故障预警系统-PPT课件
合集下载
气象灾害监测与预警系统模板课件

气象灾害监测与预警系统模板课件
汇报人:可编辑
2024-01-01
目录 Contents
• 气象灾害监测与预警系统概述 • 气象灾害监测技术 • 气象灾害预警系统 • 气象灾害监测与预警系统的应用与发展 • 案例分析
01
气象灾害监测与预警系统概 述
气象灾害的定义与分类
气象灾害定义
气象灾害是指由于大气圈异常变 化引起的各种自然灾害,包括暴 雨、洪涝、干旱、台风、寒潮等 。
总结词
长期积累、经验丰富
详细描述
该地区长期开展气象灾害监测与预警工作,积累了丰富的 实践经验。通过对历史数据的分析,不断优化监测站点布 局和设备选型,提高预警准确率。此外,还定期开展应急 演练和培训,加强部门间的协作配合,提高应对能力。
台风灾害的监测与预警
总结词
全方位监测、多手段预警
详细描述
针对台风灾害的特点,该地区采用卫星遥感、雷达、地面观测等多种手段进行全方位监测,实时获取 台风的位置、强度、移动方向等信息。同时,通过电视、广播、短信、社交媒体等多种渠道发布预警 信息,确保覆盖到所有可能受影响的人群。
提高应急响应能力
准确监测和预警有助于政 府部门和救援机构快速响 应,采取有效措施应对灾 害。
保障公共安全
确保公众及时获取气象灾 害预警信息,提高公众安 全意识和自救能力。
气象灾害监测与预警系统的技术发展
遥感技术的应用
预警信息发布手段多样化
利用卫星遥感技术对气象灾害进行大 面积、高精度监测。
利用手机短信、社交媒体、广播电视 等多种渠道发布预警信息,确保覆盖 更广泛的人群。
台风灾害的监测与预警
总结词
科学分析、精准预测
详细描述
该地区建立了专业的气象分析团队,利用先进的计算机模型对台风数据进行科学分析, 预测台风可能经过的路径、强度变化和影响时间。通过精准预测,提前做好防范措施,
汇报人:可编辑
2024-01-01
目录 Contents
• 气象灾害监测与预警系统概述 • 气象灾害监测技术 • 气象灾害预警系统 • 气象灾害监测与预警系统的应用与发展 • 案例分析
01
气象灾害监测与预警系统概 述
气象灾害的定义与分类
气象灾害定义
气象灾害是指由于大气圈异常变 化引起的各种自然灾害,包括暴 雨、洪涝、干旱、台风、寒潮等 。
总结词
长期积累、经验丰富
详细描述
该地区长期开展气象灾害监测与预警工作,积累了丰富的 实践经验。通过对历史数据的分析,不断优化监测站点布 局和设备选型,提高预警准确率。此外,还定期开展应急 演练和培训,加强部门间的协作配合,提高应对能力。
台风灾害的监测与预警
总结词
全方位监测、多手段预警
详细描述
针对台风灾害的特点,该地区采用卫星遥感、雷达、地面观测等多种手段进行全方位监测,实时获取 台风的位置、强度、移动方向等信息。同时,通过电视、广播、短信、社交媒体等多种渠道发布预警 信息,确保覆盖到所有可能受影响的人群。
提高应急响应能力
准确监测和预警有助于政 府部门和救援机构快速响 应,采取有效措施应对灾 害。
保障公共安全
确保公众及时获取气象灾 害预警信息,提高公众安 全意识和自救能力。
气象灾害监测与预警系统的技术发展
遥感技术的应用
预警信息发布手段多样化
利用卫星遥感技术对气象灾害进行大 面积、高精度监测。
利用手机短信、社交媒体、广播电视 等多种渠道发布预警信息,确保覆盖 更广泛的人群。
台风灾害的监测与预警
总结词
科学分析、精准预测
详细描述
该地区建立了专业的气象分析团队,利用先进的计算机模型对台风数据进行科学分析, 预测台风可能经过的路径、强度变化和影响时间。通过精准预测,提前做好防范措施,
设备维保中的故障预警与设备保养管理

根据预警和保养的实际效果,持 续优化预警模型和保养策略,提 高设备运行效率。
04
实际案例分析
案例一:某工厂的设备预警与保养管理实践
总结词:成功应用
详细描述:某工厂通过引入先进的设备预警系统,实现了对关键设备的实时监测 。同时,结合定期保养管理,有效降低了设备故障率,提高了生产效率。
案例二:预警系统在大型设备维保中的应用
提高设备使用寿命
通过及时发现和解决潜在 故障,延长设备使用寿命 ,降低总体维护成本。
预警系统的优势与局限性
优势
预警系统能够实时监测设备状态,提 前发现潜在故障,提高设备维保的效 率和效果。
局限性
预警系统需要专业的技术支持和维护 ,同时数据分析和算法的准确性和可 靠性有待验证。此外,预警系统并不 能完全替代人工检查和经验判断。
可持续性维护
在保障设备正常运行的同时,注重环保和可 持续发展,降低设备维护过程中的能源消耗 和环境污染。
THANKS
感谢观看
总结词:技术升级
详细描述:针对大型设备的维护保养需求,某企业采用智能预警系统,通过数据分析预测设备故障,实现了精准维修,减少 了非计划停机时间。
案例三:保养管理优化与企业效益的提升
总结词:效益提升
详细描述:某企业通过对设备保养管理的持续优化,提高了设备使用寿命和稳定性。从而降低了维修 成本,增加了企业经济效益。
反馈保养效果
保养后的设备性能数据可以反馈 给预警系统,用于评估保养措施 的有效性。
预警与保养的协同优化策略
01
整合资源共享信息
建立统一的设备管理平台,整合 预警系统和保养管理系统的资源 ,实现信息共享。
02
制定协同工作流程
03
平台系统故障应急预案
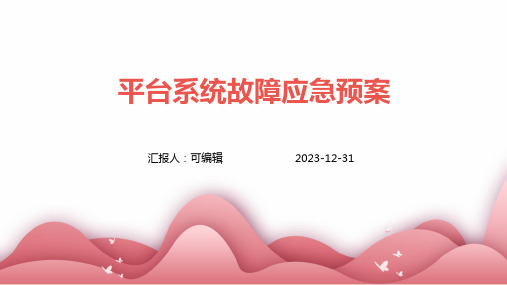
按照影响范围和严重程度,故障可分 为局部故障和全局故障;按照发生频 率,可分为常见故障和偶发故障。
故障识别机制
监控与日志分析
建立全面的监控体系,实时监测系统 各项指标,通过分析日志文件,及时 发现异常情况。
定期巡检与维护
制定定期巡检计划,对关键设备和系 统进行预防性检查和维护,确保系统 稳定运行。
故障定位与隔离
总结词:精准定位
详细描述:通过监控系统、日志分析等手段,精准定位故障原因,并立即采取措施隔离故障,防止故 障扩大影响整个系统。
紧急恢复计划启动
总结词:快速恢复
详细描述:根据故障情况,启动相应的紧急恢复计划,包括数据备份恢复、系统重构等措施,尽快恢复平台系统的正常运行 。
资源协调与调配
预警系统建设
预警指标设定
根据历史数据和经验,设定关键性能指 标的阈值,一旦超过阈值即触发预警。
VS
预警响应流程
建立预警响应流程,明确各岗位人员职责 ,确保在预警发生时能够迅速响应并采取 措施。
02
应急响应流程
响应小组组建
总结词:快速响应
详细描述:在平台系统发生故障时,迅速成立由技术专家、运维人员和相关管理 人员组成的应急响应小组,负责故障的快速定位、隔离和恢复工作。
总结词:高效协调
详细描述:对应急响应小组所需的资 源进行协调和调配,包括硬件资源、 软件资源、网络资源等,确保应急响 应工作的顺利进行。
