注射剂除菌
注射剂灭菌工艺研究内容以及资料撰写格式
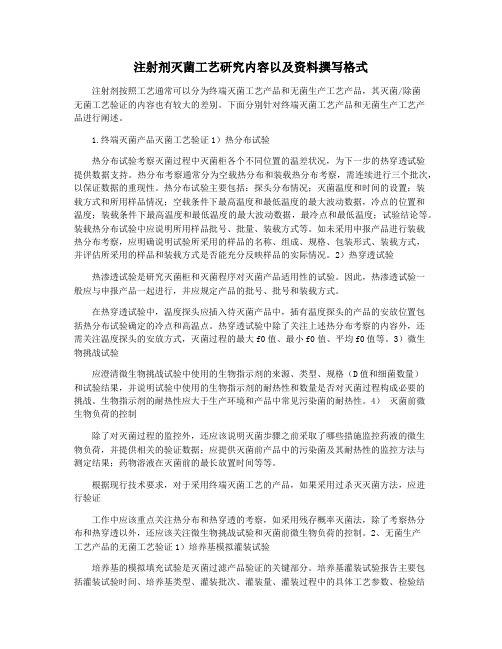
注射剂灭菌工艺研究内容以及资料撰写格式注射剂按照工艺通常可以分为终端灭菌工艺产品和无菌生产工艺产品,其灭菌/除菌无菌工艺验证的内容也有较大的差别。
下面分别针对终端灭菌工艺产品和无菌生产工艺产品进行阐述。
1.终端灭菌产品灭菌工艺验证1)热分布试验热分布试验考察灭菌过程中灭菌柜各个不同位置的温差状况,为下一步的热穿透试验提供数据支持。
热分布考察通常分为空载热分布和装载热分布考察,需连续进行三个批次,以保证数据的重现性。
热分布试验主要包括:探头分布情况;灭菌温度和时间的设置;装载方式和所用样品情况;空载条件下最高温度和最低温度的最大波动数据,冷点的位置和温度;装载条件下最高温度和最低温度的最大波动数据,最冷点和最低温度;试验结论等。
装载热分布试验中应说明所用样品批号、批量、装载方式等。
如未采用申报产品进行装载热分布考察,应明确说明试验所采用的样品的名称、组成、规格、包装形式、装载方式,并评估所采用的样品和装载方式是否能充分反映样品的实际情况。
2)热穿透试验热渗透试验是研究灭菌柜和灭菌程序对灭菌产品适用性的试验。
因此,热渗透试验一般应与申报产品一起进行,并应规定产品的批号、批号和装载方式。
在热穿透试验中,温度探头应插入待灭菌产品中,插有温度探头的产品的安放位置包括热分布试验确定的冷点和高温点。
热穿透试验中除了关注上述热分布考察的内容外,还需关注温度探头的安放方式,灭菌过程的最大f0值、最小f0值、平均f0值等。
3)微生物挑战试验应澄清微生物挑战试验中使用的生物指示剂的来源、类型、规格(D值和细菌数量)和试验结果,并说明试验中使用的生物指示剂的耐热性和数量是否对灭菌过程构成必要的挑战。
生物指示剂的耐热性应大于生产环境和产品中常见污染菌的耐热性。
4)灭菌前微生物负荷的控制除了对灭菌过程的监控外,还应该说明灭菌步骤之前采取了哪些措施监控药液的微生物负荷,并提供相关的验证数据;应提供灭菌前产品中的污染菌及其耐热性的监控方法与测定结果;药物溶液在灭菌前的最长放置时间等等。
兽用化学药品注射剂灭菌和无菌工艺研究及验证指导原则

兽用化学药品注射剂灭菌和无菌工艺研究及验证指导原则一、灭菌工艺研究兽用化学药品注射剂的灭菌工艺是确保产品无菌的重要环节。
在灭菌工艺研究中,应选择合适的灭菌参数,如温度、压力、时间等,并对灭菌设备进行确认,以确保其性能满足工艺要求。
同时,应对产品的热稳定性和灭菌效果进行评估,以确保灭菌工艺的有效性和安全性。
二、无菌工艺研究无菌工艺研究是兽用化学药品注射剂生产中的关键环节,其主要目标是确保产品在整个生产过程中保持无菌状态。
应进行无菌工艺验证,以证明所采取的措施能够确保产品无菌。
在无菌工艺研究中,应对生产环境、设备、操作方法等进行严格控制,并对产品的无菌性能进行检测和评估。
三、工艺验证工艺验证是确保兽用化学药品注射剂生产过程中灭菌和无菌工艺稳定性和可靠性的重要手段。
在工艺验证中,应对生产过程中的各项参数进行严格控制,并进行多批次的验证。
验证成功后,应定期对工艺进行复查,以确保其持续有效性。
四、持续生产验证持续生产验证是对灭菌和无菌工艺在实际生产过程中的表现进行监测和评估的重要环节。
应定期对生产过程中的各项参数进行检查和记录,并对产品的无菌性能进行检测。
同时,应对生产环境和设备进行定期清洁和消毒,以确保其符合无菌要求。
五、产品质量检测产品质量检测是确保兽用化学药品注射剂安全性和有效性的重要手段。
在灭菌和无菌工艺验证和持续生产验证中,应对产品的各项质量指标进行检测和评估,如外观、澄清度、pH值、含量等。
同时,应对产品的无菌性能进行严格检测,以确保其符合规定要求。
六、安全性评估安全性评估是对兽用化学药品注射剂可能对使用者产生的风险进行评估的重要环节。
在灭菌和无菌工艺研究和验证中,应考虑产品的毒性和副作用,并进行相应的风险评估和控制。
同时,应对产品的安全性和有效性进行长期的跟踪监测和评估。
七、稳定性考察稳定性考察是评估兽用化学药品注射剂在储存和使用过程中的稳定性的重要手段。
在灭菌和无菌工艺研究和验证中,应对产品在不同条件下的稳定性进行考察和评估,并确定产品的有效期和储存条件。
用于最终灭菌药品(注射剂)的蒸汽灭菌工艺及验证指南

用于最终灭菌药品(注射剂)的蒸汽灭菌工艺及验证指南用于最终灭菌药品(注射剂)的蒸汽灭菌工艺及验证指南一、范围由于蒸汽,湿热灭菌本身具备无残留,不污染环境,不破坏产品表面,并容易控制和重现等优点,被广泛应用于最终灭菌药品(注射剂)的除菌过程中。
本指南为有关人员提供最终灭菌药品(注射剂)的蒸汽灭菌柜的验证指南,以及蒸汽灭菌工艺及验证的一些操作方法的指南。
本指南依据《药品生产质量管理规范》(1998年修订)的相关准则,但本指南叙述的通用原则和方法不是法定的。
本指南的着重于最终灭菌药品(注射剂)的蒸汽-湿热灭菌工艺的验证,但有些通用原则和方法对于冻干机的湿热灭菌、某些设备的在线蒸汽灭菌等可能也具备参考价值。
