撞件改善报告
安全事故改善报告
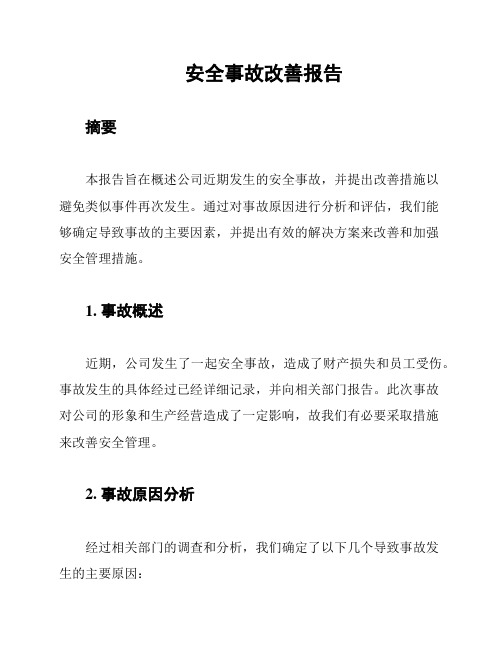
安全事故改善报告摘要本报告旨在概述公司近期发生的安全事故,并提出改善措施以避免类似事件再次发生。
通过对事故原因进行分析和评估,我们能够确定导致事故的主要因素,并提出有效的解决方案来改善和加强安全管理措施。
1. 事故概述近期,公司发生了一起安全事故,造成了财产损失和员工受伤。
事故发生的具体经过已经详细记录,并向相关部门报告。
此次事故对公司的形象和生产经营造成了一定影响,故我们有必要采取措施来改善安全管理。
2. 事故原因分析经过相关部门的调查和分析,我们确定了以下几个导致事故发生的主要原因:- 设备维护不及时:相关设备长期没有进行维护保养,导致设备出现故障并引发事故。
- 员工缺乏安全意识:部分员工对安全操作规程缺乏了解和重视,操作不规范,增加了事故发生的风险。
- 管理制度不完善:公司现有的管理制度存在一定漏洞,未能及时发现和纠正潜在的安全隐患。
3. 改善措施为了避免类似的安全事故再次发生,我们提出以下改善措施:- 设备维护计划:建立定期的设备维护计划,并确保设备正常运行和安全使用。
- 培训和教育:加强员工的安全意识培训,提高员工对安全操作规程的了解和重视程度。
- 安全管理体系改进:完善公司的安全管理体系,包括完善安全管理制度,建立安全检查和自查制度,及时发现和解决安全隐患。
4. 实施计划为了确保改善措施的有效实施,我们制定了以下实施计划:- 设备维护计划:在下一周开展设备维护工作,并确保维护计划得到落实。
- 培训和教育:下个月开展员工安全意识培训,并在每季度进行一次安全操作规程培训。
- 安全管理体系改进:成立专门的安全管理团队,在一个月内进行全面的安全管理体系评估,并提出改进意见和方案。
5. 结论通过对近期安全事故的分析和评估,我们确定了事故的原因并提出了适当的改善措施。
我们相信,只有加强安全管理和意识,才能有效避免类似事故再次发生。
我们将认真执行改善措施,并定期进行监督和评估,以确保公司的员工和财产安全。
XXX电感撞件调查分析报告

不良品处理过程 中B面电感受力
置件
顶Pin
炉后目检与贴 贴条码过程中B面
条码
电感受力
没有撞件风险 撞件风险1 撞件风险3
现顶Pin设置OK 撞件风险4
装板数量未定义 作业过程中B面没有防
护措施治具
作业过过程中B面没有 防护措施治具
“风险点
与现况数
据统计发
生段”吻 合
维修站
维修过程中B面电 感受力
三、问题查找与风险排除
5. 炉后目检与贴条码:
6. 维修
电感受力被顶
电感受力被顶
员工贴条码过程中 1. 若将板子拿在左手中,同 时右手撕条码贴在板子上, 这样操作较不方便。 2. 若将板子放在轨道旁操作 台上作业,则B面电感正受 力被顶住,易造成零件裂碎。
A面生产过程中,若AOI出现 的不良在维修工位的过程中, 目前是放在一硬静电板上, 在维修过程中易造成零件裂 碎。
XXX PCB撞件起铜皮调查 分析报告
目录
➢ 不良问题描述 ➢ 在线现况数据统计 ➢ 问题调查与风险排除 ➢ 调查分析结论 ➢ 改善措施 ➢ 标准化
一、不良问题描述
✓ 不良现象:测试段在目检站发现不良品过多,不良为主板撞件, 目检650PCS,不良有13PCS,参考如下不良图片 ✓ 不良率:2.0% ✓ 不良位置:电源插座处PCB板边
不良图片1
不良图片2
二、在线现况数据统计
根据生产后段反馈的现象及不良板的确认,针对现SMT正在 生产现场按四个管制点( B面炉后、 B面装周转车后、 A面炉后、 A面装周转车后)进行不良统计收集,具体数据参考如下表:
二、问题查找与风险排除
• 根据生产后段反馈的现象及不良板的确认,针对现SMT正在生 产现场对生产工艺流程中存在的作业风险点进行确认与排除
SMT产品线撞件不良分析与改进措施

体 行 业 2008:12-47. [2] 张文典.实用表面组装技术(第二版)[M].
