一份手机零件的材料及技术要求
手机常用材料和工艺介绍2019-PPT精品文档

3). 镍
• 性能:可做的非常薄,通常厚度0.2,另外超薄电 铸厚度可做到0.05mm,缺点超薄电铸只能做平 面产品,普通电铸也不能做复杂的弧面 • 用途:在手机上常用作装饰件,铭牌。可以在装 饰件表面做出高光、拉丝、和雾面、镭射等效果
4). 镁
• 性能:在很薄的情况下达到很好的强度,缺点是 模具价格非常高,周期长。 • 用途:常用在一些要求比较薄的产品上。例如笔 记本电脑的液晶支撑架。在手机上应用到一些品 牌机的高端手机上。例如:Nokia 的超薄翻盖机 N76。
1). 电镀-2
• 用途:水电镀广泛用于家庭的生活用品,汽车装 饰件等。在手机上常用于装饰件,按键等。真空 电镀由于对材料的选择性不高,在手机上可用于 水电镀不方便或者不能镀出的颜色的地方。例如 手机的壳体,镜片等。真空镀也可作半透效果。
2). 电铸
• 电铸实际上不是一种工艺,很多人容易把电铸和电镀混淆起来。 • 电铸的概念:利用金属的电解沉积原理来精确复制某些复杂或特殊形状工件的特种加 工方法。它是电镀的特殊应用。 • 电铸的基本原理:把预先按所需形状制成的原模作为阴极,用电铸材料作为阳极,一 同放入与阳极材料相同的金属盐溶液中,通以直流电。在电解作用下,原模表面逐渐 沉积出金属电铸层,达到所需的厚度后从溶液中取出,将电铸层与原模分离,便获得 与原模形状相对应的金属复制件。原模的材料有石膏、蜡、塑料、低熔点合金、不锈 钢和铝等。电铸的金属通常有铜、镍和铁3种,有时也用金、银、铂镍-钴、钴-钨等合金, 但以镍的电铸应用最广。 • 手机上应用电铸工艺制作要求比较精细的图案,例如按键上的 复杂符号,电铸镍片等。
5). TPU
• 性能:流动性好,耐拉伸 • 用途:在手机上广泛应用杂件。ቤተ መጻሕፍቲ ባይዱ如:各种螺丝 塞,USB 塞等。
(工艺技术)手机金属部件设计及制造工艺

手机金属部件设计及制造工艺1.1 前言金属部件在手机结构设计中发挥越来越大的作用.某些手机的翻盖上壳采用的是铝合金冲压成形再进行阳极氧化的制造工艺而翻盖下壳则是采用镁合金射铸工艺成型,由于金属的强度较高,因此可以实现塑件无法实现的结构。
本章将介绍目前手机中常用的金属部件的结构设计及其制造工艺。
1.2 镁合金成型工艺在手机结构件中,镁合金由于其重量轻,强度高等特点已大量的被采用。
镁合金零件目前主要采用压铸(die-casting)和半固态射铸法(thixomolding)进行生产。
本节主要介绍镁合金压铸工艺和半固态射铸工艺特点及设计注意事项。
1.2.1 镁合金压铸工艺压铸机通常分为热室(hot-chamber)的与冷室的(cold-chamber)两类。
前者的优点是:模具中积流的残料少,铸件表面平整,内部气孔、疏松少,但设备维护费较高。
镁合金熔体对钢的浸蚀并不特别严重,因此,除采用热室压铸机制造零部件外,也可选用冷室压铸机。
通常,可根据零部件大小与铸件特性来选择压铸工艺。
如铸造大的与较大的汽车零件;若压铸机的压力较小,则只好用冷室压铸;若压铸机较多,大中小结构搭配合理,还是宜选用热室压铸法。
而铸造轻薄的3C(笔记本电脑,照相机,摄像机)机壳零部件与自动控制阀的细小零件,则可选热室压铸工艺,因其压铸速度快,成品率也较高(此处成品率=铸件质量/所消耗的熔体质量)。
1.2.2 镁合金半固态射铸工艺半固态射铸是美国道化学公司(Dow chemical Co.0)开发的一种高新技术,在工业发达国家是一项成熟的工艺,在我国台湾省此项技术已趋于成熟。
我国此项技术已经开始进入生产阶段,但是模具国内仍然无法自主设计和开发。
它的制造原理是将镁合金粒料吸入料管中,加热的同时通过螺杆的高速运转产生触变现象,射出时以层流的方式充填模具,形成结构致密的产品。
如图5-1所示为镁合金半固态射铸系统示意图。
图5-1 镁合金半固态射铸系统示意图镁合金半固态射铸法的优点是:1.零件表面质量高,低气孔率,高致密性,抗腐蚀性能优良;2.可铸造壁厚薄达0.7~0.8mm的轻薄件,尺寸精度高,稳定性好;3.强度高,刚性好;4.不需要熔炼炉,不但安全性高、劳动环境好而且不产生热公害;5.不使用对臭氧层有严重破坏作用的六氟化硫气体,不会形成重金属残渣污染;6.铸件收缩量小;7.铸件的表面良品率高,可达50%或更高些,此处所说的良品是压铸工序无表面缺陷的。
手机结构件技术标准

