各种连铸连轧生产线的比较
连铸连轧法生产铜杆---图

连铸连轧法生产铜杆一、连铸连轧铜杆生产工艺过程:电解铜加料机竖炉上流槽保温炉下流槽浇堡铸造机夹送辊剪切机坯锭预处理设备轧机清洗冷却管道涂蜡成圈机包装机成品运输二、连铸连轧铜杆生产线当前世界各国采用的铜杆连续生产线新工艺主要有:意大利的Properzi系统(缩称CCR系统),美国的SouthWire系统(缩称SCR系统)、联邦德国的Krupp/Hazelett系统(缩称Contirod系统)、以及将法国的SECIM系统。
这些系统在原理上基本相同,工艺上也大同小异,其差异主要是在铸机和轧机的形式和结构上。
CCR系统沿用铝连铸连轧的双轮铸机和三角轧机形式连铸连轧铜杆。
最初铜铸锭截面1300mm²,现在最大可达2300mm²,理论能力18t/h,轧制孔型系“三角——圆”系统。
当锭子截面太大时,原轧机前面加两平一立辊机架,采用箱式孔型开坯,箱孔型道次减缩率在40%左右。
SCR系统是在CCR的基础上改进而成的如图2-35,铸机由双轮改为五轮(一大四小),轧机则改为平一立辊式连轧机,孔型改为箱—椭—圆系统。
头上两道箱式孔型同样起开坯作用。
SCR五轮铸机可铸铜锭截面6845 mm²,理论能力2518t/h。
图2-351——提升机及加料台2——熔化炉3——保温炉4——液压剪5——铸锭整形器6——飞剪7——酸洗8——卷取装置9——精轧机组10——粗轧机组11——连铸机Contirod系统工艺和生产规模基本上和SCR一样,只是铸机改用了“无轮双钢带式”即Hazelett式。
SECIM系统(图2-36),采用四轮式连铸机,(一大三小),最大铸锭截面4050mm²,11机架,孔型前三道为箱—扁—圆系统。
生产铜杆φ7~16mm,重量达到5t,生产能力30 t/h。
图2-361——熔化炉2——保温炉3——四轮式连铸机4——去切边角装置5——予处理装置6——粗轧机7——中间剪刀8——精轧机9——清洗管道10——自动绕杆机三、主要工艺设备1.竖炉竖炉熔铜炉是由美国熔炼公司研究设计的,它是用来连续熔化电解铜,也可以加入一些清洁的废铜屑,这种竖炉简称ASARCO,它具有生产效率高,控制方便不需要吹氧去硫和插木还原,就能获得合格的铜液。
不同连铸工艺生产电工钢的工艺技术比较

摘要 : 合常规厚板坯工艺 、 结 中等 厚 度 板 坯 工 艺 和 薄 板 坯 工 艺 生 产 电工 钢 的工 艺 技 术 特 点 、 坯 铸 态 组 织 、 出物 的 分 板 析 布 和 大 小 、 坯 表 面 质 量 等 方 面 进 行 了工 艺 技 术 比较 , 电工 钢 的生 产 工 艺 选 择 和 铸 坯 质 量控 制提 供 技 术 参 考 。 铸 为
Ke r : h n s a r e s;t c lb pr c s ;e e ti a t e ;t c i a o p rs n y wo ds t i l b p oc s hik sa o e s l c rc ls e l e hn c lc m a io
