有害物质风险评估程序通用版
危害识别和风险评估程序

危害识别和风险评价管理程序一、目的二、范围三、职责HSE管理者代表:对危害识别与风险评价工作直接负责,确定及审批管理程序、危害识别及风险评价的结果。
安全环保部门和HSE管理人员:组织开展危害识别和风险评价工作,负责对各单位的工作进行指导、控制和更新。
省公司安全环保部门负责编制发布和危害识别和风险评价管理程序,对全省工作进行指导,负责组织相关专业技术人员对全省的识别和评价结果进行总的分析和认证。
各市地分公司的安全环保部门及HSE管理人员负责本公司各项工作的开展。
其它各部门:参与开展危害识别与风险评价的查找、分析、控制和更新工作。
所有员工:接受安全环保部门组织的培训,参与危害识别和风险控制的查找、分析、控制和更新工作。
四、定义危害:可能造成人员伤害、职业病、财产损失、环境破坏或其组合的根源或状态。
危害识别:认知危害的存在并确定其特征的过程。
风险:特定危害事件发生的可能性及后果严重性的结合。
风险评价:依照现有的专业经验、评价标准和准则,评价风险程度并确定风险是否可容忍的全过程。
事故:造成死亡、职业病、财产损失、环境破坏的事件。
事件:导致或可能导致事故的事情。
五、工作程序危害识别及风险评估程序流程,参照附录1,具体步骤概括如下:1、成立评估小组省、市、县公司及所属部门应成立有专业技术人员和操作人员参加的评估小组,所有评估人员需经过专门培训并有能力、资格开展职业安全健康的危害识别、风险评估和指导工作,同时各部门也应要求其他员工参与危害的确定。
2、选择和确定评估范围和对象评估小组应首先识别出公司从事的经营活动、产品或服务范围,包括规划、设计、建设、投用、采购、销售、产品、储运、设备、设施、服务、检维修、消防、合约商的服务和设备,以及行政和后勤等活动的全过程。
所有可能导致重要危害的活动,包括非常规活动如检维修等都必须充分得到识别。
在确定评估范围后,评估小组可按下列方法,确定评估对象:——按地理区域或部门;——按装置、设备、设施;——按作业任务。
危害风险评估程序

XXX-SOP-036
危害风险评估管理规范
版本/版次
A/0
页次
2/6
2008年10月6日制订
核准
审查
制订
2008年10月8日生效
(2)危害是指必须预以控制的、可能发生的、会对消费者健康造成损害的危害。风险评分≥5分的,可判为显著危害。
总在发生
高
4
5
6
7
经常发生
中等
3
4
5
6
偶尔发生
低
2
3
4
5
历史上未发生
产品在流水线上依次过紫外灯,然后入胶袋
紫外线消毒灯
15.包装
注意外箱注明日期,包装合格后,按照包装的顺序摆放在卡板上.
流水线
18.QA:
按抽样计划进行抽检,按照成品检验规范进行检验,
19.成品仓
按照客户、订单、ITEM进行分类摆放。
20装箱
按照要求装箱
文件编号
XXX-SOP-036
危害风险评估管理规范
版本/版次
A/0
页次
5/6
2008年10月6日制订
核准
审查
制订
2008年10月8日生效
6、危害风险分析
(1)
成分及加工步骤
(2)
确定在此步骤出现的潜在危害
(3)危害风险评估
(4)
对第(3)列判断提出理由和依据
(5)
防止显著危害的措施
危害发生的可能性
对人体危害程度
是否为显著危害
1美
耐皿粉
验收
生物性
无
化学性
3.2风险分析评估标准
根据产品安全危害造成不良健康后果的严重性及发生的可能性,对每种产品安全危害进行评价和分类,应指明在原料、加工和分销中哪个环节每种食品安全危害可能被引入、产生或增加程度。
hsf有害物质管理风险评估表

无 无 直接接触 无 直接接触
直接接触
低 低 高 低 低 高 低 低 高 低 中等 中等 中等 中等 中等 中等
中等 中等 高 低
中等
中等
注意防止破袋预防污染 检查卡板防止刺坏的包装袋 每批取样用XRF测试确认 注意防止破袋预防污染 注意防止破袋预防污染
1 注意防止破袋预防污染 注意防止破袋预防污染
直接接触 无
16
工程检
工程検査
XFR检测仪器
无
缝袋机
无
17
包装袋印字
包装
插车/卡板
无
18
出货
出货
货车
无
备注: ➀ 生产□ 移动 信息流♀ 储存◇ 检査☐
中等 中等 中等
中等 中等 中等 低风险 中等 中等 中等 中等 低 中等 中等 低 中等 中等 中等 中等 低 中等
中等
中等 中等 低
高
低
低
低
采用金属材料耐磨 采用金属材料耐磨
有害物质管理风险评估
批准
颜色:所有
歩骤 生产流程与流程图 受注/订单
1 评审
过程描述
机器/设备装置、 是否与材料、 易耗品、材料 中间物料、成 ROHS管理风险等级 管理要求与措施
品直接接触
传真机
无
受 注 / 订 单 评 电子邮件/电脑 审
无
打印机
无
中等
准确接受客户要求,并进行内部评审,及时 将客户要求转化内部管控要求
采用耐磨型金属材料
上一页
9 材料/颜料/添
加剂定量
挤出
8
冷却
9
10
沥水干燥
11
切粒
12
有害物质风险评估工作程序

有害物质风险评估工作程序引言随着人类对环保意识的提高以及工业化进程的不断加速,涉及到人类生产和生活的各种有害物质的种类和数量不断增多,与之相关的风险也在不断增加。
因此,对有害物质的风险评估工作成为了当前环境保护和工业安全领域面临的一个重要问题。
本文将介绍有害物质风险评估工作的基本流程和注意事项。
有害物质风险评估的基本流程第一步:确定目标人群和暴露途径有害物质的危险性与其接触方式和接触量密切相关,因此在评估有害物质的风险时必须首先确定有哪些人群会接触这种有害物质以及接触途径。
例如,某些有害物质可能只对从事相关工作的人员有危害,而对于普通消费者则没有影响;有些有害物质只有通过食入或者呼吸等途径才会对人体产生影响,因此要评估其风险必须明确相关的暴露途径。
第二步:收集有害物质的毒理学数据和流行病学数据评估有害物质风险的过程中需要收集有害物质的毒理学数据和流行病学数据。
毒理学数据通常包括各种动物的实验数据和人体研究数据,主要用来确定有害物质的毒性程度、剂量-效应关系等参数;流行病学数据主要通过流行病学调查等方式获取,用来确定在实际人群中有害物质暴露所导致的健康影响。
第三步:确定曝露水平在评估有害物质的风险时还需要确定人体实际接触到有害物质的水平,通常包括内源性曝露和外源性曝露两种形式。
内源性曝露是指人体自身产生有害物质,外源性曝露则是指从环境或者饮食等途径摄入有害物质。
确定曝露水平是评估有害物质风险的重要一步,因为只有明确了实际曝露水平,才能正确评估风险。
第四步:风险特征描述和剂量-反应关系建立在确定了有害物质暴露水平后,还需要描述该物质的风险特征和建立其剂量-反应关系。
风险特征描述包括出现的健康影响的种类和程度等,而剂量-反应关系建立则是指根据毒理学数据建立有害物质对不同剂量的反应程度等数据,这些数据有助于评估不同曝露水平下的风险。
第五步:基于风险特征和剂量-反应关系进行风险评价在第四步确定了有害物质的风险特征和剂量-反应关系后,可以基于这些参数进行风险评价,以确定实际曝露水平下人体健康风险。
限制性物质污染风险评估程序
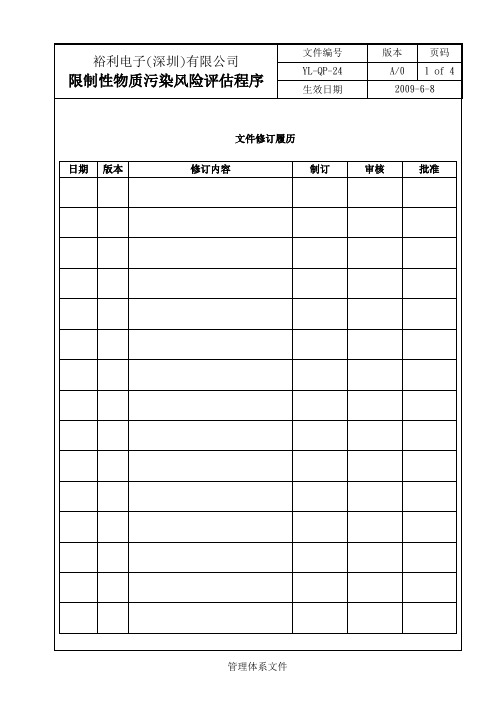
日期
版本
修订内容
制订
审核
批准
1.目的
通过对本司制程、供应商所提供的原材料及委托加工的产品(包括其加工的制程等)进行环境有害物质使用的风险性评估,对制程所使用的工治具,供应商所提供的原材料、委托外加工等进行选择,从而有效的防止本司制程及供应商所提供的原材料、委托加工过程中出现HSF不符合因素,达到逐步禁用或消减使用环境有害物质的目的。
6.1.2制程添加物供应商必须提供:真实有效并符合标准的相关物质的含量测试报告、MSDS(化学品必须)、有害物质不使用保证书及添加物本身的风险自评。
6.1.3辅助材料供应商必须提供:真实有效并符合标准的相关物质的含量测
试报告、有害物质不使用保证书、及其材料本身的风险评估。
6.1.4加工供应商必须提供:加工处理结果(如电镀)及处理过程中使用添加物、辅助材料的真实有效并符合标准的相关物质的含量测试报告、MSDS(化学品必须)、有害物质不使用保证书及其对自身(包括其处理结果与处理过程)的风险自评。
