IE工业工程训练之生产线平衡.pptx
产线平衡与产能计算-IE-工业工程课件

五.产能计算
前面的线平衡资料准备齐全后,我们就可 以计算机种的产能.
1.确定瓶颈工序
2.计算时产能
时产能=3600/瓶颈时间
3.人均时产能计算 人均时产能=时产能/标准作业人数
4.日产能计算 日产能=时产能×一天的工作时间
例:12B7490020机种产能计算
准备数据: 12B7490020-FC中有标准作业人数以及标准 工时。
产线平衡与产能计算
制作:XX 2010/8/10
目录
一.何为线平衡(Line Balancing) 二.线 平 衡 名 词 解 释 三.线 平 衡 率 计 算 四.线 平 衡 方 法 五.产能计算
一.何为线平衡(Line Balancing)
Line balancing即是对生产的全部工序进 行平均化,调整作业负荷,以使各作业时 间尽可能相近的技术手段与方法,是生产 流程设计及作业标准化中最重要的方法。
1.马表法
标准工时=量测工时*宽放率*评比系数
量测工时是用马表直接测出的时间 宽放率和评比系数详见附档
正常速度相当于在不负重的条件下,以68cm左右 的步长和每小时4.8公里的速度,在平坦的道路上 行走的情况;或者相当于用30秒钟把一付52张扑 克牌,逐张摆在一个正方形的四个角上.
2.另一种标准工时的计算方法是预定标准工时法(模特法),此处不 再详细介绍
1.人员方面 1-1. 瓶颈站应由效率较佳或训练较久之人 员担任并有效运用有经验的作业者; 1-2. 将流水线上的NG品移走,以离线作业处理; 1-3. 消除重复性之作业;(如多次的检查,可适当减
少次数)
四.线 平 衡 方 法
1-4. 第一站工作及新手避免工作负荷过重; 1-5. 建立候补人员制度;(如领班和领班助理) 1-6. 鼓励有经验者的老员工从事瓶颈站的
IE生产线平衡的资料PPT资料37页

上例中,若换线时间是15分钟,则计划停线工时为20人 *15min=300min=5H,则投入工时和稼动率为:
60H-5H=55H 稼动率=55H/60H=92%
2019/10/22
时间测试
分解动作时间量测,一般每个动作测量5 次为宜; 量测人员应站在作业员斜后面1米以外, 以能看清楚全部操作动作为准则; 测试中不能打扰作业员的正常操作和引 起作业员的紧张;
时间测量流程
作业内容
数据与信息记录
测试中判断作业员的速度水平,并作如 实记录,不可修改量测数据; 若有其他特殊情況,也应加以实录;
2019/10/22
6
相关的概念
概念6:平衡损失 平衡损失=(总工时-单件标准时间)*设定产能
时间
T1 T2 T3 T4 T5
等待时间
单个产品平衡损失 =等待时间之和
S1 S2 S3 S4 S5
工站
概念7:平衡率100%代表﹕ 1.工站之间无等待,前后产能一致﹔ 2.工站节拍相同,动作量相同(动作量是指工站中各种必要动
素的时间总量); 3.平衡损失时间为零; 4.设计效率最大化; 5.前后流程的设计可以更完善(如下图).
2019/10/22
7
相关的概念
(交叉流程)
(直通流程 1 ) (直通流程 2 )
概念8:高效率 1. 通常认为高效率就是:快速,简单&大规模 2. 我们认为沒有浪费的时候才是高效率的 操作效率=实际产量/设定产能*100% 整体工厂效率(OPE)=平衡率*稼动率*操作效率
现代工业工程(IE)技术PPT

工业工程师的素养
Zhaoqing Kidstar Manufatory Co.,Ltd.
什么是工业工程?
Industrial Engineering IE
• 工业工程是对人员、物料、设备、能源和信息所 组成的集成系统, 进行设计、改善和设置的一 门学科。 • 综合运用数学、物理学、社会科学的专门知识、 技术以及工程分析与设计的原理、方法,对由人、 物料、设备、能源、信息组成的集成系统,进行 规划、设计、评价、改进(创新)的一门学科。 • Improve Efficiency 改善效率。
程序分析的特点:生产过程的宏观分析。
程序分析包含:工艺程序分析、流程程序分析、布置和
路径程序分析。
Zhaoqing Kidstar Manufatory Co.,Ltd.
程序分析符号
工序要素
加工 搬运 检查 等待
记 号
说 明
表示材料形状、功能发生变化,装配等。 材料、产品或人员的位置变化。 质量或数量检查。 材料或人员计划外的停滞状态。
Zhaoqing Kidstar Manufatory Co.,Ltd.
