橡胶无促进剂硫磺硫化
橡胶硫化
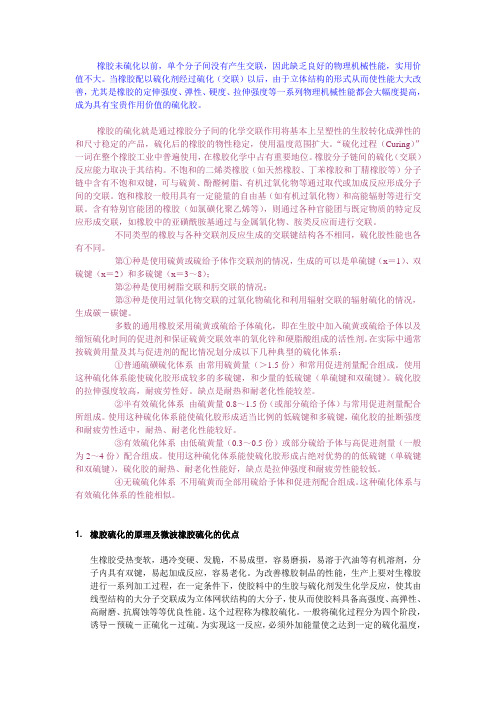
橡胶未硫化以前,单个分子间没有产生交联,因此缺乏良好的物理机械性能,实用价值不大。
当橡胶配以硫化剂经过硫化(交联)以后,由于立体结构的形式从而使性能大大改善,尤其是橡胶的定伸强度、弹性、硬度、拉伸强度等一系列物理机械性能都会大幅度提高,成为具有宝贵作用价值的硫化胶。
橡胶的硫化就是通过橡胶分子间的化学交联作用将基本上呈塑性的生胶转化成弹性的和尺寸稳定的产品,硫化后的橡胶的物性稳定,使用温度范围扩大。
“硫化过程(Curing)”一词在整个橡胶工业中普遍使用,在橡胶化学中占有重要地位。
橡胶分子链间的硫化(交联)反应能力取决于其结构。
不饱和的二烯类橡胶(如天然橡胶、丁苯橡胶和丁腈橡胶等)分子链中含有不饱和双键,可与硫黄、酚醛树脂、有机过氧化物等通过取代或加成反应形成分子间的交联。
饱和橡胶一般用具有一定能量的自由基(如有机过氧化物)和高能辐射等进行交联。
含有特别官能团的橡胶(如氯磺化聚乙烯等),则通过各种官能团与既定物质的特定反应形成交联,如橡胶中的亚磺酰胺基通过与金属氧化物、胺类反应而进行交联。
不同类型的橡胶与各种交联剂反应生成的交联键结构各不相同,硫化胶性能也各有不同。
第①种是使用硫黄或硫给予体作交联剂的情况,生成的可以是单硫键(x=1)、双硫键(x=2)和多硫键(x=3~8);第②种是使用树脂交联和肟交联的情况;第③种是使用过氧化物交联的过氧化物硫化和利用辐射交联的辐射硫化的情况,生成碳-碳键。
多数的通用橡胶采用硫黄或硫给予体硫化,即在生胶中加入硫黄或硫给予体以及缩短硫化时间的促进剂和保证硫黄交联效率的氧化锌和硬脂酸组成的活性剂。
在实际中通常按硫黄用量及其与促进剂的配比情况划分成以下几种典型的硫化体系:①普通硫磺硫化体系由常用硫黄量(>1.5份)和常用促进剂量配合组成。
使用这种硫化体系能使硫化胶形成较多的多硫键,和少量的低硫键(单硫键和双硫键)。
硫化胶的拉伸强度较高,耐疲劳性好。
缺点是耐热和耐老化性能较差。
橡胶硫化促进剂

橡胶硫化促进剂简介天然胶与合成胶用促进剂,具有宽广的硫化范围,可单独使用,或与二硫代氨基甲酸盐类、秋兰姆类、胍类和其它碱性促进剂并用。
主要用于制造轮胎、胶带、胶鞋和其他工业橡胶制品。
主要产品橡胶硫化促进剂ETU(Na-22) 、橡胶硫化促进剂DETU 、橡胶硫化促进剂ZDC(EZ) 、橡胶硫化促进剂ZDMC(PZ) 橡胶硫化促进剂ZDBC(BZ) 、橡胶硫化促进剂ZMBT(MZ) 、橡胶硫化促进剂TMTM 、橡胶硫化促进剂MBT(M)、橡胶硫化促进剂MBTS(DM)其中橡胶硫化促进剂ETU(Na-22)又称乙烯硫脲,其详细指标如下:分子式: C3H6N2S结构式:分子量: 102.17CAS编号: 155-04-4同类名称: Perkacit ETU,Robac 22,Rodanin S 62,Ekagom CLB指标名称:粉料纯度(%,≥) 98.0外观(目测:白色粉末初熔点(℃,≥) 195.0终熔点(℃,≥) 195.0-200.0加热减量(%,≤) 0.30灰份(%,≤) 0.30筛余物(63μm)(%,≤) 0.30杂质(个/g) 10性状:由乙醇中结晶的产品为针状结晶,从戊醇中结晶的产品为柱状捷径。
比重1.42-1.43。
熔点203-204℃。
有苦味。
易溶于水,溶于乙醇、甲醇、乙二醇和吡啶,不溶于丙酮、乙醇、氯仿等。
用途:本品系各种类型氯丁胶、氯磺化聚氯乙烯橡胶、氯乙醇橡胶、聚丙烯酸酯橡胶用的促进剂。
适于金属氧化物作硫化剂,尤以氧化镁、氧化锌作硫化剂时效果更好。
操作安全,不易燃烧。
本品特别适用于54-1(W)型及通用GN型氯丁胶。
在胶料中易分散、不污染、不变色。
在一般制品中用量为0.25-1.5份,在54-1(W)型氯丁胶耐水制品中用量为0.2-0.5份,并要配以10-20份的一氧化铅。
包装和储存 25Kg纸塑复合袋、牛皮纸袋或集装塑料袋。
储存在阴凉、干燥、通风的地方。
避免阳光橡胶硫化促进剂的定义加入橡胶胶料后能降低硫化温度或缩短硫化时间的物质,称之为硫化促进剂。
橡胶硫化剂和硫化助剂
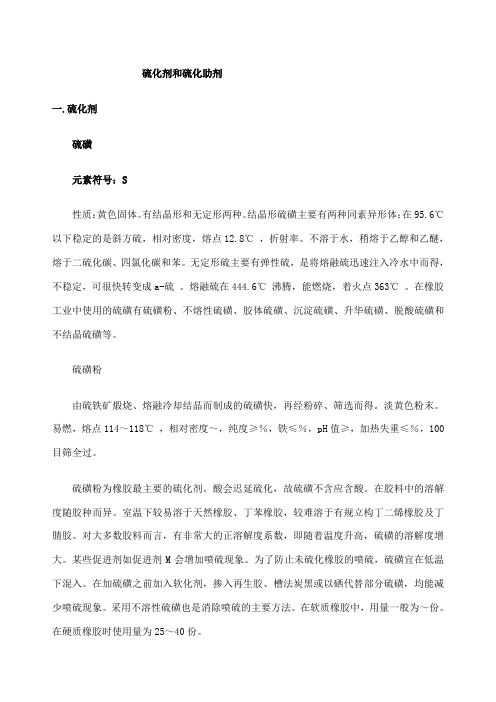
硫化剂和硫化助剂一.硫化剂硫磺元素符号:S性质:黄色固体。
有结晶形和无定形两种。
结晶形硫磺主要有两种同素异形体:在95.6℃以下稳定的是斜方硫,相对密度,熔点12.8℃,折射率。
不溶于水,稍熔于乙醇和乙醚,熔于二硫化碳、四氯化碳和苯。
无定形硫主要有弹性硫,是将熔融硫迅速注入冷水中而得,不稳定,可很快转变成a-硫。
熔融硫在444.6℃沸腾,能燃烧,着火点363℃。
在橡胶工业中使用的硫磺有硫磺粉、不熔性硫磺、胶体硫磺、沉淀硫磺、升华硫磺、脱酸硫磺和不结晶硫磺等。
硫磺粉由硫铁矿煅烧、熔融冷却结晶而制成的硫磺快,再经粉碎、筛选而得。
淡黄色粉末。
易燃,熔点114~118℃,相对密度~,纯度≥%,铁≤%,pH值≥,加热失重≤%,100目筛全过。
硫磺粉为橡胶最主要的硫化剂。
酸会迟延硫化,故硫磺不含应含酸。
在胶料中的溶解度随胶种而异。
室温下较易溶于天然橡胶、丁苯橡胶,较难溶于有规立构丁二烯橡胶及丁腈胶。
对大多数胶料而言,有非常大的正溶解度系数,即随着温度升高,硫磺的溶解度增大。
