电子产品设计中的bga焊点空洞问题详解
BGA、QFN、CSP器件焊点空洞分析

BGA、QFN、CSP器件焊点空洞分析在SMT生产中,BGA、QFN、CSP等无引脚的元器件,在进行焊接时,无论是回流焊接还是波峰焊接,无论是有铅制程还是无铅制程,冷却之后都难免会出现一些在所难免的空洞(气泡)现象的产生。
焊点内部发生空洞的主要成因是FLUX中的有机物经过高温裂解后产生的气泡无法及时逸出。
在回流区FLUX已经被消耗殆尽,锡膏的粘度发生了较大的变化,此时锡膏之中的FLUX发生裂解,导致高温裂解后的气泡无法及时的逸出,被包围在锡球中,冷却后就形成空洞现象。
目前,一般使用X-Ray设备进行检查空洞的面积,通过X-Ray都可以看到焊球的空洞分布状况。
只要有些器件空洞所占面积的比例不是很大,常常认为是符合接受标准标准(如IPC-A-610D 8.2.12.4),因此在检验时没有引起足够的重视。
在众多的空洞现象中发现,产生空洞现象与焊料本身的表面张力有着直接的联系。
锡膏的表面张力越大,高温裂解的气泡越难逸出焊料球,气泡被团团包围在锡球之中(无铅焊料的表面张力达到4.60×10-3 N/260 ℃),表面张力越小,高温裂解后的气泡就很容易逃出焊料球,被锡球团团包围的机率就相当小(有铅焊料的表面张力达到3。
80×10-3 N / 260 ℃,Sn63-Pb37,m.p为183 ℃)。
已经陷入高温裂解的气泡,在有铅焊料密度较大(约8.44 g/cm3)的情况之下,焊料中的合金在相互挤压下,有机物就会向外面逃脱,所以有机物残留在焊点中的机率是相当小的,但是无铅就完全不一样了。
比重不但比有铅小,而且无铅的表面张力又比有铅高出很多,同时熔点又比有铅高出34 ℃之多(Sn63-Pb37,熔点为183 ℃,SAC305熔点约为217 ℃),在种种环境不利的情况下,无铅焊料中的有机物就很难从焊球中分解出来,有机物常常被包围在焊球中,冷却后就会形成空洞现象。
从焊点的可靠度来讲,空洞现象会给焊点带来不可估计的风险,同时空洞现象比较严重的话,还影响焊点的电气连接,影响电路的畅通。
焊点空洞形成的原因

焊点空洞形成的原因哎,你说这焊点空洞,可真是个让人头疼的事儿。
我这一天天在车间里头转悠,看着那些焊点上的小空洞,心里头就跟猫爪子挠似的,痒痒得慌。
今儿咱们就聊聊这焊点空洞,到底是咋形成的。
你瞧,焊点空洞这事儿啊,说简单也简单,说复杂也复杂。
头一个原因,就是那助焊剂里头的有机物,一受热就分解,跟放鞭炮似的,“砰砰砰”地产生一堆气泡。
这些气泡要是不能及时排出去,等焊点一冷却,嘿,就成了空洞了。
你说这有机物产生的气体,它要是浮力小,比焊料的表面张力还小,那就只能被焊点给“吞”进去了,成了名副其实的“气泡馅儿饺子”。
再一个,焊接时间也得说说。
就像那Sn63-Pb37焊料,浸渍时间就短得跟眨巴眼似的,0.6秒,一眨眼就过去了。
还有那SnAgCu焊料,时间稍微长点,1.5秒,但在这短短的时间里,有机物热解产生的气体也是很难逃出去的,只能乖乖地被焊点“扣留”了。
锡膏里的水分,也是个不容小觑的角色。
那锡膏从冰箱里拿出来,得在室温下放四个钟头,跟咱们人一样,得缓缓,不能一下子就从冰箱里出来就干活。
不然啊,它吸了空气中的水分,到了焊接的时候,水分一蒸发,空洞就来了。
你说这锡膏,搅拌的时候还不能太使劲,时间也不能太长,得恰到好处,跟咱们做饭炒菜似的,火候得掌握好。
焊盘氧化物,这事儿也得提一提。
那PCB焊盘啊,要是表面氧化了,或者脏了,焊接后焊点上的空洞就多。
为啥呢?因为氧化程度越大,处理起来就越费劲,得用更强的活性剂才行。
你说这焊盘,就跟咱们的脸似的,得干净,才能焊出好焊点。
还有啊,焊点合金的晶体结构,要是不合理,焊接的时候也容易出空洞。
这就跟咱们盖房子似的,地基不稳,房子就容易出问题。
PCB 板的设计,要是出了问题,焊盘位置不对,间距不合适,那空洞也就跟着来了。
助焊膏的沉积量,也得刚刚好。
少了,焊接不充分,空洞就来了;多了,又容易桥接或者短路,真是让人头疼。
回流焊工艺,那温度曲线、升温速度,都得拿捏得恰到好处,不然焊点里头就容易出空洞。
BGA焊点的缺陷分析与工艺改进
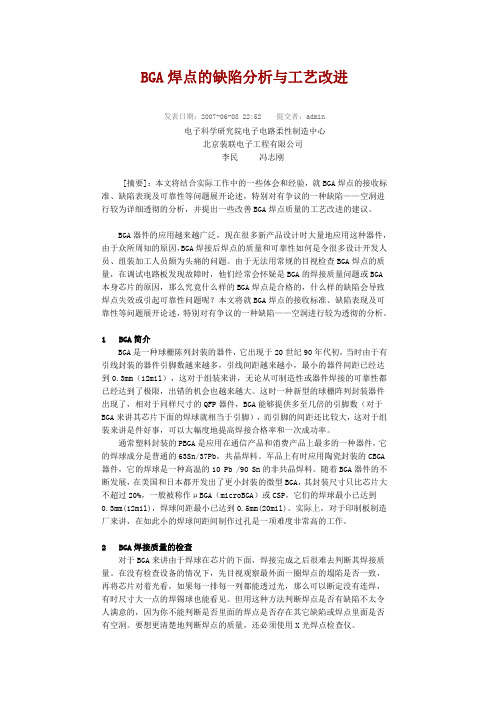