二、目的蒸汽,湿热灭菌验证的目的,就是通过一系列验证试验提供足够的数据和文件依据,从而找到最有效最合理的灭菌参数,并把已经验证过的饱和蒸汽灭菌设备和灭菌工艺参数应用到药品生产的除菌过程中去,以证明用于药品生产过程中的每一台饱和蒸汽灭菌设备都能起到灭菌的效果,并且对不同灭菌物品的灭菌过程和灭菌效果具有可靠性和重现性,即验证结果必须证明生产中所采用的灭菌过程对经过灭菌的物品能够保证残存微生物污染的概率或可能性低于百万分之一。
蒸汽-湿热灭菌周期的设计和开发与蒸汽灭菌柜的性能以及被灭菌产品的适用性有关。
蒸汽-湿热灭菌介质包含以下几种:饱和蒸汽,空气-蒸汽混合气体,过热水等等。
其中:饱和蒸汽的加热速度最快,但是对于大型的软包装产品,过热水浸泡灭菌的方法效率更高,然而在过热水灭菌法中,热量的转移很大程度上依赖于容器中介质的强制运动。
饱和蒸汽是与液体状态的水保持平衡时的水蒸汽,因此饱和蒸汽只能存在于水汽的分界线上,即温度与压力之间的关系是固定的。
灭菌效果是通过蒸汽,蒸汽-空气混合物,过热水等介质与灭菌物品的热传递或产生冷凝水的水合作用来实现的。
蒸汽-空气混合物与受压的水或蒸汽相比,单位体积所包含的热容量较低,但是,蒸汽-空气混合物作为灭菌戒指具有能够适当调整蒸汽-空气比例达到不同结果的优点。
小容量注射剂生产中湿热灭菌基础知识
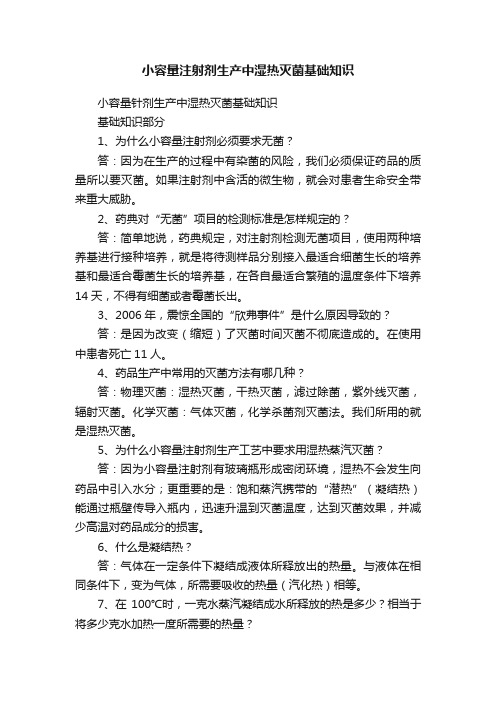
小容量注射剂生产中湿热灭菌基础知识小容量针剂生产中湿热灭菌基础知识基础知识部分1、为什么小容量注射剂必须要求无菌?答:因为在生产的过程中有染菌的风险,我们必须保证药品的质量所以要灭菌。
如果注射剂中含活的微生物,就会对患者生命安全带来重大威胁。
2、药典对“无菌”项目的检测标准是怎样规定的?答:简单地说,药典规定,对注射剂检测无菌项目,使用两种培养基进行接种培养,就是将待测样品分别接入最适合细菌生长的培养基和最适合霉菌生长的培养基,在各自最适合繁殖的温度条件下培养14天,不得有细菌或者霉菌长出。
3、2006年,震惊全国的“欣弗事件”是什么原因导致的?答:是因为改变(缩短)了灭菌时间灭菌不彻底造成的。
在使用中患者死亡11人。
4、药品生产中常用的灭菌方法有哪几种?答:物理灭菌:湿热灭菌,干热灭菌,滤过除菌,紫外线灭菌,辐射灭菌。
化学灭菌:气体灭菌,化学杀菌剂灭菌法。
我们所用的就是湿热灭菌。
5、为什么小容量注射剂生产工艺中要求用湿热蒸汽灭菌?答:因为小容量注射剂有玻璃瓶形成密闭环境,湿热不会发生向药品中引入水分;更重要的是:饱和蒸汽携带的“潜热”(凝结热)能通过瓶壁传导入瓶内,迅速升温到灭菌温度,达到灭菌效果,并减少高温对药品成分的损害。
6、什么是凝结热?答:气体在一定条件下凝结成液体所释放出的热量。
与液体在相同条件下,变为气体,所需要吸收的热量(汽化热)相等。
7、在100℃时,一克水蒸汽凝结成水所释放的热是多少?相当于将多少克水加热一度所需要的热量?答:一克水蒸汽凝结成水所释放的热是539卡,相当于将539克水加热一度所需要的热量。
这是一份很大的热量,正是小容量注射剂灭菌所需要的。
8、湿热灭菌强度的强度主要由哪两种参数决定的?答:温度和时间。
9、常见微生物有哪些种类?答:病毒,如流感病毒;细菌,如大肠杆菌;真菌,如酵母、曲霉等。
10、一般微生物死亡的条件是什么?答:一般微生物死亡65℃30分钟11、霉菌厚垣孢子和细菌的芽孢死亡的条件是什么?答:一般杀死芽孢为115℃20分钟12、影响湿热灭菌效果的因素有哪些?答:(1)微生物的种类和数量。
注射剂的灭菌方法

注射剂的灭菌方法
注射剂的灭菌方法通常有以下几种:
1. 高温灭菌:使用高温蒸汽或干热方法对注射剂进行灭菌。
高温蒸汽灭菌是将注射剂置于高压蒸汽中进行灭菌,一般在121C下持续加热15-30分钟,可以有效地杀灭细菌、孢子和病毒。
干热灭菌则是使用高温干热空气灭菌,通常在160-170C下持续加热1-2小时。
2. 化学灭菌:使用化学消毒剂对注射剂进行灭菌。
常用的化学消毒剂包括过氧化氢、醛类、氯化物等。
化学灭菌方法比较适用于对热敏感的注射剂。
3. 过滤器灭菌:通过将注射剂通过微孔过滤器进行灭菌。
过滤器通常具有0.2微米的孔径,可以有效过滤掉细菌和较大的微生物。
4. 辐射灭菌:使用电离辐射(如γ射线、X射线)对注射剂进行灭菌。
辐射灭菌可以杀灭各类微生物,但可能对一些药物的化学性质产生一定影响,需要进行适当的产品质量控制。
在医药行业中,以上灭菌方法通常会根据具体情况和要求进行选择和应用。
灭菌过程需要严格控制,以确保注射剂的安全性和有效性。
药学专业知识:注射剂的物理灭菌方法

药学专业知识:注射剂的物理灭菌方法注射剂的灭菌方法包括物理灭菌法、化学灭菌法和无菌操作法。
物理灭菌法:干热灭菌法、湿热灭菌法、射线灭菌法、滤过除菌法;化学灭菌法:气体灭菌法、化学药剂杀灭菌法。
今天主要介绍注射剂的物理灭菌方法:(一)湿热灭菌法本方法特点:由于蒸气潜热大,穿透力强,容易使蛋白质变性或凝固,灭菌效率高。
包括煮沸灭菌法、流通蒸汽灭菌法、热压灭菌法和低温间歇灭菌等方法。
根据药品性质进行选用。
1.热压灭菌法本法一般公认为最可靠的湿热灭菌法。
应用大于常压的饱和水蒸气加热杀灭微生物的方法,能杀灭所有细菌增殖体和芽胞。
热压灭菌所需的温度及与温度相当的压力及时间如下115℃(67kpa),30分钟;121℃(97kpa),20分钟;126℃(139 kpa)15分钟。