电工钢 , 包括 取 向电工钢 和无 取 向电工钢 , 是制 造 电机 、 变压器 和镇 流器 铁 芯 以及 各 种 电 器元 件 用 以 节 能 的最 重 要 的金 属 功 能 材 料 。据 统 计 , 个 国 家 的 一 6 以上 的 电量 都是 由这些 电工 钢 制造 的 电机 、 压 O 变 器和 电器消耗 掉 的 。近 年来我 国 的发 电量 以较 大 的幅 度增长 , 特别是 随着 三 峡 水 电工 程 的 投入 运 行 和 长 江 上游大 型水力 发 电系统 以及 其 他 大型 核 电、 电 发 电 火
艺技术 特 点 、 板坯 铸 态组 织 、 出物 的分 布 和 大小 、 析 板 坯表 面质量 、 成材 率 以及 生 产操 作 等 方 面及 其 对 电工 钢铸坯 产量 和质量 的影 响进行 综合 分析 和技术 比较 。
系统的建 设 , 国的发 电量 将大 幅度增 加 , 我 因此必 将带 动 电工钢 的强 劲 需 求 。随着 国 民 经 济 的 健 康 快 速 发
连铸连轧生产:连铸的优越性

1.1 钢的浇注概述
1.1.3连铸的优越性
2 提高金属收得率 采用模铸工艺,金属收得率为84%~88%,而连铸工艺则为 95%~96%,金属收得率提高10%~14%。 3 降低能源消耗 采用连铸工艺比传统模铸工艺可节能1/4~1/2,如果连铸坯采 用热装技术或者直接轧制技术,能源消耗还会进一步降低,同时 生产周期也会减少。
感谢聆听
1.1 钢的浇注概述
1.1.3连铸的优越性
需要指出的是,现阶段连铸工艺还不能完全取代模铸工艺, 主要原因在于,有些钢种的特性不适合于连铸生产,比如高锰钢。 另外一方面对于一些小批量、大厚度高强度的钢材,连铸还是无 法取代模铸。虽然目前连铸机生产最大板坯厚度可以达到700mm, 不能轧制200mm以上的钢板,而且连铸坯厚度越厚,存在的生产 问题与质量问题也越多。
连续铸钢生产
1.1 钢的浇注概述
1.1.3连铸的优越性
两种工艺之间最根本的区别在于模铸属于间断生产,而连铸 属于连续生产,正是基于这一根本区别,相比于模铸工艺,连铸 工艺具有以下优越性:
1 简化工序,缩短流程 连铸工艺省去了脱模、整模、钢锭均热、初轧开坯等工序, 可节省基建投资费用约40%,减少占地面积约30%,节省性
4生产过程机械化、自动化程度高 设备和操作水平的提高,采用全过程的计算机控制管理,不 仅从根本上改善了劳动环境,还大大提高了劳动生产率。 5提高质量,扩大品种 大部分钢种均可以采用连铸工艺生产,如硅钢、工具钢等约 500多个钢种都可以用连铸工艺生产,而且质量很好。
铝合金连续铸轧和连铸连轧技术

铝合金连续铸轧和连铸连轧技术近几年,铝合金连续铸轧和连铸连轧技术得到了广泛的关注和应用,在航空、交通、电子和生产等领域发挥着重要作用,并取得了可喜的成就。
本文介绍了铝合金连续铸轧和连铸连轧技术,总结其优点和应用领域,并展望未来发展。
首先,让我们先来介绍连续铸轧技术。
连续铸轧是把铸态的毛坯在双辊铸轧机上连续铸轧的一种特殊的铸轧技术。
它不仅可以在一条生产线上完成整体模块的加工,还可以连续涂层、连续切削、连续横切,从而实现大批量生产,提高生产效率。
此外,它还可以提高材料的性能,降低成本,但是操作起来比较复杂,容易出错。
连铸连轧技术,也称为热轧技术,是将铁水经连续送料炉溅射、蒸发冷凝池或冷却池自动加工成一定规范形状的毛坯精加工成所需规格和性能的钢材的一种特殊的技术。
