钢的连铸连轧技术
薄带连铸连轧技术-宝钢
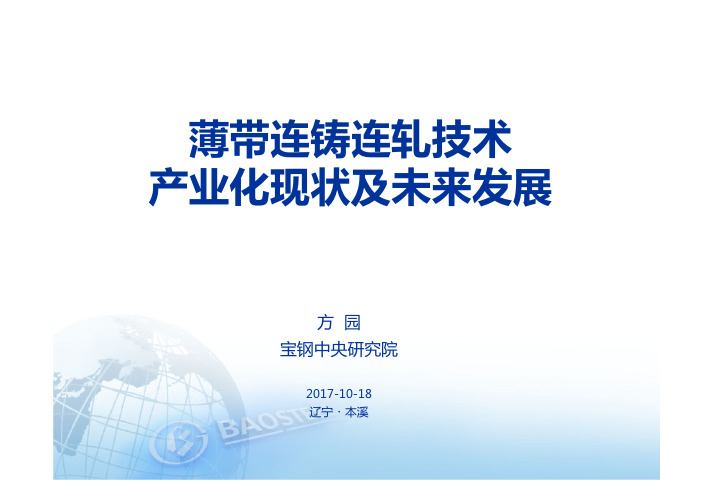
Castrip LLC Baostrip POSTRIP castrip Baostrip
技术
P,双辊薄带连铸 双辊薄带连铸
电磁侧封 中试工厂
汽车用钢
碳钢产品
eurostrip castrip
工业化线建成 工业化线建成 商业化试生产 中试线建成 工业化线建成 第二条工业化线建成 工业化线建成
•轧后板凸度: C40<50um
•轧后板楔形 W40<30um
•单机架最大压下: 45%
•表面夹渣:
<ID2
•表面微裂纹:
<ID2
2、带钢厚度、板形、表面质量、边 部质量良好,表面无肉眼所见裂纹, 性能和质量达到ASTM1039标准要 求。 3、产品实现了批量市场应用。应用
领域主要包括集装箱外板、保险箱
NBS 表面质量和边部质量
着色探伤
原始板面
未切边
宝钢薄带连铸® 简单就是最好
切边后
BaoStrip® Simple is the best
NBS 产品经过酸洗、热镀锌、冷轧、连退
1.2mm屈服410MPa热轧板直接热镀锌
冷轧到0.48mm
连续退火
宝钢薄带连铸® 简单就是最好
酸洗
BaoStrip® Simple is the best
E2strip
RAL
1856-2016
Europe
Henry Bessmer
40-50 TEAMS 宝钢薄带连铸® 简单就是最好
$4000-5000M BaoStrip® Simple is the best
世界薄带铸轧技术发展大事记
年
1856 1911 1930-35 1956 1957-69 1972-80 1980 1983 1984 1986 1986 1987 1989
带钢无头连铸连轧技术(ESP)简介

带钢无头连铸连轧技术(ESP)简介截止2013年底,我国共有70套热轧宽带钢机组己投产,产能达到2.29亿吨,由此产生的能耗巨大。
近年来,为了节能降耗,欧洲、日本和韩国等国家的钢铁企业在努力实现热轧板带减量化制造技术方面进行了大量的研究开发工作并取得显著效果。
其中,开发和发展热轧板带无头轧制技术,进一步提高板带成材率、尺寸形状精度与薄规格超薄规格比例、实现部分〃以热代冷〃、降低辐耗等方面取得显著成绩。
该项技术是钢铁生产技术的又一次飞跃, 代表了当今世界热轧带钢的前沿技术。
1997年浦项和日立联合着手开始研制采用剪切、焊接工艺,进行中间坯连接的带钢无头轧制新工艺。
1998年4月,日本新日铁大分厂研制成功了利用高能激光器对中间板坯实现对焊的钢板无头轧制生产线。
2006-2007年浦项和日立采用剪切、焊接工艺进行中间坯连接的带钢无头轧制新工艺投入工业化生产,这种基于摆剪概念的新型固态连接工艺,实现了无头轧制连接技术的创新。
2009年意大利钢铁企业阿维迪与西门子公司联手打造的世界第一套ESP无头铸轧带钢生产线投产,当年产量达到45万吨。
本文以阿维迪ESP线为例,简要介绍带钢无头连铸连轧的工艺特点及技术优势。
一、ESP工艺流程及主要特点(一)ESP工艺流程介绍阿维迪ESP生产线如图1所示,该项技术是在德马克公司的ISP技术基础上开发的,其生产线中的连铸机采用平行板式直—弧形结晶器,铸坯导向采用铸轧结构,经液芯压下铸坯直接进入初轧机轧制成中厚板,而后经剪切可下线出售,不下线的板坯经感应加热后, 进入五架精轧机轧制成薄带钢,经冷却后卷曲成带卷。
ESP工艺生产线布置紧凑,不使用长的加热炉或克雷莫纳炉,生产线全长仅190m,是世界上最短的连铸连轧生产线。
ii tt UH 电tt BMr MH 泳冷"口谅、勇矗*图1.意大利阿维迪ESP生产线示意图(二)ESP工艺的主要技术特点1 .较高的浇铸速度。
连铸连轧新技术培训

连铸连轧新技术培训1. 概述连铸连轧是一种现代金属加工技术,通过连续铸造和连续轧制工艺,可高效地生产各种形状和尺寸的金属材料。
这项技术在钢铁、铜、铝等金属行业得到广泛应用,它具有节能、高效、减少环境污染等优点。
为了提高工人的专业技能和生产效率,连铸连轧新技术培训成为企业重要的任务之一。
2. 连铸连轧工艺概述连铸连轧是一种集连续铸造和连续轧制于一体的金属加工流程。
其基本原理是通过连铸机将熔融金属倾注到连铸结晶器中,通过结晶器内的冷却工艺将金属液固化成坯料;然后将坯料传送至连轧机进行连续轧制,最终得到所需尺寸的金属材料。
连铸连轧工艺具有以下优点:•节省能源:连续工艺能够减少能量损失和热能浪费。
•提高生产效率:连铸连轧工艺可以实现高速连续生产,减少工艺中的停机时间,提高材料的产量。
•保证产品质量:连续工艺可以有效控制金属材料的组织和性能,提高产品的一致性。
•减少环境污染:连铸连轧工艺可以减少废水、废气和废渣的排放,是一种环保的金属加工技术。
3. 连铸连轧新技术培训的意义连铸连轧技术的应用给企业带来了巨大的改变,但也带来了对工人技能要求的提升。
新技术的引入需要对操作人员进行培训,以确保其熟练掌握新工艺和设备操作,提高工作效率和产品质量。
连铸连轧新技术培训的意义主要包括以下几个方面:3.1 提高工人技能水平通过新技术培训,工人能够掌握先进的操作技能和工艺知识,提高他们在连铸连轧生产线上的技能水平。
准确、熟练的操作有助于提高工作效率和产品质量。
3.2 降低操作失误率连铸连轧工艺操作复杂,一些操作失误可能导致设备故障和产品缺陷。
通过培训,可以帮助工人了解工艺流程和设备操作规范,提高操作的准确性和规范性,降低操作失误率。