03
故障恢复与优化
数据备份与恢复
数据备份
定期对平台系统中的数据进行备份,确保在故障发生时能够快速恢复数据。
恢复策略
制定详细的数据恢复计划,明确恢复流程和责任人,以便在需要时迅速执行。
系统重构与优化
故障识别机制
监控与日志分析
建立全面的监控体系,实时监测系统 各项指标,通过分析日志文件,及时 发现异常情况。
定期巡检与维护
制定定期巡检计划,对关键设备和系 统进行预防性检查和维护,确保系统 稳定运行。
故障定位与隔离
总结词:精准定位
详细描述:通过监控系统、日志分析等手段,精准定位故障原因,并立即采取措施隔离故障,防止故 障扩大影响整个系统。
紧急恢复计划启动
总结词:快速恢复
详细描述:根据故障情况,启动相应的紧急恢复计划,包括数据备份恢复、系统重构等措施,尽快恢复平台系统的正常运行 。
资源协调与调配
预警系统建设
预警指标设定
根据历史数据和经验,设定关键性能指 标的阈值,一旦超过阈值即触发预警。
VS
预警响应流程
建立预警响应流程,明确各岗位人员职责 ,确保在预警发生时能够迅速响应并采取 措施。
02
应急响应流程
响应小组组建
总结词:快速响应
详细描述:在平台系统发生故障时,迅速成立由技术专家、运维人员和相关管理 人员组成的应急响应小组,负责故障的快速定位、隔离和恢复工作。
总结词:高效协调
详细描述:对应急响应小组所需的资 源进行协调和调配,包括硬件资源、 软件资源、网络资源等,确保应急响 应工作的顺利进行。
03
故障恢复与优化
数据备份与恢复
数据备份
定期对平台系统中的数据进行备份,确保在故障发生时能够快速恢复数据。
恢复策略
制定详细的数据恢复计划,明确恢复流程和责任人,以便在需要时迅速执行。
系统重构与优化
设备故障处理PPT课件
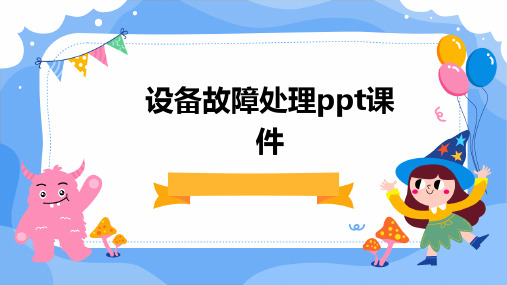
断电路是否正常。
用于观察设备的信号波 形,判断信号是否正常。
用于检测设备的频率成 分,判断是否存在干扰
或异常。
逻辑分析仪
用于分析设备的逻辑电 路,判断是否存在逻辑
错误或时序问题。
故障诊断流程
仪表测试
使用专业的检测仪器和工具对 设备进行测试,获取准确的测 量数据。
修复处理
对故障部位进行修复或更换部 件,使设备恢复正常工作。
故障诊断与预测
利用故障诊断和预测技术,对设备进行实时监测 和预警,提前发现潜在问题。
THANKS
感谢观看
设备故障的影响
01
02
03
生产效率下降
设备故障会导致生产流程 中断,生产效率降低。
运营成本增加
设备故障需要维修和更换 部件,增加了企业的运营 成本。
安全风险增加
某些设备故障可能对操作 人员和周围环境造成安全 威胁,增加安全风险。
02
设备故障诊断
故障诊断方法
01
02
03
04
直接观察法
通过检查设备的外观、声音、 气味等,初步判断故障原因。
设备故障处理ppt课 件
目录
• 设备故障概述 • 设备故障诊断 • 设备故障处理 • 设备故障案例分析 • 设备故障预防与优化
01
设备故障概述
设备故障的定义
01
设备故障的定义
设备故障是指设备在运行过程中出现的异常现象,导致设备不能正常工
作。
02
设备故障的判定标准
设备故障通常以设备性能参数、工作精度、安全性、可靠性等是否正常
初步检查
通过观察、听诊、触诊等方式 初步判断故障部位和原因。
故障定位
根据测试结果和经验,定位故 障部位和原因。
用于观察设备的信号波 形,判断信号是否正常。
用于检测设备的频率成 分,判断是否存在干扰
或异常。
逻辑分析仪
用于分析设备的逻辑电 路,判断是否存在逻辑
错误或时序问题。
故障诊断流程
仪表测试
使用专业的检测仪器和工具对 设备进行测试,获取准确的测 量数据。
修复处理
对故障部位进行修复或更换部 件,使设备恢复正常工作。
故障诊断与预测
利用故障诊断和预测技术,对设备进行实时监测 和预警,提前发现潜在问题。
THANKS
感谢观看
设备故障的影响
01
02
03
生产效率下降
设备故障会导致生产流程 中断,生产效率降低。
运营成本增加
设备故障需要维修和更换 部件,增加了企业的运营 成本。
安全风险增加
某些设备故障可能对操作 人员和周围环境造成安全 威胁,增加安全风险。
02
设备故障诊断
故障诊断方法
01
02
03
04
直接观察法
通过检查设备的外观、声音、 气味等,初步判断故障原因。
设备故障处理ppt课 件
目录
• 设备故障概述 • 设备故障诊断 • 设备故障处理 • 设备故障案例分析 • 设备故障预防与优化
01
设备故障概述
设备故障的定义
01
设备故障的定义
设备故障是指设备在运行过程中出现的异常现象,导致设备不能正常工
作。
02
设备故障的判定标准
设备故障通常以设备性能参数、工作精度、安全性、可靠性等是否正常
初步检查
通过观察、听诊、触诊等方式 初步判断故障部位和原因。
故障定位
根据测试结果和经验,定位故 障部位和原因。
故障预警系统-PPT课件

工作流程范围设备选择监视设备人员分析与业人员对预警信息进行分析判断通知设备负责人查找具体原因针对设备劣化程度提前安排检修针对设备创建个性化的动态模型采集数据数据库从实时数据库采集实时数据界面友好的可视化界面系统工作流程实施范围实施范围汽轮机汽轮机锅炉汽水系统锅炉汽水系统发电机发电机一次风机一次风机主变压器主变压器送风机送风机凝汽器凝汽器引风机引风机给水加热器给水加热器fgdfgd增压风机增压风机锅炉给水泵锅炉给水泵空气预热器空气预热器炉水循环泵炉水循环泵磨煤机磨煤机循环水泵循环水泵前置泵前置泵凝结水泵凝结水泵定子冷却水泵定子冷却水泵燃油泵燃油泵闭式循环冷却水泵闭式循环冷却水泵或其他可检测设备根据实际情况讨论添加或其他可检测设备根据实际情况讨论添加系统实施范围
02/20—03/20 劣化低频状态
03/20—04/01 劣化高频状态
04/01 凝泵A 恢复备用
1#机组凝泵A电机轴承振动
4月1日
1#机组凝泵A电机轴承温度1
复正常,恢复备用状态。其后,再次运 行后,发现设备状态已恢复正常。 避免了一次由于电机轴承损坏而引起的 凝泵跳泵,甚至可能导致机组非停的事 故,挽回了大量的经济损失。
。经检查发现电机轴承磨损十分严重, 必须马上更换才能继续使用。
3月21日分析人员发现预警事件频率大
1#机组凝泵A电机轴承温度2
电机轴承温度实际值与估计值频繁偏离 3度以上,达到70度以上,仍未达到90 度的固定报警热工定值,普通软件无法 检测到劣化状态。
1#机组凝泵A电流
01/01—02/20 设备正常状态
故障开始
现有的传感器观测 设备看起来一直正常
未发现设备 劣化状态
直到故障发生, 才报警
因为现有的监测手段观测不到设备的劣化状态,不能对 历史数据和设备工况进行分析,触发报警时已太晚!
