汽车制造工艺学复习重点汇总
汽车制造工艺学复习资料
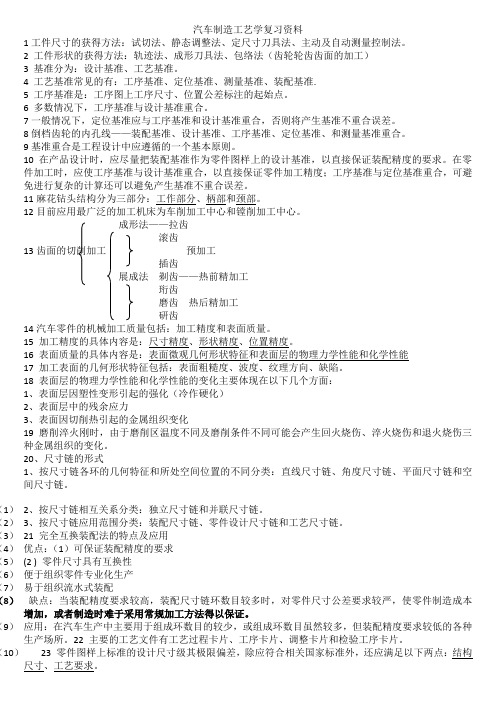
汽车制造工艺学复习资料1工件尺寸的获得方法:试切法、静态调整法、定尺寸刀具法、主动及自动测量控制法。
2 工件形状的获得方法:轨迹法、成形刀具法、包络法(齿轮轮齿齿面的加工)3 基准分为:设计基准、工艺基准。
4 工艺基准常见的有:工序基准、定位基准、测量基准、装配基准.5 工序基准是:工序图上工序尺寸、位置公差标注的起始点。
6 多数情况下,工序基准与设计基准重合。
7一般情况下,定位基准应与工序基准和设计基准重合,否则将产生基准不重合误差。
8倒档齿轮的内孔线——装配基准、设计基准、工序基准、定位基准、和测量基准重合。
9基准重合是工程设计中应遵循的一个基本原则。
10 在产品设计时,应尽量把装配基准作为零件图样上的设计基准,以直接保证装配精度的要求。
在零件加工时,应使工序基准与设计基准重合,以直接保证零件加工精度;工序基准与定位基准重合,可避免进行复杂的计算还可以避免产生基准不重合误差。
11麻花钻头结构分为三部分:工作部分、柄部和颈部。
12目前应用最广泛的加工机床为车削加工中心和镗削加工中心。
成形法——拉齿滚齿13齿面的切削加工预加工插齿展成法剃齿——热前精加工珩齿磨齿热后精加工研齿14汽车零件的机械加工质量包括:加工精度和表面质量。
15 加工精度的具体内容是:尺寸精度、形状精度、位置精度。
16表面质量的具体内容是:表面微观几何形状特征和表面层的物理力学性能和化学性能17 加工表面的几何形状特征包括:表面粗糙度、波度、纹理方向、缺陷。
18 表面层的物理力学性能和化学性能的变化主要体现在以下几个方面:1、表面层因塑性变形引起的强化(冷作硬化)2、表面层中的残余应力3、表面因切削热引起的金属组织变化19 磨削淬火刚时,由于磨削区温度不同及磨削条件不同可能会产生回火烧伤、淬火烧伤和退火烧伤三种金属组织的变化。
20、尺寸链的形式1、按尺寸链各环的几何特征和所处空间位置的不同分类:直线尺寸链、角度尺寸链、平面尺寸链和空间尺寸链。
汽车制造工艺学复习提纲
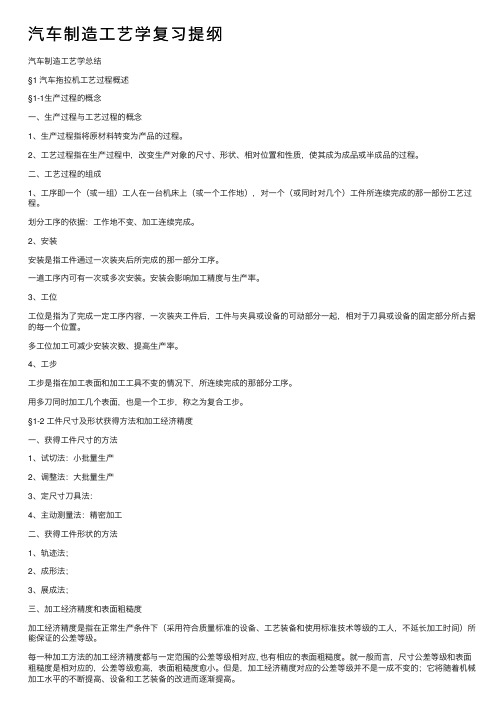
汽车制造⼯艺学复习提纲汽车制造⼯艺学总结§1 汽车拖拉机⼯艺过程概述§1-1⽣产过程的概念⼀、⽣产过程与⼯艺过程的概念1、⽣产过程指将原材料转变为产品的过程。
2、⼯艺过程指在⽣产过程中,改变⽣产对象的尺⼨、形状、相对位置和性质,使其成为成品或半成品的过程。
⼆、⼯艺过程的组成1、⼯序即⼀个(或⼀组)⼯⼈在⼀台机床上(或⼀个⼯作地),对⼀个(或同时对⼏个)⼯件所连续完成的那⼀部份⼯艺过程。
划分⼯序的依据:⼯作地不变、加⼯连续完成。
2、安装安装是指⼯件通过⼀次装夹后所完成的那⼀部分⼯序。
⼀道⼯序内可有⼀次或多次安装。
安装会影响加⼯精度与⽣产率。
3、⼯位⼯位是指为了完成⼀定⼯序内容,⼀次装夹⼯件后,⼯件与夹具或设备的可动部分⼀起,相对于⼑具或设备的固定部分所占据的每⼀个位置。
多⼯位加⼯可减少安装次数、提⾼⽣产率。
4、⼯步⼯步是指在加⼯表⾯和加⼯⼯具不变的情况下,所连续完成的那部分⼯序。
⽤多⼑同时加⼯⼏个表⾯,也是⼀个⼯步,称之为复合⼯步。
§1-2 ⼯件尺⼨及形状获得⽅法和加⼯经济精度⼀、获得⼯件尺⼨的⽅法1、试切法:⼩批量⽣产2、调整法:⼤批量⽣产3、定尺⼨⼑具法:4、主动测量法:精密加⼯⼆、获得⼯件形状的⽅法1、轨迹法;2、成形法;3、展成法;三、加⼯经济精度和表⾯粗糙度加⼯经济精度是指在正常⽣产条件下(采⽤符合质量标准的设备、⼯艺装备和使⽤标准技术等级的⼯⼈,不延长加⼯时间)所能保证的公差等级。
每⼀种加⼯⽅法的加⼯经济精度都与⼀定范围的公差等级相对应, 也有相应的表⾯粗糙度。
就⼀般⽽⾔,尺⼨公差等级和表⾯粗糙度是相对应的,公差等级愈⾼,表⾯粗糙度愈⼩。
但是,加⼯经济精度对应的公差等级并不是⼀成不变的;它将随着机械加⼯⽔平的不断提⾼、设备和⼯艺装备的改进⽽逐渐提⾼。
§1-3 ⽣产类型与⼯艺特征⼀、⽣产纲领与⽣产类型(⼀)⽣产纲领指企业计划期内应当⽣产的产品产量和年度计划。
汽车制造工艺复习资料.doc
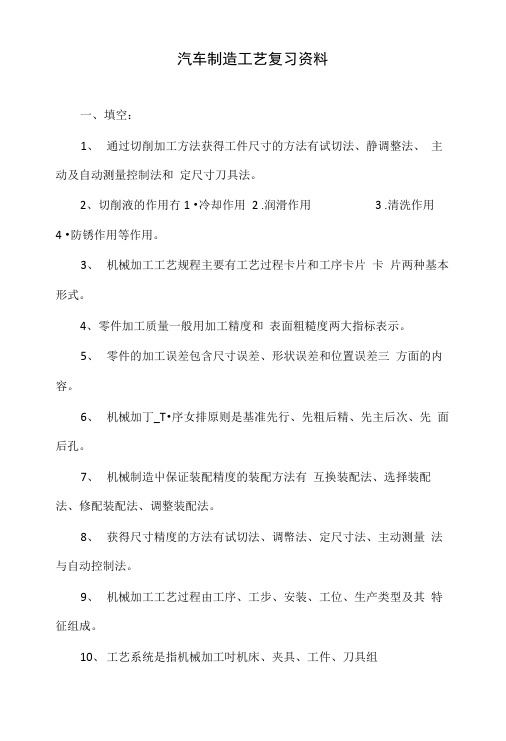
汽车制造工艺复习资料一、填空:1、通过切削加工方法获得工件尺寸的方法有试切法、静调整法、主动及自动测量控制法和定尺寸刀具法。
2、切削液的作用冇1 •冷却作用2 .润滑作用 3 .清洗作用4 •防锈作用等作用。
3、机械加工工艺规程主要有工艺过程卡片和工序卡片卡片两种基本形式。
4、零件加工质量一般用加工精度和表面粗糙度两大指标表示。
5、零件的加工误差包含尺寸误差、形状误差和位置误差三方面的内容。
6、机械加丁_T•序女排原则是基准先行、先粗后精、先主后次、先面后孔。
7、机械制造屮保证装配精度的装配方法有互换装配法、选择装配法、修配装配法、调整装配法。
