常用机床参数功能设定说明整理
数控机床参数及设置

数控机床参数及设置数控机床参数及设置首先要了解的题目是:什么是机床参数,为什么要设置参数。
数控系统制造厂家的用户是机床制造厂家,而不是使用机床的终极用户,机床厂往向数控装置厂家往买数控装置。
当然,也有些机床厂家是自己制造数控装置,不用往买别人的数控系统。
但是不管怎么说,从设计、试制、最后制造生产品,都希看这种数控系统或者说数控装置,能用在各式各样机床上,这样,自己的用户就多了,市场占有就大了。
为此,数控装置制造厂家为了适用面广,而为数控装置预留了很大的适应范围的余地,或者说,留了很多空缺点,要用户根据自己的需要往填写,以便适应自己设计,制造的机床。
例如某一个轴的加减速时间,跟随误差大小;还有一些是机床制造厂在调试过程中来决定的参数,如:正反向间隙,螺距的补偿等等。
当然,有些参数是数控装置制造厂家自己来规定的,比如:你所买的系统应是几轴联运,以及其他的一些规定参数。
还有一部分可以由终极用户根据必要的情况进行适当的修改的。
数控系统有一些是全数字化的,在进行调节器运算时,必须有一些参数,如比例放大系数,微分时间常数,积分时间常数等等都必须事先设定,当程序进行到这里,往查参数就可以了。
这些参数也是可以在一定范围内变化的。
总之,数控装置参数是非常重要的。
它所以重要,一方面了解和把握了参数,就给使用和更好的发挥机床性能上很大的帮助,另一方面在维修中,很多软件的题目,就是出在参数上,了解与把握参数,就可以维修一些软件的故障。
参数的种类很多,有些参考书中对它进行了分类,分为状态型,比率型,真实值型等,还可以从另一个角度分为数控装置制造商对用户的保密参数,和可以告诉用户参数含义的参数。
不管怎么说,我们确实还有很多参数弄不清楚,对于现场维修职员来说,把上千个参数都弄的明明白白是不可能的,一方面是没有资料,另一方面是没有那么多时间往研究它。
这个任务留给科研院所往做吧!对于现场维修职员,又必须弄懂一些最基本的参数,所以,我们根据维修手册提供的,以及历次这些至公司培训的记录,整理出来,供大家参考。
数控机床CNC参数设置

数控机床CNC参数设置1 CNC参数的调试修改方法⑴、在设置页面打开参数开关。
⑵、工作模式选择在录入方式。
⑶、在参数页面修改相应的参数。
⑷、修改完参数后关掉参数开关再按复位键,部分参数修改后还需关掉系统电源。
2了解每个CNC参数所对应的作用以及修改参数后机床性能的变化K1000M CNC参数一览表OTFP 1:输出最高频率为512Kpps。
0:输出最高频率为32Kpps。
RDRN 1:空运行时,快速运动指令运行有效。
0:空运行时,快速运动指令运行无效。
DECI 1:在返回参考点时减速信号为"1"表示减速(回零方式B 时有效)。
0:在返回参考点时减速信号为"0"表示减速。
IOF 1:用MDI键入时,偏置值为增量值。
0:用MDI键入时,偏置值为绝对值。
RS43 1:G43,G44的偏移矢量在复位时被清零。
0:G43,G44的偏移矢量在复位时保持不变。
DCS 1:MDI方式时,按【输出】键执行。
0:MDI方式时,按【循环启动】键执行。
SCW 1:最小指令增量按英制系统(机床是英制系统)。
0:最小指令增量按公制系统(机床是公制系统)。
NFDO 1:恒设为1TJHD 1:在手动示教方式中,手轮有效。
0:在手动示教方式中,手轮无效。
PM2,PM1:设定固定循环G76,G87中的退刀方向。
RSJG 0:按复位键时,系统自动关闭M03、M04、润滑、冷却输出。
1:按复位键时,对输出M03、M04、润滑、冷却输出没有影响。
MPOF 1:屏蔽电压低报警PPD 1:用绝对零点编程(G92)也设置相对坐标值。
0:用绝对零点编程(G92)不设置相对坐标值。
PCMD 1:输出波形是脉冲。
0:输出波形是方波。
PRGB :无意义。
TLCP 1:在与指定平面(G17,G18,G19)垂直的轴上进行刀具长度补偿。
(刀具长度补偿B)。
0:与指定平面无关,在Z轴上进行刀具长度补偿(刀具长度补偿A)。
项目3 数控机床参数设置----NC基本参数的设置
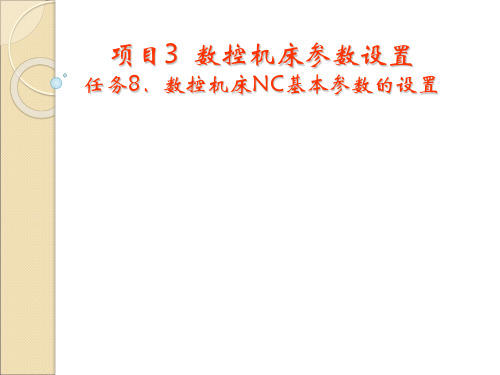
9 3
任 务 项 目. 数 数控 控机 机床 床主 参轴 数参 设数 置的 设 置
二、主轴参数初始化(伺服侧):
No4133:设定电机代码 No4019#7=1,关机开机执行参数初始化
注:主轴初始化必须在No3716#0=1,No3717非0情况下有效 。
9 3
任 务 项 目. 数 数控 控机 机床 床主 参轴 数参 设数 置的 设 置
任 务
项.