某些促进剂如促进剂M会增加喷硫现象。
为了防止未硫化橡胶的喷硫,硫磺宜在低温下混入。
在加硫磺之前加入软化剂,掺入再生胶、槽法炭黑或以硒代替部分硫磺,均能减少喷硫现象。
采用不溶性硫磺也是消除喷硫的主要方法。
在软质橡胶中,用量一般为~份。
在硬质橡胶时使用量为25~40份。
二.秋兰姆类促进剂这是一类相当重要的促进剂,它包括一硫化秋兰姆、二硫化秋兰姆和多硫化秋兰姆。
二硫化秋兰姆可用二硫化氨基甲酸钠经氧化制备,若使二硫化物脱去一个硫原子既得一硫化秋兰姆。
二硫化秋兰姆和多硫化秋兰姆因在标准硫化温度下释出活性硫,亦可作为硫化剂,使胶料不加硫磺即可进行硫化,此既所谓“无游离硫硫化”,通常成为“无硫硫化”。
采用秋兰姆类作为硫化剂的配合,也成为“无硫配合”。
作为促进剂,这类物质的活性介于二硫化氨基甲酸盐和噻唑类促进剂之间,但仍属超促进剂。
胶料的硫化温度一般不要远高于125~135℃以上,以便得到比较宽广的硫化平坦性,减少过硫危险。
橡胶硫化剂的研究进展

橡胶硫化剂的研究进展。
普通硫磺硫化的橡胶在停放时,易出现喷霜,且有焦烧倾向,极大影响最终产品的性能。
为弥补硫磺的不足,人们开始了硫磺的改性研究,成功的例子是聚合态硫磺或不溶硫(Insoluble Sulfur),简称IS,该硫磺为不溶於二硫化碳的线性高分子聚合硫,是硫的μ型体。
这种聚合态的硫磺平均分子量很大,经过不断验证,人们普遍认为其分子量为30000~40000。
不溶性硫磺在使用时通常分为充油型和未充油型两大类,而工业中使用的绝大多数(*99%)是充油型。
与普通硫磺相比,不溶性硫磺具有以下优点﹕(1)胶料在存放期内不会出现喷霜;(2)在胶料中无迁移现象(特别是在顺丁橡胶和丁基橡胶胶料中);(3)可减少混炼和存放过程中的焦烧现象;(4)有利於橡胶与其它材料的粘合;(5)可缩短硫化时间、减少硫磺用量。
不溶性硫磺可以通过硫磺的高温气相法或低温的熔融法制备,也可以通过硫化氢的氧化法制备。
低温熔融法是指普通硫磺在温度高於临界聚合温度(159℃)下按照反应机理(图2)开环聚合而成,反应结束後形成两端为自由基的链状分子,如果自由基不能被俘获,该活性中间体存在解聚的可能,这一过程为可逆聚合反应。
图2硫磺低温熔融聚合反应历程图与液相熔融不同,高温气相法是将硫磺加热至444.6℃以上,液硫沸腾气化,按自由能最小原理,气相硫的分子结构较小,主要是S8,S6,和S2。
温度越高,分子中的硫原子越少,当温度高於1000℃,硫主要以S2的方式存在。
低分子的硫反应活性很高,在快速降温的过程中很快聚合成份子量很大的聚合硫,其反应过程如下:通过上述方法制备的不溶性硫磺均属於亚稳态,稳定性较差,特别在较高硫化温度下很容易返还成普通硫磺,这将极大影响硫化胶的性能,也限制了它的应用。
因此提高不溶硫的稳定性是目前研究的重点。
国外做得最早也是最为成熟的是富莱克斯公司生产的Crystex样品,其高品位不溶硫的质量分数在90%以上,而且在高温条件下不溶硫的保持率也较高。
橡胶硫化促进剂 (2)
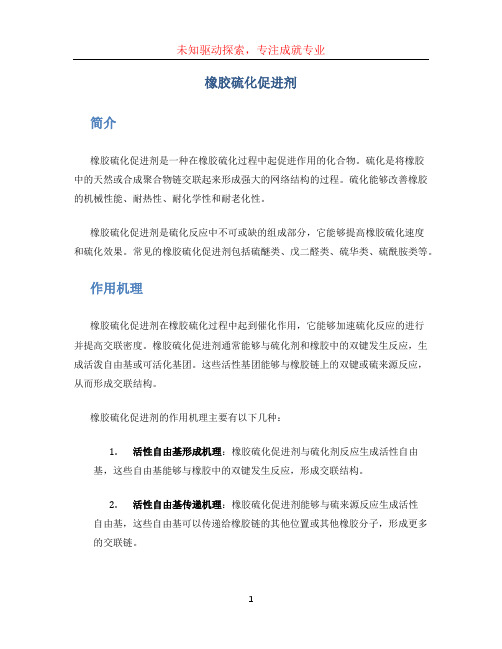
橡胶硫化促进剂简介橡胶硫化促进剂是一种在橡胶硫化过程中起促进作用的化合物。
硫化是将橡胶中的天然或合成聚合物链交联起来形成强大的网络结构的过程。
硫化能够改善橡胶的机械性能、耐热性、耐化学性和耐老化性。
橡胶硫化促进剂是硫化反应中不可或缺的组成部分,它能够提高橡胶硫化速度和硫化效果。
常见的橡胶硫化促进剂包括硫醚类、戊二醛类、硫华类、硫酰胺类等。
作用机理橡胶硫化促进剂在橡胶硫化过程中起到催化作用,它能够加速硫化反应的进行并提高交联密度。
橡胶硫化促进剂通常能够与硫化剂和橡胶中的双键发生反应,生成活泼自由基或可活化基团。
这些活性基团能够与橡胶链上的双键或硫来源反应,从而形成交联结构。
橡胶硫化促进剂的作用机理主要有以下几种:1.活性自由基形成机理:橡胶硫化促进剂与硫化剂反应生成活性自由基,这些自由基能够与橡胶中的双键发生反应,形成交联结构。
2.活性自由基传递机理:橡胶硫化促进剂能够与硫来源反应生成活性自由基,这些自由基可以传递给橡胶链的其他位置或其他橡胶分子,形成更多的交联链。
3.硫化剂活化机理:橡胶硫化促进剂能够与硫化剂进行反应,活化硫化剂,使其能够更容易与橡胶中的双键发生反应。
4.影响硫化温度的机理:橡胶硫化促进剂能够降低硫化的活化能,使硫化反应在较低的温度下进行。
常见种类1. 硫醚类硫醚类橡胶硫化促进剂是一类通过硫化剂与硫醚类化合物反应生成的活性自由基催化硫化反应的化合物。
常见的硫醚类橡胶硫化促进剂有DM(二甲硫醚)和MBTS(苯基甲硫醚)等。
硫醚类橡胶硫化促进剂主要适用于天然橡胶和合成橡胶的硫化反应。
2. 戊二醛类戊二醛类橡胶硫化促进剂是一类通过硫化剂与戊二醛类化合物反应生成的活性自由基催化硫化反应的化合物。
常见的戊二醛类橡胶硫化促进剂有HVA-2(环戊二醛)和DHBP(双环己基过氧化物)等。
戊二醛类橡胶硫化促进剂主要适用于硫化反应速度较慢的橡胶,能够加快硫化反应速度。
3. 硫华类硫华类橡胶硫化促进剂是一类通过硫化剂与硫华类化合物反应生成的活性自由基催化硫化反应的化合物。
橡胶的硫黄硫化作用

