第五章物理气相淀积
物理气相淀积(PhysicalVaporDeposition)

物理气相淀积(PhysicalVaporDeposition)物理气相淀积(PhysicalVaporDeposition)PVD概述真空系统及真空的获得真空蒸镀溅射PVD金属及化合物薄膜物理气相淀积(Physicalvapordeposition,PVD)是利用某种物理过程实现物质转移,将原子或分子由(靶)源气相转移到衬底表面形成薄膜的过程。
真空蒸发和溅射方法真空蒸发法制备薄膜的基本原理真空蒸发即利用蒸发材料在高温时所具有的饱和蒸汽压进行薄膜制备。
在真空条件下,加热蒸发源,使原子或分子从蒸发源表面逸出,形成蒸汽流并入射到硅片衬底表面凝结形成固态薄膜。
制备的一般是多晶金属薄膜。
真空系统及真空的获得低真空:1~760Torr,102~105Pa中真空:10-3~1Torr,10-1~102Pa高真空:10-7~10-3Torr,10-5~10-1Pa超高真空:<10-7T orr,<10-5Pa气体流动及导率----气体动力学气流用标准体积来测量,指相同气体,在0℃和1atm下所占的体积。
气体流动及导率----气体动力学C与电导率一样并联相加;串联时倒数相加;若大量气体流过真空系统,要保持腔体压力接近泵的压力,就要求真空系统有大的传导率----管道直径;泵放置位置;真空的获得方法初、中真空度的获得用活塞/叶片/柱塞/隔膜的机械运动将气体正向移位.有三步骤:捕捉气体-压缩气体-排出气体.压缩比真空的获得方法旋片泵旋片泵主要由定子、转子、旋片、定盖、弹簧等零件组成。
其结构是利用偏心地装在定子腔内的转子和转子槽内滑动的借助弹簧张力和离心力紧贴在定子内壁的两块旋片。
真空的获得方法在泵腔内,有二个“8”字形的转子相互垂直地安装在一对平行轴上,由传动比为1的一对齿轮带动作彼此反向的同步旋转运动。
压缩比30:1真空的获得方法真空的获得方法高、超高真空度的获得扩散泵靠高速蒸汽射流来携带气体以达到抽气的目的.适用于高真空,但入口真空也要求较高,一般前要接机械泵.压缩比可达108涡轮分子泵1958年,联邦德国的W.贝克首次提出有实用价值的涡轮分子泵。
物理气相淀积公开课一等奖优质课大赛微课获奖课件

• 溅射与热蒸发区分
• 热蒸发是由能量转化引发, 溅射含有动量转换。
• 溅射过程都是建立在辉光放电基础上, 即射向固体 表面离子都是起源于气体放电, 只是不同溅射技术 所采取辉光放电方式有所不同。
-10-18
25
第25页
一、直流辉光放电
电压V/V
• 在一圆柱形玻璃管内两端装上两个平板电极, 里面
充以气压约为几Pa到几十Pa气体, 在电极加上直
物质蒸发温度。
-10-18
10
第10页
四、真空度与分子平均自由程
1. 淀积高纯薄膜需在高真空度系统中进行原因
2. 1) 真空度高, 确保被蒸发原子或分子在真空中输 运为直线, 可有效淀积在衬底上;
3. 2) 真空度低, 则残余气体中氧和水汽会使金属原 子或分子在输运过程中发生氧化, 同时也将使加 热衬底表面发生氧化;
• 自持放电
• 气体击穿后, 电子和正离子是起源于电子碰撞和正 离子轰击, 即不存在自然电离源也将继续下去, 这 种放电方式称为自持放电;
-•10-辉18 光放电属于自持放电。
32
第32页
4.反常辉光放电区
• 电流电压特性
• 放电电压、电流同时增大。
• 原因
• 整个阴极所有由辉光放电覆盖后, 只有增大功率才 干增长阴极电流密度, 从而增大电流。
• 被蒸发材料放置于水冷坩埚, 可避免容器材料蒸发、 容器材料与蒸发材料反应, 实现高纯薄膜制备;
• 热效率高, 热量直接加到蒸发材料表面, 热传导和
-10热-18辐射损失少。
19
第19页
图5.4 电子束蒸发源示意图
-10-18
20
第20页
• 缺点 • 电子枪发出一次电子和蒸发材料发出二次电子, 使