8、获得尺寸精度的方法有试切法、调幣法、定尺寸法、主动测量法与自动控制法。
9、机械加工工艺过程由工序、工步、安装、工位、生产类型及其特征组成。
10、工艺系统是指机械加工吋机床、夹具、工件、刀具组成的完整系统。
11>轴类零件加工中常用中心孔或外圆作为统一的定位基准。
12、粗加工阶段的主耍任务是耍任务是保证各主耍表面达到图样耍求。
13、主轴冋转作纯径向跳动及漂移时,所镇出的孔是椭圆形。
14、定位误差的构成及产生原因,主耍有两个方面:和。
15、衡量一个工艺是否合理,主要是从、、三个方面去评价。
二、判断:1、同一道工序中只能有一次安装。
( )2、某些情况下加工表面自身可作为定位基准。
( )3、互换装配法是通过控制零件加工误差來保证装配精度。
( )4、测量基准是用以检验已加工表面尺寸和位置吋所依据的基准。
( )5、一个狭长平面可限制2个自由度,则2个狭长平面可限制4个自由度。
( )6、加工精度是指加工表面的光洁程度。
( )7、积屑瘤在加工中没有好处,应设法避免。
8、大批量生产应釆用工序集屮的原则。
( )9、加工原理误差在加工过程中可以消除。
( )10、退火和正火作为预备热处理常安排在毛坯制造之后,粗加工之前。
( )11>自位支承虽然与工件是多点接触但只限制工件一个自由度。
汽车制造工艺学复习
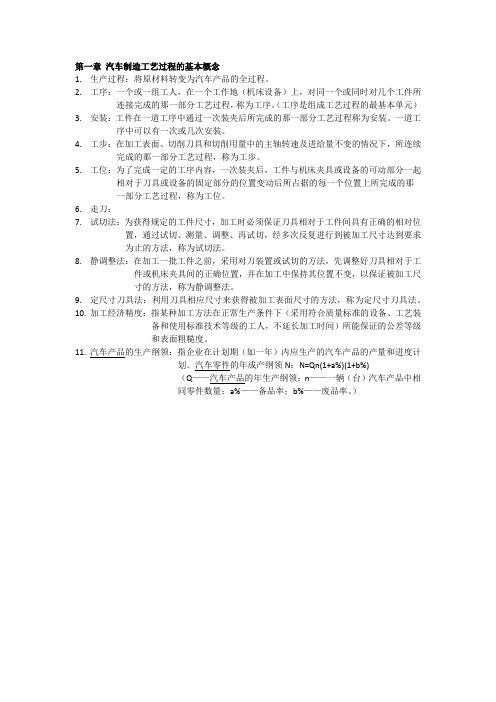
第一章汽车制造工艺过程的基本概念1.生产过程:将原材料转变为汽车产品的全过程。
2.工序:一个或一组工人,在一个工作地(机床设备)上,对同一个或同时对几个工件所连接完成的那一部分工艺过程,称为工序。
(工序是组成工艺过程的最基本单元)3.安装:工件在一道工序中通过一次装夹后所完成的那一部分工艺过程称为安装。
一道工序中可以有一次或几次安装。
4.工步:在加工表面、切削刀具和切削用量中的主轴转速及进给量不变的情况下,所连续完成的那一部分工艺过程,称为工步。
5.工位:为了完成一定的工序内容,一次装夹后,工件与机床夹具或设备的可动部分一起相对于刀具或设备的固定部分的位置变动后所占据的每一个位置上所完成的那一部分工艺过程,称为工位。
6.走刀:7.试切法:为获得规定的工件尺寸,加工时必须保证刀具相对于工件间具有正确的相对位置,通过试切、测量、调整、再试切,经多次反复进行到被加工尺寸达到要求为止的方法,称为试切法。
8.静调整法:在加工一批工件之前,采用对刀装置或试切的方法,先调整好刀具相对于工件或机床夹具间的正确位置,并在加工中保持其位置不变,以保证被加工尺寸的方法,称为静调整法。
9.定尺寸刀具法:利用刀具相应尺寸来获得被加工表面尺寸的方法,称为定尺寸刀具法。
10.加工经济精度:指某种加工方法在正常生产条件下(采用符合质量标准的设备、工艺装备和使用标准技术等级的工人,不延长加工时间)所能保证的公差等级和表面粗糙度。
11.汽车产品的生产纲领:指企业在计划期(如一年)内应生产的汽车产品的产量和进度计划。
汽车零件的年成产纲领N:N=Qn(1+a%)(1+b%)(Q——汽车产品的年生产纲领;n——一辆(台)汽车产品中相同零件数量;a%——备品率;b%——废品率。
)第二章整车企业典型制造工艺1.冲压工艺及其特点冲压是利用冲模使板料产生分离或变形的加工方法。
优点:(1)在模具的作用下,可以批量获得精度高度一致的产品,提高零件制造的互换性,易于组织后续制造工艺;(2)材料利用率高,可冲压形状复杂的零件;(3)冲压产品具有足够高的精度和较低的表面粗糙度;(4)能够在结构和工艺条件允许情况下,获得较高强度和刚度的零件;(5)冲压操作简单,工艺过程便于机械化和自动化,生产率很高,故零件成本低。
汽车制造工艺学复习资料
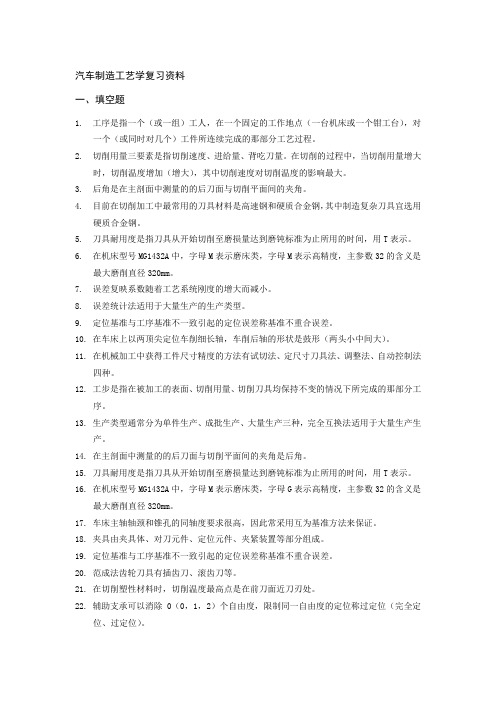
汽车制造工艺学复习资料一、填空题1.工序是指一个(或一组)工人,在一个固定的工作地点(一台机床或一个钳工台),对一个(或同时对几个)工件所连续完成的那部分工艺过程。
2.切削用量三要素是指切削速度、进给量、背吃刀量。
在切削的过程中,当切削用量增大时,切削温度增加(增大),其中切削速度对切削温度的影响最大。
3.后角是在主剖面中测量的的后刀面与切削平面间的夹角。
4.目前在切削加工中最常用的刀具材料是高速钢和硬质合金钢,其中制造复杂刀具宜选用硬质合金钢。
5.刀具耐用度是指刀具从开始切削至磨损量达到磨钝标准为止所用的时间,用T表示。
6.在机床型号MG1432A中,字母M表示磨床类,字母M表示高精度,主参数32的含义是最大磨削直径320mm。
7.误差复映系数随着工艺系统刚度的增大而减小。
8.误差统计法适用于大量生产的生产类型。
9.定位基准与工序基准不一致引起的定位误差称基准不重合误差。
10.在车床上以两顶尖定位车削细长轴,车削后轴的形状是鼓形(两头小中间大)。
11.在机械加工中获得工件尺寸精度的方法有试切法、定尺寸刀具法、调整法、自动控制法四种。