BGA焊点的缺陷分析与工艺改进发表日期:2007-06-08 22:52 提交者:admin电子科学研究院电子电路柔性制造中心北京装联电子工程有限公司李民冯志刚[摘要]:本文将结合实际工作中的一些体会和经验,就BGA焊点的接收标准、缺陷表现及可靠性等问题展开论述,特别对有争议的一种缺陷——空洞进行较为详细透彻的分析,并提出一些改善BGA焊点质量的工艺改进的建议。
BGA器件的应用越来越广泛,现在很多新产品设计时大量地应用这种器件,由于众所周知的原因,BGA焊接后焊点的质量和可靠性如何是令很多设计开发人员、组装加工人员颇为头痛的问题。
由于无法用常规的目视检查BGA焊点的质量,在调试电路板发现故障时,他们经常会怀疑是BGA的焊接质量问题或BGA 本身芯片的原因,那么究竟什么样的BGA焊点是合格的,什么样的缺陷会导致焊点失效或引起可靠性问题呢?本文将就BGA焊点的接收标准、缺陷表现及可靠性等问题展开论述,特别对有争议的一种缺陷——空洞进行较为透彻的分析。
1BGA简介BGA是一种球栅陈列封装的器件,它出现于20世纪90年代初,当时由于有引线封装的器件引脚数越来越多,引线间距越来越小,最小的器件间距已经达到0.3mm(12mil),这对于组装来讲,无论从可制造性或器件焊接的可靠性都已经达到了极限,出错的机会也越来越大。
这时一种新型的球栅阵列封装器件出现了,相对于同样尺寸的QFP器件,BGA能够提供多至几倍的引脚数(对于BGA来讲其芯片下面的焊球就相当于引脚),而引脚的间距还比较大,这对于组装来讲是件好事,可以大幅度地提高焊接合格率和一次成功率。
通常塑料封装的PBGA是应用在通信产品和消费产品上最多的一种器件,它的焊球成分是普通的63Sn/37Pb,共晶焊料。
军品上有时应用陶瓷封装的CBGA 器件,它的焊球是一种高温的10 Pb /90 Sn的非共晶焊料。
随着BGA器件的不断发展,在美国和日本都开发出了更小封装的微型BGA,其封装尺寸只比芯片大不超过20%,一般被称作μBGA(microBGA)或CSP,它们的焊球最小已达到0.3mm(12mil),焊球间距最小已达到0.5mm(20mil)。
BGA、QFN、CSP器件焊点空洞分析

空洞大 于2 %焊球X R y 线 图像 的面 积 。 5 — a射
以 上 IC中 只 是 提 到 B P GA空 洞 验 收 标 准 , 但 是 在 众 多
的 国际 大厂 中又 有许 多 厂家 是不 承认 此 标准 的 ,即比此 标
准 更 加 严 格 。 例 如 I M认 为 B B GA的 空 洞 面 积 不 可 超 过 1 % , 如 果 超 过 了 2 %就 会 影 响 焊 点 的 可 靠 度 , 影 响 焊 点 5 0
二、 空洞 的成 因与改 善
2 1助 焊 剂 活 性 的 强 弱 影 响 . 前 面 已 经 论 述 过 ,空 洞 现 象 的 产 生 主 要 是 助 焊 剂 中 的
逃脱 ,所 以有机 物残 留在焊点 中 的机率 是相 当小 的 ,但是
无 铅 就 完 全 不 一 样 了 。 比 重 不 但 比 有 铅 小 , 而 且 无 铅 的 表
的 电气 连 接 与 电 路 导 通 ,所 以 空 洞 现 象 必 须 引 起 S 业 界 MT
物 就 很 难 从 焊 球 中分 解 出来 , 有机 物 常 常被 包 围 在 焊球 中 ,冷 却后 就会 形 成空 洞现 象 。从 焊 点的 可靠 度 来讲 ,空 洞现 象 会给 焊 点抗 疲劳 性 带来 不可 估计 的 风险 ,比较 严重 的话 ,还影 响焊 点 的 电气连 接 与 电路导 通 ,所 以空洞 现 象 必须 引起S 业 界 人士 的高度重 视 。 MT
主 要 成 因是 F UX 的 有 机 物 经 过 高 湍 裂 解 后 产 生 的 气 泡 L 中
的时候 ,谈 到空 洞的验 收标 准 ,也表 示有 待完 善 。从IC— P A一 1 D版本 中的 一 些初 步 的 定 义 ( . .24表 面 安 装 阵 60 821 . 列 一 洞 】,我 们 可 以得 出 以下一 些 结 论 :从 设 计 上 减 少 空 空 洞 的 产 生 , 即焊 盘 上 的 微 孔 不 在 此 标 准 考 虑 的 范 围 之
6220主板BGA空洞分析报告

