搪塑表皮、开闭模发泡工艺简介及设计要点
搪塑技术简介及搪塑设备工艺简介
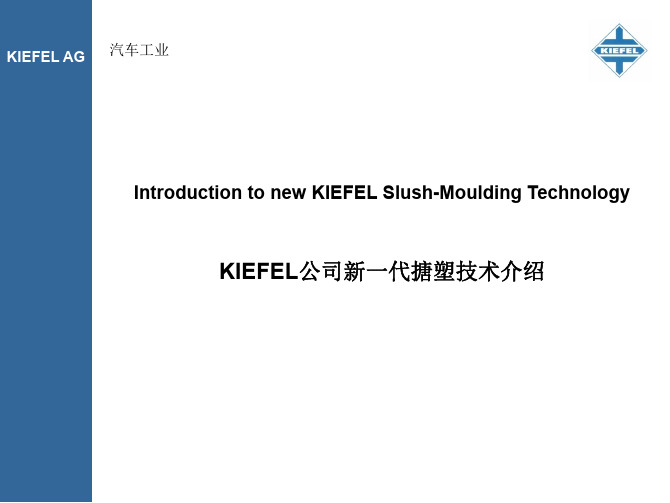
汽车工业
Existing heating-technologies of galvanos: 现有的模加热技术
Oil process: 油热工艺 • High costs for the oil-heating-equipment 油热设备具有很高的成本 • Expensive and complex galvanos with double-shell or wire-system required to fill the oil into the galvanos 昂贵而复杂的双层设计的模具,要求油路分布于模内 • Heating and cooling is possible with a wire-system 加热和冷却使用同一管路 • In case of small fatigue cracks, oil could leak out resulting in a short lifetime of the galvano 管路老化裂痕会产生油泄露, 会降低模具的寿命 Hot Air: 气热工艺 • Air is an inefficient conductor of heat 气体的热传导效率低 resulting in extended heating cycle 加热的时间长 • Very energy-intensive 能耗非常高
(1)
(2)
(3)
KIEFEL AG
汽车工业
IR-Main heating station: 红外加热工位 Approx. 150 individually adjustable IR-heaters heat up the galvano to a preset level (depending on the slush material, temperature guide 200 - 220 °C). 设有150个单独控制的加热原件, 将模具加热到约200-220 °C
汽车内饰搪塑发泡仪表板设计开发
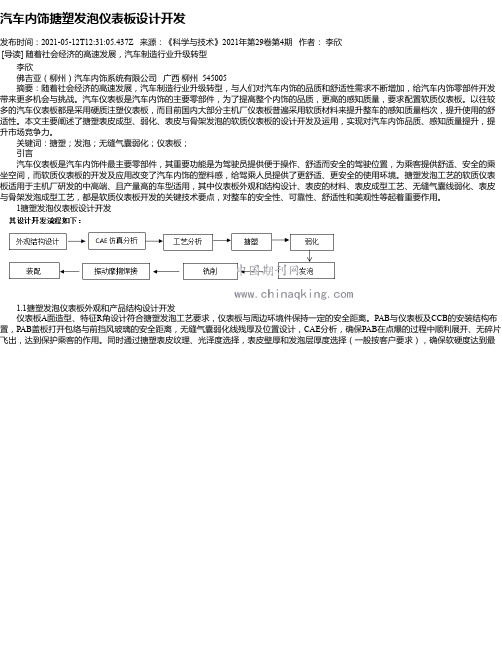
汽车内饰搪塑发泡仪表板设计开发发布时间:2021-05-12T12:31:05.437Z 来源:《科学与技术》2021年第29卷第4期作者:李欣[导读] 随着社会经济的高速发展,汽车制造行业升级转型李欣佛吉亚(柳州)汽车内饰系统有限公司广西柳州 545005摘要:随着社会经济的高速发展,汽车制造行业升级转型,与人们对汽车内饰的品质和舒适性需求不断增加,给汽车内饰零部件开发带来更多机会与挑战。
汽车仪表板是汽车内饰的主要零部件,为了提高整个内饰的品质,更高的感知质量,要求配置软质仪表板。
以往较多的汽车仪表板都是采用硬质注塑仪表板,而目前国内大部分主机厂仪表板普遍采用软质材料来提升整车的感知质量档次,提升使用的舒适性。
本文主要阐述了搪塑表皮成型、弱化、表皮与骨架发泡的软质仪表板的设计开发及运用,实现对汽车内饰品质、感知质量提升,提升市场竞争力。
关键词:搪塑;发泡;无缝气囊弱化;仪表板;引言汽车仪表板是汽车内饰件最主要零部件,其重要功能是为驾驶员提供便于操作、舒适而安全的驾驶位置,为乘客提供舒适、安全的乘坐空间,而软质仪表板的开发及应用改变了汽车内饰的塑料感,给驾乘人员提供了更舒适、更安全的使用环境。
搪塑发泡工艺的软质仪表板适用于主机厂研发的中高端、且产量高的车型适用,其中仪表板外观和结构设计、表皮的材料、表皮成型工艺、无缝气囊线弱化、表皮与骨架发泡成型工艺,都是软质仪表板开发的关键技术要点,对整车的安全性、可靠性、舒适性和美观性等起着重要作用。
1搪塑发泡仪表板设计开发1.1搪塑发泡仪表板外观和产品结构设计开发仪表板A面造型、特征R角设计符合搪塑发泡工艺要求,仪表板与周边环境件保持一定的安全距离。
PAB与仪表板及CCB的安装结构布置,PAB盖板打开包络与前挡风玻璃的安全距离,无缝气囊弱化线残厚及位置设计,CAE分析,确保PAB在点爆的过程中顺利展开、无碎片飞出,达到保护乘客的作用。
同时通过搪塑表皮纹理、光泽度选择,表皮壁厚和发泡层厚度选择(一般按客户要求),确保软硬度达到最优的效果,从而保证触感最舒适。
搪塑

搪塑是什么?滚塑电铸2008-04-18 05:28:49 阅读106 评论0 字号:大中小订阅/i?tn=baiduimage&ct=201326592&lm=-1&cl =2&fm=ps&word=%CC%C2%CB%DC搪塑图片搪塑是模塑中空制品的一种方法。
模塑时将塑料糊倒入开口的中空模内,直至达到规定的容量。
模具在装料前或装料后应进行加热,以便使物料在模具内壁变成凝胶。
当凝胶达到预定厚度时,倒出过量的液体物料,并再行加热使之熔融,冷却后即可自模内剥出制品。
一、搪塑是模塑中空制品的一种方法。
模塑时将塑料糊倒入开口的中空模内,直至达到规定的容量。
模具在装料前或装料后应进行加热,以便使物料在模具内壁变成凝胶。
当凝胶达到预定厚度时,倒出过量的液体物料,并再行加热使之熔融,冷却后即可自模内剥出制品。
目前所使用的主要是PVC塑料。
二、糊塑料热处理中的物理变化糊塑料由悬浮体变为制品的过程是树脂在加热下继续溶解成为溶液的一个过程,常称为热处理,分"胶凝"、"熔化"两个阶段。
1、胶凝阶段从糊塑料开始受热到形成薄膜表现出一定力学强度的阶段。
①由于受热,塑料不断吸收分散剂并发生肿胀。
②液体挥发,粘度逐渐增大,加热到更高的温度,糊塑料成为一种表面无光和易碎的固体物料。