橡胶的硫黄硫化作用1839年和1843年固特异(Coodyear)和汉考克(Hancook)先后发现,将天然橡胶与硫黄共热后,就会变成坚实有弹性的物质。
这一过程即是硫化。
硫黄聚为硫化剂。
从发现用硫黄硫化橡胶时,由于成本低廉,来源丰富,硫化橡胶质量较好,至今仍广泛地应用于橡胶工业。
它不仅用于天然橡胶,而且可用于二烯类合成橡胶(丁苯橡胶、顺丁橡胶、异戊橡胶、丁腈橡胶)的硫化。
低不饱和度的丁基橡胶和某些硫化速度快的三元丙橡胶有时也可用硫黄硫化。
但是。
在生产上早已不是单独采用硫黄来硫化橡胶了。
有罪是单纯用黄硫化反应很慢,硫化时间硫黄用量多,且硫化胶结构复杂,性能不好。
但为便于比较和说明含有有机硫化会促进的硫化。
反应体系的性质,先讨论单用硫黄硫化的问题。
一、硫黄的性质和品种天然硫黄分子是由八个硫原子的环状结构,空间结构为冠型配位(如图3-3)。
它是淡黄色或黄色固体物质,不溶于水,易溶于二硫化碳(CS2,室温下为菱形晶体,熔点为113℃。
159℃时硫黄的八元环可以断裂,当受到橡胶大分子双键的极化作用时,其开环能量降低,140℃即可开环。
开环所生成的活泼双基硫黄(·S8·)能够与橡胶发生硫化反应。
橡胶工业常用的硫黄有如下品种1、粉末硫黄由块状硫黄经粉碎筛选而得。
其细度在200目以上,特殊情况也有600目以上者。
2、沉淀硫黄硫黄与氢氧化钙共热生成多硫化钙,再加入稀硫酸使硫黄沉淀出来。
其粒径为1~5微米。
纯度高,在胶料中分散性好,但成本高,仅于用高级制品。
3、胶体硫黄(高分散硫黄)粉末硫黄或沉淀硫黄加入保护胶体(分散剂),经球磨或胶体磨研磨而成,其粒径为1~3微米,适用于胶乳制品。
4、不溶性硫黄由粉末硫黄加热至沸点,倾于冷水中急冷而成。
它是透明的无定形弹性硫黄,不溶于二硫化碳。
使用这种硫黄不会喷硫,也不易产生早期硫化。
很适于高温短时间硫化。
但价格较贵。
一般用于特别重要的制品。
5、表面处理硫黄在硫黄粒子表面上包覆一层油类和异丁烯等物质,有利于分散。
橡胶硫化促进剂m工艺
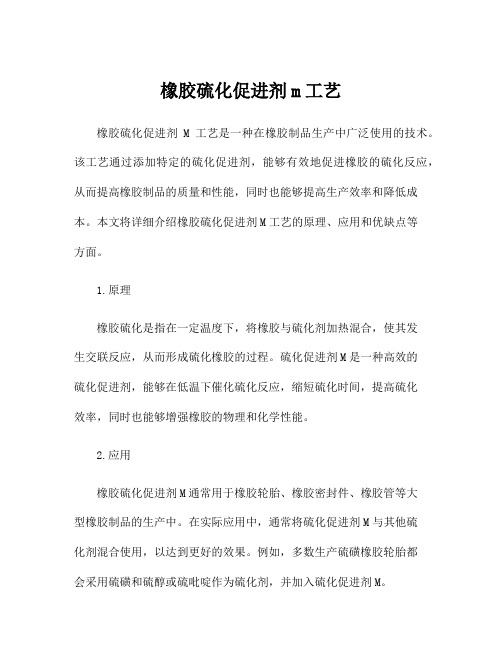
橡胶硫化促进剂m工艺橡胶硫化促进剂M工艺是一种在橡胶制品生产中广泛使用的技术。
该工艺通过添加特定的硫化促进剂,能够有效地促进橡胶的硫化反应,从而提高橡胶制品的质量和性能,同时也能够提高生产效率和降低成本。
本文将详细介绍橡胶硫化促进剂M工艺的原理、应用和优缺点等方面。
1.原理橡胶硫化是指在一定温度下,将橡胶与硫化剂加热混合,使其发生交联反应,从而形成硫化橡胶的过程。
硫化促进剂M是一种高效的硫化促进剂,能够在低温下催化硫化反应,缩短硫化时间,提高硫化效率,同时也能够增强橡胶的物理和化学性能。
2.应用橡胶硫化促进剂M通常用于橡胶轮胎、橡胶密封件、橡胶管等大型橡胶制品的生产中。
在实际应用中,通常将硫化促进剂M与其他硫化剂混合使用,以达到更好的效果。
例如,多数生产硫磺橡胶轮胎都会采用硫磺和硫醇或硫吡啶作为硫化剂,并加入硫化促进剂M。
3.优缺点优点:(1)硫化促进剂M能够缩短硫化时间,提高硫化效率,从而缩短生产周期。
(2)硫化促进剂M能够增强橡胶的物理和化学性能,使橡胶制品具有更好的耐磨、耐老化、耐热等性能,从而提高产品质量和使用寿命。
(3)硫化促进剂M使用方便,容易加工,不会对环境造成污染,符合环保要求。
缺点:(1)硫化促进剂M对一些橡胶品种的硫化效果并不理想,可能会出现硫化不良、硫化不完全等情况。
(2)硫化促进剂M价格较高,成本相对较高,对企业的经济效益有一定的影响。
4.注意事项在使用橡胶硫化促进剂M的过程中,需要注意以下一些事项:(1)硫化促进剂M应按照生产工艺要求控制加入量,过量使用或不当使用会造成反效果。
(2)硫化促进剂M与硫化剂、填料等混合物的过程中应注意搅拌均匀,以避免硫化不均、硫化不完全等现象。
(3)硫化促进剂M在存储和使用过程中应避免受潮、受热或受阳光直射,以保持其良好的性能。
总之,橡胶硫化促进剂M工艺在橡胶制品生产中具有重要的应用价值,能够提高橡胶制品的质量和性能,缩短生产周期,同时也存在一定的局限性和注意事项。
常用5类橡胶硫化剂简介
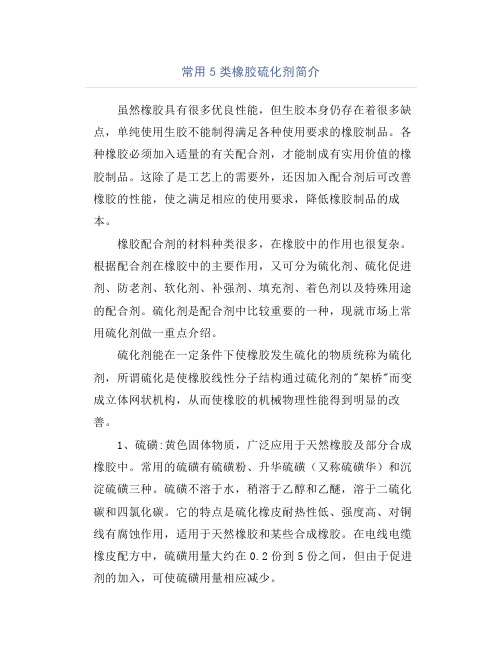
常用5类橡胶硫化剂简介虽然橡胶具有很多优良性能,但生胶本身仍存在着很多缺点,单纯使用生胶不能制得满足各种使用要求的橡胶制品。
各种橡胶必须加入适量的有关配合剂,才能制成有实用价值的橡胶制品。
这除了是工艺上的需要外,还因加入配合剂后可改善橡胶的性能,使之满足相应的使用要求,降低橡胶制品的成本。
橡胶配合剂的材料种类很多,在橡胶中的作用也很复杂。
根据配合剂在橡胶中的主要作用,又可分为硫化剂、硫化促进剂、防老剂、软化剂、补强剂、填充剂、着色剂以及特殊用途的配合剂。
硫化剂是配合剂中比较重要的一种,现就市场上常用硫化剂做一重点介绍。
硫化剂能在一定条件下使橡胶发生硫化的物质统称为硫化剂,所谓硫化是使橡胶线性分子结构通过硫化剂的"架桥"而变成立体网状机构,从而使橡胶的机械物理性能得到明显的改善。
1、硫磺:黄色固体物质,广泛应用于天然橡胶及部分合成橡胶中。
常用的硫磺有硫磺粉、升华硫磺(又称硫磺华)和沉淀硫磺三种。
硫磺不溶于水,稍溶于乙醇和乙醚,溶于二硫化碳和四氯化碳。
它的特点是硫化橡皮耐热性低、强度高、对铜线有腐蚀作用,适用于天然橡胶和某些合成橡胶。
