摩托车疲劳耐久台架试验与寿命预测研究
车架台架疲劳试验方法研究
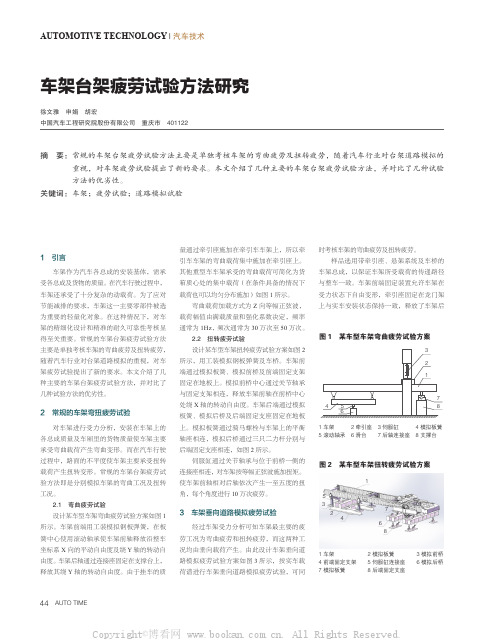
量通过牵引座施加在牵引车车架上,所以牵 引车车架的弯曲载荷集中施加在牵引座上。 其他重型车车架承受的弯曲载荷可简化为货 箱质心处的集中载荷(在条件具备的情况下 载荷也可以均匀分布施加)如图 1 所示。
弯曲载荷加载方式为 Z 向等幅正弦波, 载荷幅值由满载质量和强化系数决定,频率 通常为 1Hz,频次通常为 30 万次至 50 万次。
1 车架总成 2 车架前端固定装置 3 龙门架及牵引座固定装置 4 伺服缸
图 4 载荷谱截取图
(Ch66-Ch70 依次为左前轮、右前轮、左中轮、右 中轮、左后轮、右后轮相对于车架的位移)
图 5 载荷谱截取图
图 6 某车型车架多轴道路模拟试验方案
1 车架总成 2 车架前端固定装置 3 龙门架及牵引座固定装置 4 轴头复合加载工装 5 一号加载单元 6 二号加载单元
2.2 扭转疲劳试验 设计某车型车架扭转疲劳试验方案如图 2 所示,用工装模拟钢板弹簧及车桥。车架前 端通过模拟板簧、模拟前桥及前端固定支架 固定在地板上。模拟前桥中心通过关节轴承 与固定支架相连,释放车架前轴在前桥中心 处绕 X 轴的转动自由度。车架后端通过模拟 板簧、模拟后桥及后端固定支座固定在地板 上。模拟板簧通过骑马螺栓与车架上的平衡 轴座相连,模拟后桥通过三只二力杆分别与 后端固定支座相连,如图 2 所示。 伺服缸通过关节轴承与位于前桥一侧的 连接座相连,对车架按等幅正弦波施加扭矩。 使车架前轴相对后轴依次产生一至五度的扭 角,每个角度进行 10 万次疲劳。
3 车架垂向道路模拟疲劳试验
经过车架受力分析可知车架最主架垂向道 路模拟疲劳试验方案如图 3 所示,按实车载 荷谱进行车架垂向道路模拟疲劳试验,可同
时考核车架的弯曲疲劳及扭转疲劳。 样品选用带牵引座、悬架系统及车桥的
台架耐久性试验全周期振动监测方法研究及应用
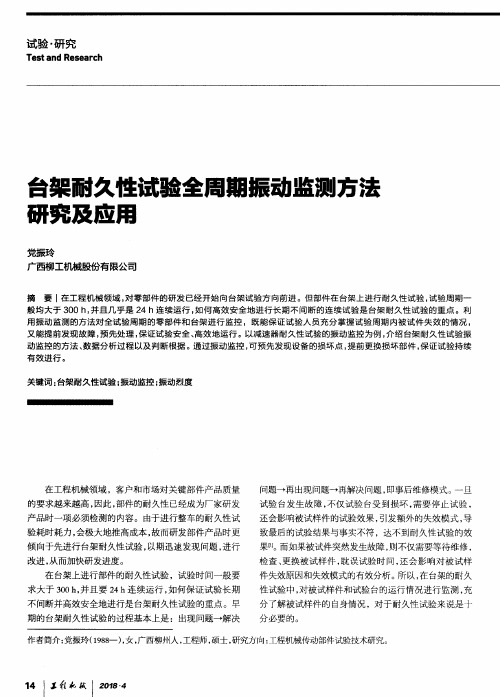
在工程机械领域 ,客户和市场对关键部件产品质量 的要求越来越高 ,因此 ,部件的耐久性已经成为厂家研发 产 品时 一 项必 须 检 测的 内 容 。由于 进行 整 车 的耐 久 性试 验耗时耗力 ,会极大地推高成本 ,故而研发部件产品时更 倾向于先进行 台架耐久性试验 ,以期迅速发现问题 ,进行 改进 ,从而加快研发进度。
2
采集系统
LMS Scadas Mobile/
Crystal instruments
3 数据分析软件
,
同时刻的相互依赖关系,其定义式为:R (z)=lim I x(t)x
f— + ∞
U
(什r)也。振动信号的频域分析 ,广泛采用快速傅里叶分析
∞
方法(FFT),时域函数 x(t)的傅里叶变换为 (厂)=I
表 1 振动监控主 要仪器设备
序号 1
仪器名称 加速度传感器
规 格型号 单 向、三 向加速度传感器
作者简介 :党振玲 (1988一 ),女 ,广西柳州人 ,工程师 ,硕士 ,研究方 向:工程机械传动部件试验技术研究 。 14 Βιβλιοθήκη 工霏表械I 20仔4 杠 拭
第 49卷 I第 4期
总第 534期
运用现代测试技术 ,测量并监视伴随试验 台架耐久 性试验过程 中的振动参量,再利用信号分析与数据处理 技术 ,对振动信息进行分析处理 ,建立动态信息与设备故 障之 间的联系 ,就可以建立一个台架耐久性试验的故障 监测 与诊断体系嚼,从而在长时间的试验过程 中及时有效 地发现问题 ,排查问题 ,保证试验安全、高效进行。本文将 以减速器台架耐久性试验为例,介绍振动监测方法在台 架耐 久性 试验 中 的具 体应 用 。
某摩托车结构疲劳寿命分析
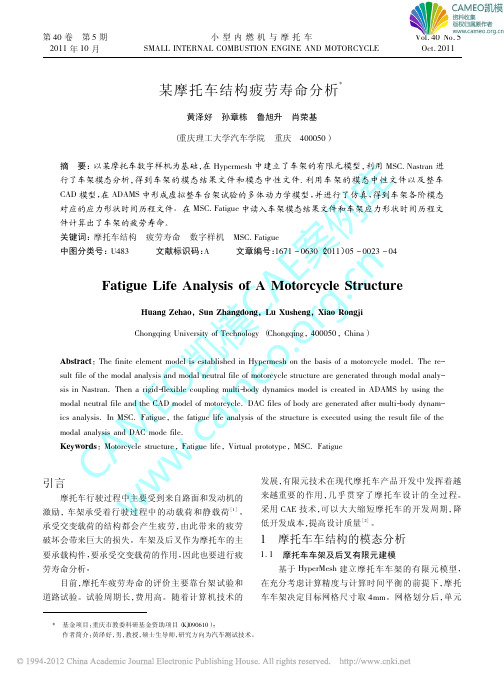
C A M E O 凯模C A E 案例库w w w .c a m e o .o r g .c n 某摩托车结构疲劳寿命分析*黄泽好孙章栋鲁旭升肖荣基(重庆理工大学汽车学院重庆400050)摘要:以某摩托车数字样机为基础,在Hypermesh 中建立了车架的有限元模型,利用MSC.Nastran 进行了车架模态分析,得到车架的模态结果文件和模态中性文件.利用车架的模态中性文件以及整车CAD 模型,在ADAMS 中形成虚拟整车台架试验的多体动力学模型,并进行了仿真,得到车架各阶模态对应的应力形状时间历程文件。
在MSC.Fatigue 中读入车架模态结果文件和车架应力形状时间历程文件计算出了车架的疲劳寿命。
关键词:摩托车结构疲劳寿命数字样机MSC.Fatigue中图分类号:U483文献标识码:A文章编号:1671-0630(2011)05-0023-04Fatigue Life Analysis of A Motorcycle StructureHuang Zehao ,Sun Zhangdong ,Lu Xusheng ,Xiao Rongji Chongqing University of Technology (Chongqing ,400050,China )Abstract :The finite element model is established in Hypermesh on the basis of a motorcycle model.The re-sult file of the modal analysis and modal neutral file of motorcycle structure are generated through modal analy-sis in Nastran.Then a rigid-flexible coupling multi-body dynamics model is created in ADAMS by using the modal neutral file and the CAD model of motorcycle.DAC files of body are generated after multi-body dynam-ics analysis.In MSC.Fatigue ,the fatigue life analysis of the structure is executed using the result file of the modal analysis and DAC mode file.Keywords :Motorcycle structure ,Fatigue life ,Virtual prototype ,MSC.Fatigue引言摩托车行驶过程中主要受到来自路面和发动机的激励,车架承受着行驶过程中的动载荷和静载荷[1]。
基于虚拟试验台架的驱动桥壳疲劳寿命分析研究
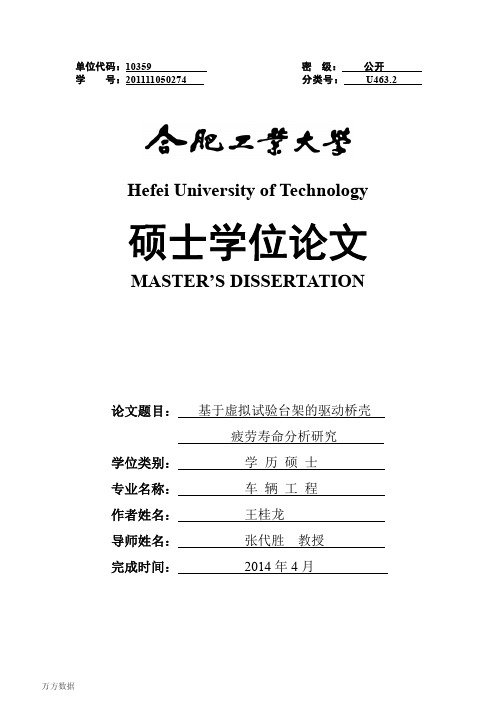
密 级: 分类号:
公开 U463.2
Hefei University of Technology
硕士学位论文
MASTER’S DISSERTATION
论文题目:
基于虚拟试验台架的驱动桥壳 疲劳寿命分析研究
学位类别: 专业名称: 作者姓名: 导师姓名: 完成时间:
万方数据
万方数据
学位论文独创性声明
本人郑重声明:所呈交的学位论文是本人在导师指导下进行独立研究工作所 取得的成果。据我所知,除了文中特别加以标注和致谢的内容外,论文中不包含 其他人已经发表或撰写过的研究成果,也不包含为获得 合肥工业大学 或其他
教育机构的学位或证书而使用过的材料。对本文成果做出贡献的个人和集体,本 人已在论文中作了明确的说明,并表示谢意。 学位论文中表达的观点纯属作者本人观点,与合肥工业大学无关。
Analysis of Drive Axle Housing Fatigue Life Based on Virtual Test Bench
By Wang Gui Long
Hefei University of Technology Hefei, Anhui, P.R.China
April, 2014
学位论文作者签名: 签名日期: 年 月 日
指导教师签名: 签名日期: 年 月 日
论文作者毕业去向 工作单位: 联系电话: 通讯地址: E-mail: 邮政编码:
万方数据
致谢