6220主板BGA空洞分析报告一、背景资料1、公司预引进新的检测设备X-RAY,外出考察设备供应商并携带我司生产的6220主板前往试样,7月4日上午带回了实照的X-RAY图片,(图1)发现空洞面积过大,于是引发对目前回流焊接过程中对空洞的关注。
Void Area BGA Void(图1)2、为了进一步验证BGA的空洞面积大小问题,是否存在批量不达标的品质隐患,下午又组织去拍了X-RAY图片,并对采用不同锡膏品牌生产的主板进行了对比。
采用SP锡膏焊接(图2),采用YT锡膏焊接(图3)。
BGA Void Void Area(图2)BGA VoidVoid Area(图3)二、 看图解析1、 从三组图片我们不难看出,不管SP 锡膏还是YT 锡膏,BGA 存在的空洞数量和面积都相差不多,空洞数量在20-24个之间(CPU 总球数为264个),SP 空洞最大面积38.73%,YT 空洞最大面积38.00%,空洞直径0.22MM 。
2、 从空洞的分布范围来看,使用两种不同品牌的锡膏焊接后,BGA 空洞存在的位置基本相同,而空洞面积超大的几个点也主要集中在:E14,E15,Void DiameterK14,M4,O7,O8,P7位置,见(图4)。
(图4)BGA 球体分布图三、原因分析1、在分析之前我们先了解下空洞是如何产生的。
A、从锡球中带来的原有空洞,在锡球的制造工艺中已经形成;B、焊盘中的盲孔的设计肯定会造成焊接点中的一些空洞,来从堵塞的通孔的空气膨胀,在焊盘下熔化的锡球内形成空洞。
C、PCB与锡球界面附近的空洞通常是由不适当的回流温度曲线造成的,在回流焊接中助焊剂蒸发,在熔化的焊锡固化期间被夹陷所引起。
D、OSP膜过厚或焊盘下的污染也可能造成界面的空洞。
我们可以通过逐步排除的方法来进行验证。
第一、查看仓库BGA来料情况,全部为真空防静电袋包装,现有SMT车间环境满足包装上的使用注意事项,拆封条件下满足48小时内贴装,BGA吸湿和锡球本身有空洞的可能性很小,可以排除A项原因。
bga焊接的空洞率

bga焊接的空洞率
BGA焊接的空洞率是指焊点中存在空洞的比例。
空洞是由于焊接时,焊料没有完全填满焊盘与焊球之间的空隙,造成焊点中的空隙。
空洞率的高低会影响焊接的质量和可靠性。
一般来说,较低的空洞率会提高焊点的连接强度和可靠性,而较高的空洞率则可能导致焊点的强度下降,从而影响整体的焊接质量。
空洞率受多种因素影响,例如焊接温度、焊料的流动性、焊盘与焊球的匹配性等。
为降低空洞率,可以采取一些措施,如焊接温度的控制、焊料的优化选择、焊接过程的调整等。
空洞率的具体数值要根据具体情况来定,一般来说,较低的空洞率在1%以下被认为是较好的,而超过5%的空洞率被认为是不可接受的。
具体的标准可以根据相关行业的要求和标准来确定。
bga底部焊盘空洞标准

bga底部焊盘空洞标准
BGA(Ball Grid Array)是半导体芯片制造中常见的电子封装技术。
BGA底部焊盘空洞标准是在BGA制造过程中,对焊盘设计的标准要求。
以下将分步骤阐述BGA底部焊盘空洞标准。
一、确定空洞的直径和深度
在制造BGA的过程中,首先需要确定空洞的直径和深度。
一般来说,空洞的直径应该小于焊盘的直径,以防止焊盘或者连接器的插针
掉进空洞导致连接不上。
同时,空洞的深度也应该不超过焊盘的厚度,以保证插针能够插入焊盘,达到连接的目的。
二、确定空洞的数量和分布
BGA的底部焊盘数量通常很多,因此需要确定空洞的数量和分布。
一般来说,空洞的数量应该根据焊盘的大小和密度来确定。
在分布上,应该遵循均匀分布的原则,而不是集中在某个区域。
三、确定空洞的形状和位置
空洞的形状和位置也是BGA底部焊盘空洞标准的重要组成部分。
一般来说,空洞的形状应该是圆形或者正方形,以减小制造难度和成本。
同时,空洞的位置应该在焊盘的中心,以达到更好的焊接效果。
四、确定焊盘和空洞的间距
BGA底部焊盘与空洞之间的间距也是需要考虑的因素。
过小的间
距可能导致焊接不牢固,过大的间距则会影响电路的传输性能。
因此,应该确定一个适当的间距,以保证焊盘和空洞之间的接触面积。
总之,BGA底部焊盘空洞标准是制造BGA的一个重要因素。
在设
计焊盘的空洞时,应该根据均匀分布、直径、深度、形状、位置和间
距等因素来确定标准要求,以确保BGA的质量和可靠性。
混装条件下BGA焊点空洞问题