此时认为胶凝阶段达到终点,温度常在100℃以上。
2、熔化阶段糊塑料在继续加热下,从胶凝终点发展到力学性能达到最佳的一段时间内的物理变化。
①肿胀的塑料颗粒粘合。
②随液体组分挥发,界面越来越小以至全部消失,树脂从颗粒成为连续透明体或半透明体。
③熔化完全后,除色料和填料外,其余的成分都处于单一相。
冷却后仍保持这种状态,且有较高力学强度。
熔化的最终温度控制在175℃左右。
搪塑设备及搪塑模具三、搪塑工艺搪塑工艺简介如下:带皮纹的搪塑模具(镍壳)背面或整体加热,模具正面扣上装有PVC(或其它塑料)粉末的粉箱,一边加热,一边转动,使粉箱中的塑料粉末粘在热模表面上,形成一个形状与仪表板一致的带皮纹的皮套,取下粉箱,模具冷却后,人工将皮套从模具上扒下。
发泡模与搪塑模的制备讲诉

二、发泡模结构及分类 – 产品特点2
2、产品特点要求:
L
切割 位置 充气密 封条
骨架:足够的工艺边用于密封 充气密封条工艺边 L>20mm 一般密封条工艺边L>15mm 硬密封L>5mm
有充气密封条过渡的凸圆角>R11;凹>R6
★ 硬密封常用于闭模浇注 ★ 充气密封条直径一般为10mm & 8mm ★ 普通密封条可使用D6或矩形 ★ 硬密封一般两种形式,a、骨架上增加凸筋, 与表皮0.2mm过 盈配合;b、模具上增加凸台
定位槽和凸台
模具公司
Tool Shop
二、发泡模结构及分类 – 零件类
4、汽车内饰常用发泡零件 仪表板
门板嵌饰板
扶手 方向盘 座椅 ……
模具公司
Tool Shop
二、发泡模结构及分类 – 发泡模分类
5、按浇注类型分类 开模浇注
闭模浇注
按表皮分类 搪塑表皮 真空吸附成型表皮 无表皮发泡,真皮包袱 按发泡区域分类 整体发泡
模具公司
Tool Shop
三、发泡模制造过程简述– 铝模翻砂
由于发泡模单件生产地性 质,铸铝模型一般用聚苯 乙烯泡沫制成(白泡), 泡沫密度越高越好。 采用重力浇注等常规浇注 方案,应将水管布局所占 区域在泡沫上加工出来; 常用水管为内径12mm,外 径14mm不锈钢钢管,泡沫 预留28mm凸起,能满足水 管铸造空间完全被包裹3 采用消失模铸造,水管弯 折在泡沫模型上,并用泡 沫碎末混合胶水包覆水管, 该方法难度较高 翻砂制成件 红色为环氧层
滑块 环氧层
密封条放置槽 加热水管
镶块
上模
滑块
气缸
下模
气缸
搪塑工艺简介

搪塑工艺流程图Slush process diagram步骤1:表皮包覆模Leather or textured foil covered master model 步骤2:阴模1#Silicone negative model #1 with supporting shell 步骤3&4:主模型及皮纹修正、客户认可Mother model corrected and engraved includingcustomer sign off步骤5:阴模2#Silicone negative model #2 with supporting shell步骤6:电镀型芯模Bath master步骤7:电镀镍壳模Electro deposition nickel shell步骤8:镍壳模表面处理Nickel shell surface treatment 搪塑模制造工艺简介Slush Shell Manufacture Process Brief Introduction步骤1:表皮包覆模Leather or textured foil covered master model步骤:1、包覆模型制造按照产品CAD数据,并计算包覆模型的材料收缩率和产品材料的收缩率,预留包覆表皮的厚度,制造包覆模型(见图I)2、表皮包覆将客户认可的表皮,按照客户要求的皮纹方向将表皮包覆在包覆模型上。
(见图II)3、客户对表皮包覆模进行确认图I 图II步骤2:阴模1#Silicone negative model #1 with supporting shell步骤:图III1、框架制造2、从表皮包覆模复制出硅氧胶阴模1#,带拼缝线(图III)步骤3&4:主模型及皮纹修正、客户认可Mother model corrected and engraved includingcustomer sign off步骤:1、框架制造2、从硅氧胶阴模1#复制出主模型,带拼缝线3、将主模型上的拼缝线处花纹进行手工修正(图IV)4、客户对修正后的主模型(图V)进行认可图IV图V步骤5:阴模2#Silicone negative model #2 with supportingshell步骤:图VI 1、框架制造2、从主模型复制出硅氧胶阴模2#(图VI),此硅氧胶阴模可复制4-6个电镀型芯模步骤6&7&8:电镀型芯模、电镀镍壳模及镍壳模表面处理Bath master、Electro deposition nickel shell、Nickel shell surface treatment1、从硅氧胶阴模2#复制出电镀型芯模图VII2、将电镀型芯模放入电镀池中进行电镀。
PVC搪塑 聚氨酯喷涂成型表皮(PU SPRAY)
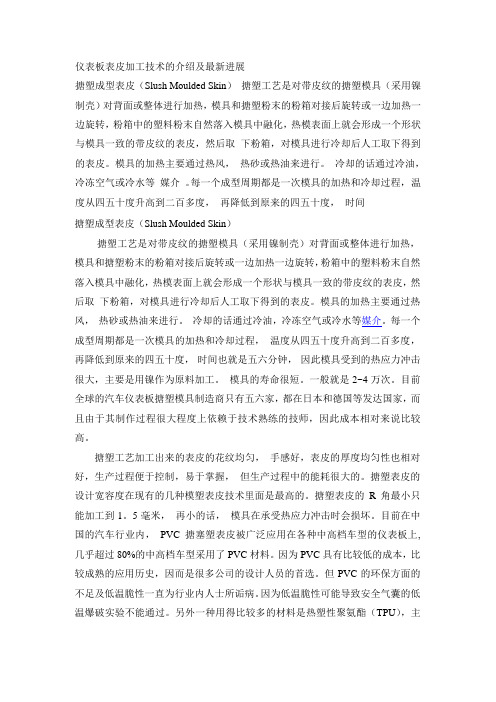
仪表板表皮加工技术的介绍及最新进展搪塑成型表皮(Slush Moulded Skin)搪塑工艺是对带皮纹的搪塑模具(采用镍制壳)对背面或整体进行加热,模具和搪塑粉末的粉箱对接后旋转或一边加热一边旋转,粉箱中的塑料粉末自然落入模具中融化,热模表面上就会形成一个形状与模具一致的带皮纹的表皮,然后取下粉箱,对模具进行冷却后人工取下得到的表皮。
模具的加热主要通过热风,热砂或热油来进行。