手机结构件技术标准(总14页)-CAL-FENGHAI.-(YICAI)-Company One1-CAL-本页仅作为文档封面,使用请直接删除技术文件技术文件名称:手机结构件技术标准技术文件编号:版本:共 14 页(包括封面)拟制审核会签标准化批准目录1、前言2、参考标准3、规格尺寸4、技术标准定义检验条件和环境技术标准塑料件及喷漆件技术标准五金件技术标准橡胶件技术标准天线技术标准镜片技术标准LCD组件技术标准5、检验规则检验、检验批及不合格分类定义抽样方法检验6、标志标志标签7、包装、运输、贮存包装运输贮存8、附件1、前言为方便手机的结构件供应的检验,保证手机的物料符合设计要求,特制定本技术标准。
2、引用标准GB/T14436 工业产品保证文件总则GB 191 运输包装收发货标志GB/T 6388-1986 运输包装收发货标志GB/T 2828-1987 逐批检查计数抽样程序及抽样表其他相关行业标准3、规格尺寸对照图纸上的规格检查重点尺寸,应符合要求。
4、技术要求定义不良或缺陷定义点缺陷具有点形状的缺陷,测量时以其最大直径为尺寸。
颗粒喷漆件表面上有附着的细小颗粒。
堆漆喷漆件表面出现局部的油漆堆积现象。
阴影喷漆件或塑料件表面出现的颜色比周围暗的区域。
桔纹喷漆件或镀件表面出现大面积细小的像桔子皮似的凹凸不平。
露底喷漆件或镀件出现局部的油漆层或镀层过薄而露出底料颜色的现象。
鱼眼由于溶剂挥发速度不对而在喷漆件表面出现凹陷或小坑。
多喷超出图纸上规定的喷涂区域。
剥落产品表面出现涂层或镀层脱落的现象。
色差产品表面颜色与标准样品(封样品)颜色有差异。
光泽差产品表面光泽呈与标准样品(封样品)光泽有差异。
手印在产品表面或零件光亮面出现的手指印。
异色点在产品表面出现颜色异于周围颜色的点。
多胶点因模具方面的损伤而造成局部细小的塑胶凸起。
缩水当塑料熔体通过一个较薄的截面后,其压力损失很大,很难继续保持很高的压力来填充而在较厚的截面形成的凹坑。
手机结构件制造工艺介绍1103

成型工艺: 一.成型工艺 成型工艺
1.1 注塑成型 注塑成型? 所谓注塑成型(Injection Molding)是指,将已加热融化的材料喷射注入到模具内, 经由冷却与固化後,得到成形品的方法。适用于量产与形状复杂产品等成形加工领域。 射出成形工程是以下列六大顺序执行.
重复执行这种作业流程,就可连续生产制品。 重复执行这种作业流程,
1.2 .成型的五大要素: .成型的五大要素:
1﹒原料 ABS﹐PP﹐ABS/PC﹐PC﹐POM等 如﹕ABS﹐PP﹐ABS/PC﹐PC﹐POM等﹒ 2﹒模具 二板模﹐三板模﹐热胶道模 如﹕二板模﹐三板模﹐热胶道模 3﹒机台 如:日精、住友、周边设备, 目前我们的注塑机型号是:住友. 日精、住友、周边设备, 目前我们的注塑机型号是:住友. 4﹒成型條件 时间﹐ 速度﹐ 如﹕温度﹐时间﹐压力﹐速度﹐位置﹒ 5﹒人員 物流﹒ 如﹕技术員﹐作业員﹐物流﹒
• PMMA
POM耐磨,融滑性好, 手机中主要应用: 1. 手写笔尖2. 锁扣,滑盖机耐磨条
•TPU
TPU有很多品種. 其主要应用领域包括:汽车工业、电线电缆、工业制品、制鞋领 域、土木建筑、医疗保健及聚合物改性等。 手机中应用:T-F 卡盖,USB卡盖,螺钉塞等。
注塑成型介绍
注塑成型介绍
注塑成型介绍
缺陷: 缺陷: 起皮 Defect: Flaking of surface layer
起皮
起皮改善对策
• • • • • • 工艺: 工艺 1.降低注射速度 降低注射速度 2.充分干燥原料 充分干燥原料 3.降低料筒温度 降低料筒温度 原料: 原料: 1.检查原料是否混有 检查原料是否混有 杂料 • 模具 模具: • 1.提高模腔表面温度 提高模腔表面温度
手机结构设计

手机中常见结构件的设计一.塑料壳体(Housing)手机中壳体的作用:是整个手机的支承骨架;对电子元器件定位及固定;承载其他所有非壳体零部件并限位。
壳体通常由工程塑料注塑成型。
1.壳体常用材料(Material)✧ABS:高流动性,便宜,适用于对强度要求不太高的部件(不直接受到冲击,不承受可靠性测试中结构耐久性测试的部件),如手机内部的支撑架(Keypad frame,LCD frame)等。
还有就是普遍用在要电镀的部件上(如按钮,侧键,导航键,电镀装饰件等)。
目前常用奇美PA-727,PA757等。
