不锈钢的电解法抛光标准912
不锈钢电解工艺
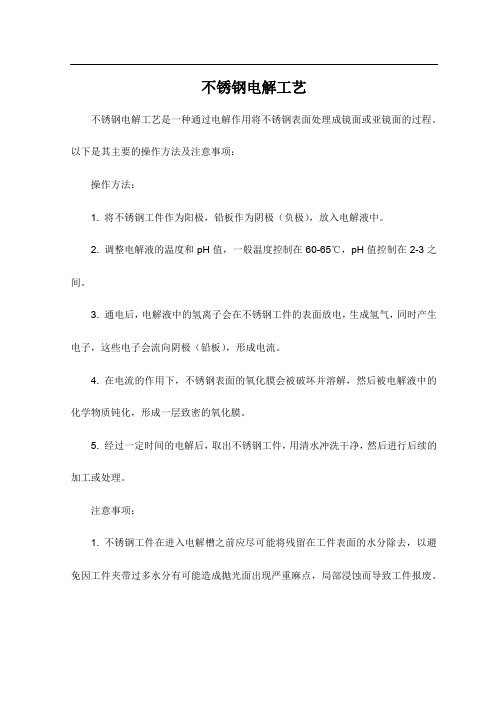
不锈钢电解工艺
不锈钢电解工艺是一种通过电解作用将不锈钢表面处理成镜面或亚镜面的过程。
以下是其主要的操作方法及注意事项:
操作方法:
1. 将不锈钢工件作为阳极,铅板作为阴极(负极),放入电解液中。
2. 调整电解液的温度和pH值,一般温度控制在60-65℃,pH值控制在2-3之间。
3. 通电后,电解液中的氢离子会在不锈钢工件的表面放电,生成氢气,同时产生电子,这些电子会流向阴极(铅板),形成电流。
4. 在电流的作用下,不锈钢表面的氧化膜会被破坏并溶解,然后被电解液中的化学物质钝化,形成一层致密的氧化膜。
5. 经过一定时间的电解后,取出不锈钢工件,用清水冲洗干净,然后进行后续的加工或处理。
注意事项:
1. 不锈钢工件在进入电解槽之前应尽可能将残留在工件表面的水分除去,以避免因工件夹带过多水分有可能造成抛光面出现严重麻点,局部浸蚀而导致工件报废。
2. 在电解过程中,作为阳极的不锈钢工件,其所含的铁、铬元素不断转变为金属离子溶入抛光液内而不在阴极表面沉积。
随着抛光过程的进行,金属离子浓度不断增加,当达到一定数值后,这些金属离子以磷酸盐和硫酸盐形式不断从抛光液内沉淀析出,沉降于抛光槽底部。
为此,抛光液必须定期过滤,去除这些固体沉淀物。
3. 电解工艺用一个高的电流密度维持工件表面膜的生成和溶解的动态平衡,使工件表面保留一层厚度一定的、致密的薄膜。
4. 在操作过程中要严格控制电流密度、电解液的温度和浓度等参数。
以上信息仅供参考,建议咨询专业人士获取具体信息。
不锈钢抛光检验标准
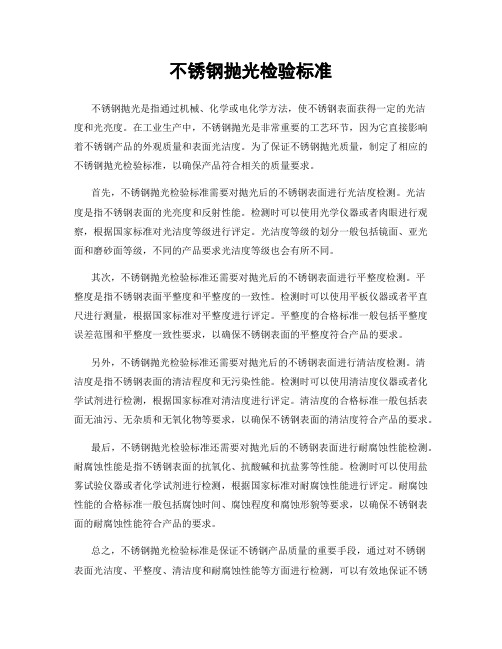
不锈钢抛光检验标准不锈钢抛光是指通过机械、化学或电化学方法,使不锈钢表面获得一定的光洁度和光亮度。
在工业生产中,不锈钢抛光是非常重要的工艺环节,因为它直接影响着不锈钢产品的外观质量和表面光洁度。
为了保证不锈钢抛光质量,制定了相应的不锈钢抛光检验标准,以确保产品符合相关的质量要求。
首先,不锈钢抛光检验标准需要对抛光后的不锈钢表面进行光洁度检测。
光洁度是指不锈钢表面的光亮度和反射性能。
检测时可以使用光学仪器或者肉眼进行观察,根据国家标准对光洁度等级进行评定。
光洁度等级的划分一般包括镜面、亚光面和磨砂面等级,不同的产品要求光洁度等级也会有所不同。
其次,不锈钢抛光检验标准还需要对抛光后的不锈钢表面进行平整度检测。
平整度是指不锈钢表面平整度和平整度的一致性。
检测时可以使用平板仪器或者平直尺进行测量,根据国家标准对平整度进行评定。
平整度的合格标准一般包括平整度误差范围和平整度一致性要求,以确保不锈钢表面的平整度符合产品的要求。
另外,不锈钢抛光检验标准还需要对抛光后的不锈钢表面进行清洁度检测。
清洁度是指不锈钢表面的清洁程度和无污染性能。
检测时可以使用清洁度仪器或者化学试剂进行检测,根据国家标准对清洁度进行评定。
清洁度的合格标准一般包括表面无油污、无杂质和无氧化物等要求,以确保不锈钢表面的清洁度符合产品的要求。
最后,不锈钢抛光检验标准还需要对抛光后的不锈钢表面进行耐腐蚀性能检测。
耐腐蚀性能是指不锈钢表面的抗氧化、抗酸碱和抗盐雾等性能。
检测时可以使用盐雾试验仪器或者化学试剂进行检测,根据国家标准对耐腐蚀性能进行评定。
耐腐蚀性能的合格标准一般包括腐蚀时间、腐蚀程度和腐蚀形貌等要求,以确保不锈钢表面的耐腐蚀性能符合产品的要求。
总之,不锈钢抛光检验标准是保证不锈钢产品质量的重要手段,通过对不锈钢表面光洁度、平整度、清洁度和耐腐蚀性能等方面进行检测,可以有效地保证不锈钢产品的质量稳定性和一致性。
制定和执行严格的不锈钢抛光检验标准,有利于提高不锈钢产品的市场竞争力,促进不锈钢产业的健康发展。
不锈钢抛光工艺标准

不锈钢抛光工艺标准不锈钢抛光是指通过机械或化学方法,使不锈钢表面光洁、光亮,并消除表面缺陷的一项工艺。
它可以改善不锈钢表面的装饰性和耐腐蚀性,延长不锈钢材料的使用寿命。
不锈钢抛光工艺标准包括了抛光前的准备工作、不锈钢抛光方法、抛光后的清洁和保养等内容。
首先,不锈钢抛光前的准备工作包括检查和清洁不锈钢表面。
检查表面是否有氧化、污垢、焊渣、划痕和凹坑等缺陷,如果有需要进行修复。
清洁不锈钢表面的方法包括机械清洗、溶剂清洗和电解清洗。
机械清洗是通过擦拭,刷洗或喷洗等方式去除不锈钢表面的污垢;溶剂清洗是利用有机溶剂溶解附着在不锈钢表面的污垢;电解清洗则是利用电化学原理去除不锈钢表面的氧化物和无机盐等物质。
其次,不锈钢抛光有多种方法,包括机械抛光、化学抛光和电解抛光。
机械抛光是最常用的抛光方法,它通过研磨、拋光和抛光等过程来提高不锈钢表面的光洁度。
化学抛光是利用化学药剂进行表面处理,去除氧化皮和氧化物,改善表面质量。