02/20—03/20 劣化低频状态
03/20—04/01 劣化高频状态
04/01 凝泵A 恢复备用
1#机组凝泵A电机轴承振动
4月1日
1#机组凝泵A电机轴承温度1
复正常,恢复备用状态。其后,再次运 行后,发现设备状态已恢复正常。 避免了一次由于电机轴承损坏而引起的 凝泵跳泵,甚至可能导致机组非停的事 故,挽回了大量的经济损失。
。经检查发现电机轴承磨损十分严重, 必须马上更换才能继续使用。
3月21日分析人员发现预警事件频率大
1#机组凝泵A电机轴承温度2
电机轴承温度实际值与估计值频繁偏离 3度以上,达到70度以上,仍未达到90 度的固定报警热工定值,普通软件无法 检测到劣化状态。
1#机组凝泵A电流
01/01—02/20 设备正常状态
故障开始
现有的传感器观测 设备看起来一直正常
未发现设备 劣化状态
直到故障发生, 才报警
因为现有的监测手段观测不到设备的劣化状态,不能对 历史数据和设备工况进行分析,触发报警时已太晚!
监狱智能预警系统ppt

利用深度学习技术,对犯人的行为特征进行分析,预测其可能的行为模式。
深度学习
自然语言处理
智能语音技术
对犯人档案、民警执法数据等文本数据进行自然语言处理,提取有用的信息。
对监控视频中的语音数据进行识别和分析,提取其中的情感和语义信息。
03
人工智能技术的应用
02
01
03
工作流程与展示
监狱智能预警系统在监狱管理系统中启动,包括硬件和软件系统的初始化、网络连接测试等。
监狱网络应部署强大的防火墙,以防止未经授权的访问和外部攻击。
系统防火墙
监狱管理部门应定期检测系统漏洞,并采取及时有效的措施加以修复,以确保系统的安全性。
系统漏洞管理
05
应用与展望
数据分析
监狱智能预警系统可以通过对大数据的分析,发现监狱内潜在的安全隐患,如囚犯行为、情绪等方面的变化,为监狱管理提供预警。
启动
对预警系统进行参数设置,包括预警级别、预警范围、预警时间等,以确保预警系统的准确性和及时性。
设置
预警系统的启动与设置
运行
预警系统在监狱管理系统的运行过程中,通过实时数据采集、处理和分析,对异常情况进行预警。
监控
监狱管理人员可以通过监控界面实时查看预警情况,了解监狱内的安全状况。
预警系统的运行与监控
xx年xx月xx日
监狱智能预警系统
CATALOGUE
目录
介绍系统设计工作流程与展示安全与保障应用与展望
01
介绍
目前,全球监狱系统面临着多种挑战,包括监狱拥挤、犯人管理、安全防范等问题。
为了解决这些问题,监狱智能预警系统应运而生,旨在提高监狱管理的效率和安全性。
背景和目的
本项目的独特之处在于采用了人工智能技术,能够实时监测和分析监狱内的情况,提早发现异常行为和潜在的犯罪活动。
设备维保的故障预警与预防措施

给相关人员,缩短响应时间。
个性化预防措施的完善
个性化预防方案
根据设备类型、运行环境和历史维护数据,为不同设备制定个性化 的预防措施,提高预防效果。
预防措施智能化
通过数据分析,自动调整预防措施,以适应设备运行状态的变化, 降低维护成本。
预防措施普及推广
随着技术的不断发展,个性化预防措施将逐渐普及,为更多设备提供 高效维护。
05
未来发展趋势与展望
智能化预警技术的发展
智能化预警技术
01
利用传感器、大数据和人工智能技术,实时监测设备运行状态
,通过分析数据预测潜在故障,及时发出预警。
预警准确率提升
02
随着算法的不断优化,预警系统的准确率将逐渐提高,减少误
报和漏报的情况。
预警实时性增强
03
通过云计算和边缘计算技术的结合,预警信息能够更快地传递
预测性维修
利用传感器和监测系统对设备进行实时监测,预测可能出现的故障 并及时维修。
替换件储备
储备设备的易损件和关键部件,以便在需要时及时更换。
设备使用规范与培训
操作规程
制定详细的设备操作规程,规范操作人员的操作行为。
安全培训
定期对操作人员进行安全培训,提高安全意识和操作技能。
应急预案
制定设备故障应急预案,确保在突发故障时能够迅速应对。
通过预警系统的数据分析,可以预测 设备可能出现的故障,提前采取相应 的预防措施,提高设备维护的效率和 效果。
预防措施对预警系统的反馈与完善
预防措施的实施过程中,可以收集设备运行数据和故障信息,为预警系统的优化 提供反馈。
根据预防措施的实施效果和设备故障情况,可以不断完善预警系统的算法和监测 参数,提高预警系统的准确性和可靠性。
《BSC告警分析》课件
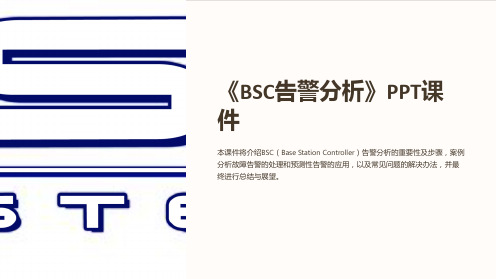
《BSC告警分析》PPT课 件
本课件将介绍BSC(Base Station Controller)告警分析的重要性及步骤,案例 分析故障告警的处理和预测性告警的应用,以及常见问题的解决办法,并最 终进行总结与展望。
BSM系统简介
BSM(Business Service Management)系统是一种用于监控、管理和优化 企业中的关键业务服务的软件系统。该系统可以帮助企业实时监测业务性 能和故障情况,以便及时采取措施,确保业务的连续性和稳定性。
BSC告警的重要性
BSC告警是监测无线通信网络中所发生问题的重要手段。通过有效地分析BSC 告警,可以提前预警网络故障和性能问题,以便及时采取措施避免业务中断, 并提高网络的可靠性和稳定性。
BSC告警分析的步骤
1
收集告警数据
从BSC系统中收集相关的告警数据,包括告警类型、告警级别、发生时间等信息。
2
分类和整理
根据告警的性质和特征对数据进行分类和整理,以便更好地理解和分析告警情况。
3
趋势分析
通过对历史告警数据进行趋势分析,可以发现和预测系统中可能出现的问题和风险。
4
异常检测
利用统计学和机器学习等方法进行异常检测,找出告警中的异常情况,以便及时解决。
案例分析:故障告警的处理
问题定位
通过对故障告警的分析和定 位,找出导致故障的具体原 因和根源。
解决方案
针对故障告警提出相应的解 决方案,并进行实施和验证。
故障修复
根据解决方案进行故障修复 工作,确保系统能够正常运 行。
