KPO精益学习第一期--工厂速读法
CTPM精益管理系列培训-第一期

8、清扫时不合理的发现要领
活用五感:视、触、听、嗅、味+感觉 ☆用手: ①摇一摇 ②敲一敲 ③拧一拧 ④按一按、摁一摁 ⑤刮一刮 ⑥紧一紧、松一松 ⑦掰一掰 ⑧拽一拽 ⑨擦一擦 ⑩理一理 ☆用眼睛 ①确认是否动作; ②确认是否变动、变更; ③确认是否变色; ④确认正常、异常; ⑤确认是否不均衡 ⑥确认是否有疑点 ☆用耳:①发现异常声音; ②发现正常声音; ☆用鼻:发现异味
三要素? 板: (活动板)工具 作用:① 信息交流. ② 情报共享. ③ 自我展示 5
主要内容
第一节、CTPM 1 STEP活动内容 第二节、CTPM 1 STEP看板 第三节、OPL教育 第四节、QC主题活动
6
1、CTPM 1STEP 活动内容
7
自主保全7STEP体系图
7STEP
实现CTPM自主管理
链条
链条是否被拉长(PIN PVSH的磨损),链轮齿的齿轮有没有被磨损,掉落,疵点 链齿与链条间的润滑是否充分,链轮齿的中心相不相称
轴、轴承、联 轴器
是否有松动、缺油而发热、振动的异常声音 固定螺丝是否松动、掉落 联轴器对中是否准确 联轴器橡胶是否磨损或螺丝是否松动 联轴器上是否没有黄油
齿轮
润滑是否适当,是否因多余的油而发生污染? 齿轮是否有磨损、疵点、残屑等? 齿轮是否有异常声音或振动?
M (Management)
管理 优化流程,提升效率,创造效益
2
CTPM思想
思想?
1. 全员参与的小集团活动思想 2. 预防思想 3. “0”化思想
3
CTPM目标
目标?
●灾害“0”化 化
●故障“0”
●不良“0”化
4
●浪费“0”
CTPM三要素
精益(LPTPS)生产管理推行实务

精益(LPTPS)生产管理推行实务
第一部分:精益生产概述 消除浪费的四步骤
第一步: 了解什么是浪费
第四步: 实施持续改进措施,
重复实施上述步骤
第二步: 识别工序中哪里存在浪费
第三步: 使用合适的工具来消除
已识别的特定浪费
精益(LPTPS)生产管理推行实务
第一部分:精益生产概述 传统生产和精益生产方式的区别
• 为了适应后工序的不均衡 • 由于错误的认识提高运转率或追
求表面的生产效率 • 害怕生产线停止 • 作业人员过多 • 生产系统有问题
过量生产的危害
1、问题即待改善点被掩盖起来 2、还会发生新的浪费
1、材料、零件的过早消耗 2、电、气等能源的浪费 3、载货托盘、空箱等的增加 4、搬运工具的增加
1. 人员的增加 2. 在库品存放场地的增加,库存
• 精益概念在非 生产领域及整 个供应链中普 及
精益(LPTPS)生产管理推行实务
第一部分:精益生产概述
精确
精
精密
精深
精致
增益 受益
益
利益
效益
精益(LPTPS)生产管理推行实务
第一部分:精益生产概述
监管
管
人
监督
条理 整理
理
事
精益(LPTPS)生产管理推行实务
第一部分:精益生产概述
“精益LEAN”释义:
传统生产方式
1. 采用推动生产方式 2. 车间布局是按功能区划分; 3. 相同类型的机器摆放在一块; 4. 大批量的生产; 5. 机器适合于大批量生产 ; 6. 工序中间容易堆积库存 ; 7. 未实现作业标准化; 8. 工人一般只会一种操作; 9. 没有或只有个体的作业改善活动
3P精益工厂设计

以安全有效方式 运营
3
3P第一印象-团队
3P印象
团
队
DANTOTSU® = 绝对领先
多元化团队
10
10
3
3P第一印象-创新
3P印象
DANTOTSU® = 绝对领先
创 新
产品、流程或服务的创新
ACTUAL INVENTORY FLOW
SIGNAL
PLATTSBURGH
实施模型
DANTOTSU® = 绝对领先
08 - Standard Work, 标准作业 BEST ONE,最优方案
DANTOTSU® = 绝对领先
一小时学习精益工厂3P设计
杨凯
精益战略顾问
1
课程学习地图
DANTOTSU® = 绝对领先
思想 要素
0
学习前提
1
3P含义
核心思想
2
内容模块
3
3P目标
3P印象方法6Fra bibliotek3P总结5
3P原则
4
3P方法
系统
7
流动设计
8
管理系统
9
实施模型
2
0
3P精益设计是高级课程需要大量精益基本知D识ANTOTSU® = 绝对领先
新产品 导入
产量剧烈变化 生产地点变化 批准新的项目投资 由批量生产转变为 单件流动生产
18
6 3P精益设计的目标平衡
3P总结
我们需要同时做好三件事情!
Reduce Lead Time 减少提前期
Improve Quality 提高质量
DANTOTSU® = 绝对领先
Reduce Cost 降低成本
精益PPT课件
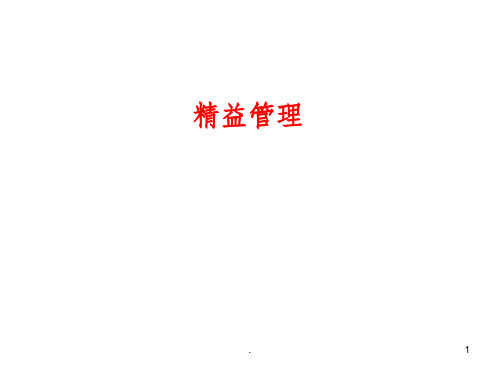
过多的、不同部门的人员签字和批准
打印了多余的报告、报告没有响应等 采购了过多的办公用具,仓库中堆积 如山
.
8
八大浪费
.