目数
3
控
数机
控床
机
床 参 数 设 置
基 本 参 数 的
设
置
NC
8
四、NC的基本参数
显示与编辑参数:
语言参数:动态语言切换 No3104#6:是否显示排除刀具长度补偿的坐标值 No3129#1:是否显示排除刀具位置偏移的编程位置 No3105#0 #2:是否显示伺服 主轴的实际速度、T代码 No3106#5:是否显示主轴倍率 No3111#0:是否显示伺服调整画面 No3111#1:是否显示主轴调整画面 No3117#7:报警时是否切换至信息画面 No3115#0:是否显示当前位置 No3115#1:是否显示绝对、相对、待走量坐标
3
控
数机
控床
机
床 参 数 设 置
基 本 参 数 的
设
置
NC
8
四、NC的基本参数
外设通讯参数: No20=0,1,2,4,17(RS232、存储卡、USB)
设定值: 0:RS232 1口(JD36A) ~ No101~No103 1:RS232 1口(JD36A) ~ No111~No113 2:RS232 2口(JD36B) ~ No121~No123 4:存储卡 17:USB
机床参数及详解

机床参数无论是哪种型号的CNC系统都有大量的参数,少则儿百个,多则上千个,看起来眼花缭乱。
经过认真讨论,归纳起来又有肯定的共性可言,现供应其分类方式以做参考。
1、按参数的表示形式来划分,数控机床的参数可分为三类。
(1)状态型参数状态型参数是指每项参数的八位二进制数位中,每一位都表示了一种独立的状态或者是某种功能的有无。
例如FANUCO-TD系统的1号参数项中的各位所表示的就是状态型参数。
(2)比率型参数比率型参数是指某项参数设置的某几位所表示的数值都是某种参量的比例系数。
例如FANUCO—TD系统的512、513、514号参数项中每项的八位所表示就是比率型参数。
(3)真实值参数真实值参数是表示某项参数是直接表示系统某个参数的真实值。
这类参数的设定范围一般是规定好的,用户在使用时肯定要留意其所表示的范围,以免千百万设定参数的参数超出范围值。
例如FANUCO—TD系统的522、523、524、525号参数项中每项的八位所表示的就是比率参数。
2、按参数本身的性质可分为两类(1) 一般型参数凡是在CNC制造厂家供应的资料上有具体介绍参数均可视为一般型参数。
这类参数只要按着资料上的说明弄清含义,能正确、敏捷应用即可。
(2)隐秘级参数隐秘级参数是指数控系统的生产厂在各类公开发行的资料所供应的参数说明中,均有一些参数不做介绍,只是在随机床所附带的参数表中有初始的设定值,用户搞不清其具体的含义。
假如这类参数发生转变,用户将不知所措,必需请厂家专业人员进行维护和修理。
西门子840D主要参数意译西门子8 4 0 D的主要参数释义文字一、通道机床数据20000通道名称20050几何轴•通道轴的安排20060通道中的几何轴名称20070通道中机床轴号20220通道中的通道轴名称20220主导主轴的号20222主轴旋转的使能/使能取消20224轴运行的M运行(西门子模式)20225轴运行的M功能(外部模式)20226 T, M刀具地址代号转变20228在MMC上显示轴20220带面对轴功能的几何轴20228大事驱动程序调用的设置20229 Prog-Events 的属性20220 RESET复位时的基本功能设置20222 NC启动的基本功能设置20224方式转变中断了MDI20226带读限制的中断程序关闭20227带信号的中断程序关闭20228几何轴转变自动使能20220复位时刀具生效20221复位的预选刀具20222 RESET复位/启动和TC时刀具生效20223 RESET 时$P_USEKT 的预选值20224刀具夹持装置号20226 RESET复位时刀架生效20228换刀在搜寻中20220 RESET复位时刀沿生效20222有效总偏差复位20220用复位健使转换生效。
牧野机床参数说明书
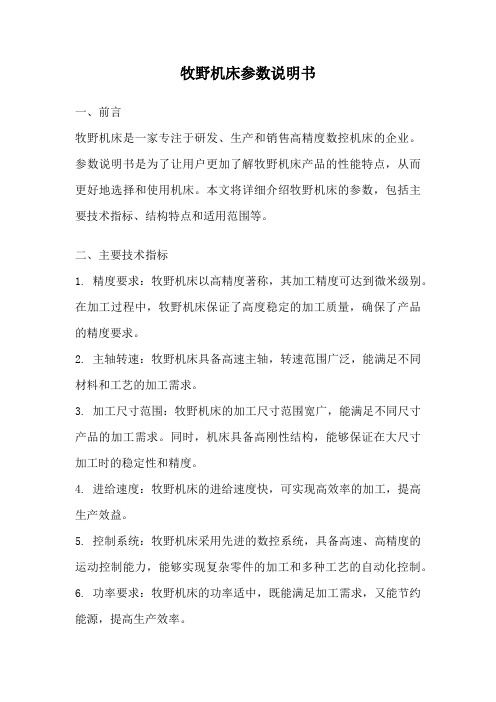
牧野机床参数说明书一、前言牧野机床是一家专注于研发、生产和销售高精度数控机床的企业。
参数说明书是为了让用户更加了解牧野机床产品的性能特点,从而更好地选择和使用机床。
本文将详细介绍牧野机床的参数,包括主要技术指标、结构特点和适用范围等。
二、主要技术指标1. 精度要求:牧野机床以高精度著称,其加工精度可达到微米级别。
在加工过程中,牧野机床保证了高度稳定的加工质量,确保了产品的精度要求。
2. 主轴转速:牧野机床具备高速主轴,转速范围广泛,能满足不同材料和工艺的加工需求。
3. 加工尺寸范围:牧野机床的加工尺寸范围宽广,能满足不同尺寸产品的加工需求。
同时,机床具备高刚性结构,能够保证在大尺寸加工时的稳定性和精度。
4. 进给速度:牧野机床的进给速度快,可实现高效率的加工,提高生产效益。
5. 控制系统:牧野机床采用先进的数控系统,具备高速、高精度的运动控制能力,能够实现复杂零件的加工和多种工艺的自动化控制。
6. 功率要求:牧野机床的功率适中,既能满足加工需求,又能节约能源,提高生产效率。
三、结构特点1. 基床:牧野机床的基床采用高刚性材料制造,具备良好的抗震性和稳定性。
同时,基床的设计经过优化,能够有效吸收加工过程中的振动,提供稳定的工作环境。
2. 主轴系统:牧野机床的主轴系统采用精密轴承和先进的冷却系统,确保主轴的高速运转和稳定性。
同时,主轴系统具备自动换刀功能,能够实现多种工艺的快速切换。
3. 进给系统:牧野机床的进给系统采用精密的滚珠丝杠和高精度的伺服电机,能够实现高速、高精度的进给运动。
同时,进给系统具备快速移动功能,提高了工作效率。
