化学选矿之影响还原焙烧的因素
贵州清镇赤铁矿磁化焙烧工艺效果的影响因素
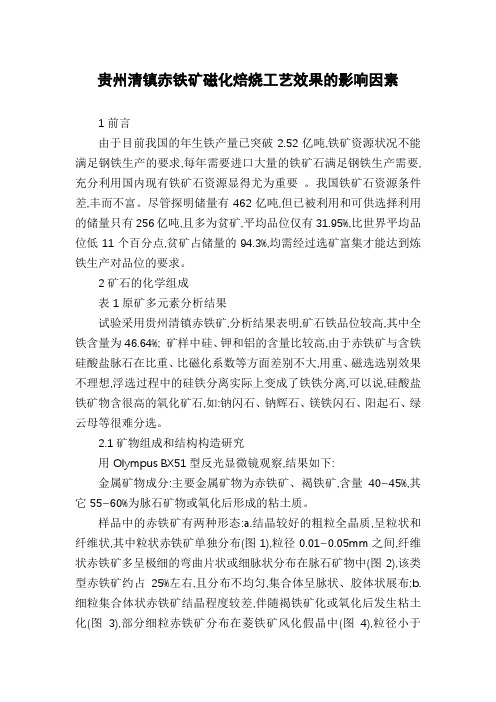
贵州清镇赤铁矿磁化焙烧工艺效果的影响因素1前言由于目前我国的年生铁产量已突破2.52亿吨,铁矿资源状况不能满足钢铁生产的要求,每年需要进口大量的铁矿石满足钢铁生产需要,充分利用国内现有铁矿石资源显得尤为重要。
我国铁矿石资源条件差,丰而不富。
尽管探明储量有462亿吨,但已被利用和可供选择利用的储量只有256亿吨,且多为贫矿,平均品位仅有31.95%,比世界平均品位低11个百分点,贫矿占储量的94.3%,均需经过选矿富集才能达到炼铁生产对品位的要求。
2矿石的化学组成表1原矿多元素分析结果试验采用贵州清镇赤铁矿,分析结果表明,矿石铁品位较高,其中全铁含量为46.64%; 矿样中硅、钾和铝的含量比较高,由于赤铁矿与含铁硅酸盐脉石在比重、比磁化系数等方面差别不大,用重、磁选选别效果不理想,浮选过程中的硅铁分离实际上变成了铁铁分离,可以说,硅酸盐铁矿物含很高的氧化矿石,如:钠闪石、钠辉石、镁铁闪石、阳起石、绿云母等很难分选。
2.1矿物组成和结构构造研究用Olympus BX51型反光显微镜观察,结果如下:金属矿物成分:主要金属矿物为赤铁矿、褐铁矿,含量40~45%,其它55~60%为脉石矿物或氧化后形成的粘土质。
样品中的赤铁矿有两种形态:a.结晶较好的粗粒全晶质,呈粒状和纤维状,其中粒状赤铁矿单独分布(图1),粒径0.01~0.05mm之间,纤维状赤铁矿多呈极细的弯曲片状或细脉状分布在脉石矿物中(图2),该类型赤铁矿约占25%左右,且分布不均匀,集合体呈脉状、胶体状展布;b.细粒集合体状赤铁矿结晶程度较差,伴随褐铁矿化或氧化后发生粘土化(图3),部分细粒赤铁矿分布在菱铁矿风化假晶中(图4),粒径小于0.001mm,含量15~20%。
褐铁矿多与细粒赤铁矿关系密切,隐晶质。
脉石矿物多为黑云母、磷灰石和绿泥石等。
组构特征:致密块状、胶状构造;他形粒状结构、片状、纤维状结构等。
赤铁矿外的硅酸盐矿物以细粒黑云母为主,多呈团状集合体(图5),或呈星点状与赤铁矿伴生,含量低于3%。
1 矿物原料的焙烧

1 矿物原料的焙烧1.1焙烧的理论基础焙烧:在适宜的气氛和低于矿物原料熔点的温度条件下,使矿物原料中的目的组分矿物发生物理和化学变化的工艺过程。
一般作为选矿的准备工作。
焙烧过程发生在固气界面的多相化学反应,遵循热力学和质量作用定律。
∆G=∆G0 +RT lnQ=-RT lnK+RT lnQ焙烧是多相化学反应,扩散吸附和化学反应低温:以化学反应为主高温:总反应决定扩散速度,温度影响小了——内扩散与外扩散——层流与紊流总结:影响焙烧的主要因素为1.气相中反应气体的浓度2.气流的运动特性(层流与紊流)3.温度及物料的物理及化学性质1.2 氧化焙烧与硫酸化焙烧硫化矿在氧化气氛条件下加热,将全部硫脱除转变为金属氧化物的过程是氧化焙烧如果只是将部分硫脱出,生成硫酸盐则为硫酸化焙烧这时的反应方向与SO2 SO3 O2的分压有关。
氧化焙烧多用脱硫率或目的组分的硫酸化程度来衡量。
1.3 还原焙烧还原焙烧是在低于炉料熔点和还原气氛条件下,使矿石中的金属氧化物转变为相应低价金属氧化物或金属的过程。
直接还原:使用C进行还原。
间接还原:使用CO进行还原。
实例:1.弱磁性贫铁矿石的还原磁化焙烧赤铁矿和褐铁矿黄铁矿(Fe2O3,FeCO3,FeS2)2.铁粒法用劣质原料处理不适于高炉炼铁的高硅贫铁矿和矿粉的方法。
品位在25-50%。
磁选或重选后品位可达95%,3.含镍红土矿的还原焙烧世界上最大的氧化矿资源,直接酸浸需要高温高压,多用还原焙烧-低压氨浸1.4 氯化焙烧在一定温度和气氛条件下,用氯化剂使矿物原料中的目的组分转为气相或凝聚相的氯化物,以使目的组分分离富集的工艺过程。
中温氯化焙烧——氯化物固态——浸出高温氯化焙烧——氯化物气态——挥发离析:挥发的同时又使金属氯化物还原呈金属态析出——物理选矿方法再选氧化氯化焙烧还原氯化焙烧。
焙烧试验2

(四)投笼
投笼要分批进行,每批可相隔2小时左右,一般笼子在炉内留时间约 6~9小时,投笼后5小时就要做好收笼准备。投笼地点在炉顶装料口处。
(五)收笼
收笼地点在炉下两侧搬出机上,投笼5小时后,派专人在搬出机处值 班,每班需2~3人。值班人员对于收笼要特别注意,以避免丢失,已经 破裂的笼子亦需拣出,核对投笼和收笼数量。冬季搬出周围水汽弥漫, 观察矿笼不便,可用管引煤气点燃,以驱散水汽。 (六)试验记录 出炉的每个笼子均需贴上标签,注明出炉时间,以便检查不同焙烧 时间的焙烧矿质量。
