OEE基础(汇总)
OEE培训资料
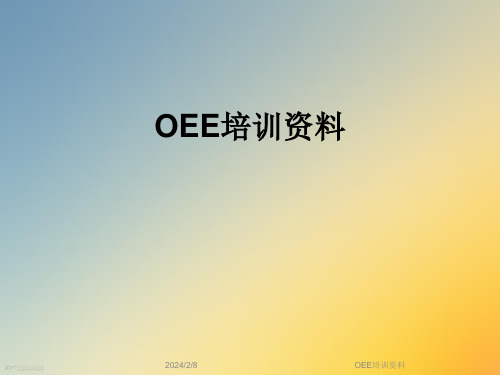
6. 启动稳定的损失 设备从启动到正常工作所需要的时间。
其原因有:
–设备要平缓加速到标准速度 –料筒需升温到设定温度 –去除多余的材料 –处理相关原料O的EE短培缺训资料
重庆光能荣能汽车配件有限公司
3. 设备综合效率的计算
稼动=开动=运转
工作时间 Total operating time A 负荷时间 Loading time
OEE培训资料
重庆光能荣能汽车配件有限公司
设
备
6大损失
设备综合效率的计算公式
工作时间
计
负荷时间
划 损
失
停
稼动时间
止 损
失
性
实 际能
稼动时间 损
失
不
价值稼 良
动时间 损
失
PPT文档演模板
0-1 计 划 停 机 0-2 教育、 早会
① 停工、故障 ② 换装、调整 ③ 空转、瞬停 ④ 速 度 降低 ⑤ 废品、返工 ⑥ 启 动 稳定
2. 设备效率损失的分类
大分类 计划损失 停止损失 性能损失 不良损失
中分类 交班时间/就餐/休息/生产中断/预防维修 设备故障/动力事故/换产/流量不足 流量调节/资材短缺/品质问题
瞬间停止/速度降低/空转
不良/再作业
公司认可的损失
影响OEE 的损失
PPT文档演模板
OEE培训资料
重庆光能荣能汽车配件有限公司
OEE就是用来表现实际的生产能力相对于理论产能的比率,它 是一个独立的测量工具 。
OEE也是一种简单实用的生产管理工具,设备效率指数已成为 衡量企业生产效率的重要标准,也是TPM实施的重要手法之一。
设备综合效率(OEE)是衡量一台设备按计划速度生产出合格产品 的时间占全部时间的百分比.
OEE定义和计算方式汇总
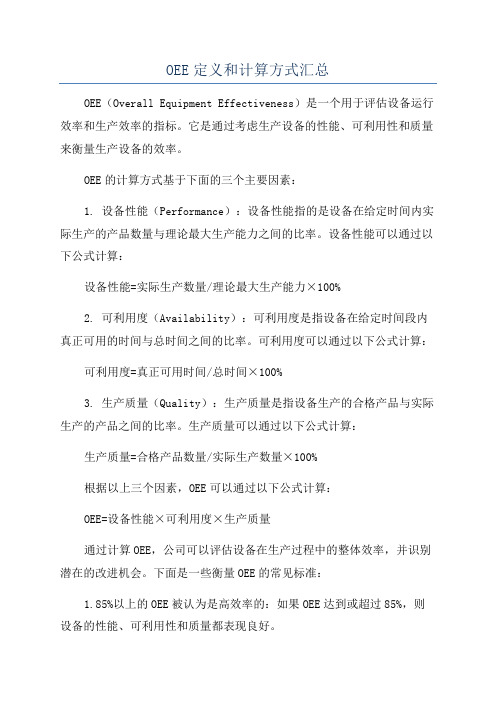
OEE定义和计算方式汇总OEE(Overall Equipment Effectiveness)是一个用于评估设备运行效率和生产效率的指标。
它是通过考虑生产设备的性能、可利用性和质量来衡量生产设备的效率。
OEE的计算方式基于下面的三个主要因素:1. 设备性能(Performance):设备性能指的是设备在给定时间内实际生产的产品数量与理论最大生产能力之间的比率。
设备性能可以通过以下公式计算:设备性能=实际生产数量/理论最大生产能力×100%2. 可利用度(Availability):可利用度是指设备在给定时间段内真正可用的时间与总时间之间的比率。
可利用度可以通过以下公式计算:可利用度=真正可用时间/总时间×100%3. 生产质量(Quality):生产质量是指设备生产的合格产品与实际生产的产品之间的比率。
生产质量可以通过以下公式计算:生产质量=合格产品数量/实际生产数量×100%根据以上三个因素,OEE可以通过以下公式计算:OEE=设备性能×可利用度×生产质量通过计算OEE,公司可以评估设备在生产过程中的整体效率,并识别潜在的改进机会。
下面是一些衡量OEE的常见标准:1.85%以上的OEE被认为是高效率的:如果OEE达到或超过85%,则设备的性能、可利用性和质量都表现良好。
2.60-85%之间的OEE可接受:如果OEE在60-85%之间,则设备可能存在一些效率和可利用性的问题,需要进行进一步的改进。
3.60%以下的OEE被认为是低效率的:如果OEE低于60%,则设备的性能、可利用度和质量都需要进行改进。
可能需要进行设备维修、培训操作员或优化生产过程。
通过计算OEE,并对其进行跟踪和改进,企业可以提高设备的效率和生产能力,从而更好地满足市场需求并提高竞争力。
OEE详解
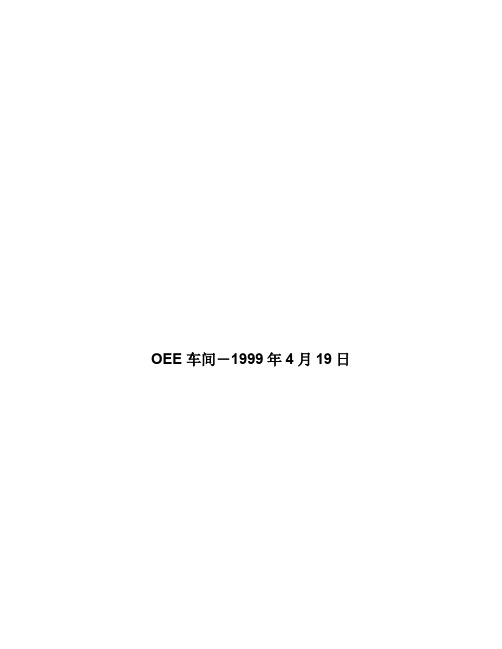
=C - D =A x E
=F x G
过程 1 3 8
480 30
450 1350 5.333 7199.55
试生产运行数据: I. 运行分钟合计 J. 无计划停机时间 合计+少量设定和调整时间 (分钟) K. 部件生产数量总计(好的+坏的) L. 良好部件生产合计 (第一次生产 – 不包括重新生产的和返修的部件〕
通常发生在: 工作车间,批量工作车间,密集性车间 举例: 某些压力机,铸模机,车床和镗床。
部件 A
部件 B
部件 C
部件 D
机器 1 机器 2 机器 3 机器 3
部件 A
部件 B
部件 C
部件 D
7
每种不同背景如何计算机控制
类型 1 举例: 一种部件,一种机器(针对一种类型的部件,用一种机器来完成一 种运作时)。
其它给你的有关信息:
班/天: 3 小时/班: 8 午饭/休息:30 分钟午饭时间/班,2 次 10 分钟休息/班 (在休息期间标签移走)。 计划的运行模式:3 班 天,周一到周五,周六,一班。 此件同时提供给其它汽车公司。需求如下:
用户 福特 克里斯乐 Chrysler GM 本田 Honda 合计