9
KAIZEN 及进行要点
人,
名词:KAIZEN (改善) --日语,即中文“改善”。“改”即改变,“善”即变的更好; --在精益管理活动中,“KAIZEN改善”表示持续改善,即每一天, 每一
1)检查集数据:检查表,又称点检表,分为点检用和记录用; 2)柏拉抓重点:柏拉图,又称帕累托图或排列图或20/80法则,即通过排列
20%的问题点就能解决
的形式来展示各个问题的名称和占比,只要改善
80%的问题。
柏
拉
检
图
查
表
.
ቤተ መጻሕፍቲ ባይዱ
18
QC 7大手法
工具2:QC7大手法2 3)鱼骨追原因:鱼骨图,又称因果图、特性要因图或石川磬图。为日本人
丰田的精益房子
.
13
带级与常用名词解释
名词:带级 --为了区分精益项目的难易程度和项目推进人员的工具应用程度,精益管 理体
系借鉴了韩国跆拳道的带级制度: 精益蓝带:入门级新人;初步了解精益管理,能支持项目团队的工作; 精益黄带:小师弟;掌握了精益管理的基础工具,能开展小的改善项目; 精益绿带:大师兄;精益管理项目改善主力,能独立带领改善团队; 精益黑带:师傅;能培训绿带人员,能独立带领改善团队攻坚克难; 精益黑带大师:指导黑带、绿带项目,培养带级人员; 精益倡导者:又称冠军、明星。负责制定精益管理的
2)改变传统观念;
.
10
精益生产培训教材(PPT 70页)
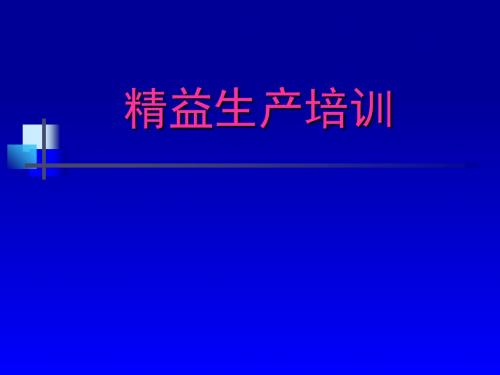
第三部分:精益生产之方式要求 3.2 单件流
第三部分:精益生产之方式要求 3.3 拉动式
何谓“拉动式生产”? 生产活动是由“客户”需求决定的,在进行生产
时,每一个生产过程都是由下一个生产过程的需求决 定,从而不生产额外的产品,这样就可以消除因生产 过剩产生的多余库存了。 为何需要“拉动式生产”? —没有需求的生产是没有意义的; —拉动使生产有了方向性; —通过一级一级的拉动可以使流程有序平稳地进行, 避免了浪费。
以顾客为导向的效率:
提高产量的做法:
改善
400pcs/4人·8hr
600pcs/5人·8hr
做客户需求的产量:
改善
400pcs/4人·8hr
360pcs/3人·8hr
以最少的人员,做出市场实际需求量的产品才是以顾 客为导向的真正的效率提升。
一、精益管理的诞生
课程内容
精益与其说是一种生产方式,更确切
Time ”,简称“JIT”。
“JIT”的概念
JIT是英文“Just In Time”的缩写,翻译成中 文为准时(及时)生产,即通常所讲的使生产做到 “在需要的时候,按需要数量生产所需要的产品”。
其主要目的是使生产过程不要处于盲目状态,而 是建立一种均匀、稳定的、有节奏的生产线。
丰田公司通过多年不断改善,建立了JIT的生产模 式:
一项很细小专一的工作 大批量:每分钟一辆,每天7000辆 价格低:像自来水一样便宜
1.3 精益生产方式
追求零浪费!!
只在适当的时
间里生产市场需 精 要的必要数量的 益
产品
所有的经营活动 都要有效益和 最大的经济性
精益生产的特点:
消除一切浪费,追求精益求精和不断改善。精 简并消除一切不增值的岗位。精简产品开发设 计,生产,管理中一切不产生附加值的工作, 以最优品质,最低成本和最高效率对市场需求 作出最迅速的响应。
精益生产理论学习总结

精益生产理论学习总结精益生产理论学习总结精益生产理论学习总结ANPS作者:川北小哥来源:blog时间:202*-02-09ANPS代表先进(A),新(N),生产(P),技术(S)。
1.何为ANPS?ANPS代表:Advanced(先进)New(新)Production(生产)Skills(技术).它是整合近代所有生产技术及管理的整合运用,其目的在协助企业赚取更多利润的改善策略。
它融合了下列的主要观念及技法:(1)SixSigma六个西格码(2)LeanProduction精益生产(3)ToyotaProductionSystem丰田生产方式(4)JustInTime及时生产(5)TotalQualityManagement(TQM)全员品质管理(6)TotalProductiveMaintenance(TPM)全员生产保全(7)SupplyChainManagement供应链管理(8)QualityControlCircle(QCC)品管圈活动2.ANPS先进新生产技术它包含了“心”、“技”、“体”三大内涵的完整改善体系。
“心”"是指思想,观念的部份,ANPS与传统生产观念思想有完全不同的认识。
“技”"是指技法,手法的意思。
虽然有了思想观念,但若不知道有什么方法才能实现些思想观念。
那么,这些思想观念也只能像空中楼阁幻存在,一点用处都有。
ANPS为实现前面的"心",即思想观念,也特提供了相关的改善技法,分为"四大招式":(1)第一招:流线化生产以建立"一贯化、一个流、同步化"的产品胞式(CellProduction)的流线生产线为目标。
透过流线生产,可以快速短生产交期,少在制品库存,提高劳动生产力,降低不良率,节省空间等诸多好处,可以说是"ANPS-Lean6Sigma"改善活动的切入点。
(2)第二招:安定化生产追求使生产线能定生产,又包含如下六个子技法:a.6Sigma六标准差:借用统计手法及寻找真因七手法及防错机制的(FoolProof)来追求零ppm不良的品质保护,满足顾客之要求。
【精益学堂】POKAYOKE(一)

【精益学堂】POKAYOKE(一)精弘益导读:学习POKA YOKE 前先来看看下面的两个改善案例:(1)一个世界500强的日用品生产商,在制造香皂的生产线上发现会有没有香皂的空盒子从流水线上流入包装箱,造成客户投诉,于是工厂立即为此成立一个team来解决这个问题,通过一系列分析并请来专业人员对流水线进行改造,在最后一段流水线增加了一个称重装置,并能自动将重量超出设定公差的包装盒剥离流水线,经过一段时间的监视使用,最后成功关闭了该问题,并做了Success story在整个集团中分享。
(2)同时另一个做肥皂的乡镇企业也发生了同样的问题,空包装盒流入包装箱,私人老板立马命令生产线班长解决此问题。
那位班长在生产线转了半天后,找来一台电扇,调整了一下距离流水线的距离,风扇的风正好可以将空盒子吹下来,班长满意的走了。
防错法概述防错法日文称POKA-YOKE,又称愚巧法、防呆法。
意即在过程失误发生之前即加以防止。
是一种在作业过程中采用自动作用、报警、标识、分类等手段,使作业人员不特别注意也不会失误的方法。
一、防错法的作用在作业过程中,作业者不时会因疏漏或遗忘而发生作业失误,由此所致的质量缺陷所占的比例很大,如果能够用防错法防止此类失误的发生,则质量水平和作业效率必会大幅提高。
1、防错法意味着“第一次把事情做好。
因为防错法采用一系列方法和或工具防止失误的发生,某结果即为第一次即将事情做好。
2、提升产品质量,减少由于检查而导致的浪费防错法意味着“第一次即把事情做好”,直接结果就是产品质量的提高,与靠检查来保证质量相比,防错法是从预防角度出发所采取的预防措施。
而检查不能防止缺陷的产生,检查发现的缺陷只能去纠正。
这是一种浪费,防错法消除了这种浪费。
3、消除返工及其引起的浪费:防错法会提升产品质量,消除缺陷,这会导致返工次数的削减,由于返工所致的时间和资源浪费便得以消除。
二、失误与缺陷失误是由于作业者疏忽等原因造成的。
工厂速读法简要介绍

工厂速读法简要介绍工厂速读法(Factory Rapid Reading Method)是一种高效的阅读方法,旨在提高阅读速度和阅读理解能力。
该方法主要通过训练读者的眼球在页面上快速移动,以获取更多的信息,并通过一系列练习来提高阅读的效率。
工厂速读法起源于美国,最早是由一位名叫Evelyn Wood的教育家提出的。
她研究发现,眼球的自然移动速度比大多数人的阅读速度要快得多。
基于这一发现,她创造了一系列练习和技巧,帮助人们提高阅读速度和理解能力。
工厂速读法的核心思想是“一眼一词”。
即在阅读过程中,眼球每次应该扫过页面上的一组词语,而不是逐个阅读单词。
这样可以大大提高阅读速度,并通过大量快速获取信息来提高理解能力。
通过练习,人们可以逐渐提高眼球的移动速度,从而达到更高的阅读速度和更好的理解能力。
在进行工厂速读法练习时,需要注意以下几点:1. 创造良好的阅读环境。
选择一个安静、舒适的地方进行阅读,尽量避免干扰和噪音。
2. 定下目标和计划。
在开始阅读前,明确自己的阅读目标,并设置合理的时间和进度计划。
3. 采用正确的姿势。
采用正确的姿势可以帮助提高阅读效率。
身体放松,保持良好的坐姿或站姿。
4. 加强眼球训练。
通过一些特定的练习来加强眼球移动的速度和准确性,如追踪练习、跳跃练习等。
5. 提高词汇量。
词汇量是理解和阅读的基础。
通过广泛阅读和词汇训练来提高自己的词汇量。
6. 关注阅读目标。
在快速阅读过程中,要时刻关注阅读的目标,不要被细节和琐碎的信息分散注意力。
7. 练习阅读理解。
快速阅读不仅仅是提高阅读速度,更重要的是提高合理的理解能力。
通过练习阅读理解题来锻炼自己的理解能力。
工厂速读法是一种高效的阅读方法,它可以帮助人们快速获取信息,并提高阅读理解能力。
通过一系列练习和技巧,人们可以提高眼球的移动速度,从而达到更高的阅读速度和更好的理解能力。
但需要注意的是,虽然工厂速读法可以提高阅读速度,但并不意味着可以忽略理解和思考的重要性。
精益生产培训系列课件

18
IE七大手法
丰田生产模式TPS学习
动作改善原则:有关人体运用的原则 1﹑双手并用原则:两手同时开始及完成动作
❖ 用一只手:插完30只销子需30S
❖ 用双手:插完30只销子只需23S,节约时间29%
19
IE七大手法
丰田生产模式TPS学习
动作改善原则:有关人体运用的原则
2﹑除休息时间外,两手不应同时空闲: 不必要的动作会浪费操作时间,使动作效率下降,必须
4、使动作轻松: 如,汽车装配时车轮由自动提升设备,自动提升到与车轴高 度,操作人员只需要用开关进行控制就可以了
15
IE七大手法
丰田生产模式TPS学习
动作经济的四个基本原理:
4、使动作轻松: 如,操作人员的装配零部件时必须将零部件转向,但零部件 过大、过重时,可使用带转向的工装台。
16
IE七大手法
10
IE七大手法
丰田生产模式TPS学习
动作经济的四个基本原理:
2、同时进行动作: 不管是工具的改善,方法的改善或零件摆放方法改善等,
想办法使两手能同时使用,或脚也能同时使用。 例, 打麻将动两手;开汽车;打鼓、弹钢琴;两手同时拿取 2个部件;两手同时上两个螺丝; 在制品槽移动时拿取配件;走动 中按开关等。
排除。而即使必要的动作,通过改变动作的顺序、重整操作 环境等也可以减少。
20
IE七大手法
丰田生产模式TPS学习
动作改善原则:有关人体运用的原则
3﹑对称反向原则:两只手臂的动作应反向同时对称 大多数人均惯一手拿着东西另一手去工作,这是动作浪
费。应当使双手用对称方式一起工作,同时开始和结束。工 作要适当地分布在双手的工作区域,使双手能同时发挥。
单手操作容易使人体产生心理上及生理上不平衡感,为 克服此种不平衡就必须用身体的应力去反制,因而使我们容 易身心疲劳。对称的动作方式,使操作者的身体部位产生平 衡感,而减少了身体运用应力的机会,使工作者较轻松愉快 而不容易疲劳。
工厂速读法

工厂速读法附件一评估小组构成与培训工厂快速评估小组人数不多,通常由4~5人构成,其中一人担任组长。
具备被评估行业的设备知识者为恰当人选,具备生产经验者则最为理想;但是,不管如何,整个小组应具备不一致类型、不一致层次的经验。
我曾派过好几个小组参观同一家工厂,尽管他们的经验组合各不相同,但是,其评分结果与提出的改进建议却惊人地一致。
小构成员通常需经1-3天的培训来掌握“工厂速评法”解读工厂,培训时间长短则取决于他们对精益生产的熟悉程度。
初次精益生产培训后,学员最好先在自己的工厂内试用此法。
另外,试用与正式使用此法后形成的报告也可成为公司记录的重要补充,为改善绩效提供基准,为未来培训提供素材。
正式参观工厂前,小组应先熟悉具体行业的特征,这非常重要,由于在某些行业被认为是过高的库存与冗赘的做法,到了另外一些行业则可能避免不了。
比如,医药行业的公司为满足法规对纯净度的要求,会加设一定程度的监控,而关于日用品企业这往往是多余的。
还有,餐馆与发电厂库存往往会较高,产能往往也会部分闲置,这种状况其他行业却常常不能同意。
通盘考虑过这些操作层面与法规层面的要求后,小组评估将会更加准确。
附件二工厂快速评分表假如工厂希望得分逐年提高,那么最好每年都评估打分;同时,我们建议评估结果最好在各工厂间共享;另外,锐意改进的工厂管理者应首先从得分最低的方面着手。
精益评估工厂:参观时间:评分人:11个分类总得分(最高分=121分)附件三工厂速评问卷本问卷中的“是”的数量标志着工厂的精益程度:“是”的数量越多,则工厂的精益程度越高。
只有当工厂明显遵循了该问题隐含的原则时,才能回答“是”。
如有任何疑问,则回答“否”。
1 参观者是否受到欢迎,并得到有关工厂布局、员工、客户与产品等方面的信息?2 客户满意度与产品质量方面的得分是否具有张榜公布?3 设施是否安全、清洁、有序,同时光线充足?空气质量是否好?噪音是否低?4 直观标志系统是否明确指示库存、工具、流程与物流方向?5 所有东西是否都各有所位,同时各就其位?6 最新的营运目标与相应的绩效评估标准是否具有醒目地张榜公布?7 生产物料是否沿生产线放置,而不是在几个库存区分隔储藏?8 工作区是否能够看见工作指令与产品质量规格?9 所有小组是否都能看到有关产出、质量、安全与“攻关”成果的最新图表?10 营运现状是否能够通过中央操纵室、进度板或者电脑屏幕一目了然?11 生产线安排是否按照一个统一的“进展程序”?每一工段的库存水平是否恰当?12 物料是否只需移动一次,移动的距离是否最短?移动时物料是否具有置于恰当的运输箱中以提高移动效率?13 工厂布局是否保证产品流淌持续顺畅,而不是一个个车间块状分隔?14 工作小组是否受过培训、得到授权、并参与“攻关”与日常工作改进?15 员工是否致力于持续改进?16 预防性设备保养及日常工具流程改进的具体时间有否张榜公布?17 启动新产品时,是否制定了有效的项目管理流程与具体的成本、时间目标?18 供应商认证程序(包含质量、交货与成本衡量标准)有否张榜公布?19 产品关键性能是否明确?是否使用了自动故障防护措施防止瑕疵蔓延?20 你是否会购买该工厂的产品?“是”的总数附件四工厂速评数据库自1998年以来,我与我的学生在对不一致生产与服务行业的150多个运营单位(范围从汽车零部件供应商、航天器材公司到书籍出版商、电影制片厂、汽车经销商与小型啤酒酿造厂)的400多次参观中使用了“工厂速评法”。
精益生产培训
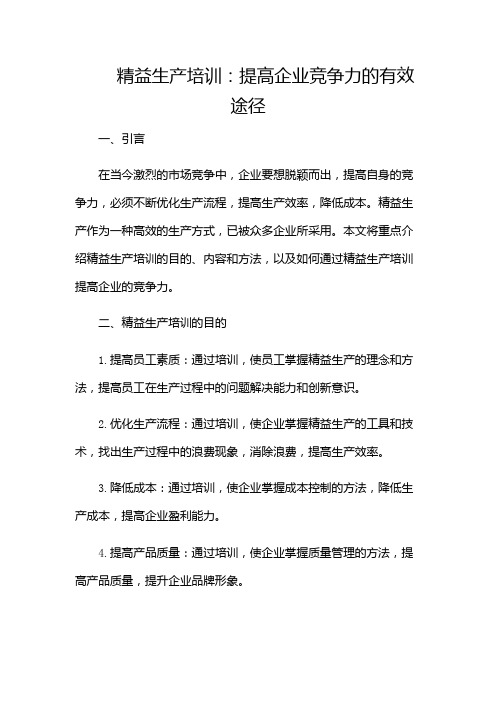
精益生产培训:提高企业竞争力的有效途径一、引言在当今激烈的市场竞争中,企业要想脱颖而出,提高自身的竞争力,必须不断优化生产流程,提高生产效率,降低成本。
精益生产作为一种高效的生产方式,已被众多企业所采用。
本文将重点介绍精益生产培训的目的、内容和方法,以及如何通过精益生产培训提高企业的竞争力。
二、精益生产培训的目的1.提高员工素质:通过培训,使员工掌握精益生产的理念和方法,提高员工在生产过程中的问题解决能力和创新意识。
2.优化生产流程:通过培训,使企业掌握精益生产的工具和技术,找出生产过程中的浪费现象,消除浪费,提高生产效率。
3.降低成本:通过培训,使企业掌握成本控制的方法,降低生产成本,提高企业盈利能力。
4.提高产品质量:通过培训,使企业掌握质量管理的方法,提高产品质量,提升企业品牌形象。
5.提高企业竞争力:通过培训,使企业掌握精益生产的系统方法,提高企业在市场中的竞争力。
三、精益生产培训的内容1.精益生产理念:培训员工了解精益生产的起源、核心理念和基本原则,使员工认识到精益生产对企业发展的重要性。
2.精益生产方法:培训员工掌握5S、TPM、看板管理、价值流分析等精益生产工具和方法,提高员工在生产过程中的问题解决能力。
3.流程优化:培训员工掌握流程优化的方法,找出生产过程中的瓶颈和浪费现象,制定改进措施,提高生产效率。
4.成本控制:培训员工掌握成本控制的方法,降低生产成本,提高企业盈利能力。
5.质量管理:培训员工掌握质量管理的方法,提高产品质量,提升企业品牌形象。
6.精益生产实施策略:培训员工掌握精益生产实施的步骤和策略,确保精益生产在企业内部的顺利推进。
四、精益生产培训的方法1.理论培训:通过课堂讲解、案例分析、小组讨论等形式,使员工掌握精益生产的理念和方法。
2.情景模拟:设置实际生产场景,让员工在实际操作中体会精益生产的方法,提高员工的问题解决能力。
3.在职培训:结合员工的工作岗位,进行针对性培训,使员工能够将所学知识运用到实际工作中。
「1精益师基础知识」

精益师基础知识问答【基础知识与理念】1.TPS是指什么?TPS是指丰田生产方式(是Toyota ProductionSystem 的简称),T代表丰田、P代表生产、S 代表方式。
2.TPS的创立有赖于三位杰出的人物,他们是谁?丰田佐吉(自働化思想的提出者)、丰田喜一郎(准时化的提出者)和大野耐一(TPS的实践者)。
3.TPS的基本思想是什么?通过改善活动彻底消除隐藏在企业里的种种浪费现象。
4.TPS的最终目的(宗旨)是什么?降低成本,提高效益。
5、TPS的精神是什么?①纪律:个人服从组织,少数服从多数,下级服从上级和自我约束;②决心:坚定不移的意志,持之以恒的决心,玩命疯狂的态度;③改善:拿出智慧,对公司的所有领域进行持续不断地改进;④创造力:要摒弃传统观念,跳出思维僵局,发现和创造新事物,取得新成果;⑤执行力:把企业战略、规划转化成为效益、成果,按时按质按量完成自己的工作任务。
6.TPS的两大支柱是什么?准时化(JIT)和自働化(带人字旁的自动化),准时化是方法,自働化是工具。
7.丰田生产方式追求什么?追求:高品质,低成本,短前置期和灵活弹性。
17.实现“准时化生产”的方式有哪些?看板方式、后工序取用方式、单个流动方式、平准化生产。
7.TPS中所说的生产现场7种浪费是指哪7种浪费?生产过剩的浪费、库存的浪费、等待的浪费、搬运的浪费、加工的浪费、动作的浪费、不良品的浪费;其中生产过剩的浪费是最大的浪费,库存的浪费是万恶之源。
8.精益制造追求的终极目标是什么?零库存、零切换、零浪费、零不良、零故障、零停滞、零事故。
9.现场监察的观察点有哪些?①瓶颈作业②堆积③材料流动④等待⑤步行⑥身体的动作⑦手的动作⑧眼睛的动作。
10.精益生产中所说的顾客包括什么?内部顾客和外部顾客。
11.改善的目标是什么?工作轻松、质量变好、速度加快、成本降低。
12.戴明环(PDCA循环)是什么?戴明环又叫PDCA循环(P—plan,计划;D--do,执行,实施;C--check,检查;A- act,处理)。
精益生产知识--培训课程

Flow:使产品顺畅地流动起来;
Pull:让客户拉动; Perfection:通过持续管理达到完美。
始终坚持以上五个原则,
避免仅仅关注到孤立的
技术上。
价值与价值流程图——现状的价值流程图(光网络)
2004.12.06 PM 16:30 2E27R
Supplier Forecast 3 months) Weekly PO
大规模定制
• High variety • Small volume per product • Near perfect quality • Engaged workforce 1975 2000
1875
1900
1925
1950
精益生产的历史与含义
精益思想的五个基本原则:
没有任何事 情是完美的 持续改进 Perfect 完美 站在客户的立 场上思考价值 Value 价值 从订单到发货 过程一切有价 值的活动 Value stream 价值流
精益生产的历史与含义
精益生产:Lean Manufacturing or Lean Production
Lean Means “Manufacturing without waste”. 浪费(日语叫Muda)有很多种形式,如多余的材料、等待时间、闲 置的设备、库存等。
大部分公司浪费了70%~90%的可用资源,即使是业界最Lean的企业 也有30%的浪费。
I
50 pcs
1
1
I
50 pcs
1 C/T = 4 days C/O = 0 1 shift=8 hs 1 shifts
C/T = 1.5 mins C/O = 3 mins 1 shift=8 hs 2 shifts Uptime=65% ? days ? days 1.5 minutes
精益生产--用于要求多的KPO培训
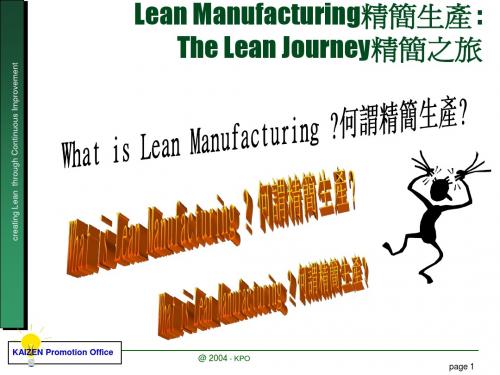
PRATT & WHITNEY AS AN EXAMPLE 以PRATT & WHITNEY公司 為實例:
SMALL PRODUCT TEAM (<30) MOVING FIRST DESIGN FROM CONCEPT TO LAUNCH IN NINE MONTHS小形的生產 小組(<30),在9個月時間內完成從概念設計到生產的過程.
Taiichi Ohno
Shigeo Shingo
KAIZEN Promotion Office
@ 2004 - KPO page 8
Lean Manufacturing精簡生產
creating Lean through Continuous Improvement
Lean is 精簡是:
Mindset of continuous improvement.持續性改善的觀念
Breaking the Circle of Doom打破厄運圖
4 Steps to break the circle of doom打破
厄運圖的4個步驟:
Integrity正直
Enthusiasm and Commitment積極/有責任感
Action行動 Understanding
the customer fully and clearly充
A Time based Strategy時間為基礎的策略
Time時間
Product Pre-Plan計劃 Development開發
Manufacturing生產
Accounts Distribution銷售 Receivable結算
工厂速评法

工厂速读法尤金.古德森(R.Eugene Goodson)20世纪80年代初,我负责胡佛环球公司(Hoover Universal)的汽车座椅业务,后来江森自控(Johnson Controls)收购了该公司。
当时,有家为丰田汽车(Toyota)供应零部件的日本同行,要求派员参观我们工厂。
我们认为从简短的参观中他们不可能了解到什么,就答应了他们;不过附了个条件,就是回访他们的工厂。
来访者在我们最好的工厂呆了不到一个小时,也没做任何记录。
但当我们最后看到他们的参观报告时,却不由大吃一惊。
他们对我们工厂和技术的描述细致入微,甚至对我们销售成本的估算也不失毫厘。
而与此同时,我们的高级管理人员也参观了他们在日本的工厂,却近乎空手而归。
痛定思痛,我决心让我们的管理人员(包括我自己)练就火眼金睛,在参观工厂时,能像日本同行那样明辨其优势和劣势。
“十年磨一剑”,终于,我打造出了速读工厂的利器――“工厂速评法”(RPA,Rapid Plant Assessment)。
自1998年以来,此法在对150多家工厂的400多次参观中行到了应用。
它提供的信息影响了从基准比较、竞争对手分析一直到战略收购等一系列的活动和决策。
更重要的是,应用此法后,参观结果不出一天即可得出;而绝大多数评估系统却往往要费尽周折、耗时数周。
举个例子来看看此法威力究竟有多大。
在我担任奥什科什卡车公司(Oshkosh Truck)首席执行官时,我们参与了一次竞争异常激烈的拍卖,标的是一家领先的美国消防车生产商――皮尔斯制造公司(Pierce Manufacturing)。
该公司的管理人员对由奥什科什最终收购他们心存芥蒂,因此公允许我们对其属下的三家工厂各进行限时30分钟的参观,而参观的时间间隔只有数小时。
但是,就是在这样的走马观花中,我们充分掌握了他们工厂运作的信息,这些信息足以使我们确信:通过消除物料处理方面的瓶颈、整合工厂、降低库存以及改油漆车间三班制为一班制等办法,我们每年能够削减几百万美元的成本。
精益生产第一期培训(2)
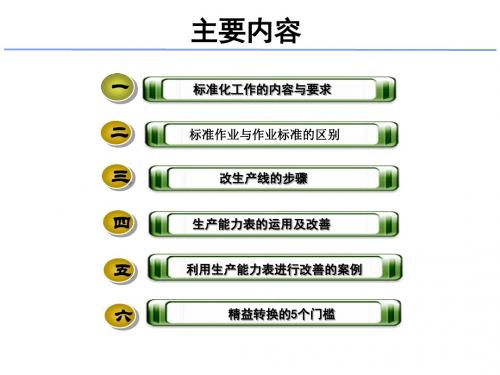
OEE – 设备综合利用率
可动率 性能开动率 合格品率
OEE损失时间
停机时间损失 速度损失 质量损失
1 故障 2 更换
3 空转和小停机 4 降低速度
5 废料和重新加工 6 开车损失
1/3
如何提高生产线平衡率? 平衡改善法则
名称
说明
取消 合并 重排 简化
对于不合理、多余的动作或工序给予取消
对于无法取消又是必要的,看是否可以合并 以达到省时、简化的目的
3
类型Ⅰ调查作业时间举例
主要内容
四
员工负荷表的运用及改善
什么是木桶定律?
一个木桶盛水多少,并不取决于桶 壁上最高的那块木板,而恰恰取决 于桶壁上最短的那块木板,这一规 律我们称之为“木桶定律”。
1
什么是生产线平衡
生产线平衡是指构成生产线各道工序所需的 时间处于平衡状态,作业人员的作业时间尽 可能的保持一致,从而消除各道工序间的各 种等待的浪费,进而取得生产线平衡,达到 生产效率的最大化。
主要内容
一
标准化工作的内容与要求
二
标准作业与作业标准的区别
三
改生产线的步骤
四
生产能力表的运用及改善
五
利用生产能力表进行改善的案例
六
精益转换的5个门槛
主要内容
一
标准化工作的内容与要求
1
标准作业三要素
标准作业是企业认可的,能够 安全、保证质量、很少浪费、 合理成本、以人的动作为中心, 应该严格遵守的作业方法。
分担转移
作 业 时 间
工序 1 2 3 4 5
合并重排
作 业 时 间
工序 1 2 3 4 5
减人(分解消除)
作 业 时 间
- 1、下载文档前请自行甄别文档内容的完整性,平台不提供额外的编辑、内容补充、找答案等附加服务。
- 2、"仅部分预览"的文档,不可在线预览部分如存在完整性等问题,可反馈申请退款(可完整预览的文档不适用该条件!)。
- 3、如文档侵犯您的权益,请联系客服反馈,我们会尽快为您处理(人工客服工作时间:9:00-18:30)。
上海飞奥燃气设备有限公司Shanghai Fiorentini Gas Equipment Ltd,. Co.精益学习(2010)第一期工厂速读法尤金.古德森(R.Eugene Goodson)只要短短30分钟,你就能对一家工厂了如指掌20世纪80年代初,我负责胡佛环球公司(Hoover Universal)的汽车座椅业务,后来江森自控(Johnson Controls)收购了该公司。
当时,有家为丰田汽车(Toyota)供应零部件的日本同行,要求派员参观我们工厂。
我们认为从简短的参观中他们不可能了解到什么,就答应了他们;不过附了个条件,就是回访他们的工厂。
来访者在我们最好的工厂呆了不到一个小时,也没做任何记录。
但当我们最后看到他们的参观报告时,却不由大吃一惊。
他们对我们工厂和技术的描述细致入微,甚至对我们销售成本的估算也不失毫厘。
而与此同时,我们的高级管理人员也参观了他们在日本的工厂,却近乎空手而归。
痛定思痛,我决心让我们的管量人员(包括我自己)练就火眼金睛,在参观工厂时,能像日本同行那样明辨其优势和劣势。
“十年磨一剑”,终于,我打造出了速读工厂的利器――“工厂速评法”(RPA,Rapid Plant Assessment)。
自1998年以来,此法在对150多家工厂的400多次参观中行到了应用。
它提供的信息影响了从基准比较、竞争对手分析一直到战略收购等一系列的活动和决策。
更重要的是,应用此法后,参观结果不出一天即可得出;而绝大多数评估系统却往往要费尽周折、耗时数周。
举个例子来看看此法威力究竟有多大。
在我担任奥什科什卡车公司(Oshkosh Truck)首席执行官时,我们参与了一次竞争异常激烈的拍卖,标的是一家领先的美国消防车生产商――皮尔斯制造公司(Pierce Manufacturing)。
该公司的管理人员对由奥什科什最终收购他们心存芥蒂,因此公允许我们对其属下的三家工厂各进行限时30分钟的参观,而参观的时间间隔只有数小时。
但是,就是在这样的走马观花中,我们充分掌握了他们工厂运作的信息,这些信息足以使我们确信:通过消除物料处理方面的瓶颈、整合工厂、降低库存以及改油漆车间三班制为一班制等办法,我们每年能够削减几百万美元的成本。
由此,我们开出的价格比该公司财务数据所能显示的价值更高,最终赢得了竞拍。
当然,“工厂速评法”并不能代替收购时应做的审慎调查;同样,在选择供应商时,除此法涉及的那些因素之外,应该考虑的因素还有很多。
但是,管理者往往对直观信息熟视无睹,对数字情有独钟。
结果,他们就可能挂一漏万,忽略一些关键线索,不能真正了解到对方的优势和劣势。
由此导致的结果,要么是坐失良机,要么是“交友不慎”:――合作关系初看起来“柳暗花明”,不久却发现已身陷“山重水复”。
此外,“工厂速评法”也可用于自我评估,从而揭示自己的工厂向参观者传递了哪些信息,并且以掘改进的机会。
我知道现在就有一些公司在向精益生产转变(leantransformation)的过程中使用着“工厂速评法”,其中有唐纳利电子公司(Donnelly Electronics)、伊顿公司(Eaton Corporation)属下的航空设备集团(Aeroquip Group)、洛克希德.马丁公司(Lockheed Martin)属下的哈沃斯公司(Haworth)的办公家具厂以及希捷科技公司(Seagate Technology)。
下面我将详细介绍这种方法,并提供两张表格以帮助对参观结果进行整理分析。
工厂评估工具“工厂速评法”的核心是给工厂参观小组提供两个评估工具――“工厂快速评分表”和“工厂速评问卷”。
前者采用了11个分类来评估工厂的精益程度,后者则包括了20个相关的是非题,来确定工厂在这11个分类中是否采用了最佳方法。
参观结束后,小组成员需要将自己观察的结果填入两张表格(表格形式参见副栏“精益评估”)。
事实上,还有许多可量化因素能够用来评估工厂在“工厂快速评分表”中11个分类上的表现。
读者如果需要详细了解这些因素,可以访问网站,网址为/rpa。
在该网站上,还可以找到副栏“估算销售成本”中提到的其他一些高级评估工具。
参观时,小组成员应该仔细观察工厂环境的方方面面,要与操作人员和管理人员交谈,并要寻找该工厂坚持采用最佳方法的证据。
另外,在参观时千万不要记笔记,否则注意力会分散,原本可以发现的线索会错漏,与现场员工的交流也会受到影响。
正确的做法是:每个小组成员应负责几个分类,参观结束后所有成员应迅速集合,交流各自的观感,并完成表格的填写。
我们还建议,所有成员都应回答最后一个问题,即“你是否会购买该工厂的产品?”(有关参观小组人员构成及参观前准备工作的讨论,参见副栏“评估小组构成与培训”)下面,我们逐一看看每个分类。