案例分析:预测性告警的应用数据分析利用预测性分析方法对历史数据 进行分析,以预测未来可能出现 的故障情况。
机器学习
应用机器学习算法,通过对大量 数据的学习和训练,建立故障预 测模型。
本课件将介绍BSC(Base Station Controller)告警分析的重要性及步骤,案例 分析故障告警的处理和预测性告警的应用,以及常见问题的解决办法,并最 终进行总结与展望。
BSM系统简介
BSM(Business Service Management)系统是一种用于监控、管理和优化 企业中的关键业务服务的软件系统。该系统可以帮助企业实时监测业务性 能和故障情况,以便及时采取措施,确保业务的连续性和稳定性。
BSC告警的重要性
BSC告警是监测无线通信网络中所发生问题的重要手段。通过有效地分析BSC 告警,可以提前预警网络故障和性能问题,以便及时采取措施避免业务中断, 并提高网络的可靠性和稳定性。
BSC告警分析的步骤
1
收集告警数据
从BSC系统中收集相关的告警数据,包括告警类型、告警级别、发生时间等信息。
2
分类和整理
根据告警的性质和特征对数据进行分类和整理,以便更好地理解和分析告警情况。
3
趋势分析
通过对历史告警数据进行趋势分析,可以发现和预测系统中可能出现的问题和风险。
4
异常检测
利用统计学和机器学习等方法进行异常检测,找出告警中的异常情况,以便及时解决。
案例分析:故障告警的处理
问题定位
通过对故障告警的分析和定 位,找出导致故障的具体原 因和根源。
解决方案
针对故障告警提出相应的解 决方案,并进行实施和验证。
故障修复
根据解决方案进行故障修复 工作,确保系统能够正常运 行。
案例分析:预测性告警的应用数据分析利用预测性分析方法对历史数据 进行分析,以预测未来可能出现 的故障情况。
机器学习
应用机器学习算法,通过对大量 数据的学习和训练,建立故障预 测模型。
突发事件预警PPT课件

21
台风预警信号
24小时内可能受热带气旋影响,平均风 力可达6级以上,或阵风7级以上;或者已经 受热带气旋影响,平均风力为6~7级,或阵 风7~8级并可能持续。
24小时内可能受热带气旋影响,平均风力 可达8级以上,或阵风9级以上;或者已经受 热带气旋影响,平均风力为8~9级,或阵风 9~10级并可能持续。
2
2003年SARS疫情爆发后,突发公共卫生事件的预 警受到重视。
世界卫生组织(WHO)修订了国际卫生条例,建立了 全球传染病突发预警和应对网络 the global outbreak alert and response network, GOARN
3
我国 2003 年5 月颁布的《突发公共卫生事件 应急条例》中规定县级以上地方人民政府应当建 立和完善突发事件监测与预警系统。
12小时内降雪量将达6毫米 以上,或者已达6毫米以上 且降雪持续,可能对交通或 者农牧业有影响。
1、政府及相关部门按照职责落实防雪灾和防冻害措施; 2、交通、铁路、电力、通信等部门应当加强道路、铁路、线路巡查 维护,做好道路清扫和积雪融化工作; 3、行人注意防寒防滑,驾驶人员小心驾驶,车辆应当采取防滑措施; 4、农牧区和种养殖业要备足饲料,做好防雪灾和防冻害准备; 5、加固棚架等易被雪压的临时搭建物。
这场南方的暴风雪天气预报部门虽有预报,但对长期 低温造成冰雪灾害程度的预报不准确不到位,未能引导 全国上下的警觉和应急反应,以至冰雪灾害造成交通、 煤电供应中断多日的情况后才发出黄色警报,以至延误 了战机,造成数百亿元的损失。大雪灾就是一份大考卷, 天气预报滞后导致新闻报道滞后,政府反应滞后。
美国“国际先驱论坛报”:“中国的暴风雪暴露了一
建立预警系统其主体自然是政府机构,把零散的 信息通过一定的、理顺的渠道进行收集,保证信息的 准确性、可靠性,然后对其进行分析,做出科学判断, 发出正确预告。
台风预警信号
24小时内可能受热带气旋影响,平均风 力可达6级以上,或阵风7级以上;或者已经 受热带气旋影响,平均风力为6~7级,或阵 风7~8级并可能持续。
24小时内可能受热带气旋影响,平均风力 可达8级以上,或阵风9级以上;或者已经受 热带气旋影响,平均风力为8~9级,或阵风 9~10级并可能持续。
2
2003年SARS疫情爆发后,突发公共卫生事件的预 警受到重视。
世界卫生组织(WHO)修订了国际卫生条例,建立了 全球传染病突发预警和应对网络 the global outbreak alert and response network, GOARN
3
我国 2003 年5 月颁布的《突发公共卫生事件 应急条例》中规定县级以上地方人民政府应当建 立和完善突发事件监测与预警系统。
12小时内降雪量将达6毫米 以上,或者已达6毫米以上 且降雪持续,可能对交通或 者农牧业有影响。
1、政府及相关部门按照职责落实防雪灾和防冻害措施; 2、交通、铁路、电力、通信等部门应当加强道路、铁路、线路巡查 维护,做好道路清扫和积雪融化工作; 3、行人注意防寒防滑,驾驶人员小心驾驶,车辆应当采取防滑措施; 4、农牧区和种养殖业要备足饲料,做好防雪灾和防冻害准备; 5、加固棚架等易被雪压的临时搭建物。
这场南方的暴风雪天气预报部门虽有预报,但对长期 低温造成冰雪灾害程度的预报不准确不到位,未能引导 全国上下的警觉和应急反应,以至冰雪灾害造成交通、 煤电供应中断多日的情况后才发出黄色警报,以至延误 了战机,造成数百亿元的损失。大雪灾就是一份大考卷, 天气预报滞后导致新闻报道滞后,政府反应滞后。
美国“国际先驱论坛报”:“中国的暴风雪暴露了一
建立预警系统其主体自然是政府机构,把零散的 信息通过一定的、理顺的渠道进行收集,保证信息的 准确性、可靠性,然后对其进行分析,做出科学判断, 发出正确预告。
800MHz列尾和列车安全预警系统课件

•20
800MHz列尾装置功能介绍
查询指令转发流程转发流程:
②查询应答 ①查询
列尾主机
车载综合电台
②查询应答
列尾中继
①查询 ③查询应答
•800MHz列尾和列车安全预警系统
•21