4. 控制系统:牧野机床的控制系统采用先进的数控技术,具备强大的功能和稳定的性能。
用户可以通过触摸屏操作界面,实现各种加工参数的调整和监控。
5. 保护系统:牧野机床具备完善的安全保护系统,包括紧急停机按钮、过载保护、断电保护等功能,保障了操作人员和机床的安全。
四、适用范围牧野机床广泛适用于各种行业的加工需求,包括航空航天、汽车制造、模具制造、电子设备等。
数控车床技术参数
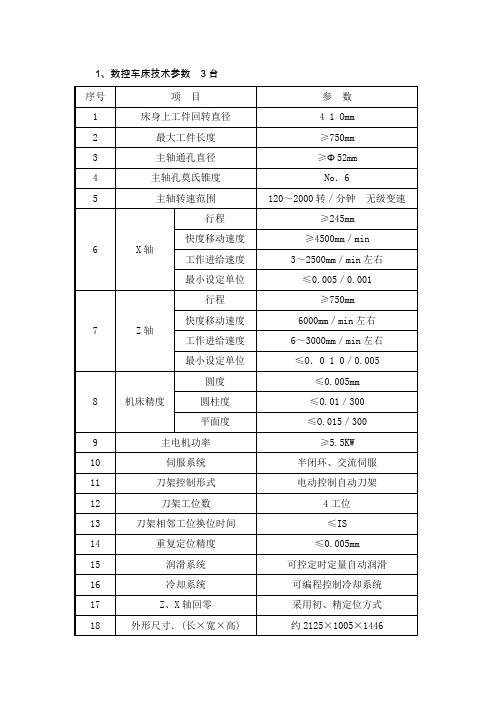
12
刀架工位数
4工位
13
刀架相邻工位换位时间
≤IS
14
重复定位精度
≤0.005mm
15
润滑系统
可控定时定量自动润滑
16
冷却系统
可编程控制冷却系统
17
Z、X轴回零
采用初、精定位方式
18
外形尺寸.(长×宽×高)
约2125×1005×1446
l9
控制系统配置
FANUC—Oi中文界面
注:要求配置相匹配的机床减震垫铁。
22
配置相匹配防震垫铁及活顶针、卡盘等附件
3、二氧化碳气体保护焊机主要技术参数:NBC--250A型1台
序号
项目
参数
1
输入电源
三相380V±10%50HZ
2
额定输入电流
14A
3
额定输入容量
9.2KVA
4
最大工作电压
27V
5
额定焊接电流
60-250A
6
额定负载持续率
60%
7
适用焊丝直径
0.8/1.0
8
No.6
11
进纹范围
l一192mm
13
英制螺纹范围
2—24tpi
l4
模数螺纹范围
O.25~48
15
径节螺纹范围
1—96DP
16
横刀架行程
320rnm
17
小刀架移动行程
140mm
18
床尾主轴最大行程
150mm
19
床尾主轴直径
Φ75mm
20
床尾主轴孔锥度
No.5
21
主电机
7.5KW
FANUC常用系统参数说明

FANUC常用系统参数说明FANUC常用系统参数是一些特定的数值,在FANUC系统中用来配置和调整机床和控制系统的功能和性能。
这些参数可以被读取、修改和保存,以满足特定的加工需求和设备配置。
下面是一些常用的FANUC系统参数的说明:1.机床坐标系参数(G53,G54-G59):这些参数用于定义机床的坐标系。
每个坐标系可以代表不同的加工位置和工件夹持方式。
通过调整这些参数,可以在不同的工件加工过程中实现坐标系的切换和调整。
2.加工坐标系参数(G92):这个参数用于定义加工过程中的零点和坐标系位置。
通过调整这些参数,可以将工件的零点和坐标系原点设置为加工过程中的任意位置。
3.进给速率参数(F):这个参数用于定义进给速率。
通过调整这个参数,可以控制机床的进给速度,以便在不同的加工条件下达到最佳的加工效果。
4.进给倍率参数(G93,G94,G95):这些参数用于设置进给倍率。
通过调整这些参数,可以在加工过程中调整进给速率的倍数,以满足不同的加工要求。
5.插补方式参数(G01,G02,G03):这些参数用于定义插补方式。
通过调整这些参数,可以控制机床的插补方式,包括直线插补、圆弧插补等,以满足不同的加工需求。
6.主轴转速参数(S):这个参数用于定义主轴的转速。
通过调整这个参数,可以控制主轴的转速,以满足不同的加工要求。
7.刀具半径补偿参数(G40,G41,G42):这些参数用于刀具半径补偿。
通过调整这些参数,可以在加工过程中补偿刀具半径的影响,以确保加工轮廓的准确性和精度。
8.切削进给参数(G96,G97):这些参数用于定义切削进给方式。
通过调整这些参数,可以选择恒速切削进给(G96)或恒功率切削进给(G97),以适应不同的切削条件。
9.向前补偿参数(G43,G49):这些参数用于定义向前补偿。
通过调整这些参数,可以在加工过程中补偿刀具的尺寸和位置变化,以确保加工结果的准确性和精度。
10.循环启动参数(G80):这个参数用于循环启动。
FANUC数控系统参数设定
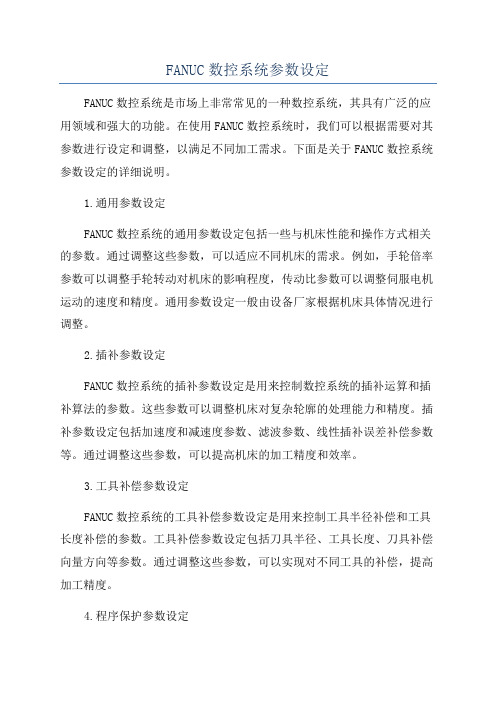
FANUC数控系统参数设定
FANUC数控系统是市场上非常常见的一种数控系统,其具有广泛的应用领域和强大的功能。
在使用FANUC数控系统时,我们可以根据需要对其参数进行设定和调整,以满足不同加工需求。
下面是关于FANUC数控系统参数设定的详细说明。
1.通用参数设定
FANUC数控系统的通用参数设定包括一些与机床性能和操作方式相关的参数。
通过调整这些参数,可以适应不同机床的需求。
例如,手轮倍率参数可以调整手轮转动对机床的影响程度,传动比参数可以调整伺服电机运动的速度和精度。
通用参数设定一般由设备厂家根据机床具体情况进行调整。
2.插补参数设定
FANUC数控系统的插补参数设定是用来控制数控系统的插补运算和插补算法的参数。
这些参数可以调整机床对复杂轮廓的处理能力和精度。
插补参数设定包括加速度和减速度参数、滤波参数、线性插补误差补偿参数等。
通过调整这些参数,可以提高机床的加工精度和效率。
3.工具补偿参数设定
FANUC数控系统的工具补偿参数设定是用来控制工具半径补偿和工具长度补偿的参数。
工具补偿参数设定包括刀具半径、工具长度、刀具补偿向量方向等参数。
通过调整这些参数,可以实现对不同工具的补偿,提高加工精度。
4.程序保护参数设定
5.通讯参数设定
总之,FANUC数控系统的参数设定可以根据实际加工需求进行灵活的
调整和配置,使数控系统更加适应不同的加工任务。
通过合理的参数设定,可以提高机床的加工精度和效率,保证加工质量。
同时,设定好的参数也
可以提高操作的安全性,保护程序的机密性。
5、标准机床参数的设定

标准机床参数的设定1)多次按压MDI键盘上的[SYSTEM]按键,直至屏幕横向功能条出现[参数设定],通过对应横向软键选择,选择后,画面跳转为[参数设定支援]画面。