Chap5物理气相沉积

• ð溅射:真空系统中充入惰性气体ห้องสมุดไป่ตู้在高压电 场作用下,气体放电形成的离子被强电场加速, 轰击靶材料,使靶原子逸出并被溅射到晶片上
1
蒸 发 原 理 图
反应 • 3. 射频辉光放电
15
5.4 溅射
• 溅射是利用等离子体中的离子,对 被溅射物体电极进行轰击,使气相等离 子体内具有被溅射镀物的粒子,使其淀 积到硅片表面并形成薄膜的一种PVD 方法,因此将高纯粒子从某种物质的表 面撞击出原子的物理过程叫溅射。
• 溅射是目前大规模集成电路制造中 应用得最广泛的一种镀膜方法,它可以 用来淀积不同的金属,包括铝、铝合金、 钛、钨钛合金。
造成铝层氧化有以下原因:
1)钨丝纯度不够,杂质含量太多或清洁处理得 不够;
2)真空度低或真空零件不干净;
3)蒸发时挡板打开的过早,即在,铝溶液表面 的氧化层还未去掉时就开始蒸发。因而把赃物也 蒸发上去了;
4)衬底加热温度较高,并且取片过快;
5)扩散泵抽气率不高,在蒸发时,各部分加热 后放出的气体未及时抽走;
2
• 在薄膜淀积技术发展的最初阶段,蒸 发法用的多。其优点:较高的淀积速率、 相对高的真空度、较高的薄膜质量。
• 缺点:台阶覆盖能力差,淀积多元化 合金薄膜时组分难以控制。
• 溅射法优点:淀积多源化合金薄膜时, 化学成分容易控制、淀积的薄层与衬底 附着性好等。
• 溅射技术制备薄膜的技术已基本取 代真空蒸发法。
这样可以获得质量更好的薄膜。
17
• 一、溅射特性 • 1. 溅射阈值:10~30ev取决于靶材料 • 2. 溅射率:被溅射出来的原子数与入
硅工艺 第五章 物理气相淀积
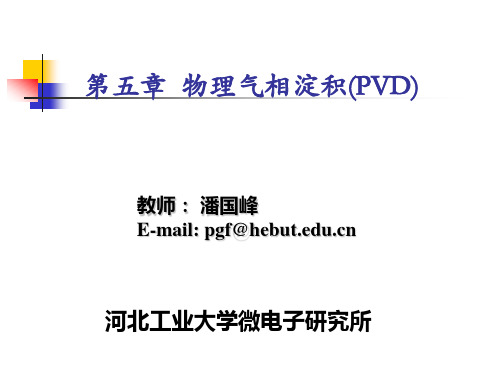
5.3.3 射频辉光放电
(1)射频溅射设备 (2)射频溅射的基本原理
两极间接上射频(5-30MHz,国际上多 采用13.56MHz)电源后,两极间等离子体中 不断振荡运动的电子从高频电场中获得足够的 能量,并更有效地与气体分子发生碰撞,并使 后者电离,产生大量的离子和电子,此时不再 需要二次电子来维持放电过程,射频溅射可以 在低压(1Pa左右)下进行,沉积速率也较二 极溅射为高;高频电场可以经由其他阻抗形式 耦合进入沉积室,而不必再要求电极一定要是 导体;由于射频方法可以在靶材上产生自偏压 效应,即在射频电场作用的同时,靶材会自动 处于一个较大的负电位下,从而导致气体离子 对其产生自发的轰击和溅射,而在衬底上自偏 压效应很小,气体离子对其产生的轰击和溅射 可以忽略,主要是沉积过程,因此,沉积速率 较快。
高真空 阀
高真空泵
机械泵
汽化热(△H):真空蒸发系统的能源将蒸发材料加热到足够温度,使其 原子或分子获得足够能量,克服固相(或液相)的原子束缚而汽化 到真空环境中,并形成具一定动能的气相原子或分子,该能量即为 汽化热。
必须保持真空环境的理由:
(1)如果真空度很低,被蒸发的原子或分子在输运过程中不断与残余 气体的分子碰撞,运动方向不断改变,很难保证被蒸发的原子或分 子有效地淀积在衬底上。
第五章 物理气相淀积(PVD)
教师: 潘国峰 E-mail: pgf@
河北工业大学微电子研究所
引言
薄膜淀积是芯片加工过程中一个至关重要的工艺步骤,通过淀积 工艺可以在硅片上生长导各种导电薄膜层和绝缘薄膜层,比如金属 (Cu、W、Au)、多晶硅、二氧化硅(SiO2)以及氮化硅(Si3N4); 作为欧姆接触、互连栅电极和肖特基二极管等方面的薄膜;铂、钛等在 多层互连中常用作粘附或阻挡层薄膜。 各种不同类型的薄膜淀积到硅片上,在某些情况下,这些薄膜成为器 件结构中的一个完整部分,另外一些薄膜则充当了工艺过程中的牺牲层, 并在后续工艺中被去掉。
物理气相淀积--溅射
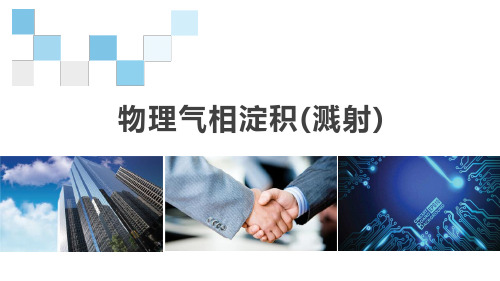
