二区4 号板坯连铸机投产 于 20 08年 1 ,至今已稳定运行了 1 个月, 生 月 5 产的钢种包括汽车板 、管线钢 、 压力容器钢、高强
,
电磁搅拌是改善铸坯内部组织和表面质量的一
种重要的方法 ,也是连铸高拉速的一个重要保证 ,
其原理就是在连铸结 晶器内安装一套 电磁感应线 圈,通过电磁感应实现能量无接触转换 , 将电磁能 转换 为钢水的旋转动力 , 推动钢水旋转运动 , 改善 钢水凝固组织 ,提高连铸坯质量 。 北营第二炼钢厂在 4 号板坯连铸机上已实现了
we e e au td b s d o t n e e a u e me s r me ta e o d r o l g z n s a d ma r sr c u e r v ae a e n sr d tmp r t r a u e n t s c n a y c o i o e l a n n c o tu t r ea nt n x mi a o .T e ,t e s c n a y o l g c e wa o t z d M - S e h o o y i a fe tv i h n h e o d r c o i s h me n s pi e . i m EM t c n l g s e c i e t c n l g o r v n e i tr a u l y o o t o s c s n lb T i a e r s n s a v r i w f e h oo y f r i mp o i g t n e lq ai f c n i u a t g sa . h s p p r p e e t n o e v e o h n t n i a p ia i n o e t h o o y i . lb c n i u u a t r p l t f n w e n l g n No4 s o t o s c se .By me n f n w e h o o y u l a o , c o c a n a s o e tc n l g t i t n i zi t c n c l n o a o & r n v t n n o t z t n t e lb i tr a a d u f c q aiy a b e e h ia i n v t n i e o ai a d p i ai . h sa n e n l n s ra e u l h s e n o mi o t c n iea l rv . o sd r b yi mp o e d Ke wo d : ee t - g e i t rn y r s lc o ma n t s ri g;h d a l s i a o r c i y r u i o cl t n; s f d c o C li o t e u t n;t es c n a yc o i gd n m c r i h e o d r o l y a n i
薄带连铸技术

薄带连铸技术1.前言薄带连铸技术是冶金及材料研究领域内的一项前沿技术,它的出现正为钢铁工业带来一场革命,它改变了传统治金工业中薄型钢材的生产过程。
传统的薄型钢材一般采用板坯连铸法,在生产中需要经过多道次热轧和反复冷轧等工序。
能耗大,工序复杂,生产周期长,劳动强度大,产品成本高,转产困难等缺点。
厚板坯(200~300mm)连铸连轧工艺线长度一般在500~800m之间,薄板坯(50~60mm)为300~400m,而采用薄带连铸技术,将连续铸造、轧制、甚至热处理等整合为一体,使生产的薄带坯稍经冷轧就一次性形成工业成品,简化了生产工序,缩短了生产周期,其工艺线长度仅60m。
设备投资也相应减少,产品成本显著降低,并且薄带质量不亚于传统工艺。
此外,利用薄带连铸技术的快速凝固效应,还可以生产出难以轧制的材料以及具有特殊性能的新材料。
但从目前的研究情况看,主要集中在不锈钢、低碳钢和硅钢片方面。
薄带连铸技术工艺方案因结晶器的不同分为带式、辊式、辊带式等,其中研究得最多、进展最快、最有发展前途的当属双辊薄带连铸技术。
该技术在生产0.7—2mm厚的薄钢带方面具有独特的优越性,其工艺原理是将金属液注入一对反向旋转且内部通水冷却的铸辊之间.使金属液在两辊间凝固形成薄带。
双辊铸机依两辊辊径的不同分为同径双辊铸机和异径双辊铸机.两辊的布置方式有水平式、垂直式和倾斜式三种,其中尤以同径双辊铸机发展最快、已接近工业规模生产的水平。
1857年,英国的Bessemer[1]首次尝试采用双辊技术直接铸造钢带,并获得了该项技术的第一项专利。
在最初的100多年里,由于制造技术和控制技术等相关技术的落后.过程控制较为困难,产品质量无法保证,使得这项技术基本上处干停滞状态。
