铸件专项审核标准
铸件检验标准
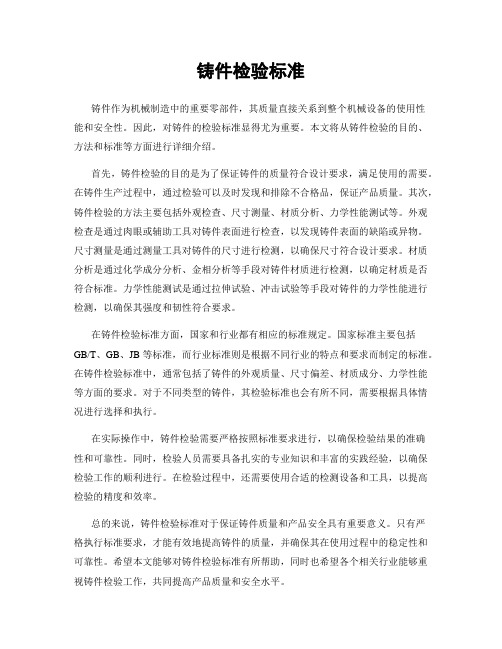
铸件检验标准铸件作为机械制造中的重要零部件,其质量直接关系到整个机械设备的使用性能和安全性。
因此,对铸件的检验标准显得尤为重要。
本文将从铸件检验的目的、方法和标准等方面进行详细介绍。
首先,铸件检验的目的是为了保证铸件的质量符合设计要求,满足使用的需要。
在铸件生产过程中,通过检验可以及时发现和排除不合格品,保证产品质量。
其次,铸件检验的方法主要包括外观检查、尺寸测量、材质分析、力学性能测试等。
外观检查是通过肉眼或辅助工具对铸件表面进行检查,以发现铸件表面的缺陷或异物。
尺寸测量是通过测量工具对铸件的尺寸进行检测,以确保尺寸符合设计要求。
材质分析是通过化学成分分析、金相分析等手段对铸件材质进行检测,以确定材质是否符合标准。
力学性能测试是通过拉伸试验、冲击试验等手段对铸件的力学性能进行检测,以确保其强度和韧性符合要求。
在铸件检验标准方面,国家和行业都有相应的标准规定。
国家标准主要包括GB/T、GB、JB等标准,而行业标准则是根据不同行业的特点和要求而制定的标准。
在铸件检验标准中,通常包括了铸件的外观质量、尺寸偏差、材质成分、力学性能等方面的要求。
对于不同类型的铸件,其检验标准也会有所不同,需要根据具体情况进行选择和执行。
在实际操作中,铸件检验需要严格按照标准要求进行,以确保检验结果的准确性和可靠性。
同时,检验人员需要具备扎实的专业知识和丰富的实践经验,以确保检验工作的顺利进行。
在检验过程中,还需要使用合适的检测设备和工具,以提高检验的精度和效率。
总的来说,铸件检验标准对于保证铸件质量和产品安全具有重要意义。
只有严格执行标准要求,才能有效地提高铸件的质量,并确保其在使用过程中的稳定性和可靠性。
希望本文能够对铸件检验标准有所帮助,同时也希望各个相关行业能够重视铸件检验工作,共同提高产品质量和安全水平。
铸件验收标准审批稿
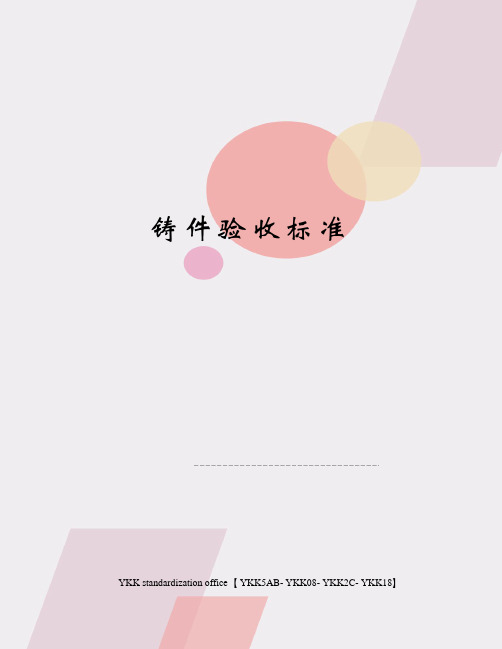
铸件验收标准YKK standardization office【 YKK5AB- YKK08- YKK2C- YKK18】本技术标准根据国标GB/T 1173,作为验收砂型铝合金铸件之用。
一.铸件分类:1、铸件按照工作条件和用途分为三类:第Ⅰ类:承受大载荷,工作条件复杂,用于关键部位、铸件损坏将危及整机安全运行的重要铸件。
第Ⅱ类:承受中等载荷,用于重要部位,铸件损坏将影响部件的正常工作,造成事故的铸件。
第Ⅲ类:承受低载荷,用于一般部位的铸件。
二.技术要求和检验:1.化学成分1)合金的化学成分应符合GB/T 1173的规定。
2)对于铸件的化学成分,供应商必须进行检测并出具相关报告。
2.力学性能1)单铸件或附铸试样的力学性能应符合GB/T 1173的要求。
2)从铸件上切取试样检验力学性能,三根试样的抗拉强度和伸长率的平均值,分别不低于GB/T 1173规定值的70%和50%。
3)铸件硬度检验按GB/T 进行,硬度不合格的铸件允许进行重复热处理,随后再检验硬度,第三次热处理后仍不合格时铸件予以报废。
4)铸件尺寸和几何形状应符合图纸规定,铸件尺寸公差及加工余量应符合GB/T6414。
三.表面质量:1.铸件表面粗糙度应符合铸造表面粗糙度比较样块的规定。
2.铸件需抛光加工的表面按的规定执行。
3.铸件需喷丸,喷砂加工的表面按的规定执行。
4.铸件不允许有裂纹,欠铸,疏松,气泡和任何穿透性缺陷。
?5.铸件不允许有擦伤,凹陷,缺肉和网状毛刺等腰三角形缺陷。
6.铸件的浇口,飞边,溢流口,隔皮等应清理干净,但允许留有痕迹。
7.螺纹孔内起始旋入四个牙距之内不允许有缺陷。
8.在不影响铸件使用的条件下,当征得需方同意,供方可以对铸件进行浸渗和修补(如焊补,变形校整等)处理,经修补处理后的压铸件应做相应的质量检验。
9.铸件内表面表面粗糙度为:25um。
10.铸件非加工表面及加工后表面,允许有:1)在非加工表面上,单个孔洞的最大直径不大于3mm,深度不超过壁厚的1/3。
铸件检验标准

铝合金铸造件检验技术条件(试行)1 内容及适用范围本标准根据GB/T 1173-1995及GB/T 9438-1999的相关内容,规定了铝合金铸件的分类和铸件的外观质量、内在质量以及铸件修补等内容的技术要求与检验规则等。
本标准适用于我公司采用金属型铸造所生产的制动器上、下泵体等铸件(不含压力铸造)。
根据工作条件、用途以及在使用过程中如果损坏,所能造成的危害程度,将铸件分类如下:2 技术要求2.1 化学成分2.1.1合金的化学成分根据GB/T 1173-1995的规定,应符合表2-1及表2-2的规定。
2.1.2当使用杂质总和来表示杂质含量时,如无特殊规定,其中每一种未列出的元素含量不大于0.02%。
2.2 状态2.2.1铸件按表2-3的规定,呈铸态或热处理状态供应。
注:在保证合金机械性能前提下,可以不加铍(Be)。
2.3 机械性能2.3.1 每批铸件应按其类别检验机械性能。
2.3.2 合金及其铸件的机械性能应符合表2-3的规定。
2.4外观质量2.4.1铸件在进行表面粗糙度、表面缺陷、尺寸等外观质量检验之前,飞边、溢流口、隔皮等应清理干净、平整,但不可在非加工表面上留有明显的凿痕,且宽度不得超过2mm。
2.4.2铸件的表面粗糙度Ra为6.3μm以上。
2.4.3非加工表面的浇冒口,应清理到与铸件表面齐平;待加工表面的浇冒口残留量应不大于3mm。
2.4.4清除飞翅、夹砂等多肉类缺陷,铸件的内外表面由于型芯及顶杆的磨损所产生的飞边、毛刺应清除干净。
2.4.5根据顾客图样或技术文件的要求,铸件表面可进行喷砂处理。