12.工步是指在被加工的表面、切削用量、切削刀具均保持不变的情况下所完成的那部分工序。
13.生产类型通常分为单件生产、成批生产、大量生产三种,完全互换法适用于大量生产生产。
14.在主剖面中测量的的后刀面与切削平面间的夹角是后角。
15.刀具耐用度是指刀具从开始切削至磨损量达到磨钝标准为止所用的时间,用T表示。
16.在机床型号MG1432A中,字母M表示磨床类,字母G表示高精度,主参数32的含义是最大磨削直径320mm。
17.车床主轴轴颈和锥孔的同轴度要求很高,因此常采用互为基准方法来保证。
18.夹具由夹具体、对刀元件、定位元件、夹紧装置等部分组成。
19.定位基准与工序基准不一致引起的定位误差称基准不重合误差。
20.范成法齿轮刀具有插齿刀、滚齿刀等。
21.在切削塑性材料时,切削温度最高点是在前刀面近刀刃处。
汽车车身制造工艺学(重点)

【绪论】1.汽车的基本结构大致有发动机、地盘、车身和电器与电子设备四大部分。
1.非承载式车身的汽车有独立的刚性车架,又称底盘大梁架。
2.承载式车身的汽车没有刚性车架。
大本分轿车车身采用这种车身结构。
3.冲压工艺:车身大致可以划分为发动机盖、车顶盖、行李箱盖、翼子板和前围板五部分,它们都是由钢板冲压成形4.焊接工艺:车身几乎全部由冲压件焊接而成5.涂装工艺:汽车涂装可以起到保护、装饰和标志作用,并能起到车内隔热、消音、抗振密封等特殊作用1.【第一章】1.冲压工艺特点:冲压成形工艺是一种先进的金属加工工艺方法,它是建立在金属塑性变形的基础上,在常温条件下利用模具和冲压设备对板料施加压力,使板料产生塑性变形或分离,从而获得具有一定形状、尺寸和性能的零件(冲压件)2.板料、模具和冲压设备是冲压生产的三大要素。
3.冲压工序按加工性质的不同,可以分成两大类:分离工序(常用:落料、冲孔)和成形工序(常用:弯曲、拉伸、翻边、胀形)。
4.四个基本工序为:冲裁(包括冲孔、落料、修边、剖切等)、弯曲、拉深、局部成形(包括翻边、胀形、校平和整形工序等)。
5.影响板料冲压性能的质量指标主要是材料的力学性能(),此外还有化学成分、金相组织和板料的表面质量和尺寸精度。
6.力学性能指标及其对冲压性能的具体影响:1.屈服极限2.屈强比3.延伸率4.硬化指数(应变刚指数)n5.厚向异性系数r 6.板平面各向异性系数7.冷弯试验:将试样在万能材料试验机上做180°冷弯。
在达到规定的冷弯直径D后,若试验没有裂纹、分层等即可认为冷弯合格。
杯突试验:杯突试验又称顶压试验或胀形实验。
试验时,用一规定的球状凸模(或钢球)向夹紧在规定的凹模内的试样施加压力,一直到试样开始出现裂纹为止。
这是的凹模压入深度就是杯突深度。
杯突深度越大,表明冲压性能越好。
杯突试验结果反映钢板在胀形类成形中的冲压性能。
1.【第二章】1.冲裁就是利用冲裁模在压力机上使板料的一部分与另一部分分离的冲压分离工序。
汽车车身制造工艺学(第二版)期末复习要点资料

第一章冲压工艺1、冲压成形工艺:成立在金属塑性变形的基础上,在常温条件下利用模具和冲压设施对板料施加压力,使板料产生塑性变形或分别,进而获取拥有必定形状、尺寸和性能的部件的金属加工工艺方法。
2、冲压生产的三大体素:板料、模具、冲压设施。
3、分别工序:使冲压件或毛坯在冲压过程中沿必定的轮廓相互分别,同时冲压部件的分别断面要知足必定的断面质量要求。
落料:用落料模沿关闭轮廓曲线冲切,冲下部分是部件。
冲孔:用冲孔模沿关闭轮廓曲线冲切,冲下部分是部件。
4、成形工序:板料在不产生损坏的前提下使毛坯发生塑性变形,获取所需求的形状及尺寸的部件。
5、冲压工序四个基本工序为:冲裁、曲折、拉深、局部成形。
6、厚向异性系数:指单位拉伸试样宽度应变和厚度应变的比值。
7、简述冲压工艺的特色和冲压工序的分类。
答:冲压生产是一种优良、高产、低耗费和低成本的加工方法,但冲压生产也有必定的限制性。
因为模具多为单件生产,精度要求高,制造难度大,制造周期长,所以模具制造花费高,不宜用于单件和批量小的部件生产。
冲压工序分类:①分别工序:使冲压件或毛坯在冲压过程中沿必定的轮廓相互分别,同时冲压部件的分别断面要知足必定的断面质量要求。
②成形工序:板料在不产生损坏的前提下使毛坯发生塑性变形,获取所需形状及尺寸的部件。
第二章冲裁工艺1、冲裁:从板料上分别出所需求形状和尺寸的部件或毛坯的冲压方法。
2、冲裁工件断面特色区:圆角带、光明带、断裂带。
3、冲裁空隙:凸、凹模刃口工作部分尺寸之差。
4、冲裁空隙对冲裁件的影响:断面质量、尺寸精度、冲模使用寿命、冲裁力。
5、毛刺形成的原由?答:在冲裁过程中,空隙过小,上下两面裂纹不重合,隔着必定距离,相互平行,最后在此间形成毛刺。
空隙过大,关于薄料会使资料拉入空隙中,形成拉长的毛刺。
6、降低冲裁力的举措:加热冲裁、斜刃冲裁、阶梯冲裁。
7、冲裁模分类:简单模、连续模、复合模。