3.3 提高生产效率熟练的连铸连轧技术操作员能够高效地完成生产任务,减少停机时间,提高生产线的运行效率。
培训可以帮助工人学习提高操作速度和配合其他操作员的技巧,从而提高生产效率。
3.4 推动企业发展连铸连轧新技术的应用可以提高产品的质量和竞争力,推动企业在市场上的发展。
连铸连轧技术
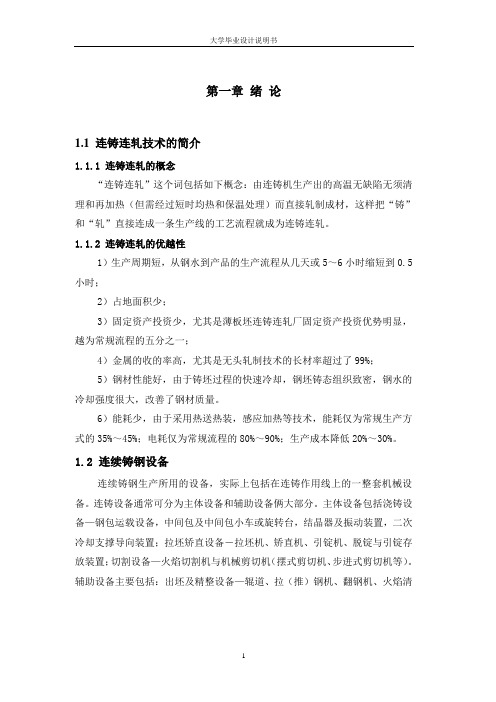
第一章绪论1.1 连铸连轧技术的简介1.1.1 连铸连轧的概念“连铸连轧”这个词包括如下概念:由连铸机生产出的高温无缺陷无须清理和再加热(但需经过短时均热和保温处理)而直接轧制成材,这样把“铸”和“轧”直接连成一条生产线的工艺流程就成为连铸连轧。
1.1.2 连铸连轧的优越性1)生产周期短,从钢水到产品的生产流程从几天或5~6小时缩短到0.5小时;2)占地面积少;3)固定资产投资少,尤其是薄板坯连铸连轧厂固定资产投资优势明显,越为常规流程的五分之一;4)金属的收的率高,尤其是无头轧制技术的长材率超过了99%;5)钢材性能好,由于铸坯过程的快速冷却,钢坯铸态组织致密,钢水的冷却强度很大,改善了钢材质量。
6)能耗少,由于采用热送热装,感应加热等技术,能耗仅为常规生产方式的35%~45%;电耗仅为常规流程的80%~90%;生产成本降低20%~30%。
1.2 连续铸钢设备连续铸钢生产所用的设备,实际上包括在连铸作用线上的一整套机械设备。
连铸设备通常可分为主体设备和辅助设备俩大部分。
主体设备包括浇铸设备—钢包运载设备,中间包及中间包小车或旋转台,结晶器及振动装置,二次冷却支撑导向装置;拉坯矫直设备-拉坯机、矫直机、引锭机、脱锭与引锭存放装置;切割设备—火焰切割机与机械剪切机(摆式剪切机、步进式剪切机等)。
辅助设备主要包括:出坯及精整设备—辊道、拉(推)钢机、翻钢机、火焰清理机等;工艺设备—中间包烘烤装置、吹氖装置、脱气装置、保护渣供给与结晶润滑装置等;自动控制与测量仪表—结晶器液面测量与显示系统、过程控制计算机、测温、测重、测长、测速、测压等仪表系统。
在连续铸钢的生产线上,出拉坯矫直机脱锭后的连铸坯需按用户或下部工序的要求,将铸坯切成定尺或倍尺。
因此在所有的连铸设备中,切割设备是非常重要的一种设备。
由于连铸坯必须在连续的运动过程中实现切割,因而连铸工艺对切割设备提出了特殊的要求,既不管采用什么型式的切割设备都必须与连铸坯实行严格的同步运动。
连铸连轧工艺
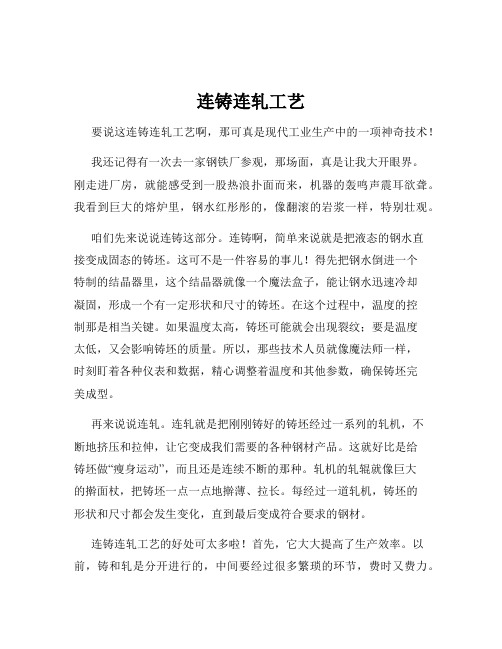
连铸连轧工艺要说这连铸连轧工艺啊,那可真是现代工业生产中的一项神奇技术!我还记得有一次去一家钢铁厂参观,那场面,真是让我大开眼界。
刚走进厂房,就能感受到一股热浪扑面而来,机器的轰鸣声震耳欲聋。
我看到巨大的熔炉里,钢水红彤彤的,像翻滚的岩浆一样,特别壮观。
咱们先来说说连铸这部分。
连铸啊,简单来说就是把液态的钢水直接变成固态的铸坯。
这可不是一件容易的事儿!得先把钢水倒进一个特制的结晶器里,这个结晶器就像一个魔法盒子,能让钢水迅速冷却凝固,形成一个有一定形状和尺寸的铸坯。
在这个过程中,温度的控制那是相当关键。
如果温度太高,铸坯可能就会出现裂纹;要是温度太低,又会影响铸坯的质量。
所以,那些技术人员就像魔法师一样,时刻盯着各种仪表和数据,精心调整着温度和其他参数,确保铸坯完美成型。
再来说说连轧。
连轧就是把刚刚铸好的铸坯经过一系列的轧机,不断地挤压和拉伸,让它变成我们需要的各种钢材产品。
这就好比是给铸坯做“瘦身运动”,而且还是连续不断的那种。
轧机的轧辊就像巨大的擀面杖,把铸坯一点一点地擀薄、拉长。
每经过一道轧机,铸坯的形状和尺寸都会发生变化,直到最后变成符合要求的钢材。
连铸连轧工艺的好处可太多啦!首先,它大大提高了生产效率。
以前,铸和轧是分开进行的,中间要经过很多繁琐的环节,费时又费力。
现在呢,一气呵成,从钢水到钢材,速度快得惊人。
其次,它还能节省能源和原材料。
因为整个过程是连续的,减少了中间的停顿和运输,也就降低了能源的消耗和材料的损失。
而且啊,这种工艺生产出来的钢材质量也更稳定,性能更优越。
在实际应用中,连铸连轧工艺已经广泛用于生产各种类型的钢材,比如建筑用的螺纹钢、汽车制造用的板材等等。
可以说,我们生活中的很多东西都离不开它。
不过,这连铸连轧工艺也不是没有挑战的。
比如说,设备的维护就是个大问题。
那些轧机和结晶器整天高强度工作,很容易出现故障。
一旦出了问题,就得赶紧抢修,否则会影响整个生产进度。
还有就是对操作人员的技术要求很高,他们得时刻保持警惕,应对各种突发情况。
连铸连轧
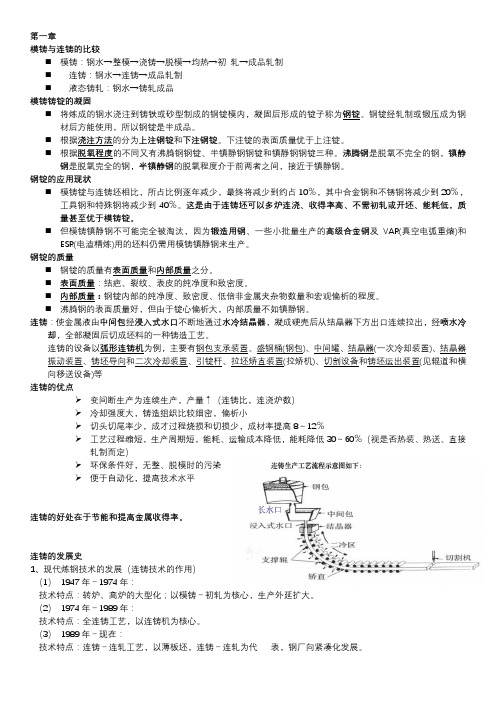
第一章模铸与连铸的比较⏹模铸:钢水→整模→浇铸→脱模→均热→初轧→成品轧制⏹连铸:钢水→连铸→成品轧制⏹液态铸轧:钢水→铸轧成品模铸铸锭的凝固⏹将炼成的钢水浇注到铸铁或砂型制成的钢锭模内,凝固后形成的锭子称为钢锭。
钢锭经轧制或锻压成为钢材后方能使用,所以钢锭是半成品。
⏹根据浇注方法的分为上注钢锭和下注钢锭。
下注锭的表面质量优于上注锭。
⏹根据脱氧程度的不同又有沸腾钢钢锭、半镇静钢钢锭和镇静钢钢锭三种。
沸腾钢是脱氧不完全的钢,镇静钢是脱氧完全的钢,半镇静钢的脱氧程度介于前两者之间,接近于镇静钢。
钢锭的应用现状⏹模铸锭与连铸坯相比,所占比例逐年减少,最终将减少到约占10%,其中合金钢和不锈钢将减少到20%,工具钢和特殊钢将减少到40%。
这是由于连铸坯可以多炉连浇、收得率高、不需初轧或开坯、能耗低,质量甚至优于模铸锭。
