螺旋输送机叶片成型工艺
螺旋叶片钣金展开与成形工艺
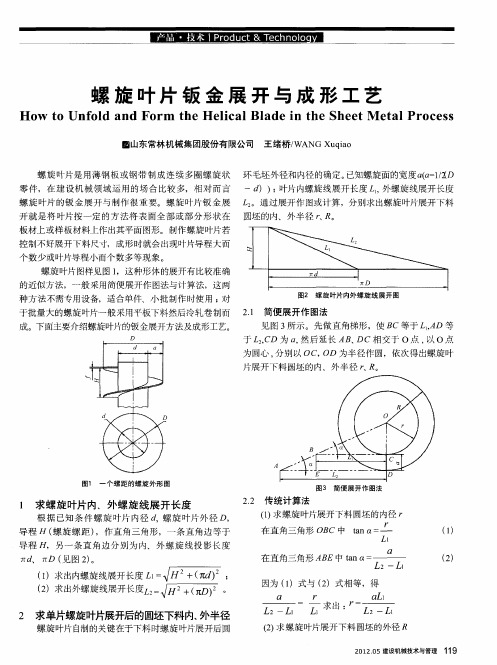
图1 一个螺距 的螺旋 外形图
图3 简便展 开作图法
l 求螺旋叶片内、外螺旋线展 开长度
根 据 已知条 件 螺 旋 叶片 内径 d 螺 旋 叶片外 径 D, , 导程 H ( 旋螺 距 ) 螺 ,作 直 角三角形 ,一 条直 角边等 于
导程 ,另一条 直 角边分 别 为 内、 外螺 旋 线 投 影长度
螺旋线展开长度 ( 见图 2 h );为焊接间隙,常取 3~5 mm。
考虑板厚 ,这里有一个简单陕捷的计算方法 ,在 已知螺旋
Ⅱ片内径 导程 钢板厚度 t 十 这三个基础数据的条件下'
3 单片外螺 旋叶片展开后的开口角度
因螺旋 叶片在 制作 时,要 向里收缩 ,需在 外圆上截
根据公式可以很陕求出螺旋口片展开下料 的内径 r 十 o
L1求出 :
() 2 求螺 旋 叶片展 开下料 圆坯 的外径 R
2 1 建设棚械桔 未与管理 0 20 19 1
在直 角三角形 。 D 中 tn6: a c
L2
螺旋 叶片的正确制作 ,可使各焊缝 相互错开,改善 了受
力环境 ,有利于应力分布,防止螺旋轴 弯曲变 形,特 别 不会造成 由于焊缝在 同一方位而使 运动不平稳 ,另外还 可 以节约原 材料,提 高材料 利用率 ; 要求各 螺旋 叶片 若
于批量 大的螺 旋 叶片_ 采用平板下料然后冷轧卷 制而 21 简便 展 开作 图法 一般 . 见 图 3所示。先做 直角梯形 ,使 B C等于 L,D 等 A
于 L ,D 为 a 然后 延长 AB DC相 交于 0点 , 0点 C , 、 以 为 圆心 , 分别 以 OC OD 为半径作 圆,依次得 出螺 旋 叶 , 片展开下料 圆坯 的 内、外半径 、 。
输送机螺旋叶片制作方法
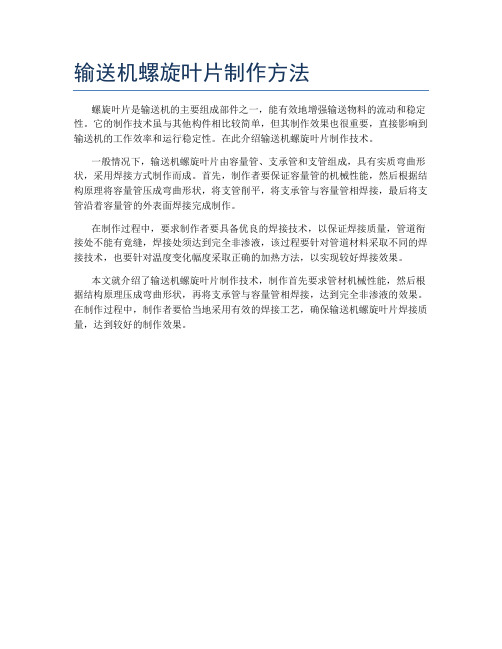
输送机螺旋叶片制作方法
螺旋叶片是输送机的主要组成部件之一,能有效地增强输送物料的流动和稳定性。
它的制作技术虽与其他构件相比较简单,但其制作效果也很重要,直接影响到输送机的工作效率和运行稳定性。
在此介绍输送机螺旋叶片制作技术。
一般情况下,输送机螺旋叶片由容量管、支承管和支管组成,具有实质弯曲形状,采用焊接方式制作而成。
首先,制作者要保证容量管的机械性能,然后根据结构原理将容量管压成弯曲形状,将支管削平,将支承管与容量管相焊接,最后将支管沿着容量管的外表面焊接完成制作。
在制作过程中,要求制作者要具备优良的焊接技术,以保证焊接质量,管道衔接处不能有竟缝,焊接处须达到完全非渗液,该过程要针对管道材料采取不同的焊接技术,也要针对温度变化幅度采取正确的加热方法,以实现较好焊接效果。
本文就介绍了输送机螺旋叶片制作技术,制作首先要求管材机械性能,然后根据结构原理压成弯曲形状,再将支承管与容量管相焊接,达到完全非渗液的效果。
在制作过程中,制作者要恰当地采用有效的焊接工艺,确保输送机螺旋叶片焊接质量,达到较好的制作效果。
螺旋输送器回旋叶片成型工艺
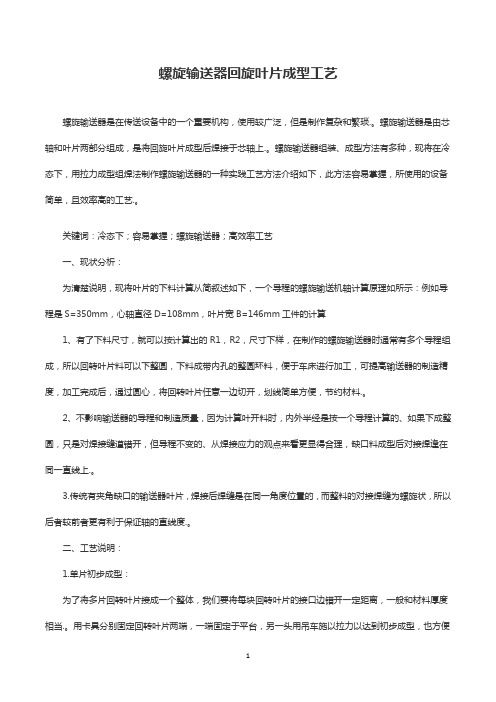
螺旋输送器回旋叶片成型工艺螺旋输送器是在传送设备中的一个重要机构,使用较广泛,但是制作复杂和繁琐.。
螺旋输送器是由芯轴和叶片两部分组成,是将回旋叶片成型后焊接于芯轴上.。
螺旋输送器组装、成型方法有多种,现将在冷态下,用拉力成型组焊法制作螺旋输送器的一种实践工艺方法介绍如下,此方法容易掌握,所使用的设备简单,且效率高的工艺.。
关键词:冷态下;容易掌握;螺旋输送器;高效率工艺一、现状分析:为清楚说明,现将叶片的下料计算从简叙述如下,一个导程的螺旋输送机轴计算原理如所示:例如导程是S=350mm,心轴直径D=108mm,叶片宽B=146mm工件的计算1、有了下料尺寸,就可以按计算出的R1,R2,尺寸下样,在制作的螺旋输送器时通常有多个导程组成,所以回转叶片料可以下整圆,下料成带内孔的整圆环料,便于车床进行加工,可提高输送器的制造精度,加工完成后,通过圆心,将回转叶片任意一边切开,划线简单方便,节约材料.。
