铸件磁粉检测缺陷分析及预防
铸件磁粉检验中常见的伪缺陷磁痕
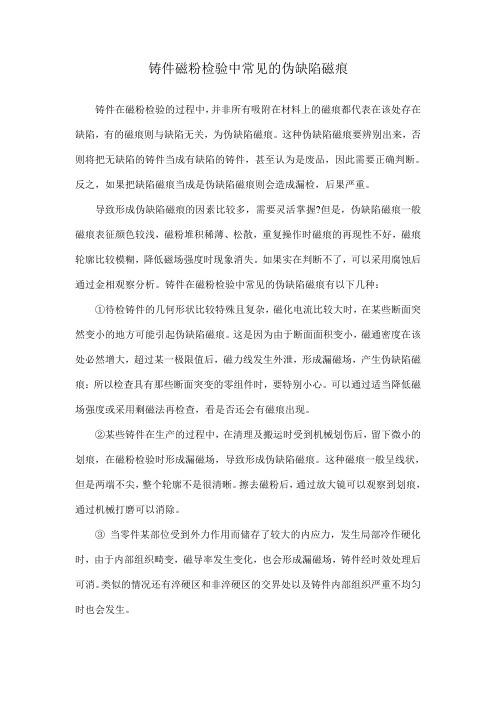
铸件磁粉检验中常见的伪缺陷磁痕铸件在磁粉检验的过程中,并非所有吸附在材料上的磁痕都代表在该处存在缺陷,有的磁痕则与缺陷无关,为伪缺陷磁痕。
这种伪缺陷磁痕要辨别出来,否则将把无缺陷的铸件当成有缺陷的铸件,甚至认为是废品,因此需要正确判断。
反之,如果把缺陷磁痕当成是伪缺陷磁痕则会造成漏检,后果严重。
导致形成伪缺陷磁痕的因素比较多,需要灵活掌握?但是,伪缺陷磁痕一般磁痕表征颜色较浅,磁粉堆积稀薄、松散,重复操作时磁痕的再现性不好,磁痕轮廓比较模糊,降低磁场强度时现象消失。
如果实在判断不了,可以采用腐蚀后通过金相观察分析。
铸件在磁粉检验中常见的伪缺陷磁痕有以下几种:①待检铸件的几何形状比较特殊且复杂,磁化电流比较大时,在某些断面突然变小的地方可能引起伪缺陷磁痕。
这是因为由于断面面积变小,磁通密度在该处必然增大,超过某一极限值后,磁力线发生外泄,形成漏磁场,产生伪缺陷磁痕:所以检查具有那些断面突变的零组件时,要特别小心。
可以通过适当降低磁场强度或采用剩磁法再检查,看是否还会有磁痕出现。
②某些铸件在生产的过程中,在清理及搬运时受到机械划伤后,留下微小的划痕,在磁粉检验时形成漏磁场,导致形成伪缺陷磁痕。
这种磁痕一般呈线状,但是两端不尖,整个轮廓不是很清晰。
擦去磁粉后,通过放大镜可以观察到划痕,通过机械打磨可以消除。
③当零件某部位受到外力作用而储存了较大的内应力,发生局部冷作硬化时,由于内部组织畸变,磁导率发生变化,也会形成漏磁场,铸件经时效处理后可消。
类似的情况还有淬硬区和非淬硬区的交界处以及铸件内部组织严重不均匀时也会发生。
④磁悬液中如果磁粉含量过高,磁粉流动性不好,铸件表面的微凹或锈蚀部位可能会引起伪缺陷磁痕。
铸件缺陷分析PPT课件

铸件在凝固末期或刚凝固 后不久产生的裂纹。
03
铸件缺陷形成原因及机理分析
原材料因素
原材料质量
使用不合格或质量差的原材料, 如废钢、生铁等,其中含有的杂 质元素和气体可能导致铸件缺陷 。
原材料配比
原材料配比不合理,如碳、硅等 元素含量过高或过低,会影响铸 件的凝固过程和机械性能。
熔炼工艺因素
熔炼温度
介绍了常用的铸件缺陷检测与评估方法,如目视检查、无损检测、 金相分析等,以及各种方法的优缺点和适用范围。
缺陷预防与控制措施
重点讲解了铸件缺陷的预防和控制措施,包括优化铸造工艺、提高原 材料质量、加强过程监控等方面。
学员心得体会分享
知识收获
学员们表示通过本次课程,对铸件缺陷的类型、成因、检 测与评估方法有了更深入的了解,对铸件质量控制的重要 性有了更深刻的认识。
其他可能影响因素
生产环境
生产环境中的温度、湿度和清洁度等因素对铸件质量也有一 定影响。例如,湿度过高可能导致型砂粘结力下降,温度过 高则可能导致铁液冷却速度过快。
操作技能
操作工人的技能水平和经验对铸件质量也有重要影响。例如 ,合箱时定位不准确、浇注时铁液温度控制不当等都可能导 致铸件缺陷。
04
铸件缺陷预防措施与改进方法
控制熔炼温度
根据原材料成分和熔炼设备特点, 合理设置熔炼温度,避免过高或 过低的熔炼温度对铸件质量产生 不良影响。
调整化学成分
通过添加合金元素和调整废钢、生 铁等原材料的配比,控制铁水的化 学成分,提高铸件的力学性能和耐 蚀性。
减少熔炼杂质
采取过滤、除渣等措施,减少熔炼 过程中产生的氧化物、硫化物等杂 质,提高铁水的纯净度。
夹渣和夹杂物
01属夹杂物,夹杂 物则是金属或非金属杂质。
铸件常见缺陷的产生原因及防止方法
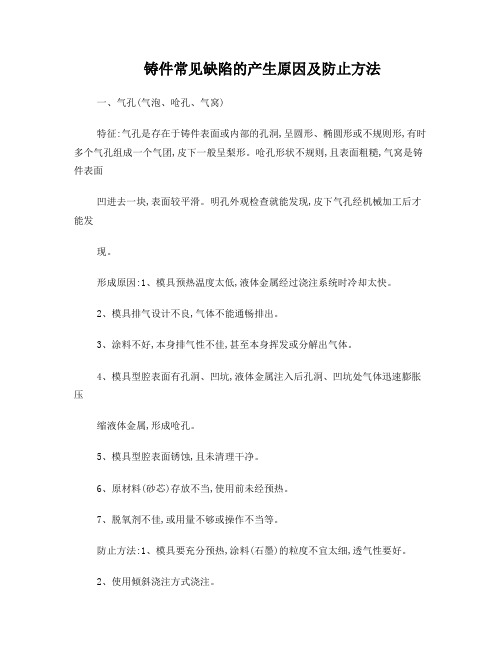
铸件常见缺陷的产生原因及防止方法一、气孔(气泡、呛孔、气窝)特征:气孔是存在于铸件表面或内部的孔洞,呈圆形、椭圆形或不规则形,有时多个气孔组成一个气团,皮下一般呈梨形。
呛孔形状不规则,且表面粗糙,气窝是铸件表面凹进去一块,表面较平滑。
明孔外观检查就能发现,皮下气孔经机械加工后才能发现。
形成原因:1、模具预热温度太低,液体金属经过浇注系统时冷却太快。
2、模具排气设计不良,气体不能通畅排出。
3、涂料不好,本身排气性不佳,甚至本身挥发或分解出气体。
4、模具型腔表面有孔洞、凹坑,液体金属注入后孔洞、凹坑处气体迅速膨胀压缩液体金属,形成呛孔。
5、模具型腔表面锈蚀,且未清理干净。
6、原材料(砂芯)存放不当,使用前未经预热。
7、脱氧剂不佳,或用量不够或操作不当等。
防止方法:1、模具要充分预热,涂料(石墨)的粒度不宜太细,透气性要好。
2、使用倾斜浇注方式浇注。
3、原材料应存放在通风干燥处,使用时要预热。
4、选择脱氧效果较好的脱氧剂(镁)。
5、浇注温度不宜过高。
二、缩孔(缩松)特征:缩孔是铸件表面或内部存在的一种表面粗糙的孔,轻微缩孔是许多分散的小缩孔,即缩松,缩孔或缩松处晶粒粗大。
常发生在铸件内浇道附近、冒口根部、厚大部位,壁的厚薄转接处及具有大平面的厚薄处。
形成原因:1、模具工作温度控制未达到定向凝固要求。
2、涂料选择不当,不同部位涂料层厚度控制不好。
3、铸件在模具中的位置设计不当。
4、浇冒口设计未能达到起充分补缩的作用。
5、浇注温度过低或过高。
防治方法:1、提高磨具温度。
2、调整涂料层厚度,涂料喷洒要均匀,涂料脱落而补涂时不可形成局部涂料堆积现象。
3、对模具进行局部加热或用绝热材料局部保温。
4、热节处镶铜块,对局部进行激冷。
5、模具上设计散热片,或通过水等加速局部地区冷却速度,或在模具外喷水,喷雾。
6、用可拆缷激冷块,轮流安放在型腔内,避免连续生产时激冷块本身冷却不充分。
7、模具冒口上设计加压装置。
8、浇注系统设计要准确,选择适宜的浇注温度。
磁粉检测技术及缺陷分析
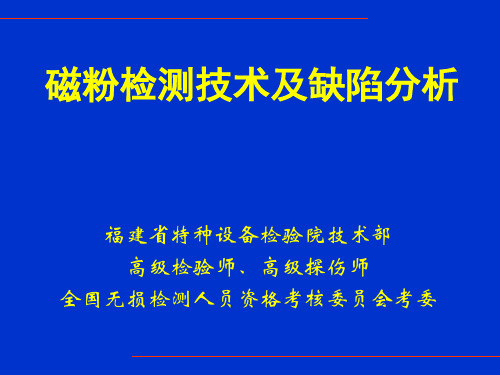
α的大a小rcta反n(B映/H)铁磁性材料被磁化 的难易程度。
铁磁性材料特性:
(1)高导磁性——能在外加磁场中强烈的磁化, 产生非常强的附加磁场,其磁导率很高,相对磁 导率可达数百甚至数千。
(2)磁饱和性——铁磁性材料由于磁化所产生的 附加磁场,不会随外加磁场增加而无限地增加, 当外加磁场达到一定程度后,全部磁畴的方向都 与外加磁场的方向一致,磁感应强度B不再增加 ,呈现饱和。
S C' Hm H
磁滞:在同样的磁场强度H下,退磁 时的磁感应强度比磁化时的磁感应强
R' Bm
S'
度大,这种B的变化落后于H变化的
现象,叫做磁滞现象。
造成磁滞的主要原因是,铁磁质中的掺杂和内应力 在退磁过程中阻碍磁畴恢复到原来的状态。
• 饱和磁感应强度± B m ,表示工件在 饱和磁场强度± 磁H m化下B达到饱 和,不再随H的增大而增大,对应 的磁畴全部转向与磁场方向一致。