它有很多优点:操作简单,精度高,材料质量好,成品率高,生产效率高,投资少,特别适用于量大、精度高的产品的生产,有较好的经济效益。
铝合金连续铸轧和连铸连轧技术可用于制造高性能的铝空心结构件、铝芯轴以及汽车零部件等铝合金结构件。
它具有节能、环保、能耗低、操作方便等优势,应用于航空航天、汽车、电子电器、医疗器械等领域可以节约资源,提高工作效率。
未来,随着技术的发展,铝合金连续铸轧和连铸连轧技术将更加成熟,获得更多的关注和应用。
同时,随着用户消费趋向的变化,针对不同类型的产品,研究者也会发展出更多新型的生产工艺,以期在节能、环保、成本等方面取得更好的效果。
综上所述,铝合金连续铸轧和连铸连轧技术是近几年中取得可喜成绩的一种先进技术,它具有节能、环保、成本低等优势,将带给我们更多的经济和社会效益。
未来,铝合金连续铸轧和连铸连轧技术将朝更高层次发展,为人类社会做出更多的贡献。
浅谈Hazelett连铸连轧产品的特性与应用
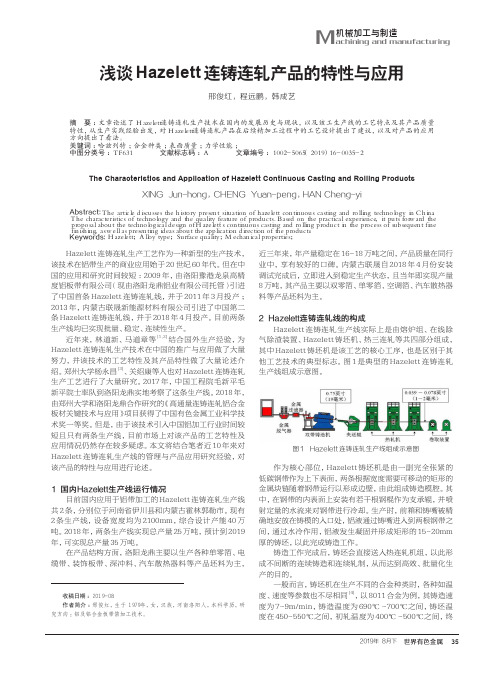
机械加工与制造M achining and manufacturingHazelett连铸连轧生产工艺作为一种新型的生产技术,该技术在铝带生产的商业应用始于20世纪60年代。
但在中国的应用和研究时间较短:2009年,由洛阳豫港龙泉高精度铝板带有限公司(现由洛阳龙鼎铝业有限公司托管)引进了中国首条Hazelett连铸连轧线,并于2011年3月投产;2013年,内蒙古联晟新能源材料有限公司引进了中国第二条Hazelett连铸连轧线,并于2018年4月投产。
目前两条生产线均已实现批量、稳定、连续性生产。
近年来,林道新、马道章等[1,2]结合国外生产经验,为Hazelett连铸连轧生产技术在中国的推广与应用做了大量努力,并该技术的工艺特性及其产品特性做了大量论述介绍。
郑州大学杨永昌[3]、关绍康等人也对Hazelett连铸连轧生产工艺进行了大量研究。
2017年,中国工程院毛新平毛新平院士率队到洛阳龙鼎实地考察了这条生产线。
2018年,由郑州大学和洛阳龙鼎合作研究的《高通量连铸连轧铝合金板材关键技术与应用》项目获得了中国有色金属工业科学技术奖一等奖。
但是,由于该技术引入中国铝加工行业时间较短且只有两条生产线,目前市场上对该产品的工艺特性及应用情况仍然存在较多疑虑。
本文将结合笔者近10年来对Hazelett连铸连轧生产线的管理与产品应用研究经验,对该产品的特性与应用进行论述。
1 国内Hazelett生产线运行情况目前国内应用于铝带加工的Hazelett连铸连轧生产线共2条,分别位于河南省伊川县和内蒙古霍林郭勒市。
现有2条生产线,设备宽度均为2100mm,综合设计产能40万吨。
2018年,两条生产线实现总产量25万吨,预计到2019年,可实现总产量35万吨。
在产品结构方面,洛阳龙鼎主要以生产各种单零箔、电缆带、装饰板带、深冲料、汽车散热器料等产品坯料为主,近三年来,年产量稳定在16-18万吨之间,产品质量在同行业中,享有较好的口碑。
各类连铸连轧生产线比较
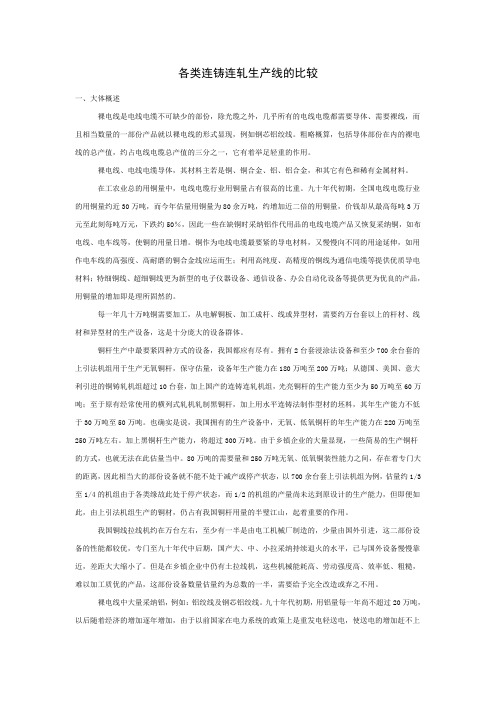
各类连铸连轧生产线的比较一、大体概述裸电线是电线电缆不可缺少的部份,除光缆之外,几乎所有的电线电缆都需要导体、需要裸线,而且相当数量的一部份产品就以裸电线的形式显现,例如钢芯铝绞线。