2、不影响输送器的导程和制造质量,因为计算叶开料时,内外半经是按一个导程计算的、如果下成整圆,只是对焊接缝道错开,但导程不变的、从焊接应力的观点来看更显得合理,缺口料成型后对接焊逢在同一直线上.。
3.传统有夹角缺口的输送器叶片,焊接后焊缝是在同一角度位置的,而整料的对接焊缝为螺旋状,所以后者较前者更有利于保证轴的直线度.。
二、工艺说明:1.单片初步成型:为了将多片回转叶片接成一个整体,我们要将每块回转叶片的接口边错开一定距离,一般和材料厚度相当.。
用卡具分别固定回转叶片两端,一端固定于平台,另一头用吊车施以拉力以达到初步成型,也方便后续多片回转叶片首尾之间的焊接,由于回转叶片的旋向不同,所以固定端要注意按图纸技术要求施工.。
2,拉伸组焊法:a、将初步成型的回转叶片,首尾相连,相互焊接.。
片数要根据输送轴的长度和螺旋叶片的导程来确定,焊缝正面是一块一块依次焊接的,每块连接都可以方便焊好,反面由于间隙较小不利于焊接,可用斜楔来增加焊接空间,以利于焊接成型.。
螺旋输送机叶片介绍

螺旋输送机叶片螺旋输送机的螺旋叶片有实体螺旋面、带式螺旋面和叶片螺旋面三种形式,其中,叶片式螺旋面应用相对较少,主要用于输送粘度较大和可压缩性物料,这种螺悬面型,在完成输送作业过程中,同时具有并完成对物料的搅拌、混合等功能。
目录1螺旋叶片2其中冷轧成形的方法1螺旋叶片冷轧机是用带钢连续轧制叶片的先进设备,它通过调整部位(轧辊偏移、喂入高度、碾轧压力、导向轮等)的调整,可以轧制出所需要的各种规格的叶片。
目前国内制造叶片的方法有:单件冲压焊接成形、挤压成形、缠绕成形、冷轧成形等方法。
2其中冷轧成形的方法具有生产效率高、节省原材料、叶片质量好、硬度高、耐磨性好等优点。
影响轧制成形的因素,有带钢的材质和厚度,轧辊的偏移量大小、喂入高度、轧辊的碾压力、导向轮、叶片的规格的不同以及轧制过程中,轧辊温度升高等诸多因素。
我公司在经过多年不懈的努力后,研制开发了这种连续冷轧螺旋叶片,它具有表面光滑、硬度高、耐磨、一次成形、连续无焊螺旋输送机可采用右螺旋也可采用左螺旋,这由如何形成螺旋叶片来确定。
面对螺旋叶片如果在螺旋叶片的边缘顺右臂倾斜则为右螺旋;顺左臂倾斜则为左螺旋。
标准螺距单头螺旋——输送机螺旋的螺距等于螺旋的直径,称为标准螺距。
这种螺旋对物料有广泛的适应性,经常被采用。
短螺距单——旋螺距减少到2/3直径称为短螺距。
推荐用于倾角超过20度的倾斜输送机,甚至可垂直使用。
也可用于螺旋给料机。
较短的螺距可防止流态化的物料产生自流。
标准螺距双头螺旋——可使物料平稳的输送及有规律地流动,对于一定类型的物料可保证均匀一致的输送。
短螺距双头螺旋——这种螺旋可使具有流态性质的物料平稳并有规律地流动。
长螺距单头螺旋——一般用来搅动流态化的物料或者快速输送流动性极好的物料。
标准螺距单头锥形螺旋——螺旋叶片的直径由2/3逐渐增大到全直径称为锥形螺旋。
用于螺旋给料机从料仓中均匀地卸下块状物料。
与变距螺旋比较,其作用相同但更为经济。
标准螺距双头锥形螺旋——这种类型的螺旋用于具有易自流物料的给料,物料从料仓沿出料口全长均匀一致被卸下。
螺旋叶片的几种成形方法
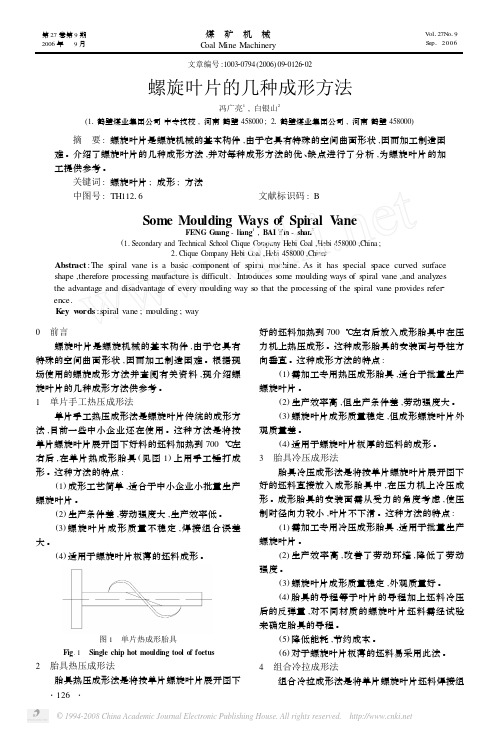
(2) 将单片螺旋叶片坯料剪开 (见图 2 中 A 、B 两点间) 并微开角度焊接组合 ,为有利于冷拉成形 , 需将组合后的螺旋叶片 (16Mn) 进行一次再结晶退 火。
(3) 将组合螺旋叶片两端焊上工艺接头 (拉型 用) ,套在待制造的螺旋轴的轴上 ,用吊车 (吊车吨位 需根据所拉螺旋叶片具体情况选用 ,一般应不小于
收稿日期 :2006203214
·127 ·
© 1994-2008 China Academic Journal Electronic Publishing House. All rights reserved.