也就是说理论上焙烧矿还原度为42.8%时 质量最佳。如R值大于42.8%,说明矿石过还 原,小于42.8%则欠还原。无论是过还原还是 欠还原,矿石的磁性均降低。 据实践得知,不同类型和不同粒度的矿 石,其最佳还原度并不一致。如对于鞍山赤 铁石英岩的焙烧,当矿石粒度为75%~10毫米 时,还原度达52%左右时选别效果较好。
在焙烧试验时,尚需注意以下事项:
1、焙烧矿样必须放在炉内高温带; 2、热电偶插放位置要恰当,不能太深,也不 能太浅; 3、经常检查瓷管,如坏了漏气,必须马上更 换; 4、如矿样含结晶水高,应先预热,去掉水份, 并使物料较疏松有利于还原。
四、实验室还原焙烧试验结果应用于工业生 产的有关问 题
1、试验室焙烧试验结果,可以说明这种铁矿石磁化焙 烧的可能性及指标,所得到的适宜焙烧条件,可供工业焙 烧炉设计参考。 2、影响磁化焙烧的因素很多,只能抓住温度和时间、 矿石粒度、热工制度等,小型试验与大型试验就有很大差 距,在试验室条件下,只能抓住温度和时间、还原剂种类 和用量这几个主要矛盾进行试验。试验室焙烧试验结束后, 必须进行扩大试验,将来生产上用什么样炉型结构,扩大试验 就在什么样炉型结构上进行。
矿物原料焙烧原理及方法
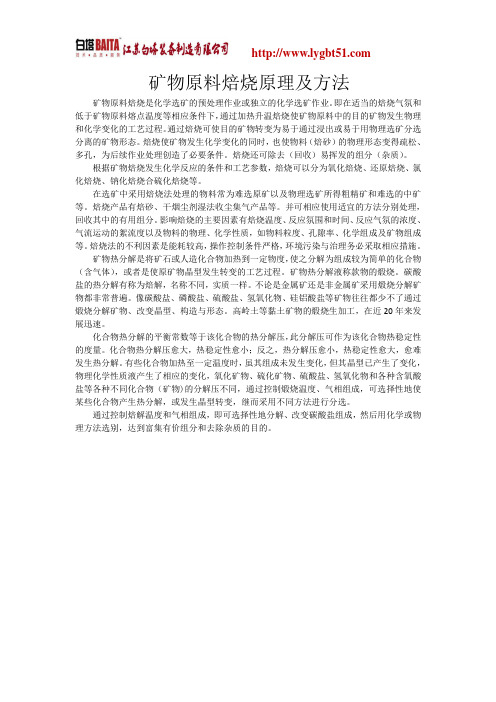
矿物原料焙烧原理及方法矿物原料焙烧是化学选矿的预处理作业或独立的化学选矿作业。
即在适当的焙烧气氛和低于矿物原料熔点温度等相应条件下,通过加热升温焙烧使矿物原料中的目的矿物发生物理和化学变化的工艺过程。
通过焙烧可使目的矿物转变为易于通过浸出或易于用物理选矿分选分离的矿物形态。
焙烧使矿物发生化学变化的同时,也使物料(焙砂)的物理形态变得疏松、多孔,为后续作业处理创造了必要条件。
焙烧还可除去(回收)易挥发的组分(杂质)。
根据矿物焙烧发生化学反应的条件和工艺参数,焙烧可以分为氧化焙烧、还原焙烧、氯化焙烧、钠化焙烧合硫化焙烧等。
在选矿中采用焙烧法处理的物料常为难选原矿以及物理选矿所得粗精矿和难选的中矿等。
焙烧产品有焙砂、干烟尘剂湿法收尘集气产品等。
并可相应使用适宜的方法分别处理,回收其中的有用组分。
影响焙烧的主要因素有焙烧温度、反应氛围和时间、反应气氛的浓度、气流运动的絮流度以及物料的物理、化学性质,如物料粒度、孔隙率、化学组成及矿物组成等。
焙烧法的不利因素是能耗较高,操作控制条件严格,环境污染与治理务必采取相应措施。
矿物热分解是将矿石或人造化合物加热到一定物度,使之分解为组成较为简单的化合物(含气体),或者是使原矿物晶型发生转变的工艺过程。
矿物热分解液称款物的煅烧。
碳酸盐的热分解有称为焙解,名称不同,实质一样。
不论是金属矿还是非金属矿采用煅烧分解矿物都非常普遍。
像碳酸盐、磷酸盐、硫酸盐、氢氧化物、硅铝酸盐等矿物往往都少不了通过煅烧分解矿物、改变晶型、构造与形态。
高岭土等黏土矿物的煅烧生加工,在近20年来发展迅速。
化合物热分解的平衡常数等于该化合物的热分解压,此分解压可作为该化合物热稳定性的度量。
化合物热分解压愈大,热稳定性愈小;反之,热分解压愈小,热稳定性愈大,愈难发生热分解。
有些化合物加热至一定温度时,虽其组成未发生变化,但其晶型已产生了变化,物理化学性质液产生了相应的变化,氧化矿物、硫化矿物、硫酸盐、氢氧化物和各种含氧酸盐等各种不同化合物(矿物)的分解压不同,通过控制煅烧温度、气相组成,可选择性地使某些化合物产生热分解,或发生晶型转变,继而采用不同方法进行分选。
化学选矿考试重点

1、资源加工学是由传统的选矿学、矿物加工学发展演变形成的。
传统选矿学、矿物加工学均以天然矿物资源为主;资源加工学包括一切资源(如二次资源)2、选矿学是用物理化学方法,对天然矿物资源(金属矿物、非金属矿物、煤炭等)进行选别、分离、富集其中的有用矿物的科学技术,其目的是为冶金化工等行业提供合格原料。
矿物加工学是在选矿学的基础上发展起来的,是用物化方法对天然矿物资源进行加工,以获得有用物质的科学技术,目的也可最直接获得金属、矿物材料。
3、化学分选是基于物料组分的化学性质的差异,利用化学方法改变物料性质组成,然后用其他的方法使目的组分富集的资源加工工艺。
包括化学浸出与化学分离两个过程。
4、化学分选与物理分选的区别与联系:联系-都是用来处理矿物原料并使目的组分得到富集、分离,其目的是综合利用矿产资源。
区别:物理分选成本低,化学分选成本较高;物理分选处理物料粒度相对较粗的矿物,化学分选处理物料粒度范围较物理分选更宽、更广;化学分选可以处理品位低、嵌布粒度细、矿物组成复杂的矿石,而物理分选方法不能;化学分选可以从“三废”中回收有用组分,能最大限度地综合回收原料中的有价成分。
5、化学分选过程准备作业:包括对物料的破碎与筛分、磨矿与分级及配料混匀等机械加工过程。
(2)焙烧作业:其目的是为了改变矿石的化学组成或除去有害杂质,使目的组分转变为容易浸出或有利于物理分选的形态,为下一作业准备条件。