卧式热压灭菌柜,是一种大型灭菌器,使用时应注意的问题:①必须使用饱和蒸汽。
②必须将灭菌器内的空气排出。
③灭菌时间必须由全部药液温度真正达到所要求的温度时算起。
④灭菌完毕后,停止加热,一般必须使压力表所指示的压力逐渐下降到零,才能放出锅内蒸气,使锅内压力与大气压相等后,稍稍打开灭菌锅待10-15分钟,再全部打开。
影响热压灭菌的因素:细菌的种类与数量;药物性质与灭菌时间;蒸气的性质;介质的性质2.流通蒸气灭菌指在常压下100℃流通蒸汽加热杀灭微生物的方法。
杀灭时间为:30~60min。
特点:1)适用于对热不稳定的药品2)不能杀灭所有细菌3)需加入抑菌剂或避菌操作、无菌操作3.煮沸灭菌法是把安瓿或其他物品放入水中煮沸灭菌。
通常煮沸30~60分钟,此法灭菌效果差。
4.低温间歇灭菌法作法:a.温度60~80℃1hr 灭菌b.室温或37℃下放置24hr,再进行上述条件下的灭菌c.反复操作3~5次(二)干热灭菌法1.火焰灭菌法:直接在火焰中烧灼,适用于耐火焰材质,不适用于药品。
2.干热空气灭菌法:在高温干热空气中灭菌的方法。
干热空气灭菌的条件药典规定160℃~170℃需2小时。
贝伐单抗注射液生产工艺中的灭菌方法与制剂包装

贝伐单抗注射液生产工艺中的灭菌方法与制剂包装贝伐单抗注射液是一种常用的抗癌药物,其生产工艺中的灭菌方法和制剂包装非常重要。
本文将详细介绍贝伐单抗注射液生产工艺中常用的灭菌方法以及适用的制剂包装。
一、贝伐单抗注射液生产工艺中的灭菌方法1. 高温高压灭菌法:该方法是传统的灭菌方法之一,通过将贝伐单抗注射液装入灭菌器,在高温高压条件下进行灭菌。
一般使用的温度为121摄氏度,压力为0.1MPa,持续时间为15-20分钟。
这种方法能够有效地杀灭细菌、真菌和病毒,但对产品质量影响较大,需加强对产品的保护。
2. 冷凝灭菌法:这是一种温度较低的灭菌方法,将贝伐单抗注射液置于配备有冷凝剂的灭菌器中,加热至65摄氏度,持续时间为30-45分钟。
该方法适用于热敏感性较高的药物,能够有效杀死细菌和病毒,但对真菌的灭菌效果较差。
3. 双滤法:该方法是将贝伐单抗注射液通过0.22微米过滤器和0.45微米过滤器进行连续过滤,以进行灭菌。
此方法主要用于降低微生物的数量,但并不能杀死微生物。
4. 微波辅助灭菌法:这是一种新兴的灭菌方法,通过微波加热来杀灭微生物。
贝伐单抗注射液在密闭的容器中进行微波辅助灭菌,可快速杀灭微生物,并能够有效保持药物的活性。
然而,该方法的应用还需要进一步的研究和验证。
二、贝伐单抗注射液的制剂包装贝伐单抗注射液的制剂包装需要符合相关的药品包装标准和要求,保证药品的质量和安全性。
1. 注射用小容量袋:贝伐单抗注射液常使用的包装形式之一是小容量注射用袋装。
这种包装方式具有剂量准确、易于使用和携带的优点,能够有效保护药物免受外界环境的污染。
2. 注射用安瓿:贝伐单抗注射液也可以使用注射用安瓿进行包装。
注射用安瓿具有密封性好、使用方便等特点,能够避免药物的污染和氧化。
3. 其他包装形式:除了小容量袋和安瓿,贝伐单抗注射液还可以采用其他形式的包装,如玻璃瓶、塑料瓶等。
无论采用何种包装形式,都需要符合药物包装的相关标准和法规,确保药品的质量和安全性。
化学药品注射剂灭菌和无菌工艺研究及验证指导原则(试行)
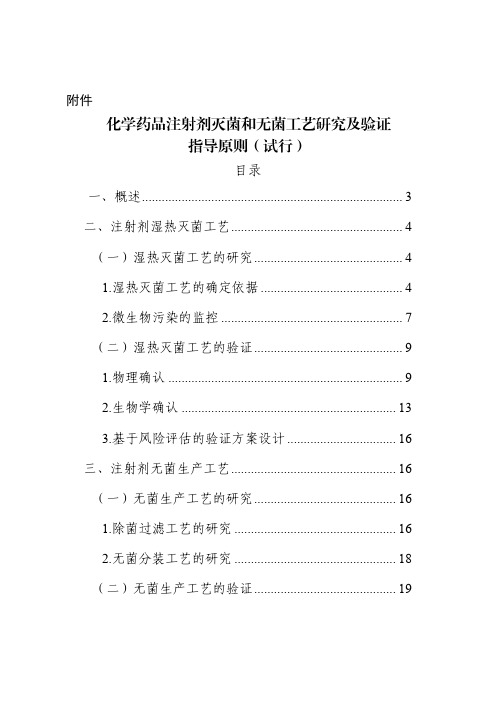
附件目录一、概述 (3)二、注射剂湿热灭菌工艺 (4)(一)湿热灭菌工艺的研究 (4)1.湿热灭菌工艺的确定依据 (4)2.微生物污染的监控 (7)(二)湿热灭菌工艺的验证 (9)1.物理确认 (9)2.生物学确认 (13)3.基于风险评估的验证方案设计 (16)三、注射剂无菌生产工艺 (16)(一)无菌生产工艺的研究 (16)1.除菌过滤工艺的研究 (16)2.无菌分装工艺的研究 (18)(二)无菌生产工艺的验证 (19)1.除菌过滤工艺验证 (19)2.无菌工艺模拟试验 (22)四、附件 (25)五、参考文献 (26)一、概述无菌药品是指法定药品标准中列有无菌检查项目的制剂和原料药,一般包括注射剂、无菌原料药及滴眼剂等。
从严格意义上讲,无菌药品应不含任何活的微生物,但由于目前检验手段的局限性,绝对无菌的概念不能适用于对整批产品的无菌性评价,因此目前所使用的“无菌”概念,是概率意义上的“无菌”。
特定批次药品的无菌特性只能通过该批药品中活微生物存在的概率低至某个可接受的水平,即无菌保证水平(Sterility Assurance Level, SAL)来表征,而这种概率意义上的无菌需通过合理设计和全面验证的灭菌/除菌工艺过程、良好的无菌保证体系以及在生产过程中严格执行药品生产质量管理规范(GMP)予以保证。
本指导原则主要参考国内外相关技术指导原则和标准起草制订,重点对注射剂常用的灭菌/无菌工艺,即湿热灭菌为主的最终灭菌工艺(Terminal Sterilization Process)和无菌生产工艺(Aseptic Process)的研究和验证进行阐述,旨在促进现阶段化学药品注射剂的研究和评价工作的开展。
本指导原则主要适用于注射剂申请上市以及上市后变更等注册申报过程中对灭菌/无菌工艺进行的研究和验证工作,相关仪器设备等的验证及常规再验证不包括在本指导原则的范围内。
