无氧铜杆连铸连轧生产线
无氧铜生产工艺流程.
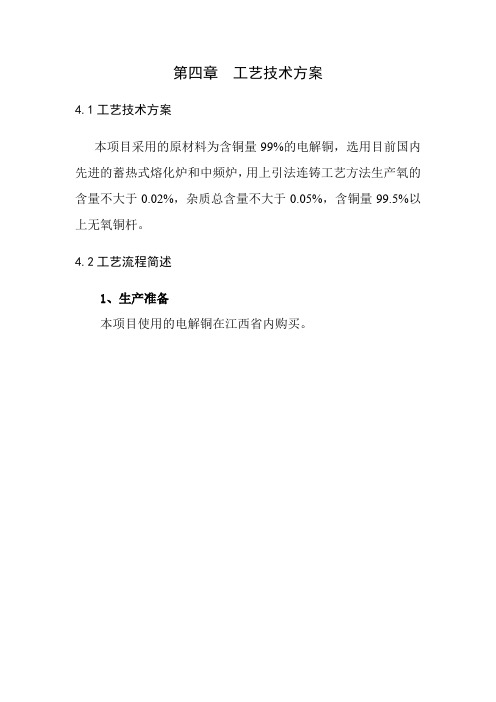
第四章工艺技术方案4.1工艺技术方案本项目采用的原材料为含铜量99%的电解铜,选用目前国内先进的蓄热式熔化炉和中频炉,用上引法连铸工艺方法生产氧的含量不大于0.02%,杂质总含量不大于0.05%,含铜量99.5%以上无氧铜杆。
4.2工艺流程简述1、生产准备本项目使用的电解铜在江西省内购买。
图4-1 项目生产工艺流程图2、上引法连铸工艺流程本项目采用上引法连铸工艺生产无氧铜杆。
上引法连铸铜杆的基本特点是“无氧”,即氧含量在10ppm以下。
上引法与连铸连轧和浸涂法相比,其特点是:1)由于拉扎工艺和铸造工艺不是连续的,拉扎是在常温下进行的,不需要气体保护,钢材也不会被氧化。
因此设备投资小,厂房布置也灵活。
2)单机产量变化范围大,年产量可以从几百吨到几万吨,可供不同规模的厂家选用不同型号的上引机组。
此外,由于连铸机是多头的,可以很容易的通过改变铸造规格(铸杆直径),来改变单位时间的产量,因此其产量可视原材料的供应情况和产品的需求情况来确定,便于组织生产、节约能源。
3)只需更换结晶器和改变石墨模的形状,即可生产铜管、铜排等异型铜材,并可在同一机器上上产不同规格、品种的铜材,灵活机动,这是上引法的中最大特点。
上引法连铸工艺流程:原料通过加料机加入融化炉进行熔化、氧化、扒渣处理后,熔融的铜液经过一段时间的静置还原脱氧并达到一定的温度后,通过有CO气体保护的流槽经过渡腔(铜液在此进一步还原脱氧、清除渣质),进而平稳的流入中频炉保温静置,铜液的温度由热电偶测量,温度值由仪表显示,温度控制在1150℃±10℃。
连铸机固定于中频保温炉的上方,连铸机铜液在结晶器中快速结晶连续不断地生产出铜杆,最后经双头挠杆机等辅助设备装盘成产品。
⑴加料:原料一般用加料机加入,炉头多加、炉尾少加。
加冷料时要使铜料距炉顶及烟道口有一定距离,以保证燃料燃烧和炉气流动的顺畅。
加料时要保证炉膛有足够高的温度,一般应达到1300℃以上,炉内应保证零压或微负压。
铜杆连铸连轧生产线年度检查内容

铜杆连铸连轧生产线年度检查内容一、设备检查1. 检查铜杆连铸连轧设备的机械部分,包括轧机、连铸机、冷却设备等,确保设备运行平稳、无杂音、无明显振动。
2. 检查设备的电气部分,包括电机、电控柜、传感器等,确保电气系统正常工作,无短路、漏电等现象。
3. 检查设备的润滑系统,确保润滑油的供给充足,润滑部位无异常磨损。
二、工艺参数检查1. 检查连铸机的结晶器温度、拉速、结晶器水流量等参数,确保连铸过程中铜杆的凝固和形状控制良好。
2. 检查轧机的轧辊压力、轧制速度、轧制温度等参数,确保轧制过程中铜杆的尺寸和表面质量符合要求。
3. 检查冷却设备的冷却水温度、流量等参数,确保冷却过程中铜杆能够快速降温,避免内部应力过大。
三、质量检查1. 检查铜杆的外观质量,包括表面光洁度、无裂纹、无气孔等,确保产品外观符合要求。
2. 进行尺寸检查,测量铜杆的直径、长度、直线度等,确保产品尺寸精确度符合要求。
3. 进行化学成分分析,检测铜杆的成分含量,确保产品化学成分符合标准要求。
四、安全检查1. 检查设备的安全保护装置是否完好有效,包括防护罩、急停按钮、安全门等,确保操作人员的安全。