2.4.6铸件上作为基准用的部位应平整,不允许存在任何凸起痕迹,装饰面上不允许有推杆痕迹(图样上注明)。
2.4.7非加工表面上,由于模具组合镶并或受分型面影响而形成的铸件表面高低不平差值不得超过0.3mm。
2.4. 8非加工表面上,不允许有超过表2-4(Ⅰ)级规定的花纹、麻面和有色斑点。
2.4.9铸件尺寸应符合图样的要求。
铸件质量检验标准

铸件质量检验标准铸件质量检验标准铸件质量检验标准铸件质量检验标准铸件质量检验标准⼀、⽬的:为了确保外协⽑坯铸件、采购⽑坯铸件、标准铸件、成品铸件质量符合⼯艺、技术要求,为了满⾜产品特性,结合相关⽂件特制定本标准。
⼆、适⽤范围:本标准适⽤于我公司产品外协、采购、⽣产、装配过程中,全部铸件质量检验标准。
三、检验标准:3.1 铸件结构要符合设计要求或加⼯⼯艺要求。
⽆特殊要求时按铸件通⽤标准执⾏。
通⽤标准等级分为:交货验收技术条件标准;铸件质量分等通则(合格品、⼀等品、优等品)材质、检验⽅法;⼯艺和材料规格等⼀般性规则。
3.2 铸件成品检验。
铸件成品检验包括:铸件的内部质量检验和外观质量检验。
铸件内部质量检验包括:化学成分、机械性能等。
铸件外观质量检验包括:表⾯质量、粗糙度、铸件尺⼨、重量等。
3.2.1 铸件内部质量检验①化学成分:表1牌号标准化学成分C Si Mn Cr P S Ni Cu MoWCAASTMA2160.25 0.60 0.70 0.50 0.04 0.045 0.50 0.30 0.20WCBASTMA2160.30 0.60 1.00 0.50 0.04 0.045 0.50 0.30 0.20WCCASTMA2160.25 0.60 1.20 0.50 0.04 0.045 0.50 0.30 0.20LCBASTMA3520.30 0.6 1.00 0.5 0.04 0.045 0.05 0.3 0.20LC1ASTMA3520.25 0.6 0.5~0.8 — 0.04 0.045 — — 0.45~0.65 LC2ASTMA3520.25 0.6 0.5~0.8 — 0.04 0.045 2~3 — —LC3ASTMA3520.15 0.6 0.5~0.8 — 0.04 0.045 3~4 — —WC6ASTMA217M0.05~0.201.50.04 0.045 0.5 0.5 0.45~0.65WC9ASTMA217M0.05~0.180.600.4~0.72.0~2.750.04 0.045 0.5 0.5 0.90~1.20C5ASTMA217M0.20 0.750.4~0.74.0~6.50.04 0.045 0.5 0.5 0.45~0.65CF3ASTMA3510.03 2.0 1.5 17~21 0.04 0.04 8~12 0.5CF8ASTMA3510.08 2.0 1.5 18~21 0.04 0.04 8~11 0.5CF3MASTMA3510.03 1.5 1.5 17~21 0.04 0.04 9~13 2~3CF8MASTMA3510.08 1.5 1.5 18~21 0.04 0.04 9~12 2~3CG3MASTMA3510.03 1.0 2.0 18~20 0.035 0.03 11~15 3~4CG8MASTMA3510.08 1.0 2.0 18~20 0.035 0.03 11~15 3~4②机械性能表2牌号标准⼒学性能σb(MPa) σs(MPa) δ(%) ψ(%)WCA ASTM A216 415~585 205 24 35WCB ASTM A216 485~655 250 22 35WCC ASTM A216 485~655 275 22 35 LCB ASTM A352 450~620 240 24 35 LC1 ASTM A352 450~620 240 24 35LC2 ASTM A352 485~655 275 24 35LC3 ASTM A352 485~655 275 24 35WC6 ASTM A217M 485~655 275 20 35CF3M ASTM A351 485 205 30CF8M ASTM A351 485 205 30CG3M ASTM A351 480 177 40CG8M ASTM A351 520 205 403.2.2 铸件外观质量检验①表⾯质量检验。
铸件专项审核标准
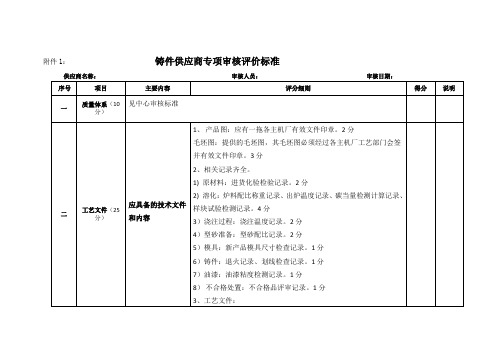
供应商名称:审核人员:审核日期:
序号
项目
主要内容
评分细则
得分
说明
一
质量体系(10分)
见中心审核标准
二
工艺文件(25分)
应具备的技术文件和内容
1、产品图:应有一拖各主机厂有效文件印章。2分
毛坯图:提供的毛坯图,其毛坯图必须经过各主机厂工艺部门会签并有效文件印章。3分
2、相关记录齐全。
1)原材料:进货化验检验记录。2分
2)溶化:炉料配比称重记录、出炉温度记录、碳当量检测计算记录、样块试验检测记录。4分
3)浇注过程:浇注温度记录。2分
4)型砂准备:型砂配比记录。2分
5)模具:新产品模具尺寸检查记录。1分
6)铸件:退火记录、划线检查记录。1分
7)油漆:油漆粘度检测记录。1分
8)不合格处置:不合格品评审记录。1分
9、铸件精清理设备(砂轮风铲)3分
10、浸漆槽1分
四、
工装保障
(25分)
监视和测量
1、炉料承重:电子称或电磁称、磅秤、定量计等5分
2、熔液出炉温度及浇注温度检测:热电偶6分
3、碳当量检测仪(如光谱仪)6分
4、模具和铸件检查:划线平台、高度尺、卡尺5分
5、铸件退火温度和时间控制:钟表、测温仪表2分