□ ▽
检验
等候 持住
第四讲:IE方法研究之动作研究
• 动作分析的含义和目的 • 动作经济性十大原则
Zhaoqing Kidstar Manufatory Co.,Ltd.
动作分析
动作分析:以动作为对象进行的分析,去掉多余动作,降低动 作等级,把必要的动作组合成标准动作系列,以开 发合理、高效的工作方法。
共同工作
单独工作
空闲
人机协作图标
Zhaoqing Kidstar Manufatory Co.,Ltd.
人机操作分析图的构成
IE生产线平衡资料课件
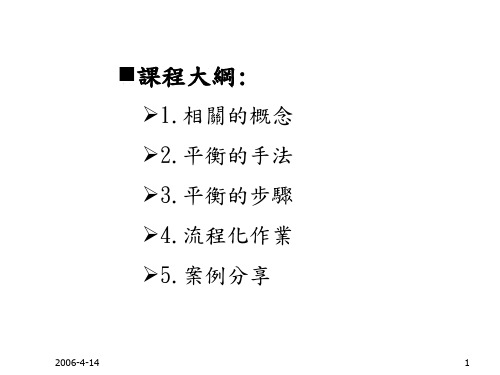
Steps 7: 改善總結報告: 平衡率 設定產能﹑實際產能﹑人均產能(單機產能) 損失分析 品質分析 成本改善率 Steps 8: 標準化
流程化作業
1. 平衡率目標:與大設備相連≧85% 其他≧ 95%
2. 平衡改善小組的職責:
生產單位:改善前/后之工時測量,山積表制作﹑分析及改善方案之實施.制工單位:協助生產單位擬定及推動改善方案,跟蹤方案效果評估及各種相關文件修訂及系統表單發行﹔品管單位:負責改善前/后產品品質評估﹔工務單位:主導及其它改善事項協助﹐設備改善﹔ IE﹑經管﹑企划:改善前后產線效益評估及跟進.
平衡的步驟
S1標准時間為﹕t2+t3; S1工站時間為﹕t4
S1-2
S1-1
當S1-1不需等S1-2就能開始, S1工站時間為﹕ T3+S1-1提前開始的時間(t4-t3)
S1工站時間=?
?
Steps 5: 建立新的模擬流程 新的FLOW CHART/ SOP (SWR發行)Steps 6: 實施新的模擬流程 改善后時間測量 改善后山積表制作
程序分析使用的圖表: 工藝程序圖 / 流程程序圖/ 路線圖程序分析符號--表示操作--表示搬運/運輸--表示檢驗--表示暫存或等待--表示受控的貯存 --派生符號,由上面的符號合成.
程序改善
例: 流程程序圖
程序分析技巧通過5W1H系統地分析程序的組成是否合理和必要“ECRS”四大原則: 取消(Eliminate); “完成了什么?是否必要?為什么?” 合並(Combine); “誰完成?何時完成?哪里?如何?” 重排(Rearrange); 取消合並重排 簡化(Simplify); 確認必要簡單方法/設備生產.五大內容: 工藝流程分析—取消/合並/重排工序,減少浪費 搬運分析—考量重量、距離、方法、工具、路線 檢驗分析—按產品要求設計合理站點和方法 貯存分析—使物料及時供應 等待分析—減少和消除引起等待的因素
基础工业工程 生产线平衡 课件

工业工程基础(C512)第一章概述工业工程(Industrial Engineering,IE)。
其基本思想是提高效率,如何以尽可能少的投入得到尽可能大的产出是工业工程的核心。
制造业是最主要和最有代表性的一个领域。
80年代以前,制造业关心的问题是设计和加工的基本问题,即解决如何做的问题;90年代制造业则主要关心引入CAD/CAM等技术,提高设计和加工水平,从而提高产品质量,即解决如何做的好的问题;而在CAD/CAM技术已经成熟的新世纪,企业主要关心的是如何高质量,高效率,高速度地完成生产任务,使企业在市场竞争中立于不败之地,即解决如何以最低的成本做得好、同时又做得快的问题。
这就要靠工业工程等技术来完成。
涉及到以下方面:1.工业工程基础(工作研究)。
2.设施规划与设计。
3.生产计划与控制。
4.工程经济与价值工程。
5.质量管理与可靠性技术。
6.工效学。
研究生产系统中人、机器和环境之间的相互作用。
7.人力资源开发和管理。
研究如何有效地使用人力资源和提高劳动力的素质。
8.管理信息系统。
9.现代制造系统。
主要内容包括:a)数控技术(CNC)。
b)成组技术(GT)。
c)计算机辅助设计与制造(CAD/CAM)。
d)计算机辅助工艺设计(CAPP)。