到了1989年,澳大利亚BHP(Broken Hill Proprietary Company)公司和日本的IHI(Ishikawajima-Harima Heavy Industries)公司决定联合开发钢的双辊薄带连铸技术。
连铸连轧新技术培训

连铸连轧新技术培训1. 概述连铸连轧是一种现代金属加工技术,通过连续铸造和连续轧制工艺,可高效地生产各种形状和尺寸的金属材料。
这项技术在钢铁、铜、铝等金属行业得到广泛应用,它具有节能、高效、减少环境污染等优点。
为了提高工人的专业技能和生产效率,连铸连轧新技术培训成为企业重要的任务之一。
2. 连铸连轧工艺概述连铸连轧是一种集连续铸造和连续轧制于一体的金属加工流程。
其基本原理是通过连铸机将熔融金属倾注到连铸结晶器中,通过结晶器内的冷却工艺将金属液固化成坯料;然后将坯料传送至连轧机进行连续轧制,最终得到所需尺寸的金属材料。
连铸连轧工艺具有以下优点:•节省能源:连续工艺能够减少能量损失和热能浪费。
•提高生产效率:连铸连轧工艺可以实现高速连续生产,减少工艺中的停机时间,提高材料的产量。
•保证产品质量:连续工艺可以有效控制金属材料的组织和性能,提高产品的一致性。
•减少环境污染:连铸连轧工艺可以减少废水、废气和废渣的排放,是一种环保的金属加工技术。
3. 连铸连轧新技术培训的意义连铸连轧技术的应用给企业带来了巨大的改变,但也带来了对工人技能要求的提升。
新技术的引入需要对操作人员进行培训,以确保其熟练掌握新工艺和设备操作,提高工作效率和产品质量。
连铸连轧新技术培训的意义主要包括以下几个方面:3.1 提高工人技能水平通过新技术培训,工人能够掌握先进的操作技能和工艺知识,提高他们在连铸连轧生产线上的技能水平。
准确、熟练的操作有助于提高工作效率和产品质量。
3.2 降低操作失误率连铸连轧工艺操作复杂,一些操作失误可能导致设备故障和产品缺陷。
通过培训,可以帮助工人了解工艺流程和设备操作规范,提高操作的准确性和规范性,降低操作失误率。
3.3 提高生产效率熟练的连铸连轧技术操作员能够高效地完成生产任务,减少停机时间,提高生产线的运行效率。
培训可以帮助工人学习提高操作速度和配合其他操作员的技巧,从而提高生产效率。
3.4 推动企业发展连铸连轧新技术的应用可以提高产品的质量和竞争力,推动企业在市场上的发展。
连铸新技术

三、CSP工艺
• CSP工艺(Compact Strip Production)也称紧凑式热带 生产工艺,是德国西马克(SMS)公司开发的连铸连轧工艺。 CSP工艺具有流程短、生产简便、稳定、产品质量好等优点。
160m长的辊 底式均热炉
四辊式四机 架连轧机
四、ISP工艺
• 在线带钢生产线(in-line strip production),简称ISP生 产线。
二水平连铸坯的凝固特点水平连铸中结晶器与中间包直接密封联接分离环水口受水冷影响温度较低因此钢水传热除径向通过铜套壁而被冷却水流带走外沿轴向经过分离环也将导热另外钢液沿已凝固坯壳方向也有少量传热
连铸新技术
本课内容:
—水平连铸 —近终形连铸
本课重点:
—水平连铸机的主要设备 —水平连铸坯的凝固特点 —近终形连铸的类型 —CSP工艺与ISP工艺
二、薄板坯连铸连轧优越性与关键技术
1、薄板坯连铸连轧优越性
1)简化了板材的生产工序,缩短了生产线,相应减少了厂房 占地面积和投资费用。 (2)生产周期短,从钢水冶炼到热轧板卷的输出仅用1.5h, 节约了流动资金,降低了生产成本。
(3)节约能源,提高成材率。
(4)由于铸坯厚度薄,凝固速度快,铸坯的组织细而致密,
本课难点:
—水平连铸坯的凝固特点
水平连铸
• 水平连铸机的中间包、结晶器、二次冷却区、拉坯机、切割 装置等设备安装在水平位置上,呈水平直线布置。
一、水平连铸机的主要设备
1、中间包 与其他连铸机不同的是,水 平连铸机所用的中间包水口 安装在底部侧面的水平方向 上,以便与结晶器直接密封 连接。
中间包水口的启闭采用 双滑板滑动水口
1、连铸机采用平行 板式直弧形结晶
连铸工作中的改进方案和总结
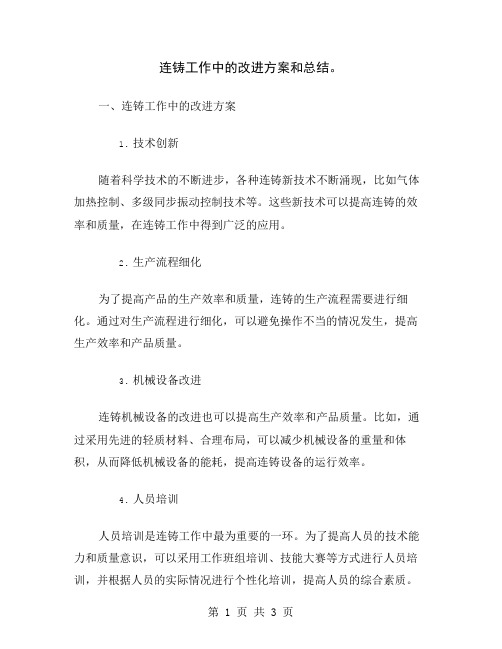
连铸工作中的改进方案和总结。
一、连铸工作中的改进方案1.技术创新随着科学技术的不断进步,各种连铸新技术不断涌现,比如气体加热控制、多级同步振动控制技术等。
这些新技术可以提高连铸的效率和质量,在连铸工作中得到广泛的应用。
2.生产流程细化为了提高产品的生产效率和质量,连铸的生产流程需要进行细化。
通过对生产流程进行细化,可以避免操作不当的情况发生,提高生产效率和产品质量。
3.机械设备改进连铸机械设备的改进也可以提高生产效率和产品质量。
比如,通过采用先进的轻质材料、合理布局,可以减少机械设备的重量和体积,从而降低机械设备的能耗,提高连铸设备的运行效率。
4.人员培训人员培训是连铸工作中最为重要的一环。