8、冲裁变形过程?①弹性变形阶段:凸模接触板料,加压后板料发生弹性压缩与曲折,并略有挤入凹模洞口,板料内应力没有超出折服极限。
汽车制造工艺学考点归纳(非官方版)

填空1.机械加工工艺过程主要分为:工序、安装、工位、工步、走刀等工作内容。
2.生产类型:单件生产、成批生产、大量生产。
3.合金的铸造性能主要是指:流动性、收缩性、偏析和吸气性。
4.铸造工艺参数:加工余量、起模斜度、铸造圆角、型芯头、收缩余量。
5.特种铸造:金属型铸造、压力铸造、低压铸造、离心铸造。
6.锻造按所用工具与模具的安置情况不同分为:自由锻、胎模锻、模锻。
7.影响金属塑性变形能力和变形抗力的因素主要有:化学成分、金属组织、变形温度、变形速度。
8.常用的汽车零件的毛坯有:铸件、锻压件、焊接件、粉末冶金件。
9.机械制造工艺问题的三个指标是:质量、生产率、经济性。
10.零件的加工精度包括:尺寸精度、形状精度、位置精度。
11.机床夹具的组成:定位元件、夹紧装置、对刀导向元件、夹具连接元件、夹具体、其他装置或元件。
12.按工艺过程的不同,夹具可分为:机床夹具、装配夹具、焊接夹具;按机床种类不同可分为:车床夹具、铣床夹具、钻床夹具;按动力源不同又可分为:手动夹具、气动夹具。
13.与工件的定位平面相接触的定位元件有:支承钉、支承板、可调支承、自位支承、辅助支承。
14.夹紧装置的组成:动力装置、中间传力装置(其作用是改变夹紧力大小、方向,实现自锁)、夹紧元件。
15.典型夹紧机构:16.尺寸链的组成:封闭链、组成链。
17.尺寸链的分类:按作用分为:装配尺寸链、零件设计尺寸链、工艺尺寸链;按空间位置分为:直线尺寸链、平面尺寸链、空间尺寸链;按尺寸链间相互关系可分为:独立尺寸链、并联尺寸链、串联尺寸链。
18.保证装配精度的装配方法:互换装配法、选择装配法、调整装配法、修配装配法。
其中,互换装配法又分为:完全互换装配法、大数互换装配法;选择装配法分为:直接选配法、分组选配法、复合选配法;调整装配法分为可动调整装配法、固定调整装配法。
19.零件机构工艺性可以分为零件结构的:切削工艺性、装配工艺性两方面。
20.孔系可以分为:平行孔系、同轴孔系、交叉孔系。
汽车制造工艺学考点整理

l −l பைடு நூலகம் l0
。
2、均匀延伸率:指试样在拉伸试验中,达到强度极限,即试样开始出现局部颈缩时的延伸 率。 Ch1: 1、 冲裁是指冲压分离工序, 板料受力是从弹性变形开始, 经过塑性变形, 以断裂分离结束。 2、 冲裁分为哪几个阶段: (1)弹性变形阶段 凸模接触板料后,开始向下压缩材料,使材料产生弹性压缩和弯曲变形。板料与 凸模和凹模的接触处形成很小的圆角。随着凸模的继续压入,材料的内应力达到弹性极 限。此时,凸模下的材料略有弯曲,凹模上的材料则向上翘。 (2)塑性变形阶段 当凸模继续下行、材料的内应力达到屈服极限时,材料除了有剪切变形外,还同 时伴有弯曲和拉伸变形。 随着凸模挤入材料的深度逐渐增大, 即塑性变形程度逐渐增大。 材料内部的拉应力和弯矩也都增大,变形区材料硬化加剧。直至凸、凹模刃口附近的材 料应力集中,在拉应力作用下出现裂纹时,塑性变形阶段即告结束。此时冲裁变形力达 到最大值。 (3)断裂分离阶段 断裂分离阶段从材料在模具刃口附近出现微裂纹开始。随着凸模继续压下,已形 成的上、下两面的微裂纹逐渐扩大,并向材料内延伸。当上下两条裂纹相遇重合时,材 料便被剪断分离。 3、 冲裁断面的区域性特征:塌角、光亮带、剪裂带和毛刺等四个部分。 塌角:在凸模压入材料时,刃口附近的材料被牵连拉入变形而形成。 光亮带:表面光滑,表面质量最佳,它是在塑性变形过程中由凹、凸模挤压切入材料所 形成的。 剪裂带:表面较粗糙,带斜度而不与板平面垂直.它是材料剪断分离时所形成的。 毛刺:材料出现微裂纹时形成,随凸模的下行被拉长,并残留在冲裁件上。 4、冲裁模间隙 Z:指凸、凹模之间的间隙,其对冲裁件的质量影响极大,同时影响:冲裁 力、模具寿命。 1、 对冲裁件质量的影响 1)对冲裁件断面的影响 冲裁模间隙较大时,材料中的拉应力也较大,容易产生裂纹,塑性变形阶段结束 较早,因此光亮带较小,而剪裂带、塌角和毛刺都较大,冲裁件的翘曲也较显著。 间隙较小,情况刚好相反。 间隙过大或过小均导致上、下两面的剪裂纹不能相交重合于一线。 2)对冲裁件尺寸精度的影响(受拉,回弹收缩;受挤,恢复伸张) 冲裁模间隙较大时,材料受拉伸作用大,冲裁后材料的弹性恢复也较大,因此,使 落料尺寸小于凹模尺寸,冲孔孔径大于凸模直径。另一方面,冲裁模间隙较大使翘曲严重,
大学汽车制造工艺学复习资料

大学汽车制造工艺学复习资料汽车制造工艺学复习资料(加工质量)1.什么是工序、安装、工位、工步、走刀?工序:一个(组)工人,在一台机床(某个地方),对一个(多个)工件所连续完成那部分工艺过程。
安装:工件通过一次装夹后所完成的那一部分工序。
工位:一次安装内,工件在机床上所占的每一个位置。