物理气相淀积(溅射)物理气相淀积的主要方法蒸发电阻丝加热蒸发电子束蒸发溅射直流溅射射频溅射磁控溅射利用等离子体中的离子,对被溅镀物体电极进行轰击,使气体等离子体内具有被溅镀物的粒子,这些粒子沉积到晶片上就形成薄膜。
溅射方法直流溅射射频溅射磁控溅射溅射工艺的原理溅射的步骤A. 在高真空腔等离子体中产生正氩离子,并向具有负电势的靶材料加速。
B. 在加速过程中离子获得动量,并轰击靶。
C. 离子通过物理过程从靶上撞击出溅射原子,靶具有所需要的材料组份D. 被撞击出的原子迁移到硅片表面E. 被溅射的原子在硅片表面凝聚并形成薄膜。
F. 额外材料由真空泵抽走。
A. 能够在直径为200毫米或更大的硅片上控制淀积均匀薄膜。
E. 能够淀积高温熔化和难熔金属C. 具有淀积并保持复杂合金原组份的能力F. 具有多腔集成设备,能够在淀积金属前清除硅片表面沾污和本身的氧化层。
D. 台阶覆盖能力优于蒸发B. 膜厚容易控制,只要调节时间就可以得到所需的膜厚溅射的特点简单平行金属板直流溅射系统++++++-+阴极阳极金属靶衬底1)电场产生Ar +离子2)高能Ar +撞击金属靶3)将金属原子从靶中撞出6)用真空泵将多余的物质从腔中抽走尾气进气4)金属原子向衬底迁移5)金属原子淀积在衬底上直流溅射1)直流溅射的原理:①电场产生Ar+离子②高能Ar+与金属靶撞击③高能Ar+将金属原子从靶中撞出④金属原子向衬底迁移⑤金属原子淀积在衬底上⑥用真空泵将多余的物质从腔中抽走2)特点:直流溅射的优点是设备简单,但它的缺点之一是不能淀积绝缘介质,因为会造成放电停止。
衬底表面会受二次电子的轰击,造成表面发热和损伤。
+阴极绝缘材料阳极捕获一个电子成中性原子-阴极电位迅速升高,使两极之间电位减小,放电终止射频溅射1)射频溅射的原理:在电极的两极之间加上交流信号,使绝缘体表面维持电负性,使辉光放电维持,从而使淀积维持。
射频溅射的实质是交流溅射,只是工作频率为13.56MHz,落在射频范围内,因此称为射频溅射。
物理气相沉积CVD演示课件

2013.6.28
1 ? Sputter工艺介绍 2 ? Sputter成膜与关键参数 3 ? Sputter 常见异常介绍 4 ? Sputter工艺应用
Copyright ? 昆山工研院新型平板显示技术中心有限公司
Summary
1
1.Sputter 工艺介绍
?PVD---物理气相沉积技术(Physical Vapor Deposition) ?定义
ITO之后
ITO之前
A:passivation之后 B:平坦化层 C:平坦化层退火 D:平坦化层Ashing E:ITO sputter之后 F:ITO退火之后
ITO sputter之后Ioff上升很明显,退火之后会有一点下降,说明sputter工艺会造成 Ioff上升。
Copyright ? 昆山工研院新型平板显示技术中心有限公司
Copyright ? 昆山工研院新型平板显示技术中心有限公司
14
? Splash
?产生原因
治具
3. Sputter 常见异常介绍
靶材局部散热不均,造成融化滴在基板上
Oxide or Void
Target
Heated area
arcing
Melted particle Ar+
慧星狀
圆形
Copyright ? 昆山工研院新型平板显示技术中心有限公司
1.Sputter 工艺介绍
(1)对于任何待镀材料,只要能制作成靶材,就可以实现溅射; (2)溅射所获得的薄膜与基板间附着力较好; (3)溅射所得到的薄膜纯度高,致密性好; (4)溅射工艺重复性好,膜厚可控;同时可以实现大面积镀膜;
溅射存在缺点: 沉积速率低;基板升温严重。
第五章___物理气相淀积

溅射镀膜的基本原理
用高能粒子(经电场加速的正离子)冲击作为阴极 的固态靶,靶原子与这些高能粒子交换能量后从表面 飞出,淀积在作为阳极的硅片上,形成薄膜。
高真空蒸发系统