论文的完成离不开我的导师张代胜教授的帮助和指导, 也离不开谭继锦 老师的指导和校正。在百忙之中,张老师仍然挤出时间并投入较大的精力来 指导我的论文,提出了修改及完善建议,点拨了我的论文撰写。从选择论文 课题,到搜集课题相关资料,至后续的模型的建立及仿真,到论文撰写和修 改、完善,直至最后的论文定稿,老师都给了我详细而细致的指导。 时光荏苒, 在两年半左右的时间里, 张老师还在生活上给我提供了帮助, 在为人上、政治上也深刻地影响了我。张老师本人学识渊博,见识广泛,而 且治学态度严谨, 工作兢兢业业。 他的这些优良品质在潜移默化中影响着我, 让我深刻的懂得了做人、做学问的道理、方法。同时,合肥工业大学谭继锦 教授以其扎实的专业知识,先进的学术理念,稳重的工作方法在我撰写及修 改完善论文的整个过程中给予了我指导和帮助。正是因为老师们,我才有幸 能走到今天,在此向张老师、谭老师表达最最真挚、诚恳的敬意以及感谢。 祝老师们桃李满天下! 感谢论文评委专家为评阅论文所付出的宝贵时间和精力。 本论文的完成也离不开同一课题组的王殿鹏、李彦保、赵强等同学的帮 助。 在我完成论文的整个过程中,我们相互进步, 也从中汲取了很多的知识。 不仅如此,生活中我们相互关爱,和睦相处,学习生活的环境十分的融洽、 和谐。让我在学到了很多东西的同时,能够十分愉悦的度过有意义的研究生 生活。我十分珍惜这份来之不易的同窗之情。在此,一并向他们表示深深的 感谢,希望他们前程似锦。 感谢马洪龙同学对我论文修改的帮助。 最后,向远在故里的父母家人、亲朋好友致以最最真诚的感谢。正是他 们一直以来对我默默地支持和包容, 我才能得以完成学业, 实现多年的梦想。 谨以此文献给爱护和关心我及我爱和关心的人! 作者:王桂龙 2014 年 4 月
扭力梁耐久等效台架试验设计及疲劳寿命预测方法
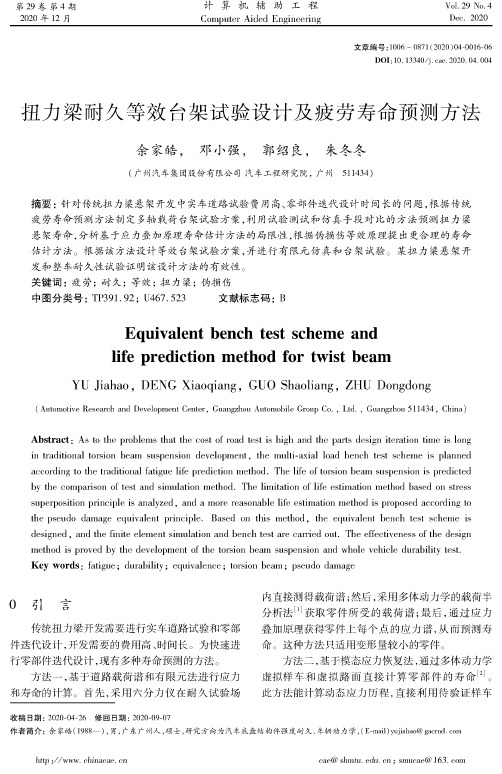
计算机辅助工程 Vcl.29 Nc.4Computee Aided EngineeringDec. 202029 42020 12文章编号:1"6 - 0871(2020)04-0016-06DOI : 10. 13340/j. cac. 2020. 04. 004扭力梁耐久等效台架试验设计及疲劳寿命预测方法余家皓,邓小强,郭绍良,朱冬冬(广川汽车集团股份有限公司汽车工程研究院,广川511434)摘要:针对传统扭力梁悬架开发中实车道路试验费用高、零部件迭代设计时间长的问题,根据传统疲劳寿命预测方法制定多轴载荷台架试验方案,利用试验测试和仿真手段对比的方法预测扭力梁 悬架寿命,分析基于应力叠加原理寿命估计方法的局限性,根据伪损伤等效原理提出更合理的寿命估计方法。
根据该方法设计等效台架试验方案,并进行有限元仿真和台架试验。
某扭力梁悬架开 发和整车耐久性试验证明该设计方法的有效性。
关键词:疲劳;耐久;等效;扭力梁;伪损伤中图分类号:TP391.92; U467.523 文献标志码:BEquivalent bench test scheme and life prediction method for twist beamYU Jiahao ,DENG Xiaoqiang ,GUO Shaoyang ,ZHU Dongdong(Automotive Research and Development Centee , Guangzhou Automobile Group Cc. , Ltd. , Guangzhou 511434, China )Abstract : As to the problems that the cost of road test is high and the parts design iteration time is long in traditional torsion beam suspension development , the multi 位xil load bench test scheme is plannedaeeoedingtotheteaditionaefatigueeifepeedietion method.Theeifeoftoesion beamsuspension ispeedieted by the comparison of test and simulation method. The limitation of lit estimation method based on stresssuperposition principle is analyzed , and a more reasonable lit estimation method is proposed according toth.ps.udodamag..quieaentpeineipe.Bas.d on thism.thod , th..quieaentb.neh tstseh.m.isdesigned , and the finite element simulation and bench Wst are carried out. The effectivenss of the design method is proved by the development of the torsion beam suspension and whole vehicle durability test.Key words : fatigue ; durability ; equivelence ; torsion beam ; pseudo damage0引言传统扭力梁开发需要进行实车道路试验和零部件迭代设计,开发需要的费用高、时间长。
摩托车车架台架实验载荷的确定及疲劳寿命探讨
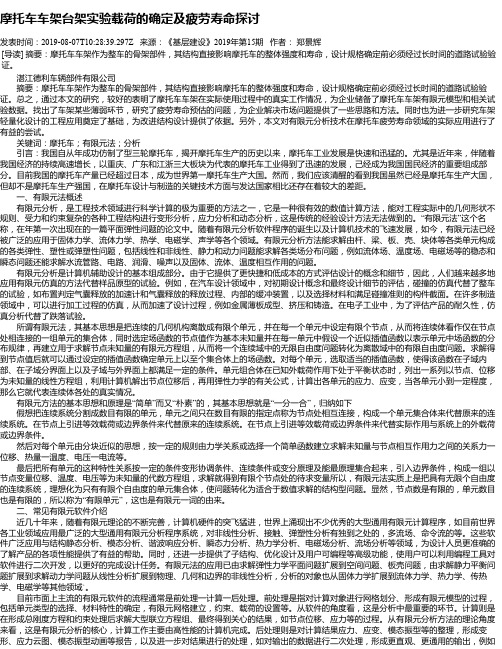
摩托车车架台架实验载荷的确定及疲劳寿命探讨发表时间:2019-08-07T10:28:39.297Z 来源:《基层建设》2019年第15期作者:郑景辉[导读] 摘要:摩托车车架作为整车的骨架部件,其结构直接影响摩托车的整体强度和寿命,设计规格确定前必须经过长时间的道路试验验证。
湛江德利车辆部件有限公司摘要:摩托车车架作为整车的骨架部件,其结构直接影响摩托车的整体强度和寿命,设计规格确定前必须经过长时间的道路试验验证。
总之,通过本文的研究,较好的表明了摩托车车架在实际使用过程中的真实工作情况,为企业储备了摩托车车架有限元模型和相关试验数据。
找出了车架某些薄弱环节,研究了疲劳寿命预估的问题,为企业解决市场问题提供了一些思路和方法。
同时也为进一步研究车架轻量化设计的工程应用奠定了基础,为改进结构设计提供了依据。
另外,本文对有限元分析技术在摩托车疲劳寿命领域的实际应用进行了有益的尝试。
关键词:摩托车;有限元法;分析引言:我国自从年成功仿制了型三轮摩托车,揭开摩托车生产的历史以来,摩托车工业发展是快速和迅猛的。
尤其是近年来,伴随着我国经济的持续高速增长,以重庆、广东和江浙三大板块为代表的摩托车工业得到了迅速的发展,己经成为我国国民经济的重要组成部分。
目前我国的摩托车产量已经超过日本,成为世界第一摩托车生产大国。
然而,我们应该清醒的看到我国虽然已经是摩托车生产大国,但却不是摩托车生产强国,在摩托车设计与制造的关键技术方面与发达国家相比还存在着较大的差距。
一、有限元法概述有限元分析,是工程技术领域进行科学计算的极为重要的方法之一,它是一种很有效的数值计算方法,能对工程实际中的几何形状不规则、受力和约束复杂的各种工程结构进行变形分析,应力分析和动态分析,这是传统的经验设计方法无法做到的。
“有限元法”这个名称,在年第一次出现在的一篇平面弹性问题的论文中。
随着有限元分析软件程序的诞生以及计算机技术的飞速发展,如今,有限元法已经被广泛的应用于固体力学、流体力学、热学、电磁学、声学等各个领域。
摩托车车架疲劳强度试验方法及设备
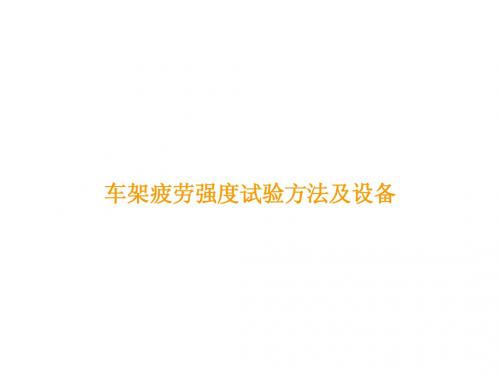
车架疲劳强度试验及试验设备
在国内,单独对车架强度进行试验的研究几乎还是一遍空白, 在国内,单独对车架强度进行试验的研究几乎还是一遍空白, 国内其他的摩托车企ቤተ መጻሕፍቲ ባይዱ中既无车架疲劳强度试验设备, 国内其他的摩托车企业中既无车架疲劳强度试验设备,也无 疲劳强度试验方法,国家标准中也没有相关内容, 疲劳强度试验方法,国家标准中也没有相关内容,所有的研 究工作,只能从零开始. 究工作,只能从零开始. 三,车架疲劳强度试验的原理浅析 车架疲劳强度试验原理起源于摩托车在道路上的实际状况. 车架疲劳强度试验原理起源于摩托车在道路上的实际状况. (1)当摩托车行驶在凹凸不平的路面时,其受力状况分别 )当摩托车行驶在凹凸不平的路面时, 如图1, 所示: 如图 ,图2所示: 所示
�
F
t2
Ft
Ft1
图2 行驶在凹面上时
车架疲劳强度试验及试验设备
同样的分析,当摩托车通过凹面路面上时, 同样的分析,当摩托车通过凹面路面上时,作用在车架上 的力便为水平方向上的拉力F 的力便为水平方向上的拉力 t1. 因此,在车架疲劳强度试验中,我们可以通过不断施加 因此,在车架疲劳强度试验中, 水平方向反复的推,拉力来激励车架, 水平方向反复的推,拉力来激励车架,这就是车架疲劳 强度试验中的水平加载试验,如图3所示 所示: 强度试验中的水平加载试验,如图 所示:
车架疲劳强度试验及试验设备
