车发动机铝合金缸体和缸盖的铸造技术
汽车铝合金缸体缸盖铸造工艺研究现状

汽车铝合金缸体缸盖铸造工艺研究现状摘要:对铝合金零件的使用,减轻汽车的重量是节能减排的重要措施之一。
缸体缸盖作为汽车中最重要的部件,其结构比较复杂,对于高缸体缸盖的制造水平的提高是非常重要的研究方向。
在本文将就缸体缸盖主要铸造方法进行简单的介绍并对铸造工艺的未来发展进行了展望。
关键词:铝合金;铸造工艺;研究现状一、引言1.铝合金代替钢铁材料的必要性就相关数据表明,耗油量与汽车的质量成正相关,一般情况下,汽车质量每降低一个百分点,其耗油量相应的降低0.6到一个百分点。
为了缓解能源紧张的局势,以及人们的环境保护意识的加强,节能减排是保护环境最有效的手段之一。
而汽车重量的减轻非常好的契合了节能减排这一目的。
对铝合金零件的使用可以有效的减轻汽车自重。
因此铝合金的应用是汽车零部件行业的未来发展趋势。
在一辆汽车中,最重要的部件就是发动机的缸体以及缸盖,而且也是汽车部件中重量比重占得最大的。
因此对铝合金的应用可以有效减少汽车的重量。
铝合金材料几乎应用在了所有轿车缸体缸盖部分。
2.简述铝合金缺陷发动机的缸体缸盖作为汽车中最重要的部件,其结构比较复杂,其特点主要有几何形状复杂以及对加工尺寸的加工精度要求高,工作强度高,而工作条件十分恶劣等特征。
所以,在生产中,铝合金缸体缸盖铸件的合格率一般很低。
因此,在本文中将就缸体缸盖的制造的只要工艺以及其优缺点进行简要的介绍。
二、缸体缸盖主要铸造方法1.金属型铸造工艺金属型铸造工艺是比较传统的对铝合金缸体缸盖进行铸造的工艺,其主要优点是铸件冷却时间短、零件组织细密、力学性能较高等优点;其主要缺点是由于金属性铸造工艺不透气且无退让性,铸造的部件容易产生气孔、裂纹以及浇不足等缺陷。
但其总体质量还是明显比砂型铸造质量高。
金属型铸造工艺由于其工艺的特殊性,制造成本相对较高,并且生产周期长,对于单件或小批量生产的零部件一般不采用此种铸造方法。
外型上采用金属型铸造工艺,而内腔采用砂芯,这两种工艺相结合使得对缸体缸盖的金属铸造工艺变得相对简单,并且灵活。
汽车缸体铸造工艺

汽车缸体铸造工艺一、缸体材料车用发动机缸体缸盖的材质主要有灰铸铁,铝合金,蠕墨铸铁等。
传统的发动机无论是缸体还是缸盖都是采用铸铁的,但是铸铁有着许多先天的不足,例如重量大、散热性差、摩擦系数高等等。
所以,许多发动机厂商都在寻找更适合的材料制造发动机的构成部件,比如密度小的铝。
铝的比重轻,单位体积的铝结构强度要小于铸铁,所以铝缸体通常体积反而大些。
但铝容易和燃烧时产生的水发生化学作用,耐腐蚀性不及铸铁缸体,尤其对温度压强都更高的增压引擎更是如此。
铸铁缸体和铝缸体各有其优缺点,所以所以高增压的引擎很多都采用铸铁缸体,小型车的缸体则更多向铝缸体发展。
金属中的元素组成会对金属材料的性能产生较大的影响,就钢铁而言,钢中含碳量增加,屈服点和抗拉强度升高,但塑性和冲击性降低,当碳量0.23%超过时,钢的焊接性能变坏,因此用于焊接的低合金结构钢,含碳量一般不超过0.20%。
碳量高还会降低钢的耐大气腐蚀能力,在露天料场的高碳钢就易锈蚀;此外,碳能增加钢的冷脆性和时效敏感性。
不同的缸体元素配比也是有差别的。
合肥江淮铸造有限责任公司缸体化学成分要求化学成分(%)C Si Mn P S Cr Cu Ti Sn Pb下限 3.25 1.95 0.60 0.00 0.06 0.25 0.30 0.00 0.06 0.00 0上限 3.40 2.10 0.90 0.06 0.10 0.35 0.50 0.03 0.09 0.00 4二、原材料熔炼熔炼设备选用:中频感应保温电炉:生产效率10t/h,外水冷长炉龄大排距冲天炉:生产效率7t/h。
1、原材料原材料一般为回炉料,废钢和生铁。
回炉料是厂家的常备材料,在使用时必须注意其本身的干净程度。
回炉料的加入量必须严格按一定比例,否则会导致铁水的Si、S含量不易控制。
江淮生产的缸体铸件回炉料使用量一般不超过20%。
在江淮的缸体生产中,废钢的使用量超过50%。
这是由于生铁本身含有粗大石墨,而石墨熔点较高,在2000℃以上,在熔炼中不能熔尽,使得结晶过程中石墨变得粗大。
铝合金发动机缸盖制造技术探讨

合金 的熔化需要通过氩气旋转吹气 , 加入锶变质等其他 物质 ; 浇筑时先对模具进行清理 , 预热至2 0 0  ̄ C进行涂料 , 涂料时要根据 缸
3总 结 与展 望
对于铝合金发动机缸盖的铸造工艺而言 , 不只是为制造出高质
【 摘 耍l 铝合 金发动 机缸 盖的制 造 包括 了压 力铸 造 、 金属 型铸造 、 冷芯盒砂 芯组 芯造型 等几种 工 艺。 本 文对这 几种 制造 工艺进行 了简要分 析 并阐述 了在铝 合金 发动机 缸盖 制造 中常 见的低 压铸造 工艺 内容, 总结 并展 望 了未 来铝合金发 动机缸 盖制 造前景 。 I 关键 词 】 铝合 金 发动机 缸盖 制造 技术
量 的 汽车 零 件 , 还 需 要 根 据 实 际情 况 , 按 照 工厂 的生 产 条 件 和 缸 盖 机构 需求 , 选择最适合 的制造方法 。 现在 制造 铝合金缸盖多使用金
该铸造工 艺介于重力铸造和压力铸造之间 , 低压铸工艺对铝材 料 的利用 率较高 , 产品缺陷较少 , 所需压力 不高 , 产品较为完美 。 但 是采 用低压铸 造的生产率较低 , 生产时间较长 , 总体产品 的成 品率 低, 虽然在铝合金发动机缸盖 的制 造 中属于传统工艺 , 但使用该铸
1铝合金发动机缸盖制造工艺