(3)浸出作业:这一作业是根据原料性质和工艺要求,使有组分或杂质组分选择性溶于浸出溶剂中,从而使有用组分与杂质相分离,或者使不同有用组分之间相分离。
(4)固—液分离作业:一般采用沉降、过滤和分级等方法处理浸出料浆,以得到下一作业处理的澄清溶液和浸渣。
(5)净化与富集作业:为了得到高品位的化学精矿,浸出液常用化学沉淀法、离子交换法或溶剂萃取法等进行净化分离,以除去杂质,同时得到有用组分含量较高的净化溶液。
(6)制取化合物或金属作业:一般可采用离子沉淀法、金属置换法、电积法、炭吸附法、离子交换或溶剂萃取法。
铬铁矿的还原焙烧过程

铬铁矿的还原焙烧过程铬铁矿的还原焙烧过程1、焙烧温度对铬铁矿还原焙烧效果的影响图1铬铁矿经不同温度下焙烧120min后所得产物的SEM图像图1为铬铁矿在不同焙烧温度下还原120min后产物表观形貌的SEM图像。
从图中可以看出,当焙烧温度为950℃时,矿石颗粒表面存在明暗不同两相,但相互分离并不彻底,相界面难以辨别。
温度为1050℃时,明亮物相与相对较暗物相己能够明显分辨,且较950℃时体积有所增大。
当温度升至1150℃时,明亮物相由球状发展为棒条状。
通过EDS检测可知,明亮物相为还原析出相,其主要成分为金属铁、金属铬和少量的碳,较暗物相为铬铁矿基体相。
不考虑各析出相中的碳元素,排除相分离尚不充分的950℃还原产物,可将其他试样析出相中铁和铬的比例关系绘如图2。
由图2可知,在1050℃和1100℃时,析出相中主要成分为铁元素,而当温度升至1150℃时,铬元素成为析出相的主体元素。
由此可以得出在950-1100℃的范围内主要发生的是铬铁矿中铁的还原,铬仍存在于矿石基体中。
当焙烧温度达到如1150℃时,大量的铬被还原为金属态进入析出相,证明在此温度下部分含铬尖晶石相参与了还原反应。
实验所得结论与热力学分析结果一致。
图2 不同焙烧温度下还原120min后析出相金属元素组成图3为Factsage软件计算得出的1100℃和1150℃下Cr-Fe-C-O系优势区域图。
在1100℃时,常压线(由“+”组成)穿过了优势区域图中的灰色区域()和浅灰色区域(),意味着从热力学角度讲,当石墨增锅内气压为1 atm时Cr2O3和Fe(或Fe3C)可以作为还原产物共存。
当温度为1150℃时,常压线穿过了深灰色区域(Cr3C2+Fe),说明在此温度下铬会被大量还原为金属态,并以碳化物的形式存在。
此时,选择性还原铬铁矿中铁元素的目标难以实现。
另外,从图中还可得出,当体系中二氧化碳分压很低时(如反应的初始阶段Cr3C2会与Fe3C共存于析出相。
化学选矿复习题
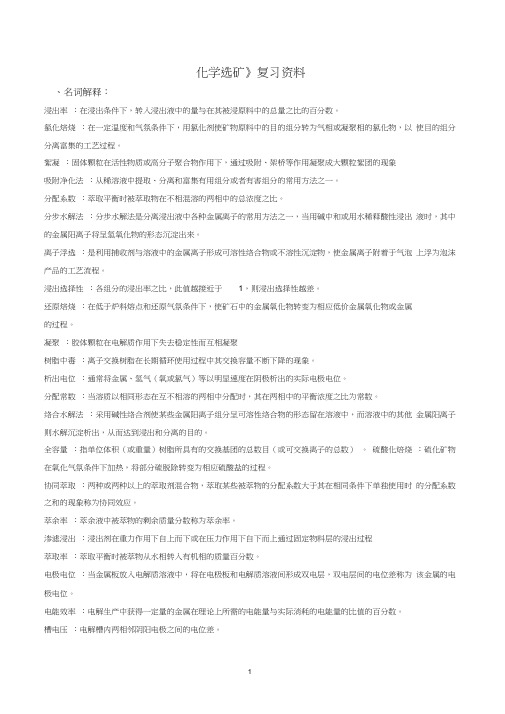
化学选矿》复习资料、名词解释:浸出率:在浸出条件下,转入浸出液中的量与在其被浸原料中的总量之比的百分数。
氯化焙烧:在一定温度和气氛条件下,用氯化剂使矿物原料中的目的组分转为气相或凝聚相的氯化物,以使目的组分分离富集的工艺过程。
絮凝:固体颗粒在活性物质或高分子聚合物作用下,通过吸附、架桥等作用凝聚成大颗粒絮团的现象吸附净化法:从稀溶液中提取、分离和富集有用组分或者有害组分的常用方法之一。
分配系数:萃取平衡时被萃取物在不相混溶的两相中的总浓度之比。
分步水解法:分步水解法是分离浸出液中各种金属离子的常用方法之一,当用碱中和或用水稀释酸性浸出液时,其中的金属阳离子将呈氢氧化物的形态沉淀出来。
离子浮选:是利用捕收剂与溶液中的金属离子形成可溶性络合物或不溶性沉淀物,使金属离子附着于气泡上浮为泡沫产品的工艺流程。
浸出选择性:各组分的浸出率之比,此值越接近于1,则浸出选择性越差。
还原焙烧:在低于炉料熔点和还原气氛条件下,使矿石中的金属氧化物转变为相应低价金属氧化物或金属的过程。
凝聚:胶体颗粒在电解质作用下失去稳定性而互相凝聚树脂中毒:离子交换树脂在长期循环使用过程中其交换容量不断下降的现象。
析出电位:通常将金属、氢气(氧或氯气)等以明显速度在阴极析出的实际电极电位。
分配常数:当溶质以相同形态在互不相溶的两相中分配时,其在两相中的平衡浓度之比为常数。
络合水解法:采用碱性络合剂使某些金属阳离子组分呈可溶性络合物的形态留在溶液中,而溶液中的其他金属阳离子则水解沉淀析出,从而达到浸出和分离的目的。
全容量:指单位体积(或重量)树脂所具有的交换基团的总数目(或可交换离子的总数)。
硫酸化焙烧:硫化矿物在氧化气氛条件下加热,将部分硫脱除转变为相应硫酸盐的过程。
协同萃取:两种或两种以上的萃取剂混合物,萃取某些被萃物的分配系数大于其在相同条件下单独使用时的分配系数之和的现象称为协同效应。
萃余率:萃余液中被萃物的剩余质量分数称为萃余率。
选矿工艺之磁化焙烧