为了提高人员的技术能力和质量意识,可以采用工作班组培训、技能大赛等方式进行人员培训,并根据人员的实际情况进行个性化培训,提高人员的综合素质。
二、连铸工作中的总结1.高品质的原材料在连铸工作中,高品质的原材料是保证产品质量的基础。
因此,在原材料采购时,一定要选择质量好、纯度高的原材料。
2.加强管理和监控为了确保连铸工作的正常进行,必须要加强对生产过程的管理和监控。
通过实时监测,可以及时发现和解决生产过程中的问题,避免问题扩大并影响生产效率和产品质量。
3.用先进技术提升质量为了确保连铸生产的高效率和高质量,必须使用先进技术。
只有掌握了先进技术,才能不断提升连铸生产的效率和质量。
4.确保生产安全安全是连铸工作中最为重要的一环。
为了确保生产过程的安全,必须严格遵守生产规程,在工作过程中注意安全,提高员工的安全意识,加强设备的安全保障。
连铸工作中的改进方案和总结可以提高生产效率和产品质量,以适应市场需求的不断增长。
通过不断探索和发展,连铸技术和生产工艺将会得到更加广泛的应用,为实现精准制造和高质量发展做出贡献。
连铸新技术_PPT幻灯片
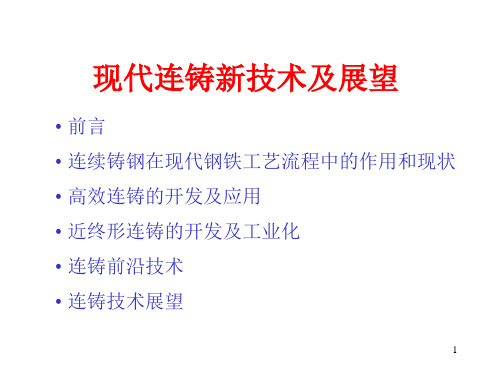
三、 高效连铸的开发及应用
• 高效连铸技术是20世纪80年代中后期发展起 来的,是连铸技术优化发展的方向。所谓高 效连铸通常是指比常规连铸生产效率更高, 以高拉速为核心,以高质量、无缺陷铸坯生 产为基础,实现高连浇率、高作业率的连铸 系统技术。其核心是高拉速技术。
17
三、 高效连铸的开发及应用
连铸机高的作业率和高的铸坯质量是与钢水在连铸机 凝固过程紧密相连的,这样就需要不断改进连铸机设备、 工艺技术和过程控制技术以实现优化配置,使连铸机生产 达到高产量、高质量、低成本的目的。
因此,今天简要介绍为实现这一目标,目前连铸生产 中所采用的先进技术和今后的发展趋势。
3
2.1 连续铸钢技术的发展历程
量扩张到结构优化的战略转移。突出的贡献之一在于连 续铸钢技术的工业化,取代了用钢锭模铸钢、初轧机开 坯的第一代钢液成形技术,从而使从炼钢到轧制成材的 工艺生产线连续化成为可能。而今,随着相关行业科学
技术的进步,特别是控制技术的发展,传统连铸技术已 无竞争能力可言,即将为以高效连铸、近终形连铸为代 表的新一代连铸技术所代替。目前,连铸技术水平的高 低已成为一个国家钢铁工业技术水平的重要指标之一。
—出结晶器均匀的坯壳厚度; —液相穴的长度; —铸坯的冷却强度。
• 第一阶段(1840—1930年)
连续浇铸金属液思想的启蒙阶段。 最早 (1887年)提出与现代连铸机相似的连铸设备建议 的是德国人R.M.Daelen,在其开发的设 备中已包括了上下敞开的结晶器、液态金属注入、 二次冷却段、引锭杆和铸坯切割装置等。
6
2.1 连续铸钢技术的发展历程
• 第二阶段(1940—1949年)
高 效
20
3.1 高效连铸的应用
炼钢与连铸若干新技术
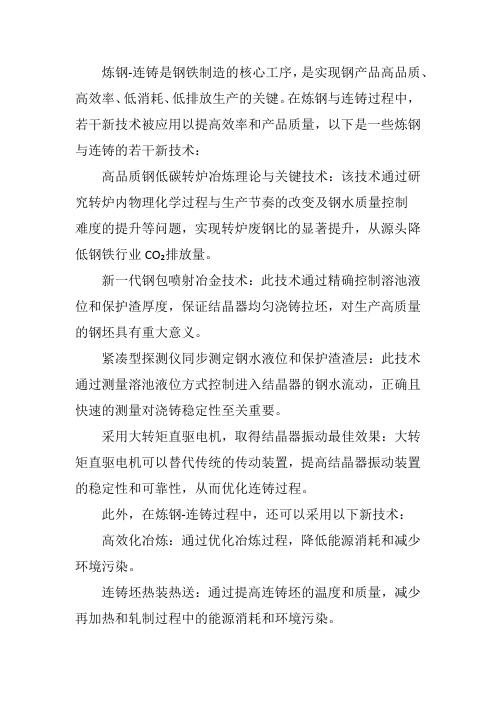
炼钢-连铸是钢铁制造的核心工序,是实现钢产品高品质、高效率、低消耗、低排放生产的关键。
在炼钢与连铸过程中,若干新技术被应用以提高效率和产品质量,以下是一些炼钢与连铸的若干新技术:高品质钢低碳转炉冶炼理论与关键技术:该技术通过研究转炉内物理化学过程与生产节奏的改变及钢水质量控制难度的提升等问题,实现转炉废钢比的显著提升,从源头降低钢铁行业CO₂排放量。
新一代钢包喷射冶金技术:此技术通过精确控制溶池液位和保护渣厚度,保证结晶器均匀浇铸拉坯,对生产高质量的钢坯具有重大意义。
紧凑型探测仪同步测定钢水液位和保护渣渣层:此技术通过测量溶池液位方式控制进入结晶器的钢水流动,正确且快速的测量对浇铸稳定性至关重要。
采用大转矩直驱电机,取得结晶器振动最佳效果:大转矩直驱电机可以替代传统的传动装置,提高结晶器振动装置的稳定性和可靠性,从而优化连铸过程。
此外,在炼钢-连铸过程中,还可以采用以下新技术:高效化冶炼:通过优化冶炼过程,降低能源消耗和减少环境污染。
连铸坯热装热送:通过提高连铸坯的温度和质量,减少再加热和轧制过程中的能源消耗和环境污染。
近终形化生产:通过采用先进的工艺和技术,生产更小断面的连铸坯,提高成材率和生产效率。
精确控制结晶器液面和保护渣厚度:通过精确控制结晶器液面和保护渣厚度,提高连铸坯的质量和稳定性。
电磁搅拌技术:通过采用电磁搅拌技术,改善连铸坯的凝固过程,提高产品质量和生产效率。
自动化的物流系统:通过采用先进的物流系统和技术,实现生产过程中物料的自动化运输和跟踪管理,提高生产效率和产品质量。
高效节能的轧制技术:通过采用高效节能的轧制技术,降低轧钢过程中的能源消耗和提高产品质量。
环保型轧制工艺:通过采用环保型轧制工艺和技术,减少轧钢过程中的环境污染和资源浪费。
集成化工艺控制技术:通过采用集成化工艺控制技术,将炼钢、连铸和轧制等工艺过程进行优化和控制,提高生产效率和产品质量。