冷却的话通过冷油,冷冻空气或冷水等媒介。
每一个成型周期都是一次模具的加热和冷却过程,温度从四五十度升高到二百多度,再降低到原来的四五十度,时间搪塑成型表皮(Slush Moulded Skin)搪塑工艺是对带皮纹的搪塑模具(采用镍制壳)对背面或整体进行加热,模具和搪塑粉末的粉箱对接后旋转或一边加热一边旋转,粉箱中的塑料粉末自然落入模具中融化,热模表面上就会形成一个形状与模具一致的带皮纹的表皮,然后取下粉箱,对模具进行冷却后人工取下得到的表皮。
模具的加热主要通过热风,热砂或热油来进行。
冷却的话通过冷油,冷冻空气或冷水等媒介。
每一个成型周期都是一次模具的加热和冷却过程,温度从四五十度升高到二百多度,再降低到原来的四五十度,时间也就是五六分钟,因此模具受到的热应力冲击很大,主要是用镍作为原料加工。
模具的寿命很短。
一般就是2~4万次。
目前全球的汽车仪表板搪塑模具制造商只有五六家,都在日本和德国等发达国家,而且由于其制作过程很大程度上依赖于技术熟练的技师,因此成本相对来说比较高。
搪塑工艺加工出来的表皮的花纹均匀,手感好,表皮的厚度均匀性也相对好,生产过程便于控制,易于掌握,但生产过程中的能耗很大的。
搪塑表皮的设计宽容度在现有的几种模塑表皮技术里面是最高的。
搪塑表皮的R角最小只能加工到1。
5毫米,再小的话,模具在承受热应力冲击时会损坏。
目前在中国的汽车行业内,PVC搪塞塑表皮被广泛应用在各种中高档车型的仪表板上,几乎超过80%的中高档车型采用了PVC材料。
发泡模与搪塑模的制备
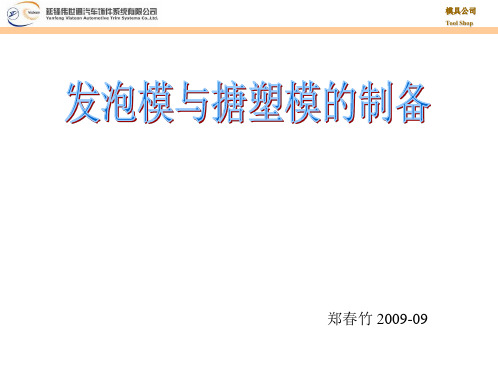
滑块、抽芯、镶块 等结构分型边界均 应放置在圆角上
模具公司
Tool Shop
用分析工具找出倒勾面,确定 脱模结构,方法同设计注塑模
模具公司
Tool Shop
二、发泡模结构及分类
–
型腔系统2
表皮真空抽气槽 充气密封条
滑块环氧层
6、发泡模型腔系统
表皮
②环氧层厚度5-8mm;
铸铝厚度15-20mm;
③在表皮不易紧密吸附
采用消失模铸造,水管弯 折在泡沫模型上,并用泡 沫碎末混合胶水包覆水管, 该方法难度较高
模具公司
Tool Shop
红色为环氧层
翻砂制成件
三、发泡模制造过程简述– 铝模翻砂
模具公司
Tool Shop
铸造技术提高:
真空铸造技术的应用,能 提高铸件的密度和强度, 减少铸造缺陷
铝模采用真空铸造是发泡 模制造的趋势
模具公司
Tool Shop
二、发泡模结构及分类 – 产品特点2
2、产品特点要求: 骨架:足够的工艺边用于密封
充气密封条工艺边 L>20mm
L
切割 位置
一般密封条工艺边L>15mm 硬密封L>5mm
充气密 封条
有充气密封条过渡的凸圆角>R11;凹>R6
R
★ 硬密封常用于闭模浇注 ★ 充气密封条直径一般为10mm & 8mm ★ 普通密封条可使用D6或矩形 ★ 硬密封一般两种形式,a、骨架上增加凸筋,
般先抽有定位凸台和定位槽区域, 其余区域轻微真空,待表皮铺设 准确,再全力抽真空
⑤上模吸盘推荐使用3.5褶皱 的硅胶吸盘,根据骨架形状可采 用伸缩气缸辅助吸附
带伸缩气缸 的吸盘
发泡模与搪塑模的制备解读

⑤上模吸盘推荐使用3.5褶皱 的硅胶吸盘,根据骨架形状可采 用伸缩气缸辅助吸附
带伸缩气缸 的吸盘 普通吸盘
模具公司
Tool Shop
Φ10 &Φ8 二、发泡模结构及分类 – 密封系统
6、密封系统 ①PU料密封:a、根据排气和 工艺需要,采用分段充气密封策 略,侧壁或陡峭斜面推荐采用充 气密封条;b、平坦区域可采用一 般密封条密封;c、密封边界狭窄 区域采用硬密封。 ②滑块之间、滑块与本体之间 均需要严格密封,形成封闭的真 空缝隙;(为了防止密封条在运 动中磨损,设法放置在垂直碰面 上,至少保证斜面45°
模具公司
Tool Shop
一、发泡模生产流程
开模浇注生产流程: ①顶出机构、滑块复位→②铺设表皮(自动感应抽真空吸附) →③ 上模放置骨架(自动感应,吸盘或真空吸附) →④模架旋转(合适 的浇注位置) →⑤浇注→⑥合模→⑦锁模→⑧气垫顶出(加锁模力) →⑨充气密封条充气(根据排气情况分段充气密封) →⑩气垫下降 或充气密封条放气排气(上模真空或吸盘断)→ ⑾合紧模熟化→⑿ 模架旋转至取件状态→⒀开锁、气垫下降(断真空)→⒁开模→⒂ 开模→⒃滑块、抽芯依次打开→⒄顶块将产品顶出→⒅取件……. (切割) 闭模模浇注生产流程: …… → ⑤放置在⑩前;其它过程相似
15~25mm
充气密封 条截面
60 ° 充气密封条进 气接头方式
滑块、本体之间密 封条形状(4*6)
Tool Shop
二、发泡模结构及分类 – 产品特点2
2、产品特点要求:
L
切割 位置 充气密 封条
骨架:足够的工艺边用于密封 充气密封条工艺边 L>20mm 一般密封条工艺边L>15mm 硬密封L>5mm
搪塑工艺介绍-SMCA

S.M.C.A.Route de Lapugnoy 62920 CHOCQUES Phone : +33 3 21 57 20 20 Fax : +33 3 21 57 66 11 Email : smca2@日期 :14/03/2005 主题 :自动搪塑机自动搪塑机 C.A.S.Ma) 搪塑工艺介绍搪塑工艺是对带皮纹的搪塑模具(采用镍制壳)对背面或整体进行加热,模具和装 有 PVC(或其它材料)粉末的粉箱对接后旋转或一边加热一边旋转(其方式取决于模具 的类型和实现搪塑工艺的方法方式),粉箱中的塑料粉末自然落入模具中融化或是胶 化,热模表面上就会形成一个形状与仪表板一致的带皮纹的皮套,然后取下粉箱,对模 具进行冷却后人工取下得到的 PVC 皮膜。