800MHz列尾装置功能介绍
列尾主机和列尾中继同时收到机车台的查询指 令,此时列尾主机准备回复机车台,中继处于 守侯状态,观察列尾主机在规定的 时间是否应 答。
当列车运行在复线上时,发生列车脱线倾覆,威
胁临线行车安全时,列车乘务员按下控制盒黄色预 警键后,控制盒将列车车次、公里标、时间等信息 以FFSK编码方式传输给电台,电台将FFSK信号调 制到866.2375MHz频点上发送出去。
•800MHz列尾和列车安全预警系统
•18
800M列尾装置概述
800MHz列车接近预警原理:
车载综合电台
列车接近预警信息
列尾主机
确认信息
•800MHz列尾和列车安全预警系统
•19
800M列尾装置概述
800MHz列车二次故障防护预警原理:
列尾主机
车载综合电台 列车二次事故防护预警信息 车载综合电台 列车二次事故防护预警信息
列尾主机
列车脱线事故 车载综合电台
列尾主机
•800MHz列尾和列车安全预警系统
•800MHz列尾和列车安全预警系统
•13
800M列尾装置概述
2. 道口安全预警电台设备
道口安全预警设备包括:WJTD-II道口 安全预警电台、WJDY-I道口电源、 WJPD-I型道口显示屏。附属设备:道口 数据采集器、道口数据读取软件。
实现功能:接收列车接近预警信息,提醒道 口看守人员及时关闭道口。当道口发生危 及行车安全的障碍或事故时,通过操作道 口设备向接近的列车发送障碍预警信息。
《故障预警系统》课件
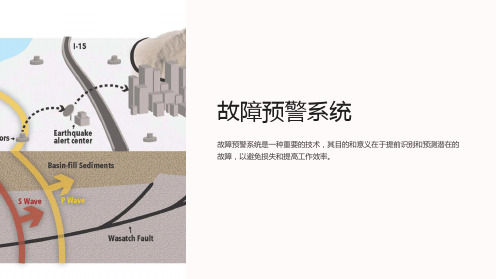
全和通行效率。
3
机械制造系统
监测设备运行和工艺参数,减少生产 故障和维修成本。
故障预警系统的优势和劣势
1 优势
提前发现故障、降低维修成本、增加工作效率。
2 劣势
依赖于数据准确性、系统成本较高、存在误报的风险。
3 后续发展
不断改进算法和技术,提高系统性能和可靠性。
故障预警系统的未来展望
技术趋势
人工智能和大数据分析将进一 步提升故障预警系统的性能。
故障预警系统的设计
硬件设计
选择适合的传感器和设备, 确保准确监测和数据收集。
软件设计
开发优化的算法和模ห้องสมุดไป่ตู้,实 现故障预测和数据分析。
网络通信设计
建立稳定的网络通信,将故 障信息及时传输给用户。
故障预警系统应用示例
1
电力系统
监测电网负载和传输设备状态,减少
交通系统
2
停电和损失。
监测信号灯和道路设备,提高交通安
应用领域
故障预警系统将广泛应用于制 造业、能源领域和城市基础设 施等。
可能带来的变化
故障预警系统将改变故障维修 模式,提高设备可靠性和工作 安全。
总结和展望
1 重点回顾
2 未来展望
故障预警系统的重要性、功能和应用示例。
继续改进技术、应用领域的拓展和成本效 益的提升。
参考文献
期刊论文 专利文献 网络资料
致谢
感谢支持和帮助的人员
特别感谢所有协助和支持我的人员。
表达自己的感激之情
表示对所有支持和帮助的人员的真诚感激之情。
故障预警系统
故障预警系统是一种重要的技术,其目的和意义在于提前识别和预测潜在的 故障,以避免损失和提高工作效率。
最新安全监测预警系统中文PPT课件

5、系统组成 按功能划分,共由六个部份组成,下面分别介绍如下: 利用GPS卫星定位技术实现的坝体形变监测系统 GPS卫星定位技术是目前国际上在形变监测应用方面最前沿和先进的技术之一,在长期的应用中,该种监测方式已经得到实践验证,并日益成熟。该技术是以现代卫星大地测量理论、技术为基础,以基于多元统计分析的数据处理和变形分析理论、技术为核心,以现代通讯和计算机网络技术为手段,实现精密监测工程自动化的监测系统,它是GPS定位技术、数字通讯技术、计算机网络技术、自动控制技术、精密工程测量技术和现代数据处理技术等高新技术的集成,利用此技术开发的尾矿坝体形变监测系统优点如下: A、可实现长期、连续、全自动、全天候实时监测。 B、能实时提供坝体监测点的三维变形量,监测精度达到毫米级。 C、可实现从数据采集、传输、处理、分析、显示、存储全自动化。 D、观测时间同步,能客观反映某一时刻坝体各监测点的变形状况; E、各监测点的三维位移能同步测出。
3、系统数据流分析 通过充分的总体分析与设计确定系统由数据采集子系统、数据管理信息子系统和三部分主体功能组成,系统的数据流图如图3-1所示: 图一 系统数据流
ቤተ መጻሕፍቲ ባይዱ
尾矿库安全监测数据采集系统
4、系统架构 我们所设计的这样一套监测系统,采用了三级构架结构体系: 最低层为原始数据采集层,利用现场的智能化设备,采用传感器技术,实时采集库区水位、降雨量、干滩、形变位移、浸润线埋深等各种原始数据; 中间层为数据层,它以数据库技术为核心,将现场采集的各种原始数据按照一定算法还原后存入SQL后台数据库中,供专家系统分析、统计、预警使用; 三级结构的最顶层为用户层,它采用的是专用的专家软件系统对数据库中的数据按照用户的不同需要,根据不同的数学模型进行计算,并给出相应结果。 各层之间的通信联系以光纤和无线通信设备相结合作为载体,组成一个尾矿安全监测预警专用数字化网络系统。
3、系统数据流分析 通过充分的总体分析与设计确定系统由数据采集子系统、数据管理信息子系统和三部分主体功能组成,系统的数据流图如图3-1所示: 图一 系统数据流
ቤተ መጻሕፍቲ ባይዱ
尾矿库安全监测数据采集系统
4、系统架构 我们所设计的这样一套监测系统,采用了三级构架结构体系: 最低层为原始数据采集层,利用现场的智能化设备,采用传感器技术,实时采集库区水位、降雨量、干滩、形变位移、浸润线埋深等各种原始数据; 中间层为数据层,它以数据库技术为核心,将现场采集的各种原始数据按照一定算法还原后存入SQL后台数据库中,供专家系统分析、统计、预警使用; 三级结构的最顶层为用户层,它采用的是专用的专家软件系统对数据库中的数据按照用户的不同需要,根据不同的数学模型进行计算,并给出相应结果。 各层之间的通信联系以光纤和无线通信设备相结合作为载体,组成一个尾矿安全监测预警专用数字化网络系统。