2)移动光标至[轴设定],通过横向软件选择[操作]---[初始化]---出现[是否设定初始值?]---选择[执行],系统自动将轴设定中的相关参数设定为标准值。
3)设定完成后,将跳转至[报警信息]画面,并增加了[PW0000 必须关断电源]的报警,忽略此报警,再次选择[SYSTEM]按键,进入[参数设定支援]画面,移动光标至[轴设定]处,通过横向软键选择[操作]---[选择],进行以下标准参数设定。
轴设定参数设置列表参数号参数名称参数中文注解设定值1006#3 X DIA 各轴的移动指令为:0: 半径指定。
1: 直径指定。
11320 XZ LIMIT + 各轴的存储行程限位的正方向坐标值调试期间不使用软限位时,此参数设置为-1.机床动作调试完毕后,此参数设置应距离硬件限位5mm。
1321 XZ LIMIT - 各轴的存储行程限位的负方向坐标值调试期间不使用软限位时,此参数设置为1.机床动作调试完毕后,此参数设置应距离硬件限位5mm。
1410 DRY RUN RATE 空运行速度此参数设置为机、电、液协议中轴快速移动速度的一半1420 XZ RAPID FEEDRATE 各轴的快速移动速度此参数设置为机、电、液协议中轴快速移动速度。
1421 XZ RAPID OVR F0 每个轴的快速移动倍率的F0 速度200mm200mm1423 XZ JOG FEEDRA TE 每个轴的JOG 进给速度1000mm1000mm1424 XZ MANUAL RAPID 每个轴的手动快速移动速度此参数设置为机、电、液协议中轴快速移动速度的一半1425 XZ REF RETURN FL 每个轴的手动返回参考点的FL 速度300mm300mm1428 XZ REF FEEDRA TE 每个轴的参考点返回速度3000mm3000mm4)设置参数完毕后,选择横向软键左侧的[回退键],并通过横向软键选择[参数设定],返回至上一级画面,移动光标至[伺服设定]处,通过横向软键选择[操作]---[选择],进入[伺服设定]参数画面,并根据下表设置相应参数 参数名称 中文注解设定值电机代码由于0ID 系统要求使用HRV2功能,所以调试时应根据电机铭牌查询电机代码,并加100为设定值。
brother机床系统参数说明书

brother机床系统参数说明书Brother机床系统参数说明书一、引言Brother机床系统是一种先进的数控机床系统,具有多项优异的性能指标和功能特点。
本文将对Brother机床系统的参数进行详细的说明,以帮助用户更好地了解和使用该系统。
二、系统参数1. 控制系统参数Brother机床系统采用先进的数控控制系统,具有高速、高精度、高可靠性等特点。
其控制系统参数包括控制器型号、主轴驱动功率、控制通道数、控制分辨率等。
其中,控制器型号决定了系统的控制能力和功能扩展性,主轴驱动功率决定了系统的加工能力,控制通道数和控制分辨率则影响了系统的精度和平滑度。
2. 运动系统参数Brother机床系统的运动系统参数包括伺服电机型号、伺服电机功率、导轨类型、滚珠丝杠规格等。
伺服电机型号和功率决定了系统的动力性能和定位精度,导轨类型和滚珠丝杠规格影响了系统的运动平稳性和传动精度。
3. 加工能力参数Brother机床系统的加工能力参数包括最大加工尺寸、最大负载、最高转速、最大进给速度等。
最大加工尺寸决定了系统能够加工的工件尺寸范围,最大负载决定了系统的承载能力,最高转速和最大进给速度影响了系统的加工效率和加工质量。
4. 自动换刀系统参数Brother机床系统配备了先进的自动换刀系统,其参数包括刀库容量、刀具规格、换刀时间等。
刀库容量决定了系统能够存放的刀具数量,刀具规格影响了系统的加工能力和灵活性,换刀时间影响了系统的生产效率。
5. 辅助功能参数Brother机床系统还具有多项辅助功能,如自动测量、自动校正、自动补偿等。
这些功能的参数包括测量精度、校正精度、补偿精度等。
测量精度决定了系统的工件尺寸测量精度,校正精度影响了系统的定位精度,补偿精度影响了系统的加工精度。
三、系统特点1. 高速高精度Brother机床系统具有高速高精度的特点,可实现高效率的加工。
通过先进的控制系统和运动系统,系统能够实现高速、高精度的运动控制,提高加工效率和加工质量。
常用各种数控机床控制面板功能简介

常用各种数控机床控制面板功能简介数控机床的控制面板是数控机床最重要的部分之一,它是数控编程和加工的核心。
本文将介绍常用各种数控机床控制面板的功能,以帮助读者更好地了解数控机床的操作方法。
数控机床控制面板基本介绍数控机床控制面板是数控机床的操作界面,通常包括主界面、编程面板、存储面板、参数设置面板、IO口扩展面板、轴面板等多个部分。
在不同的数控机床上,这些面板的形式和布局都有所不同,但它们的基本功能却都是相似的。
数控机床上的控制面板通常由控制器、断电保留器、推动按钮开关、转换开关、指示灯以及手轮等多个组成部分组成。
数控机床控制面板的常见功能1. 动态调整功能动态调整功能是数控机床上比较常见的控制面板功能之一。
这个功能通常可以让操作者通过手柄来调整机床的不同参数,比如调整加工速度、加工深度等等。
这种功能通常非常的实用,可以大大提高数控机床的加工效率。
2. 编辑程序功能数控机床控制面板的另一个常见功能是程序编辑功能。
这个功能可以让操作者自行编写程序代码,并通过控制面板来将程序下载到数控机床中,以便机床可以进行自动加工。
3. 加工记录功能加工记录功能是数控机床上非常重要的功能之一。
它可以记录机床加工时的各项数据,例如加工时间、加工精度、加工速度、加工温度等等,以便后续的数据分析和加工优化。
4. 设备监控功能数控机床控制面板通常都可以提供设备监控功能。