电解抛光则是利用电化学原理,在电解液中通过电流作用使不锈钢表面离子释放,消除表面缺陷。
不锈钢抛光后需要进行清洁和保养。
清洁时应避免使用有机溶剂和酸碱溶液,以免对不锈钢表面造成损害。
通常使用温和的洗涤剂和清水进行清洁。
保养时应定期擦拭不锈钢表面,以保持光洁度和美观。
如遇到严重损伤,应及时修复,以免影响使用性能。
总结起来,不锈钢抛光工艺标准包括抛光前的准备工作、抛光方法的选择和抛光后的清洁与保养。
在进行不锈钢抛光时,需要根据具体情况选择合适的抛光方法,并注意保护不锈钢表面,以延长使用寿命和提高表面质量。
这些标准对于保证不锈钢制品的质量和装饰性具有重要意义。
总字数:623字。
电解抛光技术参数

糖精 2-4g / L;DA30-60A/ dm2;T 50-70℃;t 5-8 min; 钝化:CrO3 100-150g / L;H2SO4 1-5ml / L;室温 10-20℃。
电解抛光技术参数
序号 1 2 3 4 药物名称 磷酸 硫酸 铬酐 明胶 用量 500 毫升 400 毫升 50 克 7克
使用方法: 1.温度 60℃ 2.时间 5 分钟 3.电压 4.电流
பைடு நூலகம்
]
不锈钢电化抛光新工艺
在生产过程中不锈钢表面容易出现一些黑色氧化皮或是微观不平等, 影响其 使用价值。只有对其再加工如机械抛光、化学抛光和电化抛光处理来提高其自 身价值,因此推荐以下的工艺或许可获得较好的效果。 化学去油→水洗→酸洗→水洗→化学抛光→水洗→电抛光→水洗→钝化→ 水洗→烘干→检验。 化学抛光:30%H2O2 150-220ml / L;H2SO4 约 5 ml / L;稳定剂 10g / L; T 50-70℃;t 5-10min; 电化学抛光: 85% H3PO4 600ml / L; 94%H2SO4 300ml / :L; 丙三醇 30ml / L;
不锈钢电解检验标准
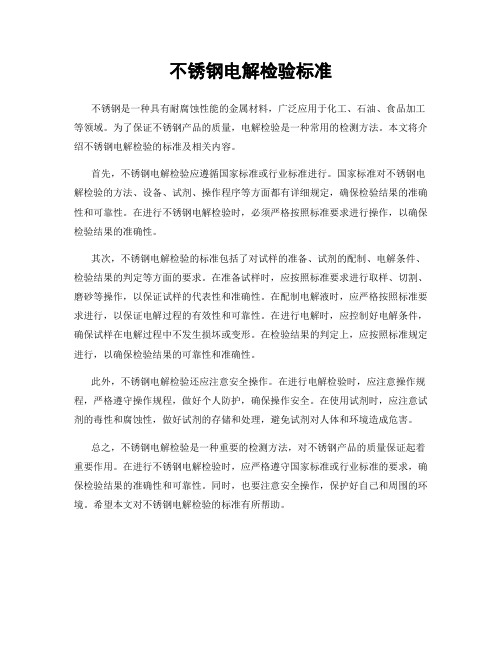
不锈钢电解检验标准
不锈钢是一种具有耐腐蚀性能的金属材料,广泛应用于化工、石油、食品加工等领域。
为了保证不锈钢产品的质量,电解检验是一种常用的检测方法。
本文将介绍不锈钢电解检验的标准及相关内容。
首先,不锈钢电解检验应遵循国家标准或行业标准进行。
国家标准对不锈钢电解检验的方法、设备、试剂、操作程序等方面都有详细规定,确保检验结果的准确性和可靠性。
在进行不锈钢电解检验时,必须严格按照标准要求进行操作,以确保检验结果的准确性。
其次,不锈钢电解检验的标准包括了对试样的准备、试剂的配制、电解条件、检验结果的判定等方面的要求。
在准备试样时,应按照标准要求进行取样、切割、磨砂等操作,以保证试样的代表性和准确性。
在配制电解液时,应严格按照标准要求进行,以保证电解过程的有效性和可靠性。
在进行电解时,应控制好电解条件,确保试样在电解过程中不发生损坏或变形。
在检验结果的判定上,应按照标准规定进行,以确保检验结果的可靠性和准确性。
此外,不锈钢电解检验还应注意安全操作。
在进行电解检验时,应注意操作规程,严格遵守操作规程,做好个人防护,确保操作安全。
在使用试剂时,应注意试剂的毒性和腐蚀性,做好试剂的存储和处理,避免试剂对人体和环境造成危害。
总之,不锈钢电解检验是一种重要的检测方法,对不锈钢产品的质量保证起着重要作用。
在进行不锈钢电解检验时,应严格遵守国家标准或行业标准的要求,确保检验结果的准确性和可靠性。
同时,也要注意安全操作,保护好自己和周围的环境。
希望本文对不锈钢电解检验的标准有所帮助。
不锈钢电解抛光标准

不锈钢电解抛光标准不锈钢电解抛光是一种常见的表面处理工艺,它可以使不锈钢表面获得良好的光洁度和平整度,提高其美观性和耐腐蚀性。
为了确保不锈钢电解抛光的质量,制定了一系列的标准来规范该工艺的操作和要求。
首先,不锈钢电解抛光的标准应包括对原材料的要求。
原材料应选择具有良好表面质量和机械性能的不锈钢材料,以确保在抛光过程中不会出现气孔、裂纹等缺陷。
同时,对原材料的化学成分、硬度、拉伸强度等指标也应有明确的规定,以保证抛光后的产品符合相关的使用要求。
其次,不锈钢电解抛光的标准还应包括对抛光工艺的要求。
包括电解液的配制、电解抛光设备的选择和操作、抛光时间、电流密度等参数的控制,都应在标准中有所规定。
这些要求旨在确保抛光过程中能够获得一致的抛光效果,避免出现过度抛光或不足抛光的情况。
另外,不锈钢电解抛光的标准还应包括对抛光后表面质量的评定标准。
这包括表面光洁度、平整度、氧化膜厚度、腐蚀性能等指标的检测方法和要求。
这些评定标准的设立可以帮助生产厂家和使用者对抛光后的产品进行质量检验,确保产品的质量稳定性和一致性。
最后,不锈钢电解抛光的标准还应包括对产品包装、储存和运输的要求。
这些要求包括包装材料的选择、包装方式、标识和储存条件等,以确保产品在运输过程中不会受到损坏,同时也为使用者提供了正确的存储和使用方法。
