航空发动机叶片增材制造
航空发动机叶片关键技术发展现状分析
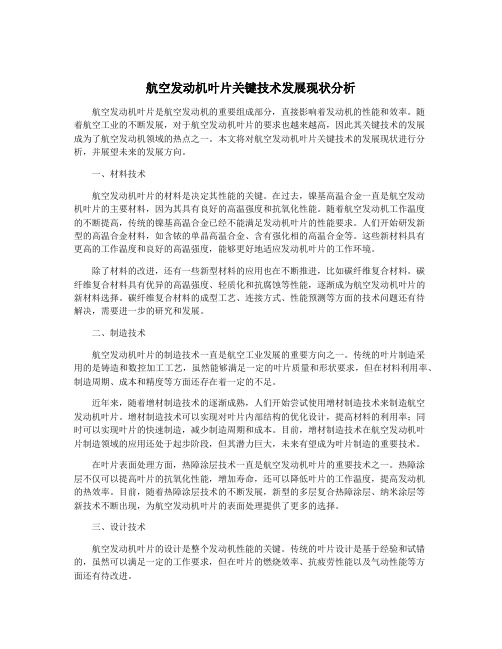
航空发动机叶片关键技术发展现状分析航空发动机叶片是航空发动机的重要组成部分,直接影响着发动机的性能和效率。
随着航空工业的不断发展,对于航空发动机叶片的要求也越来越高,因此其关键技术的发展成为了航空发动机领域的热点之一。
本文将对航空发动机叶片关键技术的发展现状进行分析,并展望未来的发展方向。
一、材料技术航空发动机叶片的材料是决定其性能的关键。
在过去,镍基高温合金一直是航空发动机叶片的主要材料,因为其具有良好的高温强度和抗氧化性能。
随着航空发动机工作温度的不断提高,传统的镍基高温合金已经不能满足发动机叶片的性能要求。
人们开始研发新型的高温合金材料,如含铱的单晶高温合金、含有强化相的高温合金等。
这些新材料具有更高的工作温度和良好的高温强度,能够更好地适应发动机叶片的工作环境。
除了材料的改进,还有一些新型材料的应用也在不断推进,比如碳纤维复合材料。
碳纤维复合材料具有优异的高温强度、轻质化和抗腐蚀等性能,逐渐成为航空发动机叶片的新材料选择。
碳纤维复合材料的成型工艺、连接方式、性能预测等方面的技术问题还有待解决,需要进一步的研究和发展。
二、制造技术航空发动机叶片的制造技术一直是航空工业发展的重要方向之一。
传统的叶片制造采用的是铸造和数控加工工艺,虽然能够满足一定的叶片质量和形状要求,但在材料利用率、制造周期、成本和精度等方面还存在着一定的不足。
近年来,随着增材制造技术的逐渐成熟,人们开始尝试使用增材制造技术来制造航空发动机叶片。
增材制造技术可以实现对叶片内部结构的优化设计,提高材料的利用率;同时可以实现叶片的快速制造,减少制造周期和成本。
目前,增材制造技术在航空发动机叶片制造领域的应用还处于起步阶段,但其潜力巨大,未来有望成为叶片制造的重要技术。
在叶片表面处理方面,热障涂层技术一直是航空发动机叶片的重要技术之一。
热障涂层不仅可以提高叶片的抗氧化性能,增加寿命,还可以降低叶片的工作温度,提高发动机的热效率。
目前,随着热障涂层技术的不断发展,新型的多层复合热障涂层、纳米涂层等新技术不断出现,为航空发动机叶片的表面处理提供了更多的选择。
航空发动机叶片再制造技术的应用及其发展趋势

航空发动机叶片再制造技术的应用及其发展趋势航空发动机叶片再制造技术是指对废旧的航空发动机叶片进行修复、再制造或更新的技术,以降低航空发动机的维修成本、延长使用寿命,并提高发动机的性能和可靠性。
这一技术在航空领域中具有重要意义,能够进一步推动航空发动机的发展与创新。
1.修复与再制造:通过对叶片进行修复和再制造,使其恢复到原有性能水平,以减少修复成本和提高使用寿命。
修复过程中主要包括清洗、去除受损材料、填充修补、表面处理等步骤,再制造则涉及到材料选择、加工和热处理等工艺。
通过修复和再制造,航空发动机叶片的性能可以恢复到几乎与新制品相当。
2.更新与改进:利用再制造技术,对旧有叶片进行更新和改进,以提高性能和可靠性。
例如通过采用新材料、改变叶片结构、优化叶片内部流道等方式,实现对叶片性能的提升。
这样可以延长航空发动机的使用寿命,提高发动机的性能指标,同时降低运营成本。
3.节能环保:再制造技术对航空工业的发展有着重要意义。
航空发动机叶片是航空发动机中易受损的关键部件,采用再制造技术可以降低其对环境的影响。
通过再制造,可以避免废旧叶片的填埋和焚烧,减少对环境的污染,同时还可节约大量原材料和能源的消耗。
1.材料创新:新型材料的研发将是航空发动机叶片再制造技术的重要发展方向。
高温合金、复合材料等新材料的应用可以提高叶片的耐用性、抗疲劳性和耐高温性能,从而延长其使用寿命。
2.进一步精细化加工:随着精密制造技术的不断发展,航空发动机叶片再制造将越来越具有精细化的特点。
高精度加工和表面处理技术的应用可以进一步提高叶片的空气动力性能和剩余寿命,实现优化再制造。
3.数字化技术的应用:随着数字化技术的飞速发展,航空发动机叶片再制造也将借助于数字化技术的应用实现更高效、更精准的再制造。
通过建立叶片的数字模型、使用虚拟仿真技术和智能制造技术,可以提高制造过程的一体化和智能化水平。
4.航空维修市场的需求:全球航空业的持续发展将对航空发动机叶片再制造技术提出更高的要求。
航空发动机部件增材制造修复工艺及质量检测

航空发动机部件增材制造修复工艺及质量检测航空发动机部件增材制造修复工艺及质量检测是航空工业中的一个重要领域。
增材制造修复工艺是指利用3D打印等技术对损坏的航空发动机部件进行修复的方法。
它可以将金属材料逐层添加或熔化,将部分或整个部件复原到设计要求的尺寸和形状。
以下是航空发动机部件增材制造修复工艺及质量检测的一般步骤和关键点:1. 损伤评估:对损坏的部件进行彻底的评估和分析,确定修复的可行性和必要性。
这包括对损伤的类型、大小、位置和严重程度进行检查和记录。
2. 设计修复方案:根据损伤评估结果,设计适当的修复方案。
这包括确定修复区域、修复方式、修复材料等。
3. 工艺规划:制定增材制造修复的详细工艺规划。
这包括选择合适的增材制造设备和参数,确定部件的分层加工路径和能源输入方式。
4. 制造修复:根据工艺规划,进行增材制造修复过程。
这可能涉及到激光熔化、电子束熔化、电弧增材制造等技术,根据需要进行适当的预热、后处理和热处理等工艺步骤。
5. 完成加工和后处理:对修复部件进行机械加工、表面处理和热处理等工艺,以满足设计要求的尺寸、形状和性能。