TPM-原有的 OEE 总的原有生产率及维护(TPM)用 APICS 定义如下:预防性维护加连续的努力, 采用,修改和改进设备,以提高其灵活性,减少材料的处理,促进连续的流程。操 作手定向维护及所有有资历的维护人员的共同参于。 TPM 的目标是提高设备的效率,以使设备能发挥其所有潜力和妥善的维护。取得 这一目标能产生 2 个主要推动。 1. 定量,强调最终产品产量提高,并定期改善生产率。 2. 定量,强调废品的减少和质量的稳定。
问题:
背景
最新OEE培训讲义

I.OEE 的组成
OEE=Availability ×Performance efficiency ×Quality rate
设备综合效率=时间稼动率×性能稼动 率×合格品率
焦点:它衡量的目的在设备及制程的改 善,而不是对人的评价。
OEE培训讲义
2017-10-16
注意事项
欢迎大家参加本次课程,本课程将为您 打下一个基本的OEE知识基础,提高您的能 力和水平.请提前5分钟到场签到;
请注意以下的几点: 1、手机 上课期间请将您的手机开为振动
或关闭. 2、吸烟 在课堂内请不要吸烟. 3、其它
上课期间请不要大声喧哗, 举手提问, 不要随意走动.
结束语:
谢谢大家
重点:掌握造成OEE低下的各类型损失, 并加以改善。
II.OEE挂图
III.OEE的损失结构图
IV.OEE的计算---Availability时间稼动率
Availability的计算练习
Availability = B / A [练习] 某公司每班上班总时间为540分钟,其中用餐时间与
IV.OEE的计算---Performance性能稼动率
Performance的计算练习C
Performance = D / C [练习] 某公司每班上班总时间为540分钟,其中用餐时间与休
息为60分钟,上班前的交接班为10分钟,每班操作前 点检时间额定为10分钟。A=540-60-10-10=460 7月5日每班订单量为10k,每个的生产标准时间为2.76 秒,当日切换工程与调整总共花了30分钟,设备中途 故障与修复总时间为15分钟。另外这一班生产过程中 小停止10次,每次额定估算值为2分钟15=415, C=B*60/2.76=9021, D=9000, D/C=9000/9021=0.997 请计算这一班的Performance.
OEE介绍和计算方法

OEE(Overall Equipment Effectiveness),即设备综合效率,其本质就是设备负荷时间内实际产量与理论产量的比值。
企业在进行OEE计算时常常遇到很多迷惑的问题,如工厂停水、停电、停气、停汽使设备不能工作,等待定单、等待排产计划、等待检查、等待上一道工序造成的停机,不知如何计算。
本文引入非设备因素停机的概念,修改了OEE的算法,使计算得到的OEE更能够真实反映设备维护的实际状况,让设备完全利用的情况由完全有效生产率这个指标来反映。
本文同时介绍了在不同情况下如何分析设备损失的PM分析流程。
1、 OEE表述和计算实例OEE= 时间开动率×性能开动率×合格品率其中,时间开动率 = 开动时间/负荷时间而,负荷时间 = 日历工作时间-计划停机时间开动时间 = 负荷时间–故障停机时间–设备调整初始化时间性能开动率 = 净开动率×速度开动率而,净开动率 = 加工数量×实际加工周期/开动时间速度开动率 = 理论加工周期/实际加工周期合格品率 = 合格品数量/ 加工数量在OEE公式里,时间开动率反映了设备的时间利用情况;性能开动率反映了设备的性能发挥情况;而合格品率则反映了设备的有效工作情况。
反过来,时间开动率度量了设备的故障、调整等项停机损失,性能开动率度量了设备短暂停机、空转、速度降低等项性能损失;合格品率度量了设备加工废品损失。
OEE还有另一种表述方法,更适用于流动生产线的评估, 即OEE= 时间开动率×性能开动率×合格品率而,时间开动率 = 开动时间/计划利用时间而,计划利用时间 = 日历工作时间-计划停机时间开动时间 = 计划利用时间–非计划停机时间性能开动率 = 完成的节拍数/计划节拍数其中,计划节拍数 = 开动时间/标准节拍时间合格品率 = 合格品数量/加工数量这与前述的OEE公式实际上是同一的。
计算:停机时间 = 115+12 = 127 min计划开动时间 = 910 – 127 = 783 min时间开动率 = 783/910 = 86%计划节拍数 = 开动时间/标准节拍时间 = 783/3 = 261性能开动率 = 203/261 = 77.7%合格品率 = 一次合格品数/完成产品数 = 152/203 = 74.9%于是得到 OEE = 86% ×77.7%×74.9% = 50%2、 OEE的实质如果追究OEE的本质内涵,其实就是计算周期内用于加工的理论时间和负荷时间的百分比。