1 . 1金 属 型铸 造 盖的形状决定薄厚 , 如浇 口附近需要涂厚一些 , 注意过滤 网的放置 , 在铝合金发动机缸盖的制造工艺中, 金属 型铸造属于传统铸造 避 免 氧 化物 杂 质 进 入 ; 浇 注 时 的 温度 要 控 制 在 7 1 0  ̄ C左 右 , 将 偏 差控 方法 , 为 重力 铸 造 的一 类 , 使用 较普 遍 。 这 种 制 造 工 艺 虽 然 有 较 好 的 制在2 0 C内, 以减小铝液温度造成 的缸盖 内部缺陷 ; 冷却时使用水 力学性和冷却性 , 但是成本较高 , 且生产过程 中易产生裂纹、 气孔等 冷或气冷 , 对于一 些浇 口 距 离过 近的位置要强制冷却 。 一般以间接 现象 。 采用金属 型铸 造的缸盖质量 同砂型铸造相 比较 , 质量 明显高 冷却为主 , 在 一些较厚 的位置可 以使用直接冷却, 冷却强度 可通过 出很 多 , 但金属型铸造不适用于小 批量零件 生产 。 时间和温度两个因素控制 ; 从缸盖的充型到浇 口凝固时间为加压时 1 . 2压 力铸 造 间, 一般控制在5 分钟左右 , 若要提升生产效率 , 可 以采用一模两件 压力铸造 , 即为压铸 , 是 目前使用较多的一种制造工艺 , 较多应 等方法进行 。 同样的 , 起模时间也受到温度 的影响, 若 时间过短会造 用于 铝合 金发动机 的缸体铸造 中, 在缸 盖铸 造中也有涉及 。 压铸 是 成缸盖 形状 变形, 时间太长则取 不出来 , 一般 的起 模时间是在加压 通过 高压 作用 , 将液态或半液态金属迅速成型凝 固。 在高压力条件 时间的三分之一处时, 起模时先 脱侧模, 再起上模 , 低压铸造时 , 要 下, 这种方法能够制造 出数据 精密程度高的铝合金零件 , 特别 是对 注意加压曲线, 如 冒口的补缩压力在0 . O 0 7 MP a 左右。 同样的, 坩埚 内 于轿车所 使用的铝合金发动机缸体和缸盖 , 应用较广泛。 使用压 铸 的液面高度也会影响到加压曲线的变化 , 升液管同坩埚底部的间隔 这种 制造工艺 , 获得的产品有较高的成 品率 , 生产力 也比较高 , 且不 高度 同样有着影响 , 一般维持在2 0 0 am左 右。 r 需要进行 热处理 , 缺点是在金属液 体的高速 流转 下 , 浇注 时产 品较
摩托车铝合金气缸盖的金属型铸造工艺

t h i c k n e s s , c o r e s e t t i n g a n d d i e c l o s i n g , p o u r i n g t e mp e r a t u r e a n d o p e n i n g t i me o n c a s t i n g q u a l i t y a r e
p r oc e s s .Th e e f f e c t s o f c l e a ni n g me t hod a nd p r e he a t i ng t e mp e r a t ur e f or pe r ma ne n t m ol d ,c o a t i n g
a na l yz e d. T o ge t h i g h q ua l i t y c y l i n de r h e a d, t h e v i t a l f un c t i o n o f a f t e r t r e a t me nt p r o c e s s c o nt r ol , i n c l u di ng s u r f a c e c l e a n i n g, p ol i s hi n g, he a t t r e a t me nt , s h ot bl a s t i n g a n d p a s s i v a t i o n, i s e x po u nd e d . Ke y wor ds :p e m a r n e n t mo l d c a s t i ng; a l u mi n u m a l l o y; c yl i nd e r h e a d
画
摩托 车铝合 金气 缸盖 的金属型 铸造 工艺
论汽车铝合金缸体缸盖铸造工艺研究现状

论汽车铝合金缸体缸盖铸造工艺研究现状作者:孙洪强来源:《时代汽车》 2018年第6期本文就从铝合金缸体缸盖铸造层面出发,列举了当前主要的铸造方式,有金属型铸造工艺、压力铸造方式、中压铸造方式、低压铸造方式、消失模铸造方式、冷芯盒砂芯造型铸造方式等七种。
并分别对其优点以及不足进行分析,探讨其方式最适用的情况和状态,并分析其相应铸造方式所铸造出铸件的各自特点,并对其所需要的生产成本进行说明,以此使得汽车行业能够根据自身的实际特点,与其生产的汽车特色,来选择最适合自身的铸造方式,并对其不断的进行完善和改进,使得汽车零件铸造工艺能够不断的发展。
1铝合金缸体缸盖随着时代科技的不断发展,汽车已经逐渐成为人们出行的必要工具,因为共强大的便利性和功能,深受广大群众的喜欢。
一辆汽车是由各式各样的零部件所构成的。
这些零部件慢慢的拼装出庞大的汽车系统,才实现了汽车飞快的速度以及其他强大的功能。
因此,汽车工业可以在一定程度上带动很多其他行业的发展,正像:缸体缸盖铸造工艺。
发动机作为一辆汽车最为核心的部分,其缸体与缸盖是核心中的核心,是汽车众多有色零件中原辅材料消耗较大,工艺技术含量较高的零件之一,共重量达到汽车有色零部件的首位。
当前,汽车的轻量化已经是现下以及未来的发展方向。
汽车轻量化主要足在确保机车安全和性能的前提下,通过轻量化材料把汽车的重量整体变轻以此可以减少油量的损耗,做到节能减排的效果,达到保护环境的目的。
汽车轻量化极其符合当前的环保需要,因此汽车轻量化逐渐成为了最有效以及便利的保护环境的方式之一。
共为了达到减少汽车重量的目的,可以使用轻合金材料,如铝合金材料,因其轻便,以及美观,在汽车零部件的生产中非常常见。
目前汽车轻量化的重要实现方式就是发动机使用铸造铝合金缸体缸盖。
研究汽车发动机的缸体缸盖铸造工艺,其不仅仅可以达到汽车轻量化的目的,还需要设计好内部结构以及选择合理的生产工艺。
就共是汽车发动机最重要的零件之一而言,在其生产和后续加工过程中需要严格按要求控制好其尺寸精度。
车发动机铝合金缸体和缸盖的铸造技术

8、湿型铸造
美国GM汽车公司萨基诺金属铸造厂(SMCO)数年前将其原生用于生产铸铝件的高压造 型线改建用于生产铝缸盖,在2001年用粘土砂湿型生产了1,925,000铝缸盖。
丹麦DISA公司近年来一直致力于开发利用其垂直分型无箱射压造型机及低压浇注来生
日本Toyota丰田公司采用类似于低压铸造的真空吸铸法(图6)生产铝缸体。
i.........。......。,.。.......................一
M£,AL RE TtffqN.