✧PC+ABS:流动性好,强度不错,价格适中。
适用于绝大多数的手机外壳,只要结构设计比较优化,强度是有保障的。
较常用GE CYCOLOY C1200HF。
✧PC:高强度,贵,流动性不好。
适用于对强度要求较高的外壳(如翻盖手机中与转轴配合的两个壳体,不带标准滑轨模块的滑盖机中有滑轨和滑道的两个壳体等,目前指定必须用PC材料)。
较常用GE LEXAN EXL1414和Samsung HF1023IM。
在材料的应用上需要注意以下两点:避免一味减少强度风险,什么部件都用PC料而导致成型困难和成本增加;在对强度没有完全把握的情况下,模具评审T ooling Review时应该明确告诉模具供应商,可能会先用PC+ABS生产T1的产品,但不排除当强度不够时后续会改用PC料的可能性。
这样模具供应商会在模具的设计上考虑好收缩率及特殊部位的拔模角。
通常外壳都是由上、下壳组成,理论上上下壳的外形可以重合,但实际上由于模具的制造精度、注塑参数等因素的影响,造成上、下外形尺寸大小不一致,即面刮(面壳大于底壳)或底刮(底壳大于面壳)。
可接受的面刮<0.15mm,可接受底刮<0.1mm。
在无法保证零段差时,尽量使产品的面壳大于底壳。
一般来说,面壳因有较多的按键孔,成型缩水较大,所以缩水率选择较大,一般选0.5%。
底壳成型缩水较小,所以缩水率选择较小,一般选0.4%,即面壳缩水率一般比底壳大0.1%。
制作手机的材料
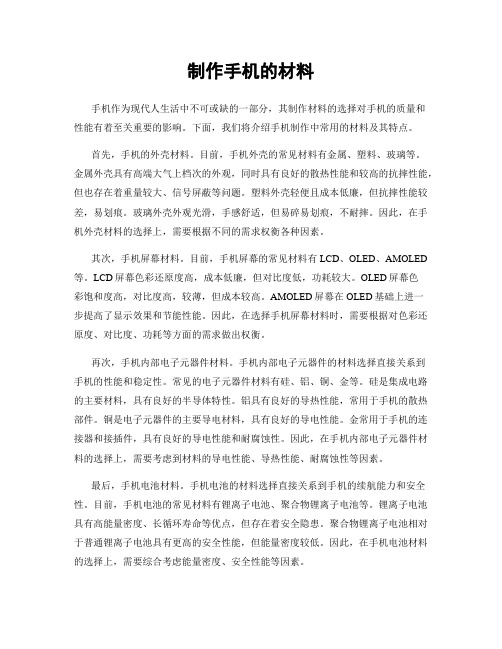
制作手机的材料手机作为现代人生活中不可或缺的一部分,其制作材料的选择对手机的质量和性能有着至关重要的影响。
下面,我们将介绍手机制作中常用的材料及其特点。
首先,手机的外壳材料。
目前,手机外壳的常见材料有金属、塑料、玻璃等。
金属外壳具有高端大气上档次的外观,同时具有良好的散热性能和较高的抗摔性能,但也存在着重量较大、信号屏蔽等问题。
塑料外壳轻便且成本低廉,但抗摔性能较差,易划痕。
玻璃外壳外观光滑,手感舒适,但易碎易划痕,不耐摔。
因此,在手机外壳材料的选择上,需要根据不同的需求权衡各种因素。
其次,手机屏幕材料。
目前,手机屏幕的常见材料有LCD、OLED、AMOLED 等。
LCD屏幕色彩还原度高,成本低廉,但对比度低,功耗较大。
OLED屏幕色彩饱和度高,对比度高,较薄,但成本较高。
AMOLED屏幕在OLED基础上进一步提高了显示效果和节能性能。
因此,在选择手机屏幕材料时,需要根据对色彩还原度、对比度、功耗等方面的需求做出权衡。
再次,手机内部电子元器件材料。
手机内部电子元器件的材料选择直接关系到手机的性能和稳定性。
常见的电子元器件材料有硅、铝、铜、金等。
硅是集成电路的主要材料,具有良好的半导体特性。
铝具有良好的导热性能,常用于手机的散热部件。
铜是电子元器件的主要导电材料,具有良好的导电性能。
金常用于手机的连接器和接插件,具有良好的导电性能和耐腐蚀性。
因此,在手机内部电子元器件材料的选择上,需要考虑到材料的导电性能、导热性能、耐腐蚀性等因素。
最后,手机电池材料。
手机电池的材料选择直接关系到手机的续航能力和安全性。
目前,手机电池的常见材料有锂离子电池、聚合物锂离子电池等。
锂离子电池具有高能量密度、长循环寿命等优点,但存在着安全隐患。
聚合物锂离子电池相对于普通锂离子电池具有更高的安全性能,但能量密度较低。
因此,在手机电池材料的选择上,需要综合考虑能量密度、安全性能等因素。
综上所述,手机的制作材料选择需要综合考虑外观、性能、成本、安全等多方面因素。
手机结构设计规范(图文)

手机结构设计规范(图文) 手机结构设计规范第一章总体结构设计一、手机总体尺寸长、宽、高的确定(一)宽度(W)计算:宽度一般由LCD、主板、电池三者之一决定。
1、LCD决定宽度W1:W1 =A+2(2+0.5)=A+52、主板PCB决定宽度W2:W2 =A+2(2+0.5)=A+53、电池决定宽度W3:此为常规方案W3=A+2(0.3+0.7+0.5+1)=A+5W3=A+2(0.3+0.7+0.5+1)=A+5此为手机变窄方案W3=A+2(0.3+1)=A+2.6然后比较W1、W2、W3的大小,其中值最大的为手机的宽度。
(二)、厚度(H)计算: 1、直板手机厚度(H):(1)、直板手机的总厚度H:直板手机厚度H由以下四部分组成:①电池部分厚度H1;②电池与PCB板间的厚度H2;③PCB板厚度H3;④LCD部分厚度H4。