2. 检查生产线周围的消防设施是否齐全,包括灭火器、喷淋系统等,确保能够及时有效地应对火灾风险。
3. 检查操作人员的个人防护用品是否齐全,包括安全帽、防护眼镜、防护手套等,确保操作人员的身体安全。
五、环境检查1. 检查生产线周围的环境卫生状况,包括道路清洁、车间清洁等,确保工作环境整洁、无异味。
2. 检查废水处理设施的运行情况,确保废水排放符合环保要求。
3. 检查废气处理设施的运行情况,确保废气排放符合环保要求。
通过对铜杆连铸连轧生产线的年度检查,可以确保设备正常运行,工艺参数控制良好,产品质量符合要求,操作人员安全,生产环境卫生和环保要求得到满足。
这对于保证铜杆连铸连轧生产线的持续稳定运行、提高产品质量和效率具有重要意义。
无氧铜杆连铸连轧生产线
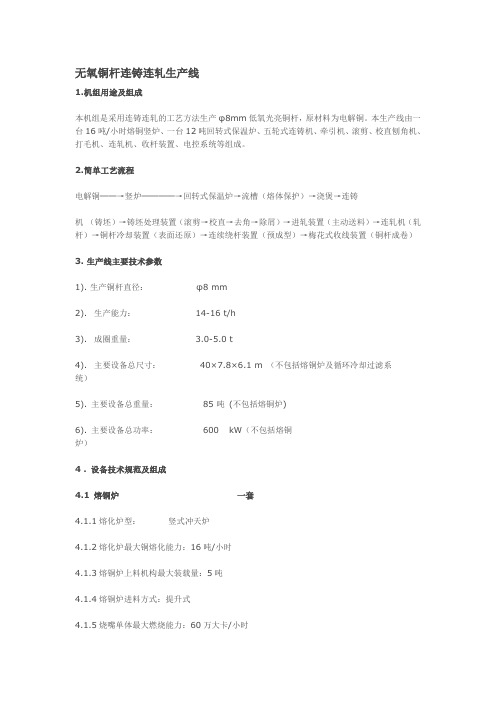
无氧铜杆连铸连轧生产线1.机组用途及组成本机组是采用连铸连轧的工艺方法生产φ8mm低氧光亮铜杆,原材料为电解铜。
本生产线由一台16吨/小时熔铜竖炉、一台12吨回转式保温炉、五轮式连铸机、牵引机、滚剪、校直刨角机、打毛机、连轧机、收杆装置、电控系统等组成。
2.简单工艺流程电解铜──→竖炉────→回转式保温炉→流槽(熔体保护)→浇煲→连铸机(铸坯)→铸坯处理装置(滚剪→校直→去角→除屑)→进轧装置(主动送料)→连轧机(轧杆)→铜杆冷却装置(表面还原)→连续绕杆装置(预成型)→梅花式收线装置(铜杆成卷)3. 生产线主要技术参数1). 生产铜杆直径:φ8 mm2). 生产能力:14-16 t/h3). 成圈重量: 3.0-5.0 t4). 主要设备总尺寸: 40×7.8×6.1 m (不包括熔铜炉及循环冷却过滤系统)5). 主要设备总重量: 85 吨(不包括熔铜炉)6). 主要设备总功率: 600 kW(不包括熔铜炉)4 .设备技术规范及组成4.1熔铜炉一套4.1.1熔化炉型:竖式冲天炉4.1.2熔化炉最大铜熔化能力:16吨/小时4.1.3熔铜炉上料机构最大装载量:5吨4.1.4熔铜炉进料方式:提升式4.1.5烧嘴单体最大燃烧能力:60万大卡/小时4.1.6熔铜炉烧嘴数量:15只4.1.7烧嘴冷却方式:水冷4.1.8烧嘴点火方式:自动4.1.9使用燃料:天然气、液化气、城市煤气4.1.10保温炉炉型:液压回转式4.1.11保温炉有效容量:12吨4.1.12保温炉最高倾力角度:>70º4.1.13烧嘴单体最大燃烧能力:60万大卡/小时4.1.14保温炉烧嘴数量:1只4.1.15燃烧控制方式:比例燃烧,具有保护装置4.1.16燃气阀检漏方式:手动/自动熔铜炉包括冲天式铜熔化炉、回转式保温炉、上下流槽、燃烧控制系统等四大部分。
具有熔化速度快、铜水含氧量低、流量连续可调、铜水温度独立可控、单位铜水燃气消耗量低等特点。
无氧铜杆的生产方法
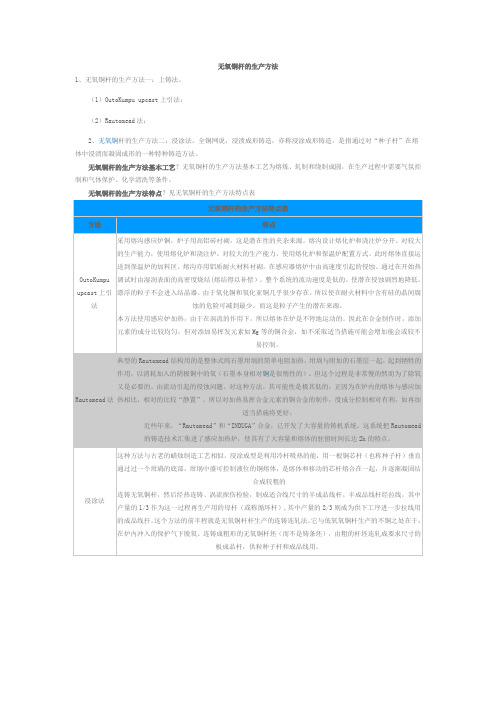
无氧铜杆的生产方法1、无氧铜杆的生产方法一:上铸法。
(1)OutoKumpu upcast上引法:(2)Rautomead法:2、无氧铜杆的生产方法二:浸涂法。
全铜网说,浸渍成形铸造,亦称浸涂成形铸造,是指通过对“种子杆”在熔体中浸渍而凝固成形的一种特种铸造方法。