图5
o…。,.........。j
i
、’_:
图6
4、金属型铸造
金属型铸造主要用于生产铝缸盖及简单的铝缸体。 德国Daimler—Chrysler公司有两台直径分别为12米及13米的12工位转盘金型机(图7) 缸盖,生产铝缸盖。 毛坯重12公斤,浇冒口重6公斤。浇注温度为730"C,浇注时间为9秒,生产节拍为30 秒。浇注后缸盖进行热处理。
. …。.~~一…l
图3
图4
3,低压铸造
低压铸造是铝液在很低的压力("-0.03Mpa)下由下而上地充填型腔(图5)通常采用的 是金属型和砂芯,因此可以获得闭舵结构的缸体。
这种方法的缺点是生产率低,因为虽然充型时间一般仅需5一.15秒,但保压时间则需3~ 6分钟,整个生产循环达10b l 1分钟。在大量生产轿车缸体、缸盖时,就需要多台机器和多 套模具。美国福特公司用此法生产铝缸盖。
实型铸造
BH
H
精确砂型 铸造
B
B
说明:B为缸体:H为缸盖
由此可见,由于铝合金浇注温度低(700"C上下),其铸件工艺是多样化的。但是对于一 个轿车制造厂来讲,选择适宜的铸造工艺是极为重要的。为此,必须对各种铸造工艺产品质 肇的综合影响进行深入的调研和分析.才有可能作出正确的选择。
压铸铝合金缸体生产工艺简介

压铸铝合金缸体生产工艺简介摘要:本文叙述了压铸铝合金缸体的生产工艺技术。
分析了化学成分、球化及孕育处理等主要工艺因素对铸铁质量的影响。
通过工艺研究、现场生产及对影响铸件质量的主要因素进行分析,给出了该铸件合理的合金配比、球化处理及复合孕育工艺。
关键词:化学成分球化处理复合孕育随着汽车行业轻量化趋势明显,对铝合金部件拉动巨大,汽车零部件轻量化发展进入黄金时期,尤其是能源和环保问题的日益突出,对产品零件轻量化提出了更高的要求。
铝合金发动机缸体时汽车发动机的核心零部件之一,对汽车产业轻量化的发展起着至关重要的推动作用。
现将发动机缸体铸件的全生产工艺做简要介绍,为广大读者提供参考。
1. 产品简介四缸铝合金缸体(长宽高:385*390*285),缸体重约18kg,材质:AlSi9Cu3,排量1.5L。
产品主要技术要求:抗拉强度≥ 240MPa;硬度≥HB80;延伸率≥1.0%。
2. 生产工艺简介生产线主要工艺流程为:熔化-压铸-抛丸-粗加工-浸渗-检验。
2.1 熔化生产工艺熔化生产工艺流程有:配料→加料→熔化→出铝→去渣→除气检测→转运→保温。
集中熔化炉为塔式天然气炉,熔化量为800kg/h。
保温炉为热电偶加热炉,最大保持量2500kg。
铝锭原材料要保证铝锭的化学成分、力学性能、断面检查符合要求,铝锭与回炉料质量配比≥50%;熔化温度750±20℃,出铝温度720±10℃,每班开线前需对铝包进行预热;除气机惰性气体压力≥0.5MPa,除气时间:4 min~10min;除渣剂加入量按每包铝水(约700kg)加入1Kg±50g,;铝液密度要求为2.61g/cm3;精炼后的铝液成分需满足要求,合格铝液通过叉车转移至压铸机旁的保温炉,铝液保温温度控制在660±10℃。
2.2 压铸生产工艺压铸机选用压铸主机为DCC2500T冷压室压铸单元。
压铸的生产工艺流程有机边保温炉浇注→放置缸套→压铸→机器人取铸件→光电检测渣包→去渣包→打码→冷却→去除浇冒口→取铸件放置到输送带。
汽车铝合金汽缸体低压铸造技术分析
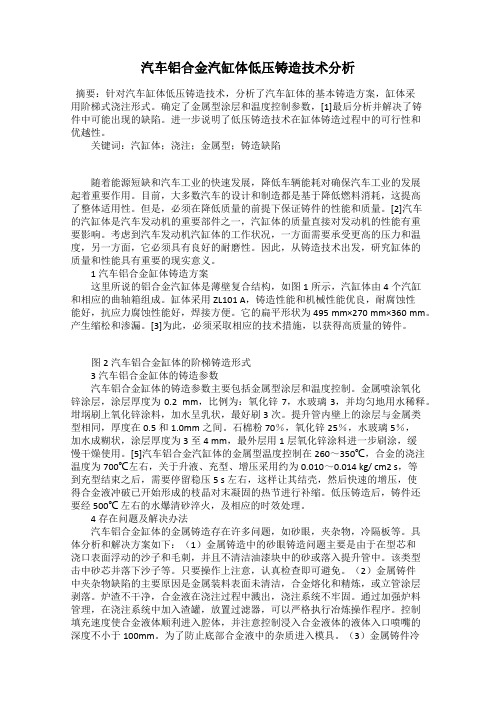
汽车铝合金缸体的金属铸造存在许多问题,如砂眼,夹杂物,冷隔板等。具体分析和解决方案如下:(1)金属铸造中的砂眼铸造问题主要是由于在型芯和浇口表面浮动的沙子和毛刺,并且不清洁油漆块中的砂或落入提升管中。该类型击中砂芯并落下沙子等。只要操作上注意,认真检查即可避免。(2)金属铸件中夹杂物缺陷的主要原因是金属装料表面未清洁,合金熔化和精炼,或立管涂层剥落。炉渣不干净,合金液在浇注过程中溅出,浇注系统不牢固。通过加强炉料管理,在浇注系统中加入渣罐,放置过滤器,可以严格执行冶炼操作程序。控制填充速度使合金液体顺利进入腔体,并注意控制浸入合金液体的液体入口喷嘴的深度不小于100mm。为了防止底部合金液中的杂质进入模具。(3)金属铸件冷绝缘缺陷的主要原因是金属温度低,铸造温度低,涂层薄,铸造速度慢,二次填充等。防止的方法应对症采取措施。[6]一般而言,汽车铝合金缸体的金属型铸造工艺中的相关缺陷可以对称解决,以确保铸件的性能。
图2汽车铝合金缸体的阶梯铸造形式
3汽车铝合金缸体的铸造参数
汽车铝合金缸体的铸造参数主要包括金属型涂层和温度控制。金属喷涂氧化锌涂层,涂层厚度为0.2 mm,比例为:氧化锌7,水玻璃3,并均匀地用水稀释。坩埚刷上氧化锌涂料,加水呈乳状,最好刷3次。提升管内壁上的涂层与金属类型相同,厚度在0.5和1.0mm之间。石棉粉70%,氧化锌25%,水玻璃5%,加水成糊状,涂层厚度为3至4 mm,最外层用1层氧化锌涂料进一步刷涂,缓慢干燥使用。[5]汽车铝合金汽缸体的金属型温度控制在260~350℃,合金的浇注温度为700℃左右,关于升液、充型、增压采用约为0.010~0.014 kg/ cm2 s,等到充型结束之后,需要停留稳压5 s左右,这样让其结壳,然后快速的增压,使得合金液冲破已开始形成的枝晶对末凝固的热节进行补缩。低压铸造后,铸件还要经500℃左右的水爆清砂淬火,及相应的时效处理。