这个功能可以监测设备的各项参数,包括温度、电压、电流等等,以确保设备正常运行,并且及时预警设备出现故障的情况。
5. 自动校准功能自动校准功能是数控机床上比较高级的功能之一。
它可以让机床在加工前自行进行校准,以确保机床的加工质量和精度。
6. 报警系统数控机床控制面板上的报警系统是非常重要的功能之一。
这个功能可以在机床出现故障时发出警报,并解决故障及时避免机床太大的损害。
7. 模拟仿真功能数控机床控制面板上一些高端机床还会提供模拟仿真功能。
这个功能可以对加工过程进行模拟,以便操作者可以更好地了解机床运转过程,从而进行更优化的改进。
常用车床参数

8940-8949
初始画面标题字符代码1-9
5
可以编辑()
7
0: 报警通过“CAN” + “RESET”操作来清除。
12255 往后是防止错误操作相 关的参数
伺服电机的最大速度
伺服电机的最大加速度
伺服电机的最大加速度
7105设 1 时
第1台手轮的 X 地址
12351
手轮进给m n的倍率
看说明书
0
设置为1 时显示SV1067 FSSB配置错误(软件)
3701
3701
2
1
外部操作信息履历画面显示
键盘上显示的请看参数资料
0
是否对当前位置显示
1
是否显示待走量显示
屏保时间 分钟
当前显示的轴名称 绝对坐标 当前显示的轴名称 相对对坐标
本参数设定为0时,使用参数(NO.1020)的设定值
0 是否对程序8000-8999的编辑
0不禁止 1禁止
4 是否对程序9000-9000的编辑
M,S,T,B 的选通脉冲信号和结束 信号之间的
0 G4.3 1 使用高速信号(关机重启M功能无效)
0
进给,快速移动倍率信号0:使用负逻辑 1:使用正逻辑
1
互锁信号无效,G8.0
1
各轴互锁信号无效,G130
1
不同轴向的互锁信号无效,G132,G134
回参考点时 0信号在0时减速
1信号在1时减速
程序段开始互锁
对9000后程序编辑设置口令
对9001后程序编辑口令输入解码后才能改3202#4
0
8000-8999的程序显示
1
9000-9999的程序显示
7
C系列 储存器保护信号,参数可 写设定
主轴手动档—(LK-164)机床PLC参数说明

主轴手动档机床----FANUC----适用面板:LK-164一、T参数说明T03----360 000 (R200.2间隙润滑泵开时间:6 min)T04----360 000 (R200.3间隙润滑泵关时间:6 min)T10---- 1800 (R201.1换刀相序检测时间:1.8 s)T11----150000 (R201.2换刀刀位监控时间:15s)T12----1800 (R201.3刀架反转锁紧时间:1.8 s)T13----16 (R201.4刀架电机正反转间延时:16 m s)T14----2500 (R201.5主电机Y起动时间:2.5 s)T15----16 (R201.6主电机星三角间延时:16 m s)T16----8 (R201.7主电机△运行后延时:8 m s)T17----16 (R202.0主轴停指令发出,延时:16 m s)T18----50 (R202.1主电机Y制动准备好,延时:50 m s)T19----1000 (R201.2主电机Y制动,直流接入时间:1 s)T20----8 (R110.7刀架锁紧后,延时:8 m s)二、K参数说明K0.0----硬限位选择:0,无效;1,有效K0.1----绝对编码器选择:0,绝对;1,增量K0.2----互锁警示:0,有效;1,无效K0.3----SVM起动检测:1,有效;0,无效K0.4----BU.OH检测:K3.0----刀架锁紧信号:0,有效;1,无效K3.1----CDZ功能:0,无效;1,有效K3.2----SMZ功能:0,无效;1,有效K3.6----侧门信号:0,有效;1,无效K4.2----刀位选择:0,6工位;1,4工位三、其他说明1、适用面板:LK-164(注意手动换刀按键灯无,Y4.6端子引出,已通知洛克更正)2、急停、复位、点动均不带制动注意,进给齿轮比N/M=3/1000(X轴)N/M=3/500(Z轴)sram_bak.001内容有误1、使用最新程序2、SRAM_BAK.001参数伺服传动比有误,需重设。
机床常用参数介绍
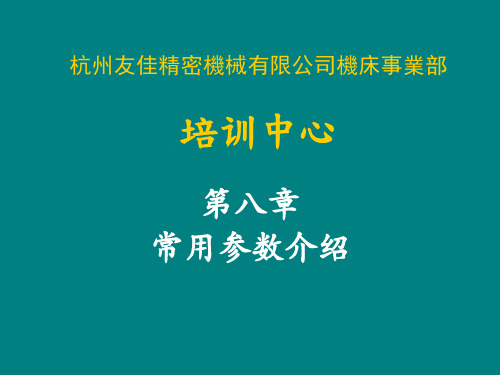
数据单位
1mm/min 0.1inch/min 1deg/min
有效的数据范围
30~240000 30~96000 30~240000
各轴快速运行倍率的F0速度
设定单位 数据单位 有效的数据范围
公制机床 1mm/min
30~15000
英之机床 0.1inch/min
30~6000
旋转轴 1deg/min
1:一致
有关伺服的参数
1825
各轴的伺服环增益
字轴型
[数据范围] 1~9999
该参数设定各轴的位置控制环的增益。 进行直线与圆弧等插补(切削 加工)时,请将所有轴设定相同的值。机床只做定位时,各轴可设定不 同的值。环路增益越大,则位置控制的响应越快,但如果太大,伺服系 统不稳定。 位置偏差量(误差寄存器内累积的脉冲量)和进给速度的 关系如下:
0000
SEQ
INI ISO TVC
数据类型:位型
TVC 是否进行TV检查 0:不进行 1:进行
ISO 数据输出时的代码 0:EIA代码
SEQ 是否进行顺序号的自动插入
0:不进行
1:进行
在编辑方式,用MDI键编程时可自 动地插入顺序号,顺序号的增量值 在参数NO.3216中设定。
1:ISO代码
INI 输入单位 0:公制单位 1:英制单位
有关显示及 编辑的参数