从居里温度以上的高温冷却 下来,只要没有外磁场的影响, 材料仍处于退磁状态。
材料 纯铁 硅钢(热轧) 硅钢(冷轧) 45坡莫合金 78坡莫合金 超坡莫合金 铁氧体
Tc/℃ 770 690 700 440 580 400 100-600
部分铁磁性材料的居里点
磁化过程
1、未加外加磁场时,磁畴磁矩杂乱无章,对外不显磁性,如图a; 2、在较小磁场作用下,磁矩方向与外磁场方向一致或相近的磁畴
大小:典型磁畴体积约为10-3mm3 ,在这个小区域内,含有 大约 1012~1015个原子,各原子的磁化方向一致,对外呈 现磁性。
• 特点:1、在没有外加磁场作用时,铁磁材料内各磁畴的 磁矩方向互相抵消,对外不显示磁性,如图(a)所示。
常见铸造缺陷产生的原因及防止方法

常见铸造缺陷产生的原因及防止方法铸件缺陷种类繁多,产生缺陷的原因也十分复杂.它不仅与铸型工艺有关,而且还与铸造合金的性制、合金的熔炼、造型材料的性能等一系列因素有关.因此,分析铸件缺陷产生的原因时,要从具体情况出发,根据缺陷的特征、位置、采用的工艺和所用型砂等因素,进行综合分析,然后采取相应的技术措施,防止和消除缺陷.一、浇不到1、特征铸件局部有残缺、常出现在薄壁部位、离浇道最远部位或铸件上部.残缺的边角圆滑光亮不粘砂.2、产生原因1 浇注温度低、浇注速度太慢或断续浇注;2 横浇道、内浇道截面积小;3 铁水成分中碳、硅含量过低;4 型砂中水分、煤粉含量过多,发气量大,或含泥量太高,透气性不良;5 上砂型高度不够,铁水压力不足.3、防止方法1 提高浇注温度、加快浇注速度,防止断续浇注;2 加大横浇道和内浇道的截面积;3 调整炉后配料,适当提高碳、硅含量;4 铸型中加强排气,减少型砂中的煤粉,有机物加入量;5 增加上砂箱高度.二、未浇满1、特征铸件上部残缺,直浇道中铁水的水平面与铸件的铁水水平面相平,边部略呈圆形.2、产生原因1 浇包中铁水量不够;2 浇道狭小,浇注速度又过快,当铁水从浇口杯外溢时,操作者误认为铸型已经充满,停浇过早.3、防止方法1 正确估计浇包中的铁水量;2 对浇道狭小的铸型,适当放慢浇注速度,保证铸型充满.三、损伤1、特征铸件损伤断缺.2、产生原因1 铸件落砂过于剧烈,或在搬运过程中铸件受到冲撞而损坏;2 滚筒清理时,铸件装料不当,铸件的薄弱部分在翻滚时被碰断;3 冒口、冒口颈截面尺寸过大;冒口颈没有做出敲断面凹槽.或敲除浇冒口的方法不正确,使铸件本体损伤缺肉.3、防止方法1 铸件在落砂清理和搬运时,注意避免各种形式的过度冲撞、振击,避免不合理的丢放;2 滚筒清理时严格按工艺规程和要求进行操作;3 修改冒口和冒口颈尺寸,做出冒口颈敲断面,正确掌握打浇冒口的方向.四、粘砂和表面粗糙1、特征粘砂是一种铸件表面缺陷,表现为铸件表面粘附着难以清除的砂粒;如铸件经清除砂粒后出现凹凸不平的不光滑表面,称表面粗糙.2、产生原因1 砂粒太粗、砂型紧实度不够;2 型砂中水分太高,使型砂不易紧实;3 浇注速度太快、压力过大、温度过高;4 型砂中煤粉太少;5 模板烘温过高,导致表面型砂干枯;或模板烘温过低,型砂粘附在模板上.3、防止方法1 在透气性足够的情况下,使用较细原砂,并适当提高型砂紧实度;2 保证型砂中稳定的有效煤粉含量;3 严格控制砂水分;4 改进浇注系统,改进浇注操作、降低浇注温度;5 控制模板烘烤温度,一般与型砂温度相等或略高.五、砂眼1、特征在铸件内部或表面充塞有型砂的孔眼.2、产生原因1 型砂表面强度不够;2 模样上无圆角或拔模斜度小导致钩砂、铸型损坏后没修理或没修理好就合箱;3 砂型在浇注前放置时间过长,风干后表面强度降低;4 铸型在合箱时或搬运过程中损坏;5 合箱时型内浮砂未清除干净,合箱后浇口杯没盖好,碎砂掉进铸型.3、防止方法1 提高型砂中粘士含量、及时补加新砂,提高型砂表面强度;2 模样光洁度要高,并合理做出拔模斜度和铸造圆角.损坏的铸型要修好后再合箱;3 缩短浇注前砂型的放置时间;4 合箱或搬运铸型时要小心,避免损坏或掉入砂型腔砂粒;5 合箱前清除型内浮砂,并盖好浇口.六、披缝和胀砂1、特征披缝常出现在铸件分型面处,是垂直于铸件表面,且厚薄不均匀的薄片状金属突起物. 胀砂是铸件内、外表面局部胀大,形成不规则的瘤状金属突起物.2、产生原因1 紧实度不够或不匀;2 面砂强度不够、或型砂水分过高;3 液态金属压头过大、浇注速度太快.3、防止方法1 提高铸型紧实度、避免局部过松;2 调整混砂工艺、控制水分,提高型砂强度;3 降低液态金属的压头、降低浇注速度.七、抬箱1、特征铸件在分型面处有大面积的披缝,使铸型外形尺寸发生变化.抬箱过大,造成跑火——铁水自分型面外溢,严重时造成浇不足缺陷.2、产生原因1 砂箱未紧固、压铁质量不够或去除压铁过早;2 浇注过快,冲击力过大;3 模板翅曲.3、防止方法1 增加压铁重量,特铁水凝固后再去除压铁;2 降低浇包位置,降低浇注速度;3 修正模板.八、掉砂1、特征铸件表面上出现的块状金属突起物,其外形与掉落的砂块很相似.在铸件其它部位,则往往出现砂眼或残缺.2、产生原因1 模样上有深而小的凹槽,同于结构特征或拔模斜度小,起模时将砂型带坏或震裂;2 紧实度不匀,铸型局部强度不足;3 合箱、搬运铸型时,不小心使铸型局部砂块掉落.3、防止方法1 模样拔模斜度要合适、表面光洁;2 铸型紧实度高且均匀;3 合箱、搬运过程中,操作小心.九、错型错箱1、特征铸件的一部分与另一部分在分型面的接缝处错开,发生相对位移,使铸件外形与图纸不相符合.2、产生原因1 模样制作不良,上下模没有对准或模样变形;2 砂箱或模板定位不准确,或定位销松动;3 挤压造型机上零件磨损,例如正压板下衬板、反压板轴承的磨损等;4 浇注时用的套箱变形,搬运、围箱时不注意,使上下铸型发生位移.3、防止方法1 加强模板的检查和修理;定2 经常检查砂箱、模板的定位销及销孔、并合理地安装;3 检查挤压造型机的有关零件,及时调整,磨损大的要更换;4 定期对套箱整形.脱箱后的铸型在搬运时要小心.在面浇注的砂型,应该做一排砂型围一排.十、灰口和麻点1、特征铸件断口呈灰黑色或出现黑色小点,中心部位较多,边部较少,金相观察可见到片状石墨.2、产生原因1 铁水化学成分不合要求,碳、硅含量过高;2 炉前孕育的铋加入浇包内过早或过迟,或是铋量不足.3、防止方法1 正确选择化学成分,合理配料,使铁水中碳、硅量在规定范围内;2 增加铋的加入量并严格炉前孕育工艺.十一、裂纹热裂、冷裂1、特征铸件外部或内部有穿透或不穿透的裂纹.热裂时带有暗色或黑色的氧化表面断口外形曲折.