6. 质量检测:对修复部件进行全面的质量检测和评估。
这包括非破坏性检测(如超声波、X射线、磁粉检测等)、金相显微镜分析、机械性能测试等。
7. 质量控制和认证:建立合适的质量控制体系,确保修复部件符合相关标准和要求。
对修复部件进行认证和授权,以确保其安全可靠性。
航空发动机部件增材制造修复工艺及质量检测需要综合考虑材料特性、工艺参数、设备性能和修复部件的使用环境等因素。
通过严格的修复工艺和质量检测,可以保证修复部件的性能和可靠性,延长航空发动机的使用寿命,减少航空公司的成本和维修时间。
航空发动机叶片材料及制造技术现状
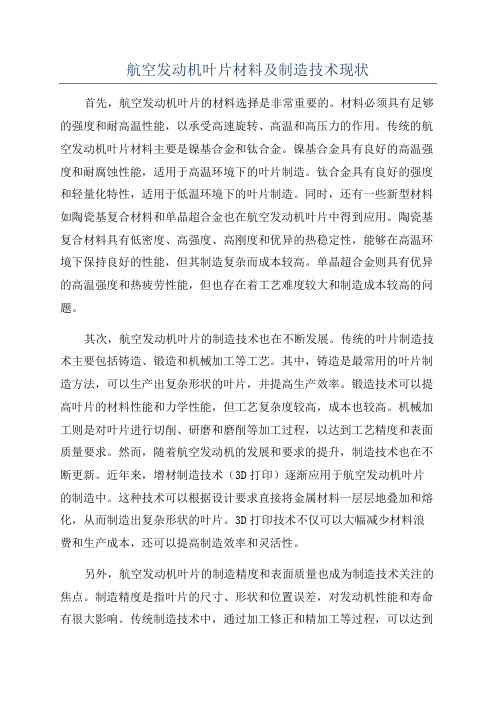
航空发动机叶片材料及制造技术现状首先,航空发动机叶片的材料选择是非常重要的。
材料必须具有足够的强度和耐高温性能,以承受高速旋转、高温和高压力的作用。
传统的航空发动机叶片材料主要是镍基合金和钛合金。
镍基合金具有良好的高温强度和耐腐蚀性能,适用于高温环境下的叶片制造。
钛合金具有良好的强度和轻量化特性,适用于低温环境下的叶片制造。
同时,还有一些新型材料如陶瓷基复合材料和单晶超合金也在航空发动机叶片中得到应用。
陶瓷基复合材料具有低密度、高强度、高刚度和优异的热稳定性,能够在高温环境下保持良好的性能,但其制造复杂而成本较高。
单晶超合金则具有优异的高温强度和热疲劳性能,但也存在着工艺难度较大和制造成本较高的问题。
其次,航空发动机叶片的制造技术也在不断发展。
传统的叶片制造技术主要包括铸造、锻造和机械加工等工艺。
其中,铸造是最常用的叶片制造方法,可以生产出复杂形状的叶片,并提高生产效率。
锻造技术可以提高叶片的材料性能和力学性能,但工艺复杂度较高,成本也较高。
机械加工则是对叶片进行切削、研磨和磨削等加工过程,以达到工艺精度和表面质量要求。
然而,随着航空发动机的发展和要求的提升,制造技术也在不断更新。
近年来,增材制造技术(3D打印)逐渐应用于航空发动机叶片的制造中。
这种技术可以根据设计要求直接将金属材料一层层地叠加和熔化,从而制造出复杂形状的叶片。
3D打印技术不仅可以大幅减少材料浪费和生产成本,还可以提高制造效率和灵活性。
另外,航空发动机叶片的制造精度和表面质量也成为制造技术关注的焦点。
制造精度是指叶片的尺寸、形状和位置误差,对发动机性能和寿命有很大影响。
传统制造技术中,通过加工修正和精加工等过程,可以达到较高的制造精度。
而3D打印技术可以根据设计要求直接打印出精密的叶片,可以实现更高的制造精度。
叶片的表面质量是指叶片的光洁度和粗糙度等表面特性。
传统制造技术中,通常需要通过机械加工和抛光等过程来改善叶片的表面质量。
航空发动机叶片制造及再制造技术研究
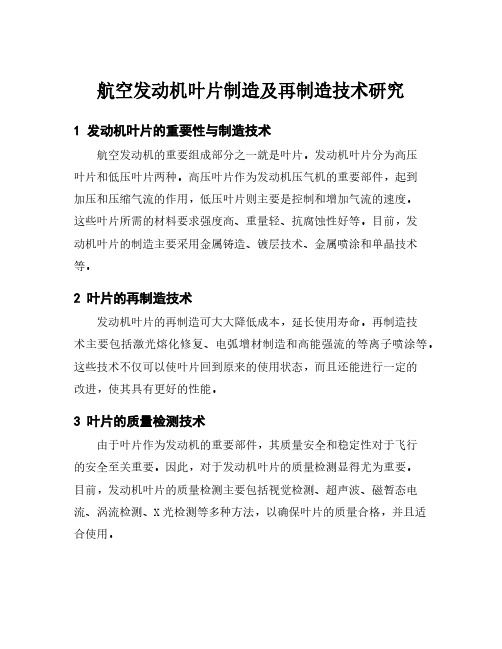
航空发动机叶片制造及再制造技术研究
1 发动机叶片的重要性与制造技术
航空发动机的重要组成部分之一就是叶片。
发动机叶片分为高压
叶片和低压叶片两种。
高压叶片作为发动机压气机的重要部件,起到
加压和压缩气流的作用,低压叶片则主要是控制和增加气流的速度。
这些叶片所需的材料要求强度高、重量轻、抗腐蚀性好等。
目前,发
动机叶片的制造主要采用金属铸造、镀层技术、金属喷涂和单晶技术等。
2 叶片的再制造技术
发动机叶片的再制造可大大降低成本,延长使用寿命。
再制造技
术主要包括激光熔化修复、电弧增材制造和高能强流的等离子喷涂等。
这些技术不仅可以使叶片回到原来的使用状态,而且还能进行一定的
改进,使其具有更好的性能。
3 叶片的质量检测技术
由于叶片作为发动机的重要部件,其质量安全和稳定性对于飞行
的安全至关重要。
因此,对于发动机叶片的质量检测显得尤为重要。
目前,发动机叶片的质量检测主要包括视觉检测、超声波、磁暂态电流、涡流检测、X光检测等多种方法,以确保叶片的质量合格,并且适
合使用。
发动机叶片是一个复杂的工艺要求高的零部件,需要不断研究和探索,以提高其质量和稳定性,确保飞行的安全。
对于发动机叶片的制造和再制造技术的研究如今已经非常成熟,但其在未来的发展和研究仍会是一个不断探索和突破的领域。
飞机发动机零部件粉末床融合增材制造工艺-概述说明以及解释
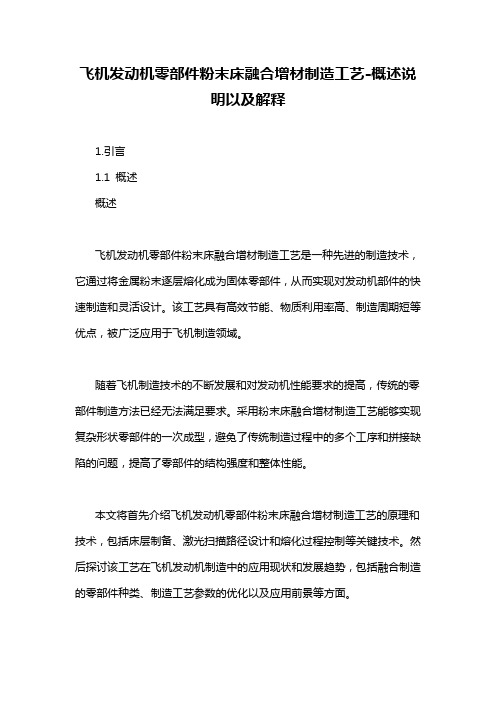
飞机发动机零部件粉末床融合增材制造工艺-概述说明以及解释1.引言1.1 概述概述飞机发动机零部件粉末床融合增材制造工艺是一种先进的制造技术,它通过将金属粉末逐层熔化成为固体零部件,从而实现对发动机部件的快速制造和灵活设计。
该工艺具有高效节能、物质利用率高、制造周期短等优点,被广泛应用于飞机制造领域。
随着飞机制造技术的不断发展和对发动机性能要求的提高,传统的零部件制造方法已经无法满足要求。
采用粉末床融合增材制造工艺能够实现复杂形状零部件的一次成型,避免了传统制造过程中的多个工序和拼接缺陷的问题,提高了零部件的结构强度和整体性能。
本文将首先介绍飞机发动机零部件粉末床融合增材制造工艺的原理和技术,包括床层制备、激光扫描路径设计和熔化过程控制等关键技术。
然后探讨该工艺在飞机发动机制造中的应用现状和发展趋势,包括融合制造的零部件种类、制造工艺参数的优化以及应用前景等方面。
通过对飞机发动机零部件粉末床融合增材制造工艺的研究和应用,可以提高飞机的整体性能和可靠性,实现对零部件性能和质量的精确控制。
同时,该工艺也具有很大的经济效益和环境效益,能够提高制造效率,降低能源消耗和废料产生。