工步:在加工表面、加工工具、切削用量中的转速、进给量不变的情况下,所连续完成的那一部分工序。
走刀:在一个工步内,由于有些表面加工余量太大,需用同一把刀具以及同一切削用量对其多次切削。
这样的每一次切削就称为一次走刀。
2.说明加工精度、加工误差、公差的概念及区别。
加工精度:零件在加工以后的几何参数(尺寸、形状和位置)的实际值与理想值的符合程度。
加工精度包括:(1)尺寸精度(2)形状精度(3)位置精度加工误差:零件加工后的几何参数的实际值与理想值的偏离程度。
公差:实际参数的允许变动量。
区别:加工精度和加工误差都是从不同的角度在描述误差,但是加工误差的大小由零件的实际测量的偏离量来衡量,而加工精度的高低由公差等级或者公差值来衡量,并由加工误差的大小来控制。
一般来说,只有加工误差小于公差时才能保证加工精度。
3.加工质量的两大指标是?加工精度:尺寸精度、形状精度、位置精度。
表面质量:1、表面微观几何形状特征:1)表面粗糙度2)波度3)纹理方向4)缺陷2、表面物理、化学性能:1)冷作硬化2)残余应力3)金相组织变化4.何为原始误差,他与加工误差有何关系?原始误差:工艺系统本身的误差。
原始误差通过加工过程直接反映到工件上就成为加工误差。
5.原始误差包括哪些内容?1、机床误差2、刀具误差3、工艺系统受力变形引起的加工误差4、工艺系统热变形引起的加工误差5、工件残余应力引起的加工误差6.车床导轨误差怎么影响加工精度?水平面内的直线度误差:在纵向切削过程中,刀尖的运动轨迹相对工件轴线之间的距离会发生变化,引起工件半径的尺寸变化,即产生圆柱度误差。
汽车制造工艺学复习
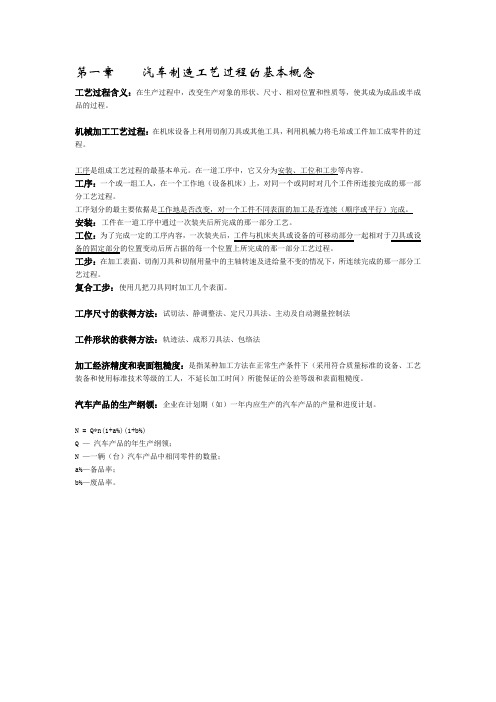
第一章汽车制造工艺过程的基本概念工艺过程含义:在生产过程中,改变生产对象的形状、尺寸、相对位置和性质等,使其成为成品或半成品的过程。
机械加工工艺过程:在机床设备上利用切削刀具或其他工具,利用机械力将毛培或工件加工成零件的过程。
工序是组成工艺过程的最基本单元。
在一道工序中,它又分为安装、工位和工步等内容。
工序:一个或一组工人,在一个工作地(设备机床)上,对同一个或同时对几个工件所连接完成的那一部分工艺过程。
工序划分的最主要依据是工作地是否改变,对一个工件不同表面的加工是否连续(顺序或平行)完成。
安装:工件在一道工序中通过一次装夹后所完成的那一部分工艺。
工位:为了完成一定的工序内容,一次装夹后,工件与机床夹具或设备的可移动部分一起相对于刀具或设备的固定部分的位置变动后所占据的每一个位置上所完成的那一部分工艺过程。
工步:在加工表面、切削刀具和切削用量中的主轴转速及进给量不变的情况下,所连续完成的那一部分工艺过程。
复合工步:使用几把刀具同时加工几个表面。
工序尺寸的获得方法:试切法、静调整法、定尺刀具法、主动及自动测量控制法工件形状的获得方法:轨迹法、成形刀具法、包络法加工经济精度和表面粗糙度:是指某种加工方法在正常生产条件下(采用符合质量标准的设备、工艺装备和使用标准技术等级的工人,不延长加工时间)所能保证的公差等级和表面粗糙度。
汽车产品的生产纲领:企业在计划期(如)一年内应生产的汽车产品的产量和进度计划。
N = Q*n(1+a%)(1+b%)Q —汽车产品的年生产纲领;N —一辆(台)汽车产品中相同零件的数量;a%—备品率;b%—废品率。
第二章工件的装夹和机床夹具定位:确定工件在机床上或机床夹具中占有正确位置的过程。
夹紧:工件定位后将其固定,使其在加工过程中保持定位位置不变的操作。
装夹:将工件在机床上或机床夹具中定位、夹紧的过程。
工艺基准包括:工序基准、定位基准、测量基准、装配基准。
工序基准:在工序图上用来确定本道工序被加工件表面加工尺寸、位置公差的基准,工序尺寸:联系加工表面和工序基准间的加工尺寸,是本道工序应直接保证的尺寸。
汽车制造工艺 期末复习重点
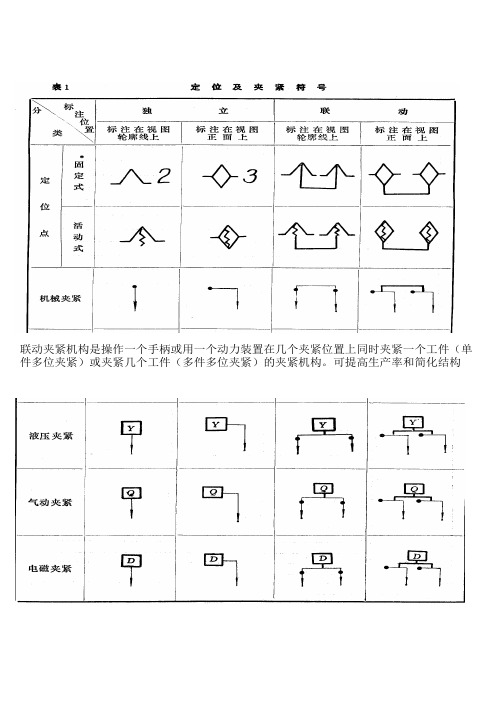
件多位夹紧)或夹紧几个工件(多件多位夹紧)的夹紧机构。
可提高生产率和简化结构表1-9 定位及夹紧符号(续)汽车制造工艺学一、填空题1. 主轴回转作纯径向跳动及漂移时,所镗出的孔是_椭圆__形。
2. 零件的加工质量包括_加工精度_和_加工表面质量__。
3. 零件光整加工的通常方法有_珩磨_、研磨、超精加工及_抛光_等方法。
4. 机械加工工艺规程实际上就是指规定零件机械加工工艺过程和操作方法等的_工艺文件5. 工艺过程是指生产过程中,直接改变生产对象形状、尺寸、相对位置、及性质的过程。
6. 零件的几何(尺寸,形状,位置)精度、表面质量、物理机械性能是评定机器零件质量的主要指标。
7. 加工经济精度是指在正常加工条件下(采用符合标准的设备,工艺装备和标准技术等级的工人,不延长加工时间)所能保证的加工精度。
8. 轴类零件加工中常用两端中心孔作为统一的定位基准。
9. 零件的加工误差指越小(大),加工精度就越高(低)。