各种蒸发装置
三. 电阻式加热特点和局限性
(1)特点: ① 设备简单、操作方便、造价低 ② 成膜速率快、效率高 ③ 膜厚便于控制 (2)缺点:
① 坩埚、加热元件以及各种支撑部件可能造成污染
② 电阻加热的加热功率和加热温度受到限制;
③ 不适用于高纯和难熔物质的蒸发; ④ 蒸发源寿命短,不能长时间连续蒸发。
特点:
1. 空心阴极可以提供数安培至数百安培的高强度电子 流,从而提高薄膜的沉积速度; 2. 大电流蒸发出来的物质原子进一步发生部分的离化, 从而生成大量的被蒸发物质的离子。如果在阳极与 衬底之间加上一定幅度的偏臵电压的话,被蒸发物 质的离子可以轰击衬底,从而影响薄膜的沉积过程, 改善薄膜的微观组织。
加速(数千伏) 偏转(横向磁场)
轰击坩埚
薄膜沉积
磁场偏转法的使用可以避免灯丝材料的 蒸发对于沉积过程可能造成的污染。
优点: 1、能克服电阻加热方法可能受到坩埚,加热体以及 各种支撑部件的污染的缺点。 2、能克服电阻加热方法受到加热功率或温度的限制 可蒸发高熔点材料薄膜(3000℃) 。 3、在同一蒸发沉积装臵中可以安臵多个坩埚,这使 得人们可以同时或分别对多种不同的材料进行蒸发。
• 在加速过程中获得动量,并轰击靶;
• 离子通过物理过程从靶上撞击出(溅射)原子,靶具 有想要的材料组分;
• 被撞击出(溅射)的原子迁移到硅片表面(阳极); • 被溅射的原子在硅片表面凝聚形成薄膜,与靶材料相 比,薄膜具有与它基本相同的材料组分; • 额外材料由真空泵抽走。
5.2 气相沉积法

气相沉积技术是一种在基体上形成一层功能膜 的技术,它是利用气相中发生的物理、化学反应在 材料表面沉积单层或多层薄膜,从而使材料获得所 需的各种优异性能。 例:用TiN、TiC等超硬镀层涂敷刀具、模具等表 面,由于化学稳定性好,摩擦系数小,具有优良的 耐热、耐磨、抗氧化、耐冲击等性能,既可以提高 刀具、模具等的工作特性,又可以提高寿命,一般 可使刀具寿命提高3-10倍。
岛 薄膜
成膜机理
真空蒸发所得到的薄膜,一般都是多晶膜或无定形膜,经历 成核和成膜两个过程。
• 蒸发的原子(或分子)碰撞到基片时,或是永久附着在 基片上,或是吸附后再蒸发而离开基片,其中有一部分 直接从基片表面反射回去。
• 粘附在基片表面的原子(或分子)由于热运动可沿表面 移动,如碰上其它原子便积聚成团。这种团最易于发生 在基片表面应力高的地方,或在晶体衬底的解理阶梯上, 因为这使吸附原子的自由能最小。这就是成核过程。
Heat decomposition
金属有机化合物与氢化物体系的热分解
Ga(CH3)3 AsH3 630-675℃ GaAs 3CH4 Zn(C2H5)2 H2Se 725750℃ ZnSe 2C2H6
广泛用于制备化合物半导体薄膜。
33
氢还原反应 ---利用氢气将一些元素从其卤化物中还原出来
例如二氧化硅可采用下面几个反应: SiCl4 (g) O2 (g) SiO2 (s) 2Cl2 (g) SiH4 (g) O2 (g) SiO2 (s) 2H2 (g)
SiCl4 (g) 2CO2 (g) 2H2 (g) SiO2 (s) 4HCl(g) 2CO(g)
Chapter5 Preparation of Materials
物理气相淀积PVD+溅射
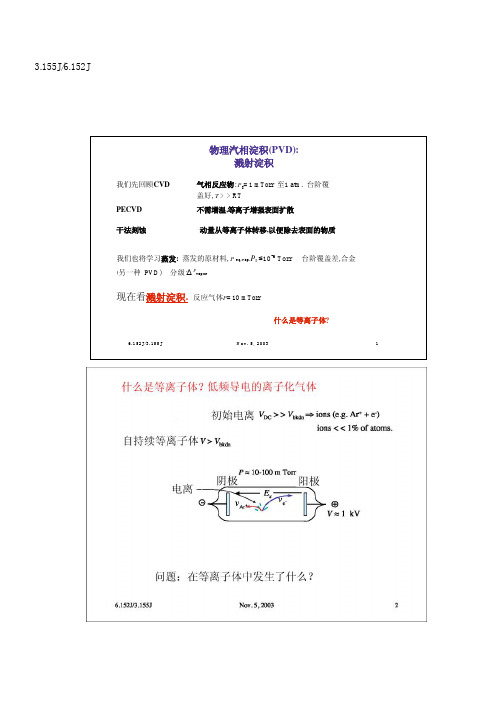
Ta rg et
F . C . C. 储 量 : 溅 射 的 为 1 3 . 5 6 M H z f or 6.152J/3.155J Nov. 5, 2003 18
3.155J/6.152J
3.155J/6.152J
3.155J/6.152J
靶上源材料的 溅射速率 很关键. 典型的为0.1 - 3 原子/Ar,随着材料的不同, 溅
射速率稍有不同
蒸 汽 压 或源不重要
(对于不同的材料,这个相差很大).