粗略概算,包括导体部份在内的裸电线的总产值,约占电线电缆总产值的三分之一,它有着举足轻重的作用。
裸电线、电线电缆导体,其材料主若是铜、铜合金、铝、铝合金,和其它有色和稀有金属材料。
在工农业总的用铜量中,电线电缆行业用铜量占有很高的比重。
九十年代初期,全国电线电缆行业的用铜量约近30万吨,而今年估量用铜量为80余万吨,约增加近二倍的用铜量,价钱却从最高每吨3万元至此刻每吨万元,下跌约50%,因此一些在缺铜时采纳铝作代用品的电线电缆产品又恢复采纳铜,如布电线、电车线等,使铜的用量日增。
铜作为电线电缆最要紧的导电材料,又慢慢向不同的用途延伸,如用作电车线的高强度、高耐磨的铜合金线应运而生;利用高纯度、高精度的铜线为通信电缆等提供优质导电材料;特细铜线、超细铜线更为新型的电子仪器设备、通信设备、办公自动化设备等提供更为优良的产品,用铜量的增加即是理所固然的。
每一年几十万吨铜需要加工,从电解铜板、加工成杆、线或异型材,需要约万台套以上的杆材、线材和异型材的生产设备,这是十分庞大的设备群体。
铜杆生产中最要紧四种方式的设备,我国都应有尽有。
拥有2台套浸涂法设备和至少700余台套的上引法机组用于生产无氧铜杆,保守估量,设备年生产能力在180万吨至200万吨;从德国、美国、意大利引进的铜铸轧机组超过10台套,加上国产的连铸连轧机组,光亮铜杆的生产能力至少为50万吨至60万吨;至于原有经常使用的横列式轧机轧制黑铜杆,加上用水平连铸法制作型材的坯料,其年生产能力不低于30万吨至50万吨。
也确实是说,我国拥有的生产设备中,无氧、低氧铜杆的年生产能力在220万吨至250万吨左右。
加上黑铜杆生产能力,将超过300万吨。
由于乡镇企业的大量显现,一些简易的生产铜杆的方式,也就无法在此估量当中。
ESP生产线与常规热连轧生产线的对比分析
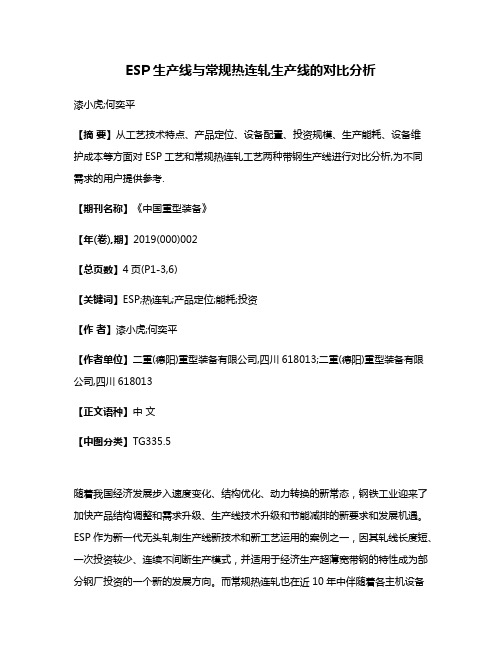
ESP生产线与常规热连轧生产线的对比分析漆小虎;何奕平【摘要】从工艺技术特点、产品定位、设备配置、投资规模、生产能耗、设备维护成本等方面对ESP工艺和常规热连轧工艺两种带钢生产线进行对比分析,为不同需求的用户提供参考.【期刊名称】《中国重型装备》【年(卷),期】2019(000)002【总页数】4页(P1-3,6)【关键词】ESP;热连轧;产品定位;能耗;投资【作者】漆小虎;何奕平【作者单位】二重(德阳)重型装备有限公司,四川618013;二重(德阳)重型装备有限公司,四川618013【正文语种】中文【中图分类】TG335.5随着我国经济发展步入速度变化、结构优化、动力转换的新常态,钢铁工业迎来了加快产品结构调整和需求升级、生产线技术升级和节能减排的新要求和发展机遇。
ESP作为新一代无头轧制生产线新技术和新工艺运用的案例之一,因其轧线长度短、一次投资较少、连续不间断生产模式,并适用于经济生产超薄宽带钢的特性成为部分钢厂投资的一个新的发展方向。
而常规热连轧也在近10年中伴随着各主机设备的功能不断完善和优化,计算机控制技术的不断提高,核心配套件制造水平的不断提升,真正实现了对热轧带钢产品从规格到品种的全覆盖,因此始终保持着稳定的投资需求。