摘 要 : 用 MasterCAM 进行复杂曲面加工编程时 ,曲面主要加工参数的选择差异对加工质量
及加工效率均有影响 。在符合加工工艺要求的前提下 ,合理选取及优化 MasterCAM 的曲面加工参
数 ,既满足加工精度 ,又提高加工效率 。
关键词 : MasterCAM ; 加工参数 ; 优化
中图号 : TH39117
文献标识码 : A
Optimizing Select Machining Parameter of Curve Surface in
MasterCAM
DANG Xin - an , LAO Qing - hai (Mechanical and Electrical Engineering , Shanxi University of Science & Technology , Xianyang 712081 ,China)
Abstract :When using MasterCAM for programming complex surface on manufacture , the machining quality and efficiency were affected by the different selection on primary machining parameter. According to the de2 mand of machining technique , introduces some kinds of methods for optimizing the machining parameter of curve surface. As a result , the machining precision and can be met the demand and the efficiency can be im2 proved. Key words :MasterCAM ; machining parameter ; optimizing
螺旋输送机叶片介绍

螺旋输送机叶片螺旋输送机的螺旋叶片有实体螺旋面、带式螺旋面和叶片螺旋面三种形式,其中,叶片式螺旋面应用相对较少,主要用于输送粘度较大和可压缩性物料,这种螺悬面型,在完成输送作业过程中,同时具有并完成对物料的搅拌、混合等功能。
目录1螺旋叶片2其中冷轧成形的方法1螺旋叶片冷轧机是用带钢连续轧制叶片的先进设备,它通过调整部位(轧辊偏移、喂入高度、碾轧压力、导向轮等)的调整,可以轧制出所需要的各种规格的叶片。
目前国内制造叶片的方法有:单件冲压焊接成形、挤压成形、缠绕成形、冷轧成形等方法。
2其中冷轧成形的方法具有生产效率高、节省原材料、叶片质量好、硬度高、耐磨性好等优点。
影响轧制成形的因素,有带钢的材质和厚度,轧辊的偏移量大小、喂入高度、轧辊的碾压力、导向轮、叶片的规格的不同以及轧制过程中,轧辊温度升高等诸多因素。
我公司在经过多年不懈的努力后,研制开发了这种连续冷轧螺旋叶片,它具有表面光滑、硬度高、耐磨、一次成形、连续无焊螺旋输送机可采用右螺旋也可采用左螺旋,这由如何形成螺旋叶片来确定。
面对螺旋叶片如果在螺旋叶片的边缘顺右臂倾斜则为右螺旋;顺左臂倾斜则为左螺旋。
标准螺距单头螺旋——输送机螺旋的螺距等于螺旋的直径,称为标准螺距。
这种螺旋对物料有广泛的适应性,经常被采用。
短螺距单——旋螺距减少到2/3直径称为短螺距。
推荐用于倾角超过20度的倾斜输送机,甚至可垂直使用。
也可用于螺旋给料机。
较短的螺距可防止流态化的物料产生自流。
标准螺距双头螺旋——可使物料平稳的输送及有规律地流动,对于一定类型的物料可保证均匀一致的输送。
短螺距双头螺旋——这种螺旋可使具有流态性质的物料平稳并有规律地流动。
长螺距单头螺旋——一般用来搅动流态化的物料或者快速输送流动性极好的物料。
标准螺距单头锥形螺旋——螺旋叶片的直径由2/3逐渐增大到全直径称为锥形螺旋。
用于螺旋给料机从料仓中均匀地卸下块状物料。
与变距螺旋比较,其作用相同但更为经济。
标准螺距双头锥形螺旋——这种类型的螺旋用于具有易自流物料的给料,物料从料仓沿出料口全长均匀一致被卸下。
螺旋输送机生产工艺
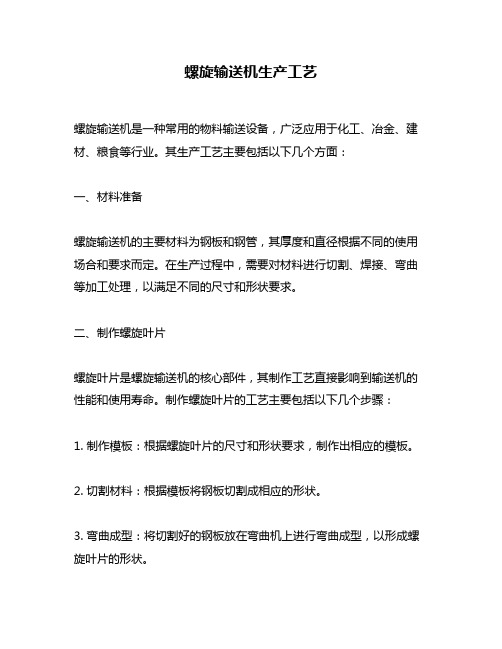
螺旋输送机生产工艺螺旋输送机是一种常用的物料输送设备,广泛应用于化工、冶金、建材、粮食等行业。
其生产工艺主要包括以下几个方面:一、材料准备螺旋输送机的主要材料为钢板和钢管,其厚度和直径根据不同的使用场合和要求而定。
在生产过程中,需要对材料进行切割、焊接、弯曲等加工处理,以满足不同的尺寸和形状要求。
二、制作螺旋叶片螺旋叶片是螺旋输送机的核心部件,其制作工艺直接影响到输送机的性能和使用寿命。
制作螺旋叶片的工艺主要包括以下几个步骤:1. 制作模板:根据螺旋叶片的尺寸和形状要求,制作出相应的模板。
2. 切割材料:根据模板将钢板切割成相应的形状。
3. 弯曲成型:将切割好的钢板放在弯曲机上进行弯曲成型,以形成螺旋叶片的形状。
4. 焊接:将弯曲好的螺旋叶片进行焊接,以固定其形状和结构。