这些新技术的应用可以显著提高炼钢-连铸生产的效率和产品质量,同时降低能源消耗和环境污染。
生产高级特厚钢板的新连铸技术(PCCS法)

出了特厚钢板。
为 了解决前述特厚 钢板生产过程 中的铸造缺陷 , 鹿岛制铁所 2 号连铸机上 , 利用普通连铸机进行 了 P C 法 CS 的开发 。 所谓 P C 法是在铸坯厚度 中心未完全凝 固前对铸坯施加大压下 , CS 在中心疏松形成阶段将其压合的方法 。
因为铸坯表 面温度与中心温度差约为 50o左右 , 以这种方法 的特点是 : 面到高温 中心部的压下变形可有 0 C 所 从表 效地使中心疏松压合。实施 P C 法 的条件 , CS c含量为 0 9 01%, 为 4 0 5 0 60M a 的钢种。铸坯尺 . %~ . 0 5 强度 0 、0 、0 P 级
2 1 年第 5 00 期
天舜罐 分
据悉 , 中关铁矿项 目总投 资 1. 亿元 , 39 4 设计年采选铁 矿石 20万 t年产含铁 6 %的铁精粉 17 0 , 6 0. t 4万 。该项
目将采用地下开采形式 , 为我国深部地质条件复杂铁矿的开采提供技术示 范。石人沟铁矿项 目总投资 5 3 元 , .亿 7
油天然气管道局共 同承担研发任务。 各项试 验中, 焊丝熔 敷金属试验的难度极大 。 由于气体保护焊线能量小 , 焊缝
熔深浅 , 而且需要多层 多道焊接 , 在狭小 的坡 口内填充近 7 0道焊缝 , 很容易产生焊接缺陷 。 为 了进行焊丝 的工艺性能试验 , 经过近一个月的工艺调试 , 成功焊接出合格的焊 口。 焊丝检测报
采钢结构等能源领域 的需求 , 近几年也不断增加 。
对这种特厚钢板 , 确保 内在质量 的生产是最重要 的 , 了确保厚度 中心 的机械性 能和确保 中心疏松( 为 气孔) 焊
合, 采用 了强压下轧制。但是 , 用普通连铸机生产的普通铸坯在轧制时 因受轧机能力限制 , 虽经强压下轧制 , 轧后 仍残 留少许疏松缺陷。 只有用高灵敏度超声波能探伤发现缺 陷, 所以超厚板生产 的厚度受到限制 。 因此 , 过去生产
炼钢与连铸若干新技术

炼钢与连铸若干新技术炼钢与连铸作为钢铁生产的重要环节,关系着钢铁质量、生产效率以及能源消耗。
近年来,随着科学技术的不断发展,炼钢与连铸领域出现了许多新技术,这些新技术在提高产品质量、降低生产成本等方面发挥着重要作用。
本文将介绍一些关于炼钢与连铸的若干新技术。
一、炼钢新技术1. 超高炉渣碱度炼钢技术传统炼钢过程中,高炉渣的碱度一般在1.5以上,导致了炼钢中的碱度冶炼难度大。
超高炉渣碱度炼钢技术通过增加炉渣碱度,提高炼钢过程中的碱度,使得钢水中的夹杂物得以吸附和浮渣,从而有效提高了钢水的质量,降低了夹杂物含量。
2. 高炉富氧燃烧技术传统的高炉燃烧采用煤气、焦炭等作为还原剂,而高炉富氧燃烧技术则采用富氧燃烧,使得炉顶煤气中氧分压大大提高,煤气焚烧效率显著提高,从而有效减少了炼钢过程中的二氧化碳排放,降低了生产成本。
3. 高效矿石还原技术传统的炼钢制程中,矿石还原效率低,而高效矿石还原技术采用高效还原剂和改良还原工艺,可以明显提高还原效率,减少资源的浪费,降低生产成本。
二、连铸新技术1. 动态软浇铸技术动态软浇铸技术是指在连铸过程中,通过实时数据分析,调整结晶器冷却水的流速和温度,实现钢坯凝固过程中的动态调控,确保钢坯结晶组织的均匀性和合格率。
2. 连铸直齿轮技术传统连铸转辊采用辊凹槽结构,而连铸直齿轮技术则采用直齿轮结构,使得连铸转辊的传动机构更加紧凑、稳定、可靠,最大限度地减小了设备的占地面积,提高了生产效率。
3. 连铸在线水平矫直技术传统的连铸坯的矫直需要通过离线操作进行,而连铸在线水平矫直技术则采用在线连铸坯的自动矫直设备,实现了连铸坯的在线矫直,提高了生产效率,降低了生产成本。
以上所提到的炼钢与连铸的新技术只是其中的一部分,随着科学技术的不断进步,相关新技术也在不断涌现。
这些新技术的应用,将进一步推动炼钢与连铸领域的发展,为钢铁行业的持续发展注入新的活力。
连铸新技术ppt课件

主要包括: 传统轻压下技术 铸轧技术 液芯压下技术。
(1)传统轻压下技术
目的: 在连铸的凝固末端进行适量压下,以减小 铸坯中心宏观偏析及疏松,改善铸坯质量;
具体形式: 有辊式轻压下技术 锻压式轻压下技术。
轻压下工艺示意图 a—辊式轻压下;b—锻压轻压下
喷雾成形生产钢管简图 1—中间包;2—气体雾化器;3—喷雾室; 4—材料基体;5—传动;6—产品;7—废气
此课件下载可自行编辑修改,供参考! 感谢您的支持,我们努力做得更好!
和防止形成凝固桥。
电磁搅拌对液相穴形态的作用
(3)凝固末端电磁搅拌(F-EMS)
有效地改善铸坯的中心偏析: 使中心偏析金属趋向均匀; 产生较多的结晶核心; 扩大等轴晶区; 细化晶粒。