冷裂是较干净的脆性裂纹,断口较平,具有金属光泽或轻微的氧化色泽.2、产生原因1 铁水中碳、硅含苞欲放量过低,含硫量过高;2 浇注温度过高;3 冒口颈过大、过短,造成局部过热严重,或重口太小,补缩不好;4 铸件在清理、运输过程中,受冲击过大.3、防止方法1 控制铁水化学成分在规定的范围内;2 降低浇注温度;3 合理设计冒口系统;4 铸件在清理、运输过程中避免过度冲击.十二、气孔1、特征气孔的孔壁光滑明亮,形状有圆形、梨形和针状,孔的尺寸有大有小,产生在铸件表面或内部.铸件内部的气孔在敲碎后或机械加工时才能被发现.2、产生原因1 小炉料潮湿、锈蚀严重或带有油污,使铁水含气量太多、氧化严重;2 出铁孔、出铁槽、炉衬、浇包衬未洪干;3 浇注温度较低,使气体来不及上浮和逸出;4 炉料中含铝量较高,易造成氢气孔;5 砂型透气性不好、型砂水分高、含煤粉或有机物较多,使浇注时产生大量气体且不易排出.3、防止方法1 炉料要妥善管理,表面要清洁;2 炉缸、前炉、出铁口、出铁槽、浇包必须烘干;3 提高浇注温度;4 不使用铝量过高的废钢;5 适当降低型砂的水分、控制煤粉加入量,扎通气孔等.十三、缩松、疏松1、特征分散、细小的缩孔,带有树枝关结晶的称缩松,比缩松更细小的称疏松.常出现在热世部位.2、产生原因1 铁水中碳、硅含量过低,收缩大;2 浇注速度太快、浇注温度过高,使得液态收缩大;3 浇注系统、冒口设计不当,无法实现顺序凝固;4 冒口太小,补缩不充分.3、防止方法1 控制铁水的化学成分在规定范围内;2 降低浇注速度和浇注温度;3 改进浇冒口系统,利用顺序凝固;4 加大冒口体积,保证充分补缩.十四、反白口1、特征铸件断口内部出现白口组织,边缘部分出现灰口.2、产生原因1 碳、硅含量较高的铁水,含氢量过高;2 炉料中带入的铬等白口形成元素过多;3 元素偏析严重;3、防止方法1 控制化学成分、碳、硅含量不宜过高;2 炉衬、包衬要烘干;型砂水分不宜过高;3 加强炉料管理,减少带入白口化元素.。
常见铸件缺陷及其预防措施

常见铸件缺陷及其预防措施常见铸件缺陷及其预防措施(序+缺陷名称+缺陷特征+预防措施)1 气孔在铸件内部、表面或近于表面处,有大小不等的光滑孔眼,形状有圆的、长的及不规则的,有单个的,也有聚集成片的。
颜色有白色的或带一层暗色,有时覆有一层氧化皮。
降低熔炼时流言蜚语金属的吸气量。
减少砂型在浇注过程中的发气量,改进铸件结构,提高砂型和型芯的透气性,使型内气体能顺利排出。
2 缩孔在铸件厚断面内部、两交界面的内部及厚断面和薄断面交接处的内部或表面,形状不规则,孔内粗糙不平,晶粒粗大。
壁厚小且均匀的铸件要采用同时凝固,壁厚大且不均匀的铸件采用由薄向厚的顺序凝固,合理放置冒口的冷铁。
3 缩松在铸件内部微小而不连贯的缩孔,聚集在一处或多处,晶粒粗大,各晶粒间存在很小的孔眼,水压试验时渗水。
壁间连接处尽量减小热节,尽量降低浇注温度和浇注速度。
4 渣气孔在铸件内部或表面形状不规则的孔眼。
孔眼不光滑,里面全部或部分充塞着熔渣。
提高铁液温度。
降低熔渣粘性。
提高浇注系统的挡渣能力。
增大铸件内圆角。
5 砂眼在铸件内部或表面有充塞着型砂的孔眼。
严格控制型砂性能和造型操作,合型前注意打扫型腔。
6 热裂在铸件上有穿透或不穿透的裂纹(注要是弯曲形的),开裂处金属表皮氧化。
严格控制铁液中的 S、P含量。
铸件壁厚尽量均匀。
提高型砂和型芯的退让性。
浇冒口不应阻碍铸件收缩。
避免壁厚的突然改变。
开型不能过早。
不能激冷铸件。
7 冷裂在铸件上有穿透或不穿透的裂纹(主要是直的),开裂处金属表皮氧化。
8 粘砂在铸件表面上,全部或部分覆盖着一层金属(或金属氧化物)与砂(或涂料)的混(化)合物或一层烧结构的型砂,致使铸件表面粗糙。
减少砂粒间隙。
适当降低金属的浇注温度。
提高型砂、芯砂的耐火度。
9 夹砂在铸件表面上,有一层金属瘤状物或片状物,在金属瘤片和铸件之间夹有一层型砂。
严格控制型砂、芯砂性能。
改善浇注系统,使金属液流动平稳。
大平面铸件要倾斜浇注。
10 冷隔在铸件上有一种未完全融合的缝隙或洼坑,其交界边缘是圆滑的。
铸铁件缩松、缩孔、凹陷缺陷的原因分析与防止方法
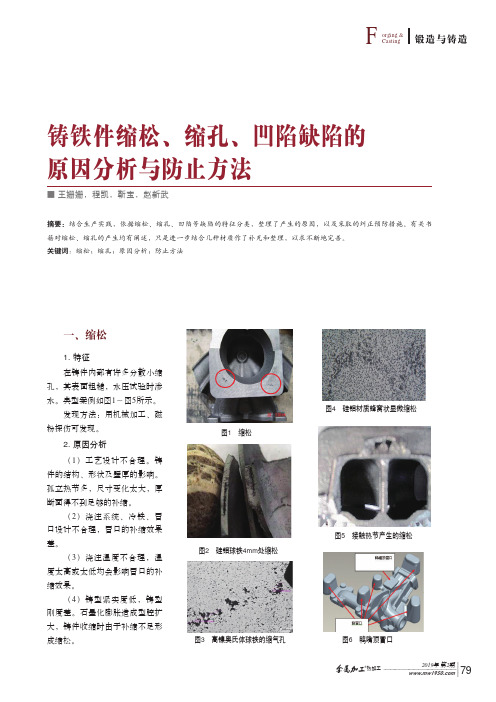
2019年第2期热加工79F锻造与铸造orging &Casting铸铁件缩松、缩孔、凹陷缺陷的原因分析与防止方法■王姗姗,程凯,靳宝,赵新武摘要:结合生产实践,依据缩松、缩孔、凹陷等缺陷的特征分类,整理了产生的原因,以及采取的纠正预防措施。
有关书籍对缩松、缩孔的产生均有阐述,只是进一步结合几种材质作了补充和整理,以求不断地完善。
关键词:缩松;缩孔;原因分析;防止方法一、缩松1. 特征在铸件内部有许多分散小缩孔,其表面粗糙,水压试验时渗水。
典型案例如图1~图5所示。
发现方法:用机械加工、磁粉探伤可发现。
2. 原因分析(1)工艺设计不合理。
铸件的结构、形状及壁厚的影响。
孤立热节多,尺寸变化太大,厚断面得不到足够的补缩。
(2)浇注系统、冷铁、冒口设计不合理,冒口的补缩效果差。
(3)浇注温度不合理,温度太高或太低均会影响冒口的补缩效果。
(4)铸型紧实度低,铸型刚度差。
石墨化膨胀造成型腔扩大,铸件收缩时由于补缩不足形成缩松。
图1 缩松图2 硅钼球铁4mm处缩松图4 硅钼材质蜂窝状显微缩松图3 高镍奥氏体球铁的缩气孔图5 接触热节产生的缩松图6 鸭嘴顶冒口2019年 第2期 热加工80F锻造与铸造orging &Casting(5)碳、硅含量低,磷含量较高;凝固区间大。
硅钼和高镍球墨铸铁对碳、硅含量和氧化铁液的敏感性特大,铁液严重氧化或碳、硅量低时,易出现显微缩松。
即便在薄壁处也容易出现缩松(见图2、图3、图4)。
(6)孕育不充分,石墨化效果差。
(7)残余镁量和稀土量过高。
钼含量较高时也会增加显微缩松。
(8)浇注速度太快。
(9)炉料锈蚀,氧化铁多。
(10)铁液在电炉内高温停放时间太长,俗称“死铁水”,造成严重氧化。
(11)冲天炉熔炼时底焦太底,风量太大,元素烧损大,铁液严重氧化。
(12)冒口径处形成接触热节产生缩松(见图5)。
(13)压箱铁不够(或箱卡未锁紧,箱带断裂等),浇注后由于涨箱造成缩松。
磁粉检测技术及缺陷分析
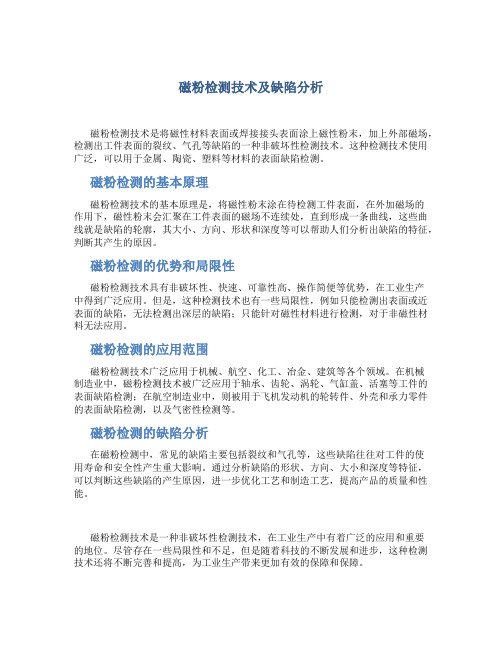
磁粉检测技术及缺陷分析磁粉检测技术是将磁性材料表面或焊接接头表面涂上磁性粉末,加上外部磁场,检测出工件表面的裂纹、气孔等缺陷的一种非破坏性检测技术。
这种检测技术使用广泛,可以用于金属、陶瓷、塑料等材料的表面缺陷检测。
磁粉检测的基本原理磁粉检测技术的基本原理是,将磁性粉末涂在待检测工件表面,在外加磁场的作用下,磁性粉末会汇聚在工件表面的磁场不连续处,直到形成一条曲线,这些曲线就是缺陷的轮廓,其大小、方向、形状和深度等可以帮助人们分析出缺陷的特征,判断其产生的原因。