无氧铜杆的生产方法基本工艺?无氧铜杆的生产方法基本工艺为熔炼、轧制和绕制成圆,在生产过程中需要气氛控制和气体保护、化学清洗等条件。
无氧铜杆的生产方法特点?见无氧铜杆的生产方法特点表Rautomead铸机截面图无氧铜杆的生产方法优势?性能优良,工艺先进,生产效率高并节约能源,不需酸洗。
此外,能减少加工工序,而且铜的损耗率低。
无氧铜杆的生产方法之冶金化学反应?1、阴极铜予处理阶段,阴极铜加入熔化炉前,如在预热炉热(700*c左右)。
此时铜板表面存在的胆矾和碱碳酸铜及水分发生离解和蒸发,其反应式如下CuSO4·5H2O→CuO+SO2↑+H2O↑CuCO3·Cu(OH)2250~270℃→CuCO3+CuO+H2O↑CuCO3560~600℃→CuO+CO2↑H2O(液)→H2O(汽)↑2、阴极铜加入炉内熔化,对浸涂法,铜板加入工频感应熔化炉内,熔体在电磁感应作用下不断运动,铜液中杂质元素间及碳层和保护氨气中的氢元素之间(一般木炭覆盖层厚100~150mm;炉内充入含有2%氢的氮气会发生一系列化学反应,如下4CuO1025℃→2Cu2O+O2↑4Cu+O2≡2Cu2OCu2O+Me←→MeO(造渣)+2Cu(Me—金属杂质)2Cu2O+Cu2S≡6Cu+SO2↑Cu2O+H2≡2Cu+HO2↑Cu2S+H2←→2Cu+H2S↑2Cu2O+C≡4Cu+CO2↑SO2+C≡S+CO2↑2Me+C≡2Me+CO2↑无氧铜杆无氧铜杆的生产方法之生产线参数?下面说的是浸涂法的生产线参数。
1、表格化:现场工艺控制。
现代化生产线的有效管理方法之一,是采取表格化的形式,实行现场工艺控制。
各种连铸连轧生产线的比较

各种连铸连轧生产线的比较一、基本概述裸电线是电线电缆不可缺少的部分,除了光缆以外,几乎所有的电线电缆都需要导体、需要裸线,而且相当数量的一部分产品就以裸电线的形式出现,例如钢芯铝绞线。
粗略概算,包括导体部分在内的裸电线的总产值,约占电线电缆总产值的三分之一,它有着举足轻重的作用。
裸电线、电线电缆导体,其材料主要是铜、铜合金、铝、铝合金,以及其它有色和稀有金属材料。
在工农业总的用铜量中,电线电缆行业用铜量占有很高的比重。
九十年代初期,全国电线电缆行业的用铜量约近30万吨,而今年估计用铜量为80余万吨,约增加近二倍的用铜量,价格却从最高每吨3万元至现在每吨1.5万元,下跌约50%,因此一些在缺铜时采用铝作代用品的电线电缆产品又恢复采用铜,如布电线、电车线等,使铜的用量日增。
铜作为电线电缆最主要的导电材料,又逐步向不同的用途延伸,如用作电车线的高强度、高耐磨的铜合金线应运而生;使用高纯度、高精度的铜线为通信电缆等提供优质导电材料;特细铜线、超细铜线更为新型的电子仪器设备、通信设备、办公自动化设备等提供更为优良的产品,用铜量的增加便是理所当然的。
每年几十万吨铜需要加工,从电解铜板、加工成杆、线或异型材,需要约万台套以上的杆材、线材和异型材的生产设备,这是十分庞大的设备群体。
铜杆生产中最主要四种方法的设备,我国都应有尽有。
拥有2台套浸涂法设备和至少700余台套的上引法机组用于生产无氧铜杆,保守估计,设备年生产能力在180万吨至200万吨;从德国、美国、意大利引进的铜铸轧机组超过10台套,加上国产的连铸连轧机组,光亮铜杆的生产能力至少为50万吨至60万吨;至于原有常用的横列式轧机轧制黑铜杆,加上用水平连铸法制作型材的坯料,其年生产能力不低于30万吨至50万吨。