二,国内外车架疲劳强度试验开展的现状 目前, 目前,车架强度方面的研究工作在国外进行得相当普 日本的摩托车企业(如本田公司) 遍,日本的摩托车企业(如本田公司)在早些年已通过 不断施加载荷激励车架的某些部位来开展车架强度方面 的研究工作; 美国的摩托车企业运用MTS设备和技术 的研究工作 ; 美国的摩托车企业运用 设备和技术 藕合模拟道路特征来开展这方面的研究( 藕合模拟道路特征来开展这方面的研究(主要是利用多 通道的路采系统,在实验室开展模拟的道路试验) 通道的路采系统,在实验室开展模拟的道路试验);欧 洲摩托车企业的研究方法则起源于日本, 洲摩托车企业的研究方法则起源于日本,并在此基础上 得到发展.国外的车架疲劳强度试验经过多年的积累, 得到发展.国外的车架疲劳强度试验经过多年的积累, 已达到了一个较成熟的水平, 已达到了一个较成熟的水平,多数摩托车企业都已形成 了自己的企业标准,其研究成果对外都是秘而不宣的, 了自己的企业标准,其研究成果对外都是秘而不宣的, 作为这些企业内部的经典来指导摩托车的设计开发工作. 作为这些企业内部的经典来指导摩托车的设计开发工作.
摩托车车架系统疲劳寿命研究
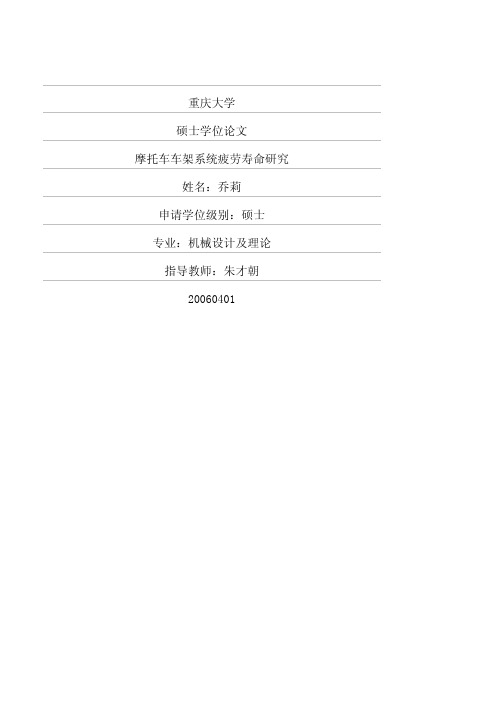
II
重庆大学硕士学位论文
1
绪
论
1
1.1 课题背景及意义
绪
论
目前,我国生产的摩托车绝大部分仍属中低档产品,技术上处于中低水平, 且大部分产品没有自己独立的知识产权。生产规模大而技术水平落后是我国摩托 车工业的现状和特点。 目前的新车型开发大多是“克隆”国外车型或在不改变车体和 发动机等核心技术基础上的外观改形,尤其在新车开发过程中,没有进行充分的 研究分析和试验考核,导致产品开发周期长、开发费用高,性能往往得不到保证。 造成这样的状况一方面是因为缺乏自主开发的技术基础和专门技术人才,另一方 面缺乏相应的检测评价方法和手段及大量试验基础数据的积累。为改变目前这种 状况,开展对摩托车性能的研究尤为必要。 众所周知,摩托车车架在摩托车中起着举足轻重的作用。车架是一个结构和 受力均复杂的组合零件,它将发动机、传动部分、行车部分、操纵部分等有机的 连结在一起,构成一个整体,承受着全车及载荷的重量,接受动力传递装置的扭 矩,通过驱动轮与路面的附着作用,产生对摩托车的牵引力;承受着路面作用于 车轮的各种力及力矩;承受着摩托车在不平路面行驶时产生的冲击和振动载荷等。 车架的主要功能不仅用于固定及支承车辆的发动机、传动系统和悬架系统以及其 它相关元件等,还起着抑制来自前后车轮的各种负荷所引起的扭曲变形以及对骑 乘人员提供良好的操纵稳定性和骑乘舒适性等作用。摩托车操纵的平顺性、驾驶 的安全性、乘坐的舒适性和在各种路面条件下的通过性与车架都有不可分割的关 联。因此,摩托车车架是一个要求严格的大型受力构件,必须有足够的强度和刚 性,而且在重量、造型等方面也有相应的要求。在载荷的作用下,车架必须有足 够的静强度和疲劳强度。静强度是指在承受冲击载荷时,车架抵抗永久变形的能 力。疲劳强度是指摩托车在行驶过程中,承受交变应力时不产生疲劳裂纹和疲劳 断裂的能力。实践证明,目前摩托车车架主要损坏形式是疲劳破坏,一般先在局 部区域(焊接接头处)产生裂纹,然后裂纹扩展导致断裂。疲劳强度不够,使用一段 时间后,容易发生车架断裂、永久变形等严重事故,给人身安全带来严重威胁。 通过对摩托车车架系统结构进行疲劳强度分析及寿命预估, 不但可以对现行摩 托车进行剩余寿命评估,而且能有效地指导新型摩托车的开发,提高了国内摩托 车的设计水平,具有十分重要的理论意义和实用价值。同时,通过对摩托车车架系 统的疲劳强度研究,制定疲劳强度试验标准,最终实现在疲劳试验机上对摩托车 车架系统进行疲劳试验,不仅可以大大缩短产品开发周期、降低开发费用,避免路 试中的安全事故,而且为摩托车开发和定型抽检中对车架系统疲劳耐久性考核试
F5211车辆悬挂(完全)台架疲劳试验(块曲线)
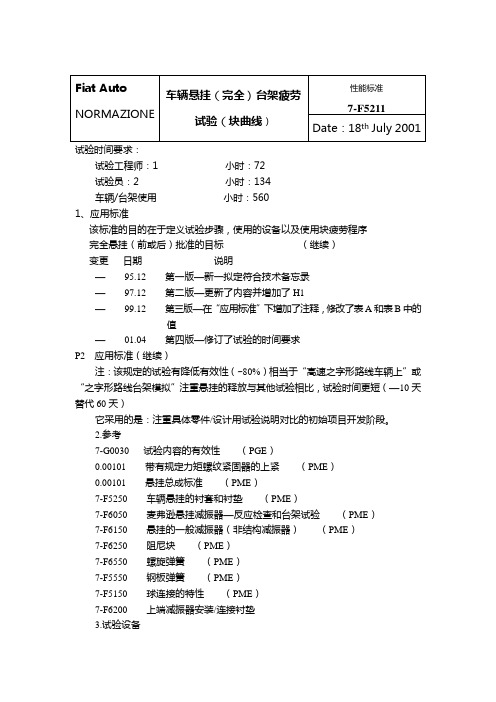
试验时间要求:试验工程师:1 小时:72试验员:2 小时:134车辆/台架使用小时:5601、应用标准该标准的目的在于定义试验步骤,使用的设备以及使用块疲劳程序完全悬挂(前或后)批准的目标(继续)变更日期说明—95.12 第一版—新一拟定符合技术备忘录—97.12 第二版—更新了内容并增加了H1—99.12 第三版—在“应用标准”下增加了注释,修改了表A和表B中的值—01.04 第四版—修订了试验的时间要求P2 应用标准(继续)注:该规定的试验有降低有效性(~80%)相当于“高速之字形路线车辆上”或“之字形路线台架模拟”注重悬挂的释放与其他试验相比,试验时间更短(—10天替代60天)它采用的是:注重具体零件/设计用试验说明对比的初始项目开发阶段。
2.参考7-G0030 试验内容的有效性(PGE)0.00101 带有规定力矩螺纹紧固器的上紧(PME)0.00101 悬挂总成标准(PME)7-F5250 车辆悬挂的衬套和衬垫(PME)7-F6050 麦弗逊悬挂减振器—反应检查和台架试验(PME)7-F6150 悬挂的一般减振器(非结构减振器)(PME)7-F6250 阻尼块(PME)7-F6550 螺旋弹簧(PME)7-F5550 钢板弹簧(PME)7-F5150 球连接的特性(PME)7-F6200 上端减振器安装/连接衬垫3.试验设备●三轴疲劳试验台,MTS型完全用控制电器●T-RACMTS型控制信号管理的编程器●专用的486计算机●车辆底盘模型,模拟悬挂连接或者(如果是严格目的)车身的部分●6频道记录仪注:可以用相同的设备替代,但其特性必须等于或超过所替设备的性能P4 5 试验零件的重要性/有效性评价试验有效性的零件的权及特性零件类型有效性%(A) 权影响试验有效性零件主要特性最小制制造等级有效0.09 横架,底盘子材料、尺寸 C有效0.09材料、尺寸 C有效0.05 完全支柱材料、尺寸 C有效0.05 减振器材料、性能 C有效0.09 阻尼块材料、性能 C有效0.09 衬套材料、性能 C有效0.09 稳定杆材料、性能 C有效0.05 球连接材料、性能 C有效0.05 衬垫材料、性能 C有效0.09 支柱,转向横拉杆材料、性能 C有效0.09 减振器连接衬垫材料、性能 C有效0.08 螺旋弹簧、钢板弹簧材料、性能 C有效0.09 螺纹紧固器材料 C试验零件的有效位(%)=∑(A×B)=注:对于每一个零件,标准7-G0030中指明了评价三个不同等级的有效性%P5 6 基本操作6.1 得到设计技术文件(轴上重量、最大轨迹、悬挂移动、图纸或螺纹连接的标准上紧力矩)最新的总成图,并在试验内容名称中输入这些数据。
摩托车车架系统疲劳强度分析及寿命预估

前言
摩托车车架主要损坏形式是疲劳破坏 ,一般先 在局部区域产生裂纹 ,然后裂纹扩展导致断裂 ,给人 身安全带来严重威胁 。疲劳强度及寿命预估是评价 摩托车可靠性的重要因素之一 ,疲劳试验是评价车 架疲劳强度的主要方法 ,通过对摩托车车架系统结 构进行疲劳强度分析及寿命预估 ,不但可以对现行 摩托车剩余寿命进行评估 ,还能有效地指导新型摩 托车的开发设计 ,具有十分重要的理论意义和实用 价值 。
3 新世纪优秀人才支持计划 (NCET - 05 - 0766)资助 。 原稿收到日期为 2006年 10月 23日 ,修改稿收到日期为 2006年 12月 22日 。
2007 (Vol. 29) No. 10
朱才朝 ,等 :摩托车车架系统疲劳强度分析及寿命预估
· 901 ·
1 疲劳试验机的研制
对摩托车车架强度的考核主要通过整车的道路 试验完成 ,因路试试验的条件 、环境等因素使其与疲 劳试验机相比开发周期延长 ,试验成本高且安全性 差 。因此开发针对我国摩托车实际情况的疲劳试验 机 ,制定相关试验规范和试验标准 ,以代替产品开发 初期的路试试验 ,具有十分重要的实际意义和经济 效益 。
摩托车车架系统承载全车和载荷的质量 ,以及 摩托车在不平路面行驶时产生的冲击和振动载荷 , 其疲劳破坏形式属机械疲劳破坏 。同时摩托车车架 系统受到冲击和振动载荷都是随机的 ,在其结构内
产生的交变应力也是随机的 ,没有固定的应力幅度 和频率 ,因而属于机械随机疲劳 。在设计摩托车车 架系统时 ,出于安全考虑 ,一般其设计名义应力都远 小于材料的屈服极限 ,其使用寿命也要求较长 ,因此 摩托车车架系统的疲劳属于高周疲劳 [ 1 - 2 ] 。但在实 际过程中很难模拟随机路面的激励 ,摩托车车架疲 劳试验机是在摩托车车架水平方向和垂直方向 ,施 加对称或非对称循环激励载荷来模拟摩托车通过凸 凹路面时给车架的冲击激励 [ 3 ] 。根据疲劳累计损 伤原理 、国内外摩托车行驶的自身特点以及摩托车 车架系统的疲劳类型 ———机械高周疲劳 ,建立了基 于车架结构 、材料疲劳属性和变幅载荷谱下摩托车 车架及悬挂系统可靠性疲劳寿命预测模型 。对某摩 托车车架系统疲劳强度和疲劳寿命进行了预估 ,并 在车架疲劳试验机上进行试验验证 ,为车架疲劳强 度分析及寿命预估提供了理论依据 。
摩托车车架可靠性分析
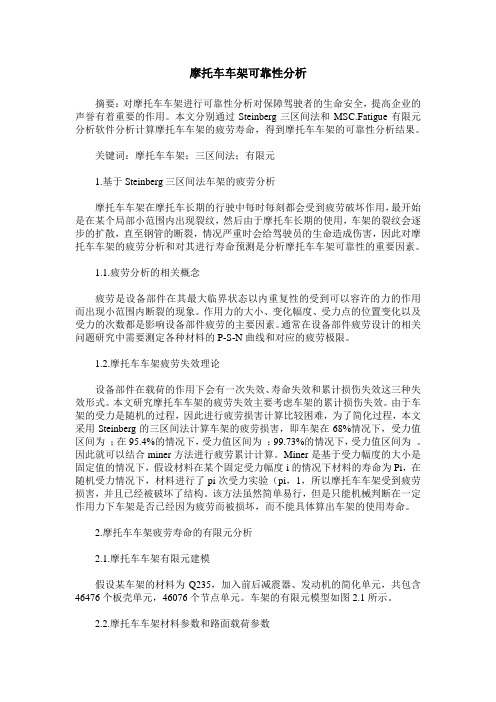
摩托车车架可靠性分析摘要:对摩托车车架进行可靠性分析对保障驾驶者的生命安全,提高企业的声誉有着重要的作用。
本文分别通过Steinberg三区间法和MSC.Fatigue有限元分析软件分析计算摩托车车架的疲劳寿命,得到摩托车车架的可靠性分析结果。
关键词:摩托车车架;三区间法;有限元1.基于Steinberg三区间法车架的疲劳分析摩托车车架在摩托车长期的行驶中每时每刻都会受到疲劳破坏作用,最开始是在某个局部小范围内出现裂纹,然后由于摩托车长期的使用,车架的裂纹会逐步的扩散,直至钢管的断裂,情况严重时会给驾驶员的生命造成伤害,因此对摩托车车架的疲劳分析和对其进行寿命预测是分析摩托车车架可靠性的重要因素。