2) 中性靶(Al),被 踢掉.
-
~V≈ 1 k V
6) Al 的一些物理再溅射, 由Ar cos q
6.152J/3.155J Nov.5,2003 11
溅射效率
#靶上的原子,分子数 S=溅射效率= #入射的离子
πd 2
#/面积
每层受 激发的 数量
随意移动到 表面 Eb=束缚能
Oring, Fig. 3.18, Table 3-4
溅射速率取决于入射角,相对质量,动能.
6.152J/3.155J
Nov. 5, 2003 12
3.155J/6.152J
6.152J/3.155J Nov. 5, 2003 17
RF 等离子溅射
低f时 , 等离子传导
因 此 ,等 离 子 内 V = 0
w p~ 1 0 7 s- 1
Ta rg et
由于高的e-速度,等离子体电势> 0 . 电势此时是对称的. 靶的迁移率仍然足够大=>每1/2个周期电极一次
小的靶 =>更高的场
3.155J/6.152J
物理汽相淀积(PVD): 溅射淀积
我们先回顾CVD 气相反应物: Pg≈ 1 mTorr 至1 atm. 台阶覆 盖好, T > > RT PECVD 干法刻蚀 不需增温,等离子增强表面扩散 动量从等离子体转移,以便除去表面的物质
工艺课件物理气相淀积详解演示文稿

的体积。1标准升是273K、1atm下占据1升空间的气体。
➢入射气体流量为Q,假定气体以均匀压力P1流过真空室,导率为C的导 管与真空泵相连,泵入口压力为P2,气体导管的导率C定义为:
C Q
P1 - P2
➢ C与电导率一样并联相加;串联时倒数相
加;
阀门
➢ 若大量气体流过真空系统,要保持腔体
压力接近泵的压力,就要求真空系统有
➢ 电离规:热阴极发射电子电离气体分子,离子被收 集集所收集,根据收集的离子流量来测量气体的压 强。
➢ 复合真空计:由热偶规与热阴极电力计组成。 ➢ B-A规(热阴极电离规) :一种阴极与收集极倒
置的热阴极电离计。
第十一页,共39页。
8.3真空蒸镀
➢ 真空蒸镀又称真空蒸发,将装有衬底的真空室抽吸至高真空度 ,加热原材料使其升华,形成源蒸汽流入射到衬底表面,在衬 底凝结形成固态薄膜的一种工艺。
扩散泵剖面照片
第九页,共39页。
8.2.2真空的获得方法
涡轮分子泵
➢ 1958年,联邦德国的W.贝克首次提出有实用价值
的涡轮分子泵。
➢ 原理:利用高速旋转的动叶轮将动量传给气体 分子,使气体产生定向流动而抽气的真空泵。
➢ 涡轮分子泵主要由泵体、带叶片的转子(即动 叶轮)、静叶轮和驱动系统等组成。
➢ 动叶轮外缘的线速度高达气体分子热运动的 速度(一般为150~400米/秒)。具有这样的
机械运动将气体正向移位。 ➢ 三个步骤:捕捉气体、压缩气体、排出气体。 ➢ 机械泵也称为压缩泵。
➢ 压缩比:压缩泵气体出口和入口的压力比成为压缩比。
第七页,共39页。
8.2.2真空的获得方法
➢ 旋转叶片机械泵主要由定子、转子、旋片 、定盖、弹簧等零件组成。
第五章 物理气相淀积(上)

真空度:低于大气压的气体稀薄程度。 真空区域划分:粗真空、低真空、高真空、超高真空