e)柔性制造单元和系统(FMC、FMS)。
f)计算机集成制造(CIM).第二章方法研究第一节工作研究一、概念工作研究是以系统为对象,通过对生产组织、劳动分工、工装设计、操作方法、工作环境等因素的综合分析与改进,使人、机、物、时间、空间、环境等受到有效地控制和充分利用,从而保证工作质量,使整个系统处于受控状态,以达到降低消耗、提高生产效率和竞争力的目的。
工作研究包括:1.方法研究。
对现有的和拟议的工作方法进行系统和严格的考查,开发出更简单易行和有效的工作方法。
其指导思想是求新和整体优化。
2.作业测定。
提供一种方法,用以衡量完成某项操作或者一系列操作所需的时间。
方法研究关心的是改进工作方法以减少作业的工作量。
IE生产线平衡资料PPT课件
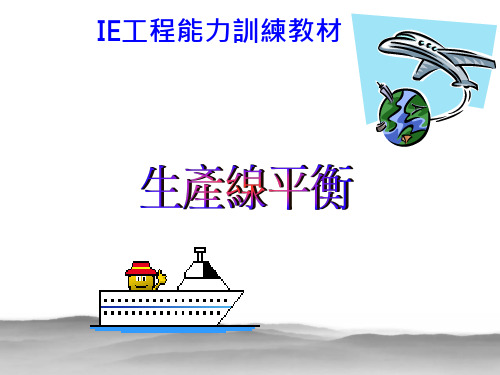
23.11.2020
16
例: 流程程序圖
材料仓库
2 AI、 SMT加 工 1 前加工
3 手插件 4 锡炉 5 剪脚 6 修 整 (正 背 面 )
7 折分基板 8 ICT测 试
8 穿 焊 OPC(PSC) 9 锡 面 /正 面 检 查 10 中 间 检 查 11 组 装 CASE 12 溶 着 /锁 螺 丝 13 电 测 检 查 14 包 装 15 OQC检 查
2
2
0
12 0.5
1.8 1
1.5
10
10
2 2.5 5 2
5
3
1 0.5
4
2 1.5
0.5 1 1
0
0 2
0.5 1
2
10 2
12
2 1.5 6.5 4
2 2.5
1
M5 M4 M3 M2 M1
S1 S2 S3 S4 S5 S6 S7 S8 S9 S10 S11 S12 S13 S14 S15 S16 工站
数据整理和计算
测试完毕,对数据进行整理和计算,补充 测量有怀疑或错漏的数据; ❖ 计算可信度95%所需的样本数量,补测差 异样本数量.
资料分析与处理
对量测记录之所有资料进行分析,对比 ST的差异程度,解决发现的问题; ❖ 若分析发现标准时间制定不当,应及时 修改,必要时调整制程.
工时测量的作用﹕ n 获取各工站的实际操作时间,为山积表制作,时间平衡作准备; n 通过时间观测,分析作业价值,发现问题和改善空间; n 形成标准,比较实际差异,找出问题;
用语衡量流程中各工站节拍符合度的一個综
合比值;
单件标准时间
平衡率= ----------------------100%
IE工业工程训练之生产线平衡

數據整理和計算
測試完畢,對數據進行整理和計算,補充測量有懷疑 或錯漏的數據; ❖ 計算可信度95%所需的樣本數量,補測差異樣本數量
資料分析與處理
對量測記錄之所有資料進行分析,對比ST的差異程 度,解決發現的問題; ❖ 若分析發現標準時間制定不當,應及時修改,必要時 調整制程.
工時測量的作用﹕
❖ 獲取各工站的實際操作時間﹐為山積表制作﹐時間平 衡作准備﹔
(直通流程 2 )
相關的概念
概念9:改善
I. 同樣的投入更大的輸出; II. 不增值(無效)增值(有效)
?不增值? 等待 不良 庫存 移動 ……
例1: 減少移動與庫存提高效率 例2: 減少無效動作提高效率
概念10:多能工
平衡的手法
工時測量 山積表 程序改善 損失分析 作業條件改善 打破平衡
3.平衡損失時間為零
4.設計效率最大化
5.前后流程的設計可以更完善(如下圖)
相關的概念
(交叉流程)
(直通流程 1 )
概念8:高效率 1. 通常認為高效率就是:快速,簡單&大規模 2. 我們認為沒有浪費的時候才是高效率的 操作效率=實際產量/設定產能*100% 整體工廠效率(OPE)=平衡率*稼動率*操作效率
燥劑放入箱內
13 封裝及貼出廠標簽
搬運到暫存區 暫存等待出貨
程序改善
❖ 程序分析技巧
1. 通過5W1H系統地分析程序的組成是否合理和必要
2. “ECRS”四大原則:
3.