磁粉检测的优势和局限性磁粉检测技术具有非破坏性、快速、可靠性高、操作简便等优势,在工业生产中得到广泛应用。
但是,这种检测技术也有一些局限性,例如只能检测出表面或近表面的缺陷,无法检测出深层的缺陷;只能针对磁性材料进行检测,对于非磁性材料无法应用。
磁粉检测的应用范围磁粉检测技术广泛应用于机械、航空、化工、冶金、建筑等各个领域。
在机械制造业中,磁粉检测技术被广泛应用于轴承、齿轮、涡轮、气缸盖、活塞等工件的表面缺陷检测;在航空制造业中,则被用于飞机发动机的轮转件、外壳和承力零件的表面缺陷检测,以及气密性检测等。
磁粉检测的缺陷分析在磁粉检测中,常见的缺陷主要包括裂纹和气孔等,这些缺陷往往对工件的使用寿命和安全性产生重大影响。
通过分析缺陷的形状、方向、大小和深度等特征,可以判断这些缺陷的产生原因,进一步优化工艺和制造工艺,提高产品的质量和性能。
磁粉检测技术是一种非破坏性检测技术,在工业生产中有着广泛的应用和重要的地位。
尽管存在一些局限性和不足,但是随着科技的不断发展和进步,这种检测技术还将不断完善和提高,为工业生产带来更加有效的保障和保障。
铸铁件粉末涂装中的针孔缺陷的分析

铸铁件粉末涂装中的针孔等缺陷之分析(草稿)摘要:针对喷粉生产线中出现产品表面有针孔等缺陷问题,概述了铸铁件在静电粉末喷涂中因工件材质、前处理、水分烘干、粉末喷涂、粉末固化等而产生的针孔缺陷,重点分析其成因及解决方法。
关键词:针孔高远红外辐射加热铸铁件粉末涂料一.涂装技术参数1.工件:铸铁件≤39KG 工件最大综合尺寸: 520×410×360 缝纫机机头形状比较复杂,喷砂质量、表观比较差。
2. 工作链速:0.7m/min3. 粉末涂料种类:环氧(热固性江苏太仓“老虎”牌10min,200℃)4. 环境要求:相对湿度:60-80%,温度:20-30℃(≥10℃)5. 压缩空气要求:1)压力:0.7MPa2)含水量:小于1.3克/m33)含油率:0.1ppm 0.01 m g/ m34)含尘量:小于1.0克/m3附:单螺杆空压机(上海佳力士机械0G08F 1.1 m3/h 0.85MPa)储气罐0.28 m3膜式高效净化器(活性炭沈阳德国技术)二.涂装工艺流程及参数1.前处理:大连恒利提供锌系磷化药液,常温脱脂-水洗1-表调-磷化-水洗2-水洗3要求控制磷化膜粗糙问题,锌系最佳膜厚为1.5-2克每平方米2.水分烘干10min,120-220℃,现140℃螺旋翅片加热,循环风机3. 喷粉进入喷粉室工件表面温度:≤50℃喷粉室附近干扰气流横向速度:≤0.3m/s4. 粉末固化高远红外辐射加热10min,120-220℃,现11min,240℃循环风机三. 铸铁件常见铸铁件为灰口铸铁,含碳量在2%至4%之间,碳主要以石墨相存在。
铸铁件表面疏松多孔,特别是当铸造质量不高的情况下,铸铁件表面缺陷更加突出,因此,铸铁喷粉比较困难,废品率较高。
主要表现在涂层结合强度差,孔隙率高,容易返锈。
因此在做铸铁件前处理工艺时要格外的小心。
四.针孔1. 针孔是指涂膜表面存在像被针尖刺过的小圆孔,类似皮革毛孔,孔径约100μm。
铁磁性材料加工件磁粉检测缺陷分析及预防措施

铁磁性材料加工件磁粉检测缺陷分析及预防措施伴随着工业技术和社会经济的不断发展,我国各行各业都有了大跨度的发展,人们对产品的质量有了更高的要求,尤其在材料的加工及检测上。
文章作者对磁粉检测及其应用领域进行了简要的介绍与分析,并进一步分析了磁粉检测的步骤、检测的缺陷以及预防措施,希望能够为铁磁性材料加工件的检测提供一定的借鑒,仅供参考。
标签:铁磁性材料加工件;磁粉检测;缺陷;预防措施引言我国是制造大国,制造业相当发达,尤其是在中国加入WTO以来,“中国制造”享誉世界,但是,近年来“中国制造”备受挑战,我国许多产品质量不达标,受到了国际上的质疑,尤其是机械加工产品。
磁铁性材料作为机械加工中的一种主要材料,其质量检测十分重要。
磁粉检测是磁铁型材料加工件中最常用的一种检测方法,受到广大行业人员的喜爱。
在进行磁铁性材料加工件的生产时,在加工件的表面撒上适量的磁粉,通过磁铁特有的吸附原理对加工件的质量好坏进行判断,这种判断方法被称为磁粉检测。
磁粉检测的应用范围很广,许多领域都有所涉猎,例如航空、造船、电子、机械设备的生产等方面,因为磁粉检测具有操作方便、成本低廉、检测效果好、效率高的特点。
磁粉检测也有着特殊性,在检测过程中要求无损,不可损坏磁铁性材料加工件的质量,保证加工件的质量达到生产厂家的质量标准。
然而在实际的生产过程中,一些检测人员缺乏专业的检测知识,业务能力不够,检测经验不足,对无损检测缺乏正确的认识,在检测过程中出现了许多问题,不能保证磁铁性材料加工件的质量,造成了磁粉检测缺陷的出现,对产品的生产造成了严重的后果。
1 磁粉检验检测出的铁磁性材料加工件缺陷的分类在对铁磁性材料加工件进行检测时会出现磁痕,磁痕是磁铁性材料加工件缺陷的最主要的表现形式,但是受一些外在和内在因素的影响,有些磁痕并不能真实、准确的反映出加工件的质量问题,使得工作人员不能对缺陷进行正确的认识和预防处理,这就需要对磁粉检测检出的铁磁性材料加工件的缺陷进行分类。
不合格品磁型铸造件的缺陷原因分析及改进方法
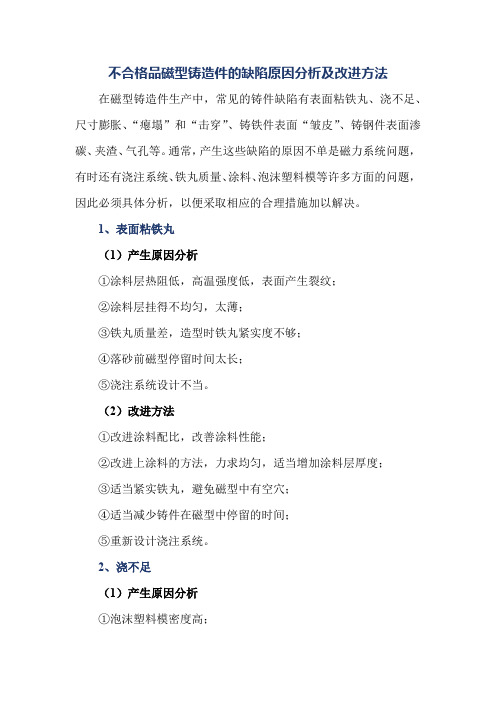
不合格品磁型铸造件的缺陷原因分析及改进方法在磁型铸造件生产中,常见的铸件缺陷有表面粘铁丸、浇不足、尺寸膨胀、“瘪塌”和“击穿”、铸铁件表面“皱皮”、铸钢件表面渗碳、夹渣、气孔等。
通常,产生这些缺陷的原因不单是磁力系统问题,有时还有浇注系统、铁丸质量、涂料、泡沫塑料模等许多方面的问题,因此必须具体分析,以便采取相应的合理措施加以解决。
1、表面粘铁丸(1)产生原因分析①涂料层热阻低,高温强度低,表面产生裂纹;②涂料层挂得不均匀,太薄;③铁丸质量差,造型时铁丸紧实度不够;④落砂前磁型停留时间太长;⑤浇注系统设计不当。
(2)改进方法①改进涂料配比,改善涂料性能;②改进上涂料的方法,力求均匀,适当增加涂料层厚度;③适当紧实铁丸,避免磁型中有空穴;④适当减少铸件在磁型中停留的时间;⑤重新设计浇注系统。
2、浇不足(1)产生原因分析①泡沫塑料模密度高;②涂料层透气性低;③浇注方法不好;④浇注温度太低。
(2)改进方法①改进发泡成型工艺,降低泡沫塑料模密度;②改进涂料性能及上涂料的方法;③改进浇注工艺,注意浇注速度;④适当提高浇注温度。
3、尺寸膨胀(1)产生原因分析磁感应强度低。
(2)改进方法提高磁感应强度。
4、“瘪塌”和“击穿”(1)产生原因分析①磁感应强度太高;②浇注速度太慢。
(2)改进方法①降低磁感应强度;②提高浇注速度。