oee培训ppt课件
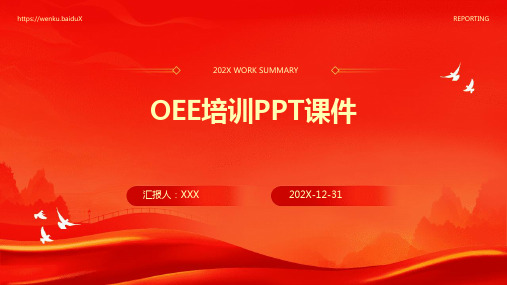
OEE培训PPT课件
汇报人:XXX
202X-12-31
REPORTING
目录
• OEE基本概念 • OEE的重要性和影响 • 如何提高OEE • OEE的监控与改进 • OEE的未来人和时间节点,确保措施的 有效执行。
对改进措施进行风险评估和经 济效益分析,确保措施的公道 性和可行性。
跟踪改进效果
实施改进措施后,持 续监测OEE数据的变 化情况,评估改进效 果。
根据跟踪结果,及时 调整和优化改进措施 ,持续提高OEE水平 。
对改进效果进行统计 分析和可视化展示, 便于团队成员了解改 进成果。
下落生产成本
提高装备效率可以下落生产成本,因为装备效率的提高意味 着生产进程中所需的人力和物力资源更少,能源消耗更低, 从而下落了生产成本。
OEE培训可以帮助员工更好地掌握成本控制的方法和技能, 通过优化生产流程、减少浪费等措施,进一步下落生产成本 。
提升产品质量
01
装备效率的提高可以提升产品质 量,因为装备的稳定高效运行可 以减少产品缺陷和不良品率。
PART 04
OEE的监控与改进
OEE数据收集与整理
确定数据收集的指标
根据装备特点和生产要求,确定需要收集的OEE指标,如开机率 、故障率、准备时间等。
制定数据收集计划
确定数据收集的时间间隔、采集人员和采集方式,确保数据的准确 性和实时性。
数据整理与存储
对收集到的数据进行整理、分类和存储,便于后续的分析和查询。
备用装备
配备备用装备,在主装备故障时,能 够迅速切换到备用装备,保证生产连 续性。
提高操作员技能
培训教育
定期对操作员进行技能培训和安 全教育,提高操作员的专业素养
产线效率计算及提升基础知识
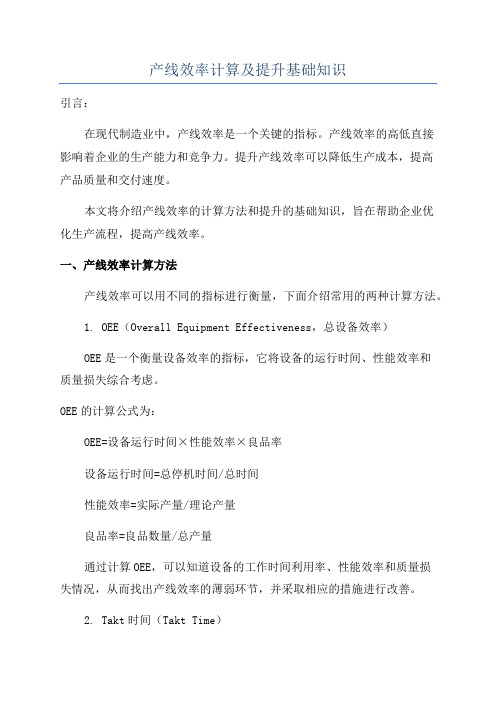
产线效率计算及提升基础知识引言:在现代制造业中,产线效率是一个关键的指标。
产线效率的高低直接影响着企业的生产能力和竞争力。
提升产线效率可以降低生产成本,提高产品质量和交付速度。
本文将介绍产线效率的计算方法和提升的基础知识,旨在帮助企业优化生产流程,提高产线效率。
一、产线效率计算方法产线效率可以用不同的指标进行衡量,下面介绍常用的两种计算方法。
1. OEE(Overall Equipment Effectiveness,总设备效率)OEE是一个衡量设备效率的指标,它将设备的运行时间、性能效率和质量损失综合考虑。
OEE的计算公式为:OEE=设备运行时间×性能效率×良品率设备运行时间=总停机时间/总时间性能效率=实际产量/理论产量良品率=良品数量/总产量通过计算OEE,可以知道设备的工作时间利用率、性能效率和质量损失情况,从而找出产线效率的薄弱环节,并采取相应的措施进行改善。
2. Takt时间(Takt Time)Takt时间是指单位时间内完成一个产品的节拍时间,即生产一个产品的平均时间。
Takt时间的计算公式为:Takt时间 = 计划生产时间 / 需求量通过计算Takt时间,可以根据市场需求和生产能力确定产品的生产周期,并对生产线进行合理的规划和调度。
二、产线效率提升的基础知识1.合理的生产布局合理的生产布局可以减少物料和产品的运输时间,节约生产成本,提高生产效率。
生产布局应该考虑到生产流程的顺序和物料的流动路径,以实现最小化的物料和人员移动。
2.汇总和分析数据汇总和分析数据可以帮助企业了解生产过程中的问题和瓶颈,并采取相应的措施进行改善。
通过数据分析,可以找出影响产线效率的关键环节,并针对性地进行改进。
3.标准化操作通过建立标准操作程序和培训员工,可以确保生产中的每一步都按照最佳实践进行。
标准化操作可以减少错误和浪费,提高生产效率和产品质量。
4.持续改进持续改进是提高产线效率的关键。
OEE简介

工厂整体效率
评估整体绩效
OEE可以用来评估整个工厂或生产车间的绩效,通过计算工厂或 车间的可用性、性能和质量,反映工厂或车间的整体效率。
对比不同工厂或车间
通过比较不同工厂或车间的OEE,可以评估不同工厂或车间的效率 水平,找出需要改进的环节。
改进生产管理
通过对工厂或车间的OEE进行监测和分析,可以发现生产管理中的 问题和浪费,进而进行改进。
OEE简介
汇报人: 日期:
目录
• OEE定义及意义 • OEE的应用场景 • OEE的改善方法 • OEE的实践案例 • OEE的未来趋势
CHAPTER 01
OEE定义及意义
OEE的定义
设备综合效率(Overall Equipment Effectiveness,简称OEE)是一种衡量设备 性能、产量和质量的指标,它通过将设备的实际产量与理论产量进行比较,以评 估设备的整体效率。
某食品制造企业OEE提升案例
总结词
某食品制造企业通过引入自动化生产线、加强品质管理 和实施5S管理等方法提高OEE。