3102 3119 3190
DTH SPN HNG ITA CHI HUN
FRN GRM JPN POR
HUN DTH POR SPN HNG ITA CHI FRN GRM JPN 显示语言
0
0
0
0
0
0
0
0
雕刻机参数设置说明
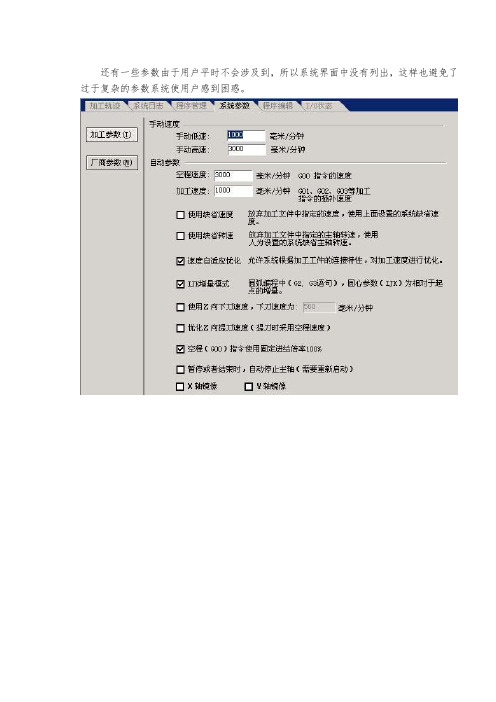
还有一些参数由于用户平时不会涉及到,所以系统界面中没有列出,这样也避免了过于复杂的参数系统使用户感到困惑。
手动速度:包括手动高速速度和手动低速速度,这两个值用来控制用户在“点动”模式下的运动速度。
●手动低速速度是指只按下手动方向键时的运动速度;●手动高速速度是指同时按下“高速”键时的运动速度。
这两个值也可以在数控状态窗口中直接设定。
参见4.6节。
自动参数:●空程速度:G00 指令的运动速度;●加工速度:G01、G02、G03等加工指令的插补速度。
这两个值控制以自动方式运动时的速度,如果自动模式下的加工程序、或者MDI指令中没有指定速度,就以这里设定的速度运动。
注意:增量方式的运动速度是空程速度。
这两个值也可以在数控状态窗口中直接设定。
参见4.6节。
●使用缺省速度:是否放弃加工程序中指定的速度,使用上面设置的系统缺省速度。
●使用缺省转速:指示系统是否放弃加工程序中指定的主轴转速,使用人为设置的系统缺省转速。
●速度自适应优化:是否允许系统根据加工工件的连接特性,对加工速度进行优化。
●IJK增量模式:圆心编程(IJK)是否为增量模式,某些后处理程序生成的圆弧编程使用的IJK值是增量值。
关于这一点,请参考对应的后处理程序说明。
●使用Z向下刀速度:是否在Z向垂直向下运动时,采用特定的速度落刀速度。
●优化Z向提刀速度:是否在Z向垂直向上运动时,采用G00速度提刀。
点)。
●空程(G00)指令使用固定进给倍率100%:这个参数是一个选项。
指示系统在执行空程指令时,是否忽略进给被率的影响。
这样当改变倍率时,不影响空程移动的速度。
●暂停或者结束时,自动停止主轴(需要重新启动):设定当一个加工程序中途暂停或加工结束后,是否自动停止主轴转动。
●X轴镜像:设定X轴进行镜像。
●Y轴镜像:设定Y轴进行镜像。
换刀位参数:●使用换刀位:如果希望在加工完成后自动回到某个位置,请选择该选项。
其他换刀位参数只有在使用换刀位有效时,才起作用。
数控机床串行主轴参数设定
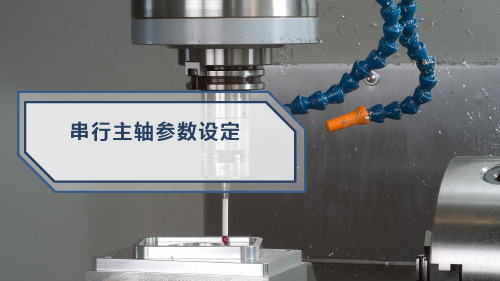
二、串行主轴参数设定
示范操作:串行主轴参数设定
谢谢
246 αic12/6000
244
αi3/10000 308
αiI22/7000
245
αi6/10000 310
αiI30/6000
320
322
αiI3/12000 αiI6/12000
309
401
αiI22/10000
406
一、串行主轴相关参数 主轴电机型号及含义
一、串行主轴相关参数
一、串行主轴相关参数
一、串行主轴相关参数
单击【操作】,将光标移动至“主轴设定”处,单击【选择】,出现主轴设定页 面。此后的参数设定就在该页面中进行。
一、串行主轴相关参数
一、串行主轴相关参数
型号
代码 型号
代码 型号 代码 型号
代码 型号
代码 型号
代码
部分主轴电机代码表
βiI3/10000 βiI6/10000 βiI8/8000
αiI18/7000
312
314
316
318
αiI40/600 αiI50/4500 αiI1.5/15000 αiI2/15000
323
324
305
307
αiI8/1000 αiI12/10000 αiI15/10000 αiI18/10000
402
403
404
405
αic15/6000
αic8/6000
βiI12/7000
332
333
334
αic1/6000 αic2/6000 αic3/6000
335 αic6/6000
240
αi5/10000 301
机器工具产品参数设定手册说明书
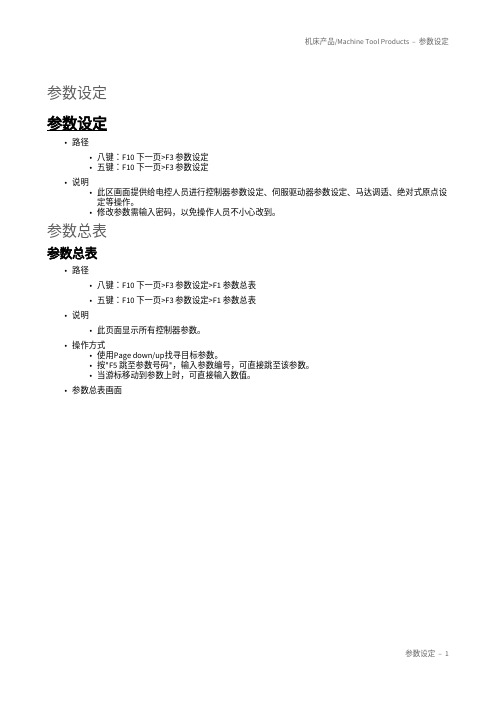
••••••••••••••••参数设定参数设定路径八键:F10 下一页>F3 参数设定五键:F10 下一页>F3 参数设定说明此区画面提供给电控人员进行控制器参数设定、伺服驱动器参数设定、马达调适、绝对式原点设定等操作。
修改参数需输入密码,以免操作人员不小心改到。
参数总表参数总表路径八键:F10 下一页>F3 参数设定>F1 参数总表五键:F10 下一页>F3 参数设定>F1 参数总表说明此页面显示所有控制器参数。
操作方式使用Page down/up 找寻目标参数。
按"F5 跳至参数号码",输入参数编号,可直接跳至该参数。
当游标移动到参数上时,可直接输入数值。
参数总表画面•••••••••••••••轴向/主轴参数轴向/主轴参数路径八键:F10 下一页>F3 参数设定>F2轴向/主轴参数五键:F10 下一页>F3 参数设定>F2轴向/主轴参数说明此页面显示与轴向、主轴、原点/极限/参考点相关的控制器参数,以二维表格的方式呈现,方便电控人员查阅与设定。
轴向参数轴向参数有效版本:10.118.41O, 10.118.48路径八键:F10 下一页>F3 参数设定>F2 轴向/主轴参数>F1轴向参数五键:F10 下一页>F3 参数设定>F2 轴向/主轴参数>F1轴向参数说明此页面显示与轴向相关的控制器参数,例如轴卡端口号码、轴名称等。
每个页面显示六个轴的参数,若超过六轴,可使用"左右键"切换页面。
左/右键切换页面时,一次切换上/下一个轴向显示。
轴向参数上方显示对应轴名称,未开启之轴向则显示*轴名称。