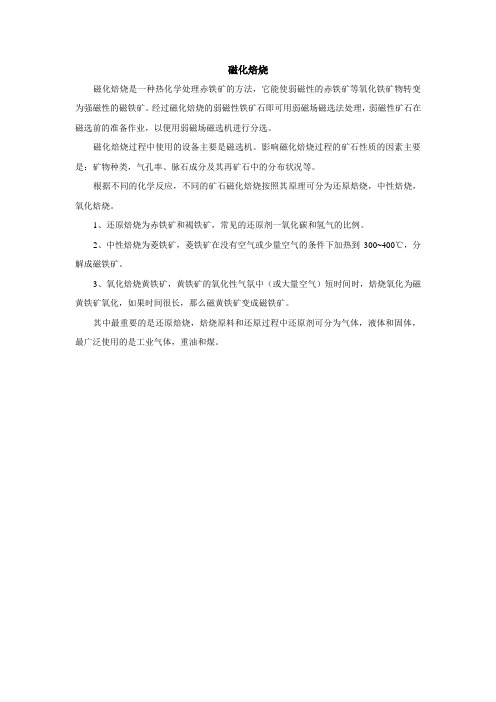
磁化焙烧
磁化焙烧是一种热化学处理赤铁矿的方法,它能使弱磁性的赤铁矿等氧化铁矿物转变为强磁性的磁铁矿。
经过磁化焙烧的弱磁性铁矿石即可用弱磁场磁选法处理,弱磁性矿石在磁选前的准备作业,以便用弱磁场磁选机进行分选。
磁化焙烧过程中使用的设备主要是磁选机。
影响磁化焙烧过程的矿石性质的因素主要是:矿物种类,气孔率、脉石成分及其再矿石中的分布状况等。
根据不同的化学反应,不同的矿石磁化焙烧按照其原理可分为还原焙烧,中性焙烧,氧化焙烧。
1、还原焙烧为赤铁矿和褐铁矿,常见的还原剂一氧化碳和氢气的比例。
2、中性焙烧为菱铁矿,菱铁矿在没有空气或少量空气的条件下加热到300~400℃,分解成磁铁矿。
3、氧化焙烧黄铁矿,黄铁矿的氧化性气氛中(或大量空气)短时间时,焙烧氧化为磁黄铁矿氧化,如果时间很长,那么磁黄铁矿变成磁铁矿。
其中最重要的是还原焙烧,焙烧原料和还原过程中还原剂可分为气体,液体和固体,最广泛使用的是工业气体,重油和煤。
还原焙烧
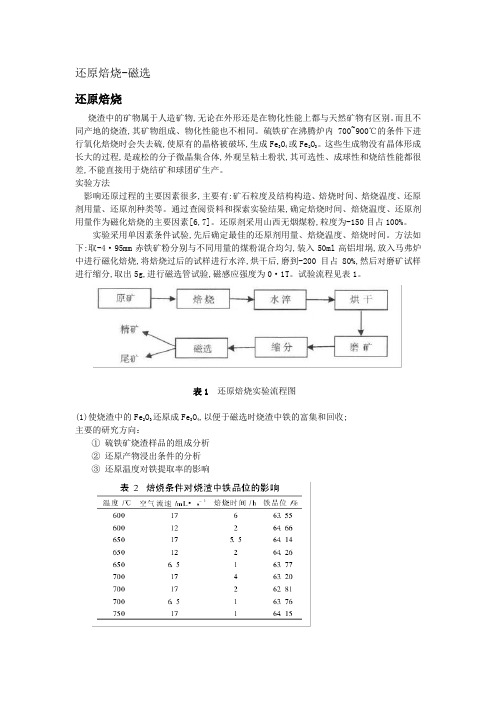
还原焙烧-磁选还原焙烧烧渣中的矿物属于人造矿物,无论在外形还是在物化性能上都与天然矿物有区别。
而且不同产地的烧渣,其矿物组成、物化性能也不相同。
硫铁矿在沸腾炉内700~900℃的条件下进行氧化焙烧时会失去硫,使原有的晶格被破坏,生成Fe3O4或Fe2O3。
这些生成物没有晶体形成长大的过程,是疏松的分子微晶集合体,外观呈粘土粉状,其可选性、成球性和烧结性能都很差,不能直接用于烧结矿和球团矿生产。
实验方法影响还原过程的主要因素很多,主要有:矿石粒度及结构构造、焙烧时间、焙烧温度、还原剂用量、还原剂种类等。
通过查阅资料和探索实验结果,确定焙烧时间、焙烧温度、还原剂用量作为磁化焙烧的主要因素[6,7]。
还原剂采用山西无烟煤粉,粒度为-150目占100%。
实验采用单因素条件试验,先后确定最佳的还原剂用量、焙烧温度、焙烧时间。
方法如下:取-4·95mm赤铁矿粉分别与不同用量的煤粉混合均匀,装入50ml高铝坩埚,放入马弗炉中进行磁化焙烧,将焙烧过后的试样进行水淬,烘干后,磨到-200目占80%,然后对磨矿试样进行缩分,取出5g,进行磁选管试验,磁感应强度为0·1T。
试验流程见表1。
表1还原焙烧实验流程图(1)使烧渣中的Fe2O3还原成Fe3O4,以便于磁选时烧渣中铁的富集和回收;主要的研究方向:①硫铁矿烧渣样品的组成分析②还原产物浸出条件的分析③还原温度对铁提取率的影响④还原时间对铁提取率的影响⑤还原剂用量对铁提取率的影响(2)通过焙烧使烧渣中的锌、铅、锑、铟的氧化物还原成单质并挥发,以利于回收;(3)通过焙烧改善烧渣中铁矿物的结晶度、成球性和烧结性,以利于磁选和烧结矿、球团矿生产;(4)降低烧渣中的硫含量,满足炼铁原料的要求。
磁选不同磁场强度实验为了考察磁场强度对回收率和品位的影响,进行了不同磁场强度试验。
由刘丽娜,李萌,牛福生,赵礼兵几人所做的实验结果(见表)可知,随着磁场强度由64kA/m增加到120kA/m,精矿品位也由原来的63·02%降低到60·13%,而回收率却不断提高。
焙烧

多相反应的动力学:多相反应及其步骤
• 在多于一相之间发生的反应称为多相反应。 虽然反应体系中可能存在着更多的相,但实 际上只可能有两个相参加反应
其理由在于反应过程的总速度只被其中某些反应步骤的速度所决定(即速度控制 步骤)。如金的氰化反应过程是在固体金、NaCN溶液和氧气三相之间发生的, 但氧由气相转入液相的速度很快,所以可简化成固-液反应。多相反应可分为五 类:固-气(与焙烧过程直接相关的多相反应)、固-液、固-固、液-气、 液-液。
还原焙烧
还原焙烧是在低于炉料熔点和还原气氛条件下,使矿石中的金属氧化物转 变为相应低价金属氧化物或金属的过程。
除了汞和银的氧化物在低于400℃温度条件下于空气中加热可分解析出金属外, 绝大多数金属氧化物不能用热分解的方法还原,只能采用添加还原剂的方法将其 还原,其中最常用的是CO、氢气和固体碳. 金属氧化物的还原可用下式表示:
化学热力学指出了一个解决化学反应方向问题的方法,同 16:29 时也表明了化学反应等温式的重要性。
6
2. Roasting:焙烧过程的理论基础
• 焙烧过程动力学:在给定的焙烧条件下,若ΔG<0,只能说明焙烧反
应可能发生,但反应实际进行的速度如何,热力学并不能回答,而是属于化 学动力学的研究范畴 。
即PO2(RO)< PO2(MO)
因此凡是对氧的亲和力比被还原的金属对氧 的亲和力大的物质均可作为该金属氧化物的 还原剂
16:29
16
Reduction methods for producing some common metals.