1) 粗真空(1×105Pa~ 1×102Pa),气态空间的特性和 大气差不多,气体分子的平均自由程短; 2) 低真空(1×102Pa~ 1×10-1Pa),每立方厘米的气体 分子数为1016~ 1013个,此真空区域由于分子数减少, 分子的平均自由程和容器的尺寸相当; 3) 高真空(1×10-1Pa~ 1×10-6Pa),气体分子的平均 自由程大于一般容器的线度。 4) 超高真空(<1×10-6Pa),此时每立方厘米的气体分 子数在1010个以下,超高真空的用途之一是得到纯净的 气体,其二是可获得纯净的固体表面。
3) 过程:右图式出了机械泵转 子在连续旋转过程中的四个 典型位置,图1表示正在吸 气,同时把上一周期吸入的 气体逐步压缩;图2表示吸 气截至,此时泵的吸气量达 最大并将开始压缩;图3表 示吸气空间另一次吸气,而 排气空间继续压缩;图4表 示排气空间内的气体已被压 缩到当压强超过一个大气压 的时候,气体推开排气阀由 排气管道排出。如此不断进 行吸气、压缩和排气,于是 和机械泵连接的真空容器便 获得了真空。
第五章
物理气相淀积
内容
概述
真空技术
蒸发 溅射 薄膜淀积机理
概述
形成薄膜技术:薄膜生长技术、薄膜淀积技术 薄膜生长技术:专指衬底材料也是形成薄膜的元素之一, (如硅的热氧化生长二氧化硅) 薄膜淀积技术:薄膜形成过程中不消耗晶片或衬底材料,
薄膜淀积技术一般可分为两类:
kT 2d P
2
式中d为分子直径,P为腔体压强; n为单位体积内的气体分子数;式 中m为气体分子质量,
L 注意:这些公式只是在 时适用,L为腔体的特征长度
物理气相沉积的基本过程
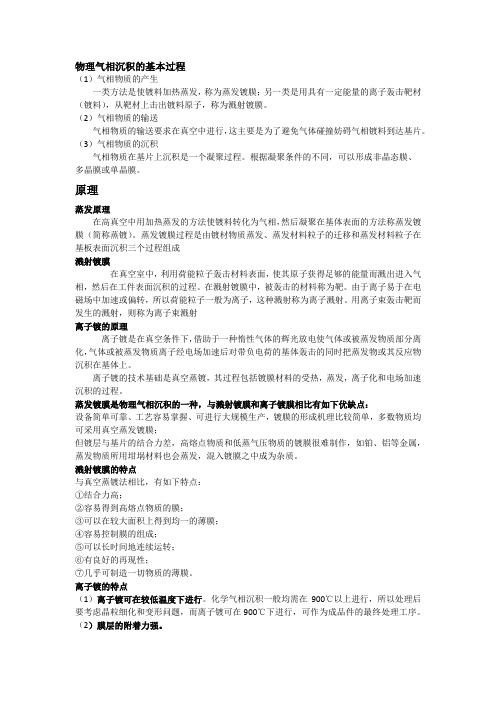
物理气相沉积的基本过程(1)气相物质的产生一类方法是使镀料加热蒸发,称为蒸发镀膜;另一类是用具有一定能量的离子轰击靶材(镀料),从靶材上击出镀料原子,称为溅射镀膜。
(2)气相物质的输送气相物质的输送要求在真空中进行,这主要是为了避免气体碰撞妨碍气相镀料到达基片。
(3)气相物质的沉积气相物质在基片上沉积是一个凝聚过程。
根据凝聚条件的不同,可以形成非晶态膜、多晶膜或单晶膜。
原理蒸发原理在高真空中用加热蒸发的方法使镀料转化为气相,然后凝聚在基体表面的方法称蒸发镀膜(简称蒸镀)。
蒸发镀膜过程是由镀材物质蒸发、蒸发材料粒子的迁移和蒸发材料粒子在基板表面沉积三个过程组成溅射镀膜在真空室中,利用荷能粒子轰击材料表面,使其原子获得足够的能量而溅出进入气相,然后在工件表面沉积的过程。
在溅射镀膜中,被轰击的材料称为靶。
由于离子易于在电磁场中加速或偏转,所以荷能粒子一般为离子,这种溅射称为离子溅射。
用离子束轰击靶而发生的溅射,则称为离子束溅射离子镀的原理离子镀是在真空条件下,借助于一种惰性气体的辉光放电使气体或被蒸发物质部分离化,气体或被蒸发物质离子经电场加速后对带负电荷的基体轰击的同时把蒸发物或其反应物沉积在基体上。
离子镀的技术基础是真空蒸镀,其过程包括镀膜材料的受热,蒸发,离子化和电场加速沉积的过程。
蒸发镀膜是物理气相沉积的一种,与溅射镀膜和离子镀膜相比有如下优缺点:设备简单可靠、工艺容易掌握、可进行大规模生产,镀膜的形成机理比较简单,多数物质均可采用真空蒸发镀膜;但镀层与基片的结合力差,高熔点物质和低蒸气压物质的镀膜很难制作,如铂、铝等金属,蒸发物质所用坩埚材料也会蒸发,混入镀膜之中成为杂质。
溅射镀膜的特点与真空蒸镀法相比,有如下特点:①结合力高;②容易得到高熔点物质的膜;③可以在较大面积上得到均一的薄膜;④容易控制膜的组成;⑤可以长时间地连续运转;⑥有良好的再现性;⑦几乎可制造一切物质的薄膜。