也就是说,我国拥有的生产设备中,无氧、低氧铜杆的年生产能力在220万吨至250万吨左右。
加上黑铜杆生产能力,将超过300万吨。
由于乡镇企业的大量出现,一些简易的生产铜杆的方法,也就无法在此估计之中。
无氧铜生产工艺流程

第四章工艺技术方案4.1工艺技术方案本项目采用的原材料为含铜量99%的电解铜,选用目前国内先进的蓄热式熔化炉和中频炉,用上引法连铸工艺方法生产氧的含量不大于0。
02%,杂质总含量不大于0。
05%,含铜量99。
5%以上无氧铜杆。
4.2工艺流程简述1、生产准备本项目使用的电解铜在江西省内购买。
图4—1项目生产工艺流程图2、上引法连铸工艺流程本项目采用上引法连铸工艺生产无氧铜杆。
上引法连铸铜杆的基本特点是“无氧”,即氧含量在10ppm以下。
上引法与连铸连轧和浸涂法相比,其特点是:1)由于拉扎工艺和铸造工艺不是连续的,拉扎是在常温下进行的,不需要气体保护,钢材也不会被氧化.因此设备投资小,厂房布置也灵活。
2)单机产量变化范围大,年产量可以从几百吨到几万吨,可供不同规模的厂家选用不同型号的上引机组.此外,由于连铸机是多头的,可以很容易的通过改变铸造规格(铸杆直径),来改变单位时间的产量,因此其产量可视原材料的供应情况和产品的需求情况来确定,便于组织生产、节约能源。
3)只需更换结晶器和改变石墨模的形状,即可生产铜管、铜排等异型铜材,并可在同一机器上上产不同规格、品种的铜材,灵活机动,这是上引法的中最大特点。
上引法连铸工艺流程:原料通过加料机加入融化炉进行熔化、氧化、扒渣处理后,熔融的铜液经过一段时间的静置还原脱氧并达到一定的温度后,通过有CO气体保护的流槽经过渡腔(铜液在此进一步还原脱氧、清除渣质),进而平稳的流入中频炉保温静置,铜液的温度由热电偶测量,温度值由仪表显示,温度控制在1150℃±10℃.连铸机固定于中频保温炉的上方,连铸机铜液在结晶器中快速结晶连续不断地生产出铜杆,最后经双头挠杆机等辅助设备装盘成产品。
⑴加料:原料一般用加料机加入,炉头多加、炉尾少加。
加冷料时要使铜料距炉顶及烟道口有一定距离,以保证燃料燃烧和炉气流动的顺畅.加料时要保证炉膛有足够高的温度,一般应达到1300℃以上,炉内应保证零压或微负压。
无氧铜杆生产工艺流程
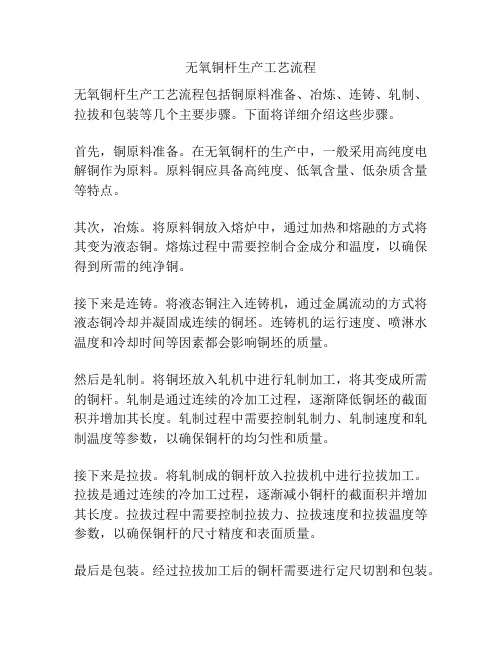
无氧铜杆生产工艺流程
无氧铜杆生产工艺流程包括铜原料准备、冶炼、连铸、轧制、拉拔和包装等几个主要步骤。
下面将详细介绍这些步骤。
首先,铜原料准备。
在无氧铜杆的生产中,一般采用高纯度电解铜作为原料。
原料铜应具备高纯度、低氧含量、低杂质含量等特点。
其次,冶炼。
将原料铜放入熔炉中,通过加热和熔融的方式将其变为液态铜。
熔炼过程中需要控制合金成分和温度,以确保得到所需的纯净铜。
接下来是连铸。
将液态铜注入连铸机,通过金属流动的方式将液态铜冷却并凝固成连续的铜坯。
连铸机的运行速度、喷淋水温度和冷却时间等因素都会影响铜坯的质量。
然后是轧制。
将铜坯放入轧机中进行轧制加工,将其变成所需的铜杆。