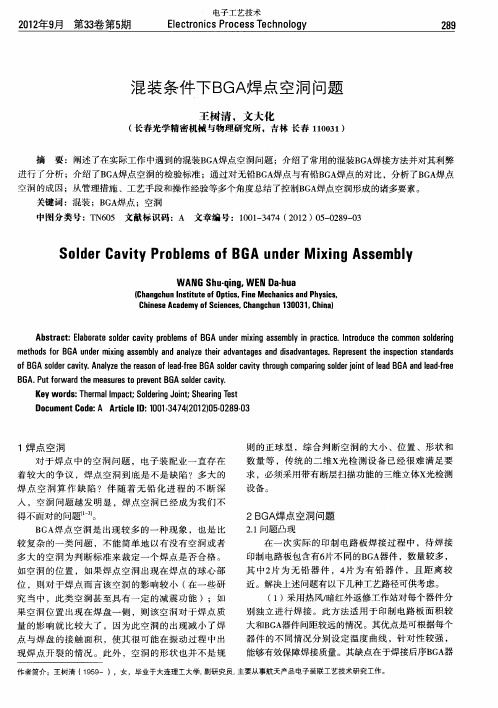
则 的正球 型 ,综合 判断 空洞 的大 小 、位 置 、形状 和
数 量等 ,传统 的 二维 x 光检 测 设备 已经 很 难满 足要
求 ,必须采 用带有断层扫描 功能的三维立体x 光检测
设备 。
焊 点 空 洞算 作 缺 陷 ? 伴 随 着 无 铅 化 进 程 的不 断 深 入 ,空洞 问题越 发 明显 ,焊 点空 洞 已经成 为我 们不
究 当 中 ,此 类空 洞甚 至具 有一 定 的减震 功 能 );如
在一 次实 际 的印制 电路 板焊 接过 程 中 ,待 焊接 印制 电路板包含有 6 片不 同的B A G 器件 ,数 量较多 , 其 中2 为无 铅 器 件 ,4 为 有 铅 器 件 ,且 距 离 较 片 片
近 。解决上述 问题有 以下几种工艺路径 可供考虑 。 ( )采用热风/ 1 暗红外返修 工作 站对每个器件分
摘
要 :阐述 了在实 际工作 中遇到 的混装B A G 焊点 空洞问题 ;介绍 了常用 的混装B A G 焊接方法并对其利弊
进行 了分 析 ;介绍 了B A G 焊点 空洞的检验标准 ;通过对无铅B A G 焊点 与有铅 B A G 焊点 的对 比 ,分析 了B A G 焊点 空洞 的成 因 ;从 管理措施 、工艺手段和操作经验等多个 角度 总结了控制B A G 焊点空洞形成 的诸多要素 。 关键词 :混装 ;B A G 焊点 ;空洞
o G o e cv yA a z te esn fed r G o e cv y h uh o p rg o ejn o I d G n a-e f Asl r ai. nl e h ao a-e B Asl r ai r g m a n l ro t fe Aaded r B d t y r o l fe d tto c i s d i a B l fe
BGA 空洞

BGA中的空洞IPC-7095标准“实现BGA的设计和组装过程”详述了实现BGA、细间距BGA(FBGA)的设计及组装技术。
BGA和FBGA在现代技术及元器件中的影响越来越大。
本文将就BGA如何检查、返修及可靠性等问题展开论述。
本文主要针对从事电子组装、检查及返修过程的管理人员、设计人员及工程师,目的是能够一些提供有实用价值的实践经验和体会。
目前尚有一个没有解决的问题是关于BGA中空洞的接收标准。
空洞问题并不是BGA独有的。
在通孔插装及表面贴装的焊点中也可以见到空洞。
但是,表面贴装及通孔插装元件的焊点通常都可以用目视检查看到空洞,而不用X射线。
在BGA中,由于所有的焊点隐藏在封装的下面,只有使用X射线才能检查到这些焊点。
当然,用X射线不仅可以检查BGA的焊点,所有的各种各样的焊点都可以检查,使用X射线,空洞很容易就可以检查出来。
那么空洞一定对BGA的可靠性有负面影响吗?不一定。
有些研究人员甚至说空洞对于可靠性是有好处的。
IPC-7095委员会认为有些尺寸非常小,不能完全消除的空洞可能对于可靠性是有好处的,但是多大的尺寸应该有一个界定的标准。
空洞的来源及位置在BGA的焊点检查中在什么位置能发现空洞呢?BGA的焊球可以分为三个层,一个是元件层(靠近BGA元件的基板),一个是焊盘层(靠近PCB的基板),再有一个就是焊球的中间层。
根据不同的情况,空洞可以发生在这三个层中的任何一个层。
BGA焊球中可能本身在焊接前就带有空洞,那么在再流焊接过程完成后就形成了空洞。
这些空洞可能是由于焊球制作工艺中就引入了,或是组装工艺参数或材料的问题导致的。
电路板的设计也是形成空洞的一个主要原因。
例如,把过孔设计在焊盘的下面,在焊接的过程中,外界的空气通过过孔进入熔溶状态的焊球,焊接完成冷却后焊球中就会留下空洞。
焊盘层中发生的空洞可能是由于焊盘上面印刷的焊膏中的助焊剂在再流焊接过程中挥发,气体从熔溶的焊料中逸出,冷却后就形成了空洞。
BGA空洞的形成机理
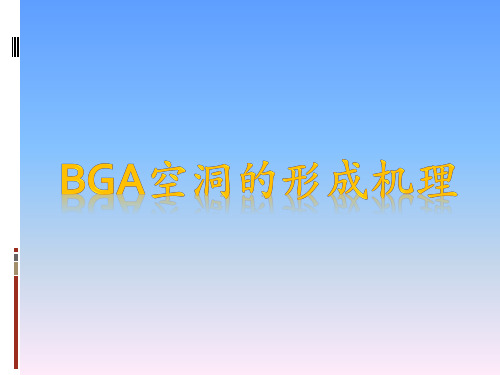
从本质上来说,任何 SMT焊点中出现空洞都 是因为锡膏在熔融时, 锡膏中包裹的气体没有 被及时排放出去所造成 的,影响BGA焊球空洞 形成的原因是多方面的, 右侧是常见的主要形成 机理:
1.锡膏 2.炉温曲线 3.PCB焊盘的表面处理方式 4.回流的气氛 5.焊盘微孔、盘中孔设计 6.芯片的封装形式 7.PCB焊盘或物料的氧化
空洞的形成机理1-----锡膏
A.在SMT工艺中,锡膏形成空洞的直 接原因是锡膏中的助焊剂在回流过 程经高温裂解后产生气泡 很难逸出, 导致气体被包裹在合金焊料中从而 形成空洞。 B.锡膏影响BGA空洞形成的另一个因 素是锡膏在空气中的暴露时间,随 着锡膏暴露时间的增长,使锡膏氧 化和 吸潮,出现空洞的机率就更大。 C.锡膏中锡粉的尺寸对空洞的形成也 有一定的影响,研究表明随着锡粉 直径的减小,空洞比例有轻微的上 升趋势,原因在于随着锡膏颗粒尺 寸的减小,锡粉接触到空气的整体 表面积增大,使得氧化面积相应增 加,从而产生更多空洞。
空洞的形成机理7----- PCB或物料氧化
PCB焊盘表面氧化和脏污程度越高, 焊接后PCBA焊点产生的空洞就越 多。因为焊盘氧化程度越大,需要 更强的活性剂来处理焊接物体表面 的氧化物。特别是对于OSP(有机溶 剂防腐剂)表面处理,OSP垫上的一 层有机保护膜很难被去除。如果不 能及时去除焊盘表面的氧化物,氧 化物就会留在被焊物体表面。此时 氧化物会阻止合金粉与被焊金属表 面接触,从而形成不良出现拒焊现 象。表面氧化严重,高温分解的有 机物气体会隐藏在合金粉中。同时 无铅焊料表面张力大,合金比重也 比较大,气体很难逸出,故气体会 被包围在合金粉中。
空洞的形成机理2-----炉温曲线
当使用的Profile曲线在熔点以上的 时间太长时(通常217 ℃以上的时 间应设为30 s~60 s),会让助焊 剂中可以挥发的物质消耗殆尽,进 而使助焊剂的粘度发生变化或者助 焊剂被烧干,甚至裂解之后不能移 动。这样气体就会被包裹从而无法 移动,导致空洞的产生。
BGA焊点空洞问题分析

K e y Wo r d s :V o i d s ; S o l d e r ; R e l i a b i l i t y ; B G A D o c u me n t C o d e : A A r t i c l e l D : 1 O 0 1 - 3 4 7 4 , 2 0 1 3 , 0 4 . 0 2 2 3 - 0 4
1 . 1 B GA 封装的优点 ( 1 )I / o引脚数较 多 ,B G A 封装器件 的[ / 0数主 要 由封装 体 的尺寸 和焊 球 间距决 定 ,由于B GA 封 装
的焊 球是 以 阵列形 式排 布在 封 装基 板下 面 ,故可 极 大地提高器件 的I / 0数 ;
( 3)对 温度 / 湿 度敏 感 ,B G A元件 是一 种高度 的温 度 和 湿 度 敏 感 器 件 ,所 以BGA必 须 在恒 温 干
摘 要 :B G A 器件 已经广泛应用 于各个领域 ,首先对B G A 器件进行 了简介 ,在给出其焊点质量检验合格判据 后 ,针对B G A 组装过程 中常见现象空洞 ,分析了空洞产生 的机理 ,并进一步说明空洞对焊点可靠性 的影响 。最后 根据空洞产生机理提出了一些措施以减少 和改善空洞。
电路 的性能 ;
是 美 国Mo t o r o l a 公司 开 发的 ,它 是在 印 制基板 的 背
面按 陈列 方式 制作 出球 形 凸点 用 以代 替 引脚 ,在 印 制基板 的正面装 配L s I 芯 片 ,然后进行 封装 。根据不 同的分 类依 据 ,BG A封装芯 片 可以有 不 同的种 类 , 根 据衬 底的不 同 ,有塑料 B G A、陶瓷B G A ̄ I 3 玻 璃 纤 维 环氧树 J  ̄BG A 等 ;根 据 内部芯 片和衬 底 连接 的不
BGA焊点空洞的形成与预防

BGA焊点空洞的形成与预防BGA空洞(图1、图2)会引起电流密集效应,降低焊点的机械强度。
因此,从可靠性角度考虑,应减少或降低空洞。
那么,如何可以降低BGA空洞?要回答这个问题,我们有必要探索一下空洞的形成原因。
BGA空洞的形成原因有多方面,如:焊点合金的晶体结构、PCB 板的设计、印刷时,助焊膏的沉积量、所使用的回流焊工艺等、焊球在制作过程中夹杂的空洞。
下面我们从助焊膏的层面对GBA焊点空洞的形成与防止作一些阐述,以期减少BGA焊点空洞的形成数量。