鉴于上述两种生产工艺方式都是目前国内钢铁行业主要的投资方向,因此本文将对上述两种热连轧生产线技术进行对比分析,为不同需求的钢厂提供选择参考。
1 ESP生产线的技术发展历程ESP(Endless Strip Production)是在ISP(Inline Strip Production)工艺基础上发展而来,属于薄板坯连铸连轧工艺之一。
德马克公司早期开发的ISP使用传统的平行板型结晶器,浇出厚60 mm左右的铸坯,经液芯压下,厚度由60 mm降低至40 mm,经3机架粗轧机将40 mm厚度轧成15 mm~25 mm,铸坯经克雷莫纳炉(Cremona)卷取、开卷,送至4机架精轧机,终轧成3 mm或更薄的带卷。
论薄板坯连铸连轧与传统板带轧制的区别

论薄板坯连铸连轧与传统板带轧制的区别1 铸坯质量薄板坯连铸连轧具有凝固组织致密、中心疏松小、中心偏析轻微、柱状晶细小及二次枝晶臂间距小、头尾温差晓等特点,所以从理论上分析,薄板坯连铸连轧生产薄规格的热带具有独特的优势。
但薄板坯连铸连轧也存在铸坯表面质量不高、产品覆盖范围较小的特有的一些痼疾。
对薄板坯连铸连轧而言,表面质量是影响其产品质量档次的主要原因之一。
在生产中常见的缺陷有表面夹渣、表面纵向裂纹等。
对于薄板坯而言,由于铸坯厚度薄,宽厚比大,铸坯表面积大,需用的保护渣量大,如果保护渣选用不当,熔点高的保护渣来不及熔化,可能导致夹渣;结晶器开口度小,固态保护渣熔化的空间小,增大了液面紊流,易于把保护渣卷入钢液。
薄板坯的纵裂纹一方面与凝固坯壳表面受到的各种应力有关,如初始坯壳在结晶器内受到温差引起的热应力、钢水的静压力、静压力与凝固坯壳收缩应力产生的动摩擦力及液面波动产生的弯曲应力,以及连铸过程的拉应力。
另一方面,薄板坯纵裂纹的形成与铸坯凝固组织有关。
在薄板坯连铸过程中,通常在铸坯皮下2~3 mm处由于凝固速度快,杂质元素来不及析出便发生凝固,而当凝固前沿推进到柱状晶区域时,出现杂质元素的富集析出,使该区域的熔点降低从而形成低塑性区,在极小的外力作用下也会成为裂纹源进而发展为皮下裂纹,皮下裂纹延伸到铸坯表面形成细小的纵裂纹缺陷。
纵裂纹开始于树枝晶,结束于柱状晶与树枝晶之间,沿树枝晶生长方向扩展。
薄板坯的氧化铁皮在板坯表面很薄并且很粘,氧化铁皮很难去除,因而用薄板坯生产热带动表面质量一直是个比较大的问题。
薄板坯连铸连轧工艺与传统工艺相比,具有不同的热历史及组织转变特征。
晶器内的冷却强度远大于传统的板坯,其二次和三次枝晶更短,薄板坯原始的铸态组织晶粒比传统板坯更细、更均匀。
在传统厚板坯的情况下,铸坯的最大晶粒尺寸约2000-3000微米。
为在薄板坯的情况下,铸坯的最大晶粒尺寸约为1000微米。
同时由于冷却强度大,薄板坯的微观偏析也可得到较大的改善,分布也更均匀。
- 1、下载文档前请自行甄别文档内容的完整性,平台不提供额外的编辑、内容补充、找答案等附加服务。
- 2、"仅部分预览"的文档,不可在线预览部分如存在完整性等问题,可反馈申请退款(可完整预览的文档不适用该条件!)。
- 3、如文档侵犯您的权益,请联系客服反馈,我们会尽快为您处理(人工客服工作时间:9:00-18:30)。
各种连铸连轧生产线的比较一、基本概述裸电线是电线电缆不可缺少的部分,除了光缆以外,几乎所有的电线电缆都需要导体、需要裸线,而且相当数量的一部分产品就以裸电线的形式出现,例如钢芯铝绞线。