(2)、电池部分厚度H1:H1=A1+1.1(3)、电池与PCB板间的厚度H2:H2=屏蔽罩高度A+标签0.2+与电池部分的间隙0.2=A+0.4。
(4)、PCB的厚度H3:手机的PCB板的长度大于80时,H3=1,否则PCB板易翘曲变形;手机的PCB板的长度小于80时,H3=0.8。
(5)、LCD部分厚度H4:H4=A2+1.92、翻盖手机(翻盖上装有LCD)厚度H:(1)、翻盖手机(装有LCD)的总厚度H: H=H1+H2+H3+H4+H5翻盖手机的厚度H由以下五部分组成:①电池部分厚度H1;②电池与PCB板间的厚度H2;③PCB板厚度H3;④PCB板与LCD部分的厚度H4;⑤LCD部分(即翻盖)的厚度H5。
(2)、电池部分厚度H1:电池部分厚度与直板手机相同,参考直板手机的计算方法。
(3)、电池与PCB板间的厚度H2:电池与PCB板间的厚度与直板手机相同,参考直板手机的计算方法。
(4)、PCB板厚度H3:PCB板的厚度与直板手机相同,参考直板手机的计算方法。
(5)、PCB板与LCD部分(即翻盖)间的厚度H4:(6)、LCD部分(即翻盖)厚度H5:LCD部分的厚度取决于LCD的放置方式,通常有以下两种形式:要求B≥0.6,是因为当小护镜承受较大的力时,要保证小护镜变形后,小护镜不能接触到LCD,以免使LCD损坏。
常见手机零部件技术要求精髓

常见手机零部件技术要求精髓本文介绍了常见手机零部件的技术要求精髓。
熟悉这些要求可以帮助手机制造商和供应商确保他们的产品符合市场需求,并提供出色的用户体验。
1. 显示屏要求显示屏是手机最重要的组成部分之一。
为了提供清晰、亮度高且色彩饱满的显示效果,显示屏应满足以下要求:- 分辨率高:显示屏的像素密度应足够高,以提供清晰的图像和文本显示。
- 色彩准确:显示屏应能准确还原图像和视频的色彩,以提供真实的视觉体验。
- 抗眩光:显示屏应具备抗眩光功能,以在阳光下能够清晰可见。
- 高亮度:显示屏的亮度应足够高,以在各种环境条件下都能看清屏幕内容。
2. 电池要求电池作为手机的能源来源,其性能优劣直接关系到手机的续航能力。
以下是电池的技术要求:- 大容量:电池容量应足够大,以支持长时间的使用。
- 快速充电:电池应支持快速充电技术,以减少充电时间。
- 安全性:电池应具备防止过充、过放和过热的保护机制,以确保使用安全。
3. 摄像头要求摄像头是手机用户拍摄照片和录制视频的主要工具。
以下是摄像头的技术要求:- 高像素:摄像头的像素数应足够高,以拍摄清晰、细节丰富的照片和视频。
- 光学稳定:摄像头应具备光学稳定功能,以减少拍摄时的模糊和抖动。
- 低光拍摄:摄像头应具备良好的低光拍摄能力,以在暗光环境下拍摄清晰的照片和视频。
4. 处理器要求处理器是手机的核心部件,影响手机的性能和响应速度。
以下是处理器的技术要求:- 高性能:处理器应具备强大的计算和图形处理能力,以保证流畅的操作和应用运行。
- 低能耗:处理器应具备低能耗的特性,以延长电池续航时间。
- 高集成度:处理器应具备高集成度,以减少占用手机空间。
5. 存储器要求存储器是手机用于存储数据和应用程序的重要组成部分。
以下是存储器的技术要求:- 大容量:存储器容量应足够大,以存储大量的数据和应用程序。
- 高速度:存储器应具备高读写速度,以提供快速的数据访问和应用程序运行。
- 可扩展性:存储器应支持扩展,以便用户能够根据需要增加额外的存储容量。
手机结构设计要求

手机产品的开发和设计技术规范——骨位设计
骨位高度≤8.00mm
顶部尺寸:≥0.40mm.
此尺寸做到均匀胶厚的62%以下,防止骨位胶厚 导致外观缩水、变形等缺陷。
SHEET 8OF62
手机产品的开发和设计技术规范——螺丝柱设计
M1.4螺丝
沉孔深度:0.3mm.用于溢胶
间隙:单边0.1mm 间隙:0.05mm
SHEET 30OF62
手机产品的开发和设计技术规范——电池盖装配结构设计(一)
1.电池盖后模与底壳相配的面间隙需预留0.15mm以上. (因底壳喷油后可能积油影响电池盖与底壳之间的装配效果)
2.电池盖扣位运动方向同底壳的间隙≥0.2mm 此处间隙为0.15mm以上
SHEET 31OF62
手机产品的开发和设计技术规范——电池盖装配结构设计(二)
注:如果扣位力度不够时,可考虑上壳扣位相应处加胶,达到设计要求。
X方向间隙: 0.10mm.