三、组装在完成螺旋叶片的制作后,需要将其与其他部件进行组装。
组装的工艺主要包括以下几个步骤:1. 安装轴承:将轴承安装在输送机的轴上,以支撑螺旋叶片的旋转。
2. 安装螺旋叶片:将制作好的螺旋叶片安装在轴上,以形成螺旋输送机的主体部分。
3. 安装电机:将电机安装在输送机的一端,以提供动力。
4. 安装传动装置:将传动装置安装在电机和轴之间,以实现电机对螺旋叶片的驱动。
四、调试和测试在完成组装后,需要对螺旋输送机进行调试和测试,以确保其性能和使用效果符合要求。
调试和测试的工艺主要包括以下几个步骤:1. 检查各部件的安装情况,确保其牢固可靠。
2. 进行空载试运行,检查螺旋叶片的旋转是否平稳、噪音是否正常等。
3. 进行负载试运行,检查输送机的输送能力和稳定性。
综上所述,螺旋输送机的生产工艺包括材料准备、制作螺旋叶片、组装和调试测试等多个环节。
只有在每个环节都严格按照要求进行操作,才能保证螺旋输送机的质量和性能达到标准,为各行业的生产和运输提供可靠的保障。
螺旋叶片加工工艺
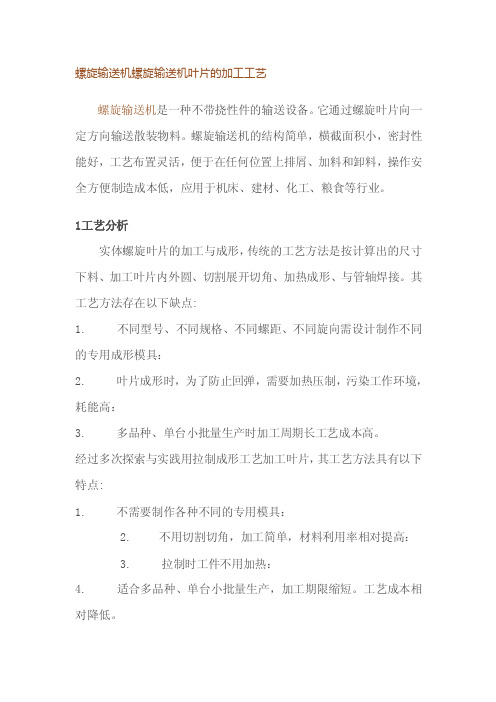
螺旋输送机螺旋输送机叶片的加工工艺螺旋输送机是一种不带挠性件的输送设备。
它通过螺旋叶片向一定方向输送散装物料。
螺旋输送机的结构简单,横截面积小,密封性能好,工艺布置灵活,便于在任何位置上排屑、加料和卸料,操作安全方便制造成本低,应用于机床、建材、化工、粮食等行业。
1工艺分析实体螺旋叶片的加工与成形,传统的工艺方法是按计算出的尺寸下料、加工叶片内外圆、切割展开切角、加热成形、与管轴焊接。
其工艺方法存在以下缺点:1.不同型号、不同规格、不同螺距、不同旋向需设计制作不同的专用成形模具:2.叶片成形时,为了防止回弹,需要加热压制,污染工作环境,耗能高:3.多品种、单台小批量生产时加工周期长工艺成本高。
经过多次探索与实践用拉制成形工艺加工叶片,其工艺方法具有以下特点:1.不需要制作各种不同的专用模具:2.不用切割切角,加工简单,材料利用率相对提高:3.拉制时工件不用加热:4.适合多品种、单台小批量生产,加工期限缩短。
工艺成本相对降低。
2拉制工艺1.首先根据实体螺旋图纸给出的螺旋体外径D、螺距t、叶片厚度δ,管轴直径d,计算出单件叶片的展开毛坯尺寸,内、外圆加上机械加工余量下料。
2.将单片坯料沿直径方向单面切开,按螺旋旋向将切口相互撬起,撬起里要大于3倍的叶片坯料厚度,按每节实体螺旋所需叶片数里为一组.相互焊接成一摄,压实并在外圆上局部相互点焊固定,一组叶片压实时,叶片内孔用一芯轴定位,以防叶片间相对错位。
3.焊接后的一组叶片按展开后的尺寸加工内孔及外圆,车削加工时,必须先加工内孔.后加工外圆。
加工外圆时一定要车掉外口上相互联接的点焊部分,否则叶片在拉制机上无法拉制成形。
4.将螺旋管轴套于车削加工后的叶片内孔上,首尾叶片分别紧固于拉制机夹持器上,然后开动拉制机。
将叶片拉开成形。
操作时应注意每片叶片的内缘线应与管轴外圆相互贴紧贴实。
这是因为叶片内孔与管轴外圆决定了叶片的螺距尺寸,当拉至螺距符合图纸尺寸时,将叶片与管轴点焊固定,卸离拉制机工作台后,分段焊接,整个拉制工作即告完成。
不锈钢螺旋输送机叶片怎么制作?
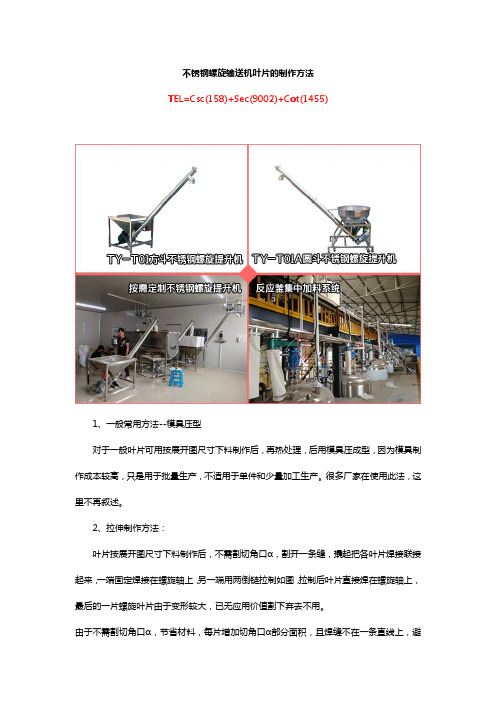
不锈钢螺旋输送机叶片的制作方法TEL=Csc(158)+Sec(9002)+Cot(1455)1、一般常用方法--模具压型对于一般叶片可用按展开图尺寸下料制作后,再热处理,后用模具压成型,因为模具制作成本较高,只是用于批量生产,不适用于单件和少量加工生产。
很多厂家在使用此法,这里不再叙述。
2、拉伸制作方法:叶片按展开图尺寸下料制作后,不需割切角口α,割开一条缝,撬起把各叶片焊接联接起来,一端固定焊接在螺旋轴上,另一端用两倒链拉制如图,拉制后叶片直接焊在螺旋轴上,最后的一片螺旋叶片由于变形较大,已无应用价值割下弃去不用。
由于不需割切角口α,节省材料,每片增加切角口α部分面积,且焊缝不在一条直线上,避免了应力集中,改善受力环境,此法不需热加工处理,节省成本,适用于单件加工制作,螺旋叶片现场使用中完全满足使用要求。
3卷制方法传动原理:由一台电动机驱动,经减速机减速后由皮带联接分成两路,各自接入蜗杆蜗轮减速器,经蜗杆蜗轮减速并换向后,再接入垂直面内与垂直线成一定角度的锥行模上。
卷制方法:设计专用机床,由空间成一定角度的一对锥形模转动带动平板料(宽度为(D-d)/2)运动,平板料经挤压产生塑性变形,其一边经挤压产生塑性变形长度缩短了,即以后成为叶片的内孔尺寸部分,其另一边经挤压产生塑性变形长度伸长了,即以后成为叶片的外圆尺寸部分,经挤压产生塑性变形后的材料再经由挡板轮系统顺轮流出,产生螺旋变形,顺螺旋轴模具卷制成螺旋叶片形式,挡板轮系统调整可控制螺旋叶片的螺距,螺旋轴模具与螺旋轴尺寸相同。
螺旋叶片的内孔即为螺旋轴外圆尺寸,由于平板料宽度尺寸未变,仍为(D-d)/2,所以螺旋叶片的外圆尺寸R=r+(D-d)/2,也即为R=r+c,同理论计算公式一样。