搪塑皮膜与仪表板框架放在发泡模中,注入 PU 发泡料,熟化后成为搪塑表皮发泡仪表板。
搪塑模具加热有 3 种方式:煤气加热 (或电加热)、油加热、沙加热。
搪塑仪表板的优点是生产的皮套皮纹均匀、清晰、 美观。
在搪塑工艺未出现以前,主要采用的真空热成型工艺或真空复贴工艺,它是将带 皮纹的 PVC 表皮加热,拉伸后吸附在成型模或仪表板框架上,由于 PVC 表皮经不均匀 的拉伸,使皮纹变形影响了美观。
而搪塑表皮的皮纹是刻在模具上的,所以得到的表皮 皮纹清晰美观。
b) 自动搪塑机系统介绍 1. 系统机构机器由一个主搪塑模具旋转循环传送器、一个煤气或电加热炉(一套胶化系统)、 一套冷却系统、(一套粉末传送系统)、一套自动粉末加料系统、一套监控监测系统和 多个外围设备组成。
系统的硬件软件都实现了模块化,可以根据客户的需求方便的安装 拆卸以适应不同的产品和生产率的要求。
例如:CASM4 (4 臂自动搪塑机)加热炉 框架, 模具置于框架中卸模工位 加粉岗位(或胶化)冷却中心循环传送器 4 个臂S.M.C.A.- 1/9 -中国联络处:上海能多机电设备有限公司 电话:86-21-6460 0782 传真:86-21-64600792S.M.C.A.Route de Lapugnoy 62920 CHOCQUES Phone : +33 3 21 57 20 20 Fax : +33 3 21 57 66 11 Email : smca2@日期 :14/03/2005主题 :自动搪塑机2.系统特点系统采用燃气(或电加热方式),和油加热与沙加热方式相比气热电热方式更加轻便,客 户可方便的拆卸搬运。
发泡模具设计详解

发泡模具设计详解发泡模具设计详解2016发泡成型的模具就是塑料发泡模具。
将发泡性树脂直接填入模具内,使其受热熔融,形成气液饱和溶液,通过成核作用,形成大量微小泡核,泡核增长,制成泡沫塑件。
常用的发泡方法有三种:物理发泡法,化学发泡法和机械发泡法。
下面一起来看看发泡的模具设计原理,希望对大家的学习有所帮助!一、发泡模成型机的原理1、发泡原材料的种类:EPS,EPP,EPE,EPO等。
2、成型原理:合模,加料,利用蒸汽加热成型,再冷却,脱模。
二、 EPS模具总体结构根据客户机型的种类来设计模具,与客户机台配套。
1、水箱(汽室):三片式模具,客户有标准水箱。
台湾机、方圆机、等机台没有标准水箱,必须根据产品的排模来定水箱,又叫一体模。
2、三片式模具,都具有三片板,分别叫凸模板、凹模板、枪板,凸模板来固定连接凸模型腔,凹模板用来固定连接凹模型腔,枪板也叫做后封板、背板、主要装顶杆套和料枪。
3、压料:为凸模与凹模配合,方便预开加料成型而设计的一种结构,起到预开加料时不跑料。
根据水箱的合模台阶、模板来计算,压料有离空和没有离空两种,没有离空的,凹凸模的压料相同,有离空的,凹模压料加离空等于凸模压料,凹模压料不少于10 mm。
4、法兰边:也就是凹模与凹模板连接处的.空间,方便安装螺丝钉,根据水箱合模台阶和模板来定,一般做到15 mm左右为宜,不能少于10mm,还有一种,从模板下面往上面套,叫反托,反托高度根据模板的厚度来定,如库尔特机型,一般采用反托式,日本机型一般采用正面安装,有法兰边。
5、壁厚:EPP模具的壁厚一般在15 mm左右,EPS模具、EPO 模具的壁厚在8~10 mm之间,EPE模具的壁厚一般在15 mm,除客户特别说明要求。
6、缩水:一般的发泡模具EPS材料的缩水为0.3%(国内)国外0.4%,倍率低的客户要求提供0.25%、0.2%等,EPO材料一般在0.9%~1.0%之间;EPP、EPE材料根据倍率的不同,缩水也不同;EPP、EPE材料又分JSP原料、卡内卡原料等,缩水又不同,所以EPP、EPE 等材料的缩水是客户提供,也可以叫生产原材料厂家提供,如国内两家原料公司,JSP、卡内卡;7、气芯:气芯∮4、∮6、∮8、∮10、∮12等规格,有条型和针孔两种类型,还有一种叫无孔气芯,闷气芯;根据要求分一般气芯,特殊气芯,如条型的,条型直缝为0.25mm~0.4mm的为特殊气芯,一般用线切割加工制作;普通的条型直缝为0.8 mm ~0.7mm;EPS原材料模具,采用针孔气芯比较多,EPP、EPE等原材料模具采用条型气芯比较多,指平面、侧面一般用针孔;气芯按材质分,有铝气芯,铜气芯、不锈钢气芯,常用的是铝气芯,其它根据客户要求来定。
汽车内饰主流的六大制造工艺

汽车内饰主流的六大制造工艺随着汽车技术的快速发展,大量的新技术、新材料和新工艺在汽车上得到广泛应用尤其是对汽车内饰的精致性、舒适性和豪华性要求越来越高。
而满足用户对汽车内饰的要求,更离不开汽车内饰的各种制造工艺。
为此,今天小编针对当前汽车内饰的主流制造工艺及应用情况进行了介绍。
一、搪塑成型1. 什么是搪塑成型搪塑成型,又称旋转成型,主要用于制作软质仪表板和门护板的表皮。
该技术起源于日本,在21世纪初才开始引进国内的,最初只在少数合资企业中得到应用,直到近几年才在国内的自主品牌中开始逐步应用。
2. 优点与缺点优点:原材料来源广泛,价格便宜,有着丰富的设计和生产经验,表皮的花纹不仅清晰、美观,而且一致性非常好。
可以设计出比较复杂的型面特征,制得的产品有良好的弹性和低收缩率。
缺点:模具的投资成本大,且寿命短(一般模具的质量保证只有2~3万次表皮寿命);设备的投资成本大;需要不断清理模具,导致辅助工时较长。
3. 成型工艺原理图搪塑工艺先将带有表面花纹的搪塑模具加热到搪塑表皮的成型温度,然后将粉箱与搪塑模扣合,使之按设定的程序进行旋转。