Y方向间隙: 0.05mm. 扣位避空位处因胶 厚不均,表面易产生 厚薄胶印,此处应与 周边平滑过渡。
SHEET 6OF62
手机产品的开发和设计技术规范——反扣的设计 反扣的定义: 扣位的配合方向与止口的配合方向不一致时,我们常称此扣位结构为反扣. 反扣的特点: 1: 配合牢固, 不易摔开.
电池盖因平面面积过大,尺寸要求严格,导致注塑困难,加上又是运动部 件,因此在设计和评审图纸时,需注意均匀胶厚需≥0.8mm,在平面上如有高度 ≥0.1mm的台阶,需做相切顺滑过渡,后模所有骨位尽量控制在均匀胶厚的 50%以内,靠边的胶厚可以做到62%左右.
更改前
更改后 SHEET 32OF62
手机产品的开发和设计技术规范——电池盖装配结构设计(三)
手机电子物料技术标准

一、目的为规范本部门电子物料技术标准特立订。
二、范围凡本部门所用电子物料技术标准,均依本规范标准统一行使。
三、定义电子物料为:显示屏组,摄像头,FPC,喇叭,咪头,马达,DAME片电池,充电器。
四.描述1.充电器1.1使用环境1.2充电器电源输入方式交流输入电压:供电电压AC100〜240V;最低电压:90V;最高电压264V。
输入电源频率:47〜63Hz空载时输入电流W5mA,输入电压在AC90-264V范围内;负载400-500mA (最大500mA)时输入电流120mA,输入电压在AC90-264V范围内。
1.3 AC输入端最大电流通电瞬间浪涌电流W30A,正常工作过程的电流W120 mAo1.4漏电流充电器对地漏电流W0. 25 mAo1.5充电器工作效率充电器效率$50% (输入电压为AC 90-264V,输出电流在400-500mA, 输出电压$4. 2V)o1.6充电器空载输出电压USB 口输出电压:5. 2V-5. 8V;电池槽输出电压:4.17V-4.23V.1.7充电器输出电流USB 口输出电流范围在400-500 mA之间(输出电压24.2V)。
最大输出电流为500 mAo电池槽输出电流范圉在250-350mA之间(输出电压23. 0V)1.8最大输出纹波电压300mV1.9负载能力充电器DC在接通电源时,输出端可长期连续开路或接其他任何阻性负载,而没有任何电气损坏。
1.10响应时间充电器从通电瞬间到输出电路正常工作的时间应小于3S (AC输入为AC90〜264V,输出电流为0〜500mA时)。
1.11绝缘强度输出电路和壳体之间应能承受50Hz,有效值为500V的电压lmin,无击穿或飞弧现象。
1.12绝缘电阻在环境温度为15〜35°C、相对湿度为90%、试验电压为直流500V时, 带电部件和输出电路及壳体之间的绝缘电阻不低于7MQ O输出电路和壳体之间的绝缘电阻不低于2 MQo1.13外观结构A、充电器外壳表面应平整光滑无刮痕、毛刺及其他机构损伤,外露五金无绣蚀、氧化等现象。
(待分)手机整机常用技术
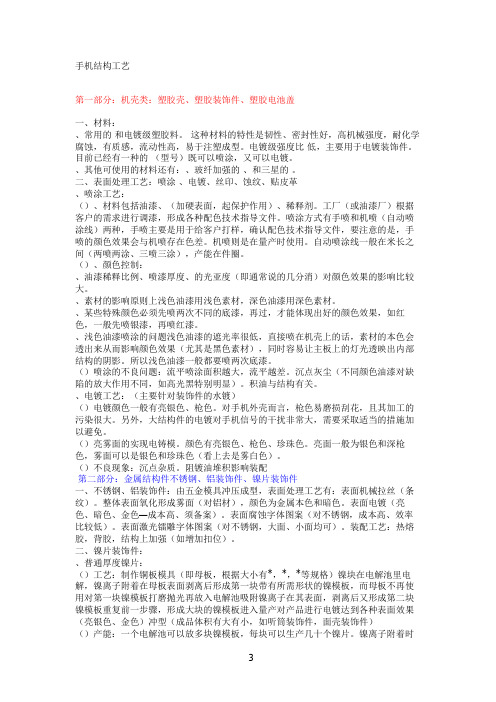
手机结构工艺第一部分:机壳类:塑胶壳、塑胶装饰件、塑胶电池盖一、材料:、常用的和电镀级塑胶料。
这种材料的特性是韧性、密封性好,高机械强度,耐化学腐蚀,有质感,流动性高,易于注塑成型。
电镀级强度比低,主要用于电镀装饰件。
目前已经有一种的(型号)既可以喷涂,又可以电镀。
、其他可使用的材料还有:、玻纤加强的、和三星的。
二、表面处理工艺:喷涂、电镀、丝印、蚀纹、贴皮革、喷涂工艺:()、材料包括油漆、(加硬表面,起保护作用)、稀释剂。