总之,不锈钢电解抛光的标准是保证产品质量和生产工艺稳定性的重要依据。
只有严格遵守相关标准,才能够生产出符合要求的不锈钢电解抛光产品,提高产品的市场竞争力和用户满意度。
希望生产厂家和相关从业人员能够认真遵守相关标准,共同推动不锈钢电解抛光工艺的健康发展。
不锈钢电解抛光工艺【详解】

不锈钢电解抛光工艺内容来源网络,由“深圳机械展(11万㎡,1100多家展商,超10万观众)”收集整理!更多cnc 加工中心、车铣磨钻床、线切割、数控刀具工具、工业机器人、非标自动化、数字化无人工厂、精密测量、3D打印、激光切割、钣金冲压折弯、精密零件加工等展示,就在深圳机械展.一.工作原理⑴、电解是以抛光工件为阳极,不溶性金属为阴极,两极同时浸入电化学槽中,通直流电而产生有选择性的阳极溶解,因此不锈钢表面达到高度光洁和光泽的外观。
⑵、电解作用不锈钢经过电解,其色泽内外一致,清洁光亮,光泽持久,表面形成---黏性薄膜,抗腐蚀性能增强。
二. 电解溶液组成和工艺条件1.磷酸:能起溶解作用又能在不锈钢表面形成磷酸盐保护膜,阻止不锈钢表面发生过腐蚀。
其含量变化较宽,以750mL/L左右为佳。
(1)含量过高时,槽液电阻增大,黏度提高,导致所需电压较高,使整平速度迟缓。
(2)含量过低时,活化倾向大,钝化倾向小,导致不锈钢表面不均匀腐蚀。
2.硫酸:是活化剂,能提高溶液的导电率,降低电阻,从而降低槽电压,节约电能,有利于改善分散能力和提高阳极电流效率。
其含量控制在180~210mL/L为最佳。
(1)含量过高时,活化倾向太大,易使抛光表面出现过腐蚀,呈现均匀的密集麻点。
(2)含量过低时,出现严重的不均匀腐蚀。
3.铬酐:是强氧化剂,使表面形成钝化膜,避免表面腐蚀,有利于获得光洁表面。
其含量控制在50~60g/L为宜。
(1)铬酐浓度太低,不易获得光亮表面。
(2)浓度太高时在大电流下,易产生沉淀析出,降低电流效率,使抛光表面产生麻点等过腐蚀。
4.丙三醇(甘油):能起到良好的缓蚀作用,与磷酸生成络合物及其金属衍生物,使抛光表面非常光亮细致,甘油还能防止不锈钢在电解液中的化学腐蚀。
(1)含量过低时,抛光表面虽然光亮,但有腐蚀粗糙之处。
(2)含量高时,即可克服粗糙,又使抛光面光亮细致。
(3)含量过高时,会产生太多的泡沫,影响操作,也浪费材料。
不锈钢电解新抛光工艺介绍(pdf 7页)

不锈钢电解新抛光工艺一、特点1、抛光效率高,数分钟内可抛光至镜面光亮,且抛光深度强,抛光后光泽保持长久不变。
2、抛光液磷酸含量低,成本低,较一般使用的传统抛光液低30%以上。
3、抛光电流密度小,电压低,电能消耗较传统工艺低1倍左右。
4、抛光液稳定容易维护管理。
5、适用18-8类型奥氏体不锈钢抛光,也适用镍基合金抛光。
二、抛光液组成和操作条件浓磷酸(比重1.74)510ml/L88 7.4g/L浓硫酸(比重1.84)395ml/L72 6.8g/LLQ-60添加剂50ml/L52.5g/ L水50ml/L50g/L温度50–75℃最佳60–65℃阳极电流密度,DA6–15A/dm2最佳10–12A/dm2电压5–8伏抛光时间3–5分钟阴极材料铅或铅合金阴极面积∶阳极面积2–3∶1三、开槽步骤LQ-60添加剂是一种表面活性剂,在其使用初期电解抛光时会产生大量泡沫,因此抛光液液面与抛光槽顶部之间的距离不应≤15cm。
准确计算将欲配制的电解抛光液的体积,再根据抛光液组成将所要加入的抛光液各组分按下列顺序加入抛光槽内。
1、注入所需水量。
2、加入所需磷酸量。
3、切记硫酸用水稀释时会释放出大量热量,溶液温度急剧升高,边搅拌边添加,当温度升至80℃时应停止添加,待溶液冷却后再进一步添加直至全部加完。
4、加入所需数量LQ-60添加剂,边搅拌边添加,添加完毕后彻底搅拌以确保均匀混合。
四、工艺流程温度50–75℃最佳60–65℃阳极电流密度,DA6–15A/dm2最佳10–12A/dm2电压5–8伏抛光时间3–5分钟阴极材料铅或铅合金阴极面积∶阳极面积2–3∶1三、开槽步骤LQ-62添加剂是一种表面活性剂,在其使用初期电解抛光时会产生大量泡沫,因此抛光液液面与抛光槽顶部之间的距离不应≤15cm。
准确计算将欲配制的电解抛光液的体积,再根据抛光液组成将所要加入的抛光液各组分按下列顺序加入抛光槽内。
1、注入所需水量。
2、加入所需磷酸量。
不锈钢电解抛光工艺及配方
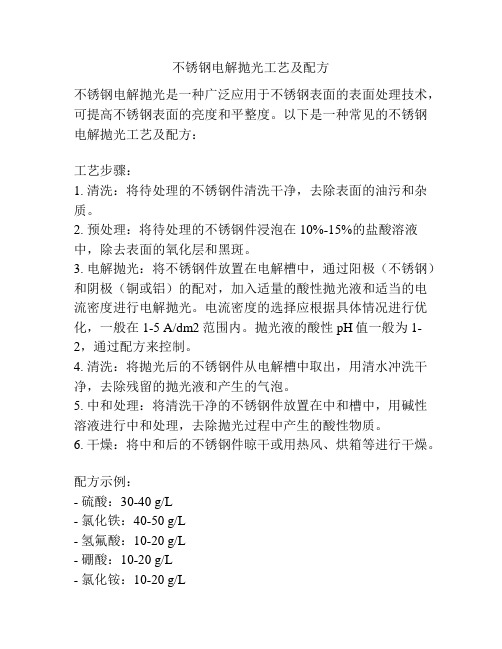
不锈钢电解抛光工艺及配方
不锈钢电解抛光是一种广泛应用于不锈钢表面的表面处理技术,可提高不锈钢表面的亮度和平整度。
以下是一种常见的不锈钢电解抛光工艺及配方:
工艺步骤:
1. 清洗:将待处理的不锈钢件清洗干净,去除表面的油污和杂质。
2. 预处理:将待处理的不锈钢件浸泡在10%-15%的盐酸溶液中,除去表面的氧化层和黑斑。