在未来,飞机发动机零部件粉末床融合增材制造工艺有望进一步发展,推动飞机制造技术的革新和升级。
随着材料科学和工艺技术的不断进步,相信该工艺在飞机制造领域的应用前景将更加广阔,为飞机制造产业的发展提供了新的思路和解决方案。
1.2 文章结构文章结构部分的内容可以描述整篇文章的组织结构和内容安排,包括各个章节的主题和内容概述。
以下是一个可能的编写内容:文章结构:本篇文章主要分为引言、正文和结论三个部分,具体结构安排如下:1. 引言在引言部分,将会对飞机发动机零部件粉末床融合增材制造工艺进行概述,介绍其重要性和应用领域。
同时,还会简要介绍本文的结构和目的,为读者提供整体的内容框架。
2. 正文正文部分将分为两个主要章节:飞机发动机零部件粉末床融合增材制造工艺的原理和技术以及其应用与发展。
航 空 发 动 机 叶 片 涂 层

航空发动机叶片涂层技术一.涡轮叶片是先进航空发动机核心关键之一航空发动机被称为现代工业“皇冠上的明珠”,航空发动机是飞机的“心脏”,价值一般占到整架飞机的20%-25%。
目前,能独立研制、生产航空发动机的国家只有美、英、法、俄、中5个。
但是,无论“昆仑”、“秦岭”发动机、还是“太行”系列,我国航空发动机的水平距离这一领域的“珠穆朗玛”依然存在不小的差距。
美、俄、英、法四个顶级“玩家”能够自主研发先进航空发动机。
西方四国由于对未来战场与市场的担忧,在航空发动机核心技术上一直对中国实施禁运和封锁。
技术难关有很多。
本人认为涡轮叶片是先进航空发动机的核心技术之一。
随着航空航天工业的发展,对发动机的性能要求越来越高,要使发动机具有高的推重比和大的推动力,所采用的主要措施是提高涡轮进口温度。
国外在20世纪90年代,要求涡轮前燃气进口温度达1850-1950K。
美国在IHPTET计划中要求:在海平面标准大气条件下,航空燃气涡轮机的的涡轮进口温度高达2366K。
涡轮进口温度的提高要求发动机零件必须具有更高的抗热冲击、耐高温腐蚀、抗热交变和复杂应力的能力。
对于舰载机,由于在海洋高盐雾环境下长期服役,要求发动机的叶片的耐腐蚀性更高;常在沙漠上飞行的飞机,发动机的叶片要具有更好的耐磨蚀。
众所周知:镍基和钴基高温合金具有优异的高温力学和腐蚀性能,广泛用于制造航空发动机和各类燃气轮机的涡轮叶片(blade and vane)。
就材质来看:各国的高温合金型号虽各不相同,但就相近成分的高温合金来说,其性能相近(生产工艺方法不同有也造成性能有大的差异)。
好的高温合金的使用温度也只有1073K左右,为达到前面所说的要求温度,采用的方法有二:一是制成空心的叶片。
空心叶片自20世纪60年代中期出现以来,经历了对流冷却、冲击冷却、气膜冷却以及综合冷却的发展历程,使进气口温度高出叶片材料约300—500℃,内腔的走向复杂化和细致化。
这一步的改进仍难满足需要,且英国发展计划将取消冷却。
先进航天发动机叶片材料

先进航天发动机叶片材料先进航天发动机叶片材料的研究与开发,是航天航空技术领域的一个重要方向。
航天发动机的叶片材料需要具备高温抗氧化、高强度、低密度、高刚度等特点,以满足航天器在极端工作环境下的要求。
近年来,随着航天技术的不断发展,对航天发动机叶片材料的要求也越来越高,因此针对这些要求,科学家们进行了大量的研究工作。
目前,常用于航天发动机叶片材料的有镍基合金、钛基合金和复合材料等。
镍基合金具有良好的高温抗氧化性能和高强度,广泛用于航空发动机叶片材料。
钛基合金在高温和高强度方面具有优良的性能,尤其适用于航天飞行器中的高温燃气轮机叶片材料。
复合材料则以其低密度、高强度和良好的热稳定性,在航天三维推进系统中得到了广泛应用。
镍基合金是当前航天发动机叶片材料中使用最广泛的一类。
镍基合金具有优异的高温抗氧化性能、高强度和高热蠕变强度,并且在高温环境中具有良好的抗腐蚀性能。
此外,镍基合金还具有良好的可加工性和焊接性能,使其成为最常用的航天发动机叶片材料。
然而,传统的镍基合金在高温下容易发生热疲劳,这限制了其在航天发动机中的使用。
为了克服传统镍基合金的缺点,科学家们提出了许多改进的镍基合金材料。
例如,含有微量添加元素的高温合金,在提高镍基合金的高温强度和耐热性能的同时,还能够减轻材料的热蠕变损伤。
此外,也有研究人员提出了采用股状晶粒结构的大晶粒镍基合金,该结构能够阻止晶粒细化和晶界破坏,从而提高材料的高温持久性能。
钛基合金是另一类常用于航天发动机叶片材料的材料。
由于钛基合金具有低密度、高强度和优良的高温性能,因此被广泛应用于航天飞行器的高温燃气轮机叶片材料中。
钛基合金可以分为α+β型和β型两类,其中β型钛基合金具有优异的高温强度和低温塑性,因此在高速航空领域具有很大的潜力。
除了镍基合金和钛基合金,复合材料也在航天发动机叶片材料的研发中发挥着重要的作用。
复合材料以其低密度、高强度和良好的热稳定性而受到广泛关注。
目前,复合材料在航空航天领域中的应用主要是碳纤维增强复合材料。
新型增材制造技术在航空航天领域中的应用

新型增材制造技术在航空航天领域中的应用随着科技的不断进步,新型增材制造技术已经逐渐成为了航空航天领域中的新宠儿。
新型增材制造技术是指通过逐层堆积材料来制造三维物体的一种技术,与传统的制造方式完全不同。
与传统的加工方式相比,新型增材制造技术具有制造效率高、精度高、适用性广等明显优势,因此在航空航天领域中得到了广泛的应用。
一、新型增材制造技术在航空航天领域中的应用1、制造燃烧室航空发动机中的燃烧室是一个非常重要的部件,决定着发动机的性能和寿命。