4. 连铸坯热送热装技术
概念 铸坯切成定尺后,一般表面温度在
800~900℃以上,利于这部分热量将切成 定尺后的铸坯趁高温直接送进加热炉加热 后进行轧制 。
CSP工艺(Compact Strip Production)也 称紧凑式热带生产工艺,是德国西马克 (SMS)公司开发的连铸连轧工艺;
优点: 流程短、生产简便、稳定、产品质量好等;
工艺流程: 电炉→钢包精炼炉→薄板坯连铸机→均热 (保温)炉→热连轧机→层流冷却→地下 卷取。
CSP工艺
核心技术: 漏斗形结晶器、 液心压下技术、 液压振动装置、 电磁闸技术、 高压水除鳞装置、
板形控制技术等。
漏斗形结晶器
这种结晶 器在形状上 满足了长水 口插入、保 护渣熔化和 薄板铸坯的 厚度要求。
漏斗形结晶器,西马克公司CSP工艺
喷射沉积:
是生产扁平产品的特殊生产工艺; 从中间包流出钢水由喷嘴粒化喷出,在基
最新兴澄特殊钢连铸技术概述
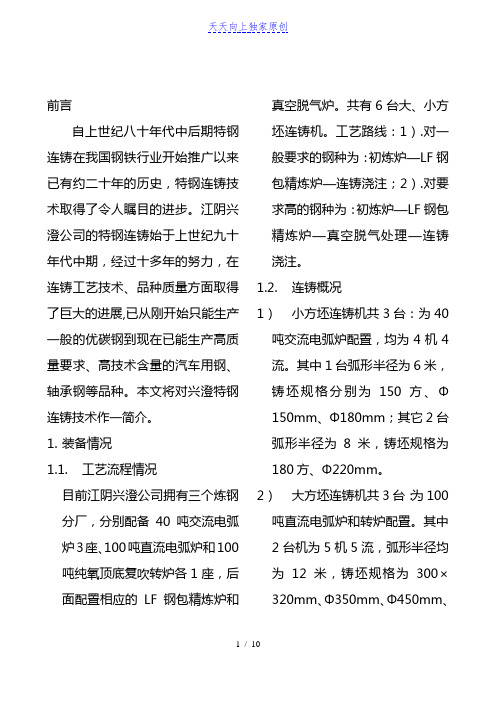
天天向上独家原创前言自上世纪八十年代中后期特钢连铸在我国钢铁行业开始推广以来已有约二十年的历史,特钢连铸技术取得了令人瞩目的进步。
江阴兴澄公司的特钢连铸始于上世纪九十年代中期,经过十多年的努力,在连铸工艺技术、品种质量方面取得了巨大的进展,已从刚开始只能生产一般的优碳钢到现在已能生产高质量要求、高技术含量的汽车用钢、轴承钢等品种。
本文将对兴澄特钢连铸技术作一简介。
1.装备情况1.1.工艺流程情况目前江阴兴澄公司拥有三个炼钢分厂,分别配备40吨交流电弧炉3座、100吨直流电弧炉和100吨纯氧顶底复吹转炉各1座,后面配置相应的LF钢包精炼炉和真空脱气炉。
共有6台大、小方坯连铸机。
工艺路线:1).对一般要求的钢种为:初炼炉—LF钢包精炼炉—连铸浇注;2).对要求高的钢种为:初炼炉—LF钢包精炼炉—真空脱气处理—连铸浇注。
1.2.连铸概况1)小方坯连铸机共3台:为40吨交流电弧炉配置,均为4机4流。
其中1台弧形半径为6米,铸坯规格分别为150方、Φ150mm、Φ180mm;其它2台弧形半径为8米,铸坯规格为180方、Φ220mm。
2)大方坯连铸机共3台:为100吨直流电弧炉和转炉配置。
其中2台机为5机5流,弧形半径均为12米,铸坯规格为300×320mm、Φ350mm、Φ450mm、Φ500mm、Φ600mm。
另1台为3机3流,弧形半径为16.5米,铸坯规格为370×490mm。
2.特殊钢连铸面临的技术课题[1]兴澄公司主要生产轴承钢、弹簧钢、齿轮钢、易切削非调钢、高压管坯钢、油田用钢、系泊链钢、硬线钢等特殊钢。
这些钢种比普通碳素钢对钢质有更高要求。
⑴由于特殊钢中的合金元素较多,含量较高,碳含量控制范围大(0.02%~1.1% C),因此其凝固特性与普通碳素钢有所不同。
⑵特殊钢的纯净度(气体含量、夹杂物数量及形态)、均匀性(低倍组织、微观组织)等要求比普通碳素钢高。
⑶特殊钢中常含有V、Ti、Nb、Al 等活泼元素,极易与氧、氮反应生成高熔点化合物;某些特殊钢中含有S、Al、N元素在浇注、凝固过程中极易形成脆性区或者坚硬质点,这给铸坯质量尤其是表面及内在质量带来一定危害。
8#八机八流连铸机新技术在韶钢的应用
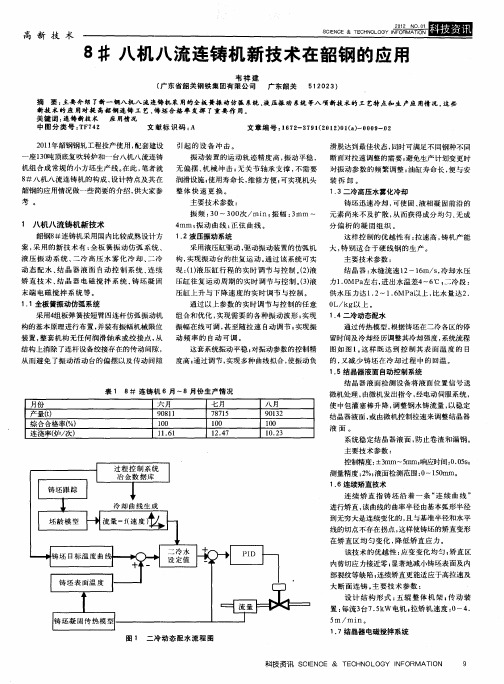
采 用4 组板弹 簧按短 臂四连杆 仿弧 振动机 组 合和优化 , 现需 要 的各种 振 动波形 ; 现 实 实 构 的基本 原理进 行布置 , 装有振幅 机械 限位 振 幅 在线 可调 , 并 甚至 随 拉速 自动 调节 ; 现振 实 装置, 整套 机构 无任 何润 滑轴 承或 绞接 点 , 从 动 频 率 的 自动可 调 。 结 构上消 除 了连 杆设备绞接 存在 的传动 间隙 , 从 而 避免 了振 动活 动 台的偏 摆以 及传 动 间隙 这套 系统振动 平稳 ; 对振 动参 数的控制 精
14二冷动态 配水 .
通过传 热模型 , 根据铸坯 在二冷各 区的停 留时间及 冷却经 历调整其 冷却强度 , 系统流程 图如 图 l 这 样 既 达 到 控 制 其 表面 温 度 的 目 。 的, 又减 少 铸坯 在 冷却 过 程 中的 回温 。 1 5结 晶器液 面 自动 控制 系统 .
座 10 3 吨顶 底复吹转 炉和一 台八机八 流连铸
韶钢 的应用情 况做一些 简要 的介绍 , 大家参 整 体 快 速 更换 。 供 考 。
主 要技 术参数 : 振 频 : 0 0 次 / i 振 幅 : mm ~ 3 ~3 0 a r n; 3 4 m ; 动 曲 线 : 弦 曲线 。 a r 振 正
力1 0 .MPa 右 , 出水温 差4~6 二冷 段 : 左 进 ℃l 供水 压 力达 1 2~1 6 . . MPa 以上 , 比水量 达2.