粗略概算,包括导体部分在内的裸电线的总产值,约占电线电缆总产值的三分之一,它有着举足轻重的作用。
裸电线、电线电缆导体,其材料主要是铜、铜合金、铝、铝合金,以及其它有色和稀有金属材料。
在工农业总的用铜量中,电线电缆行业用铜量占有很高的比重。
九十年代初期,全国电线电缆行业的用铜量约近30万吨,而今年估计用铜量为80余万吨,约增加近二倍的用铜量,价格却从最高每吨3万元至现在每吨1.5万元,下跌约50%,因此一些在缺铜时采用铝作代用品的电线电缆产品又恢复采用铜,如布电线、电车线等,使铜的用量日增。
铜作为电线电缆最主要的导电材料,又逐步向不同的用途延伸,如用作电车线的高强度、高耐磨的铜合金线应运而生;使用高纯度、高精度的铜线为通信电缆等提供优质导电材料;特细铜线、超细铜线更为新型的电子仪器设备、通信设备、办公自动化设备等提供更为优良的产品,用铜量的增加便是理所当然的。
每年几十万吨铜需要加工,从电解铜板、加工成杆、线或异型材,需要约万台套以上的杆材、线材和异型材的生产设备,这是十分庞大的设备群体。
铜杆生产中最主要四种方法的设备,我国都应有尽有。
拥有2台套浸涂法设备和至少700余台套的上引法机组用于生产无氧铜杆,保守估计,设备年生产能力在180万吨至200万吨;从德国、美国、意大利引进的铜铸轧机组超过10台套,加上国产的连铸连轧机组,光亮铜杆的生产能力至少为50万吨至60万吨;至于原有常用的横列式轧机轧制黑铜杆,加上用水平连铸法制作型材的坯料,其年生产能力不低于30万吨至50万吨。
也就是说,我国拥有的生产设备中,无氧、低氧铜杆的年生产能力在220万吨至250万吨左右。
加上黑铜杆生产能力,将超过300万吨。
由于乡镇企业的大量出现,一些简易的生产铜杆的方法,也就无法在此估计之中。
80万吨的需要量和250万吨无氧、低氧铜装机能力之间,存在着很大的距离,因此相当大的部分设备就不得不处于减产或停产状态,以700余台套上引法机组为例,估计约1/3至1/4的机组由于各种原因而处于停产状态,而1/2的机组的产量尚未达到原设计的生产能力,但即使如此,由上引法机组生产的铜材,仍占有我国铜杆用量的半璧江山,起着重要的作用。
我国铜线拉线机约在万台左右,至少有一半是由电工机械厂制造的,少量由国外引进,这二部分设备的性能都较优,特别至九十年代中后期,国产大、中、小拉采用连续退火的水平,已与国外设备逐步靠近,差距大大缩小了。
然而在乡镇企业中仍有土拉线机,这些机器能耗高、劳动强度高、效率低、粗糙,难以加工质优的产品,这部分设备数量估计约为总数的一半,需要给予彻底改造或弃之不用。
裸电线中大量采用铝,例如:铝绞线及钢芯铝绞线。
九十年代初期,用铝量每年尚不超过20万吨,以后随着经济的增长逐年增加,由于以前国家在电力系统的政策上是重发电轻送电,使送电的增长赶不上发电的增长速度。
近年来开始的城市电网和农村电网改造,使送电的增长速度急剧加快,兼之九十年代开始建设的大型电站,像二滩电站、黄河小浪底电站和长江三峡电站,将相继逐步建成,送电便成为电站建设以后的重中之重,送电工程建设步入本世纪以来最辉煌、最灿烂的黄金时代。
作为送电线路建设的最重要器材,铝绞线及钢芯铝绞线、铝包钢芯铝绞线的产量剧增。