5、铸铁件表面“皱皮”(1)产生原因分析①泡沫塑料模密度太大;②涂料层透气性低;③浇冒口系统设计不适合;④浇注方法不好;⑤液体金属中渣子进入磁型。
(2)改进方法①降低泡沫塑料模密度;②提高涂料层透气性;③改进浇冒口设计;④改进浇注工艺,注意浇注速度;⑤注意挡渣。
6、铸钢件表面渗碳(1)产生原因分析①泡沫塑料模密度大;②涂料层透气性低;③浇冒口系统设计不合适。
(2)改进方法①降低泡沫塑料模密度;②提高涂料层透气性;③改变浇冒口系统,变暗冒口为明冒口。
7、夹渣,包括铸件表面上“碳孔”铸件内部的“黑点”或“黑线”(1)产生原因分析①泡沫塑料模密度大;②涂料层透气性差;③浇冒口系统不合理;④浇注温度低。
铸件缺陷分析及防止措施

称为脉纹。
规则。
布不均.数量不够,紧箱操作不当,金属液压头过大,造成抬型。
2.毛刺形成原因
1)型、芯砂成分或混制工艺不当,使型、芯砂性能低下不均。
2)型、芯紧实不均匀,局部紧实度过大或过小,使型、芯在起模、烘干、存放、搬运和浇注过程中开
裂。
3)型、芯烘干规范不正确,烘干不足或过烧,导致型、芯开裂。
4)干型、干芯或自硬砂型、芯在放置过程中吸湿返潮,强度下降,浇注时开裂。
铸件常见缺陷分析表
缺陷 缺陷 类别 名称
定义和特征
检验与鉴别
原因分析
飞翅(飞 1.飞翅:又称飞边或披缝,是产生在分型面、分芯面、芯头、活 肉眼外观检查。注意区分飞翅和毛刺:飞翅出 1.飞翅形成原因 1)分型面、分芯面、芯头间隙过大。2)模样、芯盒、砂箱或金属型变形,使分型面
边、披 块及型与芯结合面等处,通常垂直于铸件表面的厚度不均匀的薄 现在型-型、型-芯、芯-芯接合面上,成连片 、分芯面、芯头芯座贴合不严。3)由于型、芯放置和烘干不当等原因,使型、芯变形,导致分型面、
与掉落的砂块相似,通常伴有残缺;胀砂一般 动或冲击,使型、芯局部砂块掉落。
发生在铸件侧面和下部,边缘与铸件本体平滑
过渡;夹砂与发生在铸件上表面的掉砂极其相
似,这时,掉砂缺陷内也裹有砂块,但其边缘
的金属与铸件本体相连,而夹砂的金属边缘尖
锐,一般不与铸件本体相连。
防止方法
补救措施
1.飞翅的防止 1)改进工艺设计,合理选择参数,严格检修模样和芯盒,使 飞翅和毛刺一般不会使铸件报废,但
缝)、毛 片状金属突起物。2.毛刺:是铸件表面的刺状金属突起物,常出 状,系接合面间隙过大所引起;毛刺系型、芯 分芯面、芯头与芯座贴合不严。4)修型、芯时,误将棱边修圆。 5)铸型装配时芯头磨小,芯头间隙
球墨铸铁件磁粉探伤缺陷及预防措施
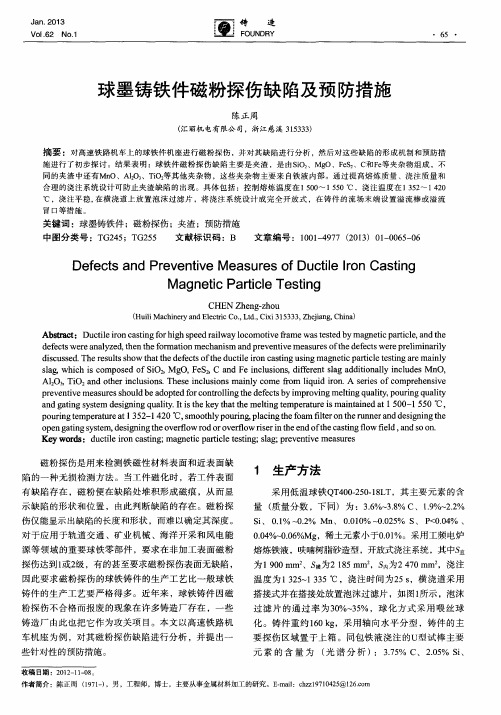
铸
造
・6 5 ・
F OUN DR Y
球墨铸铁件磁粉探伤缺 陷及预 防措施
陈 正 周
( 汇 )
摘 要 :对高速铁路机车上的球铁件机座进行磁粉探伤, 并对其缺陷进行分析,然后对这些缺陷的形成机制和预防措
Ab s t r a c t : Du c t i l e i r o n c a s t i n g f o r h i g h s p e e d r a i l wa y l o c o mo t i v e la f me wa s t e s t e d b y ma g n e t i c p a r t i c l e . a n d t h e
p o u r i n g t e mp e r a ur t e a t l 3 5 2 - 1 4 2 0℃ . s mo o t h l yp o u r i n g , p l a c i n g t h e oa f m i f l t e r o n t h e r t mn e r a n d d e s i g n i n g t h e
冒口等措施 。
关键 词 :球 墨铸铁 件 ;磁粉探 伤 ;夹渣 ;预 防措施 中 图分类 号 :T G 2 4 5 ;T G 2 5 5 文 献标 识码 :B 文章编 号 :1 0 0 1 — 4 9 7 7( 2 0 1 3 )0 1 — 0 0 6 5 — 0 6
De f e c t s a n d Pr e v e n t i v e Me a s u r e s o f Du c t i l e I r o n Ca s t i n g
铸件常见缺陷及防止方法

一、表面缺陷和内部缺陷
产生原因
防止方法
A、欠铸(浇不到):液体金属未充满型腔造成铸件缺肉
1、浇铸温度和型壳温度低,流动性差
2、金属液含气量大,氧化严重以致流动性下降
3、铸件壁太薄
4、浇铸系统大小和设置位置不合理,直浇道高度不够
5、型壳焙烧不充分或型壳透气性差,在铸型中形成气袋
6、浇铸速度过慢或浇注时金属液断流
2、壳烧不充分,没排除蜡残余及壳中发气杂质
3、冷壳浇铸,型壳受潮
4、钢水含气多,脱氧不良
5、浇铸系统设计不合理,浇铸时卷入气体
1、改善壳透气性,
2、充分焙烧型壳
3、热壳浇铸,防止受潮
4、改进脱氧方法
5、改进浇铸系统结构
N、多孔性气孔和针孔:铸件上的细小、分散或密集的孔眼
1、炉料不干净,
2、钢水脱氧不良,镇静时间不够,含气量高
1、水玻璃型壳热水脱蜡时,脱蜡液碱性偏大,模料皂化,造成型壳内层局部酥软煮烂
2、面层涂料粘度过大,局部堆积,硬化不透,热水脱蜡时,局部面层涂料层不规则脱落
3、模料熔失不充分,焙烧不彻底,使皂化物和其它有害杂质沉积在型壳内表面某个部位
4、水玻璃型壳的水玻璃模数高、密度大、硬化不充分,造成型壳局部钠盐集聚
5、改进涂料配方,适当增加层数,必要时可采用一些局部强化措施
H、铁刺:铸件表面上出现许多分散或密集的小突刺
1、面层涂料中粉料量少,粘度低
2、面层涂料相对易熔模的涂挂性差
3、面层涂料配制时搅拌时间不充分,涂挂时面层涂料中的粉料趋向撒砂砂粒分布
4、表面层撒砂砂粒较大
1、适当增加面层涂料中粉料加入量,提高粘度
2、严格控制涂料粘度,涂料要涂均匀,力求减少局部堆积,合理选择硬化工艺参数
磁粉检测技术常见问题及解决方案

磁粉检测技术常见问题及解决方案磁粉检测技术是一种常用的无损检测方法,广泛应用于工业领域。
它通过应用磁法以及磁粉材料的吸附能力,在金属材料上发现表面和近表面的缺陷。
然而,对于初学者和经验不足的操作人员来说,磁粉检测技术可能会遇到一些常见的问题。
本文将介绍一些常见问题,并提供相应的解决方案。
一、磁粉检测过程中的漏报缺陷磁粉检测技术的主要目的是检测金属材料上的缺陷,如裂纹、变形等。
然而,在实际应用中,有时可能会因为一些原因漏报一些缺陷,这可能是由于以下几个原因造成的:1. 磁粉材料不合适:使用了不适合该材料的磁粉材料会导致漏报缺陷。
解决办法是选择合适的磁粉材料,要考虑材料的磁性和粒度。
2. 磁场强度不足:磁场强度不足会导致磁粉材料无法吸附在缺陷处。