第1类客户满意最佳工厂的工人一定知道谁是他们的客户(包括内部客户和外部客户),并把客户满意作为自己的首要目标。
除此之外,他们还明白,让来访者体验与众不同的经历,让他们离去时仍啧啧称道,正是自己的责任。
工厂对客户究竟是倾心关怀,还是麻木不仁,通过短短一次参观就能泾渭立见。
在客户至上的工厂里,你会受到热烈欢迎,会有人热情为你介绍工厂布局、员工、客户和产品情况;质量与客户满意度的评分结果也会醒目地公布出来。
如果你问某个员工“你手头的产品接下来流向哪儿?”,而回答是“福特”或“6号线的约翰”,那么,在此评估指标上,给这家工厂的打分就可以高;如果回答是“我把它放进这个桶里,接下来怎么样我不清楚”,那么,打分就应该低。
(“工厂速评问卷”中问题1、2和20与这一评估指标相关)第2类安全、环境、整洁与秩序整洁有序的工厂里,零部件易于找到,库存易于清点估算,并且产品转移动也是安全和高效的。
这样的工厂光线充足,空气质量好,噪音低。
库存、工具和流程都有直观的标志系统清楚标明。
一家工厂在这些方面究竟做得有多好,只需略作浏览便可一目了然。
所有零部件都应受到同等重视。
许多公司殚精竭虑将贵重部件安排得井井有条,对标签、紧固件等低值部件却常常掉以轻心。
这种习惯有时代价非常高昂。
事实上,江森自控公司生产汽车座椅时,我们从未遗失过一张靠背或一块坐垫,可是,将倾斜装置与靠背坐垫连接起来的螺栓却经常遗漏缺失。
我们不可能交付给客户缺少螺栓的座椅(即使交付了,也收不到货款),因此,小小一颗螺栓,其价值其实与贵重部件难分伯仲。
(参见“工厂快速评估问卷”中问题3-5和20)第3类直观管理系统提供直观线索、明确指示方向的视觉工具在运行良好的工厂随处可见。
这些标志为员工清楚指明了位置和任务,极大提高了生产效率。
参观时,应注意寻找各种工作安排工具,如生产计划“看板”(kanban)、分色标志的生产线或工段、醒目张贴的工作要求、质量产出图表以及维修记录。
反映工厂良好的直观管理的其他标志还包括:公布小组成员名单、生产改进措施以及休假计划等信息的布告栏,可以通览当前总体运作情况的中央控制室或整体进度板等。
通常,化工及其他加工行业的工厂直观管理程度相当高,但并非各种标志层出不穷、杂乱无章;即便是一些规模最大的工厂也倾向于将产品流动、工厂布局和其他重要信息一并集中显示。
(参见问卷中问题2、4、6-10和20)以下三个分类相互关联,根据显而易见直观线索就能对一家工厂在这三方面的表现迅速打分。
第4类生产计划系统最佳工厂依靠一个统一的“定速程序“(pacing process)来管理各条生产线及其供应商。
该程序常常位于生产线尾端,它控制着所有上游活动的速度和产量,很像领跑车在赛道上设定并控制着所有赛车的速度。
每道工序的生产要求都由下道工序的生产要求决定。
这就有效地控制了库存,提高了质量,缩短了停工时间,因为生产线再也不停工待料了。
相比之下,在使用中央生产计划系统的工厂中,则会在流程的某个点上出现过多呀过少生产某些部件的情况。
这是因为给每条生产线发布指令的是中央电脑,而不是实际使用该部件的生产线。
在参观前苏联的一家拖拉机厂时,我目睹了极端中央生产计划固有的许多兢兢业业生产着拖拉机,但是引擎厂交付的引擎数量一直不足,最后,他们只好将那些没有“心脏” 的拖拉机拖出,停到了露天。
我数了一下,那些了无生气的拖拉机足足相当于6个月的产量,它们都在露天悄无声息,翘首以待最后的、也是最最重要的部件。
通过询问工厂或者观察库存水平,可以知道一家工厂是如何实施生产计划的。
如果库存在某个工段出现了积压,那么,各生产计划系统极有可能是“各扫自家门前雪”;或者,整个流程“流速”不当。
同样,如果生产计划是由中央制造物料规划系统(central MRP system)做出的,生产线上则随处可见电脑屏幕或堆积如山的工作任务单。
此外,还应留意同一生产线操作人员之间的视觉交流与语言交流。
他们之间的距离应该近到可以随时交谈,并能看到对方的库存。
操作人员根据看到的实际状况可暂不理会中央生产计划,而便宜行事。
例如,当看到下道工序库存出现积压,他们可以放缓生产速度。
(参见问卷中问题11和20)第5类空间使用、物料移动与生产线流动最佳工厂的空间使用率很高。
理想状态是:物料仅移动一次,移动距离尽可能短,移动时物料置于高效率的运输箱中。
生产物料应沿生产线存放,而不是在几个库存区分隔储藏。
工具和工艺装置摆放应尽量靠近机器。
工厂布局应保证产品流动持续顺畅,而不是围绕特定种类的机器分成不同的“车间”,一个个块状分隔。
20世纪90年代中期,我第一次参观了总部位于奥地利的卢森宝亚国际有限公司(Rosenbauer),该公司是欧洲最大消防车辆和设备生产商之一。
我给该公司打的分数很高,只是水泵和车辆组装除外,因为该公司仍在传统的“单元”中组装水泵和车辆。
两年后我再次参观该公司时,它的水泵和车辆组装已实现了精益生产。
另据公司管理人员报告,生产效率和产品质量都有所提高。
了解工厂空间使用情况的一个简捷方法是数一下铲车数量。
铲车通道占地大,操作成本高,会加得污染,还会鼓励不必要的物料移动。
最佳工厂里,物料如需短距离移动,员工会使用手推车;如果太重推不动,他们则会将手推车连接起来,用小电动牵引车拖动。
在任何工厂里,空间都是宝贵的必需品。
有些工厂把腾出新的空间定为提高生产效率的目标。
我们有位厂长甚至将这一概念提升到了艺术的高度,他经常腾出生产空间,然后将地板擦得锃亮,并用栏杆围起这块空间,然后向销售部门提出挑战,要求他们开发新的业务,使腾出的空间再次得到利用。
(参见问卷中问题7、12、13和20)第6类库存与在制品水平内部运作常常所需库存很少,因此,可见零部件数量是衡量工厂精益生产水平的很好标准。
看一看生产线,数一数每个工段的库存,你就能快速了解工厂的库存水平。
例如,如果生产线每分钟生产1件产品,你就知道每小时的产量是60个。
如果你发现某工段旁堆着约500件这种产品,你就知道静静躺在那儿的是8个小时的产量。