10. 10.粗加工阶段的主要任务是获得高的生产率。
11.精加工阶段的主要任务是使各主要表面达到图纸规定的质量要求。
12.工艺系统的几何误差包括加工方法的原理误差、制造和磨损所产生的机床几何误差和传动误差,调整误差、刀具、夹具和量具的制造误差、工件的安装误差。
13. 13.零件的加工误差值越小(大),加工精度就越高(低)。
14.机械产品的质量可以概括为__实用性____、可靠性和__经济性____三个方面。
15.通过切削加工方法获得工件尺寸的方法有试切法、静调整法、_定尺寸刀具法__、主动及自动测量控制法16、表面质量:是指机械加工后零件表面的状况。
17、形状精度:是指零件表面或线的实际形状与理想形状的接近程度。
18、工艺系统:在机械加工时,机床、机床夹具、刀具和工件形成了一个完整的加工系统。
粗基准:用未经加工过的表面作为定位基准称为粗基准。
19、工艺系统刚度:在外力作用下,工艺系统抵抗变形的能力。
汽车制造工艺学复习整理1.doc

汽车制造工艺学汽车制造工艺过程中的基本概念工艺过程:是指在生产过程中,改变生产对象的形状、尺寸、相对位置和性质等,使其成为成品或半成品的过程。
生产过程指将原材料转变为产品的过程。
机械加工工艺过程:在机床设备上利用切削刀具或其它工具易用机械力将毛坯或工件加工成零件的过程。
工序:一个或一组工人在一个机床设备上对同一个或同时对几个工件所连续完成那一部分工艺过程。
工序是组成工艺过程的最基本单元安装:同一道工序中,零件在加工位置上装夹一次所完成的那一部分工序。
P4 工位:零件在每个位置上完成的那一部分加工过程。
P4 工步:在一次安装中,在加工表面、加工刀具、切屑用量不变的情况下,所连续完成的那一部分工艺过程。
几把刀同时加工几个表面叫(一个)复合工步工件尺寸的获得方法①试切法:通过试切、测量、调整、再试切,经多次反复进行到被加工尺寸达到要求为止的方法适用于单件货几件工件的加工②静调整法:在加工一批工件之前,采用对刀装置或试切的方法,先调整好刀具相对于工件或机床夹具间的正确位置,并在加工中保持其位置不变,以保证被加工尺寸的方法适合产量较大的场合广泛用于半自动机床和自动线上的生产;③定尺寸刀具法:利用刀具相应尺寸来获得被加工表面尺寸的方法适用于孔沟槽等表面的加工适用于各种产量的场合;④主动及自动测量控制法;在加工过程中,利用测量装置、进给机构及控制系统保证被加工表面尺寸的方法产量大的汽车制造企业。
工件形状的获得方法①轨迹法:依靠刀具运动轨迹来获得所需工件形状的方法用于产量较大较大工件形状较为复杂的零件形状的切削加工;②成型刀具法:使用成形刀具获得工件形状的方法生产率高;③包络法;在刀具与工件相对运动过程中,由刀具切削刃连续运动的轨迹包络成工件形状的方法加工经济精度:是指某种加工方法在正常生产条件下不延长加工时间所能保证的公差等级和表面粗糙度。
P83 •汽车零件表面的尺寸公差与表面粗糙度具有何种关系?答: 一般被加工表面的尺寸公差值小表面粗糙度值也一定较小o但是有些被加工表面要求的表面糙度值较小不一定尺寸公差值也必须小。
汽车制造工艺学整理

汽车制造工艺学(整理)————————————————————————————————作者:————————————————————————————————日期:ﻩ第一章汽车制造工艺过程的基本概念1-1、机械产品常用的材料钢板、钢材(型材)、铸铁、有色金属、工程塑料、复合材料、橡胶、玻璃、皮革、油漆以及铬、钨和木材等。
1-2、汽车的生产过程:将原材料转变为汽车产品的全过程。
包括生产准备、毛坯制作、零件加工、检验、装配、包装运输、油漆和试验调整等过程。
总成:是由若干零件按规定技术要求组装的装配单元。
如变速器总成、驱动桥总成、车架总成、发动机总成等。
工艺装备:是指产品制造时所需的刀具、夹具、量检具、附具、模具等各种工具的总称。
1-3、工艺过程:生产过程中,改变生产对象的形状、尺寸、相对位置和性质等使其成为成品或半成品的过程。
1. 工艺过程可分为:铸造工艺过程锻造工艺过程机械加工工艺过程:(在机床上利用刀具、机械力,将毛坯或半成品加工成零件的过程。
)热处理工艺过程装配工艺过程……等等2.工艺规程:以文件形式确定下来的工艺过程称为工艺规程。
1-4、机械加工工艺过程的组成机械加工工艺过程是由若干个顺次排列的工序组成。
工序又可分为安装、工位、工步和走刀。
1)安装指在一道工序中工件经一次装夹后所完成的那部分工序内容。
2)工位工件在机床上占据每一个位置所完成的加工3)工步指在加工表面、刀具和切削速度和进给量均保持不变的情况下完成的部分内容。
4)走刀刀具在加工表面上切削一次所完成的内容。
1-5、工件尺寸的获得方法保证尺寸公差的方法主要有以下四种:1.试切法2.调整法3.定尺寸刀具法4.主动测量法1-6、工件形状的获得方法主要有以下三种:1.轨迹法:依据刀具运动轨迹来获得所需要工件形状的一种方法。
2.成形法:使用成形刀具加工,获得工件表面的方法。