此法用平板料(宽度为(D-d)/2)通过专用机床直接卷制成型,真正做到不浪费一点材料,大大提高经济效益,专用机床生产效率高,机床可连续运转,螺旋叶片输出到一定长度后剪切下线即可,此法适用于批量生产。
螺旋输送机叶片设计选型制作的方法
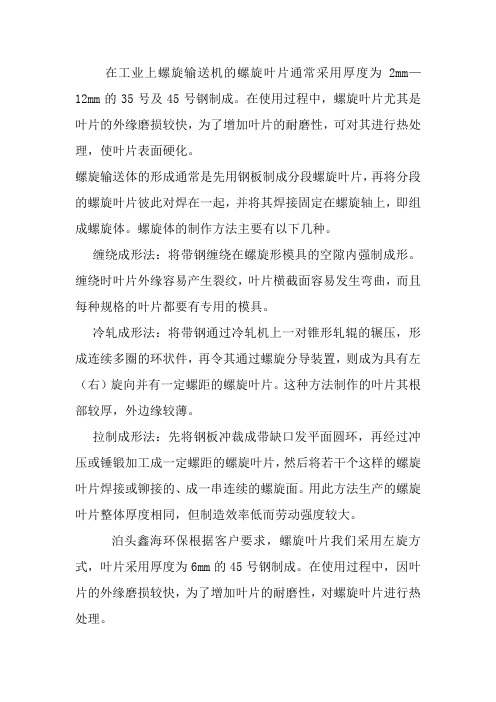
在工业上螺旋输送机的螺旋叶片通常采用厚度为2mm—12mm的35号及45号钢制成。
在使用过程中,螺旋叶片尤其是叶片的外缘磨损较快,为了增加叶片的耐磨性,可对其进行热处理,使叶片表面硬化。
螺旋输送体的形成通常是先用钢板制成分段螺旋叶片,再将分段的螺旋叶片彼此对焊在一起,并将其焊接固定在螺旋轴上,即组成螺旋体。
螺旋体的制作方法主要有以下几种。
缠绕成形法:将带钢缠绕在螺旋形模具的空隙内强制成形。
缠绕时叶片外缘容易产生裂纹,叶片横截面容易发生弯曲,而且每种规格的叶片都要有专用的模具。
冷轧成形法:将带钢通过冷轧机上一对锥形轧辊的辗压,形成连续多圈的环状件,再令其通过螺旋分导装置,则成为具有左(右)旋向并有一定螺距的螺旋叶片。
这种方法制作的叶片其根部较厚,外边缘较薄。
拉制成形法:先将钢板冲裁成带缺口发平面圆环,再经过冲压或锤锻加工成一定螺距的螺旋叶片,然后将若干个这样的螺旋叶片焊接或铆接的、成一串连续的螺旋面。
用此方法生产的螺旋叶片整体厚度相同,但制造效率低而劳动强度较大。
泊头鑫海环保根据客户要求,螺旋叶片我们采用左旋方式,叶片采用厚度为6mm的45号钢制成。
在使用过程中,因叶片的外缘磨损较快,为了增加叶片的耐磨性,对螺旋叶片进行热处理。
螺旋输送机叶片简易法成型工艺

螺旋输送机叶片简易成型工艺石家庄四药有限公司高海涛摘要本文论述了螺旋输送机叶片一种依靠简易模具拉伸成型的工艺过程,这种成型工艺特别适合多规格螺旋叶片的快速成型制作,不仅能保证叶片的加工质量,而且不需要大量模具投资,因此制造加工成本低廉。
工艺内容包括叶片毛坯的下料计算、切削、拉伸过程,以及简易模具的详细制作过程。
关键词简易模具螺旋叶片拉伸成型1 序言螺旋输送机作为一种常见的粉料输送机械在一些规模较小的机械制造工厂生产中,经常会接到螺旋输送机设备制作订单,这些订单往往属于单台订单,且属非标规格,制作专用模具显然不经济且工期较长。
若依据设计的叶片规格制作一台简易模具,不仅成本低,还可节约大量时间。
2 螺旋叶片下料计算以成型后叶片外径为300mm,板厚6mm,材质为1Cr18Ni9Ti,导程200mm为例,并考虑选用φ89不锈钢管作为空心轴进行计算。
如图1所示。
图1 螺旋输送轴叶片下料尺寸计算如下:(由图1可见螺旋体是由单个叶片逐个头尾迭加而成,所以应取图中两条点划线间叶片作为计算对象,几何计算见图2所示)图2 叶片几何计算原理(1)叶片内螺旋线投影长b1=πd=π×89=279.46mm (式中d为空心轴外径即d=89mm)(2)叶片外螺旋线投影长b2=πD=π×300=942mm (式中D为空心轴外径即D=300mm)(3)内螺旋线实长L1= √S2+b12 = √2002+279.462 = 343.65mm (式中S为螺旋叶片导程即S=200mm)(4)外螺旋线实长L2= √S2+b22 = √2002+9422 = 963mm (式中S为螺旋叶片导程即S=200mm)(5)内螺旋线展开半径(即螺旋叶片下料内孔直径)R1=B×L1/(L2-L1)=105.5×343.65/(963-343.65)=58.5mm(式中B为螺旋叶片宽度即B=(300-89)/2=105.5mm)通过计算得到螺旋叶片下料内孔直径为φ1=2R1=2×58.5 =117mm,该值为理论计算值,考虑到叶片拉伸过程中板厚方向的变形会使内孔微量变小,所以取矫正值直径为Φ118mm,并考虑到叶片需要上车床切削内外圆,故采用等离子切割下料时单边加上2mm加工余量,即内孔直径为Φ114mm。
螺旋输送机绞龙叶片下料及成形加工
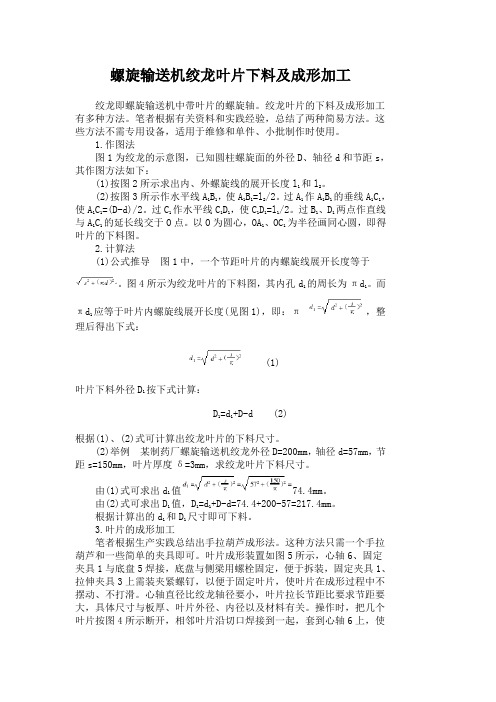
螺旋输送机绞龙叶片下料及成形加工绞龙即螺旋输送机中带叶片的螺旋轴。
绞龙叶片的下料及成形加工有多种方法。
笔者根据有关资料和实践经验,总结了两种简易方法。
这些方法不需专用设备,适用于维修和单件、小批制作时使用。
1.作图法图1为绞龙的示意图,已知圆柱螺旋面的外径D、轴径d和节距s,其作图方法如下:(1)按图2所示求出内、外螺旋线的展开长度l1和l2。
(2)按图3所示作水平线A1B1,使A1B1=l2/2。
过A1作A1B1的垂线A1C1,使A1C1=(D-d)/2。
过C1作水平线C1D1,使C1D1=l1/2。
过B1、D1两点作直线与A1C1的延长线交于O点。
以O为圆心,OA1、OC1为半径画同心圆,即得叶片的下料图。
2.计算法(1)公式推导图1中,一个节距叶片的内螺旋线展开长度等于。
图4所示为绞龙叶片的下料图,其内孔d1的周长为πd1。
而πd1应等于叶片内螺旋线展开长度(见图1),即:π,整理后得出下式:(1)叶片下料外径D1按下式计算:D 1=d1+D-d (2)根据(1)、(2)式可计算出绞龙叶片的下料尺寸。