⏹但模铸镇静钢不可能完全被淘汰,因为锻造用钢、一些小批量生产的高级合金钢及VAR(真空电弧重熔)和ESR(电渣精炼)用的坯料仍需用模铸镇静钢来生产。
钢锭的质量⏹钢锭的质量有表面质量和内部质量之分。
⏹表面质量:结疤、裂纹、表皮的纯净度和致密度。
⏹内部质量:钢锭内部的纯净度、致密度、低倍非金属夹杂物数量和宏观偏析的程度。
⏹沸腾钢的表面质量好,但由于锭心偏析大,内部质量不如镇静钢。
连铸:使金属液由中间包经浸入式水口不断地通过水冷结晶器,凝成硬壳后从结晶器下方出口连续拉出,经喷水冷却,全部凝固后切成坯料的一种铸造工艺。
连铸的设备以弧形连铸机为例,主要有钢包支承装置、盛钢桶(钢包)、中间罐、结晶器(一次冷却装置)、结晶器振动装置、铸坯导向和二次冷却装置、引锭杆、拉坯矫直装置(拉矫机)、切割设备和铸坯运出装置(见辊道和横向移送设备)等连铸的优点变间断生产为连续生产,产量↑(连铸比,连浇炉数)冷却强度大,铸造组织比较细密,偏析小切头切尾率少,成才过程烧损和切损少,成材率提高8~12%工艺过程缩短,生产周期短,能耗、运输成本降低,能耗降低30~60%(视是否热装、热送、直接轧制而定)环保条件好,无整、脱模时的污染便于自动化,提高技术水平连铸的好处在于节能和提高金属收得率。
连铸连轧综述
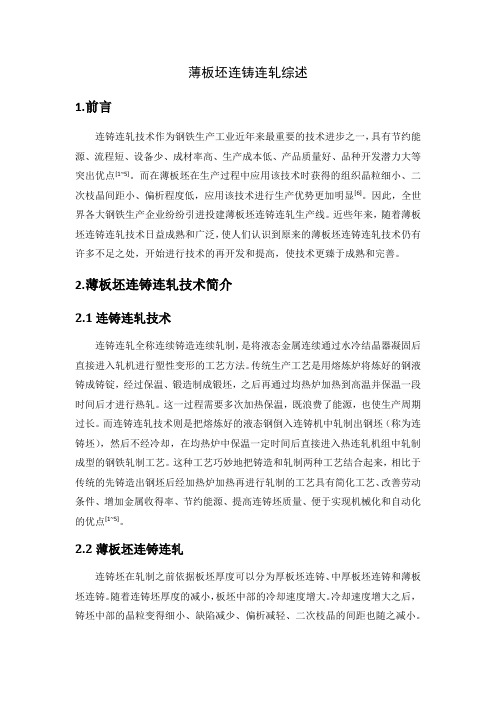
薄板坯连铸连轧综述1.前言连铸连轧技术作为钢铁生产工业近年来最重要的技术进步之一,具有节约能源、流程短、设备少、成材率高、生产成本低、产品质量好、品种开发潜力大等突出优点[1~5]。
而在薄板坯在生产过程中应用该技术时获得的组织晶粒细小、二次枝晶间距小、偏析程度低,应用该技术进行生产优势更加明显[6]。
因此,全世界各大钢铁生产企业纷纷引进投建薄板坯连铸连轧生产线。
近些年来,随着薄板坯连铸连轧技术日益成熟和广泛,使人们认识到原来的薄板坯连铸连轧技术仍有许多不足之处,开始进行技术的再开发和提高,使技术更臻于成熟和完善。
2.薄板坯连铸连轧技术简介2.1连铸连轧技术连铸连轧全称连续铸造连续轧制,是将液态金属连续通过水冷结晶器凝固后直接进入轧机进行塑性变形的工艺方法。
传统生产工艺是用熔炼炉将炼好的钢液铸成铸锭,经过保温、锻造制成锻坯,之后再通过均热炉加热到高温并保温一段时间后才进行热轧。
这一过程需要多次加热保温,既浪费了能源,也使生产周期过长。
而连铸连轧技术则是把熔炼好的液态钢倒入连铸机中轧制出钢坯(称为连铸坯),然后不经冷却,在均热炉中保温一定时间后直接进入热连轧机组中轧制成型的钢铁轧制工艺。
这种工艺巧妙地把铸造和轧制两种工艺结合起来,相比于传统的先铸造出钢坯后经加热炉加热再进行轧制的工艺具有简化工艺、改善劳动条件、增加金属收得率、节约能源、提高连铸坯质量、便于实现机械化和自动化的优点[1~5]。
2.2薄板坯连铸连轧连铸坯在轧制之前依据板坯厚度可以分为厚板坯连铸、中厚板坯连铸和薄板坯连铸。
随着连铸坯厚度的减小,板坯中部的冷却速度增大。
冷却速度增大之后,铸坯中部的晶粒变得细小、缺陷减少、偏析减轻、二次枝晶的间距也随之减小。
表1为文献[7]中根据钢研院提供的报告资料所做的统计。
因此,连铸连轧技术应用于薄板坯后的优势更加明显。
3.薄板坯连铸连轧技术的发展历史根据产品生命周期理论和薄板坯连铸连轧技术各个不同发展阶段的具体特征,特别是市场特征,可将薄板坯连铸连轧技术的发展分为下列四个阶段[8~12]:1、研发期(1985~1989)1986年德国施罗曼—西马克公司(SMS)建造了一台采用“漏斗型”结晶器的立弯式薄板坯连铸机,并以6 m/min的拉速成功地生产出50 mm×1600 mm的薄板坯,该技术被称为CSP。
最新薄带连铸连轧技术-宝钢专用

报告提纲1薄带铸轧研发历程薄带铸轧技术产业化现状及宝钢发展水平23薄带铸轧技术特征4宝钢薄带铸轧产品拓展及市场应用5薄带铸轧产业化存在问题及未来发展方向薄带铸轧,钢铁人一直的梦想160年前,英国冶金学家 H.Bessemer提出设想:直接把钢水浇铸成带钢。
直接浇铸1.4-2.5mm 一道次轧制0.7-2.0mm薄带连铸连轧工艺示意图薄带铸轧,前赴后继,不断成长D S C Hi k a r i N S C J A P ANHenry BessmerCHI N A E u r o p eAme r i c a M H IW a s ed a u n i ve r s i t y N K K H i t a c h i Z o s e n N M S H it ac h i P aci f i c m e t a l N i s h in s t e e l N i p p o n s t a i n l e s s s t e e l N i p p o n m e t a l s N i p p o n y a k i nSM I G e n e r a l e l e c t r i c w e s t i n g h o u s e Al l e g h e n y B a t e l l e i n l a n d M I T A r m c o W e i r t o n s t e e l Be h t l e h e m s t e e l I n l an d st e e lP r o j e c t B e s s e m e r Ca s t r i p B H PIH I K o r e aMEFOSBritish