3.展成法1-7、汽车零件的年生产纲领N的计算公式?生产纲领:计划期内,包括备品率和废品率在内的产量称为生产纲领。
汽车制造工艺学(吉大第3版)期末考试知识点总结

【名词解释】1.生产过程:指将原材料转变为汽车产品的全过程。
2.工艺过程:在生产过程中,改变生产对象的形状、尺寸、相对位置和性质等,使其成为成品或半成品的过程。
3.机械加工工艺过程:在机床设备上利用切削刀具或其他工具,利用机械力将毛坯或工件加工成零件的过程。
4.切削加工:利用切削刀具从生产对象(工件)上切除多余材料的加工方法。
5.装配工艺过程:按规定的装配技术要求,将零件或总成(部件)进行配合和连接,使之成为半成品或成品的工艺过程。
6.工序:一个或一组工人,在一个工作地(机械设备上)对同一个或同时对几个工件所连续完成的那一部分工艺过程。
7.安装:工件在一道工序中通过一次装夹后所完成的那一部分工艺过程。
8.工位:在某一工序中,工件在机床所占的每一个位置上所完成的那一部分工艺过程。
9.工步:在一次安装或工位中,加工表面、加工工具和切削用量中的主轴转速及进给量不变的情况下,所连续完成的那一部分工序,称为工步。
(填空题)10.试切法:通过试切、测量、调整、再试切,经过多次反复进行到被加工尺寸达到要求为止的方法。
11.加工经济精度:在正常生产条件下,每种加工方法所能保证的公差等级。
12.生产纲领:指企业在计划期内应生产的汽车产品的产量和进度计划。
13.定位:通常将确定工件在机床上或机床夹具中占有正确位置的过程。
14.夹紧:工件定位后将其固定,使其在加工过程中保持定位位置不变的操作。
15.装夹:将工件在机床或机床夹具中定位和夹紧的过程称为装夹。
16.机床夹具:用以装夹工件或引导刀具的装置。
17.基准:用以确定生产对象上几何要素间几何关系所依据的那些点线面。
18.设计基准:设计图样上采用的基准。
19.工艺基准:工艺过程中采用的基准。
20.工序基准:在工序图上用以确定本道工序被加工表面的加工尺寸、位置的基准。
21.定位基准:在加工中确定工件在机床或机床夹具中占有正确位置的基准。
22.测量基准:测量时所采用的基准,用来确定被测量尺寸、形状和位置的基准、23.装配基准:装配时用来确定零件或部件在产品中相对位置的基准。
汽车制造工艺期末复习知识点
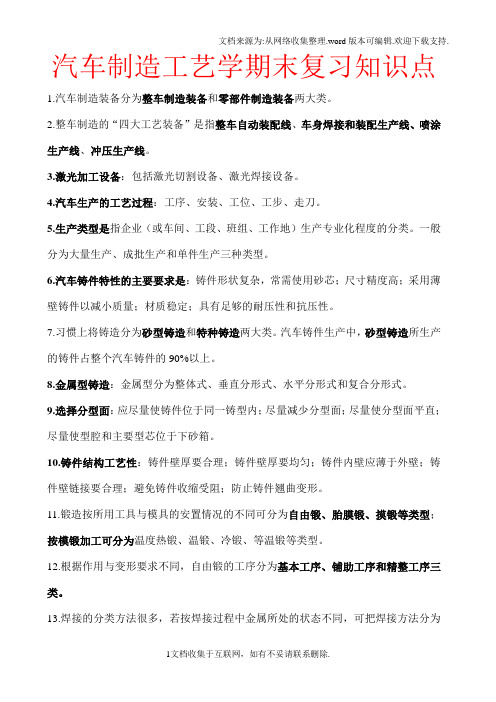
汽车制造工艺学期末复习知识点1.汽车制造装备分为整车制造装备和零部件制造装备两大类。
2.整车制造的“四大工艺装备”是指整车自动装配线、车身焊接和装配生产线、喷涂生产线、冲压生产线。
3.激光加工设备:包括激光切割设备、激光焊接设备。
4.汽车生产的工艺过程:工序、安装、工位、工步、走刀。
5.生产类型是指企业(或车间、工段、班组、工作地)生产专业化程度的分类。
一般分为大量生产、成批生产和单件生产三种类型。
6.汽车铸件特性的主要要求是:铸件形状复杂,常需使用砂芯;尺寸精度高;采用薄壁铸件以减小质量;材质稳定;具有足够的耐压性和抗压性。
7.习惯上将铸造分为砂型铸造和特种铸造两大类。
汽车铸件生产中,砂型铸造所生产的铸件占整个汽车铸件的90%以上。
8.金属型铸造:金属型分为整体式、垂直分形式、水平分形式和复合分形式。
9.选择分型面:应尽量使铸件位于同一铸型内;尽量减少分型面;尽量使分型面平直;尽量使型腔和主要型芯位于下砂箱。
10.铸件结构工艺性:铸件壁厚要合理;铸件壁厚要均匀;铸件内壁应薄于外壁;铸件壁链接要合理;避免铸件收缩受阻;防止铸件翘曲变形。
11.锻造按所用工具与模具的安置情况的不同可分为自由锻、胎膜锻、摸锻等类型;按模锻加工可分为温度热锻、温锻、冷锻、等温锻等类型。
12.根据作用与变形要求不同,自由锻的工序分为基本工序、铺助工序和精整工序三类。
13.焊接的分类方法很多,若按焊接过程中金属所处的状态不同,可把焊接方法分为熔焊、压焊和钎焊三大类。
14.焊接结构件种类各式各样,在其材料确定以后,对焊接结构件进行工艺设计主要包括三方面内容:焊缝布置、焊接方法选择和焊接接头设计等。
15.板料冲压的基本工序有冲裁、弯曲、拉深、成形等。
16.冲裁是使板料沿封闭的轮廓线分离的工序,包括冲孔和落料。
17.在切削加工形成零件需要表面的全过程中,刀具和工件间的相对运动,按作用的不同分为切削运动和铺助运动。
18.常用刀具标注角度参考系有正交平面参考系、法平面参考系和假定工作平面参考系三种。
- 1、下载文档前请自行甄别文档内容的完整性,平台不提供额外的编辑、内容补充、找答案等附加服务。
- 2、"仅部分预览"的文档,不可在线预览部分如存在完整性等问题,可反馈申请退款(可完整预览的文档不适用该条件!)。
- 3、如文档侵犯您的权益,请联系客服反馈,我们会尽快为您处理(人工客服工作时间:9:00-18:30)。