取消(Eliminate); “完成了什么?是否必要?為什
么?”
❖ 合並(Combine); “誰完成?何時完成?哪里?如何?”
IE工业工程训练之生产线平衡
課程大綱:
生产线平衡方法.pptx

传统效率衡量方 式只计算了部分
时间损失
总时间损失
六种重大OEE损失类型 OEE时间损失分为6大类
质量缺陷
计划外停 机
机器故障
速度下降
换线
损坏
OEE计算 – 模型
六种重大损失降低机器效能说明
设备时间
设备损失
设备最大可用工时
可使用总工时
时间稼动
SD损失
性能稼动 速度损失 价值稼动
• 14、Thank you very much for taking me with you on that splendid outing to London. It was the first time that I had seen the Tower or any of the other fam ous sights. If I'd gone alone, I couldn't have seen nearly as much, because I wouldn't have known my way about.
Station 2: G:11.3-11.3=0 Total time=11.3
Station 5: N:11.3-10.7=0.6 Total time=10.7
Station 3: C:11.3-2.1=9.2 D:9.2-2.5=6.7 E:6.7-1.8=4.9 F:4.9-1.8=3.1 H:3.1-2.1=1 Total time=10.3
6. 设定产能 标准产能
实际产能
1:TT & CT
1.Tact time=Cycle time的计算:
B
①A
班长IE专训课程-生产线平衡
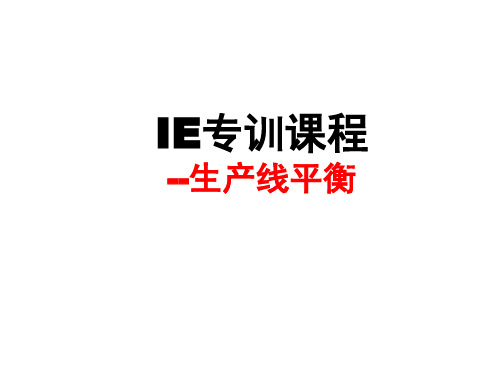
--Henry.福特《福特理想》
二.线平衡相关概念
2.2.流水线基本特征
1) 固定生产一种或少数几种产品
2) 工作中心专业化程度高
3) 按节拍生产
表示
4) 生产能力保持平衡 常数
t1 = t2 =a = tm
三.线平衡改善
3.3.作业方法改善技术
5W2H提问技术
(包括:5why提问,通过5W2H系统地分析程序的组成是否 合理和必要)
ECRS四大原则
取消(Eliminate); “完成了什么?是否必要?为什么?” 合並(Combine);“谁完成?何时完成?哪里?如何?” 重排(Rearrange);取消合并重排 简化(Simplify);确认必要简单方法/设備生产.
平衡率﹕70% 打破平衡﹐打开了可平衡局面
瓶颈未变的情况下,平衡率短期内下降是 好事。
三.线平衡改善
3.7.总结及标准化
改善总结报告: 平衡率 设定产能﹑实际产能﹑人均产能(单机
产能) 损失分析 质量分析 成本改善率
标准化: 按照改善后的要求制作相应SOP等标准文件
下步工作:
IE专训课程
--生产线平衡
大纲
一、生产线介绍
二、线平衡相关概念
三、线平衡改善
一.生产线介绍
SMT 成型
装配
涂装 冲压
二.线平衡相关概念
2.1.流水线起源
1863:出生于美国密歇根州的农庄(父母为爱尔兰移民);12 岁自己的机械坊;15岁制造第一台内燃机 1879:底特律做机械学徒,后进入西屋电气公司 1891:爱迪生照明公司工程师,2年后任主工程师 1896:第一辆汽车“四轮车” 1896-1901:制造赛车 1903:福特汽车公司 “福特999” 1908:T型车,到1927生产1500万辆(后45年内世界记录) 员工分享、投资橡胶、研究塑料、转车型、转营销 流水线之父--亨利·福特 1945年退位 (Henry Ford,1863-1947) 1947:逝世于故乡,83岁
IE手法生产线平衡ppt课件
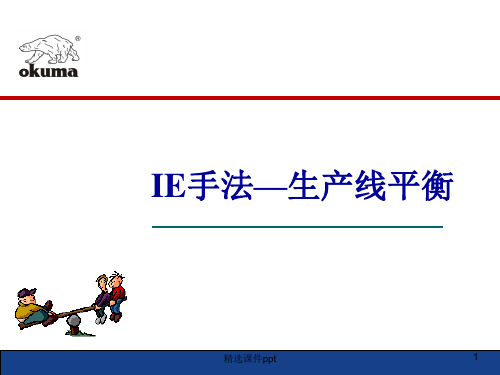
作 业 时 间
工序 1 2 3 4 5
2、合并作业 省略工序
精选课件ppt
1人
作
业
2人
时
间
工序 1 2 3 4 5
3、减人
34
提高平衡率的四大手法
符号 名 称
内容
E
取 消 任何无价值的可作以业不,做如吗?搬运等,
Eliminate 予以取消 如果不做会变如何?