6、油漆粘度检测:φ4粘度杯、秒表1分
五、
外观质量
(5分)
实物质量
1、毛坯外观:非加工表面及定位面不允许有飞边毛刺、粘砂、多肉、缺料、凸凹不平等现象;合模缝、浇冒口必须打磨平整;3分
2、毛坯铸造外表面粗糙度必须以本次封样为标准,并有提高。2分
(供方现场有样件)
六、
不合格品处置(5分)
铸件质量检查标准

一、目的:为了确保外协标准铸件、成品铸件质量符合工艺、技术要求,为了满足产品特性,结合相关文件特制定本标准。
二、适用范围:本办法适用于我公司产品外协、采购、装配过程中、全部铸件质量检查标准。
三、检查标准:3.1、铸件结构要符合设计要求或加工工艺要求。
无特殊要求时按铸件通用标准执行。
通用标准等级分为:交货验收技术条件标准;铸件质量分等通则(合格品、一等品、优等品)材质、检验方法;工艺和材料规格等一般性规则。
3.2、铸件成品检验。
铸件成品检验包括:相关技术条件的检验、表面质量检验、几何尺寸检验等项内容。
①相关技术条件的检验。
包括铸件化学成分、机械性能等检验内容。
机械性能检验和金相及化学成分检验等技术条件的检验,均必须按相关国家标准执行检验(此处略)。
②表面质量检验。
机械加工生产一线人员在工艺过程中对铸造毛坯的检查主要是对其外观铸造缺陷(如有无沙眼、沙孔、疏松、有无浇不足、铸造裂纹等)的检验;以及毛坯加工余量是否满足加工要求的检验。
表3-1铸件外观质量检验项目(GB6060.1—1985)表3-2 铸件表面粗糙度(R a 值μm)(GB6414—1986)③铸件成品几何尺寸检验。
主要一种是采用划线法检查毛坯的加工余量是否足够。
另一种方法是:用毛坯的参考基准面(也称工艺基准面)作为毛坯的检验基准面的相对测量法(需要测量相对基准面的尺寸及进行简单换算)。
表3-3 铸件尺寸公差数值(mm)(GB6414—1986)注:铸件基本尺寸≤10mm 时,其公差等级提高3 级;大于10mm 至等于15mm 时,其公差等级提高2级;大于16mm 至25mm 时,其公差等级提高1 级。
附表:铸件质量检验与缺陷处理实用技术。
压铸件检验规范
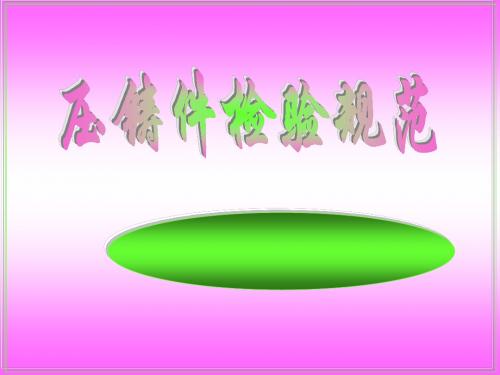
≤0.5
≤1.3
A380 7.5~9.5 3.0~4.0 ≤0.1 ≤3.0 ≤2.0
≤0.5 ≤0.6 ≤0.35 ≤0.5
≤0.5 ≤0.3 余量 余量
≤0.5 ≤0.15 余量 ≤0.5 ≤0.35 余量
HD2-A 9.6~10.5 1.5~2.3 ≤0.2 ≤1.0 0.6~0.9 ≤0.5
装饰面不允许,
2
冷隔 所在面上不允许超过的数量不允许 2处
离铸件边缘不小于mm
4
2处
2、长度是指缺 陷流向的展开长
非装饰面1~2级, 内表面3级。
4 度。
两冷隔间距不小于mm
10 10
深度不大于mm 3 擦伤
面积不大于总面积的%
0.05
0.1
0.25
浇口部位增加一 倍可接受
3 5 10
同上
装饰面不允
铸件边长>100mm时 0.5 0.8 1.2
同上
凹入铸件深度不超过
1/8壁厚
装饰面不允
7 顶杆痕迹 最大凹入量 凸起高度
≤0.4mm ≤0.2mm
许,非装饰 面及内表面2 级。
8 网状毛刺 凸起或凹下
≤0.2mm
不利手
同上
9 各类缺陷总和 面积不超过总面积的
5
注:根据产品总技术条件或要求进行检验。
3
允许两种气泡 同时存在,但
对于第4项基带 电路高频盒内
格
0.3
大气泡不超过 3个,总数不
底层表面1级。
超过10个,且
1 边距不小于 10mm
3
同上
合 格
5
气泡凸起高度
0.3 0.5
注:1、对于1级或有特殊需求的表面,只有通过抛光或研磨去除缺陷。
铸造铜合金检验标准
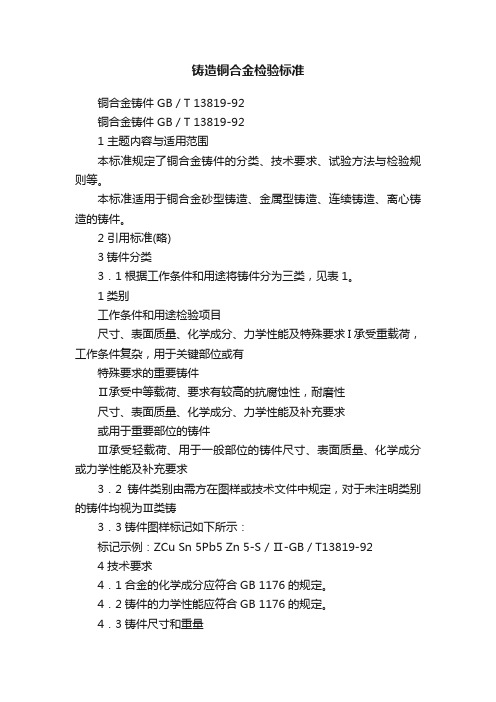
铸造铜合金检验标准铜合金铸件 GB/T 13819-92铜合金铸件 GB/T 13819-921 主题内容与适用范围本标准规定了铜合金铸件的分类、技术要求、试验方法与检验规则等。
本标准适用于铜合金砂型铸造、金属型铸造、连续铸造、离心铸造的铸件。
2 引用标准(略)3铸件分类3.1根据工作条件和用途将铸件分为三类,见表1。
1类别工作条件和用途检验项目尺寸、表面质量、化学成分、力学性能及特殊要求 I承受重载荷,工作条件复杂,用于关键部位或有特殊要求的重要铸件Ⅱ承受中等载荷、要求有较高的抗腐蚀性,耐磨性尺寸、表面质量、化学成分、力学性能及补充要求或用于重要部位的铸件Ⅲ承受轻载荷、用于一般部位的铸件尺寸、表面质量、化学成分或力学性能及补充要求3.2铸件类别由需方在图样或技术文件中规定,对于未注明类别的铸件均视为Ⅲ类铸3.3铸件图样标记如下所示:标记示例:ZCu Sn 5Pb5 Zn 5-S / Ⅱ-GB/T13819-924 技术要求4.1合金的化学成分应符合GB 1176的规定。
4.2铸件的力学性能应符合GB 1176的规定。
4.3铸件尺寸和重量4.3.1铸件的几何形状及尺寸应符合图样要求,尺寸公差应符合GB 6414的规定。
有特殊要求时,应在图样中注明。
铸件尺寸公差不包括由起模斜度而引起的尺寸增减,如有特殊要求,由供需双方商定。
4.3.2铸件的机械加工余量可参照GB/T 11350的规定。
4.3.3铸件的重量公差可参照GB/T 11351的规定。
4.4铸件的表面质量4.4.1铸件表面粗糙度应符合图样要求4.4.2铸件的浇冒口、毛刺、飞边等,在非加工表面上应清理到与铸件表面平齐,在待加工表面上允许的残留高度应符合表2 的规定。
4.4.3铸件表面不允许有裂纹、冷隔及穿透性缺陷。
4.4.4铸件上的铸字、标志应清晰,字体与位置应符合图样要求。