1.1.疲劳分析的相关概念疲劳是设备部件在其最大临界状态以内重复性的受到可以容许的力的作用而出现小范围内断裂的现象。
作用力的大小、变化幅度、受力点的位置变化以及受力的次数都是影响设备部件疲劳的主要因素。
通常在设备部件疲劳设计的相关问题研究中需要测定各种材料的P-S-N曲线和对应的疲劳极限。
1.2.摩托车车架疲劳失效理论设备部件在载荷的作用下会有一次失效、寿命失效和累计损伤失效这三种失效形式。
本文研究摩托车车架的疲劳失效主要考虑车架的累计损伤失效。
由于车架的受力是随机的过程,因此进行疲劳损害计算比较困难,为了简化过程,本文采用Steinberg的三区间法计算车架的疲劳损害,即车架在68%情况下,受力值区间为;在95.4%的情况下,受力值区间为;99.73%的情况下,受力值区间为。
因此就可以结合miner方法进行疲劳累计计算。
Miner是基于受力幅度的大小是固定值的情况下,假设材料在某个固定受力幅度i的情况下材料的寿命为Pi,在随机受力情况下,材料进行了pi次受力实验(pi,1,所以摩托车车架受到疲劳损害,并且已经被破坏了结构。
该方法虽然简单易行,但是只能机械判断在一定作用力下车架是否已经因为疲劳而被损坏,而不能具体算出车架的使用寿命。
摩托车车架疲劳强度分析_吕冬慧
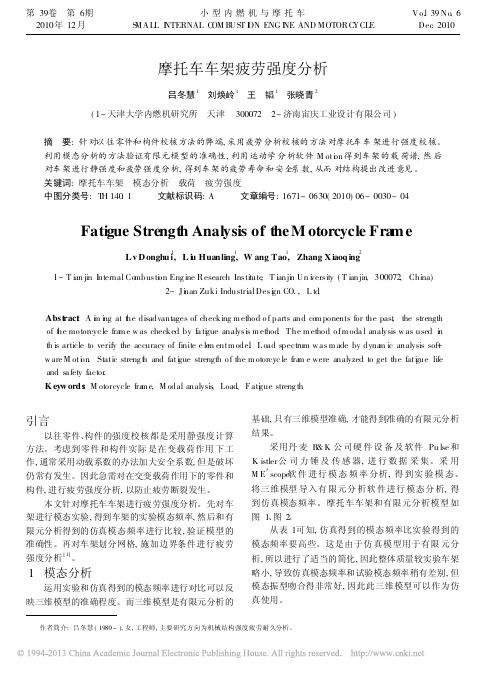
析, 所以进行了适当的简化, 因此整体质量较实验车架 略小, 导致仿真模态频率和试验模态频率稍有差别, 但 模态振型吻合得非常好, 因此此三维模型可以作为仿 真使用。
作者简介: 吕冬慧 ( 1980 - ), 女, 工程师, 主要研究方向为机械结构强度疲劳耐久分析。
摘 要: 针对以往零件和构件校核方法的弊端, 采用疲劳分析校核的方法对摩托车车架进行强度校核。
利用模态分析的方法验证有限元模型的准确性, 利用运动学分析软件 M ot ion得到车架的载荷谱, 然后
对车架进行静强度和疲劳强度分析, 得到车架的疲劳寿命和安全系数, 从而对结构提出改进意见。
关键词: 摩托车车架 模态分析 载荷 疲劳强度
3 结论
1) 和传统柴油相比, 生物柴油有较高的有效燃油 消耗率和高的热效率, 同时 CO、H C 和微粒质量浓度 排放降低, 但是 NOx 和微粒总数量有所升高。
2) 使用混合燃料使得发动机热效率比纯生物柴 油略有降低, 但仍高于使用传统柴油。
3) 生物柴油 /甲醇混合燃料可以明显降低生物柴
油所带来的高 NOx 和微粒总数量排放, 并且可以进一 步降低微粒的质量浓度, 但是 HC、CO 和 NO2 的排放 比传统柴油更高。
6 Cheng Chuanhu,i Cheung CS, Chan T L, e t a.l Com pa rison o f em issions of a direct injection diese l eng ine ope rating on b iodiese lw ith em ulsified and fum igated m ethano l[ J]. Fue,l 2008, 87( 10- 11): 1870~ 1879
Part-III 整车零部件台架耐久性试验及其试验
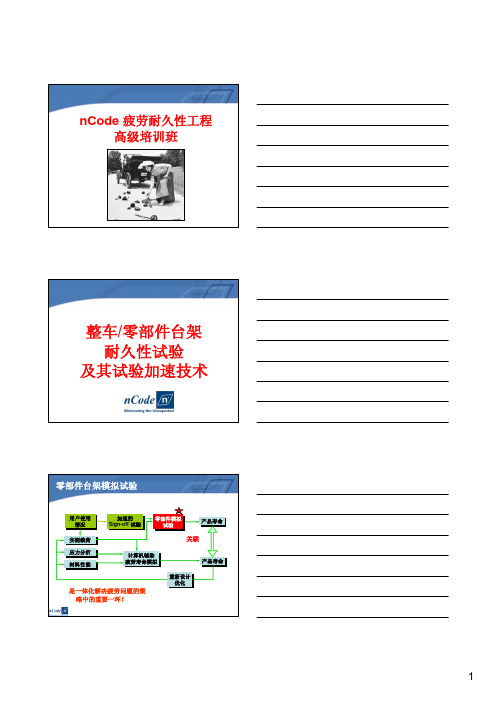
nCode 疲劳耐久性工程高级培训班整车/零部件台架耐久性试验及其试验加速技术零部件台架模拟试验是一体化解决疲劳问题的策略中的重要一环!重新设计优化重新设计优化零部件模拟试验零部件模拟试验计算机辅助疲劳寿命模拟计算机辅助疲劳寿命模拟用户使用情况用户使用情况实测载荷实测载荷应力分析应力分析材料性能材料性能产品寿命产品寿命关联产品寿命产品寿命加速的Sign-off 试验加速的Sign-off 试验台架试验的好处•可重复的试验环境•易对试验进行监控•通过比较试验对设计参数变化进行评价•早期检验零部件的性能•可能能实现试验加速•验证理论模型•...根据实测的载荷及响应信号,在实验室里重现实际工况,模拟零部件的性能及寿命进行台架试验的好处:台架试验时也可进行数据采集!做哪些台架试验?•能模拟道路试验的台架试验•能一定程度评价零部件耐久性能的试验•模拟损伤最严重的,要看车辆的特点•。
不要做和实际工况无关的试验!实验室负责人的困境•预先预测台架试验大概需要多长时间,费用大概多少?•高效地利用试验台•判断被要求做的试验是否是一个不合理的试验•在试验开始前,使用疲劳编辑技术“合法地”加速试验•“合法地”过滤掉试验台不能模拟的高频•…要求的疲劳寿命要长,但试验结果必须尽快出来!疲劳分析能够帮助...How should we test in lab?From P.G. or Field to Test RigCustomer Usage Test TrackIndividualSurfaces, EventsTest RigWhat Do We Want From A Durability Test?•Durability test that ’s suitable for the item in question: a component, sub-assembly, or a whole vehicle•Test must replicate the same failuremechanisms as seen in the real world•Test should be representative of the realloading environment•Test should be accelerated where possible to reduce project time scales and costs•Test specification can be used in FE based virtual test or real physical testTest Synthesis –Route MapDeterministicRandom Quasi-static Dynamic Uniaxial Multiaxial Test Synthesis Frequency DomainTime DomainPeak-Valley DomainDynamic Time Series Load Scaling Uniaxial Signal / Fatigue Fatigue Editing Accelerated Testing •PSD random •Sine sweep •Sine on random •Peak valley extraction•Block load sequence•Statistical exceedence•Constant amplitude•Is it proportional i.e. dominant plane?•Multiaxial peak valleyextraction •Buffered fatigue editing •Remote parameter simulation test •Proving ground •Increase frequency of Time SeriesVibration Load Scaling Deterministic and StochasticDeterministic StochasticLoad ScalingLoad Scaling•Scaling up the load will reduce the test duration exponentially.•Target life is influenced by endurance limit and onset of local plasticity as well as dynamic response of component•Scaling should be used with extreme care to avoid local yielding and changing the load paths•Not suitable for most inertia reacted testsScaled RangeOriginal RangeReal DurationTest DurationWhere b is the Basquin Exponent (gradient of SN curve)This is only approximate!Load ScalingPositive •Maintains Sequence •Maintains Phase between multiple channels •Maintains FrequencyContentNegative•Amplitude is not maintained (may affect the failure mechanism)Increasing Load FrequencyIncrease loading frequency •Doubling the frequency will half the test time•Limit acceleration to max 1/3first mode naturalfrequency•Not suitable for inertia reacted tests1/3 * natural frq Increase loading frequencyPositive•Maintains Amplitude •Maintains Sequence •Maintains Phase between multiple channels Negative •Frequency is not maintained (cannotconsider dynamicresponse)Peak valley extractionPeak valley extractionWhat is it?