• Note: • In general, the ease of reducing an ore to the free metal increases from left to right of the periodic table.
化学选矿

1.化学选矿:所谓化学选矿是基于矿物组分的化学性质的差异,利用化学方法改变矿物的性质,使目标组分或杂质组分选择性地溶于浸出溶剂中,从而达到分离的目的。
化学选矿广泛地用于处理各种难选的黑色金属、有色金属、贵金属和非金属矿产资源的开发。
2.化学选矿与物理选矿的区别重选、浮选、磁选、电选等都是在没有改变矿物化学组成的情况下进行的。
化学选矿改变矿物化学组成的情况下进行的。
化学选矿需要消耗大量的化学试剂。
3.化学选矿的主要过程:答法:①原料准备阶段→物料分解阶段→产品的制取阶段②焙烧→浸出→固液分离→净液→产品制取固液分离采用沉降倾析、过滤和分级等方法处理浸出矿浆,以便获得供后续作业处理的澄清液或固体物料。
机械:浓缩机(池)、过(压)滤机、离心机、水力旋流器。
1. 焙烧是在适宜的气氛和低于物料熔点的温度条件下,使矿物原料中的目的组分矿物发生物理和化学变化的工艺过程。
该过程通常是作为选矿准备作业,以使目的组分转变为易浸出或易于物理分选的形态。
2. 根据焙烧在化学选矿过程中的作用和其主要化学反应性质可分为:还原焙烧;氧化焙烧;氯化焙烧;氯化离析;加盐焙烧;煅烧。
3. 还原焙烧金属氧化物矿石等在还原剂作用下的焙烧。
目的在于将物料还原为较低价的氧化物或金属,以便于分离和富集,如镍矿石还原成金属后利于浸出;贫赤铁矿还原为磁铁矿石可以磁选富集。
5. 氧化焙烧利用空气中氧与硫化矿作用,将金属硫化物在空气中焙烧成金属氧化物或硫酸盐,或将低价氧化物转变为高价氧化物,有时还可脱去挥发性物质,如砷、锑、硒等。
铜的硫酸化焙烧应该温度低于650℃,氧化焙烧要高于650 ℃。
氧化焙烧温度应高于相应硫化物的着火温度,而硫化物的着火温度与其粒度有关。
实践中焙烧温度常常波动于580~850℃,一般不超过900 ℃6氯化焙烧:在氯化剂存在的条件下,焙烧矿石、精矿、冶金过程的中间产品,使其中某些金属氧化物、硫化物转化为氯化物的过程。
7. 煅烧在低于熔点的适当温度下,加热物料,使其分解并除去所含结晶水、二氧化碳或三氧化硫等挥发性物质的过程称为煅烧。
钼精矿氧化焙烧影响因素浅析

8 . 7
2 . 1 4
条件 :试验在 1 . 2 m× 2 4 m 的回转窑 中进行 ,台效 6 t / d 采 用螺旋 给料机均匀给料 ,空气流量的改变通过风机转速来实现 。
反 应 速度 加 快 , 对整 个 焙 烧 有 利 , 且 台效 可 以适 当
对 钼 精矿 加工 指标 也会 有一 定影 响 。对 杂质特 别是
剧烈反应 区长 , 烧结 区含硫 高 ,物料烧结 剧烈反应区长 ,烧结区含硫较高 ,物料烧结 剧烈反应 区较合 适 ,烧结区含硫较合理 ,物料无 明显烧结 剧 烈反 应区合适 ,烧结区含硫合理 ,物料无烧结
2 . 6 3 . 1 3 . 9 4 . 8 6 . 5
9 1 . 2 9 2 . 6
9 5 . 9
1 . 6 9
1 . 5 8 1 . 6 3 1 . 6 1 1 . 8 9
9 6 . 1 9 6_ 2
9 6 . 3
4 0 剧烈反应区较短, 烧结区含硫较低 , 物料无烧结 , 燃油消耗较大 , 钼挥发率较高
4 5
剧烈反应 区短 , 烧 结区含硫低 ,物料无烧结 ,燃油消耗大 ,钼挥发率 高
从 动 力学 角度 考虑 ,随着温 度 的升高 ,分 子运 动 和扩散 速度 将显 著提 高 ,分子 间 的相互 碰撞 的机
少 氧 时 ,M o O 3 与M o S 2 反应 生成 褐色 M o O 2 ,
6 Mo O 3 + M0 S 2 = 7 MO O2 + 2 S O2
率也随之增加 ,反应速度加快 ,且铼的挥发率也随 着温度的升高而增大。资料表 明,辉钼矿在 4 0 0  ̄ C 左右会生成致密 的保护膜 ,反应主要受该膜扩散 控制 ,在 5 5 0 — 6 0 0 ℃时生成物疏松多孔 ,附着在物
CaO在红土镍矿直接还原焙烧中的作用机理
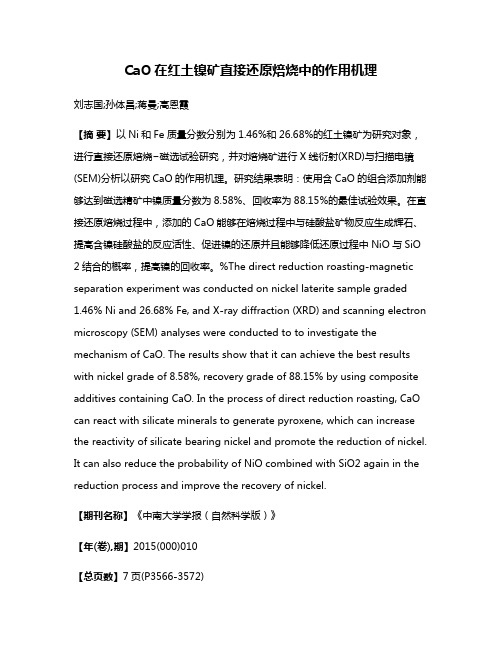
CaO在红土镍矿直接还原焙烧中的作用机理刘志国;孙体昌;蒋曼;高恩霞【摘要】以Ni和Fe质量分数分别为1.46%和26.68%的红土镍矿为研究对象,进行直接还原焙烧−磁选试验研究,并对焙烧矿进行X线衍射(XRD)与扫描电镜(SEM)分析以研究CaO的作用机理。
研究结果表明:使用含CaO的组合添加剂能够达到磁选精矿中镍质量分数为8.58%、回收率为88.15%的最佳试验效果。
在直接还原焙烧过程中,添加的CaO能够在焙烧过程中与硅酸盐矿物反应生成辉石、提高含镍硅酸盐的反应活性、促进镍的还原并且能够降低还原过程中NiO与SiO 2结合的概率,提高镍的回收率。