工厂(或油漆厂)根据客户的需求进行调漆,形成各种配色技术指导文件。
喷涂方式有手喷和机喷(自动喷涂线)两种,手喷主要是用于给客户打样,确认配色技术指导文件,要注意的是,手喷的颜色效果会与机喷存在色差。
机喷则是在量产时使用。
自动喷涂线一般在米长之间(两喷两涂、三喷三涂),产能在件圈。
()、颜色控制:、油漆稀释比例、喷漆厚度、的光亚度(即通常说的几分消)对颜色效果的影响比较大。
、素材的影响原则上浅色油漆用浅色素材,深色油漆用深色素材。
、某些特殊颜色必须先喷两次不同的底漆,再过,才能体现出好的颜色效果,如红色,一般先喷银漆,再喷红漆。
、浅色油漆喷涂的问题浅色油漆的遮光率很低,直接喷在机壳上的话,素材的本色会透出来从而影响颜色效果(尤其是黑色素材),同时容易让主板上的灯光透映出内部结构的阴影。
所以浅色油漆一般都要喷两次底漆。
()喷涂的不良问题:流平喷涂面积越大,流平越差。
沉点灰尘(不同颜色油漆对缺陷的放大作用不同,如高光黑特别明显)。
积油与结构有关。
、电镀工艺:(主要针对装饰件的水镀)()电镀颜色一般有亮银色、枪色。
对手机外壳而言,枪色易磨损刮花,且其加工的污染很大。
另外,大结构件的电镀对手机信号的干扰非常大,需要采取适当的措施加以避免。
()亮雾面的实现电铸模。
颜色有亮银色、枪色、珍珠色。
亮面一般为银色和深枪色,雾面可以是银色和珍珠色(看上去是雾白色)。
()不良现象:沉点杂质。
阻镀油堆积影响装配第二部分:金属结构件不锈钢、铝装饰件、镍片装饰件一、不锈钢、铝装饰件:由五金模具冲压成型,表面处理工艺有:表面机械拉丝(条纹)。
手机注塑工艺(3篇)
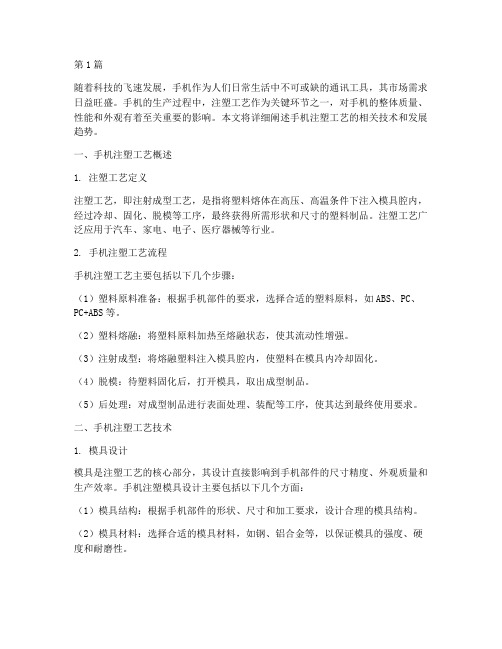
第1篇随着科技的飞速发展,手机作为人们日常生活中不可或缺的通讯工具,其市场需求日益旺盛。
手机的生产过程中,注塑工艺作为关键环节之一,对手机的整体质量、性能和外观有着至关重要的影响。
本文将详细阐述手机注塑工艺的相关技术和发展趋势。
一、手机注塑工艺概述1. 注塑工艺定义注塑工艺,即注射成型工艺,是指将塑料熔体在高压、高温条件下注入模具腔内,经过冷却、固化、脱模等工序,最终获得所需形状和尺寸的塑料制品。
注塑工艺广泛应用于汽车、家电、电子、医疗器械等行业。
2. 手机注塑工艺流程手机注塑工艺主要包括以下几个步骤:(1)塑料原料准备:根据手机部件的要求,选择合适的塑料原料,如ABS、PC、PC+ABS等。
(2)塑料熔融:将塑料原料加热至熔融状态,使其流动性增强。
(3)注射成型:将熔融塑料注入模具腔内,使塑料在模具内冷却固化。
(4)脱模:待塑料固化后,打开模具,取出成型制品。
(5)后处理:对成型制品进行表面处理、装配等工序,使其达到最终使用要求。
二、手机注塑工艺技术1. 模具设计模具是注塑工艺的核心部分,其设计直接影响到手机部件的尺寸精度、外观质量和生产效率。
手机注塑模具设计主要包括以下几个方面:(1)模具结构:根据手机部件的形状、尺寸和加工要求,设计合理的模具结构。
(2)模具材料:选择合适的模具材料,如钢、铝合金等,以保证模具的强度、硬度和耐磨性。
(3)冷却系统:设计合理的冷却系统,以控制塑料的冷却速度和固化时间,提高产品质量。
(4)模具表面处理:对模具表面进行抛光、镀膜等处理,以提高其光洁度和耐磨性。
2. 注塑设备注塑设备是注塑工艺的关键设备,主要包括注射机、模具和控制系统等。
手机注塑设备应具备以下特点:(1)高精度:注射机应具备较高的注射精度,以保证手机部件的尺寸精度。