当粉料熔化并粘附于模具表面达到一定厚度后,脱开粉箱;接着,继续加热模具的外表面,使模具内表面的搪塑表皮得以塑化烧结;最后,快速冷却模具外表面,使表皮冷却成型。
1. 成型工艺图膜内转印的膜片结构2. 成型工艺图膜内转印的制作工艺流程是指将事先设计有不同花纹的膜片在合模前吸附到注塑模具的型腔表面,再将熔融状态的塑胶(一般为PC+ABS)注射到模具内,从而使膜片与塑胶融合为一体。
3. 优点与缺点优点:1)一体成型,制程简化,降低生产/库存成本及工时,缩短产品制造周期,提高生产效率;2)各类可靠性测试均为业界最高水准,保证产品的稳定性及耐久性;3)高自动化生产,保证高良品率稳定生产;4)采用自动印刷及环保油墨,符合环保要求;5)可作多色印刷,如木纹丶炭纤维丶金属色系等。
产品表面纹理及坑纹可同时着色。
搪塑工艺及搪塑模具知识

1 介绍我们的任务是按照客户的要求生产出合格的仪表板。
2 说明在设计并生产任何产品之前,必须建立详细的说明书。
客户提供详细的技术说明书。
对于仪表板主要部分的技术说明,主要为:•表皮•骨架•泡沫上述三者都必须是完美的,才能生产出合格的仪表板。
在这本教材中,我们主要是讲解仪表板表皮生产中的一种技术,即搪塑。
仪表板搪塑表皮有哪些技术特点?外观:必须满足的要素:•光泽•花纹•颜色( 色牢度)•外表的凝胶状态需要避免的缺陷:•穿孔•污迹•水迹、油迹、指纹等痕迹•变形•烧伤为了降低表皮成本及使发泡容易,控制表皮重量( 即表皮厚度)优良的粘结力撕剥力延伸率肖氏硬度3技术3.1 制造方式的特性是基于什么技术•安全性、可靠性•生产速度•精确性•花纹质量•颜色•设备对于其它产品的通用性•较低的材料消耗率优点:•模具费用较低•没有合模线•表皮较软、手感较好•花纹一致性较高采用的最好方式:旋转成型3.2 旋转成型的原理是什么?旋转成型,又称搪塑成型,是一种用热塑性和/ 或热固性树脂制造中空部件的工艺。
这种工艺制造的产品能具有各种外形并且具有持续的厚度,范围从0.5-15mm。
在产品的制造过程中,产品的外表面取决于模具内表面的形状。
3.3 就仪表板而言,旋转成型的重点是什么?使用的半模叫一个壳(shell), shell 和料盒结合后绕着一个单轴作旋转。
这种方式更适于搪塑成型。
旋转过程中,粉末进入模具,与热的模具接触、熔化并在模具内壁上形成厚度不均匀的片材。
4材料4.1 材料描述4.1.1 哪些是材料必须具备的特点?•搪塑所用材料必须与生产中的其它材料有良好的相容性,如:PUR 泡沫。
•必须有良好的流动性。
•必须有良好的柔性。
•良好的防腐性。
•良好的抗老化性。
•低收缩率。
•染色的可能性。
•较低的受污染性。
•较低的水敏感性。
4.1.2 哪种材料对于搪塑成型是最好的?PVC4.1.3.1 综述PVC,即聚氯乙烯,其分子式为:PVC 是目前搪塑工艺中应用最多的材料。
仪表板表皮加工介绍

仪表板表皮加工技术的介绍及最新进展搪塑成型表皮(Slush Moulded Skin) 搪塑工艺是对带皮纹的搪塑模具(采用镍制壳)对背面或整体进行加热,模具和搪塑粉末的粉箱对接后旋转或一边加热一边旋转,粉箱中的塑料粉末自然落入模具中融化,热模表面上就会形成一个形状与模具一致的带皮纹的表皮,然后取 下粉箱,对模具进行冷却后人工取下得到的表皮。
模具的加热主要通过热风, 热砂或热油来进行。
冷却的话通过冷油,冷冻空气或冷水等 媒介 。
每一个成型周期都是一次模具的加热和冷却过程, 温度从四五十度升高到二百多度, 再降低到原来的四五十度, 时间搪塑成型表皮(Slush Moulded Skin)搪塑工艺是对带皮纹的搪塑模具(采用镍制壳)对背面或整体进行加热,模具和搪塑粉末的粉箱对接后旋转或一边加热一边旋转,粉箱中的塑料粉末自然落入模具中融化,热模表面上就会形成一个形状与模具一致的带皮纹的表皮,然后取 下粉箱,对模具进行冷却后人工取下得到的表皮。
模具的加热主要通过热风, 热砂或热油来进行。
冷却的话通过冷油,冷冻空气或冷水等媒介。
每一个成型周期都是一次模具的加热和冷却过程,温度从四五十度升高到二百多度, 再降低到原来的四五十度, 时间也就是五六分钟, 因此模具受到的热应力冲击很大,主要是用镍作为原料加工。
模具的寿命很短。
一般就是2~4万次。
目前全球的汽车仪表板搪塑模具制造商只有五六家,都在日本和德国等发达国家,而且由于其制作过程很大程度上依赖于技术熟练的技师,因此成本相对来说比较高。
搪塑工艺加工出来的表皮的花纹均匀, 手感好,表皮的厚度均匀性也相对好,生产过程便于控制,易于掌握, 但生产过程中的能耗很大的。
搪塑表皮的设计宽容度在现有的几种模塑表皮技术里面是最高的。
搪塑表皮的R角最小只能加工到1。
5毫米, 再小的话, 模具在承受热应力冲击时会损坏。
目前在中国的汽车行业内, PVC搪塞塑表皮被广泛应用在各种中高档车型的仪表板上,几乎超过80%的中高档车型采用了PVC材料。
(完整版)搪塑工艺及搪塑模具知识

1 介绍我们的任务是按照客户的要求生产出合格的仪表板。
2 说明在设计并生产任何产品之前,必须建立详细的说明书。
客户提供详细的技术说明书。
对于仪表板主要部分的技术说明,主要为:•表皮•骨架•泡沫上述三者都必须是完美的,才能生产出合格的仪表板。
在这本教材中,我们主要是讲解仪表板表皮生产中的一种技术,即搪塑。
仪表板搪塑表皮有哪些技术特点?外观:必须满足的要素:•光泽•花纹•颜色( 色牢度)•外表的凝胶状态需要避免的缺陷:•穿孔•污迹•水迹、油迹、指纹等痕迹•变形•烧伤为了降低表皮成本及使发泡容易,控制表皮重量( 即表皮厚度)优良的粘结力撕剥力延伸率肖氏硬度3技术3.1 制造方式的特性是基于什么技术•安全性、可靠性•生产速度•精确性•花纹质量•颜色•设备对于其它产品的通用性•较低的材料消耗率优点:•模具费用较低•没有合模线•表皮较软、手感较好•花纹一致性较高采用的最好方式:旋转成型3.2 旋转成型的原理是什么?旋转成型,又称搪塑成型,是一种用热塑性和/ 或热固性树脂制造中空部件的工艺。