可以通过增加磁场的强度或改变磁场的方向来解决这个问题。
3. 检测时间不足:检测时间不足也可能导致漏报缺陷。
确保检测时间足够长,使磁粉能够充分吸附在缺陷上,以便于观察。
二、磁粉检测过程中的误报缺陷与漏报缺陷相反,有时也可能发生误报缺陷。
这是由于以下原因:1. 磁粉材料不纯:使用了掺杂有杂质的磁粉材料会导致产生误报缺陷。
解决办法是使用高纯度的磁粉材料。
2. 检测环境干净度不足:周围环境的杂质会干扰磁粉检测的结果,产生误报缺陷。
确保检测环境的干净度以减少误报。
3. 操作人员技术不熟练:不熟练的操作人员可能会出现误判,将表面粗糙度或其他因素误判为缺陷。
提高操作人员的培训和技术水平,可以减少误报缺陷的发生。
三、磁粉检测过程中的背景杂乱信号问题在磁粉检测中,背景杂乱信号是一种常见的问题。
这可以通过以下方式解决:1. 使用合适的磁粉材料:选择适合该材料的磁粉材料,可以减少背景杂乱信号的干扰。
2. 做好清洁工作:在进行磁粉检测前,确保被测物表面干净,以减少背景杂乱信号的干扰。
3. 调整检测参数:合理调整探头和磁场的距离,选择合适的检测参数,可以降低背景杂乱信号。
四、磁粉检测技术的局限性虽然磁粉检测技术是一种常用的无损检测方法,但它也有一些局限性:1. 只适用于导电材料:磁粉检测技术只适用于导电材料,对于非导电材料无法进行有效的检测。
磁粉探伤仪如何解决漏磁及缺陷磁痕等现象 磁粉探伤仪常见问题解决方法

磁粉探伤仪如何解决漏磁及缺陷磁痕等现象磁粉探伤仪常见问题解决方法所谓的磁性是指金属具有导磁的性能;从应用意义讲如:可用磁性材料(金属)制造长期磁铁、电工材料,也可用磁性来检查磁性金属是否有裂纹等。
磁粉探伤仪就是利用工件磁化时,若工件表面有缺陷存在,由于缺陷处的磁阻增大而产生漏磁,形成局部磁场,磁粉便在此处显示缺陷的形状和位置,从而判定缺陷的存在。
磁粉探伤仪适用于:1、检测未加工的原材料(如纲坯)和加工的半成品、成品件及在役与使用过的工件.2、检测马氏体不锈钢和沉淀硬化不锈钢材料,不适用于检测奥氏体不锈钢材料.3、检测铁磁性材料工件表面和近表面尺寸很小,间隙极窄的裂纹和目视难以看出的缺陷.4、检测管材棒材板材形材和锻钢件铸钢件及焊接件.5、使用于检测工件表面和近表面的缺陷,但不适用于检测工件表面浅而宽的缺陷、埋藏较深的内部缺陷和延长方向与磁力线方向夹角小于20度的缺陷。
磁粉探伤仪的运用有时还会显现漏磁及缺陷磁痕等现象由于铁磁性材料的磁率宏大于非铁磁材料的导磁率,依据工件被磁化后的磁通密度B=H来分析,在工件的单位面积上穿过B根磁线,而在缺陷区域的单位面积上不能容许B根磁力线通过,就迫使一部分磁力线挤到缺陷下面的材料里,其它磁力线不得不被迫逸出工件表面以外出形成漏磁,磁粉将被这样所引起的漏磁所吸引。
缺陷磁痕类型1、各种工艺性质缺陷的磁痕;2、材料夹渣带来的发纹磁痕;3、夹渣、气孔带来的点状磁痕。
产生漏磁的影响因素1、缺陷的磁导率:缺陷的磁导率越小、则漏磁越强。
2、磁化磁场强度(磁化力)大小:磁化力越大、漏磁越强。
3、被检工件的形状和尺寸、缺陷的形状大小、埋藏深度等:当其他条件相同时,埋藏在表面下深度相同的气孔产生的漏磁要比横向裂纹所产生的漏磁要小。
微型磁粉探伤仪是利用磁轭对铁磁性材料制成的工件进行磁化的快捷微型磁粉探伤设备,能对各种零件磁化;因锻压、淬火、焊接、疲乏等引起的表面及近表面缺陷,如链杆、曲轴、轴承、高强度螺栓、弹簧、锻件、石化管件、阀门、叶片、齿轮、轧辊、锚链以及焊缝等几何形状多而杂工件的探伤。
铸造缺陷与防止(精选五篇)
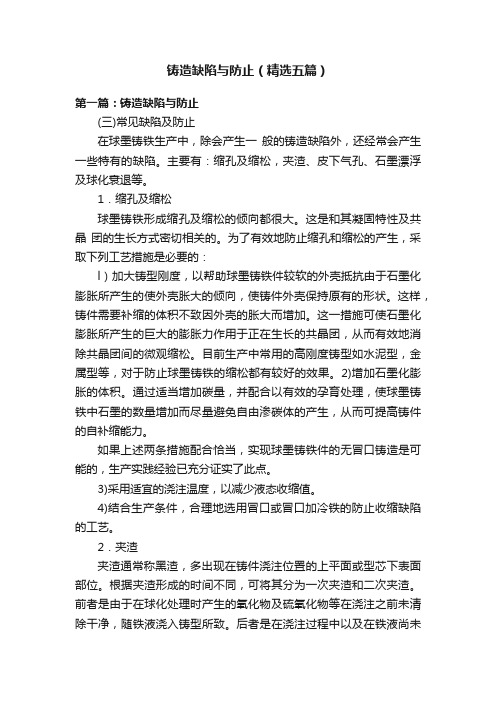
铸造缺陷与防止(精选五篇)第一篇:铸造缺陷与防止(三)常见缺陷及防止在球墨铸铁生产中,除会产生一般的铸造缺陷外,还经常会产生一些特有的缺陷。
主要有:缩孔及缩松,夹渣、皮下气孔、石墨漂浮及球化衰退等。
1.缩孔及缩松球墨铸铁形成缩孔及缩松的倾向都很大。
这是和其凝固特性及共晶团的生长方式密切相关的。
为了有效地防止缩孔和缩松的产生,采取下列工艺措施是必要的:l)加大铸型刚度,以帮助球墨铸铁件较软的外壳抵抗由于石墨化膨胀所产生的使外壳胀大的倾向,使铸件外壳保持原有的形状。
这样,铸件需要补缩的体积不致因外壳的胀大而增加。
这一措施可使石墨化膨胀所产生的巨大的膨胀力作用于正在生长的共晶团,从而有效地消除共晶团间的微观缩松。
目前生产中常用的高刚度铸型如水泥型,金属型等,对于防止球墨铸铁的缩松都有较好的效果。
2)增加石墨化膨胀的体积。
通过适当增加碳量,并配合以有效的孕育处理,使球墨铸铁中石墨的数量增加而尽量避免自由渗碳体的产生,从而可提高铸件的自补缩能力。
如果上述两条措施配合恰当,实现球墨铸铁件的无冒口铸造是可能的,生产实践经验已充分证实了此点。
3)采用适宜的浇注温度,以减少液态收缩值。
4)结合生产条件,合理地选用冒口或冒口加冷铁的防止收缩缺陷的工艺。
2.夹渣夹渣通常称黑渣,多出现在铸件浇注位置的上平面或型芯下表面部位。
根据夹渣形成的时间不同,可将其分为一次夹渣和二次夹渣。
前者是由于在球化处理时产生的氧化物及硫氧化物等在浇注之前未清除干净,随铁液浇入铸型所致。
后者是在浇注过程中以及在铁液尚未在铸型中凝固以前的一段时间内产生的渣。
一次渣的尺寸较大,二次渣一般很细小,在铸件的加工表面上表现为暗灰色无光泽的斑纹或云片状。
夹渣缺陷严重影响铸件的力学性能,特别是硬度、韧性及耐磨性,并能导致耐压铸件发生渗漏。
防止措施主要有:1)尽量降低原铁液的含硫量。
2)在保证石墨球化条件下,降低铁液的残留镁量和残留稀土量。
3)提高浇注温度,应不低于1350℃。
铸件磁粉探伤

铸件磁粉探伤是一种重要的无损检测技术,广泛应用于铸造行业,用于检测铸件中的表面和近表面缺陷。
这种技术基于磁粉在磁场作用下的聚集原理,通过磁化铸件并施加磁粉,使得缺陷处形成可见的磁粉堆积,从而实现对缺陷的检测和定位。
铸件磁粉探伤的基本原理是,当铸件被磁化时,缺陷处会形成漏磁场。
这个漏磁场会吸引磁粉,使得磁粉在缺陷处聚集,形成可见的磁痕。
通过观察和分析磁痕的形状、大小和分布,可以判断缺陷的性质、位置和严重程度。
铸件磁粉探伤的优点在于其操作简单、成本低廉、灵敏度高,能够检测出微小的表面和近表面缺陷。
此外,该技术对于铁磁性材料的检测效果尤为显著,因此在铸造行业中得到了广泛应用。
在进行铸件磁粉探伤时,需要注意以下几点:首先,磁化方法的选择应根据铸件的形状、尺寸和材质来确定,以确保磁化效果均匀且充分。
其次,磁粉的选择也很关键,应根据铸件的表面状况和缺陷类型来选择合适的磁粉类型和粒度。
最后,在观察和分析磁痕时,需要具备丰富的经验和专业知识,以确保准确判断缺陷的性质和位置。