•Remove non peak or valley points in the signal and reduce the length of the signal in order to accelerate the fatigue test•Frequency may be re-adjusted after peak-valley extraction“峰谷”点非“峰谷”点360 Points36 PointsPeak valley extractionWhat is the method based on?•Fatigue damage is calculated by cycles which are constituted by peak and valley points“峰谷”点非“峰谷”点Peak valley extractionPositive•Maintains Amplitude •Maintains Sequence•Test can be acceleratedsignificantly, typical 90%reduction in signal length•‘Gate’small cycles on range, rainflow or fatigue contribution •Be care with slew rates, etc. Negative:•Frequency is not maintained (cannot consider dynamicresponse)•Phase between multiplechannels is not maintained (so, not suitable for multiaxial)Constant amplitude Cantilever: actual load change Cantilever: simple test loadConstant amplitudeWhat is it?•Replace variable load with a constant amplitude sinusoidal load, and test the component for afixed number of cycles or until failure occurs •Sometimes called “bogey test”Constant amplitudeWhat is the method based on?• a concept of equivalent damage•Normally increase the load to accelerate the testConstant amplitudeEquivalent damage based S-N curveΔS1ΔS2Νf1Νf2D1=1/Nf1 D2=1/Nf2Nf1 cycles of ΔS1 range is equivalent to Nf2 cycles of ΔS2 range.Both make the component failureConstant amplitudeHow can calculate equivalent amplitude or lading cycles?•Assume the slope of SN curve•Estimate the accumulated damage in a component over the life of the vehicle•Specify the number of test cycle for sinusoidal load, and use equivalent damage to calculate the load amplitude •Or specify the amplitude of the sinusoidal load, and use equivalent damage to calculate the number of cycle Constant amplitudeDetermine amplitude from specified cycle numberD=sum(Di)D=N ×D ΔSNf ΔS N cycles 1 repeatΔS?D ΔS = 1/Nf Constant amplitudeDetermine cycle number from specified amplitudeD=sum(Di)D=N ×D ΔSNf ΔS N? cycles 1 repeatΔS D ΔS = 1/NfConstant amplitudeFrequency of test load•As quick as possible, say 10Hz? Constant amplitudePositive•Total damage ismaintained•Test is simple•Test can be accelerated significantly Negative•Damage distribution is not maintained (may changefailure mode)•Frequency is notmaintained (cannotconsider dynamicresponse)•Not suitable for multiaxialAn exampleCase Study 1: Durability TestBackground•Need: Create a durability test•Analysis: Create durability test specification for chassis component testing based on proving ground data–Steering knuckles and control arms–Constant amplitude lab test–Equivalent damage•How many cycles?•What size cycles?•Current Process: Infield with Excel; very manual and step-by-step •Challenges–Reduce time required to analyze proving ground loads data.–Promote standard processes for analyzing those loads.–Make sure input data are clean.•Solution: GlyphWorks SignalCase Study 1: Durability TestResults•Report–Contains results anduser inputs traceability–Archivable as Worddocument or Web page•Lab test–100,000 cycles @ +/-load–Equivalent damageCase Study 1: Durability TestValueValue:•Results are given in an archivable report.•Process is easily repeated by non-experts.•Massive reduction in analysis time and effort:Engineer:“Took the analysis time required from 2 days to 5 minutes.”Engineer:“Get the right answers without all the manual processing, and all the results are given in archivable reports.”Manager:“90% reduction in time; this kind of time savings is unheard of. The time that was eliminated was all the tedious work that made it hard to focus on the engineering.”Block loading Cantilever: actual load change Cantilever: block loadingblock loadingWhat is it?