操作方式•••••••••••••••••••使用方向键找寻目标参数及切换页面。
当游标移动到参数上时,可直接输入数值。
轴向参数画面主軸参数主軸参数有效版本:10.118.41O, 10.118.48路径八键:F10 下一页>F3 参数设定>F2 轴向/主轴参数>F2主軸参数五键:F10 下一页>F3 参数设定>F2 轴向/主轴参数>F2主軸参数说明此页面显示与主軸相关的控制器参数,例如迴授倍頻、馬達增益等。
- 1、下载文档前请自行甄别文档内容的完整性,平台不提供额外的编辑、内容补充、找答案等附加服务。
- 2、"仅部分预览"的文档,不可在线预览部分如存在完整性等问题,可反馈申请退款(可完整预览的文档不适用该条件!)。
- 3、如文档侵犯您的权益,请联系客服反馈,我们会尽快为您处理(人工客服工作时间:9:00-18:30)。
常用机床参数功能设定说明整理FANUC2016.08.151/47常用参数分类罗列以下几种u有关RS232数据传输以及存储卡DNC加工参数u有关刚性攻丝常用参数u与同步轴控制相关参数u与撞块回参考点以及光栅尺回参考点相关参数u与FSSB连接相关参数u与圆弧加工相关参数u CMR扩大10倍相关参数u模具切削系列相关参数2/47u有关RS232数据传输以及存储卡DNC加工参数将I/O CHANNEL (对应参数N20)设定为0。
波特率N103 N113 N123设定为12。
需保证RS232接口焊线正确,如右图。
3/47存储卡DNC加工这样设定:首先将I/O CHANNEL 设定为4(按上述方法设定),参数N138#7=1。
将加工程序拷贝到存储卡里(可以一次拷贝多个程序)。
选择[RMT]方式,程序画面,按右软件键[►],找[CARD],显示存储卡里面的文件列表。
选择需要加工的程序序号,按[DNC-CD],然后再按[DNC-ST](如果找不到[DNC-CD],需要按几次软件键[►],直到找到该软键为止)。
按机床操作面板上的循环启动按钮,就可以执行DNC加工了。
4/47u有关刚性攻丝常用参数普通刚性攻丝:针对刚性攻丝过程经常出现诊断号N453超差,现整理相关参数如下:N5310-N5312攻丝时位置偏差极限值,推荐值10000,超过设定值会有ALM740报警N5241-5244攻丝主轴最高转速,推荐值100~2000,设定太小会有ALM200报警。
N5280攻丝时主轴和Z轴公共位置环增益需要和主轴位置环增益N4065-N4058设定一致,推荐值1000~3000,但不可设定太大,太大会有异响。
调整攻丝时加减速时间常数:N5261-N5264进刀时加减速时间常数。
N5271-N5274退刀时加减速时间常数。
N5201#2=0进刀和退刀都使用N5261-N5264。
#2=1进刀和退刀分别用各自时间常数。
时间常数不可设定太小,否则主轴和攻丝轴来不及加速到设定速度。
P(螺距)=F(进给速度)/S(主轴转速),P值无法恒定。
监控诊断号N453,需要10以内,越小越好。
N5300 Z轴到位宽度。
N5301主轴到位宽度。
理论上这两值越小越好,对诊断号N450影响较大,诊断号N450越小越好,建议小于200。
5/47FSSB高速刚性攻丝:在31i-B系列与全新的0i-F系统中,系统与放大器支持只用一根光缆进行FSSB通信,一方面减少了传统电缆通信出现干扰的几率,另一方面可以更加节省配线。
在此基础上,FANUC推出了与传统刚性攻丝相比更为优秀的FSSB高速刚性攻丝功能。
刚性攻丝中,通过主轴放大器与伺服放大器间的FSSB高速通信,可减少同步误差或在精度不变的条件下缩短循环时间。
此外,如果同时使用刚性攻丝最优加减速(选项)功能时,可以最大限地使用主轴的扭矩,因而可进一步提高FSSB高速刚性攻丝的效果。
6/47与传统刚性攻丝相比,FSSB高速刚性攻丝与普通刚性攻丝的区别如下表所示:7/47由于位置环增益对于攻丝轴与主轴可以分别设定,主轴与攻丝轴可以最大限度的提高加工精度,同时时间常数与加工进给速度较之前可以设定更小的值,加工效率有了较大的提升。
限制条件下列情况下不能使用此功能:(1)模拟主轴刚性攻丝(2)伺服电机主轴刚性攻丝(3)主轴同步控制方式下的刚性攻丝同时在FSSB刚性攻丝中,不能使用以下功能(1)双位置反馈(2)伺服HRV4控制8/47与FSSB高速刚性攻丝常用相关参数设定参数号推荐值参数设定描述N43449800先行前馈系数N4037100速度前馈系数N4549#11FSSB高速刚性攻丝有效N5203#21刚性攻丝中前馈有效N5204#01显示诊断NO.452N24203#01FSSB高速刚性攻丝(CNC)功能有效N2429#10/0/1FSSB高速刚性攻丝(伺服轴)功能有效(Z轴)N242041与伺服轴同步的主轴的主轴编号N26105000FSSB高速刚性攻丝中的伺服轴位置增益N2423#20FSSB高速刚性攻丝反向动作补偿功能关闭N26130FSSB高速刚性攻丝反向动作补偿量N52140刚性攻丝同步误差允许范围值N46610主轴停止允许误差9/47u与同步轴控制相关参数以垂直轴W1&W2绝对式电机编码器为例,作如下步骤讲述:Ø从动轴W2的参数N8303 #0,#1, #7=1,1,0,此步骤改动会提示关机。
Ø将N1815 W1&W2#5都设1,N1815 #4=0(主/从都要设),会伴随有提示回参考点报警发生。
Ø将N8303从动轴W2#0#1设1 ,此项设定会提示关机,为校准同步误差设定。
Ø上述参数设定完毕后,执行回参考点操作,首次回参考点会有请关闭电源报警提示,可监控N8326有无值赋入。
Ø再次回参考点,有挡块的情况压挡块减速至零,参数N1815#4自动由0跳1。