在电线电缆橡皮配方中,硫磺用量大约在0.2份到5份之间,但由于促进剂的加入,可使硫磺用量相应减少。
2、金属氧化物:金属氧化物主要用于氯丁橡胶、氯磺化聚乙烯等的硫化剂。
常用的有氧化锌、氧化镁、氧化铅、四氧化三铅等。
氧化锌比重为5.6,是一种白色粉末,无毒、无味。
氧化锌在橡胶中应用比较广泛,在通用型氯丁橡胶中常与氧化镁并用作为主硫化剂。
在天然橡胶及其他烯烃橡胶中它可作为促进剂的活化剂。
除此之外它还兼有补强作用。
在耐日光老化的橡皮中起屏蔽紫外线的作用。
氧化锌在天然橡胶和丁基橡胶中用量为5~10份,在氯丁橡胶中与氧化镁并用一般用量为5份。
氧化镁氧化镁在氯丁橡胶中作为副硫化剂使用,混炼时能防止氯丁橡胶先期硫化。
本品能提高氯丁橡胶的抗拉强度、定伸强度和硬度。
能中和卤化橡胶等在硫化期间或在其他氧化条件下所产生的少量硫化氢。
橡胶用硫磺硫化的工艺流程
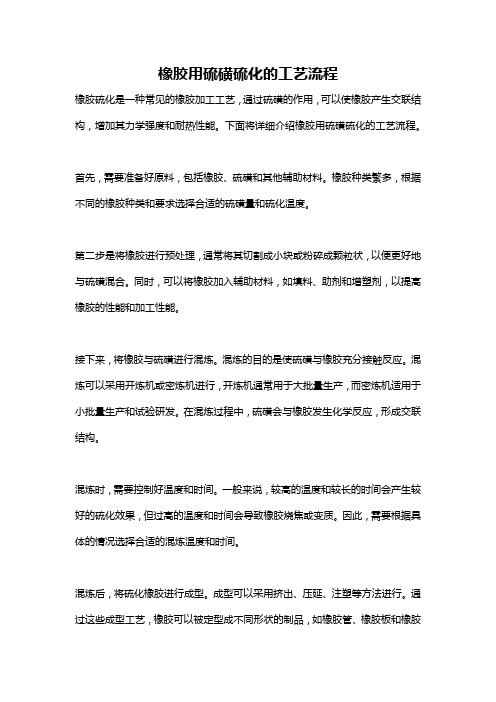
橡胶用硫磺硫化的工艺流程橡胶硫化是一种常见的橡胶加工工艺,通过硫磺的作用,可以使橡胶产生交联结构,增加其力学强度和耐热性能。
下面将详细介绍橡胶用硫磺硫化的工艺流程。
首先,需要准备好原料,包括橡胶、硫磺和其他辅助材料。
橡胶种类繁多,根据不同的橡胶种类和要求选择合适的硫磺量和硫化温度。
第二步是将橡胶进行预处理,通常将其切割成小块或粉碎成颗粒状,以便更好地与硫磺混合。
同时,可以将橡胶加入辅助材料,如填料、助剂和增塑剂,以提高橡胶的性能和加工性能。
接下来,将橡胶与硫磺进行混炼。
混炼的目的是使硫磺与橡胶充分接触反应。
混炼可以采用开炼机或密炼机进行,开炼机通常用于大批量生产,而密炼机适用于小批量生产和试验研发。
在混炼过程中,硫磺会与橡胶发生化学反应,形成交联结构。
混炼时,需要控制好温度和时间。
一般来说,较高的温度和较长的时间会产生较好的硫化效果,但过高的温度和时间会导致橡胶烧焦或变质。
因此,需要根据具体的情况选择合适的混炼温度和时间。
混炼后,将硫化橡胶进行成型。
成型可以采用挤出、压延、注塑等方法进行。
通过这些成型工艺,橡胶可以被定型成不同形状的制品,如橡胶管、橡胶板和橡胶密封件等。
最后,将成型的橡胶制品进行硫化处理。
硫化可以采用加热硫化和热压硫化两种方法。
在加热硫化中,将制品放入硫化箱或硫化室中,加热到一定温度,使硫磺与橡胶发生硫化反应。
热压硫化是在加热的同时施加压力,以加快硫化反应速度和提高硫化效果。
硫化温度和时间是硫化过程中的重要参数,需要根据橡胶种类和制品要求进行调整。
过低的温度和时间会导致硫化不完全,影响橡胶的性能;而过高的温度和时间会导致橡胶过硫化,出现老化和变质现象。
总结来说,橡胶用硫磺硫化的工艺流程包括原料准备、橡胶预处理、混炼、成型和硫化处理。
每个步骤都需要根据橡胶种类和制品要求进行操作,以保证橡胶硫化的效果和质量。
详解:橡胶硫化促进剂及其使用原则
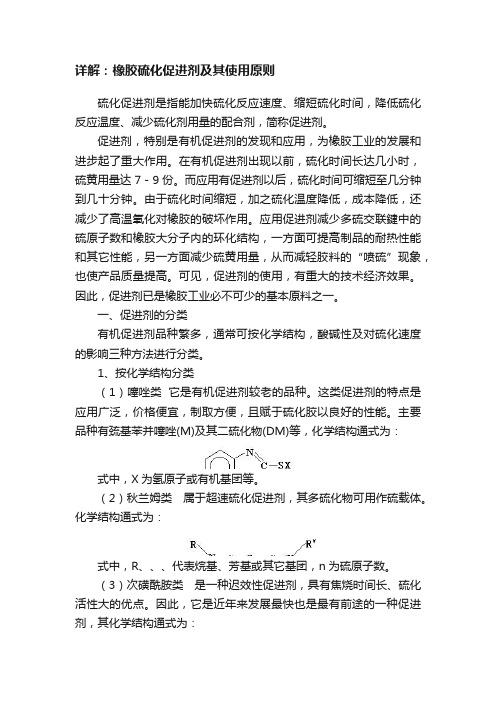
详解:橡胶硫化促进剂及其使用原则硫化促进剂是指能加快硫化反应速度、缩短硫化时间,降低硫化反应温度、减少硫化剂用量的配合剂,简称促进剂。
促进剂,特别是有机促进剂的发现和应用,为橡胶工业的发展和进步起了重大作用。
在有机促进剂出现以前,硫化时间长达几小时,硫黄用量达7-9份。
而应用有促进剂以后,硫化时间可缩短至几分钟到几十分钟。
由于硫化时间缩短,加之硫化温度降低,成本降低,还减少了高温氧化对橡胶的破坏作用。
应用促进剂减少多硫交联鍵中的硫原子数和橡胶大分子内的环化结构,一方面可提高制品的耐热性能和其它性能,另一方面减少硫黄用量,从而减轻胶料的“喷硫”现象,也使产品质量提高。
可见,促进剂的使用,有重大的技术经济效果。
因此,促进剂已是橡胶工业必不可少的基本原料之一。
一、促进剂的分类有机促进剂品种繁多,通常可按化学结构,酸碱性及对硫化速度的影响三种方法进行分类。
1、按化学结构分类(1)噻唑类它是有机促进剂较老的品种。
这类促进剂的特点是应用广泛,价格便宜,制取方便,且赋于硫化胶以良好的性能。
主要品种有巯基苯并噻唑(M)及其二硫化物(DM)等,化学结构通式为:式中,X为氢原子或有机基团等。
(2)秋兰姆类属于超速硫化促进剂,其多硫化物可用作硫载体。
化学结构通式为:式中,R、、、代表烷基、芳基或其它基团,n为硫原子数。
(3)次磺酰胺类是一种迟效性促进剂,具有焦烧时间长、硫化活性大的优点。
因此,它是近年来发展最快也是最有前途的一种促进剂,其化学结构通式为:式中R、为烷基、芳基或其它基团。
(4)胍类是碱性促进剂。
主要用作副促进剂。
化学结构通式为:式中R、为芳基或其它基团。
(5)二硫代氨基甲酸盐类是一种超速促进剂,多用于胶乳制品,某些盐类亦可作为硫载体,即作硫化剂使用。
其化学结构通式为:式中R、为烷基、芳基或其它基团,Me为金属原子,n为金属原子的原子价。
(6)醛胺类是醛和胺类的缩合物,一般为粘稠状流体。
化学结构通式为:RN=CH式中,R为芳基或脂肪族胺基,CH为醛基。
橡胶常用的六大硫化体系

橡胶常用的六大硫化体系橡胶常用的硫化体系有:1.硫磺硫化体系。
2.金属氧化物硫化体系。
3.过氧化物硫化体系。
4.树脂硫化体系。
5.醌肟类硫化体系6.多元胺硫化体系。