C
合 并 对可于以把无两法个取以消上而的又工程必结要合者在,一看起是吗否?
了解﹐如出现不平衡的状态时﹐习惯用人员增补来 弥补﹐这是一个不动脑筋的做法﹐不足为取。
除了上面介绍的技法以外﹐也可以对材料﹑零件包
括设计方法来检讨﹐有否缩短工时的方法。
生产线补进新手时﹐因新手对工作不熟悉﹐熟练不
足。在配置上尤其要注意﹐会造成很大的不平衡使 产量大幅度下降﹐或对新手造成异常的工作压力。
IE手法—生产线平衡
精选课件ppt
1
精选课件ppt
2
生产线中的问题点
WIP(在制品) 生产周期长 各种浪费多(等待、动作、搬运…) ……
精选课件ppt
3
产生这些问题的主要原因
生产线中各工序时间不均衡
精选课件ppt
4
生产平衡的两个基本概念
瓶颈
标准工时
精选课件ppt
5
什么是瓶颈?
瓶颈是企业在 实现其目标的过 程中现存的或潜
如生产在线的各个工序都能互相配合无间﹐我 们称之谓生产线平衡﹐而这生产线定能获得一 定的效益;
但如各工序间不能相互配合﹐拥有不少等候的 时间﹐这情况我们则称之谓生产线不平衡。
精选课件ppt
15
影响的因素
IE基础知识培训生产线平衡分析.pptx

3/38
生产线平衡的优点
1. 平均分配各作業員的工作負荷 2. 找出瓶頸作業項目 3. 建立裝配線的標準速度 4. 決定工位的數目 5. 決定裝配以及包裝的人工成本 6. 決定每項作業項目佔總工作量的百分比 7. 幫助工廠佈置的工作 8. 降低生產成本
1/38
IE 基 础 知 识 培 训
---生产线平衡分析
2/38
生产线平衡的定义
依照流動生產的工程順序 ,從生產目標算出週期時間 ,將作業分割或結合,使各工作站的負荷均勻,提高生產效 率的技法,稱之生产线平衡。
生产线平衡的目的
生产线平衡的目的是通过平衡生产线使现场更加容易理解 “一个流”的必要性及生产作业控制的方法。
11/38
使用标准时间的优点
1 客观分析动作,不受产品性质,作业性质等影响.避免了对 操作者熟练程度,工作状态等的判断及对ST的影响.
2 避免了以往经验数据和停表法的人为因素对ST影响,提高 产能评估精度.
3 能发现操作人员的无效动作和浪费现象,可使操作者,操作 对象,工具三者合理地布置和安排.简化操作方法,删除无 效动作.
4 合理调配工位,提高平衡率
提高效率.
5 利用绩效管理,评估操作的工作表现.
6 增强分析者和操作者的信心.
12/38
标准时间的建立
1 专业时间分析法有:胶卷分析法;跑表法;PTS 法;WF法;MTM法等等.现在SONY工司将以上法 则综合起来,业内人士称为MOST法.但此法则 没有世界认证和论文出版,这里也不做详细解 释.