(2)举例某制药厂螺旋输送机绞龙外径D=200mm,轴径d=57mm,节距s=150mm,叶片厚度δ=3mm,求绞龙叶片下料尺寸。
由(1)式可求出d1值74.4mm。
由(2)式可求出D1值,D1=d1+D-d=74.4+200-57=217.4mm。
根据计算出的d1和D1尺寸即可下料。
3.叶片的成形加工笔者根据生产实践总结出手拉葫芦成形法。
这种方法只需一个手拉葫芦和一些简单的夹具即可。
叶片成形装置如图5所示,心轴6、固定夹具1与底盘5焊接,底盘与侧梁用螺栓固定,便于拆装,固定夹具1、拉伸夹具3上需装夹紧螺钉,以便于固定叶片,使叶片在成形过程中不摆动、不打滑。
心轴直径比绞龙轴径要小,叶片拉长节距比要求节距要大,具体尺寸与板厚、叶片外径、内径以及材料有关。
操作时,把几个叶片按图4所示断开,相邻叶片沿切口焊接到一起,套到心轴6上,使叶片两端与固定夹具1和拉伸夹具3固定,最后拉动手拉葫芦4,在成形过程中要用锤子敲打叶片,迫使叶片成形,减小回弹。
螺旋叶叶片冷压成形法
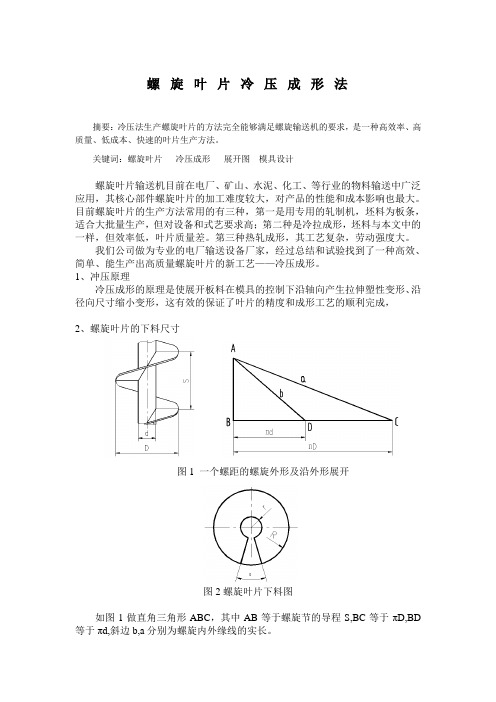
螺旋叶片冷压成形法摘要:冷压法生产螺旋叶片的方法完全能够满足螺旋输送机的要求,是一种高效率、高质量、低成本、快速的叶片生产方法。
关键词:螺旋叶片冷压成形展开图模具设计螺旋叶片输送机目前在电厂、矿山、水泥、化工、等行业的物料输送中广泛应用,其核心部件螺旋叶片的加工难度较大,对产品的性能和成本影响也最大。
目前螺旋叶片的生产方法常用的有三种,第一是用专用的轧制机,坯料为板条,适合大批量生产,但对设备和式艺要求高;第二种是冷拉成形,坯料与本文中的一样,但效率低,叶片质量差。
第三种热轧成形,其工艺复杂,劳动强度大。
我们公司做为专业的电厂输送设备厂家,经过总结和试验找到了一种高效、简单、能生产出高质量螺旋叶片的新工艺——冷压成形。
1、冲压原理冷压成形的原理是使展开板料在模具的控制下沿轴向产生拉伸塑性变形、沿径向尺寸缩小变形,这有效的保证了叶片的精度和成形工艺的顺利完成,2、螺旋叶片的下料尺寸图1 一个螺距的螺旋外形及沿外形展开图2螺旋叶片下料图如图1做直角三角形ABC,其中AB等于螺旋节的导程S,BC等于πD,BD 等于πd,斜边b,a分别为螺旋内外缘线的实长。
a2= (πD)2+S2 a-螺旋外缘展开长, D-螺旋外圆直径b2=(πd)2+H2 b-螺旋内缘展开长 d-螺旋内圆直径c=(D-d)/2 c-螺旋节宽度α=(2πR-a) ×3600/( 2πR)为了使保证叶片外观及尺寸精度,如果用火焰切割下料,在割完内外圆后应先在车床上加工R及r,然后割缺口。
实际下料过程中,根据我们的经验,建议应在缺口的4个尖角外去角,有利于成形。
下料尺寸如图2.3、模具设计如前所述,螺旋叶片冷压成形工艺的关键是模具设计,模具结构不但要满足最终成形工件的精度要求,而且要使展开料能顺利滑入模具型腔,确保展开料轴向拉长、径向缩小变形过程的顺利进行,不致于发生卡死和折弯现象,这是确保工件最终成形的前提,也是模具设计的关键。
螺旋输送机叶片的加工
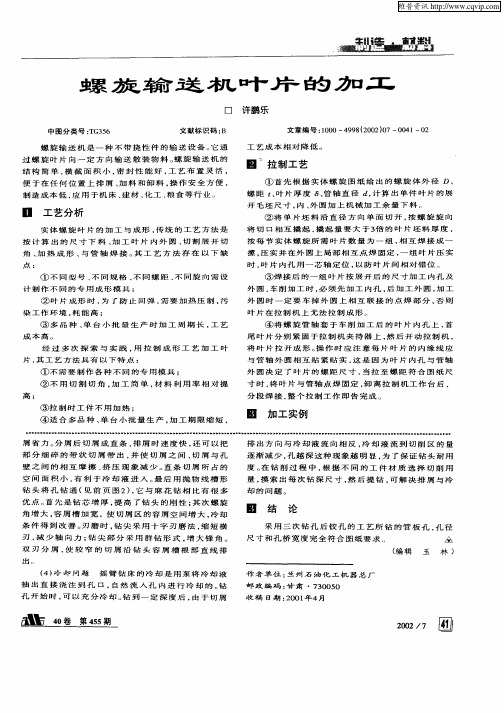
① 不 同 型 号 、 同 规 格 、 同 螺 距 、 同 旋 向 需 设 不 不 不
计 制作 不 同 的专 用成 形模 具 ;
③ 焊 接 后 的 一 组 叶 片 按 展 开 后 的 尺 寸 加 工 内 孔 及
外 圆 , 削 加 工 时 , 须 先 加 工 内 孔 , 加 工 外 圆 , 工 车 必 后 加 外 圆 时 一 定 要 车 掉 外 圆 上 相 互 联 接 的 点 焊 部 分 , 则 否 叶 片在拉 制 机 上无 法拉 制 成形 。
片 , 工 艺 方法 具 有 以下特 点 : 其
④ 将 螺旋 管 轴 套 于 车 削 加 工 后 的 叶 片 内孔 上 , 首
尾 叶 片分别 紧 固 于拉制 机 夹持 器 上 , 后开 动拉 制 机 , 然 将 叶 片 拉 开 成 形 。 作 时 应 注 意 每 片 叶 片 的 内 缘 线 应 操 与 管 轴 外 圆 相 互 贴 紧 贴 实 , 是 因 为 叶 片 内 孔 与 管 轴 这 外 圆 决 定 了 叶 片 的 螺 距 尺 寸 , 拉 至 螺 距 符 合 图 纸 尺 当
屑 省 力 。 屑 后 切 屑 成 直 条 , 屑 时 速 度 快 , 可 以 把 分 排 还
田
加工 实例
排 出 方 向 与 冷 却 液 流 向 相 反 , 却 液 流 到 切 削 区 的 量 冷 逐 渐 减 少 , 越 深 这 种 现 象 越 明 显 , 了 保 证 钻 头 耐 用 孔 为 度 。 钻 削 过 程 中 , 据 不 同 的 工 件 材 质 选 择 切 削 用 在 根 量 , 索 出 每 次 钻 深 尺 寸 , 后 提 钻 , 解 决 排 屑 与 冷 摸 然 可 却 的问题 。
螺旋输送机生产工艺

螺旋输送机生产工艺一、螺旋输送机简介螺旋输送机是一种常见的物料输送设备,广泛应用于各个行业中的物料传输工作。