工位:为了完成一定的工序内容,一次装夹后,工件与机床夹具或设备可动部分一起相对于刀具或设备的固定部分的位置变动后,所占据的每一个位置上所完成的那一部分工艺过程,称为工位。
工件尺寸获得的四种方法:试切法、静调整法(汽车零件用的最多)、定尺寸刀具法、主动及自动测量控制法。
尺寸链:由相互连接的尺寸形成的封闭尺寸组,称为尺寸链。
尺寸链中的每一个尺寸或位置公差,简称为环。
尺寸链包括组成环和封闭环,组成环是对封闭环有影响的全部环,封闭环是在装配和加工过程中间接获得的环。
增环:指该环的变化引起封闭环作同向变化的组成环、即该环增大(减小)时,封闭环也随之增大(减小)。
减环:与增环相反。
汽车的生产纲领,是指企业在计划期内应生产的汽车产品的产量和进度计划。
汽车零件的生产类型与汽车产品的类型有关,但是有可能不同于汽车产品的生产类型。
确定生产类型的参考数据
确定方法
生产类型
设备或工作地
担负的工序数目
生产节拍/min
大量生产
1~2
5以下
大批生产
2~10ห้องสมุดไป่ตู้
5~15
中批生产
10~20
15~60
小批生产
20~40
60以上
大量生产:一台机床设备上常年进行某一零件的某1~2个固定工序内容的加工,这样的生产类型称为大量生产。
单件生产:每台机床设备上常年不重复或很少重复制造同一种零件或进行相同工序内容的加工,这样的生产类型称之为单件生产。
成批生产:每台机床设备或工作地负担较多工序,并且成批轮番完成不同零件或同一零件的相似工序加工,这样的生产类型称之为成批生产。
机床误差
影响机械
加工精度
主要因素
工艺系统的热源包括:切削热、摩擦热和传动热、外部热源。
为了减少工件的热变形,主要采取如下措施:
1、采用有效的冷却措施,例如在切削区给以充足的切削液;
2、提高切削速度,使大部分热来不及传给工件,而是被切屑带走;
3、对某些加工方法,夹紧时考虑对其热变形的补偿。
刀具热变形的热源主要是切削热。
用来确定生产对象上几何要素间几何关系所依据的那些点、线、面,称为基准。
设计基准:图样上采用的基准称为设计基准
基准
工艺基准
专用机
床夹具
专用机床夹具的组成及其与工件、机床、刀具间的关系
定位误差:由于定位的不准确原因是工件工序偏离理想位置,引起工序尺寸变化的加工误差。
定位误差
夹紧装置的组成:力源装置、夹紧元件、中间传力机构
机械加工工序卡片:在卡片上绘有工序简图,图上注明定位基准符号、各加工表面的工序尺寸、表面粗糙度和其他技术要求等,并详细写明各工步的顺序和内容、使用的设备及工艺装备,以及规定的切削用量和时间定额等;它是用以指导操作工人进行生产的文件。
调整卡片:是对自动、半自动机床或某些齿轮加工机床等进行调整用的一种工艺文件;调整卡片的格式因机床而异。
汽
车
制
造
工
艺
学
期
末
复
习
资
料
汽车的生产过程是指将原材料转变为汽车产品的全过程。
汽车的生产过程包括了毛皮的制造、零件的机械加工、毛坯和零件的热处理、总成(或部件)的装配和汽车产品的总装配等基本生产过程。
工艺过程是指,在生产过程中,改变生产对象的形状、尺寸、相对位置和性质等,使其成为成品或半成品的过程。
工序:一个或一组工人,在一个工地(机床设备)上,对同一个或同时对几个工件所连接完成的那一部分工艺过程,称为工序。
从任意环为起点绕尺寸链回路连接顺序画出单向箭头,凡是与封闭环箭头方向相反的的环均为增环,与封闭环箭头相同的环均为减环。
要求理解并运用的公式:
在汽车制造中,常用的保证装配精度的方法有完全互换装配法、不完全互换装配法、分组互换装配法和修配装配法等多种方法。
公差修正时应考虑:1、标准件的尺寸公差应按标准规定;
夹紧力作用方向选择原则: 夹紧力的方向应垂直于主要定位基面,以保证加工精度; 夹紧力方向应与工件刚度最大的方向一致,以减小工件的夹紧变形; 夹紧力方向应尽量与切削力、重力等力方向一致,以减小夹紧力。
切削速度vc:
vc =
切削三要素:切削速度、进给量f(或进给速度vf)、背吃刀量ap
汽车零件质量
工艺系统:在机械加工时,机床、机床夹具、刀具和工件形成了一个完整的系统,称之为工艺系统。
2、组成环尺寸大的、加工难度大的,取较大公差,反之取较小公差,并应取标准公差值。为保证经济加工,一般零件尺寸公差取IT9或低于IT9级;
3、在组成环中选择一个协调环。
完全互换装配法
机械加工工艺规程:是规定零件制造工艺过程和操作方法的工艺文件,机械加工工艺规程要满足技术和经济两方面的要求。
机械加工工艺过程卡片:以工序为单位,简要说明零件工艺过程的一种工艺文件;其内容包括各工序的工序号、工序内容、工艺过程所经过的各个车间和工段,每个工序所使用的机床、工艺设备及时间定额等。
表面粗糙度的形成主要有两方面的原因:一是几何原因,另一是物理原因。
表面强化(冷硬化或简称冷硬):表面层由于塑性变形的结果。其强度和硬度提高,塑性和韧性降低,从而在工件表面形成一定深度的硬化层,这种现象称之为表面强化。
零件的表面质量对零件的耐磨性、疲劳强度、耐腐蚀性、配合性质等使用性能有不同程度的影响。