轧制是通过连续的冷加工过程,逐渐降低铜坯的截面积并增加其长度。
轧制过程中需要控制轧制力、轧制速度和轧制温度等参数,以确保铜杆的均匀性和质量。
接下来是拉拔。
将轧制成的铜杆放入拉拔机中进行拉拔加工。
拉拔是通过连续的冷加工过程,逐渐减小铜杆的截面积并增加其长度。
拉拔过程中需要控制拉拔力、拉拔速度和拉拔温度等参数,以确保铜杆的尺寸精度和表面质量。
最后是包装。
经过拉拔加工后的铜杆需要进行定尺切割和包装。
根据需求将铜杆切割成所需的长度,并进行包装,以便运输和储存。
以上就是无氧铜杆的生产工艺流程的简要介绍。
当然,实际的生产流程可能会因为设备和工艺的不同而有所差异,但总体上都是基于原料准备、冶炼、连铸、轧制、拉拔和包装这几个主要步骤完成的。
无氧铜杆生产工艺
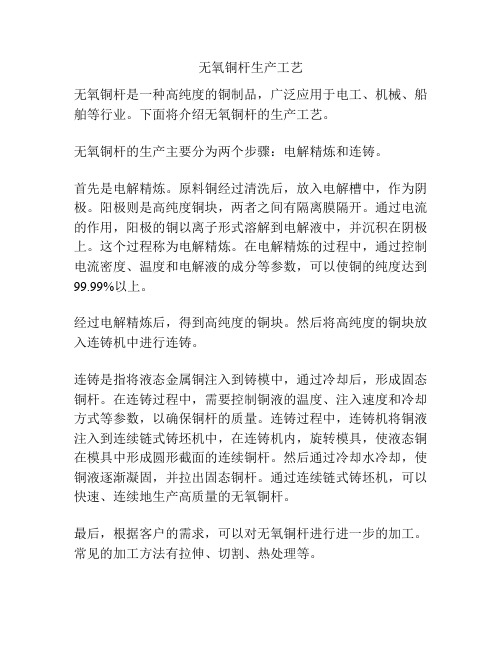
无氧铜杆生产工艺
无氧铜杆是一种高纯度的铜制品,广泛应用于电工、机械、船舶等行业。
下面将介绍无氧铜杆的生产工艺。
无氧铜杆的生产主要分为两个步骤:电解精炼和连铸。
首先是电解精炼。
原料铜经过清洗后,放入电解槽中,作为阴极。
阳极则是高纯度铜块,两者之间有隔离膜隔开。
通过电流的作用,阳极的铜以离子形式溶解到电解液中,并沉积在阴极上。
这个过程称为电解精炼。
在电解精炼的过程中,通过控制电流密度、温度和电解液的成分等参数,可以使铜的纯度达到99.99%以上。
经过电解精炼后,得到高纯度的铜块。
然后将高纯度的铜块放入连铸机中进行连铸。
连铸是指将液态金属铜注入到铸模中,通过冷却后,形成固态铜杆。
在连铸过程中,需要控制铜液的温度、注入速度和冷却方式等参数,以确保铜杆的质量。
连铸过程中,连铸机将铜液注入到连续链式铸坯机中,在连铸机内,旋转模具,使液态铜在模具中形成圆形截面的连续铜杆。
然后通过冷却水冷却,使铜液逐渐凝固,并拉出固态铜杆。
通过连续链式铸坯机,可以快速、连续地生产高质量的无氧铜杆。
最后,根据客户的需求,可以对无氧铜杆进行进一步的加工。
常见的加工方法有拉伸、切割、热处理等。
以上就是无氧铜杆的生产工艺。
通过电解精炼和连铸,可以生产出高纯度的无氧铜杆,广泛应用于各个行业。
同时,在生产过程中,需要严格控制各个参数,以确保产品的质量。
- 1、下载文档前请自行甄别文档内容的完整性,平台不提供额外的编辑、内容补充、找答案等附加服务。
- 2、"仅部分预览"的文档,不可在线预览部分如存在完整性等问题,可反馈申请退款(可完整预览的文档不适用该条件!)。
- 3、如文档侵犯您的权益,请联系客服反馈,我们会尽快为您处理(人工客服工作时间:9:00-18:30)。
无氧铜杆连铸连轧生产线1.机组用途及组成本机组是采用连铸连轧的工艺方法生产φ8mm低氧光亮铜杆,原材料为电解铜。
本生产线由一台16吨/小时熔铜竖炉、一台12吨回转式保温炉、五轮式连铸机、牵引机、滚剪、校直刨角机、打毛机、连轧机、收杆装置、电控系统等组成。