steel Danieli MDHD a v yCLECIMRUSSIE VNIMETMACHIRSID USINOR THYSSEN CSMVAI Krupp INNSES H SR IR A LC QU B a os t ee lB ao s t r i pE 2s t r i pP O S COP o s t r i pMPIIRSIDAachenMyosotisTKSEurostripKTNN UC OR P r o j e c t MMAINSMS1856-201640-50 TEAMS$4000-5000M年团队/公司/大学技术1856H.Bessemer双辊铸造概念提出1911 E.H.Strange单辊铸机1930-35 C.W.Hazelett铜、铝双辊铸造1956Hunter /Pechiney双辊铝铸造1957-69Waseda University (Japan)高硅、不锈钢双辊铸造1972-80M.Flemings流变铸造1980Mitsbishi Heavy Industries双辊铸造1983DOE单辊铸造1984Allegheny Ludlum不锈钢单辊铸造1986Nippon Steel不锈钢双辊铸造1986British Steel & Avesta Sheffield Limited双辊薄带铸机1987Pacific Metals & Hitachi Zosen不锈钢双辊铸机1989BHP & Ishikawajima Harima HeavyM,薄带铸轧Industries不锈钢双辊铸造1989POSCO Research institute of industrialscience & technology ,korea and Davyinternational年团队/公司/大学技术2014.03Baostrip工业化线建成2010.10castrip 第二条工业化线建成1989Thyssen and UsinorP ,双辊薄带连铸1992British steel and Avesta sheffield limited双辊薄带连铸1994Inland steel电磁侧封1995BHP & Ishikawajima Harima Heavy Industries中试工厂1995British steel and Avesta sheffield limited汽车用钢1997BHP & Ishikawajima Harima Heavy Industries碳钢产品1999Thyssen Krupp Usinor and VAI eurostrip 2000BHP ,Ishikawajima Harima Heavy Industries castrip 2002.05Castrip LLC 工业化线建成2002.10Nippon steel 工业化线建成2002.12Castrip LLC 商业化试生产2003.10Baostrip 中试线建成2006.08POSTRIP 工业化线建成2012-20161430工业化示范线建设NBS项目,装备、工艺技术集成,解决品种、质量及成本相关问题,产品的批量生产和销售。
连铸连轧
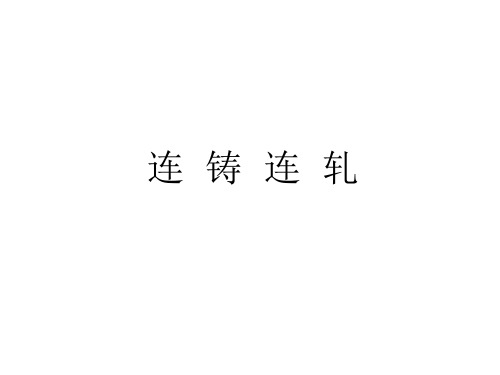
连铸机的形式
连铸工艺流程:1)炼钢炉炼出的合格钢水经炉外精炼处理;2)钢包运
送到浇铸位置注入中间包,通过中间包注入强制水冷铜模—结晶器内;3)
当结晶器内钢水升到要求的高度后,开动拉坯机,以一定速度把引锭杆(牵 着铸坯)从结晶器中拉出 4)铸坯被拉出结晶器后,为使其更快地散热,需
才能投入使用。毛管轧制就是对穿孔后的毛管进行壁厚加工,实现减 壁延伸,是壁厚接近或等于成品壁厚。
连轧管机组轧制过程示意图
1-轧辊 2-浮动芯棒 3-毛管
(4) 管材的定、减径
毛管在轧管机上进行了以减壁为主的加工后,已成为壁厚接近于
成品的荒管。为了扩大产品使用范围,就需要对其外径进行加工,同 时对壁厚继续进行少量加工,这就是钢管生产中的第三个阶段—定径、
要进行喷水冷却,称之为二次冷却,通过二次冷却支导装置的铸坯逐渐凝固。
1-钢包 2-中间包 3-结晶器及震荡装置 4-电子搅拌器 5-二冷区支导装置 6-拉矫机 7-切割装置 8-辊道 9-轧件
管 材 轧 制
三辊行星轧机生产线
电解铜
熔化
铸造
轧制
二联拉
盘拉
成品
退火
水平缠绕
内螺纹成型
退火
铸轧法生产铜管工艺流程图
连 铸 连 轧
连铸连轧(CCDR):由连铸机生产出来的高温无缺陷坯,无需清理
和再加热(但需短时间均热和保温处理)而直接轧制成材,即把“铸” 和“轧”直接连成一条生产线的工艺流程。
CCDR生产线
1-钢包 2-双臂回转架 3-中间包 4-弧形连铸机 5-剪断机 6-粗轧机组 7-中轧机组
连铸连轧知识点

连铸连轧知识点连铸和连轧是金属工业中常见的两个工艺过程。
连铸是指将液态金属连续铸造成坯料的过程,而连轧是指将坯料经过一系列压制和变形操作,连续地轧制成所需尺寸的金属板、带材或线材的过程。
本文将介绍连铸和连轧的基本概念、工艺流程和主要应用。
一、连铸连铸是一种高效的金属铸造技术,具有生产速度快、坯料质量好等优点。
连铸主要应用于钢铁、铜、铝等金属的生产中。
1. 连铸的基本原理连铸的基本原理是将熔融的金属通过连续浇注的方式,直接铸造成连续的坯料。