3. 电解抛光:将不锈钢件放置在电解槽中,通过阳极(不锈钢)和阴极(铜或铝)的配对,加入适量的酸性抛光液和适当的电流密度进行电解抛光。
电流密度的选择应根据具体情况进行优化,一般在1-5 A/dm2范围内。
抛光液的酸性pH值一般为1-2,通过配方来控制。
4. 清洗:将抛光后的不锈钢件从电解槽中取出,用清水冲洗干净,去除残留的抛光液和产生的气泡。
5. 中和处理:将清洗干净的不锈钢件放置在中和槽中,用碱性溶液进行中和处理,去除抛光过程中产生的酸性物质。
6. 干燥:将中和后的不锈钢件晾干或用热风、烘箱等进行干燥。
配方示例:
- 硫酸:30-40 g/L
- 氯化铁:40-50 g/L
- 氢氟酸:10-20 g/L
- 硼酸:10-20 g/L
- 氯化铵:10-20 g/L
以上只是一种不锈钢电解抛光的工艺及配方,具体的抛光工艺和配方应根据不同的不锈钢材质和要求进行优化和调整。
在实际操作中应严格遵守相关安全操作规程,并按照实验室或工艺流程进行操作。
电解抛光产品表面质量检验规程

电解抛光产品表面质量检验规程1范围本标准规定了不锈钢电解抛光件产品表面质量的检验条件、方法及检验内容。
本标准适用于不锈钢产品的内外表面电解抛光表面质量要求,适用于公司所有不锈钢配件产品的检验。
2规范性引用文件下列文件中的条款通过本标准的引用而成为本标准的条款。
凡是注日期的引用文件,其随后所有的修改单(不包括勘误内容)或修订版均不适用于本标准。
然而,鼓励根据本标准达成协议的各方研究是否可使用这些文件的最新版本。
凡是不注日期的引用文件、其最新版本适用于本标准。
GB/T -2012人造气氛腐蚀试验盐雾试验GB/T 6461-2002金属基体上金属和其它无机覆盖层经腐蚀试验后的试样和试件的评级GB/T2828.1-2012/的逐批检验抽样打算3术语和定义下列术语与定义适用于本文件3.1电解抛光电解抛光,是以被抛工件为阳极,不溶性金属为阴极,两极同时浸入到电解槽中,通以直流电离反应而产生有选择性的阳极溶解,从而达到工件表面除去渺小毛刺和光明度增大的效果。
4电解抛光的工序要求电解抛光应严格按以下工序要求执行,并每工序的时间应达到相关要求。
除油处理→水洗→电解抛光→水洗→中和→水洗→钝化→烘干5质量要求5.1表面质量要求5.1.1所有内、外表面电解抛光的产品应内部或外色泽一致,不可以有没有电解到的地方。
5.1.2电解表面不可有麻点。
5.1.3产品表面不可有烧伤现象。
5.1.4电解表面不可有发白、发黄、发黑现象。
5.1.5产品上不可以留有黑色及烧焦的挂点。
5.1.6外表面电解抛光不可有阴阳面,及局部无光泽的现象。
5.2其他要求5.2.1镀层耐腐蚀性要求:按照GB/T 进行24小时乙酸盐雾(AASS)试验,应不低于GB/T6461-2002标准中表1中外观评级(RA)10级以上的要求。
或按照GB/T进行8小时铜加速乙酸盐雾(CASS)试验,应不低于GB/T 6461-2002标准中表1中外观评级(RA)10级以上的请求。
不锈钢铸件电解抛光操作规范

不锈钢铸件电解抛光操作规范SANY GROUP system office room 【SANYUA16H-不锈钢铸件电解抛光操作规范一.目的:规范公司不锈钢铸件电解抛光过程操作,使电解抛光的产品能满足客户质量要求。
二.适用范围:适用于公司所有含Cr≥15.5,含Ni≥3.0的奥氏体及马氏体不锈钢铸件。
三.操作要求:1.电解前处理:1.1所有不锈钢铸件电解前必须经除油、抛丸、酸洗处理,以彻底除掉表面的油污、浆粉及氧化皮,酸洗时注意控制酸洗时间,不可将铸件酸洗过度使表面出现类似花纹状的图案,尤其是17-4等马氏体类不锈钢铸件。
1.2不得将产品上的残酸及水份带入电解槽内,以防止对电解液造成污染。
1.3不锈钢铸件电解前酸洗液配方见下表2.电解液配方(组成比例为溶液重量比)及工艺要求磷酸(浓度85%,密度1.65g/cm3)70-75%硫酸(浓度98%,密度1.84g/cm3)15-20%水5-10%糖精(光亮剂)0.5-1.0g/L电解液相对密度 1.40-1.60g/cm3阴极材料铅板电解挂钩材料紫铜或钛阴极与工件距离20-30CM工作电压6-12V电流密度15-30A/dm2工作温度50-80℃电解时间5-10min(视工件大小及工件多少定)注解:电流密度是指电解工作电流/电解工件的总面积3.电解过程中的注意事项:3.1配制或添加电解液时注意加料顺序,先往电解槽内加入磷酸,再加入硫酸,最后加水。
3.2产品电解前先检查铜棒和挂钩接触点是否通电,如有因铜锈影响导电,可用砂纸擦掉铜锈或用硝酸溶液浸泡。
3.3每班电解前要用比重计检测电解液相对密度,密度过大时加水调整,密度过小时用石英加热管加热除水调整。
3.4产品电解前检查电解液温度是否在工艺要求范围内,否则要升温或降温处理。