4.4.5铸件的非加工表面,允许有氧化夹杂,其深度不得超过规定壁厚公差的下差,其面积在I类铸件上不得超过铸件面积的5%,在Ⅱ、Ⅲ类铸件上不得超过铸件面积的10%。
铸造件通用检验标准
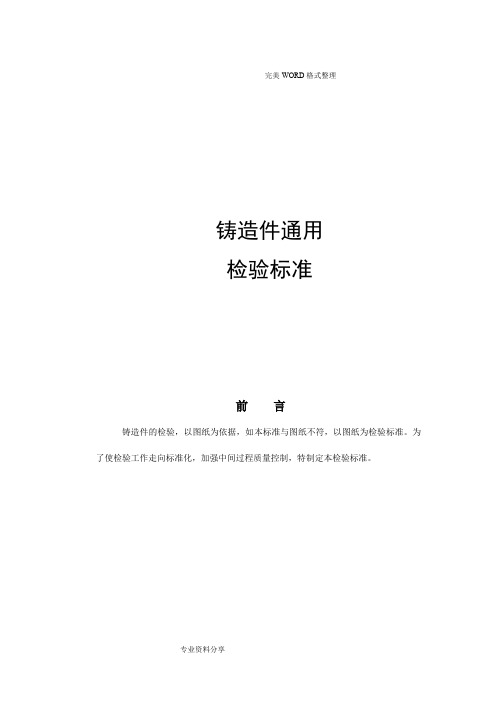
完美WORD格式整理铸造件通用检验标准前言铸造件的检验,以图纸为依据,如本标准与图纸不符,以图纸为检验标准。
为了使检验工作走向标准化,加强中间过程质量控制,特制定本检验标准。
完美WORD格式整理1.范围本标准适用于本公司产品压铸件及机加工的检验、验收。
2.引用标准本标准引用了下列标准的条款.本标准发布时,这些引用标准均为有效版本.所有标准将进行修定,因此,鼓励依据本标准达成协议的各方尽可能采用下列标准的最新版本.GB4054—83 金属涂覆层外观分级GB/T 9286—88 色漆和清漆划痕试验GB/T 6739—96 涂膜硬度铅笔测定法GB/T 1733—93 漆膜耐水性测定法GB/T6742—93 漆膜弯曲试验(园柱轴)GB/T1732-93 漆膜耐冲击测定法GB/T1771—91 色漆和清漆耐中性盐污性能的测定GB 5267—85 螺纹紧固件电镀层GB 2792—81 压敏胶带180°剥离强度测定方法GB5935—86 轻工产品金属镀层的孔隙率测试方法GB6463—86 金属和其它无机覆盖层厚度测量方法评述GB10125-97 《人造气氛腐蚀试验盐雾试验》GB5270-86 金属覆盖层结合力及脆性测试GB/T1182-96 形状和位置公差GB4208-2008 外壳防护等级(IP代码)3.目的3.1确保压铸件判定的统一标准;3.2指引QC检验,将所有检验动作标准化。
4.定义磨花/磨痕:产品表面由于摩擦而造成的擦花痕刮伤/划伤:产品表面由于与尖硬物摩擦而造成的刮痕/划痕。
刀痕:因用锉刀或机加工时刀具所留下的痕迹完美WORD格式整理砂带痕:因用砂带打磨所留下的痕迹拉模伤:顺着出模方向遗留在铸件表面上的拉伤痕迹。
凹陷:平滑表面上凹瘪的部分或者成型过程中填充不完整的部位压伤:切边模冲压或机加工时挤压所留下的痕迹碰伤:产品表面,边角受碰撞引起的变形痕迹顶针印:铸件表面由于模具顶针而形成凸出或凹下的痕迹行位印:铸件表面由于模具抽芯/镶块而形成凸出或凹下的痕迹冷隔:金属流对接未完全熔合形成的不规则下陷线性纹路,在外力作用下有发展趋势可能冷纹:肉眼可见与金属基体颜色不一样的纹络,无发展趋势印痕:铸件表面由于模具型腔磕碰挤压而形成凸出或凹下的痕迹流痕:表面上用手感觉得出的局部下陷的纹路,无发展趋势孔穴:气孔,缩孔和夹杂物等缺陷所形成的孔洞针孔:喷涂时表面产生的像针尖一样的小孔缺料/崩缺:外力敲击水口或切边模产生的缺损裂纹/裂痕:模具表面有呈直线状或波浪形的纹路,狭小而长,在外力的左右下有发展趋势龟裂纹:模具型腔表面龟裂形成的产品表面凸起或凹陷痕迹披锋:压铸件在分型面边缘出现的薄片毛边:边缘轮廓上因涂料堆积出现的边缘涂层不整齐现象斑点/麻点:产品表面形成的凸起颗粒或突出性杂物污点/脏点:颜色与正常表面不一致的色斑印迹气泡:涂层覆盖部分气体在烘烤时产生的泡状凸起缺陷桔皮/橘皮:涂层表面呈现出许多半圆状高低不平的桔子皮形状突起,易造成脱落起皮色差/异色:产品与色板的颜色差异露底/掉漆:局部无涂层或涂层缺失/覆盖不平露出底材积漆/溢漆:表面有较多漆团或漆点烧焦/发黄:喷涂烘烤不良造成表面留下的烧痕迹完美WORD格式整理少漆/薄漆:喷涂不到位或涂层流动而造成的厚度不均匀补漆:因涂层损伤而用涂料所作的局部遮盖补救A 级面:指该表面位于工件或组装后经常看到的外表面,或客户日常操作能近距离视角接触,并直接正视关注的产品表面和商标文字和图案丝印表面B 级面:指该表面位于工件或组装背面,或不经常看到但在一定条件下能看到的面,或客户不明显关注的外观表面,或不易被客户直接视角接触正视的外部表面C 级面:指该表面位于工件或组装不可视面,或客户一般不易观察并关注到的内外部表面,或只有在装配过程中才能看到的面,或经其他工件覆盖需拆卸才能被客户直接视角接触正视的内外部表面5.内容5.1外观检验完美WORD格式整理5.2性能检验5.3包装防护标识完美WORD格式整理 5.4机加工尺寸选用下表中等级-M级。
铸件检验标准

铸件检验标准1.铸件质量检测仪:用于检测合金性能、组织、表面状态等铸件质量的仪器。
2.铸件公称重量检验:根据铸件图计算或根据供需双方认定合格的标准样品铸件的称重结果订出的铸件重量。
包括铸件机械加工余量及其他工艺余量。
3.铸件重量公差检验:用占铸件公称重量的百分比表示的铸件实际重量与公称重量之差的最大允许值。
与铸件尺寸公差对应的分为16个等级,以MT1-MT16表示。
4.铸件重量偏:铸件重量与公称重量之间的正偏差或负偏差。
5.铸件尺寸公差:铸件各部分尺寸允许的极限偏差。
6.铸件尺寸稳定性:铸件在使用和存放过程中保持原来尺寸不变的性能。
7.铸件机械加工余量:为保证铸件加工面尺寸和零件精度,在铸件工艺设计时预先增加而在机械加工时切去的金属层厚度。
8.铸造表面粗糙度:铸造表面上由微小间距和峰谷组成的微观几何特征。