能提供500kV重要工程用的主要生产厂家,产量处于爆满程度,创下了历史最高纪录,预计今年输电线的产量为50万吨以上,可能达到60万吨。
此外,我国钢芯铝绞线在电线电缆产品的出口中占有重要地位,因此在计入产量时,出口量是不能忽略的。
全国拥有80台套以上的铝连铸连轧机,除少量机组由国外引进外,主要由国内生产。
近二年,每年可望新增约10台套。
80台套机组将拥有生产80万吨以上铝杆的能力,能制成120万吨钢芯铝绞线;此外,利用原有半连续浇铸机生产方锭,用横列式轧机轧铝杆的生产方式和水平引铸铝杆方法,粗略估计,这二种方法尚可生产20万吨至30万吨的钢芯铝绞线。
全国铝杆的生产能力远大于实际所需的数量,在主要生产厂任务十分饱满的情况下,其它有些工厂的连铸连轧机年产才只有1千至2千吨,尚未发挥应有效益,给企业带来不少麻烦。
我国至少拥有400台至500台铝线拉线机,绝大多数为国产的集线式拉线机,从五十年代开始使用以来,几乎没有什么本质上的改进,与国外现代拉制铝线的高速拉线机相比,差距是明显的。
国内拥有为数不多的由国外引进的铝线高速大拉机,在生产中均发挥主力作用。
国产的铝线高速大拉机,正在积极发展之中。
在乡镇企业的小工厂中,低效的单模拉线机仍有一定数量,应予及早更换、改造或淘汰。
铝绞线及钢芯铝绞线的生产,由于工序较少,所以在价格组成中,主要是材料和动力。
在供大于求的情况下,工厂之间竞相压价,使产品的利润很低,有时甚至达到无利可图的地步,这必须引起全行业的关注。
在重视送电的今天,单单依靠增加产量并不能增加工厂多大的效益,主要还是提高产品的技术含量,生产优质产品。
九十年代中期,我国从英国引进的铝包钢生产线,制造优质的铝包钢线,结合500kV送电线路的建设,铝包钢芯铝绞线已作为重要的线种正在被越来越广泛的应用,现在四家生产优质铝包钢线的工厂,正成为提供高质量输电线的厂家,有着较好的经济效益和社会效益。
高强度铝合金导线以其优良的特性,在国外已获得十分广泛的应用,然我国用量尚少。
从技术经济比较结果证明,从线路建设、线路运行都有着良好的效果,因此可以预料,在五年后,我国高强度铝合金导线的年需要量,可能达到3万至4万吨,目前我国只有3家能生产高强度铝合金导线的工厂,生产能力约1万吨,那么未来的数年间可能会出现数家生产高强度铝合金导线的工厂,这是一个值得注意的新的经济增长点。
天使有残缺2007-7-23 18:15:50二、技术进步1. 铜⑴铜杆制造技术当前最主要的有四种,分别生产不同材质的铜杆。
生产含氧量在20ppm以下的无氧铜杆,采用浸涂成型法和上引冷轧法;采用连铸连轧法制造的铜杆为光亮铜杆;采用铸锭、回线式(或称横列式)轧制的铜杆为黑铜杆。
这四种方法生产铜杆,我国应有尽有。
六十年代末,美国通用电气公司开发浸涂成型法(Dip-forming)新工艺制造铜杆。
浸涂成型是利用冷铜杆吸热的能力,用一根较细的冷纯铜芯杆(或称种子杆),垂直通过一只能保持一定液位高低的铜水池,使铜水与该移动的种子杆表面铜熔合在一起,并逐步凝固结合成较粗的铸造状态铜杆,然后经冷却、热轧、冷却、绕制成圈,整个过程是在封闭的、有惰性气体保护下进行的。
哈尔滨电缆厂引进了浸涂法设备后,生产出质量优良的含氧量在20ppm以下的铜杆,在八十、九十年代中为该厂获得良好声誉与经济效益。