北 京 :电 子 工 业 出 版 社 ,2006. [3] 周德俭.表面组装工艺技术[M].北京:电
子 工 业 出 版 社,2002. [4] 周德俭,等.SMT 组装质量检测与控制
1)VORTEX-TRINITY 机 种 ,不良位 置的脚位名称分别为 C1、C2、C5、C51、 R33、L55,具体脚位和对应数量如图 2 所
112 科技创新导报 Science and Technology Innovation Herald
工 程 技 术
科技创新导报 2009 NO.16
(1).在 90PCS 图 1:
(2).在 电 脑 E 化 数 据 中 责 任 单 位 为 SMT 段的有 48 pcs, 责任单位为 DIP 段的 有 41pcs,两 段 基 本 相 当 ,其 中 VORTEX- TRINITY 和 VORTEX-CYPHER 机种责任 单位为 SMT 段的分别占 16/22=72.7%,和 12/20=60%,CONNOLLY-MLK 机种责任 单位为 DIP 段的占 13/24=54.1% 由于此 三 个 机 种 占 不 良 比 率 较 高 ,下 面 就 此 做 重 点分析:
图 6 HS3 与 C1 和 C2 关系
图 7 静电台车与机板放置示意图 图 8 V-C 机种不良脚位及数量直方图
1 撞件不良现状分析 近一段时间,在生产线的 OQC 处不良
渐 渐 增 多 ,为 保 证 品 质,提 高 良 率 ,降 低 出 货风险,针对产线 OQC 不良,做如下分析:
查询近两个月的 E化资料发现所有机 种 OQC 的不良中撞件部分占总不良的 90/ 219= 41%,如下:
统盟刮伤异常改善报告

改變後作法 圖12
4.1的作法可避免因X-ray平台的異物造成的刮撞傷
5.1避免板件互相摩擦,造成的刮傷。
6.1
原作法 圖13
改變後作法 圖14
6.1的作法可避免因驗板重壓,造成的刮傷
10
EVA presentation
2.上料
3.下料
板子上機生產
將板子拿下機台
6.品保檢驗(出貨檢)
5.讀孔機
4.下片照X-ray
確認是否漏鑽
確認內層對位是否孔偏
7
EVA presentation
Mechanical Drilling
製造過程可能產生的刮撞傷
編號
2.1
名稱
上料前的分板
原本的作法
在工作桌上分板時,直接分6軸堆 版。(圖1) 堆疊板子至所需的配趟數(圖3) 一次拿6軸放至機台上,再分板將 板子放入PIN中。(圖5) 將板子從PIN中取出,上片與下片 分開,再放至台車(圖7) 照X-ray時,檢查板子上方後,即 移動旋轉,再檢查板子下方。 (圖9) 板子於收板段取板(輸送帶至收板段 之間有高低差,造成板件傾斜向前 傳送,造成刮傷) (圖11) 品保檢驗上片時,取一疊板子置於 台車上,再檢驗(圖13)
8 EVA presentation
Mechanical Drilling
製造過程可能產生的刮撞傷(圖例)
2.1 2.2
原作法 圖1
改變後作法 圖2
原作法 圖3
改變後作法 圖4
2.1的作法可避免上機前的分板造成的刮傷
2.2的作法可避免因重壓取板時造成的刮傷
2.3
3.1
下片 上片
原作法 圖5
改變後作法 圖6
原作法 圖7
产品磕碰伤改善报告模板
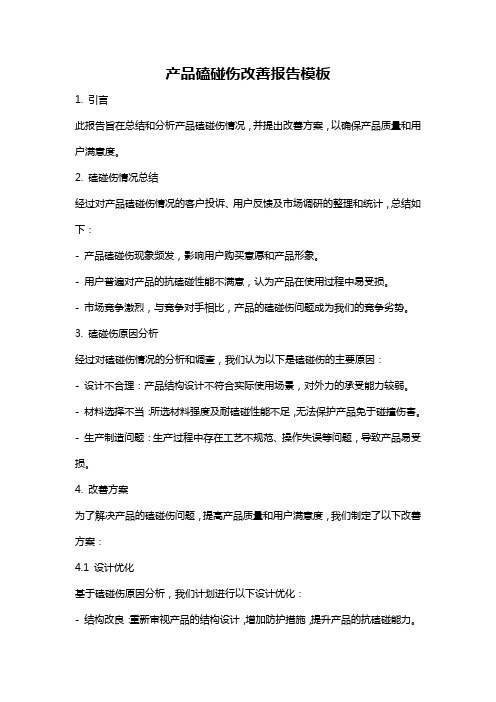
产品磕碰伤改善报告模板1. 引言此报告旨在总结和分析产品磕碰伤情况,并提出改善方案,以确保产品质量和用户满意度。
2. 磕碰伤情况总结经过对产品磕碰伤情况的客户投诉、用户反馈及市场调研的整理和统计,总结如下:- 产品磕碰伤现象频发,影响用户购买意愿和产品形象。
- 用户普遍对产品的抗磕碰性能不满意,认为产品在使用过程中易受损。
- 市场竞争激烈,与竞争对手相比,产品的磕碰伤问题成为我们的竞争劣势。
3. 磕碰伤原因分析经过对磕碰伤情况的分析和调查,我们认为以下是磕碰伤的主要原因:- 设计不合理:产品结构设计不符合实际使用场景,对外力的承受能力较弱。
- 材料选择不当:所选材料强度及耐磕碰性能不足,无法保护产品免于碰撞伤害。
- 生产制造问题:生产过程中存在工艺不规范、操作失误等问题,导致产品易受损。
4. 改善方案为了解决产品的磕碰伤问题,提高产品质量和用户满意度,我们制定了以下改善方案:4.1 设计优化基于磕碰伤原因分析,我们计划进行以下设计优化:- 结构改良:重新审视产品的结构设计,增加防护措施,提升产品的抗磕碰能力。
- 加强支撑:在产品内部或外部增加支撑结构,改善产品的承受能力。
- 减少尖锐边角:优化产品外观设计,减少尖锐边角,降低受损风险。
4.2 材料升级针对材料选择不当的问题,我们计划进行以下材料升级:- 硬度提升:选择更高强度的材料,提升产品的耐磕碰性能。
- 增加缓冲材料:在产品内部或外部增加缓冲材料,减少碰撞对产品的影响。