铸造工段铸件质量检验标准根据目前的生产情况,在初期对我单位的铸件检验制定了以下检验标准,随着以后生产和技术的进一步完善对此标准将逐步细化:1. *铸件外表面应平整,1000mm范围内的平整度(或变形量)不大于3mm(特殊要求例外),表面不允许存在高度长度大于3mm和直径大于3mm的铁瘤、脉纹;*不允许存在深度和直径大于3mm的孔洞类缺陷(砂眼、气孔、渣孔、缩孔、缩松等),如果此类缺陷存在面积大于150x150mm而失去修复价值视为废品,可以修复的必须经过焊补并打磨光洁后重新检验;*外型尺寸如有图纸要求公差的应严格按照图纸执行,未注公差的自由尺寸的偏差不能大于该尺寸的光洁度最低一级国家铸件标准规定;*铸件表面不能存在各种严重的裂纹缺陷,如果非加工表面存在长度不大于20mm的轻微裂纹,在请示技术部门后允许采用热焊补的办法进行修复;*铸件表面的粘砂必须清理干净,各种飞刺存在的面积不允许超过200x200mm,否则必须返工;2. *铸件水口冒口经过切割后不得留有高度大于2mm的根部,水口冒口根部的缩松、缩孔必须经过焊补,否则视为废品;*对比较重要的加工面,如果从外表发现各种皮下缺陷应及时反映到工段并对此铸件跟踪,一旦发现加工后存在大量气孔、渣孔、缩松等缺陷应立即将同类产品封存不得出厂并督促工段技术人员改进工艺;3. *每一批次铸件的材质要求单据在质监部门都应有存底,当炉次化验结果和要求对比后可以评判化学成分是否合乎要求;4. *对于用户在加工后发现的各种内在质量缺陷应及时核对并确定生产日期,作为考核数据重新对检验报告进行更改并及时建议工段技术人员改进工艺;5. *检验后发现问题比较严重的铸件只有在厂家提出强行发货要求,经过总经理及其授权人的书面同意后可以作为紧急放行件出厂。
铸件质量检验标准

西安重装铜川煤矿机械有限公司铸件质量检验标准为了提高铸件的质量,要求铸造分厂、相关科室不断的完善铸造工艺,解决各项铸造质量问题,控制铸造缺陷,使之降到最低。
积极的参与市场调查,不断的掌握用户对铸件质量的要求及信息反馈,持续完善改进铸造工艺,保证出厂铸件的质量,增强我公司铸件在市场的竞争力,特制定本检验标准。
铸件质量检验的依据:铸件图样、铸造工艺文件、相关标准和铸件交货验收技术条件。
铸件质量包括铸件外观质量和铸件内在质量。
铸件外观质量:铸件尺寸公差、铸件表面粗糙度、铸件重量公差、浇冒口残余量、铸件焊补质量和铸件表面缺陷。
铸件内在质量:铸件力学性能、化学成分、金相组织和内部缺陷。
1、铸件化学成分的检验分析(炉前检验分析或成品铸件终端检验分析)应符合图样要求的牌号的化学成分。
2、铸件力学性能的检验应符合相关标准及交货验收技术条件所要求的各种性能。
3、铸件外形几何形状、尺寸、尺寸公差及加工余量的检验(符合GB/T6414-1999)⑴简单铸件外形几何形状、尺寸、尺寸公差及加工余量的检验应按铸件图样、技术要求、铸造工艺文件、国家相关标准及合同规定进行全部尺寸的检验。
⑵形状复杂铸件外形几何形状、尺寸、尺寸公差、形位公差及加工余量应按铸件图样、技术要求、铸造工艺文件、国家相关标准及合同规定采用划线检验、三坐标测量仪检验及超声波测量(厚度)等检测方法进行检验。
4、铸件表面粗糙度的检验⑴不加工铸件的表面必须清理干净,不得有铸造缺陷、锈蚀、油污、砂粒及其它粘附物。
⑵加工铸件的表面必须清理干净,不得有铸造缺陷、锈蚀、油污、砂粒及其它粘附物,且不能提高生产成本。
5、铸件公称重量的检验⑴铸件的公称重量:供需双方共同认定的合格铸件中随机抽取不少于10件铸件,以实称重量的平均值作为公称重量。
⑵铸件在称重量前应清理干净,浇道和冒口残余量应达到技术条件规定的要求,有缺陷的铸件应在修补合格后称重量。
⑶图样有要求公称重量的铸件,应按铸件图样、技术文件及合同规定进行称重检验。
铸铁件检验标准
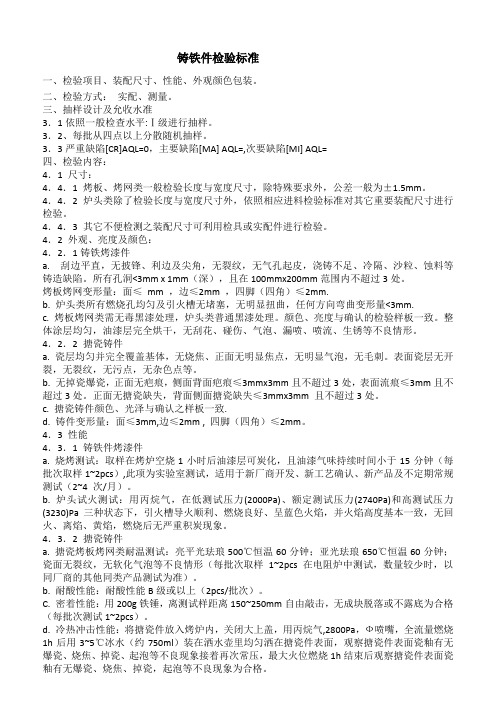
铸铁件检验标准一、检验项目、装配尺寸、性能、外观颜色包装。
二、检验方式:实配、测量。
三、抽样设计及允收水准3.1依照一般检查水平:Ⅰ级进行抽样。
3.2、每批从四点以上分散随机抽样。
3.3严重缺陷[CR]AQL=0,主要缺陷[MA] AQL=,次要缺陷[MI] AQL=四、检验内容:4.1 尺寸:4.4.1 烤板、烤网类一般检验长度与宽度尺寸,除特殊要求外,公差一般为±1.5mm。
4.4.2 炉头类除了检验长度与宽度尺寸外,依照相应进料检验标准对其它重要装配尺寸进行检验。
4.4.3 其它不便检测之装配尺寸可利用检具或实配件进行检验。
4.2 外观、亮度及颜色:4.2.1铸铁烤漆件a. 刮边平直,无披锋、利边及尖角,无裂纹,无气孔起皮,浇铸不足、冷隔、沙粒、蚀料等铸造缺陷。
所有孔洞<3mm x 1mm(深),且在100mmx200mm范围内不超过3处。
烤板烤网变形量:面≤mm ,边≤2mm ,四脚(四角)≤2mm.b. 炉头类所有燃烧孔均匀及引火槽无堵塞,无明显扭曲,任何方向弯曲变形量<3mm.c. 烤板烤网类需无毒黑漆处理,炉头类普通黑漆处理。
颜色、亮度与确认的检验样板一致。
整体涂层均匀,油漆层完全烘干,无刮花、碰伤、气泡、漏喷、喷流、生锈等不良情形。
4.2.2 搪瓷铸件a. 瓷层均匀并完全覆盖基体,无烧焦、正面无明显焦点,无明显气泡,无毛刺。
表面瓷层无开裂,无裂纹,无污点,无杂色点等。
b. 无掉瓷爆瓷,正面无疤痕,侧面背面疤痕≤3mmx3mm且不超过3处,表面流痕≤3mm且不超过3处。
正面无搪瓷缺失,背面侧面搪瓷缺失≤3mmx3mm 且不超过3处。
c. 搪瓷铸件颜色、光泽与确认之样板一致.d. 铸件变形量:面≤3mm,边≤2mm , 四脚(四角)≤2mm。
4.3 性能4.3.1 铸铁件烤漆件a. 烧烤测试:取样在烤炉空烧1小时后油漆层可炭化,且油漆气味持续时间小于15分钟(每批次取样1~2pcs),此项为实验室测试,适用于新厂商开发、新工艺确认、新产品及不定期常规测试(2~4 次/月)。
铸铁件通用检验标准(清晰整齐)
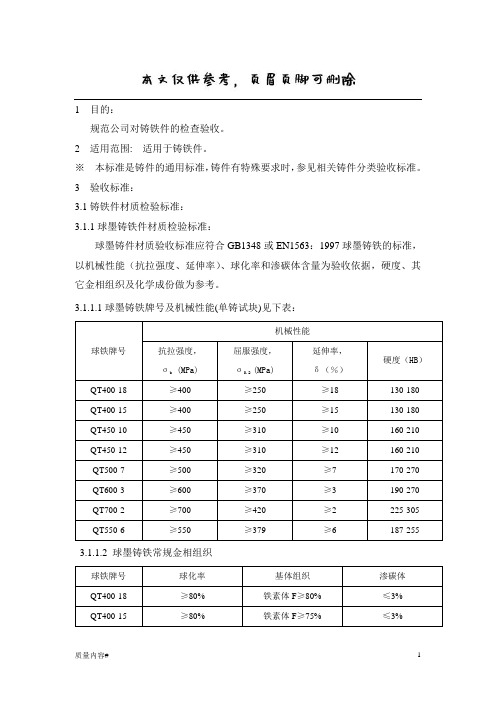
1目的:规范公司对铸铁件的检查验收。
2适用范围: 适用于铸铁件。
※本标准是铸件的通用标准,铸件有特殊要求时,参见相关铸件分类验收标准。