1.硫磺硫化体系可分为:常规硫化体系:由硫磺和少量促进剂等配合剂组成,以多硫键交联为主。
耐高温性能较差,压缩永久变形大,过硫后易出现返原现象,但耐屈挠疲劳行较好、机械强度较高,胶料及制品不易喷霜。
有效、半有效硫化体系:硫磺用量一般在0.5份以下,常用量为0.35份,配合较大量的促进剂,需要较长的焦烧时间(超速促进剂与后效性并用),活性剂应使用足量的硬脂酸(1-8份)。
几乎没有硫化返原现象,,硫化均匀性好,耐热性好,压缩变形低,生热小。
缺点为抗屈挠疲劳性差,易发生喷霜现象。
采用高TMTD的有效硫化体系配方虽然使用广泛,但加工稳定性差,切喷霜严重。
2.金属氧化物硫化体系:优点是硫化胶硬度和拉伸强度较高,并用环氧树脂后,可提高硫化胶的耐热性和动态性能。
常用的有氧化锌、氧化镁、氧化钙、氢氧化钙等。
氧化锌容易焦烧,加SA后可稍缓和焦烧倾向。
氧化镁和氧化钙焦烧倾向较小,并以氢氧化钙最好。
氧化镁用量以稍多为宜,增加用量可提高胶料硫化速度,并提高硫化胶强度和硬度。
缺点是生热大,耐屈挠性能差。
3.过氧化物类硫化体系:优点是压缩永久变形低,耐热耐寒性良好,胶料硫化时间短,不污染金属,便于制得透明橡胶。
缺点是一般不能用于热空气硫化,撕裂性能较差。
可分为①简单型:硫化体系只有有机过氧化物,或包括防焦剂。
该体系优点为硫化胶的压缩变形小,缺点是硫化过程中焦烧可控程度低,几乎不存在硫化诱导期。
②后效性:该体系硫化组分由过氧化物、活性剂和防焦剂组成。
特点是为可控制焦烧时间,又不影响硫化效率。
硫化特性与后效性硫磺硫化体系相似,过氧化物硫化体系温度系数比硫磺硫化体系高。
温度每提高10度,硫化速度约提高两倍。
(硫磺硫化体系提高一倍)焦烧性能亦是如此。
4.树脂类硫化体系:特点是形成热稳定较高的C-C键和醚键交联。
橡胶的硫化、促进、活化、防老、补强助剂概述

橡胶的硫化、促进、活化、防老、补强助剂概述一、硫化剂1、硫黄,分普通硫黄、不溶性硫黄、胶体硫黄、升华硫黄、脱酸硫黄。
硫黄是主要的硫化剂、酸会延迟硫化,故硫黄不含酸在胶料中的溶解度随胶种而异。
随着温度的升高,硫黄溶解度会增加。
某些促进如;M增加会增加喷硫的现象。
为了防止喷霜一般硫黄是最后低温加入的。
硫黄的用量一般为2—2.5份。
使用不溶性硫黄能避免胶料早期硫化极时喷霜。
2、含硫化合物,如二硫化二吗啡啉、四硫化吗非啉、秋兰姆类促进剂等。
3、过氧化物硫化剂,最典型的如过氧化二异丙苯DCP,在正常条件下贮存稳定,是毒性最低过氧化物之一。
用于天然、合成聚乙烯树脂。
不能硫化丁基橡胶。
用于白色、透明、压缩变型低,极耐热制品。
过氧化物的用量增加,交联密度增加、定伸应力增强、压缩变型改善、耐热性能甚优、抗撕裂性能变差。
二、促进剂橡胶中加入促进剂能促进橡胶与硫化剂之间的反应,提高硫化速度,降低硫化温度,缩短硫化时间,减少硫化剂用量,同时硫化胶的物理机械性能化学性质也得到改善。
A、不同的橡胶采用不同的硫化体系、不同的促进剂类型。
B、促进剂对焦烧性能起着决定性的影响,正确的促进剂选择有助于胶料的混炼、压延、压出及操作安全性。
一般模压硫化需有一定的焦烧时间,而无模硫则不需过长的焦烧时间。
C、促进剂的抗焦烧性能与其临界温度有关,超过临界温度促进剂迅速活化,多种促进剂的配合使用时,有些促进剂会受到抑制,有些促进剂在临界温度下也会出现较大的活性。
D、促进剂的搭配应使胶料具有宽广的硫化平坦性。
橡胶是热不良导体,胶料表面内部受热情况并不一至,宽广的硫化平坦性是避免过硫,并使制品各部份硫化均匀的保证。
E、促进剂的合理搭配还能改善硫化胶的老化性能,有一定的塑解作用,可改善胶料的加工性能。
缺点,促进剂分散性差、污染性、目前使用的促进剂一般是没有毒的。
促进剂的介绍1、二硫代氨基甲酸盐类,最常用的如PZ适用于要求压缩变型低的丁基橡胶、耐老化性能优良的丁睛橡胶、三元乙丙橡胶。
橡胶硫化工艺

硫化是指橡胶的线性大分子通过化学交联
而构成三维网状结构的化学变化过程。
未硫化:线性,链间可自由移动,受到外力时,分子 链重心产生相对位移,表现出较大的变形与塑性流动; 具有可溶性。
硫化后:链间产生化学交联成网状结构,使相对运动 受到了限制,外力作用下,链重心不发生位移,即失 去了流动性;不能溶解,只能溶胀。
➢cd段,相当于网络形成的前期,这时交联反应已 基本完成,继而发生交联键的重排、裂解等反应。 ➢交联、裂解同时存在,达到平衡,出现平坦区,对 应平坦硫化时间,其长短取决于胶料配方,主要是促 进剂和防老剂。 ➢胶料具有最佳综合性能,在该区选取正硫化时间
4、过硫化阶段
曲线继续上升,结构化作 用所致,通常非硫磺硫化 的SBR、NBR、CR、 E保PM持等较都长可平能坦出期现,这通种常现 象用硫磺硫化的SBR、
交联 分解 高 分 子 材 料 加 工 基 础*******
自由基(或离子) 高 分 子 材 料 加 工 基 础*******
根据是利于胶料在硫化过程中性能变化的特征来确定。
促进剂,使促进剂与硫磺
反应 高 分 子 材 料 加 工 基 础*******
高 分 子 材 料 加 工 基 础*******
橡胶
在形成网状结构时伴随着发生各种副反应。 其中橡胶与硫化剂的反应占主导地位,它是 形成空间网络的基本反应。
含促进剂、硫磺的橡胶硫化历程:
诱 促进剂
活化剂
第一阶段:诱导阶段
导
硫磺
期 先是硫磺、活化剂、促进 促进剂多硫化合物 曲线下降,网络裂解所致,NR的普通硫磺硫化是最典型的例子。
由液压泵通过平板硫化机把压力传递给模型,再由模型传递给胶料;
bc段,相当于硫化反应中 的交联反应阶段,胶料发生 交联反应,逐渐生成网状结 构,胶料的转矩或强度等性 能急剧上升。 ➢斜率大小代表硫化反应速率的快慢,斜率越大,硫 化反应速度越快,生产效率越高。 ➢热硫化时间的长短取决于硫化温度和胶料配方,通 常温度越高,促进剂用量越多,硫化速度越快。
橡胶的硫化及成型加工简介

橡胶的硫化及成型加工工艺【摘要】随着我国经济的高速发展,我国橡胶工业的技术水平和生产工艺得到很大程度上的提高。
硫化是橡胶加工的主要工艺之一,在这道工艺中,橡胶经过一系列复杂的化学反应及成型加工,失去了混炼胶的可塑性具有了交联橡胶的高弹性,仅为获得优良的物理机械性能、耐热性、耐溶剂性、及耐腐蚀性能,提高橡胶制品的使用价值和应用范围。
本文以氯丁橡胶为例,介绍橡胶的硫化及成型加工工艺。
【关键字】橡胶硫化行为成型加工工艺氯丁橡胶硫化是橡胶加工最后也是最重要的一个工艺过程。
在硫化过程中,由于橡胶的化学结构发生变化,导致其物理机械性能和化学性能得到显著改进,从而成为有价值的宝贵材料。
1 硫化对结构与性能的影响未硫化时,橡胶分子是呈卷曲状的线形结构,其分子链具有运动的独立性,大分子之间是以范德华力相互作用的。
当受外力作用时,大分子链段易发生位移,在性能上表现出较大的变形,可塑性大,强度不大,具有可溶性。
硫化后,橡胶大分子被交联成网状结构,大分子链之间有主价键力的作用,使大分子链的相对运动受到一定的限制。
在外力作用下,不易发生较大的位移,变形减小,强度增大,失去可溶性。
橡胶在硫化过程中,其分子结构是连续变化的,如交联密度在一定的硫化时间内是逐渐增加的。
硫化时所发生的化学反应是比较复杂的,交联反应和降解反应都在发生,交联反应使橡胶分子成为网状结构,降解反应使橡胶分子断键。
在硫化初期以交联为主,交联密度增加,到一定程度降解反应增加,交联密度又会下降。
硫化过程的橡胶分子结构的变化显著地影响着橡胶各种性能。
橡胶的各种性能随硫化时间的增加而有一定规律的变化。
上图说明在一定硫化时间内,永久变形随硫化时间的增加而逐渐下降;硬度随硫化时间的增加而逐渐增高;拉伸强度、定伸应力、弹性当增高到一定值后边便开始下降。
这些规律都是由于在硫化过程中橡胶分子链产生交联度不同所致。
以氯丁橡胶(CR)为例,随硫化程度的提高:1)力学性能:弹性、定伸强度、撕裂强度、硬度提高。
硫磺硫化中促进剂在橡胶中的反应机理
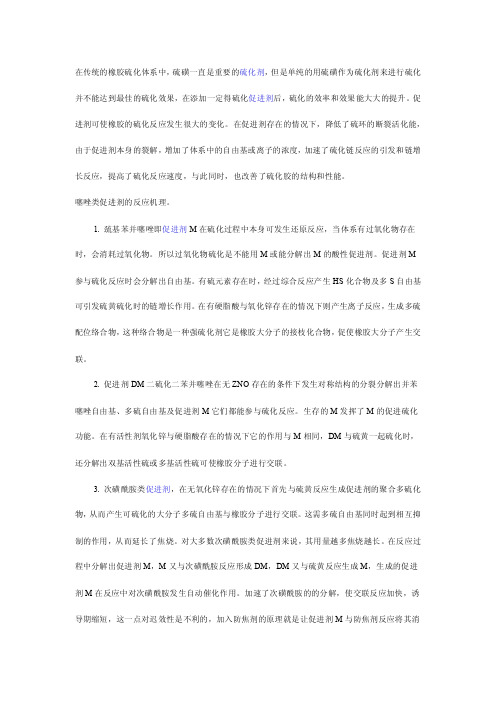
在传统的橡胶硫化体系中,硫磺一直是重要的硫化剂,但是单纯的用硫磺作为硫化剂来进行硫化并不能达到最佳的硫化效果,在添加一定得硫化促进剂后,硫化的效率和效果能大大的提升。
促进剂可使橡胶的硫化反应发生很大的变化。
在促进剂存在的情况下,降低了硫环的断裂活化能,由于促进剂本身的裂解,增加了体系中的自由基或离子的浓度,加速了硫化链反应的引发和链增长反应,提高了硫化反应速度,与此同时,也改善了硫化胶的结构和性能。
噻唑类促进剂的反应机理。
1. 巯基苯并噻唑即促进剂M在硫化过程中本身可发生还原反应,当体系有过氧化物存在时,会消耗过氧化物。
所以过氧化物硫化是不能用M或能分解出M的酸性促进剂。
促进剂M 参与硫化反应时会分解出自由基。
有硫元素存在时,经过综合反应产生HS化合物及多S自由基可引发硫黄硫化时的链增长作用。
在有硬脂酸与氧化锌存在的情况下则产生离子反应,生成多硫配位络合物,这种络合物是一种强硫化剂它是橡胶大分子的接枝化合物,促使橡胶大分子产生交联。
2. 促进剂DM二硫化二苯并噻唑在无ZNO存在的条件下发生对称结构的分裂分解出并苯噻唑自由基、多硫自由基及促进剂M它们都能参与硫化反应。
生存的M发挥了M的促进硫化功能。
在有活性剂氧化锌与硬脂酸存在的情况下它的作用与M相同,DM与硫黄一起硫化时,还分解出双基活性硫或多基活性硫可使橡胶分子进行交联。
3. 次磺酰胺类促进剂,在无氧化锌存在的情况下首先与硫黄反应生成促进剂的聚合多硫化物,从而产生可硫化的大分子多硫自由基与橡胶分子进行交联。
这需多硫自由基同时起到相互抑制的作用,从而延长了焦烧。
对大多数次磺酰胺类促进剂来说,其用量越多焦烧越长。
在反应过程中分解出促进剂M,M又与次磺酰胺反应形成DM,DM又与硫黄反应生成M,生成的促进剂M在反应中对次磺酰胺发生自动催化作用。
加速了次磺酰胺的的分解,使交联反应加快,诱导期缩短,这一点对迟效性是不利的,加入防焦剂的原理就是让促进剂M与防焦剂反应将其消耗一部份,来延长焦烧时间。
橡胶硫化处理

橡胶硫化处理摘要:1.橡胶硫化处理的概念和原理2.橡胶硫化处理的方法3.橡胶硫化处理的影响因素4.橡胶硫化处理的应用领域5.橡胶硫化处理的发展前景正文:一、橡胶硫化处理的概念和原理橡胶硫化处理是一种改善橡胶性能的重要工艺。
橡胶在经过硫化处理后,其物理、化学和机械性能都会得到显著提高,从而满足各种应用场景的需求。
橡胶硫化处理的原理是在一定的温度和压力下,使橡胶中的双键与硫磺发生反应,形成稳定的硫化橡胶。
二、橡胶硫化处理的方法橡胶硫化处理主要有以下几种方法:1.常规硫化:通过硫磺和促进剂的作用,使橡胶在一定温度下进行硫化。
这是最常用的硫化方法,适用于天然橡胶、合成橡胶等。
2.动态硫化:通过在橡胶中加入特殊的硫化剂,使橡胶在动态应力作用下进行硫化。
这种方法适用于生产轮胎等需要良好韧性和耐磨性的产品。
3.辐射硫化:通过放射线或紫外线照射橡胶,引发橡胶分子间的交联反应。
这种方法适用于医疗用品、食品包装等对硫化温度要求较高的领域。
三、橡胶硫化处理的影响因素橡胶硫化处理的效果受到以下因素的影响:1.硫磺用量:硫磺用量过多或过少都会影响硫化效果,需要根据具体情况进行调整。
2.促进剂:促进剂的种类和用量会影响硫化速度和效果。
不同种类的橡胶需要选用不同的促进剂。
3.硫化温度和时间:硫化温度和时间的选择要根据橡胶的种类和性能要求来确定。
4.橡胶的初始性能:橡胶的初始性能会影响硫化后的性能。
如橡胶的含胶量、含水量等都会对硫化效果产生影响。
四、橡胶硫化处理的应用领域橡胶硫化处理广泛应用于轮胎、胶带、胶管、密封件等橡胶制品的生产。
这些产品在经过硫化处理后,能够满足各种应用场景的需求,如耐磨、耐高温、耐油等。
五、橡胶硫化处理的发展前景随着科学技术的进步和环保理念的普及,橡胶硫化处理技术也在不断发展和创新。
- 1、下载文档前请自行甄别文档内容的完整性,平台不提供额外的编辑、内容补充、找答案等附加服务。
- 2、"仅部分预览"的文档,不可在线预览部分如存在完整性等问题,可反馈申请退款(可完整预览的文档不适用该条件!)。
- 3、如文档侵犯您的权益,请联系客服反馈,我们会尽快为您处理(人工客服工作时间:9:00-18:30)。
四、硫黄与橡胶的化学反应
• 1.硫环裂解生成双基活性硫。
S8
S8
Sx
S8-x
2.双基活性硫与橡胶大分子反应生成橡胶硫醇,硫化反应一般 是在双键的α-亚甲基上进行。
CH3
CH2 C CH CH2
Sx
CH3
CH2 C CH CH
HSx
CH3
CH2 C CH CH
HSx
CH3 CH2 C CH CH
SxH
S S1 S2 Sx Sn
Sx
Sn
S-S
图1-2 硫黄硫化的天然橡胶硫化胶结构示意图
课题2 橡胶的促进剂硫黄硫化(一)
促进剂指能降低硫化温度、缩短硫化时间、减少 硫黄用量,又能改善硫化胶的物理性能的物质。
活性剂
能增加促进剂的化学活性,提高硫化效率 ,改善硫化胶性能的化学药品。一般不直 接参与硫黄与橡胶的反应,但对硫化胶中 化学交联键的生成速度和数量有重要影响
• 4.双基活性硫直接与橡胶大分子产生加成反应。
CH3 2 CH2 C CH CH2
2 Sx
CH3 CH2 C CH CH2
Sx Sx CH2 C CH CH2
连邻位交联键
5.双基活性硫与橡胶大分子不产生橡胶硫醇也可以进行交联反应。
CH3
CH2 C CH CH2
Sx
CH3
CH2 C CH CH
S8
• (5)1920年,Bayer发现碱性物有促进硫化作用; • (6)1921年,发现了噻唑类、秋兰姆类促进剂,并逐渐认识到促进
剂的作用,用于橡胶的硫化中。在此之后又陆续发现了各种硫化促进 剂。
各种硫化剂发展状况
• (1)1846年,Parkes发现SCl的溶液或蒸汽在室温下也 能硫化橡胶,称为“冷硫化法”;
• ③一般不单独使用,常与M、DM、CZ等并用,既可以活化硫化体系 又克服了自身的缺点,只在硬质橡胶制品中单独使用。
• 另外,因其无毒无味,常用于与食品接触的制品。
• 6、硫脲类(中速中性) • 结构通式: • (1)主要品种 • ①促NA—22(乙烯基硫脲) • 用于ZnO,MgO作硫化剂的场合,此体系中加入噻唑类则
• 焦烧的危害:
• 加工困难;影响产品的物理性能及外表面光洁平整度;甚至会导致产 品接头处断开等情况。
• 预防焦烧的方法:
• (1)胶料的设计要适宜、合理,如促进剂尽可能采取 多种并用方式。 抑制焦烧。为适应高温、高压、高速炼胶工艺,在配方中还可配用适 量(0.3~0.5份) 的防焦剂。
• (2)加强炼胶及后续工序中对胶料的冷却措施,主要 通过严控机温、 辊温及保证有充沛的冷却水循环, 使操作温度不逾越焦烧临界点。
• 2、次磺酰胺类促进剂(准超速,中性,后效性)
• (1)主要品种
• 促AZ( 0.5~1.5份);促CZ( 0.5~2份);促NS( 0.5~1 份) ; 促NOBS(0.5~1 份);促 DIBS(0.4~1.5份) ;促 DZ (0.5~11 份)
• (2)特性
• ①焦烧时间长,具有后效性(目前各类促进剂中具有最高加工安全 性);硫化速度较快;硫化平坦性好;赋予硫化胶较好的综合性能。
CH3
CH2 C CH CH
RH
Sx
CH3
CH2 C CH CH
HSx
CH3
CH2 C CH CH
S8-x
Sx CH3
CH2 C CH CH
Sx CH2 CH C CH2
CH3
• 6.多硫交联键的移位
• NR在硫化过程中,当生成多硫交联键后,由于分子链上 双键位置等的移动,也有可能改变交联位置,如:
• (2)1915年,发现了过氧化物硫化; • (3)1918年,发现了硒、碲等元素的硫化; • (4)1930年,发现了低硫硫化方法; • (5)1940年,相继发现了树脂硫化和醌肟硫化; • (6)1943年,发现了硫黄给予体硫化; • (7)二战以后又出现了新型硫化体系,如50年代发现辐
射硫化;70年代脲烷硫化体系;80年代提出了平衡硫化 体系。
氧老化性能好。 • ③无毒,不污染,不变色。 • 例子1:IIR基本配方 • IIR 100 ; S 1.5;ZnO 3; 硬脂酸 1;HAF 50;促TT 1
• 4、二硫代氨基甲酸盐类(超速,酸性)和磺盐酸 盐类
• 结构通式 • ①二硫代氨基甲酸盐:
• ②磺原酸盐: • 常见品种 • 二硫代氨基甲酸盐类:PZ ZDC PX COD • 黄原酸盐类:ZBX ZEX
CZ 1.2
• 3、秋兰姆类(超速,酸性) • 结构通式 • (1)主要品种 • TMTM TBTS TMTD TETD TMTT • (2)作用特点 • ①硫化速度快,焦烧时间短,应用时应特别注意焦烧倾向。一般不单
独使用,而与噻唑类、次磺酰胺类并用; • ②可以作硫化剂使用,用于无硫硫化时制作耐热胶种。硫化胶的耐热
速、慢速。
③按酸碱性分 类
④按A、B、N (酸碱性)+ 数字1、2、3 、4、5(速级
)分类
橡胶小知识——焦烧
• 焦烧是 一 种超前硫化行为,即在硫化前的各项工序 ( 炼 胶、胶料存放、挤出、压延、成型)中出现的提前硫化现 象,故也可称为早期硫化。
• 产生焦烧现象的原因: • (1)配方设计不当,硫化体系配置失衡,硫化剂、促进剂用
➢粉末硫黄(硫黄粉) ➢沉降硫黄
➢胶体硫黄 ➢不溶性硫黄
2.硫黄在胶料中的用量及溶解特性
(1)用量范围
制品类型 硫黄用量
软质胶
0.2~5份
半硬质胶 8~10份
硬质胶
25~40份
具体制品例子 轮胎,胶管,胶带,胶鞋 胶辊,纺织皮辊 蓄电池壳,绝缘胶板
(2)溶解特性 ①溶解度随胶种而异 ②溶解度随温度升高而增大
量超常。 • (2)对某些需要塑炼的胶种,塑炼未达要求,可塑性太低,
胶质过硬,导致炼胶时急剧升温。炼胶机或其它辊筒装置 (如返炼机、压延机)辊温太高,冷却不够,也可能导致现 场焦烧。 • (3)混炼胶卸料时出片太厚,散热不佳,或未经冷却,即仓促 堆积存放,加上库房通风不良、气温过高等因素,造成热量 积累,这样也会引发焦烧。 • (4)胶料存放过程中管理不善,在剩余焦烧时间用尽之后, 仍堆放不用,出现自然焦烧。
降低胶料表面的粘着力,影响与其它部 件的粘合强度,给生产带来困难; 同时影响制品外观,成为质量缺陷。
在尽可能低的温度下或至少在硫黄的熔 点以下缩短时间且要混炼均匀;在胶料 中配用再生胶;加硫黄之前先加入某些 软化剂;使用槽法炭黑;硫黄和硒并用 均可减少喷硫,采用不溶性硫黄是消除 喷硫的最可靠方法。
• 二.硫黄的裂解和活性
• 硫在自然界中主要以菱形硫(Sα-硫)和单斜晶硫(Sβ硫)的形式存在,前者作为硫化剂使用。硫的元素形式为 S8,这种环状的硫黄分子的稳定性较高,需裂解才可反 应。
均裂 S8 双基活性硫
S8
异裂
S (+) (-)
8
• 三.不饱和橡胶分子链的反应活性
• (1)大分子链上双键数目多 • (2)α-H活泼,易发生取代反应。 • (3)取代基对双键有影响
的物质。
⑴ 无机促进剂 包括金属氧化物 (ZnO,MgO ,CaO,)目前 多作为活性剂、 碱(氢氧化物)
和盐类。
促进剂的分类
有机促进剂
有机促进剂
①按化学结构 分类(主要划
分方法)
噻唑类、次磺 酰胺类、秋兰 姆类、二硫代 氨基甲酸盐类
②按作用功能 分类(即按促 进硫化速度快
慢)
超超速、超速 、准超速、中
硫黄在天然橡胶中的溶解能力
100g橡胶中 硫黄的g数
溶解温度/℃ 析出温度/ ℃
1.5
20
—
1.0
29
—
2.0
39
—
3.0
54
16
4.0
67
35
5.0
78
58
7.0
97
82
橡胶小知识——喷硫现象
喷硫
产生喷硫 现象的原因
喷硫的危害
防止喷硫 的方法
过量的硫黄析出胶料表面形成结晶。
混炼不均匀;混炼温度过高; 配方中硫黄用量过高;停放时间过长 以及严重欠硫。
• 后效性——指具有较长的焦烧时间,较快的硫化速度等特点
• ②宜与炉法炭黑配合,有充分的安全性,利于压出、压延及模压胶料 的充分流动性;
• ③适用于合成橡胶的高温快速硫化和厚制品的硫化;
• ④与酸性促进剂(TT)并用,形成活化的次磺酰胺硫化体系,可以减 少促进剂的用量。
• 不足:能使橡胶变色,有一定的污染,有苦味,不适于纯白色及与食 品接触的制品,也不适于胶乳制品中。
CH3 CH2 C CH CH
Sx R
CH3
2 C CH CH Sx R
• 7.硫化过程中交联键断裂产生共轭三烯(多硫交 联键断裂夺取α-亚甲基上的H原子,生成共轭三 烯)
CH3
CH3
CH2 C CH CH CH2 C CH CH2 Sx
R
CH3 CH2 C CH CH CH
CH3 C CH CH2
橡胶硫醇
• 3.橡胶硫醇与其它橡胶大分子交联或本身形成分 子内环化物。
CH3 CH2 C CH CH
SxH
CH3 CH2 C CH CH2
CH2
CH3 C CH
CH2
CH Sx C CH2 CH2 CH3
CH3
CH3
CH2 C CH CH CH2 C CH CH2
SxH
CH3
CH3
CH2 C CH CH CH2 C CH CH Sx-1
• (3)重视胶料半成品的管理,每批料应有流水卡跟随,贯彻“先进先 出”的存库原则,并规定每车料的最长留库时间,不得超越。库房应 有良好的通风条件。