至此返回参考点结束,但是此时会有W1和W2坐标显示不一致的情况,需要将N8303 W2轴#7位设1,N8325(同步误差调整最大补偿值)设1,再次回零即可。
备注:同步调整过程中会出现SV0005,请检查N8314(机床坐标值同步误差检查时的最大误差值)的设定,设定为0默认不检查误差。
10/47u与撞块回参考点以及光栅尺回参考点相关参数N1005#1 各轴返回参考点方式:0挡块1无挡块N2084 柔性进给齿轮(分子)N2085 柔性进给齿轮(分母)N2024位置脉冲数N1821 参考计数器容量N1850每轴的栅格偏移量N1815#5是否使用绝对脉冲编码器作为位置检测器0不使用1使用N1815#4 绝对脉冲编码器原点位置的设定0没有建立1建立N1815#1位置检测使用类型:0内置位置编码器1分离式编码器或光栅尺N1620 快速进给加减速时间常数N1420 快速进给速度N1424 手动快速进给速度撞块返回参考点需要保证相关参数设定准确,如果设定有误,会出现返回参考点未完成,以及返回参考点位置不一致等诸多问题。
11/47光栅尺回参考点目前有以下几种情况:增量式返回参考点方式N1815#1置1距离式返回参考点方式N1815#1#2置1,1绝对式返回参考点方式N1815#1#5置1,1光栅尺返回参考点过程中,会出现DS1449 参考点返回参数不一致报警,此时首先检查光栅尺安装情况以及反馈读数头安装是否完好,是否有污渍,紧接着检查N1821,N1882参数设定是否正确,如果依然报警,请检查接入光栅接口板一侧屏蔽情况是否完好。
光栅尺移动过程中经常出现SV0445光栅尺软断线报警,此时需检查读数头安装情况,是否安装支架有晃动等,尝试将N2003#1设定为1,N2064默认为4。
12/47u与FSSB连接相关参数FSSB设定有自动设定和手动设定两种方式,在此着重介绍自动设定方式,手动方式仅着简要介绍。
①设定参数N1902#0#1为0,0。
可在FSSB画面上进行自动设定。
②在参数N1023中设定伺服轴数,分别为X:1、Y:2、Z:3、C:-1。
③各轴的伺服参数进行初始化,对应参数N2000#1。
④CNC关机后再开机。
进入FSSB的设定画面,也可用系列步骤进行自动设定:步骤1:进入FSSB的设定画面①按功能键[SYSTEM],显示系统画面。
②按数次扩展键,直到出现FSSB菜单。
③按软键FSSB。
④按软键AMP(放大器)。
13/47FSSB连接现有两种连接方式,区别主要在于主轴模块使用JA7B电缆接口还是COP10B光缆接口。
电缆与光缆连接区分14/47A1-L 1X A2-L 2Y (双轴)步骤2:放大器信息画面参数调整在放大器设定画面中,给连接到各放大器的轴设定一个控制轴号。
在此画面中,驱动器从上到下按升序列出驱动轴号。
当设定控制轴号时,要考虑哪个放大器连接到哪个CNC 轴上,也就是确定伺服通道与NC 通道的对应关系。
工作顺序是距离CNC 最近的放大器先被访问。
在放大器设定画面中,0与重复号码不得输入。
在放大器设定画面输入轴号:A2-M 3Z (双轴)15/47PS9115如果出现放大器不能正常连接,且出现PS9115报警。
报警相关16/47步骤3:进入轴设定画面在轴设定画面中,设定关于轴的信息,如分离型检测器接口(光栅尺分离接口板)单元的连接器号和Cs轮廓控制等的设定。
在M1、M2上设定对应各轴的连接器号,对于不使用分离检测器接口单元的轴,设定0。
使用分离检测器的轴,需将参数N1815#1置1,否则会有SV0417报警发生。
步骤4:完成设定记住FSSB设定画面设定完成后,皆需按[SETTING]结束,关机生效。
用这种方法,参数N1023、N1905、N1910~N1919、N1936、N1937根据自动计算的结果自动设定。
同时参数N1902#1自动跳1,以表示各参数已完成设定。
此时应关闭电源,然后开机,以使各轴按已定参数工作。
17/47FSSB手动设定方式参数N1902#0设置为0,即为手动设定方式。
相关参数N1023、N1905、N1936~N1939、N14340~N14407(带有附加轴板时,追加N14408~N14425、N14444~N14459)。
)备注:手动设定FSSB参数较多,容易遗漏出错,一般建议自动引导设置。
31B系统与31A系统FSSB设定部分有较大差异,请参考右图。
18/47u与圆弧加工相关参数影响圆弧加工相关的参数大致有以下几种情况:Ø1.反向越冲反向越冲的产生,是由于当机床某一个轴向某一方向驱动,然后必须向相反方向反向移动时,该轴驱动电机施加的扭矩不够,造成在换向处由于摩擦力的方向发生改变而出现短时的粘性停顿。
反向越冲将使圆弧插补刀具轨迹出现一个小平台后再向原轨迹复位的台阶。
在图形上表现为:在某轴上有一小尖峰,尖峰大小随机床进给率的不同而变化。
出现反向越冲时,首先检查机床参数N2003#5(反向间隙加速功能)是否为1,然后调整参数N2048,范围:0—2000,以原值为基础,以50为单位进行调整,通常设为150。
也可以配合参数N2071(作用时间)进行调整,范围:0—20,以原值为基础,以1为单位进行调整,通常设为8即可。
同时,在机床不产生震动和噪音的前提下,增大机床的速度环增益N2021可以改善反向越冲和整体圆度值。
19/47Ø2.反向间隙当机床某一轴出现丝杠磨损、螺母损坏或导轨磨损等情况时,会导致滚珠丝杠中扭曲过大而引起反向间隙。
反向间隙在球杆仪检测图形中表现为:在沿某轴线处有沿图形中心外凸(正值)或内凹(负值)的一个或数个台阶。
通过调整机床参数N1851可以减小反向间隙对圆度误差的影响,方法为:若球杆仪检测时所测结果是正值,增加N1851的值,负值则相反。