•Replace variable load with a block loading thatconsists of several constant sinusoidal load with different amplitude, and test the component for a fixed number of cycles or until failure occursblock loadingWhat is the method based on?•Rainflow cycle counting (a concept of equivalent damage and equivalent damage distribution)•Normally can accelerate the test withoutincreasing load (only gating out small amplitude loading cycles)block loadingPrinciple: rainflow cycle countingblock loadingHow can we obtain block loading time history?•Rainflow cycle counting with several bins (say, 8)•Gating out small amplitude cycles (damagecalculation is needed for appropriate gate)•Use constant amplitude cycles to representcycles for each bin. Frequency can be as high as possible•Combine all time histories obtained for each bin (normally in the order from small to largeamplitudes)block loadingNo gatingblock loadingGating out the first binblock loadingPositive•Total damage ismaintained•Damage distribution is maintained•Test is simple•Test can be accelerated significantly with gatingout small amplitude cycles Negative•Frequency is notmaintained (cannotconsider dynamicresponse)•Cycle sequence is not maintained•Not suitable for multiaxialHistogram editing Cantilever: actual load changeHistogram editingWhat is it?•Replace variable load with an equivalent re-constructed time history load for testingHistogram editingWhat is the method based on?•equivalent damage and equivalent damage distribution•Normally can accelerate the test withoutincreasing load基于损伤的直方图编辑技术思路•用应变或应力法,对循环直方图进行疲劳分析,获得对应的损伤直方图•比较循环和损伤直方图,在循环直方图中将那些无损伤循环移走(将循环数置0 即可)•根据编辑后的循环直方图重构一个只有“峰谷”的随机时域信号,作为载荷控制信号•对重构的信号再进行疲劳计算,比较编辑前后的疲劳寿命基于损伤的直方图编辑技术思路重构的应变信号0000.050.10.150.20000000应变 (uE)RESPREG.DACSample = 204.8Npts = 44Max Y = 681.9Min Y = -1152时间 (秒)z 重构时域信号:-Range-mean 雨流矩阵-Max-min 雨流矩阵-Markov 矩阵-不规则因子组合录自不同时间的时域信号信号重构Histogram editingPositive •Total damage is maintained •Damage distribution is maintained •Test can be accelerated significantly Negative•Frequency is not maintained (cannot consider dynamic response)•Cycle sequence is notmaintained •Not suitable for multiaxialMulti-channel Peak ValleyExtractionMulti-axial peak valley extraction•Maintains phaserelationship betweenmultiple channels bykeeping points thatcorrespond with a peak orvalley in a differentchannel•Ordinary peak valleywould apply all peaks /valleys simultaneouslytherefore changing theload paths•‘Gate’small cycles多通道信号的峰谷值抽取编辑前•一个应变响应信号response•四个驱动加速度信号g01,g02,g03,g04•信号点数:8000多通道信号的峰谷值抽取编辑后•不设门槛值•编辑后信号点数:7449多通道信号的峰谷值抽取•采用45.3%门槛值•编辑后信号点数:598Resultant / Critical Plane Analysis •Proportional multi-axial, or caseswith a dominant fatigue plane•Establish critical plane•Eliminate non-damaging channels•Determine a single drive channelwith fixed proportions betweeninputs or align component on theuniaxial test rig at a given angle Resultant Load PlaneMulti-axial peak valley extraction Pos:•Maintains Amplitude •Maintains Sequence •Maintains Phase between multiple channels Neg:•Frequency is not maintained (cannot consider dynamic response)•Only suitable forproportional multi-axialloadsTime-domain damage editing =编辑前编辑后试验加速技术的基本原理•根据响应信号预估疲劳寿命•用响应信号的损伤结果编辑驱动信号•编辑原理为原始响应信号和浓缩后的响应信号的损伤值和损伤分布(损伤直方图)保持不变时间关联损伤编辑技术•基于时间-疲劳损伤概念•计算应变响应信号的时间-损伤分布图•损伤可用S-N 或e-N 方法计算•用时间-损伤分布图同步移去响应和驱动信号中的无损伤或损伤小于某一门槛值的信号段•插入一个递减或连接信号,避免在连接处有一个突然的信号跳跃•可用于单通道或多通道加载时间-疲劳损伤图•每一循环周产生的损伤值对分至组成循环周的“波峰”和“波谷”•叠加所有的循环获取损伤分布图应变时域信号(4个循环)时间-损伤图11223344时间-疲劳损伤图时间-损伤图应变时域信号同步移去响应和驱动信号中的无损伤信号段•用时间-损伤图同步移去响应和驱动信号中的无损伤或损伤小于某一门槛值的信号段•插入一个递减或连接信号,避免在连接处有一个突然的信号跳跃编辑前后的驱动信号比较•编辑前信号长度39 秒•编辑后试验时间8 秒Fatigue damage editingPositive•Maintains Amplitude•Maintains Sequence•Maintains Phase between multiple channels •Maintains Frequency content•Typical acceleration 50-80% depending on amount of damage to be retained and number of failurelocations assessed•Can be used with uniaxial or multiaxial fatigue solvers一个疲劳加速实例经过疲劳编辑原先需要114 天的车体疲劳模拟试验被缩短到15 天,节省试验费用$235,000 美元!疲劳试验加速分析做台架试验需要什么?•所要模拟的道路谱(这很重要!)•道路谱数据处理软件•台架试验加速软件•台架试验控制软件•。