(2)高效率:注射机应具备较高的生产效率,以满足手机市场的需求。
(3)稳定性:注射机应具备良好的稳定性,以保证产品质量的稳定性。
(4)智能化:控制系统应具备智能化功能,如自动调节温度、压力等参数,以提高生产效率。
手机常用材料和工艺介绍

3). 镍
• 性能:可做的非常薄,通常厚度0.2,另外超薄电 铸厚度可做到0.05mm,缺点超薄电铸只能做平 面产品,普通电铸也不能做复杂的弧面 • 用途:在手机上常用作装饰件,铭牌。可以在装 饰件表面做出高光、拉丝、和雾面、镭射等效果
4). 镁
• 性能:在很薄的情况下达到很好的强度,缺点是 模具价格非常高,周期长。 • 用途:常用在一些要求比较薄的产品上。例如笔 记本电脑的液晶支撑架。在手机上应用到一些品 牌机的高端手机上。例如:Nokia 的超薄翻盖机 N76。
3. 常用手机外观工艺
• • • • • • 1). 电镀 2). 电铸 3). 喷涂 4). IML 5). 按键P+R 工艺 6). 双色模
1). 电镀-1
• 性能:手机上常用的电镀分普通水电镀和真空电镀。 • 一).水镀工艺成熟,从设备到环境得要求均没有真空离 子镀苛刻,从而被广泛应用。一般塑胶材料采用电镀级的 ABS,另外金属材料也可电镀。水电镀的可选颜色不多。 另外水电镀一般的镀层材质采用“六价铬”,这是非环保 材料,部分是属于欧盟禁用的材料,在做出口手机上这点 要注意。 • 二).真空电镀是在真空状态下将需要涂覆在产品表面的 膜层材料通过等离子体离化后沉积在工件表面的表面处理 技术。对材料的选择广泛一些。但工艺复杂,环境、设备 要求高,单价比水电镀昂贵。主要的工艺流程:产品表面 清洁--〉去静电--〉喷底漆--〉烘烤底漆--〉真空镀膜--〉 喷面漆--〉烘烤面漆--〉包装。可电镀的颜色较丰富。另 外比较环保。
1). 钢
• 性能:延展性好,弹性好,强度高。制造工艺成 熟 • 用途:在手机上常用作装饰件,一般做抛光,拉 丝和喷沙处理可以在装饰件表面做出高光、拉丝性好,弹性弱,可通过阳极处理成各 种颜色,制造工艺成熟 • 用途:在手机上常用作装饰件,一般做抛光,拉 丝和喷沙处理可以在装饰件表面做出高光、拉丝、 和雾面等效果,另外边沿可通过机械加工出高亮 的斜边
手机金属部件设计及制造工艺
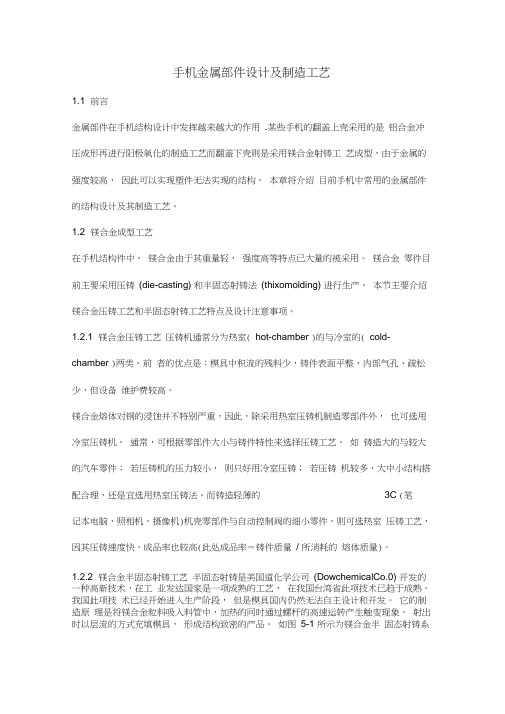
手机金属部件设计及制造工艺1.1 前言金属部件在手机结构设计中发挥越来越大的作用.某些手机的翻盖上壳采用的是铝合金冲压成形再进行阳极氧化的制造工艺而翻盖下壳则是采用镁合金射铸工艺成型,由于金属的强度较高,因此可以实现塑件无法实现的结构。
本章将介绍目前手机中常用的金属部件的结构设计及其制造工艺。
1.2 镁合金成型工艺在手机结构件中,镁合金由于其重量轻,强度高等特点已大量的被采用。
镁合金零件目前主要采用压铸(die-casting) 和半固态射铸法(thixomolding) 进行生产。
本节主要介绍镁合金压铸工艺和半固态射铸工艺特点及设计注意事项。
1.2.1 镁合金压铸工艺压铸机通常分为热室( hot-chamber )的与冷室的( cold-chamber )两类。
前者的优点是:模具中积流的残料少,铸件表面平整,内部气孔、疏松少,但设备维护费较高。
镁合金熔体对钢的浸蚀并不特别严重,因此,除采用热室压铸机制造零部件外,也可选用冷室压铸机。
通常,可根据零部件大小与铸件特性来选择压铸工艺。