4.3 生产工艺改进为解决生产制造问题,我们计划进行以下生产工艺改进:- 引入标准化操作:制定并推行生产操作标准化流程,确保生产过程规范,减少操作失误。
- 增强质检环节:加大对生产过程的质量检查,提高产品的合格率和稳定性。
5. 实施计划为了确保改善方案的有效实施,我们制定了以下实施计划:- 设计优化:成立设计小组,对产品结构进行改良,设计新版产品原型,并进行测试验证。
预计完成时间为两个月。
2023年质量事故整改报告
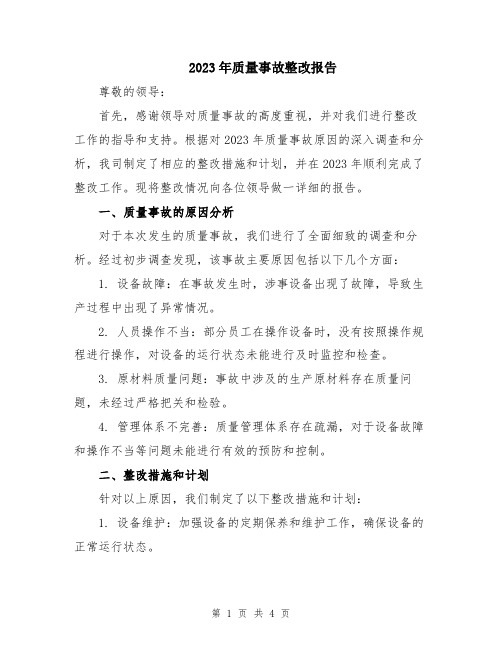
2023年质量事故整改报告尊敬的领导:首先,感谢领导对质量事故的高度重视,并对我们进行整改工作的指导和支持。
根据对2023年质量事故原因的深入调查和分析,我司制定了相应的整改措施和计划,并在2023年顺利完成了整改工作。
现将整改情况向各位领导做一详细的报告。
一、质量事故的原因分析对于本次发生的质量事故,我们进行了全面细致的调查和分析。
经过初步调查发现,该事故主要原因包括以下几个方面:1. 设备故障:在事故发生时,涉事设备出现了故障,导致生产过程中出现了异常情况。
2. 人员操作不当:部分员工在操作设备时,没有按照操作规程进行操作,对设备的运行状态未能进行及时监控和检查。
3. 原材料质量问题:事故中涉及的生产原材料存在质量问题,未经过严格把关和检验。
4. 管理体系不完善:质量管理体系存在疏漏,对于设备故障和操作不当等问题未能进行有效的预防和控制。
二、整改措施和计划针对以上原因,我们制定了以下整改措施和计划:1. 设备维护:加强设备的定期保养和维护工作,确保设备的正常运行状态。
2. 员工培训:对全体员工进行质量管理和安全操作培训,提高员工的操作技能和质量意识。
3. 建立质量检验机制:建立符合国家标准和行业规范的原材料质量检验机制,确保生产原材料的质量符合要求。
4. 加强管理体系建设:完善质量管理体系,明确责任分工,加强对设备运行和生产过程的监控和管理。
以上整改措施和计划已经在2023年顺利实施并取得明显效果。
三、整改成效和效益通过对质量事故的整改工作,我们取得了显著的成效和效益。
具体表现在以下几个方面:1. 事故频发率显著下降:通过加强设备维护和操作培训,事故频发率明显下降,生产安全得到有效保障。
2. 员工质量意识提升:通过员工培训和管理体系完善,员工质量意识得到有效提升,大大减少了操作不当和质量问题的发生。
3. 生产效率提高:设备定期保养和维护的加强,使得设备运行更加稳定可靠,生产效率得到了提高。
4. 企业声誉恢复:通过整改工作的积极推进,企业在客户和社会各界中声誉逐渐恢复,并取得了一定的信任。
产品撞件排查报告范文
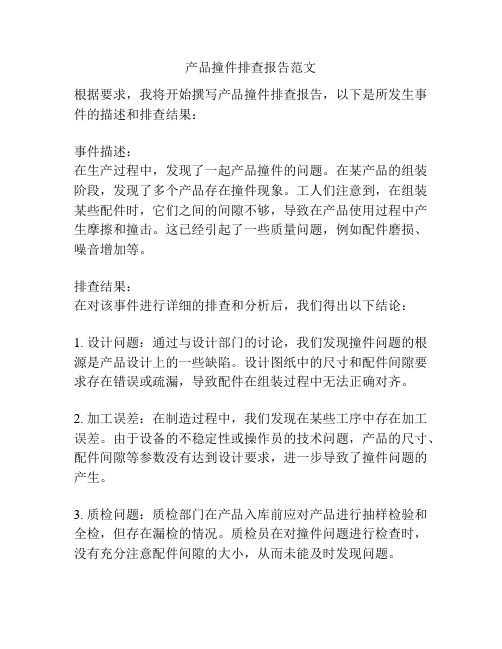
产品撞件排查报告范文根据要求,我将开始撰写产品撞件排查报告,以下是所发生事件的描述和排查结果:事件描述:在生产过程中,发现了一起产品撞件的问题。
在某产品的组装阶段,发现了多个产品存在撞件现象。
工人们注意到,在组装某些配件时,它们之间的间隙不够,导致在产品使用过程中产生摩擦和撞击。
这已经引起了一些质量问题,例如配件磨损、噪音增加等。
排查结果:在对该事件进行详细的排查和分析后,我们得出以下结论:1. 设计问题:通过与设计部门的讨论,我们发现撞件问题的根源是产品设计上的一些缺陷。
设计图纸中的尺寸和配件间隙要求存在错误或疏漏,导致配件在组装过程中无法正确对齐。
2. 加工误差:在制造过程中,我们发现在某些工序中存在加工误差。
由于设备的不稳定性或操作员的技术问题,产品的尺寸、配件间隙等参数没有达到设计要求,进一步导致了撞件问题的产生。
3. 质检问题:质检部门在产品入库前应对产品进行抽样检验和全检,但存在漏检的情况。
质检员在对撞件问题进行检查时,没有充分注意配件间隙的大小,从而未能及时发现问题。
4. 缺乏标准化流程:在生产过程中,没有明确的标准化流程和相关工艺指导文件,操作员对于产品组装的各个步骤没有统一的标准操作方法,导致操作的随意性。
解决方案:为了解决产品撞件问题,我们提出以下解决方案:1. 设计优化:与设计部门合作,重新审查和优化产品设计,确保尺寸和配件间隙满足要求,并在设计图纸中详细标注。
2. 加工控制:加强对关键工序的监控和控制,确保产品尺寸和配件间隙的精度和一致性。
同时,培训操作员,提高他们的技术水平和操作技能。
3. 质检强化:加大对撞件问题的检查力度,并建立严格的质检标准。
针对撞件问题,制定相应的检验指导和标准操作方法,确保质检员能够准确判断撞件情况。
4. 流程优化:建立标准化的生产流程和工艺指导文件,明确产品组装的每一个步骤和要求。
确保每个操作员按照标准步骤进行产品组装,避免操作的随意性。
总结:通过对产品撞件问题的分析和解决方案的提出,我们相信可以有效地抑制和解决这一问题。