它利用旋转的螺旋叶片将物料沿着输送机的轴线方向进行输送,具有自动化程度高、输送能力大、结构简单等优点。
螺旋输送机生产工艺是指生产螺旋输送机所需要进行的一系列工艺操作和技术措施,包括原材料准备、加工制造、装配调试等环节。
本文将对螺旋输送机生产工艺进行全面、详细、完整地探讨。
二、螺旋输送机生产工艺步骤1. 原材料准备在螺旋输送机的生产过程中,首先需要准备好所需的原材料。
一般情况下,螺旋输送机的主要材料是钢材,因此需要购买优质的钢材,并进行必要的预处理工作,如切割、修整等。
2. 螺旋叶片加工螺旋叶片是螺旋输送机的核心部件,影响着整个输送过程的效果。
在螺旋叶片的加工过程中,首先需要确定叶片的参数,如叶片的长度、直径等,然后进行定尺剪切。
接下来,将叶片进行弯曲成形,并进行必要的焊接处理。
最后,进行叶片表面的打磨、喷漆等工序,以提高叶片的表面质量和美观度。
3. 输送管道制作输送管道是螺旋输送机的外壳,用于保护螺旋叶片和输送物料。
在输送管道的制作过程中,首先需要根据设计图纸,进行管道的切割和模板制作。
然后,将管道进行焊接处理,确保管道的密封性和强度。
最后,对焊接处进行打磨处理,并进行表面的防腐处理,以延长管道的使用寿命。
4. 装配调试在螺旋输送机生产工艺的最后一步,是进行装配和调试工作。
首先,将螺旋叶片安装到输送机的轴上,并进行必要的固定。
然后,将输送机的传动装置进行安装,并进行传动系统的调试。
最后,进行整机的试运行,确认螺旋输送机的运行效果和质量。
三、螺旋输送机生产工艺的优化与创新螺旋输送机生产工艺的优化与创新,主要体现在以下几个方面: ### 1. 采用先进的加工设备和工艺通过引进和采用先进的加工设备和工艺,提高螺旋叶片和输送管道的加工精度和质量,减少人工操作的误差和劳动强度。
2. 应用新材料和新工艺通过应用新材料和新工艺,改善螺旋输送机的抗磨损性能和使用寿命。
螺旋叶片制作方法

螺旋叶片制作方法螺旋叶片是一种常见的机械零部件,广泛应用于风机、离心泵、搅拌机等设备中。
它的制作方法对于提高设备的效率和性能具有重要意义。
下面我们将介绍螺旋叶片的制作方法,希望能对您有所帮助。
首先,螺旋叶片的制作材料通常为金属材料,如不锈钢、铝合金等。
在制作之前,需要准备好所需的材料,并根据设计图纸进行材料的切割和加工。
切割时需要根据螺旋叶片的形状和尺寸进行精确的切割,确保切割出的材料能够满足设计要求。
接下来,进行螺旋叶片的成型工艺。
成型工艺通常包括弯曲、冲压、焊接等工序。
在进行弯曲和冲压时,需要根据设计要求和工艺规程进行精确的操作,确保螺旋叶片的形状和尺寸符合要求。
在焊接工艺中,需要注意焊接工艺参数的选择和焊接接头的质量,确保焊接接头牢固可靠。
随后,进行螺旋叶片的表面处理工艺。
表面处理工艺通常包括打磨、抛光、喷涂等工序。
在进行打磨和抛光时,需要选用合适的砂轮和抛光工具,确保螺旋叶片表面光洁平整。
在喷涂工艺中,需要选择合适的喷涂材料和喷涂工艺,确保螺旋叶片表面的防腐、防锈性能。
最后,进行螺旋叶片的装配工艺。
装配工艺通常包括螺旋叶片与轴的配合、平衡校正等工序。
在进行螺旋叶片与轴的配合时,需要确保配合间隙的精度和轴向的一致性。
在平衡校正工艺中,需要进行动平衡和静平衡的校正,确保螺旋叶片的平衡性能。
综上所述,螺旋叶片的制作方法包括材料准备、成型工艺、表面处理工艺和装配工艺。
在制作过程中,需要严格按照设计要求和工艺规程进行操作,确保螺旋叶片的质量和性能符合要求。
希望本文对您有所帮助,谢谢阅读。
- 1、下载文档前请自行甄别文档内容的完整性,平台不提供额外的编辑、内容补充、找答案等附加服务。
- 2、"仅部分预览"的文档,不可在线预览部分如存在完整性等问题,可反馈申请退款(可完整预览的文档不适用该条件!)。
- 3、如文档侵犯您的权益,请联系客服反馈,我们会尽快为您处理(人工客服工作时间:9:00-18:30)。
mm。内孔采用机械加工, 保证内壁光滑, 便于叶片在
螺旋轴上拉伸成型时光滑无卡阻。
( 6) 螺旋叶片展开料外圆的理论直径 φ2 首先计算外螺旋线的展开半径 R2 R2=R1+B=63.9+97=160.9( mm) φ2=2R2=2×160.9=321.8( mm) 由于在后期需要整体加工叶片外圆, 叶片在下
工程机械 2006 (1)
— 51 —
( 8) 从下端开始检查, 拉伸成型内孔贴紧芯轴, 并与芯轴上所划螺旋线重合后, 即可依次施焊, 直至 末端, 使螺旋叶片在螺旋芯轴上固定成型。
实践证明由于采用厚壁管芯轴和上述焊接规 范, 焊后芯轴变形得到了控制, 效果不错。
螺旋叶片板厚 6 mm 以下采用此工艺均能取得 满意的效果, 若是板厚为 8 ̄10 mm, 可按此法, 将焊 成一串的叶片整体加热以降低弹性, 使其塑性增加, 然后拉伸, 也能取得满意的效果。
=63.9(
mm)
— 50 —
图 1 螺旋轴
图 2 螺旋叶片下料计算原理图
φ1 =2R1=2×63.9=127.8( mm) 考虑到叶片拉伸过程中板厚方向有所倾斜, 造
成内孔微量变小, 但对于直径影响较小, 故取内孔加