2.简单工艺流程电解铜──→竖炉────→回转式保温炉→流槽(熔体保护)→浇煲→连铸机(铸坯)→铸坯处理装置(滚剪→校直→去角→除屑)→进轧装置(主动送料)→连轧机(轧杆)→铜杆冷却装置(表面还原)→连续绕杆装置(预成型)→梅花式收线装置(铜杆成卷)3. 生产线主要技术参数1). 生产铜杆直径:φ8 mm2). 生产能力:14-16 t/h3). 成圈重量: 3.0-5.0 t4). 主要设备总尺寸: 40×7.8×6.1 m (不包括熔铜炉及循环冷却过滤系统)5). 主要设备总重量: 85 吨(不包括熔铜炉)6). 主要设备总功率: 600 kW(不包括熔铜炉)4 .设备技术规范及组成4.1熔铜炉一套4.1.1熔化炉型:竖式冲天炉4.1.2熔化炉最大铜熔化能力:16吨/小时4.1.3熔铜炉上料机构最大装载量:5吨4.1.4熔铜炉进料方式:提升式4.1.5烧嘴单体最大燃烧能力:60万大卡/小时4.1.6熔铜炉烧嘴数量:15只4.1.7烧嘴冷却方式:水冷4.1.8烧嘴点火方式:自动4.1.9使用燃料:天然气、液化气、城市煤气4.1.10保温炉炉型:液压回转式4.1.11保温炉有效容量:12吨4.1.12保温炉最高倾力角度:>70º4.1.13烧嘴单体最大燃烧能力:60万大卡/小时4.1.14保温炉烧嘴数量:1只4.1.15燃烧控制方式:比例燃烧,具有保护装置4.1.16燃气阀检漏方式:手动/自动熔铜炉包括冲天式铜熔化炉、回转式保温炉、上下流槽、燃烧控制系统等四大部分。
具有熔化速度快、铜水含氧量低、流量连续可调、铜水温度独立可控、单位铜水燃气消耗量低等特点。
①冲天式铜熔化炉(竖炉)熔化炉简称竖炉,由炉底、炉身、碰撞保护块、加料口、上料机构、烟囱、炉衬和冷却风机等部分组成。
炉底、炉身由优质钢板和型钢制作,炉底采用25mm钢板,中间用槽钢加固,使整个炉底可以承受100吨电解铜板的重量而不变形;炉身用16mm钢板圈成桶体,炉体内贴一层硅酸铝纤维毯,可大大降低炉壁温度,中间砌筑高铝耐火砖,最内层炉衬是直接触火焰和铜水的,采用SiC砖砌筑,荷重软化温度可达1700度,保证了炉衬的使用寿命。
SiC砖采用纯度大于80%的SiC混合特殊的高温粘接剂,经压机预先压制成弧形砖,通过高温焙烧,使SiC砖形成半烧结状态,一方面增加了SiC砖的强度,便于运输、搬运、砌筑,同时在砌筑完成后,通过第二次烘烧,使竖炉内衬形成一个坚固的整体,使整个炉衬的强度大为提高。
炉体上部是防撞保护块,防止在加料时铜板撞在炉衬上,引起炉衬脱落破损甚至内衬倒塌。
防撞保护块由耐热钢整体浇注而成,整体强度高,具有耐高温、耐冲击、不易脱落等优点,使用寿命长,可有效保护加料时铜板对炉身的冲击。
加料口设计在竖炉的上方,这种加料方式可以使铜板从炉底一直堆放到炉体加料口,延长了烧嘴燃烧后产生的烟气与铜板的接触时间,使铜板可最大限度地吸收烟气余热,增加热量的利用效率,节约燃料成本。
经实际使用证明,连续状态下,每吨铜水的燃气消耗量小于70立方米(天然气)或23立方米(液化气),仅为平炉的1/2~1/3。
烟囱为钢制圆管,高于厂房屋顶3M,将燃烧产生的废气排出室外,烟囱上设有防雨帽和避雷针,避雷针用扁钢条接引入地,接地线在基础土建施工时预埋,接地电阻小于4欧姆。
铜板的加料装置为料斗式,料斗式加料装置由5吨卷扬机、提升料斗、C型上料架和导绳器、转向滑轮等组成,加料时将铜板放在料斗上,开动卷扬机提升料斗,当料斗升到加料口位置时,由于H型上料架的导向作用,料斗自动倾斜,将铜板倒入炉内。
②回转式保温炉回转式保温炉由炉体、炉衬、炉门、进料口、出料口、滚轮、限位轮和可伸缩式油缸及液压站组成。