3.5挂钩上的产品不可挂得太多、太密,防止产品间相互遮挡影响电解效果。
3.6产品与挂钩接触点尽可能大,以保证产品获得较大电流。
3.7电解时要根据产品结构及大小调整电流大小,防止因电流过大腐蚀产品棱角部位.3.8电解过程中随时观察产品表面光亮度,不够亮度可适当延长电解时间或调大电压、电流。
不锈钢电解抛光工艺 (2)

不锈钢电解抛光工艺
不锈钢电解抛光工艺是通过电解的方式,利用化学反应将不锈钢表面的氧化物去除,达到抛光的效果。
具体步骤如下:
1.准备工作:将不锈钢工件清洗干净,去除表面的污垢和油脂。
2.设备搭建:将不锈钢工件连接到阳极,将铝或不锈钢片连接到阴极。
电解槽中加入适量的电解液,如硫酸、硝酸
3.调节电解液:根据具体要求,适当调节电解液的配方和浓度,以便达到理想的抛光效果。
4.设定电解条件:根据工件的材质和要求,设置适当的电解电压、电流密度和电解时间。
5.开始电解抛光:通电后,电解液会开始起化学反应,将不锈钢表面的氧化物剥离。
6.抛光后处理:抛光结束后,将工件从电解槽中取出,用清水冲洗干净,去除电解液和残留物。
7.除锈处理:为了防止不锈钢表面再次氧化,可以进行除锈处理,常见的方法有化学除锈、机械扫光等。
8.冲洗和干燥:对工件进行彻底的冲洗,确保表面不留任何化学物质和水渍,然后用干净的布擦干。
注意事项:
1操作过程中要戴好防护手套、护目镜等防护装备,以免发生意外伤害。
2.严格控制电解条件,尽量选择合适的电压和电流密度,避免过高的电流造成烧伤或损坏工件。
3.使用合适的电解液,以避免不锈钢表面发黄或产生其他不良问题。
4.进行后续处理时,要注意保护好不锈钢表面,避免划伤或破坏。
不锈钢的电解抛光及电解腐蚀

(上接第 28ห้องสมุดไป่ตู้页) 3. 4 低压缸汽封径向间隙大
通过这次检漏试验 ,发现低压缸前后汽封处泄 漏较为严重 ,漏率达到 7 ×10 - 7 Pa/ min 。由于泄漏 面积较大 ,对机组的真空状况造成很大影响 。为此 进行了调整汽封压力的对比性试验 ,将汽封母管压 力从 0. 15 MPa 提高至 0. 23 MPa ,并调整各供汽分 门 ,增大低压缸汽封的供汽量 ,但并没有消除低压缸 汽封处的泄漏 ,这足以说明因低压缸汽封的径向间 隙较大 ,使大量空气漏入真空系统 。建议在机组大 修过程中对汽封片进行认真检查 ,并重新调整汽封 径向间隙 。 3. 5 疏水扩容器有漏点
摘要 :文章介绍采用电解抛光及电解腐蚀的不锈钢金相检验 制样过程 ,试验结果表明 ,电解抛光及腐蚀法制备试样能获 得清晰组织 。 关键词 :不锈钢 ;电解抛光 ;电解腐蚀 Abstract : This paper introduces application of electrolytic polish2 ing and electrolytic corrosion in stainless steel sample preparing for metallographic examining , The test results indicate t hat us2 ing electrolytic polishing and electrolytic corrosion to prepare ex2 amining sample can obtain microstructure wit h clear resolution. Keywords :stainless steel ; electrolytic polishing ; electrolytic cor2 rosion 中图分类号 : T G115. 21 文献标识码 :B 文章编号 :1001 - 9898 (2002) 02 - 0040 - 02
电解研磨抛光对不锈钢研磨抛光的处理方法

电解研磨抛光对不锈钢研磨抛光的处理方法不锈钢会不会生锈?大多数人认为不锈钢是不会生锈,包括全国大部分金属表面处理、金属加工厂、五金磨光厂、不锈钢金属抛光厂工作人员。
据研磨专家深圳莱纳克科技有限公司专家介绍,其实不然,不锈钢和其它许多金属一样,用手接触或者接触空气,受环境影响时也会被氧化生锈。
另外,不锈钢工件表面经过机械加工例如焊接、冲压、卷曲、热处理等工艺处理之后生成一层乌黑的氧化变质硬化层,同时又形成了许多肉眼看见和看不见的微小毛刺,以及锐角毛边等。
一、抛光方法一般情况下用机械的方法很难将它们除去,影响其工件材质本身特性的发挥。
为了解决这些问题,深圳市莱纳克科技有限公司(专业生产及销售高精度的研磨、抛光、珩磨机设备,并提供对各类材质的零部件进行平面研磨、抛光等加工服务。
)使用各种方法对不锈钢等金属表面进行研磨抛光处理。
1、机械研磨抛光:a) 砂轮抛光b) 喷沙抛光c) 研削抛光d) 挤压抛光2、化学研磨抛光:a) 电解化学研磨抛光b) 化学研磨抛光3、复合研磨抛光:机械法和化学法两种研磨方式的组合对于不同的金属材质,不同的使用场合,对金属工件表面不同的需求,必须采用不同的研磨方法或者几种研磨方式组合进行研磨加工处理才能使加工工件满足使用上的要求。