这种工艺制造的产品能具有各种外形并且具有持续的厚度,范围从0.5-15mm。
在产品的制造过程中,产品的外表面取决于模具内表面的形状。
3.3 就仪表板而言,旋转成型的重点是什么?使用的半模叫一个壳(shell), shell 和料盒结合后绕着一个单轴作旋转。
这种方式更适于搪塑成型。
旋转过程中,粉末进入模具,与热的模具接触、熔化并在模具内壁上形成厚度不均匀的片材。
4材料4.1 材料描述4.1.1 哪些是材料必须具备的特点?•搪塑所用材料必须与生产中的其它材料有良好的相容性,如:PUR 泡沫。
•必须有良好的流动性。
•必须有良好的柔性。
•良好的防腐性。
•良好的抗老化性。
•低收缩率。
•染色的可能性。
•较低的受污染性。
•较低的水敏感性。
4.1.2 哪种材料对于搪塑成型是最好的?PVC4.1.3.1 综述PVC,即聚氯乙烯,其分子式为:PVC 是目前搪塑工艺中应用最多的材料。
汽车内饰热塑性聚烯烃弹性体(TPO)搪塑表皮性能及工艺研究
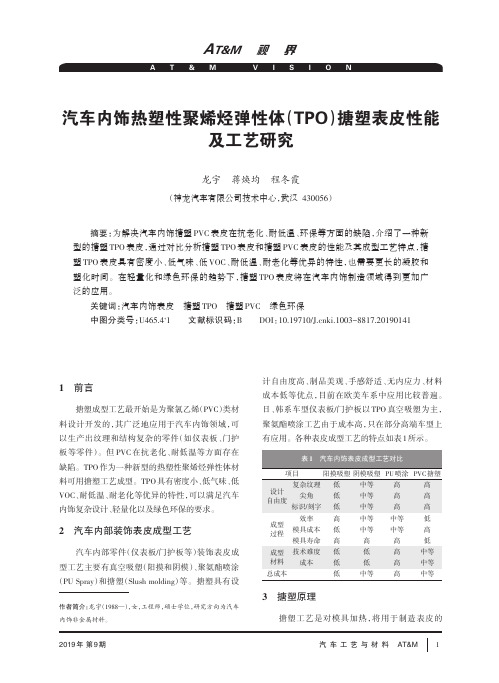
配料
熔融混合
1 mm
1 mm
(a)搪塑 PVC 粉
(b)搪塑 TPO 粉
图 3 微观示意
5 搪塑 TPO 表皮的性能
汽 车 内 饰 用 覆 盖 材 料 不 仅 要 求 质 量 轻 、美 观 精 致 、手 感 舒 适 ,并 且 对 安 全 性 能(低 硬 度 、低 脆 性),环保性能(无毒、低气味),使用性能(耐热性、
AT&M 视 界
AT&M
VISION
汽车内饰热塑性聚烯烃弹性体(TPO)搪塑表皮性能 及工艺研究
龙宇 蒋焕均 程冬霞
(神龙汽车有限公司技术中心,武汉 430056)
摘要:为解决汽车内饰搪塑 PVC 表皮在抗老化、耐低温、环保等方面的缺陷,介绍了一种新 型的搪塑 TPO 表皮,通过对比分析搪塑 TPO 表皮和搪塑 PVC 表皮的性能及其成型工艺特点,搪 塑 TPO 表皮具有密度小、低气味、低 VOC、耐低温、耐老化等优异的特性,也需要更长的凝胶和 塑化时间。在轻量化和绿色环保的趋势下,搪塑 TPO 表皮将在汽车内饰制造领域得到更加广 泛的应用。
汽 车 工 艺 与 材 料 AT&M
1
AT&M 视 界
AT&M
VISION
粉 末 状 材 料 与 受 热 的 模 具 型 腔 面 接 触 塑 化 、烧 结 等, 最终得到与模具型腔形状及纹理一致的表皮 成型过程[1]。搪塑过程主要分如下几个步骤(图 1)。
搪塑表皮、开闭模发泡工艺简介及设计要点

搪塑表皮、开/闭模发泡工艺简介及设计要点1.搪塑表皮 (1)1.1 工艺原理 (1)1.2 工艺流程 (1)1.3 搪塑优缺点 (1)1.4 搪塑工艺相关尺寸控制 (2)2. 开模发泡与闭模发泡 (2)2.1 开模发泡 (2)2.1.1工艺原理 (2)2.1.2 开模发泡的优缺点 (3)2.2 闭模发泡的特点 (3)2.3 带发泡层的仪表板相关尺寸控制 (4)1.搪塑表皮搪塑成型可设计形状复杂的产品,非常小的弧度,较深的倒角,设计自由度大,设计产品时基本不用考虑拔模角度。
工艺过程控制简单稳定,工艺控制成本低,模具清洗成本低,对工艺的影响因素较少。
同时其材料成本较低,常用来加工仪表板用表皮和门护板用表皮。
1.1 工艺原理带皮纹的搪塑模具(镍壳)背面或整体加热,模具正面扣上装有PVC(或TPU)粉末的粉箱,一边加热,一边转动,粉末在重力和热的作用下粘附在模具表面上,成型为所需形状的表皮,取下粉箱,模具冷却后,人工取下表皮。
1.2 工艺流程1)将搪塑模具本体加热至230℃~250℃;2)将模具与粉箱对合并夹紧以防止粉末露出,模具在上,粉箱在下;3)模具和粉箱一起旋转至粉箱在上,模具在下,粉箱里的粉末这时落在模具里,在高温的作用下,紧贴在模具的那一层就融化并相互粘在一起,然后继续旋转,使得模具的每个角落都有粉末,且融化并粘在一起,直至形成的表皮厚度增至符合要求为止(一般的PVC厚度为1.0mm~2.0mm),这时粉箱在下,剩余的粉末又回到粉箱。
4)模具与粉箱分离,并移到冷却工位,用水或空气等对模具进行快速冷却至60℃~80℃时,人工撕下表皮。
1.3 搪塑优缺点优点缺点1.纹理均匀美观2.手感柔软舒适3.良好的弹性以及低收缩率4.良好的机械性能5.良好的耐老化性能6.易于长途运输1.模具投资大,寿命短,一般模具的质量只有20000只表皮的寿命2.模具需要不断的清理,辅助工时消耗多3.制品的厚度、质(重)量等的准确性较差1.4搪塑工艺相关尺寸控制现以仪表罩帽檐断面为例,如图1所示,说明相关控制尺寸。
搪塑study
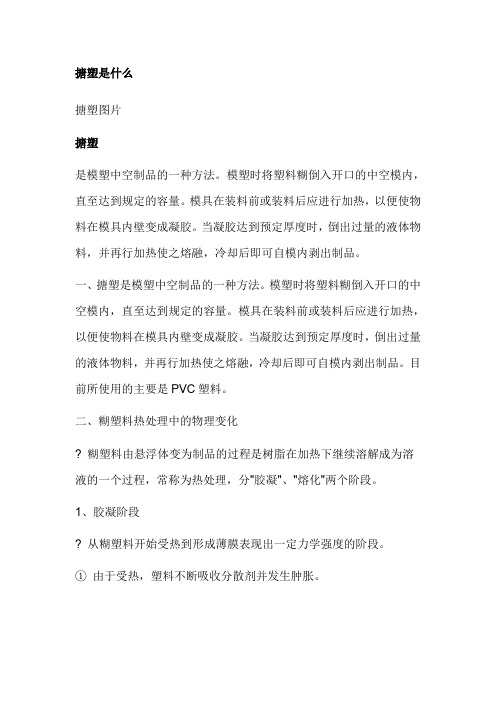
搪塑是什么搪塑图片搪塑是模塑中空制品的一种方法。
模塑时将塑料糊倒入开口的中空模内,直至达到规定的容量。
模具在装料前或装料后应进行加热,以便使物料在模具内壁变成凝胶。
当凝胶达到预定厚度时,倒出过量的液体物料,并再行加热使之熔融,冷却后即可自模内剥出制品。
一、搪塑是模塑中空制品的一种方法。
模塑时将塑料糊倒入开口的中空模内,直至达到规定的容量。
模具在装料前或装料后应进行加热,以便使物料在模具内壁变成凝胶。
当凝胶达到预定厚度时,倒出过量的液体物料,并再行加热使之熔融,冷却后即可自模内剥出制品。