事故调处报告范文模板
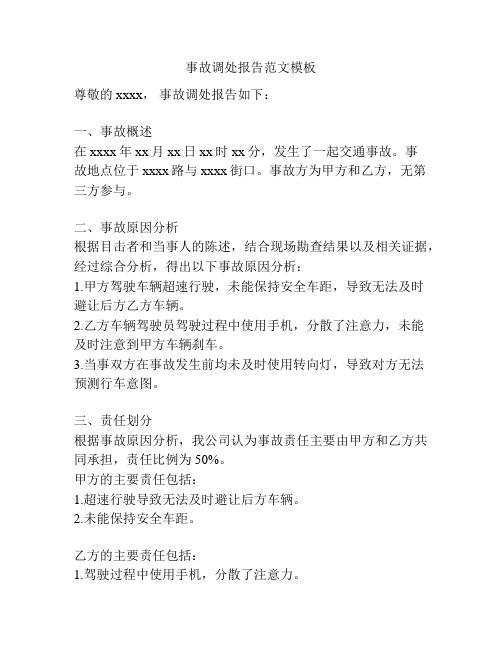
事故调处报告范文模板尊敬的xxxx,事故调处报告如下:一、事故概述在xxxx年xx月xx日xx时xx分,发生了一起交通事故。
事故地点位于xxxx路与xxxx街口。
事故方为甲方和乙方,无第三方参与。
二、事故原因分析根据目击者和当事人的陈述,结合现场勘查结果以及相关证据,经过综合分析,得出以下事故原因分析:1.甲方驾驶车辆超速行驶,未能保持安全车距,导致无法及时避让后方乙方车辆。
2.乙方车辆驾驶员驾驶过程中使用手机,分散了注意力,未能及时注意到甲方车辆刹车。
3.当事双方在事故发生前均未及时使用转向灯,导致对方无法预测行车意图。
三、责任划分根据事故原因分析,我公司认为事故责任主要由甲方和乙方共同承担,责任比例为50%。
甲方的主要责任包括:1.超速行驶导致无法及时避让后方车辆。
2.未能保持安全车距。
乙方的主要责任包括:1.驾驶过程中使用手机,分散了注意力。
2.未能及时注意到甲方车辆刹车。
四、损失赔偿根据责任划分,我公司决定采取以下赔偿措施:1.甲方应承担50%的事故赔偿责任,包括车辆维修费用及相关医疗费用。
2.乙方应承担50%的事故赔偿责任,包括车辆维修费用及相关医疗费用。
五、后续处理双方应尽快联系保险公司,启动车辆维修事宜,并按照保险公司要求提供相关材料,协助保险公司进行理赔。
同时,对事故责任及预防进行必要的教育和宣传,提醒驾驶员在驾驶过程中保持集中注意力,遵守交通法规。
六、事故调处结束经双方同意,本次事故调处报告为最终调解结果。
如对调处结果不满意,可依照相关法律规定维权。
特此报告。
调处单位:xxxx公司日期:xxxx年xx月xx日。
撞件不良解析报告

易损件位置 TOP面向下放 置 BOT面向下放 置
四、分板撞件不良解析
分板撞件形成原因: 2.使用铣刀式分板机分板时,由于万能模调试不当,导致定位PIN周边元件撞件 3.由于邮票孔靠近HDMI等端子物料,导致铣刀和端子碰撞导致损件。 4.由于机器的提刀高度不够,导致铣刀和AI电容碰撞导致损件。 预防措施: 1.工程人员在调机时定位孔旁边5MM内有贴片元件的禁止下PIN。 2.针对邮票孔旁有HDMI/AI电容等元件的,需作重点确认。
CT28位置
易损件位置
六、波峰焊工序撞件不良解析
6.1.波峰焊撞件不良案例分析:
波峰焊撞件形成原因: 1.波峰焊撞件主要集中在压浮高治具。(撞件位置主要表现为:板卡的中间且是 0603.0402的贴片物料较多)
预防措施:
1.对有撞件隐患的压浮高治具进行加工(在铁块外加热缩套管)。 2.生产时尽量不使用较大的压浮高治具。
撞件不良解析改善报告
制定:
审核: 日期:2017.3.24
目录
1. 工序排布描述 2. SMT撞件不良原因解析 3. AI撞件不良原因解析源自4. DIP撞件不良原因解析
5.小结
一、易发生撞件的工序和流程
1. 易发生撞件不良的工序和流程如下: 上板 印 刷 回流炉后 SMT维修 炉后检查 转 板 AI
OK物料
撞损NG物料 损件样图
夹取物料示意图
三、板卡周转撞件不良解析
3.板卡周转撞件不良案例分析:
板卡周转撞件形成原因: 一般为板卡周转车陈旧变形,或者是在调整宽度时调整过松,导致板卡在装入周 转车时受力或是在周转时地面不平震动受力使板卡从周转车的卡槽内掉落。 板卡周转撞件预防措施: 1.对陈旧/变形的周转车进行更换。 2.在调整宽度时应该使用三块板卡分上中下进行一致分段调试。
事故意外改善行动报告
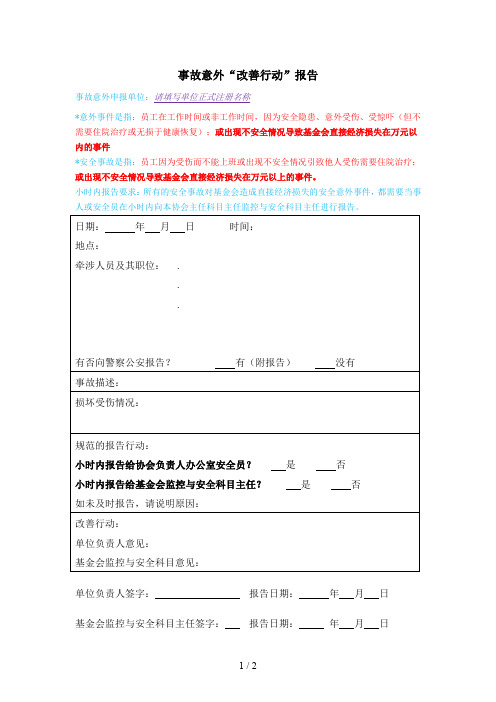
事故意外“改善行动”报告
事故意外申报单位:请填写单位正式注册名称
*意外事件是指:员工在工作时间或非工作时间,因为安全隐患、意外受伤、受惊吓(但不需要住院治疗或无损于健康恢复);或出现不安全情况导致基金会直接经济损失在万元以内的事件
*安全事故是指:员工因为受伤而不能上班或出现不安全情况引致他人受伤需要住院治疗;或出现不安全情况导致基金会直接经济损失在万元以上的事件。
小时内报告要求:所有的安全事故对基金会造成直接经济损失的安全意外事件,都需要当事人或安全员在小时内向本协会主任科目主任监控与安全科目主任进行报告。
单位负责人签字:报告日期:年月日
基金会监控与安全科目主任签字:报告日期:年月日。
撞件分析与改善措施(勿删)
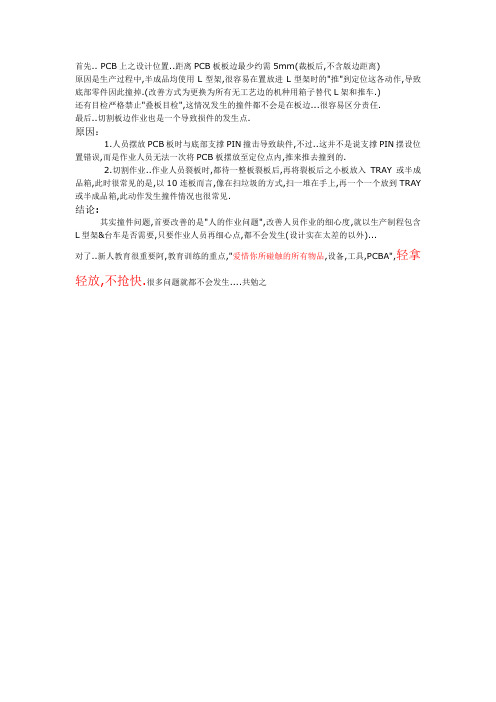
首先.. PCB上之设计位置..距离PCB板板边最少约需5mm(裁板后,不含版边距离)
原因是生产过程中,半成品均使用L型架,很容易在置放进L型架时的"推"到定位这各动作,导致底部零件因此撞掉.(改善方式为更换为所有无工艺边的机种用箱子替代L架和推车.)