离子镀的特点(1)离子镀可在较低温度下进行。
PVD-物理汽相淀积
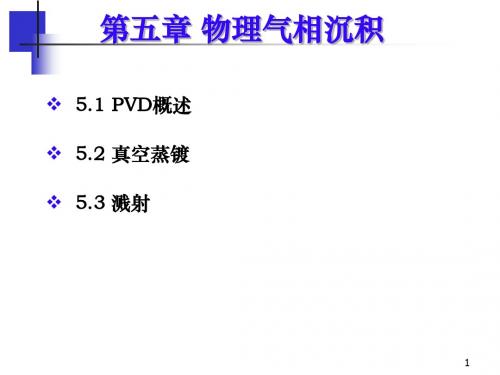
5.3 溅射
气体辉光放电
溅射
溅射的过程是建立在辉光放电的基础上的,即射向固体表 面的离子来源于气体放电,因正常辉光放电时的电流密度 比较小,溅射选在反常辉光放电区。
等离子体
放电击穿之后的气体具有一定的导电性,这种气体为等离 子体。等离子体是一种由正离子、电子、光子以及原子、 原子团、分子和它们的激发态所组成的混合气体。
与入射离子种类的关系
入射离子原子量越大,溅射率越高 凡电子壳层填满的元素作为入射离子,则溅射率最大。(惰 性气体被选为入射离子。)
5.3 溅射
溅射特性
溅射率
与被溅射物质的种类有关
一般来说随靶元素原子序数增加而增大;
与入射离子入射角的关系
随入射角的增加,溅射率以1/cosθ规律增加。 当入射角接近80o时,溅射率迅速下降。
气相输运过程:源蒸气从源到衬底表面之间的质量输
运过程。蒸气原子在飞行过程中可能与真空室内的残余 气体分子发生碰撞,两次碰撞之间飞行的平均距离为平 均自由程;
成膜过程:到达衬底的蒸发原子在衬底表面先成核再
成膜的过程。
5.2 真空蒸镀
汽化热与蒸汽热
汽化热:将蒸发源材料加热到足够高的温度,使 其原子或分子获得足够的能量,克服固相的原子 束缚而蒸发到真空中,并形成具有一定动能的气 相原子或分子,该能量为汽化热ΔH,常用金属 的ΔH为4eV; 蒸汽压:在一定温度下,真空室内蒸发物质的蒸 汽与固态或液态平衡时所表现出来的压力为饱和 蒸汽压;
5.3 溅射
气体辉光放电
模型:一个圆柱形玻璃管内的两端装上两个平板
电极,里面充以气压约为几Pa到几十Pa的气体, 在电极上加上直流电压。
5.3 溅射
- 1、下载文档前请自行甄别文档内容的完整性,平台不提供额外的编辑、内容补充、找答案等附加服务。
- 2、"仅部分预览"的文档,不可在线预览部分如存在完整性等问题,可反馈申请退款(可完整预览的文档不适用该条件!)。
- 3、如文档侵犯您的权益,请联系客服反馈,我们会尽快为您处理(人工客服工作时间:9:00-18:30)。
5.1.5 多组分蒸发
如,合金蒸发 方法:(按蒸发源分类)
①单源蒸发:具有薄膜组分比例的单一合金靶; 靶源的要求:各组分蒸汽压接近;
②多源同时蒸发:多种靶源,不同温度,同时蒸发; ③多源顺序蒸发:多种靶源,不同温度,顺序蒸发,
最后高温退火; 工艺关键:根据薄膜组分控制各层厚度;
真空室内装置简单,容易获得高真空度
5.2.4 高频感应加热源
优点: ①蒸发速率快:
蒸发面积大; ②温度控制精确、均匀; ③工艺简便; 缺点: ①成本高; ②电磁干扰。
5.4 溅射
Ar+离子能量和动量转移将使 表面原子脱离化学键束缚
原理:气体辉光放电产生等离子体→具有能量的离 子轰击靶材→ 靶材原子获得能量从靶表面逸出-被溅 射出→溅射原子淀积在表面。
利用蒸发材料熔化时产生的蒸气进行薄膜淀积; 优点:工艺及设备简单,淀积速率快; 缺点:台阶覆盖差。
5.1.1 真空蒸发设备
①真空系统 ②蒸发系统 ③基板及加热系统
基板 蒸发源 真空系统
蒸发淀积过程
①加热蒸发:加热蒸发源(固态),产生蒸气; ②输运:气化的原子、分子扩散到基片表面; ③淀积:气化的原子、分子在表面
使用时,直接删除本页!