1 八机 八流铸机新 技术
案 , 用的 新技 术有 : 板 簧振 动 仿 弧 系统 、 采 全
韶钢8 #连铸 机采用 国内 比较成熟 设计方 1 2 . 液压 振动系统 液 压振 动 系统 、 二冷 高 压 水 雾 化 冷 却 、 冷 构 , 二 实现振 动 台的往 复运 动 。 通过 该 系统 可实 动 态 配 水 、 晶 器液 面 自动 控 制 系 统 、 续 现 :1液 压 缸 行程 的 实 时调 节 与 控 制 。2 液 结 连 () () 矫 直 技 术 、 晶 器 电磁 搅 拌 系 统 、 坯 凝 固 结 铸 压缸 往 复运 动周 期 的实 时 调节 与控 制 。3 液 ()
北京科技大学科技成果——双金属复合材料双结晶器连铸新技术

北京科技大学科技成果——双金属复合材料双结晶
器连铸新技术
成果简介
由于双金属复合材料铸造成形具有易于实现批量化、连续化、自动化生产,降低生产成本,应用范围广等优点,研究开发和应用受到越来越广泛的重视。
现有双金属复合材料连续铸造成形方法可以分为两大类:
(1)使用已成形的芯材对其进行包覆的包覆铸造成形法;
(2)将两种金属同时注入同一个结晶器内进行成形的双流铸造法。
包覆铸造成形法的典型代表为用于复合轧辊成形的CPC法,这种方法的主要缺点是预处理工艺复杂,获得具有良好复合质量的界面较困难。
有代表性的双流铸造法是双流浇铸连续铸造制备梯度材料的方法,其主要优点是界面质量好,可以制备具有梯度过渡层的复合材料;其主要缺点是技术难度大、适用范围窄、包覆层厚度控制困难。
为此,本课题组开发了采用双结晶器一次铸造成形双金属复合材料的方法,其基本原理如图所示。
在上结晶器(芯材结晶器)内连铸凝固成形的芯材,在保护环的保护作用下,保持表面无氧化、无夹杂、无油污的状态,直接进入下结晶器(包覆层结晶器),热态连铸包覆层。
该方法具有工序简单、节能降耗、适用范围广、复合界面良好等优点。
双金属双结晶器连铸技术原理图
1-底盘;2-结晶器;3-包覆材料;4-加热线圈;5-耐火材料;6-预热线
圈;7-保护涂层;8-芯部材料
应用前景
电子电工材料:如铜包铝高频导线、铜包钢电话线(国外采用镀铜方式)。
耐蚀与阳极保护材料:如钛包铜导电排、镁阳极;双金属轧辊,以及有如不锈钢包覆碳钢等装饰性、耐蚀性结构材料。
双金属管:如医药、食品、石油化工用双金属管材等。
连铸连轧新技术培训
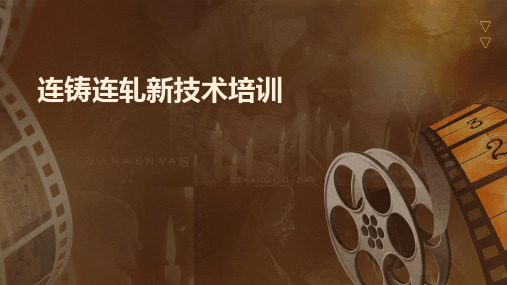
04
连铸连轧新技术的优势与挑战
连铸连轧新技术的优势
提高生产效率
节能减排
连铸连轧技术能够实现连续化生产, 提高了生产效率,降低了生产成本。
连铸连轧技术能够降低能源消耗和减 少废弃物排放,有利于实现绿色生产 。
优化产品质量
新技术能够更好地控制产品形状、尺 寸和性能,提高了产品质量和稳定性 。
连铸连轧新技术面临的挑战
01
02
03
技术更新成本高
新技术的引入需要投入大 量资金进行设备更新和技 术改造。
操作技能要求高
新技术的操作和维护需要 专业知识和技能,对操作 人员提出了更高的要求。
兼容性问题
新技术的引入可能需要对 原有生产系统进行改造和 调整,以实现与新技术的 兼容。
如何应对连铸连轧新技术的挑战
加强技术培训
对操作人员进行系统的技术培训 ,提高他们的专业知识和技能水
节能技术
采用先进的节能技术和设备,降低能耗和减少资源浪 费,实现绿色生产。
减排措施
通过优化生产工艺和加强环保管理,降低污染物排放 ,保护环境。
THANK YOU
总结词
薄带连铸技术是一种新型的连铸技术,能够生产出厚度较薄的带坯。
详细描述
薄带连铸技术采用特殊的结晶器和冷却系统,通过控制钢液的凝固过程,生产 出厚度在50-200毫米之间的薄带坯。这种技术适用于生产不锈钢、碳钢、合金 钢等不同材质的薄带,具有节能、高效、环保等优点。
连铸坯热装热送技术
总结词
连铸坯热装热送技术能够提高钢铁生产效率,降低能耗和减少环境污染。
详细描述
连铸坯热装热送技术是指在连铸过程中,将刚出炉的铸坯通过保温和密封的运输装置直接送往轧机进行轧制,避 免了传统工艺中的冷却、再加热等环节。这种技术能够减少能源消耗和缩短生产周期,同时降低氧化和减少环境 污染。
高效连铸和近终型连铸生产技术
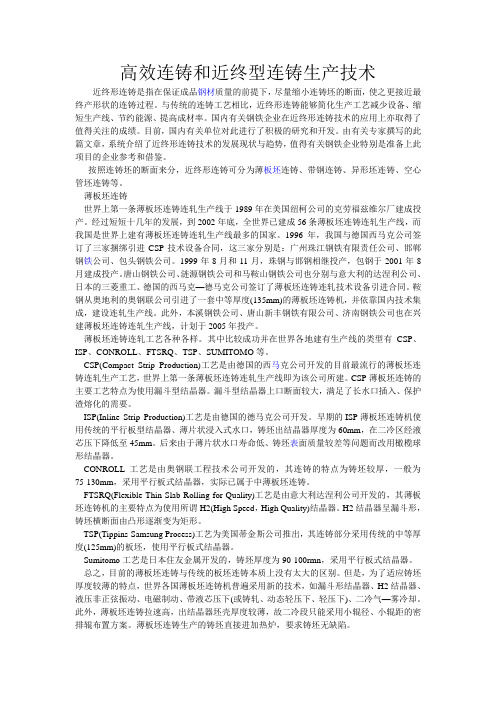
高效连铸和近终型连铸生产技术近终形连铸是指在保证成品钢材质量的前提下,尽量缩小连铸坯的断面,使之更接近最终产形状的连铸过程。
与传统的连铸工艺相比,近终形连铸能够简化生产工艺减少设备、缩短生产线、节约能源、提高成材率。
国内有关钢铁企业在近终形连铸技术的应用上亦取得了值得关注的成绩。
目前,国内有关单位对此进行了积极的研究和开发。
由有关专家撰写的此篇文章,系统介绍了近终形连铸技术的发展现状与趋势,值得有关钢铁企业特别是准备上此项目的企业参考和借鉴。