还有目检严格禁止"叠板目检",这情况发生的撞件都不会是在板边...很容易区分责任.
最后..切割板边作业也是一个导致损件的发生点.
原因:
1.人员摆放PCB板时与底部支撑PIN撞击导致缺件,不过..这并不是说支撑PIN摆设位置错误,而是作业人员无法一次将PCB板摆放至定位点内,推来推去撞到的.
2.切割作业..作业人员裂板时,都待一整板裂板后,再将裂板后之小板放入TRAY或半成品箱,此时很常见的是,以10连板而言,像在扫垃圾的方式,扫一堆在手上,再一个一个放到TRAY 或半成品箱,此动作发生撞件情况也很常见.
结论:
其实撞件问题,首要改善的是"人的作业问题",改善人员作业的细心度,就以生产制程包含L型架&台车是否需要,只要作业人员再细心点,都不会发生(设计实在太差的以外)...
对了..新人教育很重要阿,教育训练的重点,"爱惜你所碰触的所有物品,设备,工具,PCBA",轻拿轻放,不抢快.很多问题就都不会发生....共勉之。
撞件改善报告

2 PDF 檔案以 "PDF 製作工廠" 試用版建立 题httpy://
專案組織架構
瑞中/樂軒專案組織架構圖:
3 PDF 檔案以 "PDF 製作工廠" 試用版建立 昳責Ì方昳方止板人人人题撞任此成止規任此方题,禁制
撞件執行計劃表:
開始日期:2月19日 撞件驗証選定機種:VP422 384201820150 Main Board
2月19日 0 4 0 0 0 0 0 0 0
PDF 檔案以 "PDF 製作工廠" 試用版建立 f
2月20日 ---0 0 0 0 4 2 1 4
不良數 2月21日
---2 2 0 2 3 0 2 8
2月22日 ---3 0 0 2 2 0 0 6
2月23日 ---2 2 0 1 5 0 3 5
爐后 取板
錫面 檢查
補焊
安裝 散熱片
包裝
錫面檢查 罩板
零件面 檢查
F/T
在線燒錄
ICT
7 PDF 檔案以 "PDF 製作工廠" 試用版建立 香責ÿ方香方止板人人人题撞任此成止規任此方题,禁制
原因分析及改善對策
一 . A面reflow(AOI)后罩板疊板作業 As-is
To-be
2PCS疊板作業
改善項目匯總
撞件改善list一:(舊)
撞件隱患
臨時改善對策
改善單 完成時
位
間
長期改善對策
改善單 位
完成時間
AI操機人員從AI 1.從AI投板入口投板 ,IE加入SOP 機器中間投板 2.生技開啟AI機台安全操作
制造 / 生技動供板
生技
电容撞件异常改善报告
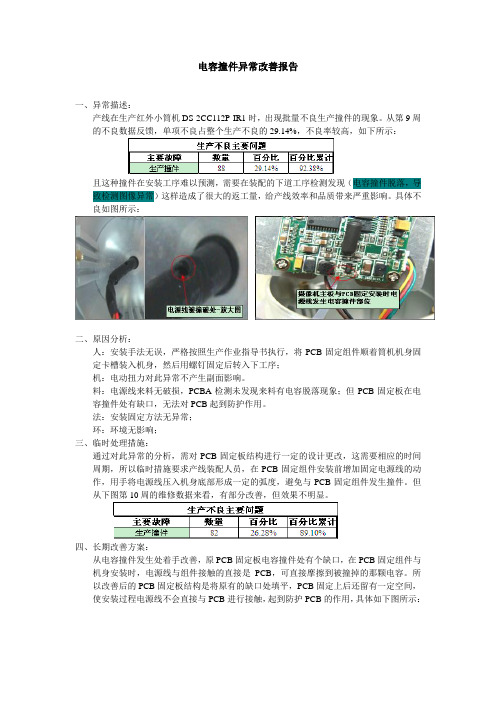
电容撞件异常改善报告一、异常描述:产线在生产红外小筒机DS-2CC112P-IR1时,出现批量不良生产撞件的现象。
从第9周的不良数据反馈,单项不良占整个生产不良的29.14%,不良率较高,如下所示:且这种撞件在安装工序难以预测,需要在装配的下道工序检测发现(电容撞件脱落,导致检测图像异常)这样造成了很大的返工量,给产线效率和品质带来严重影响。
具体不良如图所示:二、原因分析:人:安装手法无误,严格按照生产作业指导书执行,将PCB固定组件顺着筒机机身固定卡槽装入机身,然后用螺钉固定后转入下工序;机:电动扭力对此异常不产生副面影响。
料:电源线来料无破损,PCBA检测未发现来料有电容脱落现象;但PCB固定板在电容撞件处有缺口,无法对PCB起到防护作用。
法:安装固定方法无异常;环:环境无影响;三、临时处理措施:通过对此异常的分析,需对PCB固定板结构进行一定的设计更改,这需要相应的时间周期,所以临时措施要求产线装配人员,在PCB固定组件安装前增加固定电源线的动作,用手将电源线压入机身底部形成一定的弧度,避免与PCB固定组件发生撞件。
但从下图第10周的维修数据来看,有部分改善,但效果不明显。
四、长期改善方案:从电容撞件发生处着手改善,原PCB固定板电容撞件处有个缺口,在PCB固定组件与机身安装时,电源线与组件接触的直接是PCB,可直接摩擦到被撞掉的那颗电容。
所以改善后的PCB固定板结构是将原有的缺口处填平,PCB固定上后还留有一定空间,使安装过程电源线不会直接与PCB进行接触,起到防护PCB的作用,具体如下图所示:五、验证结果:改善前:L11线,10040029生产订单100台,DS-2CC112P-IR1(3.6mm),检测1发现电容撞件不良共20台,直通率仅为80%;改善后:L11线,10041235生产订单100台,DS-2CC112P-IR1(3.6mm),检测1未发现电容撞件不良,直通率为100%;从目前在一同条生产线的验证数据显示,此项长期改善措施有效。
撞件改善

改善对策
问题点:SMT印刷工 位单手拿板,在固定板 和取板时容易造成刮碰 撞件。
改善对策:SMT印刷 工位双手持板边,工艺 在印刷的作业指导书中 明确此要求。
改善对策
问题点:1.SMT外观检 查完成后,装周转架时 方向不统一,有的元件 靠近板边容易撞件。 2.未装入到位。
改善对策:SOP规定 装周转架的方向。
IPQC稽核是否有装入 不到位现象。
改善对策
问题点:SMT外观检 查完成后,装周转架未 间隔,拿取时容易造成 上下两片刮碰。
ቤተ መጻሕፍቲ ባይዱ
改善对策:SMT外观 检查完成后,装周转架 时需要间隔一层,AI的 间隔距离要更大。保证 拿取时上下两层不会刮 碰。
改善对策
取板要 从上到 下
放板要 从下往 上
问题点:取放板的顺序 不正确,容易刮碰撞件。
改善对策:SOP规定 每个工位不可以堆积超 过5PCS.