6.2.2制程添加物风险评估:
6.2.2.1包括制程中所有使用到的去渍油、除油、洗模水等添加物。
6.2.2.2根据供应商提供的相关物质的含量测试报告及MSDS等资料对添加物进行有害物质风险评估.此类物质对产品本身的化学性质并无影响,但对人体可能造成其他伤害,所以对其评估时除对其四项有害物质的评估外,必须根据MSDS对其伤害性进行评估,采购时优先选择对人体无伤害添加物。
4.2风险:指一种遭受损失的可能性。本司具体指制程或委托供应商加工处理过程中使用某种可能不符合客户环保要求的原材料、工治具及辅料而对公司造成损失的可能性。
4.3高风险:以危害物质控制标准为依据,产品中某项有害物质的含量与HSF要求标准值的百分比在71%以上者为高风险物料.(如:实测钢材料的含铅量为2800ppm、HSF要求标准值钢合金为3500ppm,2800:3500*% =80%;>71%,此物料则为高风险物料)。
有害物质风险评估工作程序
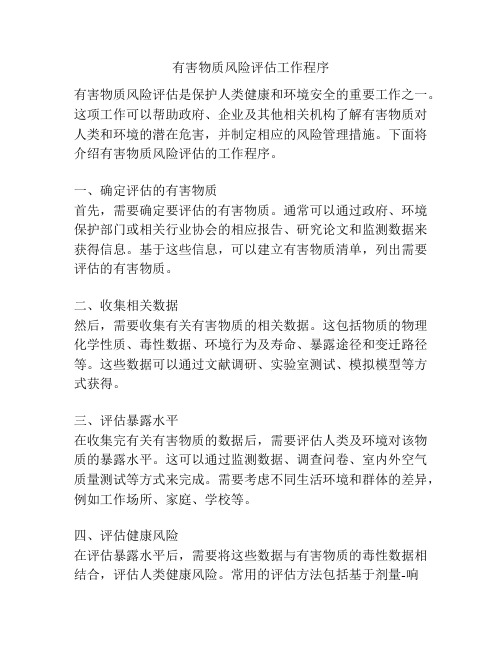
有害物质风险评估工作程序有害物质风险评估是保护人类健康和环境安全的重要工作之一。
这项工作可以帮助政府、企业及其他相关机构了解有害物质对人类和环境的潜在危害,并制定相应的风险管理措施。
下面将介绍有害物质风险评估的工作程序。
一、确定评估的有害物质首先,需要确定要评估的有害物质。
通常可以通过政府、环境保护部门或相关行业协会的相应报告、研究论文和监测数据来获得信息。
基于这些信息,可以建立有害物质清单,列出需要评估的有害物质。
二、收集相关数据然后,需要收集有关有害物质的相关数据。
这包括物质的物理化学性质、毒性数据、环境行为及寿命、暴露途径和变迁路径等。
这些数据可以通过文献调研、实验室测试、模拟模型等方式获得。
三、评估暴露水平在收集完有关有害物质的数据后,需要评估人类及环境对该物质的暴露水平。
这可以通过监测数据、调查问卷、室内外空气质量测试等方式来完成。
需要考虑不同生活环境和群体的差异,例如工作场所、家庭、学校等。
四、评估健康风险在评估暴露水平后,需要将这些数据与有害物质的毒性数据相结合,评估人类健康风险。
常用的评估方法包括基于剂量-响应关系的风险评估、无效剂量的测量、比较各种敏感性人群的风险等。
评估结果通常以急性和慢性风险比值、致癌风险等形式报告。
五、评估环境风险除了人类健康风险评估外,还需要评估有害物质对环境的潜在危害。
这涉及到有害物质在环境中的分布、降解和寿命等因素。
可以通过建立模拟模型、环境监测和生态学调查等来评估环境风险。
六、制定风险管理措施基于评估结果,需要制定相应的风险管理措施。
这可以包括禁止使用有害物质、限制使用量、改进生产工艺、提供个人防护用具等。
此外,还需要制定相应的监测计划,以跟踪有害物质的使用和暴露水平变化。
七、风险沟通与信息公开风险评估的结果需要及时向相关利益相关者沟通,包括政府、企业、公众和媒体等。
重要的是要使用易于理解的语言和形式向他们传达风险信息,以便他们能够正确理解和采取相应的行动。
有害物质管理程序(流程)

xxxXXXXXXXXXXXXXXXXXXXX 有限公司程序文件文件名称:有害物质管理程序文件编号:生效日期:版本号:适用范围:编制:审核:批准:文件制订/修改情况记录明确有害物质的管理标准,规范有害物质的识别、评价及控制,以确保高风险的物料、工艺、器具能得到有效的管制,减少其污染 HSF 产品的可能。
2适用范围:限公司内的各相关单位的有害物质管理过程。
3定义:3.1HS 物料/产品/器具(有害物质): 指的是相关的环保法规(如:RoHS、WEEE、REACH、食品卫生等)及其它适用标准或客户要求中禁止使用的材料(包括:物料、产品、工治具、机器设备、测试仪器、包装包器等);3.2HSF(有害物质减免): 指的是相关的环保法规(如:RoHS、WEEE、REACH、食品卫生等)及其它适用标准或客户要求中规定的任何材料对有害物质的减少或消除。
3.3有害物质的识别:是指对产品的提供过程及相关的物料产品器具等进行调查分析,明确其是否含有或可能会含有有害物质的过程。
4职责:4.1产品验证中心理化分析部:对相关部门申请的原材料,零部件及成品进行有害物质测试, 并负责对《RoHS 物料定期送检及监控方案》的维护更新。
4.2社会责任管理部负责HSF 标准及法律法规评价,形成《HSF 适用法规评价表》,并定期更新;有害物质管理标准的制定、修订及组织对含有害物质的物料及过程的识别和评价,形成《有害物质识别及评价总表》;负责有害物质管理体系内审及协助管理者代表组织有害物质管理评审。
4.3各分公司体系管理人员及品管部负责协助对本公司内有害物质的识别和评价。
4.4公司相关部门负责依管理标准对高风险物料、产品或过程的制定相应的管控方案来实施管控。
4.5物流管理中心及相关采购部门:负责评估和确认供应商对有害物质管控的能力及结果,监督供应商对有害物质的管控;负责从供应商处索取有害物质测试报告以及相关保证书,并负责对供应商进行有害物质控制的能力教育和培训。
危害辨识和风险评价控制程序范本(二篇)
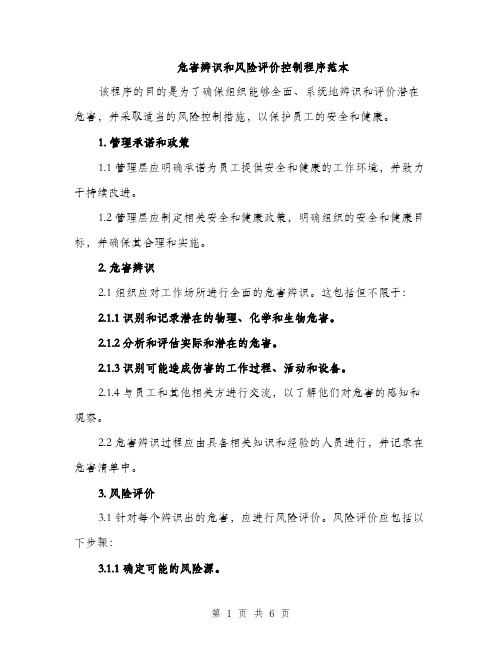
危害辨识和风险评价控制程序范本该程序的目的是为了确保组织能够全面、系统地辨识和评价潜在危害,并采取适当的风险控制措施,以保护员工的安全和健康。
1. 管理承诺和政策1.1 管理层应明确承诺为员工提供安全和健康的工作环境,并致力于持续改进。
1.2 管理层应制定相关安全和健康政策,明确组织的安全和健康目标,并确保其合理和实施。
2. 危害辨识2.1 组织应对工作场所进行全面的危害辨识。
这包括但不限于:2.1.1 识别和记录潜在的物理、化学和生物危害。
2.1.2 分析和评估实际和潜在的危害。
2.1.3 识别可能造成伤害的工作过程、活动和设备。
2.1.4 与员工和其他相关方进行交流,以了解他们对危害的感知和观察。
2.2 危害辨识过程应由具备相关知识和经验的人员进行,并记录在危害清单中。
3. 风险评价3.1 针对每个辨识出的危害,应进行风险评价。
风险评价应包括以下步骤:3.1.1 确定可能的风险源。
3.1.2 评估员工可能的接触程度和频率。
3.1.3 评估潜在的伤害情况和可能的后果。
3.1.4 评估现有的控制措施和管理措施,以确定其有效性和可行性。
3.1.5 确定风险等级和优先级。
3.2 风险评价应由具备相关知识和经验的人员进行,并记录在风险评估表中。
4. 风险控制4.1 通过建立和实施适当的控制措施来降低风险至可接受范围。
4.2 控制措施应根据风险评估结果制定,并尽可能遵循以下原则:4.2.1 优先选择技术性控制措施,如工程控制,以消除或降低危害。
4.2.2 采取行政控制措施,如工作和操作规程,以保证员工遵守安全操作规范。
4.2.3 提供个人防护装备,并确保其正确使用和维护。
4.3 控制措施的实施应经过充分的培训和沟通,确保员工理解和遵守。
4.4 控制措施的有效性应定期进行检查和评估,并采取必要的改进措施。
5. 安全文化和员工参与5.1 组织应建立积极的安全文化,鼓励员工主动参与危害辨识和风险评价。
5.2 组织应定期举行安全培训和会议,提高员工对危害和风险的认识和理解。
危害辨识风险评价控制程序模版(四篇)
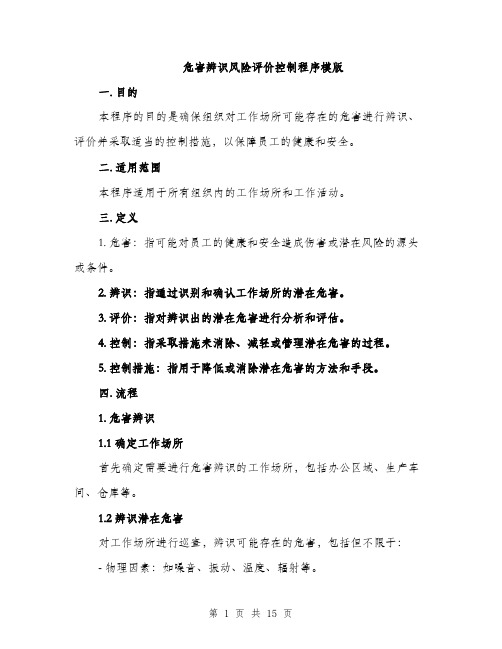
危害辨识风险评价控制程序模版一. 目的本程序的目的是确保组织对工作场所可能存在的危害进行辨识、评价并采取适当的控制措施,以保障员工的健康和安全。
二. 适用范围本程序适用于所有组织内的工作场所和工作活动。
三. 定义1. 危害:指可能对员工的健康和安全造成伤害或潜在风险的源头或条件。
2. 辨识:指通过识别和确认工作场所的潜在危害。
3. 评价:指对辨识出的潜在危害进行分析和评估。
4. 控制:指采取措施来消除、减轻或管理潜在危害的过程。
5. 控制措施:指用于降低或消除潜在危害的方法和手段。
四. 流程1. 危害辨识1.1 确定工作场所首先确定需要进行危害辨识的工作场所,包括办公区域、生产车间、仓库等。
1.2 辨识潜在危害对工作场所进行巡查,辨识可能存在的危害,包括但不限于:- 物理因素:如噪音、振动、温度、辐射等。
- 化学因素:如有毒物质、危险化学物质等。
- 生物因素:如病毒、细菌、昆虫等。
- 人员因素:如人员紧张、工作负荷过大、工作时间过长等。
2. 风险评价2.1 收集数据收集有关危害的数据,包括但不限于工作场所的材料安全数据表、危险化学品的标签和说明、工作场所的检测报告等。
2.2 分析数据对收集到的数据进行分析,评估潜在危害的影响程度、发生概率和可能的后果。
2.3 评估风险根据辨识出的潜在危害和分析的数据,对风险进行评估,确定风险的优先级。
3. 风险控制3.1 优先级排序根据评估的风险优先级,确定需要优先控制的风险。
3.2 采取控制措施针对辨识出的危害,采取相应的控制措施,包括但不限于:- 工程控制:如改变工作场所的布局、安装防护设备等。
- 行政控制:如制定安全操作规程、提供培训等。
- 个人防护措施:如佩戴个人防护装备、使用安全工具等。
3.3 控制措施的效果评估经过一定时间的实施和运行之后,对采取的控制措施进行评估,确定其是否有效,如有需要可进行调整和改进。
四. 责任分工- 所有员工:参与危害辨识和风险评估的工作,提供相关数据和信息。
化学品风险评估及管理程序新

化学品风险评估及管理程序一、目的为了对本公司化学品进行有效评估、管理﹐防止在采购﹑运输﹑储存﹑使用﹑报废的过程中对环境造成不良影响和对人员造成伤害﹐特制定本程序。
二、适用范围本程序适用于本公司化学危险物品及油品从采购到废弃全过程的风险评估及管理。
三、职责3.1仓管部负责所采购的化学危险物品及油品的接收﹑储存﹑发放﹑废弃管理﹔3.2物控部负责收集、保存相应的MSDS(物质安全指引)复印件或包含物质特性﹑四、处理方法的作业指导书。
4.0 程序4.1 化学品的采购4.1.1各部门依据本部门实际生产中的需求﹐确定本部门正常生产消耗的化学危险物品﹑油品的需求量,并有计划地进行采购,确保化学危险品及油品的库存量降到最低标准;4.1.2在选择使用化学危险品、油品时,根据生产工艺对化学危险品、油品的使用要求,满足相同条件下,优先选择毒害性与危险性较小的产品;4.1.3在与供货商签订购买合同或订货单时,应要求供货商在运输及装卸过程中采取防止泄漏﹑倾倒等预防措施;并提供化学危险物品及油品的化学性能方面的性质和禁忌,采取相应的预防和应急措施。
4.1.4由仓管部负责组织制定本公司《化学危险品一览表》管理更新化学危险品清单,并根据供应商提供的MSDS完善成相关的化学险品﹑油品的物质性能表及存储、使用规范,并将其发放到相关危险品及油品的存储﹑使用部门。
4.2化学危险品及油品的运输4.2.1运输﹑搬运化学危险品﹑油品时,要了解该化学危险品﹑油品的性质和禁忌,严禁有禁忌的化学危险品﹑油品混装运输﹐严禁人货混装运输;严禁倒置﹐并且轻拿轻放﹐避免重压﹐以防化学危险品﹑油品的包装破碎﹑4.2.2化学危险品及油品在搬运过程中﹐一定要注意箱体﹑桶体﹑箭头标识方向。
4.2.3钢瓶气体搬运时﹐不得拿着瓶盖或阀门护罩部分﹐把瓶举起搬运﹐要使用气瓶手推车或其它适当运输工具﹐待钢瓶定位妥当后﹐方可除下阀门护罩。
4.3化学品及油品的储存4.3.1对所有采购或购买的化学危险品及油品﹐必须对实物进行验收﹐检查包装是否密封﹐有无破损以及是否在有效期内﹐若不符合﹐应要求供应商退货﹐符合要求安排入库﹐危险品标识置于显眼处;4.3.2化学危险品及油品必须有专用的仓库﹐危险品仓库要有明显的标识﹐并且应有良好的通风和配备灭火器;4.3.3对易倒的化学危险品﹑油品不允许高层存放;4.3.4化学危险品管理人员应进行一定的培训。
化学品风险评估及管理程序-2018
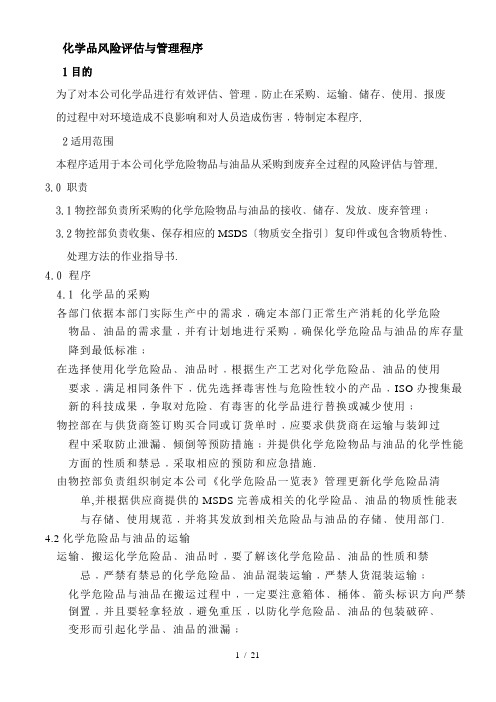
化学品风险评估与管理程序1目的为了对本公司化学品进行有效评估、管理﹐防止在采购﹑运输﹑储存﹑使用﹑报废的过程中对环境造成不良影响和对人员造成伤害﹐特制定本程序.2适用范围本程序适用于本公司化学危险物品与油品从采购到废弃全过程的风险评估与管理.3.0 职责3.1物控部负责所采购的化学危险物品与油品的接收﹑储存﹑发放﹑废弃管理﹔3.2物控部负责收集、保存相应的MSDS〔物质安全指引〕复印件或包含物质特性﹑处理方法的作业指导书.4.0 程序4.1 化学品的采购各部门依据本部门实际生产中的需求﹐确定本部门正常生产消耗的化学危险物品﹑油品的需求量﹐并有计划地进行采购﹐确保化学危险品与油品的库存量降到最低标准﹔在选择使用化学危险品﹑油品时﹐根据生产工艺对化学危险品﹑油品的使用要求﹐满足相同条件下﹐优先选择毒害性与危险性较小的产品﹐ISO办搜集最新的科技成果﹐争取对危险﹑有毒害的化学品进行替换或减少使用﹔物控部在与供货商签订购买合同或订货单时﹐应要求供货商在运输与装卸过程中采取防止泄漏﹑倾倒等预防措施﹔并提供化学危险物品与油品的化学性能方面的性质和禁忌﹐采取相应的预防和应急措施.由物控部负责组织制定本公司《化学危险品一览表》管理更新化学危险品清单,并根据供应商提供的MSDS完善成相关的化学险品﹑油品的物质性能表与存储、使用规范﹐并将其发放到相关危险品与油品的存储﹑使用部门. 4.2化学危险品与油品的运输运输﹑搬运化学危险品﹑油品时﹐要了解该化学危险品﹑油品的性质和禁忌﹐严禁有禁忌的化学危险品﹑油品混装运输﹐严禁人货混装运输﹔化学危险品与油品在搬运过程中﹐一定要注意箱体﹑桶体﹑箭头标识方向严禁倒置﹐并且要轻拿轻放﹐避免重压﹐以防化学危险品﹑油品的包装破碎﹑变形而引起化学品﹑油品的泄漏﹔钢瓶气体搬运时﹐不得拿着瓶盖或阀门护罩部分﹐把瓶举起搬运﹐要使用气瓶手推车或其它适当运输工具﹐待钢瓶定位妥当后﹐方可除下阀门护罩.4.3化学品与油品的储存对所有采购或购买的化学危险品与油品﹐必须对实物进行验收﹐检查包装是否密封﹐有无破损以与是否在有效期内﹐若不符合﹐应要求供应商退货﹐符合要求安排入库﹐危险品标识置于显眼处﹔化学危险品与油品必须有专用的仓库﹐危险品仓库要有明显的标识﹐并且应有良好的通风和配备灭火器.对易倒的化学危险品﹑油品不允许高层存放﹔化学危险品管理人员应进行一定的培训.所有进出化学危险品仓库的人员必须有具备相应化学危险品与油品储存管理常识或安全管理人员陪同﹔化学危险品仓库内应有化学危险品性能〔如化学成分﹑危险性﹑预防处理措施等〕方面资料<即物质安全指引>;4.4化学危险品﹑油品的发放和领取化学危险品仓库管理者依据批准的领料单发放物料﹐并与时将发放化学危险品的资料填入保管卡﹔在发放﹑领取﹑运输﹑储存化学危险品﹑油品时﹐相关部门必须安排具有危险品﹑油品运储管理常识的员工操作﹐避免意外事故发生﹔所有化学危险品需转换或分装到其它容器时﹐应在转移或分装后的容器标识清楚化学危险品与油品的名称﹐并尽可能按其特性贴上安全标志.4.5化学危险品与油品的使用在使用化学危险品与油品时﹐应尽量做到不洒落﹐避免泄漏﹔45.1化学危险品﹑油品使用完毕后﹐应将其空容器密封好﹐放于指定位置﹐在未净化处理以前﹐不得更换原安全标志﹔化学危险品使用现场应有该化学危险品的性能资料﹐以便查阅﹔使用化学危险品的人员应配备必要的防护用品.4.6化学危险品﹑油品的应急措施化学危险品﹑油品在储存﹑使用过程如有发现泄漏﹐应针对不同情况﹐迅速采取应急措施﹐具体参照《化学危险品储存﹑使用作业指引》.泄漏过程所收集到危险物质应按《废弃物管理程序》处理﹐不得随意处置.4.7受化学危险品﹑油品伤害的急救皮肤接触﹕当皮肤接触到强腐蚀和易经皮肤吸收引起中毒的物质时﹐要迅速脱被污染的衣着﹐立即用大量清水或肥皂彻底清洗﹐对强刺激和腐蚀性物质最少清洗15分钟﹔眼睛受污染时﹐用清水彻底冲冼﹐对强刺激和腐蚀性物质冲洗时间应不少于15分钟﹐冲洗时应将眼睑提起﹐注意将结膜内的化学危险物品全部冲出﹐要边冲洗边转动眼睛﹔口服中毒患者应首先催吐﹐在催吐前喝水500ml左右,然后用手指或钝物刺激舌根和咽后壁﹐催吐要反复数次﹐直到呕吐物全部为饮入清水为止.若食入强酸等腐蚀性毒物﹐不能催吐﹐应饮入牛奶或蛋清﹔呼吸道吸入有毒化学蒸汽的﹐应将中毒者移到空气清新处急救﹔采取自救﹑急救后症状未消失的﹐应立即就医治疗.4.8化学危险品与油品废弃各部门各工序使用过的化学危险品与油品的空瓶﹑空罐或过期化学危险物要交给人力资源部﹐由人力资源统一交有资质的单位处理﹐在没有处理之前﹐瓶罐上的标识不得撕下.有关化学危险品﹑油品废弃物的处理方法﹐按《固体废弃物控制程序》执行. 4.9监督检查物控部每天须派专人对化学品仓的温湿度进行点检﹐结果记入《温湿度记录表》中.管理部每季度对化学危险品仓库进行检查﹐记录于《环境状况检查表》中.内容包括﹕灭火器是否有效﹔化学危险品有无异常﹐如泄漏﹑容器裂开等﹔标识是否明确清晰﹔仓库内是否有化学品的异味﹔发现有任何异常﹐都必须采取纠正和预防措施.4.10培训各部门应制订培训计划﹐对使用﹑管理化学危险物品与油品岗位的工人进行特殊培训.确保在发生异常或发生紧急情况下﹐能与正确处理﹐以免对人员或环境造成危害.4.11当发生紧急事故时按《紧急事故应急救援预案》处理.4. 12 化学品的评估根据实情每年至少一次由环境管理代表组织采购部、仓储部、生产部、品质部、工程部等相关部门人员对工厂所使用的化学品进行评估,见《化学品风险评估与使用作业指引》5.0相关文件与记录5.1《化学品一览表》;5.2《固体废弃物控制程序》;5.3《环境状况检查表》;5.4《温湿度记录表》;5.5《物质安全指引》;5.6《化学品风险评估与使用作业指引》;5.7《紧急事故应急救援预案》.化学品风险评估程序1.目的:建立一个化学品风险评估程序来评价化学品在使用过程中的风险程度.2.范围:适用于所有使用化学品的车间、部门.3.职责:各使用车间、部门与生产技术部对本规程的执行负责.4.正文:4.1 定义化学品风险评估是对化学品在使用过程中可能存在的对人员产生不良影响的情况〔如化学品的毒性、暴露时间等〕进行评价或描述风险的方法,以保证人员在受控的良好的情形下进行操作.4.2 种类——定性风险评估——定量风险评估4.3 依据——化学品的毒性——使用频率——使用时间——使用量——工程控制4.4 定性风险评估程序4.4.1根据所评价的化学品使用情况建立由安全、卫生、使用部门人员组成的联合评估小组. 4.4.2 对所评估的化学品的基本信息进行调查、确认.4.4.3 查阅化学品安全数据表〔MSDS〕对该化学品的危险性〔如危险源、毒性、职业暴露等〕进行资料调查.4.4.4 根据该化学品在使用过程中的使用情况〔如暴露时间、使用频率、使用量等〕确定风险等级.4.4.5 检查现有的工业控制情况,并进行相应的记录.4.4.6 综合上述情况,对该化学品在使用中的风险进行最终评估,确定风险等级与是否需要进行风险控制的进一步措施.4.4.7 如风险评估等级确定为低级,但与国家、地方法律、法规抵触的,应以国家、地方法律、法规的要求为准,进行整改.4.4.8 如风险评估等级确定为中级,则需进行定量风险评估.4.5 定量风险评估程序4.5.1 确定行动限〔AL〕依据化学品安全数据表MSDS,确定行动限〔AL〕为接触限值〔TLV〕的50%.4.5.2 检测对该化学品所进行操作的环境进行取样测试,记录测试结果〔TV〕.4.5.3 评估将测试结果与行动限〔AL〕与接触限值〔TLV〕进行对比,根据下表做相应评估以与需采取的相应风险控制措施.风险评估表:4.6 评估记录4.6.1 化学品风险评估记录见附录1.4.6.2 化学品风险评估登记表见附录2.4.6.3 化学品风险评估由生产技术部经理审核批准.4.7 信息传递将评估结果与相关控制措施告之评估部门、卫生部门和该岗位操作人员,使其能正确操作与控制.5.附录附录1:化学品风险评估表附录2:化学品风险评估登记表6.交叉参考——危险源识别与风险评估的标准操作程序——化学品安全数据表MSDS附录1:化学品风险评估表附录2:危险化学品风险评估李海伟王芳2017年12月12日黄磷风险评估化学品名称化学品中文名称:白磷化学品英文名称:phosphorus yellow中文名称2:黄磷英文名称2:phosphorus white技术说明书编码:473 CAS No.:7723-14-0分子式:P4分子量:123.90危险性概述健康危害:急性吸入中毒表现有呼吸道刺激症状、头痛、头晕、全身无力、呕吐、心动过缓、上腹疼痛、黄疸、肝肿大.重症出现急性肝坏死、中毒性肺水肿等.口服中毒出现口腔糜烂、急性胃肠炎,甚至发生食道、胃穿孔.数天后出现肝、肾损害.重者发生肝、肾功能衰竭等.本品可致皮肤灼伤,磷经灼伤皮肤吸收引起中毒,重者发生中毒性肝病、肾损害、急性溶血等,以致死亡.慢性中毒:神经衰弱综合征、消化功能紊乱、中毒性肝病.引起骨骼损害,尤以下颌骨显著,后期出现下颌骨坏死与齿槽萎缩.环境危害:对环境有危害.燃爆危险:本品属自燃物品,高毒,具刺激性.急救措施皮肤接触:脱去污染的衣着,用大量流动清水冲洗.立即涂抹2%~3%硝酸银灭磷火.就医.眼睛接触:立即提起眼睑,用大量流动清水或生理盐水彻底冲洗至少15分钟.就医.吸入:迅速脱离现场至空气新鲜处.保持呼吸道通畅.如呼吸困难,给输氧.如呼吸停止,立即进行人工呼吸.就医.食入:立即用2%硫酸铜洗胃,或用1:5000高锰酸钾洗胃.洗胃与导泻应谨慎,防止胃肠穿孔或出血.就医消防措施危险特性:白磷接触空气能自燃并引起燃烧和爆炸.在潮湿空气中的自燃点低于在干燥空气中的自燃点.与氯酸盐等氧化剂混合发生爆炸.其碎片和碎屑接触皮肤干燥后即着火,可引起严重的皮肤灼伤.有害燃烧产物:氧化磷.灭火方法:消防人员必须穿橡胶防护服、胶鞋、并佩戴过滤式防毒面具<全面罩>或自给式呼吸器灭火.灭火剂:雾状水.泄漏应急处理应急处理:隔离泄漏污染区,限制出入.切断火源.建议应急处理人员戴自给正压式呼吸器,穿防毒服.不要直接接触泄漏物.小量泄漏:用水、潮湿的沙或泥土覆盖.收入金属容器并保存于水或矿物油中.大量泄漏:在专家指导下清除.操作处置与储存操作注意事项:应保存在水中,且必须浸没在水下,隔绝空气.储存于阴凉、通风的库房.远离火种、热源.应与氧化剂、酸类、卤素、食用化学品分开存放,切忌混储.采用防爆型照明、通风设施.禁止使用易产生火花的机械设备和工具.储区应备有合适的材料收容泄漏物.应严格执行极毒物品"五双"管理制度.储存注意事项:密闭操作,提供充分的局部排风.操作尽可能机械化、自动化.操作人员必须经过专门培训,严格遵守操作规程.建议操作人员佩戴自吸过滤式防毒面具〔全面罩〕,穿胶布防毒衣,戴橡胶手套.远离火种、热源,工作场所严禁吸烟.使用防爆型的通风系统和设备.避免与氧化剂、酸类、卤素接触.搬运时要轻装轻卸,防止包装与容9 / 21器损坏.配备相应品种和数量的消防器材与泄漏应急处理设备.倒空的容器可能残留有害物.接触控制/个体防护中国MAC<mg/m3>:0.03前苏联MAC<mg/m3>:0.03TLVTN:ACGIH 0.02mg/m3监测方法:工作现场禁止吸烟、进食和饮水.工作完毕,彻底清洗.实行就业前和定期的体检.工程控制:严加密闭,提供充分的局部排风.尽可能机械化、自动化.提供安全淋浴和洗眼设备.呼吸系统防护:可能接触毒物时,应该佩戴自吸过滤式防毒面具〔全面罩〕.眼睛防护:呼吸系统防护中已作防护.身体防护:穿胶布防毒衣.手防护:戴橡胶手套.其他防护:气相色谱法;硝酸银分光光度法理化特性主要成分:纯品外观与性状:无色至黄色蜡状固体,有蒜臭味,在暗处发淡绿色磷光.熔点<℃>:44.1沸点<℃>:280.5相对密度<水=1>:1.82相对蒸气密度<空气=1>:4.42饱和蒸气压<kPa>:0.13<76.6℃>燃烧热<kJ/mol>:3093.2临界温度<℃>:721引燃温度<℃>:30溶解性:不溶于水,微溶于苯、氯仿,易溶于二硫化碳.主要用途:用作特种火柴原料,以与用于磷酸、磷酸盐与农药、信号弹等的制造.稳定性和反应活性禁配物:强氧化剂、酸类、卤素、硫.避免接触的条件:受热、光照.运输信息包装方法:小开口钢桶〔黄磷顶面须用厚度为15厘米以上的水层覆盖〕;装入盛水的玻璃瓶、塑料瓶或金属容器〔用塑料瓶时必须再装入金属容器内〕.物品必须完全浸没在水中,严封后再装入坚固木箱.运输注意事项:铁路运输时若使用小开口钢桶包装,须经铁路局批准.运输时运输车辆应配备相应品种和数量的消防器材与泄漏应急处理设备.装运本品的车辆排气管须有阻火装置.运输过程中要确保容器不泄漏、不倒塌、不坠落、不损坏.严禁与氧化剂、酸类、卤素、食用化学品等混装混运.运输途中应防曝晒、雨淋,防高温.中途停留时应远离火种、热源.车辆运输完毕应进行彻底清扫.铁路运输时要禁止溜放.黄磷供应不与时的补救措施10 / 21当遇到铁路运输出现重大自然灾害和铁路停运等原因造成黄磷供应不与时,应采用公路运输与时补救,确保生产正常运行,并关注铁路运输何时开通.法规信息法规信息:化学危险物品安全管理条例<1987年2月17日国务院发布>,化学危险物品安全管理条例实施细则<化劳发[1992] 677号>,工作场所安全使用化学品规定<[1996]劳部发423号>等法规,针对化学危险品的安全使用、生产、储存、运输、装卸等方面均作了相应规定;常用危险化学品的分类与标志<GB 13690-92>将该物质划为第4.2 类自燃物品;剧毒物品分级、分类与品名编号<GA 57-93>中,该物质属第一类A级无机剧毒品.硫磺风险评估化学品名称化学品中文名称:硫化学品英文名称:sulfur分子式:S 分子量:32.06成分/组成信息主要成分:纯品CAS No.:7704-34-9危险性概述健康危害:因其能在肠内部分转化为硫化氢而被吸收,故大量口服可致硫化氢中毒.急性硫化氢中毒的全身毒作用表现为中枢神经系统症状,有头痛、头晕、乏力、呕吐、共济失调、昏迷等.本品可引起眼结膜炎、皮肤湿疹.对皮肤有弱刺激性.生产中长期吸入硫粉尘一般无明显毒性作用.急救措施皮肤接触:脱去污染的衣着,用肥皂水和清水彻底冲洗皮肤.眼睛接触:提起眼睑,用流动清水或生理盐水冲洗.就医.吸入:迅速脱离现场至空气新鲜处.保持呼吸道通畅.如呼吸困难,给输氧.如呼吸停止,立即进行人工呼吸.就医.食入:饮足量温水,催吐.就医.消防措施危险特性:与卤素、金属粉末等接触剧烈反应.硫磺为不良导体,在储运过程中易产生静电荷,可导致硫尘起火.粉尘或蒸气与空气或氧化剂混合形成爆炸性混合物.灭火方法:遇小火用砂土闷熄.遇大火可用雾状水灭火.切勿将水流直接射至熔融物,以免引起严重的流淌火灾或引起剧烈的沸溅.消防人员须戴好防毒面具,在安全距离以外,在上风向灭火.泄漏应急处理应急处理:隔离泄漏污染区,限制出入.切断火源.建议应急处理人员戴防尘面具〔全面罩〕,穿一般作业工作服.不要直接接触泄漏物.小量泄漏:避免扬尘,用洁净的铲子收集于干燥、洁净、有盖的容器中,转移至安全场所.大量泄漏:用塑料布、帆布覆盖.使用无火花工具收集回收或运至废物处理场所处置.操作处置与储存储存注意事项:储存于阴凉、通风的库房.远离火种、热源.包装密封.应与氧化剂分开存放,切忌混储.采用防爆型照明、通风设施.禁止使用易产生火花的机械设备和工具.储区应备有合适的材料收容泄漏物.接触控制/个体防护11 / 21最高容许浓度:中国MAC:未制定标准;前苏联MAC:6工程控制:密闭操作,局部排风.呼吸系统防护:一般不需特殊防护.空气中粉尘浓度较高时,佩戴自吸过滤式防尘口罩.眼睛防护:一般不需特殊防护.身体防护:穿一般作业防护服.手防护:戴一般作业防护手套.其他防护:工作现场禁止吸烟、进食和饮水.工作完毕,淋浴更衣.注意个人清洁卫生.理化特性外观与性状:淡黄色脆性结晶或粉末,有特殊臭味.熔点<℃>:119 沸点<℃>:444.6 相对密度<水=1>: 2.0饱和蒸气压<kPa>:0.13<183.8℃> 临界温度<℃>:1040临界压力<MPa>:11.75 引燃温度<℃>:232爆炸下限%<V/V>:35mg/m3溶解性:不溶于水,微溶于乙醇、醚,易溶于二硫化碳.主要用途:用于制造染料、农药、火柴、火药、橡胶、人造丝、医药等.稳定性和反应活性禁配物:强氧化剂.毒理学资料急性毒性:LD50:无资料LC50:无资料运输信息危险货物编号:41501 UN编号:1350 包装类别:O53包装方法:两层塑料袋或一层塑料袋外麻袋、塑料编织袋、乳胶布袋;塑料袋外复合塑料编织袋〔聚丙烯三合一袋、聚乙烯三合一袋、聚丙烯二合一袋、聚乙烯二合一袋〕;螺纹口玻璃瓶、铁盖压口玻璃瓶、塑料瓶或金属桶〔罐〕外普通木箱;螺纹口玻璃瓶、塑料瓶或镀锡薄钢板桶〔罐〕外满底板花格箱、纤维板箱或胶合板箱. 液体硫磺遇不可抗拒的因素导致供应不与时的补救措施当遇到天气原因,道路原因,车辆原因、供方原因等造成液体硫磺不能与时进厂,必须动用储备的固体硫磺投料,保证生产的正常运行,并密切关注造成液体硫磺供应不上的诸多原因,尽快恢复液体硫磺供应.法规信息国内化学品安全管理法规:化学危险物品安全管理条例<1987年2月17日国务院发布>,化学危险物品安全管理条例实施细则<化劳发[1992] 677号>,工作场所安全使用化学品规定<[1996]劳部发423号>等法规,针对化学危险品的安全使用、生产、储存、运输、装卸等方面均作了相应规定;常用危险化学品的分类与标志<GB 13690-92>将该物质划为第4.1类易燃固体.12 / 21液碱风险评估化学品名称化学品中文名称:氢氧化钠化学品英文名称:sodiun hydroxide中文名称2:烧碱英文名称2:Caustic soda技术说明书编码:813CAS No.:1310-73-2成分/组成信息分子式:NaOH分子量:40.01有害物成分含量CAS No.氢氧化钠≥99.5%1310-73-2危险性概述健康危害:本品有强烈刺激和腐蚀性.粉尘刺激眼和呼吸道,腐蚀鼻中隔;皮肤和眼直接接触可引起灼伤;误服可造成消化道灼伤,粘膜糜烂、出血和休克.环境危害:对水体可造成污染.燃爆危险:本品不燃,具强腐蚀性、强刺激性,可致人体灼伤.急救措施皮肤接触:立即脱去污染的衣着,用大量流动清水冲洗至少15分钟.就医.眼睛接触:立即提起眼睑,用大量流动清水或生理盐水彻底冲洗至少15分钟.就医.吸入:迅速脱离现场至空气新鲜处.保持呼吸道通畅.如呼吸困难,给输氧.如呼吸停止,立即进行人工呼吸.就医.食入:用水漱口,给饮牛奶或蛋清.就医.消防措施危险特性:与酸发生中和反应并放热.遇潮时对铝、锌和锡有腐蚀性,并放出易燃易爆的氢气.本品不会燃烧, 遇水和水蒸气大量放热, 形成腐蚀性溶液.具有强腐蚀性.有害燃烧产物:可能产生有害的毒性烟雾.灭火方法:用水、砂土扑救,但须防止物品遇水产生飞溅,造成灼伤.泄漏应急处理应急处理:隔离泄漏污染区,限制出入.建议应急处理人员戴防尘面具〔全面罩〕,穿防酸碱工作服.不要直接接触泄漏物.小量泄漏:避免扬尘,用洁净的铲子收集于干燥、洁净、有盖的容器中.也可以用大量水冲洗,洗水稀释后放入废水系统.大量泄漏:收集回收或运至废物处理场所处置.操作处置与储存操作注意事项:密闭操作.操作人员必须经过专门培训,严格遵守操作规程.建议操作人员佩戴头罩型电动送风过滤式防尘呼吸器,穿橡胶耐酸碱服,戴橡胶耐酸碱手套.远离易燃、可燃物.避免产生粉尘.避免与酸类接触.搬运时要轻装轻卸,防止包装与容器损坏.配备泄漏应急处理设备.倒空的容器可能残留有害物.稀释或制备溶液时,应把碱加入水中,避免沸腾和飞溅.储存注意事项:储存于阴凉、干燥、通风良好的库房.远离火种、热源.库内湿度最好不大于85%.包装必须密封,切勿受潮.应与易〔可〕燃物、酸类等分开存放,切忌混储.储区应备有合适的材料收容泄漏物.接触控制/个体防护职业接触限值中国MAC<mg/m3>:0.5前苏联MAC<mg/m3>:0.5TLVTN:OSHA 2mg/m3TLVWN:ACGIH 2mg/m3监测方法:酸碱滴定法;火焰光度法工程控制:密闭操作.提供安全淋浴和洗眼设备.呼吸系统防护:可能接触其粉尘时,必须佩戴头罩型电动送风过滤式防尘呼吸器.必要时,佩戴空气呼吸器.眼睛防护:呼吸系统防护中已作防护.身体防护:穿橡胶耐酸碱服.手防护:戴橡胶耐酸碱手套.其他防护:工作场所禁止吸烟、进食和饮水,饭前要洗手.工作完毕,淋浴**.注意个人清洁卫生.理化特性主要成分:含量: 工业品一级≥99.5%; 二级≥99.0%.外观与性状:白色不透明固体,易潮解.熔点<℃>:318.4沸点<℃>:139013 / 21相对密度<水=1>:2.12饱和蒸气压<kPa>:0.13<739℃>溶解性:易溶于水、乙醇、甘油,不溶于丙酮.主要用途:用于肥皂工业、石油精炼、造纸、人造丝、染色、制革、医药、有机合成等.稳定性和反应活性禁配物:强酸、易燃或可燃物、二氧化碳、过氧化物、水.避免接触的条件:潮湿空气.毒理学资料刺激性:家兔经眼:1%重度刺激.家兔经皮:50mg/24 小时,重度刺激.生态学资料由于呈碱性,对水体可造成污染,对植物和水生生物应给予特别注意.废弃处置废弃处置方法:处置前应参阅国家和地方有关法规.中和、稀释后,排入废水系统.运输信息危险货物编号:82001UN编号:1823包装类别:O52包装方法:固体可装入0.5 毫米厚的钢桶中严封,每桶净重不超过100 公斤;塑料袋或二层牛皮纸袋外全开口或中开口钢桶;螺纹口玻璃瓶、铁盖压口玻璃瓶、塑料瓶或金属桶〔罐〕外普通木箱;螺纹口玻璃瓶、塑料瓶或镀锡薄钢板桶〔罐〕外满底板花格箱、纤维板箱或胶合板箱;镀锡薄钢板桶〔罐〕、金属桶〔罐〕、塑料瓶或金属软管外瓦楞纸箱.运输注意事项:铁路运输时,钢桶包装的可用敞车运输.起运时包装要完整,装载应稳妥.运输过程中要确保容器不泄漏、不倒塌、不坠落、不损坏.严禁与易燃物或可燃物、酸类、食用化学品等混装混运.运输时运输车辆应配备泄漏应急处理设备.法规信息法规信息化学危险物品安全管理条例<1987年2月17日国务院发布>,化学危险物品安全管理条例实施细则<化劳发[1992] 677号>,工作场所安全使用化学品规定<[1996]劳部发423号>等法规,针对化学危险品的安全使用、生产、储存、运输、装卸等方面均作了相应规定;常用危险化学品的分类与标志<GB 13690-92>将该物质划为第8.2 类碱性腐蚀品.叔丁醇风险评估化学品名称化学品中文名称:叔丁醇化学品俗名:三甲基甲醇化学品英文名称:trimethyl carbinol技术说明书编码:354CAS No.:75-65-0成分/组成信息有害物成分CAS No.叔丁醇75-65-0危险性概述14 / 21。
有害物质风险评估控制程序

4权责
4.1各部门推行委员:有害物质污染源的识别、评价、登录及管理。
4.2采购部:
4.2.1将有害物质风险评估通知相关供方;
4.2.2督促相关供方进行改善。
4.3技术部:
4.3.1产品实现全过程HSF控制计划实施标准的确定。
4.4管理者代表:
低风险
1、一级供方直接提供的盖公司
公章的第三方检测合格报告
1.签订环保合约,要求一级供方1次/年送检
并提供合格测试报告原件.
2.现场审查供方有害物质管理体系:1次/年.
3.本公司进料时进行有害物质成分测试.
4.本公司每年将成品送第三方公证机构测试.
风险级别
判定准则
控制方法
高风险
合格分数以下
1.不予合作,或要求供方建立RoHS/QC080000
5.4.4供方评价的结果:采购部、品质部、技术部
5.4.5与以往HSF不合格的关联性:品质部
5.4.6核准:HSF管理者代表
5.5有害物质风险评价的准则
5.5.1材料/部件/活动本身的特性:
风险级别
判定准则
控制方法
高风险
可能介入有害物质
1.签订环保合约,要求一级供方1次/年送检并提供合
格报告原件.
2.要求供方建立RoHS/QC080000管理体系.
建议参考相关法规、顾客或其它要求,了解常见的有害物质通常存在何种部件/活动之中.
批准
文件编号
/WI/JS-JS-**
审核
版本号
A/0
拟定
有害物质风险评价控制程序
页次
3/5
5.5.2供方评价的结果
化学品风险评估程序

化学品风险评估程序1.目的:建立一个化学品风险评估程序来评价化学品在使用过程中的风险程度。
2.围:适用于所有使用化学品的车间、部门。
3.职责:各使用车间、部门及生产技术部对本规程的执行负责。
4.正文:4.1 定义化学品风险评估是对化学品在使用过程中可能存在的对人员产生不良影响的情况〔如化学品的毒性、暴露时间等〕进展评价或描述风险的方法,以保证人员在受控的良好的情形下进展操作。
4.2 种类——定性风险评估——定量风险评估4.3 依据——化学品的毒性——使用频率——使用时间——使用量——工程控制4.4 定性风险评估程序4.4.1根据所评价的化学品使用情况建立由平安、卫生、使用部门人员组成的联合评估小组。
4.4.2 对所评估的化学品的根本信息进展调查、确认。
4.4.3 查阅化学品平安数据表〔MSDS〕对该化学品的危险性〔如危险源、毒性、职业暴露等〕进展资料调查。
4.4.4 根据该化学品在使用过程中的使用情况〔如暴露时间、使用频率、使用量等〕确定风险等级。
4.4.5 检查现有的工业控制情况,并进展相应的记录。
4.4.6 综合上述情况,对该化学品在使用中的风险进展最终评估,确定风险等级及是否需要进展风险控制的进一步措施。
4.4.7 如风险评估等级确定为低级,但与、地方法律、法规抵触的,应以、地方法律、法规的要求为准,进展整改。
4.4.8 如风险评估等级确定为中级,那么需进展定量风险评估。
4.5 定量风险评估程序4.5.1 确定行动限〔AL〕依据化学品平安数据表MSDS,确定行动限〔AL〕为接触限值〔TLV〕的50%。
4.5.2 检测对该化学品所进展操作的环境进展取样测试,记录测试结果〔TV〕。
4.5.3 评估将测试结果与行动限〔AL〕及接触限值〔TLV〕进展比照,根据下表做相应评估以及需采取的相应风险控制措施。
4.6 评估记录4.6.1 化学品风险评估记录见附录1。
4.6.2 化学品风险评估登记表见附录2。
环境有害物质风险评估程序(含表格)

环境有害物质风险评估程序(QC080000-2017)1.0 目的为识别本公司所有物料、部件的环境管理物质风险等级,利于管理活动中对环境管理物质的控制,特制订本管理规定,作为原料、部件风险等级评估及管理。
2.0 范围本规定适用于所有物料、部件的风险评估、供应商定期监查及入料环境有害物质检测的管理。
3.0 定义3.1物料风险:指原物料、部品、组件等因构成材料成份属性或工艺等因素共同决定了其含有环境有害物质的风险,一经评定后,一般不会再发生变化;3.2供应商风险:指提供物料的供应商的环境管理物质体系的综合水准,一般通过对供应商评定的结果,以及其日常交货环境品质状况来评定。
4.0 职责4.1系统部:负责新供应商的环境风险等级评估;4.2品管部:负责物料、部件风险的评估;负责按物料风险、供应商风险等级制订环境管理物质抽样检验计划;负责供应商的定期环境监查及供应商风险等级调整;4.3采购部:负责组织新供应商现场评定审核。
5.0 作业程序5.1品管部和采购部共同评定HSF物料风险等级评估标准(见后面5.5节);5.2品管部按照风险评估标准,将供应商进行风险分类,并制订年度供应商审核计划;5.2.1评价为高风险的供应商,必须进行现场稽核,每年不少于一次;5.2.2评价为中风险的供应商,必须进行现场稽核,每2年一次;5.2.3评价为低风险的供应商,可不进行现场稽核,每年要求其进行自我评估;5.3品管部按材料风险等级,制订《物料风险评估一览表》,IQC按规定要求送样检测,保留相应的检测记录;5.3.1抽样检测频率:A、高风险物料,每周至少抽样检测一次(距上次交货时间超过1周的,也需检测);B、中风险物料,每月检测1次(距上次交货时间超过1个月的,也需检测);C、低风险物料,每3月检测1次(距上次交货时间超过3个月的,也需检测),另具挥发性的低风险物料可免检。
5.4送样、检测及判定,按《XRF检测规范》等文件规定要求执行。
危害辨识和风险评价控制程序范本(2篇)
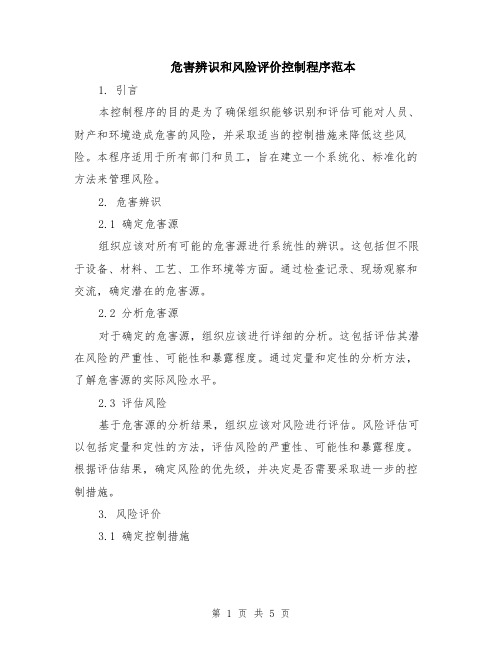
危害辨识和风险评价控制程序范本1. 引言本控制程序的目的是为了确保组织能够识别和评估可能对人员、财产和环境造成危害的风险,并采取适当的控制措施来降低这些风险。
本程序适用于所有部门和员工,旨在建立一个系统化、标准化的方法来管理风险。
2. 危害辨识2.1 确定危害源组织应该对所有可能的危害源进行系统性的辨识。
这包括但不限于设备、材料、工艺、工作环境等方面。
通过检查记录、现场观察和交流,确定潜在的危害源。
2.2 分析危害源对于确定的危害源,组织应该进行详细的分析。
这包括评估其潜在风险的严重性、可能性和暴露程度。
通过定量和定性的分析方法,了解危害源的实际风险水平。
2.3 评估风险基于危害源的分析结果,组织应该对风险进行评估。
风险评估可以包括定量和定性的方法,评估风险的严重性、可能性和暴露程度。
根据评估结果,确定风险的优先级,并决定是否需要采取进一步的控制措施。
3. 风险评价3.1 确定控制措施根据风险评估的结果,组织应该确定适当的控制措施来降低风险。
这包括技术控制、管理控制和个人防护措施等。
确保控制措施在技术可行和经济可行的范围内,并尽量消除或降低危害源。
3.2 实施控制措施组织应该将确定的控制措施纳入具体的操作程序中,并确保所有相关的部门和员工都能正确理解和遵守这些程序。
同时,组织应该提供培训和教育,确保员工能够正确使用控制措施。
3.3 监测和调整组织应该建立一个监测和调整机制,确保控制措施的有效性。
通过定期的检查和评估,发现和纠正存在的问题,并根据需要采取进一步的措施。
同时,组织应该建立一个风险沟通的机制,确保员工能够及时了解到相关的风险信息。
4. 总结本控制程序的目标是确保组织能够对潜在的危害源进行有效的辨识和评估,并采取适当的控制措施来降低风险。
通过系统化和标准化的方法,组织能够更好地管理风险,保护人员、财产和环境的安全和健康。
因此,所有部门和员工都应该遵循本程序,积极参与风险管理工作。
危害辨识和风险评价控制程序范本(二)一、定义与目的危害辨识和风险评价是指对工作场所可能对员工、环境和财产造成的危害进行识别和评估的过程,并采取相应的控制措施以降低风险水平。
有害物质识别和控制程序

有害物质识别和控制程序(RoHS)一、目的为了对公司对产品和制造流程中的有害物质进行持续识别和控制,从而确保产品在我公司内部不受到污染.二、适用范围本文件适用于公司ROHS产品的相关活动.三、职责与权限3.1公司技术部负责组织相关部门对有害物质开展识别调查和评价,并对控制措施进行制定、指导、监督、检查。
3.2生产部负责推行清洁生产、开展污染预防和控制。
3.3与RoHS有可能的污染源控制直接相关的操作工应做好本岗位污染控制工作。
四、程序5.1有害物质辨识的时机和更新a. 程序建立之初,由技术部组织进行全厂有害物资污染辨识。
b. 在相关法律法规变更或追加、涉及到新项目的活动、产品或服务、以及相关方要求等情况下,可适时进行识别c. 当环境、工艺、用料等发生改变,导致新的污染环节出现时,要重新开展评估活动。
d. 当条件没有变化时,每年至少重新评价1次,以评价控制措施的有效性。
5.2有害物质识别的开展5.2.1各部门选择和确定可能含有有害物质的原材料、辅料、包装材料等,以及可能造成产品含有有害物质的活动或服务,其中活动的选择可涉及作业过程、仓储、生产场所等多方面。
5.2.2在识别有害物质时要考虑以下几个方面:a. 污染源辨识应依据有关法律法规及有关规定及标准,并结合工厂实际情况,考虑过去、现在、将来三种情况及正常、异常、紧急三种状态。
b. 对进入现场的人员(含内部及外部人员)、相关方的活动也应辨识。
c. 有害物质识别应考虑公司所有使用的材料、辅料、包装材料等,将识别出的包含有害物质材料列入《有害物质一览表》d. 污染源辨识应考虑工厂所有与产品有关的活动及作业现场,从工作区域布置、原辅料物资、生产工艺及设备,辅助生产设施、作业环境几部分,各部门分别分析其存在的污染源,列入《污染源辨识和控制清单》登记。
e. 各部门将识别出的有害物质存在的材料和生产过程中可能造成有害物质污染的污染源交质量程部汇总,由管理者代表审批。
危害辨识风险评价控制程序(通用版)
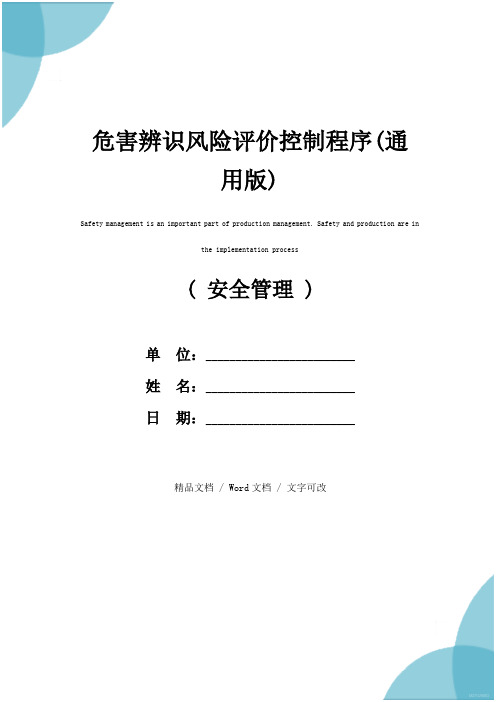
( 安全管理 )单位:_________________________姓名:_________________________日期:_________________________精品文档 / Word文档 / 文字可改危害辨识风险评价控制程序(通用版)Safety management is an important part of production management. Safety and production are inthe implementation process危害辨识风险评价控制程序(通用版)1目的对本项目在管理和施工中所有活动、产品和服务的风险因素进行识别、评价以及对其控制措施的策划。
2范围适用于本项目在管理和工程施工中所有可能涉及人员安全及财产损失的风险因素的识别、评价以及对其控制措施的策划。
3职责和权限3.1管理者代表负责危害辨识和风险评价的领导工作,并批准本项目重大风险因素清单。
3.2施工技术管理部是本程序的主管部门,负责组织有关人员进行本项目的危害辨识和风险评价工作。
工程技术人员负责所承担项目的危害辨识和风险评价。
3.3项目经理部负责本单位危害辨识和风险评价工作。
4活动描述4.1危害辨识风险评价的步骤4.1.1HSE管理部和施工技术管理部负责组织相关人员进行工程的危害辨识和风险评价工作,编制本项目的《职业安全健康危害辩识与风险评价一览表》。
4.1.2HSE管理部和施工技术管理部根据公司的《职业安全健康危害辩识与风险评价一览表》,确定《职业安全健康重大风险因素清单》,报管理者代表批准。
并把《职业安全健康危害辩识与风险评价一览表》和《职业安全健康重大风险因素清单》发放给相关单位。
4.1.3HSE管理部和施工技术管理部根据上报的新的风险因素补充本项目的《职业安全健康危害辩识与风险评价一览表》和《职业安全健康重大风险因素清单》,并下发各项目部。
4.2识别4.2.1选择活动、产品和服务根据本项目特点,从以下四个方面选择活动、产品或服务:1)施工工艺与安全技术管理;2)施工作业人员操作活动;3)设备设施安装、运行、维护;4)化学危险品储存与使用;4.2.2本项目在活动、产品和服务中的风险因素存在于以下几个环节:1)管理:安全措施计划、操作规程、人员技能培训、防护用品;2)人员素质:人员意识、技能、经验、行为;3)环境条件:施工现场作业环境与设备(设施)状态;4)职业健康、消防。
有害物质风险评估程序

有害物质风险评估程序更多免费资料下载请进:好勤学习社区有害物质风险评估程序1.0目的本程序在于全面有效的识别与评估RSC-MS产品生産中的物料、供给商和生产进程中所产生的风险,从而更好的预防、降低和操纵可能産生的交叉污染;2.0范围适用于公司ROHS治理的活动进程、子进程与ROHS产品相关之各部门及场所;3.0概念无4.0职责4.1各部门调查和识别本部门同意的物料、效劳或活动进程等所有可能存在的风险,并书面报告给风险评估小组;4.2 治理代表负责召集各组员对各部门之报告进行评估,制定出所需的操纵方法,并跟进操纵方法的完成情形;5.0 作业程序风险分类1>风险评估小组成立:本公司之风险评估小组为环境推动小组兼任;2>风险评估中风险类别分为三大类:物料风险、供给商/加工商风险、进程风险;3>风险品级分为高风险与低风险两种类型;4>物料风险评估包括:a> ROHS产品BOM所列的物料;b> 生産进程利用之物料;物料的风险评估1> 知足以下条件之一即被评定为高风险物料;a>有多种物料组成,物料中较易带有受限物质:如COB、马达等含有多种材料的元器件等;b>为增强某种功能、用途、外观成效等而在物料或制作工艺中成心增加受限物质(需由相关技术人员判定),紧固件中的螺丝/螺母等,因电镀/钝化行业中的三价铬工艺目前不够成熟,多数厂家采纳六价铬处置工艺;c>物料的成份复杂或不纯(需由相关技术人员判定),含有多种成份或成份不清楚,如线材/化工原料等;d>含有回收再用的物料,且难以被追溯;如塑胶制品生产须添加适当之PBB/PBDE阻燃剂,若是从头回收利用的塑料中阻燃剂无法衡量或操纵,容易造成交叉污染;使PBB/PBDE含量超标;2> 知足以下条件之一的物料被判定为低风险物料;a>间接物料未直接用在产品上,如包裝用的周转容器/工夾具等;b>沒有利用回收再用的物料;c>物料成份组合中沒有混合的机遇;d>由单一物料组成,受限制物质阻碍的概率低;供给商/加工商的风险评估1>知足以下条件之一即被评定为高风险供给商/加工商:a>新供给商/加工商或持续一年未有任何ROHS产品业务往来的供给商/加工商;b>以往两年物料供给或加工曾经显现过严峻的问题;c> 完全沒有ROHS概念的供给商;2>知足以下条件之一即被评定为低风险供给商/加工商:a>在以往供给的两年中都未显现过严峻问题的供给商/加工商;b>已经成立了有关ROHS产品之治理系统或有关ROHS产品的治理体系;c>世界级跨国公司或行业内声誉超卓的公司,如菲利浦、索尼等;工序的风险评估进程的风险包括生产进程中所有生产设备、工/夹具、测试仪器、工作环境、操作人员等在正常、异样、紧急的状况下所有可能致使交叉污染产生的风险状况;1> 知足以下条件之一即被评定为高风险:a> 该进程利用的设备、工/夹具、测试仪器等并非ROHS操纵生产工序专用,且将直接接触产品,假设不通过相应的处置方法,将对ROHS物料或产品造成极大的交叉污染;b>该进程致使ROHS物料与非ROHS物料的混料机遇极大,如领料时ROHS物料与非ROHS物料无明显的区分,操作人员未受过专门ROHS培训,将致使混料;2>知足以下条件之一即被评定为低风险:a>该进程所利用的设备、工/夹具、测试仪器等属于ROHS产品生产专用,(或虽非ROHS产品专用,但并非直接与产品接触)且有有效的清洁方法;b>该进程致使ROHS物料和非ROHS物料的混料机遇很小;物料风险操纵方法:a>要求供给商/加工商提供由认可机构查验的ROHS测试报告;b>提供合格ROHS检测报告的频率暂定为1年1次;c>要求供给商/加工商在更改设计或工艺时須从头提供ROHS检测报告;b>要求供给商同我司签署“环保物料供给协议保证书”工序风险操纵a) 购买/加工新的及符合ROHS要求的工/夹具、利用设备、辅助材料,而且須保证是ROHS产品专用;b) 所有与ROHS产品相关工序之区域、设备、工/夹具、辅助材料、容器等都必需有明显之标识;c) 对所有专用工/夹具、设备进行清洁后方可利用;e) 工人必需通过ROHS相关知识培训并经考核合格方给予上岗;风险评估的频率a> 对物料的风险评估在设计初期或有任何设计或物料更改的时期进行;b>对供给商的风险评估为一年一次或有新供给商加入时进行;c>工序的风险评估在生产前或有任何工艺更改时进行,高风险工序最少每一年一次引用文件无表单/记录物料风险评估表供给商风险评估表制程风险评估表。
- 1、下载文档前请自行甄别文档内容的完整性,平台不提供额外的编辑、内容补充、找答案等附加服务。
- 2、"仅部分预览"的文档,不可在线预览部分如存在完整性等问题,可反馈申请退款(可完整预览的文档不适用该条件!)。
- 3、如文档侵犯您的权益,请联系客服反馈,我们会尽快为您处理(人工客服工作时间:9:00-18:30)。
管理制度编号:YTO-FS-PD127
有害物质风险评估程序通用版
In Order T o Standardize The Management Of Daily Behavior, The Activities And T asks Are Controlled By The Determined Terms, So As T o Achieve The Effect Of Safe Production And Reduce Hidden Dangers.
标准/ 权威/ 规范/ 实用
Authoritative And Practical Standards
有害物质风险评估程序通用版
使用提示:本管理制度文件可用于工作中为规范日常行为与作业运行过程的管理,通过对确定的条款对活动和任务实施控制,使活动和任务在受控状态,从而达到安全生产和减少隐患的效果。
文件下载后可定制修改,请根据实际需要进行调整和使用。
1.0目的
本程序在于全面有效的识别与评估RSC-MS产品生産中的物料、供应商和生产过程中所产生的风险,从而更好的预防、降低和控制可能産生的交叉污染;
2.0范围
适用于公司ROHS管理的活动过程、子过程与ROHS 产品相关之各部门及场所;
3.0定义
无
4.0职责
4.1各部门调查和识别本部门接受的物料、服务或活动过程等所有可能存在的风险,并书面报告给风险评估小组;
4.2 管理代表负责召集各组员对各部门之报告进行评估,制定出所需的控制措施,并跟进控制措施的完成情况;
5.0 作业程序
5.1风险分类
1>风险评估小组成立:本公司之风险评估小组为环境推进小组兼任;
2>风险评估中风险类别分为三大类:物料风险、供应商/加工商风险、过程风险;
3>风险等级分为高风险与低风险两种类型;
4>物料风险评估包括:a> ROHS产品BOM所列的物料;b> 生産过程使用之物料;
5.2物料的风险评估
1> 满足以下条件之一即被评定为高风险物料;
a>有多种物料构成,物料中较易带有受限物质:如COB、马达等含有多种材料的元器件等;
b>为增强某种功能、用途、外观效果等而在物料或制作工艺中有意增加受限物质(需由相关技术人员判定),紧固件中的螺丝/螺母等,因电镀/钝化行业中的三价铬工艺目前不够成熟,多数厂家采用六价铬处理工艺;
c>物料的成份复杂或不纯(需由相关技术人员判定),含有多种成份或成份不清楚,如线材/化工原料等;
d>含有回收再用的物料,且难以被追溯;如塑胶制品生产须添加适当之PBB/PBDE阻燃剂,如果重新回收使用的塑料中阻燃剂无法衡量或控制,容易造成交叉污染;使PBB/PBDE含量超标;
2> 满足以下条件之一的物料被判定为低风险物料;
a>间接物料未直接用在产品上,如包裝用的周转容器/工夾具等;
b>沒有使用回收再用的物料;
c>物料成份组合中沒有混合的机会;
d>由单一物料构成,受限制物质影响的几率低;
5.3供应商/加工商的风险评估
1>满足以下条件之一即被评定为高风险供应商/加工商:
a>新供应商/加工商或持续一年未有任何ROHS产品业务往来的供应商/加工商;
b>以往两年物料供应或加工曾经出现过严重的问题;
c> 完全沒有ROHS概念的供应商;
2>满足以下条件之一即被评定为低风险供应商/加工商:
a>在以往供应的两年中都未出现过严重问题的供应商/加工商;
b>已经建立了有关ROHS产品之管理系统或有关ROHS产品的管理体系;
c>世界级跨国公司或行业内声誉超卓的公司,如菲利浦、索尼等;
5.4工序的风险评估
过程的风险包括生产过程中所有生产设备、工/夹具、测试仪器、工作环境、操作人员等在正常、异常、紧急的状况下所有可能导致交叉污染产生的风险状况;
1> 满足以下条件之一即被评定为高风险:
a> 该过程使用的设备、工/夹具、测试仪器等并非ROHS控制生产工序专用,且将直接接触产品,若不经过相应的处理措施,将对ROHS物料或产品造成极大的交叉污染;
b>该过程导致ROHS物料与非ROHS物料的混料机会极大,如领料时ROHS物料与非ROHS物料无明显的区分,操作人员未受过专门ROHS培训,将导致混料;
2>满足以下条件之一即被评定为低风险:
a>该过程所使用的设备、工/夹具、测试仪器等属于ROHS产品生产专用,(或虽非ROHS产品专用,但并不直接与产品接触)且有有效的清洁措施;
b>该过程导致ROHS物料和非ROHS物料的混料机会很小;
5.5物料风险控制措施:
a>要求供应商/加工商提供由认可机构检验的ROHS 测试报告;
b>提供合格ROHS检测报告的频率暂定为1年1次;
c>要求供应商/加工商在更改设计或工艺时須重新提供
ROHS检测报告;
b>要求供应商同我司签署“环保物料供应协议保证书”
5.6工序风险控制
a) 购买/加工新的及符合ROHS要求的工/夹具、使用设备、辅助材料,并且須保证是ROHS产品专用;
b) 所有与ROHS产品相关工序之区域、设备、工/夹具、辅助材料、容器等都必须有明显之标识;
c) 对所有专用工/夹具、设备进行清洁后方可使用;
e) 工人必须经过ROHS相关知识培训并经考核合格方给予上岗;
5.7风险评估的频率
a> 对物料的风险评估在设计初期或有任何设计或物料更改的阶段进行;
b>对供应商的风险评估为一年一次或有新供应商加入时进行;
c>工序的风险评估在生产前或有任何工艺更改时进行,高风险工序最少每年一次
6.0 引用文件
无
7.0 表单/记录
7.1 物料风险评估表
7.2 供应商风险评估表
7.3 制程风险评估表
该位置可输入公司/组织对应的名字地址
The Name Of The Organization Can Be Entered In This Location。