化学研磨、电解研磨和机械研磨的区别(1) 化学研磨与机械研磨有本质上的不同“化学研磨”是将被研磨面上的微小凸部与凹部相比较的情况下使其凸部优先溶解,改善金属表面粗糙度,获得平滑光亮表面的过程。
“机械研磨”是将被研磨面的凸部用切削,磨耗或者塑性变形等方式除去,获得平滑光亮表面的过程。
两种研磨方式对金属表面有不同的影响,金属表面的许多性质被改变,所以化学研磨与机械研磨有本质上的不同。
由于机械抛光的局限性,使不锈钢等金属工件不能发挥其应有的功能,对这些问题难于解决,在20世纪80年代出现了不锈钢电解化学研磨抛光技术,一定程度上解决了机械抛光难于解决的问题,优势明显。
不锈钢镜面抛光工艺标准及其方法和要求

不锈钢镜面抛光工艺及方法和要求不锈钢抛光工艺可以分为打磨和出光两局部。
现将该两局部工艺和方法总结以下:Ⅰ.打磨不锈钢焊接件打磨主要目标是去掉焊点,到达表面粗糙度为R10um 的工件,为出光做准备!打磨局部概括来说有:三个工序:粗磨,半精磨,精磨三个面:两个侧面一个棱边九个抛光机二十七个调治机构,详细说明以下:1、对上道转入抛光工序的工件进行目测检验,如焊缝可否有漏焊,焊穿,焊点深浅不均匀,偏离接缝太远,局部凹陷,对接不齐,可否有较深划痕,碰伤,严重变形等在本工序无法拯救的弊端,若是有上述弊端应返回上道工序修整。
若是无上述弊端,进入本抛光工序。
2、粗磨,用 600#的砂带在三面上往返磨削工件,本工序要达到的目标是去掉工件焊接留下的焊点,以及在上步工序出现的碰伤,到达焊口圆角初步成型,水平面和垂直面根本无大划痕,无碰伤,经此步工序后工件表面的粗糙度应能到达。
注意在抛光过程中注意砂带机的倾斜角度和控制好砂带机对工件的压力。
一般来说以与被抛面成一条直线比较适中!3、半精磨,用800#的砂带依照前面往返磨削工件的方法中磨工件的三面,主若是对前面工序出现的接缝进行修正以及对粗磨后产生的印痕进前进一步的细磨,对前面工序留下的印痕要屡次磨削,达到工件表面无划痕,根本变亮。
本工序表面粗糙度应能到达。
〔注意本工序不要产生新的划痕及碰伤,由于在后边的工序无法维修此类弊端。
〕4、精磨,用 1000#的砂带主若是对前步工序出现的微小纹线的修正磨削,磨削方法与上同。
本工序要到达的目标是磨削局部与工件未磨削局部的接缝根本消失,工件表面进一步光明,经过本工序磨削后的工件要根本凑近镜面收效,工件表面粗糙度应能到达R0.1mm 5、关于更换砂带的说明:一般来说, 600#的砂带可以抛磨1500mm 长的工件 6-8 根, 800#的砂带可以抛磨工件4-6 根, 1000#的砂带可以抛磨工件1-2 根,详细情况还需以工件焊接焊点情况,抛光使用的压力,以及打磨的方式方法有很大的关系。
一种用于ebsd测试的奥氏体不锈钢电解抛光方法与流程
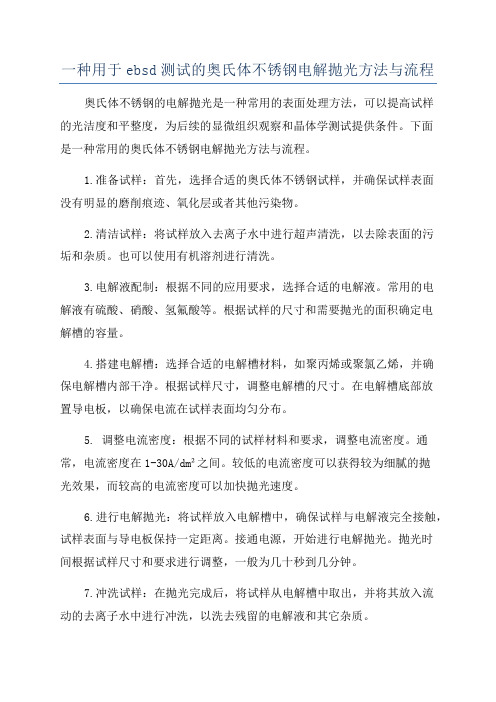
一种用于ebsd测试的奥氏体不锈钢电解抛光方法与流程奥氏体不锈钢的电解抛光是一种常用的表面处理方法,可以提高试样的光洁度和平整度,为后续的显微组织观察和晶体学测试提供条件。
下面是一种常用的奥氏体不锈钢电解抛光方法与流程。
1.准备试样:首先,选择合适的奥氏体不锈钢试样,并确保试样表面没有明显的磨削痕迹、氧化层或者其他污染物。
2.清洁试样:将试样放入去离子水中进行超声清洗,以去除表面的污垢和杂质。
也可以使用有机溶剂进行清洗。
3.电解液配制:根据不同的应用要求,选择合适的电解液。
常用的电解液有硫酸、硝酸、氢氟酸等。
根据试样的尺寸和需要抛光的面积确定电解槽的容量。
4.搭建电解槽:选择合适的电解槽材料,如聚丙烯或聚氯乙烯,并确保电解槽内部干净。
根据试样尺寸,调整电解槽的尺寸。
在电解槽底部放置导电板,以确保电流在试样表面均匀分布。
5. 调整电流密度:根据不同的试样材料和要求,调整电流密度。
通常,电流密度在1-30A/dm²之间。
较低的电流密度可以获得较为细腻的抛光效果,而较高的电流密度可以加快抛光速度。
6.进行电解抛光:将试样放入电解槽中,确保试样与电解液完全接触,试样表面与导电板保持一定距离。
接通电源,开始进行电解抛光。
抛光时间根据试样尺寸和要求进行调整,一般为几十秒到几分钟。
7.冲洗试样:在抛光完成后,将试样从电解槽中取出,并将其放入流动的去离子水中进行冲洗,以洗去残留的电解液和其它杂质。
8.试样分析:将抛光后的试样放入显微镜或电子显微镜中进行组织分析,以获取所需的显微结构和晶体学信息。
需要注意的是,在进行电解抛光时要保证安全操作,如佩戴防护眼镜和手套,定期检查电源和设备的连接。
此外,应根据试样的具体要求进行实验参数的调整,以获得最佳的抛光效果。
电解不锈钢抛光技术.