按照连铸坯的断面来分,近终形连铸可分为薄板坯连铸、带钢连铸、异形坯连铸、空心管坯连铸等。
薄板坯连铸世界上第一条薄板坯连铸连轧生产线于1989年在美国纽柯公司的克劳福兹维尔厂建成投产。
经过短短十几年的发展,到2002年底,全世界已建成56条薄板坯连铸连轧生产线,而我国是世界上建有薄板坯连铸连轧生产线最多的国家。
1996年,我国与德国西马克公司签订了三家捆绑引进CSP技术设备合同,这三家分别是:广州珠江钢铁有限责任公司、邯郸钢铁公司、包头钢铁公司。
1999年8月和11月,珠钢与邯钢相继投产,包钢于2001年8月建成投产。
唐山钢铁公司、涟源钢铁公司和马鞍山钢铁公司也分别与意大利的达涅利公司、日本的三菱重工、德国的西马克—德马克公司签订了薄板坯连铸连轧技术设备引进合同。
鞍钢从奥地利的奥钢联公司引进了一套中等厚度(135mm)的薄板坯连铸机,并依靠国内技术集成,建设连轧生产线。
此外,本溪钢铁公司、唐山新丰钢铁有限公司、济南钢铁公司也在兴建薄板坯连铸连轧生产线,计划于2005年投产。
薄板坯连铸连轧工艺各种各样。
其中比较成功并在世界各地建有生产线的类型有CSP、ISP、CONROLL、FTSRQ、TSP、SUMITOMO等。
CSP(Compact Strip Production)工艺是由德国的西马克公司开发的目前最流行的薄板坯连铸连轧生产工艺,世界上第一条薄板坯连铸连轧生产线即为该公司所建。
连铸技术的现状及发展趋势

连铸技术的现状及发展趋势摘要:随着科学技术的发展,连铸技术的发展也越来越趋向于成熟。
本文主要介绍了连铸技术在国内外的发展现状和趋势,用到电磁冶金、终形连铸、中间包的加热、结晶器液压振动、在线调宽、摩擦力监控和中间包连续测温等技术,在介绍技术的同时,又联系现实的生产状况,分析了它的发展状况。
关键词:连铸技术;现状;发展;趋势一、近终形连铸技术的介绍近终形连铸技术就是一种集连铸、轧制和热处理为一体的可以生产特殊新材料的一种技术,它最大的特点就是快速凝固,这样可以生产出传统轧制工艺无法生产的材料。
连铸技术分为多种,下面介绍薄板坯连铸和薄带连铸技术。
对于薄板坯连铸技术,薄板坯连铸技术早在1989年就开始投产,在美国最先兴起,结合了德国当时最先进的生产技术。
随着时代的发展,薄板坯连铸技术也日渐成熟,早先只有国外公司拥有这种生产技术,现在,中国已经成为薄板坯连铸产能最大、生产线最多的国家。
对于薄带连铸技术,它相对于其它连铸技术更为先进,它属于冶金领域中一项前沿技术。
它又分为前期传统的技术和现代薄带连铸技术,区别于以前它最大的特点就是薄带连铸技术更加综合,它集连铸、轧制和热处理技术为一体,生产的薄带坯更加精细,并且可以一次成型。
现在的连铸技术中最受关注还有就是双辊薄带连铸技术,它广受关注的原因就是此种高效的生产工艺可以提高生产效率,增加高额的经济效益[1]。
双辊薄带连铸这种工艺非常复杂,所以至今没有完全掌握,虽然近些年有些突破性进展,但是,想要达到商业化量产阶段是不可能的,还是需要大量的研究和探索工作。
其中有几大问题,第一就是生产中的裂纹,这是制约此项技术发展的重大原因之一。
第二就是厚度不均匀的问题,现在能实现的厚度就是在小范围内波动,但还是不利于冷轧过程的进行。
第三就是连铸的速度,上面也提到,现在的技术不足,生产成品的速率低下,不能满足商业化需求。
第四就是薄带的宽度小,并且侧封还不理想。
剩下的还有铸辊的材质问题、钢液的氧化问题、二次冷却问题等等。
- 1、下载文档前请自行甄别文档内容的完整性,平台不提供额外的编辑、内容补充、找答案等附加服务。
- 2、"仅部分预览"的文档,不可在线预览部分如存在完整性等问题,可反馈申请退款(可完整预览的文档不适用该条件!)。
- 3、如文档侵犯您的权益,请联系客服反馈,我们会尽快为您处理(人工客服工作时间:9:00-18:30)。
连铸新技术
摘要:本文开篇介绍了连续铸钢工艺流程,主要阐述了连铸新技术在钢铁厂实践中的应用以及我国连铸技术的发展应用和新的
情况。
关键词:连铸;新工艺;电磁加热;电磁搅拌技术;
abstract: in the opening, this paper introduces the technological process of continuous casting, and then mainly expounds the application of the new technology of continuous casting in the practice of steel plant, the development, application and new circumstance of continuous casting technology in china.