由于燃烧室的形状复杂,传统的制造方式往往需要进行多次加工,且制造效率低、成本高。
而利用新型增材制造技术,可以直接通过三维打印机将燃烧室一次性制造出来,不仅大幅提高了生产效率,还降低了制造成本。
2、制造大型结构件在大型飞机制造中,钛合金等材料成为了广泛应用的材料,但是这些材料的制造、加工难度很大。
利用新型增材制造技术,可以直接将钛合金等材料堆积成所需要的大型结构件,而不需要进行摆锤加工等传统的加工方式,大大提高了生产效率。
3、制造复杂曲面结构件航空航天领域中常常需要制造形状复杂的曲面结构件,如蒙皮板、翼型等。
传统的制造方式难以满足这种形状的加工需求,而利用新型增材制造技术,可以直接通过三维打印机将所需要的形状一次性打印出来,提高了生产效率,同时大大提高了精度。
二、新型增材制造技术在航空航天领域中的发展趋势1、自适应制造技术自适应制造技术是指通过对物体的形态、质量、力学性能等方面的实时控制和调整,使得制造过程变得更加智能化。
在航空航天领域中,自适应制造技术可以将制造过程中的不确定性、变化性降至最低,大幅提高产品的质量和稳定性。
2、流态抑制技术流体流动对于航空航天领域中的制造工艺有着非常重要的意义。
流态抑制技术是指通过驱动气流,将流体在流动过程中的波动抑制住,从而获得更加稳定和高精度的流动。
这种技术可以应用于制造低声噪、低阻力、高效率的飞行器。
三、新型增材制造技术在航空航天领域中的优越性1、自适应性强新型增材制造技术具有很强的自适应性,能够根据不同的制造需求,对制造过程进行自动调整和控制,从而大幅提高了制造效率和精度。
航空发动机关键部件结构及制造工艺的发展
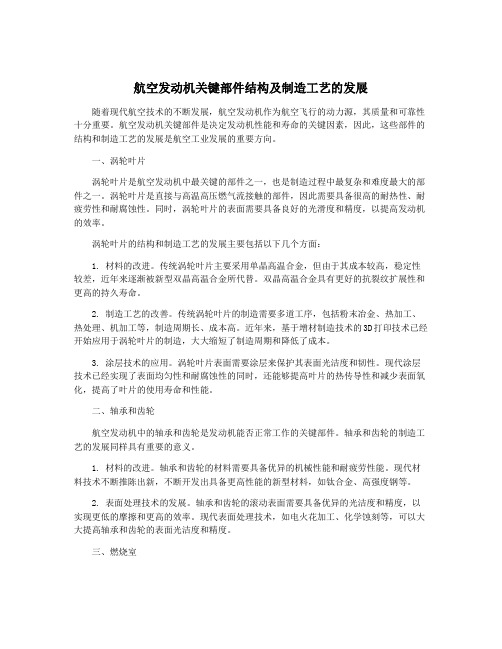
航空发动机关键部件结构及制造工艺的发展随着现代航空技术的不断发展,航空发动机作为航空飞行的动力源,其质量和可靠性十分重要。
航空发动机关键部件是决定发动机性能和寿命的关键因素,因此,这些部件的结构和制造工艺的发展是航空工业发展的重要方向。
一、涡轮叶片涡轮叶片是航空发动机中最关键的部件之一,也是制造过程中最复杂和难度最大的部件之一。
涡轮叶片是直接与高温高压燃气流接触的部件,因此需要具备很高的耐热性、耐疲劳性和耐腐蚀性。
同时,涡轮叶片的表面需要具备良好的光滑度和精度,以提高发动机的效率。
涡轮叶片的结构和制造工艺的发展主要包括以下几个方面:1. 材料的改进。
传统涡轮叶片主要采用单晶高温合金,但由于其成本较高,稳定性较差,近年来逐渐被新型双晶高温合金所代替。
双晶高温合金具有更好的抗裂纹扩展性和更高的持久寿命。
2. 制造工艺的改善。
传统涡轮叶片的制造需要多道工序,包括粉末冶金、热加工、热处理、机加工等,制造周期长、成本高。
近年来,基于增材制造技术的3D打印技术已经开始应用于涡轮叶片的制造,大大缩短了制造周期和降低了成本。
3. 涂层技术的应用。
涡轮叶片表面需要涂层来保护其表面光洁度和韧性。
现代涂层技术已经实现了表面均匀性和耐腐蚀性的同时,还能够提高叶片的热传导性和减少表面氧化,提高了叶片的使用寿命和性能。
二、轴承和齿轮航空发动机中的轴承和齿轮是发动机能否正常工作的关键部件。
轴承和齿轮的制造工艺的发展同样具有重要的意义。
1. 材料的改进。
轴承和齿轮的材料需要具备优异的机械性能和耐疲劳性能。
现代材料技术不断推陈出新,不断开发出具备更高性能的新型材料,如钛合金、高强度钢等。
2. 表面处理技术的发展。
轴承和齿轮的滚动表面需要具备优异的光洁度和精度,以实现更低的摩擦和更高的效率。
现代表面处理技术,如电火花加工、化学蚀刻等,可以大大提高轴承和齿轮的表面光洁度和精度。
三、燃烧室航空发动机中的燃烧室是将燃料和空气混合后爆炸燃烧产生动力的部件,是保持发动机高效能和低排放的关键部件。
增材制造的应用案例

增材制造的应用案例咱来唠唠增材制造那些超酷的应用案例吧。
一、医疗领域。
1. 定制化假肢。
你想啊,每个人的肢体残缺情况那可都不一样。
传统假肢制作起来可麻烦了,就像拿个模子硬套似的,好多人戴着不舒服。
但是增材制造就不一样啦!它能根据患者残肢的精确形状,像3D打印那样一层一层地做出超级贴合的假肢。
比如说,有个小伙子因为意外失去了手臂,用增材制造做出来的假肢,就像是给他量身定制的一件“高级装备”。
那假肢的外观还能根据他的喜好来设计呢,他想在上面印个超级英雄的标志都没问题。
而且,这种定制化的假肢佩戴起来更舒适,对他日常生活的帮助可大了,拿东西、做简单的工作都更方便了。
2. 个性化牙齿矫正器。
以前整牙的时候,那矫正器基本上都是大同小异的。
现在可好了,增材制造能根据每个人牙齿的具体形状和矫正需求来制作矫正器。
就像给每颗牙齿打造专属的“小房子”一样。
我有个朋友去整牙,用的就是增材制造的矫正器。
他说那感觉就像是牙齿被温柔地引导到正确的位置,不像以前那种通用的矫正器,有时候会磨得嘴疼。
而且,这种矫正器还能根据矫正的进度随时调整,就像牙齿的私人教练一样,让整牙变得更高效、更舒适。
3. 复杂手术模型。
医生们要做那些超级复杂的手术,比如说脑部手术或者心脏手术,以前只能看着X光片、CT图像在脑袋里想象手术的情况。
现在有了增材制造,就能把患者的病变器官按照1:1的比例打印出来。
比如说要做一个心脏搭桥手术,医生可以拿着这个3D打印出来的心脏模型,在上面比划着怎么搭桥,从哪里下刀最安全。
这就好比是在真正做手术之前先在一个逼真的“副本”上练习一样,大大提高了手术的成功率。