3 验收标准:3.1铸铁件材质检验标准:3.1.1球墨铸铁件材质检验标准:球墨铸件材质验收标准应符合GB1348或EN1563:1997球墨铸铁的标准,以机械性能(抗拉强度、延伸率)、球化率和渗碳体含量为验收依据,硬度、其它金相组织及化学成份做为参考。
3.1.1.1球墨铸铁牌号及机械性能(单铸试块)见下表:球铁牌号机械性能抗拉强度,σb (MPa)屈服强度,σ0.2 (MPa)延伸率,δ(%)硬度(HB)QT400-18 ≥400 ≥250 ≥18 130-180 QT400-15 ≥400 ≥250 ≥15 130-180 QT450-10 ≥450 ≥310 ≥10 160-210 QT450-12 ≥450 ≥310 ≥12 160-210 QT500-7 ≥500 ≥320 ≥7 170-270 QT600-3 ≥600 ≥370 ≥3 190-270 QT700-2 ≥700 ≥420 ≥2 225-305 QT550-6 ≥550 ≥379 ≥6 187-255 3.1.1.2 球墨铸铁常规金相组织球铁牌号球化率基体组织渗碳体QT400-18 ≥80% 铁素体F≥80% ≤3% QT400-15 ≥80% 铁素体F≥75% ≤3%QT450-10 ≥80% 铁素体F≥75% ≤3% QT450-12 ≥80% 铁素体F≥75% ≤3% QT500-7 ≥80% 铁素体F+珠光体P ≤3% QT600-3 ≥80% 珠光体P+铁素体F ≤3% QT700-2 ≥80% 珠光体P ≤3% QT550-6 ≥80% 珠光体P+铁素体F ≤3% 3.1.1.3球墨铸铁化学成份球铁牌号化学成份C,%Si,%Mn,%P,%S,%Mg,%Re,%Cu,%QT400-18 3.4-3.9 2.6-3.1 ≤0.2 ≤0.07 ≤0.03 0.025-0.06 0.02-0.04QT400-15 3.4-3.9 2.6-3.1 ≤0.2 ≤0.07 ≤0.03 0.025-0.06 0.02-0.04QT450-10 3.4-3.9 2.6-3.1 ≤0.3 ≤0.07 ≤0.03 0.025-0.06 0.02-0.04QT450-12 3.4-3.9 2.6-3.1 ≤0.3 ≤0.07 ≤0.03 0.025-0.06 0.02-0.04QT500-7 3.4-3.9 2.6-3.0 ≤0.45 ≤0.07 ≤0.03 0.025-0.06 0.02-0.04QT600-3 3.2-3.7 2.4-2.8 0.4-0.5 ≤0.07 ≤0.03 0.025-0.06 0.02-0.04 0.2-0.4 QT700-2 3.2-3.7 2.3-2.6 0.5-0.7 ≤0.07 ≤0.03 0.025-0.06 0.02-0.04 0.2-0.4 QT550-6 3.4-3.9 2.6-3.0 0.1-0.4 ≤0.06 ≤0.03 0.025-0.06 0.02-0.043.1.2灰铸铁件材质检验标准:灰铸件材质验收标准应符合GB9439或EN 1561:1997灰铸铁件的标准,以机械性能(抗拉强度)和硬度为验收依据,金相组织及化学成份做为参考。
铸铁铸件技术标准及接收准则

铸铁铸件技术标准及接收准则 ***/***—20**1.目的为确保公司铸铁铸件生产、检验、接收时有所依循并适合公司质量方针。
2.适用范围本标准适用于本公司生产的顾客没有提供或没有提供全部(有明确要求的及时纳入《顾客要求—材质》记录表中)技术标准和接受准则的灰铸铁铸件的检验和接收。
3.技术要求3.1材料力学性能采用国家标准:灰铁GB/T9439—88、球铁GB1348--88。
注:1.验收时,n牌号铸铁,其抗拉强度应在n 至(n+100)MPa的范围内。
2.要求本体性能请客户明确取样部位和性能要求。
3.1.2金相组织采用国家标准:灰铁GB/T7216-87(石墨形态、长度;金属基体;碳化物等)。
球铁GB9441-88 (球化分级、球化率;石墨大小;金属基体;渗碳体等)。
对于金像组织,用户有要求时,由供需双方商定,用户无要求时不作为验收依据。
3.1.3化学成分(%)铸铁的化学成分一般不作为铸件验收依据。
用户有要求时,由供需双方商定。
砂型铸造灰铸铁化学成分的参考数据%在保证抗拉强度、硬度及金相组织的前提下,上列各元素允许在如下范围内波动: C±0.050% Si±0.050% Mn±0.030% 。
3.1.4根据铸件性能要求,针对铸件重量、壁厚、冷却条件等不同对我公司生产的材质做如下分类:3.2铸件外观质量要求3.2.1铸字(包括铸造日期代码、生产厂家标志、模具编号、铸件号等)要清晰可辩并符合图纸要求或用户要求。
3.2.2铸件必须质地均匀、无裂纹以及影响产品性能的缺陷。
3.2.3铸件加工表面上,允许存在加工余量范围内的砂眼、气孔、渣眼等孔洞类铸造缺陷。
3.2.4铸件非加工表面上允许存在以下规定范围内的表面缺陷:在ф50mm范围内,允许存在3处—ф2mm×1.5mm的孔洞类缺陷,允许用铸造修补胶对其填塞修补,修补处刷硝基黑漆(按规定配比稀释后使用),然后防锈处理。
压铸件检验标准

文件名称压铸件检验标准生效日期页码 1 of 3 使用状态文件编号版本 A / 0 审核拟定目的确保本公司压铸件制程或进料品质符合客户要求。
范围适应于压铸件制程或进料入库检验。
抽样标准MIL-STD-105E单次Ⅱ级正常检验;CR=0;MA=1.0;MI=2.5。
检验环境在正常光源条件下,距离30cm远检验,以及适宜的角度检验产品。
参照标准1、GB / T2828.1-2003逐批检查计数抽样及抽样表。