改善对策
问题点:工位下方放置 工具,容易造成撞件。
改善对策:工具必须放 置于工具盒内不可以随 意摆放。
改善对策
问题点:PCB板随意放 置。
改善对策:对人员进行 宣导,板不可以侧放, 不可以随意放置, IPQC稽核。
改善对策
问题点:流水线上金属 边刮碰。
SMT印刷工位顶PIN设置不合理
方法
机器
SMT DIP 研发
撞件原因汇总
1.印刷工位拿板方式不正确(法) 2.周转工具使用不正确(法) 3.周转架装板方式不正确(法) 4.取放板的顺序不正确(法) 5.SMT周转工具宽度调整不正确(机器) 6.SMT印刷工位顶PIN设置不合理(机器) 1.DIP分板方式不正确 2.DIP投板工位流水拉堆板 3.拉线上使用架桥,有推板现象 4.使用过炉载具的板,在流水拉上装载具 5.取放板的顺序不正确 6.分板后放置层数太多 7.隔板上放置数量太多超边 8.流水线工序间隔条堆板 9.流水线工位堆积 10.工位下方放置工具 11.产品随意摆放 12.流水线金属边刮碰 13.测试治具行程小刮碰 设计不合理
撞件回复报告

撞件回复报告1. 引言撞件回复报告是指针对撞件事件的调查和处理结果的汇报文档。
在该报告中,我们将详细介绍撞件事件的经过、原因分析以及针对该事件所采取的解决方案和预防措施。
2. 事件描述撞件事件发生在2022年1月15日的上午10点左右,地点位于公司总部的停车场。
一辆公司员工的私家车在停车过程中,不慎与停在旁边的另一辆车辆发生碰撞。
3. 事件经过据事故现场的监控录像回放显示,员工车辆在倒车过程中,司机没有注意到旁边的车辆,导致发生了碰撞。
碰撞造成了两辆车辆的轻微损坏,并导致停车场交通秩序受到了一定的干扰。
4. 事件原因分析经过调查和分析,撞件事件的原因主要有两个方面:4.1 司机疏忽事故发生时,司机没有做好倒车时的观察和判断,没有意识到旁边的车辆,导致了碰撞的发生。
这与司机对于安全驾驶的重要性认识不足有一定关系。
4.2 停车场设计问题停车场的设计存在一些问题,例如停车位之间的间距较小,司机在倒车时难以观察到旁边的车辆。
此外,停车场的标志和指示不够清晰,也增加了司机在操作中的困难程度。
5. 解决方案和预防措施为了解决撞件事件并预防类似事件的再次发生,我们提出以下解决方案和预防措施:5.1 司机培训和安全意识提升公司将组织驾驶员培训课程,提高其安全驾驶意识和技能水平。
培训内容将涵盖安全驾驶常识、倒车技巧等方面,以提高驾驶员在倒车过程中的观察和判断能力。
5.2 停车场改进公司将对停车场进行改进,优化停车位之间的间距,确保驾驶员在倒车时有足够的空间进行观察。
同时,增加停车场标志和指示牌的数量和清晰度,提高驾驶员在停车操作中的准确性。
5.3 安全监控系统为了及时发现和处理类似事件,公司将在停车场安装安全监控系统。
该系统将通过摄像头对停车场进行全天候监控,实时录像和报警。
一旦发现异常情况,相关人员将能够快速采取行动,并保障停车场的安全秩序。
6. 结论通过对撞件事件的调查和分析,我们找到了事件发生的原因,并提出了相应的解决方案和预防措施。
产品因端面磕碰外丝磕碰的整改报告

产品因端面磕碰外丝磕碰的整改报告产品质量整改报告***(被报告单位名称):贵单位检查中发现的我单位**产品的缺陷,我单位对此非常重视,单位主要领导亲自过问,并举一反三,召开单位全体领导、部门领导与全体员工会议,分析问题原因、认识问题的危害,并完善了有关工作标准、工作程序及工作制度。
对以前存在质量问题的产品,没有出厂的全部返工,已经出厂的全部召回。
我们一定会认真汲取这次教训,视产品质量为企业生命。
以后决不让一件有质量瑕疵的产品出厂。
*****(报告单位名称并加盖公章)年月日人民币冠字号码查询一是取款机渠道,二是存取款一体机渠道,三是柜台渠道。
金融消费者(查询人)在金融机构办理现金取款业务后,对现金真伪存在异议,经金融机构进行真伪识别确认是假币的,查询人可向办理取款业务的金融机构网点(查询受理单位)提出冠字号码查询业务申请,以确认假币是否由该金融机构网点付出。
冠字号码是指印在票券上的号码与符号,用以表示各种票券和印制数量的批号。
中国历史上各银行印制纸币时,所采用的冠字不尽相同。
冠字号码除了具备控制货币数量和防伪作用外,还具有收藏意义。
冠字号码是用以控制各种票券印制数量和防伪作用的冠字和号码。
依靠纸币上的“冠字”与“号码”,再辅以银行和印钞厂的存档资料,可以追溯任何一张纸币的印刷时间、印刷地点、印刷人员、检查封装人员等等相关信息。
人民币纸币冠字号码是央行人民币印制生产管理控制的措施之一,根据人民币印制生产管理的需要不断调整变化。
2010年,央行调整了人民币纸币的冠字号码排列方式,如所见到的“A0A0000001”方式。
随着现金发行量的增加,人民币纸币冠字号码排列方式仍会不断调整变化(如“A00A000001”和“A000A00001”等排列方式)。
车辆事故处理流程改进建议报告

车辆事故处理流程改进建议报告摘要:车辆事故处理流程是指当车辆发生交通事故时,相关机构和个人按照一定的程序和规定进行处理的过程。
然而,目前存在一些问题,如处理时间长、流程复杂等,亟需改进。
本文将针对此类问题提出改进建议,旨在优化车辆事故处理流程,提高处理效率和质量。
1. 引言车辆事故时有发生,其处理流程关系着交通安全和社会秩序。
对于当事人而言,能够快速高效地完成事故处理不仅可以减轻损失,还能避免进一步的纷争和困扰。
因此,我们有必要对车辆事故处理流程进行改进,提出以下建议。
2. 简化报案流程当前的车辆事故报案流程繁琐,增加了事故处理的时间和成本。
为了简化这一流程,建议采取以下措施:2.1 提供在线报案平台:建立一个便捷的在线报案平台,车主和目击者可以通过该平台迅速报案,提供必要的信息并上传事故现场照片等证据。
2.2 车险公司自动报案:引入智能化系统,使车险公司能够在车辆事故发生后自动接收报案信息,并向当事人发送相关指引。