精选IE工业工程生产线平衡课件
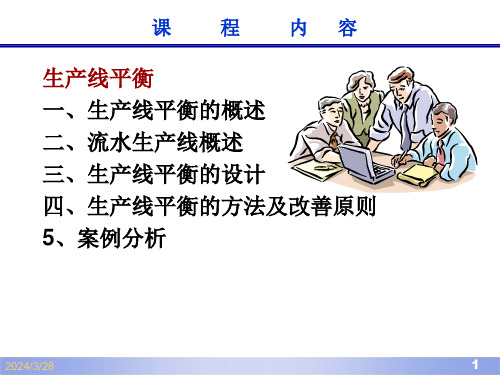
三、流水生产线平衡的设计方法
● 进行产品和零件的分类● 改进产品和零件的结构,使之适合流水生产● 审查和修改工艺规程● 收集整理设计工作所需要的资料
2、 流水线平衡设计的准备工作
三、流水生产线平衡的设计方法
G
7
E
H
11
E
I
3
G、H
总时间
66
解:
阶位法的工作步骤如下
① 作图表示装配工艺过程中各作业元素的先后关系,并标明每项作业元素的时间。 ② 从作业元素先后关系图找出每项作业元素的后续作业元素,计算它们的时间总和,即每项作业元素的阶位值。 ③ 按阶位值的大小,由大到小,将作业元素排队,制成作业元素阶位表。 ④ 从阶位值最高的作业元素开始,向工作地分配作业要素。每分配一项作业元素,计算一次在节拍时间内的剩余时间。若剩余时间足够安排另一项作业元素,从阶位表中找出阶位值次高的作业元素分给该工作地。若剩余时间不够安排其它作业元素,就向下一个工作地分配,直到全部作业要素都被安排入工作地为止。
3、 单品种流水线平衡方法
②平衡图分析
②平衡图分析---改善案例:
③生产线平衡率的计算:
衡量生产线平衡的好坏,可以用生产线平衡率或平衡损失率来进行定量衡量。在计算生产线平衡率或平衡损失率前,必须先设定计算的时间基准,即生产周期。如案例2-1,可以发现决定生产线的作业时间周期的工序时间是最长工序的时间(Pitch Time),也就是说Pitch Time(节拍时间)等于周期时间 (Ct)(注:在完成各工序后,每隔Pitch Time完成一个或批产品)另外一种计算方法同样可以得到Cycle Time,即由以每小时平均成品产量,求得一个产品的Ct
生产线平衡 ppt课件
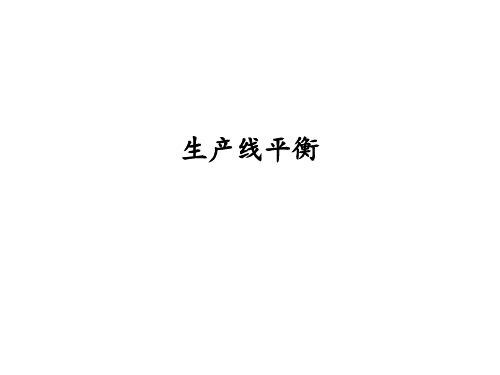
时间 t4 t3 t2
S1标准时间为﹕t2+t3;S1 工站时间为﹕t4
t1
S1-1 S1-2 S1-1 S1-2 S1-1 S1-2
当S1-1不需等S1-2就 能开始,S1工站时间 为﹕S1-2的时间
工站
25
Steps4:山积表平衡
(6) 联合操作的工站时间(S1-1>S1-2)
时间 t4 t3 t2
S1标准时间為 ﹕t2+t3;S1工站时间 为﹕t4
t1 S1-1 S1-2 S1-1 S1-2
工站
26
Steps4:山积表平衡
S1工站时间=?
(6) 联合操作的工站时间(S1-1>S1-2)
?
时间 t4 t3 t2
t1
S1-1 S1-2 S1-1 S1-2
工站
27
Steps 5:建立新的流程
新的FLOW CHART/ SOP
出料
入料
定义:生产线平衡即是对生产的全部工序进行平均化,调整作业负
荷,以使各作业时间尽可能相近的技术手段与方法。目的是消除作
业间不平衡的效率损失以及生产过剩。
瓶颈工序决定
最大产能
生产中的瓶颈(bottleneck)是指那些限制工作流整体水平(包括工作 流完成时间,工作流的质量等)的单个因素或少数几个因素。
作 业 时 间
工序 1 2 3 4 5 分担转移
作 业 时 间
工序 1 2 3 4 5 合并重排
工序 1 2 3 4 5 减人(分解消除)
作 业 时 间
工序 1 2 3 4 5 6 加 人(作业分解)
作 业 时 间
工序 1 2 3 4 5 减人(作业改善压缩)
生产线平衡(实例版)PPT课件
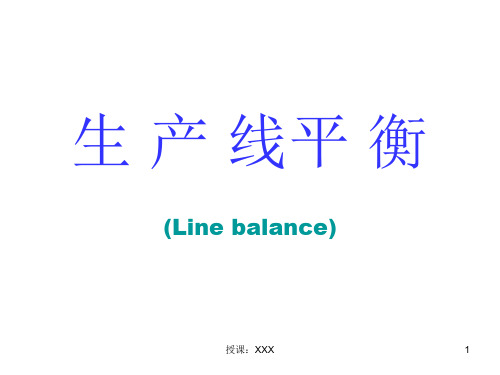
其计算公式:
计划期内有效工作时间
节拍r= 计划期内计划产量
[时间/件]
授课:XXX
11
1﹑生产线平衡的相关概念
例﹕节拍计算
某制品流水线计划年销售量为500000件﹐另 需生产备件10000件﹐良率98%﹐两班制工作 ﹐每班8小时﹐每周6天工作时间﹐时间有效 利用系数95%﹐求流水线的节拍。
按A 键 按 B 键归零
23
2﹑生产线平衡的实施
2.1.3时间记录表
授课:XXX
9.23
24
2﹑生产线平衡的实施
2.1.4工时测量的作用
➢ 获取各工站的实际操作时间﹐为山积表 制作﹐时间平衡作准备﹔
➢ 通过时间观测﹐分析作业价值﹐发现问 题和改善空间﹔
➢ 形成标准﹐比较实际差异﹐找出问题.