目前所使用的主要是PVC塑料。
二、糊塑料热处理中的物理变化? 糊塑料由悬浮体变为制品的过程是树脂在加热下继续溶解成为溶液的一个过程,常称为热处理,分"胶凝"、"熔化"两个阶段。
1、胶凝阶段? 从糊塑料开始受热到形成薄膜表现出一定力学强度的阶段。
①由于受热,塑料不断吸收分散剂并发生肿胀。
②液体挥发,粘度逐渐增大,加热到更高的温度,糊塑料成为一种表面无光和易碎的固体物料。
此时认为胶凝阶段达到终点,温度常在100℃以上。
2、熔化阶段? 糊塑料在继续加热下,从胶凝终点发展到力学性能达到最佳的一段时间内的物理变化。
①肿胀的塑料颗粒粘合。
②随液体组分挥发,界面越来越小以至全部消失,树脂从颗粒成为连续透明体或半透明体。
③熔化完全后,除色料和填料外,其余的成分都处于单一相。
冷却后仍保持这种状态,且有较高力学强度。
? 熔化的最终温度控制在175℃左右。
搪塑设备及搪塑模具???? 三、搪塑工艺???? 搪塑工艺简介如下:? ? 带皮纹的搪塑模具(镍壳)背面或整体加热,模具正面扣上装有PVC(或其它塑料)粉末的粉箱,一边加热,一边转动,使粉箱中的塑料粉末粘在热模表面上,形成一个形状与仪表板一致的带皮纹的皮套,取下粉箱,模具冷却后,人工将皮套从模具上扒下。
搪塑皮套与仪表板骨架放在发泡模中,注入PU发泡料,熟化后成为搪塑表皮发泡仪表板。
搪塑工艺介绍
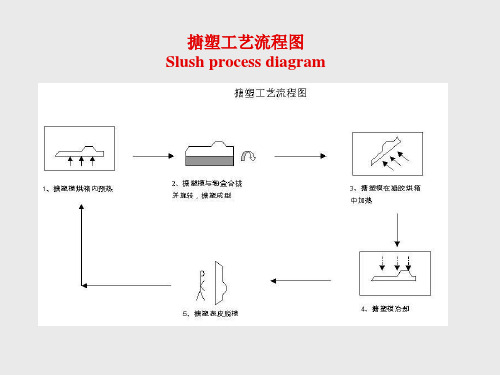
步骤: 步骤:
1、框架制造 2、从硅氧胶阴模1#复制出主 模型,带拼缝线 3、将主模型上的拼缝线处花纹 进行手工修正(图IV) 4、客户对修正后的主模型(图 V)进行认可
图IV
图V
步骤5 阴模2 步骤5:阴模2# Silicone negative model #2 with supporting shell
搪塑模制造工艺简介 Slush Shell Manufacture Process Brief Introduction
步骤1 步骤1: 步骤2 步骤2: 步骤3&4: 步骤3&4: 3&4 表皮包覆模 Leather or textured foil covered master model 阴模1 阴模1# Silicone negative model #1 with supporting shell 主模型及皮纹修正、 主模型及皮纹修正、客户认可 Mother model corrected and engraved including customer sign off 阴模2 阴模2# Silicone negative model #2 with supporting shell 电镀型芯模 Bath master 电镀镍壳模 Electro deposition nickel shell 镍壳模表面处理 Nickel shell surface treatment
时 间 Time 温 度 Temperature 角 度 Angle 速 度 Velocity
搪 塑 流 水 线 特 点(六) The characteristic of the slush line VI
• 搪 塑 模 具 与 粉 盒 的 自 由 组 合 Free combination between the slush mold and powder container • 对 加 料 系 统 的 自 动 控 制,加 料 精 确, 节 省 原 材 料 Automatically control material feeding system, ensure accurate material quantity, save the raw material
PVC搪塑 聚氨酯喷涂成型表皮(PU SPRAY)
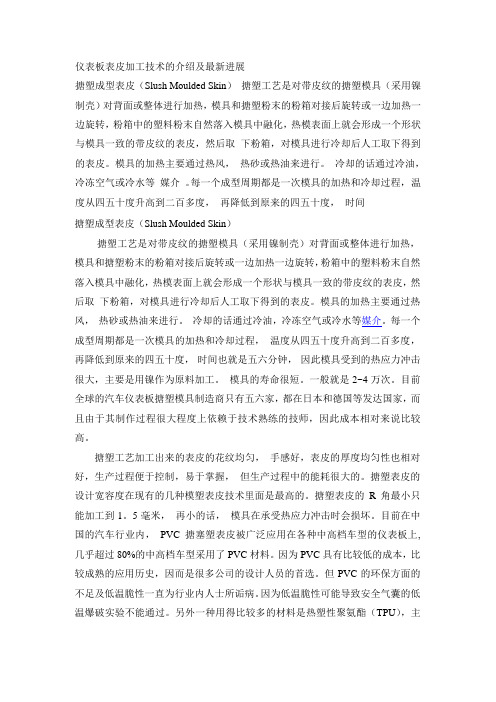
仪表板表皮加工技术的介绍及最新进展搪塑成型表皮(Slush Moulded Skin)搪塑工艺是对带皮纹的搪塑模具(采用镍制壳)对背面或整体进行加热,模具和搪塑粉末的粉箱对接后旋转或一边加热一边旋转,粉箱中的塑料粉末自然落入模具中融化,热模表面上就会形成一个形状与模具一致的带皮纹的表皮,然后取下粉箱,对模具进行冷却后人工取下得到的表皮。
模具的加热主要通过热风,热砂或热油来进行。
冷却的话通过冷油,冷冻空气或冷水等媒介。
每一个成型周期都是一次模具的加热和冷却过程,温度从四五十度升高到二百多度,再降低到原来的四五十度,时间搪塑成型表皮(Slush Moulded Skin)搪塑工艺是对带皮纹的搪塑模具(采用镍制壳)对背面或整体进行加热,模具和搪塑粉末的粉箱对接后旋转或一边加热一边旋转,粉箱中的塑料粉末自然落入模具中融化,热模表面上就会形成一个形状与模具一致的带皮纹的表皮,然后取下粉箱,对模具进行冷却后人工取下得到的表皮。
模具的加热主要通过热风,热砂或热油来进行。
冷却的话通过冷油,冷冻空气或冷水等媒介。
每一个成型周期都是一次模具的加热和冷却过程,温度从四五十度升高到二百多度,再降低到原来的四五十度,时间也就是五六分钟,因此模具受到的热应力冲击很大,主要是用镍作为原料加工。
模具的寿命很短。
一般就是2~4万次。
目前全球的汽车仪表板搪塑模具制造商只有五六家,都在日本和德国等发达国家,而且由于其制作过程很大程度上依赖于技术熟练的技师,因此成本相对来说比较高。
搪塑工艺加工出来的表皮的花纹均匀,手感好,表皮的厚度均匀性也相对好,生产过程便于控制,易于掌握,但生产过程中的能耗很大的。
搪塑表皮的设计宽容度在现有的几种模塑表皮技术里面是最高的。
搪塑表皮的R角最小只能加工到1。