我听说有个医院就是用这种方法做了一个非常罕见的脑部肿瘤切除手术,医生在模型上研究了好久,手术的时候就特别顺利,就像开着导航去摘除肿瘤一样准确。
二、航空航天领域。
1. 制造轻量化零部件。
在航空航天里,重量那可是超级重要的。
飞机、火箭每减轻一克重量,都能节省好多燃料呢。
金属增材制造技术在航空制造领域的应用

金属增材制造技术在航空制造领域的应用随着机载电子设备和复合材料的发展,轻量化一直是航空工业的发展趋势。
金属增材制造技术为航空制造领域提供了新的解决方案,不仅可以减轻整机重量,更可以实现快速制造,提高了生产效率。
本文将从材料、工艺、应用三个方面介绍金属增材制造技术在航空制造领域的应用。
一、金属材料在航空制造中的应用金属增材制造领域使用最广泛的材料是钛合金。
钛合金因其高强度、高韧性和轻重量比而被广泛应用于航空制造领域。
在实际生产中,通过金属增材制造技术可以制备出复杂的几何形状的零件,而钛合金材料也正是满足这一需求的理想选择。
除此之外,金属增材制造还可以使用不同的金属材料制造复合材料。
例如,通过选择不同的金属材料,可以在生产过程中获得更好的强度和刚度。
这些复合材料可用于制造航空发动机叶片等高温部件。
二、金属增材制造的工艺过程金属增材制造技术的主要工艺过程包括熔融沉积、电子束融合、激光成形等。
其中,激光成形是最常用的一种工艺。
下面以激光成形为例来介绍金属增材制造的工艺过程。
1. 原材料预处理金属增材制造的原始材料一般为钛合金等金属粉末,因此需要对其进行预处理。
预处理目的是使金属粉末颗粒具有所需的形状和尺寸,以便于后续成形过程使用。
预处理方式主要有筛选、颗粒整形、烘烤等。
2. 构建支撑结构和预热基于CAD的设计将被导入微波炉的控制系统中。
系统会按照预设的CAD文件准确控制激光束的运动轨迹,$CO_2$激光束在精确控制的垂直方向上扫描并定位于工作区域所需成型的部位上。
3. 层层叠加激光束和金属粉末可用于建立任意复杂形状的零件。
因此,可以通过将多层分别加工制造成形,再将其堆叠组合,在高温与压力条件下焊接成整体复合体系。
该成型方法可以获得高精度形状和尺寸,并且还可以减少开发和制造时间。
三、金属增材制造在航空制造领域的应用1. 航空发动机叶片目前,航空发动机叶片是使用金属增材制造技术制造的最常见部件之一。
利用这种技术,可以在叶片表面上制造复合材料,从而使叶片在高温和高压的环境下具有更好的性能。
航空发动机叶片的生产制造技术

航空发动机叶片的生产制造技术航空发动机叶片是航空发动机的重要组成部分,它在整个发动机运行过程中承受着极高的温度、压力和振动等力载荷。
因此,航空发动机叶片的生产制造技术对航空发动机的性能、可靠性和寿命都有着重要影响。
在这篇文章中,我们将详细介绍航空发动机叶片的生产制造技术。
1.材料选择与预处理在进行叶片制造之前,需要对材料进行预处理,以去除杂质、提高材料的均匀性和晶粒细化。
预处理方法包括热处理、化学处理和表面处理等。
2.叶片造型与设计叶片的造型与设计是叶片制造的关键环节。
叶片的形状、结构和轮毂之间的连接方式直接影响着叶片的性能和寿命。
通常情况下,叶片的内部结构是由空腔、腔板和护腔等组成的。
这些结构可以提高叶片的强度和刚度,在高速旋转过程中减小振动和压力损失。
叶片的形状通常采用空气动力学原理和结构力学原理进行设计,以提高发动机的效率和推力。
同时,还需要考虑到叶片的制造可行性和工艺性,确保叶片可以顺利制造出来。
3.叶片制造工艺铸造是叶片制造的主要工艺,通常采用真空熔模铸造或单晶铸造等方法。
真空熔模铸造是指将预熔的合金材料注入到陶瓷模具中,然后进行冷却凝固,最后得到具有复杂形状和精密尺寸的叶片。
单晶铸造则是通过在模具中形成单一晶体结构,去除晶界和晶粒边界,提高叶片的高温性能和抗腐蚀性能。
锻造是叶片制造的另一种常见工艺,通过对金属材料进行加热和塑性变形,使其达到所需的形状和尺寸。
复合材料制造是使用纤维增强树脂基体材料制造叶片的工艺。
这种工艺具有良好的抗腐蚀性和高温性能,适用于制造大型和复杂形状的叶片。
机加工是对叶片进行最后加工和整形的工艺。
这包括数控机床加工、电火花加工、冲压和磨削等方法,以保证叶片的几何尺寸和表面质量。
热处理是对叶片进行热处理,以改善材料的组织结构和性能。
常见的热处理方法包括固溶处理、时效处理和表面处理等。
4.质量控制与检测质量控制主要通过严格的制造工艺和生产流程来实现,确保叶片的尺寸和形状的精确性。
复合材料在航空发动机叶片中的应用研究

复合材料在航空发动机叶片中的应用研究1. 引言航空发动机作为现代飞机的核心部件,对性能要求极高。
随着科技的不断进步,传统的金属材料在满足要求方面越来越受限制。
复合材料因其轻质、高强度和抗腐蚀等特性,成为航空发动机叶片的理想材料。
2. 复合材料的基本特性复合材料是由两种或多种不同类型的材料(如纤维增强塑料)组成的复合结构。
它由纤维增强物和基体材料组成,通过增强物的力学性能提高整体材料的强度和刚度。
3. 复合材料在航空发动机叶片中的应用3.1 轻量化设计复合材料具有很高的强度和刚度,比重较轻,使得航空发动机的叶片实现了更轻量化的设计。
相比传统金属材料,使用复合材料制造叶片可以降低重量,提高飞机的整体性能,包括燃油效率和航程。
3.2 抗腐蚀性能航空发动机叶片在恶劣环境下工作,常受到高温、高压和化学腐蚀等影响。
复合材料具有良好的抗腐蚀性能,能够抵抗氧化、酸碱和热腐蚀等。
这使得使用复合材料制造的叶片能够更好地适应航空发动机工作环境的要求。
3.3 强度与刚度提升通过使用纤维增强复合材料,航空发动机叶片的强度和刚度可以得到显著提升。