某型跨骑式摩托车结构的疲劳寿命分析
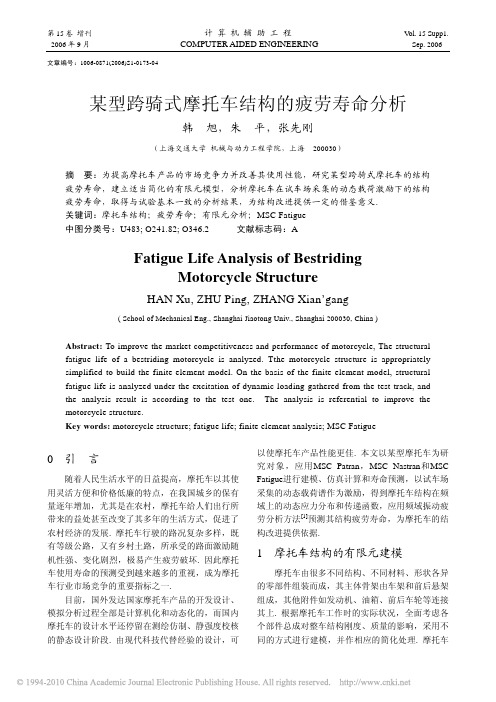
第15卷增刊计算机辅助工程 V ol. 15 Supp1.年月20069COMPUTER AIDED ENGINEERING Sep. 2006 文章编号:1006-0871(2006)S1-0173-04某型跨骑式摩托车结构的疲劳寿命分析韩旭,朱平,张先刚(上海交通大学机械与动力工程学院,上海 200030)摘要:为提高摩托车产品的市场竞争力并改善其使用性能,研究某型跨骑式摩托车的结构疲劳寿命,建立适当简化的有限元模型,分析摩托车在试车场采集的动态载荷激励下的结构疲劳寿命,取得与试验基本一致的分析结果,为结构改进提供一定的借鉴意义.关键词:摩托车结构;疲劳寿命;有限元分析;MSC Fatigue中图分类号:U483; O241.82; O346.2文献标志码:AFatigue Life Analysis of BestridingMotorcycle StructureHAN Xu, ZHU Ping, ZHANG Xian’gang( School of Mechanical Eng., Shanghai Jiaotong Univ., Shanghai 200030, China ) Abstract: To improve the market competitiveness and performance of motorcycle, The structural fatigue life of a bestriding motorcycle is analyzed. Tthe motorcycle structure is appropriately simplified to build the finite element model. On the basis of the finite element model, structural fatigue life is analyzed under the excitation of dynamic loading gathered from the test track, and the analysis result is according to the test one. The analysis is referential to improve the motorcycle structure.Key words: motorcycle structure; fatigue life; finite element analysis; MSC Fatigue0引言随着人民生活水平的日益提高,摩托车以其使用灵活方便和价格低廉的特点,在我国城乡的保有量逐年增加,尤其是在农村,摩托车给人们出行所带来的益处甚至改变了其多年的生活方式,促进了农村经济的发展. 摩托车行驶的路况复杂多样,既有等级公路,又有乡村土路,所承受的路面激励随机性强、变化剧烈,极易产生疲劳破坏. 因此摩托车使用寿命的预测受到越来越多的重视,成为摩托车行业市场竞争的重要指标之一.目前,国外发达国家摩托车产品的开发设计、模拟分析过程全部是计算机化和动态化的,而国内摩托车的设计水平还停留在测绘仿制、静强度校核的静态设计阶段. 由现代科技代替经验的设计,可以使摩托车产品性能更佳. 本文以某型摩托车为研究对象,应用MSC Patran,MSC Nastran和MSC Fatigue进行建模、仿真计算和寿命预测,以试车场采集的动态载荷谱作为激励,得到摩托车结构在频域上的动态应力分布和传递函数,应用频域振动疲劳分析方法[1]预测其结构疲劳寿命,为摩托车的结构改进提供依据.1 摩托车结构的有限元建模摩托车由很多不同结构、不同材料、形状各异的零部件组装而成,其主体骨架由车架和前后悬架组成,其他附件如发动机、油箱、前后车轮等连接其上. 根据摩托车工作时的实际状况,全面考虑各个部件总成对整车结构刚度、质量的影响,采用不同的方式进行建模,并作相应的简化处理. 摩托车计算机辅助工程年174 2006结构的有限元模型[2]如图1所示,共含有47 406个单元和51 022个节点.图 1 摩托车结构的有限元模型摩托车车架是摩托车的主要结构件,承受着复杂多变的动态载荷,其性能决定整车设计的成败.为了能够比较细致地反映车架结构的动态应力分布,预测其结构的疲劳寿命,采用板壳单元构建车架分析模型,并应用多点约束(MPC)将各构件连接起来构成整体.摩托车在行驶过程中承受动态载荷,其自身质量以及附加质量对摩托车的动态响应都起着至关重要的作用,因此在分析车架的动态应力和预测其疲劳寿命时,必须考虑包含附加质量在内的所有质量. 摩托车的自身质量363 kg,取单个乘员的质量70 kg,另加货物质量5 kg. 在这种情况下,附加质量与摩托车自身质量之比达到1︰5以上,因此这部分附加质量直接关系到车架结构的动应力分布以及局部构件的疲劳寿命预测,不可忽略. 在分析模型中,采用质量点模拟这些附加质量,并用刚性单元RBE 2将质量点与车架相连.另外,发动机处于车架结构的中心位置,刚度大,基本不变形,对于车架有很强的支撑作用,其质量同样不可忽略. 根据发动机的外形应用实体单元建模,采用均布质量. 前后减振器采用CBUSH 单元建模,并赋予非线性弹性特性. 轮胎模型简化处理,只取其弹性特性和阻尼及其质量,用质量单元和弹簧单元模拟.2 摩托车结构的疲劳寿命分析文中摩托车结构的疲劳寿命分析是模拟摩托车在试车场强化路面行驶条件下,采用试车场实验工况下采集的动态载荷激励,分析并预测摩托车的结构疲劳寿命.2. 1动态载荷谱的编制摩托车在试车场内的强化路面上以35 km/h的速度行驶,采集前后轮轴位置竖向和水平的加速度载荷. 强化路面总长1 620 m,主要包括沙石路、搓板路、小卵石路、比利时路和鱼鳞坑路5种. 采集激励信号时,摩托车承载一名驾驶员和若干测试仪器设备,共75 kg.根据经验,路面不平度激励频率范围一般在0~80 Hz之间,故截取0~80 Hz频段内加速度谱线作为激励. 又因为由实际的时间历程变换过来的频域谱线其横坐标过于密集,数据量过大,不利于计算,因此需要作必要的简化处理. 简化过程中,将0~80 Hz的分析频段划分为若干个0.1 Hz的小频段,取每个小频段内相应谱线的最高峰值作为其中心频率的幅值,峰值之间线性化处理,由此得到简化的激励谱线. 以前轮轴的竖向加速度谱线为例,通过将未简化谱线和简化谱线对比(见图2)可知,简化处理既保证必要的峰值不丢失,又大大减少数据量,不仅有利于计算,而且使寿命预测的结果偏于保守,说明简化处理是合理的.(a) 未简化加速度谱线(b) 简化后的加速度谱线图 2 前轮轴竖向加速度频域谱线2. 2 单位激励下摩托车动态响应分析应用频域振动疲劳分析方法进行结构疲劳寿命预测是以单位载荷下的频域振动应力分布作为疲劳分析的几何信息输入的. 因此,分别计算0~80 Hz 频段内对应前后车轴上的竖向和水平4种单位载荷作用下的摩托车结构上的动态应力分布. 发动机上的应力分布与摩托车的结构疲劳预测并不相关,其余板壳单元对应各个输出频率的应力分布作为频域增刊韩旭,等:某型跨骑式摩托车结构的疲劳寿命分析 175 振动疲劳分析的输入,图3为前轮竖向单位激励下对应32 Hz 的应力分布云图.图 3 前轮竖向单位激励下对应32 Hz 的应力分布云图2. 3 材料的S-N 曲线摩托车结构主要由5种材料组成,分别是08 F ,HG_R_08 F ,10号钢,20号钢和Q 235. 标准试样的疲劳试验,一般在转动弯曲疲劳试验机上进行. 在不同的载荷条件下得到试样在破坏时的循环次数,从而得到材料的S -N 曲线. 在条件不具备的情况下,可以由弹性模量、泊松比和强度极限生成一个粗略的S -N 曲线[3],以08 F 和10号钢为例,其S -N 曲线见图4.图 4 08 F 和10号钢的S-N 曲线2. 4 摩托车结构疲劳结果分析摩托车在行驶过程中受到复杂的随机激励,频域振动疲劳分析方法在这种情况下比根据时域信号进行的瞬态动力分析更加快速有效. 在做频域振动疲劳分析时,采用的方法是Dirlik 法. Dirlik 法解决了频域振动疲劳分析的经验闭合解问题,可以应用Monte Carlo 技术进行全面的计算机模拟,是求解频域疲劳问题的最好方法. 由频域振动疲劳分析得到的摩托车结构的对数疲劳寿命分布见图5,这里所说的寿命,即循环周期的数目,是以摩托车在试车场强化路面行驶一圈为一个周期的.图 5 摩托车结构的对数寿命分布由寿命分布图可知,最低的寿命为0. 515个周期,出现在发动机支撑结构上,该结构属于悬臂梁结构,在梁的根部应力值较大,导致该处寿命偏低. 并且寿命最低值出现在悬臂结构的折边上,这种结构虽然可以起到一定加强刚度的作用,但是应力集中也比较明显,计算出来的寿命偏低,局部放大图见图6.图 6 发动机悬置支承结构寿命分布在不考虑计算寿命偏低的发动机悬置支撑结构的情况下,从整体上看摩托车结构的寿命分布比较合理,主要结构支撑件的寿命分布一般都在10个周期以上. 其中左右后撑管靠近货架的一端,出现较低的寿命,其值在10到20个周期之间,如图7所示. 这一分析结果与疲劳试验中得到的最先发生疲劳破坏的位置基本一致,说明该结构疲劳分析是可靠的.图 7 后撑管尾端寿命分布3 结 论针对摩托车在行驶过程中受到复杂多变的随计算机辅助工程年176 2006机载荷,建立与摩托车实际运行状况相符的有限元模型,分析摩托车在试车场强化路面行驶时采集的动态载荷激励下的结构疲劳寿命,得出与试验基本一致的分析结果. 建模和分析过程中,对车载质量、发动机、前后减振器和车轮等采取保留基本特性、忽略具体外形的简化处理,并对试车场采集的动态载荷谱进行必要的简化. 这些简化不仅保证了分析结果的可靠性,也节约了计算时间,提高计算效率,说明这些简化措施基本合理.参考文献:[1] HALFPENNY A, 林晓斌. 基于功率谱密度信号的疲劳寿命估计[J]. 中国机械工程, 1998, 9(11):16-19.[2] 张先刚, 石宁, 朱平, 等. 某125型跨骑式摩托车结构的动态特性研究[J]. 机械设计与研究, 2005, 21(1):72-75.[3] MSC. Fatigue User Reference Manual[K].(编辑 廖粤新)。
机械工程中的疲劳寿命分析研究报告

机械工程中的疲劳寿命分析研究报告研究报告:机械工程中的疲劳寿命分析摘要:本研究报告旨在探讨机械工程中的疲劳寿命分析方法。
通过对材料的疲劳行为、疲劳寿命的计算和预测方法的研究,我们可以更好地理解和评估机械结构在长期使用中的可靠性和安全性。
本报告将重点介绍疲劳寿命分析的基本原理、常用方法以及应用案例。
1. 引言机械结构在长期使用过程中往往会受到疲劳损伤的影响,这种损伤可能导致结构的失效,从而引发事故。
因此,疲劳寿命分析在机械工程中具有重要的意义。
通过对材料的疲劳行为和结构的工作环境进行分析,我们可以预测结构的疲劳寿命,从而采取相应的措施来延长结构的使用寿命。
2. 疲劳行为分析疲劳行为是材料在循环加载下的损伤积累过程。
在疲劳加载下,材料会经历应力集中、裂纹扩展和最终破坏的过程。
了解材料的疲劳行为对于疲劳寿命分析至关重要。
常见的疲劳行为分析方法包括应力-应变曲线、S-N曲线和裂纹扩展速率曲线等。
3. 疲劳寿命计算方法疲劳寿命计算是基于疲劳行为分析的基础上进行的。
常用的疲劳寿命计算方法包括极限应力法、线性累积损伤法和应力强度因子法等。
这些方法根据不同的假设和条件,通过计算应力、应变、裂纹扩展速率等参数,来预测结构的疲劳寿命。
4. 疲劳寿命预测方法疲劳寿命预测是通过对结构的工作环境和加载条件进行分析,来预测结构的疲劳寿命。
常用的疲劳寿命预测方法包括应力循环法、应力幅值法和应力时间法等。
这些方法通过测量或估计结构的工作环境和加载条件,来预测结构的疲劳寿命。
5. 应用案例本报告还将介绍一些实际应用案例,以进一步说明疲劳寿命分析在机械工程中的重要性和实用性。
这些案例包括汽车发动机曲轴、飞机机翼和桥梁等结构的疲劳寿命分析。
结论:通过对机械工程中的疲劳寿命分析方法的研究,我们可以更好地评估机械结构在长期使用中的可靠性和安全性。
疲劳寿命分析可以帮助我们预测结构的疲劳寿命,从而采取相应的措施来延长结构的使用寿命。
在未来的研究中,我们可以进一步探索新的疲劳寿命分析方法,提高分析的准确性和可靠性,以满足不断发展的机械工程需求。
某商用车车架台架疲劳寿命预测与提升
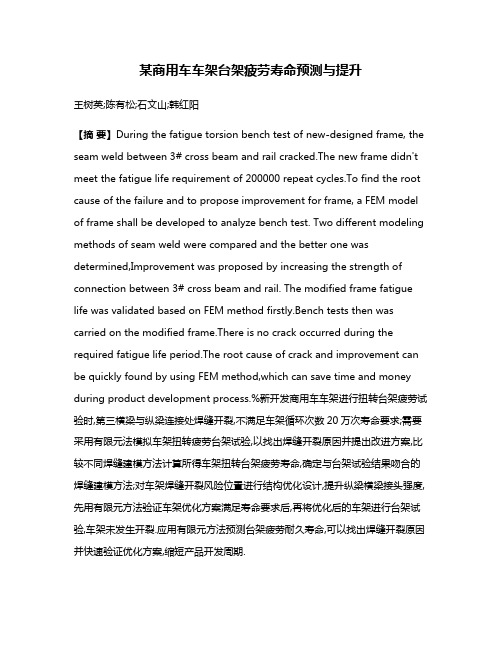
某商用车车架台架疲劳寿命预测与提升王树英;陈有松;石文山;韩红阳【摘要】During the fatigue torsion bench test of new-designed frame, the seam weld between 3# cross beam and rail cracked.The new frame didn't meet the fatigue life requirement of 200000 repeat cycles.To find the root cause of the failure and to propose improvement for frame, a FEM model of frame shall be developed to analyze bench test. Two different modeling methods of seam weld were compared and the better one was determined,Improvement was proposed by increasing the strength of connection between 3# cross beam and rail. The modified frame fatigue life was validated based on FEM method firstly.Bench tests then was carried on the modified frame.There is no crack occurred during the required fatigue life period.The root cause of crack and improvement can be quickly found by using FEM method,which can save time and money during product development process.%新开发商用车车架进行扭转台架疲劳试验时,第三横梁与纵梁连接处焊缝开裂,不满足车架循环次数20万次寿命要求;需要采用有限元法模拟车架扭转疲劳台架试验,以找出焊缝开裂原因并提出改进方案,比较不同焊缝建模方法计算所得车架扭转台架疲劳寿命,确定与台架试验结果吻合的焊缝建模方法;对车架焊缝开裂风险位置进行结构优化设计,提升纵梁横梁接头强度,先用有限元方法验证车架优化方案满足寿命要求后,再将优化后的车架进行台架试验,车架未发生开裂.应用有限元方法预测台架疲劳耐久寿命,可以找出焊缝开裂原因并快速验证优化方案,缩短产品开发周期.【期刊名称】《机械设计与制造》【年(卷),期】2018(000)005【总页数】3页(P117-119)【关键词】车架;台架试验;有限元建模;焊缝;疲劳寿命;优化设计【作者】王树英;陈有松;石文山;韩红阳【作者单位】上海汽车集团股份有限公司商用车技术中心;上海汽车集团股份有限公司商用车技术中心;上海汽车集团股份有限公司商用车技术中心;上海汽车集团股份有限公司商用车技术中心【正文语种】中文【中图分类】TH161 引言对于非承载式车身的车型,车架是整车的装配基体和承载基体[1],承载着汽车各总成,并承受着各种力及力矩。
车辆疲劳耐久性分析、试验与优化关键技术
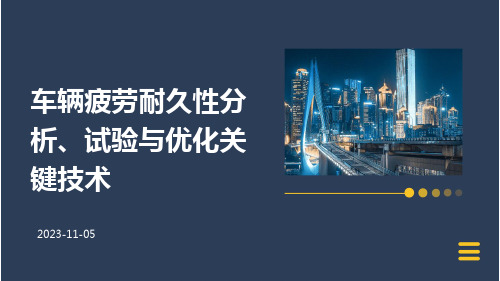
喷涂技术
喷涂技术可以提高车辆的外观质量和耐腐蚀性,如电泳涂装、静电喷涂等技术在车辆制造车辆疲劳耐久性研究展望
1
深入研究车辆疲劳损伤机理
2
3
深入研究金属材料疲劳裂纹萌生和扩展机理,包括微裂纹、界面裂纹等特殊疲劳损伤机理。
试验过程
01
安装样品
将选择的样品按照规定的安装方式安装在试验台上,确保安装牢固、稳定。
02
预处理样品
在试验开始前,对样品进行必要的预处理,如表面处理、涂层等,以消除样品本身对试验结果的影响。
数据整理
对试验过程中记录的数据进行整理,提取与疲劳耐久性相关的数据,如应力、应变、循环次数等。
数据统计
对提取的数据进行统计和分析,计算相应的指标和参数,如疲劳寿命、应力幅等。
优化设计
对新设计的发动机支架进行疲劳试验,并与原车型进行对比评估,以确保优化后的支架疲劳性能得到提升。
验证与评估
A
B
C
D
整体结构分析
利用三维扫描技术获取重型卡车的整体结构模型,进行详细的应力、应变分析。
优化设计
根据预测结果,对重型卡车的整体结构进行优化设计,如改变车身形状、增加支撑结构等。
验证与评估
针对不同使用工况和环境条件,进行疲劳寿命预测模型的修正和优化,提高预测的准确性和可靠性。
01
03
02
研究新型高强度材料和先进制造技术,以提高车辆结构和零部件的抗疲劳性能。
发展车辆疲劳耐久性设计方法和优化策略,包括优化零部件的几何形状、受力分析和优化布局等。
探索基于健康监测和无损检测的车辆疲劳损伤监测与评估技术,及时发现和修复潜在损伤,延长车辆使用寿命。