%The direct reduction roasting-magnetic separation experiment was conducted on nickel laterite sample graded 1.46% Ni and 26.68% Fe, and X-ray diffraction (XRD) and scanning electron microscopy (SEM) analyses were conducted to to investigate the mechanism of CaO. The results show that it can achieve the best results with nickel grade of 8.58%, recovery grade of 88.15% by using composite additives containing CaO. In the process of direct reduction roasting, CaO can react with silicate minerals to generate pyroxene, which can increase the reactivity of silicate bearing nickel and promote the reduction of nickel. It can also reduce the probability of NiO combined with SiO2 again in the reduction process and improve the recovery of nickel.【期刊名称】《中南大学学报(自然科学版)》【年(卷),期】2015(000)010【总页数】7页(P3566-3572)【关键词】红土镍矿;直接还原;CaO;磁选;硅酸盐【作者】刘志国;孙体昌;蒋曼;高恩霞【作者单位】北京科技大学土木与环境工程学院,北京,100083;北京科技大学土木与环境工程学院,北京,100083;山东理工大学资源与环境工程学院,山东淄博,255049;北京科技大学土木与环境工程学院,北京,100083【正文语种】中文【中图分类】TD95;TF556镍资源按地质成因主要划分为2类:岩浆型硫化镍矿床和风化型红土镍矿床。
还原焙烧处理铁矿石原理及方法

书山有路勤为径,学海无涯苦作舟还原焙烧处理铁矿石原理及方法
还原焙烧赤铁矿、褐铁矿和铁锰矿石在加热到一定温牙后,与适量的还
原剂相作用,就可使弱磁性的赤铁矿转变为强磁性的磁铁矿(Fe3O4)。
常用的
还原剂有C、CO 和H2 等。
赤铁矿(Fe2O3)与还原剂作用的反应如下:
3 Fe2O3+C2 Fe3O4+CO
3 Fe2O3+CO2 Fe3O4+CO2
3 Fe2O3+H22 Fe3O4+ H2O
褐角矿(2 Fe2O3-H2O)在加热到一定温度后开始脱水,变成赤铁矿石,按
上述反应被还原成磁铁矿。
还原焙烧程度一般用还原度表地:
R=FeO/Fe 乘以100%
式中FeO 还原焙烧矿中FeO 的含量,%;
Fe 还原焙烧矿中全铁的含量,%。
若赤铁矿全部还原成磁铁矿时,还原程度最佳,磁性最强,此时还原度R=
42.8%。
tips:感谢大家的阅读,本文由我司收集整编。
仅供参阅!。
还原焙烧

还原焙烧目录编辑本段还原焙烧是在低于炉料熔点和还原气氛条件下,使矿石中的金属氧化物转变为相应低价金属氧化物或金属的过程。
金属氧化物的还原可用下式表示:MO+R=M+RO 式中MO——金属氧化物;R,RO——还原剂和还原剂氧化物。
凡是对氧的化学亲合力比被还原的金属对氧的亲合力大的物质均可作为该金属氧化物的还原剂。
在较高的温度下,碳可以作为许多金属氧化物的还原剂,生产中常用的还原剂为固体炭、一氧化碳气体和氢气。
[1]编辑本段应用还原焙烧目前主要用于处理难选的铁、锰、镍、铜、锡、锑等矿物原料。
此外还用于精矿除杂质,粗精矿精选。
编辑本段举例含镍红土矿的还原焙烧含镍红土矿是世界上最大的氧化镍矿资源,因其品位低,镍呈化学浸染状存在,目前无法用物理选矿富集。
用还原焙烧-低压氨浸的方法回收其中的镍已得到工业应用。
预先将氧化镍还原为活性金属镍、钴镍合金,然后氨浸回收镍。
常用气体还原剂(含CO-CO2、H2-H2O)的混合气体进行选择性还原焙烧,其主要反应为:NiO+H2O=Ni+H2ONiO+CO=Ni+CO2CoO+H2=Co+H2OCoO+CO=Co+CO23Fe2O3+H2=2Fe3O4+H2O3Fe2O3+CO=2Fe3O4+CO2Fe3O4+H2=3FeO+H2OFe3O4+CO=3FeO+CO2FeO+H2=Fe+H2OFeO+CO=Fe+CO2H2O+CO=H2+CO2CO2+C=2CO若控制气相组成CO2/CO大于2。
53或H2O/H2大于2。
45时,镍钴氧化物可优先还原为金属镍、钴;氧化铁大部分被还原为磁铁矿而不生成金属铁。
但是由于矿石中金属氧化物的结合状态较复杂及为提高反应速度,上述气相组成比值应小些。
当控制气相组成在CO2:CO=1:1时,难免会生成少量氧化亚铁和金属铁。
还原焙烧含镍红土矿,国外一般多采用多层焙烧炉,也可采用回转窑。
化学选矿焙烧
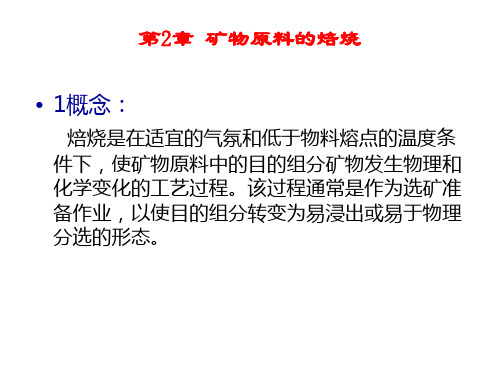
ZnS 2O 2 ZnSO 4
3ZnSO
4
200 3ZnO
2SO
3
SO
2
1 2
O2
3ZnO 2 SO 3 700 3ZnO 2SO 2 O 2
着火温度550度,生成硫酸锌和氧化锌薄层致密,较难氧化。
1.1 氧化焙烧与硫酸化焙烧
1.1.4 铅硫化物
焙烧过程方铅矿的反应:
PbS
3 2
• 化学热力学
• 化学热力学
• 化学动力学
3 焙烧理论
• 3影响焙烧反应速度的主要因素:
气体中反应气体的浓度; 气流的运动特性; 温度; 物料的物理和化学性质 (如粒度,空隙度,化学组成及矿物组成等)
第2章 矿物原料的焙烧
4 分类:根据焙烧的气氛条件及过程中目的组分发生 的主要化学变化,可将焙烧过程大致分为: 氧化焙烧与硫酸焙烧 还原焙烧 氯化焙烧与氯化离析 钠盐焙烧 煅烧
4CuO 1000 2Cu 2 O O 2
SO
2
1 2
O2
650
SO
3
CuO SO 3 650 CuSO 4
1.1 氧化焙烧与硫酸化焙烧
1.1.2 铜的硫化物
当有硫化物存在时,反应生成的硫酸铜会在很低的温 度下进行相互反应而分解,见下式。
因此,铜的硫酸化焙烧应该温度低于650℃ ,氧化焙 烧要高于650 ℃ 。
600-800 ℃时,最后三个反应进行甚为完全。
1.1 氧化焙烧与硫酸化焙烧
1.1.2 铜的硫化物
焙烧过程铜的硫化物的反应:
2CuFeS 2 550 CuS 2 2FeS S
2CuS 400 CuS 2 S
2Cu 2S 5O 2 200 ~ 300 CuO 2CuSO 4
还原焙烧

书山有路勤为径,学海无涯苦作舟
还原焙烧
还原焙烧是在低于炉料熔点和还原气氛条件下,使矿石中的金属氧化物转变为相应低价金属氧化物或金属的过程。
金属氧化物的还原可用以下式表示:式中M()金属氧化物;R,RO 还原剂和还原剂氧化物。
凡是对氧的化学亲和力比被还原的金属对氧的亲和力大的物质均可作为该金属氧化物的还原剂。
在较高的温度下,碳可以作为许多金属氧化物的还原剂,生产中常用的还原剂为固体炭、一氧化碳气体和氢气。
还原焙烧目前主要用于处理难选的铁、锰、镍、铜、锡、锑等矿物原料,此外还用于精矿除杂质,粗精矿精选。
例如,含镍红土矿是世界上最大的氧化镍矿资源,因其品位低,镍呈化学浸染状存在,目前无法用物理选矿富集,用还原焙烧-低压氨浸的方法回收其中的镍已得到工业应用。
预先将氧化镍还原为活性金属镍、钴镍合金,然后氨浸回收镍。
常用气体还原剂(含CO-CO2、H2-H2O)的混合气体进行选择性还原焙烧,其主要反应为:
若控制气相组成CO2/CO 大于2.53 或H2O/H2 大于2.45 时,镍钴氧化物可优先还原为金属镍、钴;氧化大部分被还原为磁铁矿而不生成金属铁。
但是由于矿石中金属氧化物的结合状态较复杂及为提高反应速度,上述气相组成比值应小些。
当控制气相组成在CO2:CO=1:1,难免会生成少量氧化亚铁和金属铁。
还原焙烧含镍红土矿,国外一般多采用多层焙烧炉,也可采用回转窑。
1、简易探索选矿试验实用于购买矿权之前,满足投资分析,降低投资风险初步价值评定。
化学选矿复习资料

重点归纳:1 化学分选: 基于物料组分的化学性质的差异,利用化学方法改变物料性质组成,然后用其他的方法使目的组分富集的资源加工工艺。
(它包括化学浸出与化学分离两个主要过程)2 焙烧是在适宜的气氛和低于物料熔点的温度条件下,使矿物原料中的目的组分矿物发生物理和化学变化的工艺过程。
该过程通常是作为选矿准备作业,以使目的组分转变为易浸出或易于物理分选的形态。
3 影响焙烧反应速度的主要因素:气体中反应气体的浓度;气流的运动特性;温度;物料的物理和化学性质(如粒度,空隙度,化学组成及矿物组成等)4可将焙烧过程大致分为:氧化焙烧与硫酸焙烧还原焙烧氯化焙烧与氯化离析钠盐焙烧煅烧5 氧化焙烧:硫化矿在氧化气氛条件下加热,将全部(或部分)硫脱除转变为相应的金属氧化物(或硫酸盐)的过程,称为氧化焙烧(或硫酸化焙烧)。
6在焙烧条件下,硫化矿转变为金属氧化物和金属硫酸盐的反应可表示为:2MS+2O2=2MO+2SO2⑴2SO2+O22SO3⑵MO+SO3 2MSO4⑶反应⑴是不可逆的,而⑵,⑶是可逆的。
反应的平衡常数为:在一定温度下,硫化矿氧化焙烧产物取决于气相组成和金属硫化物、氧化物及金属硫酸盐的离解压。
焙烧产物为金属硫酸盐,过程属硫酸化焙烧焙烧产物为金属氧化物,过程属氧化焙烧7 铜的硫酸化焙烧应该温度低于650℃,氧化焙烧要高于650 ℃; 锌的着火温度550度,生成硫酸锌和氧化锌薄层致密,较难氧化。
焙砂中铅主要呈氧化铅形态存在。
方铅矿的焙烧宜在低温下进行。
砷常呈毒砂(FeAsS )和雌黄(As 2S 3)。
As 2O 3易挥发,120℃时挥发已显著,部分在氧气剂的作用下可转变为发挥性小的As 2O 5,升高温度和增大空气过剩量将促进的氧化砷生成。
生成的氧化砷将与金属氧化物(PbO\CuO\FeO 等)作用生成砷酸盐。
氧化焙烧时通常难予将砷全部除去。
银的硫化物(Ag 2S):焙烧产物灰银矿、金属银和硫酸银 金(Cu):不发生变化锑化合物(Sb 2S 3、脆硫锑铅矿Pb 2Sb 2S 3):同砷相似镉化合物(CdS):氧化镉和硫酸镉,高温时挥发富集与烟尘中 铊和铟 :800-1000 ℃时以氧化态挥发。
还原焙烧定义

还原焙烧定义一、引言焙烧是一种将原料加热以改变其物理或化学性质的过程。
这个过程可以应用于很多不同的领域,例如食品加工、陶瓷制造和金属冶炼等。
在这篇文章中,我们将重点讨论还原焙烧。
二、还原焙烧的定义还原焙烧是指在缺氧或低氧气氛下进行的加热处理。
在这种条件下,原料中的氧化物会被还原成金属或其他还原产物。
这个过程通常需要一个还原剂来提供电子以减少氧化物。