一.电化学抛光理论:1.电化学抛光定义(即什么是电解?):以被抛工件为阳极,不溶性金属为阴极,两极同时浸入到电解槽中,通以直流电而产生有选择性的阳极溶解,从而达到工件表面光亮度增大的效果。
2.电解原理:电解原理现在世界各界人士争论很多,被大家公认的主要为黏膜理论。
工件上脱离的金属离子与抛光液中的磷酸形成一层磷酸盐膜吸附在工件表面,这种黏膜在凸起处较薄,凹处较厚,因凸起处电流密度高而溶解快,随黏膜流动,凹凸不断变化,粗糙表面逐渐被整平。
3.电解抛光优点:⑴内外色泽一致,光泽持久,机械抛光无法抛到的凹处也可整平。
⑵生产效率高,成本低廉。
⑶增加工件表面抗腐蚀性。
二.电化学抛光所需条件及设备1.电源:电源可选用双相220V,三相380V。
2.整流器电解抛光对电源波形要求不是太严格,可选用可控硅整流器好高频整流器。
整流器空载电压:0—20v负载电压(工作电压):8—10v工作电压低于6v,抛光速度慢,光亮度不足。
整流器电流:根据客户工件大小而定。
3.电解槽及配套设施(阳极棒)可选用聚氯乙烯硬板材焊接而成。
在槽上装三根电极棒,中间为可移动的阳极棒,接电源阳极(或正极),两侧为阴极棒,连接电源阴极(负极)。
4.加热设施及冷却设备(1)加热可选用石英加热管,钛加热管。
(2)冷却可选用盘管,盘管可加热可冷却。
5.夹具最好选用钛做挂具,因为钛较耐腐蚀,寿命长,钛离子对槽液无影响。
建议最好不要用铜挂具,因为铜离子进入会在不锈钢表面沉积一层结合力不好的铜层,影响抛光质量。
铜裸露部位可用聚氯乙烯胶烘烤成膜,在接触点刮去绝缘膜。
6.阴阳极材料阴阳极棒应用铜棒或铜管,铜管长是电解槽长加20厘米,阴极板应用铅板,铅板固定在阴极棒上,铅板长为槽高加10厘米,铅板宽根据槽长而定,一般为10厘米,20厘米规格。
三.电解液:这里具体介绍下“云清牌不锈钢通用电解液“。
1.电解液指标:(1)电解液密度:1.68—1.72(2)电解液状态:微黄色透明液体(3)PH值:<7(4)电解液工作电压:5—9v(5)各材质在电解液内的电流密度(单位为每平方分米),200系列15—25安培,300系列10—15安培,400系列20—30安培。
不锈钢电解抛光

氧气压力为0.25MPa,乙炔压力为0.25MPa。
活塞杆经预热和喷薄层保护粉预保护后,开始局部加热,当预保护粉开始湿润时,间歇地按动送粉开关喷粉,同时,将喷上去的合金粉熔融。
喷粉时焰芯尖端与工件表面的距离为20mm左右,熔融时6~7mm。
火焰向前移动时,再间歇喷粉并熔融。
喷焊层厚度为1.5mm,焊后应缓慢冷却,以防止裂纹和变形。
3.4 喷后修整缓冷至室温后,即可进行磨削,磨削按图纸要求的尺寸和规定的粗糙度进行。
4 工艺特点采用氧2乙炔火焰粉末喷熔工艺修复磨损超差的活塞杆,具有以下特点:(1)喷粉与重熔交替进行,在操作时只需用一把喷枪,工艺简单,操作方便。
由于喷粉和重熔交替进行,因此,要求粉末粒度细且均匀,合金粉的喷射方向要与表面垂直,以保证得到较好的结合效果。
在喷熔过程中,除了要仔细掌握火焰移动速度外,还要注意保持适当的喷涂距离。
(2)输入工件热量少,工件变形较小,且喷熔层厚度可在较大的范围内变化,一般为0.8~1.2mm,最好不超过2mm。
5 结论采用氧2乙炔火焰粉末喷熔工艺对30CrMnSiA 钢制活塞杆进行局部修复,工件变形小,成本低,工艺简单。
本工艺尤其适合于中小型零部件局部磨损的修复,具有较大的推广价值。
参考文献[1] 刘江南.金属表面工程学.北京:兵器工业出版社,1995.[2] 沈传渐.氧2乙炔火焰喷涂与喷焊.北京:中国铁道出版社,1984.[3] 徐滨士.表面工程与维修.北京:机械工业出版社,1996.(收稿日期1999206210)不锈钢电解抛光白祯遐(西北机器厂表面处理分厂,宝鸡722405) 我厂有部分不锈钢零件,形状复杂。
成份为1Cr18Ni9Ti及4Cr13、经机加工后,工件表面灰暗无光、微观凹凸不平、光洁度较差。
而机械抛光有一定的局限性,有些部位无法进行机械抛光。
用电化学抛光取代机械抛光,既提高了生产效率,还提高了工件的表面光洁度,使之达到镜面光洁度,取得了良好的效果。
- 1、下载文档前请自行甄别文档内容的完整性,平台不提供额外的编辑、内容补充、找答案等附加服务。
- 2、"仅部分预览"的文档,不可在线预览部分如存在完整性等问题,可反馈申请退款(可完整预览的文档不适用该条件!)。
- 3、如文档侵犯您的权益,请联系客服反馈,我们会尽快为您处理(人工客服工作时间:9:00-18:30)。
不锈钢的电解法抛光标准
1.范围
此规范涵盖了对200(UNS2xxxx), 300(UNS3xxxx),以及400(UNS4xxxx)合金钢系列进行钝化处理和用电解程序沉淀硬化合金。
注1:在电解条件下,不锈钢表面发生钝化,钝化的质量取决于不锈钢的类型,电解方案,以及运营条件。
通过去除不锈钢表面的游离铁达到提高其腐蚀性能的目的。
另外,电解抛光后,平滑的表面也能改善不锈钢的耐腐蚀性。
同时,电解抛光也能去除那些由于受热产生的彩色氧化层。
1.2本规范也涉及危险的材料,操作单元和设备。
但是此规范并不
是说能够解决所有的安全问题,如有的话,也只是相关。
用户在制定安全作业制度之前有责任准照此规范。
2.所引用的文件
2.1 ASTM标准:
A380:清除不锈钢零件设备及系统表面的铁锈
(详见ASTM标准第二卷01.03)
A967:化学钝化
(详见ASTM标准第二卷01.03)
B117:喷盐法
(详见ASTM标准第二卷03.02)
B322:电解抛光前清洗金属
(详见ASTM标准第二卷02.05)
B374:电解
(详见ASTM标准第二卷02.05)
B602:测试试样金属的属性和无机层
(详见ASTM标准第二卷02.05)
D3951:商品化包装
(查阅美国国家标准学会)
2.2 国际标准化组织的标准
ISO4519 电镀金属涂料及相关完成采样程序
ISO9227 人工盐雾下的腐蚀实验
ISO/DIS 15730 用金属和其它无机涂料电解抛光,使不锈钢表面光滑
ISO/DIS 16348 金属和无机涂料的相关释义
3. 术语
3.1 B314和ISO 2080中有术语的定义
3.2 定义
3.2.1 钝化——不锈钢受一些因素影响,化学稳定性明显增强。