1炉温曲线设置不当1)表现在在升温段,温度上梯度设置过高,造成快速逸出的气体将BGA掀离焊盘;2)升温段的持续时间不够长,当升温度结束时,本应挥发的气体还未完全逸出,这部分的气体在回流阶段继续逸出,影响助焊体系在回流阶段发挥作用。
2助焊膏溶剂搭配不当主要表现在:1)在升温阶段,快速逸出的气体将BGA 撑起,造成错位与隔阂;2)在回流阶段,仍有相当数量的气体从助焊膏体系中逸出,但受限于BGA与焊盘间的狭小空间,这些挥发气体无法顺畅地通过这个空间逸出,致使其挤压熔融的焊点。
3助焊膏润湿焊盘能力不足助焊膏对焊盘的润湿表现在它对焊盘的清洁作用。
因助焊膏润湿能力不足,无法将焊盘上的氧化层去除,或去除效果不理想,而造成虚焊。
助焊膏对BGA焊球的润湿能力不足:与助焊膏对焊盘的润湿能力不足相似,只不过,因焊球的合金类型不同,BGA上的氧化物的电动势也就不同,这样就要求助焊膏具备适应去除不同合金类型的氧化物的能力,若不匹配,则造成对BGA 焊球的润湿能力不足,导致空洞。
4回流阶段助焊膏体系的表面张力过高主要是所用的载体(主要是松香)选择不当,此外表面活性剂的选择也有关系。
我们在实验过程中发现,某些活性剂不仅可以降低助焊膏体系的表面张力,也可显著降低熔融合金的表面张力。
松香与表面活性剂的有效配合可使润湿性能充分发挥。
助焊膏体系的不挥发物含量偏高不挥发物含量偏高导致BGA焊球的熔化塌陷过程中BGA下沉受阻,造成不挥发物侵蚀焊点或焊点包裹不挥发物。
bga焊点的缺陷分析与工艺改进(doc11页)
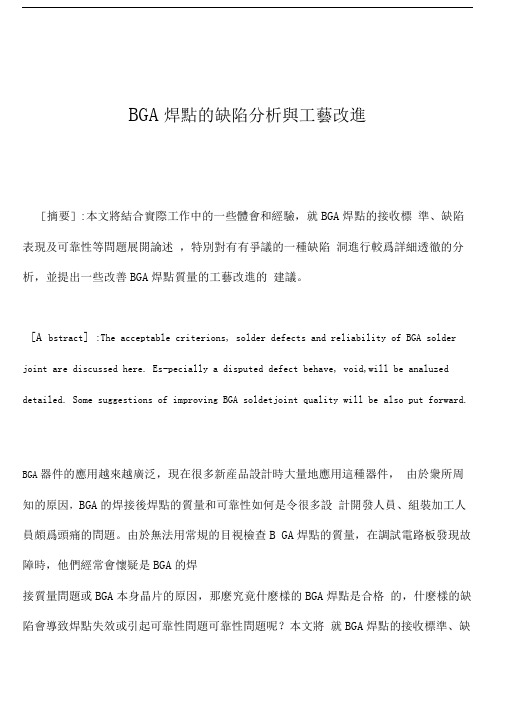
BGA焊點的缺陷分析與工藝改進[摘要]:本文將結合實際工作中的一些體會和經驗,就BGA焊點的接收標準、缺陷表現及可靠性等問題展開論述,特別對有有爭議的一種缺陷洞進行較爲詳細透徹的分析,並提出一些改善BGA焊點質量的工藝改進的建議。
[A bstract] :The acceptable criterions, solder defects and reliability of BGA solder joint are discussed here. Es-pecially a disputed defect behave, void,will be analuzed detailed. Some suggestions of improving BGA soldetjoint quality will be also put forward.BGA器件的應用越來越廣泛,現在很多新産品設計時大量地應用這種器件,由於衆所周知的原因,BGA的焊接後焊點的質量和可靠性如何是令很多設計開發人員、組裝加工人員頗爲頭痛的問題。
由於無法用常規的目視檢查B GA焊點的質量,在調試電路板發現故障時,他們經常會懷疑是BGA的焊接質量問題或BGA本身晶片的原因,那麽究竟什麽樣的BGA焊點是合格的,什麽樣的缺陷會導致焊點失效或引起可靠性問題可靠性問題呢?本文將就BGA焊點的接收標準、缺陷表現及可靠性等問題展開論述,特別對有爭議的一種缺陷空洞進行較爲透徹的分析。
1.BGA簡介BGA是一種球柵陳封裝的器件,它出現於20世紀90年代初,當時由於有引線封裝的器件引腳數越來越多,引線間距越來越小,最小的器件間距已經達到0.3mm(12mil), 這對於組裝來講,無論從可製造性或器件焊接的可靠性都已經達到了極限,出錯的機會也越來越大。
這時一種新型的球柵陣列封裝器件出現了,相對於同樣尺寸的QFP器件,BGA能夠提供多至幾倍的引腳數(對於BGA來講其晶片下面的焊球就相當於引腳)而引腳的間距還比較大,這對於組裝來講是件好事,可以大幅度地提高焊接合格率和一次成功率。
降低BGA空洞的方法
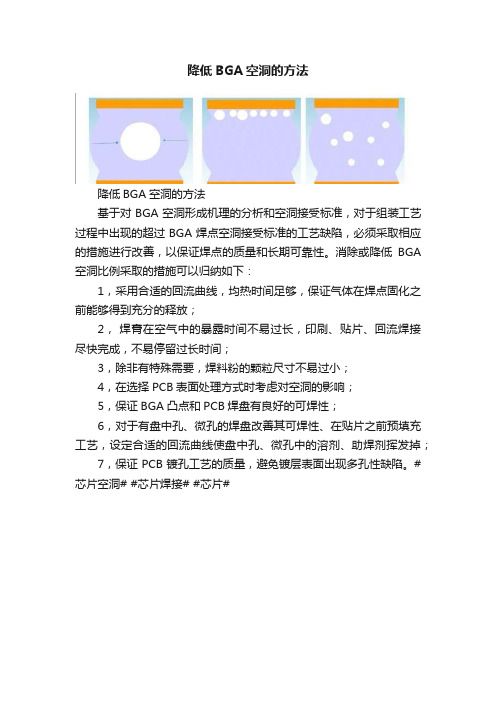
降低BGA空洞的方法
降低BGA空洞的方法
基于对BGA空洞形成机理的分析和空洞接受标准,对于组装工艺过程中出现的超过BGA焊点空洞接受标准的工艺缺陷,必须采取相应的措施进行改善,以保证焊点的质量和长期可靠性。
消除或降低BGA 空洞比例采取的措施可以归纳如下:
1,采用合适的回流曲线,均热时间足够,保证气体在焊点固化之前能够得到充分的释放;
2,焊膏在空气中的暴露时间不易过长,印刷、贴片、回流焊接尽快完成,不易停留过长时间;
3,除非有特殊需要,焊料粉的颗粒尺寸不易过小;