纤维增强材料具有高拉伸和弯曲强度,可以在高速转动和叶片受力时保持结构的完整性。
这使得航空发动机叶片能够承受更大的载荷,提高工作效率。
4. 复合材料在航空发动机叶片中的挑战4.1 制造难度复合材料的制造比传统金属材料更加复杂。
需要考虑纤维预浸料的处理、层压工艺和固化等多个制造工序。
这对制造工艺和工人的技术要求更高,增加了生产成本和制造周期。
4.2 高温性能航空发动机工作温度极高,复合材料在高温下会出现热稳定性问题。
材料的稳定性会受到影响,容易发生劣化和失效,甚至熔化。
因此,需要通过合理的材料选择和改进设计来解决高温性能问题。
5. 复合材料在航空发动机叶片中的未来发展5.1 材料性能改进为克服复合材料在高温条件下的局限性,需要进一步改进复合材料的热稳定性和耐高温性能。
研发新的增强纤维和基体材料,以及改进制造工艺,可以提高材料的高温性能。
增材制造技术在航空制造中的应用

增材制造技术在航空制造中的应用一、背景介绍随着科技的不断发展,航空工业也在不断壮大。
而在航空制造过程中,增材制造技术已经成为了一种重要的技术手段。
习惯于大量生产而不是个性化生产的航空工业也开始越来越注重增材制造技术的应用。
而本文将就增材制造技术在航空制造中的应用进行深入探讨。
二、增材制造技术的概念增材制造技术(Additive manufacturing technology)是一种利用数控机床或3D打印机等工具,逐层堆积加工原料材料制造零部件或成品的技术。
相对于传统的减材制造技术,增材制造技术具有制造出设计更加复杂的、结构性更好的零件的优势。
并且增材制造技术可以实现在一个成品中同时制造出很多原本需要分别制造的部件,这一点有助于加快产品生产和降低成本。
因此,增材制造技术已经成为了飞机制造领域的重要技术手段。
三、增材制造技术在航空制造中的应用1. 制造高性能、高可靠性的发动机叶片作为一款飞机最关键的部分,发动机叶片直接影响着飞机的整体性能,因此发动机叶片必须使用最新且最好的技术生产。
目前,在制造航空发动机叶片的过程中,增材制造技术已经被广泛采用。
通过增材制造技术,可以将叶片制造出更加强度高、性能优异、可靠性更高的单一部件,而不是传统的将不同的部分组成叶片的方式。
这样一来,发动机的整体性能也可以更好地提升。
2. 制造轻量化部件在航空制造过程中,轻量化一直是一个关键的课题。
而增材制造技术无疑是轻量化的有效工具。
相对于传统的制造方法,增材制造技术可以将硬质合金、铝合金和钛合金等材料加工成更加轻薄、高强度的零件,从而帮助轻量化、提高飞机的性能。
轻量化的好处在于降低飞机的燃油消耗,减少对环境的影响,同时也可以降低维护和生产成本。
3. 快速制造机械件和模具在航空制造过程中,机械部件和模具的制造数量通常非常巨大。
通过增材制造技术,可以在短时间内快速生产数量大、形状复杂的机械部件和模具,这样可以大大提高生产效率,从而降低生产成本。
航空发动机叶片用大尺寸复杂结构三维机织复合材料预制体的制备与应用方案(一)

航空发动机叶片用大尺寸复杂结构三维机织复合材料预制体的制备与应用方案一、背景随着航空工业的持续发展,对航空发动机的性能要求日益提高。
作为发动机的关键部件,叶片的品质和性能直接影响到整个发动机的性能。
传统上,航空发动机叶片采用金属材料制造,但随着复合材料的快速发展,其逐渐成为航空发动机叶片的首选材料。
大尺寸复杂结构三维机织复合材料预制体作为其中的一种,因其优异的力学性能和轻量化特性,受到业界的广泛关注。
二、工作原理大尺寸复杂结构三维机织复合材料预制体的制备主要依赖于先进的纺织技术和复合材料成型工艺。
首先,使用特制的织机,将玻璃纤维、碳纤维等高性能纤维按照特定的三维编织结构进行编织。
编织过程中,纤维的取向和分布可以精确控制,以形成满足设计要求的三维结构。
然后,将编织好的三维结构进行热压成型,过程中施加高温高压,使得纤维与树脂充分渗透,形成高强度、高刚度的复合材料。
最后,将得到的复合材料进行进一步的加工和修饰,以满足航空发动机叶片的特定需求。
三、实施计划步骤1.材料准备:选择适当的玻璃纤维、碳纤维以及其他增强纤维,同时选择合适的树脂作为基体。
2.织机准备:根据设计要求,调整织机的参数,确保编织过程中纤维的取向和分布可以精确控制。
3.编织:将纤维按照设计的三维结构进行编织,形成预制体。
4.热压成型:将编织好的预制体进行热压成型,过程中施加高温高压,使得纤维与树脂充分渗透。
5.加工和修饰:将得到的复合材料进行进一步的加工和修饰,以满足航空发动机叶片的特定需求。
6.性能测试:对制备好的航空发动机叶片进行性能测试,包括力学性能、热稳定性、耐腐蚀性等。
四、适用范围此制备方法主要适用于航空发动机叶片的制造,也可应用于其他需要大尺寸复杂结构复合材料的领域,如汽车、船舶等。
五、创新要点1.三维编织技术:通过先进的纺织技术,实现纤维的三维编织,形成满足设计要求的三维结构。
2.热压成型工艺:采用高温高压的工艺条件,使得纤维与树脂充分渗透,提高复合材料的性能。
增材制造技术在航空航天领域中的应用研究
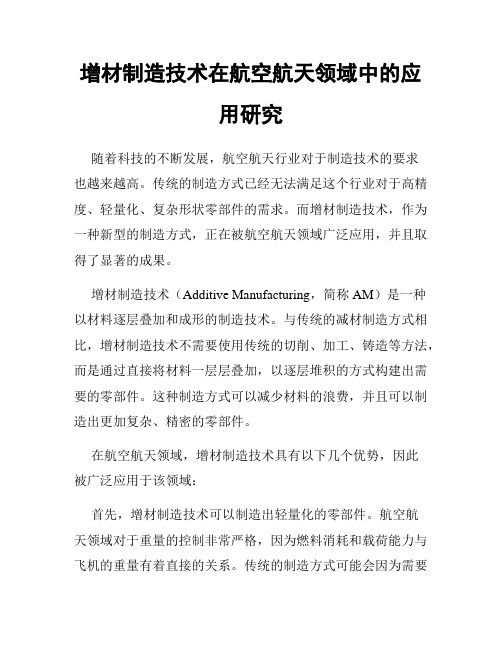
增材制造技术在航空航天领域中的应用研究随着科技的不断发展,航空航天行业对于制造技术的要求也越来越高。
传统的制造方式已经无法满足这个行业对于高精度、轻量化、复杂形状零部件的需求。
而增材制造技术,作为一种新型的制造方式,正在被航空航天领域广泛应用,并且取得了显著的成果。