汽车铝合金下缸体压铸技术要点分析及缺陷应对
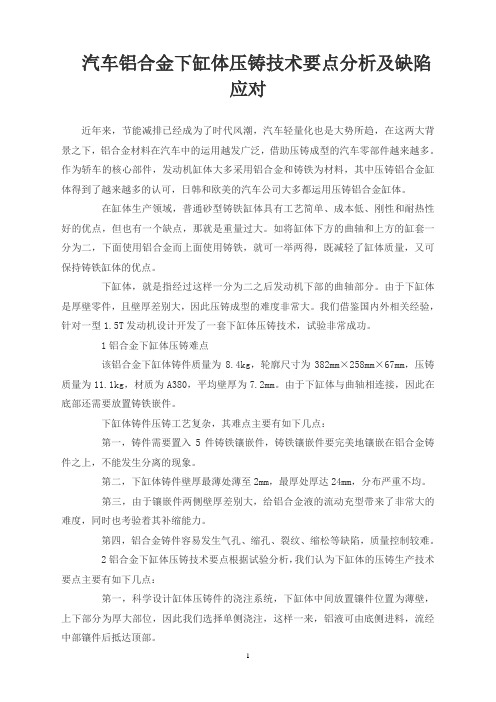
汽车铝合金下缸体压铸技术要点分析及缺陷应对近年来,节能减排已经成为了时代风潮,汽车轻量化也是大势所趋,在这两大背景之下,铝合金材料在汽车中的运用越发广泛,借助压铸成型的汽车零部件越来越多。
作为轿车的核心部件,发动机缸体大多采用铝合金和铸铁为材料,其中压铸铝合金缸体得到了越来越多的认可,日韩和欧美的汽车公司大多都运用压铸铝合金缸体。
在缸体生产领域,普通砂型铸铁缸体具有工艺简单、成本低、刚性和耐热性好的优点,但也有一个缺点,那就是重量过大。
如将缸体下方的曲轴和上方的缸套一分为二,下面使用铝合金而上面使用铸铁,就可一举两得,既减轻了缸体质量,又可保持铸铁缸体的优点。
下缸体,就是指经过这样一分为二之后发动机下部的曲轴部分。
由于下缸体是厚壁零件,且壁厚差别大,因此压铸成型的难度非常大。
我们借鉴国内外相关经验,针对一型1.5T发动机设计开发了一套下缸体压铸技术,试验非常成功。
1铝合金下缸体压铸难点该铝合金下缸体铸件质量为8.4kg,轮廓尺寸为382mm×258mm×67mm,压铸质量为11.1kg,材质为A380,平均壁厚为7.2mm。
由于下缸体与曲轴相连接,因此在底部还需要放置铸铁嵌件。
下缸体铸件压铸工艺复杂,其难点主要有如下几点:第一,铸件需要置入5件铸铁镶嵌件,铸铁镶嵌件要完美地镶嵌在铝合金铸件之上,不能发生分离的现象。
第二,下缸体铸件壁厚最薄处薄至2mm,最厚处厚达24mm,分布严重不均。
第三,由于镶嵌件两侧壁厚差别大,给铝合金液的流动充型带来了非常大的难度,同时也考验着其补缩能力。
第四,铝合金铸件容易发生气孔、缩孔、裂纹、缩松等缺陷,质量控制较难。
2铝合金下缸体压铸技术要点根据试验分析,我们认为下缸体的压铸生产技术要点主要有如下几点:第一,科学设计缸体压铸件的浇注系统,下缸体中间放置镶件位置为薄壁,上下部分为厚大部位,因此我们选择单侧浇注,这样一来,铝液可由底侧进料,流经中部镶件后抵达顶部。
汽车发动机铝合金缸体压铸工艺改进及品质提升 陈琳

汽车发动机铝合金缸体压铸工艺改进及品质提升陈琳摘要:汽车发动机作为汽车中的重要组成部分,它的性能直接影响汽车的安全性与可靠性。
传统的铝合金缸体压铸容易因为技术问题导致发动机出现漏油等问题,对缸体压铸工艺进行改进是解决此缺陷的有效途径,因此,本文就发动机缸体压铸工艺中问题发生的成因进行探讨,并在原技术的基础上进行改造。
使改造后的工艺取得显著成效。
关键词:汽车发动机;缸体压铸工艺;品质改进;一、缸体压铸工艺的优点及缺点1、效率高压铸工艺在汽车制造业的应用十分广泛,它是一种可以将原材料迅速压铸成型的工艺,尤其是其自动化、智能化的技术大大提高了机械制造的生产效率,节约了人力成本,产品的制造周期明显缩短,传统技术中需要耗费一周的产品制造,缸体压铸主需要一两天就可以完成。
2、精度高。
缸体压铸的精度进一步提升。
3、铸件的韧性和表面硬度较高。
4、减低材料成本。
一般每台设备每年可生产7万件左右。
5、占用较少的土地面积。
6、工艺流程简化。
传统的铸造工艺流程复杂,需要经过很多加工环节,费时费力。
而压铸工艺相比传统技术,不需要繁琐的加工程序,加工后也很少出现飞边毛刺等外观问题。
将模具加工完取出进行浇注,接着进行检查、加工就可以。
7、压铸也存在一定的缺点(1)铸造缺陷较多。
压铸在浇注的过程中由于需要快速将金属液体倒入型腔,在浇注时会将气体带入到型腔中,容易在产品表面留下气孔等缺陷。
另外,如果在填充过程中液体中掺有氧化后的杂质,并且没有及时排出就会留在铸件内部,影响美观。
(2)压铸首次投资成本高。
压铸需达到一定数量才能使投资成本不亏损。
二、发动机缸体油路渗漏原因分析对渗漏无法使用的发动机缸体进行拆分和外观检查,发现发动机缸体油路孔与螺纹孔之间密封不严,这是造成发动机油路漏油的主要原因,该压铸缺陷表现为形状不均匀的洞孔,且钢体内壁不光滑。
按照内壁洞孔呈现形式及发动机缸体漏油地方进行分析,发现发动机缸体漏油部位厚薄相差过大,造成缸体漏油部位铝液在此凝固,这造成此类气孔缺陷的主要原因,而此处的洞孔缺陷多是收缩气孔,一般的办法是解决不了的。
汽车发动机铝合金缸体工艺
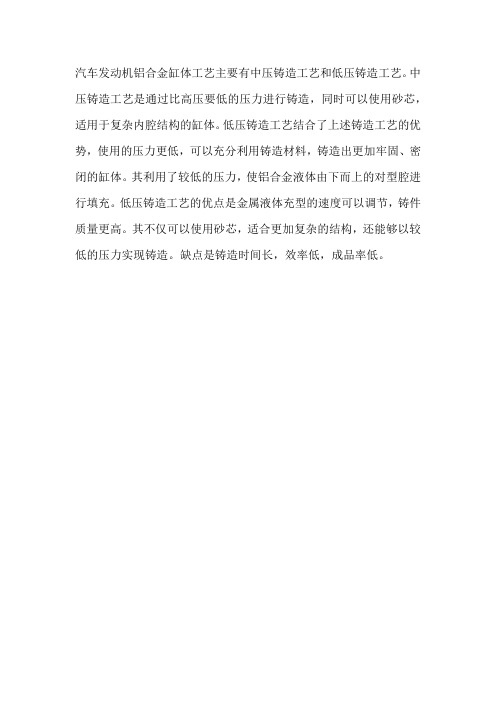
汽车发动机铝合金缸体工艺主要有中压铸造工艺和低压铸造工艺。
中压铸造工艺是通过比高压要低的压力进行铸造,同时可以使用砂芯,适用于复杂内腔结构的缸体。
低压铸造工艺结合了上述铸造工艺的优势,使用的压力更低,可以充分利用铸造材料,铸造出更加牢固、密闭的缸体。
其利用了较低的压力,使铝合金液体由下而上的对型腔进行填充。
低压铸造工艺的优点是金属液体充型的速度可以调节,铸件质量更高。
其不仅可以使用砂芯,适合更加复杂的结构,还能够以较低的压力实现铸造。
缺点是铸造时间长,效率低,成品率低。
论汽车铝合金缸体缸盖铸造工艺研究现状