炉体由25mm钢板卷成,炉体下部安装偏心弧形扇板,当炉体沿扇板面转动时,由于扇板的偏心,使炉内铜水液面抬高而从出料口溢出。
炉衬用轻质保温砖为保温层,中间砌筑高铝耐火砖,内衬采用SiC异型砖,SiC砖采用和竖炉相同的工艺烧制而成。
炉门设在保温炉上部,采用SiC捣打料捣打而成,炉门可上下翻动,方便停炉时人工清理或修理时进出炉内的需要。
保温炉进料口用SiC预先制作,砌筑时安装在保温炉上端头部,作为从竖炉熔化后的铜水经溜槽流入保温炉的入口。
保温炉出料口用SiC预制成管状,安装在保温炉下端头部,作为铜水从保温炉经下溜槽流入浇包的出口。
当保温炉需要向连铸机输送铜水时,液压站工作,油缸向上伸展,保温炉沿炉底扇形板转动,铜水液面提高从出铜口溢出溜槽向浇包输送。
③上下流槽流槽分成上下流槽两段。
从竖炉出口到保温炉进口的部分为上流槽。
上流槽为熔化后的铜水从竖炉流入保温炉提供通道,上流槽采用钢板制作外壳,内部用SiC浇注料直接捣打而成,上流槽为全封闭结构,减少铜水和空气的接触,降低铜水含氧量。
从保温炉出料口到连铸机浇包前的通道为下流槽。
下流槽外壳用钢板焊接而成,里衬用SiC浇注料捣打烧结成整体。
为减少空气和铜水的接触,下流槽也为全封闭结构。
④燃烧控制系统燃烧控制系统是本设备的核心部件,它直接关系到熔化后铜水的质量和设备的安全运行。
燃烧控制系统分竖炉燃烧控制系统、保温炉燃烧控制系统、流槽燃烧控制系统三部分。
竖炉燃烧系统由安装在竖炉炉墙底部和中部的15只80万大卡/小时的预混式烧嘴、燃气电磁阀组、燃气比例阀、助燃风机、空气电动调节阀和调节仪表及阀门检漏系统组成。
本设备采用的预混式烧嘴具有自动点火、火焰检测等功能,可为控制系统提供火焰状态信号,为安全燃烧提供保障。
烧嘴的燃气通过电磁阀组及比例阀提供,点火前检漏系统自动检测燃气电磁阀组的密封性能,一旦发现阀门关闭不严密而产生泄漏,系统发出报警信号,并指示故障位置。
为了减少铜水吸入氧气,我们采用空气燃气比例燃烧方式,即使进入烧嘴前的燃气和空气先按一定的比例充分混合,由于混合充分,并使其混合后的气体为燃气略为过量,使烧嘴燃烧产生的烟气为微还原性气氛,使铜水在无氧或低氧的环境中熔化、流动。
通过调节仪表改变助燃空气和燃气的流量可改变烧嘴燃烧功率,从而达到改变铜熔化速度的目的,根据轧机的生产情况可非常方便控制铜水熔化速度,使整条生产线稳定生产。
保温炉燃烧系统由1只60万大卡/小时高速烧嘴和燃气电磁阀组及比例阀、助燃风机、变频调节器和温度控制仪表等组成,安装在保温炉炉壁上的热电偶检测到炉内铜水的相对温度变化,通过温度控制仪对进入保温炉烧嘴的空气流量进行变频控制,同时燃气比例阀自动跟踪空气的变化,使进入烧嘴的燃气和空气成比例,从而达到温度控制和比例燃烧的目的。
保温炉烧嘴在点火前也要进行泄漏检测,以保证燃烧安全。
流槽燃烧系统包括流槽烧嘴、助燃风机、电磁阀组和比例阀组成。
上溜槽安装有6~7只5~10万大卡/小时的低压燃气烧嘴,烧嘴低氧燃烧,使其产生的烟气为微还原性,一方面给流入保温炉的铜水加热保温,另一方面保护铜水不受空气侵入,保证铜水质量。
下流槽安装7~8只5~10万大卡的低压燃气烧嘴,烧嘴工作在低氧燃烧状态,使流入浇包的铜水不受空气侵入,确保铜水的低含氧量。