详细描述
该企业在生产线上引入了自动化设备,提高了生产效率 和产品质量。同时,该企业加强了品质管理,通过严格 的质量控制标准和流程,减少了产品不合格率。此外, 该企业还实施了5S管理,即整理、整顿、清洁、清洁检 查和素养,提高了生产现场的秩序和卫生状况。这些措 施使得该企业的OEE得到了显著提升。
CHAPTER 05
OEE的未来趋势
智能化OEE监控与管理
实时监控
01
通过物联网技术和传感器,实现对设备运行状态的实时监控,
及时发现异常情况并进行预警。
数据分析
02
利用大数据和人工智能技术,对设备运行数据进行分析,提供
OEE(总和效率)
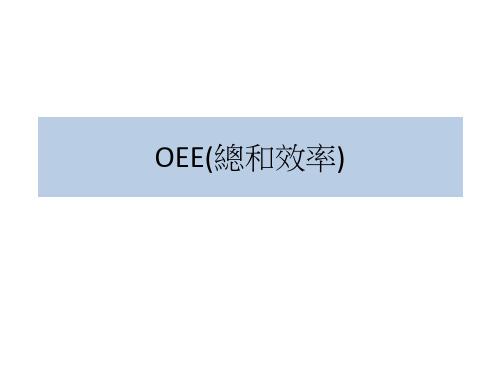
性能稼动率 理论CT╳产量 稼动时间
速 度 损 失
(4) 速度 CT实现周转数
⑦ 修 理· 加 工 再 ⑧废 弃 生产综合效率 = 时间运转率×性能运转率×良品率
中国最大的资料库下载 2
生 产 综 合 效 率 的 计 算
计算题:
三班倒的企业,每班一天工作8小时,其中 生产计划休息时间20分,设备故障停止20分, 准备作业花去20分,调整10分,一个班可以生 产400个产品,标准为半分钟生产一个,实 际每个产品平均需要0 .8分钟,不良率为2%。
故障 停机 30'
稼动时间410' 速度 损失 60'
350' 500个/日 不良 343' 损失 490个 10个 /2%
生产节拍为0.7分钟。 试计算该企业的OEE和 稼动率。
14
2-1、OEE的计算公式
OEE ( Overall Equipment Effectiveness ) = 设备稼动率× 生产率× 合格品率
工损失是不可避免的,因此很少加以消除。
12
7. 8.
点点停损失:因多处设备出现短促多发的10分钟以下的故障而 导致的生产线时转时停的停机损失。 速度低下损失:因各种原因而导致设备实际运转速度低于设计 速度而造成的损失。速度损失对设备效率的发挥产生了较大障 碍,应当仔细研究,以消除设计速度和实际速度二者之间的差 别。设备实际速度低于设计速度或理想速度的原因是多种多样 的,如机械问题和质量缺陷,历史问题或者设备超负荷等。通 常,通过查找设备的潜在缺陷,有助于问题的解决。
價值工時
負載時間 稼動時間 標準稼動時間 價值 稼動時間
不良的損耗
10 管理損耗 11 動作損耗 12 編制的損耗 13 置換成自動化的損耗 (節省 人工化) 14 量測調整重工損耗
OEE基础入门

OEE的定义OEE是Overall Equipment Effectiveness(全局设备效率)的缩写。
一般,每一个生产设备都有自己的理论产能,要实现这一理论产能必须保证没有任何干扰和质量损耗。
OEE就是用来表现实际的生产能力相对于理论产能的比率,它是一个独立的测量工具。
OEE是由可用率,表现性以及质量指数三个关键要素组成:OEE=可用率*表现指数*质量指数其中:可用率=操作时间/计划工作时间它是用来评价停工所带来的损失,包括引起计划生产发生停工的任何事件,例如设备故障,原材料短缺以及生产方法的改变等。
表现指数=理想周期时间/(操作时间/总产量)=(总产量/操作时间)/生产速率表现性是用来评价生产速度上的损失。
包括任何导致生产不能以最大速度运行的因素,例如设备的磨损,材料的不合格以及操作人员的失误等。
质量指数=良品/总产量质量指数是用来评价质量的损失,它用来反映没有满足质量要求的产品(包括返工的产品)OEE基础入门——OEE系列知识培训之一随着市场竞争的日趋激烈,生产企业要想持续获得理想的效益,其中一个重要环节就是要持续提升其生产效率——在具有“制造大国”之称的中国的今天,效率已成为众多企业是否可以赢利的关键甚至是决定性因素。
然而,中国目前大部分生产企业,特别是民营生产企业,其表面上看似良好运作的生产车间实际上并没有以最好的状态进行工作,设备和操作人员的价值存在很大的改善空间,这无形中为企业造成了巨大的损失。
但是,绝大多数企业的管理人员并没有意识到这一点,或者说只是有感观上的感觉,但缺乏定量的数据,而没有采取有效的措施予以解决。
为了解决这一问题,国际制造业提出了全局设备效率(OEE)的概念。
全局设备效率OEE是一种简单实用的生产管理工具,在欧美的制造业和中国的跨国企业中已得到广泛的应用,全局设备效率指数已成为衡量企业生产效率的重要标准,也是TPM(Total Productive Maintenance)实施的重要手法之一。
OEE的定义及计算方法
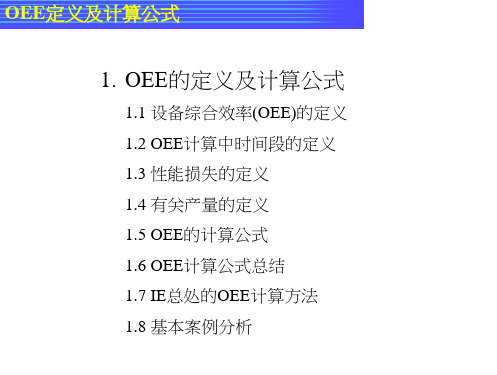
3. 负荷时间﹕设备应该正常运转的时间﹐为总投入时 间减去计划停机时间
(计算OEE1的分母)
OEE定义及计算公式
1.2. OEE计算中时间段的定义
4. 当机时间﹕指由于设备故障﹑模具故障﹑换模换线 ﹑暖机﹑换料等造成的生产停止时间。
• • 设备故障时间﹕因设备故障造成机器停机的总时间。 包含维修时间和调试时间﹐直至可正常生产 换线损失时间﹕机器因切换不同产品或为达成产品最 终特性而进行调整的总时间﹐包括从前一个产品停止 到新产品第一个良品产出所花费所有的时间 模具故障时间﹕因模具原因造成的停机的总时间 暖机时间﹕暖机时间是指﹐要开始生产时﹐启动﹑调 整运转﹑直至加工条件安定前所需要的时间
性能稼动率﹕
G.总产出量 H.理论周期时间 I. 实际周期时间 J. 纯稼动率=I*G/E K. 速度稼动率=H/I L.性能稼动率 (H * G / E)=J*K
良品率﹕
M.总的不良数 N.良品率 =(G – M) / G
_____ parts
_____ %
OEE1=F * L * N OEE=OEE1*C/A
1.5﹑ OEE计算公式
OEE(设备 综合效率) = 时间稼动率
x 性能稼动率 x
空 转 与 小 停 顿 速 度 降 低
良品率
OEE三大 要素对应 的损失
设 备 故 障
模 具 故 障
换 线 调 整
暖 机 损 失
不 良 件
OEE定义及计算公式
1.5﹑ OEE计算公式
时间稼动率是指在出勤时间中实际开机用于生产的 时间的比率﹐它显示了设备故障﹑模具故障﹑换模 换线﹑调整等对设备利用率的影响
_____ % %
OEE定义及计算公式
OEE分析和运作专业知识

8
1.公式關聯:
二 OEE 分解 之 公式 關聯
OEE=作業時間 淨利用時間
標工×生產數
×作業時間 ×
良品數 生產數
反应設備 作業時間 利用程度
反应設備 在作業時 間內生產 旳能力
反应設備 生產質量
能力
OEE=
標工*良品數 淨利用時間
=
76.19%*75%*83.75%=47.85%
23
④=③-⑤=960分 ⑤=5*60=300分
設備利用率=960÷ 1260=76.19%
6
1.含義:在實際作業時間內生產 實績達成標准之程度。
2.計算措施:
二 實際產能(pcs/台/h) ➢ 措施一:產能比值
OEE
標工*生產數
標准產能(pcs/台/h)
分解 之性 ➢ 措施二:工時比值
標准投入工時 作業時間
9
1.DC&NC OEE 數據統計表
返回
二 OEE
部OEE數據統計表
項目 機台編 產品編 良品數 返工數 報廢數
序號
號
號 (pcs) (pcs) (pcs)
標准 計劃停 工時 機時間 (pcs) (分)
作業 時間 (分)
停產 時間 (分)
日期:
設備利 用率
性能效 率
質量率
分解
之運
用表
單
合計
1.第二階段:9月以後
運作流程
責任單位
OEE目標& 對策實施
相關責任單位
使用表單
OEE數異分析
檢討
責任部 門對策
目標
對策
改善 再設定 方案
IE文員 IE
< OEE月匯總分析 表>
OEE介绍及计算方法

OEE定义及计算公式
五﹑速度损失定义
速度损失时间分为两部分﹕ 1﹑速度降低 2﹑空转和小停顿 分别定义如下﹕ • 速度降低
机器操作中与理论速度的差异造成的损 失时间。 • 空转和小停顿损失
制程中由于小的停顿(比如断料)导致的 生产损失。
稼动时间(=负荷时间-停机时间)
时间稼动率 =
出勤时间
性能稼动率 = 理论周期*加工数量
稼动时间
为了区分速度降低﹑小停顿对性能稼动率的影响﹐将性能稼动率 拆分为纯稼动率和速度稼动率﹐分别表达速度降低的影响和小停顿的 影响。
OEE定义及计算公式
纯稼动率是指设备在稼动时间内﹐以一定速度保持稳定﹑连续运 转的程度。以一定之速度运转这并不是与理论速度比快或慢﹐即 使本身速度比较慢﹐但要看是否能在长时间内保持安定的速度运 转。所以可以衡量因小停顿引起的损失﹐或在每日报表上看不出 来之微缺损失。
性能 稼动 率
纯稼动率 =(实际周期时间×加工数量)/稼动时间×100%
=×
速度稼动率 =理论周期/实际周期×100%
速度稼动率是指速度的差﹐对设备应具备的能力﹐与实 际速度比率。也就是判断是否以规定的速度进行运转。如 果设备的速度降低﹐会有多少损失。
良品数
良品率 = 总产出量
OEE定义及计算公式
= 时间稼动率 ×性能稼动率 ×良品率
OEE三大
设 备
模换暖 具线机
空速 转度
不 良
要素对应 故 故 调 损 与 降
件
的损失 障 障 整 失 小 低
停
顿
综合设备效率是从上述的时间性﹑性能﹑良率观察后得到的使 用有效率﹐来整体性进行设备评估的标准。
设备综合利用率OEE培训

根据以上的数据,理论上你可以在4天多的时间完成该旅程 -你觉得自己会四天内完成这趟公路之旅吗? -你需要考虑哪些因素才能得出更加准确的预测?
公路开车的例子
▪ 第一天结束时,你发现自己仅行驶了280公里
(相当于在最高速度下行驶了4小时)以这种 速度,13天才能到哈尔滨!
时间 (分钟)
答案举例
产品数量件产品加工 周期时间
▪ 时间转换成产品数量
产品数=时间 /单件产品加工 周期时间
任务:建立OEE图并设计改善建议
利用归类数据建立OEE图
= OEE ……%
可用性損失
作業效率損失
總時間 無生產 可用時間 ENG PR 週1-6無 計劃性 設備當機 換線
作业效率损失
总时间 无生产计 可用时间 工程试产 无订单需求 计划性保 设备停机 换线
划
养
小停机 速率损失 有效时间
OEE1 No Demand No Demand Cycle count
有线无人或是有线有人但法定 规定放假 • 国假、假日 • 没有订单,无法开班
试产
Weekday No Demand
计划盘点,保养,消防 演习等
OEE2 Break down
Pilot run (ENG)
Manpower
Cycle count
Breakdown
Rework
No Material
others
Calamity
others
Preventive Maintenance
Reflow adjusting
Weekday No Demand
17%
OEE基础

20
常见问题及注意事项
TDK Div Pts Operations - IE
常见问题
如何选择机器速度的标准? (铭牌产量/理想速度/数据统计) 如果缺原料所以做清洁设备, 我们该记录什么停机原因?(缺原料) OEE是否要统计预防维护和清洁?(是) 我的设备特殊,无法推行OEE或根本实现85%的目标
23
~End~
BU8 Module Group Confidential
24
故障
设备坏
Setup time
不同产品转换时的设备调整时间
BU8 Module Group Confidential
12
效能: 速度损失
运行速度减慢
设备实际运行速度经常低于其设计运行速度. 影响设备运行但不会导致长时期停机的异常
小停顿
BU8 Module Group Confidential
16
Example
设某设备某天工作时间为8h, 班前计划停机15min, 故障停机30min,设备调整 25min, 产品的理论加工周期为0.6 min/件, 一天共加工产品450件, 有20件废 品, 求这台设备的OEE。
根据上面可知: 计划运行时间=8x60-15=465 (min) 实际运行时间=465-30-25=410 (min) 可用性=410/465=0.881(88.1%) 生产总量=410(件) 理想速度x实际运行时间=410/0.6=683 性能=450/683=0.658(65.8%) 质量指数=(450—20)/450=0.955(95.5%) OEE=可用性x性能x质量指数=55.4% 5 Why分析 找到根本问题 和解决方案
OEE定义和计算方式汇总

OEE定义和计算方式汇总OEE是全称为Overall Equipment Effectiveness,中文名字叫做设备综合效能,是一种用于测量和评估设备性能的指标。
OEE的计算方式将设备的可用时间、性能效率和质量损失三个方面综合考虑,通过对设备的日常运行数据进行统计和分析,可以得出设备整体效率的量化指标。
OEE的计算方式如下:1. 设备的可用时间(Available Time):表示设备在规定时间段内应该可用的时间。
可用时间可以通过设备日历时间减去计划的停机时间和非计划的停机时间来计算。
可用时间=设备日历时间-计划停机时间-非计划停机时间2. 设备的性能效率(Performance Efficiency):表示设备在实际生产过程中的效率水平。
性能效率可以通过实际生产数量除以所需生产数量来计算。
性能效率=实际生产数量/所需生产数量3. 设备的质量损失(Quality Loss):表示设备生产过程中产生的质量损失。
质量损失可以通过实际良品数量除以实际生产数量来计算。
质量损失=实际良品数量/实际生产数量4.OEE的计算公式:OEE=可用时间×性能效率×质量损失OEE的计算结果可以是一个百分比值,表示设备整体的效率水平。
一般来说,高于85%的OEE被视为优秀,70%到85%的OEE被视为良好,低于70%的OEE被视为需要改进。
OEE的计算方式能够帮助企业发现设备运行中的问题和瓶颈,从而针对性地进行改进和优化。
通过准确地测量和评估设备的性能,企业能够找出并解决影响生产效率的因素,如设备故障、停机时间、性能不良等,从而提高设备的产能和生产效率。
除了OEE的计算方式,还有一些常见的OEE的改进方法包括:1.关键性能指标(KPIs)的设定和监控:设定关键性能指标,如设备的平均停机时间、停机次数、故障频率等,并定期监控这些指标的变化,从而及时发现并解决问题。
2.停机时间分析:对设备的停机时间进行分析,找出停机原因和停机时间的分布情况,从而确定采取适当的措施来减少停机时间。
OEE培训材料ppt课件
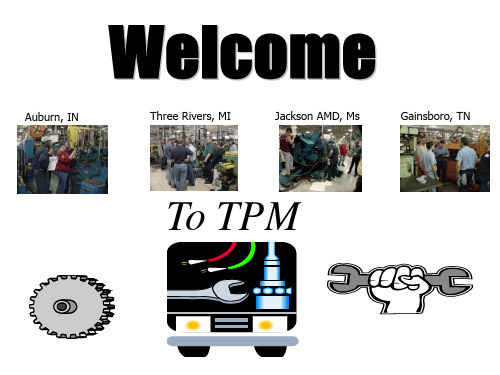
Three Rivers, MI
Jackson AMD, Ms
Gainsboro, TN
To TPM
六种损失对设备可生产时间的影响
8 小时
总机器可用时间
设备可用性角 度衡量
总可操作时间
6小时
停机损失
剩余操作时间
4.8小时
生产效率角度衡 量
速度损失
最终可操作时间 不良损失
3.2 小时
2. Observe proper "Lockout/Tagout" procedures when shutting down your equipment
for cleaning.
3. Systematically clean each part of the equipment using the checklist on the next
TPM Services
美国工厂 平均水平
30-45% OEE
55-70%
损失
隐藏的工厂
最大产
85% OEE 15%
损失
能
世界级
TPM Services
OEE
如何计算OEE
设备有效性 X 生产效率 X 质量结果
停机 换型 & 调整 其他
等待 & 微小停机 速度减缓
制程不良 开机或换型不良
提醒: OEE 衡量制造过程中的六种损失
page.
Note: An "abnormal condition" is defined as any condition within, or around the machine that affects the appearance and performance of the machine or production cell. a "normal condition" is defined as a condition in which the machine's appearance and performance is in "like new" condition and no waste is generated in time, resources, or materials. An abnormal condition can be a broken bolt, a leak, a worn or damaged part, it can also be a dirty part. As you document these conditions on your "Abnormality Summary Sheet" try and discover the reasons for them. Ask yourself the following questions:
- 1、下载文档前请自行甄别文档内容的完整性,平台不提供额外的编辑、内容补充、找答案等附加服务。
- 2、"仅部分预览"的文档,不可在线预览部分如存在完整性等问题,可反馈申请退款(可完整预览的文档不适用该条件!)。
- 3、如文档侵犯您的权益,请联系客服反馈,我们会尽快为您处理(人工客服工作时间:9:00-18:30)。
OEE基础入门2007-04-18 10:15随着市场竞争的日趋激烈,生产企业要想持续获得理想的效益,其中一个重要环节就是要持续提升其生产效率——在具有“制造大国”之称的中国的今天,效率已成为众多企业是否可以赢利的关键甚至是决定性因素。
然而,中国目前大部分生产企业,特别是民营生产企业,其表面上看似良好运作的生产车间实际上并没有以最好的状态进行工作,设备和操作人员的价值存在很大的改善空间,这无形中为企业造成了巨大的损失。
但是,绝大多数企业的管理人员并没有意识到这一点,或者说只是有感观上的感觉,但缺乏定量的数据,而没有采取有效的措施予以解决。
为了解决这一问题,国际制造业提出了全局设备效率(OEE)的概念。
全局设备效率OEE是一种简单实用的生产管理工具,在欧美的制造业和中国的跨国企业中已得到广泛的应用,全局设备效率指数已成为衡量企业生产效率的重要标准,也是TPM(Total Productive Maintenance)实施的重要手法之一。
OEE的定义OEE是Overall Equipment Effectiveness(全局设备效率)的缩写。
一般,每一个生产设备都有自己的理论产能,要实现这一理论产能必须保证没有任何干扰和质量损耗。
OEE就是用来表现实际的生产能力相对于理论产能的比率,它是一个独立的测量工具。
OEE是由可用率,表现性以及质量指数三个关键要素组成:OEE=可用率*表现指数*质量指数其中:可用率=操作时间/计划工作时间它是用来评价停工所带来的损失,包括引起计划生产发生停工的任何事件,例如设备故障,原材料短缺以及生产方法的改变等。
表现指数=理想周期时间/(操作时间/总产量)=(总产量/操作时间)/生产速率表现性是用来评价生产速度上的损失。
包括任何导致生产不能以最大速度运行的因素,例如设备的磨损,材料的不合格以及操作人员的失误等。
质量指数=良品/总产量质量指数是用来评价质量的损失,它用来反映没有满足质量要求的产品(包括返工的产品)。
OEE的作用利用OEE的一个最重要目的就是帮助管理者发现和减少一般制造业所存在的六大损失:停机损失、换装调试损失、暂停机损失、减速损失、启动过程次品损失和生产正常运行时产生的次品损失。
下面表格是六大损失的简单说明及其与OEE 的关系:OE E计算实例设某设备某天工作时间为8H,班前计划停机10MIN,故障停机30MIN,设备调整35MIN,产品的理论加工周期为1min/件,一天共加工产品400件,有20件废品,求这台设备的OEE。
根据上面可知:计划运行时间=8*60-10=470(min)实际运行时间=470-30-35=405(min)有效率=405/470=0.86(86%)表现性=400/405=0.98(98%)质量指数=(400-20)/400=0.95(95%)OEE=有效率*表现性*质量指数=80%在上表中,我们只列举了一些事件原因,在实际应用中它可能包括与生产有关的任何原因。
OEE能准确地告诉你设备效率如何,在生产的哪个环节有多少损失,以及你可以进行哪些改善工作。
长期的使用OEE工具,企业可以轻松的找到影响生产效率的瓶颈,并进行改进和跟踪,以达到提高生产效率的目的。
全局设备效率OEE打印| 推荐| 评分2006-4-4 16:49全局设备效率OEE发表时间:2005-7-17 徐亚锋全局设备效率OEE是一种简单实用的生产管理工具,在欧美的制造业里已得到广泛的应用,全局设备效率指数已成为衡量企业生产效率的重要标准,也是TPM(Total Productive Maintenance)的一个重要手法。
为了推动我国工业信息化的进程,在我国推广OEE的管理理念,从而使更多企业受益,特撰写此文。
本文主要阐述OEE的概念及其作用。
1、引入随着市场竞争的日益激烈,制造商要想持续获得高的经济效益,最大化地挖掘和改善生产车间的生产效率显得极其重要,在某些方面,它甚至成为企业是否可以赢利的决定性因素。
然而,在现在的制造业中,看似良好运作的生产车间实际上并没有以最好的状态进行工作,设备和操作人员的价值存在很大的改善空间,这无形中为企业带来了巨大的损失。
为了解决这一问题,国际制造业提出了全局设备效率(OEE)的概念。
2、OEE的定义一般,每一个生产设备都有自己的最大理论产能,要实现这一产能必须保证没有任何干扰和质量损耗。
当然,实际生产中是不可能达到这一要求,由于许许多多的因素,车间设备存在着大量的失效:例如除过设备的故障,调整以及设备的完全更换之外,当设备的表现非常低时,可能会影响生产率,产生次品,返工等。
OEE是一个独立的测量工具,它用来表现实际的生产能力相对于理论产能的比率。
国际上对OEE 的定义为:OEE是Overall Equipment Effectiveness(全局设备效率)的缩写,它由可用率,表现性以及质量指数三个关键要素组成,即:OEE=可用率X 表现性X质量指数。
其中:可用率=操作时间/ 计划工作时间它是用来考虑停工所带来的损失,包括引起计划生产发生停工的任何事件,例如设备故障,原料短缺以及生产方法的改变等。
表现性=理想周期时间/ (操作时间/ 总产量)=(总产量/ 操作时间)/ 生产速率表现性考虑生产速度上的损失。
包括任何导致生产不能以最大速度运行的因素,例如设备的磨损,材料的不合格以及操作人员的失误等。
质量指数=良品/总产量质量指数考虑质量的损失,它用来反映没有满足质量要求的产品(包括返工的产品)。
利用OEE的一个最重要目的就是减少一般制造业所存在的六大损失:停机损失、换装调试损失、暂停机损失、减速损失、启动过程次品损失和生产正常运行时产生的次品损失。
下面表格是六大损失的说明及其与OEE的关系:3、OEE计算实例我们举一个例子来说明OEE的计算方法:设某设备某天工作时间为8h, 班前计划停机15min, 故障停机30min,设备调整25min, 产品的理论加工周期为0.6 min/件, 一天共加工产品450件, 有20件废品, 求这台设备的OEE。
根据上面可知:计划运行时间=8x60-15=465 (min)实际运行时间=465-30-25=410 (min)有效率=410/465=0.881(88.1%)生产总量=410(件)理想速度x实际运行时间=1/0.6 x 410=683表现性=450/683=0.658(65.8%)质量指数=(450—20)/450=0.955(95.5%)OEE=有效率x表现性x质量指数=55.4%根据OEE系统所提供的数据,你可以方便的知道自己工厂存在什么问题,例如,如果你的有效率在某一个时间段很低,说明在六大损失中和OEE可用率损失有关的故障太多,那么,显而易见,你应该把改善重点放在这些方面了!同样,如果质量指数或者表现性导致你的OEE水平降低,那么你就应该把目光放在和它们有关的问题点上。
在表一中,我们只列举了一些事件原因,在实际应用中它可以包括和生产有关的任何原因。
世界范围的研究表明,目前制造业的平均OEE为60%.全球工业的OEE平均渴望值应该为85%(世界级OEE指数)或者更高。
显而易见,目前的OEE指数还有许多可以提高的余地,特别是在我们国家。
4、OEE的作用实践证明OEE是一个极好的基准工具,通过OEE模型的各子项分析,它准确清楚地告诉你设备效率如何,在生产的哪个环节有多少损失,以及你可以进行那些改善工作。
长期的使用OEE工具,企业可以轻松的找到影响生产效率的瓶颈,并进行改进和跟踪。
达到提高生产效率的目的,同时使公司避免不必要的耗费。
5、OEE数据采集方法OEE的计算虽然简单,但是,在实际的应用中,当与班次,员工,设备,产品等生产要素联系在一起时,便变得十分复杂,利用人工采集数据计算OEE显得麻烦费事,为了更有效的利用OEE这个工具,OEE数据采集信息化越来越成为人们关心的话题,OEE IMPACT是世界上最优秀的OEE系统,它具有自动化数据采集模块,可以轻松地获取有关设备的生产信息,为OEE提供最有价值的数据,同时,该系统也可以生成实时的生产信息报告,包括故障停工,在制品信息和OEE等。
通过这些有价值的数据,企业的管理工作无疑会变得轻松而简单。
该系统已在世界上许多著名公司得到广泛的应用,例如标致汽车,雅诗蓝黛化妆品美国伊顿汽车零部件等。
OEE设备整体效能简介(主讲人)一、引入随着市场竞争的日益激烈,制造商要想持续的获得高的经济效益,最大化的挖掘和改善生产车间的生产效率显得极其重要,在某些方面,它甚至成为企业是否可以赢利的决定性因素。
然而,在现在的制造业中,看似良好运作的生产车间实际上并没有以最好的状态进行工作,设备和操作人员的价值存在很大的改善空间,这无形中为企业带来了巨大的损失。
为了解决这一问题,国际制造业提出了全局设备效率(OEE)的概念。
二、OEE的定义一般,每一个生产设备都有自己的最大理论产能,要实现这一产能必须保证没有任何干扰和质量损耗。
当然,实际生产中是不可能达到这一要求,由于许许多多的因素,车间设备存在着大量的失效: 例如除过设备的故障,调整以及设备的完全更换之外,当设备的表现非常低时,可能会影响生产率,产生次品,返工等。
OEE是一个独立的测量工具,它用来表现实际的生产能力相对于理论产能的比率。
国际上对OEE的定义为:OEE是Overall Equipment Effectiveness(设备总体效能)的缩写,它由可用率,生产率以及优质率三个关键要素组成,即:OEE=可用率X 生产率X优质率。
其中:可用率=操作时间/ 计划工作时间它是用来考虑停工所带来的损失,包括引起计划生产停工的任何事件,例如设备故障,原料短缺以及生产方法的改变等。
生产率=理想周期时间/ (操作时间/ 总产量)=(总产量/ 操作时间)/ 生产速率或,用标准工时代替:生产率=标准工时/实际工时生产率考虑生产速度上的损失。
包括任何导致生产不能以最大速度运行的因素,例如设备的磨损,材料的不合格以及操作人员的失效等。
优质率=合格品(或优质品)数量/总产量优质率考虑质量的损失,它用来说明没有满足质量要求的那些产品,包括返工的产品。
利用OEE的一个最重要目的就是减少一般制造业所存在的六大损失:停工、设置/调节(可用率);微停工和减速(生产率);调节机器生成的次品和生产正常运行时产生的次品。
下面表格是六大损失以及他们为生产带来的影响:表一三、OEE计算实例我们举一个例子来说明OEE的计算方法:假如下面是某车间一个班次的记录:表二从上面的数据,我们可以得出:计划生产时间=班次时间—计划中断=480—2 X 15=450(分钟)工作时间=计划时间—停工时间=420—47=373(分钟)良品=生产数量—次品=19271—423=18,848(件)从而:可用率=工作时间/计划生产时间=373/420=0.888(88.8%)生产率=生产数量/(理想速度X 工作时间)=19271/(60 X 373)=0.861(86.1%)优质率=良品/生产数量= 18,848/19,271=0.978(97.8%)OEE=可用率X 生产率X 优质率=0.888 X 0.861 X 0.978=0.748(74.8%)根据OEE系统所提供的数据,你可以方便的知道自己工厂存在什么问题,例如,如果你的可用率在某一个时间段很低,说明在六大损失中和OEE可用率损失有关的故障太多,那么,显而易见,你应该把改善重点放在这些方面了!同样,如果优质率或者生产率导致你的OEE水平降低,那么你就应该把目光放在和它们有关的问题点上。