总之,铸件磁粉探伤是一种重要的无损检测技术,对于确保铸件质量和提高生产效率具有重要意义。
在实际应用中,需要选择合适的磁化方法和磁粉类型,并结合丰富的经验和专业知识来准确判断缺陷的性质和位置。
随着科技的进步和铸造行业的发展,铸件磁粉探伤技术也将不断完善和优化,为铸造行业的可持续发展提供有力支持。
【磁粉检测缺陷图片】铁磁性材料加工件磁粉检测缺陷分析及预防
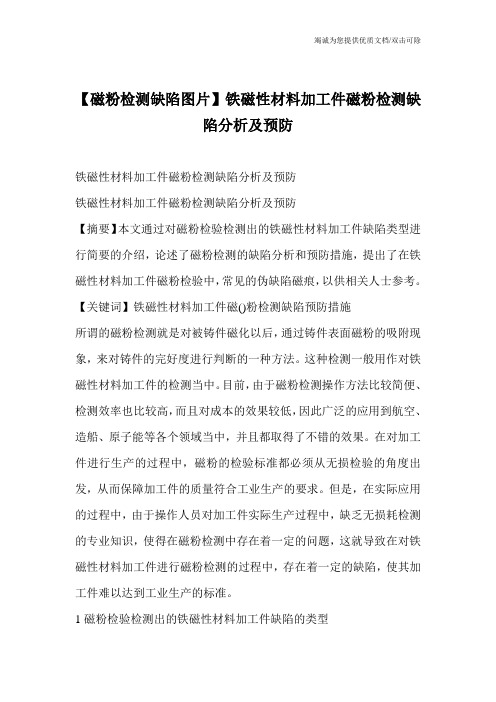
【磁粉检测缺陷图片】铁磁性材料加工件磁粉检测缺陷分析及预防铁磁性材料加工件磁粉检测缺陷分析及预防铁磁性材料加工件磁粉检测缺陷分析及预防【摘要】本文通过对磁粉检验检测出的铁磁性材料加工件缺陷类型进行简要的介绍,论述了磁粉检测的缺陷分析和预防措施,提出了在铁磁性材料加工件磁粉检验中,常见的伪缺陷磁痕,以供相关人士参考。
【关键词】铁磁性材料加工件磁()粉检测缺陷预防措施所谓的磁粉检测就是对被铸件磁化以后,通过铸件表面磁粉的吸附现象,来对铸件的完好度进行判断的一种方法。
这种检测一般用作对铁磁性材料加工件的检测当中。
目前,由于磁粉检测操作方法比较简便、检测效率也比较高,而且对成本的效果较低,因此广泛的应用到航空、造船、原子能等各个领域当中,并且都取得了不错的效果。
在对加工件进行生产的过程中,磁粉的检验标准都必须从无损检验的角度出发,从而保障加工件的质量符合工业生产的要求。
但是,在实际应用的过程中,由于操作人员对加工件实际生产过程中,缺乏无损耗检测的专业知识,使得在磁粉检测中存在着一定的问题,这就导致在对铁磁性材料加工件进行磁粉检测的过程中,存在着一定的缺陷,使其加工件难以达到工业生产的标准。
1磁粉检验检测出的铁磁性材料加工件缺陷的类型所谓的磁粉检验的缺陷是在通过磁粉检验的方法,根据工件上磁痕显现的情况进判断的时候,由于受到其他因素的影响,使得磁痕不能真实地反映出工件中存在问题。
因此,人们就将加工件经磁粉检验检测出的缺陷进行分类。
首先就要对磁痕的形状进行观察分析,而且在不同的加工件检测过程中,磁痕所呈现出来的形状也就不一样;然后在对磁痕所处的位置和生产此类磁痕的加工件的数量进行判断分析,看两者之间是否存在着规律。
最后再对加工件的生产铸造工艺的相关理论对其缺陷进行分析讨论。
目前,磁粉检验检测出的加工件缺陷的类型主要有着三种,分别是孔洞类缺陷、冷隔类缺陷以及夹杂类缺陷。
2磁粉检测出的缺陷分析和预防工作2.1孔洞类缺陷2.1.1侵入气孔入侵气孔有着数量少、尺寸大、内表面光滑的特征,这些气孔大多数都是呈现出梨形或者椭圆形。
- 1、下载文档前请自行甄别文档内容的完整性,平台不提供额外的编辑、内容补充、找答案等附加服务。
- 2、"仅部分预览"的文档,不可在线预览部分如存在完整性等问题,可反馈申请退款(可完整预览的文档不适用该条件!)。
- 3、如文档侵犯您的权益,请联系客服反馈,我们会尽快为您处理(人工客服工作时间:9:00-18:30)。
万方数据铸造聂小武等:铸件磁粉检测缺陷分析及预防·1057·1磁粉检验检测出的铸件缺陷类型’磁粉检验的缺陷是通过磁痕来显示的,但磁痕并不一定能真实地反映缺陷的本质,因为形成漏磁的因素很多,并非所有的磁痕都表征缺陷的存在,这就使得对铸件经磁粉检验检测出的缺陷进行分类比较复杂。
要判断缺陷的类型,首先要观察磁痕的形状:是点状还是线状,是聚集还是分散;其次分析磁痕所在的位置以及产生此类磁痕的铸件数量有多少,有无规律性;最后,结合铸造工艺理论判断缺陷类型。
由于铸件缺陷分类的方法比较多,可按照国际铸件缺陷图详1】分类标准,认为磁粉检验能检测出的铸件缺陷主要有三类—孔洞类缺陷,如气孔、针孔、缩孔、缩松、疏松;裂纹;冷隔类缺陷,如冷裂、热裂、冷隔、热处理裂纹;夹杂类缺陷,如夹杂物、夹渣、砂眼等。
2磁粉检测出的缺陷分析及防止2.1孔洞类缺陷2.1.1侵入气孑L侵人气孔特征是数量较少,尺寸较大,内表面光滑,形状有梨形和椭圆形,产生在铸件的局部,有时显露在铸件表面。
产生机理主要是,铸型在高温金属液的热作用下,产生的气体侵人金属液而形成的。
比如在砂型中,当砂型或砂芯产生的气体压力超过金属液对气体的阻力时,气体进入金属液中。
特别是砂型砂芯局部过湿或通气孔钻人金属液堵死,会形成侵入气孔。
侵入气孑L方向,可观察气孔的尖端指向来判断。
防止措施口卅有,①控制型(芯)砂混合料中的发气物加入量;湿型少喷水或少刷水,烘干后的型芯不要久放,不用潮湿或生锈的冷铁。
②改善型砂透气性,紧实度要合适。
③保证金属液平稳进入型腔。
④适当提高浇注温度,使侵入金属液气体有时间排出。
2.1.2析出气孔析出气孔特征是多呈细小的圆形、椭圆形或针状,往往出现在铸件的厚大断面上或热节处,经加工后显露。
产生机理,主要由于金属液在熔炼过程中吸收了较多的气体,在凝固过程中大部分气体会逐渐析出,而此时金属液的流动陛很差,气体较难聚集浮起,形成气孔。
防止措施,①炉料人炉前应进行烘干、滚光或吹砂等处理。
②熔炼时加入适量溶剂,使金属液面上形成熔渣保护层,以隔绝空气进入。
③浇包工具要烘干,对金属液采取高温出炉低温浇注等。
④采用真空熔炼和压力凝固。
2.1.3反应性气孔反应性气孔常出现在球墨铸铁件上,也称为皮下气孔,热处理去除氧化皮后会显露出来。
产生机理,高温金属液注入铸型后,与型(芯)、冷铁和熔渣等发生化学反应生成气体而形成的气孔。
铁液中逸出的镁和铁液表面的硫化镁与铸型中的水发生化学反应,生成氢和硫化氢等气体。
防止措施,①净化炉料,减少铁液中含气量;②严格控制型砂水分,在保证球化的前提下,尽量减少镁的加人量;③适当提高浇注温度,在铁液表面或铸型表面撒少量冰晶石粉或氟硅酸钠等。
上述三类缺陷在磁粉检验时显示的磁痕特征是,一般多呈圆形或椭圆形,密集形分布,均有一定面积。
2.1.4缩孔缩孔特点是形状不规则,孔壁粗糙并带有枝晶,常出现在热节或最后凝固部位。
磁粉检验时显示的磁痕特征是磁粉堆积密集,磁痕外形不规则,多呈云朵状出现。
产生机理,铸件逐层凝固时,液态收缩与凝固收缩之和大于其固态收缩。
防止措施,①工艺设计时应使各个断面的模数大致相同;②采用补贴增厚的办法改进断面形状;⑧充分考虑断面的有效距离;④根据合金特性,使用适当数量的冒口;⑤对熔模铸造,模组的分布要合理,防止局部散热困难。
2.1.5缩松、疏松缩松是细小分散的孔洞;疏松是枝晶间及枝晶臂间的细小孑L洞,和缩松相似,但孔洞更细小。
缩松部位在加水压时会渗透。
磁粉检验时显示的磁痕特征是磁粉堆积松散,多呈片状。
图1为某铸件的缩松缺陷,图2为其金相表征,可以看出是由一些不规则的孔洞组成,形状不规则。
产生机理,缩松是由于铸件体积凝固时,液态收缩与凝固收缩的总和大于固态收缩。
疏松产生的原因有两方面——铸件冷却速度过快,来不及补缩;铸件冷却速度过于缓慢,枝晶粗大妨碍补缩。