上溜槽设置扒渣口一个,用以清除铜水中的杂质。
燃烧控制系统在燃气总管入口处安装有燃气总切断阀,对燃气压力、空气压力进行实时监测,对烧嘴燃烧状态进行实时监控,当产生燃气泄漏等影响安全生产的情况时自动切断燃气供应,确保生产安全。
本系统中所有燃气电磁阀组、燃气比例阀、燃烧控制器及调节仪表等主要部件均选用美国或德国原装进口产品。
4.2五轮式连铸机(专利号:ZL00244512.3)一台结晶轮直径φ1900 mm结晶转速 1.84-2.814 r/min出锭速度 10.17-13.11 m/min浇铸截面 2300 mm2电动机 5.5 kW (AC)冷却水压力 0.3-0.5 Mpa冷却水量 170 m3/h冷却水温 < 35 ℃五轮式连铸机由结晶轮、压紧轮、张紧轮、导轮、浇堡装置、冷却装置、钢带吹干、扫尘、加热涂碳装置、剔锭器、引桥、涂碳装置、牵引机构、水节流装置、气动控制系统等组成,除导轮装置外,其余均安装在同一底板上。
4.3 滚剪机一台电机 15 kW (AC)铸坯剪切长度 700 mm滚剪机由一交流电机-驱动,针摆减速机减速。
滚剪机滚轮上分别装有两把刀,作对滚剪切,剪切长度700mm左右。
4.4 校直刨角机一台校直刨角机由校直部分及刨角机部分组成,校直共五只导轮,上面二只下面三只,错位安装,刨角部分有四把刨刀,分别刨去铸锭顶面飞边。
4.5 打毛机一台电机0.75 kW打毛机是用以扫去铣角后粘在铸锭上的切屑,两只打毛轮别由电机单独驱动。
4.6 连轧机(专利号:ZL200420032401.7)一台主电机 450 kW (DC)终轧速度10 m/s (最大)出杆直径φ8 mm轧制中心高902.5 mm机架数12 架二辊机架 4 架三辊机架8 架轧辊名义直径φ255 mm轧机采用主动喂料,动力从主传动箱输出,由气缸夹紧铸锭,助推喂入1号机架。
粗轧部分采用4付φ255两辊式机架,立辊2付,平辊2付,精轧部分采用8付φ255Y型机架,分上下传动,交替布置。
当轧制过程中发生事故而引起过载时,则安全联轴节中的剪切销被剪断,以保护传动齿轮和轴。
4.7 轧机乳液润滑系统一套乳液泵 80 m3/h , 15 kW过滤器 GLQ-100散热器35m²乳液经离心泵、过滤器、热交换器进入装在齿轮箱上面的总管,通过胶管,对各机架的齿轮、轧辊、进出口导卫进行润滑,最后乳液全部通过底座上的回流槽,经过回流管回到乳液池。
4.8机油润滑系统一套齿轮泵 5.5 kW工作压力 0.1-0.3 Mpa过滤器 GLQ-80油箱 5 m3油箱中的油通过油泵经过滤器来到齿轮箱后的进油总管,分三处进入齿轮箱,然后经过分支油管的喷嘴对齿轮和滚动轴承进行喷溅润滑。
回油是从齿轮箱端头下侧经回油管到油箱4.9 光亮收杆机一套本机主要由冷却装置、操作平台、夹送装置、引桥、环形摆线装置、贮线装置、小车、供酒精水系统等组成。
1) 牵引装置牵引速度10 m/s (最大)牵引电机7.5 kW (DC)该装置采用双主动夹送,弹簧调整压力。
由直流电机通过三角带传动带动一夹送辊转动,同时通过两对齿轮带动另一夹送辊转动(同步)。
2) 绕杆装置成圈直径φ2000mm绕杆电机 4 kW (DC)杆子在牵引推力穿入蜗轮轴,再下穿螺旋摆管进行预变形,然后绕落在小车框内。