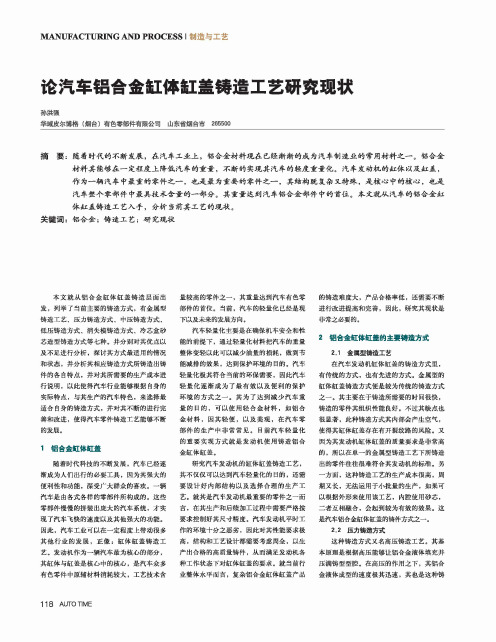
MANUFACTURING AND PROCESS I卸造与工艺论汽车铝合金缸体缸盖铸造工艺研究现状孙洪强华域皮尔博格(烟台)有色零部件有限公司山东省烟台市2655〇〇摘要:随着时代的不断发展,在汽车工业上,铝合金村料现在已经渐渐的成为汽车制造业的常用材料之一。
铝合金材料其能够在一定程度上降低汽车的重量,不断的实现其汽车的轻度重量化。
汽车发动机的缸体以及缸盖,作为一辆汽车中最重的零件之一,也是最为重要的零件之一,其结构既复杂又特殊,是核心中的核心,也是汽车整个零部件中最具技术含量的一部分。
其重量达到汽车铝合金部件中的首位。
本文就从汽车的铝合金缸体缸盖铸造工艺入手,分析当前其工艺的现状。
关键词:铝合金;铸造工艺;研究现状本文就从铝合金缸体缸盖铸造层面出发,列举了当前主要的铸造方式,有金属型 铸造工艺、压力铸造方式、中压铸造方式、低压铸造方式、消失模铸造方式、冷芯盒砂 芯造型铸造方式等七种。
并分别对其优点以 及不足进行分析,探讨其方式最适用的情况 和状态,并分析其相应铸造方式所铸造出铸 件的各自特点,并对其所需要的生产成本进 行说明,以此使得汽车行业能够根据自身的 实际特点,与其生产的汽车特色,来选择最 适合自身的铸造方式,并对其不断的进行完 善和改进,使得汽车零件铸造工艺能够不断 的发展。
1铝合金缸体缸盖随着时代科技的不断发展,汽车已经逐 渐成为人们出行的必要工具,因为其强大的 便利性和功能,深受广大群众的喜欢。
一辆 汽车是由各式各样的零部件所构成的。
这些 零部件慢慢的拼装出庞大的汽车系统,才实 现了汽车飞快的速度以及其他强大的功能。
因此,汽车工业可以在一定程度上带动很多 其他行业的发展,正像:缸体缸盖铸造工艺。
发动机作为一辆汽车最为核心的部分,其缸体与缸盖是核心中的核心,是汽车众多 有色零件中原辅材料消耗较大,工艺技术含量较高的零件之一,其重量达到汽车有色零部件的首位。
当前,汽车的轻量化已经是现下以及未来的发展方向。
汽车发动机铝合金气缸盖铸件技术条件

Q/HO汽车发动机铝合金气缸盖铸件技术条件重庆海鸥铸造有限责任公司发布前言本标准规定了铝合金汽车发动机气缸盖的要求、试验方法、检验规则、标志、包装、运输和储存的要求。
本标准由重庆海鸥铸造有限责任公司提出并负责起草。
本文件为强制性文件。
本文件的起草人:杨强秦光华王东胡值敏刘君本标准备案号:修订时间:2009.7.16 修订处数:2处(3.5、5.2.5)汽车发动机铝合金气缸盖铸件技术条件1 范围本标准规定了汽车发动机铝合金气缸盖铸件的要求、试验方法、检验规则及判定原则、标志、包装、运输及储存。
本标准适用于汽车发动机铝合金气缸盖铸件(以下简称铸件)。
2 规范性引用文件下列文件中的条款通过本标准的引用而成为本标准的条款。
凡是注日期的引用文件,其随后所有的修改单(不包括勘误的内容)或修订版均不适用于本标准,然而,鼓励根据本标准达成协议的各方研究是否可使用这些文件的最新版本。
凡是不注日期的引用文件,其最新版本适用于本标准。
GB191 包装储运图示标志GB/T228 金属材料室温拉伸试验方法GB/T231 金属布氏硬度试验方法QC/T269 汽车铸造零件未注尺寸的极限偏差GB/T1173 铸造铝合金JB4239 汽车发动机气缸盖技术条件GB/T9438 铝合金铸件技术条件ISO10049 铝合金铸件针孔度目测评定方法3 要求3.1 铸件应按经规定程序批准的图样和技术文件制造。
3.2 铸件材质及理化力学性能。
3.2.1铸件采用GB/T1173规定之Al—Si系合金铸造。
也允许采用国内外已经在推广和使用的其它铸造铝合金铸造。
3.2.2铸件本体力学物理性能指标为抗拉强度≥165MPa,延伸率≥0.8%,硬度78~125HBS。
对为达到力学性能而采用的热处理规范不作规定。
3.3 铸件外观质量3.3.1铸件上的商标、企业标识、零件号、生产批号等可追溯标志须明显、易辨。
3.3.2铸件加工基准须光滑平整,各基准点高差≤0.1mm。
铝合金汽车发动机缸体的压铸生产

铝合金汽车发动机缸体的压铸生产本文著作:布勒中国邹智厚卢宏远徐仲杰长安汽车研究院乐虎万伯谦布勒瑞士压铸有限公司FfitSche Bemhard摘要:本文阐述了高压铸造生产缸体的特点,并简单介绍了压铸岛的一些必须设各及v型缸体的生产要点。
1.缸体压铸特点众所周知,压铸产品中有很多产品用于汽车的零部件。
随着对环保,轻量化的要求日益提高,汽车中的许多关键部件,如发动机缸体等,逐渐转向压铸生产。
多年来,欧美和日本的大多数汽车公司已经采用压铸方法生产铝合金发动机缸体。
在国内,用压铸方法生产铝合金发动机缸体目前也成为一种趋势。
相比传统的铸造,压铸缸体有以下优点:(1)效率高。
在所有的铸造方法中,压铸是一种生产率最高的方法。
这主要是由压铸过程的特点决定的,且随着生产工艺过程机械化、自动化程度进一步发展而提高。
生产一个缸体的时间一般为3分钟左右,相对传统的低压或者砂型铸造省时省力:(2)精度高a只需个别部位加工即可使用:(3)铸件的强度和表面硬度较高;(4)节能省耗。