新能源汽车的车辆故障预警系统

。
系统重要性
提高安全性
通过及时发现和预警潜在故障,可以 有效降低因车辆故障引发的交通事故 风险。
延长使用寿命
及时处理潜在故障可以避免小问题发 展成大故障,从而延长车辆的使用寿 命。
提高维修效率
通过数据记录和回放功能,维修人员 可以快速定位故障点,提高维修效率 。
降低运营成本
减少因车辆故障导致的停运时间和维 修成本,从而降低整体运营成本。
多传感器融合
将多种传感器融合,实现更全面、准确的故障预警,提高车辆安全 性。
应用拓展
多种车型应用
将车辆故障预警系统拓展应用到更多种类的新能源汽车上,包括 轿车、货车、客车等。
跨国合作
加强国际合作,推动预警系统在全球范围内的应用和推广。
定制化服务
根据不同用户的需求,提供定制化的预警系统解决方案,提高用 户满意度。
通过技术手段监测车辆运行状态,预 测可能出现的故障,并及时向驾驶员 发出预警,以保障行车安全。
新能源汽车的特殊性
新能源汽车采用非传统燃料作为动力 源,具有节能环保、高效能等优点, 但也存在一些特殊问题,如电池续航 能力、充电设施等。
背景介绍
政策支持
随着全球环保意识的提高,各国政府纷纷出台政策鼓励新能源汽车的发展,如减免购置税、免费充电 等。
故障诊断
基于处理后的数据,通过算法和模型进行故障诊断, 判断车辆是否存在故障以及故障的类型和程度。
通信技术
数据传输
通过无线通信技术将传感器数据实时传输到上位 机或云平台,实现远程监控和诊断。
通信协议
采用统一的通信协议,保证不同厂商生产的传感 器和设备之间的兼容性和互操作性。
数据安全
采用加密技术、防火墙等措施,确保数据传输和 存储的安全性和保密性。
系统重要性
提高安全性
通过及时发现和预警潜在故障,可以 有效降低因车辆故障引发的交通事故 风险。
延长使用寿命
及时处理潜在故障可以避免小问题发 展成大故障,从而延长车辆的使用寿 命。
提高维修效率
通过数据记录和回放功能,维修人员 可以快速定位故障点,提高维修效率 。
降低运营成本
减少因车辆故障导致的停运时间和维 修成本,从而降低整体运营成本。
多传感器融合
将多种传感器融合,实现更全面、准确的故障预警,提高车辆安全 性。
应用拓展
多种车型应用
将车辆故障预警系统拓展应用到更多种类的新能源汽车上,包括 轿车、货车、客车等。
跨国合作
加强国际合作,推动预警系统在全球范围内的应用和推广。
定制化服务
根据不同用户的需求,提供定制化的预警系统解决方案,提高用 户满意度。
通过技术手段监测车辆运行状态,预 测可能出现的故障,并及时向驾驶员 发出预警,以保障行车安全。
新能源汽车的特殊性
新能源汽车采用非传统燃料作为动力 源,具有节能环保、高效能等优点, 但也存在一些特殊问题,如电池续航 能力、充电设施等。
背景介绍
政策支持
随着全球环保意识的提高,各国政府纷纷出台政策鼓励新能源汽车的发展,如减免购置税、免费充电 等。
故障诊断
基于处理后的数据,通过算法和模型进行故障诊断, 判断车辆是否存在故障以及故障的类型和程度。
通信技术
数据传输
通过无线通信技术将传感器数据实时传输到上位 机或云平台,实现远程监控和诊断。
通信协议
采用统一的通信协议,保证不同厂商生产的传感 器和设备之间的兼容性和互操作性。
数据安全
采用加密技术、防火墙等措施,确保数据传输和 存储的安全性和保密性。
桥梁防撞预警系统课件

3.3桥梁防撞预警前端示意图-3
智能激光预警器是国际领先技术的测距设备,其能发射出波长905纳米不可见激光,精确测量出设备与被测物体之间的距离,并把数据传送给桥梁防撞预警系统。
执法人员在控制室监控
2
A
预警区
B
3
1
1000M以上
桥梁防撞预警系统
两束水平射出的激光分别与桥梁形成一定夹角,如果船舶超高,则在船舶行进过程中,必然会依次触碰两束激光。 如图所示:当船舶接触到A发射的激光,监控中心弹出告警桥梁的实时画面,管理人员手机接收到告警桥梁的视频链接。 当船舶接触到B发射的激光,系统已经完全确定该船舶为超高船舶,前端桥梁上的告警设备开始工作,高音定向喇叭对船舶进行语音告警,LED显示屏进信息图像告警。
运用LED显示屏和信号灯对超高船舶进行安全行驶路线引导。
3、项目建设规划—四大模块
3.1桥梁防撞预警前端示意图-1
安全行驶
桥梁防撞预警系统就是在桥洞两侧安装智能激光预警器、高清网络摄像机、LED引导信息板、定向喇叭和声光预警设备。整套系统实现识别船舶、监控现场、智能预警的功能。
3.4桥梁防撞预警前端示意图-4
A
2
执法人员马上达到现场
警戒区
1
桥梁防撞预警系统前端使用定向喇叭。这种喇叭发射出均匀的超声波在空气中密度产生波动,转变成人耳可以听见的声音,就像探照灯一样,只能朝一个方向发出声音。
B
3
1000M以上
桥梁防撞预警系统
视频播放
谢谢聆听
感谢亲观看此幻灯片,此课件部分内容来源于网络, 如有侵权请及时联系我们删精确检测出 超高的船舶
引导超高船舶 安全行驶路线
及时现场进行 录像警示
桥梁防撞预警系统是利用现代化检测手段和多种预警手段提高航道运行的安全性,有效避免超高船舶进入航道造成交通意外事故。通过该系统,政府执法人员能够准确了解桥区通航情况,有效引导通航船舶,一旦发生紧急事件,系统能及时协调资源,通知执法人员现场执法,将不良影响降至最低。
智能激光预警器是国际领先技术的测距设备,其能发射出波长905纳米不可见激光,精确测量出设备与被测物体之间的距离,并把数据传送给桥梁防撞预警系统。
执法人员在控制室监控
2
A
预警区
B
3
1
1000M以上
桥梁防撞预警系统
两束水平射出的激光分别与桥梁形成一定夹角,如果船舶超高,则在船舶行进过程中,必然会依次触碰两束激光。 如图所示:当船舶接触到A发射的激光,监控中心弹出告警桥梁的实时画面,管理人员手机接收到告警桥梁的视频链接。 当船舶接触到B发射的激光,系统已经完全确定该船舶为超高船舶,前端桥梁上的告警设备开始工作,高音定向喇叭对船舶进行语音告警,LED显示屏进信息图像告警。
运用LED显示屏和信号灯对超高船舶进行安全行驶路线引导。