2、GB / T 6414-1999铸件尺寸公差。
3、GB/T 11350机械加工余量。
4、GB/T 15115-94铝合金压铸标准。
5、GB 7000.1-2007灯具第一部分:一般要求与试验。
序号检验项目接收标准检验工具及方法缺陷描述缺陷等级致命(CR)严重(MA)轻微(MI)1外观物件的外表面之合模线不能高出平面0.05mm。
目视样板手感卡尺塞规物件的外表面之合模线高出平面0.05mm以上。
√物件的边沿、孔位不能有刺手的披锋及尖角。
物件的边沿、孔位有刺手的披锋及尖角。
√孔位周边披锋,组装后可遮盖。
孔位周边披锋,组装后不能遮盖。
√孔位周边披锋,不影响产品或对内部接线无损伤。
孔位周边披锋,影响产品组装或不能装配。
√影响产品装配,或对内部接线有损伤。
√物件表面不能有明显缩水痕。
物件的主视面,有明显缩水痕。
√物件的次要面缩水面积≤2mm2,缩水深度0.05mm。
√产品外表面及口边不能有缺料痕。
产品外表面及口边,有明显的缺料痕。
√产品孔边缺料,在组装后可遮盖,不影响产品结构。
产品孔边缺料,在组装后不可遮盖,但不影响产品结构。
√产品孔边缺料,在组装后可遮盖,但影响产品的组装、结构。
√缺料面积≤4mm2,不影响产品组装、结构。
√表面龟裂纹明显,但经加工可除去,不影响产品外观。
表面龟裂纹明显,但经加工不可除去,影响产品外观。
√序号检验项目接收标准检验工具及方法缺陷描述缺陷等级致命(CR)严重(MA)轻微(MI)1外观产品外表面花纹痕迹明显,经后续加工可消除。
铸件检验标准

铸件检验作业指导书1 目的为了有效控制铸件质量。
2范围适用于所有铸件的来料检验。
3 职责本作业指导书由品质部部长签合,分管副总批准。
4 引用标准GB/T 2828.1-2003/ISO 2859-1︰1999 计数抽样检验程序5 工作程序5.1铸件交检随附资料5.1.1每次浇铸时需保留铸造试棒两支(一支品质留档,一支计量检验)规格:Ф30X200mm,请标明型号 HT250/HT300及炉号。
5.1.2铸件化学成分检测报告;5.1.3机械性能检测报告(抗拉强度);5.1.4铸件硬度检测报告;5.1.5金相组织分析报告;5.2尺寸检验检验工具:卷尺依据:设计图纸尺寸,公差参照:CT115.3 外观检验5.3.1直线度。
(在同一平面上任意600mm范围内,直线度偏差不大于2mm)。
5.3.2扭曲变形。
(在每1000mm范围内,扭曲量不超过2mm)。
5.3.3错位。
(外漏非加工面产生错型后,应打磨成小于10゜的斜坡面)。
5.3.4铸件表面不能有裂纹,气孔,砂眼,缩孔,夹渣等其他降低结构强度或影响切削加工的铸造缺陷。
5.3.5清理。
(去除多余浇注冒口,飞边和毛刺)。
5.4底漆(防锈漆)在除锈和内外清理干净后涂以防锈底漆,底漆应喷涂均匀,不应有起皱,堆积,流挂,露底等现象。
5.5铸件要求5.5.1铸铁件表面需留有铸造编号,物料编号;5.5.2铸件驰力退火:至少24小时以上,若有其他要求时,应另立标准规范。
1)加温区:由室温以每小时不大于80℃持续加温至600±25℃止。
2)恒温区:以600±25℃的温度煲温3小时以上。
3)炉冷区:由600±25℃的温度,以每小时30±10℃持续降温至200℃以下。
4)空冷区:低于200℃以后出炉,采取空气自然冷却。
铸件检验标准
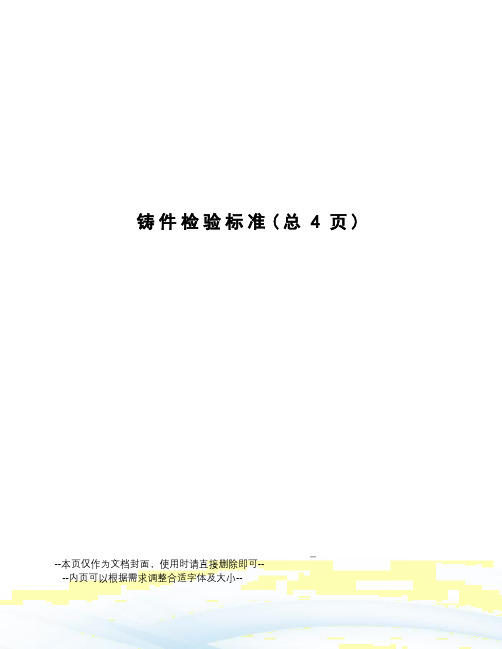
在非加工面上,缺陷的深度不超过铸件该处厚度的1/10~1/5时(重要铸件或铸件的重要部位取小值,一般铸件或铸件的一般部位取大值)
铸件质量检验是铸造生产的重要工序,其主要职能是:
a)为铸件生产和管理部门提供质量信息;保证产品质量。
b)铸件的检验主要包括铸件表面质量检验、铸件内在质量检验以及铸件质量的综合鉴定。其中,铸件的表面质量包括铸件的表面缺陷、尺寸精度、质量偏差、表面粗糙度等。
金属液冲刷型壁的时间太长,造型材料中粘土的收缩性大,大平面铸件一般容易产生包砂。
凤凰光学
集团有限公司
铸件检验规范
文件编号
版次
A0
页次
2/3
3.铸件质量检验
铸件出现铸造缺陷后,并非都是废品,应根据铸件的具体技术要求判断,判断原则如下:
a)铸件出现铸造缺陷后,其质量达不到技术要求,而又不能修补时,应列为废品;
4:铸件外观质量的检验
4.1.1检验的依据是铸件的有关标准、技术条件和图样。铸件的表面质量主要包括铸件的表面缺陷、尺寸精度、质量偏差、形状偏差、表面粗糙度和铸件表面清理质量等多方面内容。
铸件上的表面缺陷,应按具体技术要求分为3类。
凤凰光学
集团有限公司
铸件检验规范
文件编号
版次
A0
页次3/3ຫໍສະໝຸດ (1)按照技术条件允许存在的缺陷带有这类缺陷的铸件应视为合格。
冷隔
未完全融合的缝隙或洼坑,交接处是圆滑的
a) 合金浇铸温度过低,流动性差。
b)浇铸过程曾有中断,浇铸系统的形状和尺寸不合适。
错箱
铸型在分型面上错开
上、下模未对正,砂箱定位销不准,合箱时上、下箱有错动。
铝压铸件的检测标准以及铸造相关标准

大型铝压铸件的检测标准由于铝压铸件不可避免的存在气孔和夹渣,所以对铝压铸件的检测标准就显的很重要当然不同功用的铸件要求也会有所不同,不知道各大厂商是如何加强对产品的检测我公司检测标准:1)铸件的表面不允许有裂纹、欠铸、气泡、擦伤、凹陷、缺肉、网状毛刺等三角型缺陷,同时不允许有拉模现象。
2)铸件的浇口、飞边、溢流口、隔皮、顶杆痕迹等要清理干净,但允许留有痕迹。
3)铸件分型面的错型量不大于0.3mm,上下两面的平面度不大于0.3mm。
4)压铸件的顶杆痕迹凹凸量为正负0.2mm。
5)压铸未通孔厚度不大于0.3mm。