本指导原则的起草是基于对该问题的当前认知,随着相关法规的不断完善以及药物研究技术要求的提高,本技术指南将不断修订并完善。
注射液的灭菌

1.了解洁净室的净化标准、净化室的设计以及空气净 化技术、基本设备。 2.掌握灭菌与灭菌技术的原理、应用及基本概念。 3.掌握冷冻干燥的基本原理及影响因素。 4.了解注射剂的分类、特点、质量要求,常用溶剂和 附加剂,常用设备。 5.掌握注射剂与滴眼剂的制备工艺过程及其基本理论、 基本概念和常用术语。 6.掌握热原的概念、性质、组成、污染途径及除去方 法。
湿热灭菌法的比较
湿热灭菌法 热压灭菌法
流通蒸汽灭菌法 煮沸灭菌法
灭菌条件 饱和水蒸气 115℃30min; 121℃20min;126℃15min 100℃流通蒸汽 30~60min 煮沸 30~60min
3.滤过灭菌法
滤过灭菌法是指用滤过方法除去微生物 的方法,是一种机械除菌法。 一般选用孔径0.22μ m或0.3μ m的微孔薄 膜滤器或G6号垂熔玻璃漏斗。 主要适用于对热不稳定的药液、气体、 水等的灭菌。
灭菌条件 火焰中灼烧 135~145℃3~5h 160~170℃2~4h 180~200℃0.5~1h
破坏热原条件
250℃30min 200℃以上 45min
2.湿热灭菌法
采用高温饱和水蒸气或沸水或流通蒸汽进行灭 菌的方法。由于蒸气潜热大,穿透力强,因此 灭菌效率高,灭菌温度低,时间短。 (1)热压灭菌法 采用大于常压的饱和水蒸 气杀灭微生物的方法。为热力灭菌中最有效, 用 途 最 广 泛 的 方 法 。 灭 菌 条 件 为 : 115.5℃ ( 67Kpa ) , 30min ; 121.5℃ ( 97Kpa ) , 20min ; 126.5℃ ( 139Kpa ) , 15min 。 在 规 定 的时间和温度内对细菌的繁殖体和芽孢有效。
一、灭菌制剂与无菌制剂的 定义与分类
注射剂的灭菌
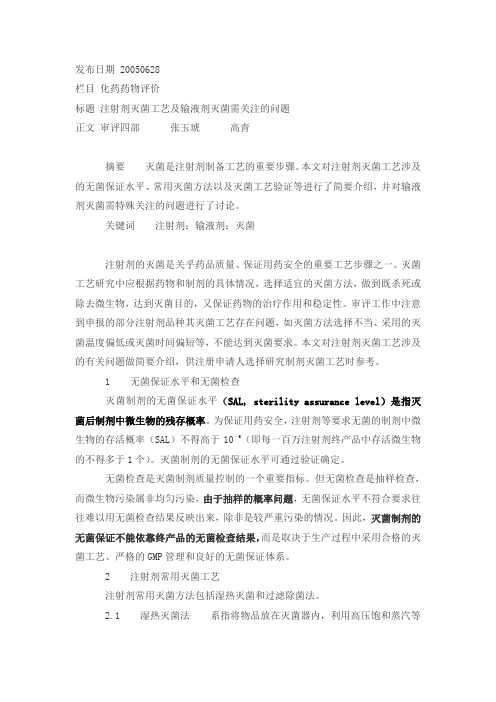
发布日期 20050628栏目化药药物评价标题注射剂灭菌工艺及输液剂灭菌需关注的问题正文审评四部张玉琥高青摘要灭菌是注射剂制备工艺的重要步骤。
本文对注射剂灭菌工艺涉及的无菌保证水平、常用灭菌方法以及灭菌工艺验证等进行了简要介绍,并对输液剂灭菌需特殊关注的问题进行了讨论。
关键词注射剂;输液剂;灭菌注射剂的灭菌是关乎药品质量、保证用药安全的重要工艺步骤之一。
灭菌工艺研究中应根据药物和制剂的具体情况,选择适宜的灭菌方法,做到既杀死或除去微生物,达到灭菌目的,又保证药物的治疗作用和稳定性。
审评工作中注意到申报的部分注射剂品种其灭菌工艺存在问题,如灭菌方法选择不当、采用的灭菌温度偏低或灭菌时间偏短等,不能达到灭菌要求。
本文对注射剂灭菌工艺涉及的有关问题做简要介绍,供注册申请人选择研究制剂灭菌工艺时参考。
1 无菌保证水平和无菌检查灭菌制剂的无菌保证水平(SAL, sterility assurance level)是指灭菌后制剂中微生物的残存概率。
为保证用药安全,注射剂等要求无菌的制剂中微生物的存活概率(SAL)不得高于10-6(即每一百万注射剂终产品中存活微生物的不得多于1个)。
灭菌制剂的无菌保证水平可通过验证确定。
无菌检查是灭菌制剂质量控制的一个重要指标。
但无菌检查是抽样检查,而微生物污染属非均匀污染,由于抽样的概率问题,无菌保证水平不符合要求往往难以用无菌检查结果反映出来,除非是较严重污染的情况。
因此,灭菌制剂的无菌保证不能依靠终产品的无菌检查结果,而是取决于生产过程中采用合格的灭菌工艺、严格的GMP管理和良好的无菌保证体系。
2 注射剂常用灭菌工艺注射剂常用灭菌方法包括湿热灭菌和过滤除菌法。
2.1 湿热灭菌法系指将物品放在灭菌器内,利用高压饱和蒸汽等手段进行灭菌的方法。
蒸汽潜热大,穿透力强,容易使微生物蛋白质变性凝固,灭菌能力强,因此湿热灭菌是最有效及用途最广的灭菌方法。
注射剂制备中常用的湿热灭菌法包括热压灭菌和流通蒸汽灭菌。
5-5注射剂的灭菌及灭菌参数

湿热灭菌法
概念:指用饱和蒸气、沸水或流通蒸气进行灭菌 的方法。 特点:由于蒸气潜热大,穿透力强,容易使蛋 白变性,同时还有作用可靠,操作简便等优点, 湿热灭菌法是应用最广泛的一种灭菌方法,本法 包括热压灭菌法,流通蒸气灭菌法,煮沸灭菌法 和低温间歇灭菌等方法。
第四节 灭菌
二、 灭菌与无菌技术 药剂学中灭菌法可分为三大类:即
物理灭菌、化学灭菌、无菌操作法。
高 压 灭 菌 仪 器
真空灭菌仪器
高压蒸汽灭菌仪器
第四节 灭菌
灭菌法
干热灭菌法
物理灭菌法 湿热灭菌法 射线灭菌法 滤过灭菌法
化学灭菌法 化学药剂杀菌法
无菌操作法
气体灭菌法
物理灭菌法
概念:用高温干热空气灭菌的方法 特点:
适用于耐高温的玻璃制品、金属制品以及不允 许湿气透的油脂类(如油性软膏基质、注射用油等) 和耐高温的粉末化学药品等。 缺点:穿透力弱,温度不易均匀,而且由于灭菌温
度过高,不适用橡胶、塑料及大部分药品。
(一)干热灭菌法
干热灭菌条件: 一般规定为135-145℃灭菌3-5小时; 160-170℃灭菌2-4小时; 180-200℃灭菌0.5-1小时。
第四节 灭菌
灭菌和无菌制剂
一
直接注入体内或直接接触创伤面、
基
粘膜等的一类制剂.