具体原理如下:首先,将金属熔融至液态,并通过加热设备保持在一定温度范围内;然后,通过连续浇注系统,将熔融金属均匀地注入到连铸结晶器中;在连铸结晶器中,通过冷却剂的作用,使金属迅速凝固,并形成坯料;最后,通过一系列传动装置,将连续产生的坯料送往下游的轧制设备或其他后续处理过程中。
2. 连铸的工艺流程连铸的工艺流程一般包括以下几个关键步骤:(1)冶炼:将矿石等原料经过熔炼处理,得到液态的金属合金;(2)调温:通过加热设备将金属保持在一定的液态温度;(3)连续浇注:通过连续浇注系统,将熔融金属注入到连铸结晶器中;(4)结晶与凝固:在连铸结晶器中,通过冷却剂的作用,使金属迅速凝固,并形成坯料;(5)切割和输送:将连续产生的坯料切割成合适的长度,并送往下游的加工设备。
3. 连铸的应用连铸广泛应用于钢铁、铜、铝等金属的生产中。
在钢铁工业中,连铸可以直接将炼钢铁水铸造成连续坯料,用于后续轧制成钢板和钢材。
在有色金属工业中,连铸可以将液态金属铸造成连续的板材、带材和线材,用于制造电线电缆、汽车零部件等产品。
二、连轧连轧是一种将金属坯料经过多道次的压制和变形操作,连续地轧制成所需尺寸的金属板、带材或线材的工艺过程。
连轧具有高效快速、坯料成形完整等特点,广泛应用于钢铁、有色金属等工业领域。
1. 连轧的基本原理连轧的基本原理是通过一系列的压制和变形操作,使金属坯料逐渐减小厚度、增大长度,并达到所需的尺寸要求。
连铸连轧生产工艺
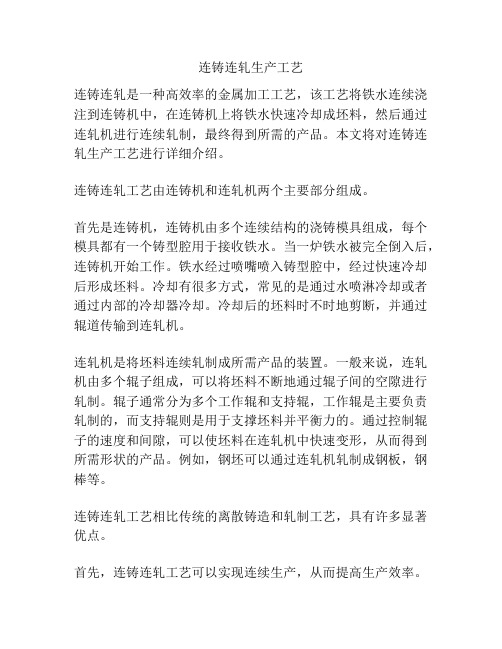
连铸连轧生产工艺连铸连轧是一种高效率的金属加工工艺,该工艺将铁水连续浇注到连铸机中,在连铸机上将铁水快速冷却成坯料,然后通过连轧机进行连续轧制,最终得到所需的产品。
本文将对连铸连轧生产工艺进行详细介绍。
连铸连轧工艺由连铸机和连轧机两个主要部分组成。
首先是连铸机,连铸机由多个连续结构的浇铸模具组成,每个模具都有一个铸型腔用于接收铁水。
当一炉铁水被完全倒入后,连铸机开始工作。
铁水经过喷嘴喷入铸型腔中,经过快速冷却后形成坯料。
冷却有很多方式,常见的是通过水喷淋冷却或者通过内部的冷却器冷却。
冷却后的坯料时不时地剪断,并通过辊道传输到连轧机。
连轧机是将坯料连续轧制成所需产品的装置。
一般来说,连轧机由多个辊子组成,可以将坯料不断地通过辊子间的空隙进行轧制。
辊子通常分为多个工作辊和支持辊,工作辊是主要负责轧制的,而支持辊则是用于支撑坯料并平衡力的。
通过控制辊子的速度和间隙,可以使坯料在连轧机中快速变形,从而得到所需形状的产品。
例如,钢坯可以通过连轧机轧制成钢板,钢棒等。
连铸连轧工艺相比传统的离散铸造和轧制工艺,具有许多显著优点。
首先,连铸连轧工艺可以实现连续生产,从而提高生产效率。
相比离散铸造和轧制工艺,连铸连轧工艺减少了产品在生产过程中的停留时间,有效减少生产周期,提高了生产效率。
其次,连铸连轧工艺可以减少产品的变形和出现缺陷的可能性。
在连铸连轧过程中,坯料的变形是在连续产生的,产品形状相对稳定,因此可以减少变形和出现缺陷的可能性。
同时,由于坯料在连轧过程中受到很大压力的作用,使其内部结构更加紧密,提高了产品的强度和硬度。
最后,连铸连轧工艺还可以减少能耗并降低生产成本。
连续生产可以减少能耗浪费,同时由于工艺参数的控制更加精准,可以减少废品率,降低了生产成本。
总之,连铸连轧是一种高效率的金属加工工艺,通过连续的铸造和轧制过程,可以快速地生产出所需的产品。
其优点包括高生产效率,减少变形和缺陷的可能性,降低能耗和生产成本等。
连铸连轧综述

薄板坯连铸连轧综述1.前言连铸连轧技术作为钢铁生产工业近年来最重要的技术进步之一,具有节省能源、流程短、设施少、成材率高、生产成本低、产品质量好、品种开发潜力大等突出优点11~文而在薄板坯在生产过程中应用该技术时获得的组织晶粒细小、二次枝晶间距小、偏析程度低,应用该技术进行生产优势更加明显⑹。
因此,全世界各大钢铁生产企业纷纷引进投建薄板坯连铸连轧生产线。
近些年来,随着薄板坯连铸连轧技术日益成熟和广泛,使人们熟悉到原来的薄板坯连铸连轧技术仍有很多不足之处,开头进行技术的再开发和提高,使技术更臻于成熟和完善。
2.薄板坯连铸连轧技术简介2.1连铸连轧技术连铸连轧全称连续铸造连续轧制I,是将液态金属连续通过水冷结晶器凝固后直接进入轧机进行塑性变形的工艺方法。
传统生产工艺是用熔炼炉将炼好的钢液铸成铸锭,经过保温、锻造制成锻坯,之后再通过均热炉加热到高温并保温一段时间后才进行热轧。
这一过程需要多次加热保温,既铺张了能源,也使生产周期过长。
而连铸连轧技术则是把熔炼好的液态钢倒入连铸机中轧制出钢坯(称为连铸坯),然后不经冷却,在均热炉中保温肯定时间后直接进入热连轧机组中轧制成型的钢铁轧制工艺。
这种工艺奇妙地把铸造和轧制两种工艺结合起来,相比于传统的先铸造出钢坯后经加热炉加热再进行轧制的工艺具有简化工艺、改善劳动条件、增加金属收得率、节省能源、提高连铸坯质量、便于实现机械化和自动化的优点口~叫2.2薄板坯连铸连轧连铸坯在轧制之前依据板坯厚度可以分为厚板坯连铸、中厚板坯连铸和薄板坯连铸。
随着连铸坯厚度的减小,板坯中部的冷却速度增大。
冷却速度增大之后,铸坯中部的晶粒变得细小、缺陷削减、偏析减轻、二次枝晶的间距也随之减小。
表1为文献⑺中依据钢研院供应的报告资料所做的统计。
因此,连铸连轧技术应用于薄板坯后的优势更加明显。