精品课件,你值得拥有! 精品课件,你值得拥有!
使用时,直接删除本页!
精品课件,你值得拥有! 精品课件,你值得拥有!
使用时,直接删除本页!
磁控溅射系统
5.1.5 多组分蒸发
5.2 蒸发源
(按加热方式分类) ①电阻加热源 ②电子束加热源 ③高频感应加热源 ④激光加热源
5.2.1 电阻加热源
直接加热源:加热体与蒸发源的载体是同一物体; 加热体-W、Mo、石墨。
间接加热源:坩埚盛放蒸发源; 坩埚-高温陶瓷、石墨。
对加热体材料的要求:不产生污染 ①熔点高:高于蒸发源的蒸发温度; ②饱和蒸汽压低:低于蒸发源; ③化学性能稳定:不发生化学反应,不形成合金。 优点:工艺简单,蒸发速率快;
5.4.3 溅射方法
2. RF溅射 原理:高频电场经其他阻抗形式耦合进入淀积室; 特点:适于各种金属与非金属靶材;
5.4.3 溅射方法
3.磁控溅射 原理:
磁场在靶材表面与电场垂直, 电子沿电场方向加速、绕磁 场方向螺旋前进,提 高了电子碰撞电离效率。 特点:淀积速率最高;
精品课件,你值得拥有! 精品课件,你值得拥有!
缺点:难以制备高熔点、高纯度薄膜。
5.2.2 电子束蒸发源
原理:电子轰击蒸发材料, 使其熔化蒸发。
特点:淀积高熔点Βιβλιοθήκη 高纯薄膜;5.2.2 电子束蒸发源
优点: ①蒸发温度高:能量密度高于电阻源,可蒸发3000 度以上的材料:W,Mo,Ge,SiO2,Al2O3; ②高纯度淀积:水冷坩埚可避免容器材料的蒸发; ③热效率高:热传导和热辐射损失少。
缺点: ①一次电子和二次电子使蒸发原子电离,影响薄膜质 量; ②设备及工艺复杂。
5.2.3 激光加热
可蒸发任何高熔点的材料(聚焦激光束功率密度 高达106W/cm2);
被蒸发材料局部受热而汽化,高纯度薄膜,(光 斑很小,防止了坩锅材料受热的污染);
淀积含有不同熔点材料的化合物薄膜可保证成分 比例(功率密度高)
特点:被溅射出的原子动能很大,10-50eV(蒸发: 0.1-0.2eV);还可实现离子注入。
优点:台阶覆盖好(迁移能力强)。
5.4.3 溅射方法
直流、射频、磁控、反应、 离子束、偏压等溅射;
1.直流溅射 (又称阴极溅射或直流二级溅射 ,常用Ar气作为工作气体。) 溅射靶:阴极 衬底:阳极(接地) 工作气体:Ar气 要求:靶材导电性好 特点:只适于金属靶材
第五章 物理气相淀积
PVD:physical vapor deposition 淀积特点:物理过程; 技术:
①蒸发:早期工艺制备金属薄膜; ②溅射:已取代蒸发。
5.1 真空蒸发的基本原理
材料的三态:solid,liquid,gas; 蒸气:任何温度下,材料表面都存在自身的气体; 蒸气压:平衡时的饱和蒸气压; 升华:低于熔化温度时,产生蒸气的过程; 蒸发:熔化时,产生蒸气的过程; 真空蒸发: