工件热变形
热变形温度和玻璃化温度的区别

热变形温度和玻璃化温度的区别“热变形温度”与“玻璃化温度”,这两个概念有很多人都不清楚。
那么接下来就让我们一起了解一下吧!不过,虽然它们的名字里都有“温度”两个字,但是它们还是有区别的。
热变形温度,也叫热脆性温度或热软化温度。
它指金属经过锻造和淬火后,其强度和硬度升高,而塑性、韧性降低的温度。
所以,热变形温度低于室温。
例如,一般碳钢在40~50 ℃时发生珠光体转变,所以工件热变形温度比室温高。
有些金属材料可以在60~80 ℃时发生马氏体转变,因此,工件热变形温度比室温低。
高于100 ℃时由于晶粒粗大,组织不均匀,严重影响使用寿命,故一般高于200 ℃才允许工作。
工件内部各晶粒内部和晶粒之间发生滑移,导致晶界面积减少,所以应力增加,韧性下降。
在一定条件下还会产生蠕变现象。
所以,热变形温度并非金属材料的屈服点。
1、在较低的温度下,脆性增大,塑性提高;2、当温度超过临界点时,塑性降低,脆性增大; 3、在某一温度下,塑性不变,脆性反而提高,这种现象叫做“相变”。
它们的区别主要在于它们所表示的物理量不同。
热变形温度是表征金属在经过锻造和淬火等热加工后,其强度和硬度升高,而塑性、韧性下降的温度。
一般高于室温。
它是判断金属材料加工性能的一项重要指标。
例如,一般碳钢在40~50 ℃时发生珠光体转变,所以工件热变形温度比室温高。
有些金属材料可以在60~80 ℃时发生马氏体转变,因此,工件热变形温度比室温低。
高于100 ℃时由于晶粒粗大,组织不均匀,严重影响使用寿命,故一般高于200 ℃才允许工作。
3、低于某一温度时,塑性降低,脆性增大;4、在某一温度下,塑性不变,脆性反而提高,这种现象叫做“相变”。
它们的区别主要在于它们所表示的物理量不同。
热变形温度是表征金属在经过锻造和淬火等热加工后,其强度和硬度升高,而塑性、韧性下降的温度。
高于室温。
工艺系统热变形对加工精度的影响
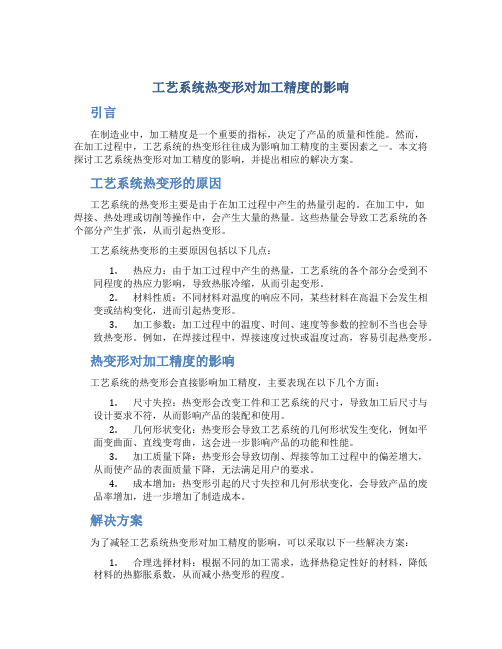
工艺系统热变形对加工精度的影响引言在制造业中,加工精度是一个重要的指标,决定了产品的质量和性能。
然而,在加工过程中,工艺系统的热变形往往成为影响加工精度的主要因素之一。
本文将探讨工艺系统热变形对加工精度的影响,并提出相应的解决方案。
工艺系统热变形的原因工艺系统的热变形主要是由于在加工过程中产生的热量引起的。
在加工中,如焊接、热处理或切削等操作中,会产生大量的热量。
这些热量会导致工艺系统的各个部分产生扩张,从而引起热变形。
工艺系统热变形的主要原因包括以下几点:1.热应力:由于加工过程中产生的热量,工艺系统的各个部分会受到不同程度的热应力影响,导致热胀冷缩,从而引起变形。
2.材料性质:不同材料对温度的响应不同,某些材料在高温下会发生相变或结构变化,进而引起热变形。
3.加工参数:加工过程中的温度、时间、速度等参数的控制不当也会导致热变形。
例如,在焊接过程中,焊接速度过快或温度过高,容易引起热变形。
热变形对加工精度的影响工艺系统的热变形会直接影响加工精度,主要表现在以下几个方面:1.尺寸失控:热变形会改变工件和工艺系统的尺寸,导致加工后尺寸与设计要求不符,从而影响产品的装配和使用。
2.几何形状变化:热变形会导致工艺系统的几何形状发生变化,例如平面变曲面、直线变弯曲,这会进一步影响产品的功能和性能。
3.加工质量下降:热变形会导致切削、焊接等加工过程中的偏差增大,从而使产品的表面质量下降,无法满足用户的要求。
4.成本增加:热变形引起的尺寸失控和几何形状变化,会导致产品的废品率增加,进一步增加了制造成本。
解决方案为了减轻工艺系统热变形对加工精度的影响,可以采取以下一些解决方案:1.合理选择材料:根据不同的加工需求,选择热稳定性好的材料,降低材料的热膨胀系数,从而减小热变形的程度。
2.控制加工参数:合理控制加工过程中的温度、时间、速度等参数,避免过高的温度或速度导致的热变形。
3.使用稳定的工艺设备:选择稳定性高的工艺设备,减小工艺系统的热变形。
平面磨床的切削力和热变形研究

平面磨床的切削力和热变形研究磨床作为一种常用的机床设备,广泛应用于金属加工领域。
其中,平面磨床是一种常见的磨床类型,其主要用于平面零件的精密加工和修整。
在磨削过程中,切削力和热变形是影响加工质量和效率的重要因素。
本文将探讨平面磨床的切削力和热变形研究,并提出相关解决方案。
切削力是材料在切削过程中受到的力,其大小直接影响加工质量和机床的稳定性。
切削力的研究对于优化切削参数、提高加工效率具有重要意义。
在平面磨床的研究中,切削力的测量是关键的一步。
通过合理选择传感器和测量方法,可以获得准确的切削力数据。
研究表明,影响切削力的因素有很多,包括切削速度、切削深度、磨削轮材料和磨削液等。
其中,切削速度是影响切削力最主要的因素之一。
增大切削速度会导致切削力的增加,但当超过一定临界速度时,切削力的增加会趋于平缓。
此外,切削深度也会显著影响切削力的大小。
增大切削深度会使切削力增加,但同时也会增加加工表面的粗糙度。
磨削轮材料对于切削力也有重要影响。
例如,使用金刚石磨削轮可以减小切削力,提高磨削效率。
而磨削液则可以起到冷却润滑的作用,减小切削时产生的热量,从而降低热变形的程度。
热变形是指在磨削过程中,由于切削热的积累而导致的工件变形现象。
热变形会严重影响加工精度和表面质量。
因此,研究磨床的热变形问题对于提高加工质量具有重要意义。
磨削过程中的切削热主要来自于材料的塑性变形和磨屑与磨削轮的摩擦。
通过降低切削速度和提高切削液的冷却效果,可以减小切削热的积累。
此外,选用低热导率的材料也可以有效降低热变形的程度。
针对磨床的切削力和热变形问题,可以采取以下一些解决方案:1. 优化切削参数:通过合理选择切削速度、切削深度和进给速度等参数,可以降低切削力和热变形的发生。
2. 选择合适的磨削轮和磨削液:选择硬度高、耐磨性好的磨削轮材料可以减小切削力,提高磨削效率。
同时,选用适合的磨削液可以有效降低切削时产生的热量。
3. 加强刀具刃磨和修整:定期对刀具进行刃磨和修整可以保持其良好的切削状态,减小切削力和热变形的发生。
数控机床操作中防止工件变形的技巧与方法

数控机床操作中防止工件变形的技巧与方法在数控机床操作中,工件变形是一个常见且令人头痛的问题。
工件变形不仅会导致加工精度下降,还会影响产品的质量和使用寿命。
因此,为了确保加工过程的准确性和稳定性,我们需要采取一些技巧和方法来防止工件变形。
首先,在数控机床操作中,选择合适的工艺参数非常重要。
不同材料对加工参数的要求有所不同,因此在加工前需要对工件材料进行充分的了解,并根据其特性来选择合适的加工参数。
例如,不同的材料对切削速度、进给速度和切削深度等参数都会有不同的要求。
合理的参数选择有助于减少切削过程中的热变形,从而避免工件的变形问题。
其次,在加工过程中,合理的夹紧方式也能够有效地防止工件的变形。
夹紧力的大小直接影响到工件在切削过程中的稳定性和变形情况。
因此,在夹紧工件时需要注意夹紧力的均匀分布和合理控制。
同时,还应选用合适的夹具和夹具形式,使其与工件紧密接触,并能够有效地固定工件,避免因工件的滑动、晃动等现象而导致的变形问题。
此外,加工过程中的冷却剂也是防止工件变形的关键因素之一。
适当的冷却剂的使用可以有效地降低工件的温度,减少切削过程中的热变形。
合理选择冷却剂的类型和使用方式,能够使切削热均匀地散发出去,从而减少工件的变形情况。
同时,还需要定期检查冷却剂的质量和使用情况,保持其在加工过程中的稳定性和可靠性。
此外,在数控机床操作中,避免切削过程中的振动和共振现象也是防止工件变形的重要手段。
振动和共振现象会导致加工过程中的冲击和不稳定性,从而使工件发生变形。
为了避免这种情况的发生,可以采取一些措施,如增加机床的刚性、加强切削刚度、合理选择切削工具的形状和参数等,从而减少切削过程中的振动和共振现象,确保加工的稳定性和准确性。
最后,在数控机床操作中,工件的后处理也是防止工件变形的重要环节。
在加工结束后,需要采取适当的冷却和退火处理,以缓解工件内部的应力和变形。
此外,在工件的测量和检验过程中,可以进一步发现工件的变形问题,并及时采取纠正措施,以确保加工质量和精度。
机床温度场和热变形的测定

机床温度场和热变形的测定一﹑实验目的1.通过实验了解﹑分析机床的热态特性,即受热后温升和热变形的情况,以及各热源对加工精度的影响;2.了解和分析减少机床热变形的措施;3.熟悉机床温度场和热变形的测试方法。
二﹑实验用设备和仪器1.普通车床一台;2.半导体点温计一个;3.千分表两只(也可用非接触式电容测微仪或涡流测微仪);4.检验棒一根。
此外,在温度场的测试中,还可采用热电偶,它的测量精度较高(0.1~0.20C),反应速度快,制作亦简单,成本不高。
具体制作方法可参考有关资料。
三﹑实验原理机床的温升和热变形是由各种“热源”引起的。
工艺系统的热源可以分为两大类:即内部热源和外部热源。
其中内部热源包括机床的传动件(如电动机﹑轴承﹑齿轮副﹑液压系统﹑离合器和导轨副等)运转时产生的“摩擦热”和机床加工工件过程中所产生的“切削热”(如工件﹑刀具﹑切屑和切削液等);外部热源包括环境温度(如气温﹑冷热风气流﹑地基温度等)的变化和各种热辐射(如阳光﹑暖气设备﹑人体等)的影响。
但热源的热量本身并不直接产生变形,只有当热源热通过热传导﹑对流和辐射等传热方式(在机床上,传热的主要方式是热传导,而对流和辐射则往往起散热作用)向外传热,使机床各部件产生温升,形成温度差以后,才会出现热变形现象。
机床在内外热源影响下,各部分的温度将发生变化。
由于热源分布的不均匀和机床结构的复杂性,机床上各部分的温度不是一个恒定的值,在一般情况下,温度是时间和空间的函数。
这种随时间而变的温度场,称之为不稳定温度场。
如果机床上各点的温度都不随时间而变,则此温度场称为稳定温度场。
机床上一般为不稳定温度场。
机床热变形的影响,主要有以下几方面:由于机床各热源的分布及其所产生的热量都是不均匀的,因此机床各个零部件的温升和热膨胀也就不均匀,从而改变了各运动部件的相对位置及其位移的轨迹,因此,影响加工精度;改变滑移面的间隙,降低油膜的承载能力,恶化机床的工作条件;由于工件升温,与测量工具的温度不同,影响了测量精度。
零件加工中工件变形产生的原因

在机械零件成形加工的过程中,我们最常使用的是切削加工工艺。
在对工件进行切削加工的时候,由于切削热、机床零件间的摩擦热、工件的内应力以及夹紧力等原因,会让工件发生变形,使得精度变差,以致造成废品。
因此,在进行机加工的时候,需要对工件变形原因有一定的了解,并做好变形的预防。
工件变形的主要原因有以下几种:一、热变形1、刀具的热变形由于切削热会使刀刃和刀体变热,使刀头变形、伸长而使工件尺寸发生变化。
刀头伸长量与刀头深处长度、截面大小、刀片厚度、刀刃锋利程度由一定关系。
刀头深入长度越大,伸长量越大;刀杆截面与伸长量成反比;刀片越厚伸长量越小。
2、机床的热变形由于切削热与机床零件之间进行摩擦所产生的热,会使机床某些部件发热而发生变形,例如车床主轴箱的变形会使主轴中心高度增加、水平方向内位移。
3、工件的热变形由于切削热会使工件变热,温度上升。
工件变热有均衡变热和不均衡变热两种。
均衡变热会使工件尺寸改变,而形状会保持不变;不均衡变热时,不仅工件尺寸变化,而且形状也会发生变化。
二、内应力引起的变形当零件在没有任何外界符合的作用而内部存在着应力时,内应力是相互平衡的,因此外边面没有什么变化。
内应力有时几乎达到破坏极限,但是在外形上与没有内应力零件并无区别。
生产中产生内应力的原因有以下几个方面:1、铸件的内应力金属液体浇入型模之后,在凝固与冷却的时候体积会发生收缩。
在收缩时会受到铸型阻碍,或者由于铸件各部分在冷却过程中存在温差而引起阻碍,让各部分拉长或压缩产生内应力。
2、锻件和热处理件的内应力锻件和热处理件的内应力,主要是由于热加工过程中,不均匀冷却造成的。
热加工中产生内应力的根源是由材料自塑性状态转变为弹性状态,各种存在温差的原因。
3、冷加工中的内应力冷加工时,使工件表面硬化,并在表面层的金属中呈现内应力。
应力层切除后应力重新分布,使棒料、薄板、圆盘产生扭曲变形。
影响机械加工精度的因素

影响机械加工精度的因素机械加工系统(简称工艺系统)由机床、夹具、刀具和工件组成。
影响加工精度的原始误差主要包括以下几方面:1) 工艺系统的几何误差(包括机床、夹具和刀具等的制造误差及其磨损);2) 工件装夹误差;3) 工艺系统受力变形引起的加工误差;4) 工艺系统受热变形引起的加工误差;5) 工件内应力重新分布引起的变形;6) 其它误差(包括原理误差、测量误差、调整误差)。
一、工艺系统的几何误差(一)机床的几何误差加工中,刀具相对于工件的成形运动,通常都是通过机床完成的,工件的加工精度在很大程度上取决于机床的精度。
机床制造误差中对工件加工精度影响较大的误差有:主轴回转误差、导轨误差和传动误差。
1. 主轴回转误差主轴回转误差是指主轴实际回转轴线相对其平均回转轴线的变动量。
为便于分析,可将主轴回转误差分解为径向圆跳动、轴向圆跳动和角度摇摆三种不同形式的误差。
2.导轨误差导轨是确定机床各主要部件相对位置关系的基准。
(1)导轨在水平面内的直线度误差对加工精度的影响(2)导轨在垂直平面内的直线度误差对加工精度的影响(3)导轨间的平行度误差对加工精度的影响3.传动链误差传动链误差是指传动链始末两端传动元件间相对运动的误差,一般用传动链末端元件的转角误差来衡量。
(二)刀具的几何误差刀具误差对加工精度的影响随刀具种类的不同而不同。
采纳定尺寸刀具(例如钻头、铰刀、键槽铣刀、圆拉刀等)加工时,刀具的尺寸误差和磨损将直接影响工件尺寸精度。
采纳成形刀具(例如成形车刀、成形铣刀、成形砂轮等)加工时,刀具的外形误差和磨损将直接影响工件的外形精度。
对于一般刀具(例如车刀、镗刀、铣刀等),其制造误差对工件加工精度无直接影响。
(三)夹具的几何误差夹具的作用是使工件相对于刀具和机床占有正确的位置,夹具的几何误差对工件的加工精度(特殊是位置精度)有很大影响。
二、装夹误差装夹误差包括定位误差和夹紧误差两个部分。
(一)定位误差的概念因定位不精确而引起的误差称为定位误差。
CNC机床加工中的切削区温度分布与热变形分析

CNC机床加工中的切削区温度分布与热变形分析CNC(Computer Numerical Control)机床是一种基于计算机控制的精密加工设备,广泛应用于各个领域的零部件加工中。
在CNC机床加工过程中,切削区的温度分布和热变形是需要关注和分析的重要问题。
本文将对CNC机床加工中的切削区温度分布与热变形进行分析和讨论。
一、切削区温度分布分析在CNC机床加工过程中,切削区温度的分布是由切削速度、进给速度、切削深度等多个参数共同决定的。
切削区的温度分布对刀具的寿命、材料的变形以及切削表面质量等都有重要影响。
1. 切削速度对温度分布的影响切削速度是指刀具相对于工件表面的移动速度,它直接影响到切削区的温度分布。
通常情况下,切削速度越高,切削区的温度也越高。
因为切削速度增加会导致切削时摩擦热的积累增加,从而使切削区温度升高。
2. 进给速度对温度分布的影响进给速度是指刀具在单位时间内相对于工件的运动距离,它对切削区的温度分布也有重要影响。
进给速度的增加会导致切削区温度的升高。
这是因为进给速度增加后,切削热量的积累速度加快,导致温度升高。
3. 切削深度对温度分布的影响切削深度是指工件上刀具切削过程中的垂直深度。
切削深度对温度分布的影响主要表现在两个方面。
首先,切削深度增加会导致切削力的增大,从而引发更多的热量产生,使切削区的温度升高。
其次,较大的切削深度会导致切槽情况的复杂化,使得局部温度的分布不均匀,进而影响到整体温度分布。
二、热变形分析热变形是指在切削加工过程中,由于高温作用下材料的体积发生改变而引起的材料变形现象。
它是由于切削区高温引起的材料热胀冷缩所导致的。
1. 热胀与热缩在切削区,刀具与工件之间的摩擦产生热量,使切削区的温度升高。
当材料达到一定温度时,材料发生热胀,即体积膨胀。
当切削热源消失或减小时,材料会受到空冷和切削力的作用而发生热缩,即体积收缩。
2. 热变形对加工精度的影响热变形会导致加工件的尺寸和形状发生变化,从而影响到加工精度。
机械加工中工件变形的原因及预防措施探微

机械加工中工件变形的原因及预防措施探微摘要:机械加工中的工件变形是由多种因素共同作用引起的。
本文首先分析了工件变形的原因,包括材料变形、加工过程中Thermal变形、刀具磨损、夹具变形等。
接着探讨了如何预防工件变形,提出对材料的选择、加工参数的优化、刀具维护与更换等方法。
引言:工件变形是机械加工中常见的质量问题之一,主要表现为轴线偏差、表面波纹、尺寸变形等。
对于高精度机械零部件的加工,特别是需要进行高精度加工的零件,工件变形会直接影响其加工质量和精度,进而影响产品质量。
因此,如何预防和控制工件变形是机械加工的关键之一。
本文旨在分析工件变形的原因及其预防措施。
一、工件变形的原因1、材料变形材料在机械加工过程中会因受热、受力、受切削压力作用而产生变形。
材料温度的变化会引起材料的热膨胀和结构变化,进而引起工件变形。
材料的受力作用也会引起工件变形。
例如在铣削过程中,切削力对材料的压缩变形是主要的变形形式。
2、加工过程中的热变形热变形是工件在机械加工中的一个重要变形原因。
一般情况下,机床和刀具在机械加工过程中会发生剧烈的热变形,从而影响工件的加工质量。
例如,在高速切削过程中,因为加工热量过大,使工件表面温度升高,导致材料热膨胀,工件变形;又由于高速切削要求高速公转,冷却与加热交替,工件更容易产生形变。
因此,在加工高精度零件时应该注意加工温度和热处理,以减少工件热变形的发生。
3、刀具磨损刀具磨损也是造成工件变形的原因之一。
虽然磨损量很小,但它会导致加工质量的下降和工件的变形。
例如,切削刃磨损后会导致加工力度的增加,从而引起工件的弹性变形。
4、夹具变形夹具变形也是造成工件变形的原因之一。
在机械加工中,夹具在合理使用的情况下,也会因长期应力变形或其松动等因素导致夹具变形。
二、预防工件变形的措施1、材料的选用选择材料是防止工件变形的关键环节。
应遵循以下原则:(1)选择均一性、强健性和稳定性良好的材料。
(2)选择铸造硬化材料,能够使工件内部达到一致的硬度和强度,减少变形。
金属材料热处理变形原因及防止变形的技术措施

金属材料热处理变形原因及防止变形的技术措施摘要:热处理能改善工件的综合机械机能,但热处理过程引起工件的变形是不可避免的。
任何因素的变化都或多或少地影响工件的变形倾向和形变大小。
在热处理过程中,能够把握工件热处理过程中导致工件变形的主要因素和关键点。
通过分析和实践,改进热处理工艺技术,一定能够在热处理工件的形变问题上得到突破,制定出合理的技术措施,保证热处理产品的质量和合格率。
关键词:金属材料;热处理;变形原因;防止变形技术引言实际工业生产中,仅凭选择材料和成形工艺并不能满足工件所需要的性能,通过对金属材料进行热处理而获得优良的综合性能是必不可少的。
但金属材料的热处理除改善材料的综合性能的积极作用外,在热处理过程中也不可避免地会产生或多或少的变形,而这又是工件生产过程中极力消除和避免的。
因此,需要找出工件热处理过程中发生形变的原因,采取技术措施把变形量控制在符合要求范围内。
1金属材料性能分析在当前的社会生产生活中,金属材料的应用范围十分的广泛。
由于金属材料具有韧性强、塑性好以及高强度的特点,因此其在诸多行业中均有所应用。
当前常用的金属材料主要包括两种:即多孔金属材料以及纳米金属材料。
纳米金属材料:一般情况下,只有物质的尺寸达到了纳米的级别,那么该物质的物理性质和化学性质均会发生改变。
在分析与研究金属材料性能的过程中,主要分析金属材料的如下两种性能:其一,硬度。
一般情况下,金属材料的硬度主要指的是金属材料的抗击能力。
其二,耐久性。
耐久性能和腐蚀性是金属材料需要着重考虑的一对因素。
在应用金属材料的过程中不可避免的会受到各种物质的腐蚀,由此就会导致金属材料出现缝隙等问题。
2金属热处理变形的原因分析在工业生产过程中,各种金属零件早已成为机械制造的必要部分。
在零件的设计、选材中,对综合性能方面也提出了更高要求。
特别是生产过程中,对产品热处理加工后的品质提出了新要求。
但在热处理过程中出现形变等质量问题,一直是热处理过程中难以克服的。
薄壁零件车削加工中热变形分析及对策

薄壁零件车削加工中热变形分析及对策薄壁零件在车削加工过程中容易受到热变形的影响,影响产品的加工精度和表面质量。
对薄壁零件车削加工中的热变形进行分析并提出对策是非常必要的。
本文将从热变形的原因、分析方法以及对策措施等方面进行深入探讨,以期为相关行业提供一些有益的参考。
一、热变形的原因1.1 刀具和工件之间的摩擦在车削加工中,刀具和工件之间的摩擦会产生大量的热量,导致工件局部升温。
当工件表面发生热变形时,其形状和尺寸都会发生变化,从而影响产品的加工精度。
1.2 切削温度的影响1.3 切削速度和进给速度对热变形的影响切削速度和进给速度的选择直接影响着切削过程中的热变形情况。
如果选择不当,容易引起工件的热变形,进而影响产品的加工质量。
二、热变形的分析方法2.1 数值模拟分析通过数值模拟分析的方法,可以对车削过程中的热变形情况进行较为准确的预测。
数值模拟分析可以方便地获取刀具和工件间的摩擦热源以及切削温度等信息,从而为热变形的分析和对策提供科学依据。
2.2 实验测量分析三、对策措施3.1 采用合适的刀具材料为了减少车削过程中的热变形,可以选择较高的热导率和热稳定性较好的刀具材料,如硬质合金等,以提高刀具的散热性能,从而减少切削时的热量积累。
3.2 优化切削参数针对薄壁零件的车削加工,可以通过优化切削速度、进给速度和切削深度等参数,以减少切削时的热量积累,从而减少热变形的产生。
3.3 冷却液的应用在车削加工过程中,适当地应用冷却液可以有效地降低工件的表面温度,从而减少热变形的产生。
冷却液还可以有效地冷却刀具,减少刀具的磨损和延长使用寿命。
3.4 加强工件的支撑在薄壁零件的车削加工过程中,应加强对工件的支撑,以减少工件的挠曲和变形,从而降低热变形的影响。
数控机床技术中的加工力与热变形分析
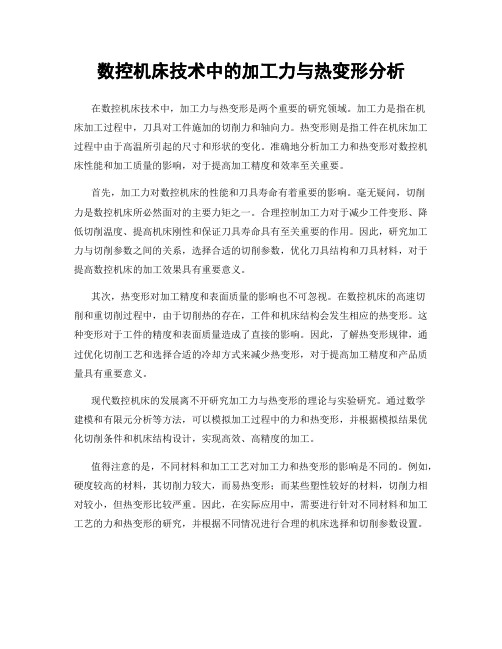
数控机床技术中的加工力与热变形分析在数控机床技术中,加工力与热变形是两个重要的研究领域。
加工力是指在机床加工过程中,刀具对工件施加的切削力和轴向力。
热变形则是指工件在机床加工过程中由于高温所引起的尺寸和形状的变化。
准确地分析加工力和热变形对数控机床性能和加工质量的影响,对于提高加工精度和效率至关重要。
首先,加工力对数控机床的性能和刀具寿命有着重要的影响。
毫无疑问,切削力是数控机床所必然面对的主要力矩之一。
合理控制加工力对于减少工件变形、降低切削温度、提高机床刚性和保证刀具寿命具有至关重要的作用。
因此,研究加工力与切削参数之间的关系,选择合适的切削参数,优化刀具结构和刀具材料,对于提高数控机床的加工效果具有重要意义。
其次,热变形对加工精度和表面质量的影响也不可忽视。
在数控机床的高速切削和重切削过程中,由于切削热的存在,工件和机床结构会发生相应的热变形。
这种变形对于工件的精度和表面质量造成了直接的影响。
因此,了解热变形规律,通过优化切削工艺和选择合适的冷却方式来减少热变形,对于提高加工精度和产品质量具有重要意义。
现代数控机床的发展离不开研究加工力与热变形的理论与实验研究。
通过数学建模和有限元分析等方法,可以模拟加工过程中的力和热变形,并根据模拟结果优化切削条件和机床结构设计,实现高效、高精度的加工。
值得注意的是,不同材料和加工工艺对加工力和热变形的影响是不同的。
例如,硬度较高的材料,其切削力较大,而易热变形;而某些塑性较好的材料,切削力相对较小,但热变形比较严重。
因此,在实际应用中,需要进行针对不同材料和加工工艺的力和热变形的研究,并根据不同情况进行合理的机床选择和切削参数设置。
在实际加工中,为了准确测量加工力和监控热变形的情况,研究者通常会采用力传感器和位移传感器来获取相关数据。
利用这些传感器获取的数据,可以通过计算和分析得到加工力和热变形的准确数值,进而优化加工工艺和机床设计。
综上所述,数控机床技术中的加工力与热变形分析对于提高加工精度、加工质量和机床性能具有重要意义。
影响机械加工精度的主要因素分析

影响机械加工精度的主要因素分析加工精度是指零件加工后的几何参数(尺寸、几何形状和相互位置)的实际值与理想值之间的符合程度。
而实际值与理想值之间的偏离程度(即差异)则为加工误差,加工误差的大小反映了加工精度的高低。
1、影响机械加工精度的主要因素(1)工艺系统的几何误差1)加工原理误差加工原理误差是指采用了近似的成形运动或近似形状的刀具进行加工而产生的误差。
比如,数控机床一般只具有直线和圆弧插补功能,因而即便是加工一条平面曲线,也必须用许多很短的折线段或圆弧去逼近它,刀具连续地将这些小线段加工出来,也就得到了所需的曲线形状。
逼近的精度可由每条线段的长度来控制。
因此,在曲线或曲面的数控加工中,刀具相对于工件的成形运动是近似的。
进一步地说,数控机床在做直线或圆弧插补时,是利用平行坐标轴的小直线段来逼近理想直线或圆弧的,这里存在着加工原理误差。
但由于数控机床的脉冲当量可以使这些小直线段很短,逼近的精度很高,事实上数控加工可以达到很高的加工精度。
又如,滚齿用的齿轮滚刀有两种误差:一是为了制造方便,采用阿基米德蜗杆或法向直廓蜗杆代替渐开线基本蜗杆而产生的刀刃齿廓形状误差;二是由于滚刀刀齿有限,实际上加工出的齿形是一条由微小折线段组成的曲线,它与理论上的光滑渐开线有一定的差异。
这里也存在着加工原理误差。
用近似的成形运动或近似形状的刀具虽然会带来加工原理误差,但往往可以简化机床结构或刀具形状,以提高生产率。
因此,只要这种方法产生的误差不超过允许的范围,往往比准确的加工方法能获得更好的经济效益,在生产中仍然得到了广泛的应用。
2)机床误差机床误差是由机床的制造、安装误差和使用中的磨损造成的。
在机床的各类误差中,对工件加工精度影响较大的主要是主轴回转误差和导轨误差。
机床主轴是带动工件或刀具回转,产生主要切削运动的重要零件。
其回转运动精度是机床主要精度指标之一,主轴回转误差主要影响零件加工表面的几何形状精度、位置精度和表面粗糙度。
10.4工艺系统的热变形误差讲解
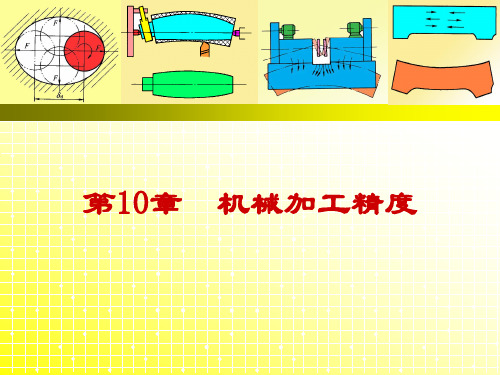
第四节 工艺系统的热变形误差
内部热源
工艺系统 热源 外部热源
切削热 摩擦热 环境热 辐射热
工件、刀具、切屑、 切削液
电机、轴承、齿轮、 油泵等
气温、室温变化、热 、冷风等
日光、照明、暖气、 体温等
一、机床热变形引起的加工误差
机 由于机床结构形式和工作条件不同,引起机床热
床 热
变形的热源和变形形式也不相同。
端面的平面度误差。
车刀的热变形曲线
刀
具
热
变
形
引
起
的
加
工
B—刀具冷却变形曲线
误
差 当车刀停止车削后,刀具冷却变形过程如曲线B。
车刀的热变形曲线
刀
当车削一批短小轴类
具
工件时,加工时断时
热 变
续(如装卸工件)间
形
断切削,变形过程如
引
曲线C。
起
的
加
C—断续切削变形曲线
工
在开始切削阶段,刀具热变形较显著,对加工
件 精密件,环境温度也有很大的影响。传入工件的热量
热 越多、工件的质量越小则热变形越大。
变 形
1.工件均匀受热
引
车镗轴套类零件圆柱面,长度及径向受热变形。
起 若在受热时测量达到规定尺寸,冷却后尺寸变小, 可
的 能出现尺寸超差。
加
工
误
差
1.工件均匀受热
工
对于一些形状简单、结构对称的零件,如轴、套
件 筒等,加工时切削热能较均匀地传入工件,工件热变
误 精度影响较大,当达到热平衡后,其热变形趋于稳 差 定,对加工精度的影响就不明显。
车刀的热变形曲线
刀
具
切割机作业中的切割热源分析与热变形控制
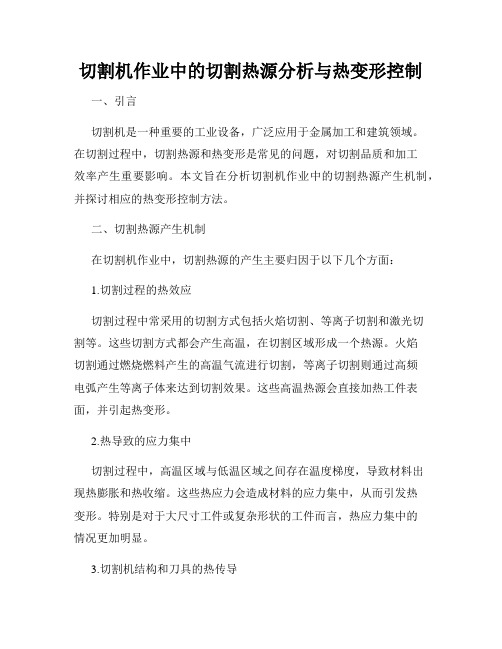
切割机作业中的切割热源分析与热变形控制一、引言切割机是一种重要的工业设备,广泛应用于金属加工和建筑领域。
在切割过程中,切割热源和热变形是常见的问题,对切割品质和加工效率产生重要影响。
本文旨在分析切割机作业中的切割热源产生机制,并探讨相应的热变形控制方法。
二、切割热源产生机制在切割机作业中,切割热源的产生主要归因于以下几个方面:1.切割过程的热效应切割过程中常采用的切割方式包括火焰切割、等离子切割和激光切割等。
这些切割方式都会产生高温,在切割区域形成一个热源。
火焰切割通过燃烧燃料产生的高温气流进行切割,等离子切割则通过高频电弧产生等离子体来达到切割效果。
这些高温热源会直接加热工件表面,并引起热变形。
2.热导致的应力集中切割过程中,高温区域与低温区域之间存在温度梯度,导致材料出现热膨胀和热收缩。
这些热应力会造成材料的应力集中,从而引发热变形。
特别是对于大尺寸工件或复杂形状的工件而言,热应力集中的情况更加明显。
3.切割机结构和刀具的热传导切割过程中,切割机本身的结构和刀具也会参与热传导。
如果切割机结构不合理或材料导热性能差,会导致切割热源无法迅速散热,从而加剧切割热变形的发生。
同样,切割刀具的导热性能也会影响切割热源的大小和分布。
三、热变形控制方法为了控制切割热源产生的热变形,可以采取以下措施:1.合理选择切割方式不同的切割方式产生的切割热源大小和分布有所差异。
在实际应用中,应根据具体工件和要求选择合适的切割方式。
例如,在对热变形要求较高的情况下,可以选择激光切割,它具有高能量密度和热影响区小的优势。
2.优化切割参数切割参数的优化对于控制切割热源和热变形至关重要。
可以通过调节切割速度、气体流量、气体种类、能量密度等参数来实现最佳切割效果。
合理的切割参数设置能够减少热输入、改善热传导和热分布,并最终减小热变形的风险。
3.提高切割机结构和刀具的导热性能切割机结构和刀具的导热性能对热变形有重要影响。
可以通过改进切割机结构设计、选择导热性能较好的材料以及进行合理的散热设计来提高切割机整体的导热性能。
工艺系统受热变形
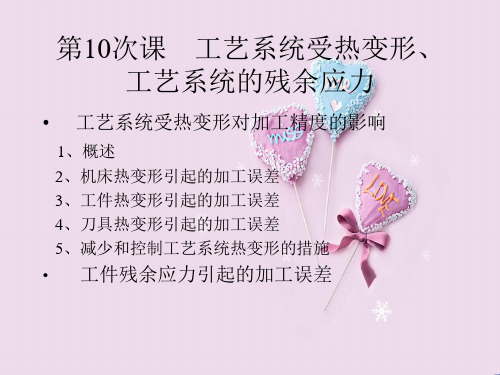
3、不稳态温度场与稳态温度场
由于作用于工艺系统各组成部分的热源,其发热的数量、位置
和作用时间各不相同,各部分的热容量、散热条件也不一样,
因此各部分的温升不等。即使是同一物体,处于不同空间位置 上的各点在不同时间的温度也是不等的。物体中各点温度的分 布称为温度场。当物体未达到热平衡时,各点温度不仅是坐标 位置的函数,也是时间的函数。这种温度场称为不稳态温度场。 物体达到热平衡后,各点温度将不再随时间而变化,而只 是其坐标位置的函数,这种温度场则称为稳态温度场。此时的
例如,对具有分度或转位 的多工位加工工序或采用转位
刀架加工的工序,其分度、转
位误差将直接影响零件有关表 面的加工精度。若将刀具垂直
安装(如图),可将转塔刀架转位
时的重复定位误差转移到零件 内孔加工表面的误差非敏感方 又如,利用镗模进行镗孔,将主轴与镗杆进 行浮动联接。这样可使镗孔时的孔径不受机 床误差的影响,镗孔精度由夹具镗模来保证。
右)传入工件。
磨削时,由于磨屑小,带走的热量很少,大部分传入工件,
故易产生磨削烧伤。
②.摩擦热
主要由机床和液压系统中的运动部分产生的,如电动
机、轴承、齿轮等传动副、导轨副、液压泵、阀等运动部
分产生的摩擦热。摩擦热是机床热变形的主要热源。 ③.外部热源 工艺系统的外部热源,主要是环境温度的变化和热的辐射,
刀具的热变形主要是切削热引起的,传给刀具的热量虽 不多,但由于刀具体积小、热容量小且热量又集中在切削部 分,因此切削部分仍产生很高的温升。
如:高速钢刀具车削时刃
部的温度可高达700 ~ 800℃ ,刀具的热伸长量 可达0.03 ~ 0.05mm。因 此,其影响不可忽略。
五、减少和控制工艺系统热变形的主要途径
影响机械加工精度的主要因素
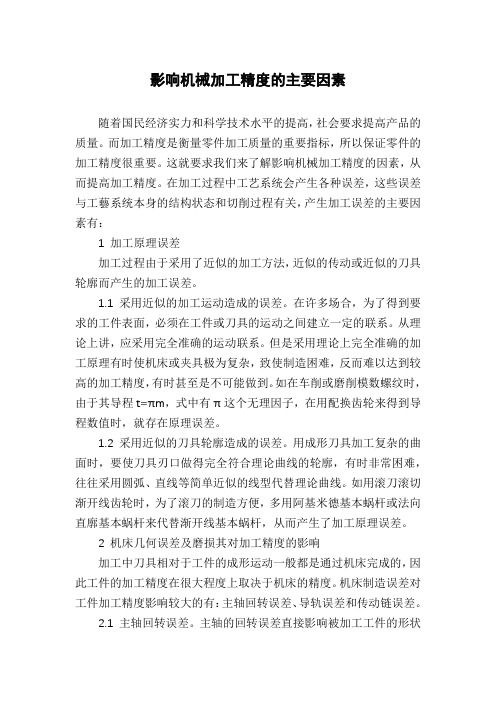
影响机械加工精度的主要因素随着国民经济实力和科学技术水平的提高,社会要求提高产品的质量。
而加工精度是衡量零件加工质量的重要指标,所以保证零件的加工精度很重要。
这就要求我们来了解影响机械加工精度的因素,从而提高加工精度。
在加工过程中工艺系统会产生各种误差,这些误差与工藝系统本身的结构状态和切削过程有关,产生加工误差的主要因素有:1 加工原理误差加工过程由于采用了近似的加工方法,近似的传动或近似的刀具轮廓而产生的加工误差。
1.1 采用近似的加工运动造成的误差。
在许多场合,为了得到要求的工件表面,必须在工件或刀具的运动之间建立一定的联系。
从理论上讲,应采用完全准确的运动联系。
但是采用理论上完全准确的加工原理有时使机床或夹具极为复杂,致使制造困难,反而难以达到较高的加工精度,有时甚至是不可能做到。
如在车削或磨削模数螺纹时,由于其导程t=πm,式中有π这个无理因子,在用配换齿轮来得到导程数值时,就存在原理误差。
1.2 采用近似的刀具轮廓造成的误差。
用成形刀具加工复杂的曲面时,要使刀具刃口做得完全符合理论曲线的轮廓,有时非常困难,往往采用圆弧、直线等简单近似的线型代替理论曲线。
如用滚刀滚切渐开线齿轮时,为了滚刀的制造方便,多用阿基米德基本蜗杆或法向直廓基本蜗杆来代替渐开线基本蜗杆,从而产生了加工原理误差。
2 机床几何误差及磨损其对加工精度的影响加工中刀具相对于工件的成形运动一般都是通过机床完成的,因此工件的加工精度在很大程度上取决于机床的精度。
机床制造误差对工件加工精度影响较大的有:主轴回转误差、导轨误差和传动链误差。
2.1 主轴回转误差。
主轴的回转误差直接影响被加工工件的形状和位置精度,可分解为径向跳动、轴向跳动和角度摆动。
由于存在误差敏感方向,加工不同表面时,主轴的径向跳动所引起的加工误差也不同。
例如,在车床上加工外圆或内孔时,主轴的径向跳动将引起工件的圆度误差,但对于端面加工没有直接影响。
车端面时,主轴的轴向跳动将造成工件端面的平面度误差,以及端面相对于内、外圆的垂直度误差;车螺纹时,会造成螺距误差。
工艺系统受热引起的加工误差
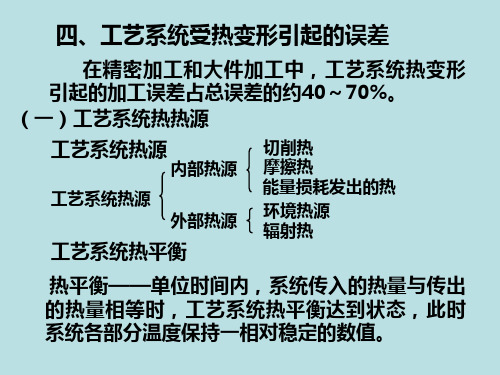
在精密加工和大件加工中,工艺系统热变形 引起的加工误差占总误差的约40~70%。
(一)工艺系统热热源
工艺系统热源
内部热源
工艺系统热源 外部热源
工艺系统热平衡
切削热 摩擦热 能量损耗发出的热
环境热源 辐射热
热平衡——单位时间内,系统传入的热量与传出 的热量相等时,工艺系统热平衡达到状态,此时 系统各部分温度保持一相对稳定的数值。
8H
8 600
平面加工热变形
此值已大于精密导轨直线度要求
2.刀具热变形对加工精度的影响
1)特点
➢热源--切削热 ➢体积小,热容量小,达到热平衡时间较短 ➢温升高,变形不容忽视(达0.03 ~0.05mm)
2)变形曲线(图)
tm—刀具切削时间, tf—刀具不参加切削时 间
3.机床热变形对加工精度的影响
机床热变形特点
1)热源--摩擦热、传动热和外界热源传入的热量 2)体积大,热容量大,温升不高,达到热平衡时间长 3) 结构复杂,温度场和变形不均匀,对加工精度影响显著
其他机床热变形
➢ 立铣 ➢ 外圆磨 ➢ 导轨磨b)外圆磨床受热形形态a)铣床受热变形形态
c)导轨磨床受热变形形态
(三) 减小工艺系统热变形的途径
(二) 工艺系统热变形对加工精度的影响
1.工件热变形对加工精度的影响 ➢工件产生热变形的热源
切削热、辐射热(精密零件) ➢ 圆柱类工件热变形
长度: 直径:
例:长400mm丝杠,加工过程温升1℃,热伸 长量为:LaL =1.17×10-5×400×1 mm =0.0047 mm
5级丝杠螺距累积误差全长≤5μm
1.工件热变形对加工精度的影响
- 1、下载文档前请自行甄别文档内容的完整性,平台不提供额外的编辑、内容补充、找答案等附加服务。
- 2、"仅部分预览"的文档,不可在线预览部分如存在完整性等问题,可反馈申请退款(可完整预览的文档不适用该条件!)。
- 3、如文档侵犯您的权益,请联系客服反馈,我们会尽快为您处理(人工客服工作时间:9:00-18:30)。
Table. 1 Character istic da ta of workp iece、wheel and f lu id
m a teria l k (w (m. ℃) ) Θ(kg m 3)
w o rkp iece 38C rM oA lA
2 基本假设
为简化磨削热变形计算, 可作如下基本假设: (1) 磨削热源简化为环状热源沿工件轴向移动, 磨削深度恒定, 输入的热量在丝杠任意一
段上是等量的;
Ξ 收稿日期: 1996 年 8 月 9 日 本研究项目得到高等学校博士学科点专项科研基金资助 © 1995-2004 Tsinghua Tongfang Optical Disc Co., Ltd. All rights reserved.
第 5 卷 第 2 期 1997 年 4 月
光学 精密工程
O PT ICS AND PR EC IS ION EN G IN EER IN G
V o l. 5,N o. 2 A p ril, 1997
精密长丝杠磨削过程中工件热变形的分析Ξ
宋洪涛 宾鸿赞
(华中理工大学机械学院 CAM 室, 武汉 430074)
© 1995-2004 Tsinghua Tongfang Optical Disc Co., Ltd. All rights reserved.
34
光学 精密工程
∃L =
m- 1
∑ ΚLLTϖ0 + Tϖm ) 2
式中, ΚL 为材质的线膨胀系数, L 为圆柱体长度。
对于导热问题的数值求解, 常用的有两种方法: 有限差分法和有限元法。 有限差分法由于 其方法简单、结果可靠等特点而得到了广泛的应用。
本文首先给出丝杠磨削热变形过程的各种基本假设即简化条件, 推导出丝杠磨削过程中 磨削热热源强度的计算公式。 在此基础上, 对丝杠内部的温度场分布进行计算, 进而得到丝杠 的热变形规律。 最后, 通过一个计算实例, 得出一些与丝杠磨削热变形有关的结论。
的面积比表示如下:
Tϖi =
1 4N
2T
i, 0
+
8 4N
2T
i+
1
+
16 4N 2T
i,
2
+
…+
4N - 1 4N 2 T i,N
(15)
令 T ∞ = 0, 则圆柱体相对 T ∞ 温度时在长度上
的总伸长量 ∃L 为:
F ig. 3 M ean2tem p era tu re a t every section
域 网格化方法, 分别以 ( i, j ) 相对 ( r, z ) 来定义周围上的不同单元, 如图 2 所示。从某个时间零
点开始, n
个时间间隔后,
( i,
j)
点 (实质上是整个圆周)
的温度用
T
n i,
j
表示 (上标表示分析的时
刻, 下标 i, j 表示分析点的空间位置) , 则 (10) 式可离散化为:
3 热源强度计算
311 总发热功率 磨削接触区的总发热功率为[ 1 ]:
q=
1 Jq
(F
tf
+
F ts) (V s ± V w ) (ca l s)
(1)
式中, J q 为热功当量, F tf 、F ts 分别为摩擦面与剪切面上的切向磨削力, V s、V w 分别 为砂轮与工
件的线速度。 其中, 逆磨时取“+ ”号, 顺磨时取“- ”号。
可得
T n+ 1 - 1, j
=
T
, n+ 1
1, j
, T n+ 1 m+ 1
j
=
, T n+ 1 m - 1, j
则 (10) 式可离散化为
-
4B
T
n+ 1 i, 1
+
(1 +
4B +
2C ) T
n+ 1 i, 0
-
CT
n+ 1 i+ 1, 0
-
= C T
n+ i-
1 1,
0
T
n i,
0
(14)
摘要 对丝杠磨削过程中磨削热的热源强度进行了分析与计算, 给出了丝杠内部
温度场的计算方法, 对丝杠的热变形规律进行了分析, 通过一个计算实例, 对丝杠磨削 过程中的一些热现象进行了总结。
关键词: 丝杠磨削; 热变形; 热源强度
1 引 言
在精密丝杠磨削, 特别是精密长丝杠磨削中, 由磨削温度变化而引起的误差在丝杠总的加 工误差中占了很大的比例。为提高丝杠的磨削精度, 必须要对丝杠磨削过程中工件的热变形进 行有效的控制。了解丝杠磨削过程中丝杠内部的温度场分布及丝杠的热变形规律, 建立丝杠热 变形规律的数学模型, 进而得到数学模型的数值解, 才能对热变形误差进行有效的补偿。
nw t1 60
=
nw t1h 1f tan 60
Α 2 (mm 3)
(4)
因此, 梯形丝杠磨削时的平均热源强度为:
gθ″w 1 =
Rq = V 01
60R q nw t1h 1f tan
Α (ca l 2
(mm 3
s) )
(5)
式中, h1 为牙形高度, Α为牙形角, f 为径向进给量, nw 为工件转速, t1 为被磨丝杠的螺距。
=
(2rf -
f 2) nw t2co s- 1 D 0 60
d+ 2r
2e (mm 3)
(7)
因此, 滚珠丝杠磨削时的平均热源强度为:
gθ″w 2 =
Rq V 02
=
(2rf -
60R q f 2) nw t2co s- 1 D 0 -
d+ 2r
2e (ca l
(mm 3
s) )
(8)
圆柱体外表面与冷却介质的换热规律可采用第三类边界条件, 即:
k
5T 5r
+
hT =
hT ∞
(11)
© 1995-2004 Tsinghua Tongfang Optical Disc Co., Ltd. All rights reserved.
2期
宋洪涛 等: 精密长丝杠磨削过程中工件热变形的分析 3 3
2期
宋洪涛 等: 精密长丝杠磨削过程中工件热变形的分析 3 1
(2) 将丝杠看作一均质圆柱体, 直径为丝杠中径; (3) 丝杠两端部轴颈部分直径折算成与丝杠中径相同; (4) 丝杠圆周表面各处与外界冷却介质换热系数相同; (5) 丝杠两端部绝热。 基于这些基本假设, 丝杠内部温度场可以当作二维问题处理。
h1
co s
Α 2
f sin
Α 2
=
h1f tan
Α 2
(m
m
2
)
(3)
则单位时间内被切除金属的体积 V 01 为:
© 1995-2004 Tsinghua Tongfang Optical Disc Co., Ltd. All rights reserved.
32
光学 精密工程
5卷
V 01 = A 1
式中, r 为滚道半径, D 0 为丝杠名义直径, d 为丝杠外径, e 为偏心距, t2 为被磨丝杠的螺距。
在理论计算中, 由于磨削力比较难确定, 发热功率 q 也就难以确定, 因而不能直接利用上
述方法来计算热源强度。 这时, 可以通过下面的经验公式来进行计算:
gθ″w = R uG
(9)
式中, uG 为单位时间内切去单位体积金属所消耗的磨削比能, 普通磨削的比能约为 20~ 60J
-
(1 +
1 2j
)B
T
n+ 1 i, j + 1
-
(1 -
1 2j
)B
T
n+ 1 i, j - 1
+
(1 +
2B +
2C ) T
n+ i, j
1
-
C
T
n+ i+
1 1,
j
-
∃ = + C T
n+ i-
1 1,
j
Tn i, j
T n+ 1 i, j
(12)
式中, B
=
Α∃ t
∃ r2, C =
Α∃ t
由
(
12)
、(
13)
、(
14)
式即可列出圆柱体上各点温度
T
n+ i, j
1
(
i
=
0~ m , j =
0~ N ) 所满足的
差分方程, 从而即可求得圆柱体内各点的温度分布。
5 丝杠热伸长计算
现已求出丝杠截面上各离散单元的温度
T
n+ i, j
1,
如图
3
所示,
则各截面上的平均温度
Tϖi
可
用离散单元的温度及各离散单元在截面上所占
滚珠丝杠磨削一般采用如图 1 (b) 所示的双面磨削方式。近似认为砂轮与丝杠接触部分的
截面形状如 A 2 所示, 而 A 2 的面积近似为:
A2=
(2rf -
f 2) co s- 1 D 0 -
d+ 2r
2e (mm 2)
(6)
则单位时间内被切除金属的体积 V 02 为:
V 02 = A 2
nw t2 60
(cm 3· s )。由于丝杠磨削为精加工, 磨削余量一般很小, 发热量不是很大, 因些可以取 uG = 20