3. 简化调解阶段事故调解是车辆事故处理流程的重要环节,如果调解过程复杂耗时,将延长整个处理流程。
为了简化调解阶段,可考虑以下改进措施:3.1 推行在线调解:利用互联网技术,提供在线调解平台,由专业调解员进行在线调解,以提高调解的效率。
3.2 设立调解陪同人员:在调解过程中,为当事人提供专业的调解陪同人员,不仅可以协助双方进行沟通,还可以提供专业的法律意见。
4. 加强信息共享目前,车辆事故处理流程涉及多个部门和机构,信息共享不畅成为影响处理效率的重要因素。
为了加强信息共享,建议采取以下措施:4.1 建立统一的信息平台:各相关部门和机构可以共享车辆事故处理信息,减少信息重复录入和传递环节。
4.2 制定信息共享协议:相关部门和机构应制定统一的信息共享协议,明确信息共享的内容、方式和权限等。
5. 加强培训和宣传车辆事故处理流程的改进离不开工作人员的培训和当事人的宣传。
为此,应采取以下措施:5.1 培训工作人员:加强相关机构工作人员的培训,提高其专业素质和业务能力。
车辆事故处理效率改进方案报告

车辆事故处理效率改进方案报告标题:车辆事故处理效率改进方案报告**摘要**本文旨在提出一种改进车辆事故处理效率的方案,并通过对现有问题的分析,提供相应的解决措施。
首先,我们将分析当前车辆事故处理的痛点,接着提出具体的改进方案,包括技术手段的运用和流程优化,最后利用数据支持方案的可行性。
**一、问题分析**车辆事故处理中存在的问题,主要集中在以下几个方面:1. 信息获取难:目前事故报告主要依赖于目击者的陈述和交警的勘查,信息获取时效性不高,容易造成虚假陈述或遗漏重要情况。
2. 事故责任认定困难:由于信息不完整、证据不充分,事故责任认定存在误差,导致争议增加,处理效率降低。
3. 流程繁琐耗时:目前的事故处理流程包括报案、勘查、责任认定、索赔等环节,流程繁琐且耗时长,不利于高效处理。
**二、改进方案**为了提高车辆事故处理的效率和准确性,我们提出以下改进方案:1. 引入科技手段:a. 车载行驶记录仪:在车辆中配置行驶记录仪,实时记录车辆行驶数据,包括车速、刹车操作等,为事故责任认定提供客观数据。
b. 智能监控系统:通过路灯、摄像头等设备,实时监控道路交通情况,准确记录事故发生瞬间的情况,为事故认定提供可靠的证据。
2. 优化流程:a. 建立统一平台:建设车辆事故处理统一平台,实现各部门之间的信息共享和协同处理,简化流程,提高信息获取效率。
b. 简化报案流程:引入手机App或在线平台,让当事人可以直接在线上报事故,优化报案环节,减少报案时间。
c. 精简勘查环节:引入无人机、三维扫描仪等技术,提高勘查效率,减少车辆占道时间。
**三、方案实施**为确保改进方案的可行性和有效性,我们需要以下步骤:1. 数据支持:通过收集历史事故数据,分析事故处理中的痛点和瓶颈,为方案的改进提供依据和合理性分析。
2. 技术试点:选取一部分地区进行技术手段的试点应用,包括车载行驶记录仪和智能监控系统的安装、统一平台的搭建等,进行实地测试和效果评估。
- 1、下载文档前请自行甄别文档内容的完整性,平台不提供额外的编辑、内容补充、找答案等附加服务。
- 2、"仅部分预览"的文档,不可在线预览部分如存在完整性等问题,可反馈申请退款(可完整预览的文档不适用该条件!)。
- 3、如文档侵犯您的权益,请联系客服反馈,我们会尽快为您处理(人工客服工作时间:9:00-18:30)。
4 PDF 檔案以 "PDF 製作工廠" 試用版建立 昳責Ì方昳方止板人人人题撞任此成止規任此方题,禁制
數據收集
目檢及數據收集站別
SMT罩板&目檢(A面)
投入數
不良率
SMT
SMT罩板&目檢(B面)
投入數
不良率
AIห้องสมุดไป่ตู้件前
投入數
不良率
爐后 取板
錫面 檢查
補焊
安裝 散熱片
包裝
錫面檢查 罩板
零件面 檢查
F/T
在線燒錄
ICT
7 PDF 檔案以 "PDF 製作工廠" 試用版建立 香責ÿ方香方止板人人人题撞任此成止規任此方题,禁制
原因分析及改善對策
一 . A面reflow(AOI)后罩板疊板作業 As-is
To-be
2PCS疊板作業
AI
投入數 AI插件后
不良率
DIP裂片前
投入數 不良率
修補段目檢
投入數 不良率
投入數 散熱片
不良率
DIP
ICT、燒錄站
投入數 不良率
F/T后罩板&目檢
投入數 不良率
1500 0
2630 0.42% 2400 0.17% 2600
0 2600 0.19% 2600 0.54% 2600 0.08% 2600 0.23% 2600 0.88%
面。 • 完成時間: 已完成
14 PDF 檔案以 "PDF 製作工廠" 試用版建立 耀
原因分析及改善對策
八.散熱片壓合治具行程修正及導入推垃式:
As-is
305H 長度: 6CM
To-be
306H 長度: 8CM
新治具圖片暫缺
• 改善前行程為60CM,人員取放PCBA空間不大,不利
效果驗證及漏失分析 總結
2 PDF 檔案以 "PDF 製作工廠" 試用版建立 题httpy://
專案組織架構
瑞中/樂軒專案組織架構圖:
3 PDF 檔案以 "PDF 製作工廠" 試用版建立 昳責Ì方昳方止板人人人题撞任此成止規任此方题,禁制
撞件執行計劃表:
開始日期:2月19日 撞件驗証選定機種:VP422 384201820150 Main Board
§ 手補AI零件剪腳動作發生碰觸,造成撞件。 § 責任部門:制造/IE
§ IE添加此站SOP,規范手補作業建立手補后檢查和防漏
失機制。 §完成時間:已完成
12 PDF 檔案以 "PDF 製作工廠" 試用版建立 耀
原因分析及改善對策
六.放板(DIP投板站)偏移時挪板、取板(波峰焊爐后)時拖板與過爐載具刮擦:
二.靜電周轉車插板不規范:大靜電周轉車兩邊插板后中間有疊板現象
As-is
To-be
§ 靜電周轉車插板不規范,PCB板之間搭疊發生碰觸, 造成撞件。