增材制造技术(Additive Manufacturing,简称AM)是一种以材料逐层叠加和成形的制造技术。
与传统的减材制造方式相比,增材制造技术不需要使用传统的切削、加工、铸造等方法,而是通过直接将材料一层层叠加,以逐层堆积的方式构建出需要的零部件。
这种制造方式可以减少材料的浪费,并且可以制造出更加复杂、精密的零部件。
在航空航天领域,增材制造技术具有以下几个优势,因此被广泛应用于该领域:首先,增材制造技术可以制造出轻量化的零部件。
航空航天领域对于重量的控制非常严格,因为燃料消耗和载荷能力与飞机的重量有着直接的关系。
传统的制造方式可能会因为需要增加零部件的强度而牺牲部分轻量化的优势。
而增材制造技术可以采用合理的结构设计,为零部件提供最优的轻量化设计方案,这样不仅可以减轻飞机的自重,还能提高飞机的燃油效率和载重能力。
其次,增材制造技术能够制造出复杂形状的零部件。
航空航天领域对于零部件的形状、结构要求非常高,有时候甚至需要制造出无法通过传统制造方式实现的形状。
增材制造技术通过逐层叠加的方式,可以根据设计需求制造出复杂且精确的形状,例如内部具有复杂空腔结构的零部件。
这种方式极大地拓展了制造的可能性,满足了航空航天领域对于复杂形状部件的需求。
再次,增材制造技术具有快速制造的特点。
航空航天行业对于开发周期和交付时间有着极高的要求。
传统的制造方式可能需要耗费大量的时间和人力,而增材制造技术则可以通过数字化设计和直接制造的方式,实现快速制造。
这种方式可以大大缩短零部件的制造周期,提升生产效率,满足航空航天行业对于快速制造的需求。
最后,增材制造技术还可以实现定制化生产。
增材制造的基本知识点
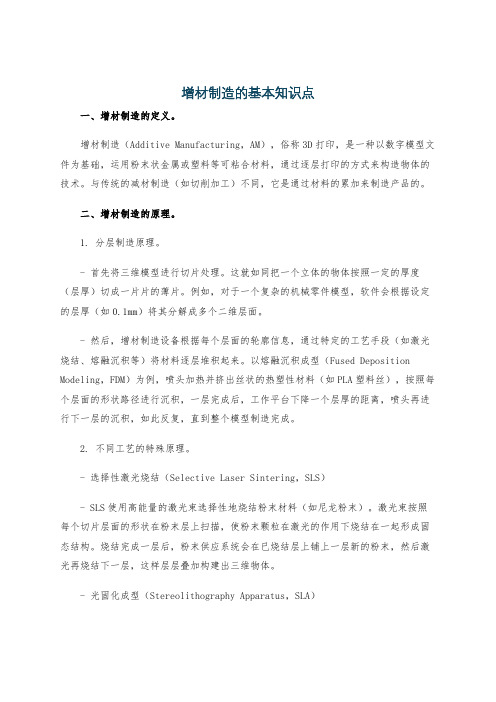
增材制造的基本知识点一、增材制造的定义。
增材制造(Additive Manufacturing,AM),俗称3D打印,是一种以数字模型文件为基础,运用粉末状金属或塑料等可粘合材料,通过逐层打印的方式来构造物体的技术。
与传统的减材制造(如切削加工)不同,它是通过材料的累加来制造产品的。
二、增材制造的原理。
1. 分层制造原理。
- 首先将三维模型进行切片处理。
这就如同把一个立体的物体按照一定的厚度(层厚)切成一片片的薄片。
例如,对于一个复杂的机械零件模型,软件会根据设定的层厚(如0.1mm)将其分解成多个二维层面。
- 然后,增材制造设备根据每个层面的轮廓信息,通过特定的工艺手段(如激光烧结、熔融沉积等)将材料逐层堆积起来。
以熔融沉积成型(Fused Deposition Modeling,FDM)为例,喷头加热并挤出丝状的热塑性材料(如PLA塑料丝),按照每个层面的形状路径进行沉积,一层完成后,工作平台下降一个层厚的距离,喷头再进行下一层的沉积,如此反复,直到整个模型制造完成。
2. 不同工艺的特殊原理。
- 选择性激光烧结(Selective Laser Sintering,SLS)- SLS使用高能量的激光束选择性地烧结粉末材料(如尼龙粉末)。
激光束按照每个切片层面的形状在粉末层上扫描,使粉末颗粒在激光的作用下烧结在一起形成固态结构。
烧结完成一层后,粉末供应系统会在已烧结层上铺上一层新的粉末,然后激光再烧结下一层,这样层层叠加构建出三维物体。
- 光固化成型(Stereolithography Apparatus,SLA)- SLA基于液态光敏树脂的光聚合原理。
在一个容器中装有液态光敏树脂,紫外激光束按照切片层面的形状在树脂表面进行扫描。
被激光照射到的树脂发生光聚合反应,由液态转变为固态。
每完成一层的固化后,工作平台下降一个层厚的距离,然后新的液态树脂覆盖已固化层,激光再进行下一层的固化,最终形成三维物体。
航空发动机叶片材料及制造技术现状

航空发动机叶片材料及制造技术现状航空发动机叶片是发动机中最关键的部件之一,它的材料和制造技术对发动机的性能和可靠性有着重要的影响。
在航空发动机的设计中,叶片材料要求具有高温强度、耐热疲劳、抗氧化和良好的耐腐蚀性能。
同时,叶片的制造技术需要保证叶片的几何尺寸精度和表面质量。
目前,航空发动机叶片的常用材料包括镍基合金、钛基合金和复合材料。
镍基合金是目前航空发动机叶片的主要材料之一,具有优异的高温强度、抗氧化和耐热疲劳性能。
由于航空发动机叶片在高温环境下长期工作,材料的高温强度至关重要。
镍基合金可以承受较高的温度下进行工作,并且具有优异的机械性能和化学稳定性,因此被广泛应用于航空发动机叶片制造中。
钛基合金在航空发动机叶片中也有广泛应用。
钛基合金具有较高的强度、刚性和耐腐蚀性能,而且具有较低的密度,是一种较为轻量化的材料。
钛基合金因其良好的力学性能和抗腐蚀性能,逐渐被应用于航空发动机叶片中,提高了叶片的综合性能。
另外,复合材料也逐渐在航空发动机叶片中得到应用。
复合材料具有高强度、轻质化和抗腐蚀性能好等优点,可以减轻航空发动机结构重量,提高整体效率。
然而,复合材料的制造工艺和维修成本较高,需要进一步的研发和改进。
对于航空发动机叶片的制造技术,传统的铸造、锻造和机械加工工艺仍然占据主导地位。
这些传统的制造工艺可以满足叶片的几何尺寸要求,但在提高叶片的复杂性和制造精度方面有一定限制。
近年来,先进制造技术,如粉末冶金成形、增材制造和光刻蚀等,开始在航空发动机叶片的制造中得到应用。
粉末冶金成形技术可以实现复杂叶片结构的生产,同时具有较高的材料利用率。
增材制造技术可以通过逐层堆积材料来制造复杂形状的叶片,具有较高的制造精度和设计自由度。