本
概
念
灭菌
应用物理或化学等方法将物体上或
介质中所有微生物繁殖体及其芽孢
全部杀灭或除去的手段。
第四节 灭菌
灭菌法
一
杀灭或除去所有微生物繁殖体和芽孢
注射剂过滤除菌工艺的讨论

国家食品药品监督管理总局药品审评中心(100038)许真玉注射剂过滤除菌工艺的讨论摘要:目的 对注射剂过滤除菌工艺的研究和验证进行讨论,供注射剂生产者参考。
方法 以国内外相关技术指导原则为基础,结合日常技术审评工作经验,进行讨论。
结果与结论 过滤除菌工艺研究需要关注物料的质量控制、除菌过滤器的选择、除菌过滤工艺参数的研究、除菌过滤生产过程的控制等。
过滤除菌工艺验证需要关注培养基模拟灌装试验、除菌过滤系统验证等。
需要通过系统的工艺研究和验证,通过整个生产环境和生产过程的合理控制,保证过滤除菌工艺实现既定的无菌保证水平。
关键词:过滤除菌工艺;工艺研究;工艺验证中图分类号:R95 文献标识码:A文章编号:1005-8257(2014)07-0083-03注射剂是指药物与适宜的溶剂或者分散介质制成的供注入体内的一种制剂,在临床应用时直接注射入人体组织、器官或者血液。
注射剂是无菌制剂的一种,注射剂的无菌是通过良好控制且经过验证的灭菌/除菌生产工艺、生产过程中严格执行药品生产质量管理规范(Good Manufacturing Practice for pharmaceutical products,GM P)实现的。
注射剂的灭菌/除菌生产工艺一般按照“决策树”进行选择(见附图所示),根据无菌保证水平(S ter i l it y Assurance Level,SAL)的高低和风险的大小,注射剂首选终端灭菌工艺,对于不能耐受终端灭菌工艺的,可以考虑采用无菌生产工艺,包括过滤除菌工艺和无菌分装工艺[1]。
由决策树可见,无菌生产工艺是无菌保证水平相对较低、而风险相对较高的一类工艺,但由于一些热不稳定的药品不能耐受终端灭菌工艺,不得不选择无菌生产工艺。
目前,国内很多注射剂生产者,在无菌生产工艺研究和验证方面还存在一些不足。
本文结合国内外相关指导原则,针对无菌生产工艺中的过滤除菌工艺的研究和验证进行讨论,希望与相关人员交流。
注射剂灭菌和灭菌工艺研究及验证指导原则

注射剂灭菌和灭菌工艺研究及验证指导原则引言:注射剂的灭菌过程是确保药品质量和安全的重要环节。
灭菌工艺的研究和验证对于保证注射剂的无菌性至关重要。
本文旨在探讨注射剂灭菌和灭菌工艺的研究以及验证指导原则,以提供指导和参考。
一、注射剂灭菌工艺研究1. 灭菌方法的选择:在注射剂灭菌工艺研究中,首先需要选择合适的灭菌方法。
常见的灭菌方法包括热灭菌、辐射灭菌和化学灭菌等。
根据不同的药品特性和使用要求,选择适当的灭菌方法,确保药品的无菌性。
2. 灭菌工艺参数的确定:灭菌工艺参数的确定是灭菌工艺研究的关键环节。
包括灭菌温度、灭菌时间、灭菌压力等参数的确定。
通过实验研究和数据分析,得出最佳的灭菌工艺参数,以确保药品在灭菌过程中的无菌性。
3. 灭菌效果的评价:灭菌效果的评价是灭菌工艺研究的重要内容。
通过微生物学方法对灭菌后的样品进行检测,评估灭菌效果。
常用的评价指标包括菌落总数、大肠杆菌和金黄色葡萄球菌等。
评价结果的合格性将直接影响灭菌工艺的验证结果。
二、灭菌工艺验证指导原则1. 灭菌工艺验证的目的:灭菌工艺验证的目的是验证所设计的灭菌工艺是否能够确保注射剂的无菌性。
通过严格的验证过程,评估灭菌工艺的有效性和可靠性,为生产实践提供科学依据。
2. 验证样品的选择:灭菌工艺验证需要选择具有代表性的样品进行验证。
样品的选择应考虑到药品的不同特性和使用要求,确保验证结果具有可靠性和可行性。
3. 验证方法的确定:灭菌工艺验证的方法应结合实际情况进行选择。
常用的验证方法包括生物指示物法、物化指标法和微生物学检测法等。
根据不同的药品特性和验证要求,选择适合的验证方法。
4. 验证参数的确定:灭菌工艺验证需要确定合适的验证参数。
包括灭菌温度、灭菌时间和灭菌压力等参数的确定。
通过合理的参数选择,验证灭菌工艺的可行性和有效性。
5. 验证结果的评估:灭菌工艺验证的结果需要进行评估。
根据验证结果,评估灭菌工艺的合格性和可行性。
如果验证结果符合要求,说明灭菌工艺设计合理;如果验证结果不符合要求,需要进行工艺调整和改进。
探索注射剂过滤除菌的风险控制
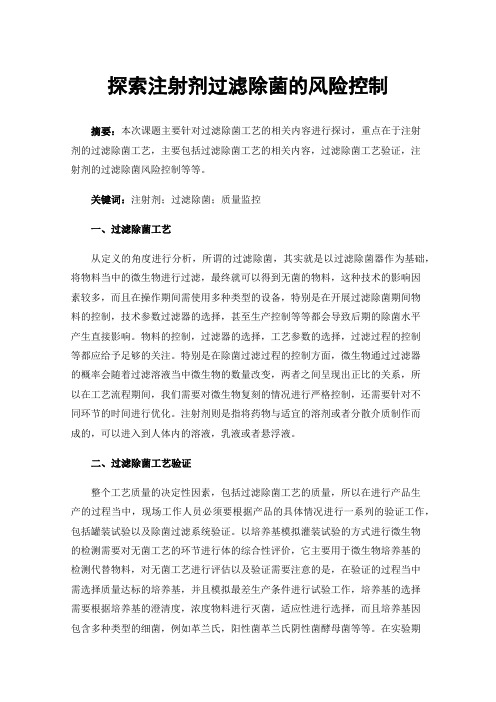
探索注射剂过滤除菌的风险控制摘要:本次课题主要针对过滤除菌工艺的相关内容进行探讨,重点在于注射剂的过滤除菌工艺,主要包括过滤除菌工艺的相关内容,过滤除菌工艺验证,注射剂的过滤除菌风险控制等等。
关键词:注射剂;过滤除菌;质量监控一、过滤除菌工艺从定义的角度进行分析,所谓的过滤除菌,其实就是以过滤除菌器作为基础,将物料当中的微生物进行过滤,最终就可以得到无菌的物料,这种技术的影响因素较多,而且在操作期间需使用多种类型的设备,特别是在开展过滤除菌期间物料的控制,技术参数过滤器的选择,甚至生产控制等等都会导致后期的除菌水平产生直接影响。
物料的控制,过滤器的选择,工艺参数的选择,过滤过程的控制等都应给予足够的关注。
特别是在除菌过滤过程的控制方面,微生物通过过滤器的概率会随着过滤溶液当中微生物的数量改变,两者之间呈现出正比的关系,所以在工艺流程期间,我们需要对微生物复刻的情况进行严格控制,还需要针对不同环节的时间进行优化。
注射剂则是指将药物与适宜的溶剂或者分散介质制作而成的,可以进入到人体内的溶液,乳液或者悬浮液。
二、过滤除菌工艺验证整个工艺质量的决定性因素,包括过滤除菌工艺的质量,所以在进行产品生产的过程当中,现场工作人员必须要根据产品的具体情况进行一系列的验证工作,包括罐装试验以及除菌过滤系统验证。
以培养基模拟灌装试验的方式进行微生物的检测需要对无菌工艺的环节进行体的综合性评价,它主要用于微生物培养基的检测代替物料,对无菌工艺进行评估以及验证需要注意的是,在验证的过程当中需选择质量达标的培养基,并且模拟最差生产条件进行试验工作,培养基的选择需要根据培养基的澄清度,浓度物料进行灭菌,适应性进行选择,而且培养基因包含多种类型的细菌,例如革兰氏,阳性菌革兰氏阴性菌酵母菌等等。
在实验期间可以通过参照中国药典附录当中的培养基微生物生产的过程进行试验,确保微生物生长的过程具有合理性的特点,当然也需要充分考虑到有可能影响试验结果的因素,排除这些因素对实验结果产生消极的影响,例如研究人员的换班,研究人员的休息过程,以及设备意外故障等问题等等。
注射剂过滤除菌的风险控制

注射剂过滤除菌的风险控制摘要:在无菌生产工艺当中主要包含了无菌分装工艺和过滤除菌工艺。
比如说,注射用阿奇霉素,这就属于无菌分装工艺,主要是设计为冻干粉针,其主要特点在于药物溶液在进行无菌过滤之后,在无菌的条件下将其注入到灭菌容器当中进行冻干封存或者是进行无菌封装封存。