三、还原剂还原剂是一种能够提供电子以减少其他化合物的物质。
在还原焙烧中,常用的还原剂包括碳和碳化合物、氢和水蒸汽、金属粉末等。
四、应用领域1. 金属冶炼:在冶金工业中,还原焙烧可以用来从氧化物中提取金属。
例如,在铁冶炼中,铁矿经过高温下的还原焙烧后可以得到纯铁。
2. 陶瓷制造:在陶瓷制造中,还原焙烧可以用来改变陶瓷的颜色和纹理。
例如,在制作青花瓷时,青花釉需要经过还原焙烧才能得到特殊的蓝色。
3. 食品加工:在食品加工中,还原焙烧可以用来改变食品的香味和口感。
例如,在咖啡豆的加工中,还原焙烧可以使咖啡豆产生特殊的焦香味。
五、还原焙烧的步骤1. 准备原料:选择适当的还原剂和氧化物,并将它们混合在一起。
2. 加热:将混合物放入加热设备中,提高温度以进行还原焙烧。
3. 控制气氛:控制气氛以保证缺氧或低氧环境。
4. 冷却:冷却混合物以停止反应。
六、影响还原焙烧效果的因素1. 温度:温度越高,反应速率越快。
2. 还原剂和氧化物比例:比例不合适会影响反应效果。
3. 气氛控制:气氛不合适会影响反应效果。
4. 反应时间:时间过短会导致反应不完全。
七、结论还原焙烧是一种重要的加热处理方式,它可以在很多领域中得到应用。
在进行还原焙烧时,需要选择适当的还原剂和氧化物,并控制好温度和气氛等因素。
这样才能得到理想的反应效果。
矿石特性对还原焙烧的影响

书山有路勤为径,学海无涯苦作舟矿石特性对还原焙烧的影响矿石特性主要指矿石的物质组成、矿石的粒度组成和脉石矿物的成分,叙述如下:1、矿石的物质组成对还原焙烧的影响。
这里所说的矿石物质组成,主要指矿物的种类和结构状态等。
进行还原焙烧的矿物主要有赤铁矿、褐铁矿和菱铁矿等,含赤铁矿的矿石,由于其结构不同,还原性能也有很大的差别。
例如石英质磁铁矿,有些呈层状结构,在加热过程中赤铁矿和石英,由于膨胀变化不同而出现裂缝。
这有利于还原剂分子的扩散,提高矿石的还原速度和焙烧矿的质量。
矿石结构呈致密块状,和结核状的,还原性能较差。
对褐铁矿来说由于褐铁矿分子中含有10%-15%或更多的结晶水,当温度到达100℃时,结晶水开始挥发,从而增加了矿石的气孔率,有利于提高还原速度。
菱铁矿加热到350℃之后,开始分解出大量的CO 和CO2 气体,这样一方面增加了矿石的气孔率,另一方面分解出的CO 又增加了反应中还原剂的浓度,有利于还原过程的进行。
2、矿石的粒度组成对还原焙烧的影响,矿石的粒度愈大,比表面及也就愈小,与还原剂接触表面就少,还原过程就比较慢,生产中常有矿块表层和内部还原不均匀的现象。
矿石粒度愈大这种现象就愈严重。
矿块的还原不均匀性又和还原温度,还原事件有着密切的关系,矿块粒度愈大,还原温度愈高,还原时间愈长,这种不均匀性愈显著。
为了改善焙烧质量,应降低入炉矿块的粒度上限,提高粒度下限(粒度过小,料层透气性差)。
对竖炉来说,焙烧粒度范围为75~20mm 是比较合适的。
此外竖炉装料时应防止矿石产生偏析,使矿石粒度盐炉体分布均匀,以便得到较好的焙烧质量。
3、脉石矿物的成分对还原焙烧的影响,以石英为主要脉石的铁矿物,在焙。
- 1、下载文档前请自行甄别文档内容的完整性,平台不提供额外的编辑、内容补充、找答案等附加服务。
- 2、"仅部分预览"的文档,不可在线预览部分如存在完整性等问题,可反馈申请退款(可完整预览的文档不适用该条件!)。
- 3、如文档侵犯您的权益,请联系客服反馈,我们会尽快为您处理(人工客服工作时间:9:00-18:30)。
书山有路勤为径,学海无涯苦作舟
化学选矿之影响还原焙烧的因素
影响还原焙烧的因素较多,归纳起来主要包括以下几个方面的因素:
(1)矿石性质。
矿石性质主要是指矿物种类、脉石成分及结构状态。
这些性质决定了矿石被还原的难易程度。
一般而言,具有层状结构的矿石要比致密状、绍状及结核状易于还原。
脉石成分以石英为主的矿石,因受热后石英产生晶型转变,体积膨胀而导致矿石的爆裂,增大了矿石的有效反应面积,从而有利于还原反应进行。
(2)矿石的粒度及粒度组成。
矿石粒度的大小及其分布对还原过程的主要影响是矿石还原的均匀性。
当其他条件不变时,小块矿石比大块矿石先完成还原过程;对于大块矿石来说,表层比中心部位先完成还原过程。
因此,为了改善矿石在还原过程中的均匀性,必须降低人炉矿石粒度上限,提高粒度下限。
据我国生产实践的经验,认为粒度在20 一75 mm 比较合适。
(3)焙烧温度和气相成分的影响。
矿石只有在一定的焙烧温度和气相成分的条件下才能完成还原反应,下面以弱磁性贫铁矿石的磁化焙烧为例进行说明。
在实践中贫赤铁矿磁化焙烧温库下限是450`C,上限700 一800%。
炉内还原气体的成分应选定P(C02)/V(CO)比值不小于1.
温度过高时,会导致弱磁性的富氏体(FeO 溶于Fe3O,中的低熔点熔体)和硅酸铁(Fee SiO4 )的生成。
因为无论是高温造成的炉料软化或是过还原生成的硅酸铁熔体,都会钻附在炉壁或附属装丑上,影响炉料正常运行。
若温度过低时,如在250 一300℃以下,虽然赤铁矿也可以被还原成磁铁矿,且不会产生过还原现象。
但是,还原反应的速度很慢,而且低温生成的Fe3O4 磁性较弱,所以生产上是不能采用低温磁化焙烧的。
各种矿石的适宜还原温度及气相成分,由于矿石性质、加热方式及还原剂的种类不同而有较大变化,应通过试验最后确。