授课:XXX
时间
瓶颈时间
T1 T2
T5
T3 T4
S1 S2 S3 S4 工站
S1 S2 S3 S4 S5 工站
授课:XXX
29
2﹑生产线平衡的实施
2.3.3提高作业者技能
--或调换高技能作业者
1.优化工站物料﹐
时
工具摆放
间
2.改善操作员的
操作方法
3.提高操作员动作
效率
授课:XXX
山积表 重合简取排并化消
工 站
时间
T2
T1
T3 T4 T5
工站 S1 S2 S3 S4 S5
单件标准时间= T1+T2+T3+T4+T5
(流程中各工站所有动作标准时间之和)
授课:XXX
13
1﹑生产线平衡的相关概念
- 1、下载文档前请自行甄别文档内容的完整性,平台不提供额外的编辑、内容补充、找答案等附加服务。
- 2、"仅部分预览"的文档,不可在线预览部分如存在完整性等问题,可反馈申请退款(可完整预览的文档不适用该条件!)。
- 3、如文档侵犯您的权益,请联系客服反馈,我们会尽快为您处理(人工客服工作时间:9:00-18:30)。
可供時間:上班時間內,為某產品生產而投入的所有時間
例:A線有20個直接作業人員,某天14:00開始換線生產B產品,到17:00生 產結束,那麼,投入到B產品的可供時間為:
20人*3H=60H 概念3:投入工時
投入工時=可供工時-計劃停線工時
稼動率=投入工時/可供工時 *100% 計劃停線工時=計劃停線時間*人數 計劃停線時間=無計劃時間+換線時間+判停時間
5
3
1 0.5
4
2 1.5
0.5 1 1
0
0 2
0.5 1
2
10 2
12
2 1.5 6.5 4
2 2.5
1
S1 S2 S3 S4 S5 S6 S7 S8 S9 S10 S11 S12 S13 S14 S15 S16
使用工站時間制作山積表
M5 M4 M3 M2 M1
工站
2006-4-14
15
程序改善
上例中,若換線時間是15分鍾,則計劃停線工時為20人 *15min=300min=5H,則投入工時和稼動率為
60H-5H=55H 稼動率=55H/60H=92%
2006-4-14
5
相關的概念
概念4:設定產能 設定產能(H) =3600(S)/瓶頸時間(S) 設定產能(班)=投入時間/瓶頸時間(S)
比值﹔
單件標準時間
平衡率= ----------------------100%
瓶頸時間工位數
時
T
瓶頸時間
間 T 2T T T
1
345
SSS S S 工 123 4 5 站
單件標准時間 = T1+T2+T3+T4+T5
(流程中各工站所有動作標准時間之和)
2006-4-14
4
相關的概念
概念2:可供工時
山積表:將各分解動作時間,以疊加式直方圖表現的一 種研究作業時間結構的手法.
樣式:
產品xxx工時山積表
秒
10
0
8 0 1.5
6
1.5 0.5
1.5
1Байду номын сангаас 2
1.5 2
10
0.5 1.3
2
10 3
0 4
44
6
1
3
1.5 3
2
2
3.5
3.5
2
2 0
12 0.5
1.8 1
1.5
10
10
2 2.5 5 2
❖ 若有其他特殊情況,也應加以實錄;
數據整理和計算
測試完畢,對數據進行整理和計算,補充 測量有懷疑或錯漏的數據; ❖ 計算可信度95%所需的樣本數量,補測 差異樣本數量
資料分析與處理
對量測記錄之所有資料進行分析,對比 ST的差異程度,解決發現的問題; ❖ 若分析發現標準時間制定不當,應及時 修改,必要時調整制程.