表2 根据钢研院提供的报告资料统计生产工艺铸坯厚度(mm)冷却速度木F品间距(mm)中间品粒组织情况厚板环连铸200-300W― 10°450晶粒粗大,有中心疏松中厚板坯连铸>90-150IO-1l~ιo∣250薄板坯连铸40-70IO1-IO240~100晶粒细小,致密,没有疏松3.薄板坯连铸连轧技术的进展历史依据产品生命周期理论和薄板坯连铸连轧技术各个不同进展阶段的详细特征,特殊是市场特征,可将薄板坯连铸连轧技术的进展分为下列四个阶段bl©:1、研发期(1985~1989) 1986年德国施罗曼一西马克公司(SMS)建筑了一台采纳“漏斗型”结晶器的立弯式薄板坯连铸机,并以6m∕min的拉速胜利地生产出50 mmX 1600 mm的薄板坯,该技术被称为CSP。
热轧薄板带钢生产-连铸连轧及连续铸轧技术教学课件46P
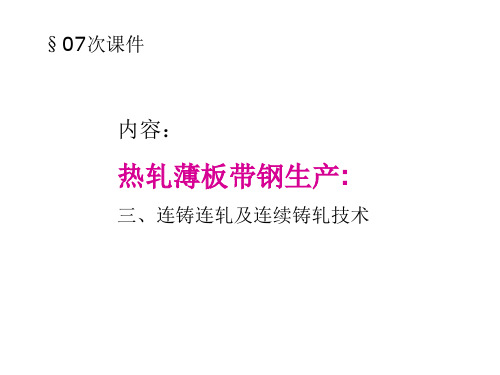
温
炉
薄
度
炼 钢 炉
外 精 炼 装
板 坯 连 铸
流 量 衔 接
热 连 轧 机
置
机
装
置
刚性工艺装置
柔性工艺装置
1.薄板坯连铸设备
2.温度、流量衔接装置:称为均热炉
形式有三种:
直通式辊底隧道炉、感应加热炉、步进炉应加热炉 1)直通式辊底隧道炉
(1) 直通式辊底隧道炉的结构、特点及参数
炉子长度:200米左右 炉子分段: 加热段、保温段、缓冲段、出料段等组成。
目的:改善轧辊磨损和轧辊辊面粗糙。
(4)润滑轧制技术
概念:在轧制过程中,向轧辊辊面喷涂一种特殊轧制 油,通过辊子的旋转,将润滑剂带入变形区,使轧辊及轧 材表面形成一层极薄的油膜。
优点:油膜改变了变形区的变形条件,降低了轧制力, 减少了轧辊的磨损,提高了产品的表面质量。
难点:如何解决轧件咬入问题,即选择最优的喷油开 闭时间
控制理论:利用液压压下的高响应性和良好的设定精度, 开发了高精度的轧机水平调整技术。它可以在极短的时 间内进行自动水平调整,使左右两侧轧制力之差恒定, 从而实现了蛇形控制。
三、典型的薄板坯连铸连轧工艺
1)CSP工艺技术 (Compact Strip Production—紧凑式带钢生产技术) (1)主要设备: 组成:CSP连铸机、辊底式加热炉、精轧机、层流冷却
C 克服在两相区轧制的危害;(因奥氏体轧制时温降 大,有时进入两相区)
D 提高轧机的生产效率;(增大压下,减小道次)
E 生产更薄规格的热轧带钢;(铁素体较软) F 为冷轧提供冲压性能更高的带钢。
(2)半无头轧制技术
概念:
铸坯长度相当于4~6块单块轧制的薄板坯,加热后进入 轧机,轧后的带钢由高速飞剪分切成所要求重量的钢卷。 优点:
薄板坯连铸连轧技术培训讲义

薄板坯连铸连轧技术培训讲义1. 引言薄板坯连铸连轧技术是一种先进的钢铁生产工艺,在钢铁制造过程中扮演着至关重要的角色。
本文档将介绍薄板坯连铸连轧技术的基本原理、流程和关键设备。
2. 基本原理薄板坯连铸连轧技术是将熔融的钢水通过连铸机连续铸造成为薄板坯,然后通过连轧机进行连续轧制,最终获得所需的薄板产品。
其基本原理如下:•连铸:钢水经过特殊的连铸机,在结晶器中快速冷凝,形成坯料,并通过辊道送至连轧机。
•连轧:坯料经过连轧机的一系列辊道,不断轧制变形,逐渐变薄并形成所需的薄板产品。
3. 工艺流程薄板坯连铸连轧工艺的主要流程包括连铸、坯料切割、连轧以及最终产品处理。
以下为具体步骤:3.1 连铸1.钢水预处理:熔融的钢水经过除杂、除气等预处理步骤,以提高钢水质量。
2.连铸开始:将预处理后的钢水注入连铸机的结晶器中,通过连续浇注形成连续的坯料。
3.结晶器冷却:结晶器中的冷却水快速冷凝坯料表面,促使坯料凝固和形成。
3.2 坯料切割1.坯料切割开始:连铸后的坯料通过切割机进行切割,得到所需长度的薄板坯。
2.切割方式:常见的切割方式为热切割和冷切割,根据材质和产品要求选择合适的方式。
3.3 连轧1.连轧机介绍:连轧机主要由多对辊道组成,用于将薄板坯逐渐轧制成所需的薄板产品。
2.轧制工艺:通过不断的轧制和辊道调整,使坯料逐渐变薄和延展,形成所需的薄板产品。
3.冷却处理:连轧后的薄板需要经过冷却设备进行冷却处理,以达到产品要求的硬度和性能。
3.4 最终产品处理1.张力控制:薄板产品在连轧过程中受到一定的拉力,需要通过张力控制系统进行控制,防止产生过大或过小的张力。
2.切边、打包:最后对薄板产品进行切边和打包,以便于运输和存储。
4. 关键设备薄板坯连铸连轧技术涉及到多种关键设备。
以下列举一些重要的设备:1.连铸机:用于将熔融的钢水连续浇注成坯料。
2.切割机:将连铸后的坯料按照所需长度进行切割。
3.连轧机:用于将坯料进行连续轧制,使其逐渐变薄并形成薄板产品。
短流程连铸连轧成套装备的设备结构和主要组成部分介绍
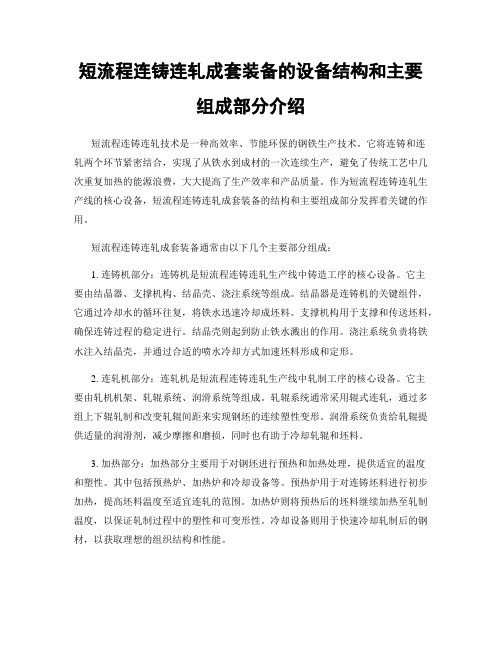
短流程连铸连轧成套装备的设备结构和主要组成部分介绍短流程连铸连轧技术是一种高效率、节能环保的钢铁生产技术。
它将连铸和连轧两个环节紧密结合,实现了从铁水到成材的一次连续生产,避免了传统工艺中几次重复加热的能源浪费,大大提高了生产效率和产品质量。
作为短流程连铸连轧生产线的核心设备,短流程连铸连轧成套装备的结构和主要组成部分发挥着关键的作用。
短流程连铸连轧成套装备通常由以下几个主要部分组成:1. 连铸机部分:连铸机是短流程连铸连轧生产线中铸造工序的核心设备。
它主要由结晶器、支撑机构、结晶壳、浇注系统等组成。
结晶器是连铸机的关键组件,它通过冷却水的循环往复,将铁水迅速冷却成坯料。
支撑机构用于支撑和传送坯料,确保连铸过程的稳定进行。
结晶壳则起到防止铁水溅出的作用。
浇注系统负责将铁水注入结晶壳,并通过合适的喷水冷却方式加速坯料形成和定形。
2. 连轧机部分:连轧机是短流程连铸连轧生产线中轧制工序的核心设备。