5毫米,再小的话,模具在承受热应力冲击时会损坏。
目前在中国的汽车行业内,PVC搪塞塑表皮被广泛应用在各种中高档车型的仪表板上,几乎超过80%的中高档车型采用了PVC材料。
- 1、下载文档前请自行甄别文档内容的完整性,平台不提供额外的编辑、内容补充、找答案等附加服务。
- 2、"仅部分预览"的文档,不可在线预览部分如存在完整性等问题,可反馈申请退款(可完整预览的文档不适用该条件!)。
- 3、如文档侵犯您的权益,请联系客服反馈,我们会尽快为您处理(人工客服工作时间:9:00-18:30)。
搪塑表皮、开/闭模发泡工艺简介及设计要点
1.搪塑表皮 (1)
1.1 工艺原理 (1)
1.2 工艺流程 (1)
1.3 搪塑优缺点 (1)
1.4 搪塑工艺相关尺寸控制 (2)
2. 开模发泡与闭模发泡 (2)
2.1 开模发泡 (2)
2.1.1工艺原理 (2)
2.1.2 开模发泡的优缺点 (3)
2.2 闭模发泡的特点 (3)
2.3 带发泡层的仪表板相关尺寸控制 (4)
1.搪塑表皮
搪塑成型可设计形状复杂的产品,非常小的弧度,较深的倒角,设计自由度大,设计产品时基本不用考虑拔模角度。
工艺过程控制简单稳定,工艺控制成本低,模具清洗成本低,对工艺的影响因素较少。
同时其材料成本较低,常用来加工仪表板用表皮和门护板用表皮。
1.1 工艺原理
带皮纹的搪塑模具(镍壳)背面或整体加热,模具正面扣上装有PVC(或TPU)粉末的粉箱,一边加热,一边转动,粉末在重力和热的作用下粘附在模具表面上,成型为所需形状的表皮,取下粉箱,模具冷却后,人工取下表皮。
1.2 工艺流程
1)将搪塑模具本体加热至230℃~250℃;
2)将模具与粉箱对合并夹紧以防止粉末露出,模具在上,粉箱在下;
3)模具和粉箱一起旋转至粉箱在上,模具在下,粉箱里的粉末这时落在模具里,在高温的作用下,紧贴在模具的那一层就融化并相互粘在一起,然后继续旋转,使得模具的每个角落都有粉末,且融化并粘在一起,直至形成的表皮厚度增至符合要求为止(一般的PVC厚度为1.0mm~2.0mm),这时粉箱在下,剩余的粉末又回到粉箱。
4)模具与粉箱分离,并移到冷却工位,用水或空气等对模具进行快速冷却至60℃~80℃时,人工撕下表皮。
1.3 搪塑优缺点
优点缺点
1.纹理均匀美观
2.手感柔软舒适
3.良好的弹性以及低收缩率
4.良好的机械性能
5.良好的耐老化性能
6.易于长途运输1.模具投资大,寿命短,一般模具的质量只有20000只表皮的寿命
2.模具需要不断的清理,辅助工时消耗多
3.制品的厚度、质(重)量等的准确性较差
1.4搪塑工艺相关尺寸控制
现以仪表罩帽檐断面为例,如图1所示,说明相关控制尺寸。
搪塑表皮深度L:≤180mm
最小发泡层厚度:H16mm
发泡表皮倒扣深度H2:建议无倒扣
发泡层顶端最大厚度L1:≤20mm
S(L/H):≤4.5
搪塑表皮最小内、外圆角R:2mm
图1
2. 开模发泡与闭模发泡
模具内发泡成型工艺可以分为开模发泡和闭模发泡。
前者是将反应物倒入敞口模具中发泡成型再切割成所需形状的泡沫制品,而闭模发泡一般为在模具浇口处注入原料,原料直接在模具中发泡成型,即制成所需形状的泡沫制品。
2.1 开模发泡
2.1.1工艺原理
开模发泡是将反应物混匀后立即倒入敞口模具中发泡成型,再切割成所需形状
的泡沫制品。
开模浇注的原料分布比较均匀,因为可以通过机器人根据泡沫用量的多少来调节浇注的时间和路径。
例如,在泡沫层比较厚的地方机器人多停一会儿,多注射一些PU原料,在泡沫层薄的地方少注入一些原料。
由于在浇注后才能合模,合模之前泡沫不能开始膨胀,否则合模时可能会导致泡沫结构的损坏。
因此,泡沫的反应速度不能太快,这同样影响到泡沫的熟化时间。
因此,生产节拍要长一点。
总体来讲,发泡质量要好一些。
2.1.2 开模发泡的优缺点
优点缺点
1.设备投资少,占地面积小;
2.设备结构简单,操作和维修简单方便;
3.生产机动灵活,国内一些资金不足的小型企业和乡镇企业多用这一工艺。
1.由于开模发泡为非连续性生产软泡的技术,所以生产效率比连续法低;
2.设备多为手动操作,劳动强度较大;
3.生产能力受到限制,泡沫塑料的切割损失也较大。
2.2 闭模发泡的特点
闭模浇注是在同一个浇口注入所有原料,之后通过PU的膨胀过程填充到整个模具的型腔内,因而泡沫制品形状完全由模具决定。
PU在反应的过程中的流动性不断降低,因此,离注入点越远,泡沫填不到的可能性越大。
为了保证最难填充的区域的最小密度,势必多添加一些原料,这样一来,在比较容易填充的区域就会出现过量的情况。
而且,由于排气相对来说比较困难,产生暗泡的隐患也很高。
闭模发泡后不需要切割是因为这些孔在发泡之前都做好了,在发泡之前要对孔的周边要进行人工贴密封条进行密封,费时费力。
同时,如果孔都做在骨架上,那么注塑模的复杂程度就会增加,成本当然会相应增加。
因此,在切割上面节省下来的成本可能转移到了其他的环节。
闭模发泡由于模具闭合以后注入原料,不存在原料反应速度对合模的影响,因此可以采用快速的PU原料体系。
生产节拍时间要短一些,生产效率要高一点。
在生产量大的情况下,可以节省模具的数量。
2.3 带发泡层的仪表板相关尺寸控制
现以仪表板总成纵横两个断面为例,如图2所示,说明带发泡层的仪表板相关控制尺寸。
图2
图2
各断面图如下:
A 断面(类型Ⅰ)
A 断面(类型Ⅱ)
最小密封长度W :5mm ~10mm 边界最小厚度H :表皮层厚度
最小翻边长度W2:3mm~5mm
边界最小厚度H2:考虑与密封筋过盈0.5mm
B断面(类型Ⅰ)
最小翻边长度W3:5mm
边界最小厚度H3:表皮层厚度+3mm
B断面(类型Ⅱ)。