一般每台设备每年可生产7万件左右:(5)占地面积少。
(6)工艺路线短。
传统的铸造工艺,缸体生产需要经过造型、制芯、浇注、冷却、落砂、清理、机加,热处理等诸多工序。
而压铸则只需提前加工模具,浇注后很快将缸体毛坯铸件从压铸岛中取出,或者由人工去除飞边毛刺,之后进行检验、加工等便可。
压铸也有一定的缺点:(1)铸造缺陷较多。
由于液体合金充型速度极快,型腔中的气体很难完全排除,常以气孔形式存留在铸件中。
另外,压铸填充过程中的氧化夹杂等,如果集渣包等设计不合理,容易残留在产品内部:(2)压铸初次投资较高。
有统计,如果生产的缸体数量低于10万个的话,低压铸造或砂型铸造的成本低于压铸。
2.缸体图片及压铸岛布局排量在2.0以下的汽车缸体一般为直列3缸或四缸,而大于2.0排量的缸体则可能为直列六缸或V型六缸。
目前来讲,一般的压铸岛(压铸机和各周边设备一起统称为压铸岛)布局比较复杂,而且没有标准的布局格式。
铝合金发动机缸体的压铸生产

铝合金发动机缸体的压铸生产采用缸体压铸方式生产发动机缸体,可缩短工艺路线,提高生产率,具有明显的技术优势和经济优势,尽管这一生产方式存在个别的缺点,但随着压铸工艺水平的不断提高,人们将不断克服,缸体的压铸生产已逐渐成为新的发展趋势。
缸体压铸特点随着人们对环保、轻量化的要求日益提高,汽车中的许多关键部件,如发动机缸体等,逐渐转向采用压铸生产。
相比传统的铸造,压铸缸体有以下优点:1.效率高。
在所有的铸造方法中,压铸是一种生产率最高的方法,这主要是由压铸过程的特点决定,且随着生产工艺过程中机械化、自动化程度的进一步发展而提高。
生产一个缸体的时间一般为3min左右,相对传统的低压或者砂型铸造省时省力。
2.精度高。
只需个别部位加工即可使用。
3.铸件的强度和表面硬度较高。
4.节能省耗。
一般每台设备每年可生产7万件左右。
5.占地面积少。
6.工艺路线短。
传统的铸造工艺,缸体生产需要经过造型、制芯、浇注、冷却、落砂、清理、机加以及热处理等诸多工序。
而压铸则只需提前加工模具,浇注后很快将缸体毛坯铸件从压铸岛(压铸机和各周边设备一起统称为压铸岛)中取出,或者由人工去除飞边毛刺,之后进行检验、加工等即可。
压铸也存在一定的缺点:1.铸造缺陷较多。
由于液体合金充型速度极快,型腔中的气体很难完全排除,常以气孔形式存留在铸件中。
另外,压铸填充过程中的氧化夹杂等,如果集渣包等设计不合理,容易残留在产品内部。
2.压铸初次投资较高。
据统计,如果生产的缸体数量低于10万个,低压铸造或砂型铸造的成本低于压铸。
缸体样式及压铸岛布局排量在2.0L以下的汽车缸体一般为直列三缸或四缸,而大于2.0L排量的缸体则可能为直列六缸或V型六缸。
图1所示分别为汽车的直列三缸、直列四缸、直列六缸和V型六缸缸体的外形。
图1 常用汽车缸体目前来讲,一般的压铸岛布局比较复杂,而且没有标准的布局格式。
每个压铸厂家都会根据自己生产的经验和特点提出一些与众不同的布置,从而方便生产。
国内外汽车发动机铝缸体铸造技术

兰冬云,等:国内外汽车发动机铝缸体铸造技术
铸造设备研究
序号
公司名称
1 广州东风本田发动机公司
2 哈尔滨东安动力股份公司 3 重庆长安汽车集团 4 重庆长安铃木发动机厂 5 中国泰克西铝业公司 6 福建漳州灿坤实业有限公司 7 渝美铸有限公司
8 广州南沙丰田发动机公司
9 重庆市蓝黛实业有限公司
10 秦皇岛市经济开发区
4
德国宏赛 HONSEL
5
法国雷诺汽车公司 Renault
合型力 37 000 kN 压铸机 1 台 合型力 35 000 kN 压铸机 1 台 合型力 21 500 kN 压铸机 2 台 合型力 30 000 kN 压铸机 8 台
V型 8 缸~12 缸体 V 型 6 缸体
L4 直列 4 缸体 L4 直列 4 缸体
EV220D 压铸机 合型力 22 000 kN
1.3L 四缸发动机,缸体尺寸 240 ×2 209(mm),质量 12.4 kg
365 ×柳州五菱汽车
合型力 25 000 kN 压铸机(意特) 4缸体
3)浇注质量 31 kg;4)缸体外形尺寸:480×380×270 10)生产节拍 110 s。
(mm);5)壁厚 3.5 mm~35 mm;6)铸孔数量 68 个;
2)生产率高,每台压铸机(合型力 25 000 kN) 全年可生产四缸体 10 万件(三班生产)。
3)缸体的尺寸精度高,表面光洁度好,机械加 工的余量小,符合净成型和循环经济的原则。
4)废品率相对较低(内外废品率约 5 %),符合 节材和节能原则。
5)缸体一般不能热处理。 6)压铸模具成本较高,例如宇部合型力 25 000 kN 压铸机缸体模具价格约 6 521 万日元,折合人民币 约 435 万元。 7)国外压铸单元均配备吸烟除尘净化装置处 理由喷涂脱模剂形成的油烟雾和蒸汽,使其达标排
- 1、下载文档前请自行甄别文档内容的完整性,平台不提供额外的编辑、内容补充、找答案等附加服务。
- 2、"仅部分预览"的文档,不可在线预览部分如存在完整性等问题,可反馈申请退款(可完整预览的文档不适用该条件!)。