我们主要对这种类型的产品在生产过程中,终端过滤除菌工艺当中,所出现的一些质量风险因素和控制途径进行分析和研究,以供参考。
关键词:注射剂;过滤除菌;风险控制引言注射剂主要指的是一种药物和相应的分散介质溶剂等共同形成的可以向体内注入的悬浊液、乳状液以及溶液等,或者是一些在使用之前稀释或者配制成混悬液溶液的粉末以及浓溶液的无菌制剂,通过我国相关要求规定,依照无菌保证水平、风险水平进行管理。
终端灭菌工艺是注射剂灭菌过程中使用最普遍最合理的一种方式,如果某些药物无法耐受终端灭菌工艺,也就是一些对热不稳定性的药物,使用的主要灭菌方式为无菌生产工艺。
1 过滤除菌工艺1.1GMP对过滤除菌的规定当前在新版的无菌药品规定当中对相应的条款作出了规定,可最终灭菌的产品不得通过过滤除菌的方式替代最终灭菌工艺,若是药品在进行生产的过程中无法在最终包装容器当中完成灭菌操作,可以通过除菌过滤器对药液进行过滤,放入到已灭菌的容器当中,因为除菌过滤器无法全部滤走病毒和支原体,所以可以通过热处理等方式对除菌过滤法无法消灭的细菌进行灭除处理。
与此同时,还可以通过相应的措施对过滤药液当中残留的细菌进行控制。
在过滤除菌工艺当中一定要控制细菌的相对水平,保证细菌的数量达到最低,并且对风险进行相关控制,是一种很难处理的除菌工艺。
1.2 过滤除菌膜选择的理论依据在进行除菌过滤工艺操作的过程中,有很多因素会对工艺的应用产生影响,主要是微生物的特征、液体的性质等,在除菌工艺操作的过程中使用的方法主要有微孔过滤法、超滤、反渗透法。
反渗透法主要是对离子进行交换,将水中的可溶性金属盐取出,与此同时还可以去除病毒、细菌和一些有机物。
化学药品注射剂灭菌无菌工艺研究及验证指导原则
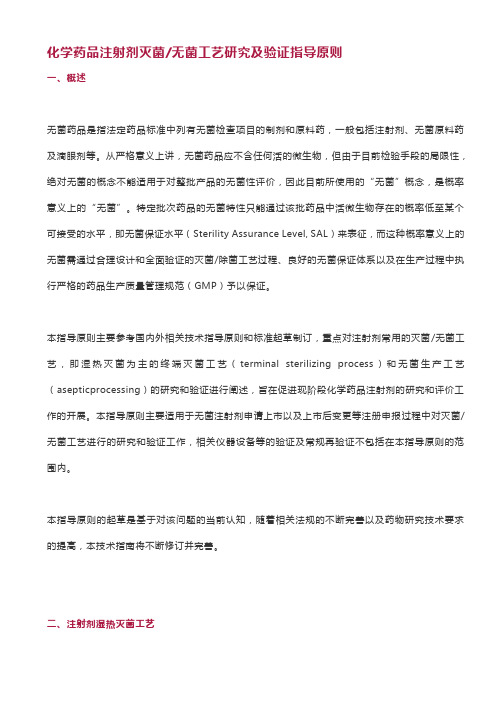
化学药品注射剂灭菌/无菌工艺研究及验证指导原则一、概述无菌药品是指法定药品标准中列有无菌检查项目的制剂和原料药,一般包括注射剂、无菌原料药及滴眼剂等。
从严格意义上讲,无菌药品应不含任何活的微生物,但由于目前检验手段的局限性,绝对无菌的概念不能适用于对整批产品的无菌性评价,因此目前所使用的“无菌”概念,是概率意义上的“无菌”。
特定批次药品的无菌特性只能通过该批药品中活微生物存在的概率低至某个可接受的水平,即无菌保证水平(Sterility Assurance Level, SAL)来表征,而这种概率意义上的无菌需通过合理设计和全面验证的灭菌/除菌工艺过程、良好的无菌保证体系以及在生产过程中执行严格的药品生产质量管理规范(GMP)予以保证。
本指导原则主要参考国内外相关技术指导原则和标准起草制订,重点对注射剂常用的灭菌/无菌工艺,即湿热灭菌为主的终端灭菌工艺(terminal sterilizing process)和无菌生产工艺(asepticprocessing)的研究和验证进行阐述,旨在促进现阶段化学药品注射剂的研究和评价工作的开展。
本指导原则主要适用于无菌注射剂申请上市以及上市后变更等注册申报过程中对灭菌/无菌工艺进行的研究和验证工作,相关仪器设备等的验证及常规再验证不包括在本指导原则的范围内。
本指导原则的起草是基于对该问题的当前认知,随着相关法规的不断完善以及药物研究技术要求的提高,本技术指南将不断修订并完善。
二、注射剂湿热灭菌工艺(一)湿热灭菌工艺的研究1. 湿热灭菌工艺的确定依据灭菌工艺的选择一般按照灭菌工艺选择的决策树(详见附件1)进行,湿热灭菌工艺是决策树中首先考虑的灭菌方法。
湿热灭菌法是利用饱和蒸汽、过热水喷淋等手段使微生物菌体中的蛋白质、核酸发生变性从而杀灭微生物的方法。
注射剂的湿热灭菌工艺应首选过度杀灭法,即F0(标准灭菌时间)值大于12的灭菌工艺;对热不稳定的药物,可以选择残存概率法,即F0值大于8的灭菌工艺。
注射剂灭菌工艺

然会导致隧道烘箱内的一部分玻璃瓶将处于高温区,
长时间滞留时会不会对瓶本身产生影响?
答:要看什么材质的,可以做验证‘,烘洗后
做耐酸耐碱试验。
2、问:热风循环烘箱温度时有失控现象,如
何解决?
答:可以检查一下温度传感器是否失灵,电磁
阀是否工作正常:一、更换温度传感器,二、更换
重要标准
冷点F0 -平均F0≤2min
13
热穿透试验
注意:
同品种不同浓度——考察不同浓度对热
穿透的影响
不同包装规格——进行最大和最小包装
规格的试验
不同装载量——进行最小和最大装载量
的试验
不同灭菌温度——进行最高温度条件下
的试验
14
微生物挑战试验
证明通过该工艺能杀灭一定污染量和D值
的微生物
--生物指示剂
否
是
产品是否可以用其他非干热方法灭菌,
如电离辐射,吸收最小剂量≥ 25KGY
否
是
产品是否可以使用经过验证的稍低辐
射剂量灭菌(参见ISO11137)
是
采用另一种替代时间和温度条件下
标准周期干热灭菌达到SAL ≤10-6
采用最小辐射吸收最小剂量≥
25KGY进行辐射灭菌
否
处方是否可以通过微生物滞留过
滤器过滤
• 共识--无菌检查合格不能得出产品无菌的结论
灭菌产品的无菌保证不能依赖于最终产品的
无菌检验,而是取决于生产过程中采用合格的灭
菌工艺、严格的GMP管理和良好的无菌保证体系
灭菌工艺的验证是无菌保证的必要条件
灭菌工艺经过验证后,方可正式用于生产
附:无菌产品检测取样的时机和位置
注射剂除菌

表 1 防污染质量控制要点
工 质量控制点
质量控制项目
频次
序
洗瓶 隧道烘箱
温度
定时/
班
洗净后安瓿 清洁度
定时/
班
烘干后安瓿 清洁与干燥程度
定时/
班
配液 药液
澄明度、色泽、滤芯必须做起泡 每批
点试验
烘干后安瓿 清洁度
随时/
灌封
班
药液
色泽澄、明度
随时/
班
灌封后半成品 澄明度、药液装量
由于预真空法一次抽真空至-98.64 kPa(20 mmHg),对设备 密封要求高,且可产生“小装量效应”,而脉动真空法在一次抽
真空的预真空法基础上改为多次抽真空法,即灭菌时,先抽真空 至-95.98~93.31 kPa(40~60 mmHg),送入蒸汽将压力上升至 101 kPa,而后再抽气至负压状态,如此反复抽送 3~5 次,即可 相当于一次抽真空至-98.64 kPa 时空气的排除程度。虽然,脉 动真空法在抽真空上要多花一些时间,但负压较一次抽真空的预 真空法小,因而对真空泵和柜室的密封要求较低,且可防止“小 装量效应”的出现,效果更为可靠。为此,对蒸汽灭菌柜而言, 我国目前推广的主要是脉动真空式灭菌柜。 2.3.4 检漏灭菌柜
按《中国药典》
素
方法
微生物指 微生物≤100 CFU/100 按《中国药典》
标
ml
方法
澄明度 无可见异物
灯检法
内包装容 酸碱度 pH 5~7
pH 计(与注射
器清洗效
水对照)
果验证
细菌内毒 ≤0.25 EU/ml
按《中国药典》
素
方法
微生物指 微生物≤100 CFU/100 按《中国药典》
注射剂的灭菌与无菌技术.