keywords: continuous casting; new technology; electromagnetic heating; electromagnetic stirring technology
中图分类号:tf777.1文献标识码:a 文章编号:2095-2104(2012)高效连铸机在我国的发展, 已经逐渐走向成熟。
可以说国内高效连铸核心技术的研究攻关已取得了突破性的进展, 无论是改造或新
建的高效连铸机, 在拉速、作业率、铸坯质量方面的指标均达到相当的水平。
但是, 与国外高效连铸相比还有差距, 而且国内各生产企业的高效化水平也参差不齐, 反映了各企业在综合技术应用上
的差距。
若能把近几年出现的一些新的连铸技术综合应用到高效连铸机上, 势必会促进其进一步发展。
1.连续铸钢工艺流程简介
连铸是把液态钢用连铸机浇注,冷凝,切割而直接得到铸坯的工艺。
它是连接炼钢和轧钢的中间环节,是炼钢生厂车间的重要组成部分。
连铸生产的正常与否,不但影响到炼钢生产任务的完成,而且也影响到轧材的质量和成材率。
一台连铸机主要是由盛钢桶运载装置,中间包,中间包车,结晶器,结晶器振动装置,二次冷却装置,拉坯矫直装置,切割装置和铸坯运出装置等部分组成的。
浇钢时把装有钢水的盛钢桶,通过盛钢桶运载装置运送到连铸机上方,经盛钢桶底部的流钢孔把钢水注入到中间包内。
打开中间包塞棒后,钢水流入到下口用引锭杆头堵塞并能上下振动的结晶器中。
钢液沿结晶器周边冷凝成坯壳。
当结晶器下端出口处坯壳有一定厚度时,带有液心并和引锭装置连在一起的铸坯在拉坯机驱动下,离开结晶器沿这由弧形排列的夹辊支撑下移。
与此同时,连铸坯被二次冷却装置进一步冷却并继续凝固。
当引锭装置进入拉矫机后脱去引锭装置,铸坯在全部凝固或带有液心状态下被矫直。
随后在水平位置被切割成定尺长度,置放于运坯装置上运送到规定地点。
上述整个过程是连续进行的。
2.钢铁厂应用的连铸新技术
连铸新技术主要体现在: 连铸机的高生产率(作业率、拉速、设备可靠) 和连铸坯的质量(铸坯洁净度、铸坯表面缺陷、铸坯内部缺陷)。
1)日本:
日本金属材料研究开发中心开发成功连铸新技术, 它利用电磁加热的作用, 使铸坯的表面质量大为提高。
连铸坯表面易生成缺陷, 为生产高精度表面加工的汽车用钢板和螺栓用特殊钢, 铸后需先将铸坯进行冷却并由人工对缺陷修复, 再加热后供轧机轧制。
新工艺则在连铸机结晶器的背面加上线圈, 对钢水施加交变磁场加热, 可使铸坯表面和结晶器间的润滑改善, 从而有利于表面质量大幅度提高, 可取消冷却后人工修复和再加热工序, 不仅缩短了生产周期,且可节约能源7%。
2)武钢:
武钢采用了一系列的连铸新技术来提高武钢产钢质量,如电磁搅拌技术(ems),动态轻压下(astc) 技术等。
在电磁搅拌技术中武钢主要针对以下进行改进:
a.提高等轴晶率
ems 对于促进“结晶雨”的形成、增加等轴晶区域、减少中心宏观偏析有着显著的作用。
实践表明在硅钢上使用电磁搅拌技术(ems) 可使连铸坯中的等轴晶率(在铸坯恒断面上等轴晶区占的空间) 达到50%以上。
如图一:
图1 使用电磁搅拌后的铸坯横断面组织
图1 反映了ems 对提高等轴晶率的显著作用。
武钢通过在无取向硅钢上使用电磁搅拌技术,大幅度减少了硅钢在轧制过程中的瓦楞废品,提高了硅钢的成材率,取得了良好的效果。
b.降低铸坯的中心偏析
连铸板坯在凝固的过程中会产生“搭桥”的现象,中心偏析主要是由于凝固坯壳冷凝收缩以及鼓肚引起负压,促使糊积区树枝晶间富含有杂质元素的钢液流动而形成中心偏析。
使用ems 时,柱状晶区长度减小,铸坯中间v 形偏析的形式也由单个大型转变为接近于密布型。
图2 和图3 所示为同钢种连铸时使用ems和未使用ems 的铸坯中心偏析对比。
由图可见,使用电磁搅拌技术可明显改善连铸坯的中心偏析,特别
是在中碳低合金中厚板钢的生产过程中效果尤为明显。
3)宝钢:
宝钢股份公司技术中心研发出以下连铸过程控制新技术,已在宝钢成功使用。
a.连铸坯内部质量自动分析技术
利用模式识别技术识别偏析、内裂,依据规则自动对板坯内部进行信息提取和缺陷判级,判别准确率达95 %以上,且具有图象压缩、长期存储等特点。
b.新型结晶器液面控制技术
该技术采用主动控制、补偿高级算法,大大提高了系统的鲁棒性。
对抑制液面波动,特别是中频以下干扰(小于011hz) 而引起的波动,效果明显。
c.柔性过程数据采集平台技术
该技术基于原系统传感器信号,但对原系统无干扰,安全性高。
可以不同采样频率和数据组合、多采样任务并行等方式动态采集数据,
速度达毫秒级,且采样频率和精度完全能满足生产和科研的需求。
d.连铸切割诊断技术
接触式测长装置随时间磨损精度降低,严重时会发生故障。
采用该技术无论切割机在切割或待机状态,均可实时显示误差,并对板坯切割未断而行进、板坯超长及系统故障等报警,避免设备事故。
e.连铸动态过程案例分析系统技术
系统由数据库、可视化界面、软测量等部分组成,能记录多种生产过程数据,重现生产过程,可以板坯号、炉号、时间等为关键字进行检索,是分析板坯缺陷提高质量的有效技术工具。
3.我国连铸新技术的发展应用及前沿技术的开发出现的新情况1)轻压下技术:
轻压下可以减轻铸坯中心偏析缺陷, 它主要针对铸坯在末端产生的凝固收缩。
奥钢联推出的smart技术在韩国浦项制铁应用获得了明显效果。
在国内, 鞍钢一炼钢的板坯连铸机已具有应用轻压下的条件, 宝钢、武钢采用二冷区辊缝收缩技术对改善板坯内部质量也有了成效。
2)方坯电磁搅拌技术:
因为进口设备昂贵, 使用寿命较短, 电磁搅拌器在2000年以前推广比较迟缓, 仅在一些大型钢厂、国家重点工程项目上有进口配套。
2000年以后的几年, 电磁搅拌器已开始在各大钢厂普及, 但推广配置好、使用好的电磁搅拌器, 还有许多工作要做。
3)板坯电磁搅拌和电磁制动:
板坯电磁搅拌和电磁制动目前实施还有些困难, 仍需进一步开发。
4)薄板坯连铸-连轧开发钢种:
目前这些生产线尚不能生产如汽车面板等品种的薄板材。
电磁技术在薄板坯连铸中的应用主要是电磁制动。
5)中间罐冶金: 尚有开发空间。
6)结晶器内软接触技术:
利用电磁技术在结晶器内产生电磁推力, 使凝固坯壳与结晶器壁
出现软接触, 从而可以减轻拉坯阻力, 提高拉速, 改善铸坯表面
质量。
突破这项技术难关,将使连铸技术实现一个飞跃。
4.结语:连续铸钢技术是一个系统工程, 要综合应用连铸新技术, 才能促进高效连铸的更大的发展。
参考文献:
[1]蔡开科,连续铸钢.(m),北京:科学出版社,1990
[2]王雅珍,张岩,刘术国等,新编连续铸钢工艺与设备(m).北京:冶金工业出版社,1996
[3]刘炳宇,刘昆华. 转炉—连铸工艺生产重轨钢的实践. 武钢科技, 2002
[4]李宪奎,张明德,连铸结晶器振动技术(m),北京:冶金工业出版社,2000
[5]魏军,等. 炼钢-精炼-连铸工序生产高碳钢的质量控制.炼钢, 2000
[6]杨吉春,等, ems对重轨钢连铸大方坯质量的改善. 炼钢,2001
[7]yim c h, park j k,oh k s. the control of internalquality bythe reduction ofbloomwith liquid cord. steelmaking confer2ence proceedings. 1998.。