3.2.1.1 钝化表面特点——表面因缺乏游离铁,稳定性大大
增强。
(详见A380)
3.2.2 电解抛光——化学电解过程中,被钝化处理对象作为阳
极浸入一定酸性介质中。
4. 订货信息
4.1 按照此规范,金属件要进行电解抛光处理时买方需要提供以下信息:
4.1.1 合金指定——金属件按照此规范进行钝化处理,买方在除提供ASTM标准的指定号码外,还应提供签发日期,合金指定号码,及测试方法(详见
5.3)
4.1.2 外观——买方应详明外观要求,例如明亮还是暗淡。
另外,买方需要提供试样或卖方做完试样后,买方核定是否合格。
如果需要的话,金属件在电解抛光前要先进行机械抛光;
4.1.3 划痕——在加工过程中很有可能出向电接触划痕,这需要买方和供应商共同商讨这个问题;
4.1.4 金属去除——在电解抛光过程中,金属表面要去掉一部分,通常是5~10微米。
有时为了提高光滑度甚至可达50微米。
订购文件中应包括最大金属去除量;
4.1.5 认证要求见第9条;
4.1.6 包装要求见第10条。
5. 产品要求
5.1 电解抛光后的金属表面,在距离0.5米,用20倍放大的视力范围内,不能有清晰可见的缺陷,如坑,粗糙度,条纹或变色;
注2:材料表面的缺陷,如划痕,缝隙,夹杂物等会影响外观和金属件的表面质量;
5.2 过程
5.2.1 表面清理
5.2.2 电解
注3:一个典型的电解溶液装备和操作条件适合许多不锈钢合金。
专有的电解方案可提供特殊功能使不锈钢合金表面有更好的光泽度,更长的寿命;
注4;由于低电流密度,形状复杂的金属件可能不会受到同样程度的钝化效果。
我们可以通过增加时间或整体电流密度来改善电解抛光的整体效果。
5.2.3 漂洗——经电解抛光后的金属件表面可能会残余一层薄膜,这层膜会对产品产生不良影响,去除这层膜的方法是在10%~30%的硝酸中漂洗。
5.2.3.1 如果本地条件无法用硝酸去除薄膜,也可以用其它酸溶液
注5:密度为60g/L的柠檬酸已经被用于薄膜清除。
一般不推荐使用其它矿物酸如硫酸或盐酸。
另外,中和反应方案(即沉浸在碱性溶液中)也不能使用
5.2.4 最后冲洗——钝化后的清洗将会去除残余酸化水,这些残余的酸化水会影响金属外观和钝化性能通常采用去离子水或蒸馏水进行冲洗,以避免污点。
5.3 钝化测试
5.3.1 电解抛光钝化一般应有下列一个或多个测试方法检验
5.3.1.1 水浸泡试验
5.3.1.2 湿度测试
5.3.1.3 盐雾试验
5.3.1.4 硫酸铜试验
5.3.1.5 游离铁试验
6. 测试程序
6.1 水浸泡试验(详见A967)金属件沉浸在蒸馏水中1小时,然后空干1小时,重复12次(总计24小时)。
钝化失败的现象是24小时后,不锈钢表面出现红色铁锈,这是因为表面游离铁的存在造成的;
6.2 湿度测试(详见A380,A967)金属件在湿度为100%,温度为38的贮藏室存放24小时,钝化失败的现象是24小时后,不锈钢表面出现红色铁锈;
6.3 盐雾试验(详见B117(ISO9227)金属件在指定的盐雾中最少持续存放2小时。
,钝化失败的现象是2小时后,不锈钢表面出现红色铁锈
6.4硫酸铜试验给金属件刷上硫酸铜液体。
钝化失败的现象是不锈钢表面有单质铜沉淀。
此试验不适用马氏体400系列的不锈钢;
6.5 游离铁试验(详见A380,A967)给金属件刷上亚铁氰化钾。
钝化失败的现象是金属表面在30s内显现深蓝色。
7. 采样要求
7.1 B602(ISO4519)中的测试方法可用于电解抛光后的最后阶段7.2 根据B602测试方法对试样大小的要求,从检测现场中随机抽
(详见7.3)现场抽取的金属件应符合B602中的有关抽样计划的规定。
注6:B602中试验方法包括四个抽样计划,其中三个是无损检测。
第四个计划所使用的测试方法是破坏性的。
如果目前尚不清楚是使用破坏性试验还是无损检测,买方应明确其中的测试方法是破坏性试验还是无损检测。
在某种情况下,为了满足某种要求,需要同时使用破坏性实验和无损检测,买方应陈述清楚使用那一种方案。
7.3 试件应是在由同一供应商在同一时间同一地点制作的同样规格的产品中抽取。
7.4 在测试中,如果样件是用来表征整个金属件性质,那么样件应符合规范所要求的性质,尺寸和编号以及所需要的测试方法。
在无损检测和视觉检测中不用准备单独的测试样本,除非需要特殊证明。
但对于破坏性试验,应该进行单独样本测试。
8. 不合格和通知
试样检测结果不符合此规范的要求即视为不合格,这个结果应及时以书面形式通知生产者或供应商,如对试验结果不满意,生产者或供应商可以提出再一次审测的要求。
9. 认证
在指定的采购订单或合同中,买方应提供证明该检测试件可以代表整个金属件所要满足的使用条件,在指定的采购订单或合同中还应含有实验结果报告。
10.1 如果有包装的要求,必须根据本规范实施。
包装过程应和D3951的相关规定一致。
11.测试报告
11.1 测试报告应包括下列内容:
11.1.1 参照此标准
11.1.2 参照此规范的测试方法
11.1.3 对每一个标本的试验区定位
11.1.4 进行测试样本的数量
11.1.5 营办商和测试实验室的名称
11.1.6 每个测试完成的日期
11.1.7 影响试验结果和有效性的外界因数
11.1.8 偏离指定测试方法的地方
11.1.9 测试结果
12. 关键词
电解抛光,钝化,不锈钢
附录
(仅供参考)
X1典型的电解溶液
X1.1 电解抛光材料
硝酸96% 50% v/v 温度75
原磷酸85% 50%v/v 时间2~4分钟
电流密度15amp/dm (最低)阴极区不锈钢,铜,铅
X2 硫酸铜试验
X2.1 材料——硫酸铜测试方案
蒸馏水100mL
硫酸96%/w 0.4Ml
硫酸铜(CuSO4.5H2O) 1.6g
X2.2 步骤——用棉絮把被测试钝化面清洗干净保持便面润湿持续6分钟,如果表面出现铜色斑点或单质铜沉淀则意味着钝化处理失败。
用于实验的试件应该丢弃或再次做钝化处理。
X2.3 记录——每两个星期做一次试验记录
X3游离铁试验
X3.1 材料——氰化钾测试方案
蒸馏水70mL
氰化钾(K3Fe(CN)6) 1.0g
硝酸70%/W 30mL
X3.2 步骤——用棉絮把被测试钝化面清洗干净,用于实验的试件应该丢弃或再次做钝化处理。
X3.3 记录——每日记录一次试验结果。