注射剂的灭菌与无菌技术一、概述1.灭菌法:是指用热力或其他适宜方法将物质中的微生物杀灭或除去的方法。
灭菌是生产灭菌制剂的重要过程之一。
2.灭菌标准:微生物包括细菌(致病与非致病菌)、真菌、病毒,这些微生物无所不在,且繁殖速度惊人。
其中细菌的芽胞具有较强的抗热性,不易杀死,因此灭菌效果以杀死芽胞为灭菌标准。
3.注意区分灭菌、防腐、消毒、概念的区别。
(1)灭菌:是制用物理或化学方法将所有致病或非致病的微生物以及细菌的芽孢全部杀灭。
(2)防腐:是指用低温或化学药品防止和抑制微生物生长和繁殖。
(3)消毒:是指用物理和化学的方法将病原微生物杀死。
4.灭菌方法可分为:(1)物理法a.干热灭菌法c.射线灭菌法d.滤过灭菌法(2)化学灭菌法(环境灭菌)a.化学气体灭菌法b.化学药剂灭菌法(3)无菌操作法灭菌方法的选择:根据灭菌的要求及制剂的稳定性两个方面来选择。
二、物理灭菌法(一)湿热灭菌法本方法特点:由于蒸气潜热大,穿透力强,容易使蛋白质变性或凝固,灭菌效率高。
1.热压灭菌法:是用大于常压的饱和水蒸汽加热杀灭微生物的方法,是最可靠的灭菌方法。
(1)常用的几个压力与温度及时间的对应关系115℃~67 kpa~30min121℃~97 kpa~20min126℃~139 kpa~15min(2)灭菌设备-灭菌柜操作注意事项A.必须使用饱和蒸气B.必须将柜内空气排净C.压力回零后再开启柜门,防止带压操作D.防止过早全部开启柜门造成骤然降温,瓶子破裂(3)影响灭菌效果因素A.细菌的种类与数量B.药物性质与灭菌时间C.蒸气的性质D.介质的性质2.流通蒸气灭菌法:指在常压下100℃流通蒸汽加热杀灭微生物的方法。
杀灭时间为:30~60min。
特点:1)适用于对热不稳定的药品2)不能杀灭所有细菌3)需加入抑菌剂或避菌操作、无菌操作3.煮沸灭菌法:把灭菌物品放入沸水中加热灭菌的方法。
灭菌时间为:30~60min。
灭菌效果差。
4.低温间歇灭菌法:作法:a.温度60~80℃1hr灭菌b.室温或37℃下放置24hr,再进行上述条件下的灭菌c.反复操作3~5次(二)干热灭菌法干热灭菌法分为:火焰灭菌法、干热空气灭菌法※1.细菌对热敏感性:杀灭繁殖型细菌需100℃、干热1hr杀死;芽胞菌:按药典规定:160℃~170℃需2hr以上、170℃~180℃需1hr以上、250℃需45 min。
- 1、下载文档前请自行甄别文档内容的完整性,平台不提供额外的编辑、内容补充、找答案等附加服务。
- 2、"仅部分预览"的文档,不可在线预览部分如存在完整性等问题,可反馈申请退款(可完整预览的文档不适用该条件!)。
- 3、如文档侵犯您的权益,请联系客服反馈,我们会尽快为您处理(人工客服工作时间:9:00-18:30)。
孔径 0.22 μm;≥0.34
MPa
澄明度 部颁《澄明度检查细 灯检法
则及判断标准》
细菌内毒 ≤0.25 EU/ml
按《中国药典》
素
方法
微生物指 ≤100 CFU/100 ml 按《中国药典》
标
方法
残留清洁 pH 5~7
pH 计(与注射
容器管道 剂
水对照)
清洁验证 细菌内毒 ≤0.25 EU/ml
原料药是供生产无菌制剂的原料,对药品质量有着决定性的 影响,产品质量控制必须从源头抓起。 1.2 设备除菌灭菌方法选择、操作及质量要求
在生产前对触药设备和管道系统进行清洗和灭菌,并在生产 过程中保证其无菌性和不受微粒污染是关键。灭菌通常是用纯蒸 汽对设备及管道内部在线灭菌,再用福尔马林喷雾的方法与环境 一起进行外表消毒。有些设备无法用纯蒸汽在线灭菌,如开放式 离心机,则用喷雾消毒后以大量注射水淋洗后再用 70%乙醇或异 丙醇淋洗后干燥[4]。
验证
瓿内充惰性 残氧量
符合工艺要求
气体
热分布试验 最冷点与平均温度< 模拟生产状
热压蒸汽灭 热穿透试 2.5 ℃
态,温度记录
菌柜验证 验
生物指标剂 无菌保证值>6
用嗜热脂肪杆
试验菌芽孢无菌检查来自2.3 灭菌设备的选择 湿热灭菌指将物品放在灭菌器内,利用高压饱和蒸汽等手段
进行灭菌的方法。饱和蒸汽潜热大,穿透力强,容易使微生物蛋 白质变性凝固,其灭菌能力强,因此湿热灭菌是最有效及用途最 广的灭菌方法。注射剂制备中常用的湿热灭菌法包括热压灭菌和 流通蒸汽灭菌。各种微生物对湿热的抵抗力不同,细菌孢子较细 菌对湿热的耐受力更强。然而,在一个大气压下,水温最高只可 达 100 ℃,除非用很长时间,否则很难将细菌孢子杀灭。如欲 使湿热的温度提高到 100 ℃以上,则需采用热压方法。热压灭 菌的压力越高,所需时间越短。注射剂灭菌通常采用的灭菌条件 为 121 ℃×15 min 或 115 ℃×30 min。注射剂灭菌也可采用其 他温度和时间参数,但必须保证制剂灭菌后的 SAL≥10-6。
随时/
班
灭菌 灭菌柜
标记、装量、温度、时间、真空 每柜
度、记录
灭菌前后半成 外观清洁度、标记、存放区
每批
品
2.2 防污染验证要点[5]
防污染验证项目、控制标准及方法如表 2 所示。
表 2 防污染验证要点
类别
项目
控制标准
方法
滤器的完 孔径 0.45 μm;≥0.24 起泡点试验
药液过滤 整性
MPa
系统
最终灭菌大容量注射剂也称大输液或输液,指 50 ml 以上最 终灭菌注射剂,采用湿热灭菌法制备的灭菌注射剂。除一般理化 性质外,无菌、热原或细菌内毒素、澄明度、pH 值等项目检查 均应符合规定。此外,其所用原料、附加剂、溶剂应符合注射用 标准;在配制、灌装时严防微生物污染,已配制药液保证无菌热
原符合要求并在规定时间内灌装;pH 值需设定内控范围及调节 方法。其容器有瓶型或袋型两种,材质有玻璃、聚乙烯、聚丙烯、 聚氯乙烯或复合膜等。由于它通过静脉直接进入血液系统,故应 在生产全过程采取防止微粒、微生物、内毒素污染。相比较,玻 瓶为容器的灌封工艺,工艺流程长易造成污染的环节多,储运亦 不方便,而且,硬瓶输液还存在病房污染性空气回瓶,可能造成 微生物污染危险。所以,除某些药品不能用塑包外,西方最终灭 菌大容量注射剂大多采用塑瓶或塑袋包装。目前,国内玻瓶为包 装容器的比重正在大幅度降低,由原来的 90%降至 60%以下。而 塑袋(瓶)包装则上升至 40%左右并呈逐渐上升趋势。大输液是 我国包装形式和规格变化最大的一个剂型,在大规模 GMP 认证前 的 20 世纪 90 年代初,基本上仅有玻璃瓶一种形式,通过大规模 的 GMP 改造,国内一些经济上有实力的企业分别引进塑料瓶、塑 料袋生产线。按材质塑料瓶分为 PP 瓶、PE 瓶及不同硬度的硬塑 瓶和半硬瓶,而软袋又可分为非 PVC 和 PVC 及复合袋(三合一袋), 近几年来又有多室袋问世,其比例大体上呈玻瓶︰塑瓶︰塑袋=4 ︰4︰2 的发展趋势。而非 PVC 膜袋集中了输液包装材料的优点, 同时又避免回气对输液的二次污染。它唯一的缺点是价高,但随 着膜材的国产化,此缺点将被克服。所以,它是最有使用价值的 包装材料。