- 3、如文档侵犯您的权益,请联系客服反馈,我们会尽快为您处理(人工客服工作时间:9:00-18:30)。
80年代中期美国Fotd汽车公司从英国引进这一技术.并且对其加一改造,使之适用于大量生 产。为此Fotd公司于1988年投资580万美元兴建一中试车间即“铸铝研究开发”车间(Casting Aluminum Research and Development,简称CARD),其中安装有与生产用设备一样大的倾转 式Cosworth铸造机及容量为22.7t的熔化炉,“真刀真枪”地试浇注V-6及v.8轿车发动机缸 体和缸盖。在工艺成熟的基础上,Ford汽车公司投资近六千万美元在1992年秋建成安装有38 台冷芯射芯机、103台机器人以及3台倾转式Cosworth转盘铸造机的全自动铸铝厂(Windsor Aluminum Plant,温莎铸铝厂现归属Nemak公司)。该厂目前己具备年产约89万件缸体的生 产能力。其铸件废品率(内、外废)仅O.6%,这样低的废品率对于大量生产复杂薄壁铝合金 铸件来讲,在世界上是罕见的。
Sand mo眦d
Vn
180" rOlalion
casting
a
6、精确砂型铸造
b
图9
由于在常温下在芯盒内通气快速硬化砂芯的“冷芯盒”制芯技术的应用,使制芯生产率 和砂芯尺寸的可预见性得以提高,精确砂芯组芯造型(即精确砂型)正在一定程度上取代目 前常用于生产铸铁及铸铝汽车件的粘土砂型及金属型。以下简述几种具有代表性的使用精确 砂型的铸造方法。
德国BMW汽车公司在几年前已建立成年产330,000铝缸盖的实型铸造厂。
8、湿型铸造
美国GM汽车公司萨基诺金属铸造厂(SMCO)数年前将其原生用于生产铸铝件的高压造 型线改建用于生产铝缸盖,在2001年用粘土砂湿型生产了1,925,000铝缸盖。
丹麦DISA公司近年来一直致力于开发利用其垂直分型无箱射压造型机及低压浇注来生
下载时间:2010年12月6日
2.期刊论文 向中元.李建华.林汉首 轿车发动机缸体压铸生产及效率控制 -机械工程师2005,""(9)
通过轿车发动机铝合金缸体压铸生产实践,分析产品设计及生产工艺,探讨影响生产效率的主要因素.提出压缩生产节拍、实现动作同步化是提高生产 效率的核心方法的观点.
本文链接:/Conference_6405998.aspx 授权使用:东风汽车(dfqc),授权号:034eda39-c8b8-48fe-9044-9e440106cb92
工位l,囱开启的金属型中自动下芯l 工位2:下芯及浇泣过程中间的安全工位, 工位3;缸盏自动浇注, 工位4~9:浇注了的缸盏进行冷却。
图7
81
德国VW公司汉诺威铸铝厂采用9台6工位转盘金型机生产铝缸盖
5、Cosworth法
英国Campbell教授发明的Cosworth法(图8)采用冷芯盒砂芯组芯造型,但是它使用锆 砂(通常在铸造生产中使用石英砂)。它利用电磁泵来实现在可控压力下使铝合金液由下而上 地充填铸型。由于锆砂的热膨胀率很小而且恒定,囡而有利于获得尺寸精确度高的铸件。但 是,由于锆砂导热性极好,比石英砂高出两倍多。因而用它所造的砂型难以浇注出壁厚小于 4mm的铝铸件。另外,砂芯采用机械组装,组装后砂型如同一个整体,也有利于确保铸件尺 寸精度。
昊泣郊清华太学机械制造工程系,北京100084
O’)£,0 D孽:一
.r~…~。
OPt:\0强“
图1
图2
2,中压铸造
日本Honda本田汽车公司及Toukei公司分别研发了新压铸法(图3)及中压压铸法(图4j
用于生产铝缸体。两者皆可采用砂芯从而可生产具有闭舵结构的缸体。
压力铸造的压射比压是55~120Mpa,而中压铸造仅为5~30Mpa。
RS
产铝铸件,特别是铝缸体。这种1二艺采用低压体铝液从砂型侧面由下而上地充填型腔。(图 13)。在充填完毕后,将砂型底侧的浇口切断,并将一通气小管从上向下插入砂型的冒口内, 引入气压体冒口进行补缩。如果这种工艺能成功地用于大量生产铝缸体,则由于上述造型机 的高生产率(200~300型,,J、时),它将带来很大的经济效益。
轿车发动机铝合金缸体和缸盖的铸造技术
清华大学吴浚郊1 摘要:从世界范围看.轿车工业是铸造工业的最大用户,同时也是铸造技术进步的~个主要推动力。为了
降低燃料消耗、减少环境污染,轿车铸件朝着轻量化、精确化、强切化和复合化方向发展。国外正在研究3mm 壁厚的灰铸铁缸体.3ram壁厚的耐热合金钢排气管和2 0~2.5 111111壁厚的球墨铸铁件。而扩大铝台金的应用 是轿车工业的重要发展趋势,国外汽车材料铝合金用量以每年l∞‘的速度递增。目前几乎全部轿车缸盖已采 用高强度铝合金生产,预计有更多的缸体也将采用铝台金生产。生产优质的精确成形铸件(Net shape costings) 是各国汽车铸件生产厂的共同目标。为此,除原有的精确铸造成形技术不断有所改进外,也开发了多种新的 铸造技术。本文介绍世界若干主要的轿车制造厂所采用的生产铝合金发动机缸体和缸盖的铸造技术。
日本Toyota丰田公司采用类似于低压铸造的真空吸铸法(图6)生产铝缸体。
i.........。......。,.。.......................一
M£,AL RE TtffqN.