它主要由轧机机架、轧辊系统、润滑系统等组成。
轧辊系统通常采用辊式连轧,通过多组上下辊轧制和改变轧辊间距来实现钢坯的连续塑性变形。
润滑系统负责给轧辊提供适量的润滑剂,减少摩擦和磨损,同时也有助于冷却轧辊和坯料。
3. 加热部分:加热部分主要用于对钢坯进行预热和加热处理,提供适宜的温度和塑性。
其中包括预热炉、加热炉和冷却设备等。
预热炉用于对连铸坯料进行初步加热,提高坯料温度至适宜连轧的范围。
加热炉则将预热后的坯料继续加热至轧制温度,以保证轧制过程中的塑性和可变形性。
冷却设备则用于快速冷却轧制后的钢材,以获取理想的组织结构和性能。
4. 输送设备:输送设备主要包括钢坯输送机、辊道输送机、插入传送机等。
它们负责将钢坯从一个部分转移到下一个部分,确保整个生产过程的连续性和协调性。
钢坯输送机通常用于将连铸机产出的钢坯送至连轧机,通过链条或链板等方式进行传送。
辊道输送机用于将连轧机轧制完成的钢材送至下一环节,如冷却设备或整热处理设备。
- 1、下载文档前请自行甄别文档内容的完整性,平台不提供额外的编辑、内容补充、找答案等附加服务。
- 2、"仅部分预览"的文档,不可在线预览部分如存在完整性等问题,可反馈申请退款(可完整预览的文档不适用该条件!)。
- 3、如文档侵犯您的权益,请联系客服反馈,我们会尽快为您处理(人工客服工作时间:9:00-18:30)。
(3) 热加工履历不同,N,C,S等析出物的固溶析出历
程,机制不同,其形态分布通过控轧控冷更易控制,更有 利于合金元素作用的发挥和组织性能的提高。冷装既析出 再固溶较难;连铸连轧时无(少)析出,始终固溶再经变 形诱导析出,更细更均布,未析出部分再经相变沉淀硬化, 进一步提高性能质量; (4) 连铸连轧工艺控制得当更有利于钢的高温塑性,防 止裂纹等缺陷的产生,提高 成形质量,CC-DR,DHCR防 止“红送裂纹”产生。
2.2 铸坯质量的保证技术
(1)保证连铸坯质量是连铸及连铸连轧工艺得以成立 和发展的前提(物美价廉) 由于炼钢技术(炉外精练)提高了钢的纯净度, (S,P,N,H,O等)杂质含量由过去500×10-6降至100×10- 6,及连铸技术的提高(保护浇注,潜入式水口,保护渣润 滑,电磁搅拌,气水雾化冷却,软压下,压缩浇铸等)已使 连铸坯质量基本得到保证。一般无缺陷率可在96%以上,满 足生产要求,故检测难而无需检测。在诸多内外表面缺陷中, 最障碍连铸连轧工艺实现的是表面裂纹缺陷,因其不能进行 表面清理; (2)表面裂纹的形成机理:开裂必须:受力;弱点,应 力集中超过断裂强度。一般碳钢三个高温脆性区为图2所示。
2.1 连铸连轧的金属学特点 (与传统工艺相比)
(1) 铸坯热履历不同使原始晶粒组织不同 1)近终形连铸快冷,枝晶短,晶粒细均,偏析少, 有利; 2)但历程无相变细化晶粒作用,无γ-α-γ,易使原 始γ体晶粒粗大, (α+γ)HCR甚至易产生混晶 (原γ长大,α被吞蚀或变成细的新γ晶), 不利。这只 有通过粗轧高温大压下再结晶作用来补救,但低温热装却与 冷装无异; (2) 热加工履历不同,液芯软压下改善中心组织,晶粒 细化作用大,疏松偏析少;;
2 流 3 × 9 0( 公 称 ) 涟源钢 7 铁厂 钢)转炉 机 / 1 05 t 实 际 出 ( CSP 铸 ( 800~1600) 机 立弯型 ( 70~55) × 230 SMS 轧 0 . 8 ~1 2. 7 炉 291m× 2 7 机架 辊底式均热 2 8. 0 2004-3
2 流 8 本溪钢铁厂 与唐钢类似 FTSR 铸 机 90~70 250 2+5 机 架 0.8~6.0 辊底式均热炉 2005
距板坯边部40mm的温 度降 板坯剪切断面的温度降 AlN沉淀
(济钢火车保温箱
平均-4℃∆t 145分温56℃
4小时 温降95℃)
大 有
小 无
表1 在板坯运距超过1000m时辊道和保温运输车的比较
1.2 连铸连轧工艺优势及关键技术
1.2.1 主要优点: 主要优点: (1)节能:装炉温越高节能越多,DR可节加热能耗80- 85%,黑匣子工艺可节70-80%甚至可90-100%,即可 达 到0燃耗。据统计钢坯热装每提高100℃,即可节能60 -70Mj/t;如安阳汽车保温装车750℃,装炉600℃,节热 能38%,出炉降60~80℃; (2)节钢耗:提高成材率0.5~1.5%(韶关1.5%); 事故少,中 废少; (3)短流程:节厂房与设备基建投资与生产费用及人工 等;缩生产 周期及资金周转期。 (4)提高产品质量:1)连铸坯提高质量; 2)表面质量提高,铸坯表面裂纹 少,氧化麻点少;
项目 运输速度 距离 时间 绝热效果
保温辊道 最高90m/min 平均70 m/min 1000m 14.5min
保温运输车 最高250 m/min 平均 200 m/min 1000m 5min
平均h=11.6 平均 h=94.2W/(m2·K).(81kc W/(m2·K)(10kcal/(m2· al/(m2·h·℃)) h·℃)) 平均-180℃
1.3.3 中、薄板坯连铸连轧技术的发展 国际上自1992年,德国CSP、ISP在Nucor及Avedi,投 产以后,1995年意大利达涅利的FTSCR、奥钢联(中板坯) CONROLL、日本佳友的QSP工艺相继推出投产,至今已有 50余条生产线投产,我国6年来,即已有12条多生产线要投 产(见表 );另外,国际上,自1997年美国IPSCO公司蒙特 利埃厂的3450mm炉卷轧机连铸连轧中板卷投产以来(美国 的TSP工艺)世界已有8套炉卷轧机,我国也有2~3条生产线 投产a-1(见表)。 我国中、薄板坯连铸连轧自90’s来至今5~6年已发展 至十多家,如下表:
9
通化钢铁公司
与唐钢类似
FTSR
90~70
250
2+5 机 架
0.8~6.0
辊底式均热炉
2006
10
济南钢铁公司
与 ASP 类 似
CONROLL
120~150
1+6 机 架
1.2( 最 小 )
步进式加热炉
2005
唐山钢 11 铁公司
与 ASP CONROLL 类似 120~150
1+6 机
1.2( 最 步进式加热炉 2006
1.3 我国钢的连铸连轧技术的发展概述
1.3.1 连铸连轧技术发展的几个阶段 1.3.2 棒线材连铸连轧技术的发展 我国小型棒线材生产过去受到坯料和轧机装备水平 限制,多采用多火成材工艺,随着炼钢、连铸水平的提高, 目前我国棒线材生产大都直接使用连铸坯成材。新建的轧 机很多采用CC—DHCR工艺,如石家庄 安阳、济南、涟源、韶关唐山和上海等地钢厂都采用 CC—DHCR工艺, 仅意大利达涅利即有7条特钢棒材连铸连轧生产线,在我 国江阴兴澄钢厂等处投产。
2流 (50~70)× 立弯型 CSP 铸 (980~1680) 机 246 SMS 轧机 小) 191.8m×2 1+6 机架 1.2(最 辊底式均热炉
鞍山 2×90 (公称) /110t 3 钢铁 (实际出钢)转炉 厂
2 流直弧型
135 2+6 机架 1.0(最 步进式加热炉 SMS 轧机 小)
由上可知,现在各家开发的工艺都已是互相嫁接混同了,为 提高产品质量品种共同的发展趋向及工艺技术要点为: 1).提高钢水质量与纯净度、生产洁净钢是重要基础。当今 所谓超细晶粒钢主要就是超洁净钢加低温大压下控轧控冷生 产的。故最好是高炉、转炉加精炼炉工艺保证钢水质量。 2).为提高铸坯质量与产量及提高压缩比和立辊轧边效率以 提高产品品种质量,增大铸坯厚度成为技术发展趋势:尤其 为了满足结晶器内流场及保护渣的熔化条件改善铸坯表面质 量(减少卷渣),应增大厚度,现CSP已由40-50mm增至60 -70mm,ISP增至70-90mm,FTSC采用70-90mm,QSP用70- 100mm,CONROLL及TSP用120-150mm厚的板坯。
中 国 现 有 14 条 薄 板 坯 连 铸 连 轧 生 产 线 概 况 Survey of TSCR production lines in China
序 钢厂 号 炼钢炉 连铸机 薄 板 坯 尺 寸 /mm
计算规模/ -1 万 t· a
最终产品 轧机 尺 寸 /mm 均(加)热炉
总投资估算/ 亿 元( 人 民 币 )
单机炉卷
中板卷
步进式加热炉
32~34
2004-9
15
韶关钢铁公司
预留炉卷机
由上表看来,我国的中、薄板坯连铸连轧工艺主要分为四类 情况即CSP工艺(5家)、FTSR工艺(4家)、CONROLL工 艺(5家)。除CSP工艺以外,其余都是分为粗轧和精轧两段 轧机,而且CONROLL工艺粗轧是可逆的,其板坯厚度属中 等在100~150mm之间,因而可采用容量大,占厂房面积小的 国产的步进式炉。邯钢、鞍钢(ASP)都申报了发明专利。
CONROLL 铸机
(100~150)×
220
(ASP)
(900~1620)
包头
2流 (50~70)× 6 机架 220 (900~1560) SMS 轧机 小) 1.2(最
辊底式均热炉
4
钢铁
2×210t 转炉
立弯型 CSP 铸
200.8m×2 摆动式
厂
机
联接
2 流直 唐山钢 弧型 5 铁 230 2× 150t 转 炉 F TS R 铸 厂 250 机 ( 850~1680) 达涅利 ( 90~70, 65) × 250 架三菱+ 0.8~6.0 炉 231m× 2 2+5 机 辊底式均热 2 6. 4 2 0 02 -12
3)中、薄、细连铸坯——必须连铸连轧——必须控轧控 冷——轧机应分粗、精轧二组。必须是强力型轧机,每道次 压下>50-40%,便于控轧控冷,高度自动控制,就2)与3) 而言,FTSCR与CONROLL工艺都比CSP工艺优越。 4)CONROLL、ASP工艺优点: ⅰ)采用厚坯便于连铸及采用步进式加热炉。 ⅱ)轧机分粗、精轧二组,且粗轧为带立辊可逆,经济灵 活。 ⅲ)粗轧后采用热卷取箱,实现均温恒速轧制。
投产日 期
珠江 2× 150t 1 钢铁 电弧炉 厂
2流 50× 立弯型 ( 950~1350) CSP 铸 机 180 SMS 轧 机 小) 191.8m× 2 6 机架 1.27( 最 辊底式均热炉 32.0 1998-11
邯郸 2×100 公称) ( /120t 2 钢铁 (实际出钢)转炉 厂
钢的连铸连轧技术 东北大学 王廷溥教授
1.钢的连铸连轧技术概述与产品质量控制技术 钢的连铸连轧技术概述与产品质量控制技术
为图1所示
1.1 连铸与连轧衔接工艺类型
类型5 —— CC-CCR冷装炉轧制 类型4 —— CC -αHCR 类型3 —— (α+γ)HCR 类型2 —— γHCR或DHCR 类型1 —— CC—DR 类型1’――CR(Cast-Rolling) 钢材生产工艺连续化,铸轧一体化趋向 连铸连轧的定义:1及2能实现均衡连续化生产,无相变工艺
3)坯温均匀,提高厚度精度及板形质量;提高性能, 均 匀质量,各向异性小; 4)采用TMCP等术,控制好晶粒及析出物更有利于 微合金化及TMCP作用的发挥,提高综合机械性能。