4,在选择PCB表面处理方式时考虑对空洞的影响;
5,保证BGA凸点和PCB焊盘有良好的可焊性;
6,对于有盘中孔、微孔的焊盘改善其可焊性、在贴片之前预填充工艺,设定合适的回流曲线使盘中孔、微孔中的溶剂、助焊剂挥发掉;
7,保证PCB镀孔工艺的质量,避免镀层表面出现多孔性缺陷。
#芯片空洞# #芯片焊接# #芯片#。
通孔焊点空洞X—RAY标准
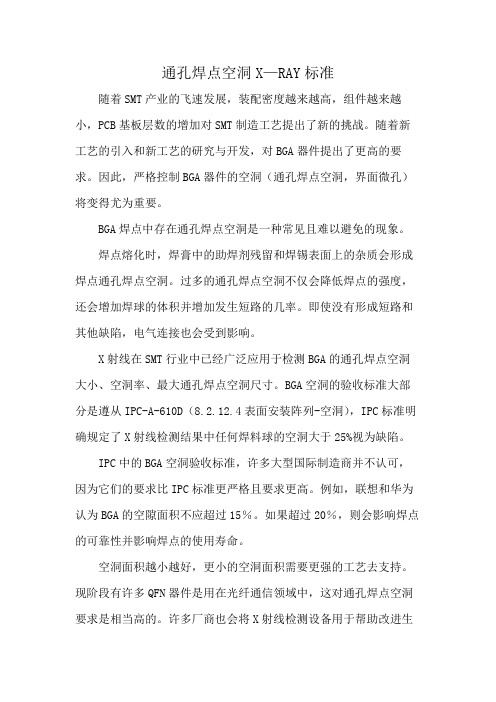
通孔焊点空洞X—RAY标准随着SMT产业的飞速发展,装配密度越来越高,组件越来越小,PCB基板层数的增加对SMT制造工艺提出了新的挑战。
随着新工艺的引入和新工艺的研究与开发,对BGA器件提出了更高的要求。
因此,严格控制BGA器件的空洞(通孔焊点空洞,界面微孔)将变得尤为重要。
BGA焊点中存在通孔焊点空洞是一种常见且难以避免的现象。
焊点熔化时,焊膏中的助焊剂残留和焊锡表面上的杂质会形成焊点通孔焊点空洞。
过多的通孔焊点空洞不仅会降低焊点的强度,还会增加焊球的体积并增加发生短路的几率。
即使没有形成短路和其他缺陷,电气连接也会受到影响。
X射线在SMT行业中已经广泛应用于检测BGA的通孔焊点空洞大小、空洞率、最大通孔焊点空洞尺寸。
BGA空洞的验收标准大部分是遵从IPC-A-610D(8.2.12.4表面安装阵列-空洞),IPC标准明确规定了X射线检测结果中任何焊料球的空洞大于25%视为缺陷。
IPC中的BGA空洞验收标准,许多大型国际制造商并不认可,因为它们的要求比IPC标准更严格且要求更高。
例如,联想和华为认为BGA的空隙面积不应超过15%。
如果超过20%,则会影响焊点的可靠性并影响焊点的使用寿命。
空洞面积越小越好,更小的空洞面积需要更强的工艺去支持。
现阶段有许多QFN器件是用在光纤通信领域中,这对通孔焊点空洞要求是相当高的。
许多厂商也会将X射线检测设备用于帮助改进生产工艺,降低研发成本,通过直观的检测图像和软件分析能力,帮助用户提高工艺改进效率,加快研发升级。
X-RAY也可以检测回流焊形成的通孔焊点空洞。
BGA焊球的制造过程与回流焊相似。
因此,如果BGA制造商不严格按照BGA焊球工艺进行控制,则焊球本身会存在大量空洞,这样还没有过回流焊之前就已经产生了空洞,回流焊之后产生空洞就可想而知了。
如果不能很好地控制BGA回流工艺,则焊球空隙的比例将增加,并且焊点的机械性能和电气性能将受到极大影响,特别是机械强度。
BGA空洞改善之一
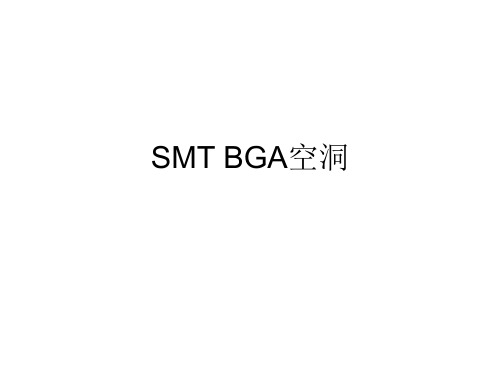
空洞分析鱼骨图
空洞会在何种合金中出现
• 共晶焊料63Sn/37Pb的BGA最易出现空洞,而成分为 10Sn/90Pb的非共晶高熔点焊球的BGA(CBGA),熔点 为302℃,一般基本上没有空洞,这是因为在焊膏熔化的 再流焊接过程中BGA上的焊球不熔化;
面对空洞我们该如何解决?
• 对于有存在空洞问题的产品对其不良位置的材料进行检查确认其中是 否存在空洞现象; • 焊盘表面的处理情况进行确认;即对每批次来料得PCB进行可焊性测 试 • 保证焊膏充分搅拌且搅拌均匀 SIC中定义搅拌时间和方法
形成空洞的原因:
• BGA焊球本身可能在焊接前就带有空洞,这样在再流焊过程完成后就 形成了空洞。 • 路板的设计也是形成空洞的一个主要原因。例如,把过孔设计在焊盘 的下面,在焊接的过程中,外界的空气通过过孔进入熔溶状态的焊球, 焊接完成冷却后焊球中会留下空洞。 • 焊盘的镀层不好或焊盘表面有污染; • 不合理的温度曲线;
面对空洞我们该如何解决
• 锡膏必须回温4小时,防止锡膏本身吸潮,水分增加,炉后产生气泡 • 锡膏印刷后必须半小时贴片,2小时过炉,防止锡膏暴露空气中吸收 水分,炉后产生气泡 • 锡膏印刷后,对BGA的厚度进行量测,保持锡膏厚度饱满,增加锡膏 与BGA 锡球的接触面,防止间隙过大,产生空气,过炉后出现气泡
面对空洞我们该如何解决
• 需要过两次回流焊的产品 不单单要控制第一面得回流曲线在生产第二面时对温度曲 线得管控同样必须依照规定执行;防止在第二面的焊接时 产生空洞现象; 建议生产第二面时采用夹具对BOT SIDE得BGA进行保护 降低其本身承受的温度;
工艺上的困难