§ 責任部門:制造/IE
§ IE制作靜電周轉車使用SOP,定義用光板來調整靜電周
轉車,對裝車人員進行培訓。 §完成時間:已完成
9 PDF 檔案以 "PDF 製作工廠" 試用版建立 耀
§責任部門:制造/品管 責任人:陶士陽/余玲玲
§ 從新整理治工具擺放位置﹐使測試站與線體之間作業順
暢。 § 完成時間:已完成
17 PDF 檔案以 "PDF 製作工廠" 試用版建立 耀
原因分析及改善對策
十一.工作台邊緣與流水線高度存在差異,PCBA容易碰到工作台邊緣
2月19日 0 4 0 0 0 0 0 0 0
PDF 檔案以 "PDF 製作工廠" 試用版建立 f
2月20日 ---0 0 0 0 4 2 1 4
不良數 2月21日
---2 2 0 2 3 0 2 8
2月22日 ---3 0 0 2 2 0 0 6
2月23日 ---2 2 0 1 5 0 3 5
於拿取板且易造成撞件。
•責任部門:工程/治且室
責任人:府建華/巫建發
§采用306H的架手, 將行程提升到80CM;
§另逐步導入推拉式治具,改變隱患作業方式。 §完成時間:部分治具暫未完成,3月底陸續導入。
15 PDF 檔案以 "PDF 製作工廠" 試用版建立
16 PDF 檔案以 "PDF 製作工廠" 試用版建立 耀
原因分析及改善對策
十. 治工具擺放阻礙行程: As-is
To-be
中間無過高治工具阻 隔行程順暢
§ DIP線測試站作業空間偏小(尤其是燒錄)﹑與線體間治工 具擺放過高(DVD等)﹐取放作業行程不暢。
As-is
To-be
§ 工作台邊緣與流水線高度存在差異,PCB板之CHIP元 件會與工作台發生碰觸,造成撞件。
§ 責任部門:工務
§ 调整流水線傳送帶高度,略高于工作台禁止疊板作業。 §完成時間:已完成
18 PDF 檔案以 "PDF 製作工廠" 試用版建立 耀
To-be
§板距過密、產線耗材(氣泡袋、周轉箱等)短缺及產線 異常時,相應站別有堆板、疊板現象,存在撞件隱患。
§責任部門:制造/品管 責任人:陶士陽/余玲玲
§品管監督產線板密(一格一片); 產線需備料充分、定 量保障生產用耗材物品,發現不良及時反映,板距過密 時及時放入周轉箱。 §完成時間:已完成
22 PDF 檔案以 "PDF 製作工廠" 試用版建立 耀
現場培訓教育,嚴格按照Sop雙手平行取放板作業 §完成時間:已完成
20 PDF 檔案以 "PDF 製作工廠" 試用版建立 耀
原因分析及改善對策
十四. 取放板雙手同時作業容易引起撞件. As-is
To-be
§ 雙手取放板同時作業發生碰觸,造成撞件。 § 責任部門:制造/IE
§ 投板人員從投板入口投板,或用送板機送板。IE加入S
OP,開啟AI機台安全操作。 §完成時間:已完成
11 PDF 檔案以 "PDF 製作工廠" 試用版建立 耀
原因分析及改善對策
五.OP在線手補AI零件剪腳動作存在較大撞件隱患. As-is
To-be
原因分析及改善對策
三 . A(B)面reflow后、AI打件前(后)裝靜電車超外護欄:
As-is
To-be
§ 改善前PCB’A板放置超出車架較多,甚至超出擭攔杠, 靜電車放置較密時,PCB’A板搭邊、刮擦容易撞件
§責任部門:制造/IE 責任人:陶士陽/朱亞峰
•IE完善SOP作業規范,對相關人員進行教育宣導; 改善後 PCB’A板放置不超出范圍,靜電車擺放整齊,杜絕碰撞隱 患。
19 PDF 檔案以 "PDF 製作工廠" 試用版建立 替呆替 序序兩上合合自自自柱顆措擊并兩何措擊序柱詳力布
原因分析及改善對策
十三 .散熱片、燒錄、ICT、F/T拿取方法: As-is
To-be
§ 改善前仍有人員單手拿取、及與治工具發生磕碰現象 §責任部門:制造/品管 責任人:陶士陽/余玲玲
§ IE及品管上線根據(取放板作業標准)對作業人員進行
5
數據分析及層別
根據收集數據及發現問題確定高隱患站別(黃色字體):
運輸周轉
A面reflow后待目檢裝排骨架﹐裝台車
B面印刷機前
SMT
B面reflow后装车
B面AOI后装车
AI前靜電車
AI:
AI后裝車
V-CUT前靜電車
裝載具
DIP
touch up
dip 流水线
不良品到維修室維修
人員拿取
A面reflow后目檢人員取放板
As-is
To-be
§ 放板偏移時挪板、取板時拖板,PCB板之CHIP元件會 與載具發生碰觸,造成撞件。
§ 責任部門:制造/IE
§ 放板偏移時需提起后重新放置,取板時需垂直提起,避 免碰到載具邊框。 IE將其加入SOP,定義放板前確認過 爐載具固定旋紐是否全部擰開再進行放板動作。 §完成時間:已完成
單板作業
§ 疊板作業時底PCB板之CHIP元件會與工作台發生碰觸 ,造成撞件。
§ 責任部門:制造
§ 此站禁止疊板作業,IE加入SOP,規范此站作業方法,
對人員進行教育訓練。 §完成時間:已完成
8 PDF 檔案以 "PDF 製作工廠" 試用版建立 耀
原因分析及改善對策
6
PDF 檔案以 "PDF 製作工廠" 試用版建立 f
生產流程
根據收集的撞件數據顯示,初步分析以下站位(橙色字體)存在撞件隱患:
SMT
AOI
入料
A面生產
目檢
裝車
SMT B面生產
AOI 目檢
裝車
AI 插件生產
裝車
ICT
裝車
罩板
DIP 裂片投板
DIP 手插件
§ 流水線一格對應放一片板,工作台保持一片板作業。 §IE將取放板步驟加入SOP,定義單手(左手/右手)作
業,對人員進行教育訓練。 §完成時間:已完成
21 PDF 檔案以 "PDF 製作工廠" 試用版建立 耀
原因分析及改善對策
十五. DIP后段作業站別堆板改善: As-is
13 PDF 檔案以 "PDF 製作工廠" 試用版建立 耀責ÿ方ÿ方止板人人人题撞任此成止規任此方题,禁制
原因分析及改善對策
七.裂片站用裂片治具折板面過寬: As-is
To-be
§ 改善前,裂片工作平面較寬,手工彎折過程中會造成 臨近PCB’A板邊元件撞件。