時
間
等待時間
TTTT T 1234 5
SSS S S
123 4 5
單個產品平衡損失 =等待時間之和
工 站
概念7:平衡率100%代表﹕
1. 工站之間無等待,前后產能一致﹔
2.工站節拍相同﹐動作量相同(動作量是指工站中各種必要動素 的時間總量)
3.平衡損失時間為零 4.設計效率最大化 5.前后流程的設計可以更完善(如下圖)
2006-4-14
13
工時測量的作用﹕ 獲取各工站的實際操作時間﹐為山積表制作﹐時間平
衡作准備﹔ 通過時間觀測﹐分析作業價值﹐發現問題和改善空
間﹔
形成標准﹐比較實際差異﹐找出問題﹔
……(將會在后續的培訓中詳細介紹)
測時樣本大小計算
2006-4-14
14
山積表
山積表的使用: [圖表生成方法]
程序分析使用的圖表: 工藝程序圖 / 流程程序圖/ 路線圖
程序分析符號 1. --表示操作 2. --表示搬運/運輸 3. --表示檢驗 4. --表示暫存或等待 5. --表示受控的貯存 6. --派生符號,由上面的符號合成.
2006-4-14
16
例: 流程程序圖
1 電視機投入及外觀檢查 2 取出廠編號標簽並貼上 3 取塑膠袋,將電視機套入 4 取襯套, 套入電視機 5 遙控器投入及外觀檢查 6 取塑膠袋,將遙控器套入 7 附件投入及外觀檢查
2006-4-14
7
相關的概念
(交叉流程)
(直通流程 1 )
(直通流程 2 )
概念8:高效率 1. 通常認為高效率就是:快速,簡單&大規模 2. 我們認為沒有浪費的時候才是高效率的
操作效率=實際產量/設定產能*100% 整體工廠效率(OPE)=平衡率*稼動率*操作效率
2006-4-14
8
相關的概念
概念9:改善
I. 同樣的投入更大的輸出; II. 不增值(無效)增值(有效)
?不增值?
等待 不良
庫存 移動
……
例1: 減少移動與庫存提高效率 例2: 減少無效動作提高效率
2006-4-14
9
概念10:多能工
2006-4-14
10
平衡的手法
工時測量 山積表 程序改善 損失分析 作業條件改善 打破平衡
思考:1)為什么設定產能(班) =投入工時/總工時 總工時=瓶頸時間*作業人數
2)總工時 VS 單件標準時間
概念5:實際產量 實際產量是可供時間內所產出的良品數 1)人均產能=實際產量/投入時間/人數 2)單機台產能=實際產量/投入時間/機台數
2006-4-14
6
相關的概念
概念6:平衡損失 平衡損失=(總工時-單件標準時間)*設定產能
時間測試
分解動作時間量測,一般每個動作測量5 次為宜; ❖ 量測人員應站在作業員斜后面1米以外, 以能看清楚全部操作動作為准則; 測試中不能打擾作業員的正常操作,和 引起作業員的緊張;
2006-4-14
12
時間測量流程
作業內容
測試中判斷作業員的速度水平,並作如 數據與信息記錄 實記錄,不可修改量測數據;
2006-4-14
8 取塑膠袋,將附件套入 9 箱子成型
IE工程能力訓練教材(五)
2006-4-14
1
課程大綱:
➢1.相關的概念 ➢2.平衡的手法 ➢3.平衡的步驟 ➢4.流程化作業 ➢5.案例分享
2006-4-14
2
相關的概念
產出的速度取決于時間 最長的工站,稱之瓶頸
瓶頸在哪里? 了解加工的過程
2006-4-14
3
相關的概念
概念1: 平衡率
用於衡量流程中各工站節拍符合度的一個綜合
工時測量(秒表)
工具: 秒表 ❖ 觀測板、鉛筆 時間記錄表、計算器 山積表
方式: 一般測時法 ❖ 連續測時法
2006-4-14
11
時間測量流程
選定測試工站
作業內容
選定工站,閱讀SOP和觀察作業員操作,了 解該工站的全部操作內容;並詢問作業員 加以確認;
拆解動作
將工站動作拆解成若幹個單一的操作內 容,並填入<<時間記錄表>>