3、项目建设规划—四大模块
3.1桥梁防撞预警前端示意图-1
安全行驶
桥梁防撞预警系统就是在桥洞两侧安装智能激光预警器、高清网络摄像机、LED引导信息板、定向喇叭和声光预警设备。整套系统实现识别船舶、监控现场、智能预警的功能。
3.4桥梁防撞预警前端示意图-4
A
2
执法人员马上达到现场
警戒区
1
桥梁防撞预警系统前端使用定向喇叭。这种喇叭发射出均匀的超声波在空气中密度产生波动,转变成人耳可以听见的声音,就像探照灯一样,只能朝一个方向发出声音。
B
3
1000M以上
桥梁防撞预警系统
视频播放
谢谢聆听
感谢亲观看此幻灯片,此课件部分内容来源于网络, 如有侵权请及时联系我们删精确检测出 超高的船舶
引导超高船舶 安全行驶路线
及时现场进行 录像警示
桥梁防撞预警系统是利用现代化检测手段和多种预警手段提高航道运行的安全性,有效避免超高船舶进入航道造成交通意外事故。通过该系统,政府执法人员能够准确了解桥区通航情况,有效引导通航船舶,一旦发生紧急事件,系统能及时协调资源,通知执法人员现场执法,将不良影响降至最低。
车辆防撞预警系统研究PPT课件

将多个传感器采集的数据 进行融合处理,提高探测 结果的准确性和可靠性。
去噪技术
对传感器采集的数据进行 去噪处理,消除干扰信号, 提取有效信息。
目标跟踪技术
对探测到的目标物体进行 跟踪,实时监测其位置和 运动轨迹。
碰撞风险评估算法
碰撞概率评估
根据传感器采集的数据和车辆的行驶状态,评估 发生碰撞的可能性。
面临的挑战与解决方案
技术难题
如传感器精度、V2X通信稳定性等,需要不断进行技 术研究和改进。
成本问题
目前车辆防撞预警系统的成本较高,需要进一步降低 成本以扩大市场应用。
法规与标准
需要制定和完善相关法规与标准,以规范市场发展。
06 结论
研究成果总结
系统有效性
实时性分析
经过实验验证,车辆防撞预警系统能够有 效降低碰撞事故的发生率,减少人员伤亡 和经济损失。
信息采集
通过传感器、雷达、摄像头等设备采集车辆 周围的环境信息。
信息处理
将采集到的信息进行处理,包括去噪、滤波、 目标识别等。
碰撞风险评估
根据处理后的信息,判断是否存在碰撞风险, 并评估风险的等级。
预警输出
根据风险等级,选择合适的方式(如声音、 灯光、震动等)向驾驶员发出预警。
03 车辆防撞预警系统技术研 究
02 车辆防撞预警系统概述
车辆防撞预警系统定义
车辆防撞预警系统是一种利用先进的技术手段,对车辆周围 的环境进行实时监测,并在发现潜在的碰撞危险时向驾驶员 发出预警的装置。
它通过传感器、雷达、摄像头等设备获取车辆周围的环境信 息,经过处理后判断是否存在碰撞风险,并通过声音、灯光 、震动等方式向驾驶员发出预警,以避免或减少交通事故的 发生。
去噪技术
对传感器采集的数据进行 去噪处理,消除干扰信号, 提取有效信息。
目标跟踪技术
对探测到的目标物体进行 跟踪,实时监测其位置和 运动轨迹。
碰撞风险评估算法
碰撞概率评估
根据传感器采集的数据和车辆的行驶状态,评估 发生碰撞的可能性。
面临的挑战与解决方案
技术难题
如传感器精度、V2X通信稳定性等,需要不断进行技 术研究和改进。
成本问题
目前车辆防撞预警系统的成本较高,需要进一步降低 成本以扩大市场应用。
法规与标准
需要制定和完善相关法规与标准,以规范市场发展。
06 结论
研究成果总结
系统有效性
实时性分析
经过实验验证,车辆防撞预警系统能够有 效降低碰撞事故的发生率,减少人员伤亡 和经济损失。
信息采集
通过传感器、雷达、摄像头等设备采集车辆 周围的环境信息。
信息处理
将采集到的信息进行处理,包括去噪、滤波、 目标识别等。
碰撞风险评估
根据处理后的信息,判断是否存在碰撞风险, 并评估风险的等级。
预警输出
根据风险等级,选择合适的方式(如声音、 灯光、震动等)向驾驶员发出预警。
03 车辆防撞预警系统技术研 究
02 车辆防撞预警系统概述
车辆防撞预警系统定义
车辆防撞预警系统是一种利用先进的技术手段,对车辆周围 的环境进行实时监测,并在发现潜在的碰撞危险时向驾驶员 发出预警的装置。
它通过传感器、雷达、摄像头等设备获取车辆周围的环境信 息,经过处理后判断是否存在碰撞风险,并通过声音、灯光 、震动等方式向驾驶员发出预警,以避免或减少交通事故的 发生。
火灾自动报警系统PPT课件
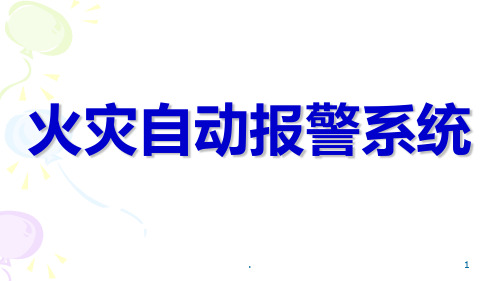
1)集中报警系统中可以有二台及以上火灾报警控 制器和消防联动控制器,但是只能设置或必须指定
其中的一台控制器,具有集中报警功能和集中控制
功能,其余控制器只作为附属设备。
2)对于水泵、风机等消防设施的专线手动控制必 须由起集中控制作用的控制器实现;对于水泵、风
机、电动排烟阀、挡烟垂壁等自动消防设施的总线 联动控制,可根据实际情况由其他相应的控制器实
现。
.
13
控制中心报警系统的组成
➢1)设置了两个及以上消防控制室; ➢2)设置了两个及以上集中报警系统。
.
14
控制中心系统的组成示意图
.
15
控制中心系统的组成示意图
.
16
控制中心报警系统消防控制室的设计要求
➢1)设置两个及以上消防控制室时,应确定一 个主消防控制室;
➢2)主消防控制室应能显示所有火灾报警信号 和联动控制状态信号,并应能控制重要的消防 设备;
➢2 任一台消防联动控制器地址总数或火灾报警控制 器(联动型)所控制的各类模块总数不应超过1600, 每一联动总线回路连结设备的总数不宜超过100,且
应留有不少于额定容量10%的余量。
.
23
控制器控制范围的设定
➢高度超过100米的建筑,除消防控制室 内设置的控制器外,每台控制器直接控 制的火灾探测器、手动火灾报警按钮和 模块等设备不应跨越避难层。
火灾自动报警系统
.
1
火灾自动报警系统的组成
火灾自动报警系统由火灾探测报警、消 防联动控制、电气火灾监控系统和可燃气体 探测报警系统等的部分或全部组成。
电气火灾监控系统和可燃气体探测报警 系统又被称为火灾预警探测报警。
.