• 采用降低温度与回流时间的方法进行处理BGA空洞问题时必须在实际 生产中监控焊点的质量特别关注冷焊虚焊等问题; • 63/37的焊料熔点为183℃通常超过该温度焊料就会融化完成焊接但由 于产品的复杂性与多样化的原因;因此对于同一个产品当出现冷热点温 差过大时必须注意工艺上的控制; 如:冷点为大的电容;热点为BGA,且BGA中存在空洞的问题,那么就 需要采取使用夹具对热点的温度降低,保证工艺上的可行性;
为什么会有BGA焊点空洞
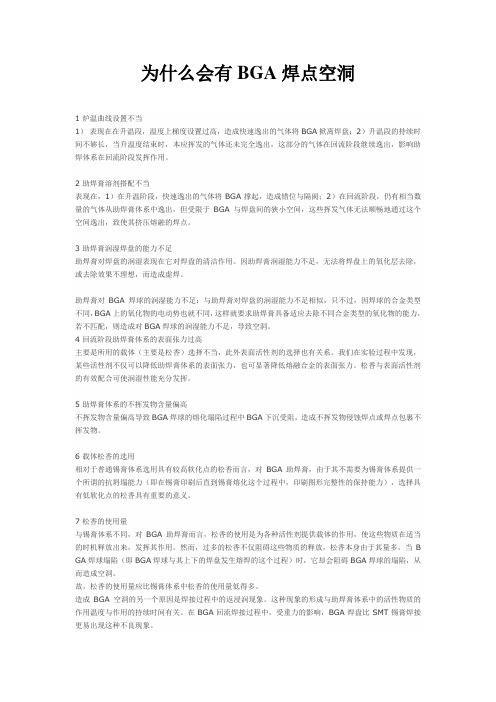
为什么会有BGA焊点空洞1 炉温曲线设置不当1)表现在在升温段,温度上梯度设置过高,造成快速逸出的气体将BGA掀离焊盘;2)升温段的持续时间不够长,当升温度结束时,本应挥发的气体还未完全逸出,这部分的气体在回流阶段继续逸出,影响助焊体系在回流阶段发挥作用。
2 助焊膏溶剂搭配不当表现在,1)在升温阶段,快速逸出的气体将BGA 撑起,造成错位与隔阂;2)在回流阶段,仍有相当数量的气体从助焊膏体系中逸出,但受限于BGA与焊盘间的狭小空间,这些挥发气体无法顺畅地通过这个空间逸出,致使其挤压熔融的焊点。
3 助焊膏润湿焊盘的能力不足助焊膏对焊盘的润湿表现在它对焊盘的清洁作用。
因助焊膏润湿能力不足,无法将焊盘上的氧化层去除,或去除效果不理想,而造成虚焊。
助焊膏对BGA焊球的润湿能力不足:与助焊膏对焊盘的润湿能力不足相似,只不过,因焊球的合金类型不同,BGA上的氧化物的电动势也就不同,这样就要求助焊膏具备适应去除不同合金类型的氧化物的能力,若不匹配,则造成对BGA焊球的润湿能力不足,导致空洞。
4 回流阶段助焊膏体系的表面张力过高主要是所用的载体(主要是松香)选择不当,此外表面活性剂的选择也有关系。
我们在实验过程中发现,某些活性剂不仅可以降低助焊膏体系的表面张力,也可显著降低熔融合金的表面张力。
松香与表面活性剂的有效配合可使润湿性能充分发挥。
5 助焊膏体系的不挥发物含量偏高不挥发物含量偏高导致BGA焊球的熔化塌陷过程中BGA下沉受阻,造成不挥发物侵蚀焊点或焊点包裹不挥发物。
6 载体松香的选用相对于普通锡膏体系选用具有较高软化点的松香而言,对BGA助焊膏,由于其不需要为锡膏体系提供一个所谓的抗坍塌能力(即在锡膏印刷后直到锡膏熔化这个过程中,印刷图形完整性的保持能力),选择具有低软化点的松香具有重要的意义。
7 松香的使用量与锡膏体系不同,对BGA助焊膏而言,松香的使用是为各种活性剂提供载体的作用,使这些物质在适当的时机释放出来,发挥其作用。
- 1、下载文档前请自行甄别文档内容的完整性,平台不提供额外的编辑、内容补充、找答案等附加服务。
- 2、"仅部分预览"的文档,不可在线预览部分如存在完整性等问题,可反馈申请退款(可完整预览的文档不适用该条件!)。
- 3、如文档侵犯您的权益,请联系客服反馈,我们会尽快为您处理(人工客服工作时间:9:00-18:30)。
电子产品设计中的bga焊点空洞问题详解
随着电子技术的发展,用户对电子产品要求的进一步提高,电子产品朝小型化、多功能化方向发展;这就要求电子元件朝着小型化、密集与高集成化发展。
BGA具备上述条件,所以被广泛地应用,特别是高端电子产品。
BGA元件进行焊接时,会不可避免的产生空洞;空洞对BGA焊点造成的影响会降低焊点的机械强度,影响焊点的可靠性与寿命;所以必须控制空洞现象的产生。
通过X-Ray检查出的空洞现象,如图1、2。
图(1):X-RAY垂直BGA面检测空洞图(2):BGA面倾斜X-RAY检测空洞
1 空洞产生机理:
1.1 空洞形成的机理:
材料中的湿气(水分)和锡膏中的有机物(助焊剂等)经过高温产生气体,BGA焊点形成前没有很好的排出,气体被包围在合金粉末中形成空洞。
空洞切片图
1.2 BGA焊球层的组成:
BGA焊球层可分为三层,一层是组件层(靠近BGA组件的基板),一层是焊盘层(靠近PCB的基板),再有一层就是焊球的中间层。
根据不同的情况,空洞可以发生在这三层中的任何一层。
空洞对焊球危害最大的是组件层与焊盘层,因为它们直接影响焊球与PCB 和BGA本体的连接;见下图。
BGA焊球结构图
2 空洞的验收标准
空洞中的气体存在可能会在热循环过程中产生收缩和膨胀的应力,作用在空洞存在的地方便会形成应力集中点,并有可能成为产生应力裂纹的根本原因。