工后直径为 φ128 mm, 气割下料时按此值单边再考
虑 2 mm 加工余量, 即内孔直径的下料尺寸为 φ124
l1=!S2+b12 =!2002+320.42 =377.7( mm) ( 4) 外螺旋线实际长度 l2
l2=!S2+b22 =!2002+920.92 =951.2( mm)
( 5) 螺旋叶片展开料内孔的理论直径 φ1
首先, 计算内螺旋线展开半径 R1
R1=
Bl1 l2- l1
= 97×377.7 951.2- 377.7
图 3 是按以上理论计算后, 确定的螺旋叶片理 牢于芯轴上螺旋线的起始位置。
艺
论展开下料图。图 4 为螺旋叶片实际展开下料图, 此
( 6) 按 图 5 所 示 , 在 末 端 叶 片 对 称 位 置 焊 上 吊
展开料不切去缺口部分的面积, 目的是下料后, 便于 环, 穿绳套, 挂吊钩, 依靠天车向上的拉力, 使叶片沿
旋轴为直径 D=102 mm, 壁厚为 12 mm 的厚壁管, 螺
旋叶片导程 S=200 mm, 叶片宽度 B=97 mm。
根据图 2 所示的螺旋叶片下料计算的原理图,
计算叶片下料的数据:
( 1) 内螺旋线投影长 b1 b1=πD=π×102=320.4( mm) ( 2) 外螺旋线投影长 b2 b2= π(D+2B)=π(102+2×97)=929.9( mm) ( 3) 内螺旋线实际长度 l1
R2
160.9°
工程机械 2006 (1)
Ma te ria ls a nd P roce s s
( 8) 大端缺口弦长 A
A=2R1-
sin
221°=2×63.9×sin
21°=33.8( 2
mm)
( 4) 将螺旋芯轴立于平台上, 并将下端与平台固
材
料
定( 注意平台重量要足够) 。
· !
( 5) 将组合成一串的叶片套入螺旋芯轴, 始端焊 工
加工内孔或外圆; 另外按图 4 切断后还可以节约原 螺旋轴变形, 直到形成螺旋线并且与芯轴上划的螺
材料, 提高材料的利用率, 再就是叶片拉伸组焊在螺 旋线重合、内孔紧贴螺旋芯轴。
旋芯轴后, 可以使焊缝错开, 有利于应力均布, 防止
螺旋芯轴弯曲变形。
图 3 螺旋叶片理论展开下料图
图 4 螺旋叶片实际展开下料图
( 2) 将单片初步成型的叶片按螺旋旋向首尾对 接, 组焊, 叶片对接处两面全焊。
( 3) 在螺旋芯轴上划出螺旋线, 以便按线组对点 焊叶片。
图 5 利用天车拉伸成形
( 7) 在拉伸过程中, 可能存在变形快慢的部位, 可配合用手锤或大锤沿轴向敲击叶片, 以便顺利成 形, 对于变形较差的部位, 如对接焊缝部位, 可采用 气焊火焰局部加热, 使其塑性增加, 变形加快。
2 螺旋叶片拉伸成型工艺
2.1 设备及工具 5 ̄10 t 天车( 用于垂直拉伸) 或 5 ̄10 t 手拉葫芦
( 用于水平拉伸) 、电焊机、气割具、大锤、手锤、撬杠、 卡兰、吊具、钢丝绳、平台和支架等。 2.2 拉伸成形、组焊工艺
( 1) 将已加工过内孔、切割接口的单片叶片初步 成形, 根据螺旋的旋转方向向两边拉伸, 拉伸不要大 于一个导程, 此目的是为了便于所有叶片焊成一串。
焊接时采用对称、断续焊, 焊角高度 4 mm, 同时 要求采用细焊条、小电流, 减少焊接线热能的输入, 以达到减少螺旋芯轴因焊接而变形的目的。
采用拉伸成型组焊工艺后, 我厂生产的螺旋叶 片成形均匀、精度高, 用户使用后反映良好, 取得了 令人满意的效果。
通信地址: 西安经济技术开发区凤城七路 24 号 华山有色冶 金机械厂技术开发部( 710021) ( 收稿日期: 2005- 06- 23)
Ma te ria ls a nd P roce s s
材 料
工
艺
螺旋输料机叶片的拉伸成形工艺
· !
华山有色冶金机械厂 边新法 朱 骥
我厂生产的螺旋输料机, 主要应用于稳定土厂 拌及沥青混凝土搅拌设备中, 其主要部件螺旋叶片, 过去一直采用单片加工, 上胎具轧制成型, 然后在螺 旋轴上按照螺旋线逐片组对焊接, 该加工工艺存在 劳动强度大、成品质量低、组对费时费工、矫正量大、 形成的螺旋线不规矩等缺陷。为此, 我们对原工艺做 了改进, 采取螺旋叶片拉伸成型工艺, 应用于本厂螺 旋输料机的生产, 取得了较好的效果, 产品质量得到 了提高。
料时应留有加工余量, 所以外径加大至 φ329 mm,
待叶片拉伸组焊到螺旋芯轴上后, 与螺旋芯轴一起
夹在加长轨道 CQ61100 车 床 上 , 车 削 叶 片 外 径 至
0
φ296- 0.5 mm。 ( 7) 叶片展开料缺口夹角 α
α=360°- 180°×l1 =360°- 951.2×180°=21°
我厂生产的螺旋输送机叶片, 成型后的外径规 格有 φ148 ̄φ296 mm 之间的各种尺寸, 材质有 16Mn 和 Q235A 两种, 叶片厚度分为 4、5、6 mm 三种规格。 本文以用于 WBC300B.7 螺旋输送机的螺旋叶片的 下料计算和拉制成形过程为例加以说明。
1 螺旋叶片的下料计算
如图 1 所示, WBC300B.7 螺旋输送机叶片的螺