6.加工面不允许有夹杂、冷隔、疏孔等缺陷。
对于机加工后可以允许表面气孔直径不大于0.3mm,在3cm×3cm的单位面积上气孔总数不多于3个,孔边距不小于1cm。
1.熟练掌握工程制图标准和表示方法。
掌握公差配合的选用和标注。
2.熟悉常用金属材料的性能、试验方法及其选用。
掌握钢的热处理原理,熟悉常用金属材料的热处理方法及其选用。
了解常用工程塑料、特种陶瓷、光纤和纳米材料的种类及应用。
3.掌握机械产品设计的基本知识与技能,能熟练进行零、部件的设计。
熟悉机械产品的设计程序和基本技术要素,能用电子计算机进行零件的辅助设计,熟悉实用设计方法,了解现代设计方法。
4.掌握制订工艺过程的基本知识与技能,能熟练制订典型零件的加工工艺过程,并能分析解决现场出现的一般工艺问题。
熟悉铸造、压力加工、焊接、切(磨)削加工、特种加工、表面涂盖处理、装配等机械制造工艺的基本技术内容、方法和特点并掌握某些重点。
熟悉工艺方案和工艺装备的设计知识。
了解生产线设计和车间平面布置原则和知识。
5.熟悉与职业相关的安全法规、道德规范和法律知识。
熟悉经济和管理的基础知识。
了解管理创新的理念及应用。
6.熟悉质量管理和质量保证体系,掌握过程控制的基本工具与方法,了解有关质量检测技术。
7.熟悉计算机应用的基本知识。
熟悉计算机数控(CNC)系统的构成、作用和控制程序的编制。
最新铸件验收标准

根本不知道□(二)大学生对DIY手工艺品消费态度分析铸件检验标准
创新是时下非常流行的一个词,确实创新能力是相当重要的特别是对我们这种经营时尚饰品的小店,更应该勇于创新。在这方面我们是很欠缺的,故我们在小店经营的时候会遇到些困难,不过我们会克服困难,努力创新,把我们的小店经营好。产品名称:零部件名称:材料牌号:
(1)价格低
大学生的消费是多种多样,丰富多彩的。除食品外,很大一部分开支都用于。服饰,娱乐,小饰品等。女生都比较偏爱小饰品之类的消费。女生天性爱美,对小饰品爱不释手,因为饰品所展现的魅力,女人因饰品而妩媚动人,亮丽。据美国商务部调查资料显示女人占据消费市场最大分额,随社会越发展,物质越丰富,女性的时尚美丽消费也越来越激烈。因此也为饰品业创造了无限的商机。据调查统计,有50%的同学曾经购买过DIY饰品,有90%的同学表示若在学校附近开设一家DIY手工艺制品,会去光顾。我们认为:我校区的女生就占了80%。相信开饰品店也是个不错的创业方针。序号
光谱仪或化学分析
试棒或本体
1次/炉
化学分析记录表
4
金相组织
石墨大部分呈团状或球状,余为团絮状,允许有极少量蠕虫状,球化率≥85%,级别>4级
金相显微镜
本体
1次/炉
金相记录表
5
外观质量
表面和芯都不能有明显的氧化皮、毛刺、批缝、毛孔、粘砂、夹砂、裂纹、多肉、冷隔、偏芯等缺陷,油漆涂层均匀,不得有流挂、漏刷、皱皮、堆积等现象,分型面错型量<2mm
目测
本体
100%
6
内部质量
内部组织致密、无缩孔、缩松、气孔缺陷
- 1、下载文档前请自行甄别文档内容的完整性,平台不提供额外的编辑、内容补充、找答案等附加服务。
- 2、"仅部分预览"的文档,不可在线预览部分如存在完整性等问题,可反馈申请退款(可完整预览的文档不适用该条件!)。
- 3、如文档侵犯您的权益,请联系客服反馈,我们会尽快为您处理(人工客服工作时间:9:00-18:30)。
1)铸造工艺文件:内容包括原材料进厂、备料、溶化、浇注、铸件落砂、抛(喷)丸处理、铸件退火、清理、浸漆。1分
2)型砂处理工艺文件:内容包括型砂准备、型砂混碾。1分
3)造型工艺文件:内容包括模具准备、造型、下芯(视产品结构需要情况)、合箱。1分
4)制芯工艺(视产品结构需要情况):内容包括芯砂准备、芯砂混碾、制芯、烘干、配芯、涂料、表面烘干。1分
9、铸件精清理设备(砂轮风铲)3分
10、浸漆槽1分
四、
工装保障
(25分)
监视和测量
1、炉料承重:电子称或电磁称、磅秤、定量计等5分
2、熔液出炉温度及浇注温度检测:热电偶6分
3、碳当量检测仪(如光谱仪)6分
4、模具和铸件检查:划线平台、高度尺、卡尺5分
5、铸件退火温度和时间控制:钟表、测温仪表2分
6、油漆粘度检测:φ4粘度杯、秒表1分
附件1:铸件供应商专项审核评价标准
供应商名称:审核人员:审核日期:
序号
项目
主要内容
评分细则
得分
说明
一
质量体系(10分)
见中心审核标准
二
工艺文件(25分)
应具备的技术文件和内容
1、产品图:应有一拖各主机厂有效文件印章。2分
毛坯图:提供的毛坯图,其毛坯图必须经过各主机厂工艺部门会签并有效文件印章。3分
2、相关记录齐全。
五、
外观质量
(5分)
实物质量
1、毛坯外观:非加工表面及定位面不允许有飞边毛刺、粘砂、多肉、缺料、凸凹不平等现象;合模缝、浇冒口必须打磨平整;3分
2、毛坯铸造外表面粗糙度必须以本次封样为标准,并有提高。2分
(供方现场有样件)
六、
不合格品处置(5分)
不合格品有标识
不合格品有标识并隔离存放。5分
4、检验文件:原材料进货检验、工艺过程检验等。2分
三、
供方应要生产设备和生产能力。
1、化验室:化学成分检测设备、硬度仪5分
2、熔炼设备(工频炉、冲天炉):5分
3、浇包2分
4、混砂机4分
5、造型机4分
6、砂芯烘干炉1分
7、抛(喷)丸室、抛(喷)丸设备4分
8、退火炉1分
1)原材料:进货化验检验记录。2分
2)溶化:炉料配比称重记录、出炉温度记录、碳当量检测计算记录、样块试验检测记录。4分
3)浇注过程:浇注温度记录。2分
4)型砂准备:型砂配比记录。2分
5)模具:新产品模具尺寸检查记录。1分
6)铸件:退火记录、划线检查记录。1分
7)油漆:油漆粘度检测记录。1分
8)不合格处置:不合格品评审记录。1分