防止缩孔的办法,①工艺设计上力求做到顺序凝固;②冒口的尺寸和数量要适当;⑧必要时采用补贴增厚的办法;④控制铁液成分,主要控制碳当量和磷,尽可能提高C与Si之比。
防止表面疏松的办法,①加快铸件表面冷却速度,如适当降低铸型温度,降低浇注温度等;②在熔模铸造中,可在型壳装箱填砂前于疏松区域上刷上石墨粉,加快散热,或采用不填砂浇注的方式。
图l缩松F培lSllrinkage2一裂纹、冷隔类缺陷2.2.1冷裂冷裂常常是穿过晶体而不是沿晶界断裂,断口金属光泽或呈轻微氧化色泽,断口形状与普通抗拉试棒 万方数据·1058·FOUNDRYOct.2006VOI.55NO.10图2缩松的金相表征Fi92ThemetallographofshrirIl(age断口相似,一般是在较低温度下产生的。
磁粉检验时显示的磁痕特征是,一般呈弯曲状,磁粉吸附紧密,轮廓清晰,端点尖细,中间粗大。
图3为某铸件的冷裂,图4为其金相表征,在冷裂的旁边有一些细小的孑L洞。
产生机理,铸件内部应力过大,或者铁液中的硫、磷含量过高,增加了脆性,在落砂、清理、搬运、热处理等工序中,受到震动、锤击或加热速度过大等引起开裂,或者铸件中夹杂物缩孑L、气孑L和粗大树枝晶造成应力集中。
防止办法,①铸件的内圆角和工艺拉筋设计要合理;②应使铸件各部分的冷却速度趋于一致;③铸件进行时效处理,减少残余应力;④尽可能使铸件在型内缓慢冷却,减少内应力。
图3冷裂Fig.3Coldtearing图4冷裂的金相表征Fig.4Themetallo鲫hofcoldtearing2.2.2热裂断口严重氧化,无金属光泽,裂纹在晶界萌生并沿晶界扩展,呈粗细不均曲折的不规则曲线,一般在铸件最后凝固的部位。
分为内裂和外裂两种,内裂多在冒口的下部。
磁粉检验时显示的磁痕特征是,磁痕多呈网状分布,磁痕端点尖细,中间粗大,轮廓清晰,吸附紧密。
图5为35Cr№Si铸件的热裂纹缺陷,图6为其经过3%HN0,腐蚀后的金相表征。
产生机理,金属液接近凝固温度时,收缩量较大,塑性较差,铸件自由收缩受阻造成。
防止办法,①提高铸型的退让性,可在型(芯)砂混合料中加入适量的木屑焦粒和炉渣等材料;②增加易裂处的抗裂能力,如加设防裂筋,采用冷铁,金属液从多处浇入型腔等;③改善铸件结构,转角处做成圆角,改变分叉或相接的断面过多等;④合金中低熔点元素不得超标。
图5热裂缺陷Fig5Hotte耐ng图6热裂纹的金相表征Fig.6Theme诅1109raphofhotte州ng2.2.3冷隔冷隔在铸件上为穿透或不穿透的缝隙,边缘成圆角状。
多出现在远离浇口的铸件宽大上表面或薄壁处、金属液流股会合处或激冷部位。
磁粉检验时显示的磁痕特征是,磁粉呈长条状,两端圆滑,磁粉浅淡而松散。
产生机理,①铸型模具温度过低;②浇注系统设计不合理;③浇注温度过低;④合金液压头过小,流速过低。
防止办法,①提高浇注温度;②改善熔炼工艺,防止金属液氧化;③合理布置浇注系统,提高型砂透气性,改变芯撑内冷铁等嵌铸物的尺寸和位置。
2.2.4热处理裂纹铸件在热处理过程中出现的穿透或不穿透的裂纹,开裂处的金属表面有氧化现象。
磁粉检验时显示的磁痕特征是,一般呈弯曲状,磁粉吸附紧密,轮廓清晰,端点尖细,中间粗大。
产生机理,热处理工艺不当或操作不当;铸件残余应力过大,热处理过程中又增加了相变应力;铸件中有气孑L、缩松、组织粗大偏析等缺陷,引起应力集中。
防止办法,①采用合理的热处理规范;②改进铸件结构,壁厚力求均匀;③改进铸造工艺,减少气孔、夹渣及偏析等缺陷。
万方数据铸造聂小武等:铸件磁粉检测缺陷分析及预防·1059·2.3夹杂类缺陷2.3.1金属(非金属)夹杂物铸件加工后,基体表面上有大小不等形状不规则色泽与基体金属不同的其它金属或非金属杂物。
磁粉检验时显示的磁痕特征是,沿一定的方向分布,呈短线状,端点不尖锐,颜色较浅,擦去磁粉后看不出痕迹。
图7为某铸件的夹杂类缺陷,图8为其金相表征,可以看出夹杂物的颜色与基体不一致。
产生机理,①液态金属中混入了外来的金属杂质;②液态金属保温温度过低。
如铝合金,含有粒状或针状结晶的金属化合物;③在液态金属中,混有尚未熔化的金属炉料或合金添加剂;④芯骨外露或芯撑漂浮,被液态金属熔合,但未熔成一体。
防止办法,①保证炉料清洁,防止混入外来金属;②在合金添加元素全部熔化后才能浇注;③坩埚底部的炉料含夹杂物较多,不进行浇注。
图7夹杂Fig.7B1ackingcoatinginclusion图8夹杂的金相表征Fig.8Themetallographofblackingcoatinginclusion2.3.2渣眼渣眼特征是孑L眼内夹杂着玻璃状熔渣,孔壁粗糙,形状不规则。
磁粉检验时显示的磁痕特征是,磁粉堆积密集,磁痕外形不规则,多呈云朵状出现。
产生机理,扒渣和挡渣不好;浇注系统设计不合理;浇注时断流;金属氧化物与造型材料相互作用时,形成低熔点熔渣(即二次渣)等。
防止办法,①浇注前,将金属液静置一段时间后,把渣扒尽;②采用有挡渣装置的浇包;③适当提高浇注温度;④浇注系统要有挡渣措施,浇口的设计应使金属液平稳地进入型腔。
3铸件磁粉检验中常见的伪缺陷磁痕铸件在磁粉检验的过程中,并非所有吸附在材料上的磁痕都代表在该处存在缺陷,有的磁痕则与缺陷无关,为伪缺陷磁痕。
这种伪缺陷磁痕要辨别出来,否则将把无缺陷的铸件当成有缺陷的铸件,甚至认为是废品,因此需要正确判断。
反之,如果把缺陷磁痕当成是伪缺陷磁痕则会造成漏检,后果严重。
导致形成伪缺陷磁痕的因素比较多,需要灵活掌握。
但是,伪缺陷磁痕一般磁痕表征颜色较浅,磁粉堆积稀薄、松散,重复操作时磁痕的再现性不好,磁痕轮廓比较模糊,降低磁场强度时现象消失。
如果实在判断不了时,可以采用腐蚀后通过金相观察分析。
铸件在磁粉检验中常见的伪缺陷磁痕有以下几种。
①待检铸件的几何形状比较特殊且复杂,磁化电流比较大时,在某些断面突然变小的地方可能引起伪缺陷磁痕。
这是因为由于断面面积变小,磁通密度在该处必然增大,超过某一极限值后,磁力线发生外泄,形成漏磁场,产生伪缺陷磁痕。
所以检查具有那些断面突变的零组件时,要特别小心。
可以通过适当降低磁场强度或采用剩磁法再检查,看是否还会有磁痕出现。
②某些铸件在生产的过程中,在清理及搬运时受到机械划伤后,留下微小的划痕,在磁粉检验时形成漏磁场,导致形成伪缺陷磁痕。
这种磁痕一般呈线状,但是两端不尖,整个轮廓不是很清晰。
擦去磁粉后,通过放大镜可以观察到划痕,通过机械打磨可以消除。
③当零件某部位受到外力作用而储存了较大的内应力,发生局部冷作硬化时,由于内部组织畸变,磁导率发生变化,也会形成漏磁场,铸件经时效处理后可消除。
类似的情况还有淬硬区和非淬硬区的交界处以及铸件内部组织严重不均匀时也会发生。