如铸造大的与较大的汽车零件;若压铸机的压力较小,则只好用冷室压铸;若压铸机较多,大中小结构搭配合理,还是宜选用热室压铸法。
而铸造轻薄的3C (笔记本电脑,照相机,摄像机)机壳零部件与自动控制阀的细小零件,则可选热室压铸工艺,因其压铸速度快,成品率也较高(此处成品率=铸件质量/ 所消耗的熔体质量)。
1.2.2 镁合金半固态射铸工艺半固态射铸是美国道化学公司(DowchemicalCo.0) 开发的一种高新技术,在工业发达国家是一项成熟的工艺,在我国台湾省此项技术已趋于成熟。
我国此项技术已经开始进入生产阶段,但是模具国内仍然无法自主设计和开发。
它的制造原理是将镁合金粒料吸入料管中,加热的同时通过螺杆的高速运转产生触变现象,射出时以层流的方式充填模具,形成结构致密的产品。
如图5-1 所示为镁合金半固态射铸系统示意图。
图5-1 镁合金半固态射铸系统示意图镁合金半固态射铸法的优点是:1. 零件表面质量高,低气孔率,高致密性,抗腐蚀性能优良;2. 可铸造壁厚薄达0.7 ~0.8mm 的轻薄件,尺寸精度高,稳定性好;3. 强度高,刚性好;4. 不需要熔炼炉,不但安全性高、劳动环境好而且不产生热公害;5. 不使用对臭氧层有严重破坏作用的六氟化硫气体,不会形成重金属残渣污染;6. 铸件收缩量小;7. 铸件的表面良品率高,可达50 %或更高些,此处所说的良品是压铸工序无表面缺陷的。
手机结构件工艺简介
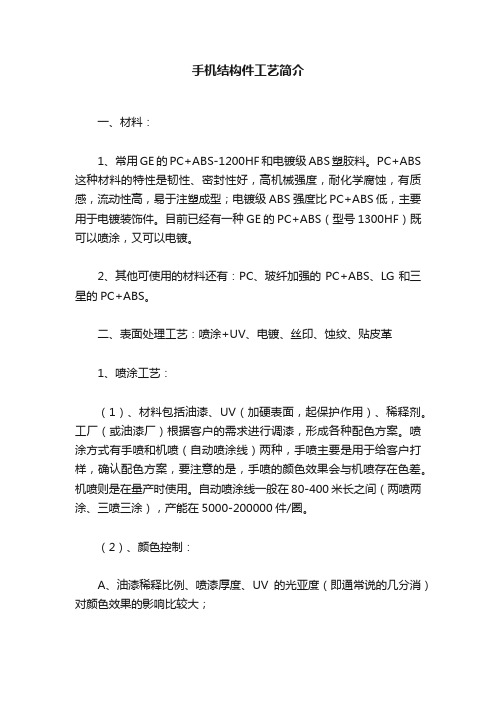
手机结构件工艺简介一、材料:1、常用GE的PC+ABS-1200HF和电镀级ABS塑胶料。
PC+ABS 这种材料的特性是韧性、密封性好,高机械强度,耐化学腐蚀,有质感,流动性高,易于注塑成型;电镀级ABS强度比PC+ABS低,主要用于电镀装饰件。
目前已经有一种GE的PC+ABS(型号1300HF)既可以喷涂,又可以电镀。
2、其他可使用的材料还有:PC、玻纤加强的PC+ABS、LG和三星的PC+ABS。
二、表面处理工艺:喷涂+UV、电镀、丝印、蚀纹、贴皮革1、喷涂工艺:(1)、材料包括油漆、UV(加硬表面,起保护作用)、稀释剂。
工厂(或油漆厂)根据客户的需求进行调漆,形成各种配色方案。
喷涂方式有手喷和机喷(自动喷涂线)两种,手喷主要是用于给客户打样,确认配色方案,要注意的是,手喷的颜色效果会与机喷存在色差。
机喷则是在量产时使用。
自动喷涂线一般在80-400米长之间(两喷两涂、三喷三涂),产能在5000-200000件/圈。
(2)、颜色控制:A、油漆稀释比例、喷漆厚度、UV的光亚度(即通常说的几分消)对颜色效果的影响比较大;B、素材的影响---原则上浅色油漆用浅色素材,深色油漆用深色素材;C、某些特殊颜色必须先喷两次不同的底漆,再过UV,才能体现出好的颜色效果,如红色,一般先喷银漆,再喷红漆。
D、浅色油漆喷涂的问题---浅色油漆的遮光率很低,直接喷在机壳上的话,素材的本色会透出来从而影响颜色效果(尤其是黑色素材),同时容易让主板上的灯光透映出内部结构的阴影;所以浅色油漆一般都要喷两次底漆。
(3)喷涂的不良问题:流平---喷涂面积越大,流平越差;沉点---灰尘(不同颜色油漆对缺陷的放大作用不同,如高光黑特别明显);积油---与结构有关。
2、电镀工艺:(主要针对装饰件的水镀)(1)电镀颜色一般有亮银色、枪色。
对手机外壳而言,枪色易磨损刮花,且其加工的污染很大。
另外,大结构件的电镀对手机信号的干扰非常大,需要采取适当的措施加以避免。