光刻蚀技术允许在特定区域进行材料的去除,可以实现叶片表面的微纳结构和涂层的制造。
总的来说,航空发动机叶片的材料和制造技术一直在不断发展和改进。
未来,随着航空发动机的需求不断增加,对叶片的性能和质量的要求也会不断提高。
- 1、下载文档前请自行甄别文档内容的完整性,平台不提供额外的编辑、内容补充、找答案等附加服务。
- 2、"仅部分预览"的文档,不可在线预览部分如存在完整性等问题,可反馈申请退款(可完整预览的文档不适用该条件!)。
- 3、如文档侵犯您的权益,请联系客服反馈,我们会尽快为您处理(人工客服工作时间:9:00-18:30)。
航空发动机叶片增材制造调查报告
总体来说,有这样几种可行性方向。
一、工艺方向,包括整体增材制造或者表面增材强化:
1. 整体增材制造:使用3d打印代替传统加工工艺,整体打印。
目前可行的3d打印技术包括:
FDM:熔融沉积(Fused Deposition Modeling)
SLM:选择性激光熔融技术(Selective Laser Melting)
SLS:选择性激光烧结成型法(Selective Laser Sintering)
DMLS:直接金属激光烧结(Direct Metal Laser Sintering)
LMD:激光金属沉积(laser metal deposition)
相比于熔模铸造,增材制造具有的优势多于劣势,因此具有较大研究价值。
如何解决增材制造新工艺存在的技术弱点正是需要研究的方向。
总结有如下几点:
①强度问题:目前最常用为镍基合金增材,使用何种材料可提升强度?
②精度问题:粘结剂喷射,然后是适当的烧结和表面处理是一种很有前途的合金制造工艺
[1],如何进一步提升表面精度?
③温度问题:3d打印叶片目前只是在常温叶片制造上有一些应用,针对于航空发动机涡轮的耐高温叶片(1400-1700℃)则鲜有研究。
需要解决问题包括:除镍基合金外,打印粉末采用何种耐高温材料(金属、非金属、复合材料[2])?最佳的高温合金打印方法是哪一种?
④建立模型:建立增材制造叶片的收缩模型、疲劳模型、力学模型等。
2.表面增材强化:使用激光熔覆或等离子喷涂,在已有叶片表面上增加强化散热层,叶片为多层结构。
(滕海灏)
二、产品方向,叶片结构智能化和新材料应用。
目前叶片结构如下图所示[3],采用熔模铸造的工艺方案,其优缺点见上表。
如前所述,如果采用3d打印工艺加工这种空心叶片结构将会实现多方面的优化。
就产品本身而言,可以在如下方面进行研究。
图1 图2
1、叶片结构智能化(4d打印)
如图2,这是风力发电机叶片结构[3],利用仿生学模仿植物脉络,将单一叶片材料更新为主动(智能)材料和被动材料两种,又称为“4d打印”。
这种新型结构采用PLA作为主动材料,利用其热响应机制实现根据外力“自适应”调整自身形状。
因此实现了叶片的智能化,提升了发电效率,另外还具有消除噪音、增强散热效果、取消叶片传感器等优点。
这种新型叶片由“硬”变“软”实现了结构的革命。
但是,目前这种结构仅仅针对于常温材料的叶片结构,高温工作叶片则鲜有报道。
因此,将此结构应用于航空涡轮的高温叶片是否可行?
2、叶片新材料
如果采用上述智能结构应用于高温工作叶片,采用何种材料作为主动材料(记忆合金?纳米材料?)、何种作为被动材料,是否采用上述仿生结构,或者采用其它植物结构,如棕榈树、橡树等[4]。
如果高温合金结构无法实现软质智能化结构,也可以采用加强筋结构提升叶片强度,这种结构很难通过传统工艺实现,只能依靠3d打印工艺实现。
参考文献
[1]Amir Mostafaei,Characterizing surface finish and fatigue behavior in binder-jet 3D-printed nickel-based superalloy 625,Additive Manufacturing 24 (2018) 200–2
[2]航空发动机复合材料叶片设计及成形技术研究,宋超,南航硕士学位论文
[3]Y.W. Dong,Modeling of shrinkage during investment casting of thin-walled hollow turbine blades,Journal of Materials Processing Technology 244 (2017) 190–203
[4]Farhang Momeni,Plant leaf-mimetic smart wind turbine blades by 4D printing, Renewable Energy 130 (2019) 329e351
[5]Markus Bambach,Hot workability and microstructure evolution of the nickel-bsuperalloy Inconel 718 produced by laser metal deposition,Journal of Alloys and Compounds 740 (2018) 278e287
[6]Yao Li,Mechanism of heat affected zone cracking in Ni-based superalloy DZ125L fabricated by laser 3D printing technique,Materials and Design 150 (2018) 171–181。