按《中国药典》
素
方法
微生物指 微生物≤100 CFU/100 按《中国药典》
标
ml
方法
澄明度 无可见异物
灯检法
内包装容 酸碱度 pH 5~7
pH 计(与注射
器清洗效
水对照)
果验证
细菌内毒 ≤0.25 EU/ml
按《中国药典》
素
方法
微生物指 微生物≤100 CFU/100 按《中国药典》
标
ml
方法
灌封系统 惰性气体 纯度含量 99.9%以上
传统的结晶器主体设备包括结晶罐、离心机、干燥器、过滤 器、灭菌设备、空气过滤设备、水处理系统,应定期对设备管道 系统及工器具进行清洗灭菌;为防止纯水、注射用水和药液染菌, 其储罐排气管道应设疏水性除菌过滤器。现在已经有集过滤、洗 涤、干燥为一体的“三合一”设备,无疑此设备使工序大大简化, 减少设备与操作的中间环节,也降低污染的几率。用于无菌原料 药干燥的设备一般喷雾干燥、冷冻干燥或“三合一”设备,产品 质量能得到保证。前两者要求干燥前的药液必须达到无菌、无热 原的质量要求,同时,还必须有确保后续工序不会造成新的微粒 及微生物的措施。在此,应该提醒注意的是药液及压缩空气、氮 气等工艺用气体的过滤精度与过滤程序,必须达到除菌的精度要 求(一般过滤粗滤→深层过滤→终端除菌,精度为 0.22~0.1 μm)。
此类药品主要指大小容量注射剂及其原料药,其药品可溶于 水或油性溶剂,在水中稳定,一般其热敏性较低,在灭菌温度下 成分不易分解。在制剂生产的规格上又分为大容量和小容量注射 剂,大容量则直接通过静脉滴注给药,而小容量则一般通过肌肉 注射给药。由于其给药方式产生的药效快、剂量准确,若药液质 量(尤其是染菌或热原超标)有问题,则其后果不堪设想,所以 必须把好生产中质量控制的每一个环节。 1.1 无菌原料药的精制
用于此类剂型的灭菌设备有传统的下排式、预真空式、脉冲 式蒸汽灭菌柜。 2.3.1 压力蒸汽灭菌柜特点
压力蒸汽灭菌柜柜室内原有冷空气,需要排净以免影响加热 效果。残存冷空气排除可分两种方法,预真空式和下排式,其区 别是将排除的方式由被动性改为主动性,即由被蒸汽从上至下靠 重力推出变为由真空泵抽出。预真空压力蒸汽灭菌柜操作方法分 为两类:一类是采用一次抽真空,将柜室内冷空气减少至规定要
指所有生产设备均已安装就绪,但未运行且没有操作人员在场状 态。“动态”是指生产设备按预定的工艺模式运行并有规定数量 的操作人员在现场操作的状态。无菌药品可分为最终灭菌和非最 终灭菌注射剂。所谓最终灭菌指大小容量注射剂,它可以通过灌 装后对其产品进行灭菌达到无菌要求。而非最终灭菌指粉针剂 (包括原料药)在精制过程中进行灭菌、除菌(包括除热原)和 在无菌的条件下进行干燥、包装及分装。 1 无菌药品
注射剂除菌、灭菌工艺及设备选择
关键词:注射剂;药品;无菌;除菌;灭菌;质量;过滤器; 灭菌柜;GMP
注射剂简称针剂,指用针头通过肌肉或血管给药的一种制剂, 包括灭菌或无菌的溶液、混悬液、乳浊液和临用前制备成溶液或 混悬液的无菌粉末。其特点是:药液注入后作用迅速、吸收快、 剂量准确、作用可靠;不经消化道避免被消化液破坏;适用于不 能吞咽或昏迷患者给药;可局部定位给药。由于通过注射给药, 所以质量要求特别高。故注射剂必须满足无菌、无热源、澄明度、 安全性、pH 值、渗透压、稳定性质量指标要求。注射剂按分散 系统可分为溶液型注射剂、注射用灭菌粉剂、混悬型注射剂和乳 浊型注射剂等 4 类[1]。
的洁净度要求,包括达到“静态”和“动态”的标准。GMP 认证
强力推动水针工艺技术的革新,其操作方式从手工间歇方式向连
续式洗灌封联动机组过渡,尤其通过引进、消化、吸收,我国水
针的工艺装备有了很大的改观。在生产过程中,质量控制要点除
满足原料药规定外,为保证无菌及热原应满足相应控制点与验证
要求。
2.1 防污染质量控制要点[5]
一般精制方法即将粗品溶于符合质量要求的定量溶剂(需经 除菌过滤)内在规定的温度下进行脱色除热原,经脱色过滤的滤 液再在精制区经预过滤器及密闭管道系统和终端除菌后进入结 晶罐(或中间罐)进行重结晶,晶体溶液经“三合一”过滤得成 品。而用于喷干或冷干的饱和滤液则经中间罐再经除菌过滤方可 进入喷(冷)干设备。
防污染质量控制点及控制项目如表 1 所示。
表 1 防污染质量控制要点
工 质量控制点
质量控制项目
频次
序
洗瓶 隧道烘箱
温度
定时/
班
洗净后安瓿 清洁度
定时/
班
烘干后安瓿 清洁与干燥程度
定时/
班
配液 药液
澄明度、色泽、滤芯必须做起泡 每批
点试验
烘干后安瓿 清洁度
随时/
灌封
班
药液
色泽澄、明度
随时/
班
灌封后半成品 澄明度、药液装量
适用范围:(1)适用范围与下排气式蒸汽灭菌柜基本相同,只 是由于所抽负压较强,可使敞口瓶内所装液体溢出,故不得用于 敞口瓶装液体的灭菌;(2)由于采用强制式抽真空且负压较强, 排除冷空气能力更强、排除冷空气更彻底,因而比下排气式灭菌 柜更适于织物类物品的消毒灭菌。 2.3.3 脉动真空式蒸汽灭菌柜的基本特点
过滤除菌是原料药无菌化的最主要手段,因此对过滤除菌工 艺验证十分重要。首先验证所使用的过滤器及其管道系统是否符 合设计要求,滤过的产品能否达到质量指标,最主要是无菌性、 内毒素或热原低于限定水平。其内容:过滤系统对所滤溶液的适 应性、滤材对溶液的污染程度、整个过滤系统的规格、过滤系统 的完整性试验、除菌效果、被过滤药液的含菌量控制及过滤时间 限定、滤器的使用寿命。对于过滤器的灭菌要求应注意允许的最 高灭菌温度、最长累积灭菌时间、安装方法和流体的流动方向。 2 最终灭菌小容量注射剂