2
火灾探测报警系统
- 1、下载文档前请自行甄别文档内容的完整性,平台不提供额外的编辑、内容补充、找答案等附加服务。
- 2、"仅部分预览"的文档,不可在线预览部分如存在完整性等问题,可反馈申请退款(可完整预览的文档不适用该条件!)。
- 3、如文档侵犯您的权益,请联系客服反馈,我们会尽快为您处理(人工客服工作时间:9:00-18:30)。
1#机组凝泵A电机轴承温度2
1#机组凝泵A电流
01/01—02/20 设备正常状态
02/20—03/20 劣化低频状态
03/20—04/01 劣化高频状态
04/01 凝泵A跳泵 设备损坏
2月21日
1#机组凝泵A电机轴承振动
2月21日分析人员发现凝泵A电机轴 承温度1,2,振动,电流出现预警 。观察趋势发现能够正常跟踪,检 修人员现场检查后,未发现设备损 热工定值 坏,数值在正常范围内,确认预警 (固定报 事件,建议延期观察。 1#机组凝泵A电机轴承温度 1
故障预警系统,对海量数据进行挖掘和分析,预知设 备异常,在设备损坏前,提前数周进行预警,使专业 人员有充足的时间进行状态检修。
目录
概述、必要性
预警系统同传统方法比较
案例分析 系统作用
原理
工作流程、路线及范围
传统方法与FPS动态预警比较
传统方法——监测单独测点, 固定报警 太迟,损失 已无法挽回
预警系统——监测所有测点, 早期发现
根据设备所 有关联测点 建立模型
测点A
测点B 测点C
提前数周发现设 备劣化状态进行 预警
测点D
数周时间内可制定检修计划,修 复设备,使设备恢复正常状态
传统方法监测的故障生命周期
传统方法
报警
设备损坏 或非停
设备故障 损失
设备正常状态
开始劣化
设备正常状态
设备劣化状态
原理
பைடு நூலகம்工作流程、路线及范围
案例分析 - 凝泵电机轴承温度过高案例
没有故障预警系统时故 障触发及处理方式
01/01—02/20 设备正常状态
02/20—03/20 劣化低频状态
03/20—04/01 劣化高频状态
04/01 凝泵A跳泵 设备损坏
2月21日 4月1日
1#机组凝泵A电机轴承振动
1#机组凝泵A电机轴承温度1
01/01—02/20 设备正常状态
02/20—03/20 劣化低频状态
03/20—04/01 劣化高频状态
04/01 凝泵A跳泵 设备损坏
1#机组凝泵A电机轴承振动
预警系统于1月 1日正式上线, 监视设备运行 状态
1#机组凝泵A电机轴承温度1
热工定值 (固定报警 ) 预警系统综合所有测点 建立模型,可以自定义 观察、监视设备任意测 点信息
01/01—02/20 设备正常状态
02/20—03/20 劣化低频状态
03/20—04/01 劣化高频状态
04/01 凝泵A跳泵 设备损坏
1#机组凝泵A电机轴承振动
3月21日
1#机组凝泵A电机轴承温度1
热工定值 幅增加,数值明显异常,偏离程度增大 (固定报 。当即命令相关人员启动凝泵B,停运 警) 凝泵 A,拆开凝泵A电机轴承,查找原因
。经检查发现电机轴承磨损十分严重, 必须马上更换才能继续使用。
3月21日分析人员发现预警事件频率大
1#机组凝泵A电机轴承温度2
电机轴承温度实际值与估计值频繁偏离 3度以上,达到70度以上,仍未达到90 度的固定报警热工定值,普通软件无法 检测到劣化状态。
1#机组凝泵A电流
01/01—02/20 设备正常状态
警)
其后,在2月21日到3月20日之间多 次发现预警产生,但现场凝泵A在运 行,未停下来查找具体原因。
1#机组凝泵A电机轴承温度2
期间,电机轴承温度实际值与估计值 多次偏离3度以上(动态报警带上限为 3度,超出则预警) ,从50多度突然 增大到60多度,设备已经开始劣化 ,但远远未达到90度的固定报警热 1#机组凝泵A电流 工定值。
热工定值 (固定报警 )
从2月21日到4月1日的 劣化状态未被发现
1#机组凝泵A电机轴承温度2
没有预警系统时,设备一直运行,直 到4月1日,电机轴承温度超过热工定 值90度,凝泵A跳泵,造成了设备损 坏,甚至有可能引起机组非停。
只监视单一测点, 与其他测点无关联
1#机组凝泵A电流
故障预警系统上线后故 障触发及处理方式
必要性
1 发电企业中, 设备运行好坏 至关重要,设 备故障对整个 系统影响巨大 传统办法--事 后分析,损失 已经形成
2
实时数据库中 海量数据堆积, 现有软件缺乏 应用,需要挖 掘和分析 利用数据建立 预知模型进行 预警
3
通过预警系统 能够提高管理 水平,让检修 进入到数字化 时代
故障开始
现有的传感器观测 设备看起来一直正常
未发现设备 劣化状态
直到故障发生, 才报警
因为现有的监测手段观测不到设备的劣化状态,不能对 历史数据和设备工况进行分析,触发报警时已太晚!
引入预警 - 预见性分析模式
预警系统
触发预警 检修完成
设备正常状态
设备劣化状态
机组恢复正常运行状态
开始劣化
捕捉故障早期征兆, 触发预警发现设备故障 分析 通知 解决
热工定值 (固定报警 经过检修处理更换,凝泵 A于4月1日恢 )
故障预警系统
演讲人:孙猛
目录
概述
传统软件同预警软件比较
案例分析 系统作用
原理
工作流程、路线及范围
概述
名称:Failure Prognostic System(FPS)故障预警系统 概述
FPS系统运用保存在企业基础信息系统中(DCS、厂级实时数据 库等)的设备原始海量运行数据,通过数据挖掘技术中的多元回归、 主分量分析等技术,在相似性理论支持下,转化成动态的设备在线模 型。将动态设备模型计算生成的实时预估值和设备测点的实测值进行 比较,并根据比较结果发布设备早期故障状态预警。 工作方法 采集设备所有测点的海量历史数据建立模型 计算实时数据预估值 比较实际值和预估值的偏差,异常时产生预警
02/20—03/20 劣化低频状态
03/20—04/01 劣化高频状态
04/01 凝泵A 恢复备用
1#机组凝泵A电机轴承振动
4月1日
1#机组凝泵A电机轴承温度1
复正常,恢复备用状态。其后,再次运 行后,发现设备状态已恢复正常。 避免了一次由于电机轴承损坏而引起的 凝泵跳泵,甚至可能导致机组非停的事 故,挽回了大量的经济损失。
预警系统根据历史 数据,针对设备建 立个性化高保真的 模型,从系统上线 时开始监测
提前预知性检修, 设备恢复正常状态, 避免了设备损坏和非计划停机
预见性分析使电厂可以主动维护设备,节约时间和费用, 避免了设备损坏及机组非停等严重损失。
目录
概述、必要性
传统软件同预警软件比较
案例分析 系统作用