图5
o…。,.........。j
i
、’_:
图6
4、金属型铸造
金属型铸造主要用于生产铝缸盖及简单的铝缸体。 德国Daimler—Chrysler公司有两台直径分别为12米及13米的12工位转盘金型机(图7) 缸盖,生产铝缸盖。 毛坯重12公斤,浇冒口重6公斤。浇注温度为730"C,浇注时间为9秒,生产节拍为30 秒。浇注后缸盖进行热处理。
图13
小结:
世界著名汽车厂铝合金缸体、缸盖所用的铸造工艺可归纳如下:
\方r。\名
GM
Ford
13’aimler Chrysler
BMW
\
VW
。Foyota Nissan Honda Renault
Fial
高压压铸
B
B
B
中压压铸
B
低压K铸
H
H
H
H
金属型铸造
H
H
H
BH
H
湿型铸造
H
Cosworth法 B
铸造
图ll
图12
7、实型铸造
实型铸造或(消失模铸造)采用遇液体金属后即气化的泡沫塑料作模样,无分型面,也 不用取模,不用砂芯,同时采用无水份、无粘结剂、无附加物的干砂造型。这种方法可以生 产出薄壁、零度拔模斜率的复杂铸件,并可直接铸出螺纹及曲折的通道。它可以减少机械加 工工序。
美国GM公司发动机总成部(GMPT)在将实型铸造用于大量生产方面在世界上处于领先 地位。
. 是铝液在很低的压力("-0.03Mpa)下由下而上地充填型腔(图5)通常采用的 是金属型和砂芯,因此可以获得闭舵结构的缸体。
这种方法的缺点是生产率低,因为虽然充型时间一般仅需5一.15秒,但保压时间则需3~ 6分钟,整个生产循环达10b l 1分钟。在大量生产轿车缸体、缸盖时,就需要多台机器和多 套模具。美国福特公司用此法生产铝缸盖。
关键词:轿车发动机、铝合金、缸体和缸盖、铸造技术
l、压力铸造(圈1)
压力铸造的优点是能生产尺寸精度高、表面光洁度好、壁厚薄的铸件。但是,因充填型 腔的铝液流速高而引起的紊流将空气和氧化膜卷进铸件结构中,使铸件的内部致密性差。这 个问题现在从以下途径来解决:
(1)在压室和压型中采用真空; (2)采用更科学、更合理的浇注系统; (3)采用半固态金属来代替液态金属。 它们都在不同程度上取得了成效。 对于缸体生产来讲,压力铸造的另一局限是由于压射比压高(55~120Mpa)须采用金属 型芯,只能铸出开舱结构的缸体(图2)。与开舵结构相比,闭舱结构的缸体具有更大的刚性, 后者即使在发动机功率增大时能降低噪声和振动水平。 德国Daimler.chrysler公司、及法国Renault公司等采用压力铸造生产铝缸体。
作者: 作者单位:
吴浚郊 清华大学机械制造工程系,北京,100084
相似文献(2条)
1.期刊论文 吴浚郊 轿车发动机铝合金缸体和缸盖的铸造技术 -铸造技术2002,23(5)
为了降低燃料消耗,轿车铸件朝着轻量化、精确化、强韧化和复合化方向发展.而扩大铝合金的应用是轿车工业的重要发展趋势,目前几乎全部轿车缸 盖已采用高强度铝合金生产,预计有更多的缸体也将采用铝合金生产.世界若干主要的轿车制造厂各自所采用铸造技术,如压力铸造、中压铸造、低压铸造 、金属型铸造、Cosworth法、精确砂型铸造、实型铸造和湿型铸造,生产轿车用的铝合金缸体和缸盖.
(”英国Zeus法采用冷芯盒砂芯组芯造型,重力浇注。由于所用的工艺装备(芯盒)制 造得十分精确,因而可获得尺寸十分精确的铝铸件,这种方法可以生产壁厚仅2.5mm的复杂 铝合金发动机缸体、缸盖。
(2)德国glucast铸造厂采用一种独特的方法来进行冷芯盒砂芯的组装。首先使制好的 一底盘砂芯滞留在第一套芯盒的下芯盒内。该底盘砂芯的下芯盒就作为一输送“夹具”逐次 通过生产线上的每一台射芯机,并利用芯盒上精确的定位销、套系统进行自动砂芯装配(图 10)。每一台射芯机生产相应的一层砂芯,除第一台射芯机外,其余的射芯机皆将制造的砂芯 滞留在上芯盒中,以便进行由上而下的组装。
经过改进的Cosworth倾转法(图9b)是从铸型的侧面注入锅液直至型腔被充满为止。随 后将整个铸型倾转t此时电磁泵仍在工作,当铸型被倾转1800后电磁泵开始降低压力以便处 于横浇道中的铝液返回到电磁泵的浇注管中,而铸件则在具有热的铝液的冒口作用下进行凝 固。这样一台电磁泵配合一台倾转铸型机每小时可浇注55型。而Ford汽车公司采用四工位转 盘式浇注机(配一台电磁泵),每小时生产率达100型。
早在80年代它即在纽约州的马森纳工厂用实型铸造生产一种4.3升V6汽车柴油机的铝缸 盖。随后在1986年将其用于生产2.2升四缸铝缸盖,迄今已生产了500万件。1986年通用公 司宣布在其所属的土星汽车厂用实型铸造生产铝缸体和缸盖以及球铁曲轴和凸轮轴。