七十年代初,芬兰的Outokumpu公司成功的采用上引冷轧法制造无氧铜杆。
它是利用一种管式铜套(即石墨结晶器)其下端伸入并浸没在熔化的铜液面下,上端与真空泵连通,开始时将结晶器内空气抽出,在真空作用下,使管内产生负压,铜液徐徐吸引向上,并在引升器附近很快凝固成光亮铸锭。
然后经冷轧或冷拉成杆。
上引法生产的铜杆含氧量在10ppm以下,表面光亮。
自八十年代初,我国由芬兰引进上引法生产铜杆的机组以后,以上海电缆研究所为主对上引组仿制并国产化,获得很大成功。
目前上引法铜产量占有我国用铜杆数量的一半。
上海电缆研究所生产的上引法机组,产量世界第一,且由于质优价廉而畅销国内外。
这是九十年代铜杆生产的很大成功。
国际上铜的连铸连轧生产线主要有:意大利的Properzi系统(缩称CCR 系统)、美国的South Wire系统(缩称SCR系统),德国的Krupp/Hazelett系统(缩称Contirod系统)、以及法国的SECIM系统。
这些系统在原理上基本相同,其差别主要在铸机和轧机的形式和结构上。
CCR系统采用双轮铸机和Y型轧机,对大截面锭子,在原轧机前加两平一立辊机架,箱式孔型。
SCR系统采用一大四小的五轮铸机,平立辊连轧机,箱-椭-圆系统。
Contirod系统与SCR 基本相同,但铸机改为“无轮双钢带式”,即Hazelett式。
SECIM系统采用一大三小的四轮式连铸机,箱-扁-圆、扁-扁-圆系统。
我国拥有CCR、SCR和Contirod的铜连铸连轧机十余台,其中产量高的年产10万吨铜杆,而且这些连铸连轧机生产出来的铜杆质量都十分好,特别像Contirod系统生产的铜杆,深受用户喜爱,而且有很大的出口份额。
我国还自己设计制造铜连铸连轧机,但采用者较少。
常规的、传统的铜杆生产法,是把铜液铸成船形锭后再加热,经横列式(或称回线式)轧机轧制而成黑铜杆。
这种铜杆表面发黑有一层氧化皮,长度又受到铜船形锭重量的限制,含氧量超过200ppm至500ppm,因此影响以下工序加工的性能,特别拉细线时更受影响。
拉线时断线事故更易发生。
现对上述四种方法生产的铜杆作一个比较:浸涂成型法:能生产大长度光亮无氧铜杆、导电率为101~102%IACS,含氧量20ppm以下,铜杆圈重3.5~10吨。
上引冷轧法:能生产大长度光亮无氧铜杆、导电率为101~101.6%IACS,含氧量10ppm以下,铜杆圈重2吨。
连铸连轧法:能生产大长度光亮低氧铜杆、导电率为101~102%IACS,含氧量200~300ppm,铜杆圈重达5吨。
回线轧制法:生产短长度有氧化皮的黑铜杆,导电率为99.5~100.5%IACS,含氧量200~500 ppm,铜杆圈重只有86~136公斤。
(因受船形铜锭重量的限制)在欧洲曾对上述四种方法的下道工序和拉线结果进行调查。
我国在九十年代中期为发展耐冷冻漆包线,对漆包线用铜材材质和加工工艺立题研究,经过大量的对比试验得出了几乎与欧洲试验相同的结论:用浸涂法生产的铜线断线的次数很少;用连铸连轧法生产的铜杆,由于含氧量适中,因此它的缺点很少,其中用Contirod法生产的铜杆,比SCR法或CCR法生产的铜杆更软,延伸率好,表面质量很好;用回线轧制法生产的铜杆,在拉制小直径的铜线时断头率高。
上引。